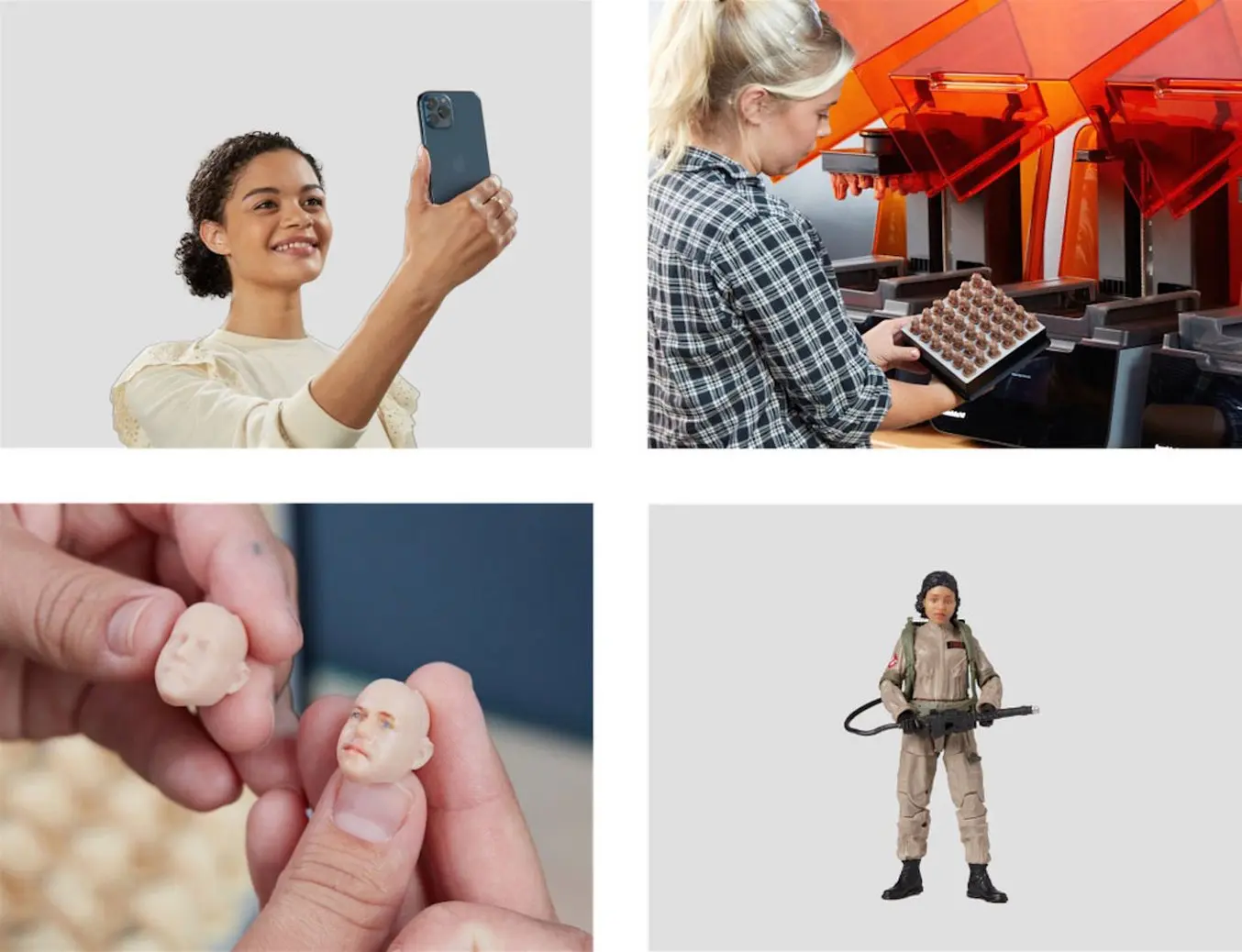
今日では、商品を購入する際に個々のニーズや要件を満たそうとする顧客の傾向が強まっています。デロイト社の調査によると、いくつかのカテゴリーでは、半数以上の消費者がカスタマイズされた製品やサービスを購入することに興味を示しており、その大半はカスタマイズされた製品やサービスに対してより多くのお金を支払ってもよいと考えています。しかし、私たちを取り巻く製品の多くが大量生産品であるにもかかわらず、どうすれば企業は、カスタマイズされた製品や体験をより多くの人々に、手頃な価格で提供できるのでしょうか。
カスタマイズされた製品を製造するには、ユーザー特有の要件に細心の注意を払う必要がありますが、数千件もの注文でそのような作業を行うと、従来の手順では製造コストが大幅に増大するだけでなく、納期も極めて長期化します。マスカスタマイゼーションとは、カスタマイズが持つオリジナリティと大量生産の利点を組み合わせ、変化する顧客要件に対応するプロセスなのです。
このガイドでは、カスタマイズのさまざまなアプローチ、最適なアプローチの選択方法、マスカスタマイゼーションの導入を実現する先端技術について、メーカー向けのインサイトを提供します。
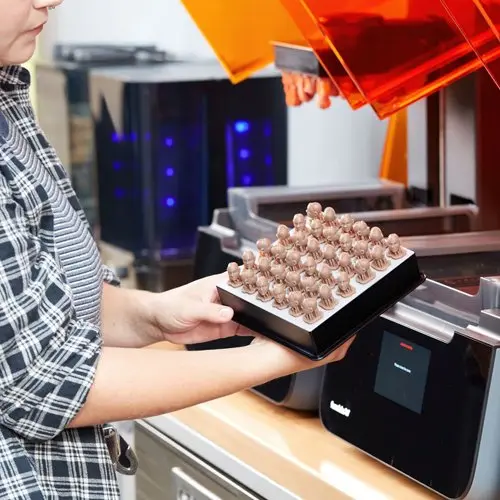
マスカスタマイゼーションを実現する方法
3Dプリントで真のマスカスタマイゼーションを迅速かつコスト効率よく実現する方法を学びます。Formlabsのエキスパートがさまざまな作業手順をご案内し、おすすめ情報を共有するほか、マスカスタマイゼーションに3Dプリントを使用している革新的な企業の実例をご紹介します。
マスカスタマイゼーションとは
マスカスタマイゼーションとは、カスタムメイド製品の柔軟性とパーソナライゼーションを、大量生産による低価格化と組み合わせるマーケティングおよび製造手法のことです。
従来の大量生産では、標準化された製品を効率的なプロセスで大量に製造していました。標準化された製品の連続生産は、電気の発見と組立ラインの発明により可能となり、第二次産業革命の始まりとなりました。組立ラインにより、生産は大規模な集中設備に移行し、商品の大量生産が可能になりました。第三次産業革命は1970年頃から始まり、生産工程全体の自動化が進み、次第に人間の手が不要となりロボットや自動化された製造機械に置き換えられていきました。そして現在は、インダストリー4.0の時代となり、情報通信技術を産業に応用するという特徴があります。
大量生産は大量の商品を可能な限りの低価格で生産することですが、カスタム製造はその対極にあり、顧客独自の仕様にもとづいて商品を設計、エンジニアリング、生産するプロセスとして定義されています。従来のカスタム製造は通常、ニッチな顧客要件を満たすために小規模または短期間の生産に適用されるもので、伝統的にコスト増と結びついていました。
今日の市場では、多数の顧客がカスタマイズされた商品を求めているため、大量生産や従来のカスタム製造ではそのニーズを満たすことはできません。マスカスタマイゼーションは、成長する市場に向けてカスタマイズされた製品を大量に生産するという、メーカーにとっての理想を実現するものです。
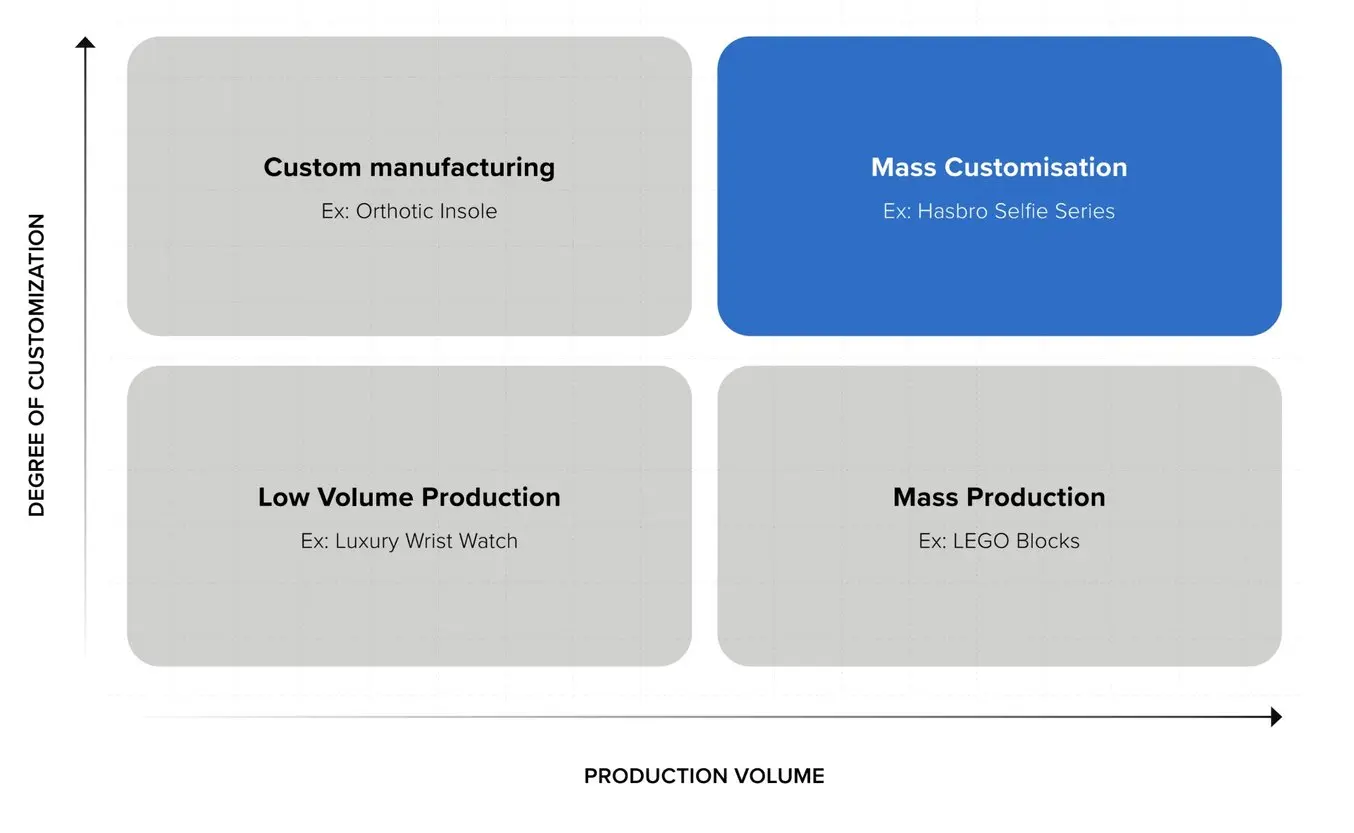
以下に、各用語とその最も重要な特徴のおおまかな比較をご紹介します。
大量生産 | カスタム製造 | マスカスタマイゼーション | |
---|---|---|---|
パーツの造形単価 | 低 | 高 | お手頃 |
製造規模 | 大規模生産 | 小規模生産 | 中〜大規模生産 |
生産アプローチ | 見込生産 | 受注生産 受注組立生産 | 受注生産 受注組立生産 |
製品のバリエーション | 極めて限定的 | 無制限 | 若干の制約あり〜無制限 |
パーツあたりの製造速度 | 早い | 遅い | 普通〜早い |
新製品のイテレーション導入に要する時間 | 長い | 短い | 短い |
一般的な生産手段と工程 | 射出成形、鋳造、板金加工、プレス加工、組立ライン、ロボティクス、オートメーション | 手作業、機械加工、工作ツール | 3Dスキャン、3Dプリント、デジタル工作ツール、従来的な製造機械のためのラピッドツーリング、ロボティクス、オートメーション |
生産規模やコスト以上に、これらの用語の特に大きな違いとなるのは、生産方式です。
-
見込生産とは、需要予測にもとづいて生産計画を立てる製造戦略です。この場合、メーカーは消費者の需要サイクルや具体的な要件を予測し、それらを満たすために製品を生産しようとします。見込生産は大量生産に適したアプローチです。大量に生産することで、メーカーは初期の生産コストを抑えることができますが、大量の在庫を抱えることでコストがかかり、需要予測に狂いが生じると莫大な廃棄物が生じます。
-
受注組立生産では、最終生産を組み立てるのに必要な部品を在庫として確保しておきます。メーカーはその後、顧客の発注とカスタム要件に応じて部品を組み立てます。受注組立生産はカスタム製造とマスカスタマイゼーションの両方に共通する戦略ですが、後者のほうがより高度な製品構成と生産プロセスを用いてコストを抑えることができます。
-
受注生産では、消費者とメーカーが全面的に協力します。メーカーは顧客から提示された正確な仕様に従って製品を開発するため、製品のバリエーションは無限となります。これはカスタム製造とマスカスタマイゼーションの両方に共通する戦略ですが、後者ではより高度なプロセスを用いて、カスタマイズに必要なデータの収集、カスタム部品の生産、最終製品の組立をすべて大規模に行うことで、コストを低く抑えます。
この3つのコンセプトは目的や生産手段、プロセスが異なるほか、特徴も異なります。
-
従来の大量生産は従来的な製造プロセスに依存しており、射出形成、鋳造、板金加工、プレス加工など、高価なツーリングに加え、製造、セットアップ、本格稼働に何か月ものリードタイムが必要となります。組立ラインやオートメーションを活用することで、さらに効率を高めることもできます。一度セットアップが完了すれば、短期間で何千もの製品を生産でき、大量生産した部品に固定費を分散できるため、結果的に単価が抑えられます。大量生産プロセスは柔軟性に欠け、設計変更の際にはツーリングと製造プロセスの調整が必要となり、コストがかかります。
-
従来のカスタム製造は手作業、 機械加工、多様な工作ツールなどのプロセスを活用します。ツーリングはほとんどないか全くなく、ワークフローがより柔軟なため、新製品の投入や設計のカスタマイズが容易となります。手作業による生産プロセスは生産能力が低く、簡単に拡張することはできません。
-
マスカスタマイゼーションは革新的な新技術を利用してデータの収集、設計、部品の製造、製品の組立を行います。また、ツーリングを必要としない製造プロセスや、従来的なプロセスに小規模なラピッドツーリングを活用してコストを抑えます。求められる開発事項や製品の複雑さによっては、市場投入までの時間が大量生産プロセスよりも長くなる場合がありますが、製品設計の変更が安価で容易なため、カスタマイズが可能となり、市場のニーズへの適応が容易になります。また、多くの企業はモジュール化の概念を活用し、さまざまなパターンで組み立て、変更、カスタム部品との組み合わせができる標準的な量産部品を使用して最終製品を製造することで、生産能力を高めるとともにコストを抑えています。
マスカスタマイゼーションのメリットとデメリット
マスカスタマイゼーションには特有のメリットがありますが、すべての用途に適用できるわけではありません。参考までに、以下にメリットとデメリットをご紹介します。
メリット | デメリット | ||
---|---|---|---|
カスタム製品に付加価値をつけることができる。また、その付加価値がカスタム部品を製品に組み込むコストよりも大幅に高くなることが多い。 | 従来的な標準化された製品の大量生産に比べて、製造コストが高い。 | ||
顧客直販型のビジネスモデルにより、中間業者に頼る必要がなくなり、マージンが増加する。また、顧客基盤と持続的な関係を築くことが可能になる。 | 実現可能性が製品の種類や、顧客がカスタマイズ料金を払うか否かに依存する。マスカスタマイゼーションはベーシックな製品よりも高級品に適している。 | ||
カスタマイズが競合他社との差別化に役立ち、さらには自社独自の強み(USP)となって、競争力を高める。 | カスタマイズにより、購入後に製品の製造・出荷が必要となるため、納期が延びる傾向がある。 | ||
柔軟な生産プロセスにより、顧客のニーズに製品を適応しやすくなるほか、高価なツーリングに先行投資する必要がなくなる。 | 従来の大量生産に比べ、カスタム製品の生産能力は比較的低い。 | ||
在庫管理が改善することで、間接費と廃棄物が削減され、顧客基盤からますます注目されている持続可能性に貢献できる。 | カスタム製品への需要増加や突発的な需要が生じると、サプライチェーンに問題が生じる可能性がある。製品の返品が複雑であったり、不可能であったりする。 | ||
カスタマイズの選択肢と顧客との関係強化により、顧客満足度が向上し、顧客離れを抑えることができ、顧客生涯価値が増加する。 |
マスカスタマイゼーションの種類
Pine and Gilmore(1992)は、マスカスタマイゼーションの4つのアプローチを定義しました。これらのアプローチは、特定の顧客に最も適したサービスを提供するため、個別に、または組み合わせて使用できるとされています。
4つのアプローチは、以下のとおりです。
-
コラボレーティブカスタマイゼーション(共創):個々の顧客との対話を通じて顧客のニーズを明確化し、そのニーズを満たす的確な提案を特定し、顧客のためにカスタム製品を製造するカスタム化です。このアプローチは、マスカスタマイゼーションという語とともに用いられることが特に多く、カスタム製品を必要とする大規模な顧客基盤を持つメーカーが主に適用しているものです。また、意思決定に悩む顧客や繊細な要件を持つ顧客に対して、顧客が必要とする正確なニーズを詳細に伝えるプラットフォームを提供します。
Nike By You(旧Nike ID)のシューズカスタマイゼーションプログラムがコラボレーティブアプローチの代表的な例です。このカスタム化プロセスでは、シューズのデザインをカスタマイズしたい消費者がデザインを制御できます。このオンラインプラットフォームで提供されるツールにより、消費者は製品をオンラインでイテレーションでき、最終製品は顧客に直接製造・出荷されます。
-
適応的カスタマイゼーション:標準的な製品でありながらもカスタマイズが可能で、受け取ったユーザーが自分でアレンジできるように設計された製品を提供するアプローチです。このカスタマイゼーションの選択肢により、顧客は多様なニーズに合わせてさまざまな方法で製品を使用できます。適応的なアプローチでは、使いやすい機能を統合することで、顧客が製品の利用方法を比較的簡単にカスタマイズできるようにしています。
IoT(モノのインターネット)システムが適応的カスタマイゼーションの代表的な例です。たとえば、IoT対応機器を自宅に設置し、照明や冷暖房、カーテン、窓の開閉、スピーカー、家電製品などを、すべて自分の好みに合わせて管理できます。
-
表面的カスタマイゼーション:標準的な製品を顧客ごとに異なる方法で提供するアプローチです。このアプローチでは、個々の顧客に販売する製品を大幅に変更する必要はなく、個々の顧客の興味をそそるようにカスタマイズした表現手段を用いて、標準的な製品をパッケージングするだけとなります。表面的カスタマイゼーションは、顧客の要望に応じて行われることもあれば、顧客情報をもとに目立たないように行われることも、ランダムに行われることもあります。
コカ・コーラ社の有名な“Share a Coke”キャンペーンは表面的カスタマイゼーションの代表的な例であり、標準的な製品を変更することなく売上を伸ばし、顧客個人のニーズを満たせることを示しています。このキャンペーンでは、標準的なコーラの缶やボトルの従来の包装やパッケージが変更され、各地域で最も一般的な名前が入れられました。顧客は自分の名前が入ったコーラを求めることや、あらゆる市場で自分だけのボトルを探すワクワク感を楽しむことができました。
-
透過的カスタマイゼーション:ユニークな商品やサービスを個々の顧客に提供しながらも、顧客に合わせてその製品やサービスをカスタマイズしたことを明確には知らせないアプローチです。透過的カスタマイゼーションを行う企業は、顧客の特定要件に自社データベースで容易にアクセスできる場合や、顧客の行動パターンを分析することで要件を把握し、顧客のニーズが予測可能である場合にこのプロセスを採用しています。
透過的カスタマイゼーションは、実施されているカスタム化について顧客に明示的に知らせることなく、控えめに行われることが多いです。このアプローチはオンラインサービスやプラットフォームで一般的に用いられており、Facebookのパーソナライズされたフィード、Spotifyのパーソナライズされた楽曲のおすすめ、Googleによるパーソナライズド広告などが例として挙げられます。美容業界では、透過的カスタマイゼーションを製品に適用することで成功した事例があるロレアル社もその1つです。美容製品メーカーである同社は、顧客が自身の美容習慣やスキンケアの目標を詳細に説明できるアプリケーションを立ち上げました。このアプリのデータを活用し、同社は自社製品を使用する個人や美容サロンに向けて、数量やパッケージが異なるカスタマイズされたスキンケア製品を提供しています。この場合、顧客の行動パターンに関する事前データにより、マスカスタマイゼーションが可能となります。また、顧客は、新たなリクエストをすることなく、自分のスキンケア習慣や居場所に合わせてリニューアルされた製品を受け取ることで、透過的カスタマイゼーションの恩恵を受けることができます。
概観として、以下の図は、カスタマイゼーションの4つのアプローチと、各アプローチが企業の標準製品に与える影響を示しています。
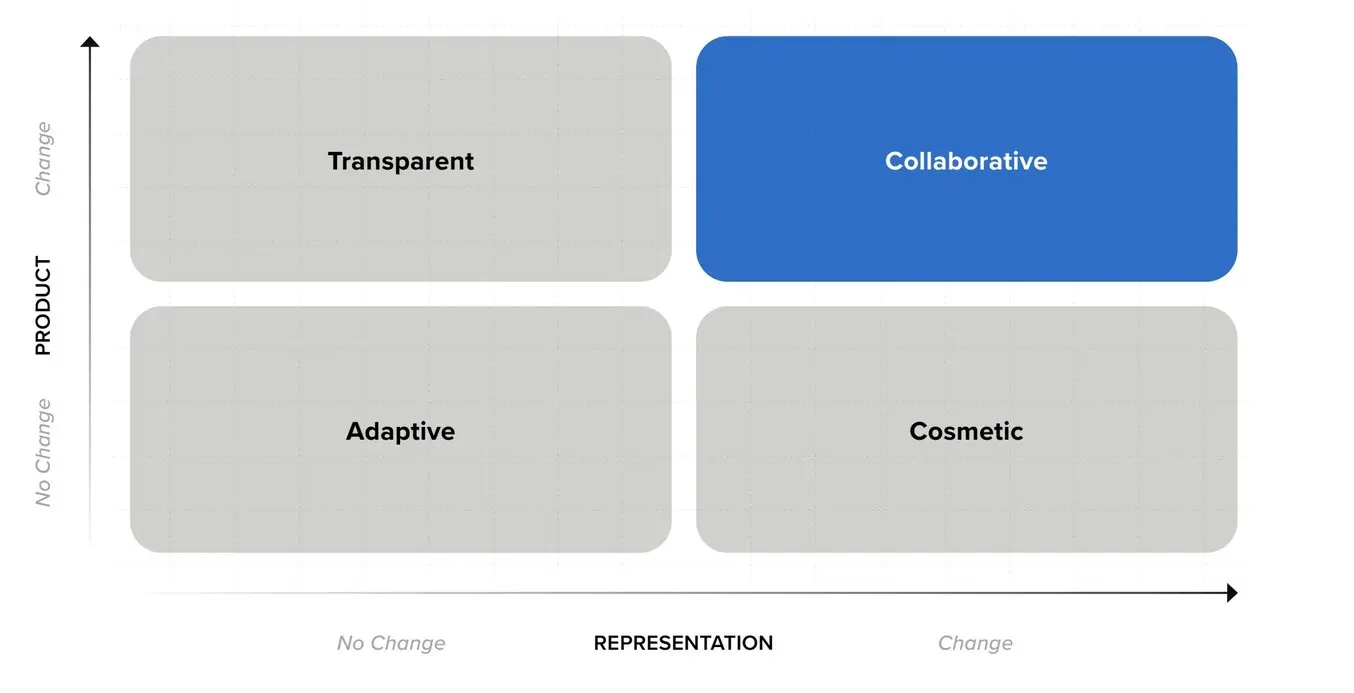
マスカスタマイゼーションとマスパーソナライゼーションの比較
マスカスタマイゼーション、特にコラボレーティブカスタマイゼーション(または共創)では、あらかじめ設定された構成から選ぶことで、顧客が自らの手で製品に変更を加え、自分のニーズや要件に合うようにします。カスタマイゼーションは塗装仕上げやカスタマイズされた生地により実現されますが、ユーザー独自の物理的形状を提供するものはほとんどありません。今日、本当にパーソナライズされた商品のほとんどは、高級品か医療機器であり、いずれも非常に高価なものです。
マスパーソナライゼーションとは、顧客データをもとに、製品の作成・変更を行い、完全にオリジナルな製品を作ることです。これまで、こうした物理的製品を作るための優れた製造手段はありませんでしたが、3Dプリントなどの高度な製造プロセスにより、カスタマイゼーションの提供方法に変革がもたらされており、真にパーソナライズされた商品を大規模に製造することが可能となりつつあります。
マスカスタマイゼーションの技術
マスカスタマイゼーションが大量生産とカスタム製造の隙間を埋める方法は、革新的な最新技術を用いてデータの収集、設計の作成、パーツの製造、製品の組立を行うことです。以下に、マスカスタマイゼーションを実現する最も一般的な技術と、その実例をご紹介します。
製品コンフィギュレーター
オンライン、アプリ、またはソフトウェアベースのコンフィギュレーターにより、コア製品の機能追加や変更、デザインや見た目の変更、カスタムデザインや機能を一から作成することができます。こうしたコンフィギュレーターは特に一般的な共創ツールであり、マーケティング目的や、顧客の好みを直接把握し、カスタマイズされた製品を生み出すための貴重なツールとなっています。
製品コンフィギュレーターの例としては、車種ごとに色やリム、内装を変えて視覚化できる自動車コンフィギュレーターや、フレームやレンズを仮想的に試着できるサングラスコンフィギュレーターなどが挙げられます。最近では、拡張現実を利用して、よりリアルな体験を提供する新しいコンフィギュレーターも登場しています。
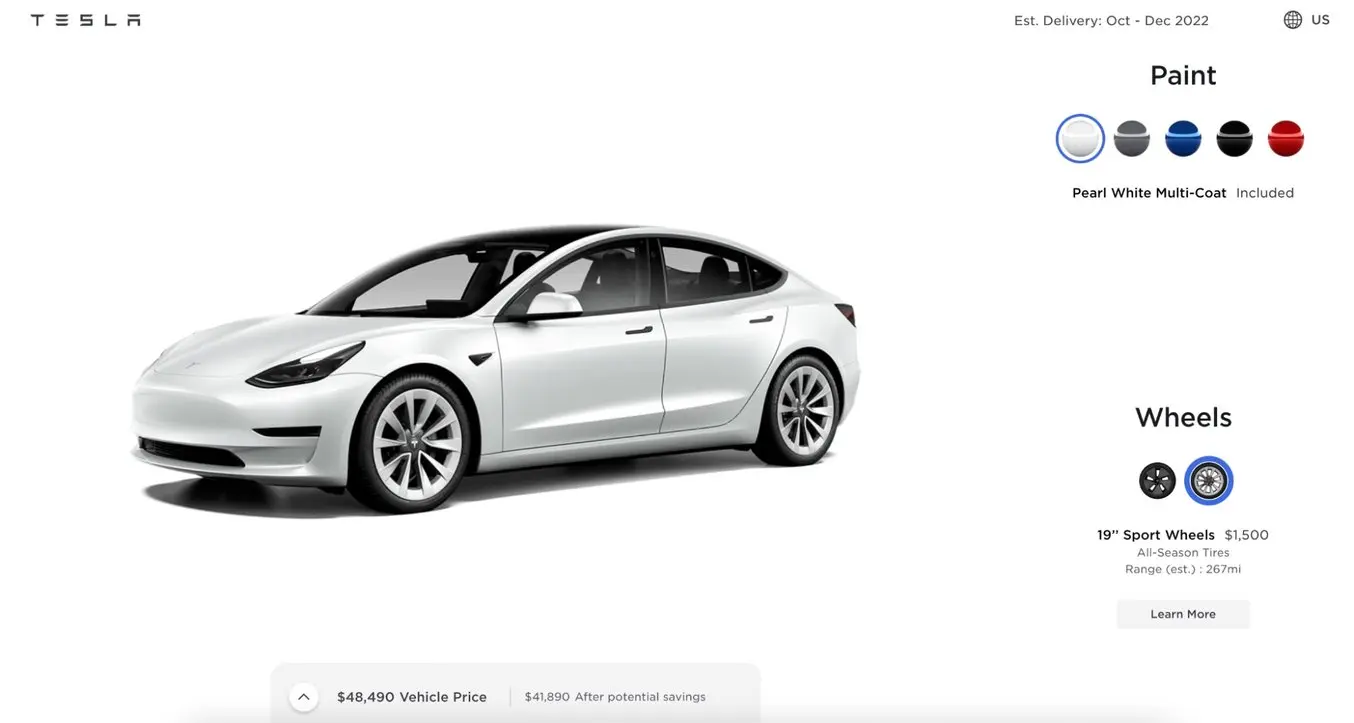
テスラ・モーターズの製品コンフィギュレーターでは、ショールームに足を運ぶことなく、オンラインで直接車をカスタマイズ・注文できます。
CAD設計
CAD(コンピューター支援設計)とは、2D図面や3Dモデルをデジタルで作成する手法で、幅広い産業分野で手作業による製図に代わって利用されています。今日、私たちを取り巻く製品の大半は、すでにCAD設計によって作られており、マスカスタマイゼーションを実現するための専用統合ツールも急速に登場しています。
従来のCADソフトは十徳ナイフとデジタル製図板を組み合わせたようなもので、設計者があらゆるものを作れるように幅広いツールを提供しています。しかし、そうしたツールは習得が難しく、設計者の数も限られています。そのため、マスカスタマイゼーション用のCADツールは特定のワークフローに合わせることで、デジタル設計の複雑さを低減し、訓練を受けた担当者や顧客が直感的に設計を作成・変更できるようになっていることが多くあります。
たとえば、患者の口腔内スキャンデータをもとに、アライナー矯正、入れ歯、かぶせ物など、歯科器具の設計に特化したCADソフトウェアツールも登場しています。医療用CADツールは医療従事者が解剖学的モデル、人工装具、サージカルガイドを設計するためのツールです。ジュエリーCADツールでは、ジュエリーデザイナーがコンピューター上で新しいカスタムデザインを作成でき、従来のワックスパターンを手で彫るよりもはるかに簡単に規模を拡大できます。
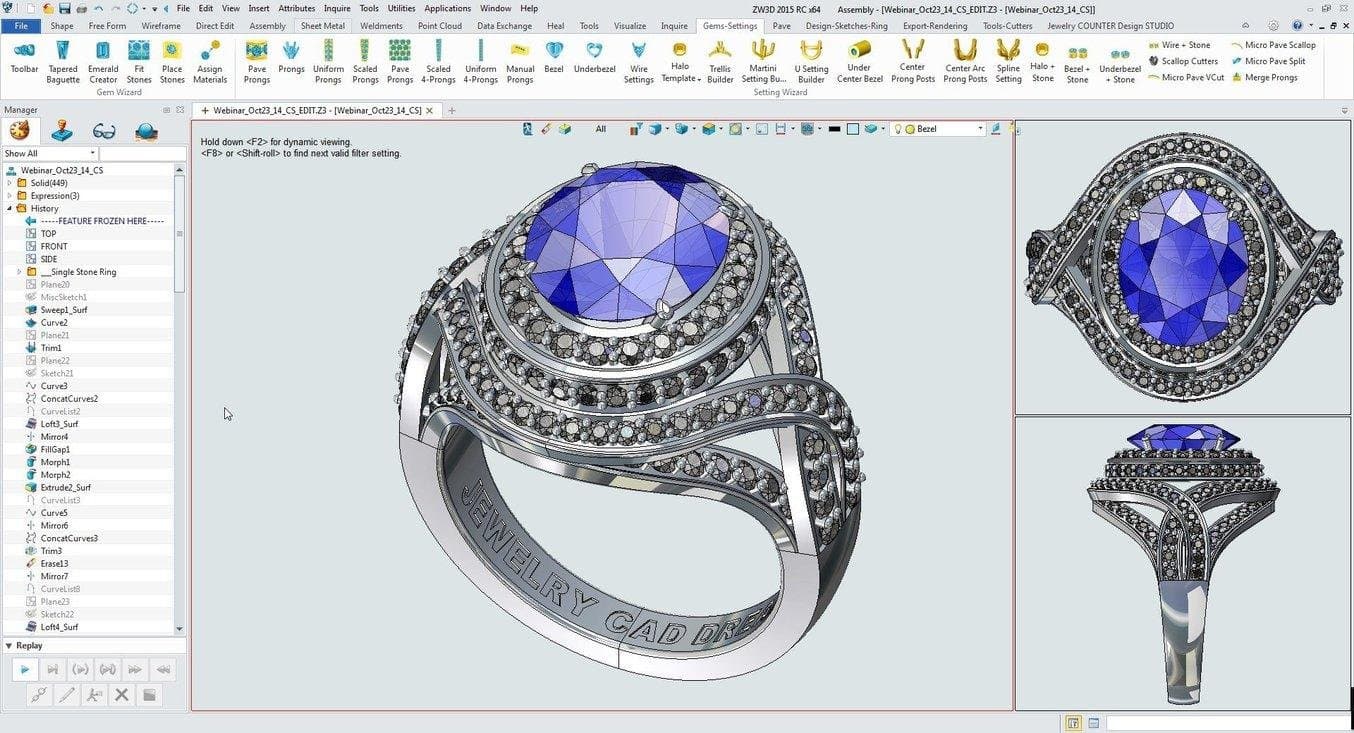
パソコン上でジュエリーをカスタマイズするのは、新しいワックスデザインを手で彫るよりもはるかに簡単です。
3Dスキャン
3Dスキャンとは、現実の物体や環境を分析し、その形状や外観に関するデータを収集するプロセスのことです。収集したデータはその後、デジタル3Dモデルの構築に使用されます。
3Dスキャナとその使用は昨今急速に増加しており、マスカスタマイゼーションに必要なデータを取得するための重要なツールとなっています。多くの場合、マスパーソナライゼーションにも欠かせない存在となっており、人体の正確な形状を参照し、カスタムフィットの製品や装具を作成するために用いられています。用途によっては専用の3Dスキャナが必要となりますが、スマートフォンによるスキャン(写真測量とLiDAR)が急速に発展したため、すでに数十億人のユーザーのポケットにスキャナがあり、マスカスタマイゼーションのインプットとして使用できるデータを収集できるようになっています。
たとえば、3Dスキャナは、カスタマイズされたメガネを作るために顧客の顔をスキャンしたり、カスタムフィットのイヤホンを作るために外耳道をスキャンしたり、さまざまな歯科装具を作るために歯をスキャンしたりするといったことができます。
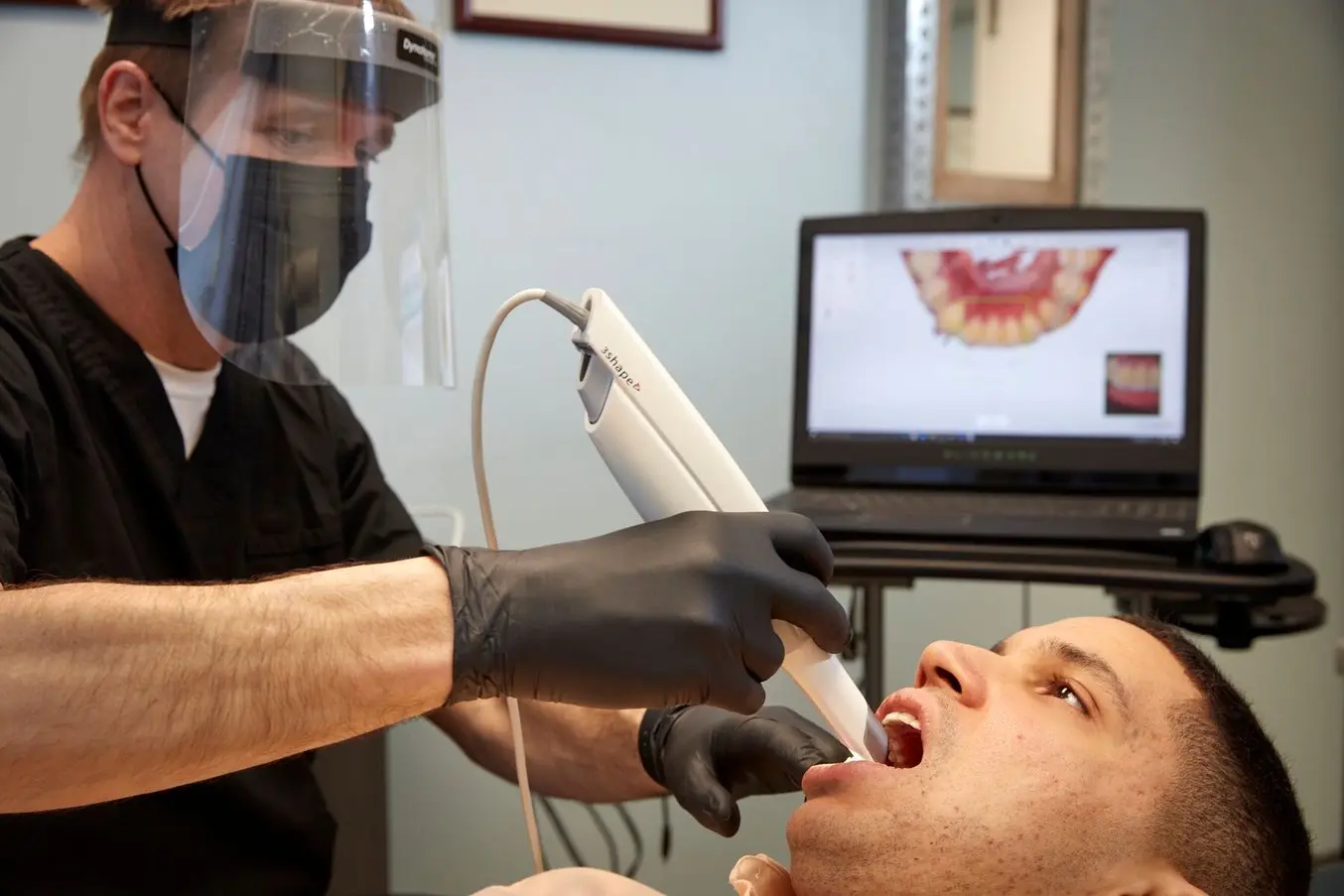
歯科用口腔内スキャナは、歯科治療においてますます一般的に用いられるようになっており、従来の不便な型取りに取って代わっています。スキャナで収集できるデジタルデータは、歯科装具の設計に利用できます。
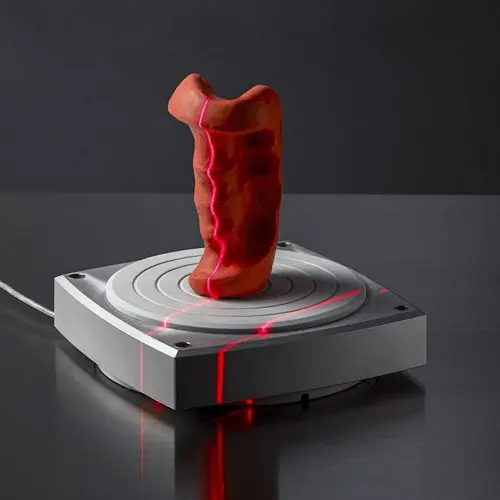
リバースエンジニアリングとその他の用途のための3Dスキャンならびに3Dプリント
3Dスキャンと3Dプリントのワークフローは、複製や修復、リバースエンジニアリング、計測などに応用できます。ホワイトペーパーをダウンロードして、これらの活用法を探り、どのように使用開始できるかを学びましょう。
3Dプリント
3Dプリントまたはアディティブマニュファクチャリング(AM)技術は、物理的部品が完成するまで、材料を次々重ねていき、コンピューター支援設計(CAD)モデルから3D部品を作成する技術です。
3Dプリント技術は1980年代から存在していましたが、近年の機械設備、材料、そしてソフトウェアの進歩により、3Dプリントはより多くの企業が利用できるものとなったほか、最終用途の部品製造をはじめ、幅広い用途が実現しました。
3Dプリントはツーリングを必要としないため、デジタル設計を変更するだけで、ツーリングに追加コストをかけることなく顧客に合わせた製品を作ることができます。また、3Dプリントでは実質的に設計上の制約が存在しません。これは、オーバーハング、マイクロチャネル、有機的な形状など、従来の製造手法では莫大なコストがかかったり、実現すら不可能だった複雑な形状や部品を製造できるためです。
アディティブマニュファクチャリングは、マスカスタマイゼーションのために特に広く使われている生産技術で、医療、歯科、聴覚機器のソリューション提供、消費財の製造などさまざまな用途に用いられています。
ハズブロ社のSelfie Seriesは、アクションフィギュアのパーソナライゼーションを同社の顧客基盤に大規模に投入する製品群です。ユーザーはスマートフォンで自分の顔をスキャンし、髪型を選んで、カスタマイズされたアクションフィギュアを作ることができます。カスタマイズされた頭部は、従来の設備で作られた標準的・市販のアクションフィギュアのボディーと組み合わされることで、手頃な価格に抑えられ、カスタマイズされたアクションフィギュアとなってユーザーに届けられます。
ジレット社はユーザーにダイレクトに届くカスタマイゼーションワークフロー、Razor Makerのコンセプトを打ち出しました。ユーザーは、オンラインのコンフィギュレーターを使って、カミソリの持ち手のデザインと色を幅広い選択肢から選び、そのデザインに自分の名前を入れることができます。持ち手は3Dプリントで製造され、標準的なカミソリ部品とともに組み立てられます。
最終用途の部品を直接製造するだけでなく、3Dプリントはラピッドツーリングや製造補助具の生産にも利用できます。これらはいずれも、マスカスタマイズ生産を支えるものです。
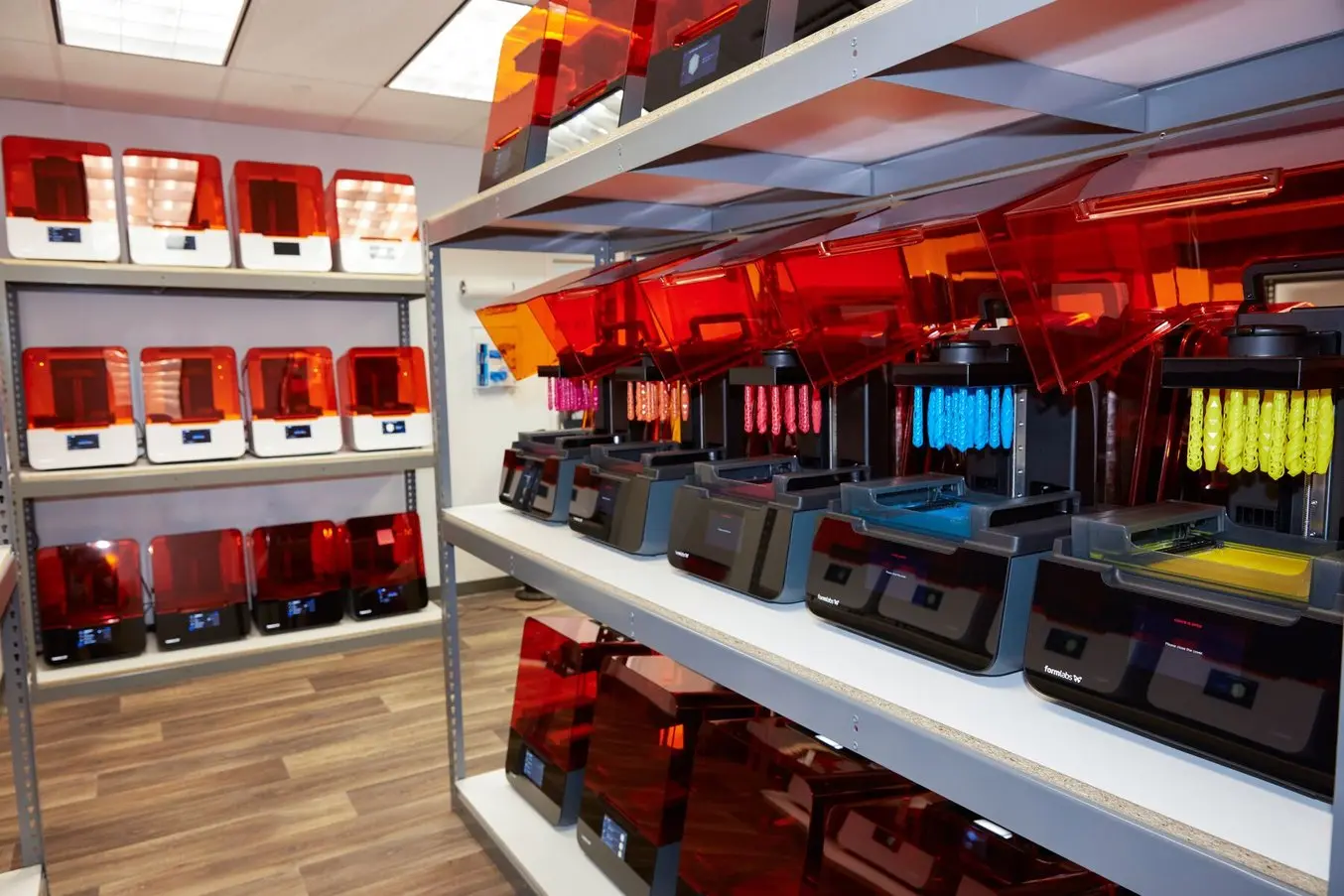
3Dプリンタで製造された最終用途の部品でカスタム品や小ロット品の生産を実現する
3Dプリンタで製造された最終用途の部品でカスタム品や小ロット品の生産を高速・安価で実現するためには、こちらのウェビナーをご覧ください。
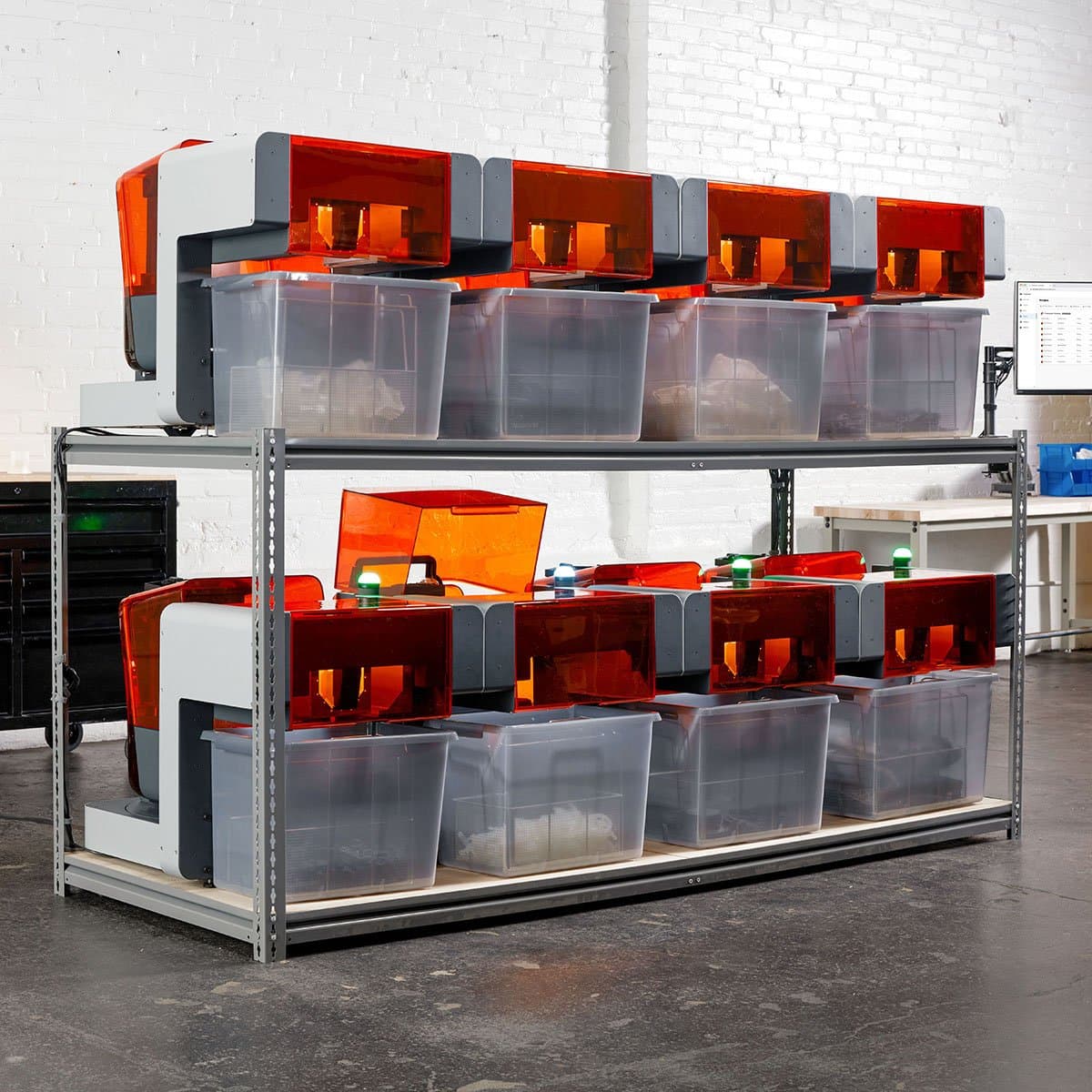
Formlabsの完全に自動化された3Dプリンタの導入により、「いつでも」「どこでも」操作可能となり、生産性をかつてないレベルに導きます。
Formlabsのオートメーションエコシステムにより、24時間365日、生産可能に
詳細はこちらラピッドツーリング
ラピッドツーリングとは、射出成形、熱成形、圧縮成形など従来型の製造法において、ツーリングを安価で高速に、そして効率的に製造することで、タイトなスケジュールや少量生産で部品を作るための技術の総称です。
従来のツーリングは、その大半が耐久性の高い金属を使用して、機械加工や鋳造等で行われています。しかし、こうした手法は規模の大きな量産プロジェクトには向いているものの、多品種小ロットやカスタム品の生産には最適とは言えません。ラピッドツーリングは、従来のツーリングでは高額なコストを要するカスタム品や小ロット品の生産をも、現場が慣れ親しんだ従来の製造プロセスに則りながら高速・安価に実現できます。これにより、メーカーは新製品の市場テストや、より幅広い製品群の提供、あるいはお客様のニーズに対応する製品カスタマイズ等が無理なく行えます。
ラピッドツーリングで最も広く活用されている製作方法は、3Dプリントと機械加工です。このうち3Dプリントがマスカスタマイゼーションに最も適しています。
実例として、患者の口腔内スキャンにもとづいて設計された3Dプリントモデルに対して真空成形を行う方法が、矯正歯科のクリアアライナー製作で一般的に採用されています。
また、ジュエラーもCAD設計を用いて原型を製作しており、それを直接鋳造することでカスタマイズされた宝石が作られています。従来、インベストメント鋳造のパターン(原型)はワンオフ品や少量だけを作る場合は、手彫りか機械加工で作られていました。しかし、3Dプリントを用いればジュエラーが原型を直接製作できるため、他のプロセスでよくあるデザインや時間の制約を受けることはありません。
インイヤーモニターや補聴器、騒音防止具などのカスタムフィットのイヤーデバイスは、従来は手間とコストがかかり、ごく一部のユーザーしか手に入れることができませんでした。現在では、3Dスキャンを使用して人の耳をスキャンし、シリコン製のイヤーチップを鋳造するための型を3Dプリントできるため、聴覚の専門家が手頃な価格でカスタムフィットの機器を大規模に製造できるようになりました。
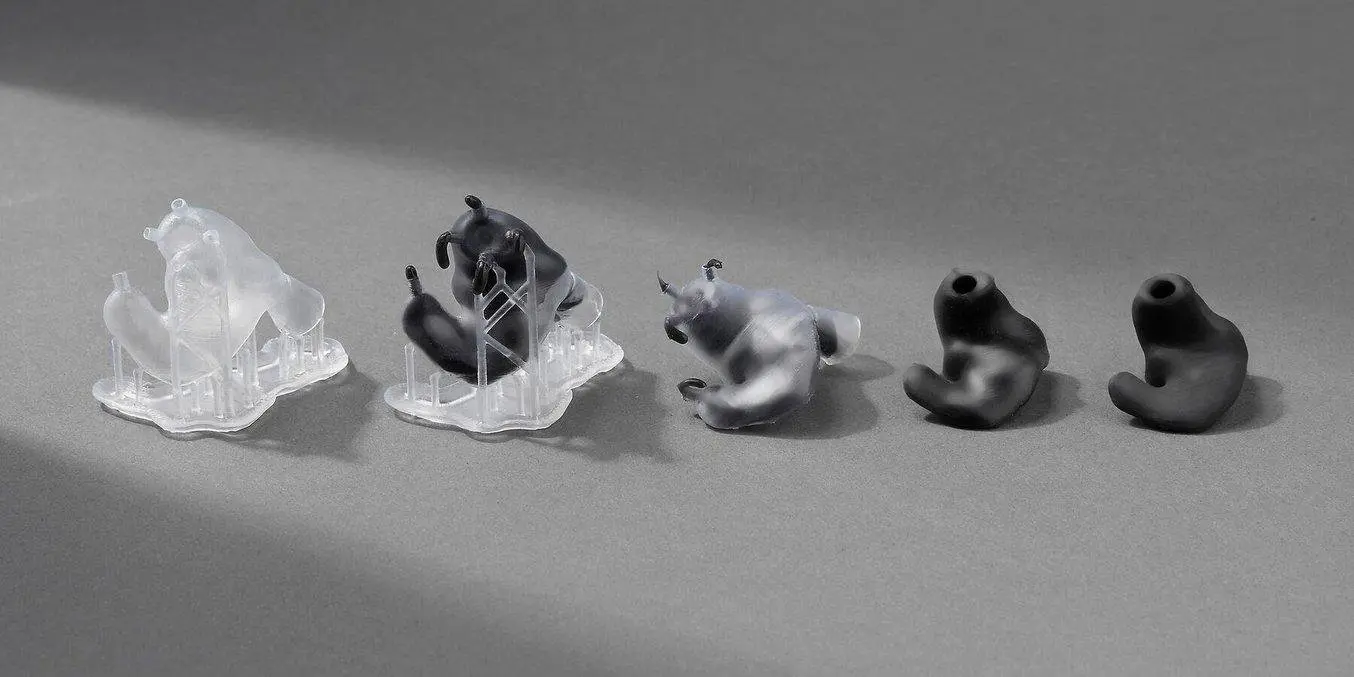
シリコン製の耳型を3Dプリントで作り、カスタムフィットのイヤーデバイスを製造できます。
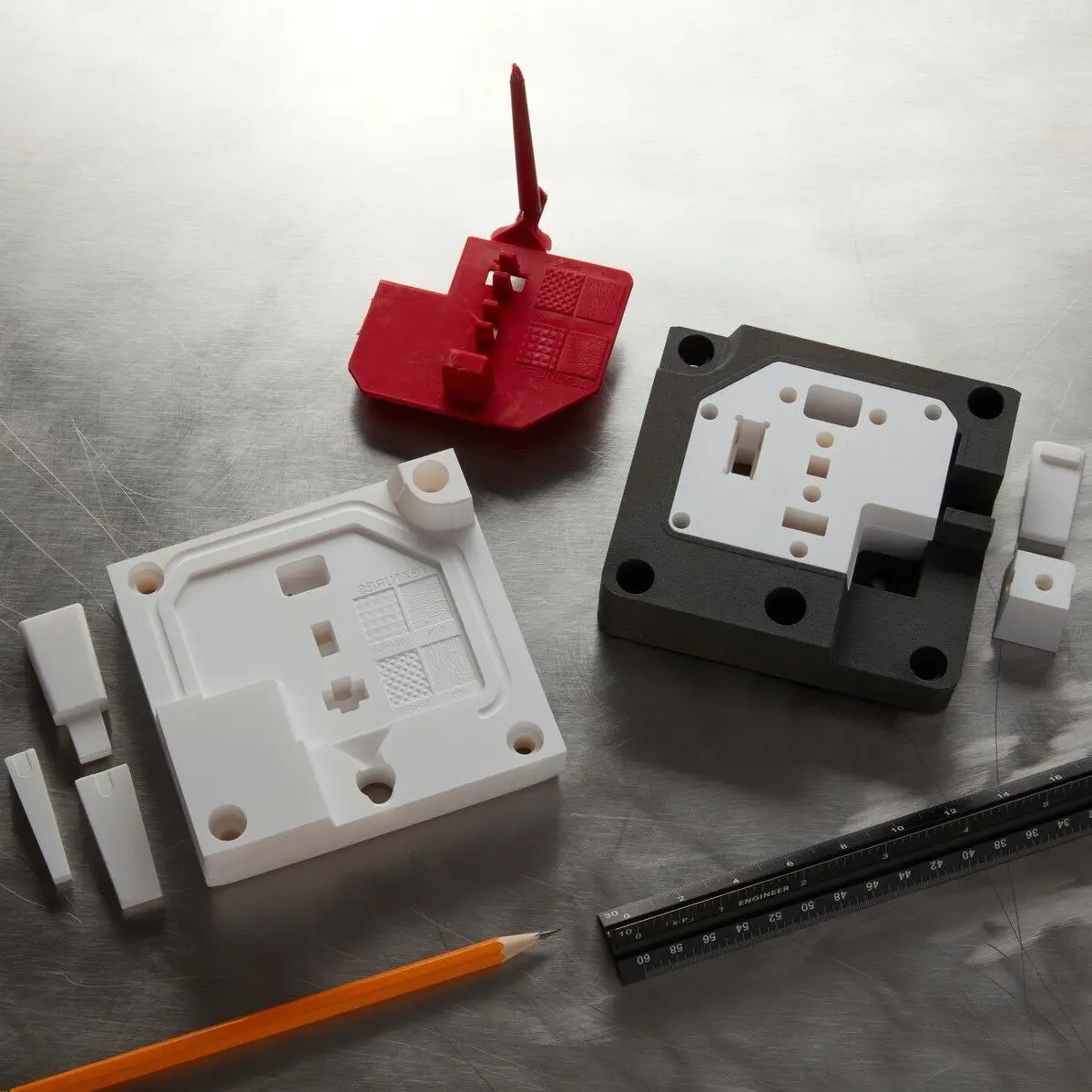
ロボティクスとオートメーション
ロボティクスとオートメーションは、第三次産業革命の際だった特徴です。次世代ロボットは、自動車産業などの従来の中心産業をはるかに超えた用途で実用化されており、多くのマスカスタマイゼーションワークフローで重要な役割を担っています。
コンピュータービジョン、センサー技術、組み込みプロセッサー、人工知能の発展により、ロボットは、不規則な物体の保持、入り組んだ生産環境のナビゲーション、人間の作業者との対話において進化を遂げています。
従来の産業用ロボットは、ケージ、バリア、安全囲いなどにより工場内で隔離され、人間と接触しないようにプログラムされていました。しかし、コラボレーティブロボットにより、自動化された工場のあり方が変わり、ロボットと人間とのさらなる相乗効果が生まれることが期待されています。
あらゆるレベルのロボットが簡単にプログラムできるようになりつつあり、企業は必ずしも高価なインテグレーターに頼る必要がなくなっています。そのため、小規模なメーカーや、カスタム化に欠かせない柔軟な生産環境を必要とするメーカーにも、産業オートメーションがアクセスしやすくなっています。
また、ロボット、センサー、組立ステーションなどの工場のコネクテッドアセットは、データプラットフォームを通じて統合され、日々のオペレーションだけでなく、発案、設計、エンジニアリングから流通、販売、サービスに至るまで、製品ライフサイクルのあらゆるステージで情報で提供できるようになりました。これはマスカスタマイゼーションにとって欠かせません。部品がすべて異なる場合、ジョブや部品の追跡が複雑になり、エラーが発生しやすくなるためです。
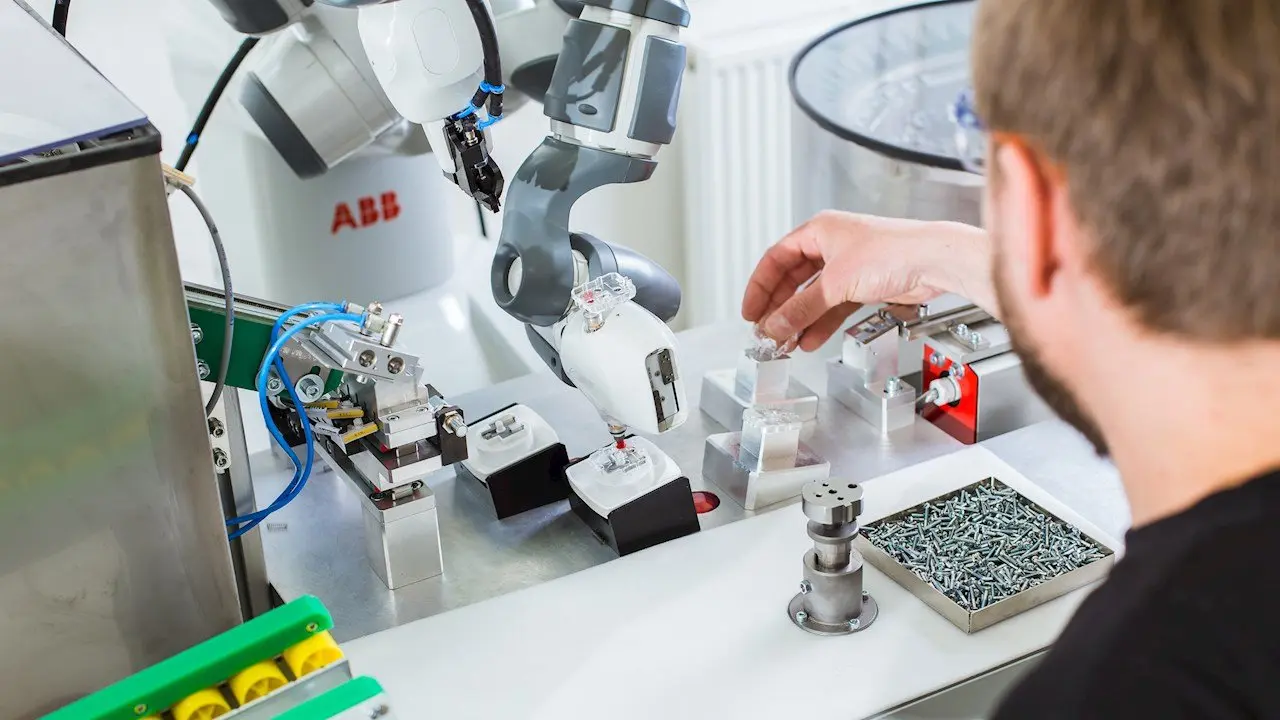
コラボレーティブロボットは人間のそばで働くことができ、マスカスタマイゼーションなどの柔軟な生産環境におけるプログラムがより簡単です。
マスカスタマイゼーションのワークフロー
すでに見た例のように、マスカスタマイゼーションのワークフローは、革新的な技術を組み合わせたり、従来のツールやプロセスと組み合わせることで、非常に多様なものとなっています。
以下に、最も一般的なステップのおおまかな概要をご紹介します。
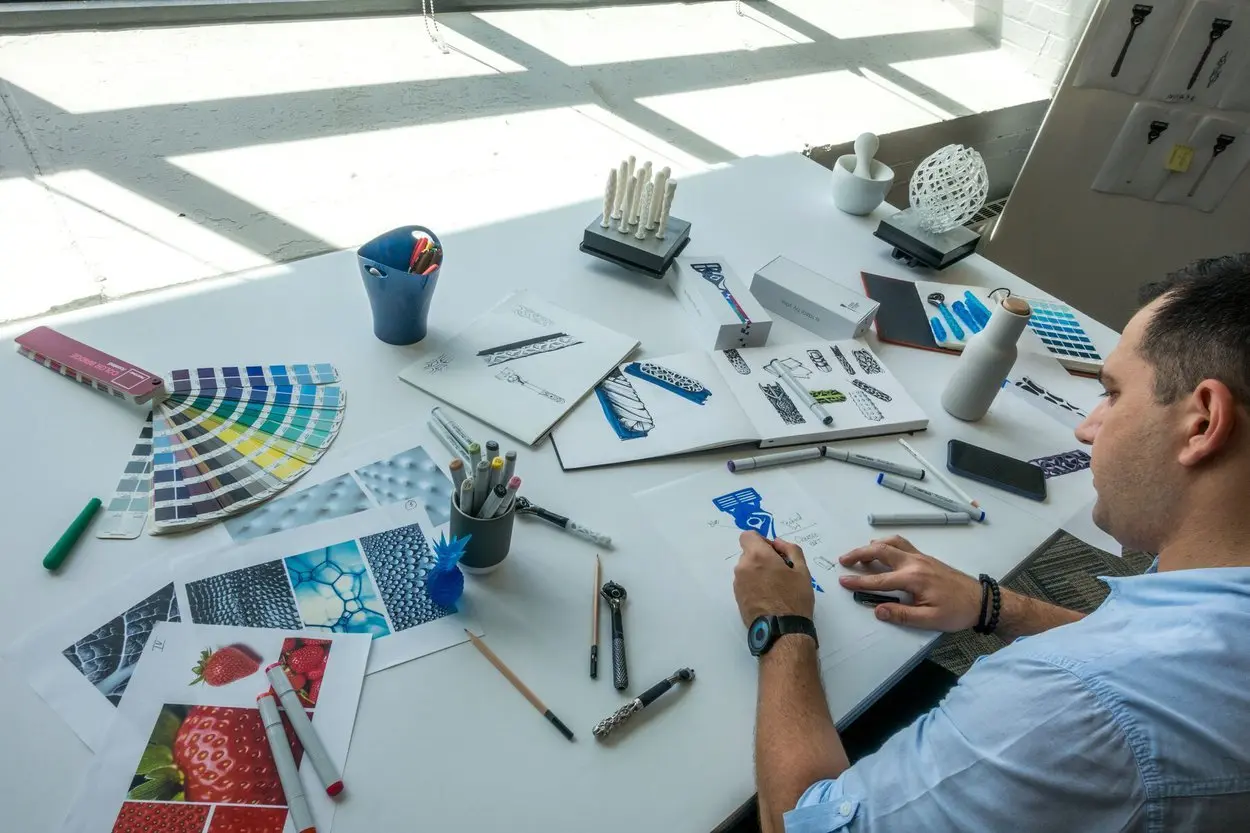
1. 設計
顧客への構成オプションの提供、CADによるカスタマイズ可能な設計の作成、または既存モデルの3Dスキャン、MRIスキャン、もしくは口腔内スキャンによるカスタムフィット設計の作成。
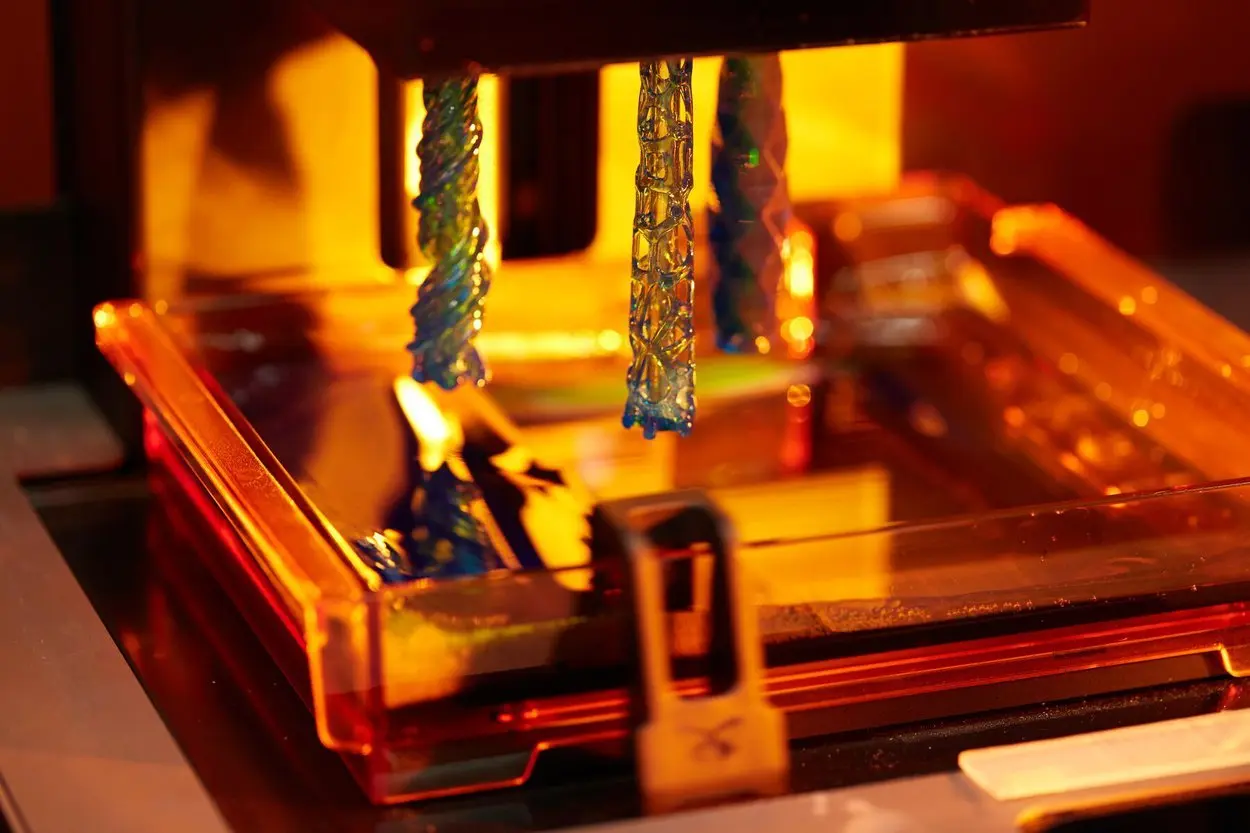
2. 製造
最終部品を3Dプリントで直接製造するか、3Dプリントされたラピッドツーリングを従来の製造方法で利用します。後処理と表面処理により、パーソナライズのオプションを追加し、より長寿命の製品を実現できます。
従来的なプロセスにおける設計上の制約はありません。カスタム部品や複雑な設計も、3Dプリントなら高いコスト効率で製造できます。
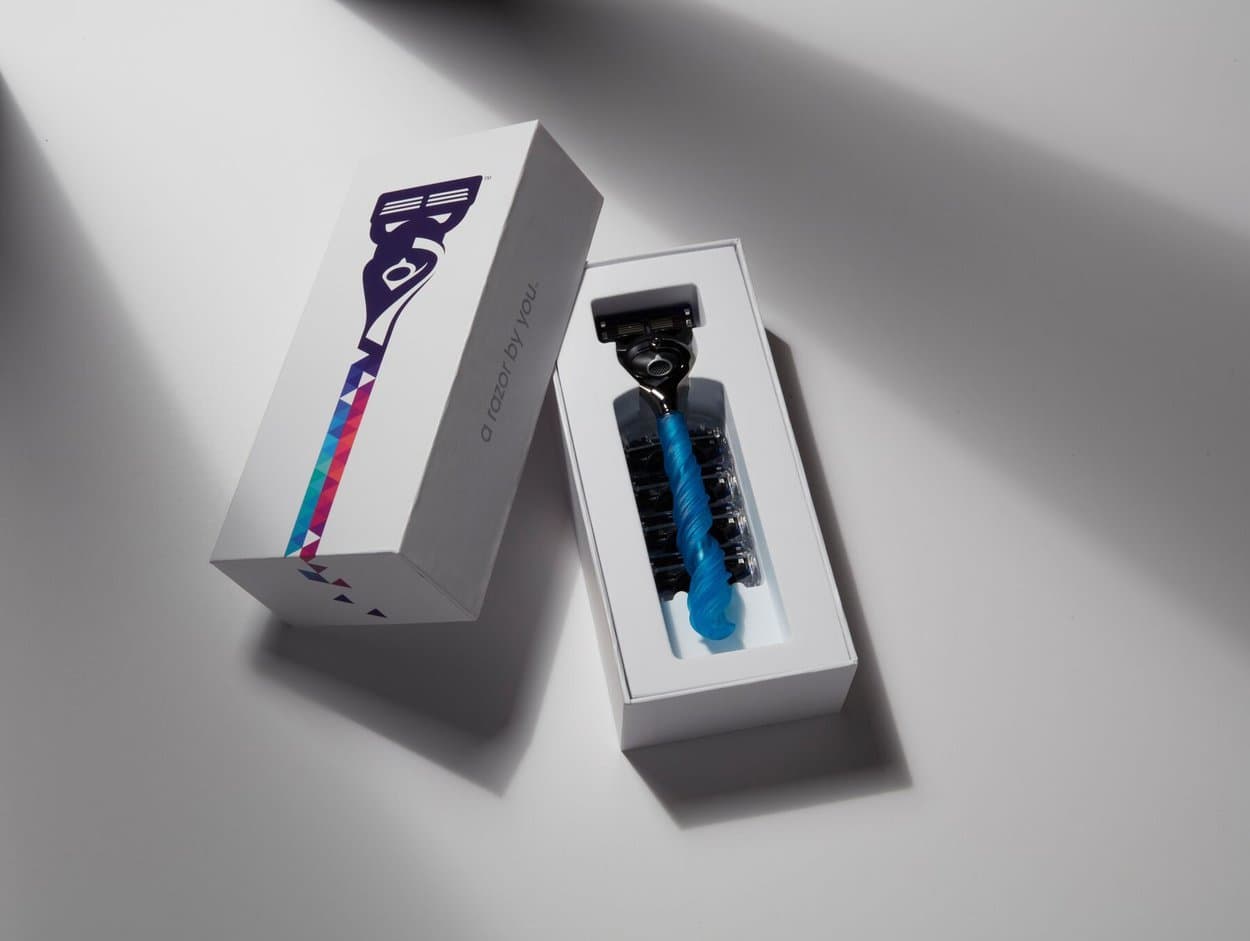
3. 組立
カスタマイズされたパーツは、従来の機械で製造されたパーツと同じように、生産工程で部品もしくは組み立て用パーツとして、または個々の製品として使用できます。
カスタムパーツを市販の部品と組み合わせることでコストを抑え、ロボティクスとオートメーションツールを活用して生産効率を高められます。
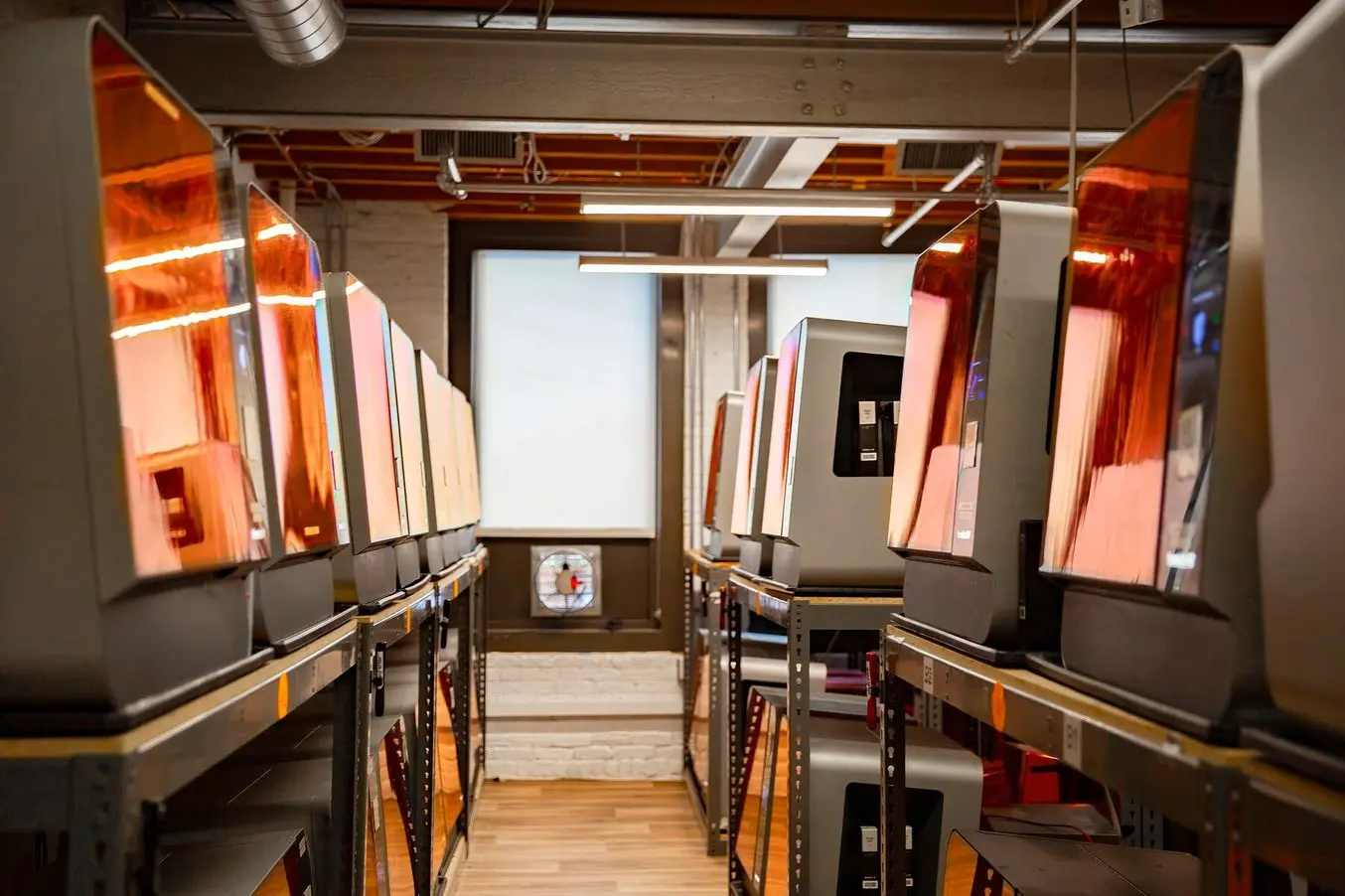
4. スケールアップと機動力
需要に応じて過剰な設備コストをかけることなくスケールアップし、オペレーションを多様化、コストのかかるツーリング変更に投資することなく、競合他社よりも迅速に市場や顧客に対応できます。
カスタマイゼーションと顧客ダイレクトの新しいビジネスモデルを活用することで、利益率を高め、顧客との関係をさらに強めます。
マスカスタマイゼーションを始める
カスタマイズされた製品やサービスの市場は、継続的に拡大しています。新しいビジネスモデルを把握・取り入れる企業は成功を収め、そうでない企業は取り残されるリスクがあります。
事業にマスカスタマイゼーションを活用するアイデアをお持ちでも、何から始めればいいのかお悩みですか? Formlabsのソリューションスペシャリストにお問い合わせのうえ、マスカスタマイゼーションへのスムーズな移行を保証する、理想的なワークフローを構築する方法についてご相談ください。