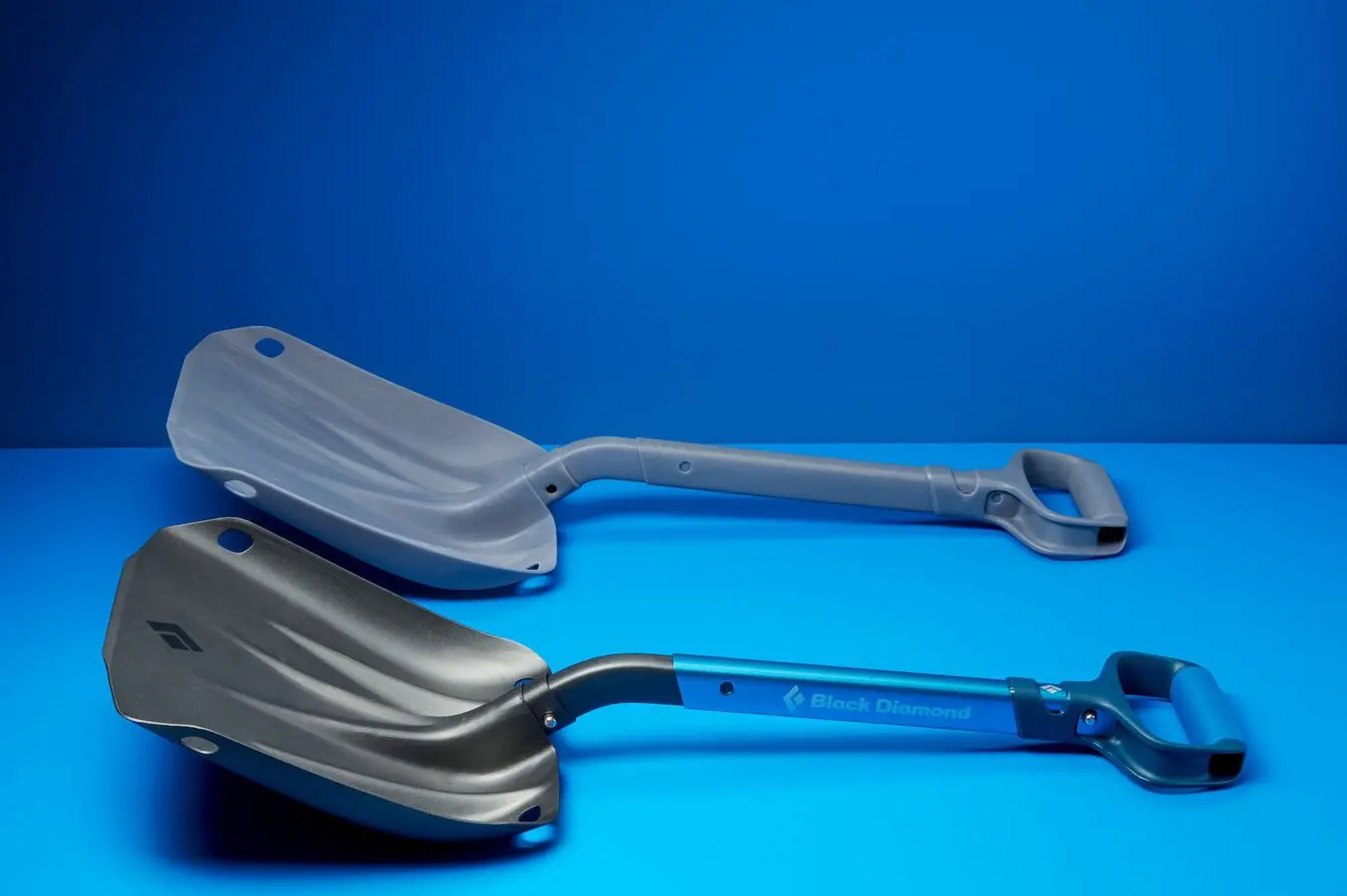
Black Diamond Equipmentでは、デザインチームで働く従業員に求める絶対条件があります。それは、同社が製作するギアに対して並々ならぬ情熱を持っていること。アウトドアクライミングと登山のエキスパートでもあるBlack Diamondの社員にとって、これは決して難しい条件ではありません。
Black Diamondのデザインチームは、細部への徹底的なこだわりにより、極めて高水準なギアを開発しています。信頼できる高機能な登山用品を製作することで、たとえ命綱一本で山壁にぶら下がっている状態であっても、安全で楽しい時間を過ごせるようにするためです。同社は設計工程で使用するツールも同様の高水準で選定しており、過去数年の間に、大容量光造形3Dプリンタ、デスクトップサイズの光造形3Dプリンタ群、SLS(粉末焼結積層造形)方式3Dプリンタなど、社内における3Dプリント導入を拡大させてきました。
今回、同社のProduct Design Labでマネージャーを務めるMatt Tetzl氏が、Black Diamondの設計工程について教えてくれました。その中で、Form 4、Form 3L、Fuseシリーズの活用でラボでの待ち時間が減り、ワサッチ山脈での製品試験により多くの時間を費やせるようになった背景についてもお話を伺いました。
高性能ギアの連続造形と検証
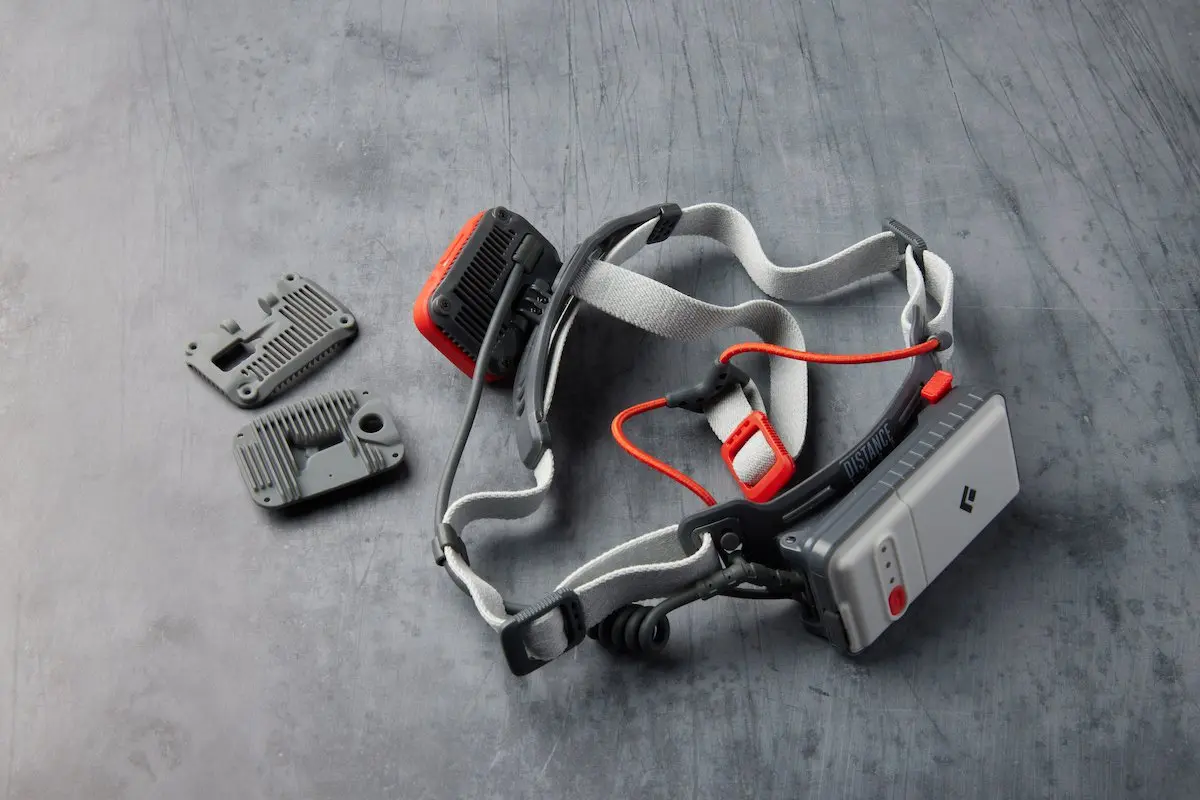
Form 4のスピードにより、Tetzl氏は写真のヘッドランプに使用する部品(写真左、GreyレジンV5で造形)の試作・検証プロセスを1日に3回繰り返すことができた。
Black Diamondのデザインチームに求められるのは、登山を始めたばかりの初心者でも快適な山登りができるような製品から、登山のプロの新記録達成を支援できるような製品まで、さまざまな課題に挑める製品の開発です。そのためには、製品によっては数百万サイクルにも及ぶ徹底的な検証が必要です。膨大な数の検証に対応するため、3Dプリントラボは24時間体制で稼働しています。Tetzl氏はこう言います。「弊社にはSLA光造形プリンタとSLSプリンタの両方がありますが、どちらも毎日稼働しています。依頼のあった部品を翌日には納品できること、これを何よりも大切にしているためです」
Tetzl氏は、Formlabsプリンタ専用のオンライン管理システムDashboardを使用して、光造形・SLSともに複数のチームから依頼を受けた造形品を管理しています。機能検証用部品は、これまで強度と耐久性に優れたNylon 12パウダーを使ってFuseシリーズで造形することがほとんどでしたが、今回のForm 4の登場が、多くの部品を再び光造形で製作するきっかけになりました。「Fuseを導入してからは毎日こちらを頼りにしていましたが、Form 4によって光造形にも比重が戻りつつあります。依頼があったその日のうちに造形品を納品できています」
初期の試作品や実製品用の機能試作を当日中に納品できること、これが設計チームにとって大きな利点となっています。「デザインレビューでは非常に優れた結果を発揮してくれています。造形に充てる日と試作・検証に充てる日を別々に設ける必要がなくなり、すべてを1日で完了できるようになりました」とTetzl氏は変化を語ります。
「ランプの開発案件があったのですが、その時はたった1日で3回もプリントできました。その日の午後のミーティングまでに、それぞれ異なる3種類のデザインを設計・造形して準備することができました」
Black Diamond Product Design Labマネージャー、Matt Tetzl氏
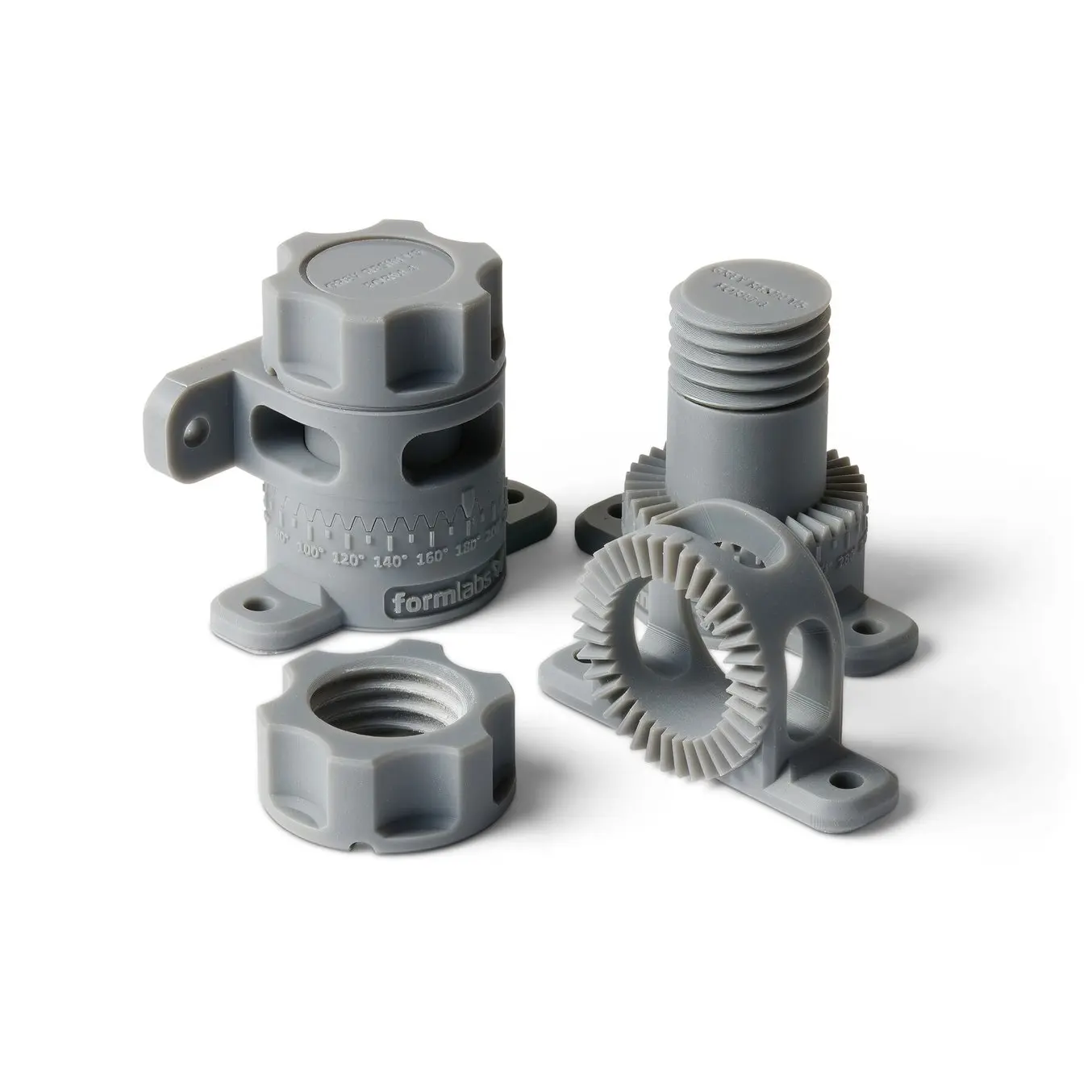
ラボでも山でも、求めるものは信頼性
登山初心者にとってもベテランのクライマーにとっても、装備が耐えられるかどうかではなく、目の前のトレイルや岩肌に集中できる環境が必要です。これは、ギアの設計でも同じです。Tetzl氏たちは、人間工学に基づくデザイン、材料の選択、疲労試験、その他さまざまな要素に焦点を当てて最高級のギアをデザインしています。造形の失敗や、造形品が公差内に収まるかどうか、といった心配をしている余裕はありません。そんな中、Form 4はセットアップ初日から製品作りに集中できる環境を提供してきました。「電源を入れたらすぐに使えるプラグアンドプレイです。ネットワークに接続さえすれば、あとは他のFormlabs製品と同じです。3Dモデルをアップロードし、ボタンをタップするだけで造形品ができあがります」とTetzl氏は言います。
セットアップから既存工程への組み込みまで、Form 4ならすべての工程をシンプルに行えます。Tetzl氏はこう続けます。「とても簡単でした。特殊な設定等もなく、プリンタを箱から出してレベリング(水平取り)をすれば、すぐに造形を開始できます。これまで使ってきたFormlabs製品と同じ使いやすさを感じます」
この使いやすさと信頼性のおかげで、Form 4での製作を決断しやすくなっています。「プリントの回数を重ねても99%は造形が成功する、という確信が持てます。たとえ1%の確率で失敗しても自分で改善することができますし、もしプリンタ本体が故障してもその日のうちに部品交換が可能です。この安定感を頼りにしています」とTezl氏は言います。
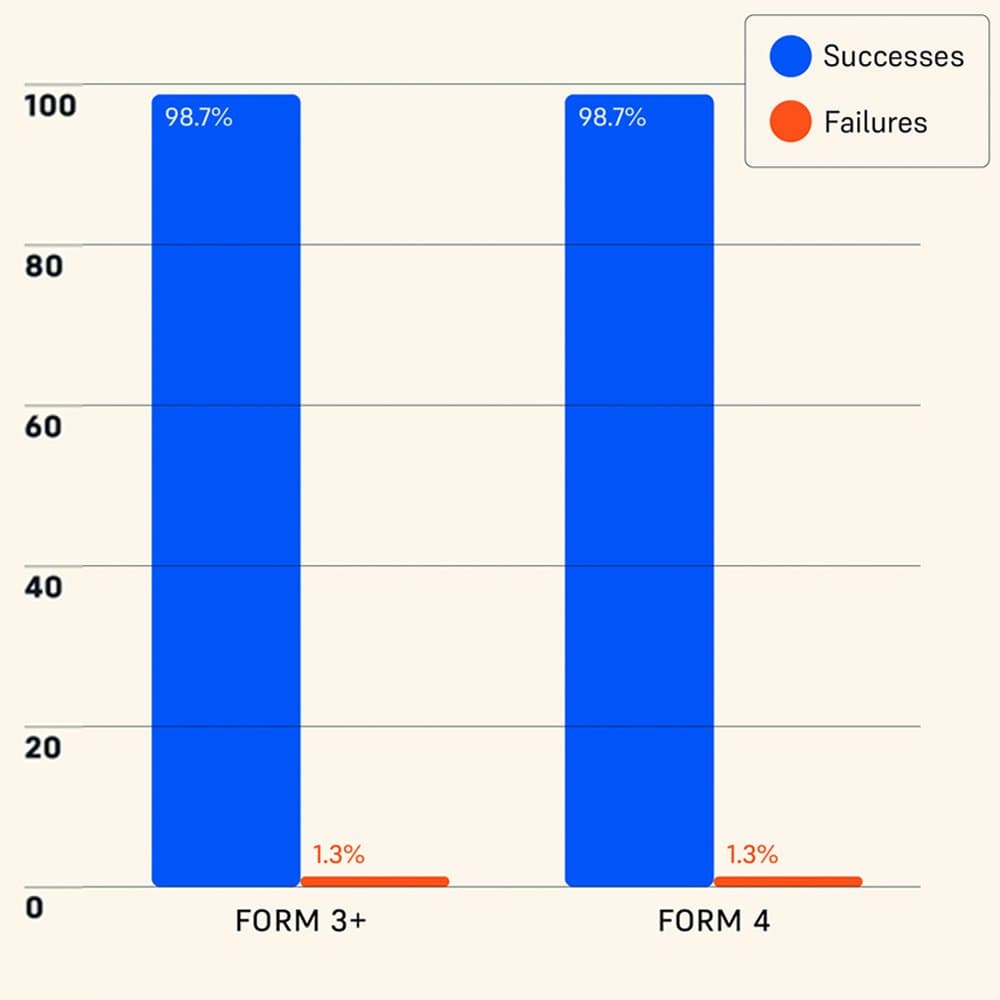
Form 4と他社製光造形3Dプリンタの信頼性に関する第三者試験
独立試験機関により、Form 4 のプリント成功率は 98.7 % と評価されました。テスト方法と結果の詳細についてはこちらの技術資料でご確認いただけます。
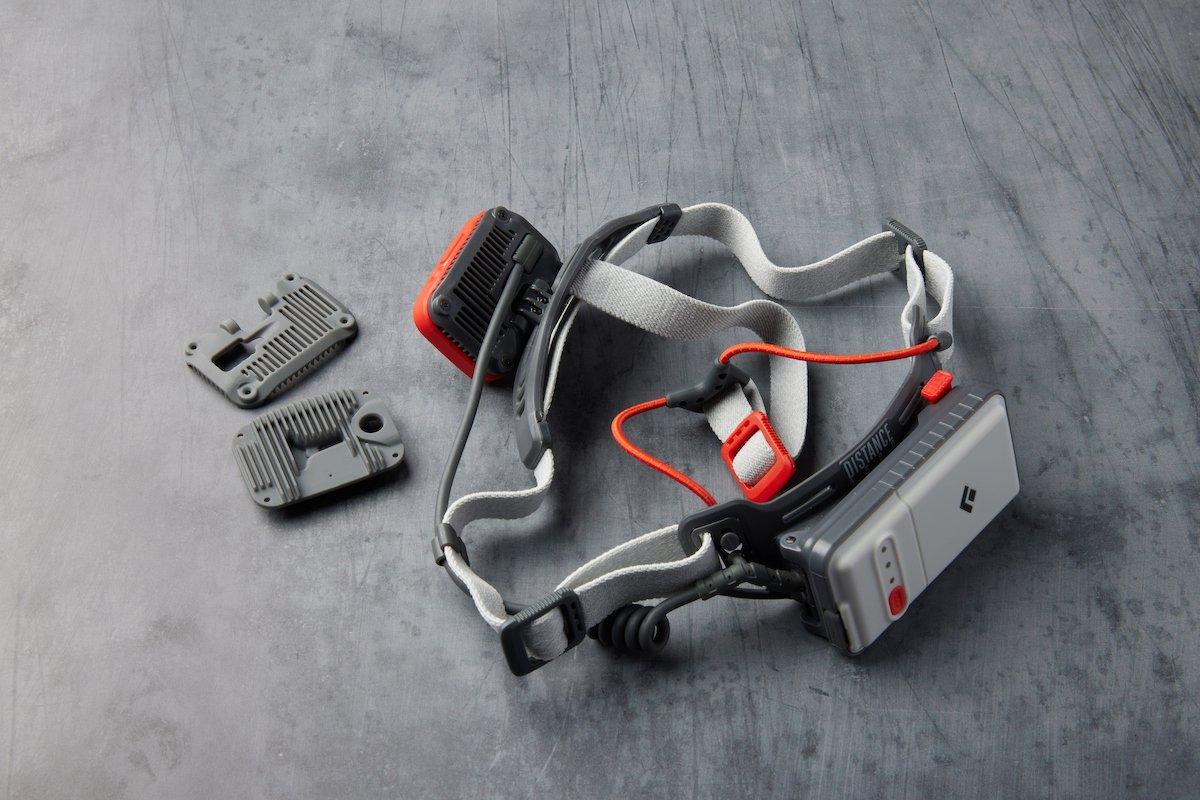
製品開発用ラピッドプロトタイピングガイド
本ガイドでは、製品開発工程にラピッドプロトタイピングを組み込む方法、活用事例、そして現代の製品開発で使用できるラピッドプロトタイピングツールをご紹介します。
材料の重要性:万能性、精度、高機能性
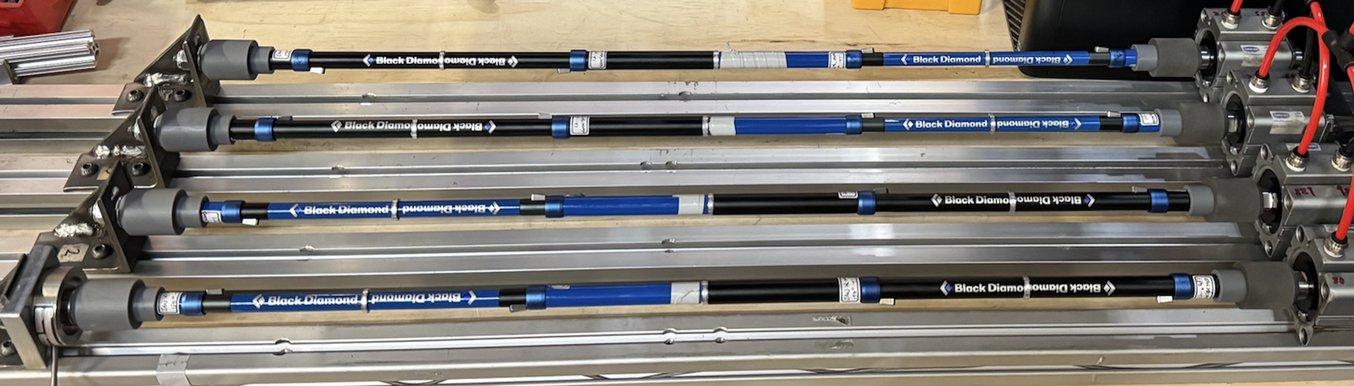
Form 4でGreyレジンV5を使って造形した治具を使ったトレッキングポール(左)とFuse 1+ 30WでNylon 12パウダーを使って造形した治具を使用したトレッキングポール(右)の疲労試験用セットアップ。
Black Diamond製のギアのように技術的に高度な製品の場合、開発工程ではさまざまな特性を持つ豊富な材料や広範な試験が必要になります。最近行われた軽量トレッキングポールの設計サイクルでは、Form 4と新材料のGreyレジンV5の性能が試されました。
トレッキングポールを構成する部品は、以前まではFuseプリンタでNylon 12パウダーを使って造形していました。「機能試験で使用する部品のほとんどはナイロン材料で製作するのですが、今回は数時間以内に複数の設計を試したくてForm 4で造形しました」とTetzl氏は言います。
最初は、トレッキングポールの広範囲にかかる圧力と摩擦にSLA光造形用レジンが耐えられるかどうか不安だったと言います。しかし、ポールに使用したGreyレジンV5製のボタンが各サイクル35ポンドの圧力で100万サイクル以上、さらにそこから100万サイクル以上も持ちこたえる様子を目の当たりにしたTetzl氏は、こう振り返ります。「以前のバージョンよりも強度が高まり、ヘルメットでは、Form 3での造形時よりもディテールが綺麗に表現できています」
このディテール表現は、デスクトップサイズとベンチトップサイズのプリンタ、Form 4とForm 3Lで造形するヘルメットの大型試作品では重要な要素だと言います。「表面品質が非常に高いですね。Form 4でGreyレジンとClearレジンを使って造形しましたが、どの造形品も高品質でみんな驚いています」
Form 3Lで可能性をさらに大きく
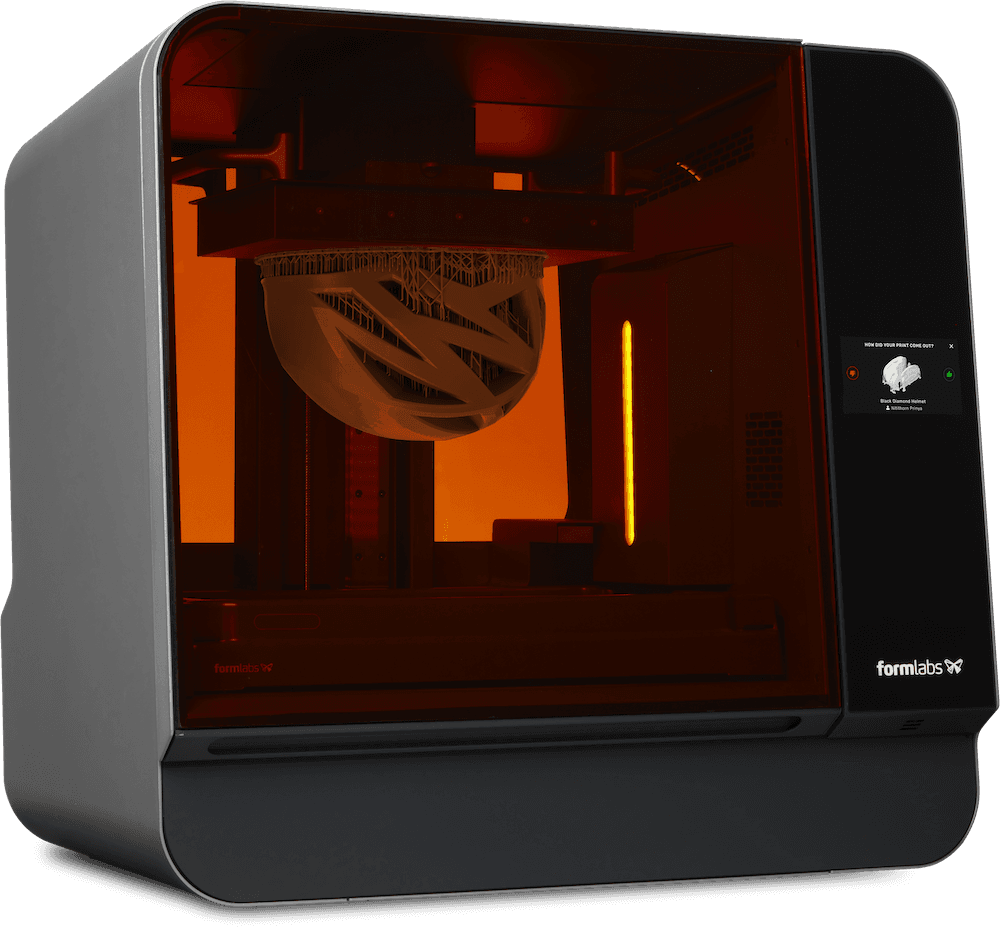
ベンチトップサイズの光造形3Dプリンタで、人間の体に合わせたサイズの試作品も表面品質や材料の選択肢を犠牲にせずに造形可能。
Form 3Lの持つスピード、材料の万能性、表面品質により、Black Diamondのデザインチームは工程の各段階をより細かくコントロールしながら、試作品を迅速に製作することができています。「当初は、ヘルメットの試作品製作のためだけにForm 3Lを購入しました。導入して数ヶ月は、『ヘルメット・プリンタ』と呼んでいたほどです。しばらくして、大容量の造形が必要になる数々のプロジェクトでも活用できると気づきました」とTetzl氏は言います。
Black Diamondは数年前、競争が激しく高度な技術が必要とされる製品カテゴリー、フットウェアの開発を社内で行うためのステップを踏み出しました。社内に靴職人を配属し、ヘルメットの造形用にForm 3Lを購入した時、フットウェア開発チームは可能性を感じたと言います。「フルサイズのミッドソールでも、非常に高い造形品質とディテール表現を実現できると気づきました。フットウェアチームはミッドソールに何度も何度も微小な変更を重ねて設計を改良するので、社内に大容量の造形が可能なマシンがあるというのは非常に大きなメリットです」とTetzl氏は言います。
当初は「ヘルメット・プリンタ」としてスタートしたForm 3Lが、すぐに部署内のさまざまなプロジェクトを実現する万能プリンタに変わりました。アイスツールの開発プロジェクトの最終段階では、Form 3Lを使って実物大の試作品を製作し、グリップ感や吊り具合をテストしました。複数の部品を組み合わせて作る試作品ですが、空中で分解してしまう心配も不要です。4年間の設計変更を経て、大容量光造形3Dプリンタを社内に導入したことで最終的な試作・検証プロセスがスピードアップしました。
Tetzl氏はこう言います。「アイスツールは、一日中眺めていても飽きないほどの外観ももちろんながら、最終的に重要になるのはグリップ感なんです。3Dプリントで試作品を製作し、大まかなグリップ感と吊り具合を把握できることは非常に大きいですね」
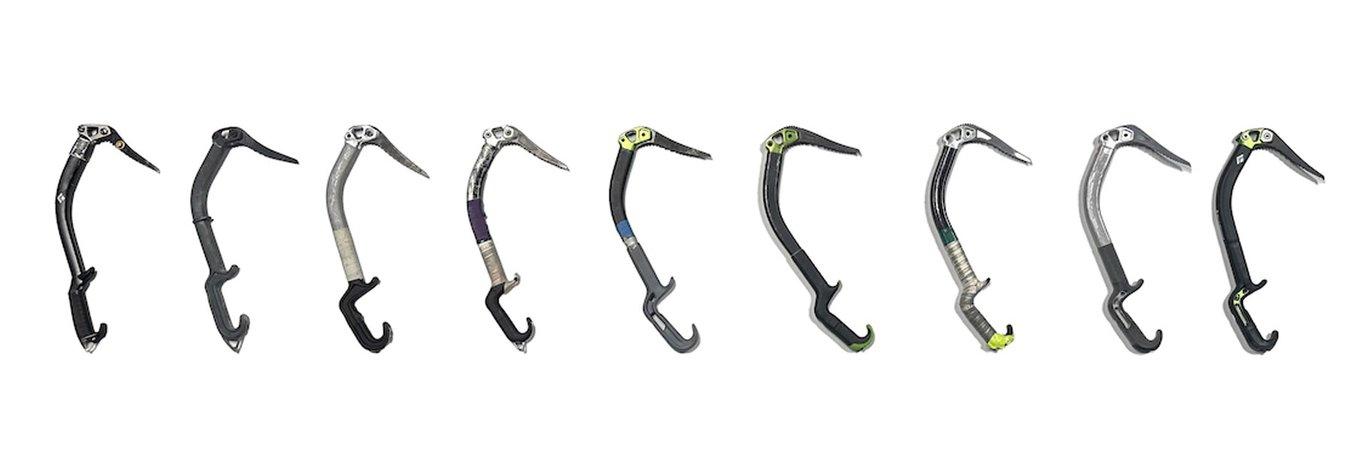
SLA光造形、SLSの両方を使って内製が可能なことで、複数の部品を組み合わせて作る構造でもグリップ感やスイングに影響を与えることなく試作品を製作できる。
部品の手触りは、材料によって左右されます。Tetzl氏は通常、大半の部品をGreyレジンで造形していますが、複数部品で構成されるウレタン型を作る際にはClearレジンを使用しています。「成形型を作る時、特にいくつもの部品を組み合わせて型を作るような場合には、Form 3LでClearレジンを使って造形しています。Clearレジンは仕上がりが非常に綺麗で、ウレタンが成形型のキャビティに流れ込む様子を確認できるところがいいですね」とTetzl氏は言います。Clearレジンで造形した成形型を洗浄・二次硬化した後、離型剤をスプレーしてからウレタンを流し込み、15分間圧力を加えます。成形型を3Dプリントで内製できることで、金型製作を外注することなく、UV耐性のあるウレタンなどの柔軟材料を使った機能試作の製作が可能になります。
大容量3Dプリンタを導入するまでは、金型製作やヘルメットなどの大型試作品の製作を外注していましたが、コストが高く設計工程が長引く原因にもなっていました。現在では、ヘルメット、フットウェアのミッドソール、成形型の製作工程をより細かくコントロールできるようになり、コストを抑えながら製作期間の短縮も実現しています。
内製したナイロン部品が実地試験などで活躍
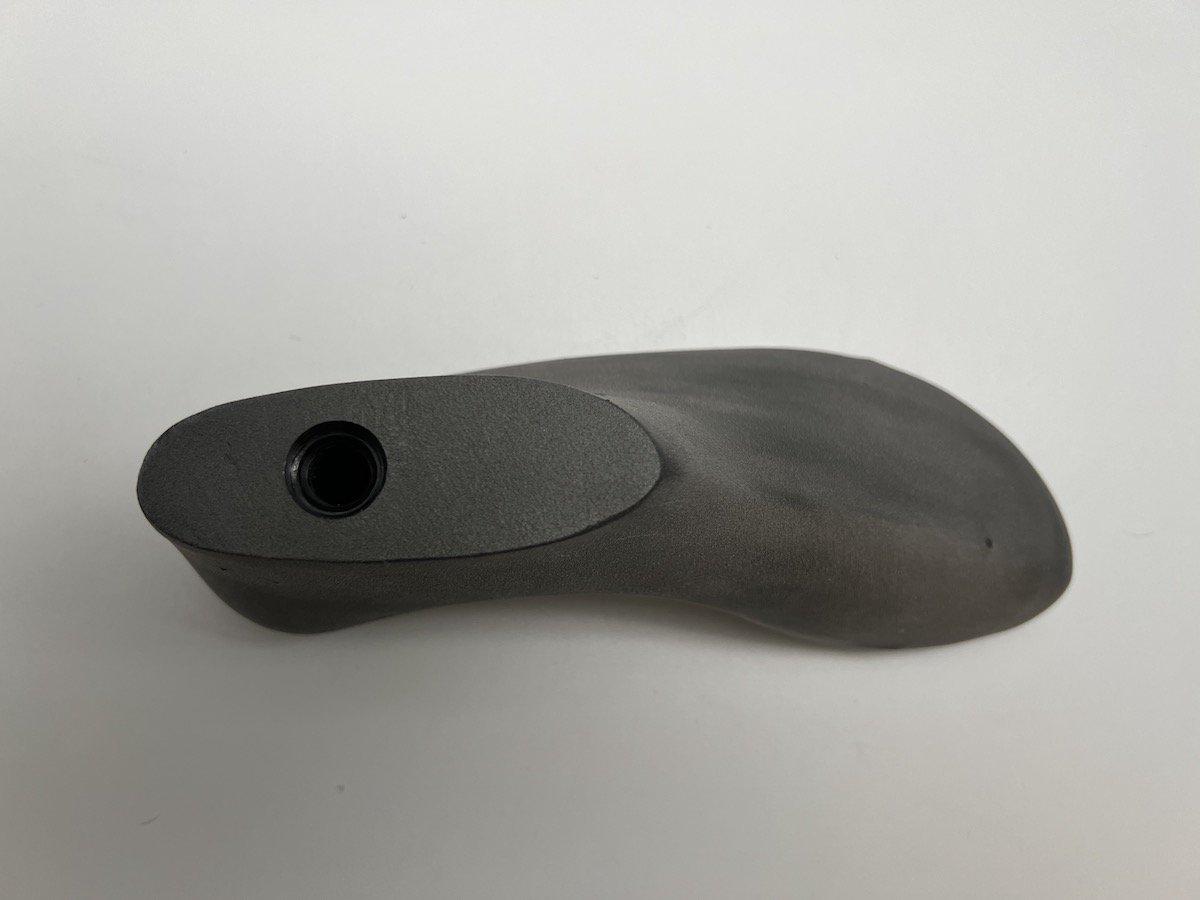
写真の靴型はFuse 1+ 30WでNylon 12パウダーを使用して内製したもの。通常、このようなナイロン製品の加工を外注すると最大$2,000かかるところ、3Dプリントを活用した内製ではわずか$65とコストの大幅削減が可能。
同社は、大容量光造形3DプリンタのほかにSLS方式3Dプリンタも導入しました。レジンを使った試作品でデザインレビューを行った後、より耐久性の高い実製品用材料を使用して実地での機能試験を行います。
Tetzl氏はこれまで、MJFプリンタのある3Dプリントメーカーに製作を外注していましたが、高額なコストがかかることが課題でした。「同じ材料を使って同じ工程を行えるのなら、内製の方が理にかなっています。製作のスピードも高速化できますし、コスト削減も実現できます。導入後は私たちの期待通りの成果が出ていて、ほとんどの部品でコストを80%削減できています」とTetzl氏は言います。
実地試験用の試作品では、強い衝撃や過酷な使用状況にも耐えられることが重要です。Nylon 12パウダーは強度と耐久性に優れているため、Black Diamondのチームは試作品を山に持って行って使用できるようになりました。2023年、カナダのエドモントンで開催されたアイスクライミング世界選手権で、Fuse 1+ 30WにてNylon 12パウダーで造形したグリップ搭載のアイスツールを使用した選手がいました。途中、ツールが80フィートの高さから落下することがありましたが、衝撃を受けても亀裂や損傷がありませんでした。「スキー用の機能部品や、かなりの荷重が繰り返しかかる落下試験機の内部部品を作ってきました。ようやく、高強度の3Dプリント製部品を内製できるようになりました」とTetzl氏は言います。
Fuse 1+ 30Wは、フットウェアの開発コスト削減にも役立っています。社内の靴職人は、靴やブーツの成形時に、通常はナイロンを旋盤加工した大判の靴型を使用します。これまでこういった大型パーツは外注していましたが、Fuse 1+ 30WにてNylon 12パウダーで造形できるようになったことで、靴型製作にかかるコストが$2,000からわずか$65まで下がり、さらに製作期間も短縮されました。「Fuseのおかげで、新しいフットウェア開発時のナイロンを使った生産をスケールアップすることができています」
同社のFuse 1+ 30Wは15%〜20%のパッキング率でほぼ毎日稼働しており、SLS 3DプリントによってBlack Diamondのフットウェア開発規模拡大および機能試験能力の向上が効率的に実現しています。
Form 4で生産能力を向上
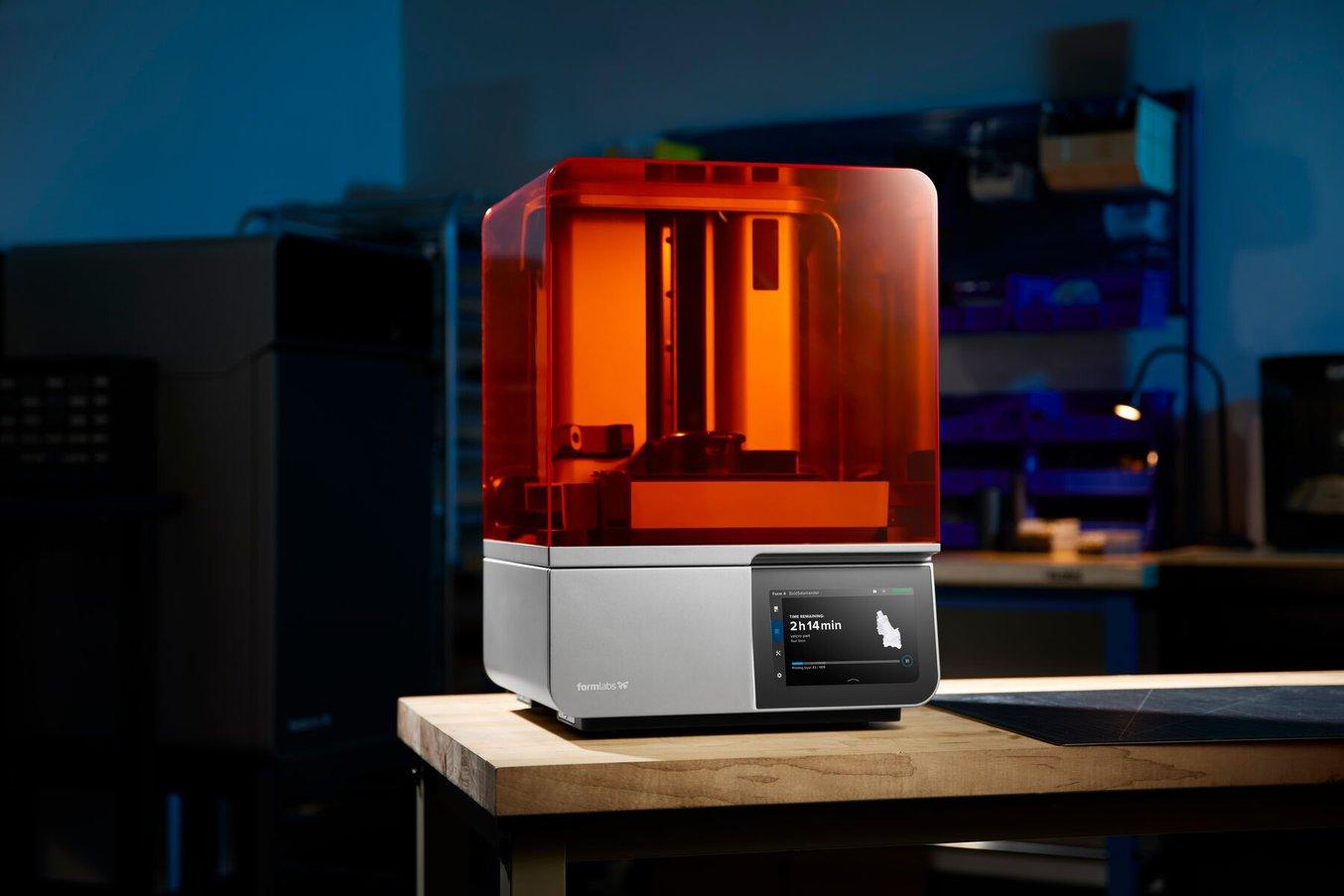
Form 4の信頼性とスピードが、新たな戦力としてBlack Diamondの3Dプリントを活用した生産に加わった。1日に何度も試作・検証プロセスを反復できることで、待ち時間を減らし、より多くの時間を登山用具の次のイノベーション創出に費やせる。
何百もの製品と途切れることのないプリントキューを抱えるTetzl氏が3Dプリンタに求めるものは、確かな信頼性とスピード、そして一貫した品質です。Black Diamondは、Form 2、Form 3、Form 3+、Form 3L、Fuse、そして今回のForm 4と、数年に渡りFormlabsの3Dプリンタに投資をしながら作業手順を構築してきました。クライマーやハイカー、登山家がレジャーとして楽しむ、そして時には命をも預けるギアを製作するBlack Diamondには、信頼できるツールが必要です。この信頼性は、たとえスピードや材料の選択肢を増やすためであっても、決して妥協することはできません。Tetzl氏は、使い慣れた製品群の中でこれらを実現することができています。
「Form 4では、まだ一度も造形に失敗していません」
Black Diamond Product Design Labマネージャー、Matt Tetzl氏
Form 4のスピードにより、造形品が出来上がるまでの待ち時間を減らし、ワサッチ山脈で業界屈指の製品を検証するという、Black Diamondのメンバーが最も楽しみにしている工程にできるだけ多くの時間を費やすことができます。