この度、Formlabsから業界初となる低価格な純シリコン材料Silicone 40Aレジンが新しく登場します。特許出願中のPure Silicone Technology™で鋳造用シリコンの優れた材料特性と3Dプリントの利点を兼ね備えた新材料です。
3Dプリントで使えるさまざまなエラストマー材料がある一方、優れた材料特性を持った純シリコン材料を3Dプリントするには、コストが高く技術的にも難易度が上がるため、使用できるプリンタが限られているのが現状です。Formlabsは特許出願中のPure Silicone Technology™ を開発し、FormlabsのSLA光造形方式プリンタで100%シリコン製部品を短時間で内製できるようにしました。
Silicone 40Aレジンでの造形品は、ショアA硬度40A、破断伸び230%、引裂強さ12kN/mを備え、繰り返しの曲げ伸ばしや圧縮にも耐えられる柔軟性と耐久性が求められる用途に最適です。また、反発弾性は34%で耐薬品性と温度安定性(-25°C~125°C)にも優れ、わずか0.3mmほどの繊細なディテールや従来の製造方法では実現が難しかった複雑な形状も実現できます。
Silicone 40Aレジンは以下の用途に最適です。
- コネクタ、グロメット、アクチュエータ、キーパッド、腕時計バンドなど、弾力性のある消費者向け製品や自動車部品、産業機器などの製品開発サイクルにおけるラピッドプロトタイピング、ベータ品のテスト、検証工程
- シールやガスケットなど屋内で使用する実製品用部品の少量生産やカスタム製造のコスト効率化
- 柔軟性のある鋳造用金型、治工具、マスキングツールなど、高品質で長持ちするカスタム治工具や金型
- 医療機器部品、患者ごとにカスタマイズした義肢装具、補聴器
- 従来の方法では製造が困難な複雑な形状の部品
シリコン材料で3Dプリントする理由
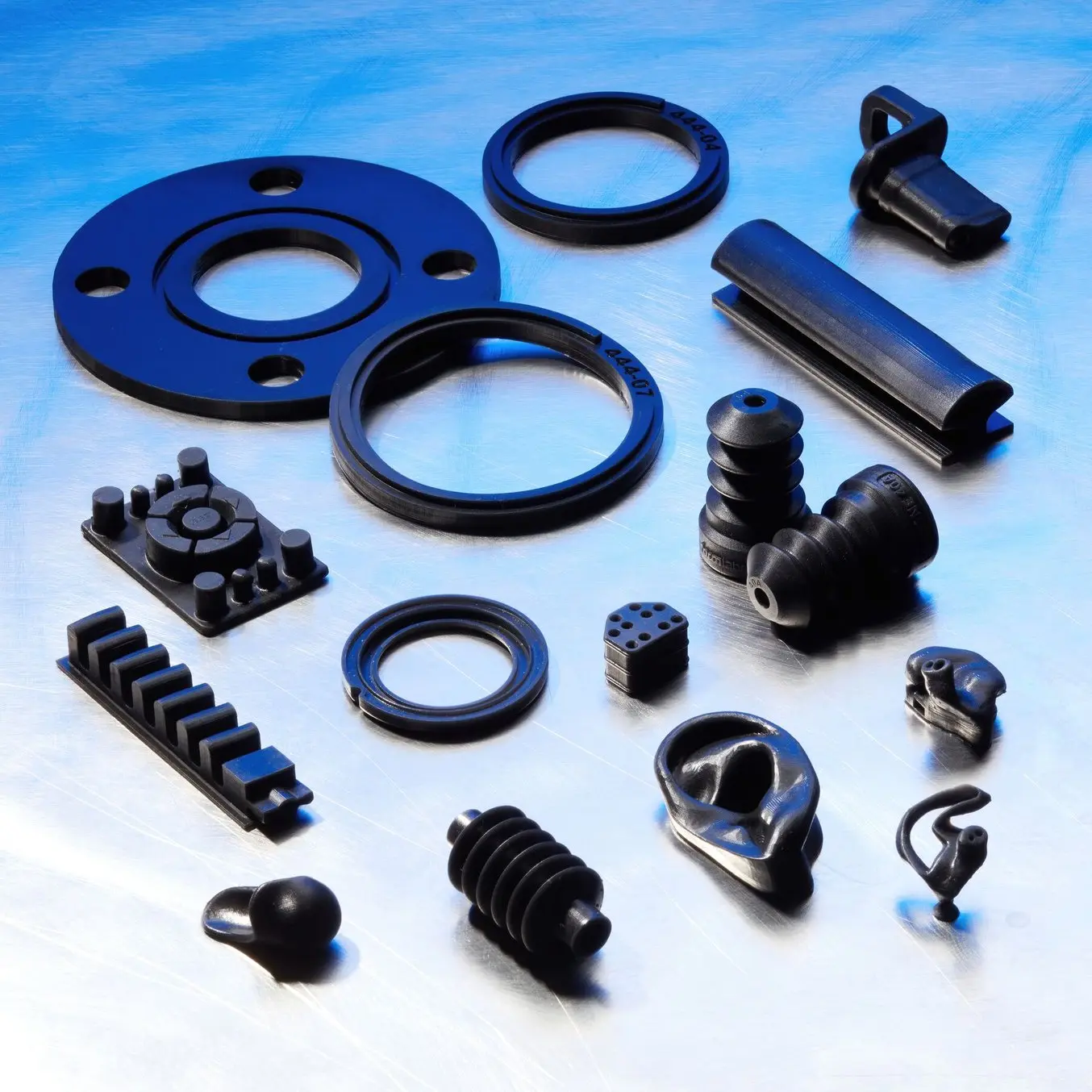
純シリコン品を素早く簡単に生産
シリコン部品は柔軟性や耐久性、圧縮性、耐薬品性、耐熱性が高く、自動車業界ではシールやガスケット、ロボット工学ではアクチュエータやベローズ、消費者向け製品ではウェアラブルやイヤホン、キッチン用品まで、さまざまな業界や用途で幅広く使用されています。
シリコン部品を何千個も大量生産する場合は、射出成形や圧縮成形、押出成形などの製造手法なら費用対効果も高く効率的な生産が可能です。しかし、これら製造手法には高額な金型や加工機械が必要で、さらにその金型の設計や製造を外部の請負業者に委託しなければならないのが一般的です。
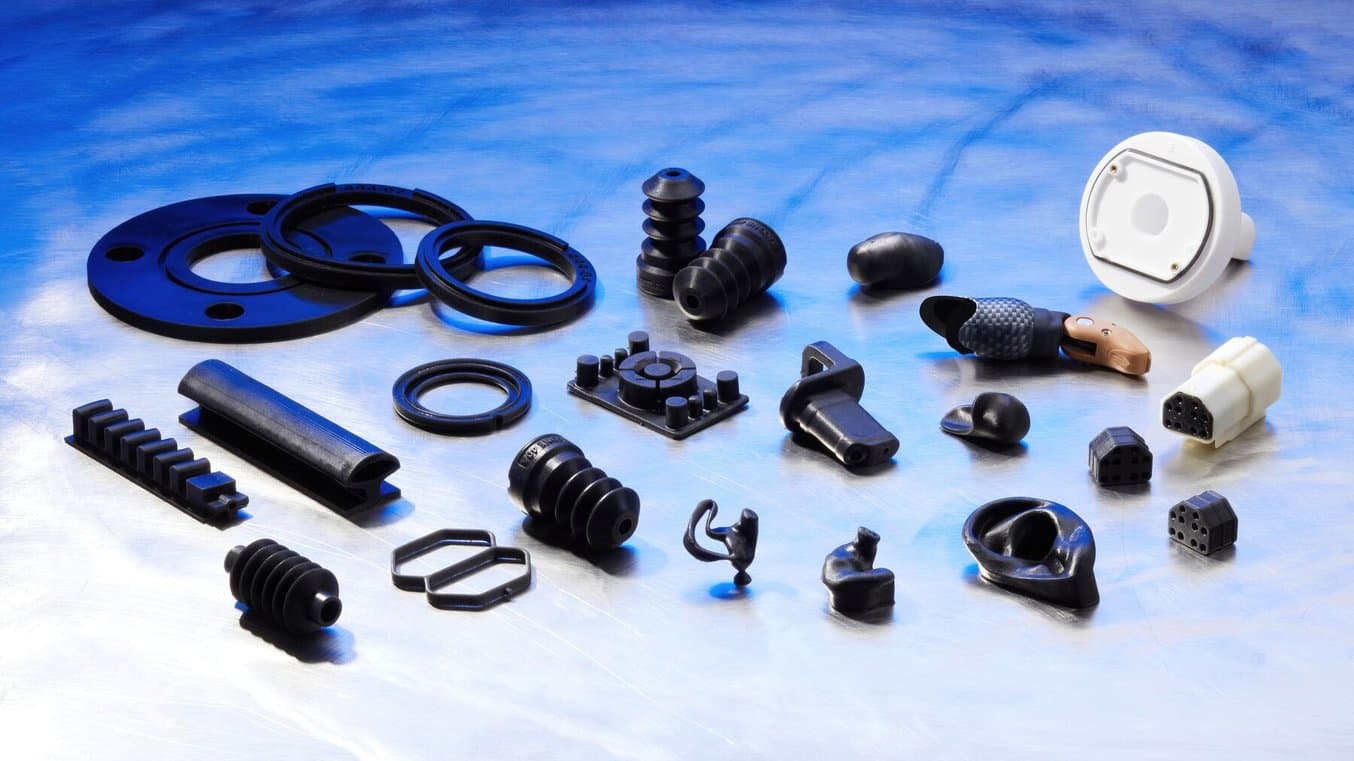
シリコン材料で3Dプリントができれば、ラピッドプロトタイピングから実製品用部品の少量生産まで、幅広い用途への適用が可能に。
純シリコン部品を少量生産(1~1000個)したいと考えるエンジニアやデザイナー、製造業者にとっては、金型製作にかかるコストと時間が課題です。シリコン鋳造のように低コストで済む製造手法なら少量生産も可能ですが、労力や時間がかかるうえに製品形状を完全に複製することは難しく、実現できる設計や形状に限界があります。代替手段として、エラストマー材料を使った3Dプリントなら迅速かつ安価に生産が可能ですが、シリコンに比べて材料特性で劣ります。純シリコン材料を使って直接シリコン部品を造形できる3Dプリンタを提供しているメーカーもありますが、プリンタの価格が$100,000以上と高額です。
新登場のSilicone 40Aレジンを使えば、価格、品質、スピードのいずれも諦めずにシリコン部品の生産ができます。FormlabsのSLA光造形方式3Dプリンタをお持ちの方なら誰でも、高品質な純シリコン部品を素早く直接3Dプリントでき、煩雑な鋳造工程や金型製作にかかる高額なコストを避けることができます。
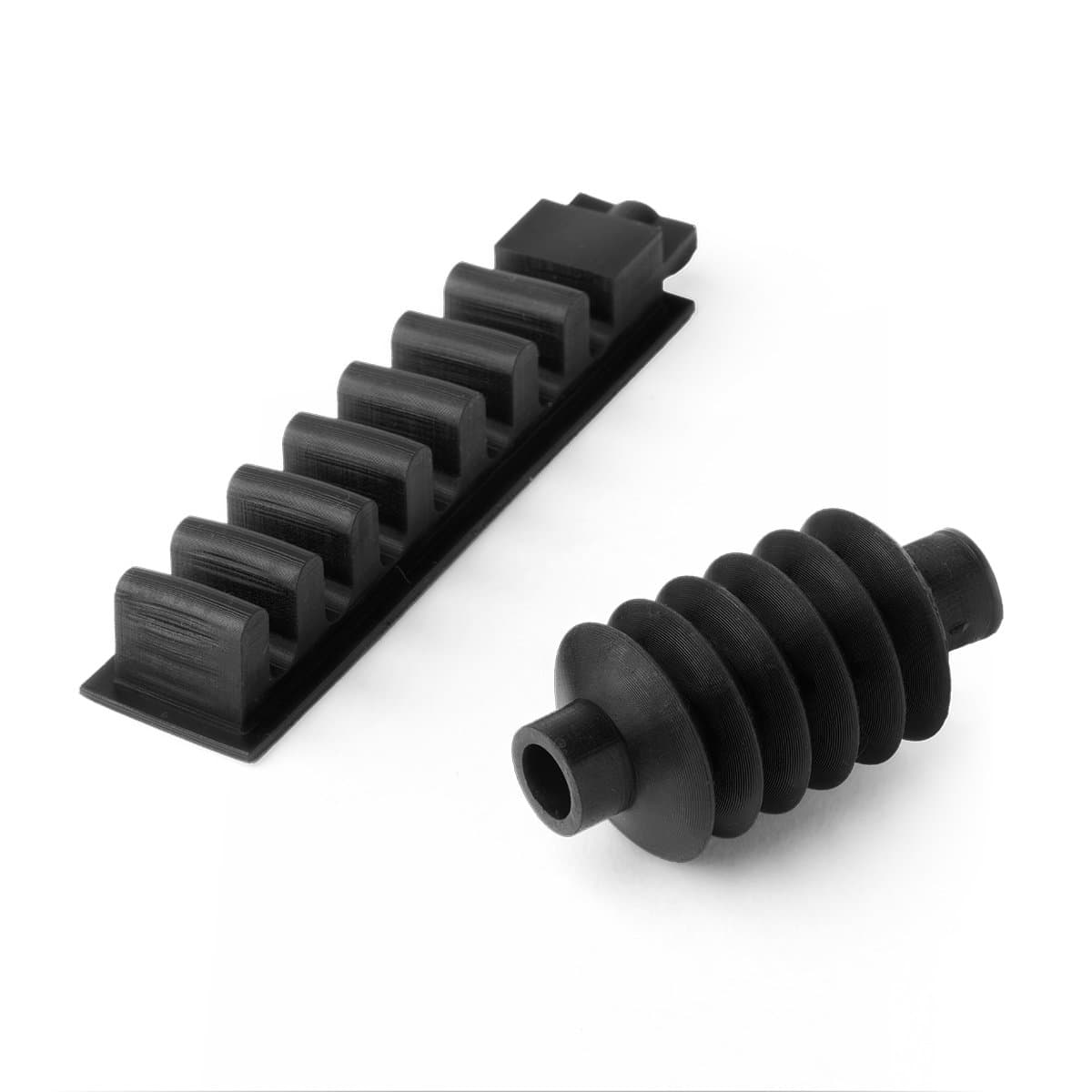
「以前は、鋳造で高品質なシリコンアクチュエータを作るには特別なトレーニングを受け、10時間以上かけて作業をする必要がありました。それでも、鋳造部品の品質にはばらつきがありました。それが今はSilicone 40Aレジンで鋳造品に劣らない機能を持った高品質なシリコン部品を製作できるようになり、義指用の設計検証工程を大幅にスピードアップすることができています」
Rui Li氏、NYU Tandon School of Engineering(ニューヨーク大学タンドン工学部)、一般工学プログラム インダストリーアシスタントプロフェッサ
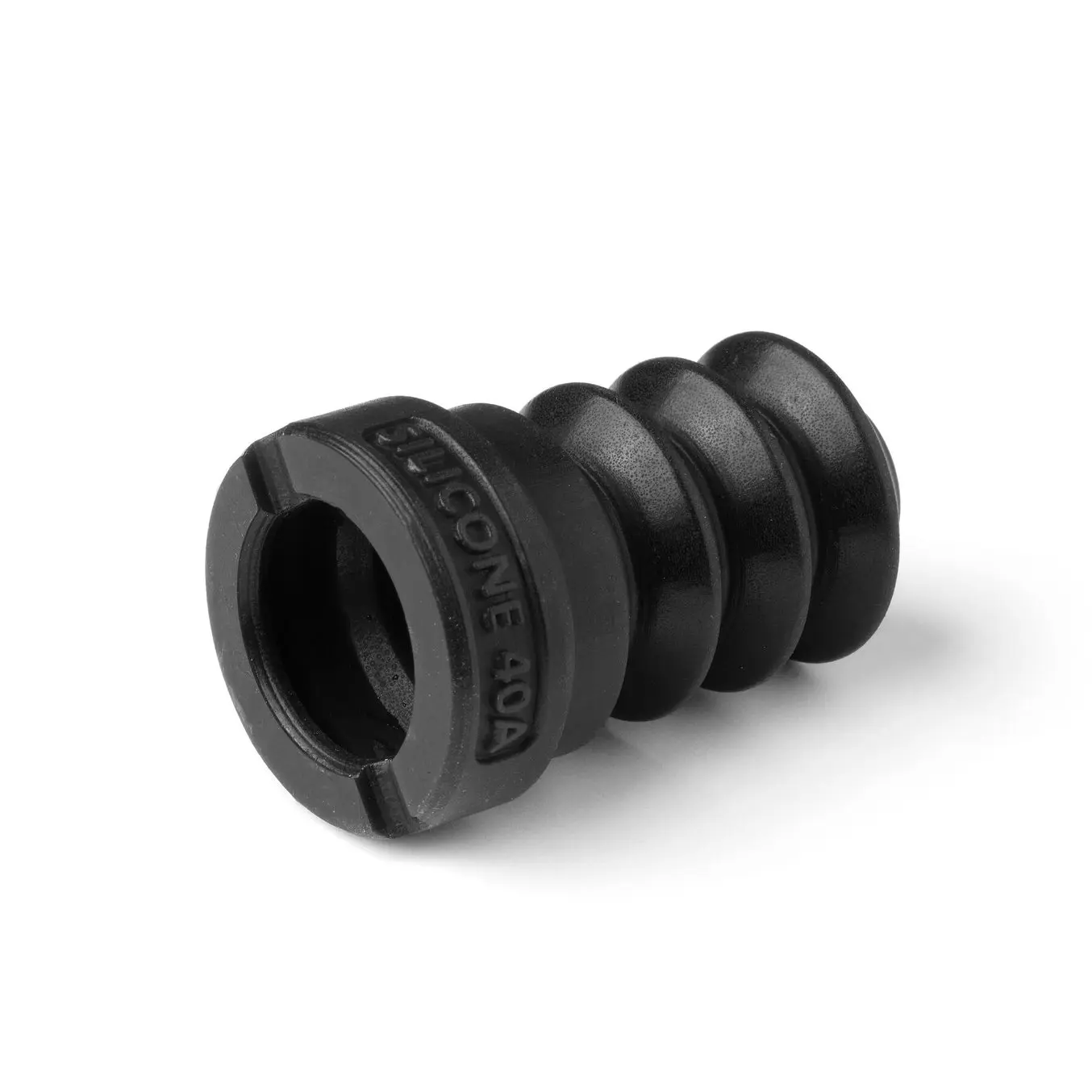
新たな用途と工程を実現
純シリコン部品の3Dプリントはこれまで、対応可能な3Dプリンタが高価なために多くの企業にとって手の届かないオプションでした。Formlabsが提供する手頃な価格の3Dプリンタにより、こういった企業や個人の方々も、メーカーや消費者にとって馴染みのある材料で実製品に劣らない品質の部品を生産できるようになります。また、これまでシリコン部品を外注に頼っていたメーカーも製造工程の主導権を取り戻すことができますし、大企業の試作製作チームの生産性も向上させることができます。
ラピッドプロトタイピング
軟質シリコンカバーは車両のクラッチアクチュエータシリンダーを水、汚れ、破片から保護するものです。Silicone 40Aレジンの優れた耐薬品性と耐熱性により、このような内部部品も自動車の実製品用部品として使用することができます。
Silicone 40Aレジンでの3Dプリントなら、金型製作や労力のかかるシリコン鋳造などを外注に頼ることなく、柔軟性に優れた部品を素早く3Dプリントして試作・検証を繰り返し、その日のうちに機能確認が行えるため、製品開発のスケジュールを短縮できます。消費者向け製品や自動車、航空宇宙、ロボティクス設計など、部品に高い機能性が求められる用途では、ウェアラブル、グリッパ、アクチュエータ、ガスケット、シールなどの部品を3Dプリントして機能確認が行えることで、チームが設計を最適化し、ベータ品のテストや検証工程をより迅速に進めることができます。
最終的に射出成形で生産されるシリコン部品とまったく同じ挙動をする製品や部品をテストできることで、開発工程に安心感と自信が生まれます。また、設計のやり直しや旧式の金型製作が必要なくなり、高額なコストを削減しながら製品の信頼性を向上させ、市場機会を活用できるようになります。
治工具と金型(シリコン金型を直接プリント)
多忙を極める製造拠点では、柔らかい治工具やマスキングツールを迅速かつコスト効率よく製作したり内製でラピッドツーリングができると、ダウンタイムを出さずに作業手順を最適化することができ、1日に数千ドルも節約することができます。
シリコン部品はクッションや圧縮用途で使用されることが多く、加工機械の寿命を延ばしたり、部品を摩擦から保護するための治工具として最適です。また、Silicone 40Aレジンの耐薬品性により、さまざまな種類の化学薬品に対して反応を起こさないことが大切なマスキングツールにも適しています。
治工具の製作は計画に含まれていないことが多いのですが、Silicone 40AレジンとForm 3+プリンタがあれば必要な部品をオンデマンドで迅速に製作できます。従来の製造手法では、柔らかい交換部品を製造するには数週間かかることがありますが、製造現場でシリコン部品を3Dプリントできれば、1日以内に設備を復旧させることができます。
シリコンの品質と3Dプリンタで実現できる形状の自由さにより、治工具のオンデマンド製作もシリコン部品の3Dプリントに最適な用途と言えます。ウレタン、エポキシ、樹脂、ワックス、石膏、その他材料を、柔らかく再利用可能な鋳型を使って鋳造する必要がある場合には、Silicone 40Aレジンの3Dプリントなら高速かつ効率的に、そして作業場を汚すことなく柔軟で再利用可能なシリコン型を作れます。
少量生産やカスタム製造
消費者向け製品メーカーにとって、シリコン製品のカスタマイズというのは非常にハードルの高い作業でした。金型製作にかかる高額なコストのせいで、生産ラインを短期または1回だけ稼働させるには効率が悪かったのです。医療機器やヘルスケア製品のメーカーは、Silicone 40Aレジンによって補聴器や患者に合わせた義肢装具、患者ごとに最適化した医療など、新しい用途を開拓することができます。
純シリコン部品を直接プリントでき、なおかつForm 3+のスケーラビリティが加わることで、メーカーは従来の成形手法に比べてほんのわずかなコストでウェアラブル、グリップなどのカスタマイズされたシリコン製品を提供できるようになります。さまざまなシリコン製品ライン用に金型を製作するよりもはるかに低いコストで、複数台のForm 3+プリンタを使って純シリコン部品をプリントし、カスタマイズ製品の需要にも応えることができます。
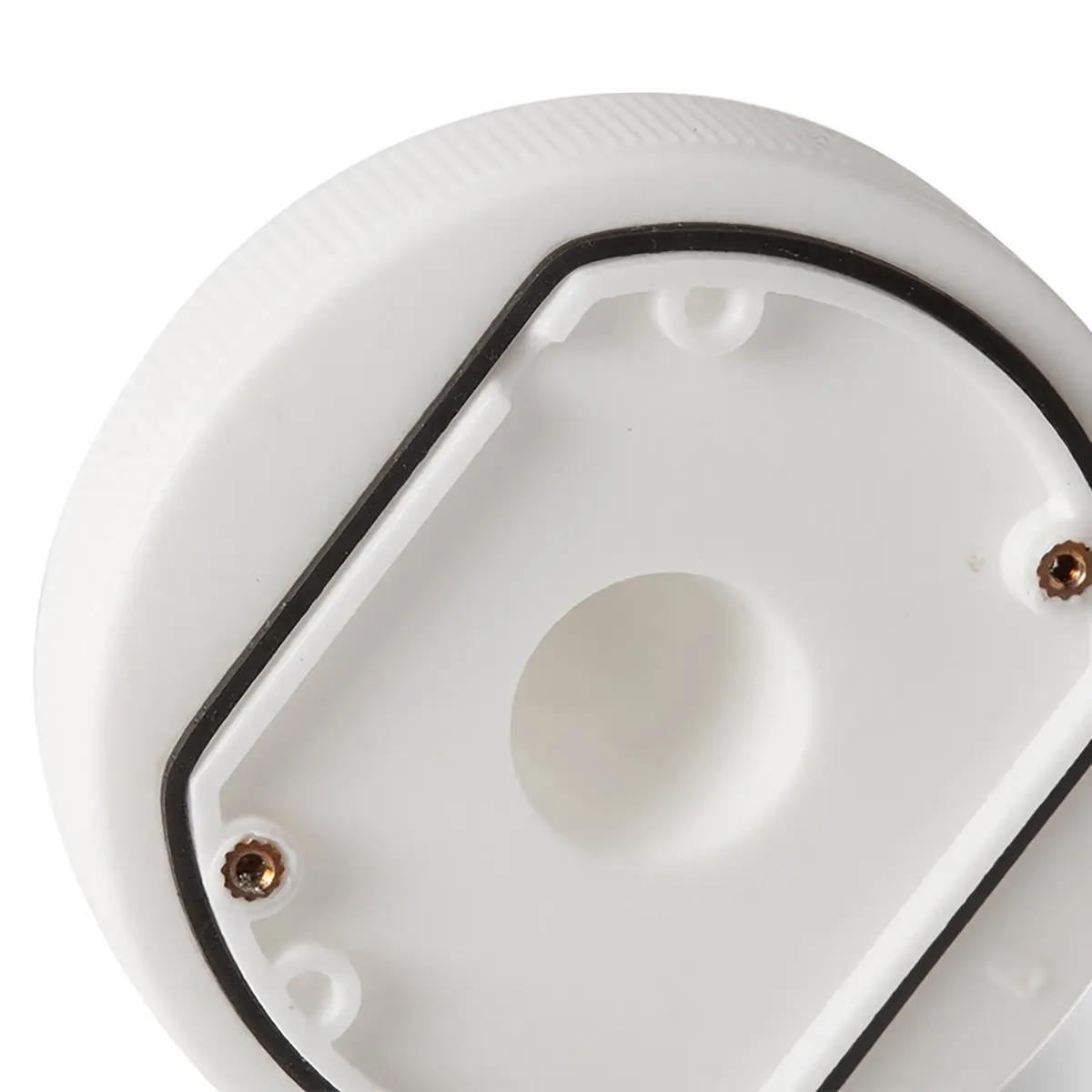
ケーススタディ
FINIS:スイミングゴーグルの試作
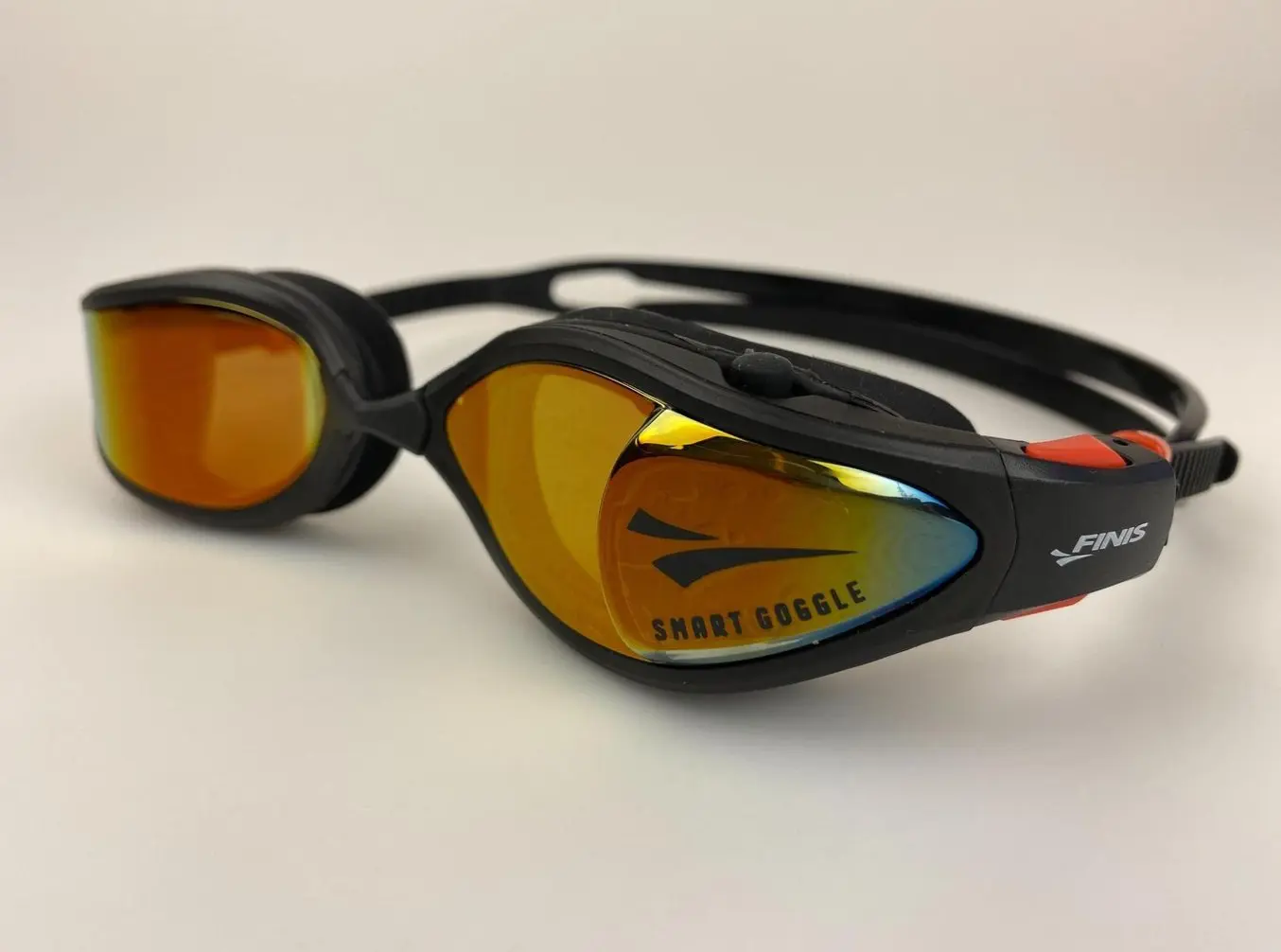
Finisは、新製品のスマートゴーグルの機能確認用試作でボタンを搭載したシリコンガスケットを3Dプリントで製作。
最先端な製品開発で有名なFINIS, Inc.は、提供する製品の優れた品質と機能であらゆるレベルのスイマーから信頼されています。米国カリフォルニア州を拠点とする同社は、スイマーやコーチからの常に変わり続ける要求を徹底的に汲み取り、革新的な製品を提供し続けています。
これまでは金型を使った鋳造でシリコン部品を製造していましたが、多大な労力が必要なことと製造期間の長さがネックでした。それが現在はForm 3+プリンタと新登場のSilicone 40Aレジンの活用により、通常であれば外注で3週間の製作期間と千ドル以上のコストがかかるところ、実製品の品質とほぼ同様のスイミングゴーグル用ガスケットをたった8時間で、ごくわずかなコストで3Dプリントすることができています。3Dプリント製のシリコンガスケットはスイミングプールの環境下で厳しい水密性評価にも耐え、製品開発スケジュールの短縮にもつながりました。
スイミングゴーグル用ガスケットの試作
製作期間 | コスト | |
---|---|---|
ウレタン鋳造 | 2~3週間 | ガスケットを2つ1セットで$1220 |
Silicone 40Aレジンで内製 | 8時間 | ガスケット1つあたり$10 |
「[シリコン鋳造や外注では]治具の製作だけで1ヶ月はかかります。それが[Silicone 40Aレジンのおかげで]、さまざまなアイデアを試せるようになりました。変更を加えて夜間にプリントしておけば、翌朝出社したら造形品を取り出して洗浄するだけ。すぐに機能確認ができます。今まで数週間もかかっていた工程が数時間で完了するようになったことが、一番のメリットだと思っています。」
David Beittel氏 FINIS, Inc. シニアデザイナー
Dorman Products:3Dプリント製ガスケットで自動車部品の検証を高速化
Dorman Productsは、乗用車と重量車のアフターマーケット用自動車部品メーカーとして100年の歴史を誇るメーカーですが、生産期間の短縮と部品の品質向上を目指して3Dプリントを導入しました。常に新しい製造工程やモデルを追加するOEM元のメーカーに遅れずに対応するため、12台の3Dプリンタを2拠点に分散して稼働させています。
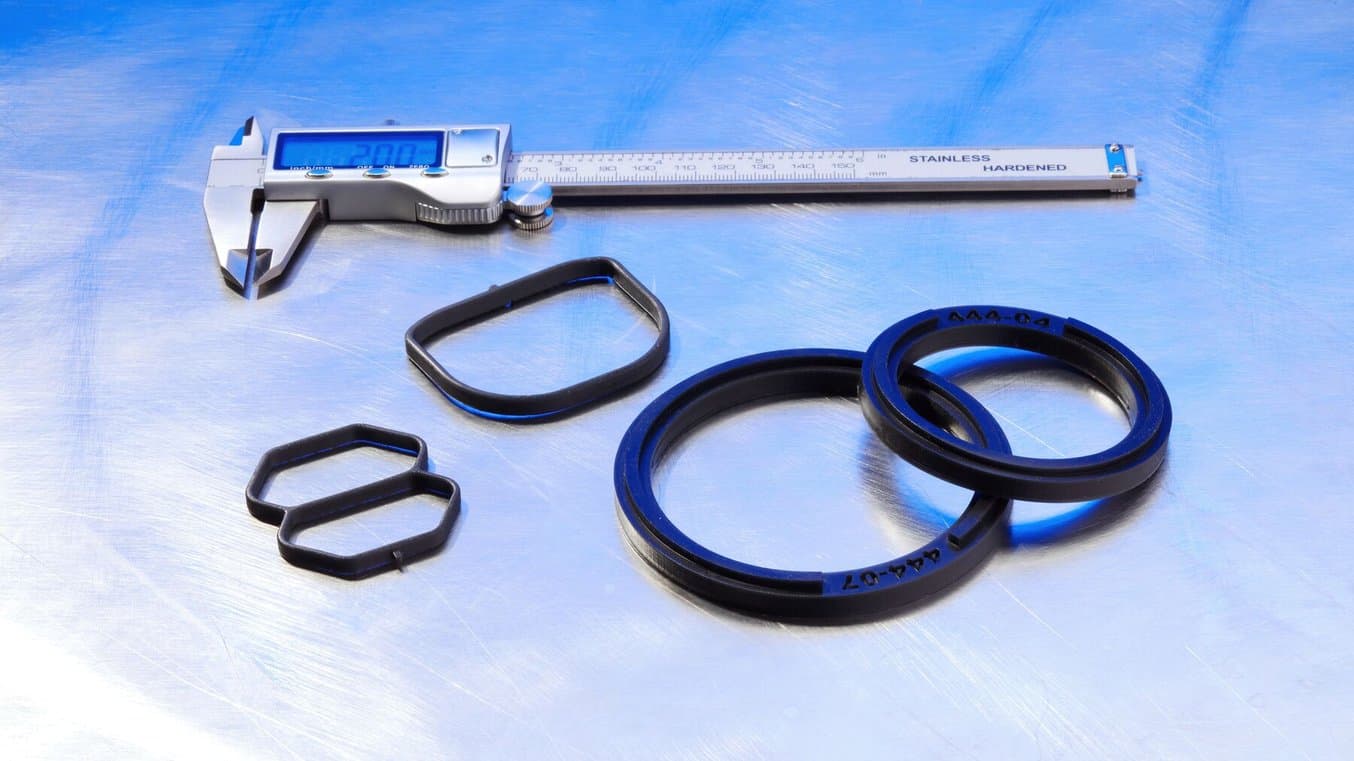
Silicone 40AレジンでプリントしたDorman Productsのカスタムガスケット。
同社内にある広大なテスト環境で、新しい設計の検証を行います。圧力試験用の部品で特定のポートや面を密閉する必要がありますが、すべての部分が嵌合形状になっているとは限らず、密閉するためにはチームが独創的なアイデアを考えなければなりません。結果的に、カスタムのガスケットや治工具を製作することになるのです。
従来は研究室で部品を測定してから金属製のダイを作り、そのダイを使ってアーバープレスでカスタム品のガスケットを切り出していました。「シートからクッキーをくり抜くようなイメージです。材料の使用率や研究室の技術者が費やす時間を考えると、非常に効率が悪いやり方でした」と、Dorman Product社のアディティブマニュファクチャリング部門リーダーであるChris Allebach氏は言います。
3Dプリントに切り替えたことで、膨大な数の新部品があったにも関わらず、製作期間とコストを大幅に削減することができました。「スロットルボディの両端を密閉するスロットルボディテスター用にカスタムガスケットを何百個もプリントして、流量テストを行いました」とAllebach氏は言います。
この目的を果たすだけならFormlabsのシリコンライク材料Elastic 50Aレジンでも十分でしたが、新登場のSilicone 40Aレジンではさらに用途の幅が広がりました。
検証用のガスケット
製作期間 | コスト | |
---|---|---|
金属製のダイを使ったシリコンシートカッティング | 1セットあたり2週間 | 1セットあたり$250 |
Silicone 40Aレジンで内製 | 1セットあたり3時間 | 1セットあたり$12 |
「ギヤーオーブンで熱老化試験を行うカスタムガスケットを作ったり、テストの観点からエンジンルームを模倣した環境でガスケットを密封したり、空中、水中、冷却水、オイルなど、部品が実際に使われる環境でテストできるということが、私たちにとっては非常に重要なんです」
Chris Allebach氏、Dorman Products、アディティブマニュファクチャリング部門リーダー
HGM Automotive:Silicone 40Aレジン製の実製品用コネクタシールを検証
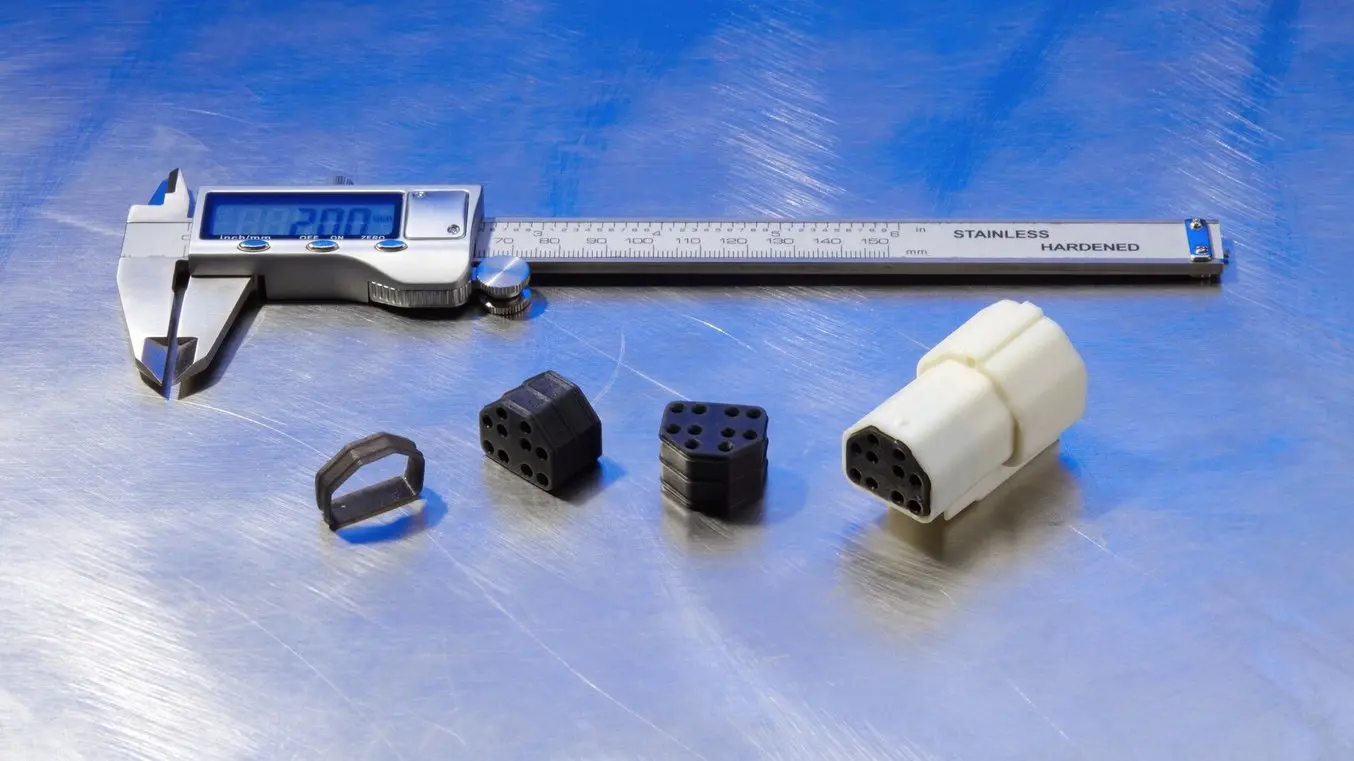
HGM Automotive ElectronicsがSilicone 40Aレジンで製作したコネクタシール
HGM Automotive Electronicsは、自動車アフターマーケット向けに最先端の電子機器を設計・供給するトランスミッション・コントローラー・メーカーです。
部品のオンデマンドで内製するのに最適な3Dプリントを、試作品製作や少量生産のために取り入れました。しかし、ここはIP保護等級や耐薬品性など特殊要件への遵守が求められる規制産業のため、使用する材料の選択が非常に重要です。
Silicone 40Aレジン製の部品は化学的・機械的特性の厳密な試験を耐え抜き、従来頼っていた射出成形のシリコン部品と同様の優れた機械的特性と耐薬品性を持っていることを実証しました。部品をエンジンベイ内に置き、通常の運転条件下で6週間の熱サイクル試験を行い、さらに化学流体に対する暴露試験を行った結果、Silicone 40Aレジンで3Dプリントした部品は実製品用の自動車部品として認定されました。
その他の製造手法 | Silicone 40Aレジンを使った3Dプリントの利点 |
---|---|
射出成形を外注 | 製造期間を90%削減 コストを98%削減 |
内製でのシリコン鋳造 | 難易度の高い複雑な形状も細部まできめ細かな表現が可能 作業時間、人為的ミスのリスク、製造期間を削減 10点〜1000点まで製造量を拡大でき、何度でも同じ部品が製造可能 |
「Silicon 40Aレジンのおかげで、以前であれば非常に高額で時間のかかる成型法でしか実現できなかった形状も試せるようになり、設計面でも柔軟性が得られました。今後、新しい市場の開拓や、これまではコストや複雑さがネックで手の届かなかった部品の生産にも乗り出せそうです。他社の3Dプリンタでも柔軟な材料はプリントできますが、本物のシリコンやTPU部品と同等の品質や耐久性を実現できるのは、FormlabsのSLA光造形プリンタでSilicone 40Aレジンを使って造形した部品だけです。」
Guy Cardwell氏 HGM Automotive Electronics 研究開発ディレクター
Formlabsエラストマー材料の比較
Elastic 50Aレジンは、アクリルベースの柔らかく透明なエラストマー材料で、ラピッドプロトタイピングに最適です。
一方のSilicone 40Aレジンは、当社初の純シリコン材料です。ショア硬度40Aを持つこの材料は、プロトタイピングだけでなく幅広い用途で使える、柔らかくしなやかな部品を製造するのに最適です。Silicone 40Aレジンでプリントした部品は耐薬品性と耐熱性に優れ、繰り返しの曲げ伸ばしや磨耗、破断にも耐えることができます。
メリット | 最適な用途 | |
---|---|---|
Silicone 40Aレジン | 耐久性:引裂強さ12kN/m、破断伸び230%、耐屈曲疲労性 > 500,000サイクル 伸張:反発弾性34%、ガラス転移温度-107 °C 温度安定性:-25°C~125°C 耐薬品性 軟質のショアA硬度40A | 機能確認用試作および内部テスト ベータ品、検証試験、量産前の簡易生産 実製品用部品の少量生産 各種治工具 軟質の成形型 |
Elastic 50Aレジン | 価格の手頃さ 透明 ショアデュロメータ硬度50A | 概念実証用プロトタイプ 実製品と遜色ない外観確認用プロトタイプ 機能確認用試作品 |
Formlabsは、このような柔らかい材料以外にも、ゴムのような柔軟性を持った試作製作用のFlexible 80Aレジン、実際の製造で使えるReboundレジン、FuseシリーズSLS方式プリンタで機能確認用試作や耐久性のある実製品用部品の製造ができるTPU 90Aパウダーなど、より硬度の高いエラストマー材料も提供しています。
簡単な作業手順と優れたプリント適性
Formlabs SLA光造形方式プリンタの通常の手順とは若干異なるものの、Silicone 40Aレジンを使った3Dプリントや後処理の手順は簡単でわかりやすいものになっています。Silicone 40Aレジンの使用方法の詳細はサポートページをご覧ください。
Silicone 40Aレジンでは、柔らかい3Dプリント材料としては前例のない設計の自由さを実現できます。ただし、すべてのエラストマー材料と同様、設計ガイドラインに沿った設計が必要です。プリント適性と設計ガイドライン、表面をスムーズに仕上げるための取り外しが簡単なサポート材の使用、そして表面品質を向上させるための表面処理についての詳細は、サポートページをご覧ください。
「このレジンのプリント適性には驚きました。こんなに柔らかい材料で、ここまでしっかりと細かい形状がプリントできるとは思いもしませんでした。40A材料では決して作らないような部品もプリントしてみたのですが、これまでは射出成形に頼っていたものが、このレベルで3Dプリントできたということに、ただただ驚いています。完成品の細部の品質は信じられないくらいでした。社員も全員、材料の肌触りと弾力性に驚いていましたよ」
Chris Allebach氏、Dorman Products社、アディティブマニュファクチャリング部門リーダー
3Dプリントでシリコン製パーツの製造を開始
Form 3+とForm 3B+は、手頃な価格、つまり必要に応じてすぐに増設できる価格で、中小規模のメーカーから大企業まですべての人が高精細な3Dプリンタにアクセスできるようにします。異なる作業手順の最適化を目指して開発された45種類以上の材料とともに、Formlabsの3Dプリンタで幅広い業界や用途に使える部品を直接3Dプリントするという新たな可能性が広がります。Silicone 40Aレジンが新しく加わったことにより、これまでも高い万能性を誇ってきたFormlabsの3Dプリンタが、業界で初めて本当の意味で手の届く純シリコン対応の3Dプリンタになりました。今回の新材料のリリースには、新たな用途を切り拓く材料を開発し続けるという、弊社のコミットメントが表れています。
Silicone 40Aレジンで、ガスケットやシール、グリッパ、アクチュエータ、ダンパ、ウェアラブルなどを直接3Dプリントできるようになります。長い製作期間や高額なコストをかけて作る金型や、二次的なシリコン鋳造工程が不要になることで、企業はこれまでより徹底した設計の試作・検証工程、迅速な対応が可能になり、製品の市場投入も高速化することができます。
材料特性についての詳細や、お手元の3Dデータのテストプリントをご希望の場合は、Formlabsまでお問合せいただくか、無料のシリコンサンプルパーツをお申込ください。