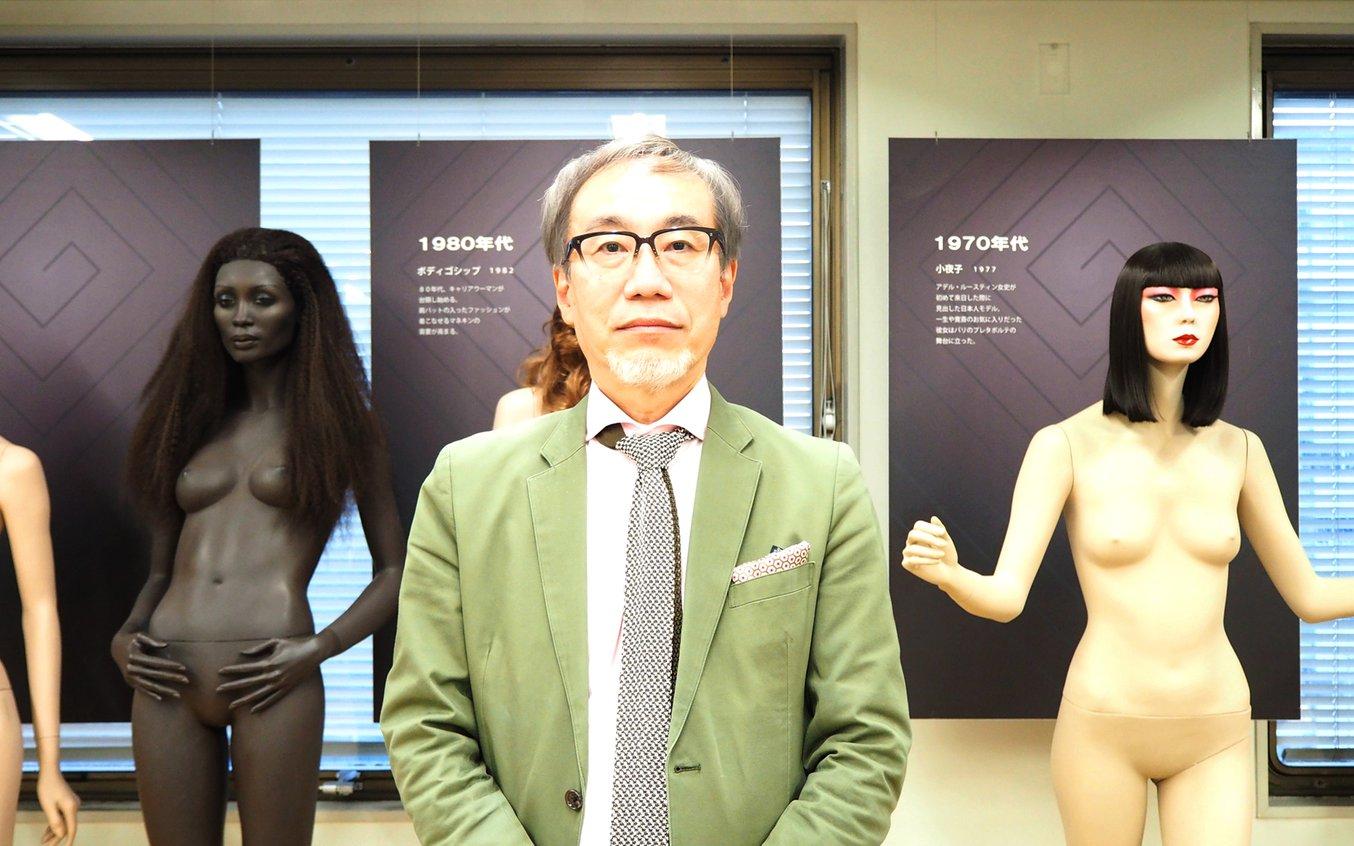
吉忠マネキン株式会社 常務取締役 川野 泰氏。背後には70年代から活躍した伝説のモデル、山口小夜子のマネキンを含め時代のトレンドを反映したマネキンが並ぶ。
User Data:
- ユーザー:吉忠マネキン株式会社(マネキン、商業店舗VMD、空間プロデュース等)
- 採用製品:Fuse 1(SLS方式)、Form 3、Form 2(SLA方式)
- 使用材料:Nylon 12パウダー(SLS)、Grey、Grey Pro、Tough 2000、Rigid 10Kレジン(SLA)
- 用途:ディスプレイロボット外装製作(実製品)
時代の変遷に合わせた「伝統と革新」
マネキンは、シーズンやコンセプトに合わせてその装いを変えていく。そしてその業界で長年トップを走り続ける企業の歴史も、まさにマネキンの如く時代に合わせ、そのビジネスを柔軟に変革して装いを新たにしてきた。1950年に京都で設立された吉忠マネキン株式会社は、戦後間もない時代から日本の高度経済成長と共にその事業を拡大し、現在ではファッション業界を中心とした商業店舗のVMDや空間プロデュース、果ては商業施設自体の設計施工を手掛けるまでにその事業を拡大してきた。また、レンタルが主流となっているマネキン業界において、そのレンタルを初めて開始したのも吉忠マネキンである。その吉忠マネキンがここ数年で開発を続けているのが、マネキンをロボット化した製品だ。店舗のショールーム化と言われたように、ネットやスマホで手軽に情報を入手できる時代となった今、店舗に足を運ぶことには見るだけでなく、五感すべてで「体験する」という付加価値が無ければならない。その体験という付加価値をどう創出するかという課題解決に、ディスプレイロボットは役立つはずだと川野常務は語る。2014年に米ニューヨークで開催された展示会で初号機をお披露目した際には、非常に多くの注目を浴び、以降テレビをはじめとするメディアでも数多く紹介されている。
そのディスプレイロボットは、マネキンの域を超えたサービスロボットとして運用され、吉忠マネキンでは画像認識や音声認識の機能を備えた案内ロボットも手掛けている。マネキンがどんなブランドの店舗に、どんな役割でディスプレイされるかによってポーズや装いが変わるのと同じく、ディスプレイロボットもどの場所にどんな役割で設置されるかによって外装や機能が変わる。
「元来FRPをレイアップ成形で製作してきたマネキンと3Dプリンタは、少量多品種生産という点において共通点があったかも知れないですね。ディスプレイロボットは、何に使うのか、ターゲットはどんなお客様なのか、どこに設置されるのかによって外装を変える必要があるので、基本的にはすべてワンオフの1点ものです。そういう点で、3Dプリンタはロボットの外装製作に非常に適していると言えますね。」川野常務は語る。
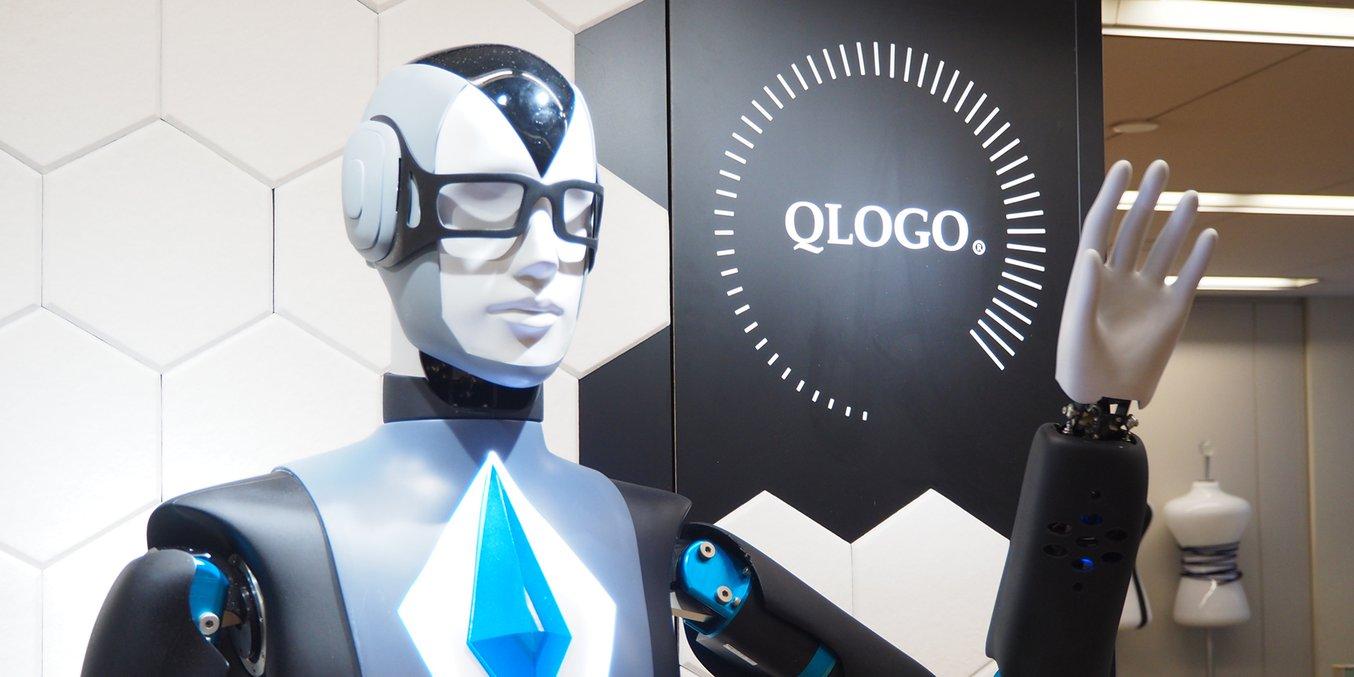
吉忠マネキンのディスプレイロボットの一つ「QLOGO」。
ロボットデザインは、人型のものは特にマネキン同様「顔」が重要だ。用途によって様々な考え方があれど、吉忠マネキンのDNAは「演出や装飾、黒子としてのデザインにある」と川野常務は言う。人間は、人型ロボットの顔がある一定の基準以上にリアルになると、不気味さを感じてしまう。いわゆる「不気味の谷」と言われるものだ。一方、キャラクター化された可愛らしいロボットではサービスロボットとして日常に溶け込む用途には適さない。そのため同社は「程よいリアルさと美しさも兼ね備え、好感が得られるロボット」の製作を目指す。
マネキンを形にするのは、原型師と呼ばれる職人が持つ長年の経験に培われた職人技だ。優れた職人を擁するということは企業の強みでもある反面、仕事が属人化してしまうというデメリットも存在する。こういった分野には常にテクノロジーによるソリューションが求められるが、同社においても3Dプリントによるデジタルファブリケーションでこの問題に立ち向かう人物が存在する。吉忠マネキン株式会社の東京アトリエで、同社の3Dプリント導入・活用を牽引する西田 真人氏だ。
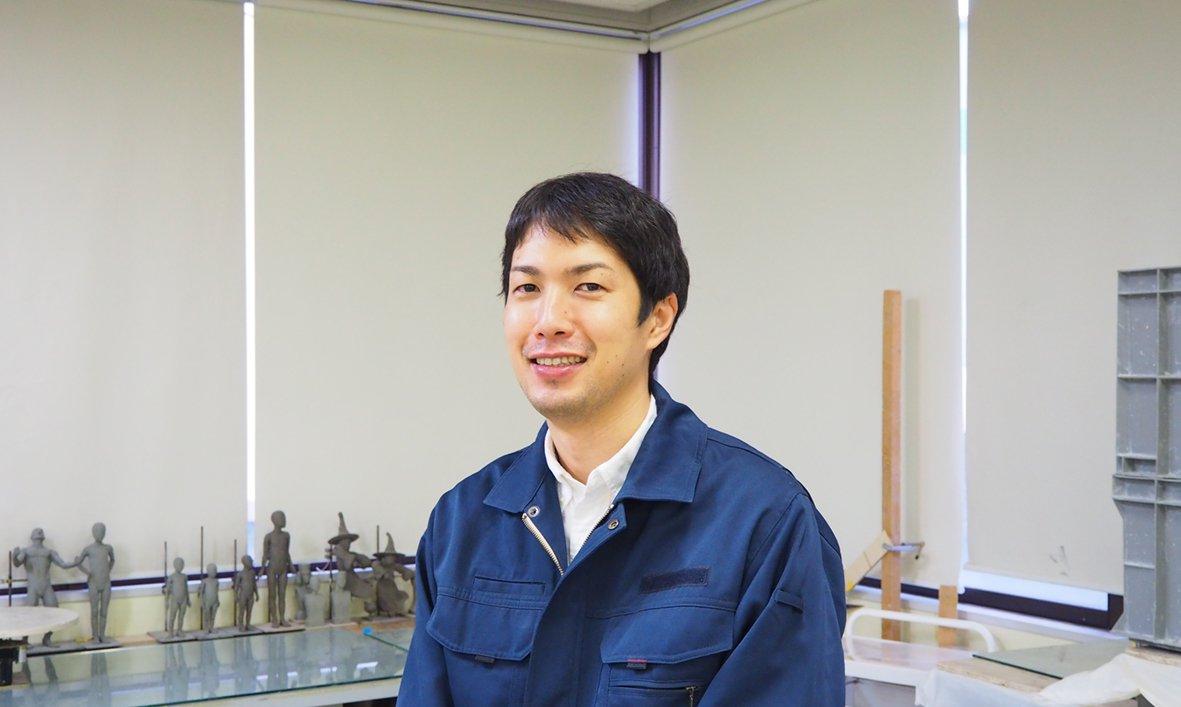
吉忠マネキン株式会社 東京店 マネキン・モデリング部 事業企画部 西田真人氏
2週間の工程が4~5日に
同社では元々、FDM(FFF)方式の3Dプリンタでマネキンのパーツなどを製作していたが、FDMに特有の積層痕や強度の異方性、造形後に発生する反り等の変形に大きな課題を感じていたという。そこで、同社の協力会社が先に導入していたというFormlabsのSLA光造形3DプリンタForm 2を導入。その後、その造形品質からForm 3も導入し、同社が開発したディスプレイロボットの外装を製造する目的で、FormlabsのSLS(粉末焼結積層造形)方式3DプリンタFuse 1の導入に至っている。「光造形機の方では、Grey、Grey Pro、Tough 2000(ABSライク)、Rigid 10K(ガラス分高配合材)レジンを使ってマネキンの手先などを作っています。マネキンよりも慎重な扱いが求められるロボット外装部品は、特に輸送中や倒れた時に破損しないように強度が高い材料が必要で、その点Fuse 1のNylon 12は高い強度とある程度の靭性が備わっており、すごく破損しにくい材料です。」
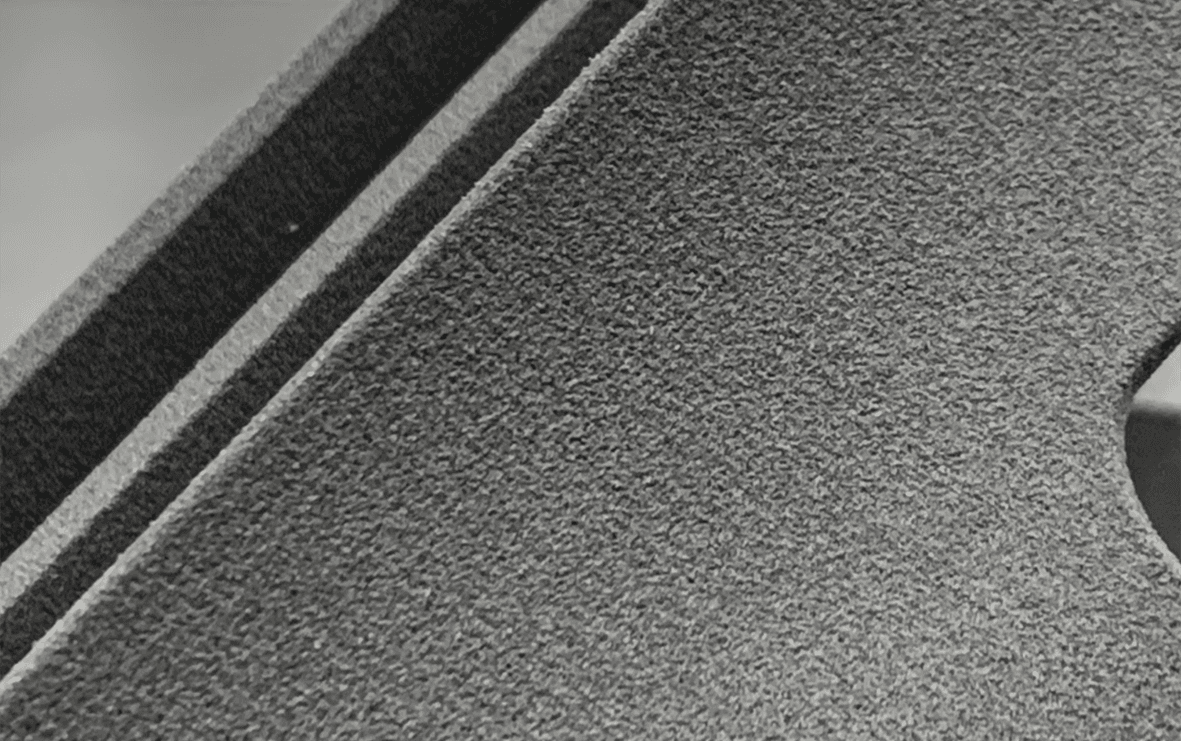
Fuse 1での造形品の表面。粉末ベースの3Dプリント品の中では抜群の表面品質が実現できる。
「当社には大型とデスクトップサイズのFDM機、そしてForm 2とForm 3があります。FDMで作ったものは独特の積層痕があるため、それを職人が研磨で消えるまで磨き上げなければ使えません。大きなものだと積層痕を除去するだけで3日、長い時は5日ほどかかります。その後で表面の凹凸を均一にするため数日かけて磨き上げ、そこからやっとサーフェサーを打つ工程に入るので、トータルで2週間はかかってしまいます。それだけの時間がかかる上に、造形後に反りも出る。また、モデリングを担当する者としては、設計段階でサポートが付く場所が磨けるかどうかを常に考えておかないといけません。
そういう課題がFuse 1では全くなくなり、4~5日あれば十分に完成してしまうので、ものすごいスピードです。Fuse 1ではFDMと違ってサポート材を使わない上に表面もきれいなので、当社ではFuse 1でプリントしたものを研磨せずそのままサーフェサーを打って仕上げています。プリントが終わった翌日にサーフェサーを塗布して、その次の日に磨いて完了です。その作業だけをやっているわけではないので、他の作業と並行してのお話です。」
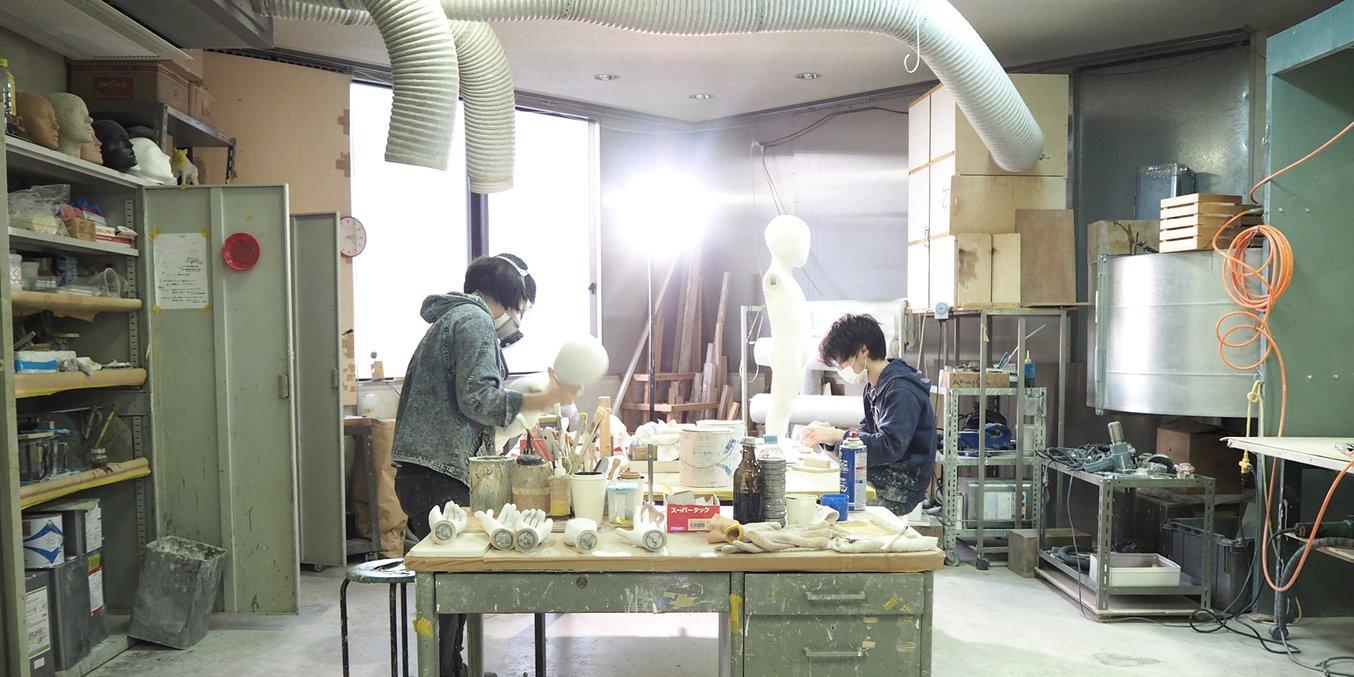
FDMでは積層痕の除去で3~5日、そこから造形品の凹凸が消えるまで数日かけて磨き上げた後にサーフェサーの工程に入る必要があった。
優れた表面品質で研磨不要に。設計の自由度も向上。
SLS等の粉末ベースの3Dプリント品では、表面が特有のざらついた仕上がりになる。FormlabsはSurface Armorテクノロジーという特許技術を用いてハイエンド機と同等以上のクオリティの造形や表面品質を実現している。表面品質が高いということは、実際に製品として出荷する状態に仕上げるまでに行う塗装や表面処理に要する時間と労力が削減できることを意味し、更に塗装や表面処理を外注するケースではそれがそのままコストに上乗せされてしまう。吉忠マネキンでは、このFuse 1での造形品の表面品質を見て、試しに研磨を行わずそのままサーフェサーで仕上げてみたところ、問題のない仕上がりとなったため研磨は行っていないという。西田氏によれば「FDMでの造形品では、爪が削れるほど細かい番手で何日も磨き続けないといけませんでした。それだけ苦労をして仕上げても、積層方向に割れが発生したり変形したりしてしまいます。Fuse 1での造形品では変形の問題も起こっていません。」という。
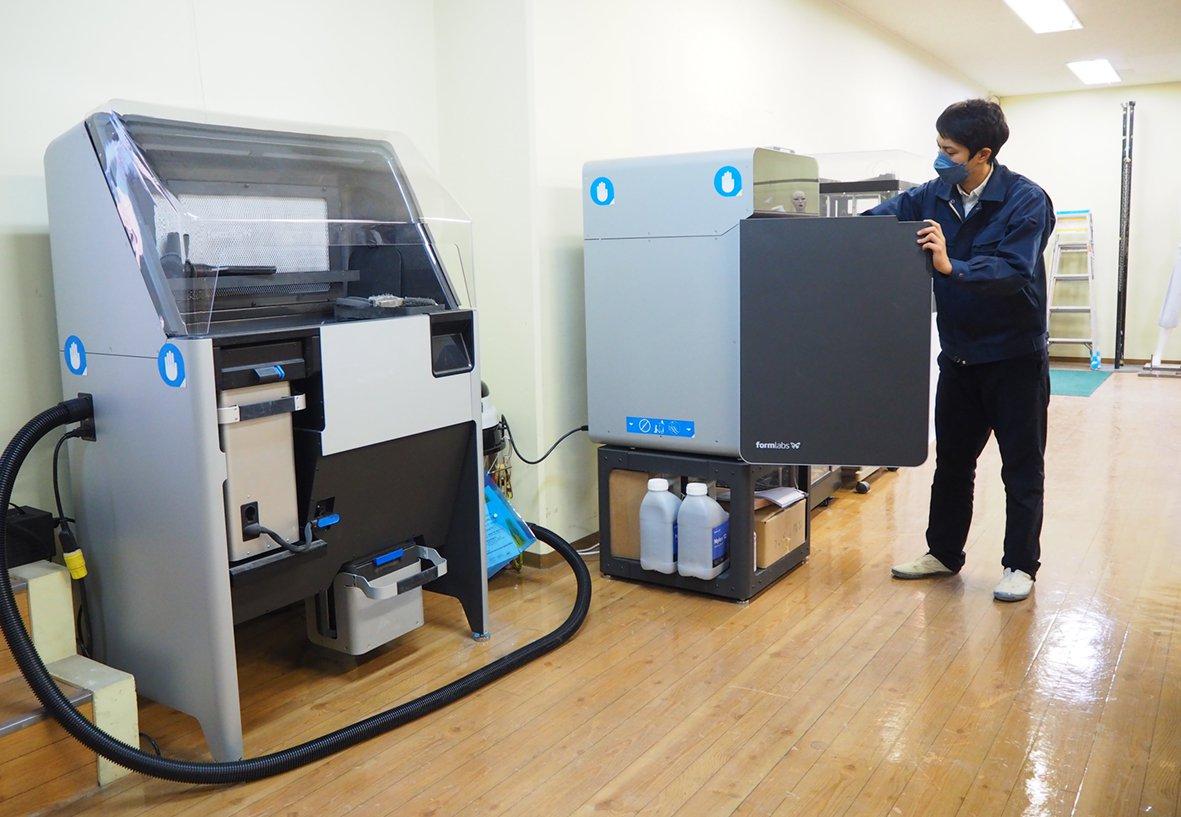
吉忠マネキン東京アトリエのFuse 1 & Fuse Siftと西田氏
Fuse 1導入前は外注という形でSLSでのプリントを活用していたが、この場合も納期が2週間ほどかかっていたという。これがFuse 1での製造に切り替えたところ、4~5日で完成し、尚且つ研磨に要していた大変な労力をゼロにできている。西田氏もこの点には「尋常じゃないくらいのスピードです」と言葉に力が入る。
「プリント管理ソフトウェアのDashboardも、土日に家にいる時でもプリントの様子が動画で確認できるので非常にありがたいです。造形が失敗することも殆どありません。造形精度も非常に高いので、FDMで作った時には埋めてしまっていたロボットの顔にある0.5mm程の見切りのラインも、Fuse 1では分割造形する必要もなく完全に表現できます。サポート材のことを気にして研磨できるだけのスペースを設ける必要もありません。FDMではねじを通す穴などは広げることができないので精度の面で困ることもありますし、積層方向も考えておかないといけません。そういうことを考えると、一番の違いは設計の自由度だと思います。Fuse 1が来てから他のプリンタの出番がぐっと減ってしまいました。やはり研磨の大変さが大きいんです。今では特に指定がない場合は殆どFuse 1で作っています(笑)。」
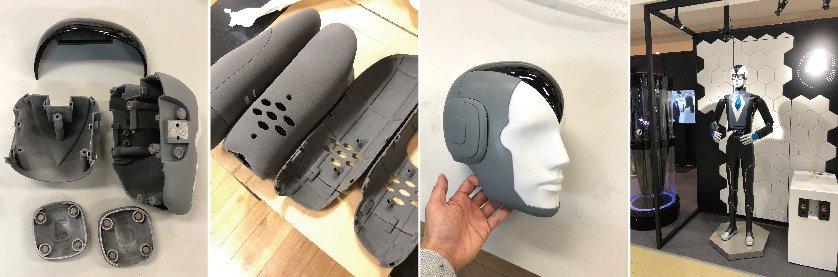
先ほどの「QLOGO」の製作フロー。頭部と腕の外装がFuse 1でプリントされている。
導入までの課題とその克服方法
現在ではFDM、SLA、そしてSLSと3つの方式の3Dプリンタを導入している吉忠マネキンだが、3Dプリンタを導入するまでにはどういう課題があったのだろうか。
「3Dデータの制作については、元々は私が個人的に趣味でやっていました。メインは3DCGですが3D CADが必要な場合はそちらも対応できます。今では複数名でデータを作ることができるので、組織的に対応できるようになりました。もう1つ、苦労したのは3Dプリンタという機械がどんなものなのか分からない人が多かったことでしょうか。私の場合は社内で10回ほど根気よくプレゼンを作成し、徐々に上層部にも理解を得ることができるようになりましたが、現場の意見をとりまとめて上申する際の決め手になったのは実際に作ったサンプルがあったからだと思います。」と西田氏は言う。
「これはFuse 1を導入した時も同じで、なぜFuse 1が良いのか、それを導入したら必ず上手くいくのか、という会社側の不安に対しても対処する必要がありました。実はFuse 1の導入を検討している時に、同じような価格帯の他社のSLSも見ているんです。でも他社のものはFuse 1やFuse Siftみたいにシンプルなワークフローではなく、現場に導入した後に誰でも使いこなせるのかという点に不安が残りました。周囲が粉だらけになるんじゃないかという心配もありましたが、Fuse 1とFuse Siftでは全くありませんでした。他社のものは手で攪拌しないといけないし、粉もすごく舞っていたので、これでは難しいと思ったんです。」
「サンプルについても有償のものしかなく、検討段階でそれは現実的ではありませんでした。Formlabsがサンプル造形を無償で対応してくれなかったら、Fuse 1の導入は実現していなかったと思います。実際のデータをテスト造形したものを社内で見せた時には、『3Dプリントでこんなことができるのか!』と感動されました。数千万円が当たり前のSLSプリンタが、この価格で導入できるのも要素として大きかったです。」
では、実際に3Dプリンタを導入した結果、会社側からはそれがどう見えているだろうか。現場からの提案を受ける立場である川野常務にも、経営視点からの3Dプリンタ導入についてお話を伺った。
「そもそもマネキンは芸術でもあります。ファッションの業界でディスプレイされるマネキンは、そのシーズン限りの一瞬を切り取るもので、ずっと残るものではありません。尚且つ熟練した職人による手作業で、悪く言えば非常に属人的なものです。しかし、それがデジタルになれば再現性があるものとなり、高い精度と材料の幅があれば永遠に残すこともできるようになる。技術継承や保存の問題が解決できるのは素晴らしいことです。」(川野常務)
今なお続く伝統と革新
早いサイクルで消費されるファッション業界において、吉忠マネキンには古くからリサイクルの概念がある。再生紙を使用したり、時には書き損じた和紙をそのまま塗装下地として使用するという試みが、既に1940年代に存在している。
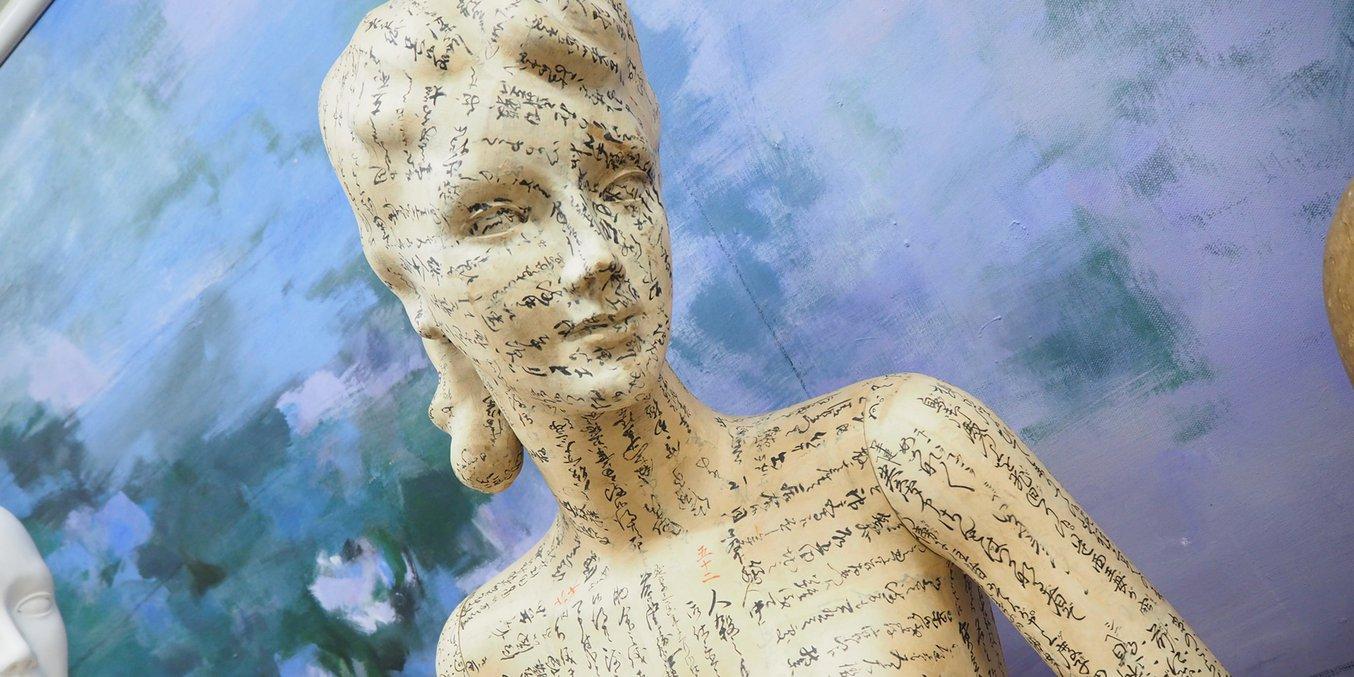
1950年代に製作された書き損じた紙を使用したマネキン(吉忠マネキン株式会社本社)
吉忠マネキンのディスプレイロボットの外装を製作するFuse 1のSLS(粉末焼結積層造形)方式は、これと同様に造形品で使用されなかった粉末(パウダー)材料を再利用することができる。造形精度や効率的なワークフローだけでなく、粉末再利用装置Fuse Siftでは半密閉式の陰圧ブースで粉末の飛散を防ぎながら、造形品からの粉末の除去、未焼結パウダーの回収と再利用がワンストップで行える。材料のリサイクルが可能な3DプリンタFuse 1で作られた外装を纏う吉忠マネキンのロボットは、テレプレゼンスと呼ばれるリモート制御によって、障がい者雇用の拡大などにも期待が寄せられている。3Dプリンタで作られたロボットという21世紀然とした革新の中には、半世紀以上にわたり守り抜かれてきた吉忠マネキンのDNAが、今なお息づいているのだ。
Fuse 1導入前後での作業手順と日数の変化
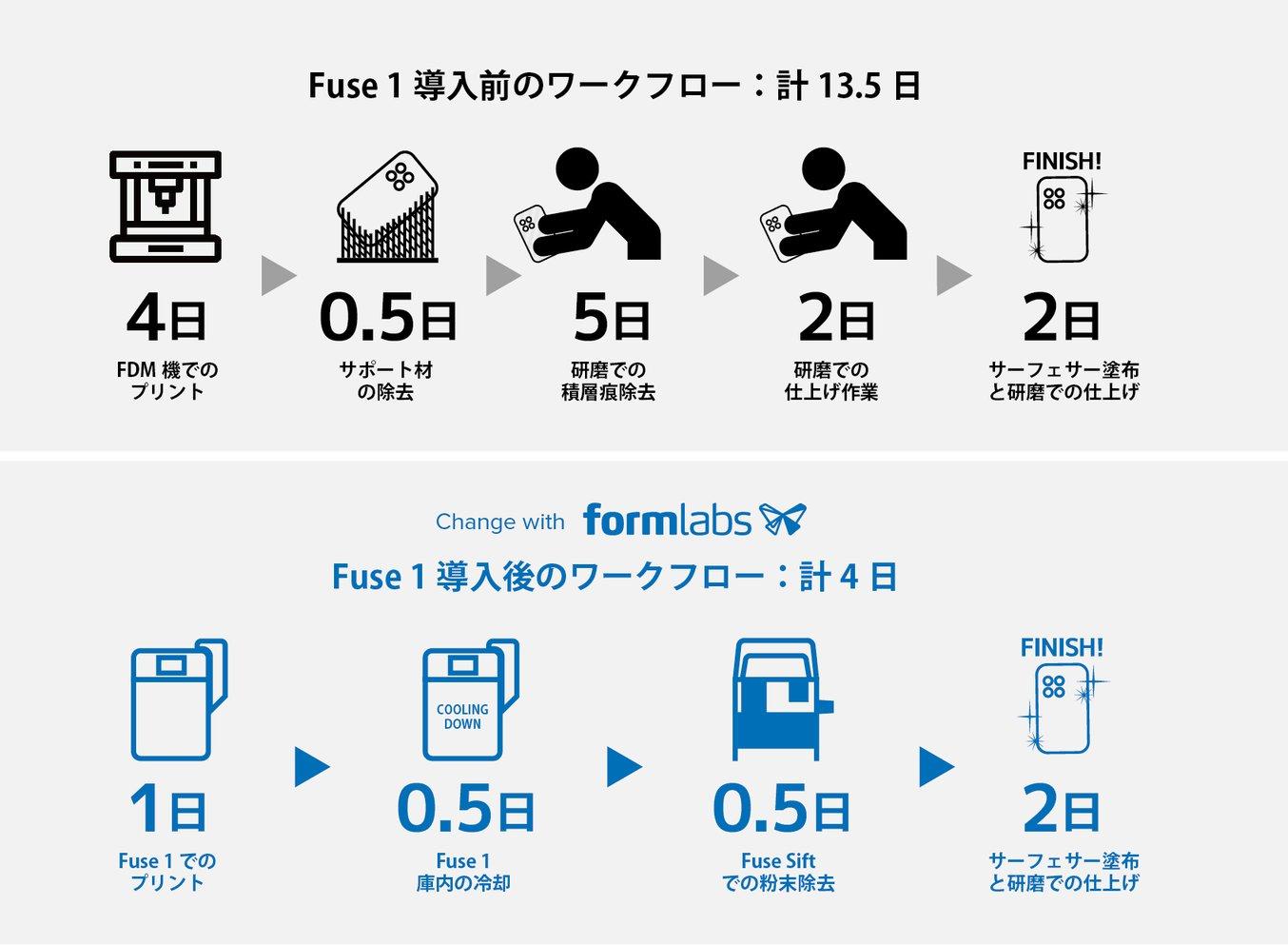
Fuse 1 導入前後で作業工程と日数が大幅に短縮された。
FormlabsのSLS方式3Dプリンタ、Fuseシリーズの他では得られない効率化されたワークフローは、以下動画にて確認できる。