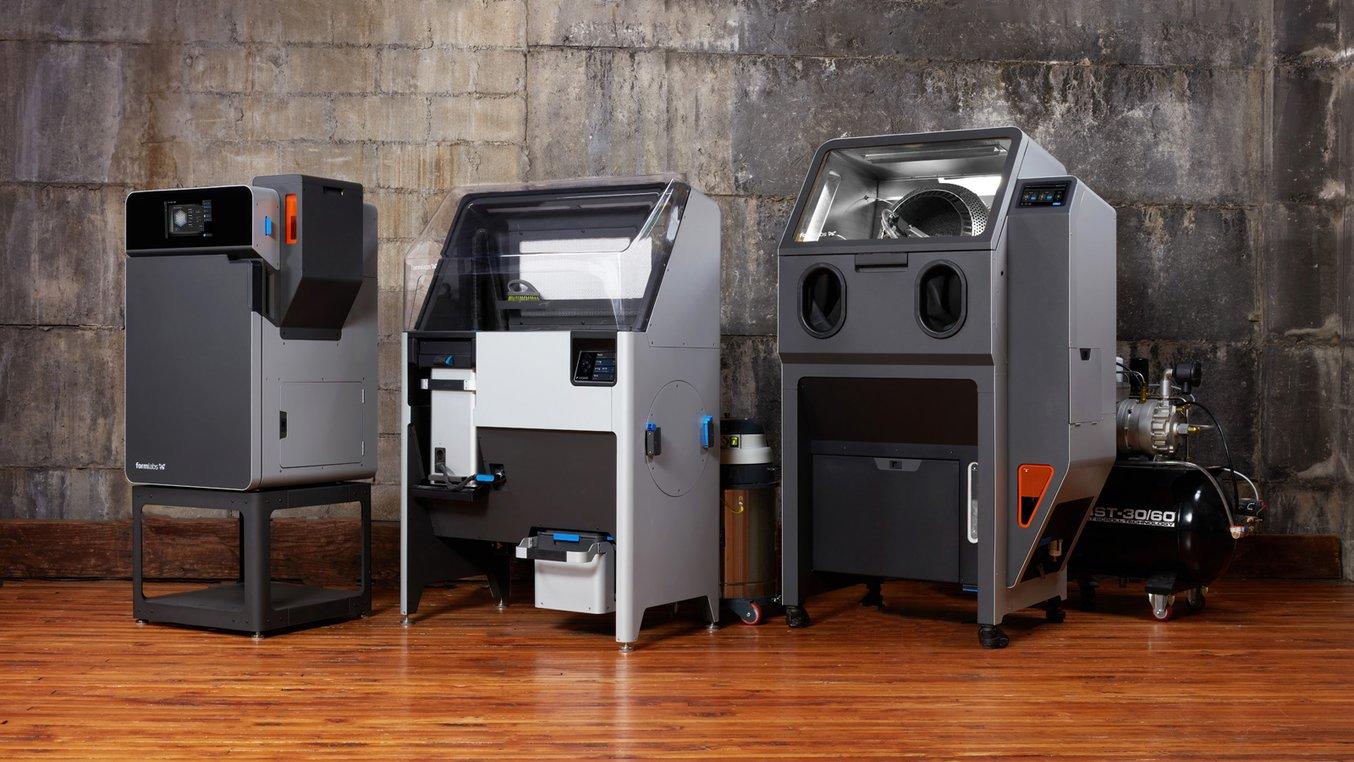
FormlabsのSLS方式3Dプリンタ Fuse 1+ 30W(左)、後処理+粉末再利用装置Fuse Sift(中央)、自動ブラスト+研磨で作業効率を劇的向上するFuse Blast(右)。
「3Dプリンタで最終製品を」は少し違う
アディティブマニュファクチャリング(AM)やデジタル製造において、欧米と比較して大きく遅れを取っていると言われる日本の製造業。しかし本当にそうでしょうか?3Dプリンタ業界を見渡せば、欧米での事例紹介と共に「3Dプリンタで最終製品を」というスローガンをよく目にしますが、それは3Dプリンタを「販売する側」の目線からの言葉であり、そのユーザーとなるメーカー各社の目線は真逆の方向性なのではないかと感じられることも多くあります。
切削や成形で製造する金属部品をそのまま樹脂の3Dプリント品に置き換えるのが多くの場合でナンセンスであるのと同様に、作るものが変わらないのに生産技術だけを3Dプリントに置き換えることもまた、ナンセンスです。部品の置き換えでは、そもそも従来工法で製造するものはDFM(製造容易性設計)のコンセプトの下で従来工法による量産に最適化された設計になっているからで、3DプリントやAMで製造または量産を行う場合はDfAM(Design for Additive Manufacturing)のようにその工法に合った設計思想が別にあります。3Dプリントの利点を活かした一体造形で部品点数を減らす、トポロジー最適化やジェネレーティブデザインを駆使した強度を維持しての軽量化や外観などはその代表例でしょう。つまり、ある製品を量産する生産技術はその工法で量産することを前提とした設計になっており、その背景にはそのプロダクトの企画段階での様々な要素があるはずです。
冒頭に「3Dプリンタで最終製品を」は少し違うとしているのは、新たな生産技術を取り入れるのであれば、それはその製品の企画段階まで遡る必要があるだけでなく、開発や設計、そして品質管理や品質保証といったものづくりに関わるほぼ全ての側面がAMという新たな技術を包含したものである必要があるからです。そして、作るものや設計は同じなのに生産技術だけを3Dプリンタに置き換えるようなアプローチには特にメリットがない場合が殆どです。そのため、組織のサイズがコンパクトなベンチャー企業や中小規模のメーカー、新規事業などの方がAMでの量産はどうしても取り入れやすくなるかと思います。
逆に大手企業では試作や治具製作といった既存の3Dプリンタの用途を(ある意味では)制限してしまっている枠組みから、どのような理由(メリット、戦略など)で、そして如何にして自社事業の本流と言える実製品の量産に3Dプリントを適用するかという点が大きな課題になるでしょう。先述のように企画~開発・設計~生産技術~製造~QC / QAといったモノづくりのプロセスほぼ全てに何かしらの変革が必要となるため、恐らくは新規事業に近い「前例のない試み」を限られたメンバーだけでスモールスタートするようなケースがあれば、AM特有の利点で自社の事業全体に大きなメリットを生み出す端緒となるかも知れません。
それでは、AMでの量産を検討すべきケースとはどのようなものか、まずは前提としてその点を見ていきましょう。
前提として考えるべきは、対価格価値
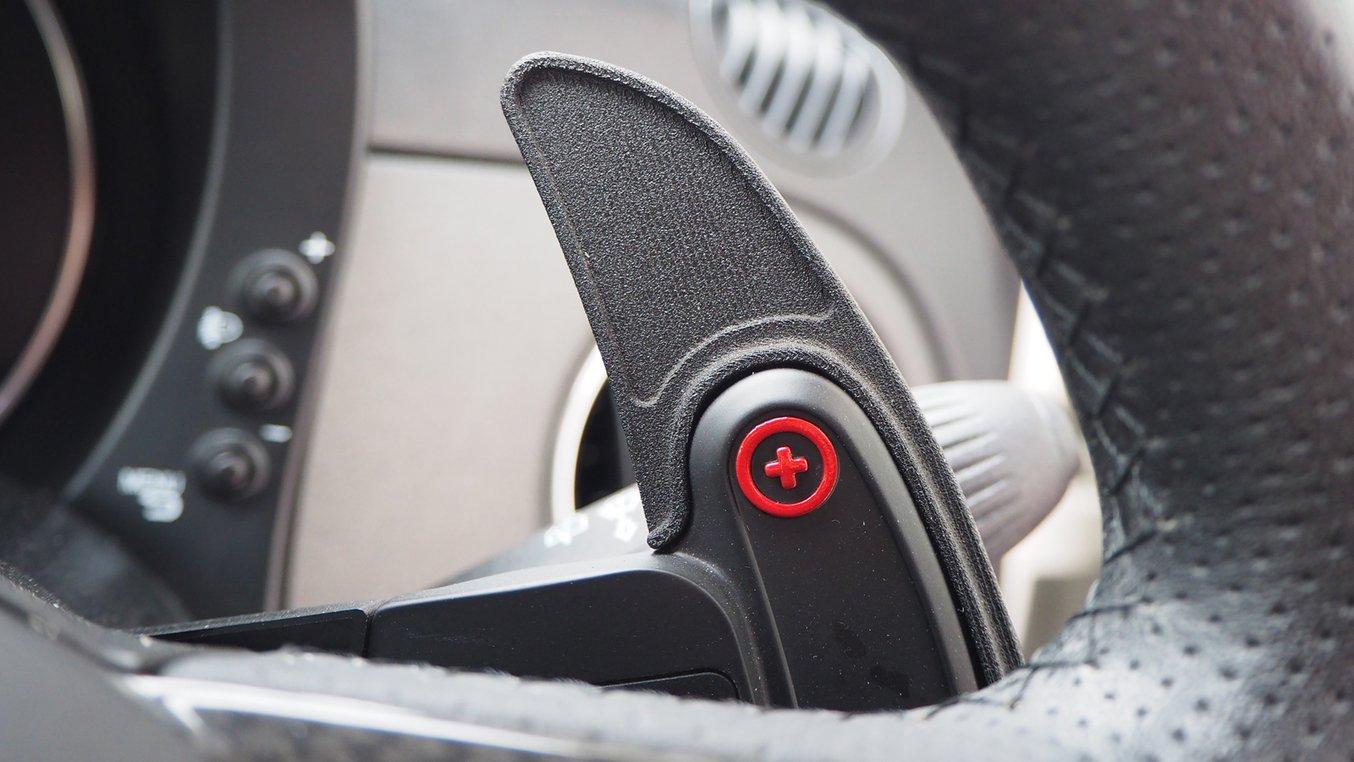
日本のコードテックCAMがFuse 1で量産するABARTH向けステアリングパドルシフトのエクステンション。欧州車オーナーという小さいながらも明確な趣味嗜好がある層に、ドライブ体験向上という価値を提供する。
数万から数十万点という単位で量産される、いわゆる大量生産品では、数の経済性によって部品1点あたりの製造単価は極限まで低く抑えられます。3DプリンタによるAM製造では通常、こうした大量生産品と比較して製造単価は高額になってしまいます。しかし、大量生産大量消費と呼ばれる20世紀とは違い、多様化の時代と称される現代では、MaaS(Manufacturing as a Service/サービスとしてのものづくり)に代表される多品種少量生産や、パーソナライズ品を提供することを通して得られるビジネスチャンスが増えてきています。
こうした多品種小ロットでの量産を行う場合、大量生産時と同様の切削や成形等の従来工法では金型製作やCAE設定などに要する量産準備コストを生産点数で消化することができず、結果として「金型を起こしていては採算が取れない」ということになってしまいます。しかし3Dプリンタであれば、生産点数に関わらず製造単価はほぼ一定で、数百点単位での小ロット量産であれば切削や成形よりも遥かに高いコスト効率で量産が行えます。しかしこれはあくまで製品の「作り手」側のお話で、その製品を購入する顧客にとっては大量生産品であろうと3Dプリント品であろうと、生産技術で購入する商品を選ぶ人は多くはないでしょう。
この大量生産品よりも製造単価が高い=販売価格が高いという点は、言い方を換えると「どんな商品であれば市場に出回る大量生産品よりも高額な商品を喜んで買ってもらえるのか」ということであり、この根本課題をクリアしない限りはアディティブマニュファクチャリングによる量産からビジネス上の利益を得ることは難しいはずです。つまり、商品企画の段階で多品種小ロットでの量産となること、そしてその商品がターゲットの顧客にとって他に無いような高い付加価値を有しているかどうかが大きなポイントになるはずです。
■3Dプリントでの量産が現実的に検討できるケース
- 小さいが“堅い”市場に向けた製品
- ターゲットにとって高い付加価値がある
- 模倣困難性または先行者利益の独占が見込める
- 一体造形によって部品点数を大幅に削減できる
設計・製造面では「不可能形状」がメリットに
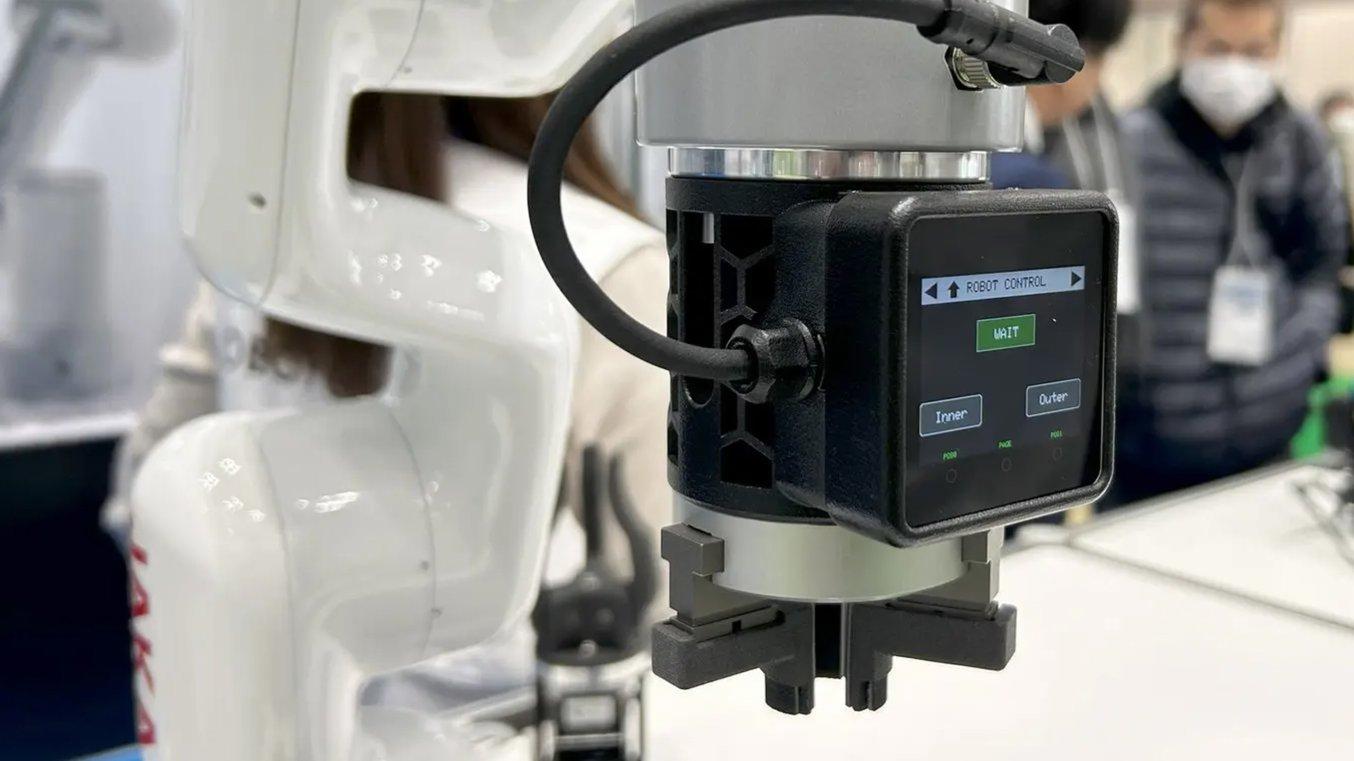
岐阜県のARMA株式会社では、ワークに合わせたカスタマイズが必須となるロボット用グリッパをFuse 1で量産している。SLSの利点である一体造形により部品点数は半分以下に激減。ねじ等を使用する必要がない点で軽量化にもメリットがある。
技術面でのメリットとしては、3Dプリント、特にSLS方式ならではの設計の自由度が挙げられます。切削では表現できない形状、成形ではどうやってもアンダーカットになってしまう形状が、SLS 3Dプリンタでは問題なくプリントできます。3Dプリンタの利点で「設計の自由度」という言葉をよく目にしますが、これは端的に言えば製造容易性または製造面での制約を考慮する必要が無くなるということです。そしてここから導かれる実地でのメリットで最も代表的なものが、一体造形による部品点数の削減、カスタマイズが必要な部品・製品への対応等となるでしょう。
実際の事例として、岐阜県各務原市の株式会社エフ・アイ・ティおよびARMA株式会社では、ワークに合わせたカスタマイズが前提となる協働ロボットのグリッパや産業用ロボットのエンドエフェクタをFormlabsのFuse 1で量産しています。詳細はこちらのページにて確認いただけますが、同社が考えるFuse 1でのAM量産の利点は下記のようなものです。
- 一体造形により部品点数を半分程度に削減
- 高強度材料により90%を樹脂部品化。40%の軽量化を実現
- AM特有のハニカム構造、一体造形によるねじ使用数減も軽量化に貢献
- カスタムが前提となるグリッパやエンドエフェクタの製造を事業化できたこと自体
- 表面処理を行えば、更に様々な機能を付加することも可能
実際に製造業においては、効率化や省力化、そして2024年問題のような文脈での働き方改革の余波で急速に自動化が進んでいます。そしてこの自動化を実現するには、その現場やワークに合わせた細かなカスタマイズが製品、部品、治具など随所に必要となってきます。ロボットやFAだけでなく、軽量化とカスタム、オプションパーツに需要のある自動車、二輪、自転車、その他モビリティ製品やドローンも、AMの導入が進んでいる業種です。これらの利点は市場のニーズとはまた別の、製造者側の社内的なメリットとなる部分ですが、カスタム品を現実的なコストで小ロット量産、あるいはワンオフ製作が行えたり、そこに更に軽量化や部品点数減によるコストメリットを生み出すことも、AMならではの強みと言えます。重要な点は、これらAMのメリットは全てのケースに該当するわけではないものの、大量生産向けの従来工法が最適解でない場合の有力なソリューションとなるということで、AMの利点が求められる場面は自動化の普及などの時代の流れに乗って、今後益々増えてくることが予想されます。
小ロット量産品が自社事業に与えるインパクト
ここまで製品レベルでの「条件」を確認してきましたが、ここで少し目線を変えてみましょう。小ロットで量産されるプロダクトは、当然ながら生産点数、引いては販売数が少なくなり、全社単位での売上構成比に占める割合も小さくなります。つまり、ここで「自社の事業にとって本当にやる意味があるのか?」という疑問が湧いてきます。経営陣や上層部にとってはこの疑問は現場からの提案を却下するには十分な理由となるでしょう。
ここで確認しておきたい点は、その小ロット量産品が顧客に対して付加価値を持つのと同様に、自社にとってもビジネス上の付加価値を持つか否か、という点です。先ほど触れた通り、大量生産品に消費者が自らのスタイルを合わせていた20世紀とは対照的に、21世紀の現在は、ものづくりが個々の、あるいは特定層の顧客ニーズに合わせて製品を提供することが求められています。例え売上構成比のマジョリティを占める製品ではなくとも、企業ブランディングの文脈で「お客様ひとりひとりに寄り添う」というメッセージを打ち出すツール、あるいは従来の大量生産品では関心を得られなかった新規顧客層を取り込み、それをきっかけに自社に興味を持ってもらい今後の製品やサービスの展開に繋げる、または今現在の主力商品の購買につなげるといったように、自社の成長曲線の上で有意義な役割を持たせた戦略商品という位置付けで展開することはできるでしょう。
このように直接的な売上額は大きくないものであっても自社製品の中で明確な役割をもって市場に投入されるものを「戦略商品」と言いますが、企業ブランディングや新規顧客の開拓以外にも、新規事業の立ち上げや市場のポテンシャルを測るための実験的なプロダクト等も、3DプリントによるAM製造では金型やCAE設定、ライン組みなど量産準備とその投資の大部分が不要となるため、従来工法でのものづくりとは比較にならないほど簡単に市場投入できるようになります。もちろんそのプロダクトが相応の価値を顧客に提供できるものである必要はありますが、大量生産品と比べて量産の初期投資が遥かに安価なAMによる量産は、マス・カスタマイゼーションのように量産とは言え全てが完全に同一の形状、デザイン、仕様である必要はなく、それ故に顧客に提供できる価値も大きな可能性を秘めています。
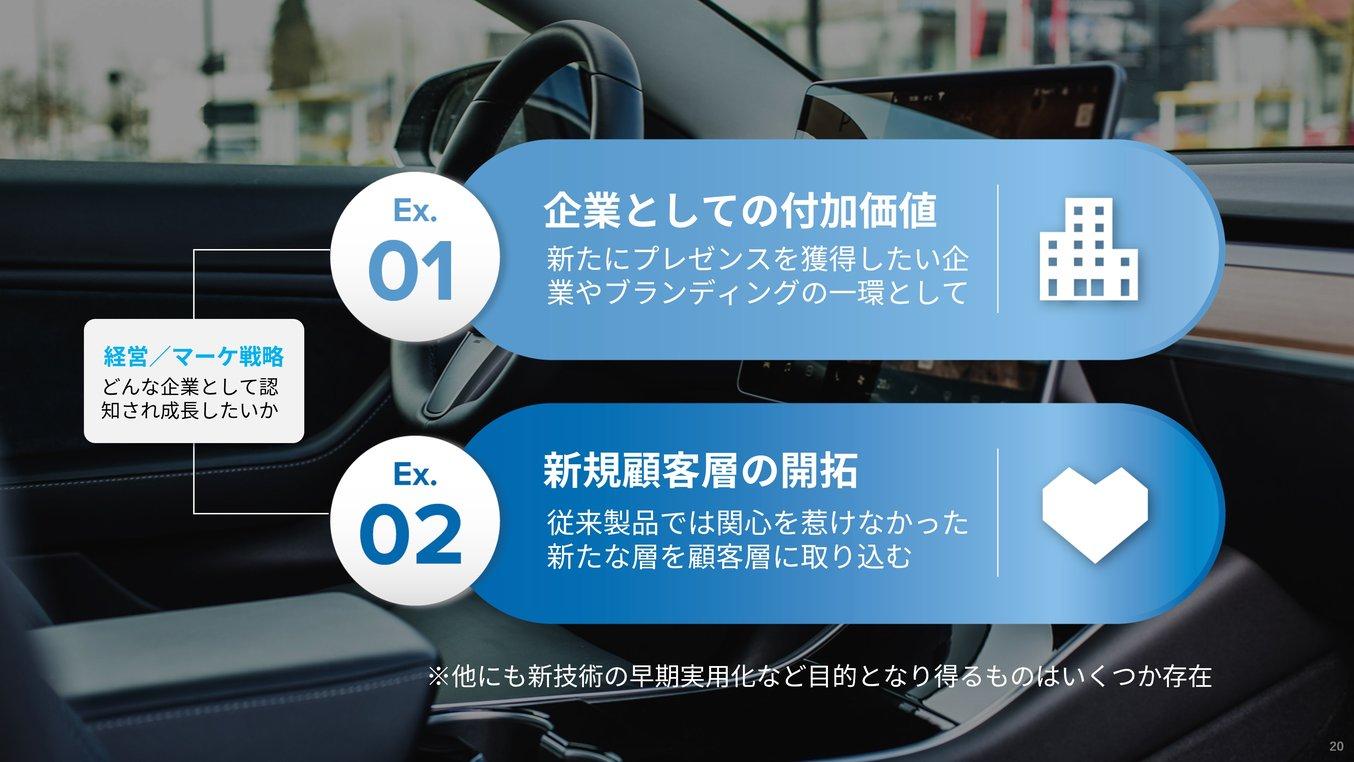
ものづくりプロセスにおけるAMの利点
ここまで見てきたような条件を満たした商品企画にGOサインが出れば、実際のプロダクト開発に入ります。大量生産式の従来工法による量産を前提とする場合では、量産開始に向けて様々な単位で試作と検証を繰り返しながらプロジェクトが進められます。そもそも試作と検証は、量産工程におけるリスク、あるいは製品化され顧客の手に届いた後のリスクを検証し、削ぎ落していく行為です。コンセプトモデルやPoC(概念実証)と呼ばれる初期段階の試作を経て、外観、技術、機能、そして製品の試作を何度も繰り返し、可能な限りすべてのリスクを削ぎ落とす作業を積み重ねていくこの開発プロセスは、原則的に後戻りができない不可逆的なものです。
とは言え現実には、量産開始直前に、時には量産開始後であっても「設計変更」という名の強制力により、甚大なコストと労力、そしてエネルギーを払って後戻りを余儀なくされるケースもままあります。
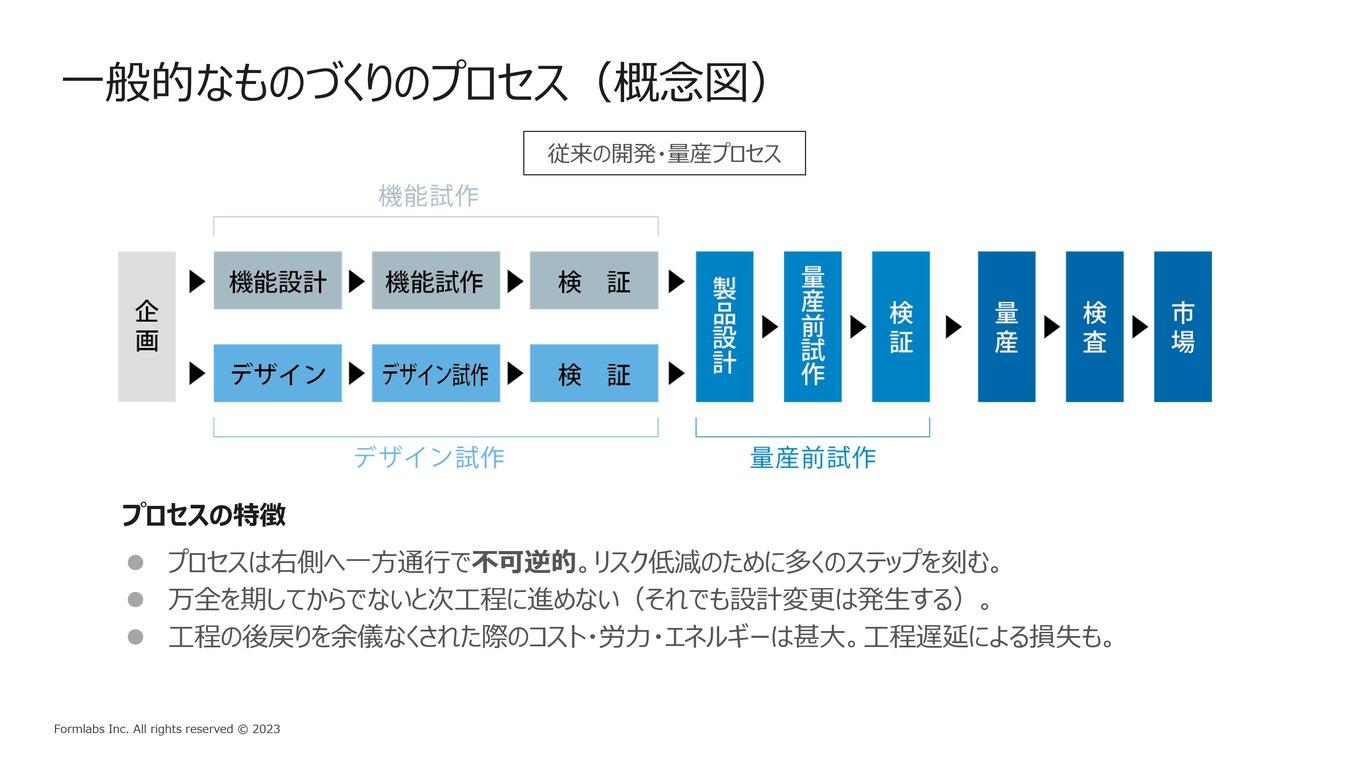
従来型の製品開発プロセスは、各ステップを積み重ねて次工程へと進む性質上、工程の後戻りには甚大なコストが伴い、ニーズの変化にタイムリーな対応を取ることは難しい。
これに対し、特にFormlabsのFuseシリーズのような3DプリンタによるAMでは、例え量産開始後に設計変更が発生しても、CAD上のデータを修正すれば当日中すぐに試作し、即座に設計変更に対応した「バージョン1.1」の量産がスタートできます。材料の加工や製造、組立がすべてプリンタで賄えてしまうため、当然金型や治具などの量産準備を行う必要はありません。
これは設計変更(”セッペン”とも)のような大掛かりな話に限った利点ではありません。この利点が当たり前に活用できるようになると、量産を行いながらも顧客からのフィードバックを基に製品にマイナーアップデートを重ねることで、市場投入後も品質向上を重ねて行くことができるのです。これは、ソフトウェア的な考え方でハードウェアを作ることができることを意味しており、量産開始当初の製品はベータ版として特定の顧客層のみに販売を行いながら実地検証を行うことも簡単にできます。
もう一つの見逃せない点は「試作時から量産時と同じ設備と材料でものを作る」ということです。各段階での試作と検証の精度が飛躍的に向上するだけでなく、開発から量産に移行するまでに行うPVT(生産検証)で行うことの大部分を、前工程の試作段階で兼ねることができるため、劇的な工程簡略化・工程短縮が実現できます。
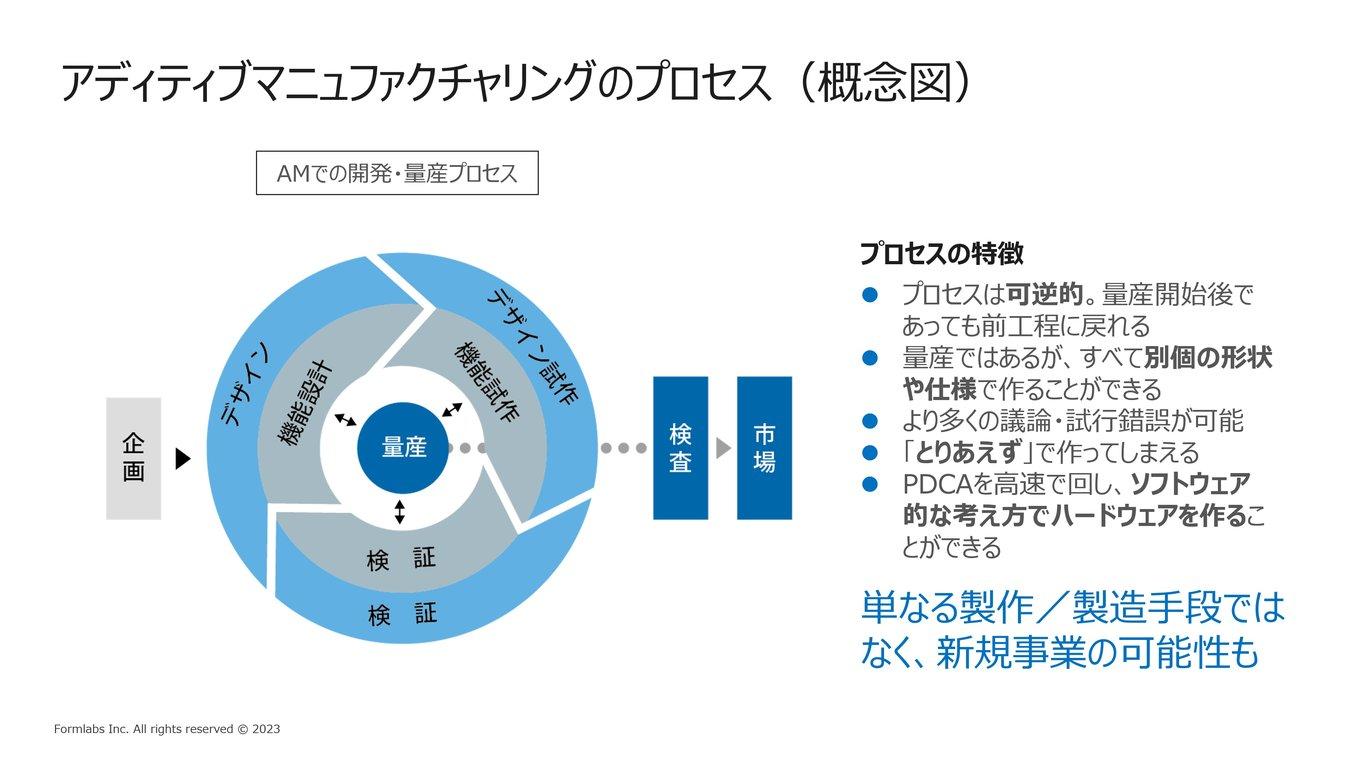
AMでのプロセスは毎回のプリントごとにデータを変更できるため、設計変更や仕様のアップデートを行う前提でソフトウェア的なものづくりが可能となる。生産検証を試作時にほぼ完了できる利点も大きい。
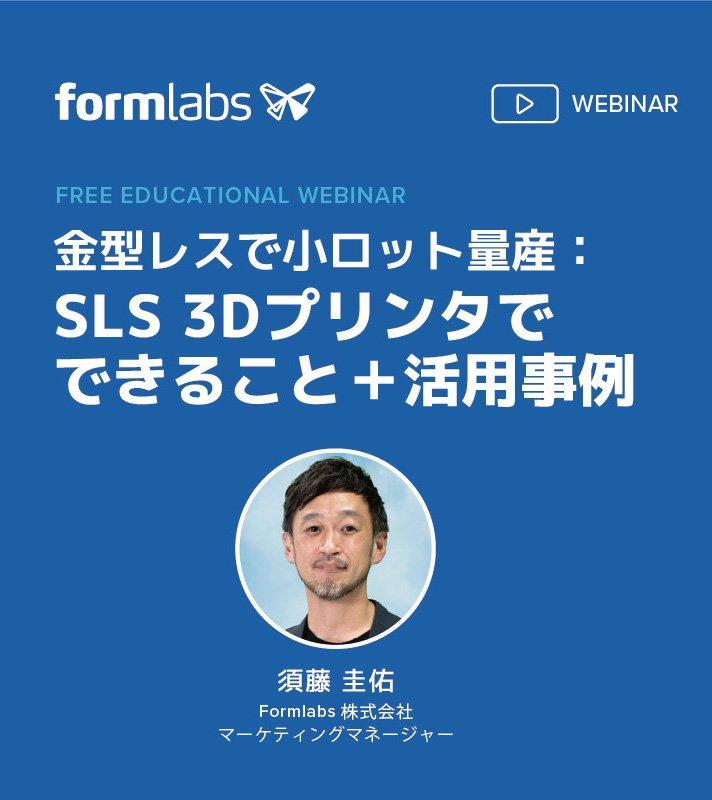
Fuseシリーズでの小ロット量産:ウェビナー動画もチェック
本ウェビナーでは、FormlabsのSLS(粉末焼結積層造形)方式3Dプリンタ、Fuseシリーズでどのように小ロット量産が実現できるのかを採用事例と共に掘り下げます。
FormlabsのFuseシリーズでできること
1. AMでの量産が1,000万円強で実現できる
まず際立っているのは、4,000万円~1億円を超えるハイエンド機並みの造形精度や品質を特許技術で実現したFuseシリーズ製品が1,000万円強で導入できる点です。この価格は、Fuseシリーズプリンタだけでなく、半密閉式の陰圧ブースで粉末除去と再利用を行うFuse Siftがセットになっています。また、300万円程でその後のブラストと研磨までを自動化できるFuse Blastを別売りの研磨装置付きで導入でき、後処理工程の作業時間と作業負荷を劇的に低減することが可能で、その省力化によってFuse Blastの導入コストはかなり早い段階で回収できます。
粉末ベースの3Dプリンタは材料の切替に念入りなクリーニングが求められるケースが殆どで、多大な時間と材料ロスが発生してしまうことから、単一材料での専用機として使用されるのが一般的ですが、Fuseシリーズの価格であれば複数台を導入することも検討できるでしょう。
使用する材料が1種類のみであればFuseシリーズのプリンタを3台とFuse SiftとFuse Blastを1台ずつという導入の仕方で生産性を大きく向上してもハイエンド機の半額程度となる2,000万円強の投資で実現でき、複数の材料を使用する場合は1,000万円未満のFuseセットを4セット導入して初めてハイエンド機並みの金額となります。
2. 唯一の国内環境測定士評価済みSLS
粉末を使用する3Dプリンタは、これまでも安価な機種が登場していましたが、どれも相当量の粉末が作業環境内に舞ってしまい、労働安全衛生上あるいは粉塵爆発も含めたハザードの懸念がありました。装置が海外製品である点も、メーカー側の見解と国内ユーザーの感覚との間に乖離が生まれる原因になっていたように思われます。
そこでFormlabsでは、日本国内で労働安全衛生法に則った作業環境評価を行う国家資格である環境測定士にリスク評価を依頼し、半密閉式の陰圧ブース内以外で粉末が飛散する機会を作らないFuseシリーズの安全設計がどの程度有効なのか、分析を受けています。結果、Fuseシリーズでの作業による作業者の健康被害リスクは最も低いレベルI(良好な作業環境)と判定されています。また、Formlabsの米本国でも大手第三者機関による2種の作業環境評価を受け、その結果をまとめたレポートを発行しています。
3. 豊富な工業用材料と続々と発売される新材料
Formlabsでは、光造形3Dプリント用レジン同様、SLS用パウダーも自社開発しており、毎年2~3種程度の新材料が発売されています。現在Fuseシリーズでは、PBF(Powder Bed Fusion/粉末床溶融結合法)として括られる粉末ベースの3Dプリンタで最もポピュラーなPA(ポリアミド)系、そしてガラスや炭素繊維による複合材、そして軟質材のTPUを提供していますが、材料ラインナップも続々と増えています。FormlabsのSLS用材料の最新ラインナップは、こちらのリンクよりご確認いただけます。
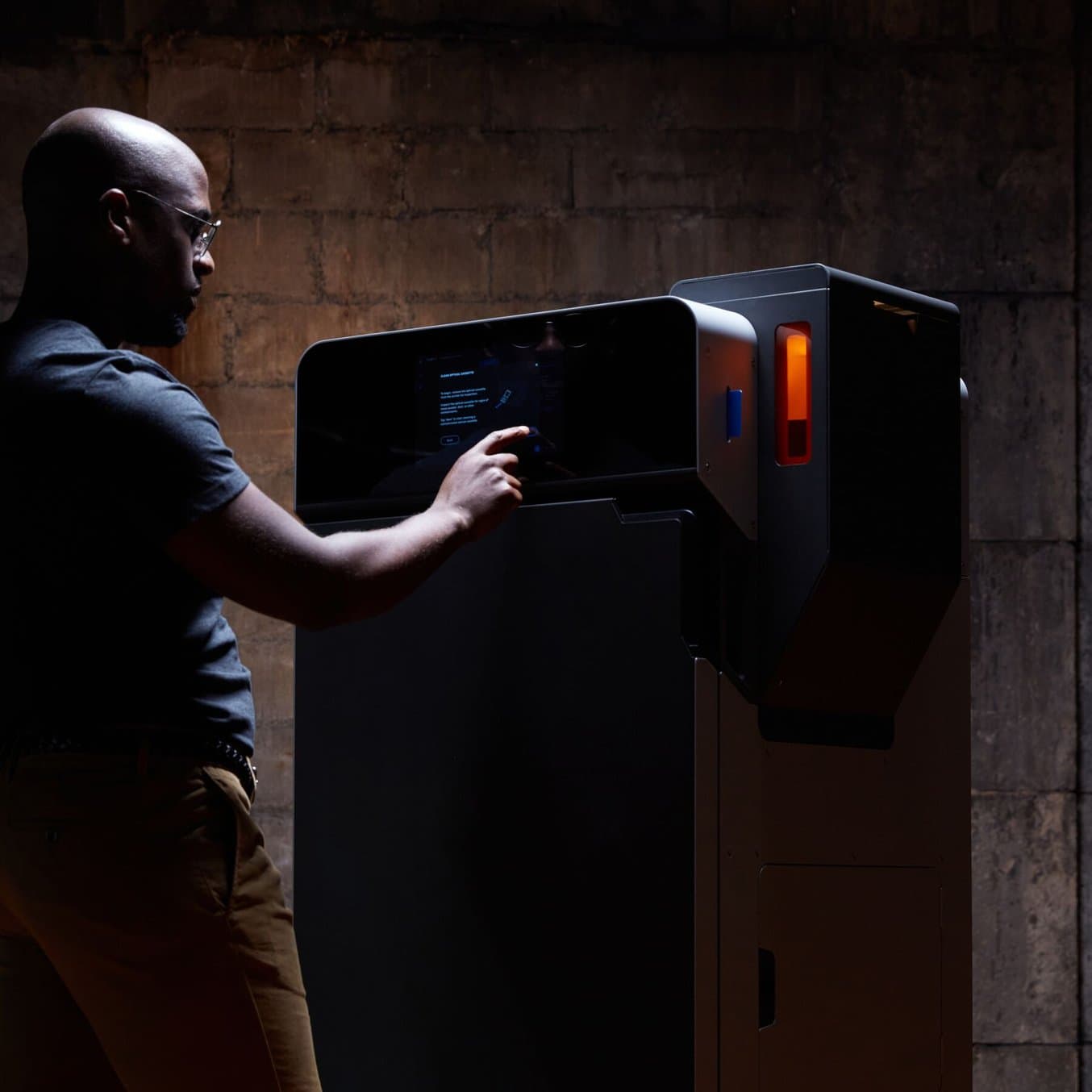
Formlabs SLS製品総合カタログ
本総合カタログでは、FormlabsのSLS方式3Dプリント製品であるFuseシリーズの最新かつ総合的な製品情報、材料情報、対応可能な表面処理、国内外での活用事例や高いコスト効率で運用いただくTIPS等をご紹介しています。
先述の通り、今日では少量多品種のものづくりに対するニーズが高まっています。しかしFormlabsのFuseシリーズのような、コスト面でも安全面でもこれまでの導入障壁を大幅に引き下げるような設備が登場したことにより、そのニーズは受け身で「対処すべきもの」から新たなビジネスチャンスを獲得するために「積極的に掴みにいくもの」へと変わりつつあります。
デジタルファブリケーションの裾野を押し広げ、誰もがものづくりに参加できる世界を目指すFormlabsは、製造業のスタートアップやベンチャー企業、あるいは新規事業を計画されている既存企業の皆さまに、ものづくりの楽しさを味わいながらも競合に差を付ける価値ある製品を製造いただけるよう、国内メーカー様をサポートしています。