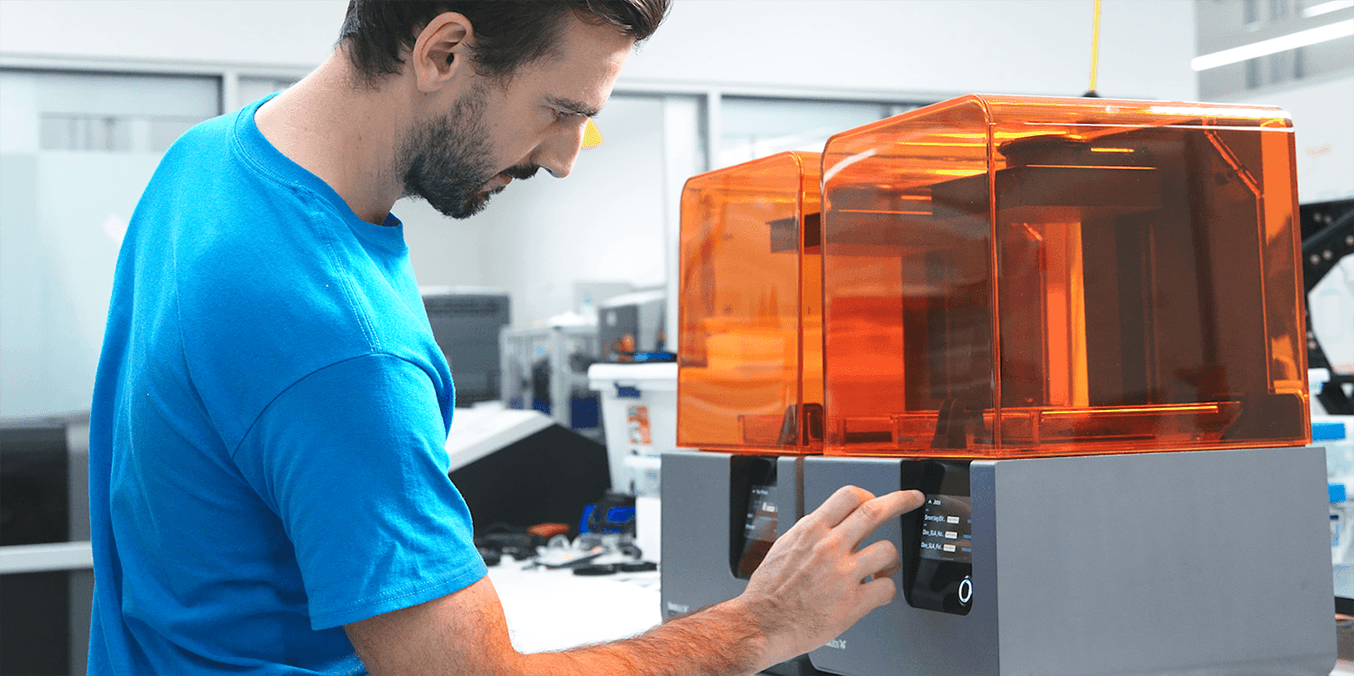
Googleアドバンスト・テクノロジー&プロジェクト(ATAP)ラボは、ハードウェアに関するプロジェクトをワンストップで担当する部門として設置されたラボです。Google ATAPは、製品自体とその生産技術に関しての方向性を定める役割を果たしていますが、開発のあらゆる段階における同社独自の考え方から、クリエイティブかつ迅速なソリューションを実現する先端技術を用いた設備機器に至るまで、あらゆる企業にとって学ぶところのある問題解決アプローチを採用しています。
ある事例では、オーバーモールドで量産を行うウェアラブルデバイスの検証段階で、複雑なサプライチェーンを利用する時間とコストを回避するプロセス革新につながる出来事がありました。高い耐熱性を持つ3Dプリント材料であるFormlabsのHigh Tempレジンを使用することで、量産用の金型を起こすことなくプリプロダクションを行い、中核的な部品の製作期間を85%も短縮し、10万ドル以上のコストを節約することができました。
Google ATAPが、Formlabsの3DプリンタとHigh Tempレジンでオーバーモールドで量産が予定されていた複雑形状のウェアラブルデバイスのプリプロダクションを効率化した3Dプリントの活用法を動画でご覧ください。
「我々は、各製品が将来的にどのような方向に進化していくかを調査するだけでなく、その生産技術がどのように進化するかも調査しています。アディティブマニュファクチャリングはその中でも大部分を占めており、我々が取り組むプロジェクトの多くで実際に活用したり採用を検討しています」と、3Dプリントなどのデジタル生産技術を専門とするGoogle ATAPの設計技術者Bryan Allen氏は言います。
「3Dプリントの世界で現在進行形で起こっている技術革新や新材料、より良い作業工程などに出会った時、そしてそれを実際のプロジェクトで導入できる道筋が見えた時は本当にエキサイティングだと感じます。それを導入することで、実際に更なる効率化、高速化、改善、そしてより美しいデザインが実現できるようになるからです」。
実例からのケーススタディ:プリプロダクションでの課題
Google ATAPは壁にぶつかっていました。あるウェアラブルデバイスのプリプロダクション品をオーバーモールドで製作する段階で、製作期間を大きく短縮する必要に迫られていました。旧来のオーバーモールドとは違った斬新な方法を採用したためサプライチェーンも複雑になっており、プリプロダクション工程をクリアするにはこのソリューションを確立する必要があったのです。「Google ATAPラボのモデルショップマネージャーでDavid Beardsley氏は「我々のプロダクトは、オーバーモールドを複数回繰り返して製造する電子機器で、その工程だからこそ必要な柔軟性と防水性が達成できるといったものでした。」
オーバーモールド自体は一般的な生産技術です。電子機器ではない一般的なオーバーモールド品であれば、工場は部品やアセンブリ1つあたり非常に低いコストで何千もの成形品を作ることができるでしょう。しかしGoogle ATAPは、別の工場から調達した複雑な電子回路を持つプリント基板アセンブリ(PCBA)を含めてオーバーモールドで作るモジュールの上から再度オーバーモールドを行って製造するという工程を想定していました。そのため金型を起こすイニシャルコストは非常に高額になり、上工程を担当する工場がPCBAをどれだけ短納期で生産できるかが課題解決の分かれ目となっていました。
オーバーモールドは射出成形の一種です。通常は成形のために金型を起こす必要があります。こうして作られる初期の成形品は、金型の微調整が進むにつれて材料の充填不足や過多、あるいは外観上の問題が発生する可能性があります。これらの課題解決に取り組む間、製造技術者たちは金型の嵌め合いが適切になされているか、型締めや射出の圧力が適正かなど、すべてのパラメータが適正なものとなっているかどうかを確認します。
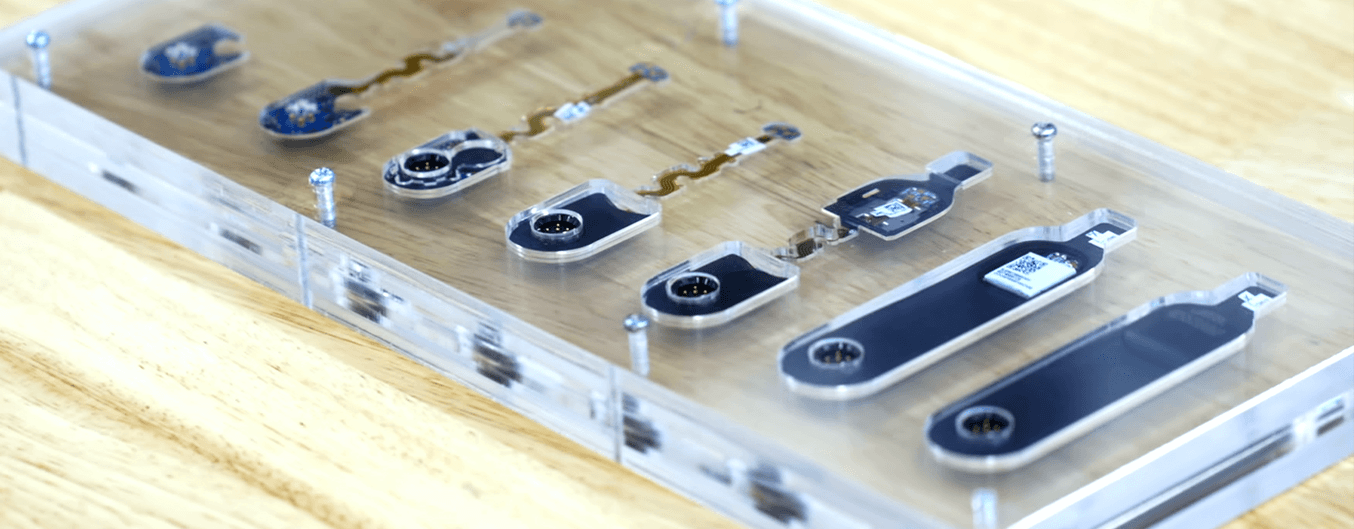
このウェアラブルデバイスの製造は、PCBボードに各部品を実装するところから始まります。このPCBは低圧での成形でカプセル化され、樹脂製のブロック状になります。このPCBのブロックと柔軟性のあるフレキシブルケーブルがサブアセンブリとなり、TPU(熱可塑性ポリウレタン)とシリコンでオーバーモールドを行います。その後PCBAは再度のオーバーモールドを経て完成品となります。Google ATAPは一般的な射出成形品よりも金型製作コストがはるかに高くなることをプリプロダクション段階で既に理解していました。予期していなかったのはサプライチェーンでのボトルネックで、検証を行うために必要なオーバーモールドのサブアセンブリの調達に3週間を要することが遅れて判明したのです。Beardsley氏は生産と出荷の体制を構築するため、この期間を大きく短縮する必要がありました。「テスト用の金型で試作する際に何百、何千ショットもの成形が必要になる可能性もあります。問題は、本物の基板に本物の電子回路を乗せ、オーバーモールドで成形したプリプロダクション品を作るとなった場合にこのサプライ・チェーン全体が必要になることでした」とBeardsley氏は言う。
「私たちが金型設計をどう調整すべきかを思案している時、何百ドル、何週間というお金が湯水のように消えていくのを目の当たりにしているうちに、あるアイデアが閃きました。実際に本物の電子機器をオーバーモールドしてしまう前に、これが機能するかどうかを検証する方法は無いのか?ということです」
彼らにはPCBAの代替案となる製作方法とその材料を探すことになりました。代替品は十分な寸法精度や実際のサブアセンブリと同じ形状面での精度が必要で、オーバーモールドで内部に埋め込む電子部品の機能を評価できるものである必要があります。また、破損したり変形することなく部品単位に分解でき、その際に破片を発生させないような頑丈なものである必要がありました。
「何千パウンドの圧力に耐え、尚且つ250℃を超える耐熱性を持つ材料を使わなければならないことがわかっていました。高い耐熱性と剛性を求めていたのです。」
Beardsley氏はAllen氏に助けを求め、彼らはある解決策に思い至りました。
「何千パウンドの圧力に耐え、尚且つ250℃を超える耐熱性を持つ材料を使わなければならないことがわかっていました。高い耐熱性と剛性を求めていたのです。」
David Beardsley氏
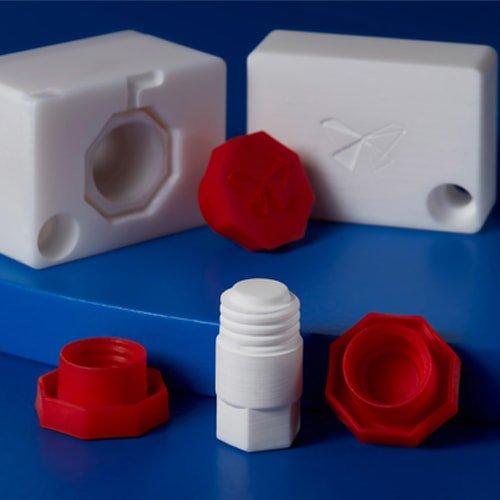
3Dプリント製金型による射出成形で小ロット量産
本技術資料は、光造形(SLA)方式の3Dプリント製の金型による射出成形でのコストと金型製作コストの削減方法やそのガイドラインを、海外の活用事例を交えながら解説いたします。
ソリューション:High Tempレジンによる3Dプリント品でのサロゲート(代替)品活用
材料の要件は非常に厳格なものでした。思い悩んだ末に、Allen氏は試しに光造形3DプリンタForm 2でHigh Tempレジンを使って代替品を3Dプリントで製作してみることにしました。実際の製品で使用する部品は、High Tempレジンの荷重たわみ温度である270℃の温度で、27,000 psiの射出圧力で成形されます。
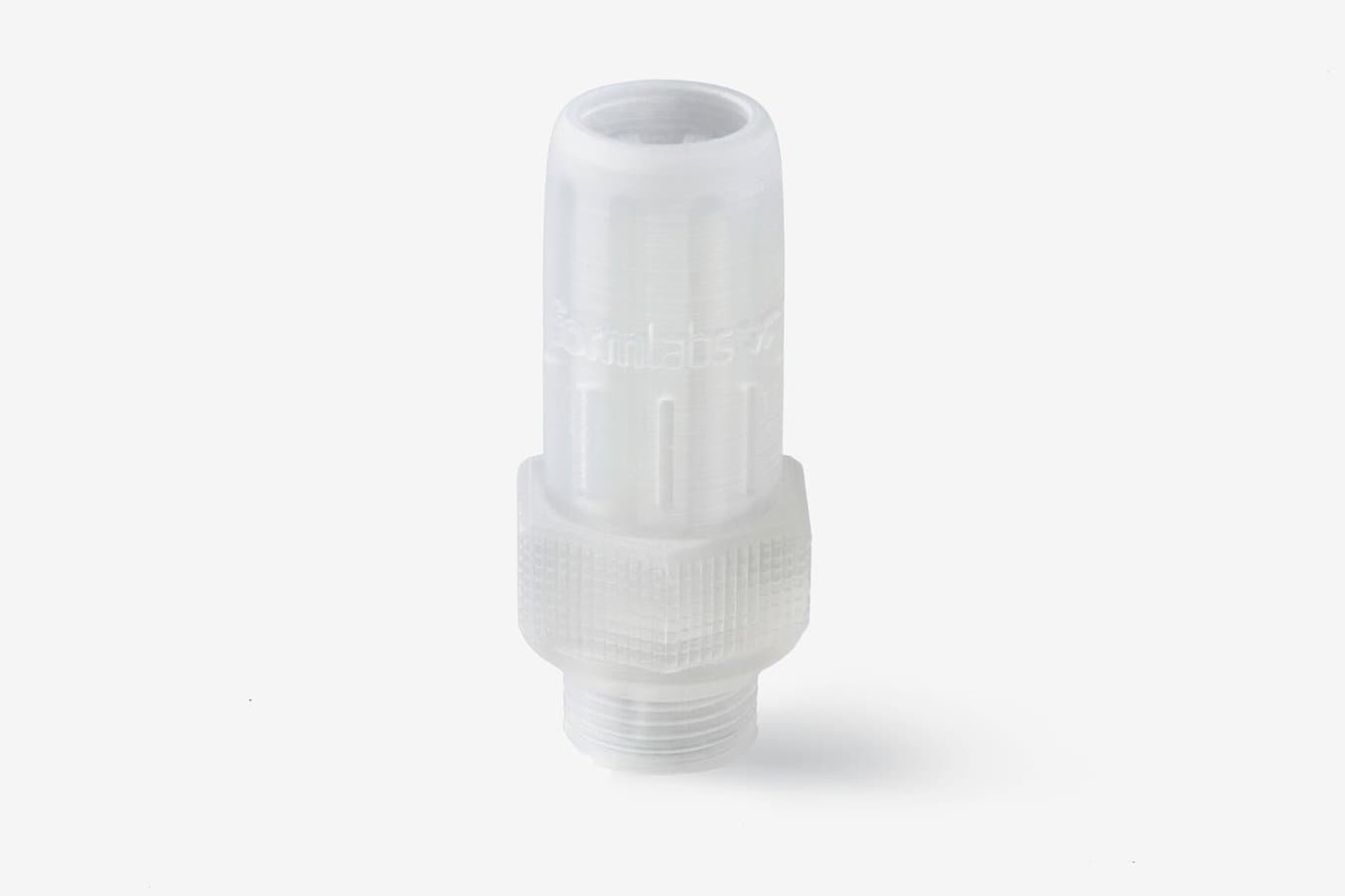
「この製品に必要な非常に細かいサイズの造形とオン・オフの切替を可能にするには、かなり高い解像度を持った3Dプリンタが必要でした。Form 2を採用したのは、非常に高い解像度と高耐熱材料の両方があったからです。我々の手元には他にも多くの生産技術の選択肢が既にありましたが、新たにこれほど小さく耐熱性のある部品を作る選択肢を得たことは、我々のラボ全体にとってかなり重要なことです。」
「我々の手元には他にも多くの生産技術の選択肢が既にありましたが、新たにこれほど小さく耐熱性のある部品を作る選択肢を得たことは、我々のラボ全体にとってかなり重要なことです。」
Bryan Allen氏
ATAPラボはすぐに作業に取りかかり、一晩のうちに試験的なプリントのいくつかを終えることができました。
「CAD上で設計をやり直す時間はありませんでした。私がやったことはCADファイルを開いてSTL形式で3Dファイルを保存し、PreFormでそのSTLを読み込んで少しの設定を調整しただけです。最初のプリントができあがると、あとはひたすらプリントを回していくだけでした。最初に200点の部品を作り、追加で100点ほどのプリントを行いました」とAllen氏は振り返ります。
PreForm:Formlabsが提供する無料のプリント準備ソフトウェア。プリント時に造形ステージとなるビルドプラットフォーム上にモデルを配置し、向きや傾きなどを決める。アルゴリズムによる自動設定でワンクリックで造形設定を終えることもできる。Allen氏は増産後、250点のインサートを10点ずつ約4時間かけてプリントした。
Allen氏はHigh Tempでのプリント品にサポート材を成形面ではなくシャットオフ面のみに付くようにし、サポート痕が成形時に金型に触れる面に付かないよう配慮しました。これにより、プリント後に一般的な洗浄と二次硬化を行うだけで、サンドがけ等の作業は不要になっています。
この3Dプリント品は、サブアセンブリの代替品として完璧に機能しました。このプロセスによりPCBAインサートの製作期間は3週間から3日に短縮でき、インサート1点あたりの製造単価は100ドルから0.80ドルにまで削減できました。
「このプロセスによって、工程をさらに下流に割り込ませることができ、前工程を大幅に削減することができました。この方法によって、3つか4つの前工程がなくなりました。時間を大幅に節約できました」とビアズリーは語った。
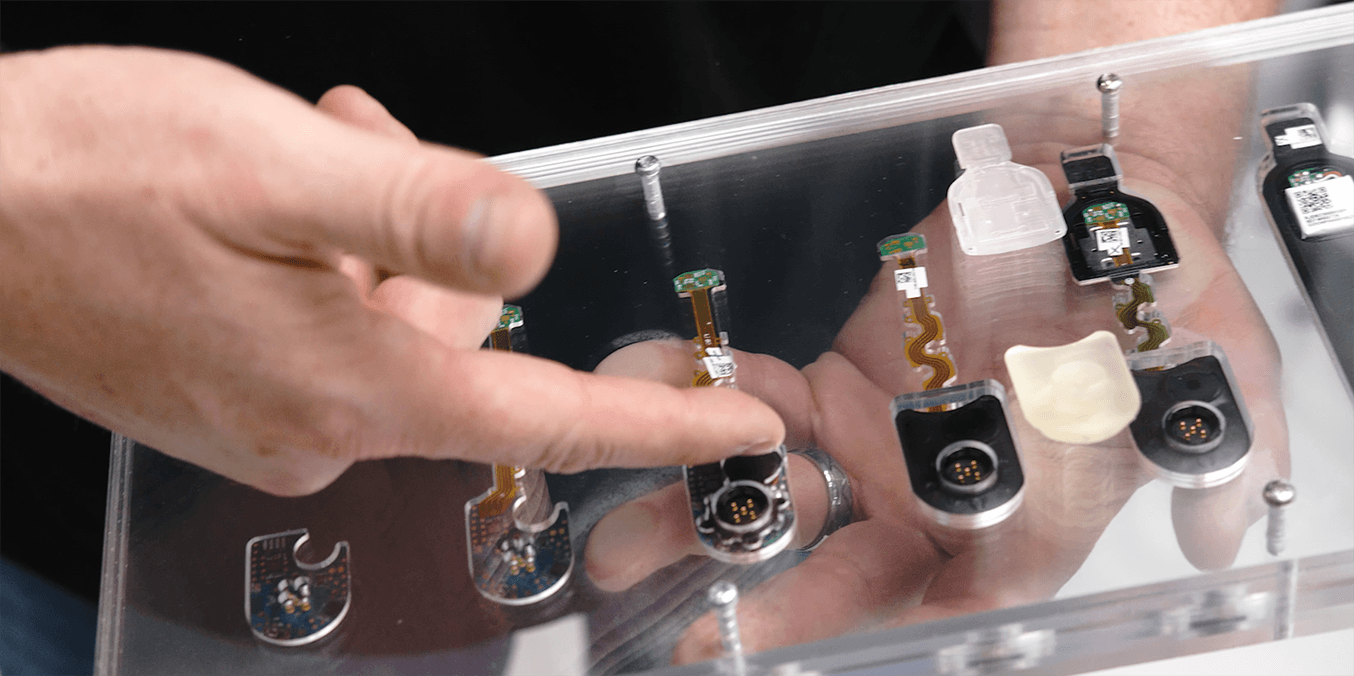
David Beardsley氏は、チームがどのようにして「工程を遮断」し、4つの工程を省くことで迅速に最後のオーバーモールド工程に集中できるようになったかを説明します。3Dプリント製の代替品は、複雑なサプライチェーンに頼ることなくインサート部品の製作期間を3週間から3日に短縮しています。
「3Dプリントで樹脂型を製作し、高圧での成形を行い、バリも発生しなかったという事実は、けっこうな大事件でした。Form 2がなかったら、このようなことはできなかったでしょう。」
David Beardsley氏
3Dプリントでの代替品は驚くほどの低コストで作ることができたため、我々は工場が伝えてきた必要数以上の数の部品が提供でき、満足のいく結果が出るまで連続して成形を継続できました。
「3Dプリントで樹脂型を製作し、高圧で成形を行い、バリすら発生しなかったという事実は、結構な大事件でした。Form 2がなかったら、こんなことはできなかったでしょう」とBeardsley氏は言います。
「これで量産もうまくいくと、確信することができました」とAllen氏は語っています。
Quick Look:Google ATAPの成果は?Formlabsの光造形3Dプリンタ Form 2とHigh Tempレジンを使用し、同社は以下の成果を上げています。
- 250℃超、27,000 psi以上で射出されるTPUのオーバーモールド成形に耐えるHigh TempレジンでPCBAの代替モジュールを3Dプリント。
- サブアセンブリのプリプロダクションコストを推定10万ドル削減。
- 複雑なサプライチェーンを回避し、PCBAインサートのプリプロダクション製作期間を3週間から3日に短縮。
「プリプロダクション品が形になっていくに従い、我々はこの試みの成功を確信するようになりました」
Bryan Allen氏
Google ATAPから学ぶ3Dプリント導入の3つの利点
Google ATAPの事例におけるウェアラブルデバイスのプリプロダクションの課題は同社独自のものですが、担当部門が課題に取り組み、テクノロジーを駆使することでそれを解決し、3Dプリントの活用方法について思案を重ねたプロセスは、あらゆる規模の企業にとって参考になるでしょう。Google ATAPのデザインテクノロジスト、Bryan Allen氏とモデルショップマネージャーのDavid Beardsley氏との会話から、以下3点の学びを得ることができそうです。
1. 試作から最終製品出荷まであらゆる段階で根本に疑問を持つ考え方で取り組む
「試作段階、サプライチェーン整備の段階、製品発表の段階......と考えるのではなく、開発のあらゆる段階で試作・検証・調整のサイクルを回していると考える。試作、検証、設計調整そして再試作という反復検証サイクルを初期の段階だけでなく、すべての工程で行うことが真の意味での品質に繋がります」とAllen氏。
「我々がここであらゆる段階において行う試作という作業は、様々な物事を明らかにするプロセスであり、将来大きな問題を引き起こすリスクに前もって対処できるチャンスなのです」とBeardsley氏は言います。
2. 各テクノロジーを課題解決のツールの一部と考え、最善の課題解決策を見つけるための方法を考える
「我々は工程全体を変更するようなことは決してしません。この機械が他の機械よりも優れている点は何か、そしてそれをどう活用するか?1つのプロセスや1つの機械に囚われないことで、さまざまな材料や方法の長所と短所を理解し、それに応じた活用法を見出していくのです」とAllen氏。
「我々は3DプリントをCNCや成形など従来工法と同じように、1つのツールに過ぎないと考えています。3Dプリントは、新しい技術を生産的な意味でどのように活用すべきかを考えるという我々の思考能力を鍛えてくれるものだと思います。」
Form 2はエンジニアやデザイナーが複雑な問題を解決し、革新的なハードウェア開発を成し遂げるために使われたGoogle ATAPラボの1ツールである。
1つの課題を解決することから始める
「設計という作業には、まだまだ多くの制約があります。これからアディティブマニュファクチャリングの導入を行おうとする段階では、1つの部品だけに限定した特定の課題を課題解決のテーマとして選ぶことをおすすめします。我々が製品すべてをプリントしようとするのではなくインサート品のみをプリントしたことが参考になればと思います。」
Formlabsの光造形3Dプリンタと3Dプリント用材料
Form 2とHigh Tempレジンは、Google ATAPラボにある様々なツールの1つに過ぎず、エンジニアやデザイナーが複雑な問題を解決したり、革新的なハードウェア開発を行う際に役立っています。
「大規模な拠点を持つ大手企業は皆、"ああ、こんなに高価な設備が必要なのか"と考えがちです。私たちは実際にそうした設備を保有していますが、実際のところForm 2は遥かに安い金額であるにも関わらず、日々圧倒的なパフォーマンスを見せています。「精度、スピード、仕上がり、プリント後の後処理まで含めた工程全体の効率、どれを取っても文句はありません」
Formlabsの光造形3Dプリンタの詳細や業界最多の種類を誇る幅広い材料ラインナップは、総合カタログにてご確認ください。