
SLS(粉末焼結積層造形)方式3Dプリントは、高強度・高機能部品を製作できる方式としてさまざまな業界のエンジニアや製造業者から信頼されています。
本ガイドでは、SLS(粉末焼結積層造形)方式の造形プロセス、現在市場に出ているさまざまなプリンタや材料、SLSプリンタの作業手順、活用例、アディティブマニュファクチャリングの他の手法や従来の製造手法と比較してSLS 3Dプリントが適している用途などについて、幅広く解説します。
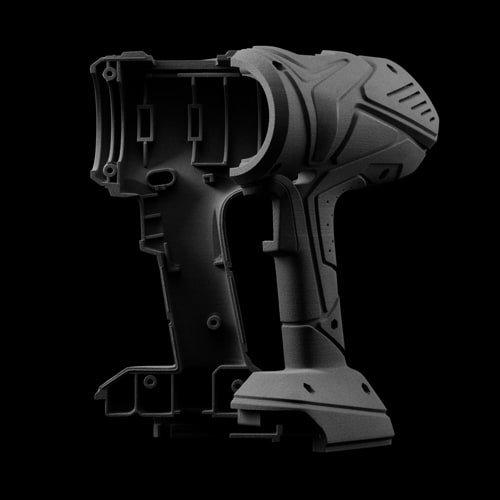
SLS(粉末焼結積層造形)方式3Dプリンタの概要
高強度・高機能な部品を製造できる3Dプリンタをお探しですか?本技術資料では、SLS方式プリンタの仕組み、そして機能確認用試作や実製品用部品の量産に広く用いられている理由を紹介しています。ダウンロードしてご覧ください。
SLS方式3Dプリントとは
SLS(粉末焼結積層造形)方式は、高出力レーザーを照射することで粉末状のポリマーを焼結し、3Dモデルをもとに造形するアディティブマニュファクチャリング技術です。
SLS 3Dプリントは、エンジニアや製造業者に何十年も選ばれている技術で、造形単価が低く、生産性が高く使用する材料も確立されていることから、ラピッドプロトタイピングから少量のバッチ生産、量産前のテスト生産、カスタム生産に至るまで幅広い用途に適しています。
SLS 3Dプリンタや材料、ソフトウェアの近年の進化によってより幅広い業種にも応用できるようになった今、これまでは数えるほどのハイテク産業しか導入できなかったツールを活用する企業が年々増えてきています。
高性能SLS 3Dプリントを身近に実現する、Formlabs Fuseシリーズ SLS 3Dプリンタ誕生。
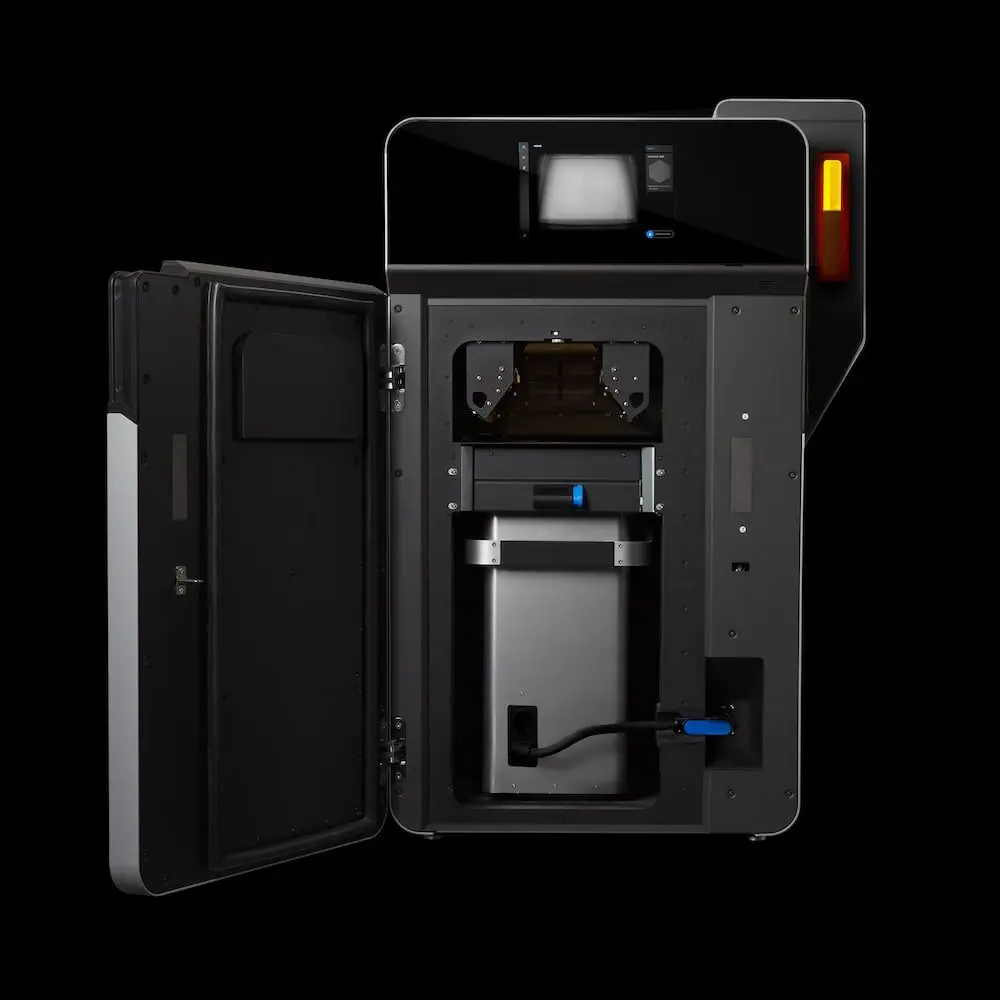
新しいSLS方式プリンタFuse 1+ 30Wで高性能部品を高速製作
本ウェビナーでは、Fuse 1+ 30Wの製品概要やSLS方式3Dプリントの概要をFormlabsのエキスパートがご説明します。
SLS方式 SLS方式3Dプリントの仕組み
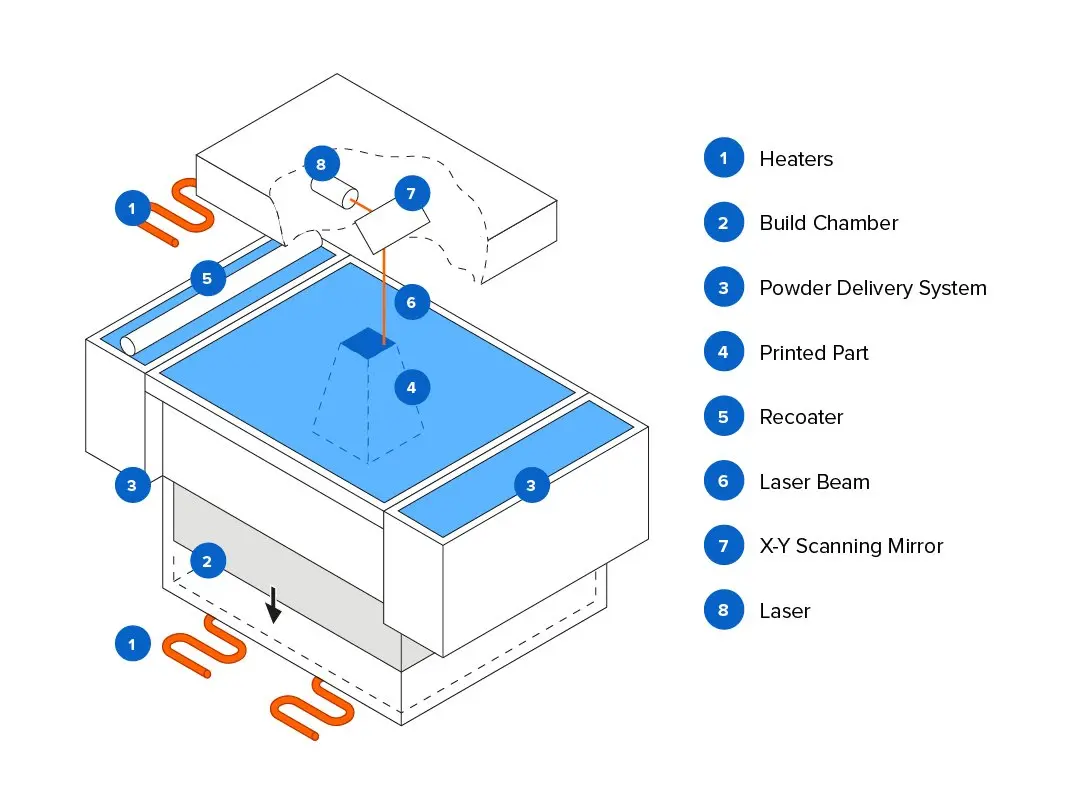
SLS方式のプロセス概略図。SLS 3Dプリンタは、高出力レーザを照射することで粉末樹脂を焼結し、3Dモデルに基づいて造形します。
-
造形:ビルドチャンバー内のプラットフォームにパウダーが薄く敷き詰められます。プリンタが原材料の融点より少し低い温度までパウダーを加熱します。これにより、モデルの形に沿ってレーザーを照射してパウダーを固形化する際、レーザー照射箇所の温度が上がりやすくなります。レーザーで3Dモデルの横断面を走査し、材料の融点より少し低い温度までパウダーを熱します。その結果、パウダーの粒が機械的に焼結し、造形品として固形化されていきます。造形中は未焼結パウダーが造形品を支えるため、専用のサポート材が必要ありません。一層でレーザー走査が終わると、ビルドチェンバーの中でプラットフォームが次の層まで下がります。下降する距離は通常50ミクロンから200ミクロンの間です。この一連の動作が各層で繰り返されることで、造形品が出来上がります。
-
冷却:造形が完了したら、ビルドチャンバーをプリンタ庫内に入れたまま一次冷却します。ビルドチャンバーの温度が下がったらプリンタから取り出し、その後さらにプリンタの外で二次冷却します。こうすることで機械的特性を最大限発揮させ、造形品に反りなどが発生するのを防ぐことができます。
-
後処理:二次冷却が完了したら、ビルドチャンバーから造形品を取り出し、余分なパウダーを除去します。未焼結パウダーは回収して次のプリントで再利用することができます。取り出した造形品には、ブラスト処理または研磨による後処理を施して表面品質を整えます。
作業工程の詳細については、下記の「SLS方式3Dプリントの作業手順」セクションでも解説しています。
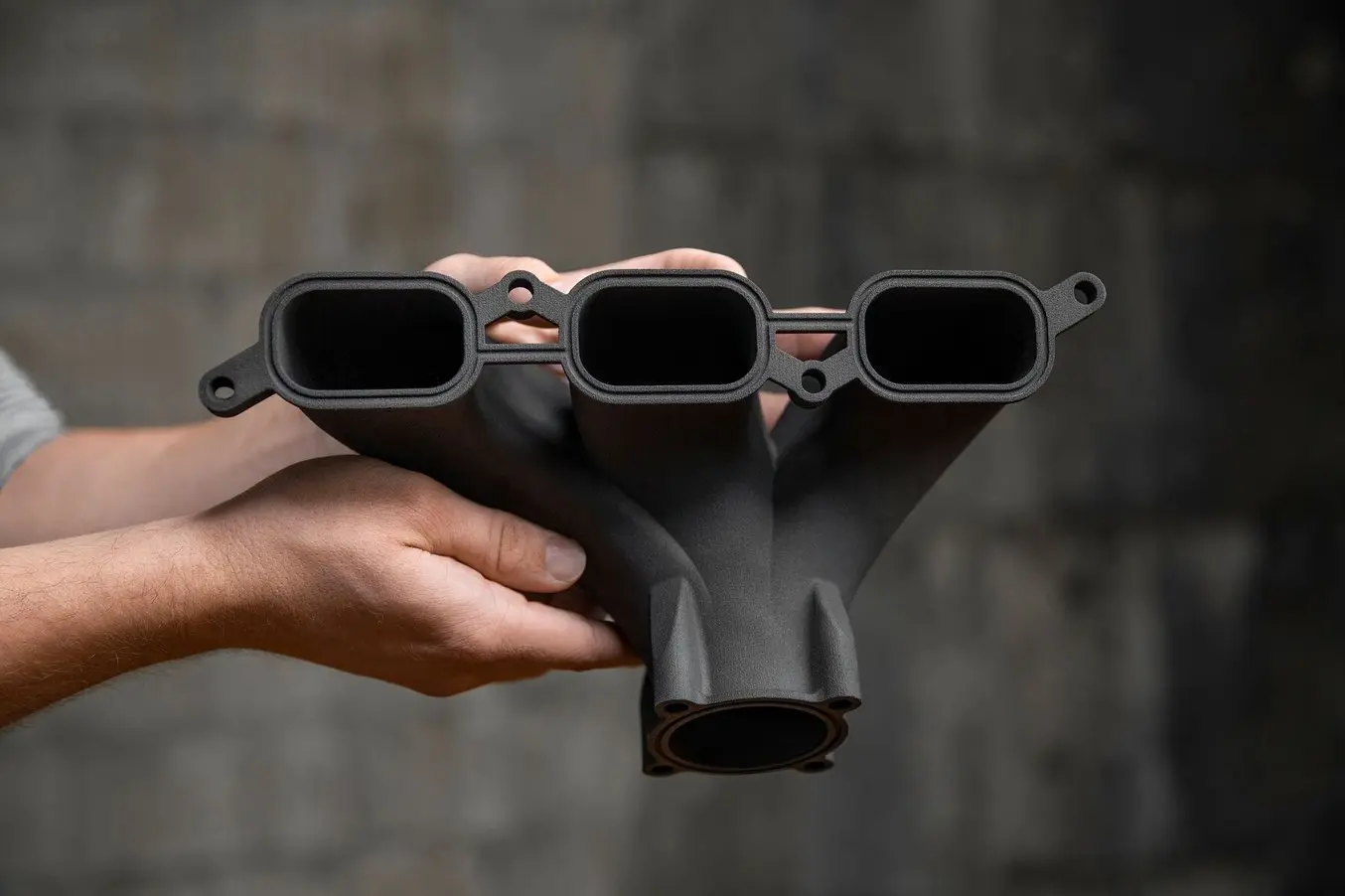
SLSの造形品はざらついた質感を持った表面に仕上がるが、積層痕はほとんど目立たない。より滑らかな表面品質に仕上げたい場合は、ブラスト処理や振動研磨による表面処理が推奨される。画像は、ベンチトップサイズの工業用SLS 3Dプリンタ Formlabs Fuse 1+ 30Wで造形したもの。
造形中は未焼結パウダーが造形品を支えるため、専用のサポート材が必要ありません。そのため、SLSは内部構造、アンダーカット、薄肉構造や中空構造など、複雑な形状の造形に最適です。
SLS 3Dプリント品は、射出成形品に匹敵するほどの高い強度と優れた機械特性を備えています。
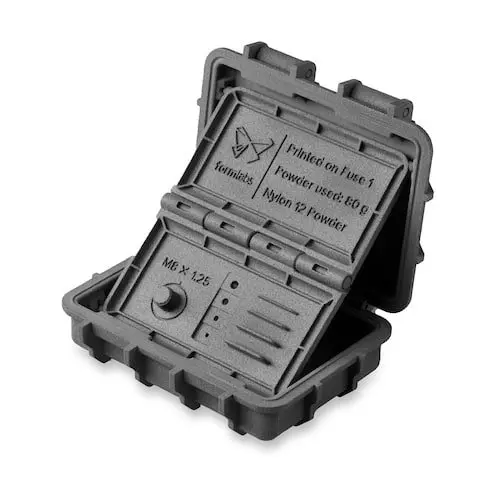
SLS方式3Dプリントの歴史
粉末焼結積層造形方式は、テキサス大学オースティン校のカール・デッカード博士とジョー・ビーマン博士が1980年代中期に開発した最初のアディティブマニュファクチャリング(AM)技術の一つです。それ以降、樹脂、金属、ガラス、セラミック、その他様々な複合材料など、幅広い材料を使った製造に応用されてきました。現在では、粉末をベースとしたSLSやMJFなどのアディティブマニュファクチャリング技術を総称してPBF(粉末床溶融結合法)と呼んでいます。
現在、PBFの中で最も広く普及しているのは、樹脂粉末でのSLS(粉末焼結積層造形)方式と、金属を主原料とするDMLS(直接金属レーザー焼結)方式またはSLM(レーザー粉末焼結積層造形)方式の2種類です。つい最近までは樹脂製・金属製どちらのPBF 3Dプリンタも非常に高額かつ扱いが難しいプリンタばかりであったため、航空宇宙業界向けの部品や医療器具など高付加価値製品や特注部品の少量生産でしか使われていませんでした。
それが近年の目覚ましい技術革新により、樹脂を使用したSLS方式も、SLA光造形方式やFDM(熱溶解積層)方式など他の3Dプリント技術と同様、手頃な価格で導入できる小型プリンタの誕生によって活用範囲の拡大が期待されています。
SLS 3Dプリンタの種類
SLS方式の3Dプリンタの造形工程は前述したとおりです。プリンタごとに違う点は、照射するレーザーの種類、最大造形サイズ、そしてプリンタの複雑さです。温度調節機能や粉末の混合機能、積層方法もプリンタごとに異なります。
SLS方式では、造形工程全体で高い精度と厳格な管理が求められます。例えば、パウダーと造形中のパーツの温度の変動幅は、予熱、焼結、取り出し前の保管の全段階で常に2°C以内に保ち、温度変化によって造形品に反りや変形が発生しないようにする必要があります。
従来型の工業用SLS方式3Dプリンタ
SLSは、3Dプリントの専門業者の間では何十年も前から広く採用されてきた技術です。しかし、その複雑さ、要件の厳しさや設備費用の高さなどから、導入できる業者は受託メーカーや大企業などに限られていました。
さらに、従来型の工業用SLS 3Dプリンタには特殊な換気空調(HVAC)システムと工業用電力が必要で、最も小型の機種でさえ10m²の設置面積が必要です。現場への設置やトレーニングなど、立ち上げまでにも数日間かかります。加えて、プリント工程が複雑で習得が難しいことから、専門知識のある専任技術者が必要となります。
価格は、安価な機種でも一式揃えると$200,000を軽く超えてしまうため、従来型の工業用SLS 3Dプリンタを導入できるのは、資金力がある少数の事業者に限られていました。
Fuseシリーズ: 業界初のベンチトップサイズSLSプリンタ
FDMやSLA光造形等の他の方式と同様、SLSにも低価格でコンパクトなプリンタが最近の市場には登場していますが、当初それらのプリンタには、造形品質の問題や複雑で手間のかかる後処理工程などかなりの妥協点があり、工業用や生産現場で広く使われることはありませんでした。
FormlabsのFuse 1はこの課題を克服し、優れた造形品質、省スペース、プリントから後処理までの一貫した作業手順の簡素化を実現し、従来の工業用SLSプリンタの数分の一の価格で導入できる業界初のベンチトップサイズの工業用SLS 3Dプリンタとして誕生しました。次世代機であるFuse 1+ 30Wはさらにパワーアップし、Fuse 1よりも高いレーザー出力と粉末の取り扱い能力で、対応可能な材料の幅も広がり、ハイエンド機と同等の造形品質と高いスループットを実現します。

Fuseシリーズを導入する場合は特殊なインフラ整備は不要で、一般的な作業スペースに簡単に設置できる。
Fuseシリーズ SLS方式3Dプリンタは単一のレーザーを使用し、ビルドチャンバーも小型化しているため、加熱出力も少なくて済みます。また、消費電力も低く、稼働に必要なのは標準のAC電源だけなので、特殊なインフラを整備する必要もありません。Fuse 1 + 30Wプリンタに搭載されているオプションの不活性ガス(窒素)充填機能では、プリンタ内に不活性ガス環境を作り出し、未焼結パウダーの質を維持することで材料のリフレッシュ率を低く抑えます。つまり、次のプリントで新しいパウダーよりも再利用パウダーの使用比率を増やすことができ、粉末のロスを最小限に抑えながら造形品の表面品質も向上させます。
さらに、特許出願中のSurface Armorテクノロジーにより、各造形品の表面外周に半溶融状のシェルを形成することで熱を均等に保ち、優れた機械的特性と表面品質、安定性と高いリフレッシュ率を実現します。
また、造形品の取り出し、パウダーの回収と保管、新品パウダーと再利用パウダーの自動ミキシングまで全てを1台で担う粉末回収ステーションFuse Sift、そして造形品のブラスト処理と研磨を完全自動で行うFuse Blastとともに、Fuseシリーズは全工程をオールインワンで提供します。
Fuseシリーズのようなベンチトップ型の工業用SLS方式3Dプリンタは、最大造形サイズの観点では従来のSLSプリンタの最小機よりも若干小さくなるものの、ビルドチャンバーが小さいことで設置面積が大幅に削減でき、作業手順も簡素化され、コスト削減が可能になります。
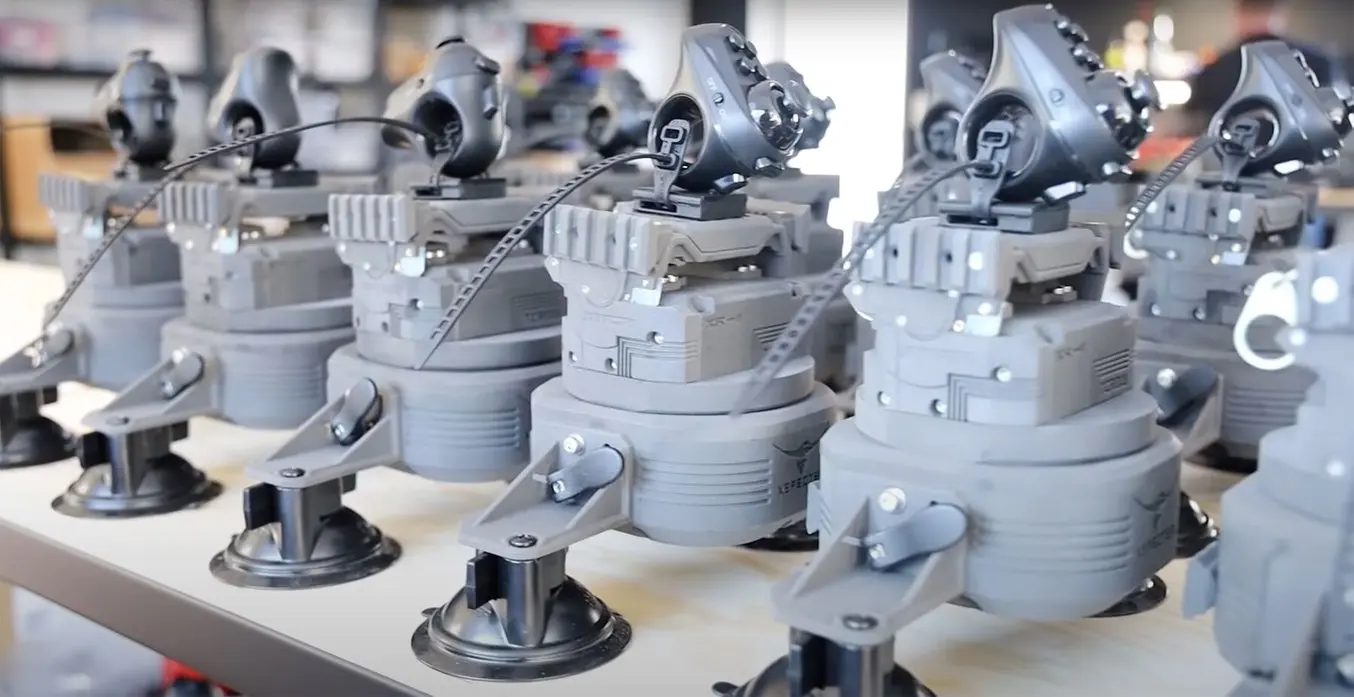
SLSを実製品の量産に活用
単に実製品の量産工程に3Dプリントの導入が可能なだけでなく、SLS Fuseシリーズを活用することでさらに安価かつ迅速に、規模の拡大にも柔軟に対応できるようになります。量産方法の比較、パウダーのボリュームディスカウントの詳細、現在Fuseシリーズを実際に量産工程に取り入れているメーカー15社の事例をご覧ください。
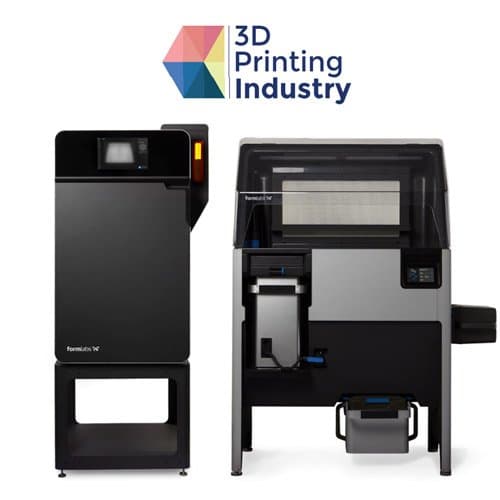
3D Printing IndustryによるFomlabs Fuse 1とFuse Siftの徹底レビュー
本技術資料では、3Dプリント関連メディア3D Printing IndustryのエンジニアによるFormlabsのSLS方式3Dプリンタの徹底レビューと精度試験の結果をご覧いただけます。
SLS方式3Dプリンタの比較
Fuse シリーズ: ベンチトップサイズの工業用SLS方式3Dプリンタ | 従来型の工業用SLS方式3Dプリンタ | |
---|---|---|
価格 | プリンタ本体:$30,000以下、一式:$60,000以下 | $200,000〜$500,000以上 |
造形サイズ | 165 x 165 x 300 mm | 最大550 x 550 x 750mm |
長所 | 手頃な価格 造形品質の高さ 高いスループット 複数の材料が使用可能 簡素化された作業手順 狭い設置面積 省メンテナンス | 大きなビルド容積 造形品質の高さ 高いスループット 複数の素材オプション |
短所 | 造形量が少ない | 機器が高額 設置面積が大きい 設備要件 高メンテナンス 専任のオペレータが必要 |
この比較情報は、Formlabs Fuseシリーズ ベンチトップ型工業用SLSプリンタをEOS社と3D System社の従来型のSLSプリンタと比較した結果に基づいています。
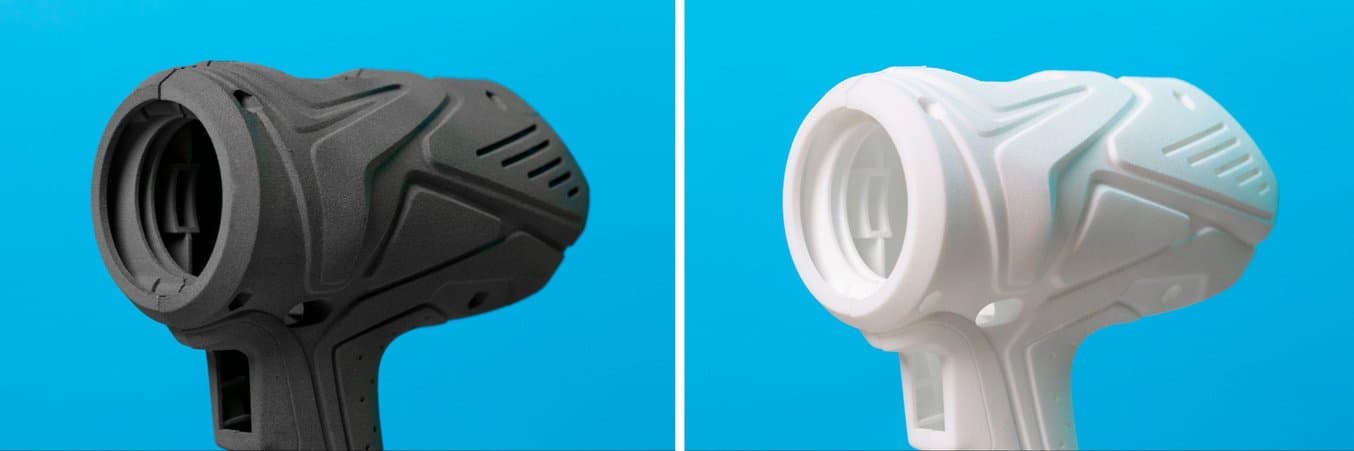
Fuse 1+ 30W(左)とEOSプリンタ(右)でプリントしたドリルの試作品。品質は同等ながら機器価格が大きく異なる。
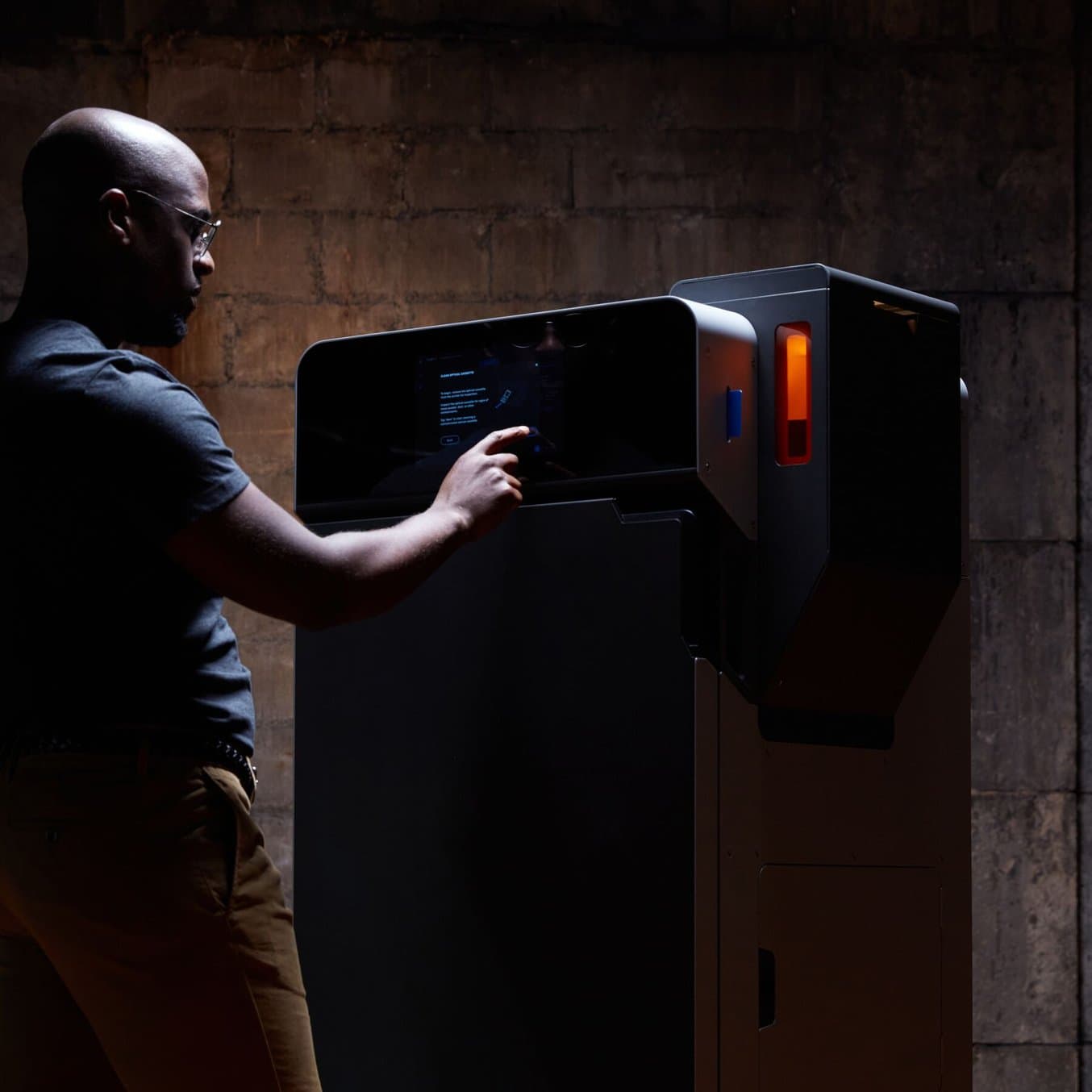
外注か内製か:SLS方式3Dプリントが適するケースとは?
本技術資料では、SLS方式3Dプリンタでの内製と、SLSプリント品を外注で製作した場合を比較し、SLS 3Dプリンタの導入の費用対効果の評価を行います。
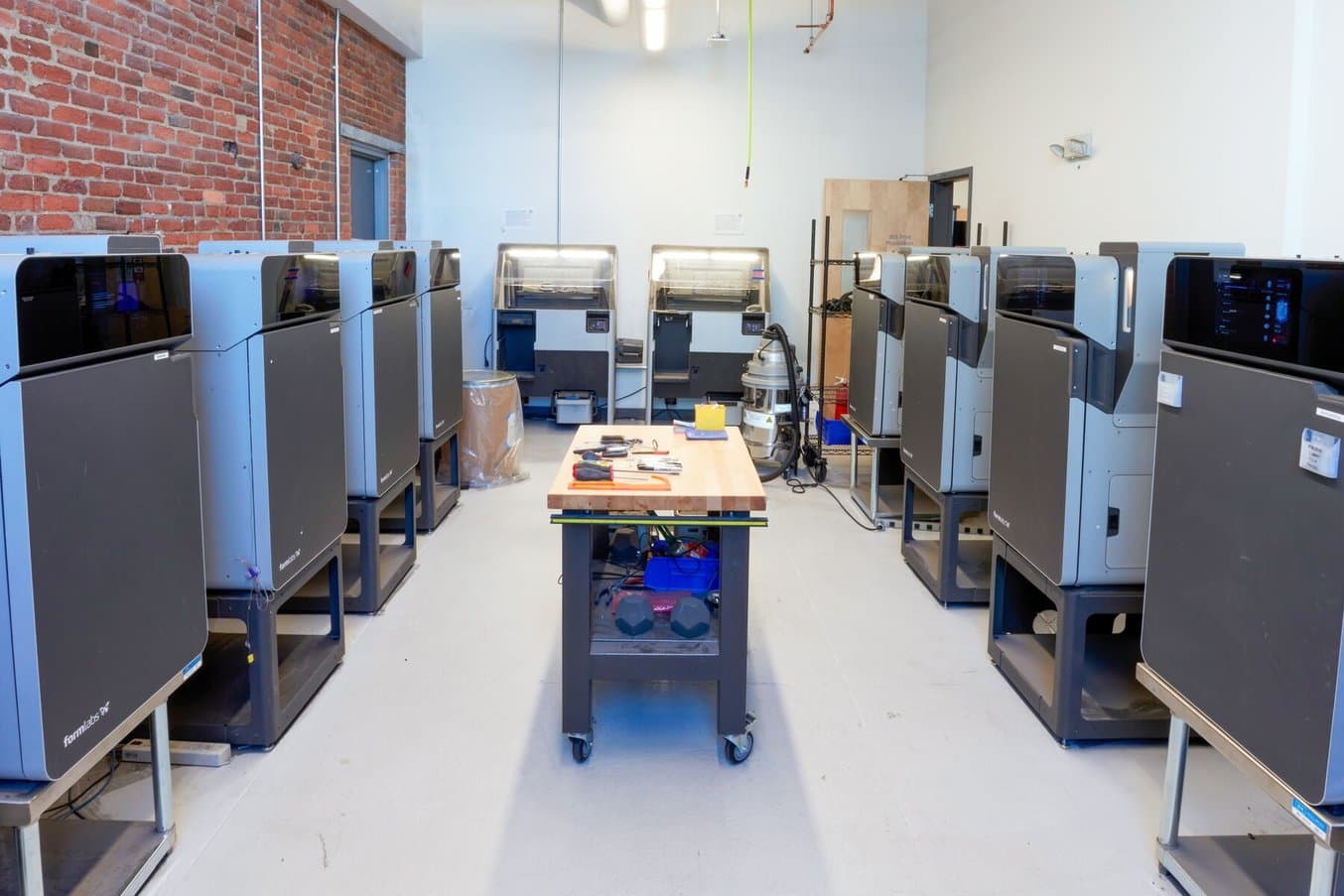
Fuseシリーズ SLSプリンタと従来の粉末床溶融結方式プリンタの比較
この比較ガイドでは、FormlabsのFuseシリーズに代表されるコンパクトサイズのSLSプリンタと、広い設置面積が必要な従来型の大型プリンタについて、主な違いを解説しています。
SLS方式3Dプリント材料
SLS(粉末焼結積層造形)方式の材料として最も一般的なのがナイロンです。ナイロンは、機能確認用の試作品制作と実製品の製造の両方に使用できる高機能なエンジニアリング系熱可塑性プラスチックです。複雑な構造を持つ部品や、過酷な環境下で使用される高耐久性部品に適しています。
ナイロンを使ってSLSでプリントした造形品は、強度、剛性、耐久性に優れています。後処理を終えた完成品は、耐衝撃性が高く、繰り返し使用しても摩損せずに長く使い続けられます。ナイロンを使って3Dプリントした造形品は、紫外線、光、熱、湿度、溶剤、温度、水に対する耐性があり、生体適合性で感作性がないため、着用が必要な用途やその他様々な用途でも安全に使用できます。
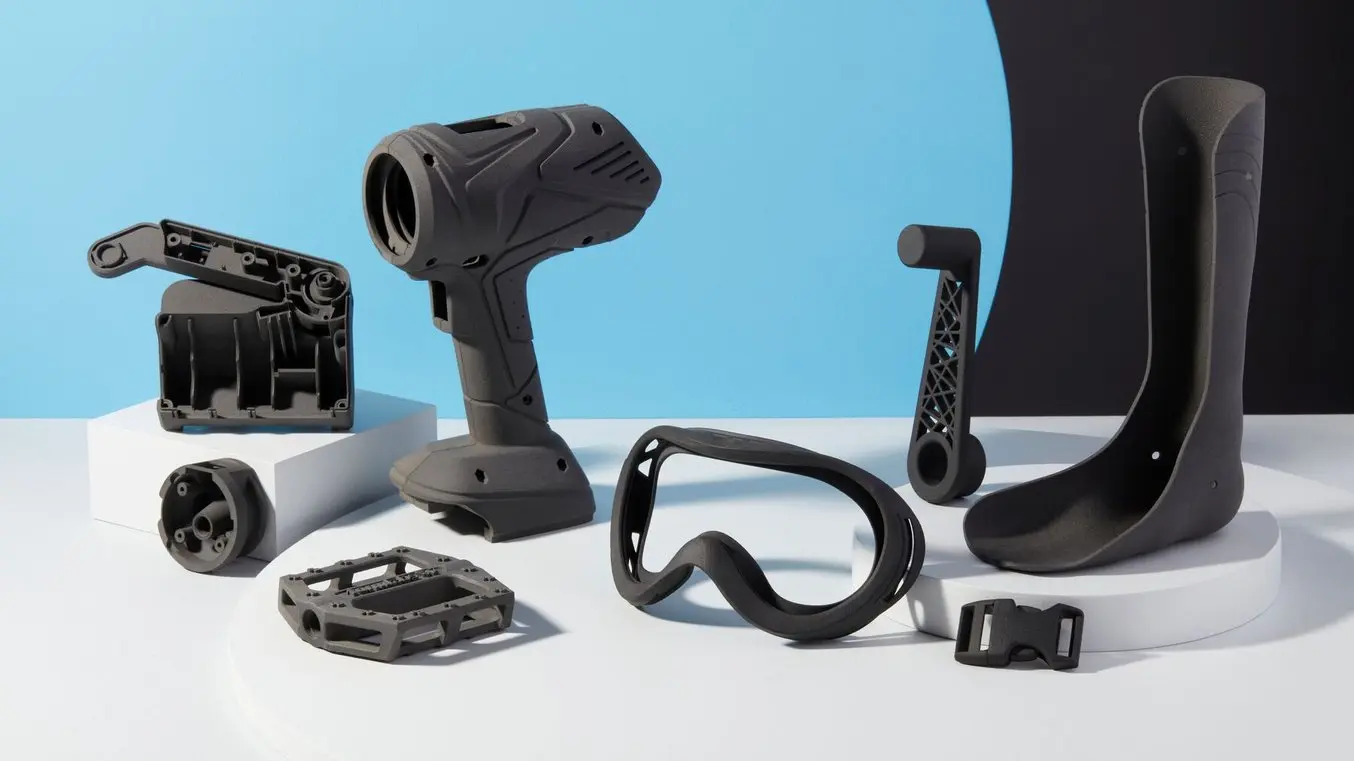
ナイロンは、工業用の消費者製品からヘルスケア用品に至るまで幅広い機能的用途に適した材料として活用されている。
ナイロンは、ポリアミド(PA)系に属する熱可塑性樹脂材料で、幅広い用途に合わせて様々な種類が開発されています。Nylon 12とNylon 11は最も一般的に使用される単一材料です。どちらもガラスや炭素繊維などその他の材料を混ぜ合わせることで強度や硬度、耐熱性などを強化した複合材にすることも可能です。
ナイロンの他に3Dプリント用材料として高い需要があるものは、PP(ポリプロピレン)です。PPは機能的な軽量部品の製作に最適です。PP製の射出成形品で一般的な機械的特性、そして過酷な環境下にも耐える耐久性で、試作品や実製品用途に向いています。
SLS方式3Dプリンタでは、熱可塑性ポリウレタン(TPU)を使った複雑な形状の軟質部品も簡単に製作できます。TPUは高い引張強さと破断伸びを兼ね備えたゴム製材料で、広い用途に活用できるSLS方式3Dプリンタにより、柔らかい感触で皮膚に触れても安全な試作品や、日々の使用にも耐える実製品用部品が製造できます。
使用できる材料は、プリンタの機種によって異なります。Fuse 1+ 30Wで使用できる材料は以下の通りです。
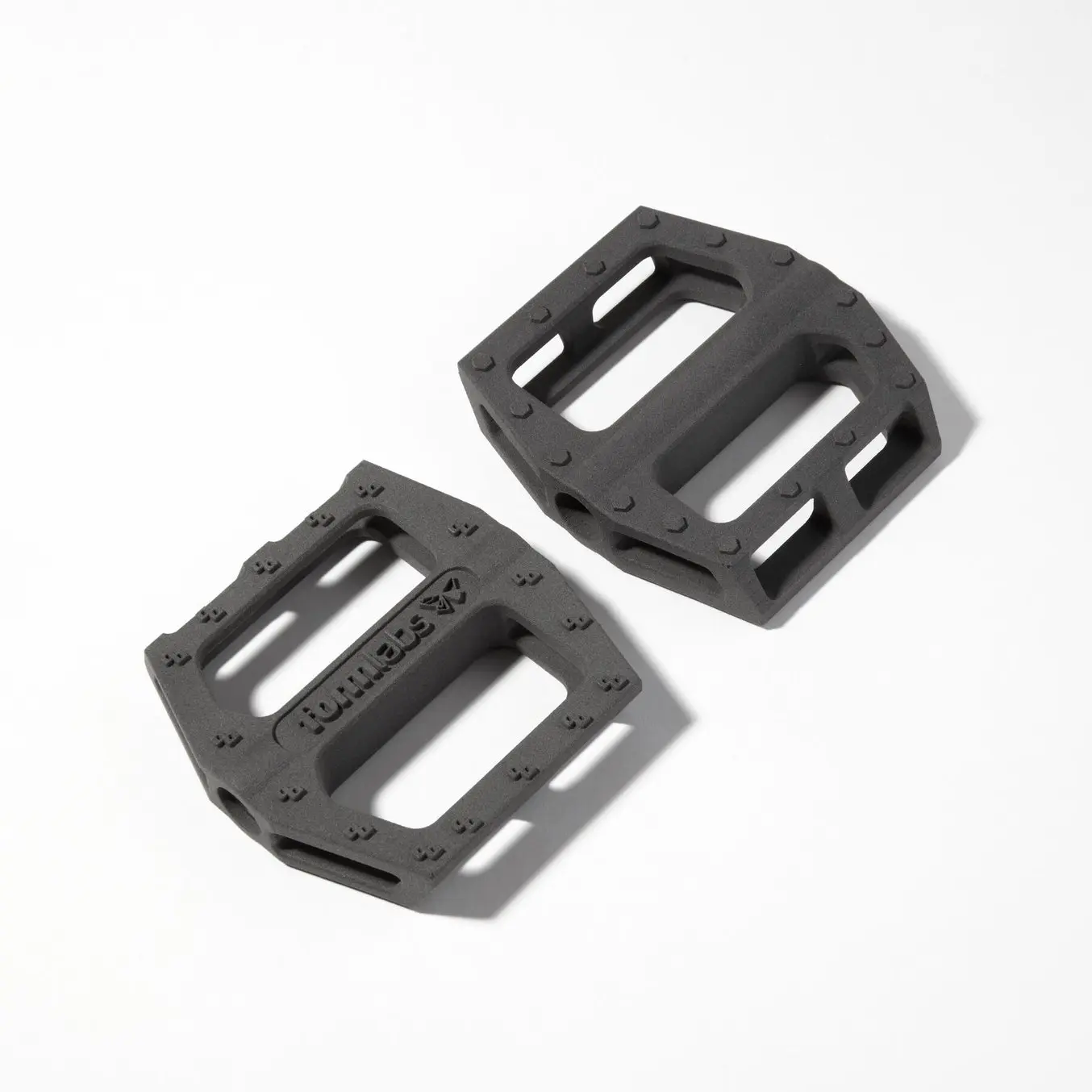
Nylon 12パウダー
ディテール表現と寸法精度に優れた多用途万能材料
- 高性能プロトタイピング
- 小ロットのバッチ生産
- 長期使用に耐えられる各種治工具
- 減菌可能な生体適合性パーツ*
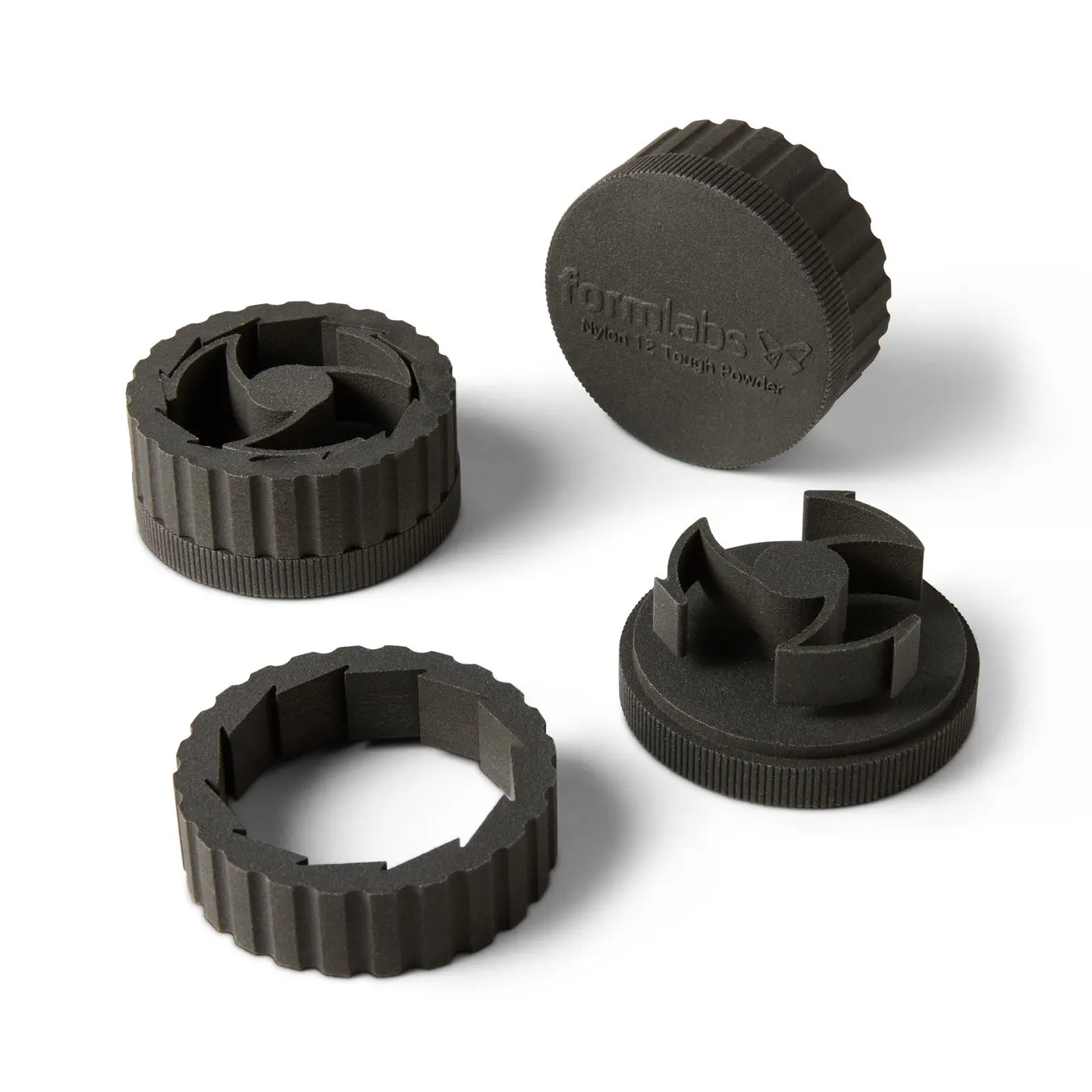
Nylon 12 Toughパウダー
最高クラスの靭性、リフレッシュ率、寸法精度を実現。
- 高性能で耐衝撃性のあるプロトタイプ
- 靭性が求められる部品(スナップ、ラチェット、ヒンジなど)
- 長く反りやすい部品
- 強い衝撃や摩耗に晒される実製品用部品
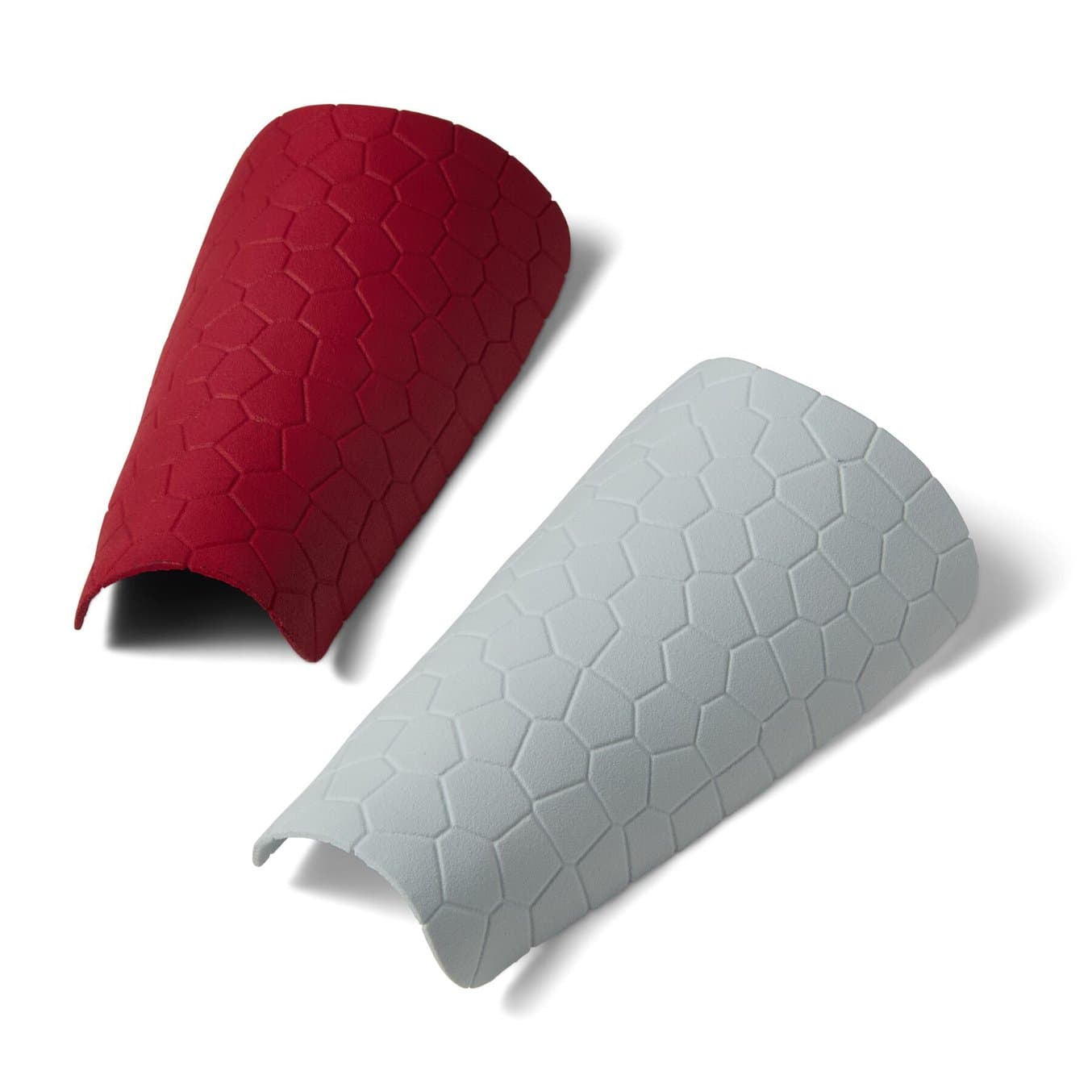
Nylon 12 Whiteパウダー
Nylon 12パウダーの信頼性、耐久性、強度はそのままに、染色や着色によるカスタマイズが可能に。
- 染色、塗装、その他方法による着色が必要な部品
- ブランドデザインを適用した外観確認用試作
- 生体適合性を備えた医療器具やサージカルガイド*
- 小ロットのバッチ生産
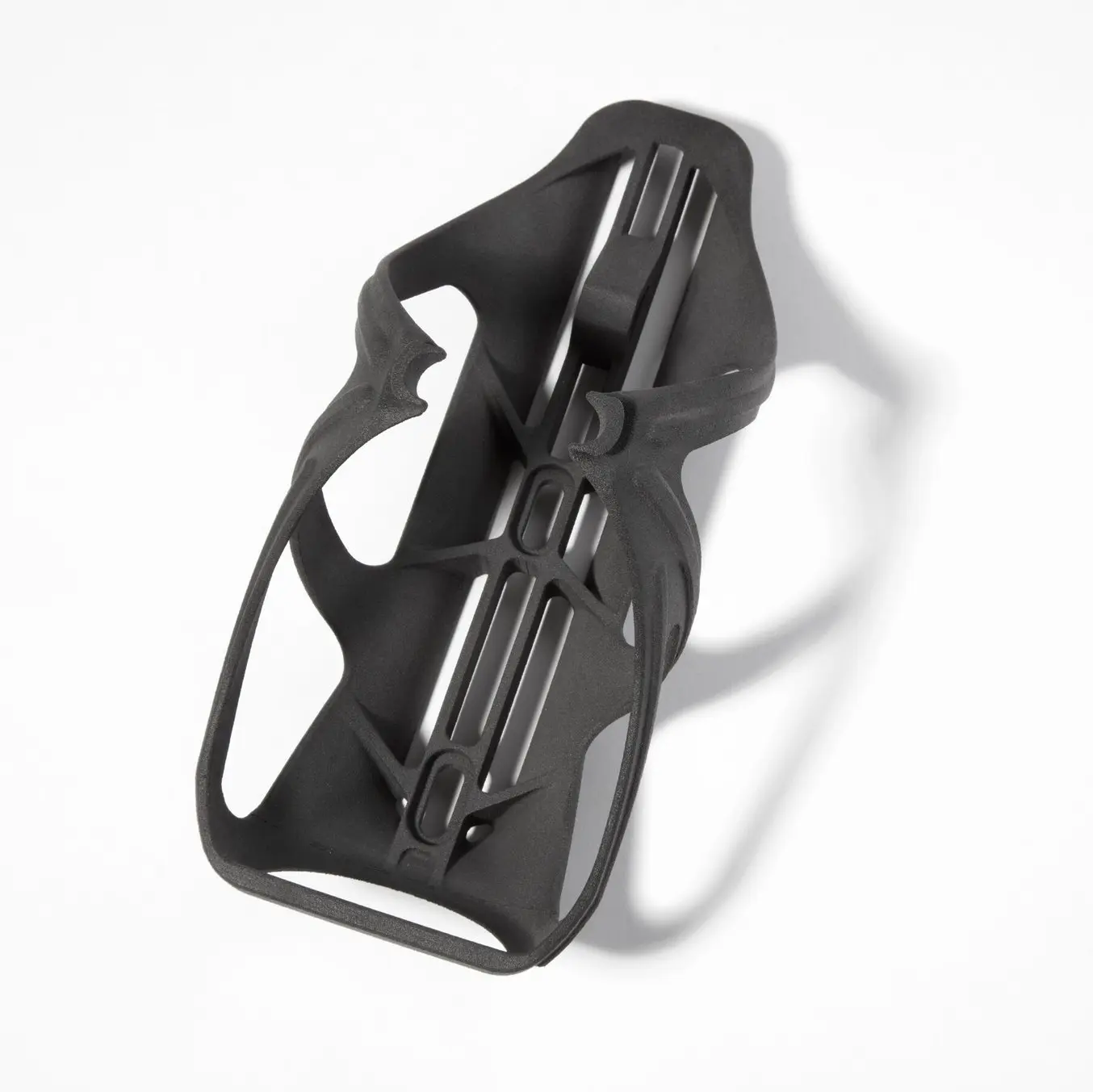
Nylon 11パウダー
高い靭性と性能が求められる用途に適した、高靭性・高強度材料
- 耐衝撃性が必要な試作品や治工具
- 薄肉構造の筐体やダクト等
- スナップやクリップ等の留め具や蝶番
- 歯列矯正用器具や人工装具*
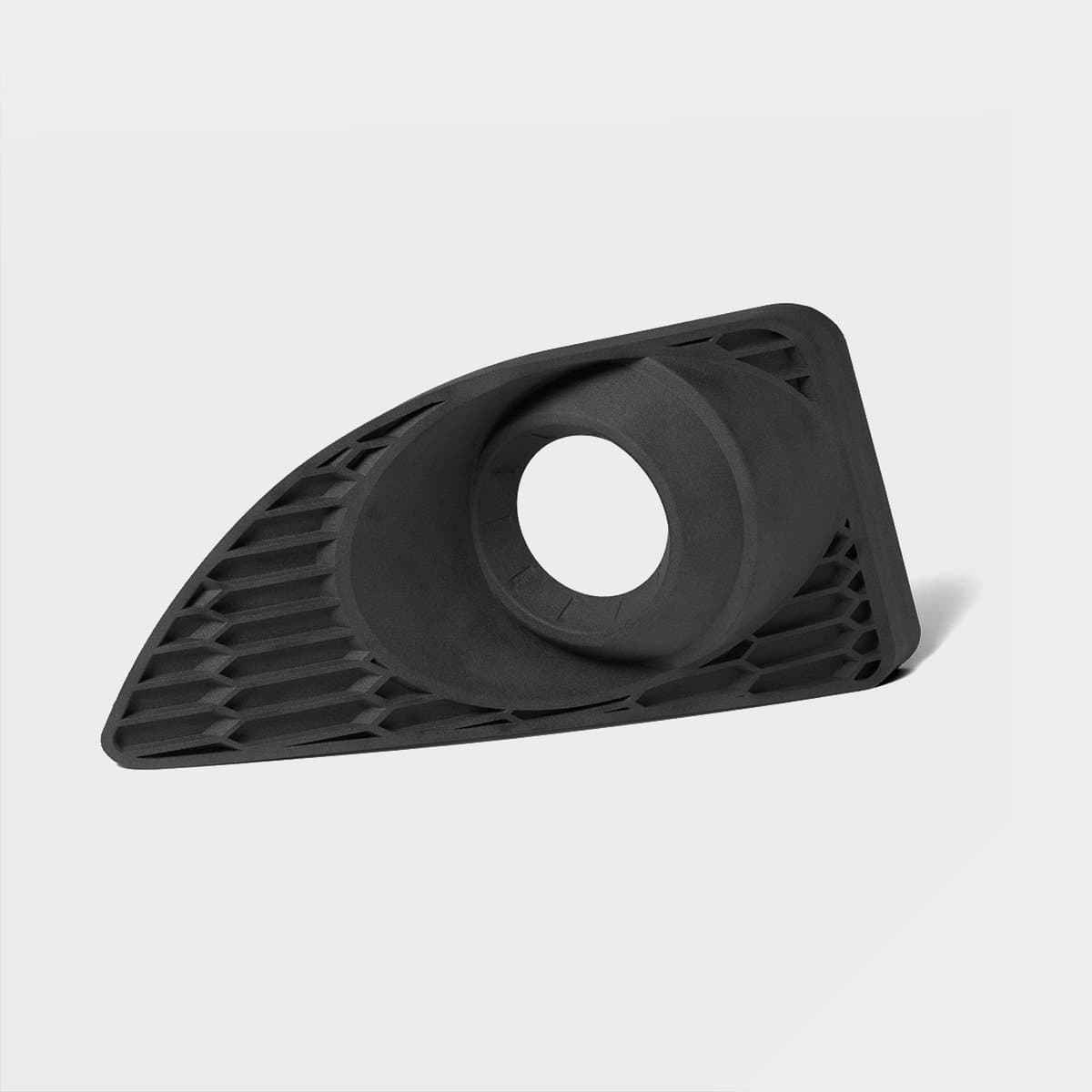
Nylon 12 GFパウダー
ガラス充填により高剛性・高耐熱化。過酷な環境下での使用に対応できるよう開発されたガラス繊維強化材料
- 高い強度が求められる治工具や交換部品
- 恒常的な負荷にさらされる部品
- ねじやソケット
- 高温環境下に置かれる部品
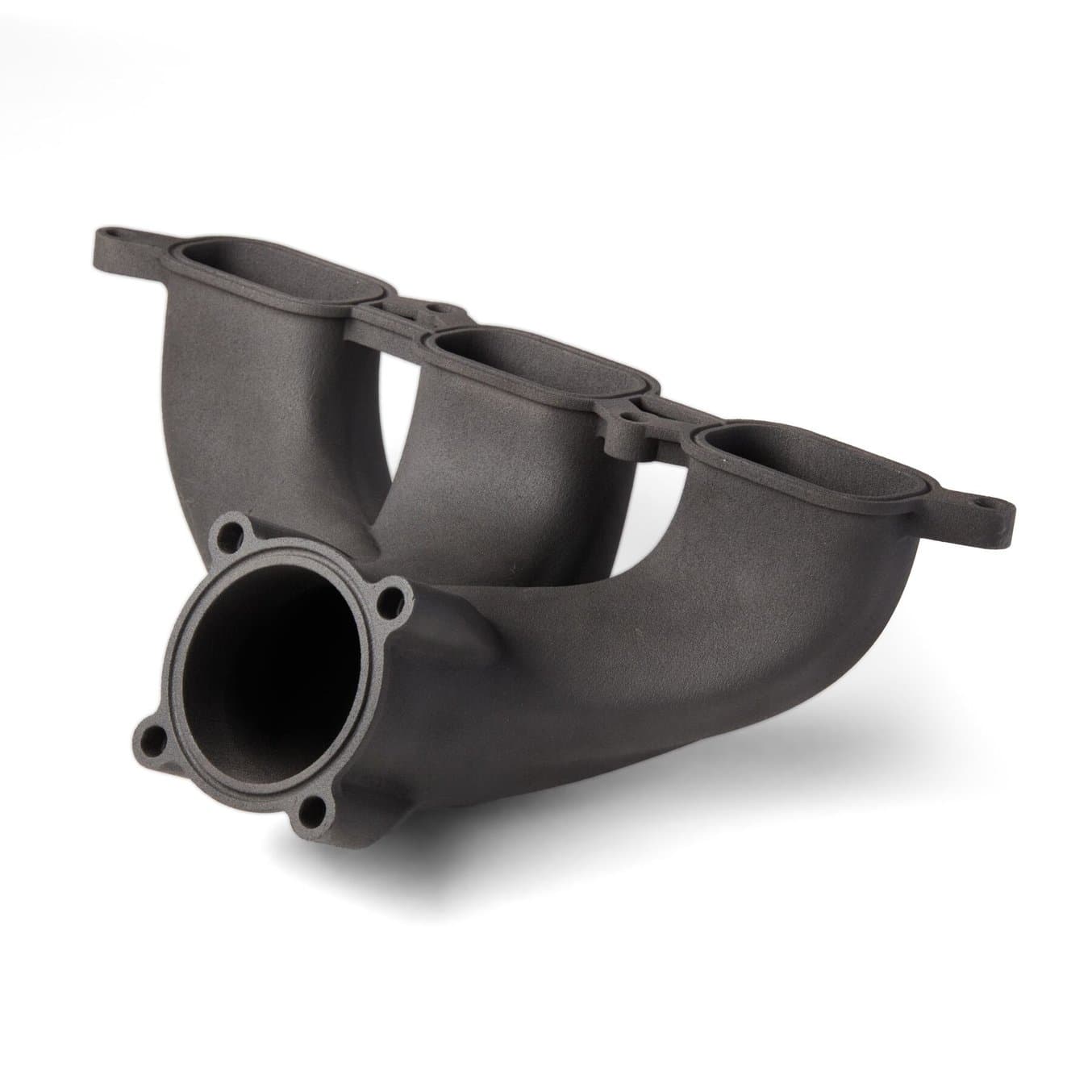
Nylon 11 CFパウダー
ナイロン材と炭素繊維材の長所を兼ね備えた、安定性が高く軽量な高機能材料
- 金属製の交換部品およびスペアパーツからの置き換え
- 金型、治工具
- 耐衝撃性が求められる機器
- 複合材による機能確認用試作
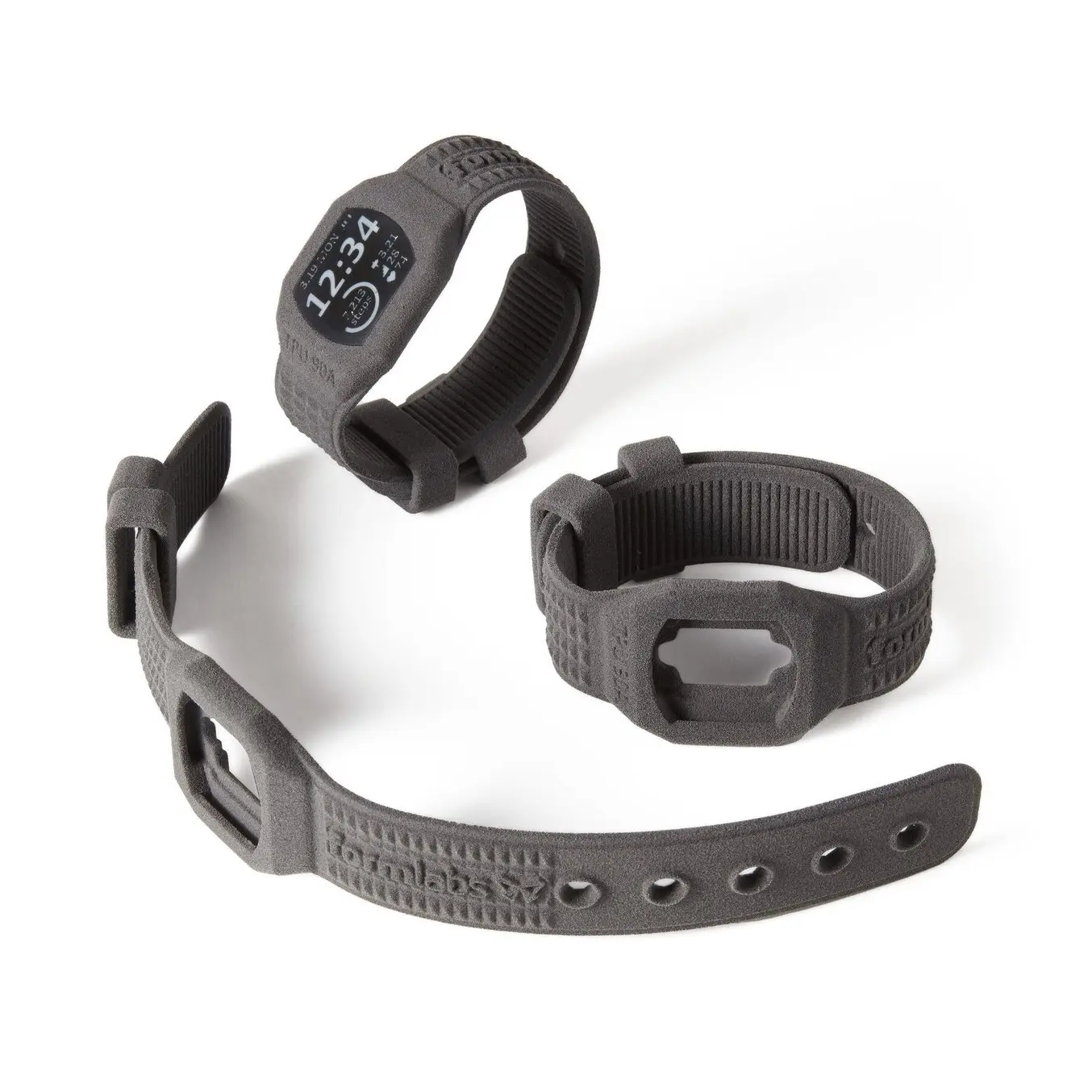
TPU 90Aパウダー
柔らかい感触で皮膚に触れても安全な試作品や実製品用部品の製造に最適な、高い引張強さと破断伸びを兼ね備えたゴム製材料。
- 柔らかい感触のウェアラブル
- パッド、ダンパー、クッション、グリッパー
- ガスケット、シール、マスク、ベルト、プラグ、チューブ
- ソール、スプリント、歯列矯正用器具、義肢装具*
*材料特性は造形品の設計や造形方法により変動する場合があります。造形した製品が目的の用途に適しているかどうかの検証は、製品製造者の責任となります。
FormlabsのSLS用パウダー:材料特性の比較
材料 | Nylon 12パウダー | Nylon 12 Toughパウダー | Nylon 12 Whiteパウダー | Nylon 11パウダー | Nylon 12 GFパウダー | Nylon 11 CFパウダー | TPU 90Aパウダー |
---|---|---|---|---|---|---|---|
最大引張強さ(X軸/MPa) | 50 | 42 | 47 | 49 | 38 | 69 | 8.7 |
最大引張強さ(Y軸/MPa) | N/A | N/A | N/A | N/A | N/A | 52 | 8.7 |
最大引張強さ(Z軸/MPa) | N/A | N/A | N/A | N/A | N/A | 38 | 7.2 |
引張弾性率(X軸/MPa) | 1850 | 1450 | 1950 | 1600 | 2800 | 5300 | N/A |
破断伸び、X/Y (%) | 11 | 25 | 8 | 40 | 4 | 9 / 15 | 310 |
破断伸び(Z軸/%) | 6 | 15 | 6 | N/A | 3 | 5 | 110 |
荷重たわみ温度@0.45 MPa(°C) | 171 | 161 | 177 | 182 | 170 | 188 | N/A |
ノッチ付アイゾット(J/m) | 32 | 60 | 28 | 71 | 36 | 74 | N/A |
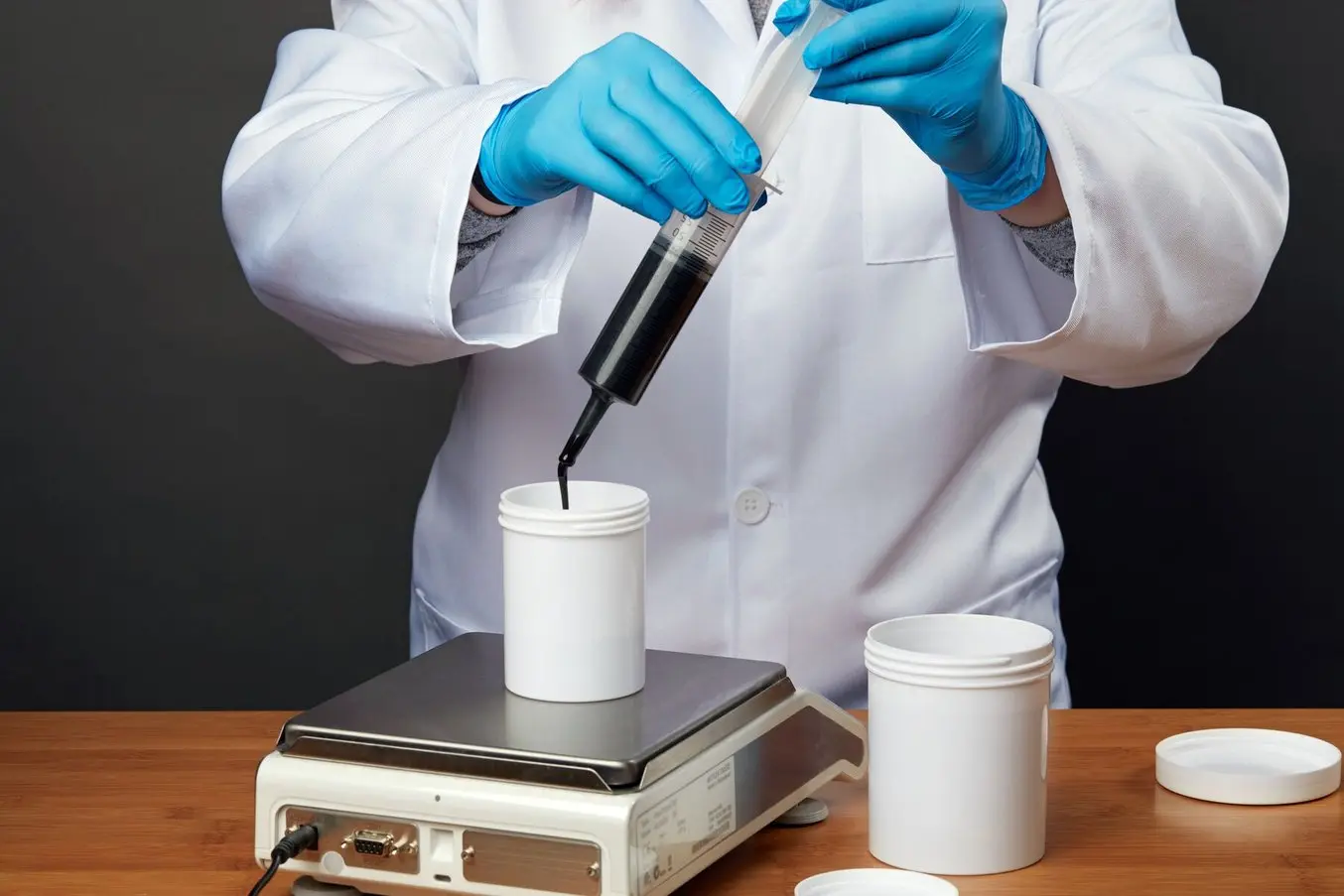
Formlabsが遂にオープンに
Formlabs Developer Platformでお使いの3Dプリンタの可能性を最大限に引き出してみませんか。波長405nmのUV光に対応するレジンや、波長1,64nmのレーザー光に対応するパウダーをFormlabsの3Dプリンタでご利用いただけるほか、造形設定のカスタマイズや他社ソフトウェアとの統合機能も実装できます。
SLS方式3Dプリントの活用例
SLS方式による3Dプリントは、イノベーションを加速させ、エンジニアリングや製造業、ヘルスケア業界など幅広い分野で多くの企業に採用されています。
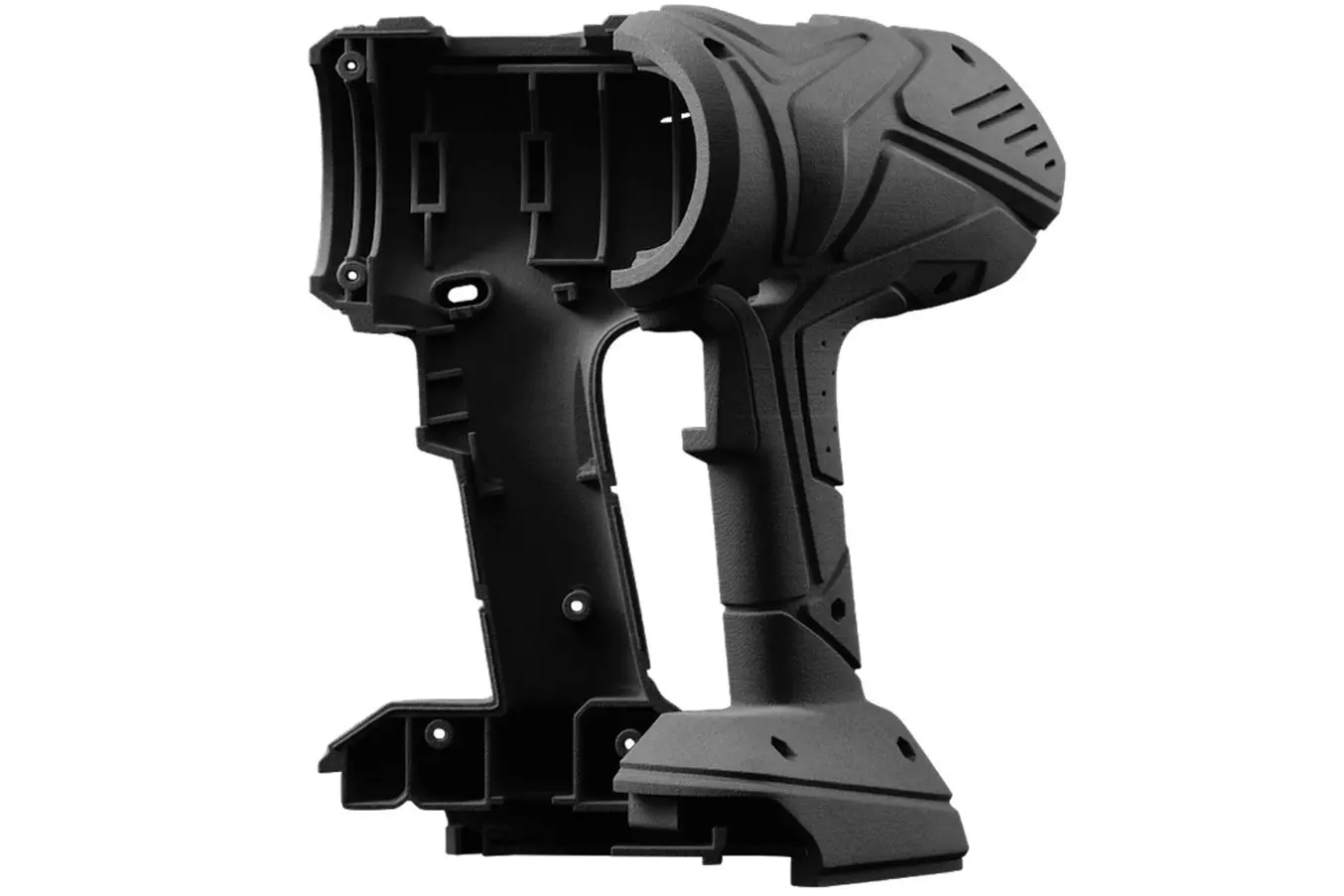
エンジニアリング
コンセプト設計の試作品製作、検証と改良を加えながらの設計内容の確定、実製品の製造に移るまでの製品開発工程全般をコントロール。
- ラピッドプロトタイピング
- 実際の現場でお客様に試用して貰うための製品モックアップ
- 機能確認用試作
- 機能検証用部品(例:配管、ブラケット)
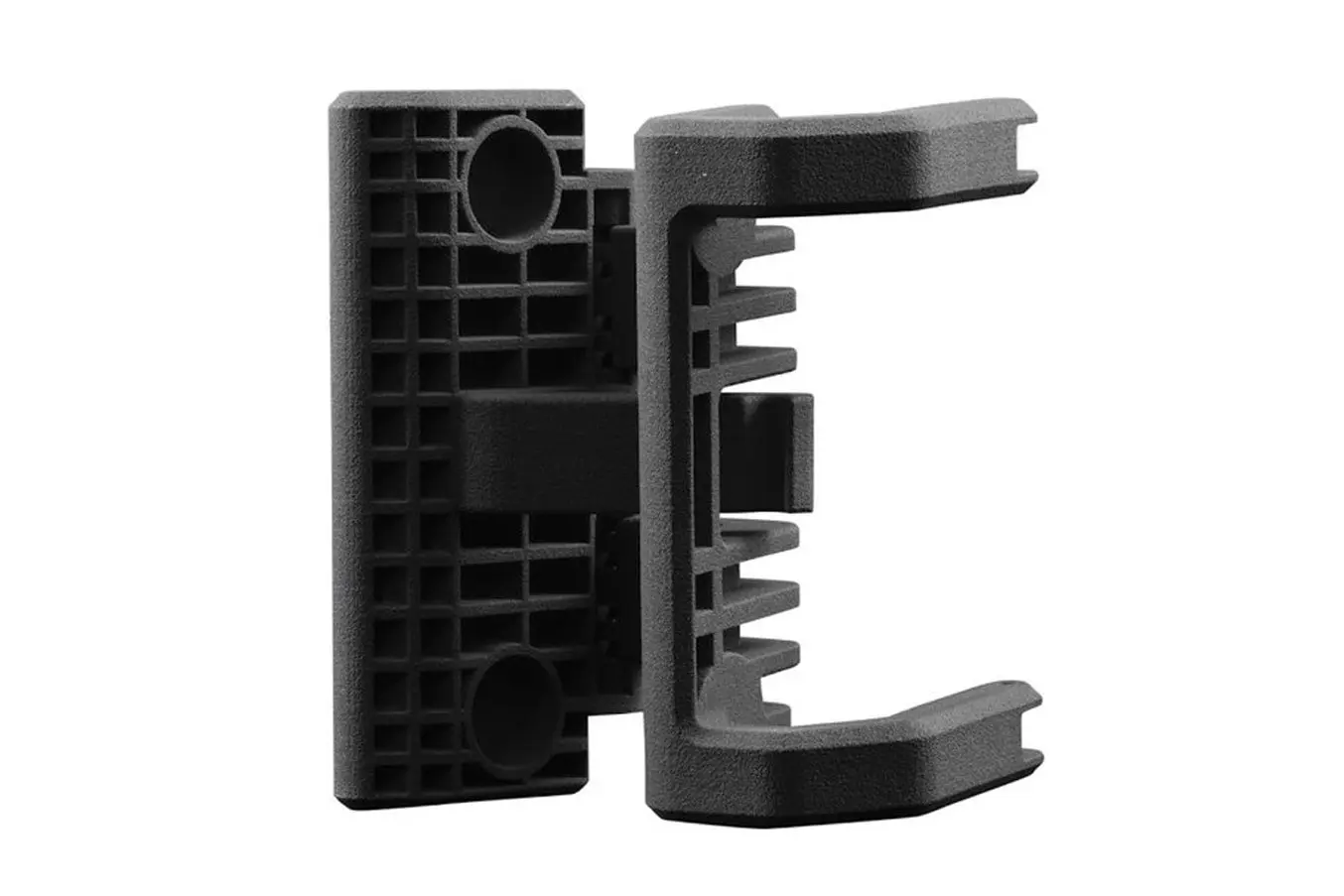
製造業
独自のサプライチェーンを確立し、変化し続ける需要に即応可能に。
- 実製品用部品の製造
- 小ロット量産、臨時生産、量産移行前のテスト生産
- マスカスタマイゼーションによる消費者製品
- 交換用部品、アフターマーケット部品、スペアパーツ
- 長期使用を前提とした耐久性の高い治具、固定具、成形型
- 特注の自動車またはバイク用部品、舶用機器、オンデマンドの補給用軍用品
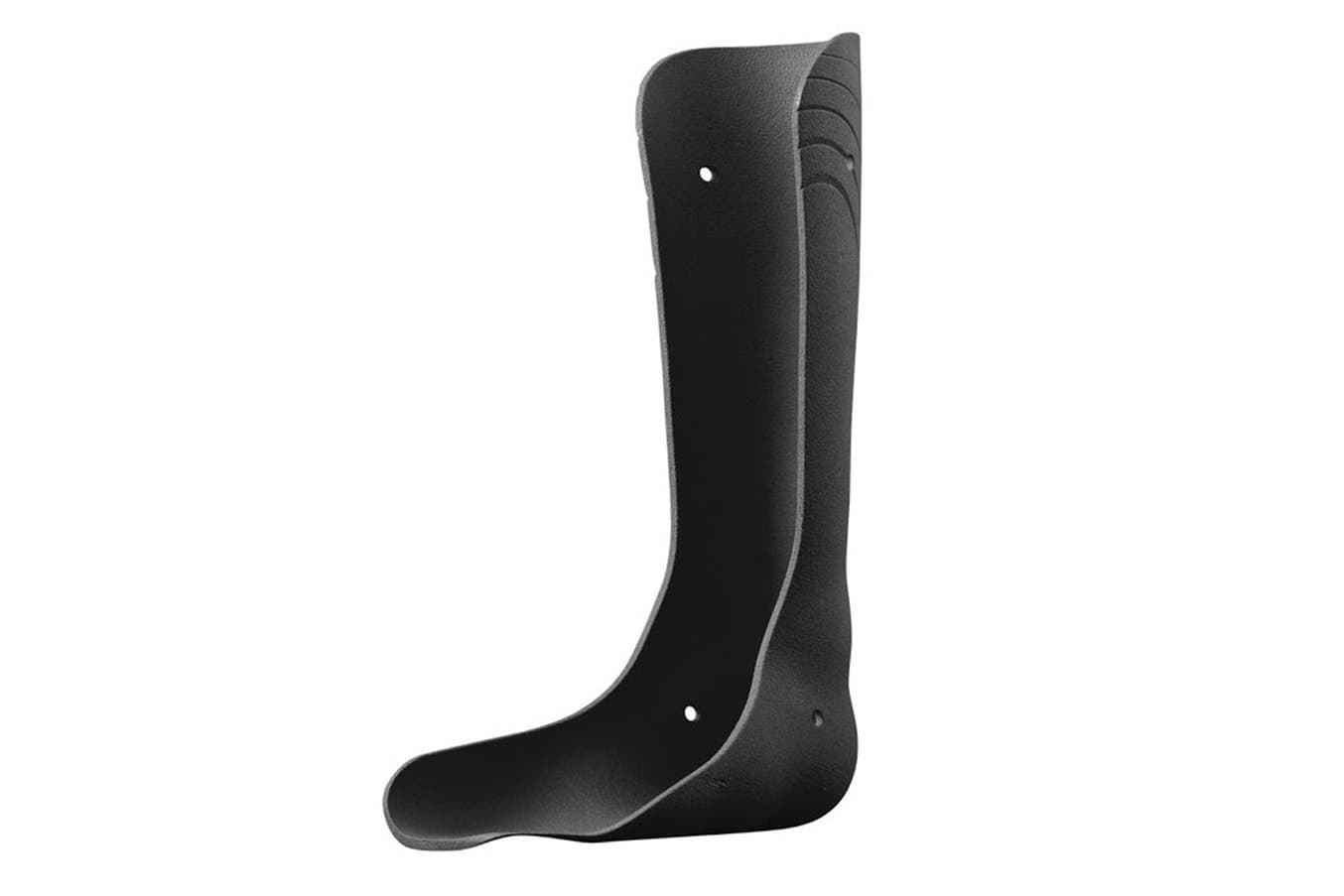
ヘルスケア
製造したらすぐに使える、各患者向けに調整された医療器具の内製化。
- 医療器具のプロトタイピング
- 人工装具や矯正器具(例:義足やサポーター)
- 外科手術用の模型や器具
- 実製品用部品*
* 材料特性は造形品の設計や造形方法により変動する場合があります。プリントした造形品が目的の用途に適しているかどうかの検証は、製造者の責任となります。
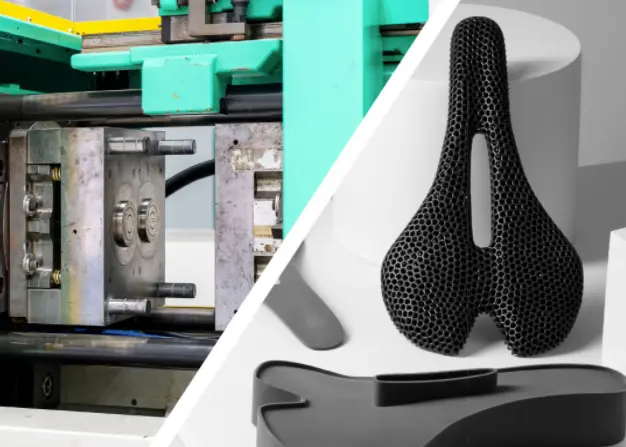
SLS 3Dプリント vs 射出成形:金型レスに切り替えるべき時は?
本技術資料では、実際のユースケースに基づいてコストの違いを解説するとともに、SLS方式3Dプリント、射出成形、またそれらの併用についてのガイドラインをご紹介します。
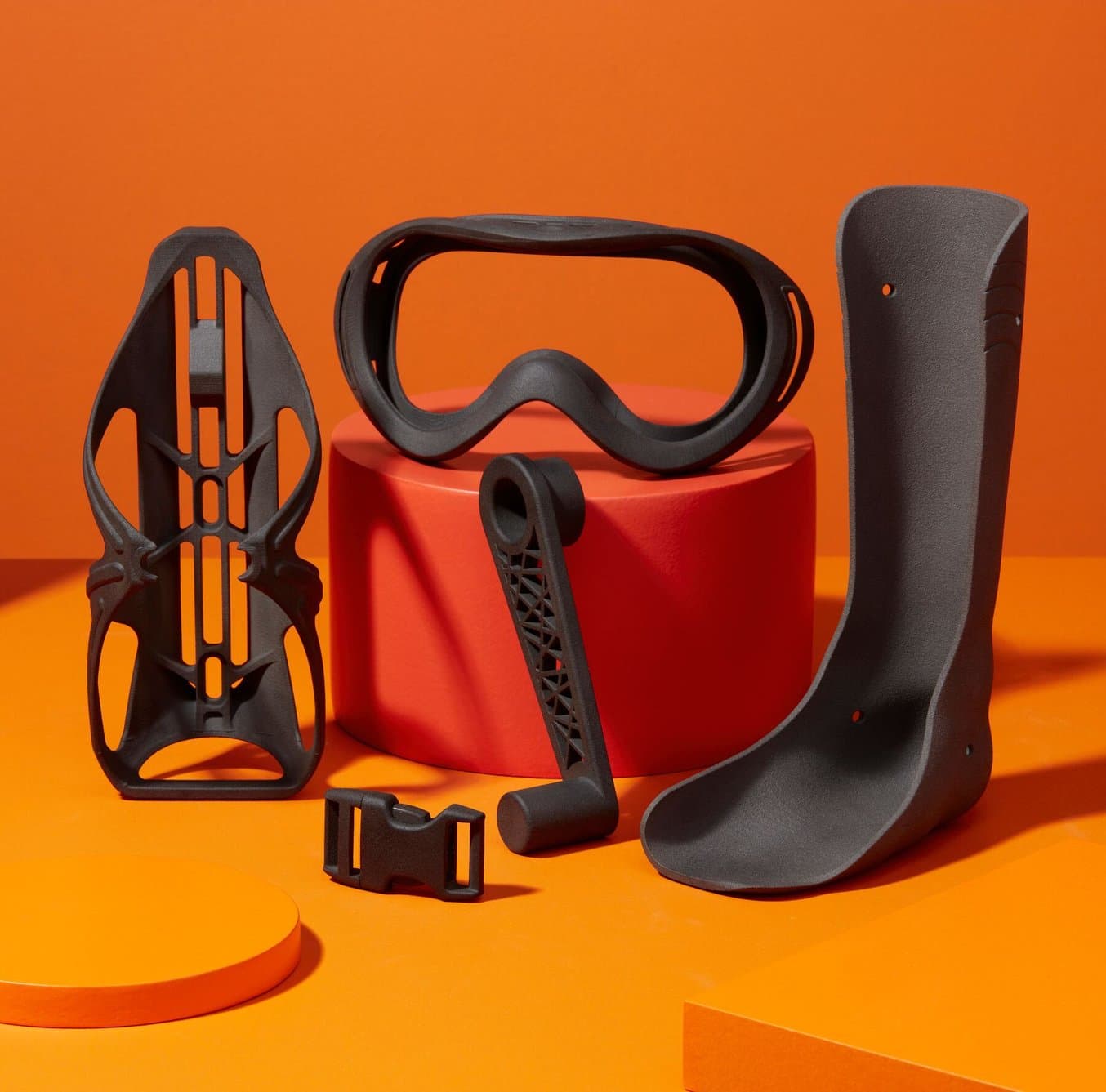
SLS 3Dプリントが最適な用途を見極める方法
このウェビナーでは、ハイエンド機と同等の高品質な造形品を低コストで製作できるSLS 3Dプリンタにより、AM技術の活用範囲が実製品製造やカスタム部品の大量生産にまで広がっている理由をご紹介します。
SLS方式3Dプリントの作業手順
本動画では、FormlabsのSLS方式3Dプリンタ Fuseシリーズと、パウダー再利用装置Fuse Siftを使ったSLS方式3Dプリントの作業手順を解説します。
1. モデルをデザインし、ファイルを準備する
3D CADや3Dスキャナでモデルをデザインし、そのデータを3Dプリント可能な拡張子(STLまたはOBJ)に変換してエクスポートします。各SLSプリンタでは、ソフトウェアによる造形設定の微調整が可能で、モデルの向きや配列の自動調整、造形時間の算出、造形用にデジタルモデルを各層にスライスすることができます。セットアップが完了したら、無線または有線で接続したプリンタに造形準備ソフトウェアからプリントファイルを送信します。
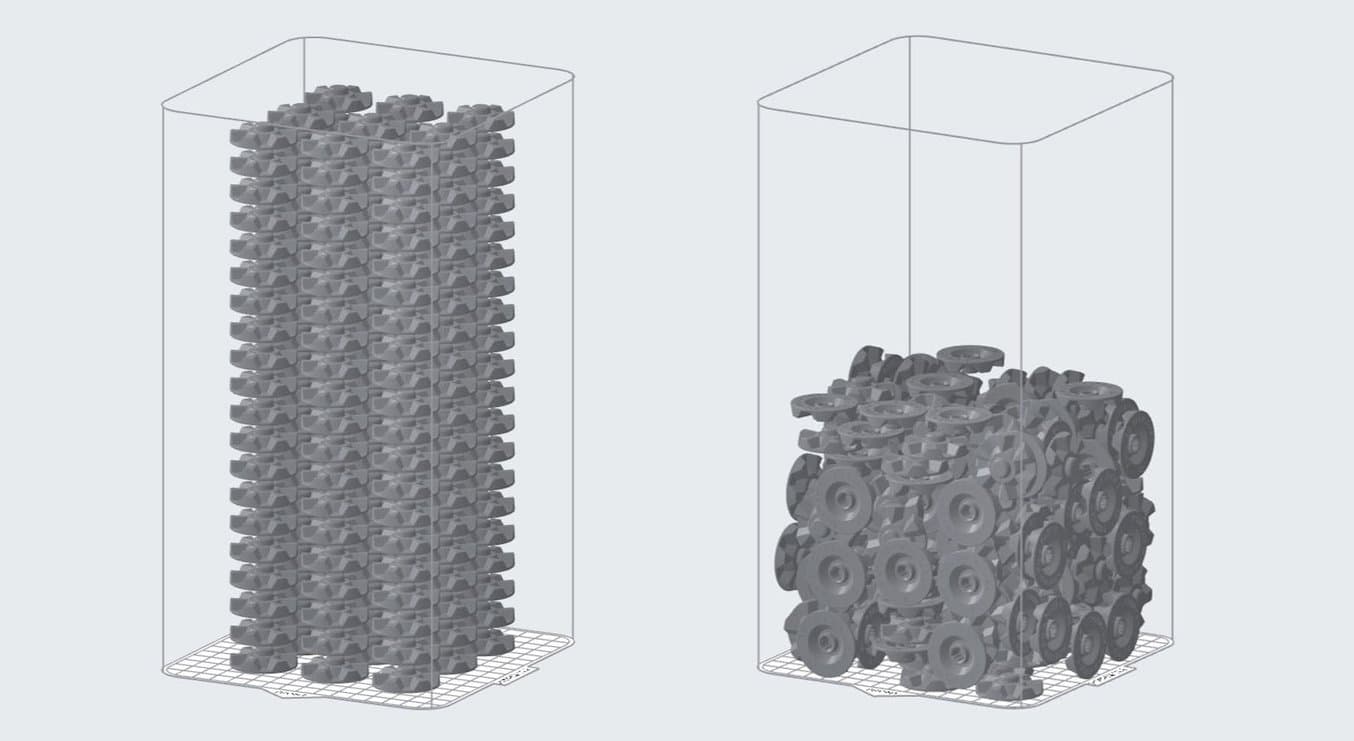
Fuseシリーズのプリンタは、3Dグリッド内で複数の造形品をシームレスに複製・整理し、1回のプリントで造形スペースいっぱいに造形できる専用の造形準備ソフトウェアPreForm(無償でダウンロード可能)を使用。PreFormはモデルの最適な向きや造形品のパッキング状態を自動的に提案してくれ、必要に応じて手動での微調整も可能。
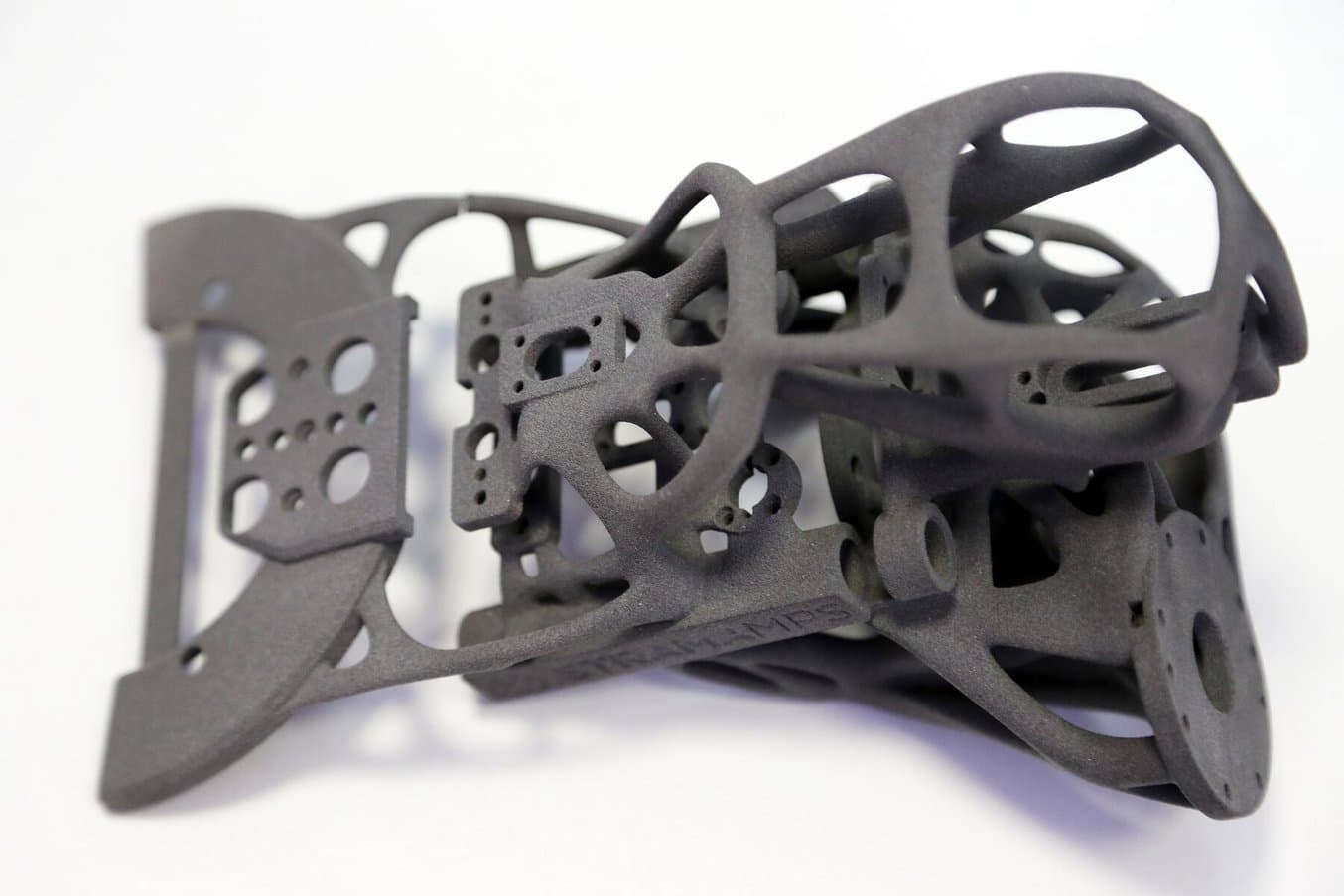
Fuseシリーズデザインガイド
本デザインガイドでは、Fuseシリーズを使ってSLS方式の3Dプリントをする際に考慮すべき重要なポイントをご紹介するとともに、このポイントを実際に活用してプリントを成功させる方法を解説しています。
2. プリンタを準備する
準備作業は、使用するプリンタの種類によって異なります。従来のSLSプリンタの多くでは、準備方法やメンテナンス方法を学ぶために徹底的なトレーニングやツール、物理的な訓練が必要でした。
一方、Fuse シリーズのプリンタではSLSの作業手順が簡素化・効率化され、モジュール化したコンポーネントによってノンストップの造形と最初から最後まで一貫したパウダーの取り扱いが可能です。
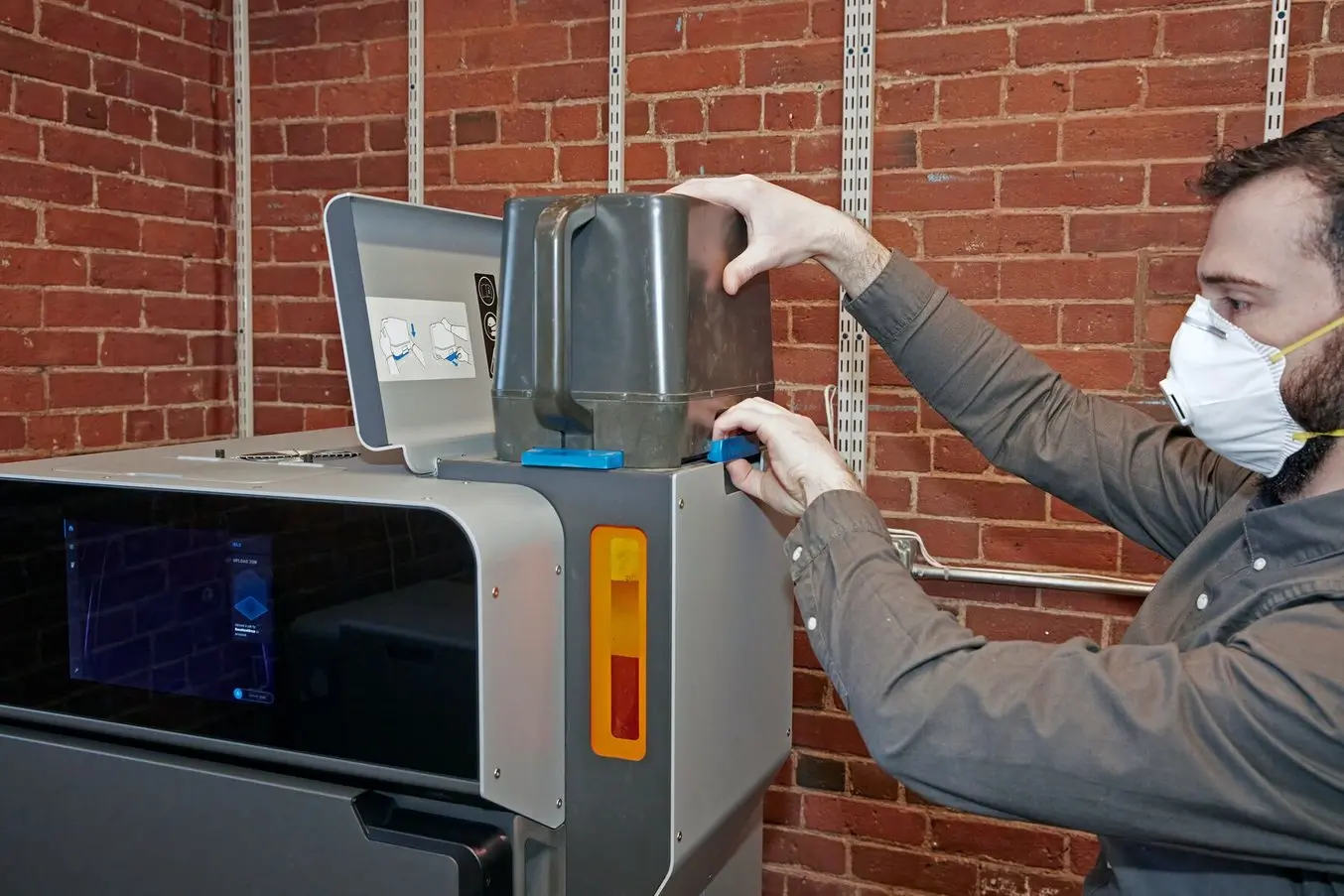
Fuse シリーズプリンタでは、パウダーカートリッジを使ってパウダーの充填も簡単に行える。
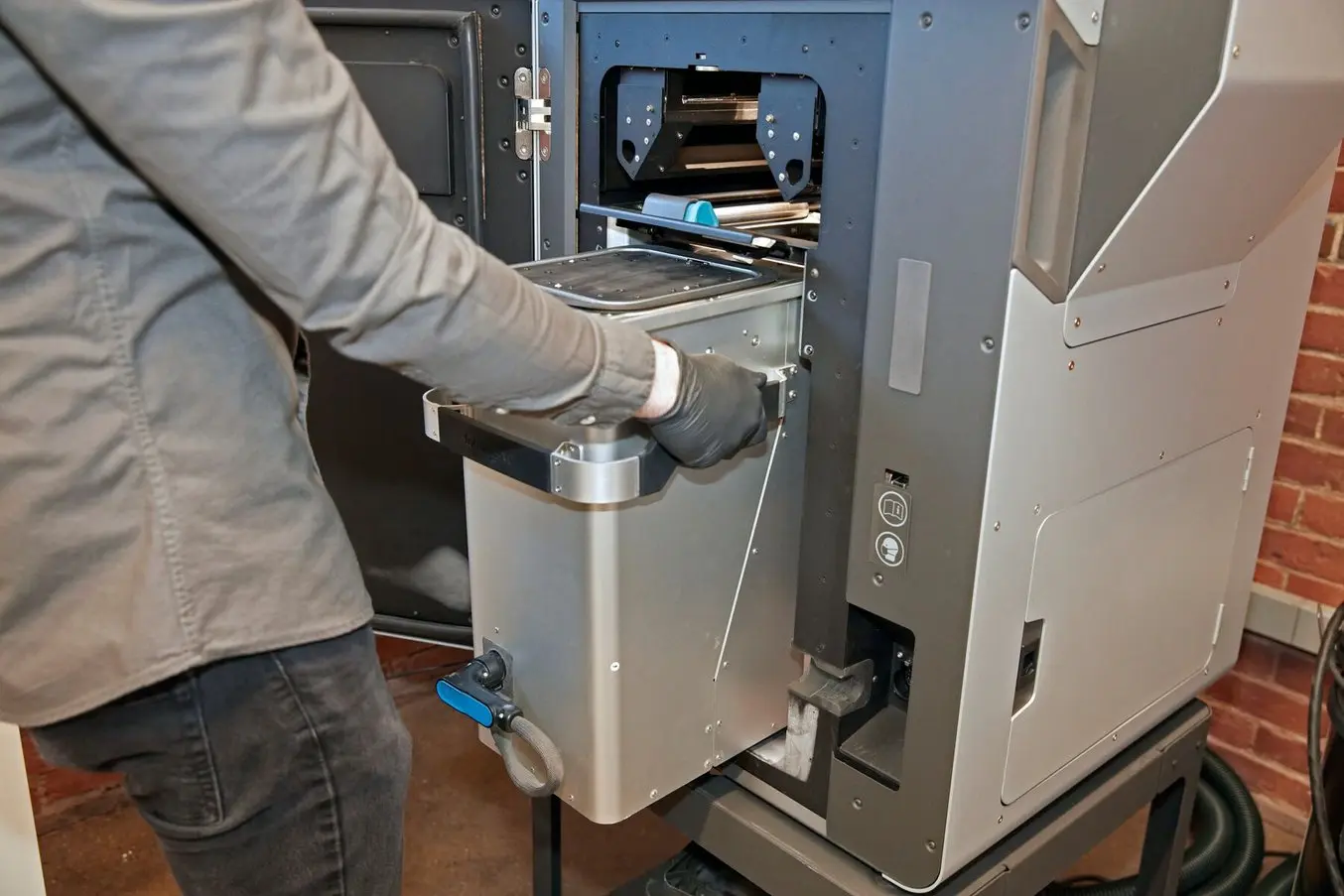
ビルドチャンバーが取り外し可能なため、プリントが完了したらプリンタから取り外して冷却し、その間に別のビルドチャンバーを装着。すぐに次の造形が開始できる。
3. 造形
造形前のチェックがすべて終われば、プリント準備は完了です。SLS 3Dプリントの所要時間は、造形品の大きさ、密度や形状の複雑さにより、短くて数時間、長いと数日かかることもありますが、高出力レーザーのおかげで、Fuse 1+ 30Wのビルドチャンバーいっぱいの分量をプリントする場合でも、殆どは24時間以内に完了します。
造形完了後は、次の工程に移る前にプリンタ内でビルドチャンバーを一度冷却させる必要があります。初期冷却が終わったら、ビルドチャンバーをプリンタから取り出し、スペアのビルドチャンバーがあれば装着して次の造形を開始できます。
ビルドチャンバーを取り出した後、造形品を取り外して後処理に進む前に、二次冷却が必要です。二次冷却をすることで、造形品が最適な機械的特性を発揮でき、後処理中に反り等の変形が発生するのを防ぐことができます。表示された造形時間のうち、実際には約半分程度がこの冷却時間に割り当てられることが多いのです。
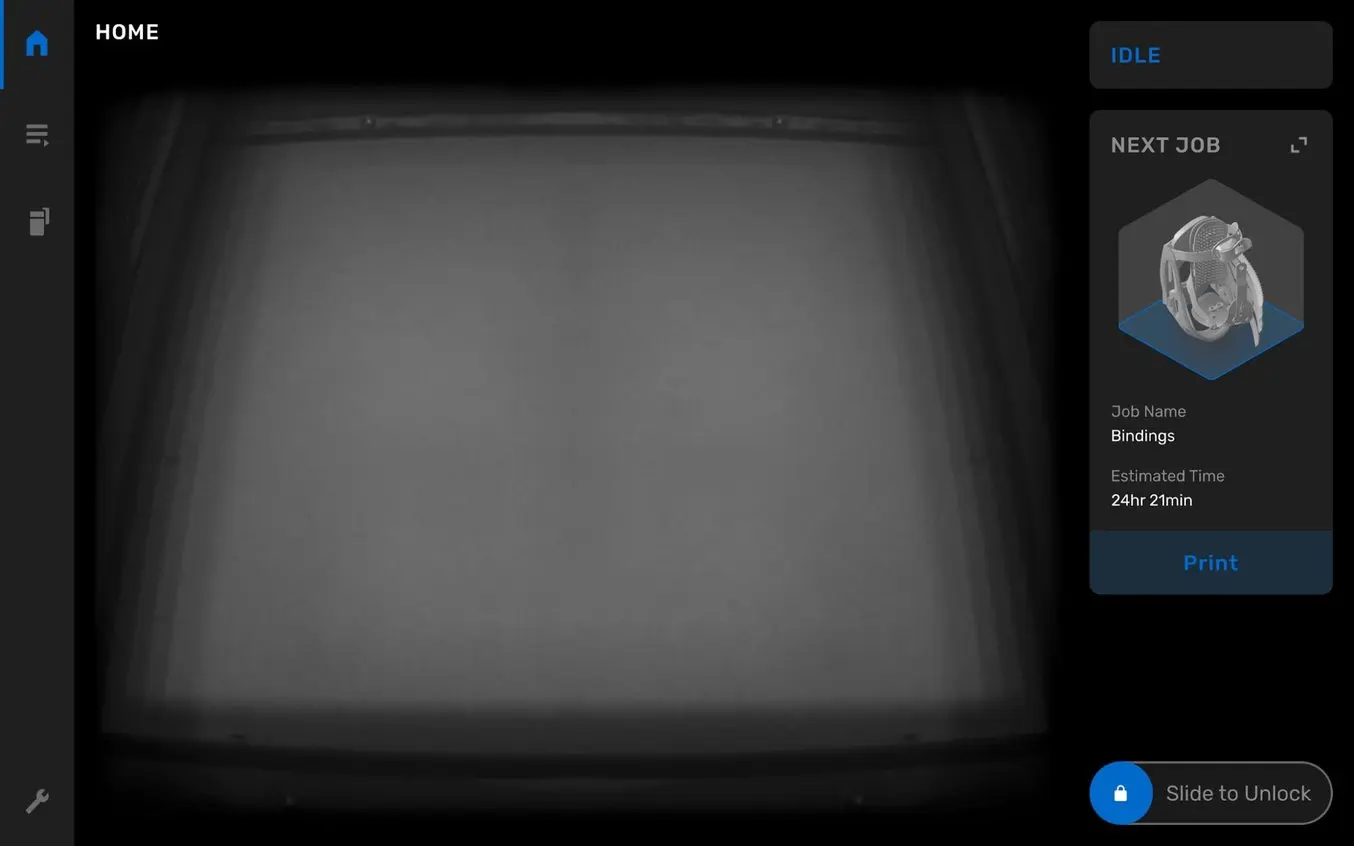
Fuseシリーズプリンタのタッチスクリーンには、ビルドチャンバー内のライブ映像が表示され、造形品が一層ごとに積層されていく様子を見ることができる。この造形中のライブ映像はコンピュータにインストールしたPreFormの画面でも確認でき、どこからでも造形状況を一目で把握できる。
4. 造形品からの粉末除去と使用済みパウダーの回収
SLS方式の造形品は、他の3Dプリント工程と比べても後処理にかかる時間・労力が最小限で済みます。また、サポート材が不要なため、造形品の量が増えても常に同じ品質で造形が可能です。
冷却後は、出来上がった造形品をビルドチャンバーから取り出し、造形品の周囲に残るパウダーを除去します。パウダーの除去には、Fuse Depowdering Kitのように安価で購入できる手作業でのパウダー回収装置から、粉末の飛散を防ぐ陰圧ブースを備えたオールインワン型のパウダー回収・再利用装置Fuse Siftまで、様々な装置が利用できます。いずれも造形品から未焼結パウダーを取り除き、保管・計量・ミキシングをして次のプリント時に再利用します。
造形品に付着した余分なパウダーは、回収後にフィルターで大粒を取り除いた後、再利用が可能です。未焼結のパウダーは高温に晒されたことで品質が若干劣化しているため、新しいパウダーと混ぜ合わせてから次のプリントで再利用することをお勧めします。パウダーを再利用できることが、SLSが最も無駄の少ない製造工程の1つとなっている理由です。
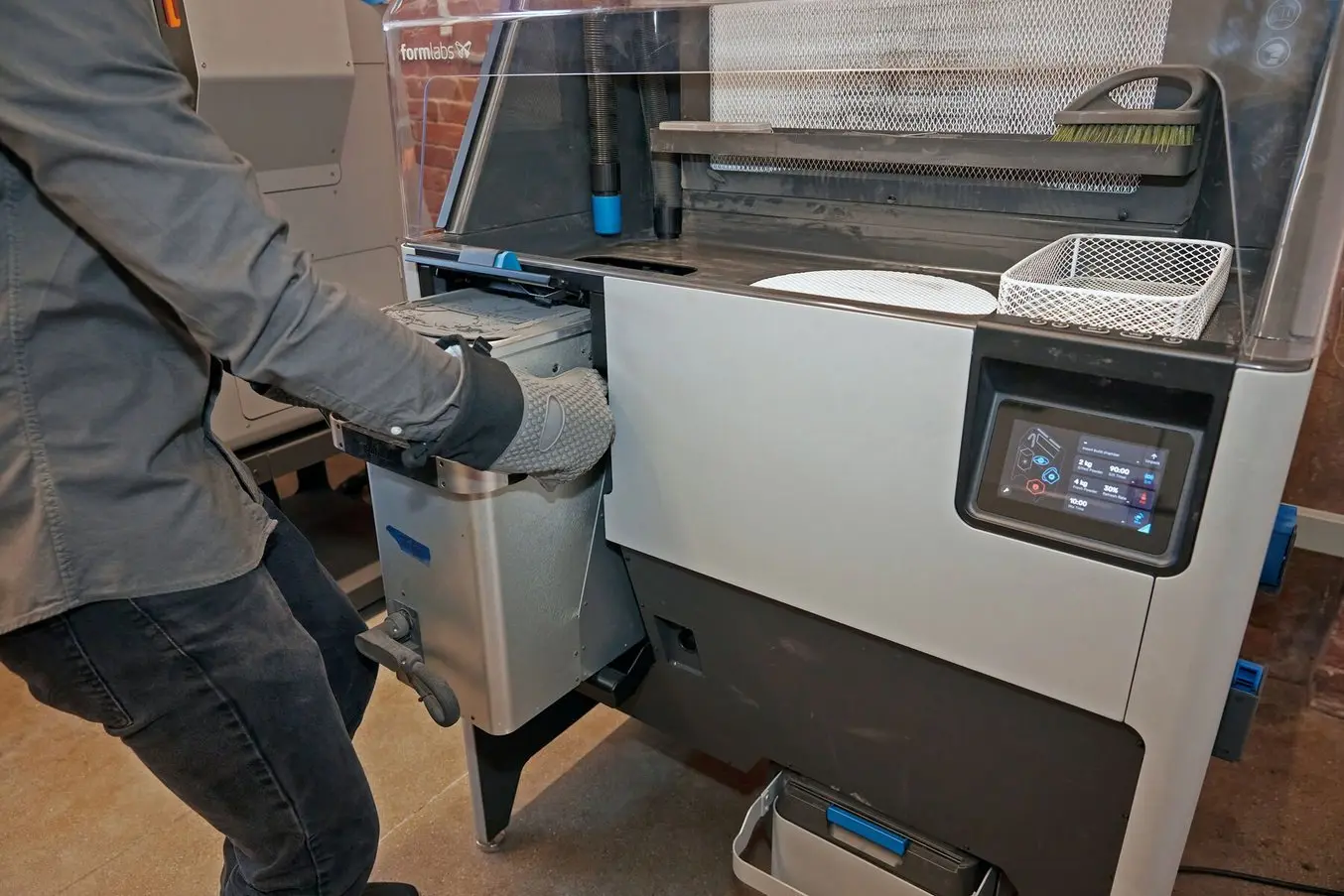
Fuseシリーズでは、造形後の残りの作業をFuse Siftがオールインワンで担い、造形品の取り出しからパウダーの再利用まで安全かつ効率的に行える。
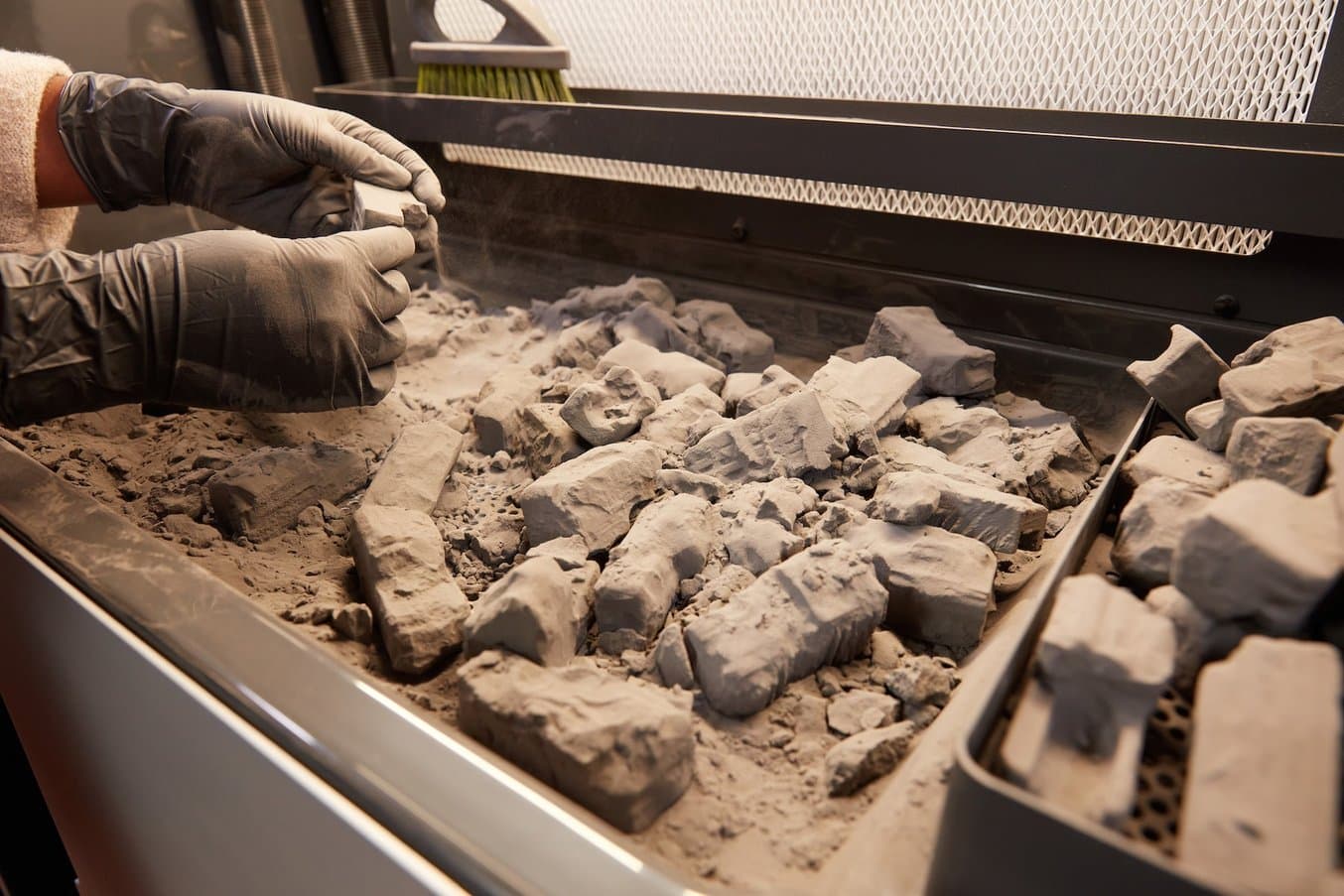
Fuse Siftは再利用パウダーと未使用パウダーを混ぜ合わせて自動ミキシングを行うため、粉末のロスが最小限で済み、在庫管理も適切に行える。
5. 後処理
SLS 3Dプリントでは、プリント完了後に造形品を粉末から取り出した後、完全に粉末を取り除き、粉っぽさのない表面に仕上げるためには事実上、ブラスト処理がマストになっています。ブラスト処理を施すことで、造形品の表面に付着する粉じんやFormlabsのFuseシリーズの特許技術である半焼結状のSurface Armorを完全に取り除くことができます。
現在、市場には様々な価格帯の自動および手動ブラスト処理装置が出ています。Formlabsの新製品Fuse Blastは、初めて手頃な価格を実現した自動ブラスト装置です。Fuseシリーズと合わせてSLS製品の作業工程を完成させることも、他社製の粉末焼結積層造形方式プリンタでプリントした造形品の後処理も、これ1台で。
ブラスト処理により、SLS 3Dプリントの作業工程で最も作業時間と労力のかかる工程を大幅に削減できます。後処理工程でFuse Siftを補完する装置としてFuse Blastを導入いただくと、造形後のブラスト処理にかかる時間を最短15分にまで短縮できます。これは、手作業の場合にかかる平均作業時間の80%減に匹敵します。
Fuse Blastにオプションで追加いただける研磨装置を使うと、造形後の粉末除去から表面処理まで、すべてオールインワンで完結します。Fuse Blastで研磨までを行うと、ワーク表面から粉っぽさは完全に排除され、滑らかで傷つきにくく、そのまま染色などの表面処理が施せる半光沢の表面品質に僅か15分で仕上がります。圧縮空気で研磨用のビーズを吹き付けることで、SLS 3Dプリント品の特徴であるざらついた表面を生み出す無数の微細な凹凸や穴を削り取り、滑らかな表面に仕上げます。
さらに、標準的な後処理工程以上の品質を実現したい場合に利用できる、高度なSLS後処理技術が複数あります。これにより、手触りをより滑らかにしたり、耐薬品性の向上、表面硬度の減少、色の変更、導電性の付与など、様々な結果が期待できます。
こちらの記事では、ぞれぞれのステップについてひとつずつ説明しています。目指す表面品質が具体的に決まっていて、どのような後処理手法を組み合わせれば実現できるのか検討中の場合は、弊社スペシャリストまでお問い合わせください。お客様のユースケースについて一緒に考えましょう。
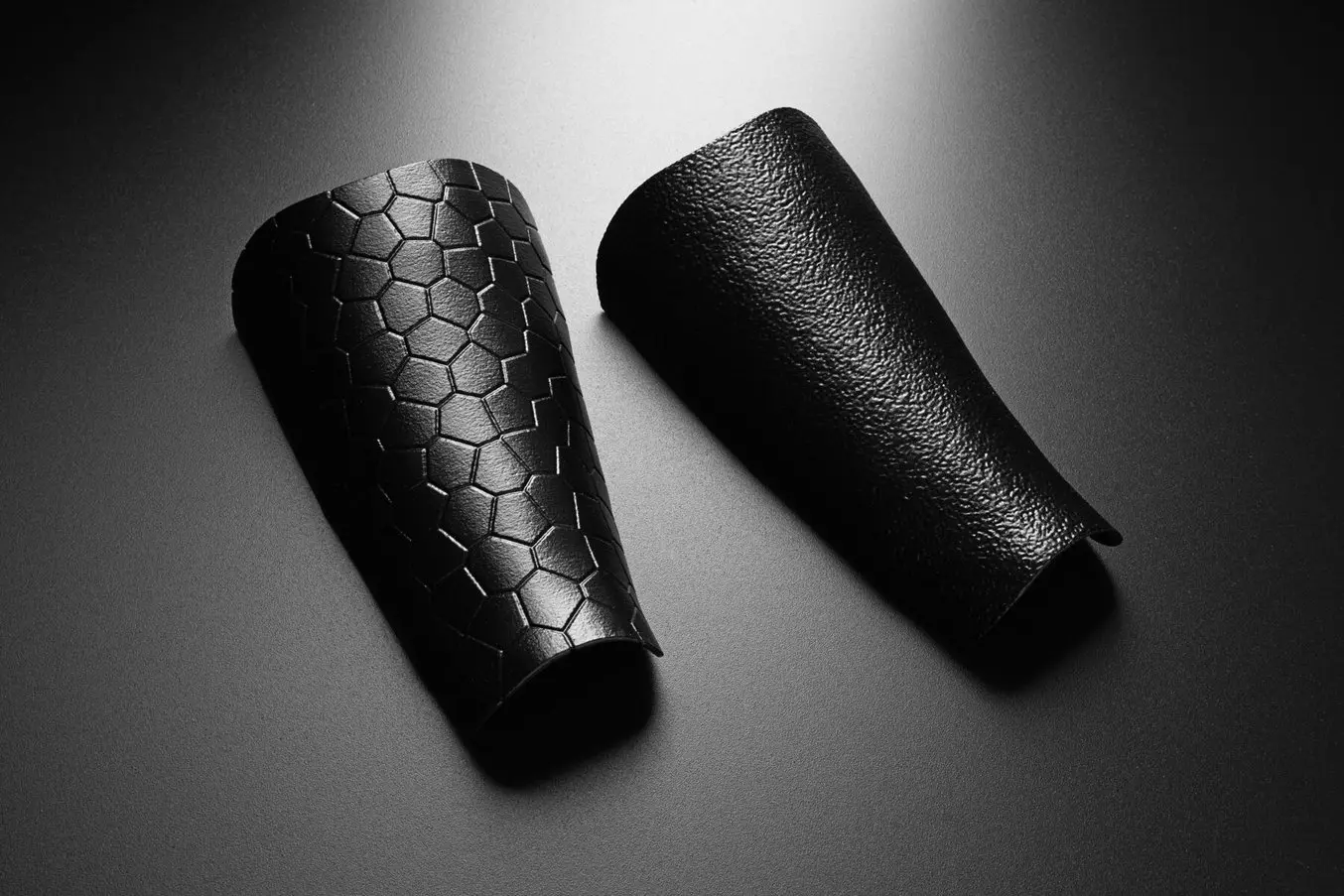
ベーパースムージング(溶剤噴霧)により、射出成形品に匹敵するほどの品質と耐久性を備えたSLS 3Dプリント品が出来上がります。
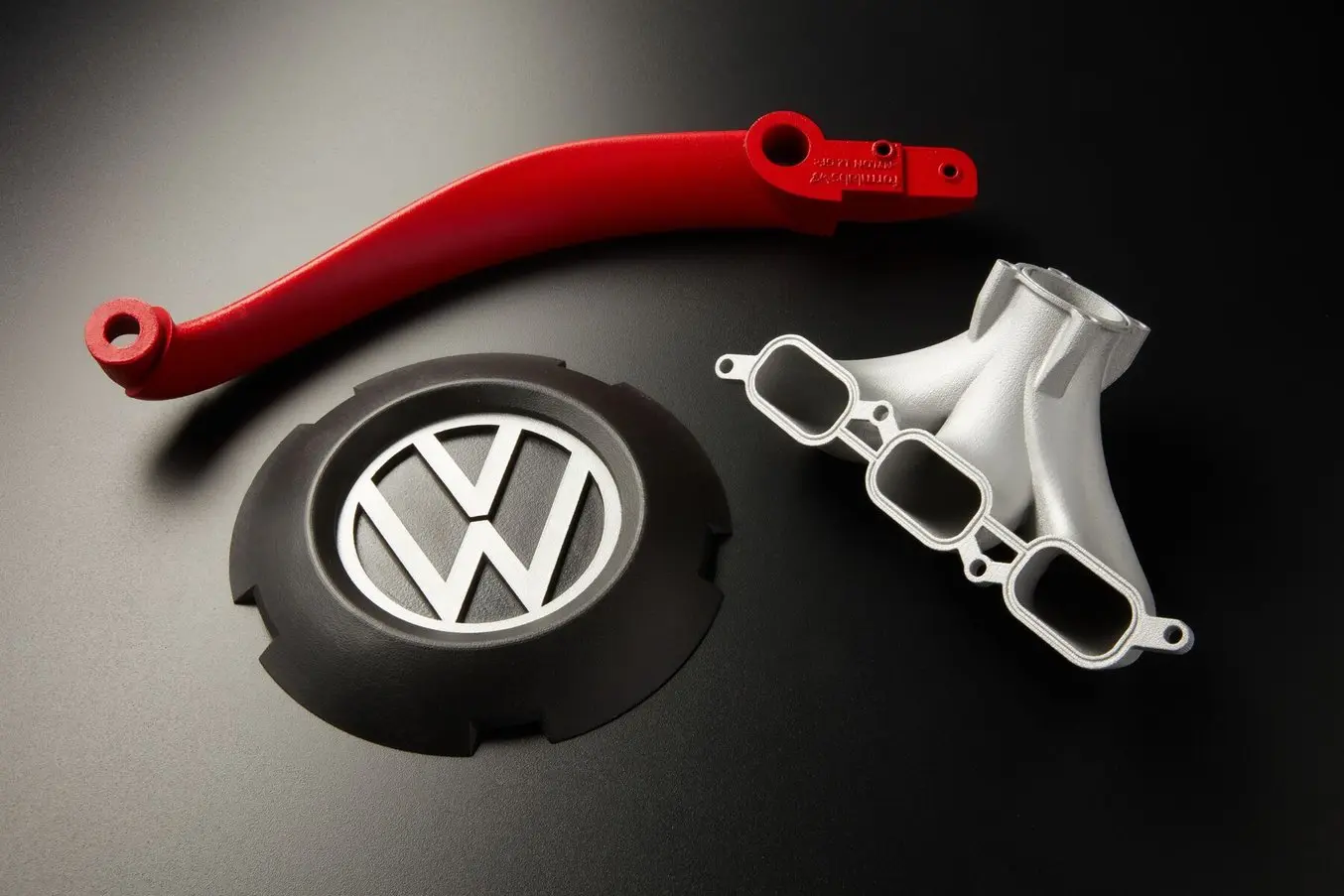
Cerakoteに代表されるセラミックコーティングでは、鮮やかな色彩など、機能性と外観の両方で良質な仕上がりが期待できます。
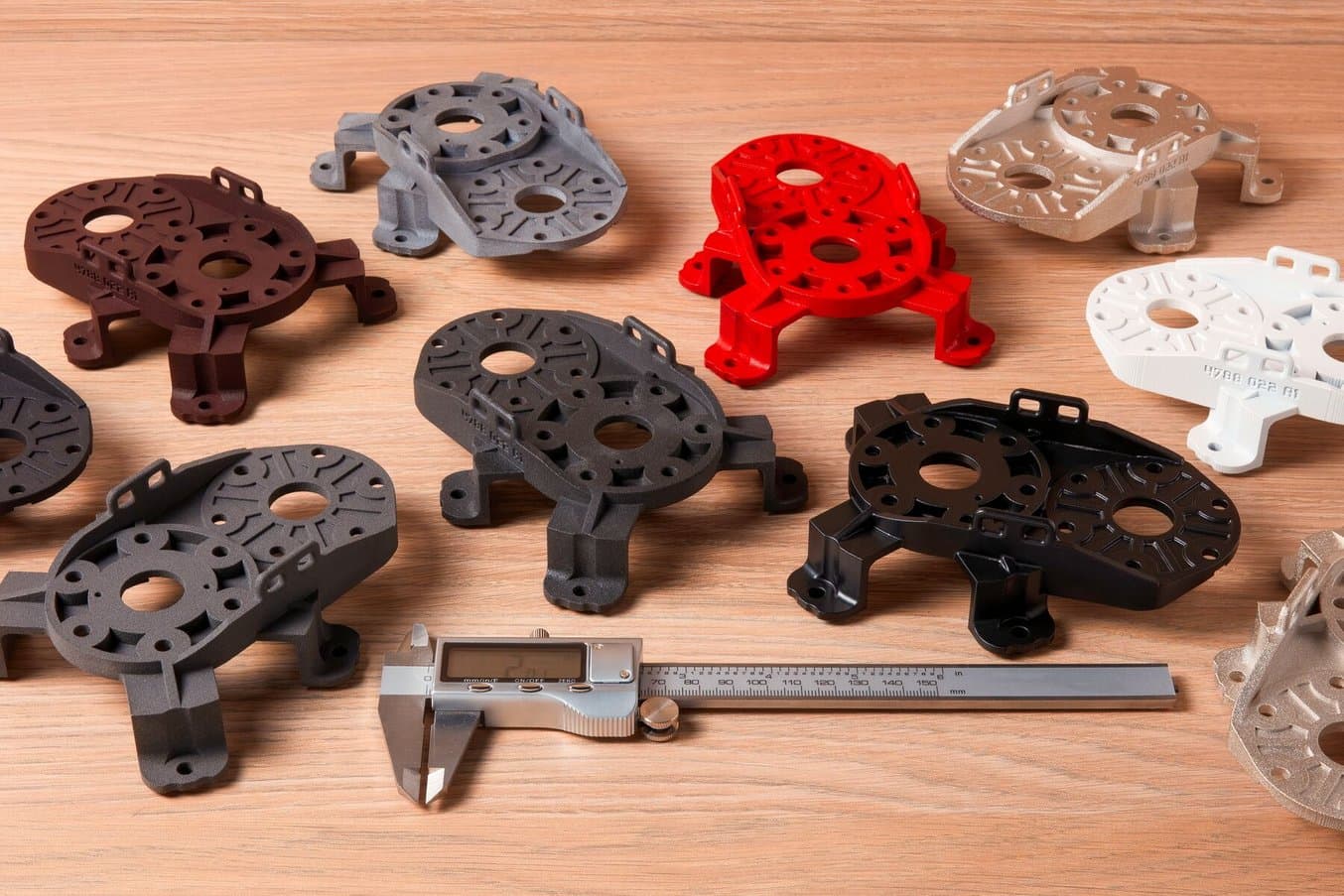
3Dプリント用の高度な後処理方法
このウェビナーでは、Cerakote、電解めっき、ベーパースムージングなど、3Dプリント品に施すことのできる11種類以上の高度な後処理方法をご紹介しています。
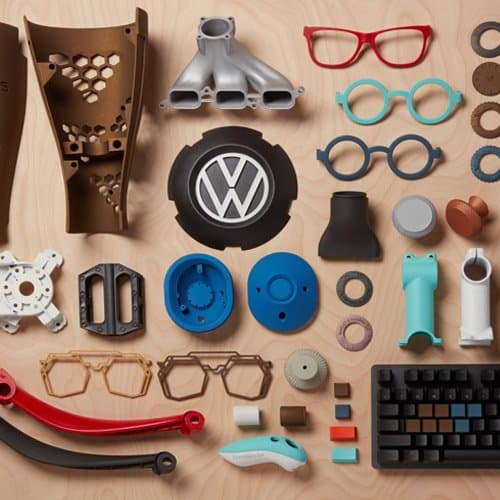
高度なセラミックコーティングで3Dプリント品の機能性を向上(英語)
本ウェビナーでは、Cerakoteによるセラミックコーティングで3Dプリント品の機能性を高める方法をご紹介します。
SLSを選ぶ理由
SLS(粉末焼結積層造形)方式がエンジニアや製造業者に選ばれる理由は、設計の自由度、高い生産性とスループット、造形単価の低さ、実製品用部品として信頼のおける材料が使用できるなど、さまざまです。
設計の自由度
SLA光造形方式やFDM(熱溶解積層)方式など、他のアディティブマニュファクチャリング技術はどれも、オーバーハングがある形状のモデルを造形する場合は特殊なサポート材が必要になります。
SLS(粉末焼結積層造形)方式では造形物の周囲で溶融されなかったパウダーが造形物を支えるためサポート材は不要で、以前であれば不可能だった格子構造や可動式の部品、内部構造や溝のある造形品など、複雑な形状のデザインにも対応できます。
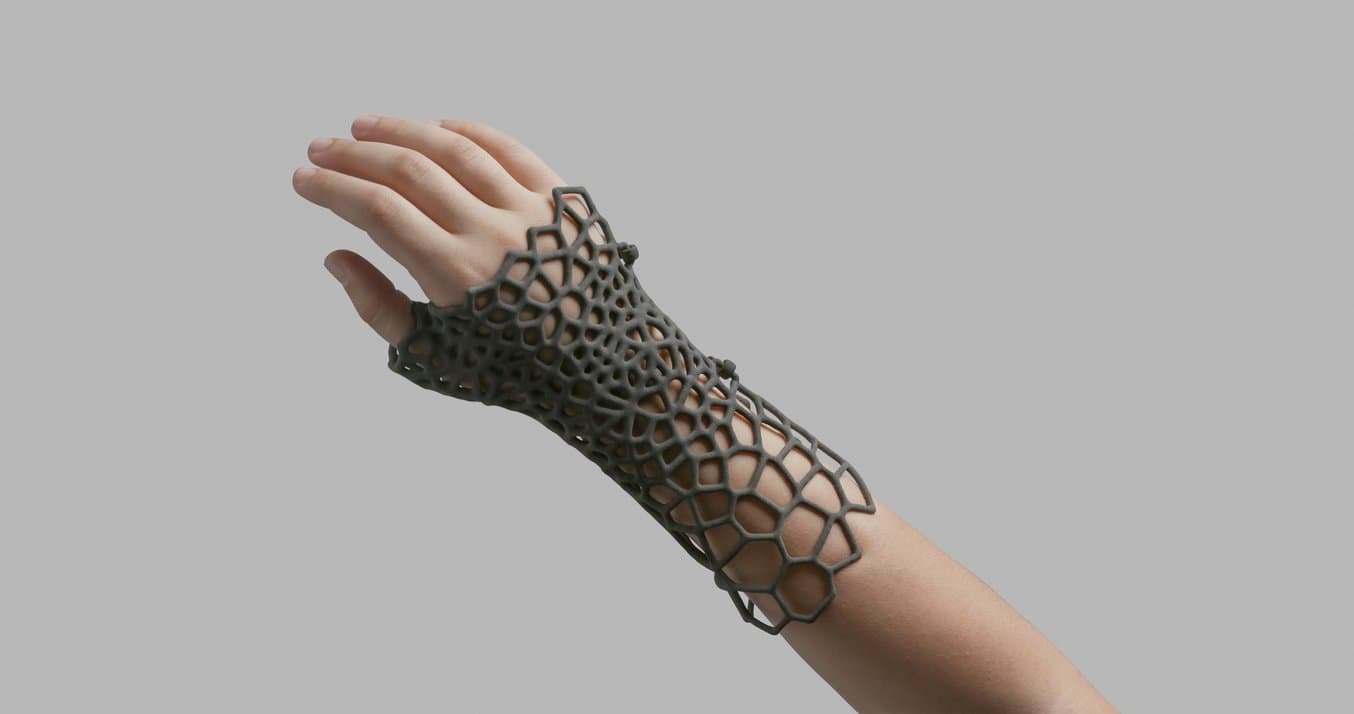
重量を減らすために複雑なパターンが施されたハンドスプリント。
エンジニアは通常、最終的な製造工程を想定しながら部品を設計します。この考え方は製造容易性設計(DFM)とも呼ばれています。アディティブマニュファクチャリング(AM)技術の活用範囲を試作品製作だけに絞ると、その試作品として設計できる形状は、従来の製造機械で実製品を作るときに再現できるものに限られてしまいます。
今後、実製品の高速生産技術としてSLS(粉末焼結積層造形)方式を活用できる用途が広がっていけば、設計やエンジニアリングの新しい可能性も広がっていくことでしょう。SLS 3Dプリンタは、従来の製造工程では不可能、もしくは製作費が高額で非現実的だと考えられていた複雑な形状のモデルの造形にも対応できます。また、SLSにより、エンジニアが通常、複数の構成部品を製作して、それを後で組み合わせて作るアセンブリを、初めから一体化した単一の部品として設計・造形することも可能になります。つまり、SLSを導入すれば、これまで強度が十分でなかった継ぎ手の課題を解消したり、組立工程に費やしていた作業時間を節約したりできるようにもなります。
SLS方式は、
ジェネレーティブデザインの可能性を最大限に引き出し、従来の手法では製造が不可能だった複雑な格子構造の軽量設計なども可能にします。高い生産性とスループット
SLS方式の3Dプリントは、アディティブマニュファクチャリング(AM)技術の中では、機能性と耐久性が求められる試作品製作や実製品用部品を最も高速に造形できます。パウダーを焼結させるレーザーの走査速度は、FDM(熱溶解積層)方式などの他の工業用積層技術よりも遥かに高速です。
複数の造形品を密接に配置して造形すれば、1回のプリントで造形スペースを最大限に有効活用できます。造形準備ソフトウェアを使うことで、造形品同士の隙間を最小限に抑えて最適化し、誰でも生産性を最大限に高められるようになります、
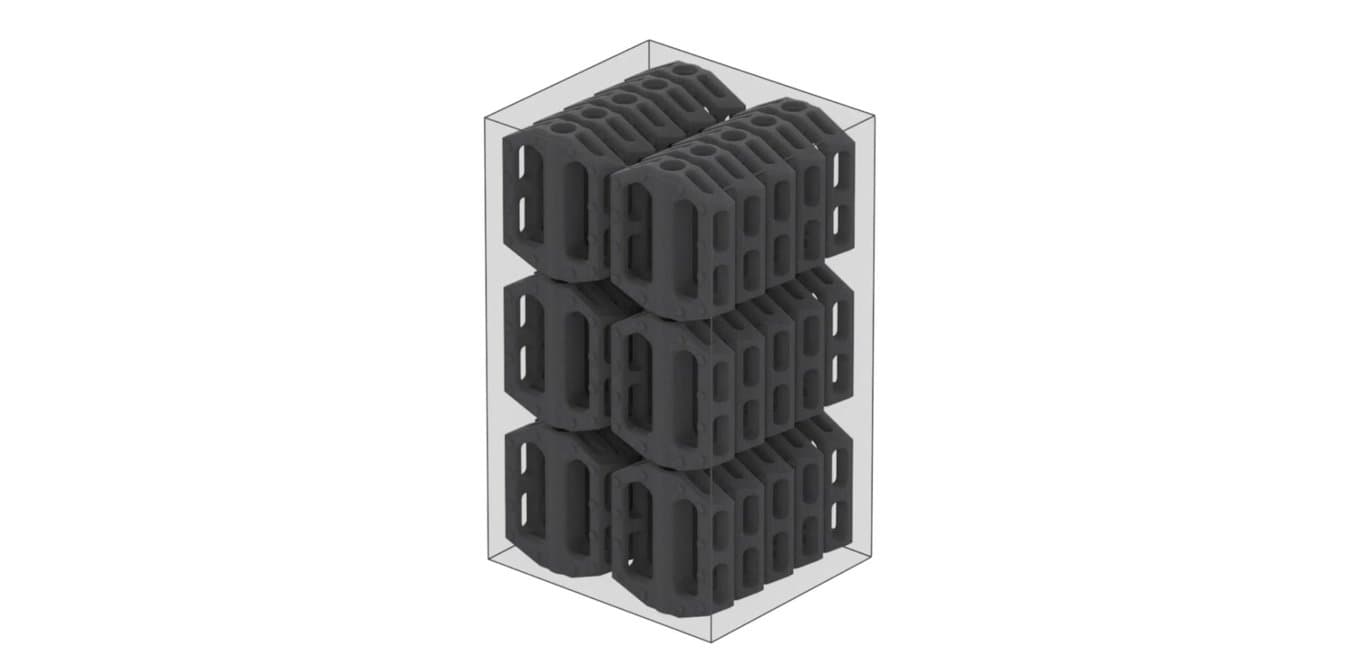
SLSはビルドチャンバー内にできるだけ多くの造形品を並べ、サポート材を使わずに造形できるため、後処理に要する時間を大幅に短縮できる。
実製品用材料としての実績
SLS方式の造形品の機能性と万能性の鍵を握るのは材料です。ナイロン、ナイロン複合材料、TPUはいずれも高品質の熱可塑性プラスチックとして高い信頼を得ています。レーザーで焼結したナイロン製の造形品は、100%に近い密度と、射出成形などの従来の製造法で製作された部品に匹敵する機械的特性を有します。
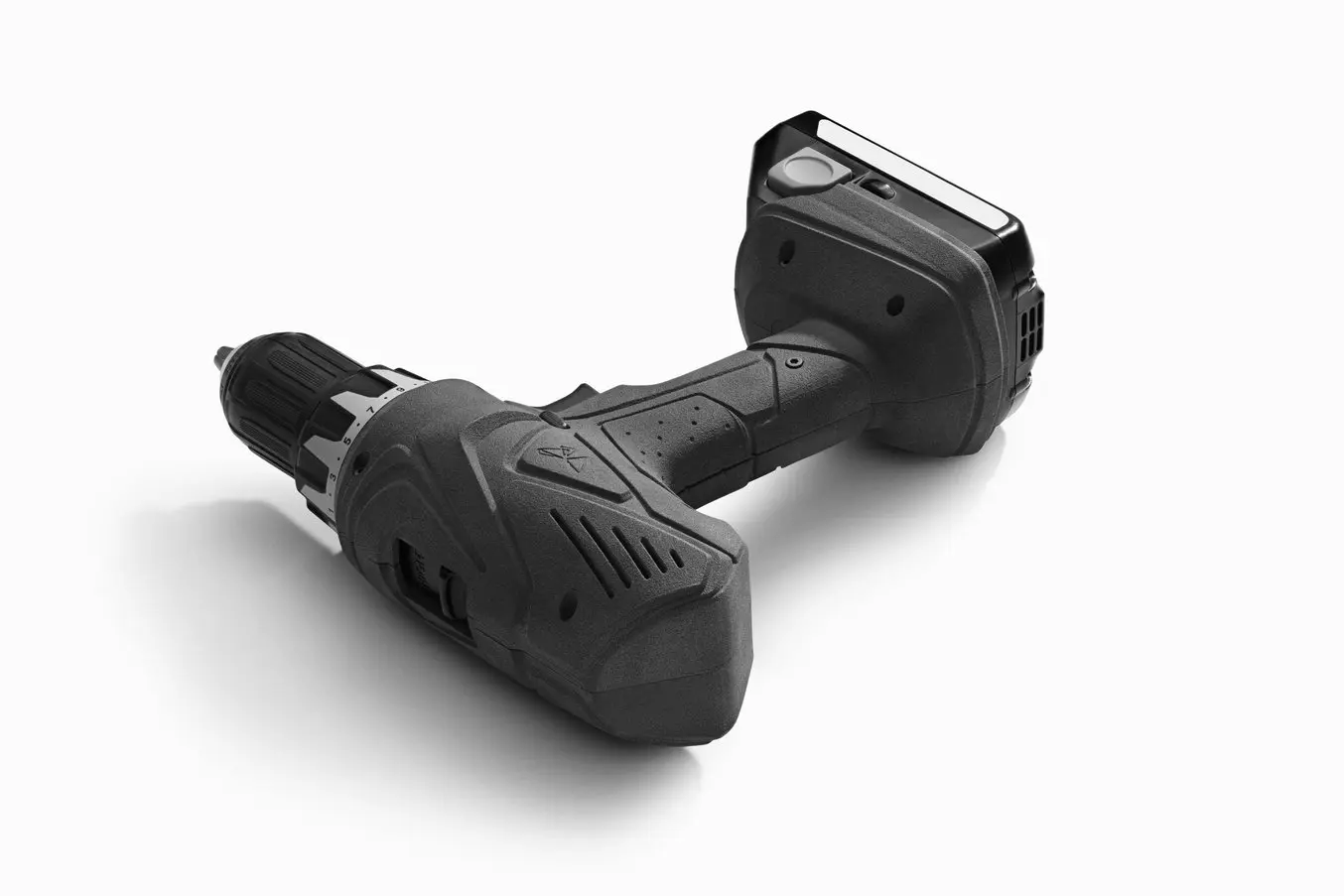
Nylon 12パウダーで造形したドリル。ナイロン製の造形品は、簡単な表面処理だけでそのまま製品として使えるほど滑らかな表面に仕上げることができる。
SLS方式でプリントしたPPやナイロン製の造形品で、射出成形によるプラスチック部品を置き換えることができます。他のどの積層造形技術で製作したスナップフィット式の部品や機械継ぎ手よりも高い品質を誇り、他の方式で製作した部品が経年劣化により脆くなりやすい一方、SLS方式の造形品ではその心配がなく、長期的な使用を目的とした機能要件があるプラスチック製品の製作に最適です。
TPUは従来の鋳造による製品を置き換えるのに最適で、丈夫で長持ちする柔らかい部品を製造する場合には、他の3Dプリント方法よりもSLS方式の方が向いています。ラピッドプロトタイピング、治工具のオンデマンド製作、実製品用部品のカスタム生産または少量生産に適しています。
造形単価の低さ
造形単価は通常、所有する設備の運用費、材料費、人件費などを計算に入れて算出されます。
-
設備所有コスト:マシンが使用可能期間中に生産できる部品の数量が多ければ多いほど、各部品の製造単価は下がります。つまり、生産性を上げると1つの部品にかかる設備所有コストが低くなります。高速レーザー走査、造形品の自動パッキングによる造形スペースの最適化、表面処理の簡素化を実現したSLS方式は、樹脂を使ったアディティブマニュファクチャリング技術としては最大の生産性とスループットを誇ります。
-
材料:ほとんどの3Dプリンタでは専用の材料を使用しますが、ナイロンは大量生産品の製造で広く使われている熱可塑性プラスチックの工業用材料で、アディティブマニュファクチャリング(AM)用の原材料としては最も安価な材料の一つです。また、SLS 3Dプリントは原則サポート材を必要とせず、再利用パウダーを使った造形も可能なため、材料のロスを最小限に抑えることができます。
-
作業時間:3Dプリントで肝となるのが、作業時間です。3Dプリント工程の多くは複雑で自動化することが難しく、自動化できない作業は人の介入が必要になるため、人件費などで造形単価が膨らんでしまいます。SLS方式の後処理がシンプルになることで作業時間を削減でき、生産量が増えた場合にも容易にスケールアップして対応できるようになります。
SLS方式の3Dプリンタ導入にはそれなりの初期投資が必要ですが、小型のプリンタよりも速く投資金額を回収できることが多いのです。ベンチトップ型SLS 3Dプリンタの登場により、これまで高額なことがネックだった新規導入のハードルを大幅に下げ、ほとんどの用途で造形単価を下げることに成功しています。
3Dプリントを必要とする案件がごく稀にしか発生しない場合は、外注することも推奨の方法ではありますが、それでも製作コストが高くつき、納期も長くなることを覚悟しなくてはなりません。3Dプリントの最大のメリットの一つは、従来の製造法と比べて遥かに早いスピードで製造できることです。それに対して、外注の場合は造形品が納品されるまでに一週間から数週間かかることもあります。
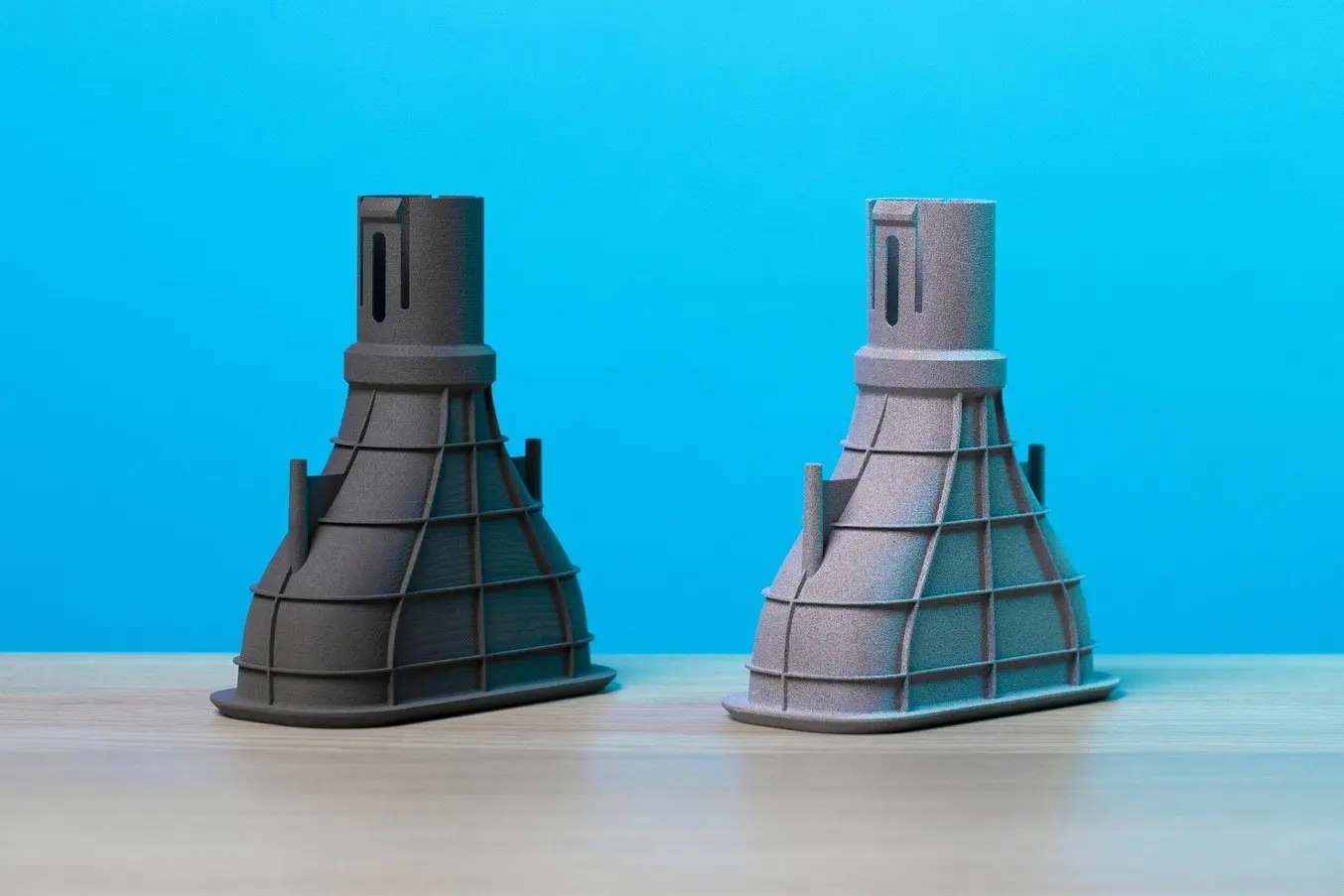
自動車用マニホールドの試作品
コスト | 製作期間 | |
外注 | $118.33 | 7~10日 |
Fuse 1+ 30W | $9.02 | 13時間 |
まずはFormlabsにご連絡ください。お持ちの設計ファイルの詳細分析で、コスト削減や作業手順の高効率化が見込める箇所を確認しましょう。
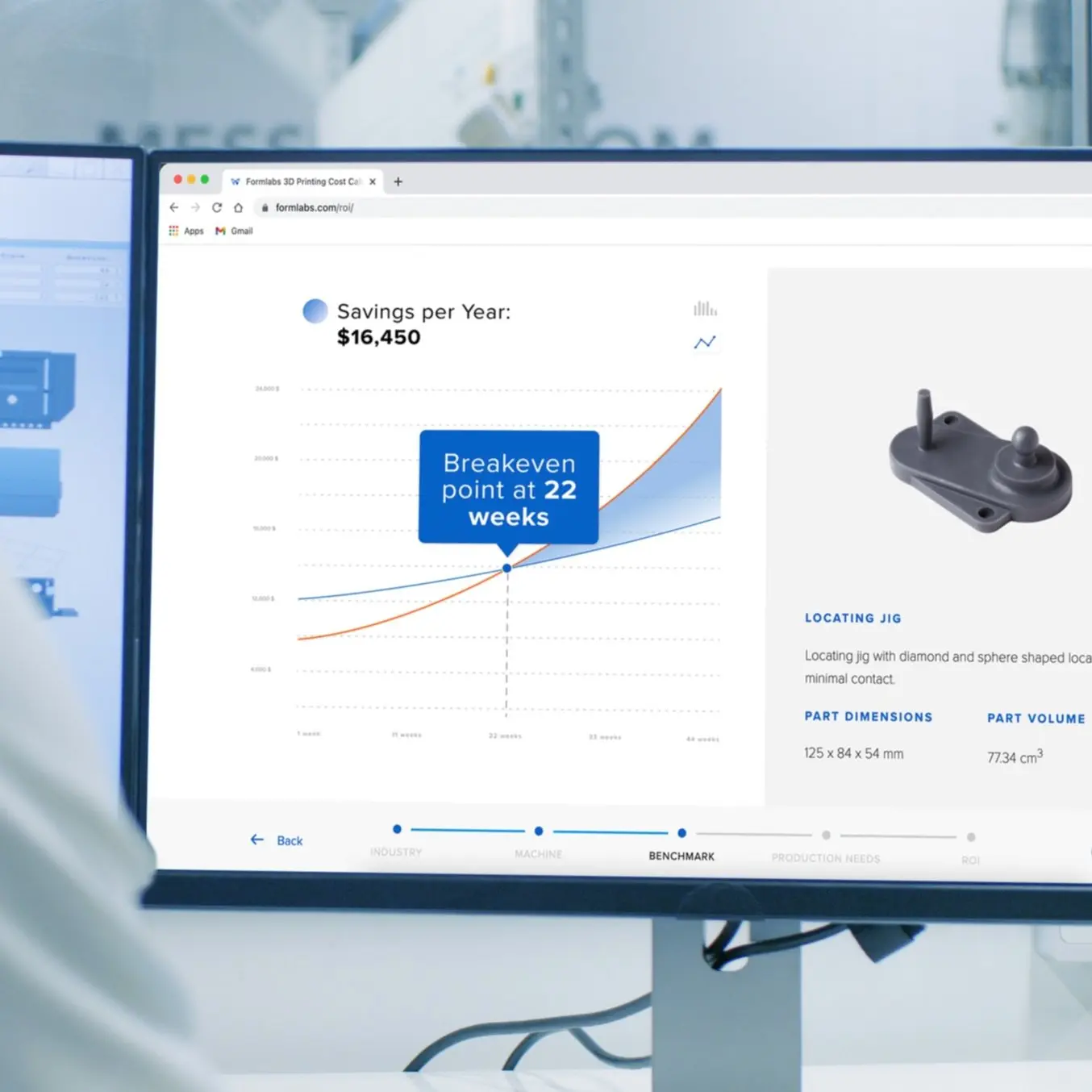
削減可能なコストと時間を算出
Formlabsの3Dプリンターでどれだけのコストと時間が削減できるのか、FormlabsのインタラクティブなROI計算ツールで是非ご確認ください。
製品開発サイクルの短縮
SLS(粉末焼結積層造形)方式なら、エンジニアは設計サイクルの早い段階で試作品を製作することができ、そのまま同じプリンタと材料を使って実製品部品も製造できます。SLS方式なら、従来の製造手法で欠かせなかった高額かつ制作期間の長い金型が不要で、部品やアセンブリの試作品の検証・改良も僅か数日間で簡単に完了できます。その結果、製品開発に要する期間を大幅に短縮できるのです。
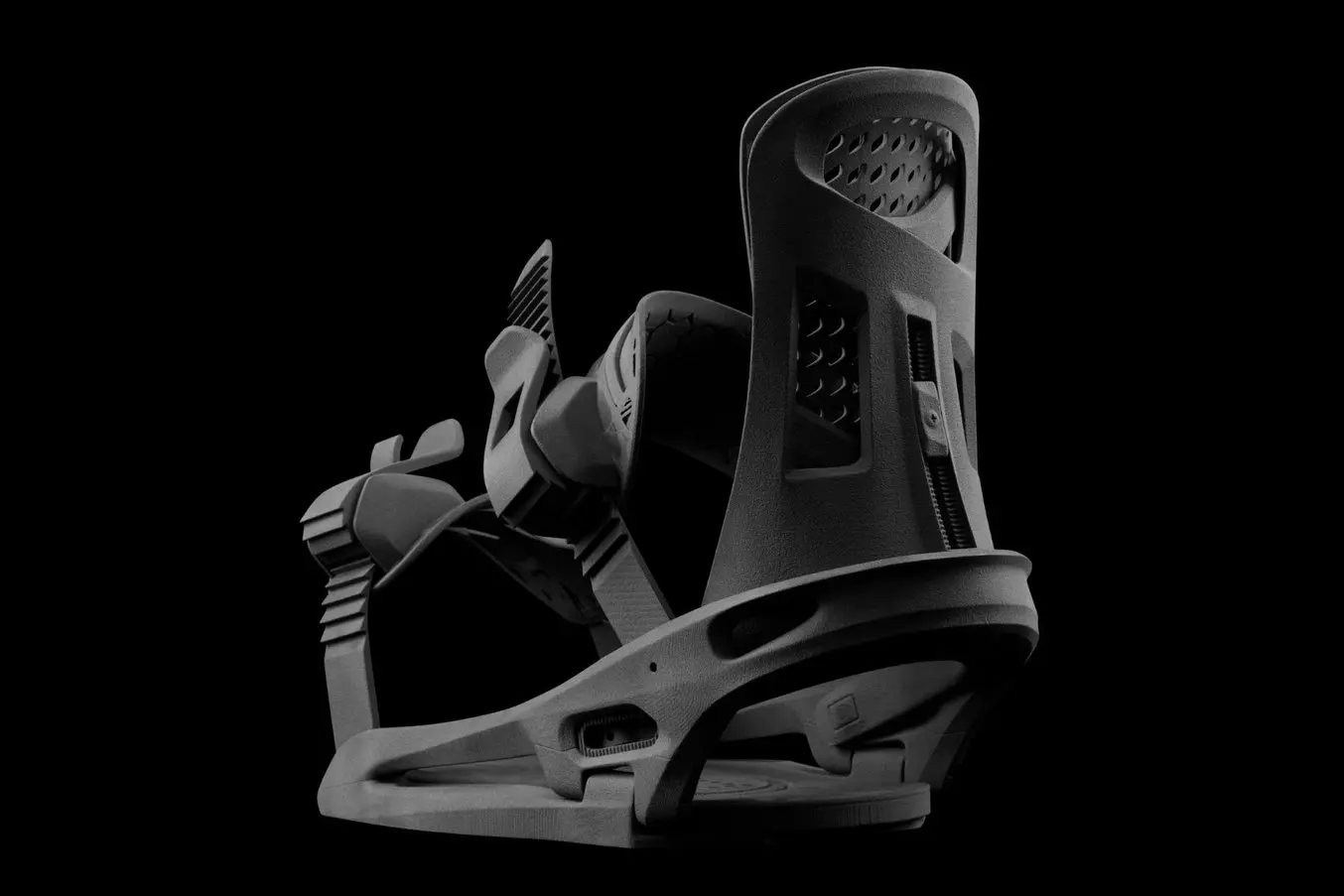
SLS方式は、そのまますぐに厳しい機能試験を行うことも、交換部品や実製品として出荷することもできる、耐久性に優れた機能確認用試作の製作に最適。
SLS方式の3Dプリントは、複雑な形状の特注製品でも実製品用の小さな部品でも、造形単価を低く抑えながら高耐久性の材料を使って製作できるため、非常に経済的です。費用対効果の面でも、限定生産や量産移行前のテスト生産などで射出成形に代わってコスト効率を高めることができます。
新登場のSLS 3Dプリンタ Fuse 1+ 30W
これまで工業用のSLS 3Dプリンタといえば、一台につき$200,000以上もする、ほとんどの企業にとっては手の出ない高額なプリンタしかありませんでした。
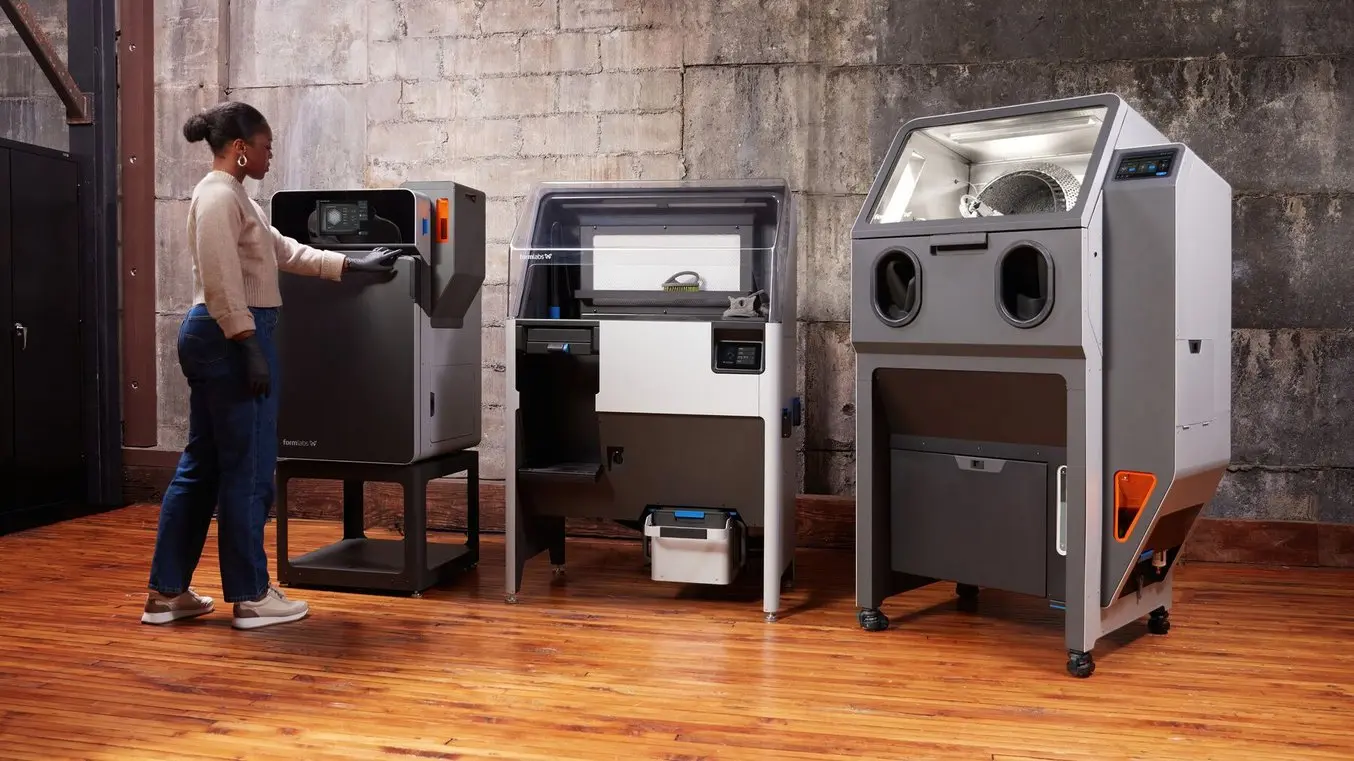
Formlabsは、これまで工業用プリンタにしか搭載されていなかったSLS(粉末焼結積層造形)方式をベンチトップサイズに小型化したFuse 1+ 30Wで、高機能材料を使いながら造形単価を最低限に抑え、省スペース化や作業手順の簡素化を実現しました。
Fuse 1+ 30Wで、外注に頼らない自立した生産や試作品製作が現実になります。