MOSOLF Special Vehicles GmbHは、ドイツのキッペンハイムを拠点とする世界をリードする特殊車両メーカーです。約50人の従業員を擁する当社は、年間1000台もの特殊車両や緊急車両を製造しています。ドイツの州立および連邦警察、防衛セクター、災害対策、技術支援機関、地方自治体、産業界などを中心としたMOSOLFの顧客は、いずれも高度なカスタマイゼーションを実装した高性能車両を必要としています。
自動車業界では、ほとんどの部品が射出成形などの量産プロセスで製造されています。これは標準化された部品を何十万ユニットも繰り返し生産する場合にはコスト効率の高い方法ですが、MOSOLFの顧客のように多様なカスタマイゼーションと少量生産が必要となる場合には、金型製作のコストがかさみ現実的ではありません。このような状況にあるMOSOLFにとって、3Dプリントが最適なソリューションとなりました。
「[ドイツでは]警察車両の3台に1台がアディティブマニュファクチャリングで製造した部品を搭載していると思います。MOSOLFは3Dプリントを非常に高度に活用していて、ここで生産される車両は1台としてアディティブマニュファクチャリング製の部品を搭載していないものはありません。今では年間5000点もの部品を3Dプリントで製作していますが、その数は上昇傾向にあります。つまり、車両1台につき少なくとも3つの部品は3Dプリント製ということになります」
MOSOLF Special Vehicles GmbH Head of Project Planning、Carsten Busam氏
MOSOLFは、SLS(粉末焼結積層造形)方式3DプリンタのFuseシリーズを活用し、警察車両やその他特殊・緊急車両に搭載する様々な実製品用部品を製造しています。
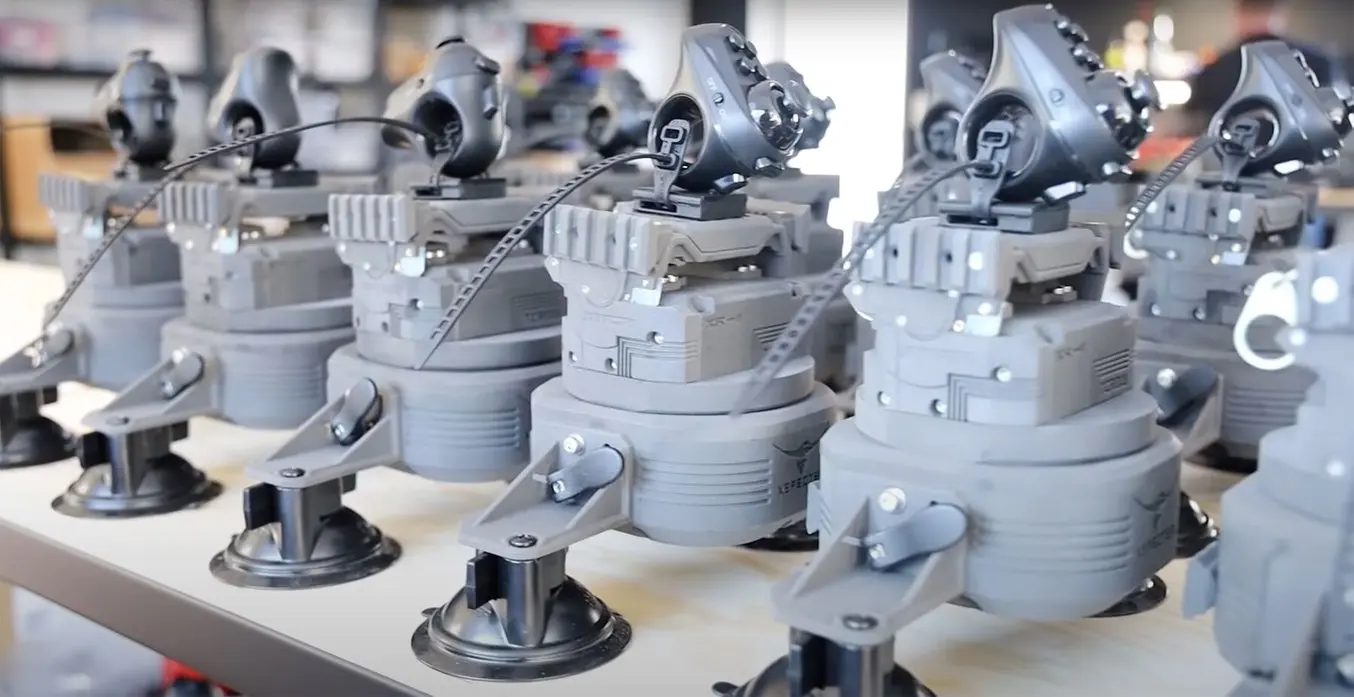
SLSを実製品の量産に活用
単に実製品の量産工程に3Dプリントの導入が可能なだけでなく、SLS Fuseシリーズを活用することでさらに安価かつ迅速に、規模の拡大にも柔軟に対応できるようになります。量産方法の比較、パウダーのボリュームディスカウントの詳細、現在Fuseシリーズを実際に量産工程に取り入れているメーカー15社の事例をご覧ください。
ドイツの17警察のニーズを満たすカスタム製品を提供
「最大の課題はバリエーションの多さです」とBusam氏が言うように、一言で「警察」といっても州や所轄によって所有する車両は数種類にも及ぶうえ、用途に応じて車両単位でもそれぞれ異なるカスタム機能が必要になります。搭載部品も多岐に渡り、警察署によって使用している無線システムや信号システムのメーカーが異なります。つまり、車両ごとに大量のカスタム部品が必要になるのです。
「ドイツの17の警察向けに車両を製造していますが、それぞれ楽な姿勢や操作方法の好みが異なります。そのため、共通の基本設計的な部品であれば生産量は比較的多くなるのですが、カスタマイゼーションが加わるとその数は一気に少なくなります」とBusam氏は言います。
MOSOLFではシリーズ車両も扱っており、商用に出回っている車両やトラック、バンを特殊仕様に合わせて改善します。この場合、顧客から依頼のあった機能を搭載するための場所を見つけなくてはならず、さらにそれが姿勢に無理がなく、耐久性があり、見た目にも影響を与えない場所でなくてはなりません。旧型の車両の場合は、比較的簡単にこの搭載場所が見つかります。ダッシュボードやコンソールに空きスペースが多く、MOSOLFはそこを活用して追加機能を搭載できるためです。しかし、新しいモデルの車両ではこれが難しくなります。
「新しい車両はどこもディスプレイで埋め尽くされていて、余分なスペースがほとんどありません。ちょっとした収納や携帯を充電するためのスペースはあるのですが、すべての機能を搭載するのに十分な場所を見つけるのは難しいですね。特に覆面車両の場合、見た目から警察車両だということがわからないようにしなければなりませんから」と、Busam氏はその難しさを語ります。
MOSOLFが3Dプリントを活用し始めたのは2016年、バイエルン警察から、所有している車両とバイク全台に新しいデジタルラジオを搭載して欲しいという注文を受けた時でした。
「各車両やバイクごとに異なるソリューションが必要でした。もしすべての部品を板金加工で作っていたら、製造に非常に時間がかかってしまいますし、見た目もあまり綺麗にならないかもしれません。そこで、初めて3Dプリントの世界に足を踏み入れることにしたんです」
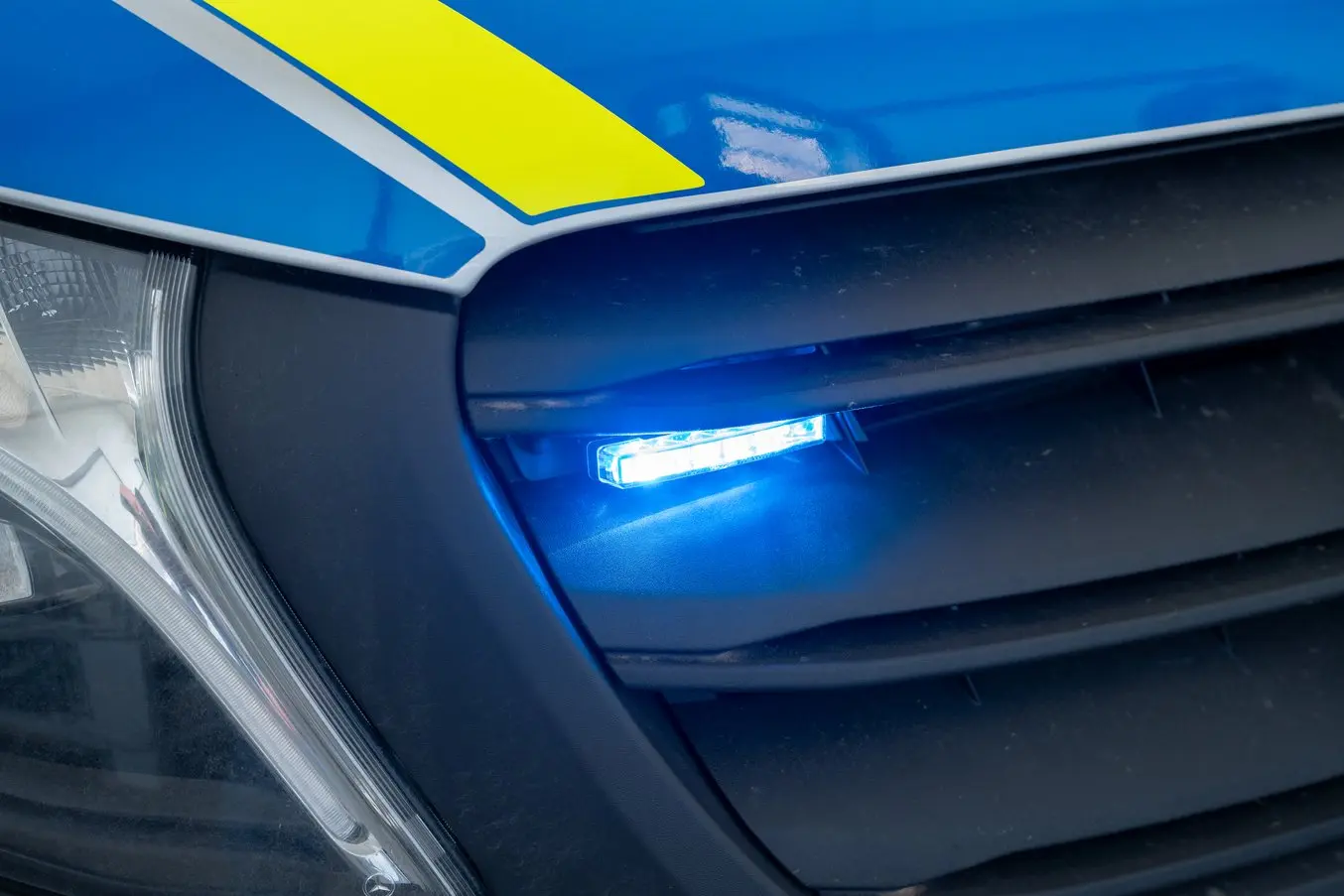
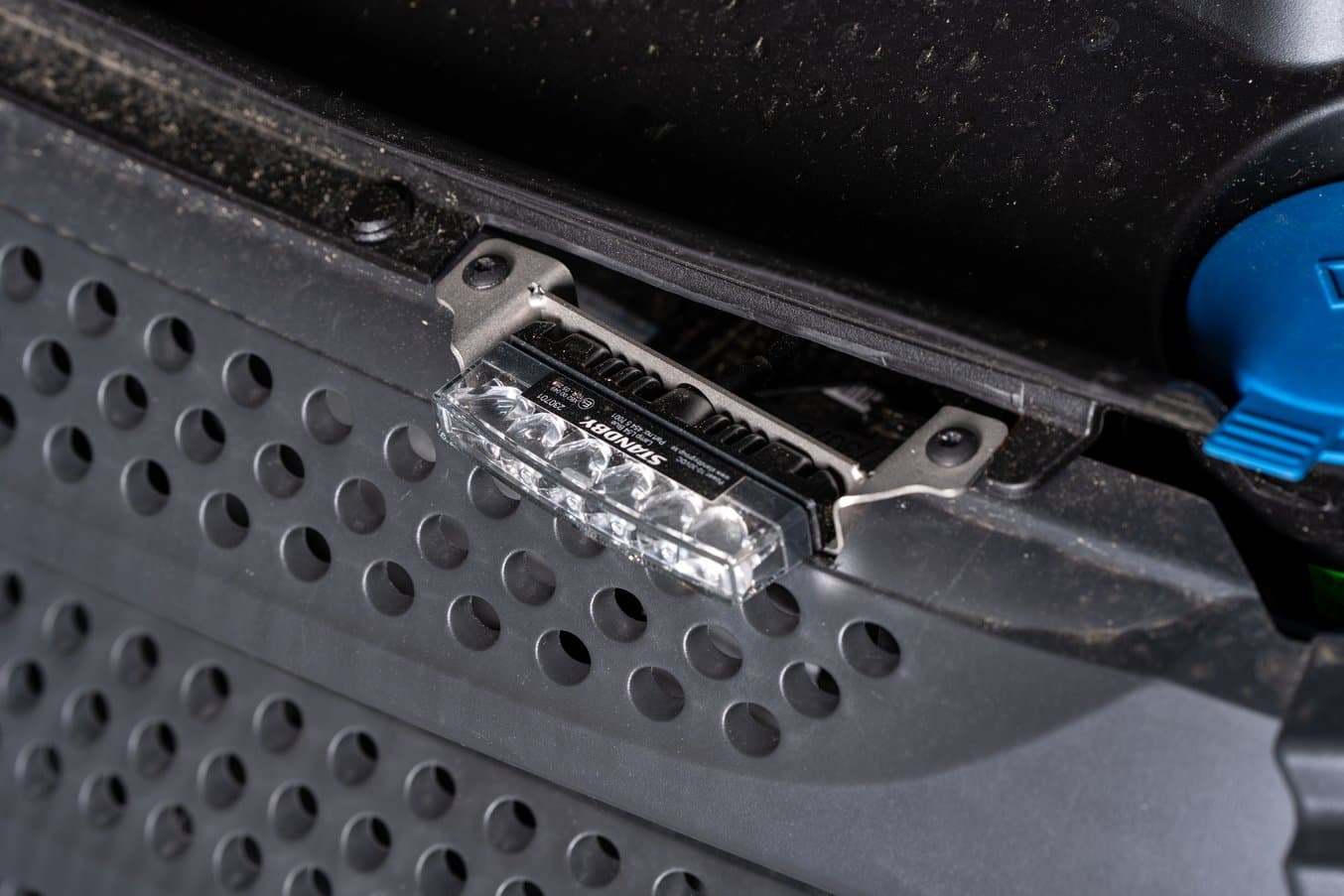
警察車両のフロントに搭載するLEDライト用のカスタムマウント。これまではこういった部品を板金加工で製造していた。
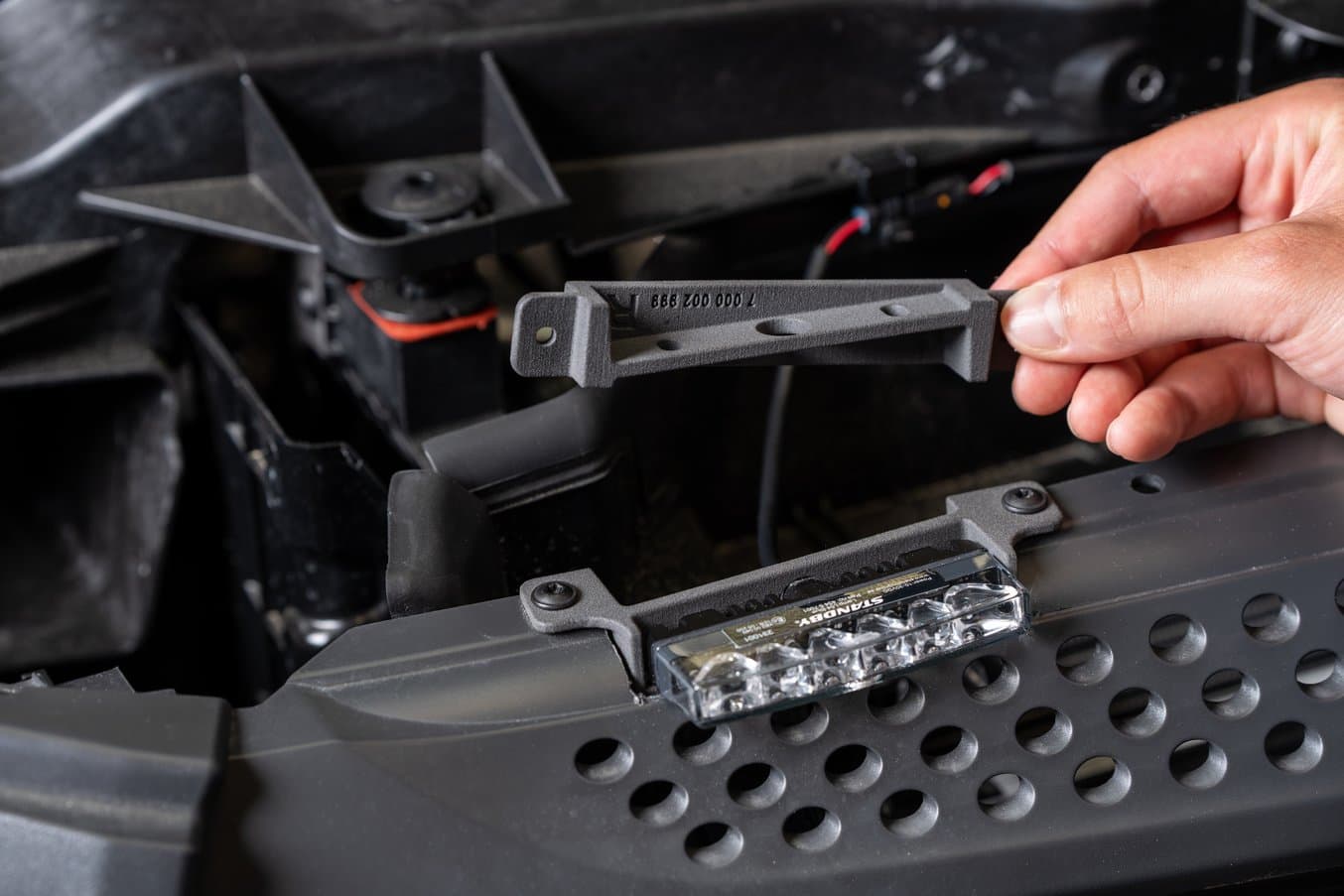
SLS 3Dプリントにより、これまでより格段に早く、簡単に、そしてコスト効率よく製造ができるように。
同社が最初に導入したのは、当時最もアクセスしやすく彼らのニーズにも合っていたFDM(熱溶解積層)方式の3Dプリントでしたが、すぐに限界を感じるようになりました。FDMでは注文数に対応できるだけの製造規模にスケールアップすることが難しく、造形品自体も工業品質とは言い難いものでした。
次に導入するとすればSLS 3Dプリントが最も理にかなったオプションでしたが、当時のSLSは最低でも€200,000と、スモールビジネスには手の届かない価格帯でした。そんな状況が、FormlabsのFuseシリーズの登場で一変します。
「SLS 3Dプリントは造形品質や精度が非常に高く、材料の性能も申し分ありません。多数の部品を一度に生産できるという点でも、MOSOLFにとって最適でした。一式を揃えても価格帯が非常に手頃なので、コストパフォーマンスも良いです」と話してくれたのは、Formlabsのパートナーである3D-WERK Black Forest GmbHの創設者兼CEOのGerhard Duda氏です。MOSOLFと初期から提携し、同社の用途にあった最適なソリューションを提案してきました。
「MOSOLFにはFuseシリーズが最適でした。取り扱い方法や作業手順の点で最も管理がしやすい製品だったからです」と、Busam氏は付け加えます。
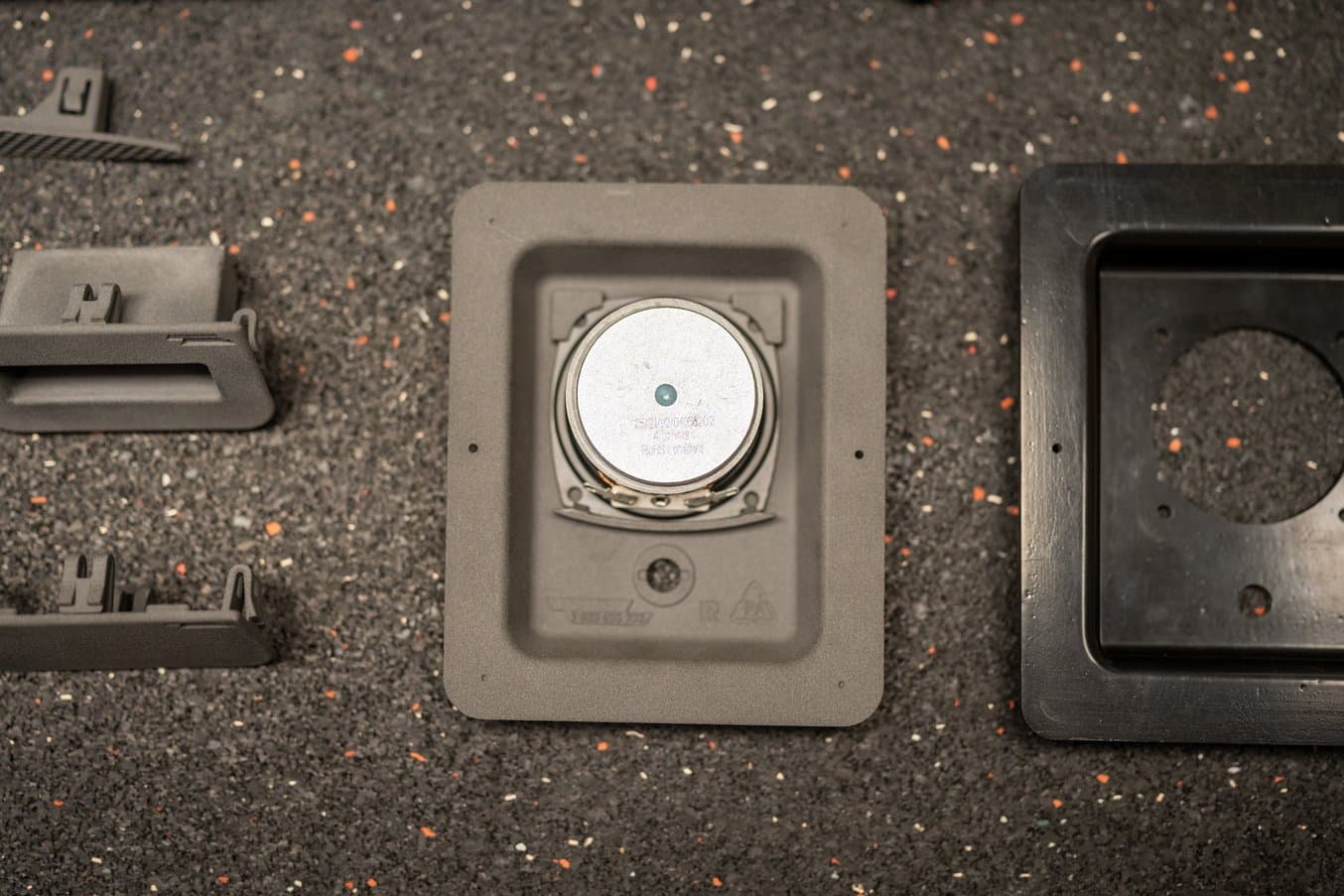
このスピーカーカバーは、事前設置費用の70%を削減できるようデザインされた。スピーカー本体は、接着や機械的な締結をせずにヘリサートに直接固定できるようになっている。
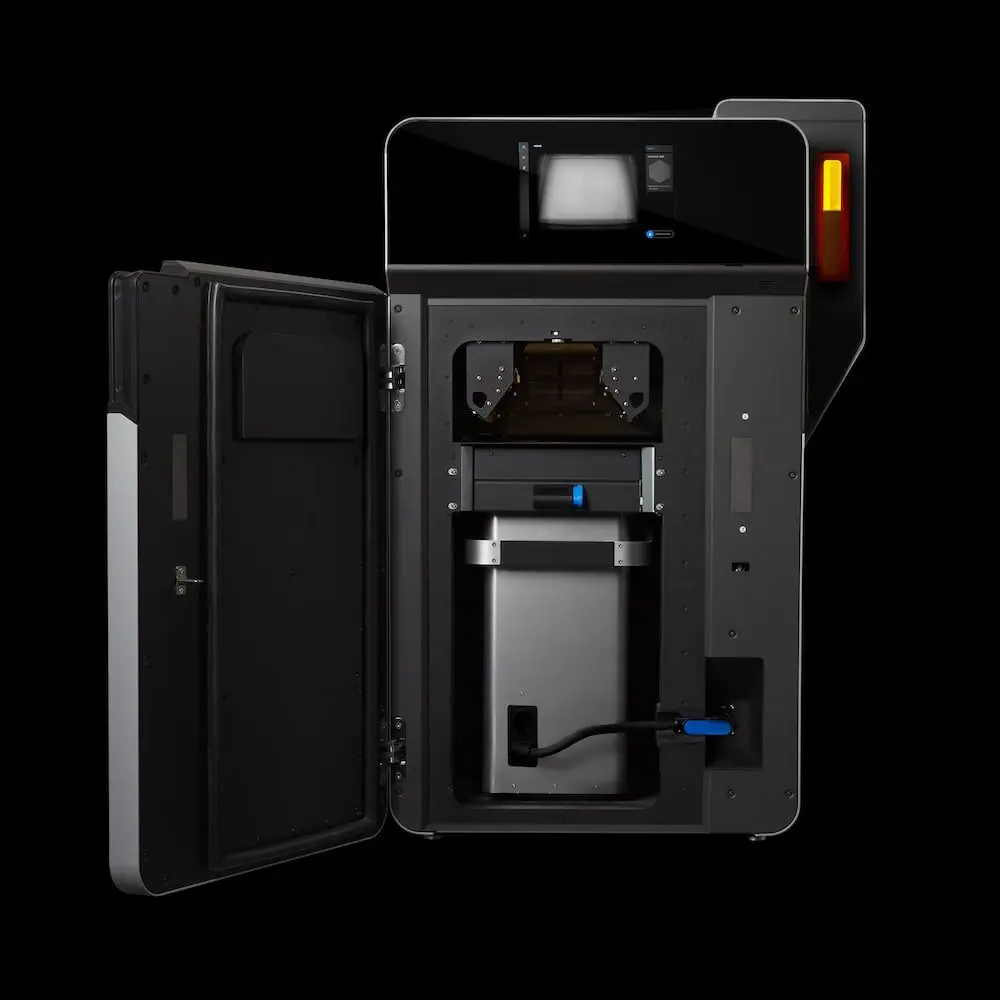
新しいSLS方式プリンタFuse 1+ 30Wで高性能部品を高速製作
本ウェビナーでは、Fuse 1+ 30Wの製品概要やSLS方式3Dプリントの概要をFormlabsのエキスパートがご説明します。
SLS 3Dプリントでカスタムの実製品用部品も24時間以内に製作
射出成形や熱成形、板金加工などの従来の量産方法と比べて、アディティブマニュファクチャリングの最大のメリットは高額な金型を使うことなく少量生産のカスタム実製品用部品を生産できる点にあります。
「弊社ではSLS、特にFuse 1+ 30Wを、シンプルなデザインの小型部品から車両に搭載する複雑なコンソールまで、様々な部品の製作に使用しています。ほぼすべてにSLSを使っていて、Fuseだけでニーズの80%を満たすことができています」と、MOSOLFでPrototyping, Design, and Technical Conceptionのリードを務めるTiberiu Morariu氏は言います。
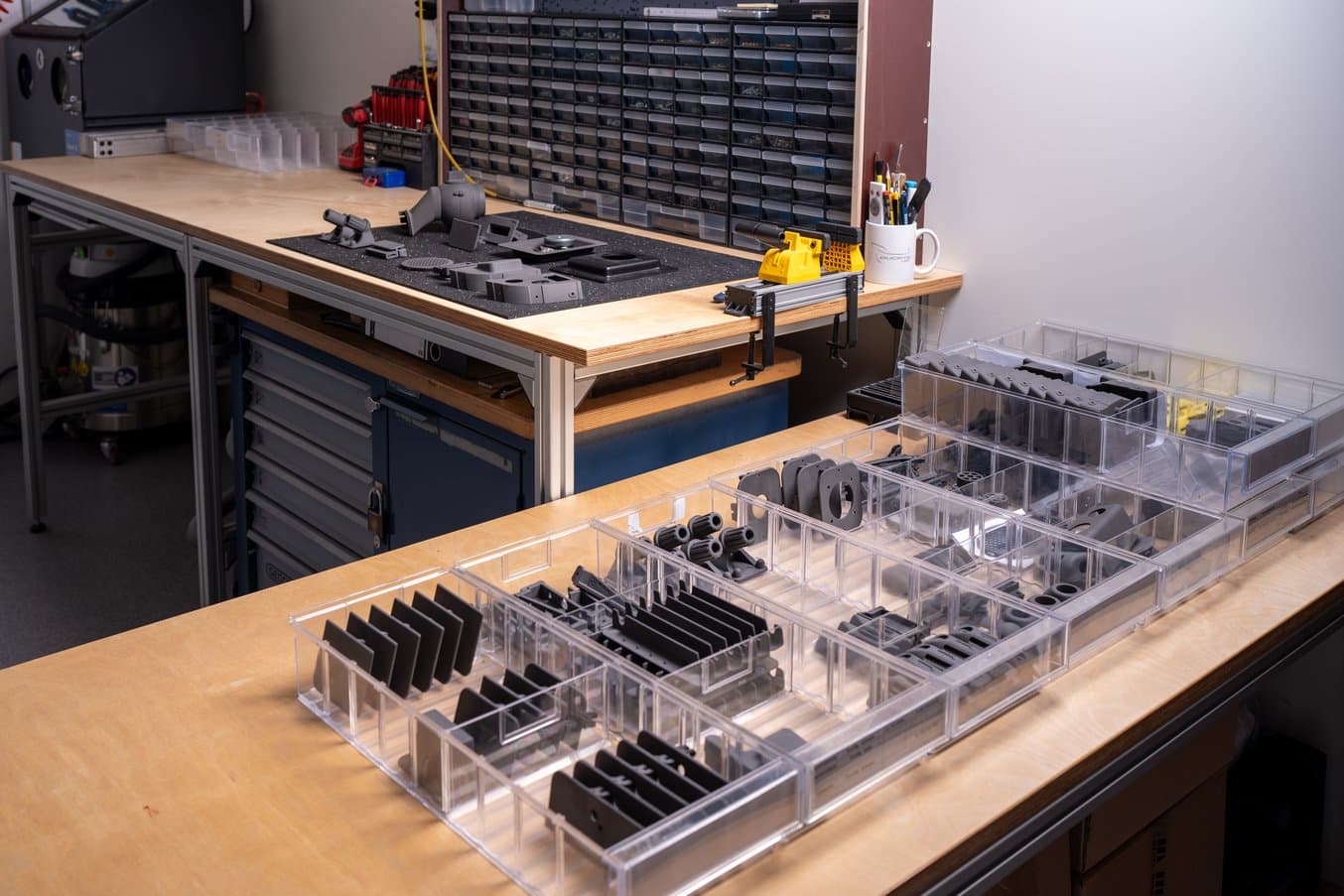
MOSOLFはSLS 3Dプリントを活用し、小型のカバーやエンクロージャから大型の複数部品からなるアセンブリやダッシュボードコンポーネントなど、数十点ものカスタデザイン部品を製作している。
「要件は州ごとに、さらに言えば警察署ごとに異なります。そういう場合には、3Dプリントの方が純粋に対応しやすいのです。車両ごとの設計変更も非常に迅速に行えます。車両が同じなら輪郭も同じものを使えますが、車両内に搭載されるシステムは顧客によって全く異なります」とMorariu氏は言います。
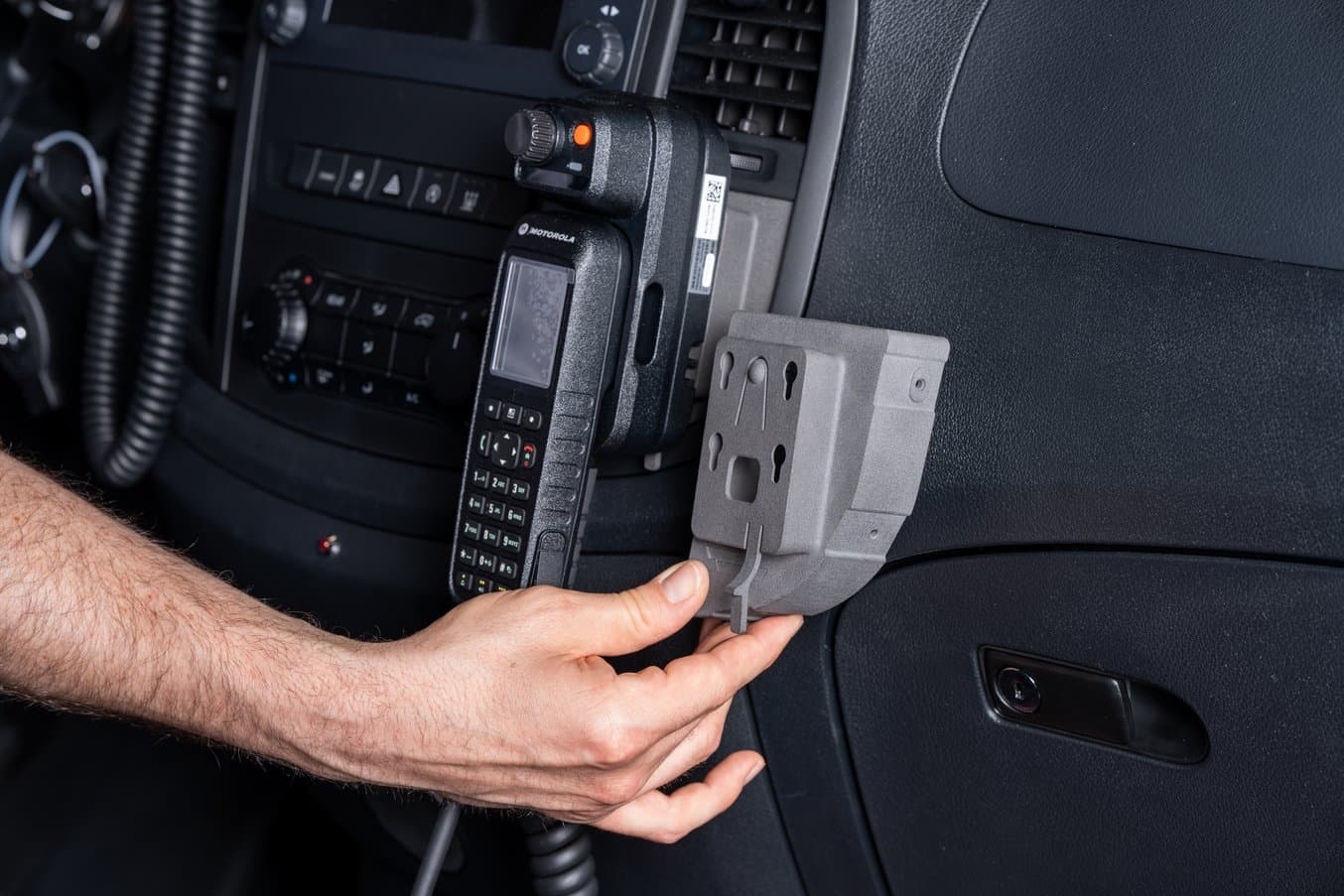
無線ホルダーはカスタマイゼーションの典型的な例。コンソールに取り付けるアタッチメントはメルセデスのバンと同じだが、全体のアセンブリは無線を作っているメーカーの仕様に応じてホルダーを簡単に変更できるようになっている。
様々なバリエーションに対応できるこの能力こそが、プロトタイピングと量産の大幅な高速化に貢献しています。特に試作品も実製品用部品も同じ機械で生産できるということが、大きなメリットです。
「その日に思いついたアイデアを次の日には実際に形あるものとして確認できる。これがやはり、デザイナー冥利に尽きる瞬間ですね」と、Morariu氏は言います。
「3Dプリントによる内製の最大のメリットは、様々な作業が格段に高速化できたことです。従来の製法であれば、特にコーティングが必要な部品などは出来上がるまでに4〜6週間ほどかかっていたでしょう。それが3Dプリントなら、実質一夜にして製作できます。3Dプリントを導入していなければ、この製造工程には相当の時間がかかっていたでしょうし、部品を製作しては調整するという過程が何度も発生して複雑さも高まっていたはずです」
MOSOLF Special Vehicles GmbH Head of Project Planning、Carsten Busam氏
SLS 3Dプリント | 板金加工(メタルシート成形) | 熱成形 | 射出成形 | |
---|---|---|---|---|
設計〜試作品製作〜シリーズ生産にかかる時間 | 1〜2週間 | 6〜8週間 | 6〜8週間 | 6〜8週間 |
実製品用部品の製作期間 | 1〜2日間 | 6〜8週間 | 6〜8週間 | 6〜8週間 |
その他の要素 | 金型が不要 カスタマイズが簡単 設計の自由度が高い 優れた審美性 | 金型が必要 設計の自由度に制約あり カスタマイズが困難 審美性が劣る | 金型が必要 設計の自由度に制約あり カスタマイズが困難 | 高額な金型が必要 カスタマイズオプションなし 設計の自由度が低い |
「最近の車両はどんどん見た目が綺麗になっていて、内装も流線的なものが多くなっています。収納場所もこれまでよりダイナミックで複雑な形状になっています。3Dプリントは車両のデザインや人間工学的な要素には非常に重要な役割を果たしてくれています。熱成形や板金加工などの他の技術では必ずしも実現できるとは限りませんから。こういった複雑形状の部品と車両自体との接続も、3Dプリントで解決できます。3Dプリントのおかげでより自由な設計が可能になり、自分のクリエイティビティを存分に発揮してデザインや形状に落とし込むことができます」
MOSOLF Special Vehicles GmbH、Prototyping, Design, and Technical Conception、Tiberiu Morariu氏
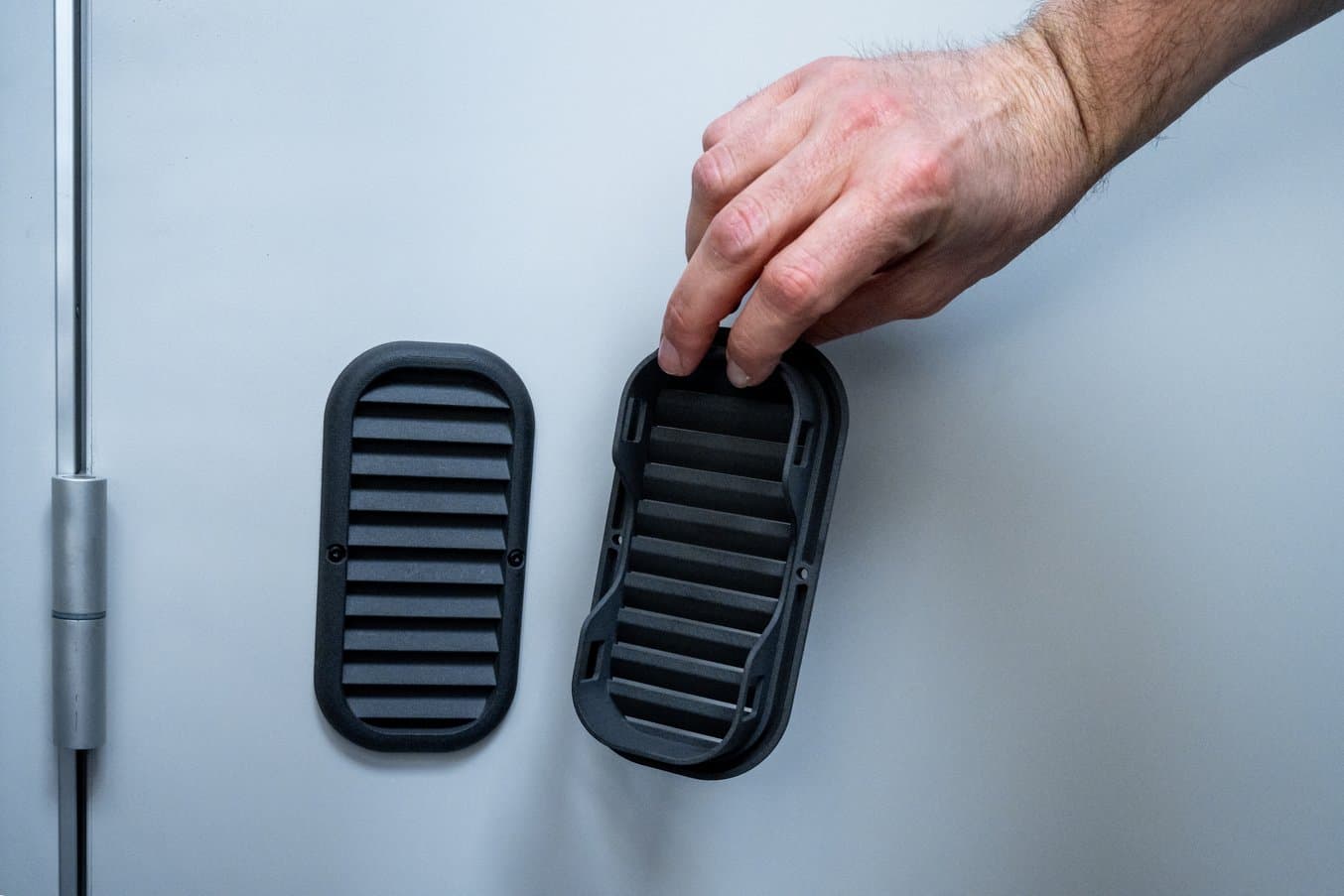
このエアベントは、放火捜査を専門とする特殊車両の白色と黒色のコンパートメントを分ける一方向弁。3つのコンポーネントをネジで締結した比較的複雑なデザインのアセンブリでMOSOLFでは当初、FDM 3Dプリントで製作を試みたが、丸みを帯びた形状と薄肉構造により製造が難しいことがわかり、より設計の自由度が高いSLS 3Dプリントに移行した。
SLS 3Dプリントの最大のメリットの1つは、エンジニアにとって馴染みのある機械的特性を持った材料を使用できることです。特にナイロン材料などは、自動車業界で内装部品にも外装部品にもよく使用されている多い材料です。MOSOLFはSLSで3Dプリントしたナイロン部品の特性をよく理解しているため、部品に求める機能性をイメージしながら、時には元の金属部品を置き換える部品もデザインすることができています。
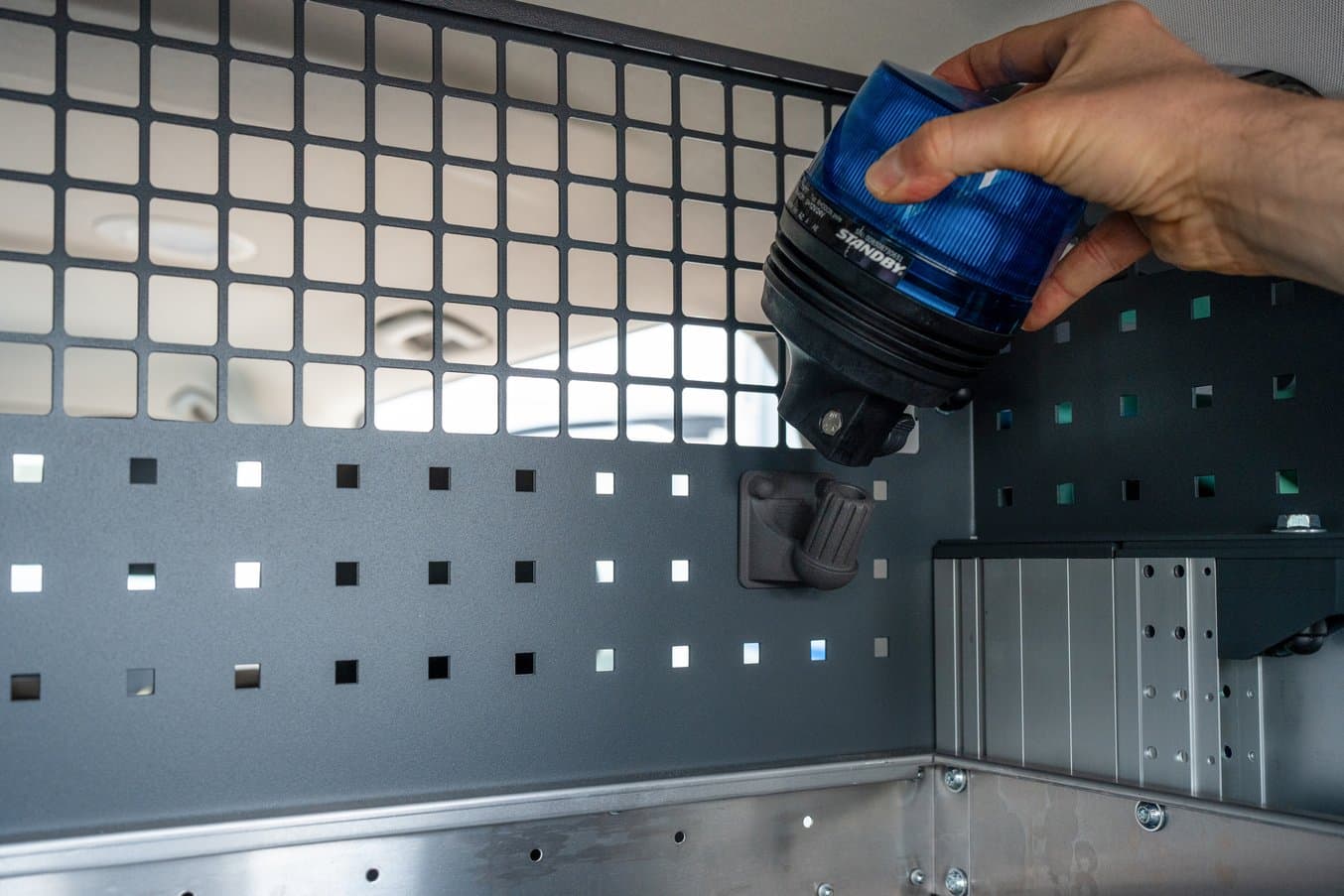
取り外し可能な緊急車両用のライトを装着できる、クリップ式のホルダー。
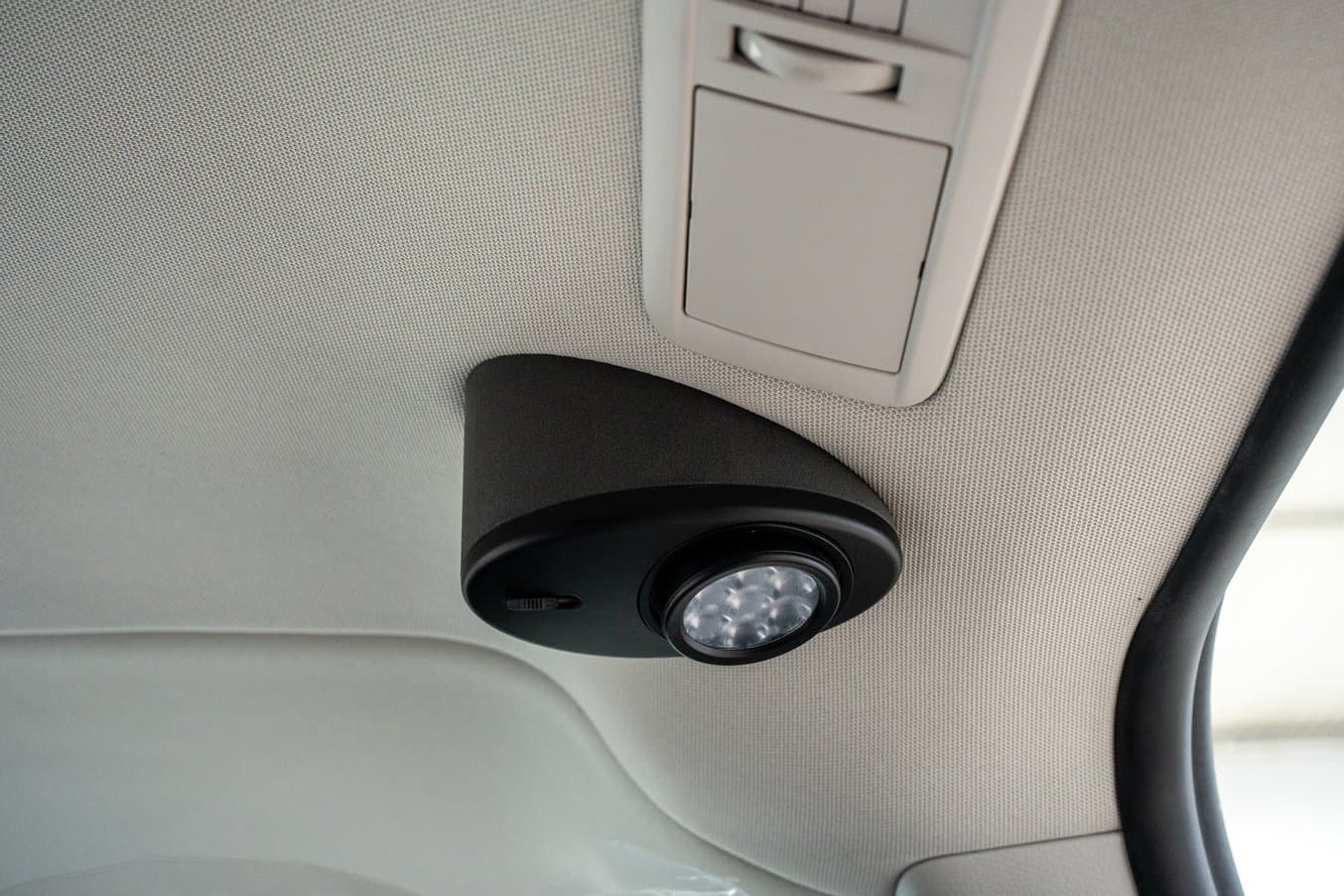
シーリングライト用のハウジングとマウント。
「Fuseシリーズなら、最適な材料を最初から使用できます。業界で長く信頼されてきた、徹底的な検証をクリアした材料です」とDuda氏は言います。
自動車用途における最重要基準には、耐久性の他に耐熱性があります。FDMの材料でいうと、PLAは荷重たわみ温度(HDT)が50º[email protected]しかなく、この基準をはるかに下回ります。HDTが90º[email protected]のABSは、PLAよりは性能が高いもののやはり多くの用途では要件を満たせません。一方、FormlabsのNylon 12パウダーはHDTが171º[email protected]と、はるかに高い耐熱性を備えています。つまり、夏場の駐車場で車内の気温が上がったとしても、無線ホルダーなどの機能性部品が壊れてしまう心配はありません。
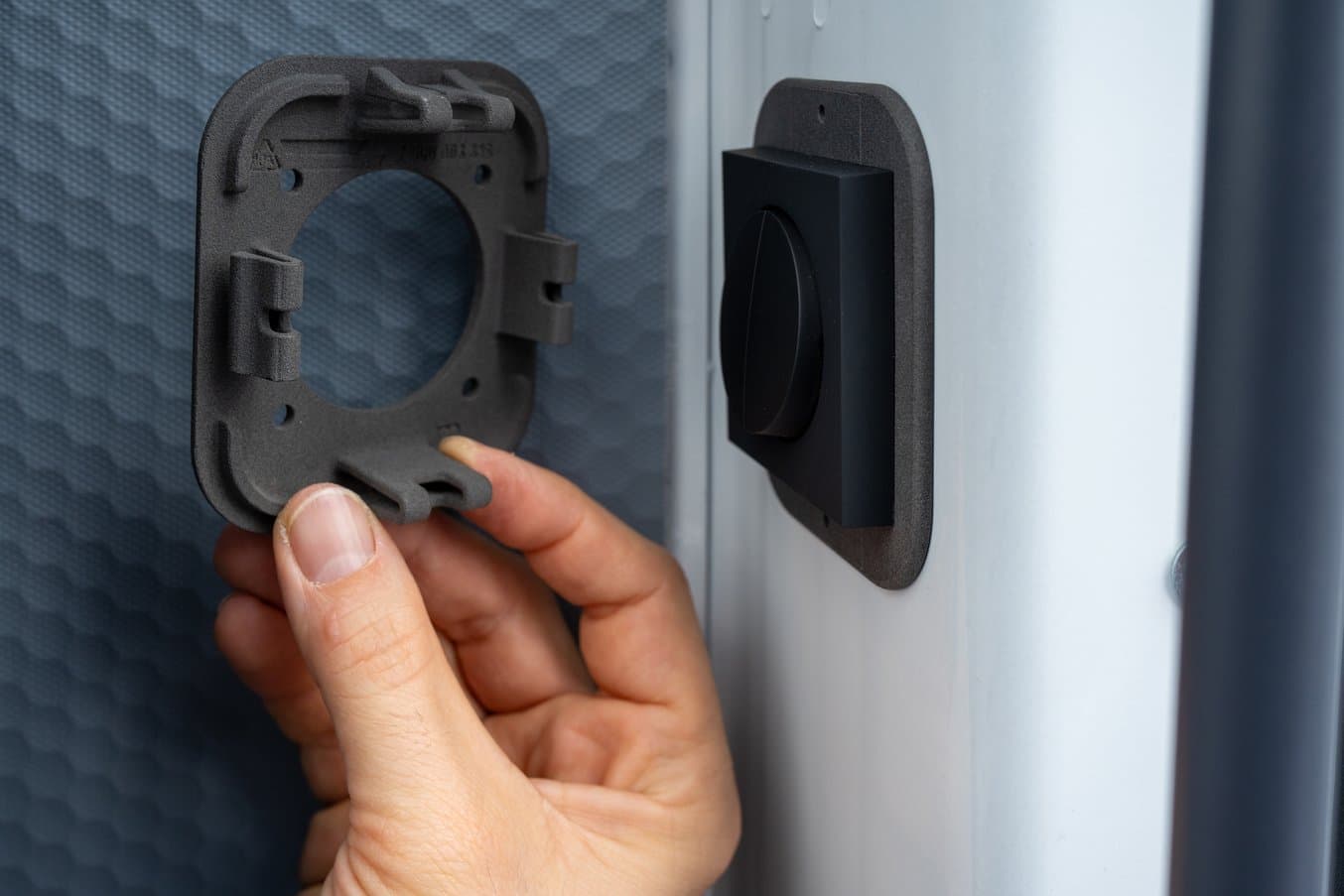
電気ソケットハウジング。
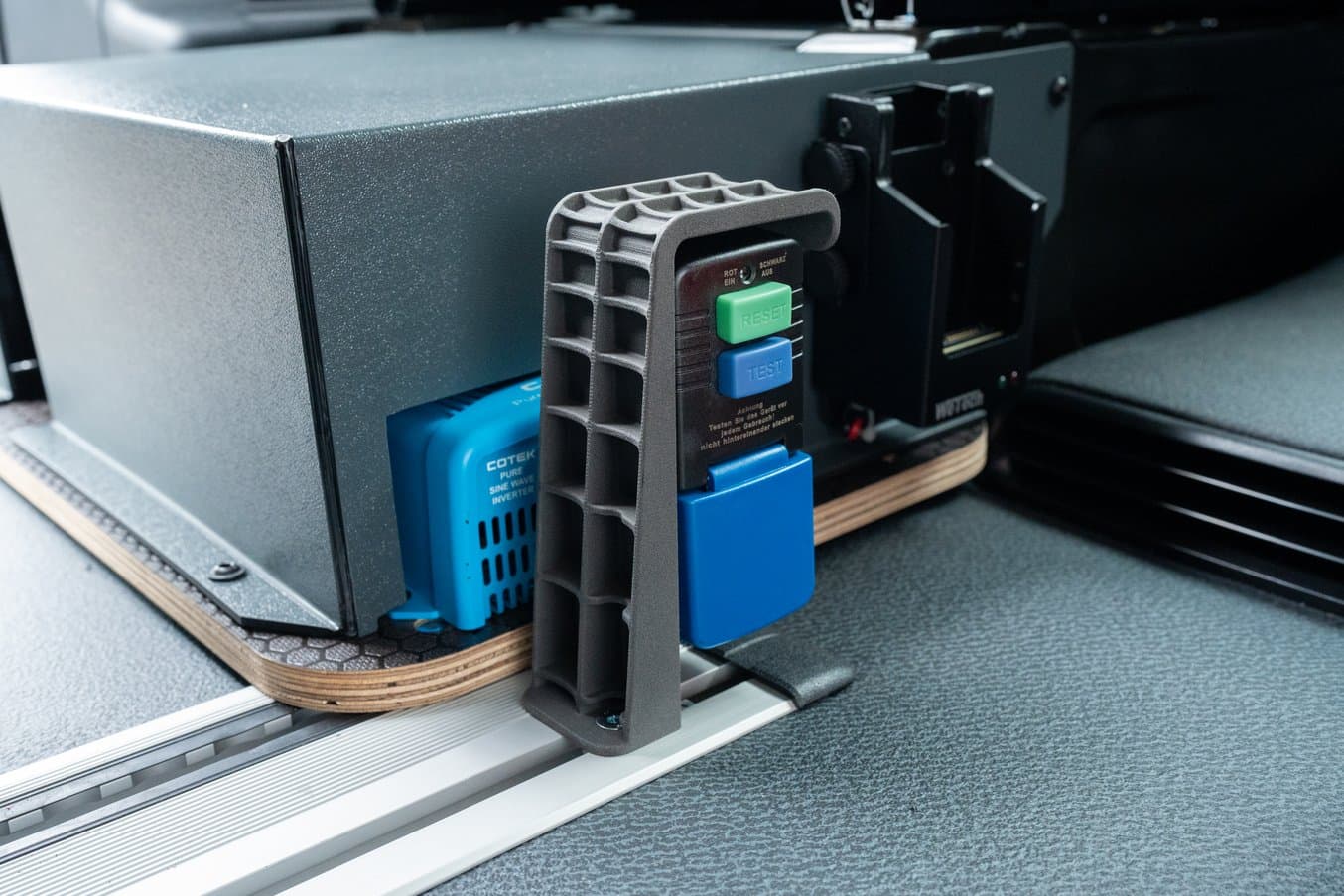
車両内で動いてしまった場合に偶発的なダメージから本体を守る保護カバー。
一部の車両は、警察や緊急部隊に貸し出された後、使用期間が終わると民間やその他の部署に売却されることがあります。このような場合を想定して、MOSOLFでは車両が任務を終えた後に簡単に元の状態に戻せるよう、恒久的に仕様を変えてしまうような変更や車両を損傷する恐れのある変更はせずに、警察車両や特殊車両としての要件を満たせる状態にする必要があります。この場合にも、アディティブマニュファクチャリングが役に立ちます。MOSOLFでは既存のコンポーネントを恒久的に変えてしまうのではなく、3Dプリント製の部品を取り付けて後で付け替えられるようにしています。
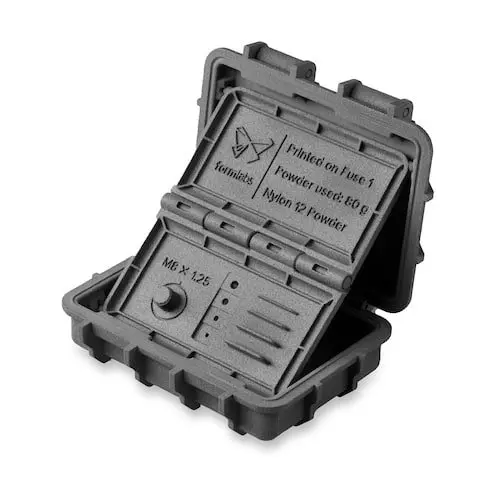
3Dプリント製部品の搭載が増える未来の警察車両
SLS 3Dプリントの導入が成功したことで、MOSOLFと3D-WERKは現在、特殊車両内でさらに広範囲にわたる部品を3Dプリント製できるよう、他の材料や追加導入が可能なプリンタを検討しています。
「もう何年もアディティブマニュファクチャリングによる製造に関わっていますが、3Dプリントでこんな機能や可能性が現実になるのかと、いまだに自分たちが設計・製造した製品を見て驚くことがありますね」と、MOSOLFのManaging Director、Michael Ringwald氏は言います。