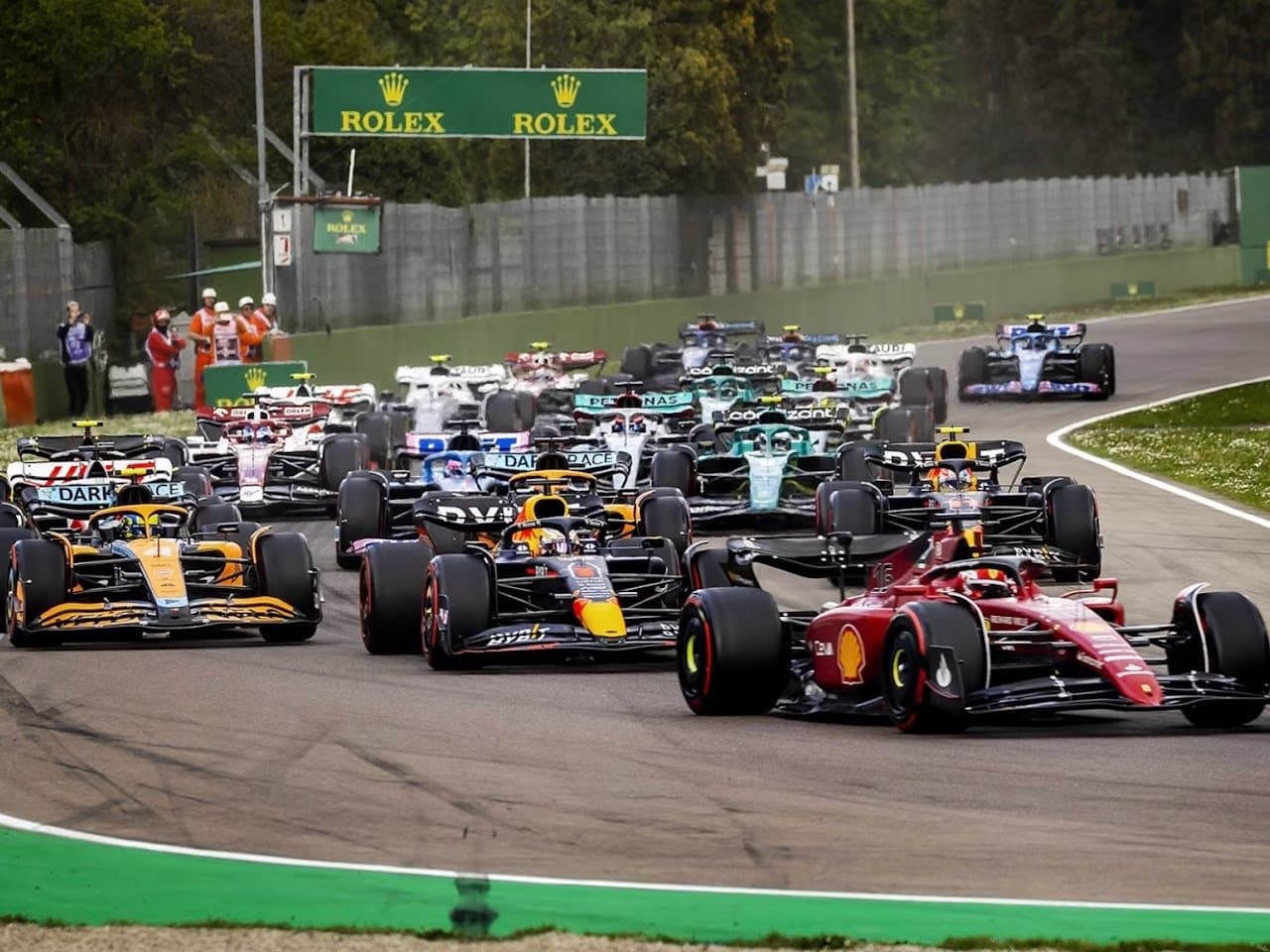
写真提供:Formula1.com
Formula Oneを始めとする国際モータースポーツ大手企業への注目が高まる中、より高速で強力な車の開発に対する期待がますます高まっています。F1チームはすでにエンジニアリング界の逸材を集めていますが、そんな第一線のチームであってもマシンの馬力を高めるために外部の専門家の力を借りることがあります。
そのうちの1つが、イギリスの中心地スタッフォードシャーを拠点とするエンジニアリングおよび製造請負業者Mackart Additiveです。エンジニアリングデザインとアディディブマニュファクチャリングで20年以上の経験を誇るMackartは、試作品製作における3Dプリンタの可能性を従来の限界を超えて広げてきました。現在、Mackartの受注案件の約80%がF1チーム向けのものです。この業界では、軽量化技術、馬力、安定性、空力性能を指数関数的に改善する方法を常に探しています。McCarthy率いるチームは、CFRP(炭素繊維強化プラスチック)製部品の製作に用いる複雑な形状の成形型の3Dプリントを得意とし、これまで実現し得なかった新しい可能性と基準を打ち立てています。
MackartはForm 3シリーズのSLA(光造形)方式プリンタを9台とForm Auto、FDM(熱溶解積層法)、複合材料プリンタを駆使し、炭素繊維部品やシリコン部品用の成形型に加え、3Dプリント製の実製品部品を製造しています。同社はFormlabs公式パートナーのSolid Print3Dと提携し、生産能力を最大限に引き出すことに成功しました。
"3Dプリントは単なる試作品製作ツールではなく、優れた製造プロセスです。"
Steven McCarthy氏 Mackart創設者兼最高経営責任者
炭素繊維部品用の複雑な成形型を3Dプリント
McCarthy氏はもともと航空宇宙エンジニアリングを専門としていましたが、2016年の設立以来Mackartは配管設備メーカーからモータースポーツの大手国際企業に至るまで幅広い業界と提携しています。
競争の激しいモータースポーツ界で最も広く採用されている材料の1つが、最近では自動車業界でも広く活用されるようになったCFRP(炭素繊維)です。CFRPに含まれる成分は、サーキットで発生する高温にも耐えることができ、優れた強度重量比でレーシングカーの性能を全面的に強化します。
炭素繊維部品は通常、炭素繊維に未硬化樹脂を含浸させたプリプレグシートを使って成形されます。プリプレグシートを金型の中や上に積層し、オートクレーブ内で加熱・加圧して硬化させます。
従来の方法では、金属材料を切削することでオートクレーブ内の高熱と圧力に耐えられる金型を作っていました。このサブトラクティブ手法の場合、材料の無駄が多く時間もかかり、かつ高額なために試作・検証を繰り返す設計プロセスが実現できませんでした。3Dプリンタと材料が進化するにつれ、このような用途にも耐えられる丈夫な金型を3Dプリントすることが可能になったのです。
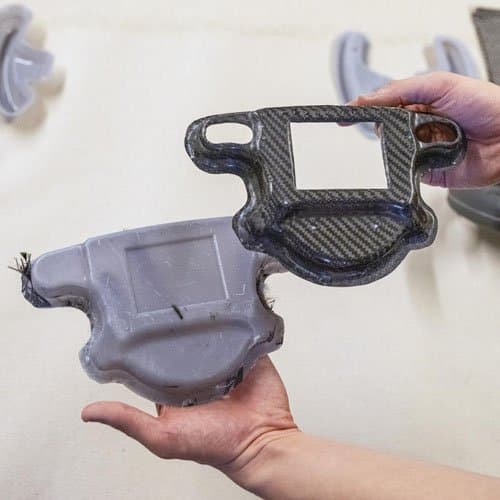
3Dプリント製の型で炭素繊維製パーツを製作
本技術資料では、複合材料を使用した成形型の設計ガイドラインや、炭素繊維部品の製造に必要なプリプレグや手作業によるラミネート成形について、手順ごとに詳しく解説しています。
様々な技術の融合で炭素繊維用金型を製作
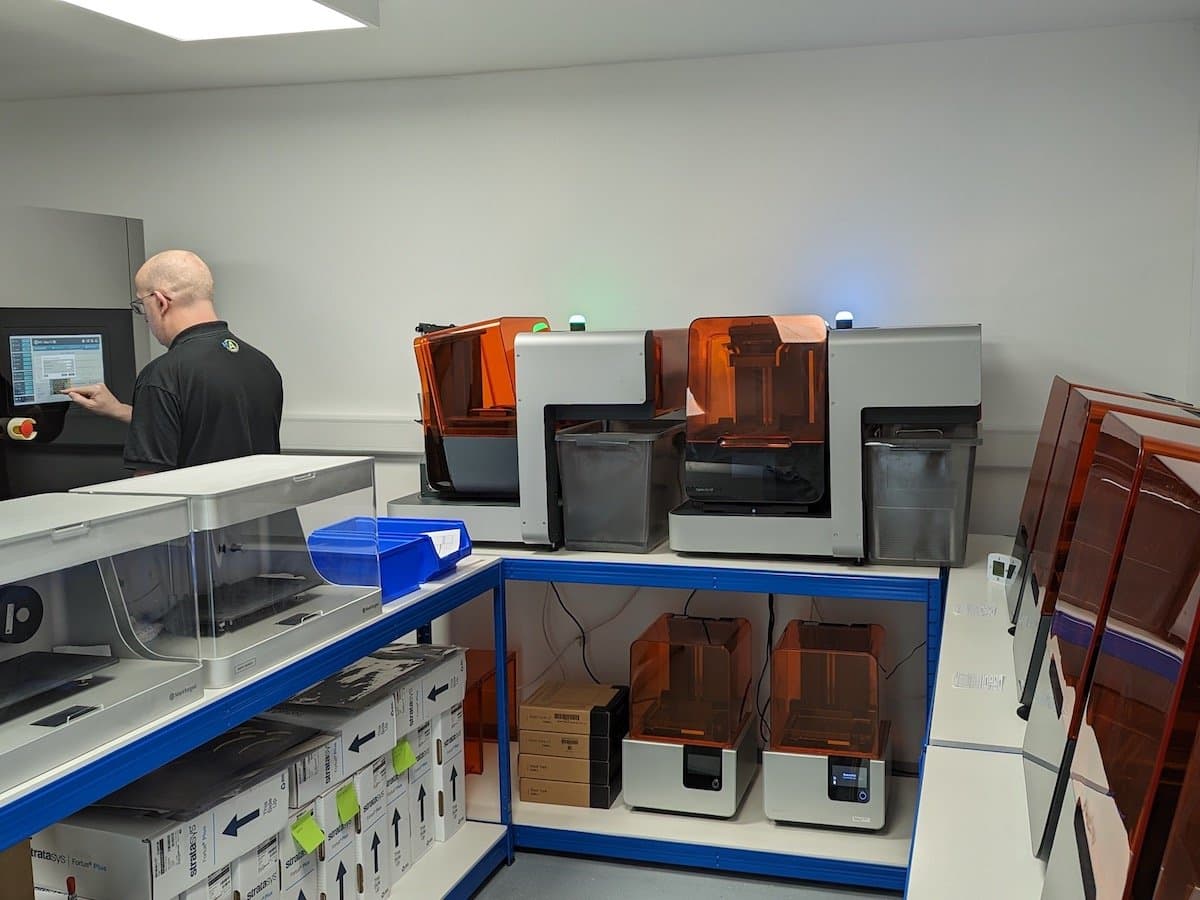
Mackart Additiveの3Dプリントラボは、Form Auto2台を始めとする様々な技術や工程を組み合わせることで、幅広い業界用途に適用できる高度な部品を製造している。
産業用途でも耐えられる金型製作の成功の秘訣は、プリント品設計と方向づけの最適化です。Mackartチームはこれらのパラメータを科学的に検証しています。複雑な炭素繊維用金型やマンドレルの設計・製造には、それぞれが持つ属性を吟味して様々な3Dプリント方式や材料を使用しています。
元々Grey レジンを使用していた同チームは、Grey Proに移行し、その後Rigid 4000レジンとRigid 10Kレジンの検証に着手しました。その結果、これらレジンのなめらかな表面品質と硬さにより、実製品用の炭素繊維部品で最高の仕上がりを実現できることがわかりました。「Rigid 4000レジンで成形用の型を1つ製作してみたところ、これが素晴らしい出来栄えでした。製作した金型をレーザー計測で検証しましたが、CAD形状のノミナル値からミクロン程度の逸脱が見られるケースもあったものの、寸法的には驚異的な結果が出ました」とMcCarthyは言います。
McCarthyのチームが大型の金型を製作する時は、まず小さな部品を製作し、入念に考慮された締結部で各部品を組み合わせることが多いです。「プリンタの最大造形サイズを超えるような大型の金型には、後で組み立てられるよう、フランジ継手を使うことが多いです。3〜4つほどの部品で構成されるアセンブリを作れば、長さが450mmにもなる金型の製作も可能です」とMcCarthyは教えてくれます。
技術比較:炭素繊維部品用の成形型製作
製作期間 | 長所 | 短所 | |
---|---|---|---|
3Dプリント製の成形型 | 1週間 | 設計の自由度が高い 制作期間とサプライチェーンの制御が可能 小ロット量産のコスト効率が良い | 熱膨張の考慮が必要 最大造形サイズに制約 取り数が少ない |
従来の成形型 | 3~4週間 | 大量の取り数 耐性が高い サイズの自由度が高い | 製作期間が長い 設計上の制約がある |
洗練されたパラメータで製作工程を最適化
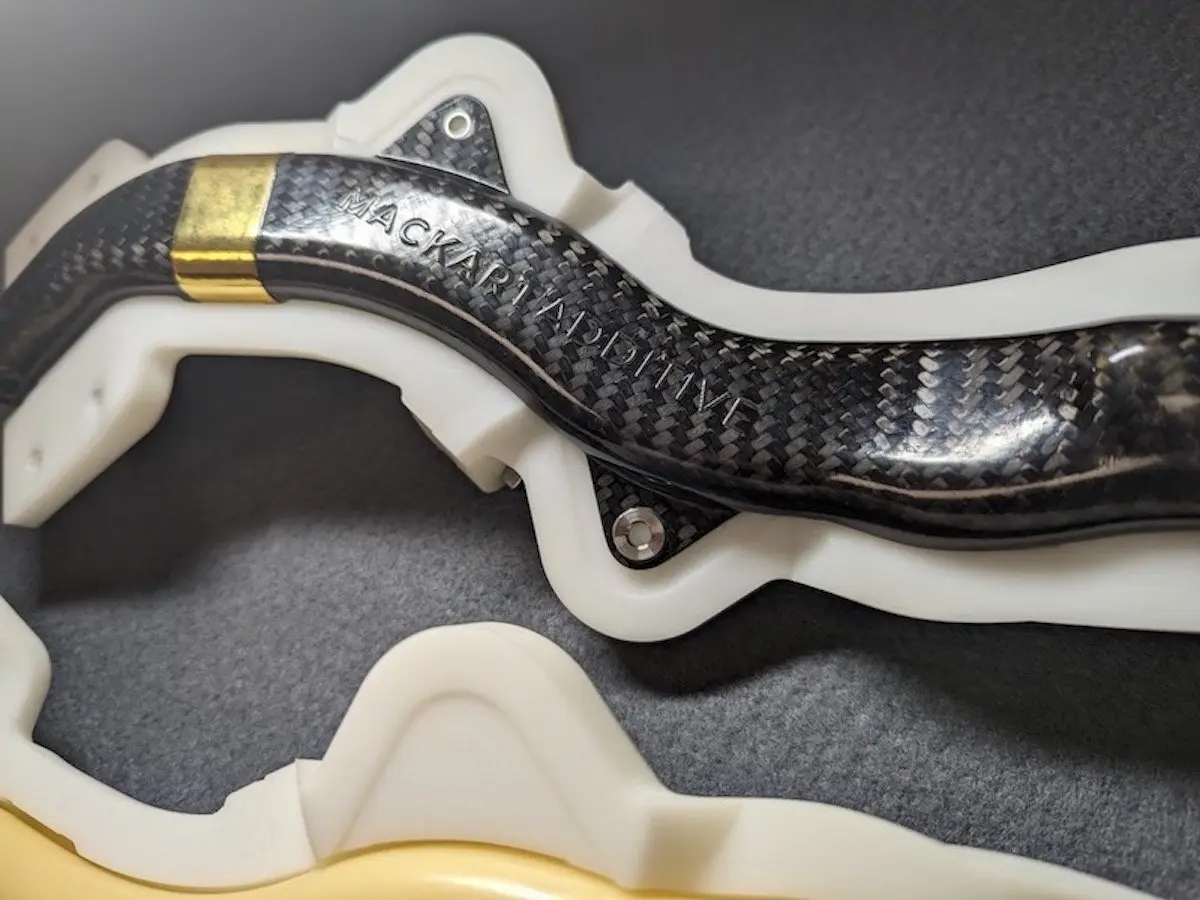
3Dプリントで高速製作(ラピッドツーリング)した金型で成形した炭素繊維のダクト部品。外枠もRigid 10Kレジンを使用してForm 3+でプリント、内部加工用のマンドレルは 別の大容量液槽光重合法SLA方式3Dプリンタ でプリントしたもの。
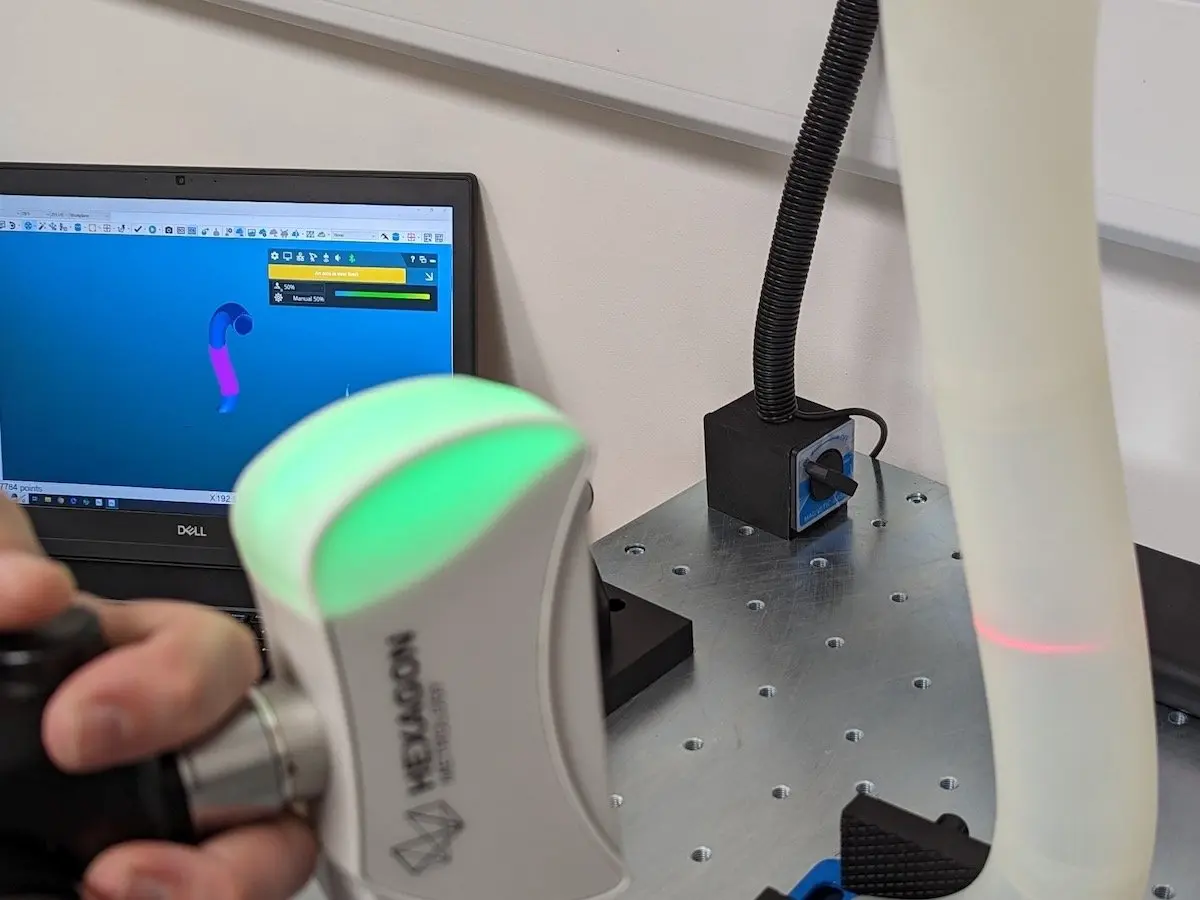
McCarthyが Form 3でプリントしたDurableレジン製のマンドレルを3Dスキャンする様子。F1の空気輸送ダクトのCFRP部品製作で使用される。
オートクレーブでの硬化工程では、内部の温度が金型に使用した材料のガラス転移点を超える可能性があります。McCarthyのチームは、Rigit 10Kレジンなら劣化したり寸法精度を損なうことなく繰り返し使用が可能であることに気づきました。「Rigid 10Kレジンは剛性が高く、表面品質も他の材料よりやや高いのです。アルミニウムの代替としては最適な材料です」とMcCarthyは言います。ガラス分を含むRigid 10Kレジンは、プリント時に感光性樹脂が硬化することでガラス分子が造形品の表面に出てきてしまうのですが、同社チームはRigid 10Kレジン製の金型の表面を軽く削って滑らかにすることで、炭素繊維シートを被せる時に触れる表面の品質を最適化しています。
また、オートクレーブ成形工程で発生するクリープも考慮して調整を行い、成形後の CFRP部品が公差内に収まるようにします。「しっかりと公差内に収めることは、それほど複雑なことではありません。大型の金型は割合が何より大切なんです」とMcCarthyは教えてくれます。
ダクトやチューブなど複雑な形状をしたCFRP部品の内部加には、従裏通り水溶性の離型剤とマンドレルを使用しますが、小さな部品(プリンタの最大造形サイズに収まるもの)であれば、引き抜き可能なマンドレルを3Dプリントして、FDM製のマンドレルと水溶性離型材を使った複雑な作業やそれにかかる時間を削減することができます。Mackartは、Durableレジンをこの用途に見事に適応させました。3Dプリンタの最大造形サイズを超える大型の引き抜きマンドレルの場合は、同社が保有する別の大容量液槽光重合法SLAプリンタを使用します。
欠かせない細部への配慮
たとえミクロン単位であっても、設計の違いが1秒の差やフィニッシュラインでの最後の一押しに影響するモータースポーツなどの業界には、アディティブマニュファクチャリングが最適です。車体を取り巻く気流、車体に流れ込む気流が鍵を握ります。
「3Dプリントなら従来のサブトラクティブ手法で制約のあった形状も自由に設計でき、モータースポーツ界に最適なソリューションです。レーシングカーの車内では空間が非常に大切です。形状設計の自由度が与えられたことで、エアロダイナミクスを最適化できるようになりました。剛性の高いCFRP部品(3Dプリント製の成形型で作ったCFRP部品)の性能を妥協することなく処理して車体に組み込むことができなければ、過去数シーズンのレースで見られたようなパフォーマンスの向上は見込めなかったかもしれません。その可能性を引き出す成形型を製作できているのは、慎重かつ考え込まれた設計技術によって3Dプリント製の成形型を最適化した結果です」とMcCarthyは言います。
「これまで、従来のサブトラクティブ手法で製作した金型で比較的複雑な形状のCFRP部品を作ろうとすると、最終的な部品装着段階で行う「鋳仕上げ」のために、部品に予備材料を追加しておく必要がありました。3Dプリント製の金型は精度も安定性も高く、この予備材料の必要性が大幅に減りました。今では最初から「完璧な」部品を期待できるようになり、これは出来上がったCFRP部品が何度も証明してくれています。 弊社が得意とするのは、驚くほど正確な形状を実現することです」とMcCarthyは言います。
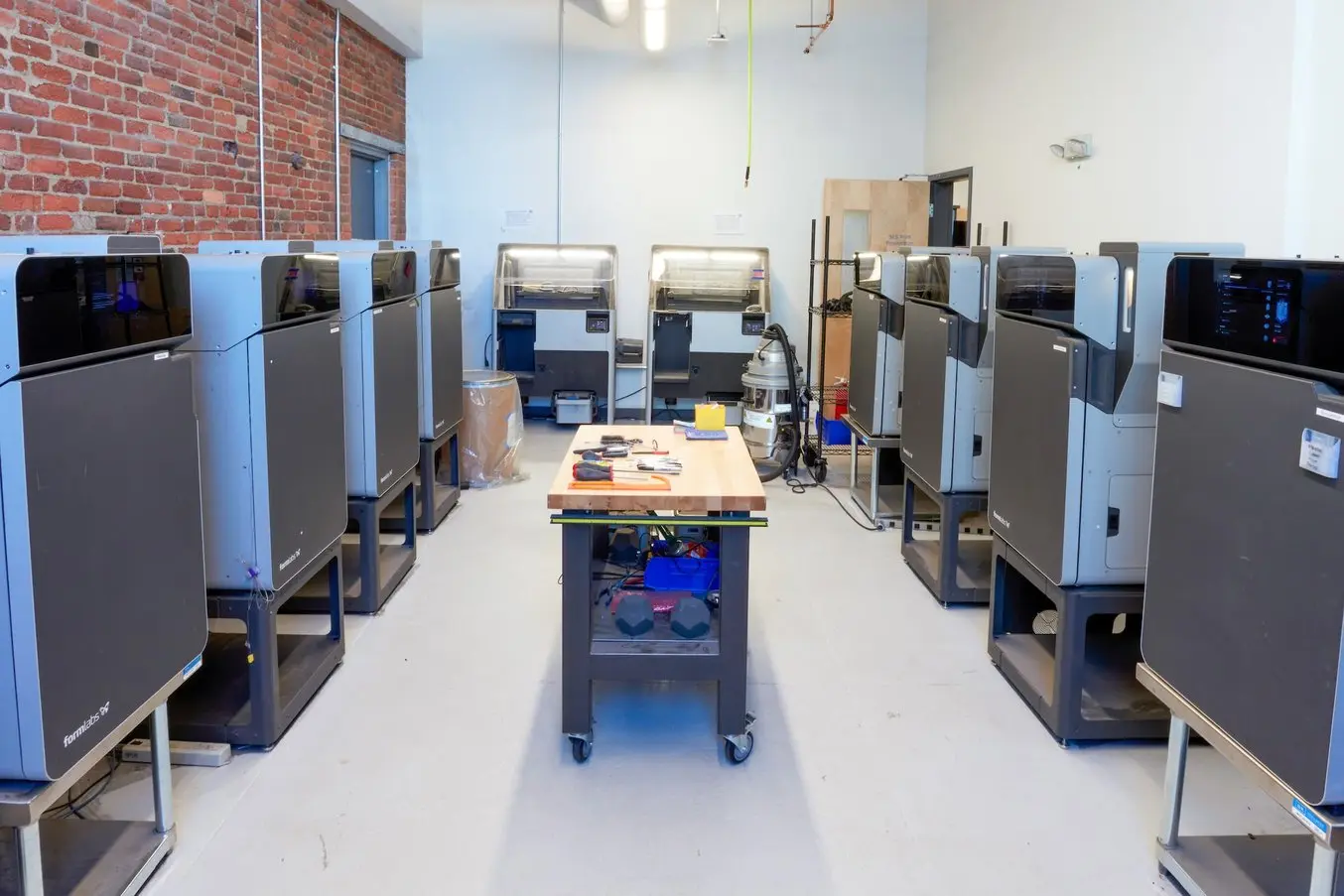
複数台の3Dプリンタを高効率に運用するには
SLA光造形方式やSLS方式3Dプリンタの複数台運用は、決して複雑なオペレーションではありません。どんな企業でもわずか1〜2日で複数台の光造形・SLSプリンタをセットアップして運用を開始できます。本ガイドでは、プリンタの複数台運用を効率的に行っている4つの事例と共に、生産量や製作品目に関わらず参考になる効果的な環境の整備方法をご紹介します。
Form Autoで常時稼働を実現
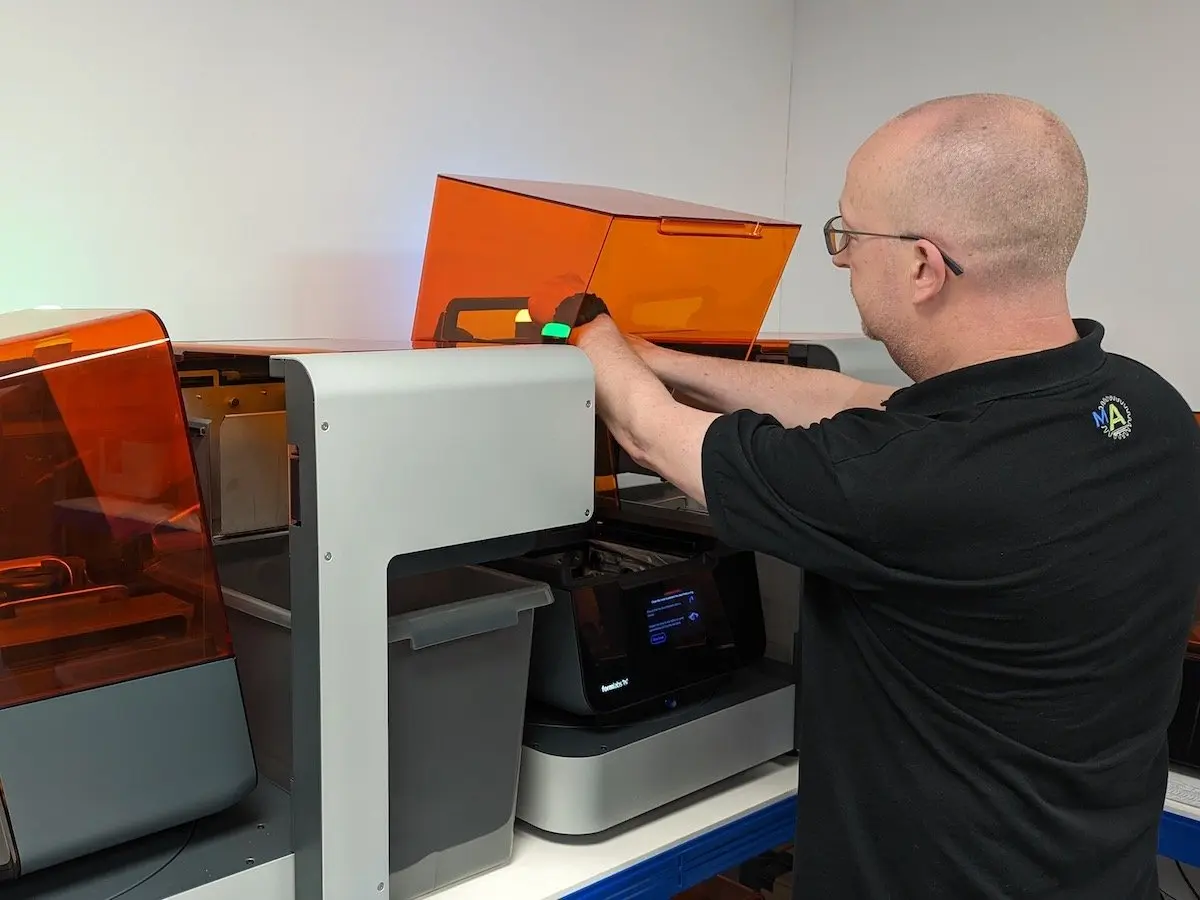
Form Autoは既存のForm 3やForm 3+プリンターに後付け可能な機能拡張ハードウェアで、ビジネスの成長に合わせて段階的にハードウェア機能を拡大することができる。
MackartはFormlabsの自動化製品をいち早く導入した企業で、2023年初頭からForm Autoの稼働を開始しました。それ以来、自動化工程を最適化し続けています。「Form Autoの利点は、夜間も稼働させて造形数を最大化できることです」とMcCarthyは教えてくれます。
同社が所有する9台のForm 3+プリンタのうち2台にForm Autoを取り付けて常時稼働させ、夜間や週末、チームが帰宅した後もプリントを続けています。
「Form Autoなら、人の手によるBuild Platformからの取り外しや交換も不要で、夜間や週末の常時稼働が実現できます。稼働状態も問題なく、小型部品や最大1000個以上の中規模バッチ生産に最適です」
Steven McCarthy氏 Mackart創設者兼最高経営責任者
同社チームは常に様々なプロジェクトに取り組んでいます。新しくより複雑な部品は手作業で対応する一方、繰り返し作業はForm Autoに任せることでプリンタのアイドル時間を減らしています。「その結果製作期間が短くなり、生産性が向上しました」とはMcCarthyの言葉です。
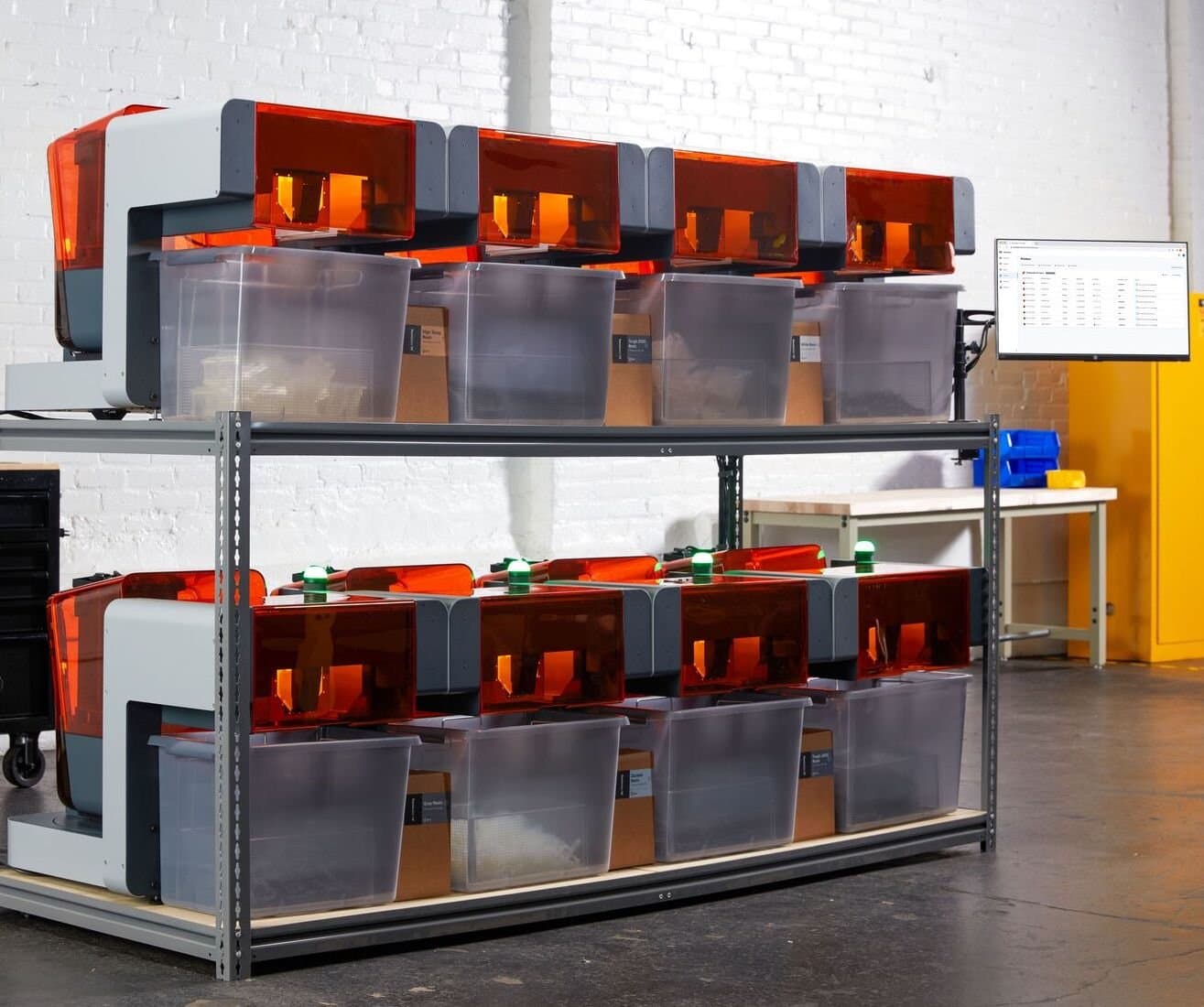
Formlabsのオートメーション製品
処理能力や生産性の概念を覆す24時間365日の連続生産から複数台プリンタの自動化まで、Formlabsのオートメーション製品について詳しく説明いたします。
クラシックカーの部品製作で£10,000を節約
繰り返し作業の中には、クラシックカーの部品のような小型部品を大量生産するものもあります。こういった部品はかつて射出成形(IM)で製造されていましたが、当時使用されていた金型の大半が時と共になくなり、現存の在庫が枯渇しています。ある顧客がMackartに助けを求めたのも、このような背景からでした。
以前は、必要な部品の在庫があれば1つあたり£0.20程度で購入できていました。これらの部品を3Dプリントする場合、部品単価は従来の5倍から10倍になりますが、新しい金型の購入費用や射出成形の最小ロット、セットアップ費用、さらにこういった生産コストを個別の部品に乗せることができない、といった心配をする必要がありません。
3Dプリント製の部品で現実的なソリューションが生まれます。「部品を3Dプリントすることで、射出成形にかかる直接経費を丸ごと除外することができます。 必要なものは何でもリバースエンジニアリングで設計し、お客様はそのうちの1つを購入すればいい。射出成形用の新しい金型やその他工程で発生する追加コストに£10,000以上も払う必要はありません。その後は、必要な数量を無限に供給することができます」とMcCarthyは言います。
自動車業界では、たった1つ、あるいは少量の部品を製造するだけでも莫大なコストがかかるため、クラシックカーの修復やメンテナンスは非常に高価になりがちでした。しかし3Dプリントの活用により、Mackartでは数量に応じた割引を顧客に提供できています。「3Dプリントは従来の方法よりはるかに柔軟で経済的です。これこそForm Autoの最大の強みとも言えます。すぐに使える状態で届きますし、必要なメンテナンスも最低限。時々新しいレジンカートリッジを入れるだけで、1000個の造形品を作ることができます」とMcCarthyは言います。
効果を証明した今、さらなる大量生産へ
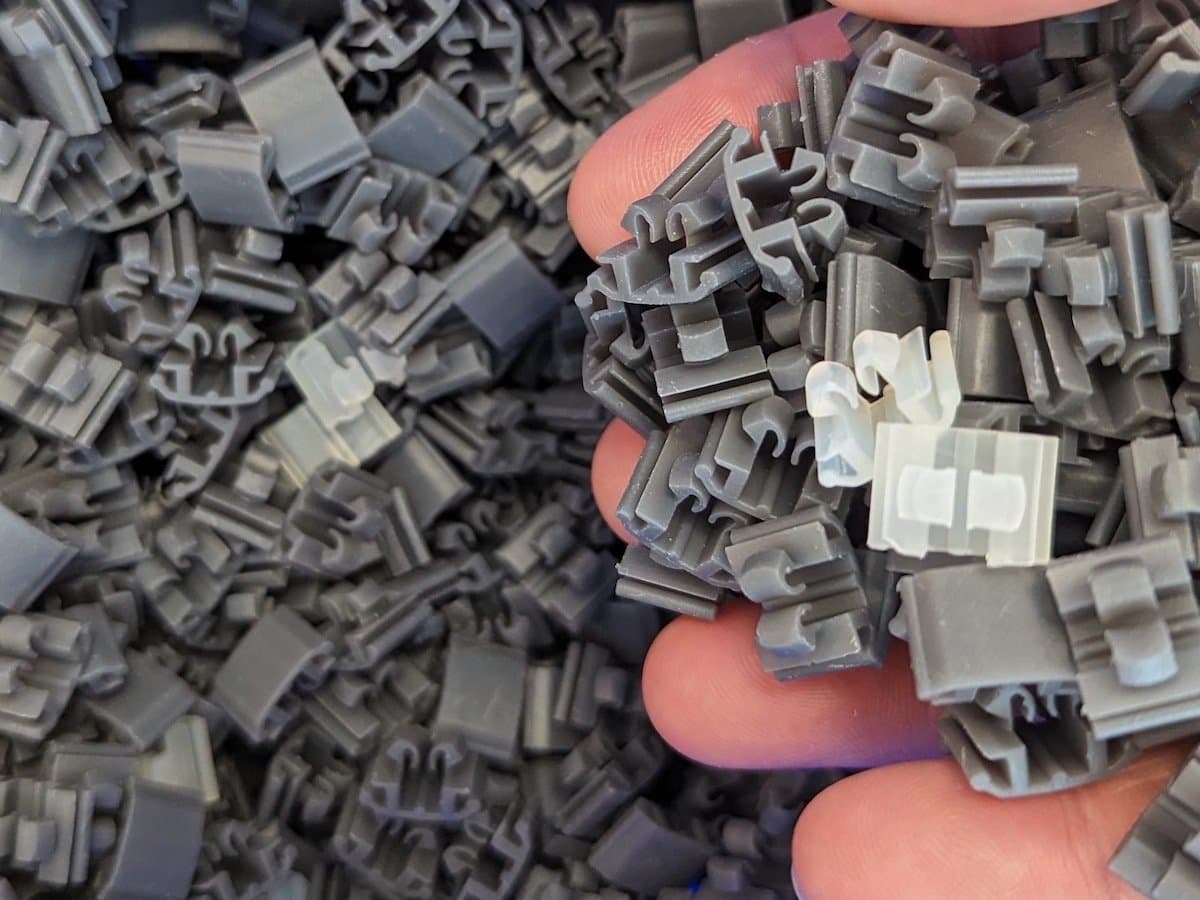
MackartはForm Autoを活用し、 クラシックカー市場に供給するトリムクリップ を何百、何千個も製造している。
Mackartは時間をかけて工程を最適化し、幅広い業界の顧客に高品質の部品を供給できるようにしてきました。そのために様々な技術を駆使し、異なる3Dプリント方式や材料の中から各用途に最適なものを選んできました。
新たにForm Autoを導入したことで、生産シフトを増やし、生産能力の向上に成功しました。McCarthy氏は、今後需要の増加に伴い、3Dプリンタ群を活用することで、世界屈指のF1チームから認められた精度と性能を活かし、新しい産業への参入や新たな用途への挑戦も可能だと確信しています。
Formlabsの3DプリンタでMackartの事業を支えてくれているのは、弊社の英国正規販売代理店Solid Print3Dです。 自動車業界における3Dプリント活用事例の詳細についてはリソースページをご覧ください。また、お客様独自の用途についてはFormlabsにご相談ください。