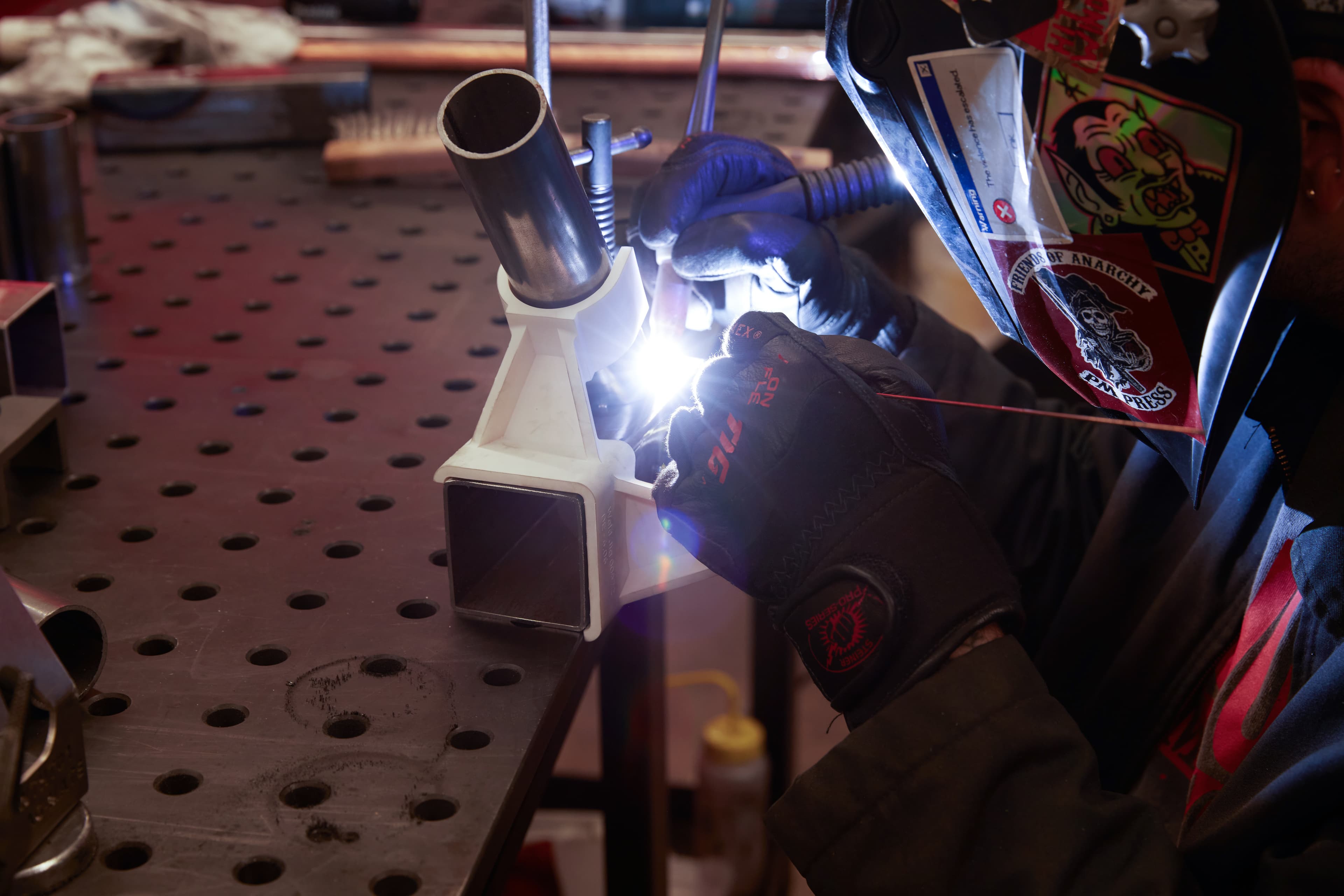
Reduce Costs and Lead Times in Metalworking With On-Demand Jigs and Fixtures
Jigs and fixtures are critical in metalworking to ensure precision, repeatability, and efficiency. Traditional tooling methods, however, often come with long lead times, high costs, and limited design flexibility. 3D printing addresses these issues by offering faster, cost-effective, and customizable solutions.
This white paper outlines a methodology for using 3D printers to produce jigs, fixtures, and other tools for metalworking. Real-world case studies show how Formlabs printers create durable, precise, and heat-resistant tools that perform well in demanding environments. It highlights how companies can cut lead times and costs by up to 90% while improving tool customization and complexity. Practical steps are provided for integrating 3D printing into operations, enabling businesses to enhance efficiency and meet evolving production needs
Reduce Costs and Lead Times in Metalworking With On-Demand Jigs and Fixtures
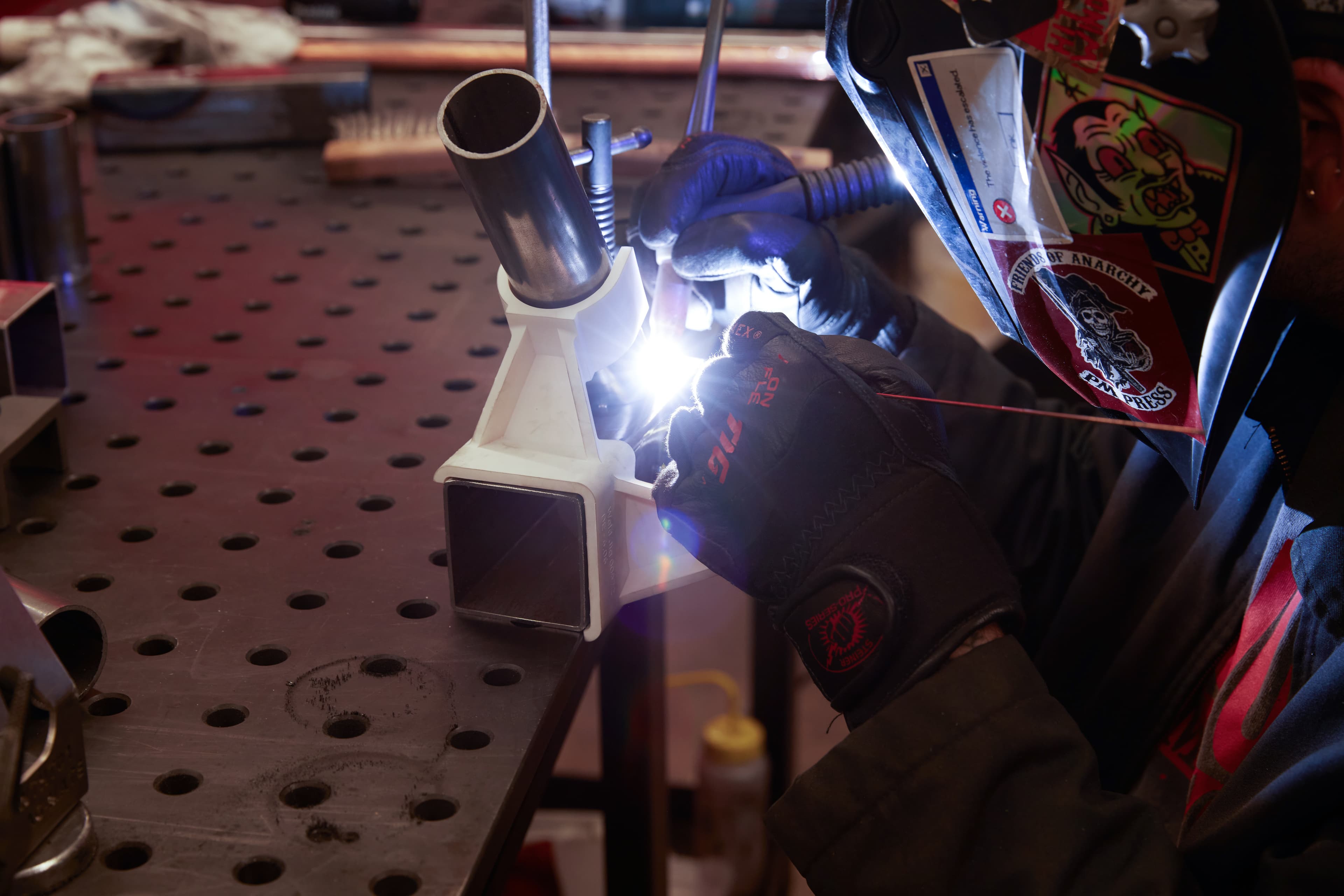
Jigs and fixtures are critical in metalworking to ensure precision, repeatability, and efficiency. Traditional tooling methods, however, often come with long lead times, high costs, and limited design flexibility. 3D printing addresses these issues by offering faster, cost-effective, and customizable solutions.
This white paper outlines a methodology for using 3D printers to produce jigs, fixtures, and other tools for metalworking. Real-world case studies show how Formlabs printers create durable, precise, and heat-resistant tools that perform well in demanding environments. It highlights how companies can cut lead times and costs by up to 90% while improving tool customization and complexity. Practical steps are provided for integrating 3D printing into operations, enabling businesses to enhance efficiency and meet evolving production needs
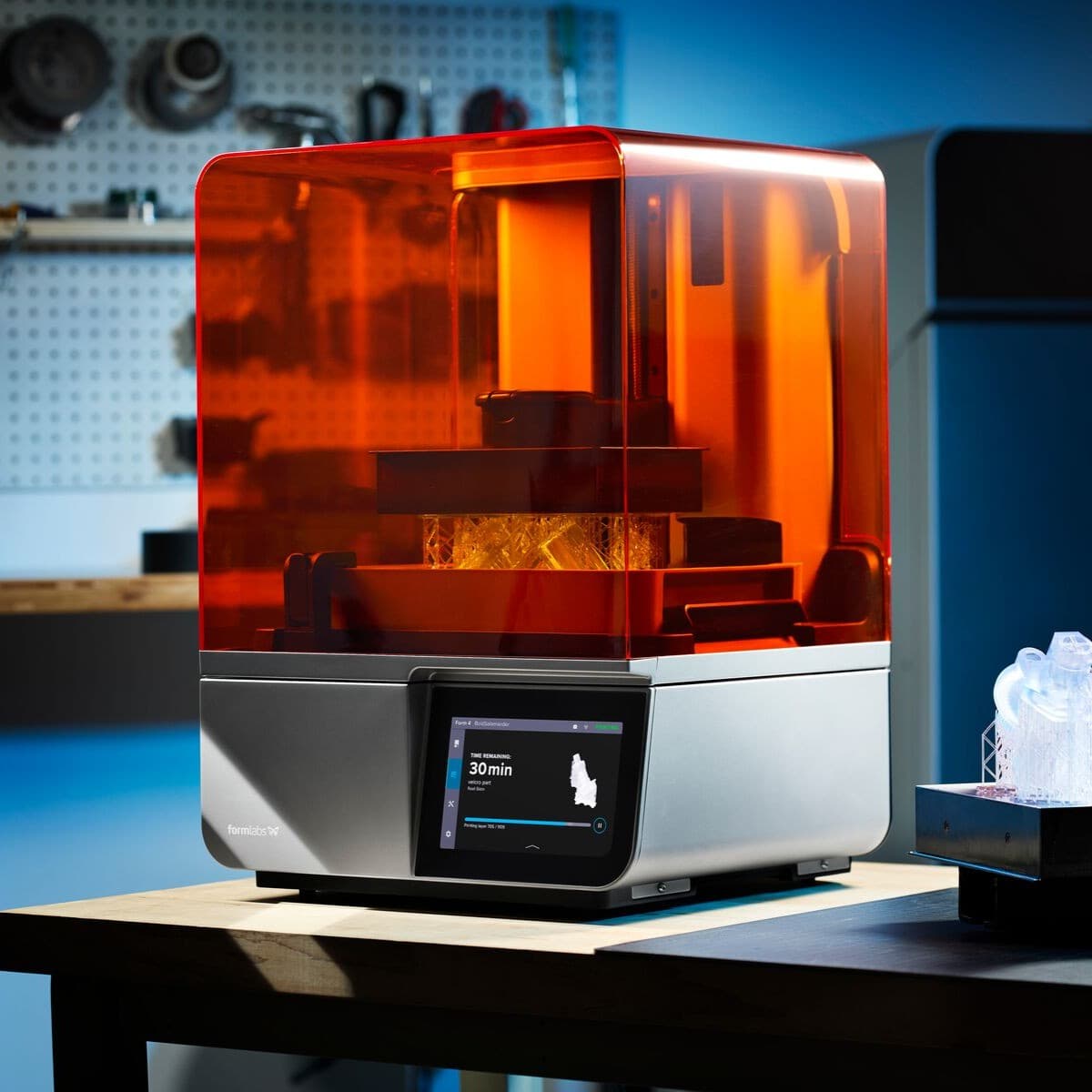
Book a Consultation
Get in touch with our 3D printing experts for a 1:1 consultation to find the right solution for your business, receive ROI analyses, test prints, and more.
Introduction
Increase Precision, Efficiency, and Safety With Jigs and Fixtures
Metalworking is the process of shaping and forming metals to fabricate metal products. Metal components are highly valued for their durability, strength, reliability, and resistance to wear and high temperatures, making metalworking a critical element in global manufacturing. It plays a pivotal role in end-use industries such as automotive, aerospace, construction, energy, and consumer goods as they rely heavily on metal parts for applications ranging from car frames to aircraft components, heavy machinery, and medical devices. As these sectors grow, the pressure to produce high-quality metal parts quickly and cost-effectively has increased. The need for precision, efficiency, and scalability has driven the evolution of tools and techniques making them an essential part of the metalworking process.
Among the most common metalworking techniques are machining, welding, forming, and casting. As they often involve high forces, heat, or chemical exposure, each of these processes requires specialized tools to hold metal parts in place, guide tools, and ensure precision, safety, and repeatability in production. For example, jigs help guide cutting tools to ensure consistent, precise cuts, while fixtures hold workpieces securely in place during machining or welding to prevent movement that could result in errors. Traditional tooling methods, such as CNC machining, casting, or manual assembly, are time-consuming and expensive. The time required to produce a custom tool can range from several days to weeks, depending on the part's complexity, and costs typically range from hundreds to thousands of dollars per tool.
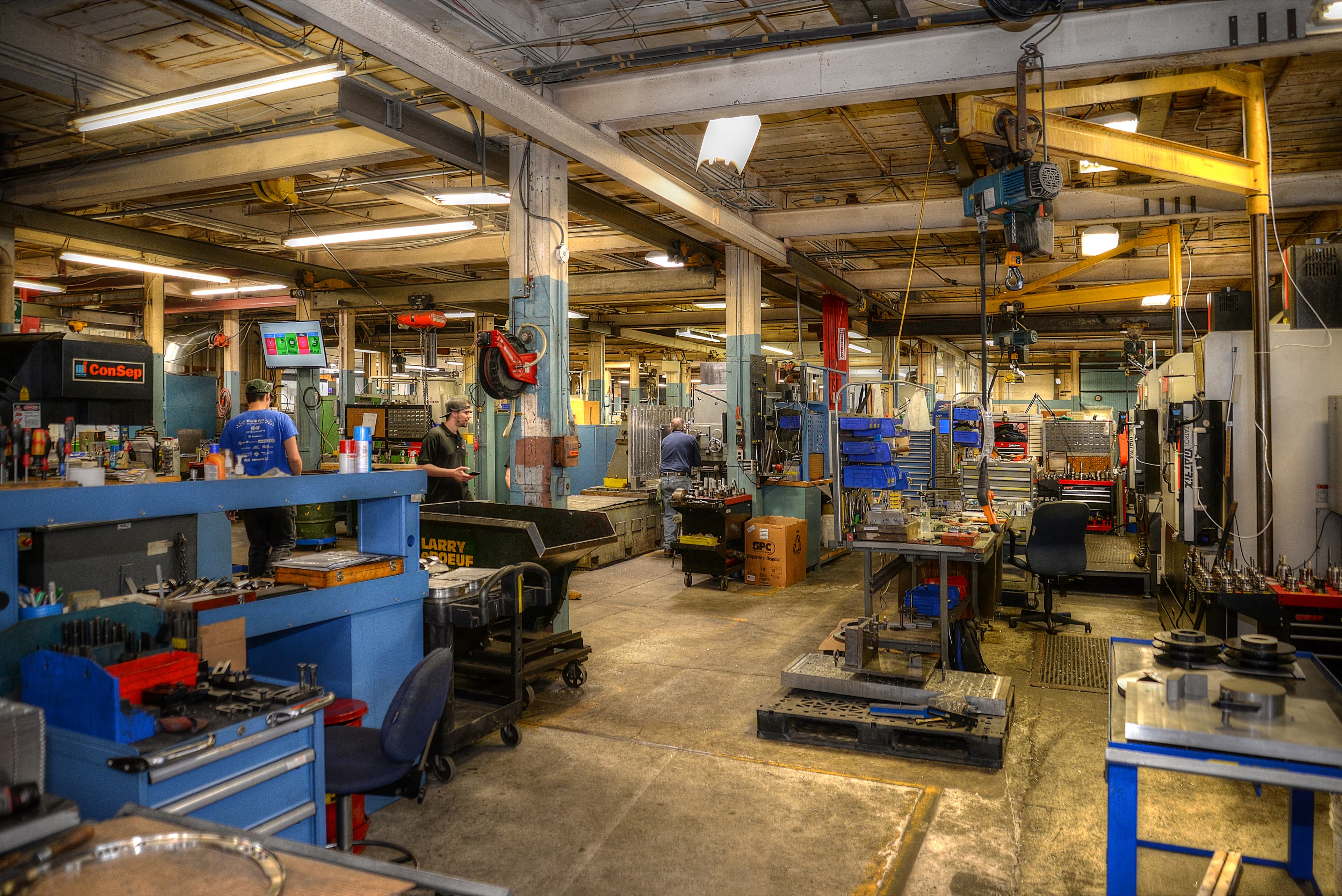
A&M Tool and Design’s machine shop includes a vast range of technologies, from Bridgeport CNC machines to large-scale manufacturing automation equipment like the PALLETECH to Formlabs SLA 3D printer.
As tooling often needs to be customized to accommodate specific part geometries, creating these customized tools with conventional methods leads to extended lead times and high costs. Moreover, any change in the design of the part or process can require the creation of a completely new tool, further increasing costs and delaying production. This inefficiency poses a challenge in industries that require frequent prototyping, small-batch production, or rapid design iterations; the expense of producing tooling hinders design iterations and limits flexibility. The challenges associated with traditional tooling are compounded by the need for precise alignment, repeatability, and rigidity in metalworking processes, which make it difficult to produce affordable, high-quality jigs and fixtures
Reduce Costs and Lead Times With 3D Printed Jigs and Fixtures
3D printing technologies, particularly stereolithography (SLA) and selective laser sintering (SLS), offer a compelling alternative for manufacturing jigs, fixtures, and tooling in metalworking. Compared to traditional manufacturing, 3D printing is significantly faster and more cost-effective, especially for custom or complex designs. A custom jig that might take two to three weeks and cost upwards of $1,000 to machine can most likely be printed in a few hours for a fraction of the cost using an SLA or SLS printer.
Formlabs printers offer the precision necessary for accurate and repeatable jig and fixture production, and the materials used in SLA and SLS printing are robust enough to withstand the harsh environments of metalworking applications. The use of 3D printing for tooling in metalworking brings a variety of benefits that address many of the challenges posed by traditional manufacturing methods:
Reduced lead times: 3D printing can produce jigs and fixtures significantly faster than traditional manufacturing methods, often cutting lead times by up to 90-95%.
Lower costs: The elimination of expensive equipment and manual labor associated with traditional tooling leads to significant cost savings, potentially reducing tooling costs by up to 90-95%.
On-demand production and digital inventory: 3D printing allows for on-demand production, minimizing the need for large physical inventories and enabling quick adjustments or replacements.
Design freedom and customization: Unlike traditional methods, 3D printing supports complex geometries and allows for easy customization, facilitating rapid modifications for different parts or projects.
Precision and repeatability: Compared to manual methods or fused deposition modeling (FDM) 3D printing, SLA and SLS technologies provide higher levels of accuracy. This ensures that jigs and fixtures are produced with precise dimensions and consistent quality across iterations.
Lightweight and ergonomic: 3D printing enables the creation of lightweight tools without sacrificing strength, improving ergonomics for operators and reducing material costs.
Formlabs is positioned to meet the needs of the metalworking industry by offering industrial-grade machines at affordable price points. With high-resolution SLS and SLA printers, robust material options, and intuitive software, companies can bring 3D printing in-house, reducing reliance on suppliers and speeding up production. Formlabs also provides automated post-processing solutions to streamline the entire process from design to finished tool.
This white paper will outline methods and case studies demonstrating how businesses can leverage Formlabs' 3D printers to produce on-demand, customized jigs and fixtures in order to streamline their tooling process.
“We are a machine shop, so we can produce very high-precision components, but the less time the peripheral tooling takes to manufacture and the less it ties up our production equipment, the better. And unlike a CNC machine, even if I'm running a production run on the Fuses, I can still pop some little tools in there in between print jobs or mixed in with other parts.”
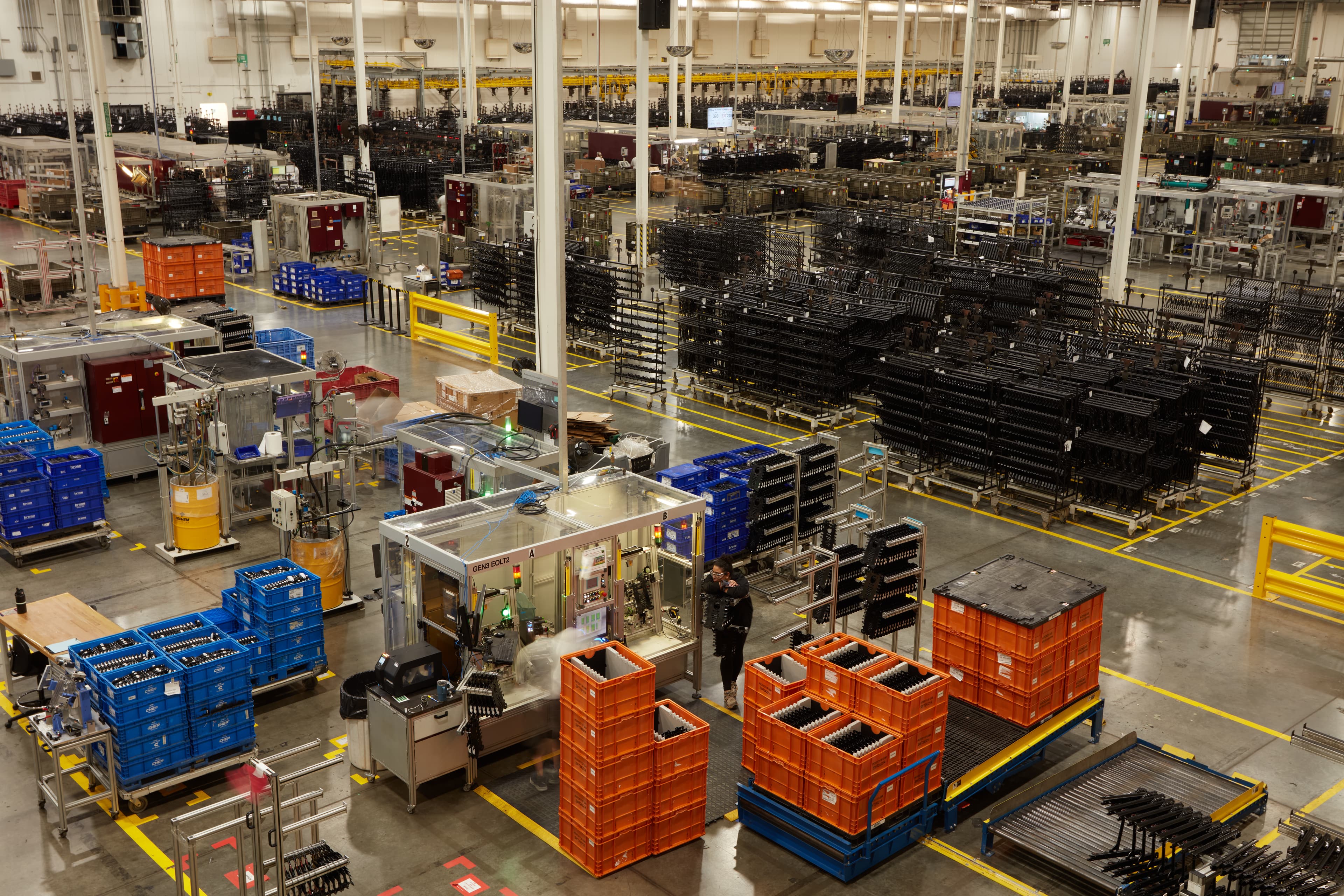
Global automotive supplier Brose, leverages SLA and SLS 3D printing in their end-use manufacturing facilities to produce complex products like car seat assemblies.
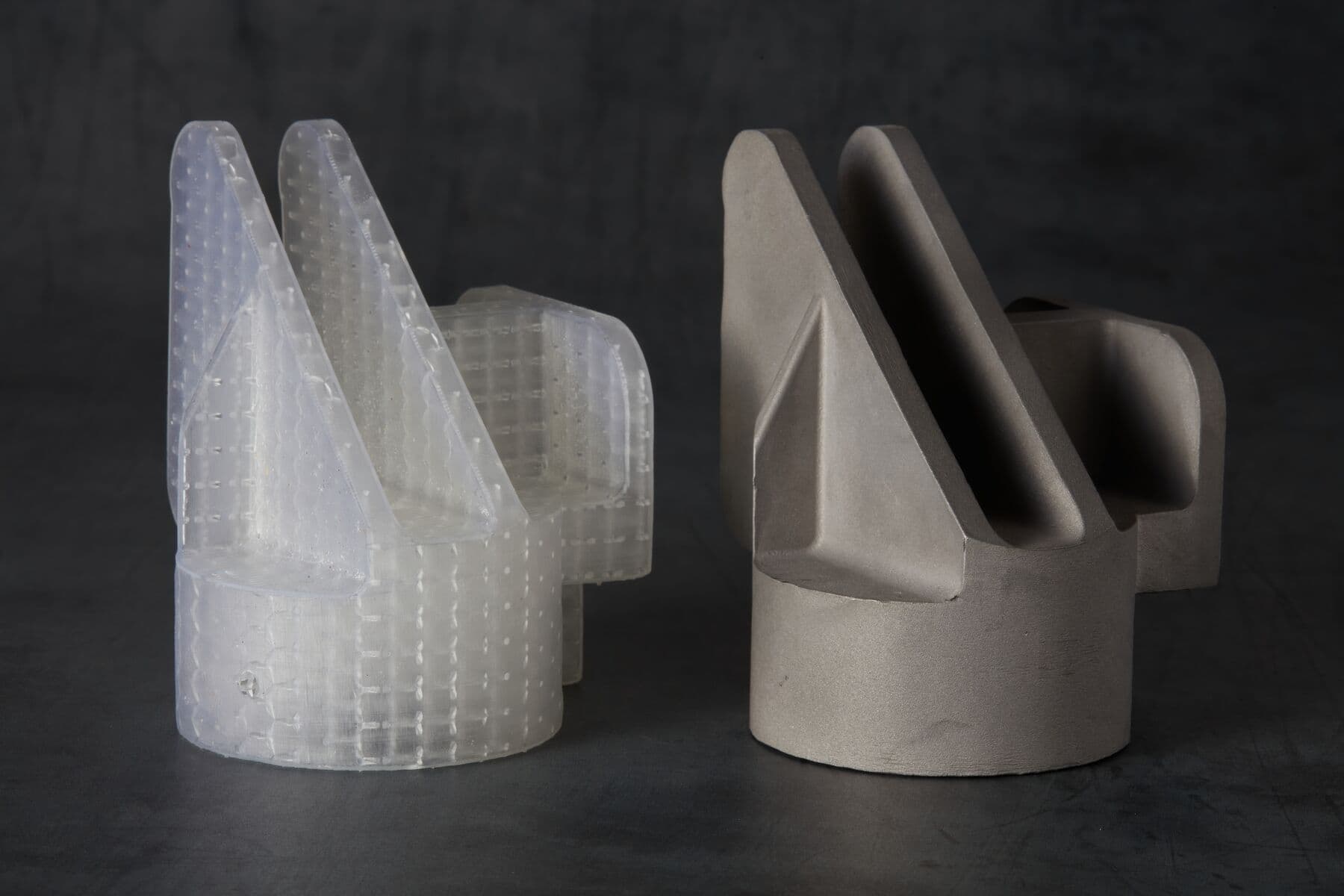
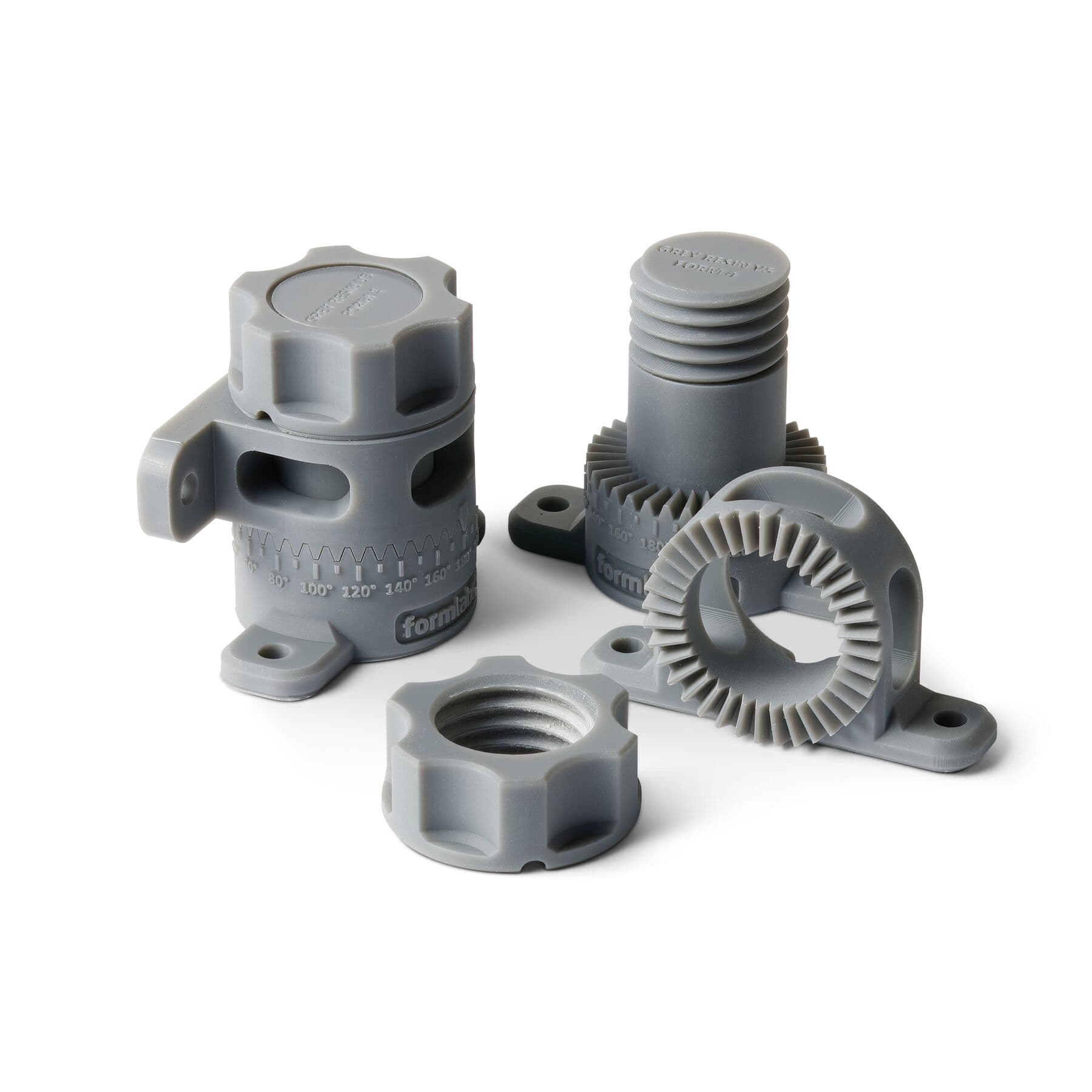
Request a Free Sample Part
See and feel Formlabs quality firsthand. We’ll ship a free 3D printed sample part to your office.
Method
Common Metalworking Processes and Tools
Machining Jigs
Machining is a subtractive manufacturing process that removes material from a workpiece using tools like lathes and mills. It is crucial for producing precision components. Jigs and fixtures play a vital role in securely holding workpieces and ensuring accurate alignment during machining. Technical requirements for these jigs include high rigidity to withstand cutting forces, precise dimensions to maintain alignment, thermal stability to resist distortion from the heat generated during machining, vibration damping, and resistance to coolants, cutting fluids, and cleaning agents running inside the machines.
Formlabs recommends 3D printing machining jigs with Nylon 12 Powder on the Fuse Series because of the chemical resistance of nylon 12.
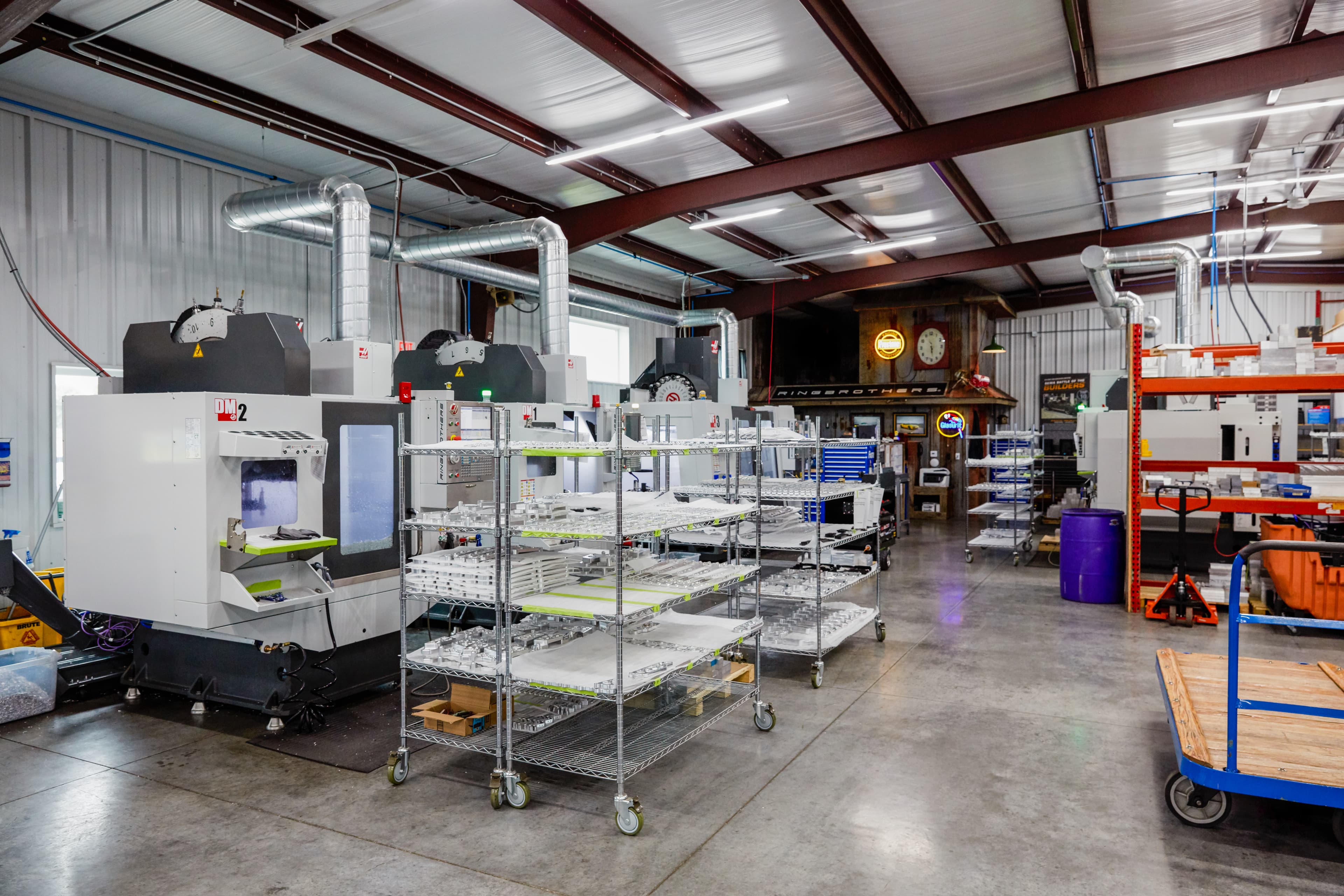
CNC machines at the Ringbrothers’ shop.
Welding Fixtures
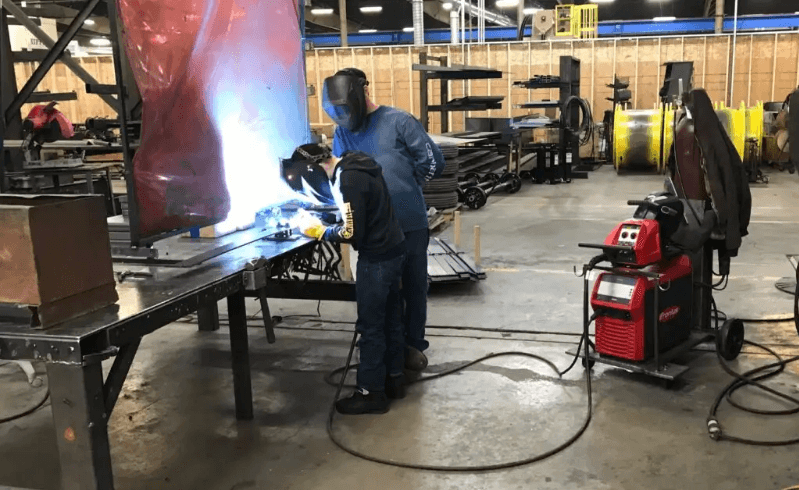
Welding operations at the Red Oak Fabrication’s shop.
Welding is a fabrication process that joins materials by applying heat and pressure to create strong bonds. Common techniques include arc welding, MIG, and TIG, widely used in construction and manufacturing for durable connections. Jigs and fixtures are essential for accurately positioning workpieces and maintaining alignment during welding. These tools must be highly heat-resistant, rigid, and durable to handle repeated cycles without warping. Precision alignment and ease of clamping are essential for accurate, repeatable welds while safety features and accessibility are critical for operator protection.
Formlabs recommends 3D printing welding fixtures with Rigid 10K Resin on the Form Series, because of the high-temperature resistance of the resin. 3D printing with Nylon 12 Powder on the Fuse Series is also an option for low-heat welding processes such as ultrasonic welding.
Tools for Forming, Assembly, Casting, and More
This white paper focuses on 3D printed jigs and fixtures for working with metal parts, in particular welding and machining. The case studies also include examples of robotic grippers and assembly fixtures. Formlabs users are already 3D printing manufacturing aids on the factory floor to streamline operations as well as rapid tooling to enable low-volume production. Consult the following documentation to learn more about 3D printed tools:
- Manufacturing aids for assembly, inspections, replacement parts, etc…
- Dies for sheet metal forming
- Patterns for investment casting
- Molds for injection molding, silicone molding, blow molding, and thermoforming
Workflow
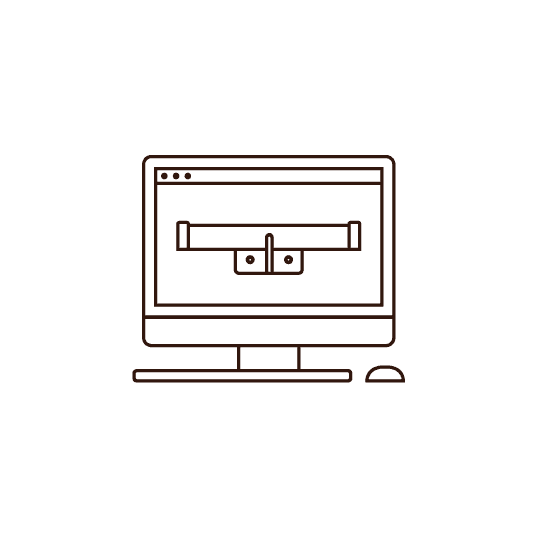
Design
Build a model of the part in CAD, respecting common design rules for additive manufacturing, or reverse engineer it with 3D scanning.
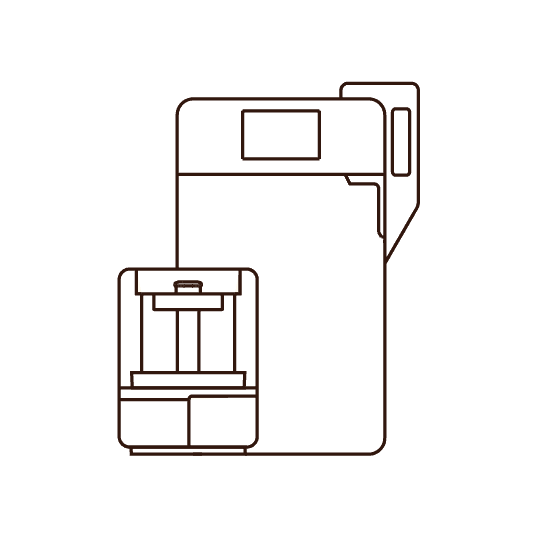
3D Print
Upload the design into PreForm print preparation software, choose the printer and material, and start the print.
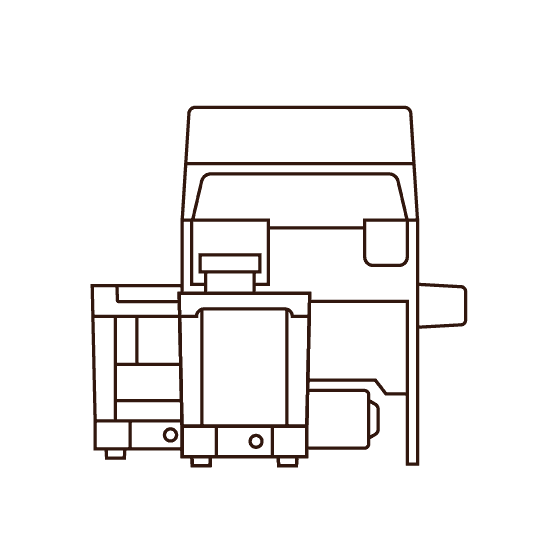
Post-Process
Finish the part according to the material specifications: wash and cure SLA parts or depowder SLS parts. Add advanced processing techniques if needed.
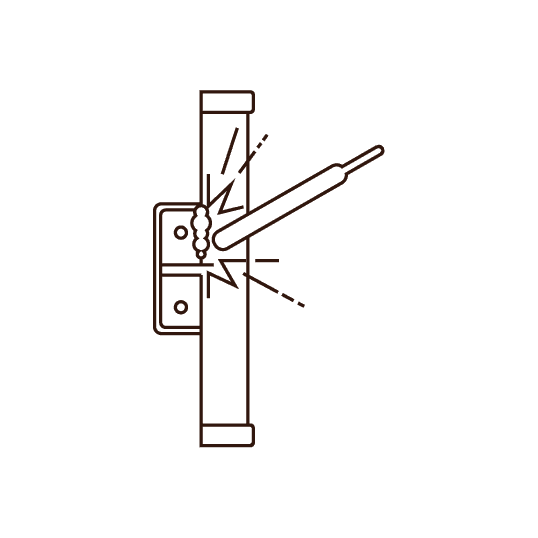
Deploy
Validate your part and integrate it into your machine or manufacturing operation. Store the CAD file in a digital inventory and replace it as needed.
3D Printing Guidelines
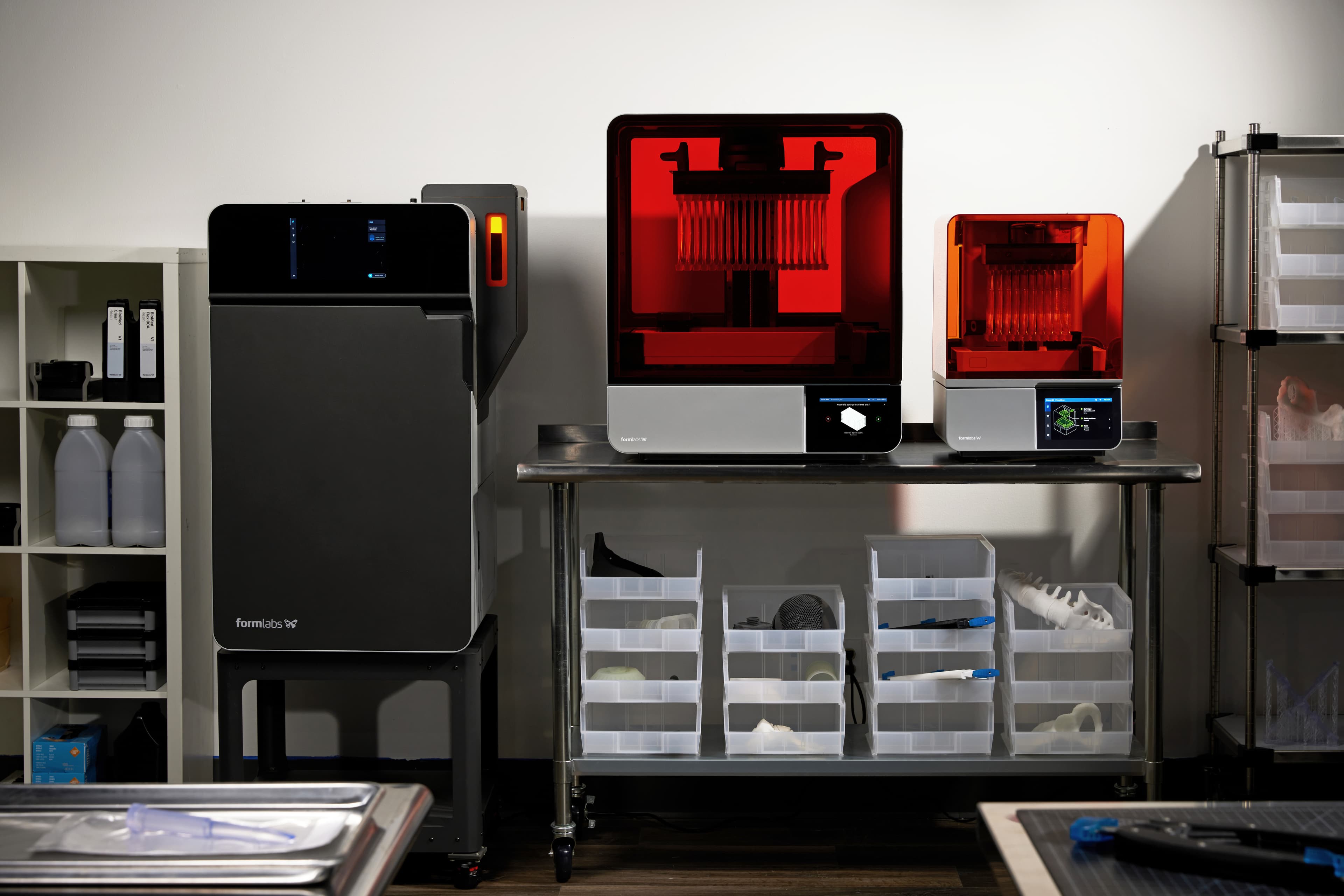
Formlabs printers Fuse 1+ 30W, Form 4L, and Form 4.
Choosing the Right 3D Printing Technology
Choose Formlabs SLS for:
- Strong, durable, heavy-duty tools: Parts that need to withstand high forces and repeated stress such as impact-resistant machining fixtures.
- Versatile, chemical-resistant, and environmentally stable: Nylon 12 Powder is a go-to material in 3D printing for general purposes. Nylon 3D printed parts absorb very little moisture and are resistant to light, heat, and chemicals. This is particularly important for machining tools as they are exposed to cooling solvents. Formlabs recommends choosing Nylon 12 Powder as the default material. For more specific use cases, consult the SLS materials catalog.
- Complex design and lightweight features: SLS eliminates the need for support structures, offering more design freedom for creating intricate or hollow geometries. It enables designs with lattice structures that reduce material use while maintaining strength, which is excellent for large, lightweight jigs used in sheet metal forming or machine replacement parts.
- High throughput: SLS is ideal for medium-volume production. The absence of supports allows operators to stack parts and reduce post-processing time. The Formlabs Fuse 1+ 30W build chamber enables operators to nest densely within the entire build volume, maximizing throughput and increasing efficiency. Formlabs' Fuse Sift and Fuse Blast simplify powder recovery and automate part cleaning and finishing.
Choose Formlabs SLA for:
- High precision, fine details, and smooth surface finish: Applications like machining alignment tools, location jigs, measurement devices, or ergonomic fixtures. Features such as custom grips for user comfort are easy to integrate.
- Wide range of material properties with an easy switch between resins: Build tools with various specifications such as elastic, ESD-safe, or flame-retardant, to enable specialized applications. Consult the SLA materials catalog for more information. Rigid 10K Resin is frequently used in metalworking environments, particularly for welding fixtures; it is a stiff and temperature-resistant material with an HDT of 218 °C @ 0.45 MPa and a tensile modulus of 10,000 MPa.
- Quick short-run production thanks to an accessible ecosystem: SLA is easy to use once the resin handling procedures are understood. Formlabs’ SLA ecosystem comes at lower price points, requires minimal equipment, and can be seamlessly integrated into any production workflow. It is a fast and easy solution for small-batch production of tools that don’t require extreme durability
Technology Comparison Table
The following table summarizes some key considerations when choosing between SLA or SLS for 3D printing manufacturing aids. Check out Formlabs’ in-depth technology comparison for more details. Both technologies can play complementary roles in a machine shop, allowing the creation of precise, durable, and customized jigs and fixtures for a variety of metalworking applications.
Selective Laser Sintering (SLS)
Fuse Series, Powder 3D Printing
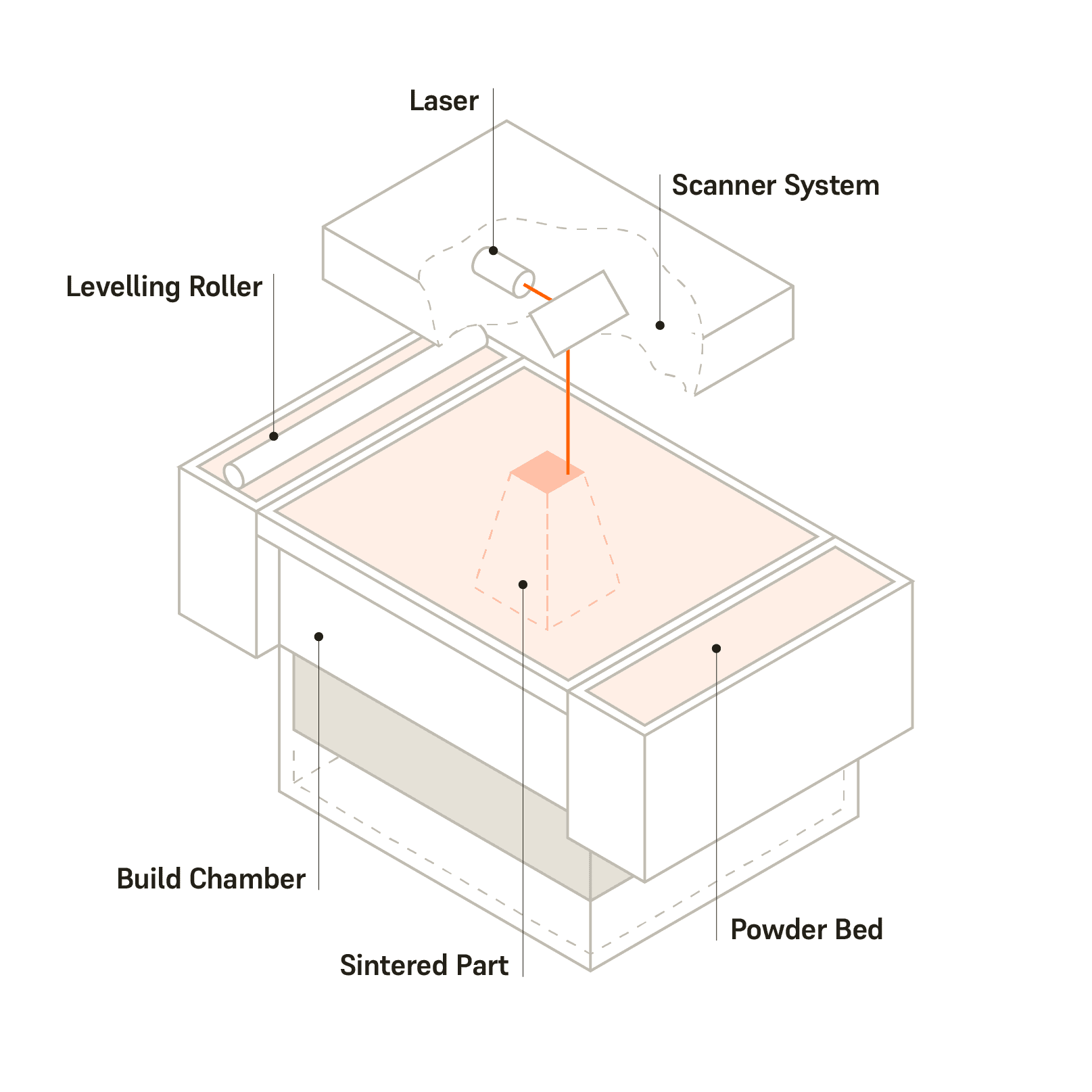
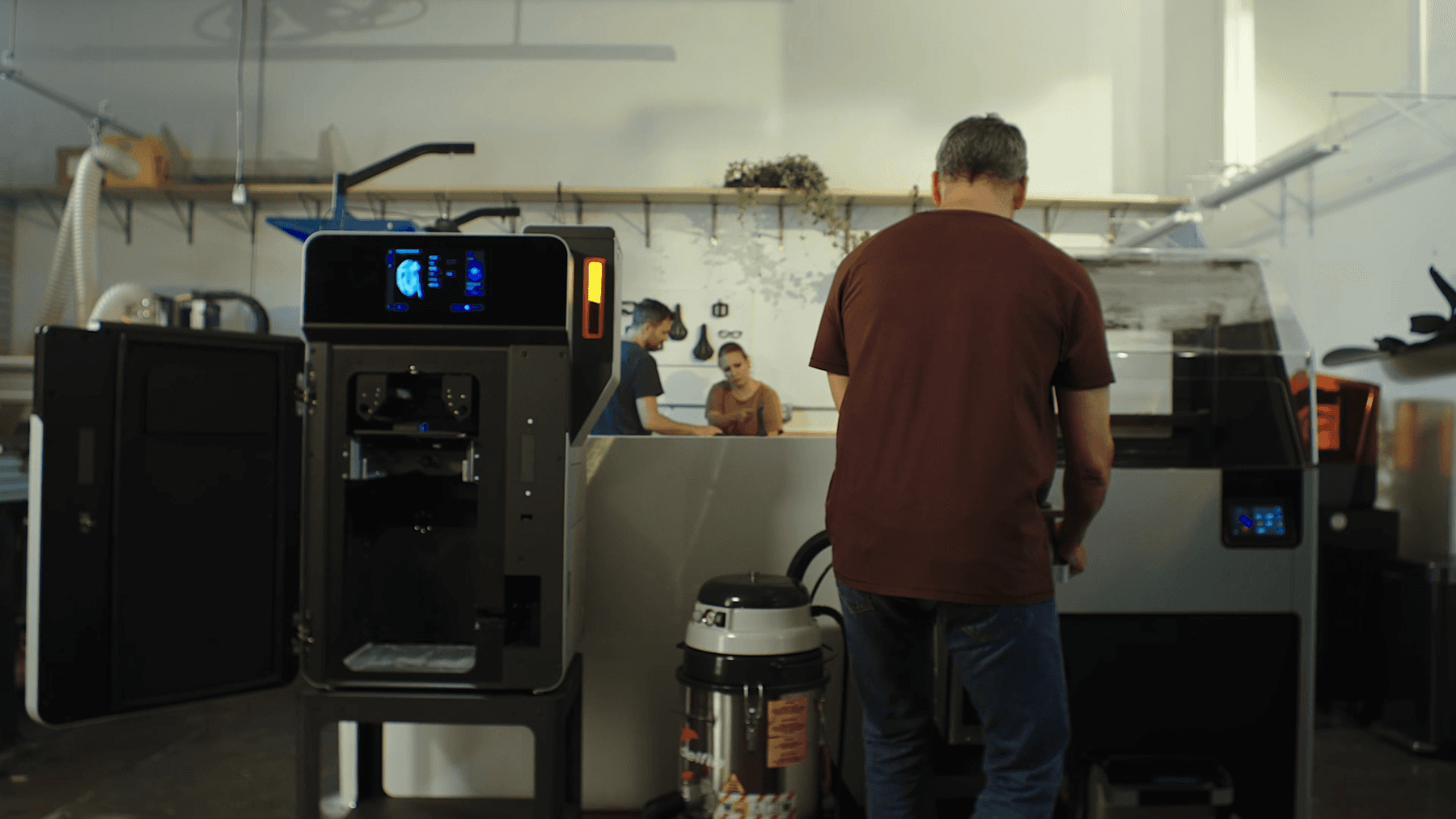
- Strong, durable, and heavy-duty tools
- Versatile, chemical-resistant, and environmentally stable
- Lightweight parts with complex design
- Cost-efficient for large volumes
Stereolithography (SLA)
Form Series, Resin 3D Printing
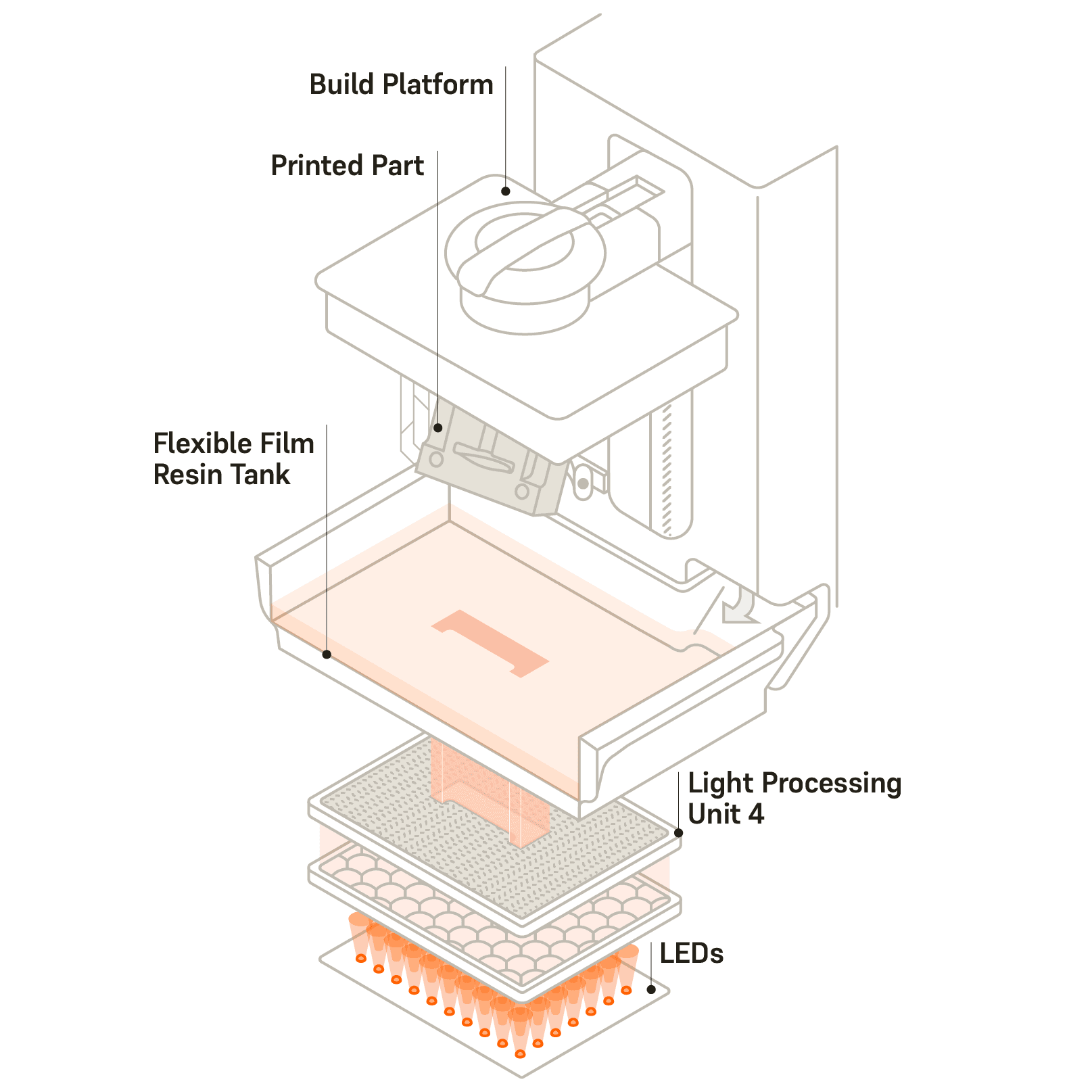
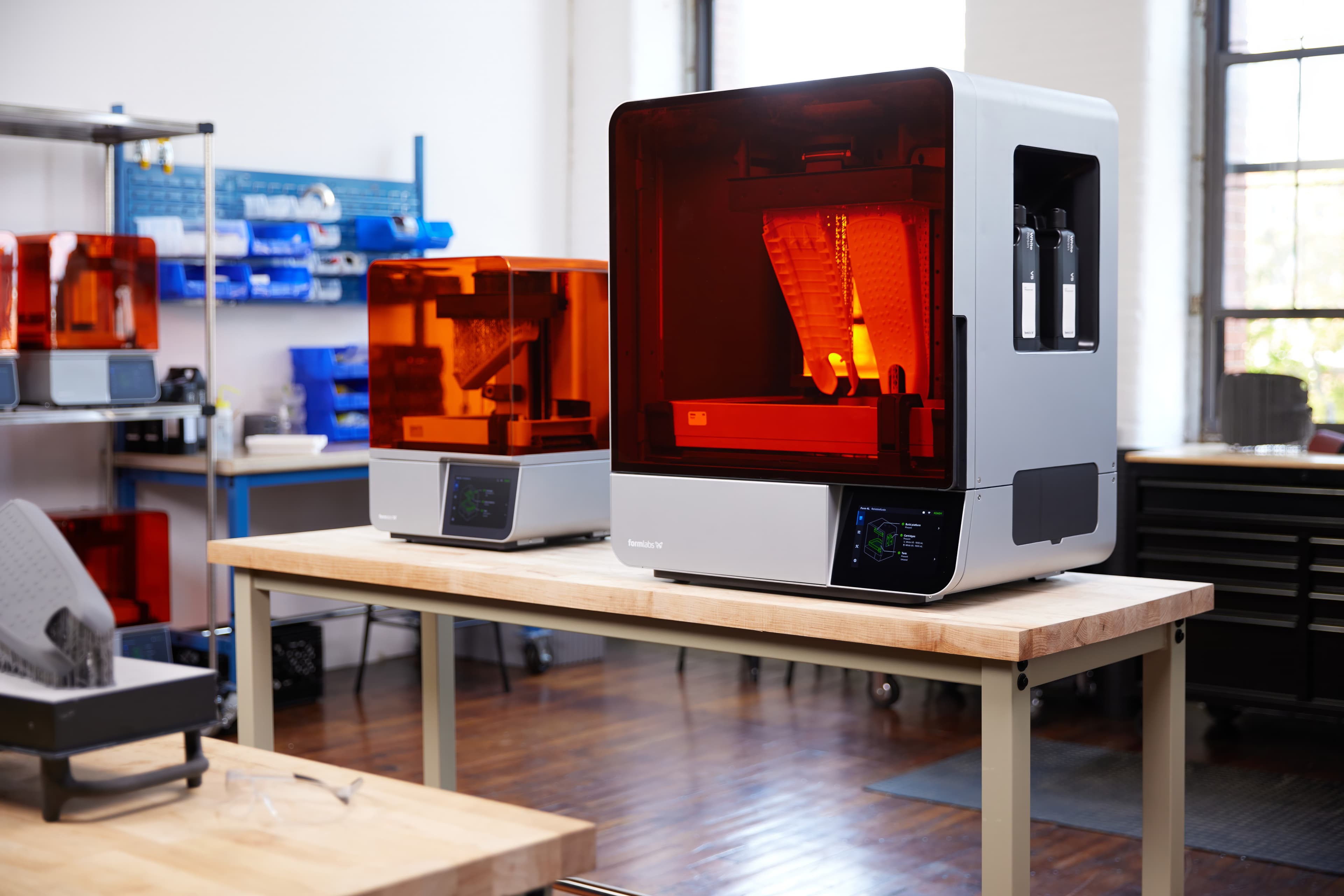
- Precise, smooth, and ergonomic tools with fine details
- Wide range of material properties
- Fast and easy for low-volumes
- Accessible entry price points
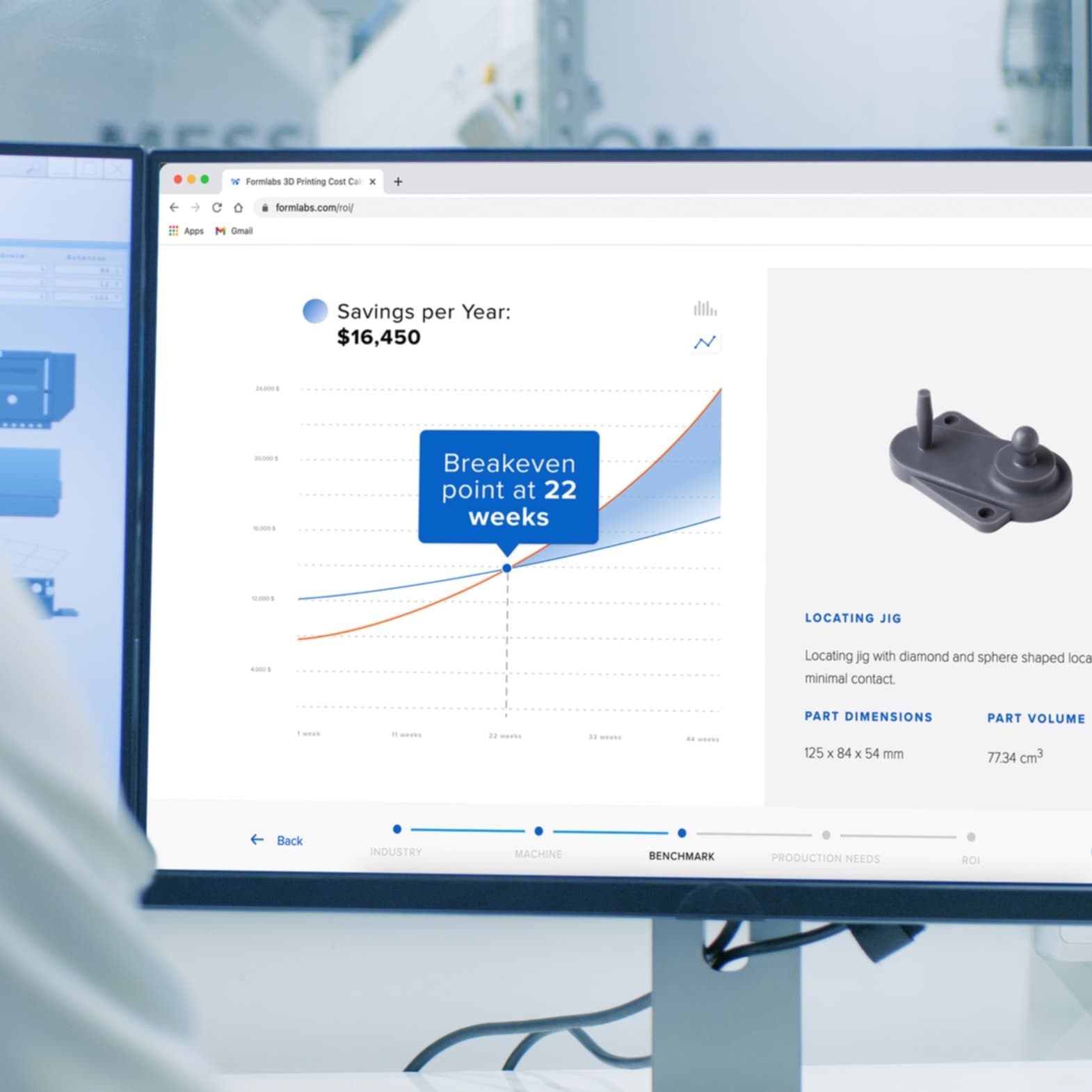
Calculate Your Time and Cost Savings
Try our interactive ROI tool to see how much time and cost you can save when 3D printing on Formlabs 3D printers.
Design Guidelines
Digitize existing tooling designs with reverse engineering to move to a digital inventory or identify tooling needs and design new tooling files. When designing a 3D printed jig or fixture, several key design considerations differ from traditional metal machined tools, allowing for unique features only possible with additive manufacturing:
Leverage complex geometries: Use 3D printing to create intricate internal features like channels, undercuts, and hollow structures, which are difficult and expensive to machine in metal. SLA is best for fine details and smooth surfaces, while SLS excels at durable, complex forms that can withstand mechanical stress.
Optimize for lightweight structures: Take advantage of SLS to create lightweight jigs with lattice or honeycomb structures. These reduce weight without sacrificing strength, which is hard to achieve with solid metal parts machined traditionally.
Design with precise wall thickness: SLA allows for precise, intricate designs with wall thicknesses around 2-3 mm. While not thinner than metal, SLA enables more complex shapes and smoother finishes without additional machining, which can improve performance and reduce costs.
Integrate multiple functionalities: 3D printing allows for the integration of features like clamps, locators, and guides into a single part. This simplifies design and reduces the need for multiple assembled components.
Incorporate smooth fillets for strength: Use SLA to add smooth fillets (1-2 mm radii) at stress points, reducing the risk of cracks and stress concentrations. While fillets are possible in machined metal, 3D printing enables more efficient, stress-resistant designs with fewer manufacturing steps.
Enhance ergonomics: Add ergonomic features such as custom grips or contoured edges directly into your SLA designs. These details improve usability and are easier and less costly to incorporate than in traditional machined metal tools.
Design for modularity and customization: Use SLS to create modular jigs and fixtures that can be easily customized or updated. This flexibility allows for faster adjustments and replacements compared to remanufacturing entire metal tools, saving time and cost.
Reduce assembly with single-part designs: Consolidate complex assemblies into a single 3D printed part, minimizing assembly time and reducing misalignment risks. SLA and SLS can streamline production workflows, offering fewer parts to manage and align compared to multi-part metal fixtures.
Post-Processing Guidelines
Formlabs SLA and SLS parts can undergo advanced post-processing methods to improve the aesthetics, mechanical properties, and overall performance of your parts. After cleaning SLA parts with isopropyl alcohol, techniques such as sanding, painting, or coating can be applied for a desired finish. SLS parts can benefit from media blasting or chemical smoothing to improve surface texture. Consult Formlabs post-processing guide to learn more.
Case Studies
The following case studies highlight the use of Formlabs SLA and SLS printed parts for welding fixtures, machining tools, and lightweight robotic grippers picking up heated (80 °C) metallic inserts. They show that Formlabs Rigid 10K Resin and Nylon 12 Powder parts are suitable for working metal in high temperatures while allowing savings between 100 and 10,000 per tool compared to alternative methods.
Validation: 3D Printing Jigs and Fixtures for Welding and Machining
Formlabs' headquarters in Somerville, MA includes a 3,000 square feet (278 square meters) machine shop delivering prototypes for the R&D team. It is a high-mix, low-volume manufacturing environment equipped with multiple CNC milling machines, CNC lathes, manual Bridgeport stations, water jets, laser cutters, tungsten inert gas (TIG) welding stations, and dedicated areas for inspection and metrology. The team uses 3D printed jigs and fixtures for all kinds of metalworking jobs: vise jaws, machining jigs, sheet metal bending dies, welding fixtures, and more.
Most of the requests the team needs to fulfill are one-offs or low-volume series of dozens of units. For this, they usually 3D print tools with Rigid 10K Resin on Form 4 for its speed. However, to 3D print workholding going inside the CNC machines they use the Fuse Series with Nylon 12 Powder because it is resistant to coolants, unlike SLA resins.
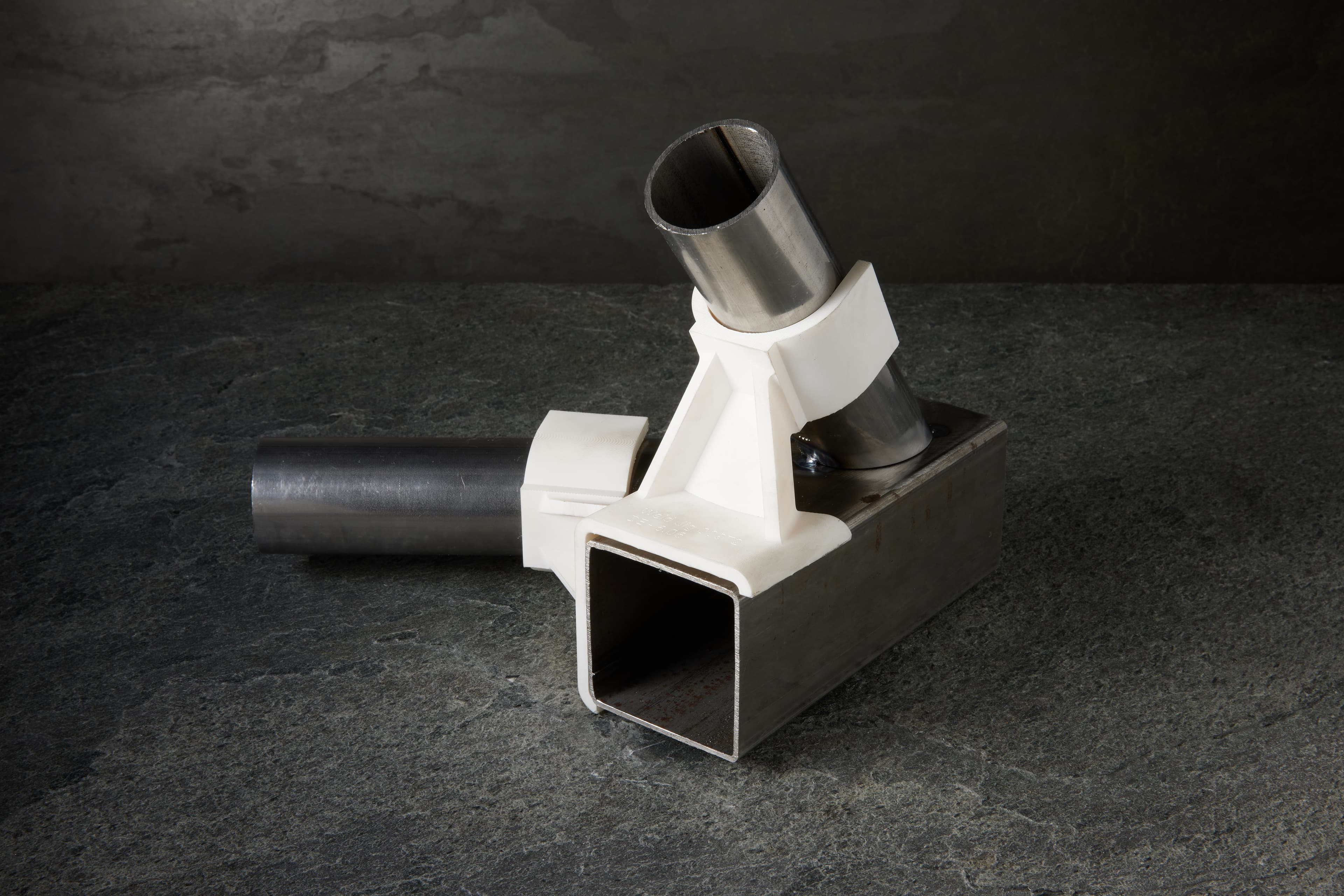
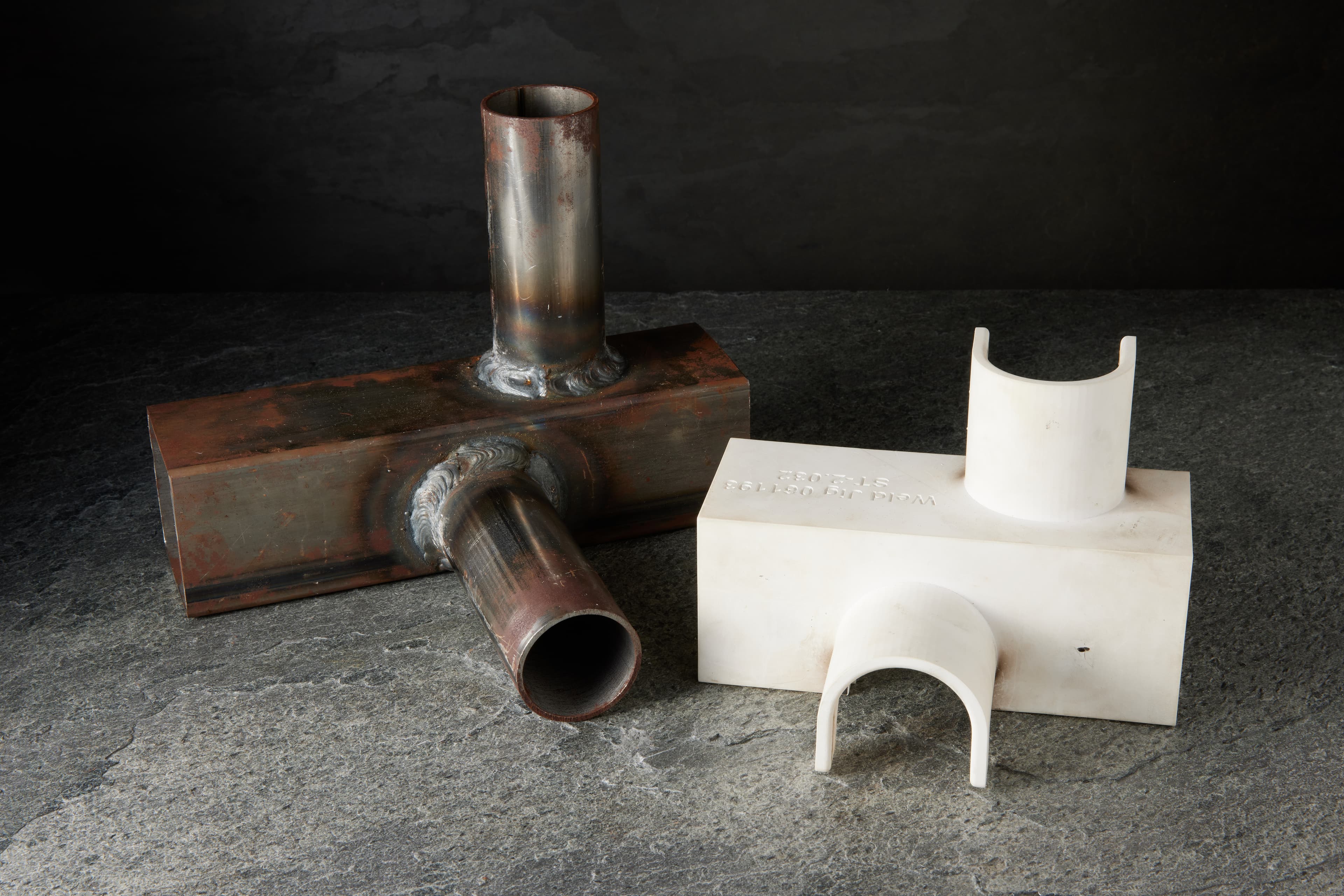
The team designed a quick test fixture to evaluate multiple Formlabs materials for TIG welding. Rigid 10K Resin, High Temp Resin, Clear Resin, Nylon 12 Powder, and Nylon 12 GF Powder were tested. The results show that Rigid 10K Resin is the most suitable material for welding at high temperatures. While the other materials reacted to the heat, 3D printed Rigid 10K Resin tools remained functional after welding.
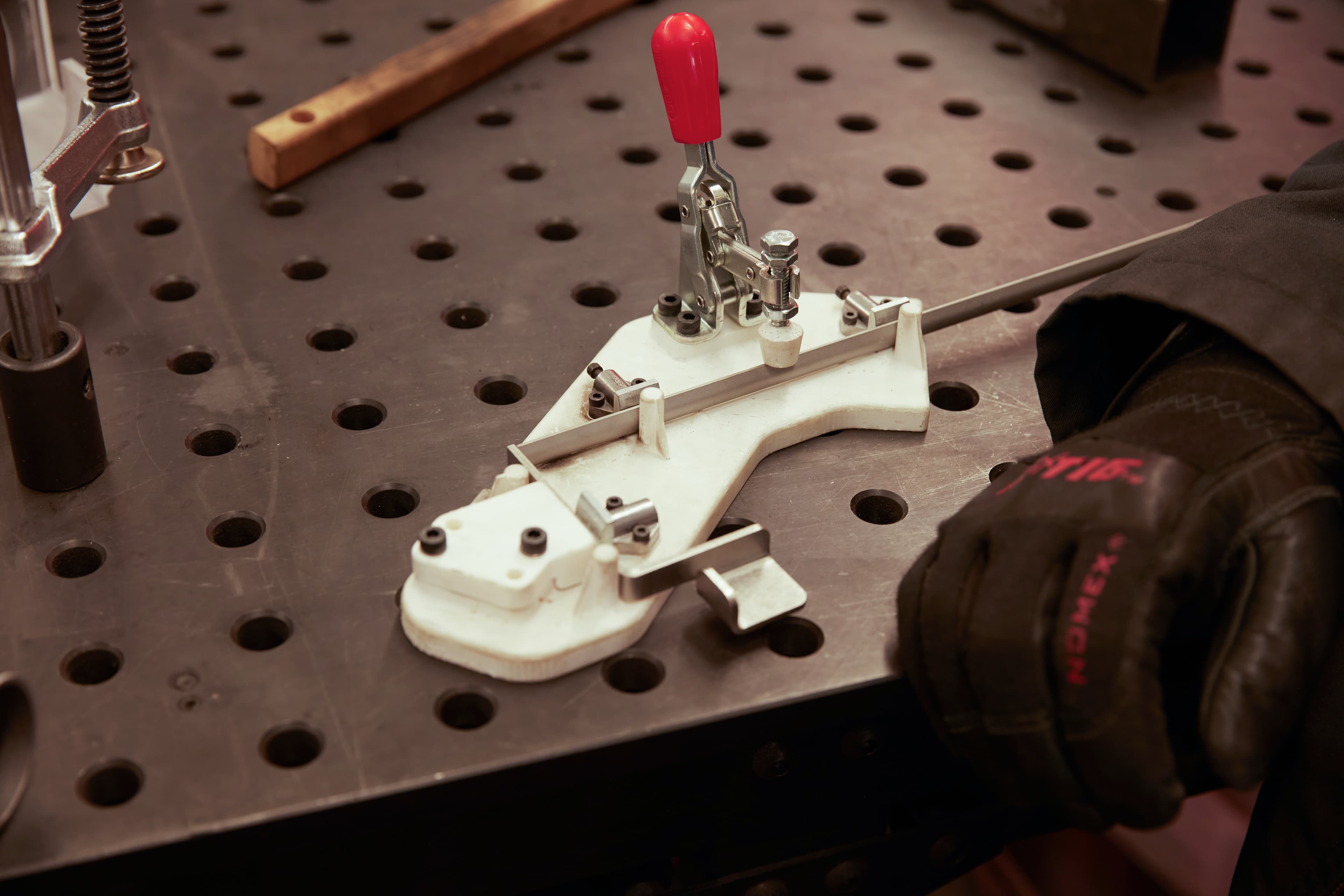
Welding fixture used by Formlabs engineers to weld the handle to the rod on the Build Platform Flex prototypes. The fixture is 3D printed with Rigid 10K Resin and is still functional after a few hundred parts.
Metal Fabrication Company 3D Prints Welding Jigs With Rigid 10K Resin
Red Oak Fabrication is a multi-faced fabrication enterprise based in Southwest Iowa that manufactures products in steel, stainless steel, and aluminum. Equipped with cutting-edge technologies, they can utilize all the industry-standard technologies to produce a metal product from start to finish. They specialize in precision plasma, laser, and water jet cutting, CNC operations, steel blasting, powder coating, sheet metal forming, and advanced robotic welding. Welding, primarily metal inert gas (MIG) welding, is a large part of their activity, with about 15 manual welding stations and three automated robotic welding cells.
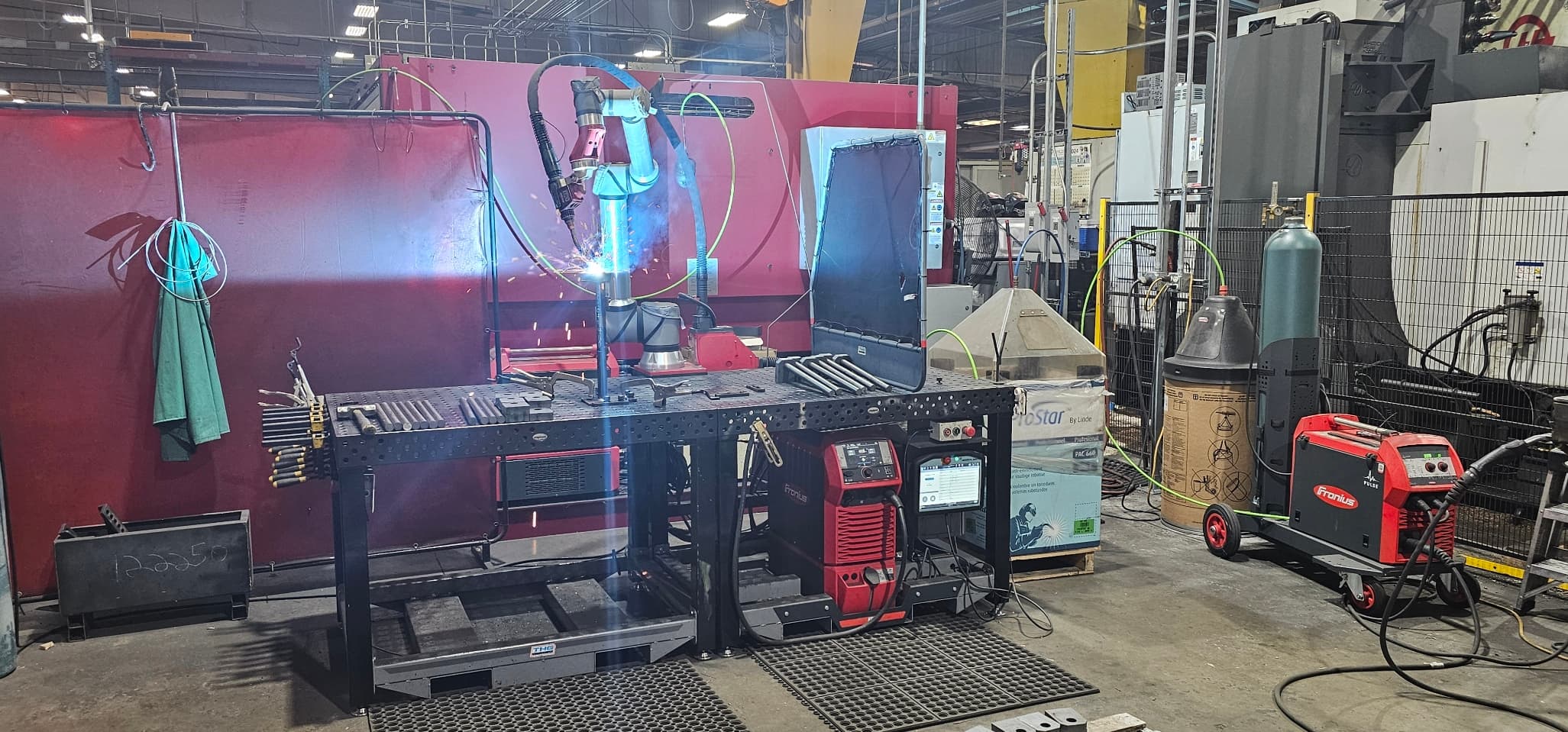
Red Oak Fabrication Genesis welding cell, equipped with a Fanuc Robotic arm.
Tool-making is critical to support daily welding operations and improve efficiency. They had two methods available in-house for making welding jigs. One option was to mount sheet metal parts together; it is rather easy and affordable but does not build accurate tools. Alternatively, they could choose to use CNC machining to fabricate high-quality metal jigs, but this comes with high costs and long lead times. However, none of these methods can respond to small and medium series orders without lead times and high costs.
To address this gap, they acquired a Form 3L SLA 3D printer to 3D print accurate and robust jigs and fixtures in one day, for a tenth of the price of CNC machining. 3D printing not only allows them to print high-quality jigs at reduced costs and time (up to 90%), but it also enables them to build complex geometries and organic shapes that would be difficult to produce in any other way. The team typically welds a few thousand parts per jig to deliver small to medium-series orders to their customers. “3D printing has opened up an easy middle ground. I can go from design to a finished jig in a couple of days instead of a couple of months,” says Taylor Smith, Drafting and Engineering Manager at Red Oak Fabrication.
Welding jig cost analysis:
Alternative Method |
3D Printing In-House |
|
Equipment |
Metal CNC machined in-house |
Form 3L, Rigid 10K Resin |
Cost |
$1,000 |
$100 |
Time |
Months |
Days |
Welding operations typically reach temperatures of a few thousand degrees Celsius, which is a challenging environment for polymeric tooling. Therefore the team chose to print with Rigid 10K Resin: a stiff and temperature-resistant material. Because the jigs are not directly in contact with the weld and the processing time is only about 10 seconds, the tools do not heat up in excess.
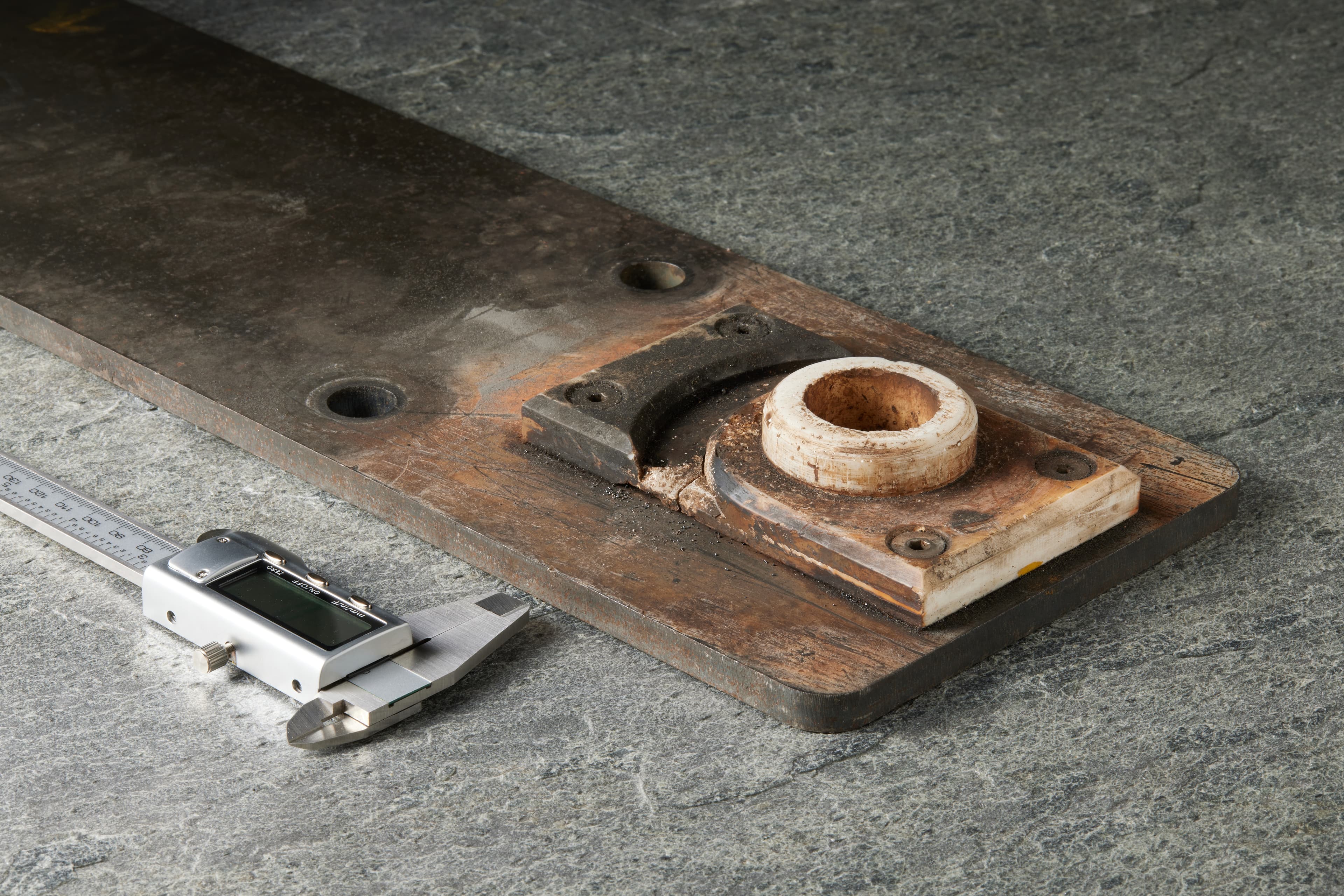
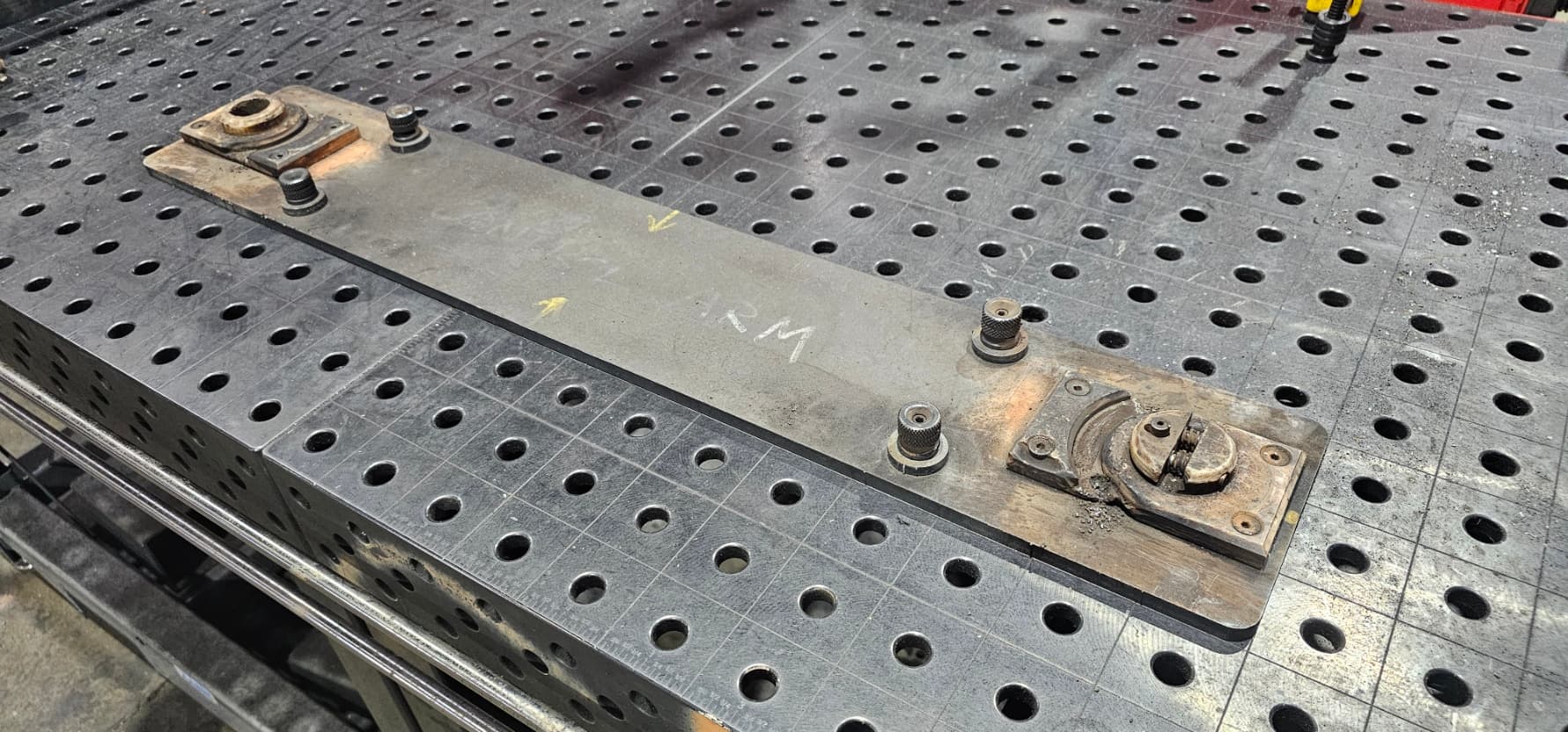
The straight arm jig is made of two small 3D printed parts mounted over a steel plate. The geometry is complex with organic shapes that would be challenging to machine and the team needed the tool in one day. After running about 2,000 welds on that jig it is still functional, even though some welds have dropped on the jigs by accident, causing some marks.
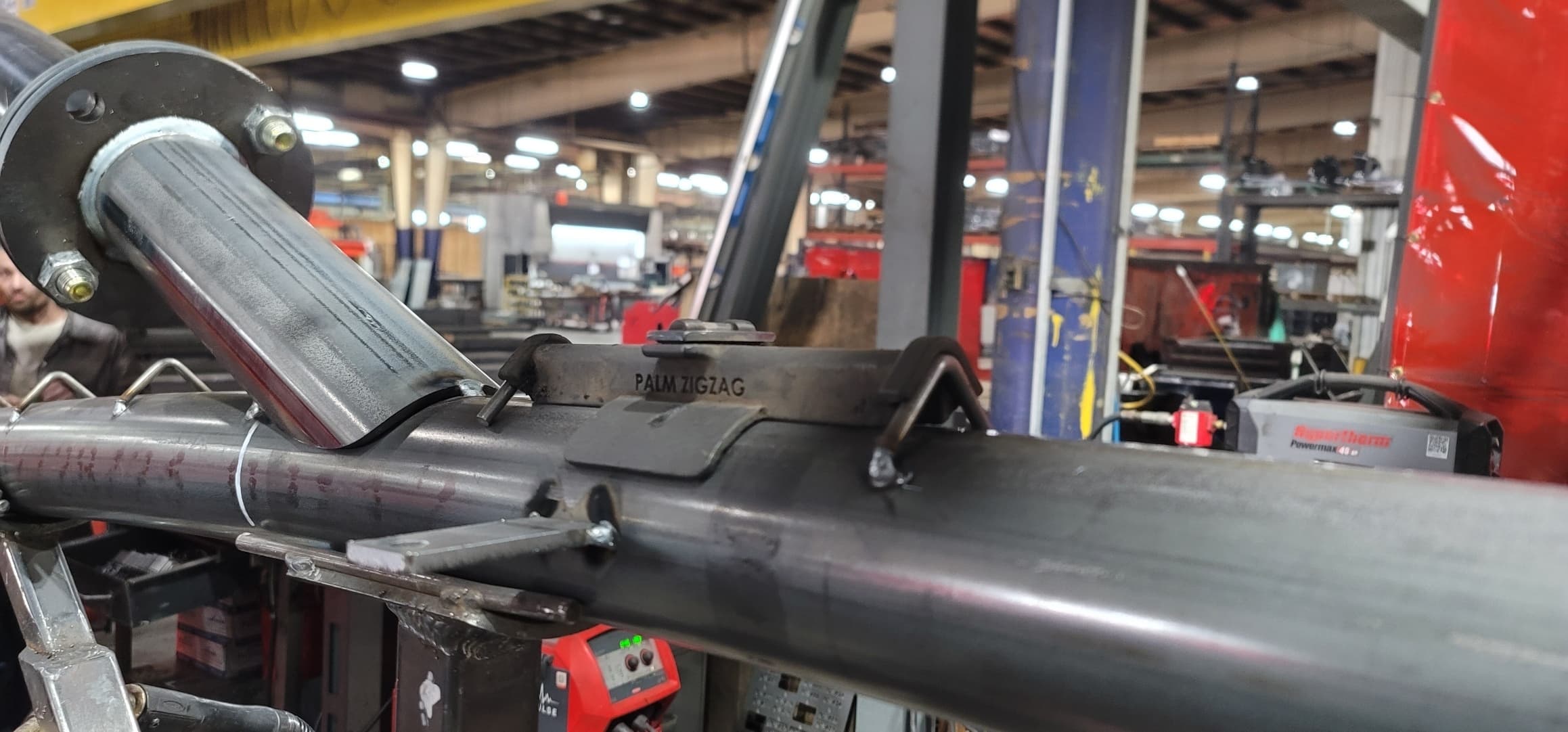
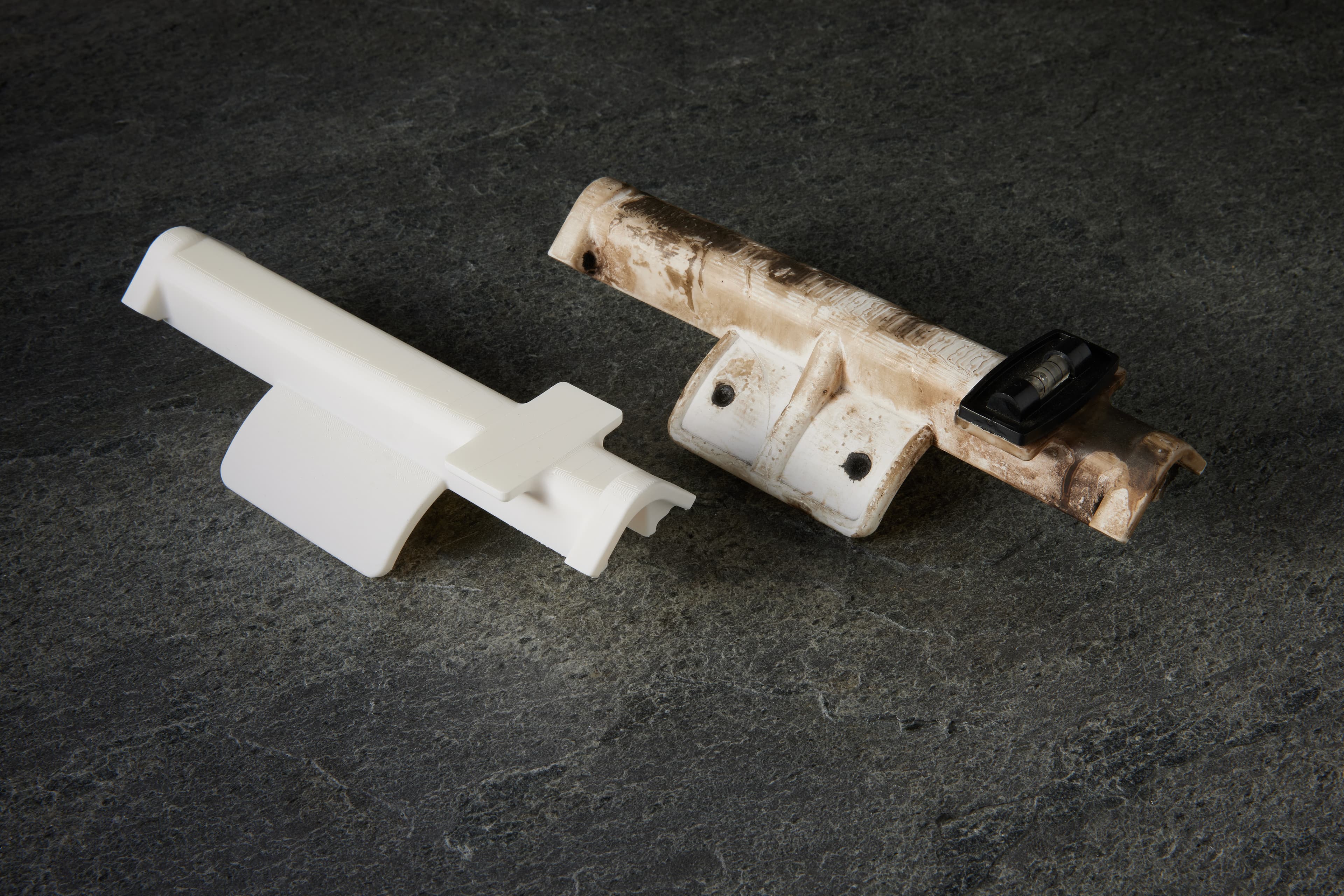
The zigzag jig welds 20 round bars along a pipe. This geometry is complex with an organic shape that would be challenging to machine. This jig ran thousands of welds and is still functional, though its color turned to black from white over time as it stays fairly close to the weld.
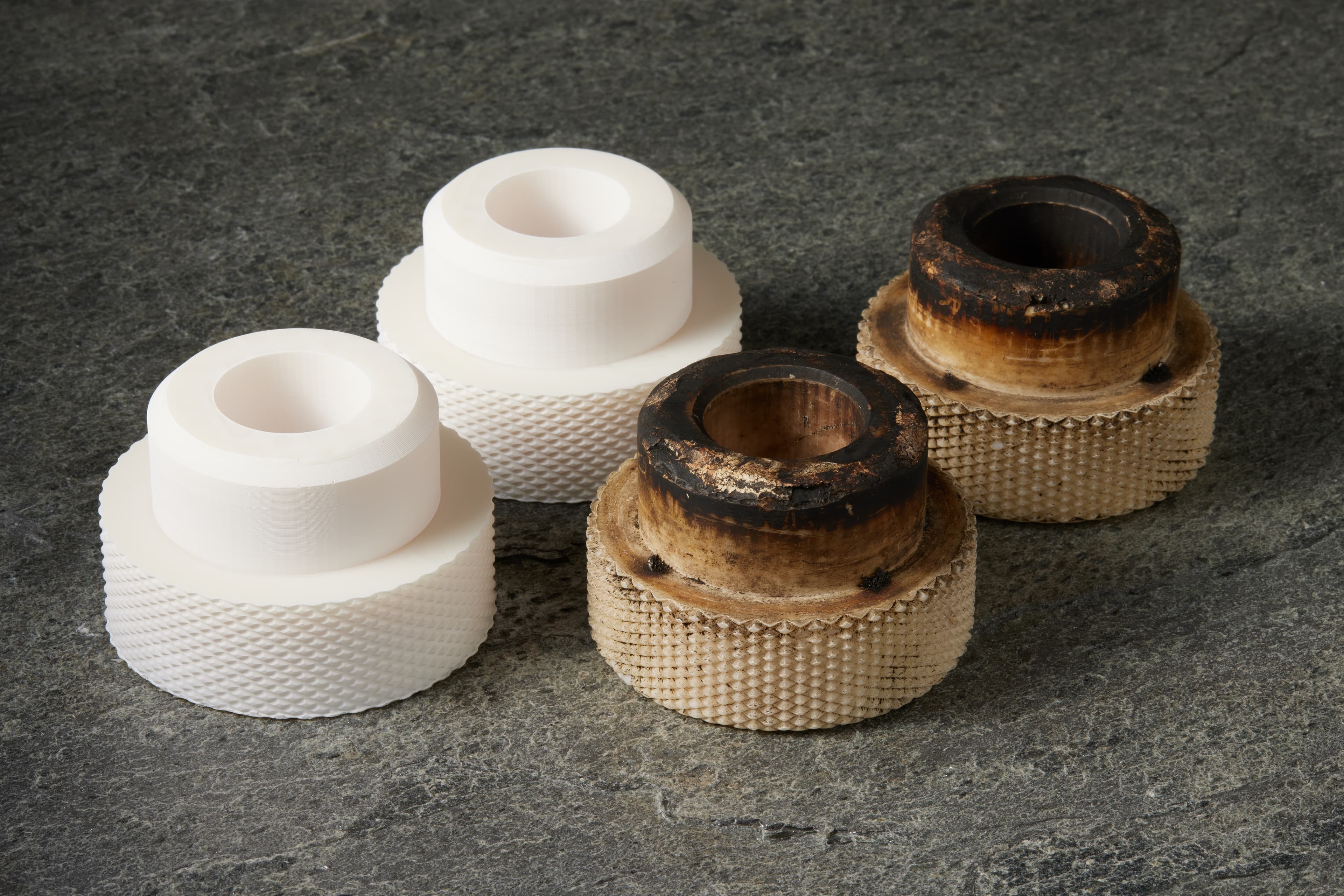
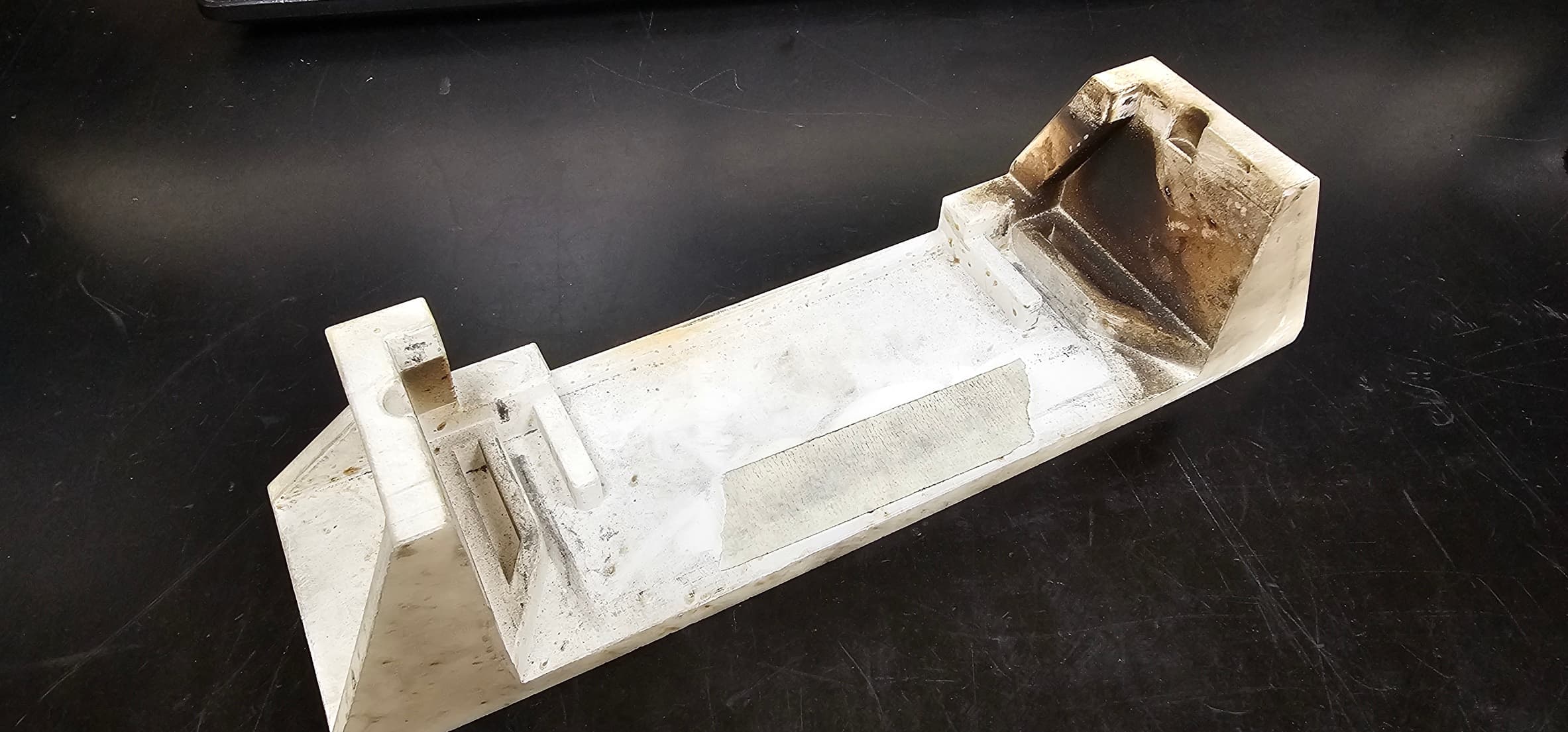
Protective plugs (left) are placed inside a steel half coupling with magnets to protect the internal thread while a pipe is being welded onto it. It prevents the weld and slag from going inside the half coupling and ruining the thread. After running about 3,000 welds on that jig, they are still in good shape. The scoop jig (right) positions a sheet metal bent plate in its correct orientation for the manual welder to assemble. This was a one-off job for about 600 welds, where precision was critical.
CNC Machine Shop 3D Prints Workholding for Turning With Nylon 12 Powder
The Factory Amsterdam (TFA) is a metal and plastic contract manufacturer based in New York State focusing on automation and lights-out manufacturing. They offer a range of services including CNC turning, additive manufacturing, laser marking, and finishing techniques for anodized aluminum, steel, stainless, and a variety of plastics. The team delivers orders from 10 to 10,000 units for a wide range of markets, from gas turbine parts to consumer electronics. With the Formlabs SLS printers, they not only operate as a 3D printing services provider but also support their metalworking activities with 3D printed tools, such as workholding for CNC machining, assembly fixtures, sheet metal forming dies, and machine replacement parts.
Collet pads for CNC turning: In turning operations, the team typically uses steel collets often featuring interchangeable pads to hold the part loaded in compression inside each of the two lathe spindles. However, turning is a demanding application. As they spin at high speed, up to a few thousand RPMs, the workholding experiences radial forces. Typically, these collet pads are hardened tool steel, but many applications require machinable workholding in order to accommodate more complex part features. These machinable pads are special-order items, available in soft steel, aluminum, or nylon, that can take up to three to four weeks to deliver. With Nylon 12 Powder on the Fuse Series, TFA can now 3D print them in one day for only $7.
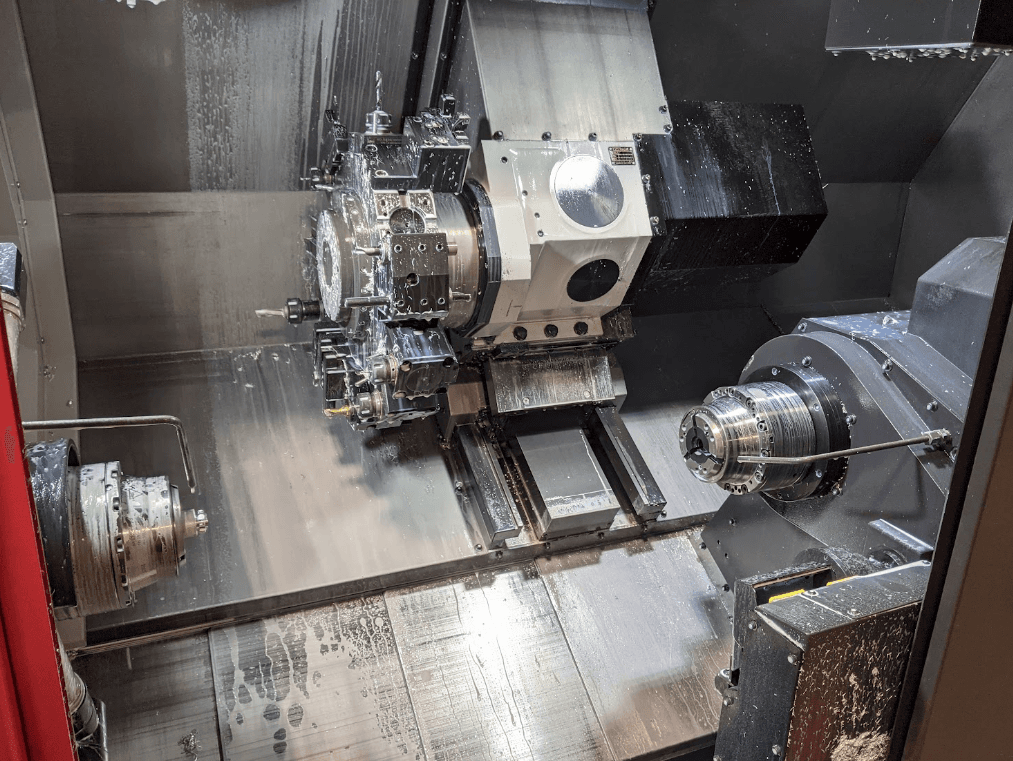
Dual spindle, Y-axis CNC turning center for complex turned parts with milled features. On the lathe spindle, the team often uses machined steel master collets with insertable pads. The hydraulic system can clamp the chuck with up to 6,000 pounds of pressure.
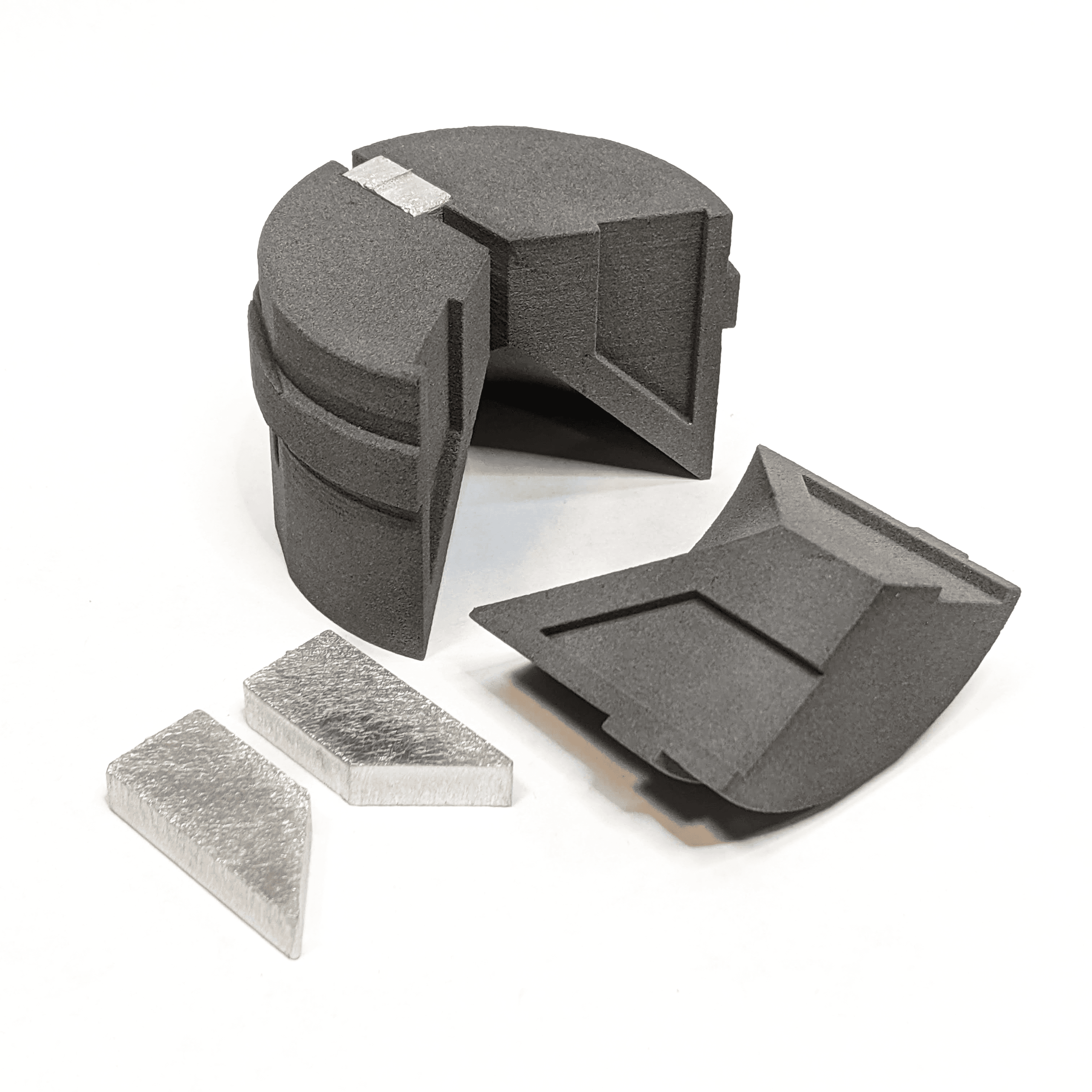
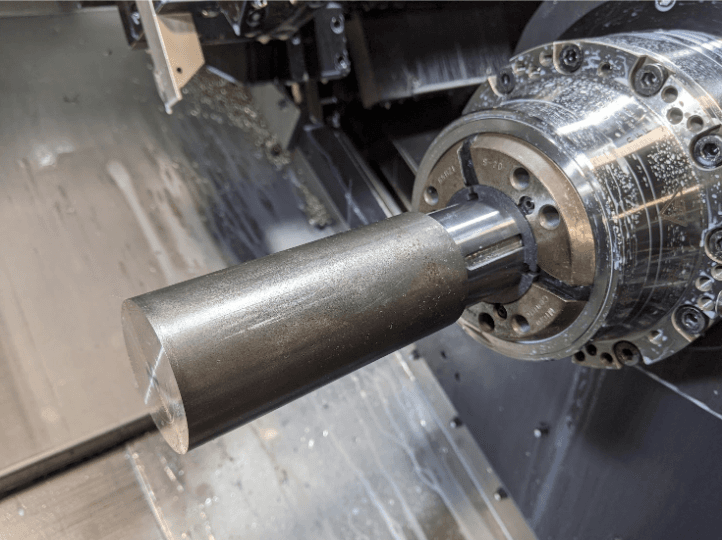
Each pad (left) also has small aluminum inserts to preload the assembly for machining to size. The picture on the right shows a large carbon steel part (50 mm diameter) clamped in 3D printed collet pads.
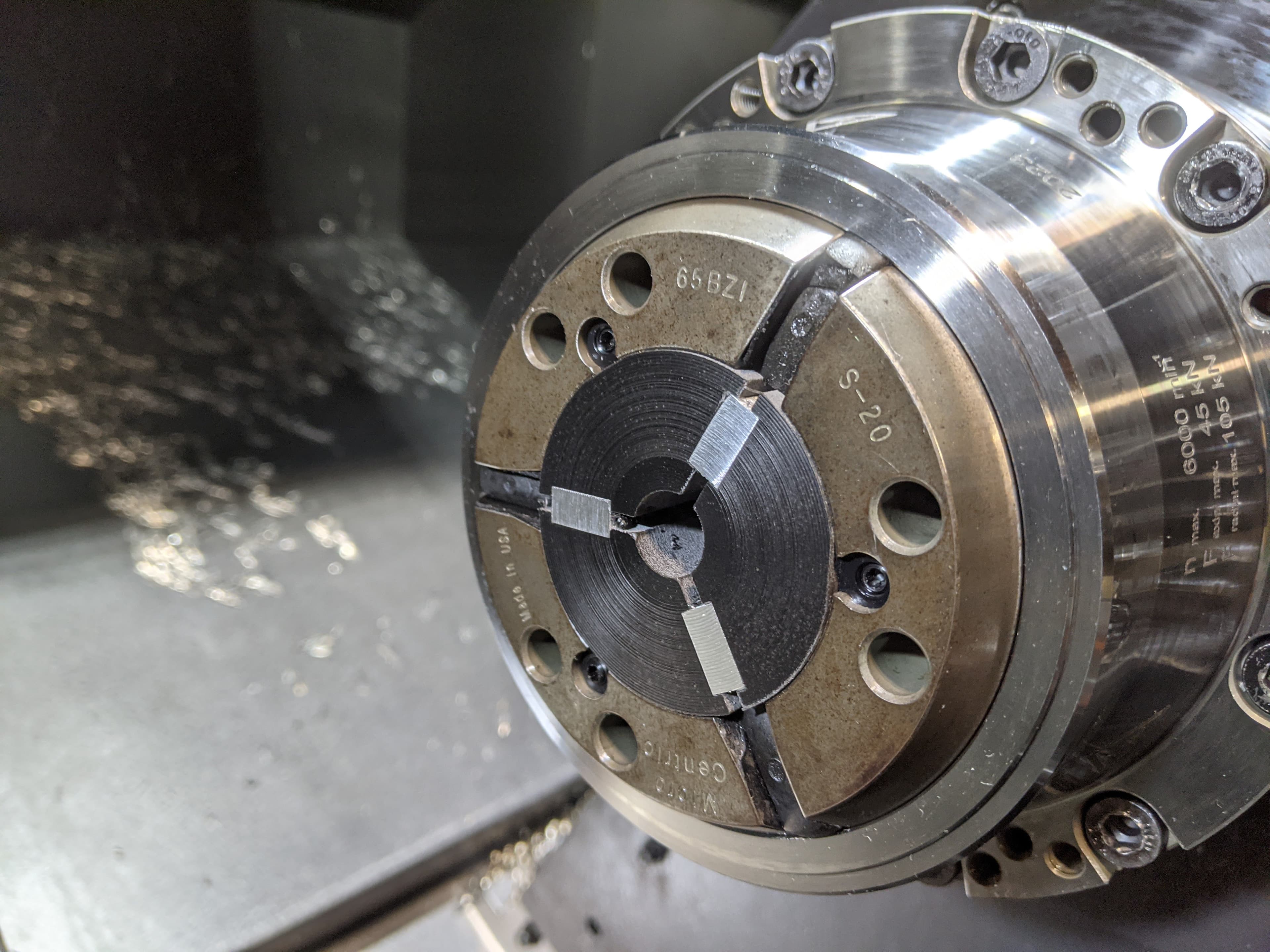
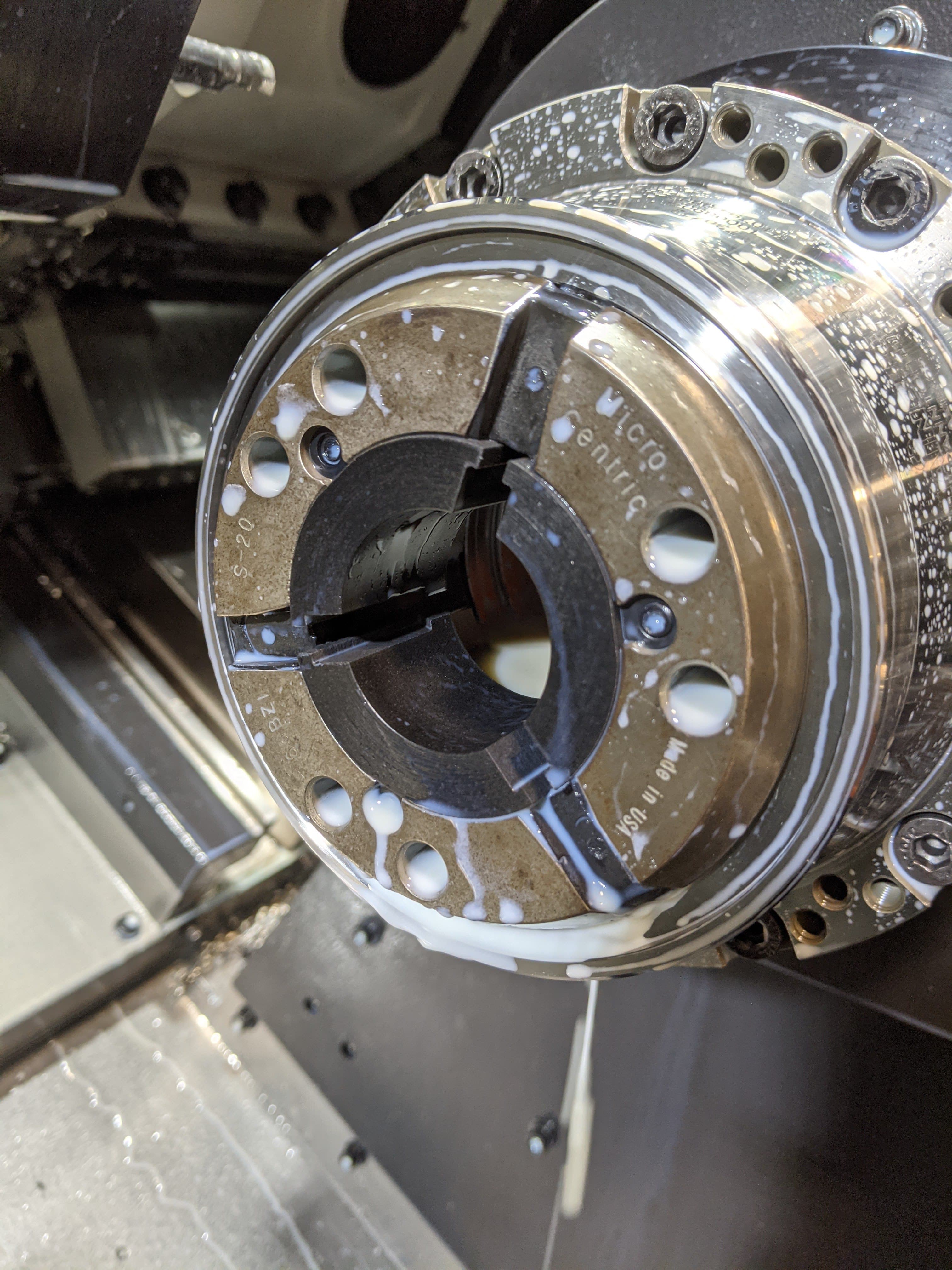
Before (left) and after (right) machining to size, the stepped bore positively controls the part location. Machining a step into the collet can improve clamping repeatability for thin-walled or narrow parts. The printed tools are continuously in contact with the coolant inside the lathe. It is a semisynthetic, water-soluble oil that is aggressive on a lot of plastics and dissolves many FDM materials. Nylon 12 Powder is chemically resistant and does not wear from it.
Nylon 12 Powder allows for high accuracy and precision, which is critical for this application. The 3D printed collet pads are inserted inside a steel master collet with a high-precision interface. “There's a little dovetail interface that needs to snap into those master collets, and that's something that is very hard to produce accurately with other 3D printing processes. So that's where the Fuse printers really shine” says Bradley Matheus. One set of printed pads can run 3,000 parts or more, which is more than 100 hours of continuous production. Additionally, they help preserve fine surface finishes on delicate parts where steel collets may mark finished surfaces.
CNC turning fixture cost analysis:
|
“It's probably not the same lifespan as a steel or aluminum set, but with the cost difference, it more than makes up for it. I have to be a lot more careful about using a set of metal pads because they do cost a lot. Most of the work that I'm doing is a very quick turnaround, so I don't even have to think about it. If it's something weird that my existing tooling can't grab onto, I just throw some of these in and it's done. They really are problem solvers. Of course, they aren’t a perfect solution for every single manufacturing challenge I encounter, but they’ve proven to be capable in a variety of demanding applications.” says Bradley Matheus.
Magnet assembly tools: TFA is also using Fuse Series SLS parts to support secondary processes. After machining, the part is post-processed and two magnets are installed in it. A typical order requires the assembly of 6,000 magnets of N52 grade, which are quite powerful and can be difficult to manipulate by hand. “It is just miserable for the operator without some kind of tool. But we have not been able to find any off-the-shelf solutions for this. The Fuse Series allows us to produce much more robust assembly tooling than we would otherwise be able to and in a cost-effective manner. It allows us to iterate faster and produce very highly accurate parts without a lot of effort,” says Bradley Matheus.
“When it comes to assembly processes, everything is bespoke, it's just not something you can often buy off the shelf. So having a highly flexible manufacturing option in-house is invaluable.”
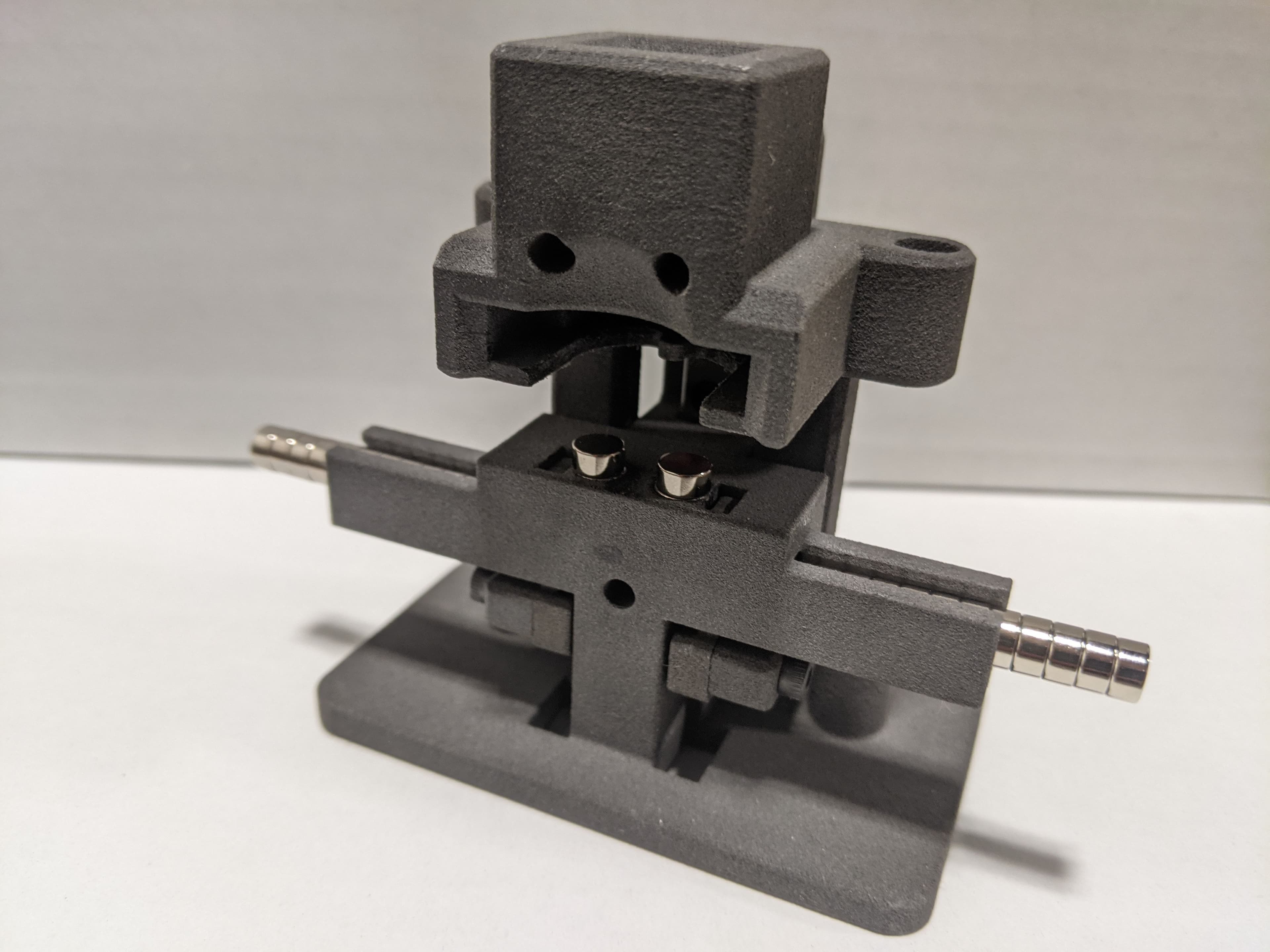
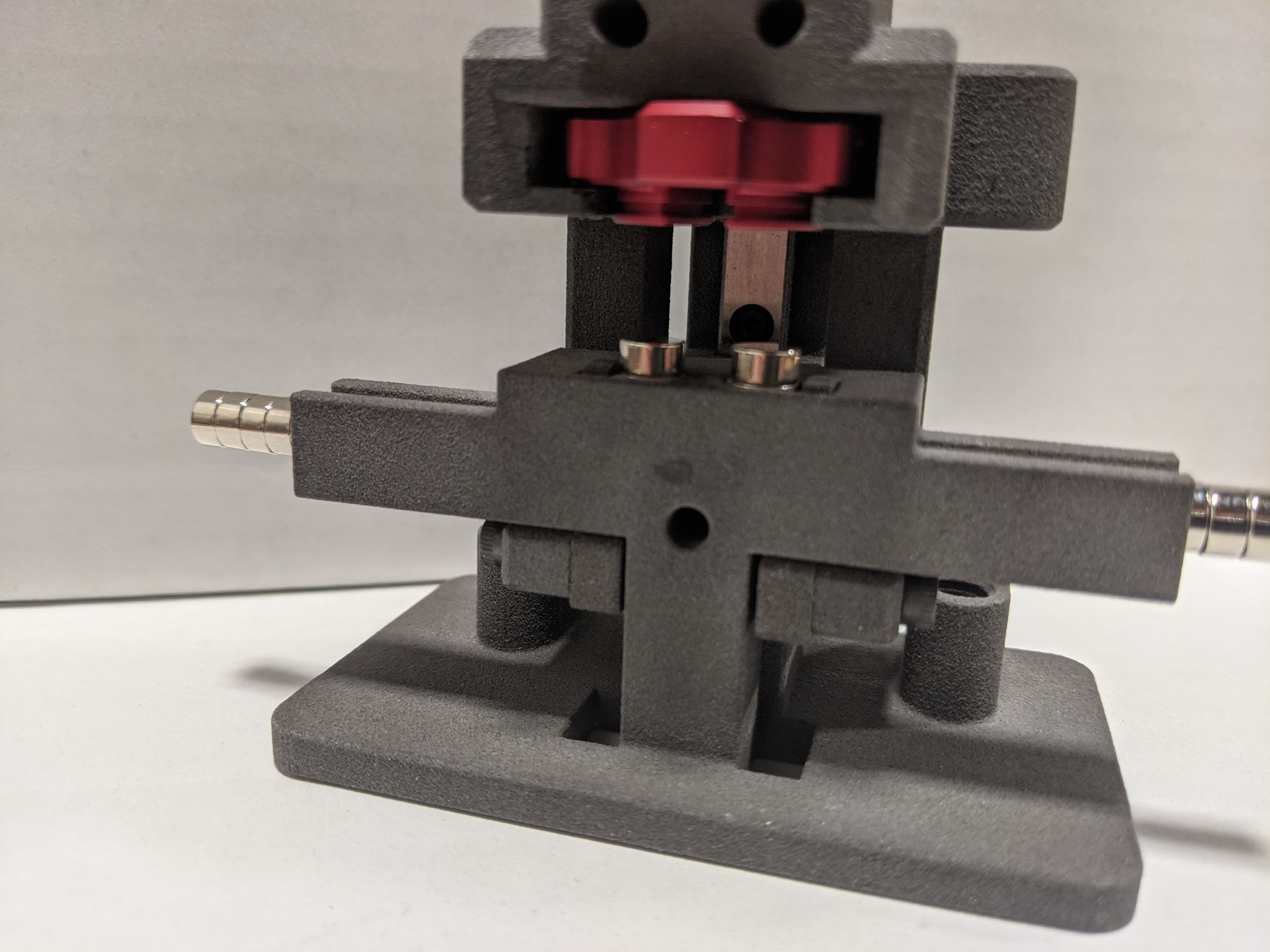
Magnet press jig: The team initially printed an assembly tool with FDM 3D printing but the material fatigued over time; it cracked and picked up contaminants in the layer lines that then contaminated the magnets.
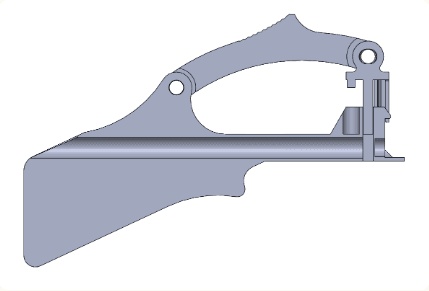
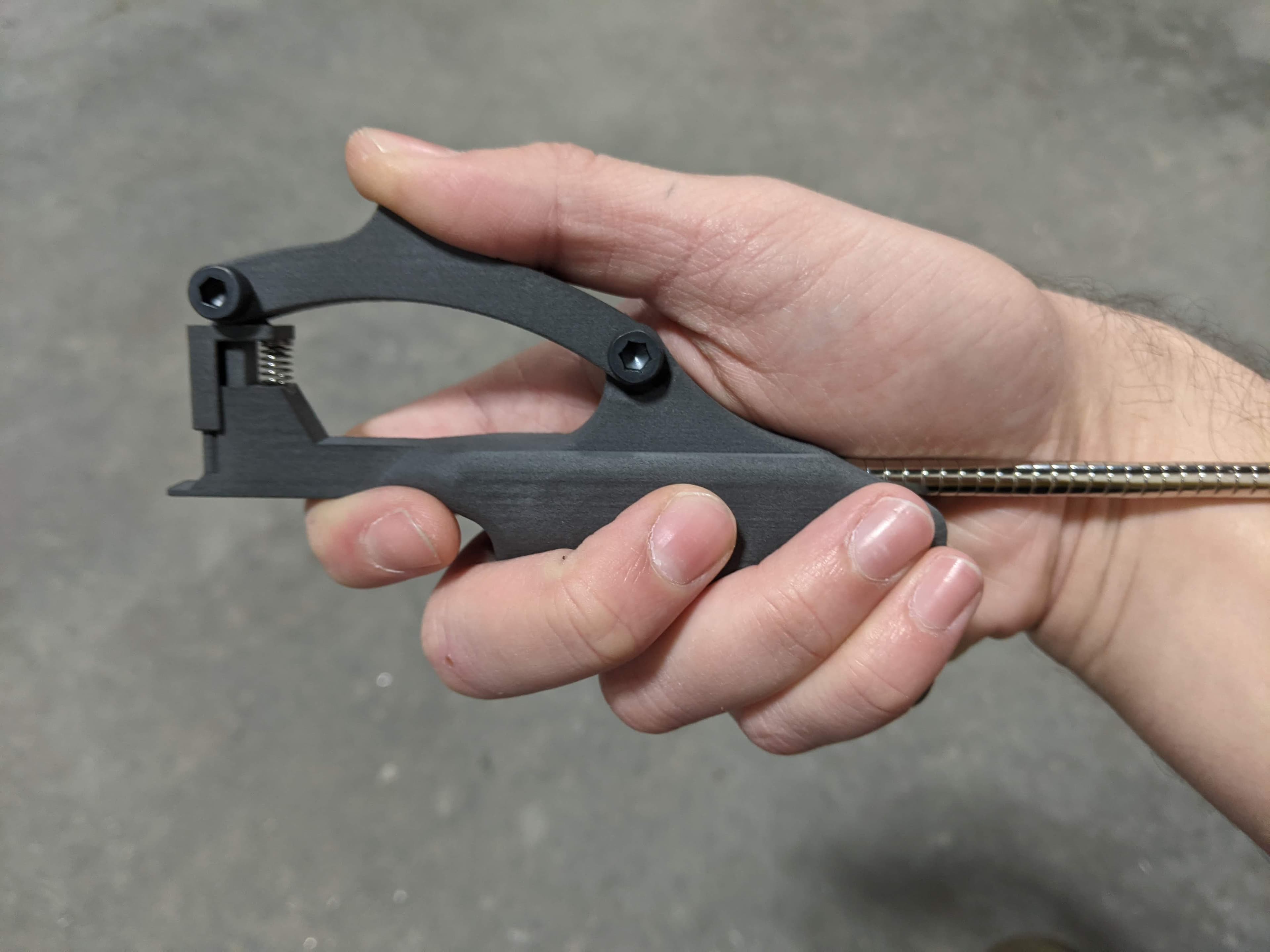
Ergonomic hardware dispenser: With the Fuse Series, critical features can be incorporated such as a 0.5 mm thickness wall to position the magnet accurately or hand-fitting curves to mitigate the operator fatigue over the course of a few thousand parts.
Global Pyrotechnics Supplier 3D Prints Ultrasonic Welding Fixtures and Robot Grippers With Nylon 12 Powder
The Etienne Lacroix Group is a global player in the pyrotechnics sector, offering comprehensive solutions for defense, security, logistics, industry, and events. Within the group, the MPM Company specializes in injection molding complex thermoplastic parts for small and medium production (up to 10,000 units). Their facilities are set up with 23 injection molding machines as well as CNC machining, welding, marking, coating, and assembly stations, to deliver sub-assemblies products to their customers.
The MPM team is also equipped with various additive technologies. They use FDM printing for proof-ofconcepts and Formlabs SLA printers for functional prototypes and short-run injection molds. Two years ago, they acquired the Fuse Series with Nylon 12 Powder for printing fixturing, machine replacement parts, and low volumes of end-use parts. Today, they 3D print about 60 parts per week for internal use with the Fuse Series, from plastic machining fixtures to welding fixtures and robotic end-of-arm tooling. Including orders for prototypes from customers, they’ve printed about 4,000 parts on the Fuse Series so far. Here are some notable examples of internal tools:
Ultrasonic welding fixtures: These tools are placed inside an ultrasonic welding machine to hold brass inserts onto an injection molded part during welding. Despite heat, pressure, and vibration exposure, the printed fixtures are still functional after running more than 3,000 welds. The tools have intricate geometries with thin ribs and alignment features that are challenging to machine, the team would need to outsource the job to a 5-axis CNC machining service. By 3D printing them, they reduced time and cost by more than 90% while gaining precision and design complexity. In addition, tools printed in Nylon 12 Powder are softer than metal fixtures and protect the welded part from being scratched.
Ultrasonic welding fixtures cost analysis:
Alternative Method |
3D Printing In-House |
|
Equipment |
Metal CNC machined (5-axis) outsourced |
Fuse Series, Nylon 12 Powder |
Cost |
€150 |
€10 |
Time |
2-3 weeks |
1 day |
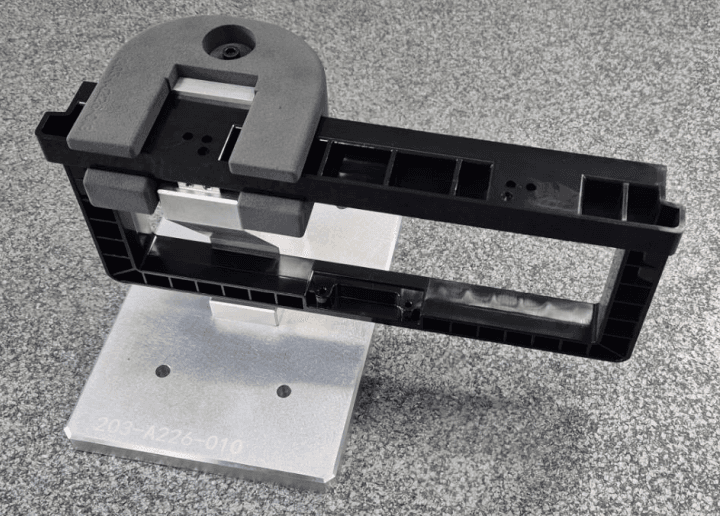
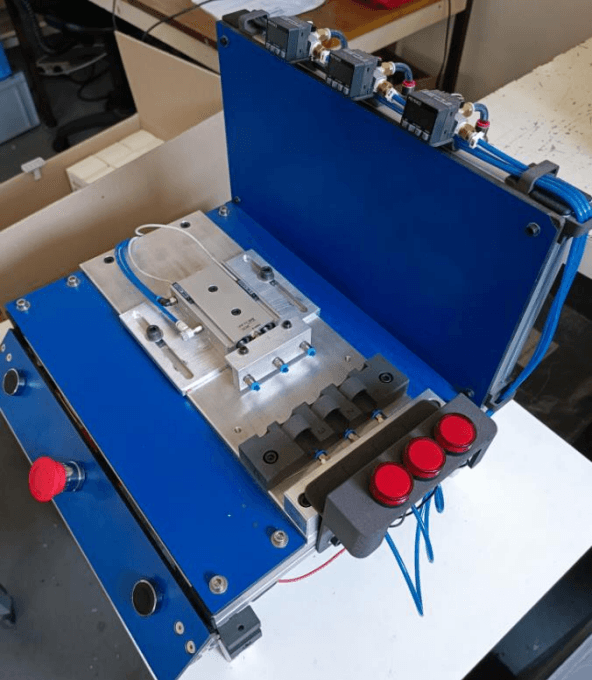
The ultrasonic welding fixture (left) is the U-shaped part placed on a metal stool to absorb some of the forces in action. On this specific model, they typically weld three parts per minute, with two welds per part. The final parts then go through tightness inspection tests with a custom machine made of 3D printed components (right). This machine is typically used three to four times a year for a series of 3,000 units each.
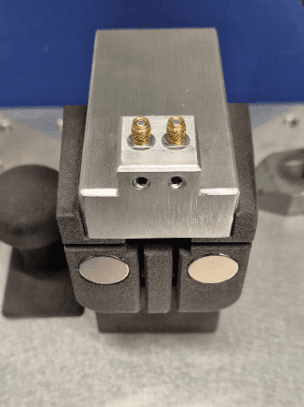
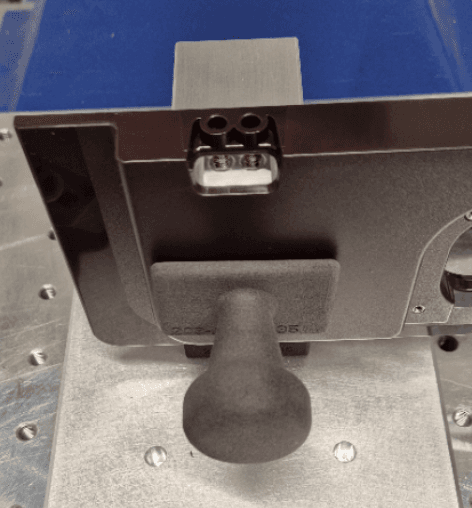
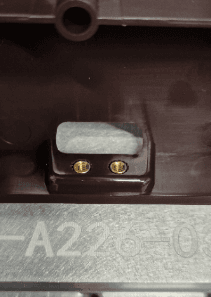
In this other example, the ultrasonic welding fixture is coupled with an aluminum part. The brass inserts are positioned onto the fixture (left), and the plastic part is installed and maintained with a 3D magnetic shim for the sonotrode to apply forces on it (middle), and weld the inserts (right).
Replacement parts for robot end-of-arm tooling (EOAT): The team 3D prints custom EOAT with the Fuse Series to replace the original worn ones and see various benefits:
- Replace the worn grippers faster and cheaper than the original method
- Reduce their weight, often by a factor of three, and extend the robot’s lifetime
- Reduce risks of scratching the metal parts as Nylon 12 Powder grippers are flexible
- Customize the grippers to the geometry of the part
One specific robot EOAT is used monthly to deliver a production series of 5,000 units of overmolded parts. The robot is made of 32 grippers picking up hot metallic inserts (at 80 °C or 176 °F) to place them inside the injection mold. The grippers used to be in plastic outsourced from the original supplier. They wore out quickly and needed to be replaced after two series, which is about 10,000 units. Each of them costs €55, €1760 per robot, with three weeks of lead time.
With the Fuse Series, the team can print them in a day for €1 each. The Nylon 12 Powder grippers are lighter than the original ones and resist much better to the high temperature of the inserts. After a year of use and about 60,000 parts, they are still functional. The team saves more than €10,500 per year with only this part.
Robot EOAT cost analysis:
Alternative Method |
3D Printing In-House |
|
Equipment |
Outsourced plastic grippers |
Fuse Series, Nylon 12 Powder |
Cost per year |
€10,560 |
€32 |
Time |
3 weeks |
1 day |
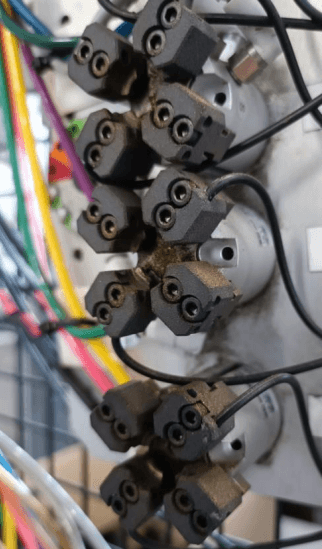
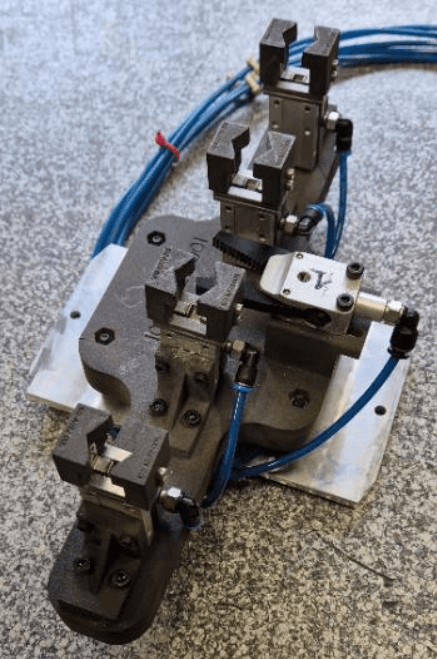
Custom, lightweight end-of-arm tooling (EOAT) to pick up heated metallic inserts. A robot with 32 jaws (left) that controls the parts by optical fiber, and a robot with four jaws and the board (right) all include components 3D printed with the Fuse Series.
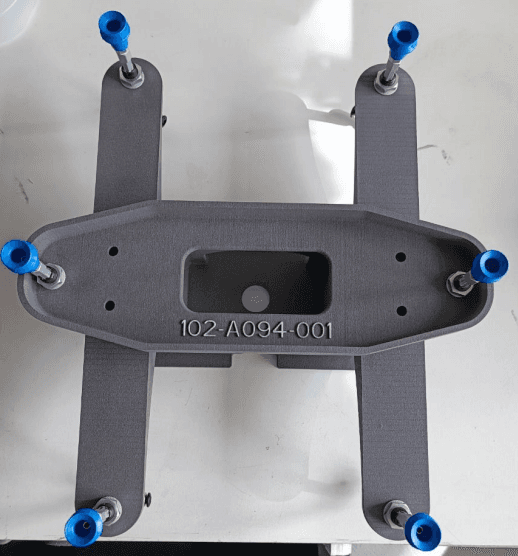
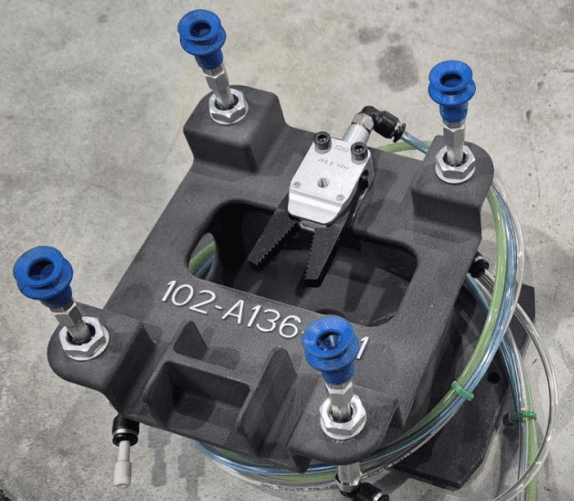
Other robotic boards 3D printed on the Fuse Series with screwed suction cups. The team usually machines the parts after printing to ensure the right dimensions.
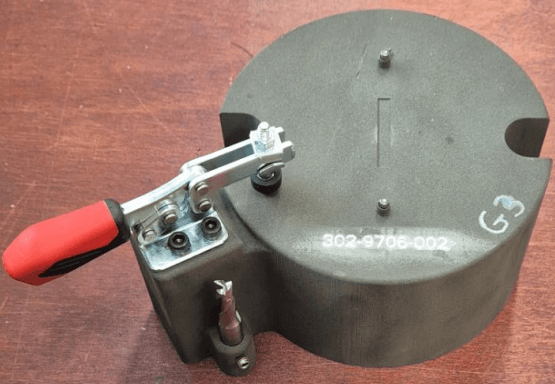
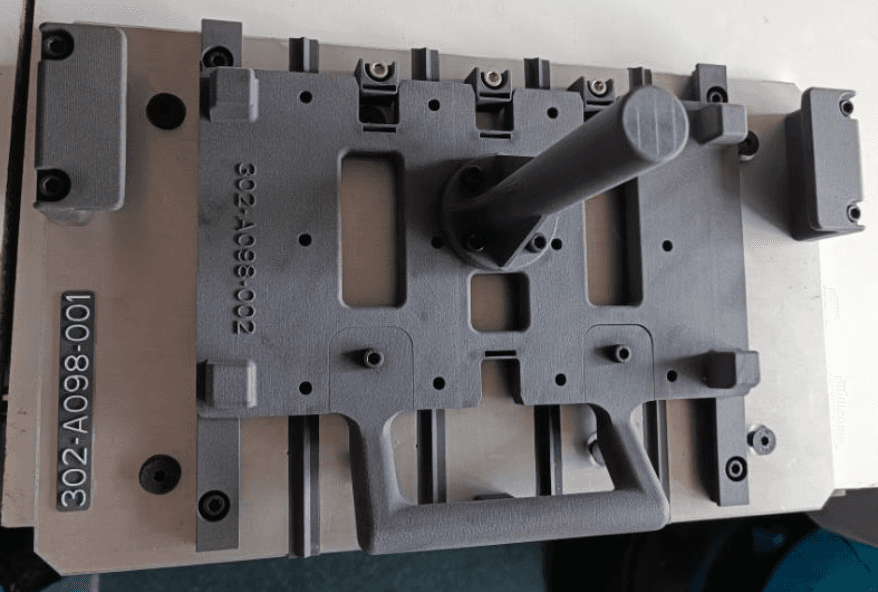
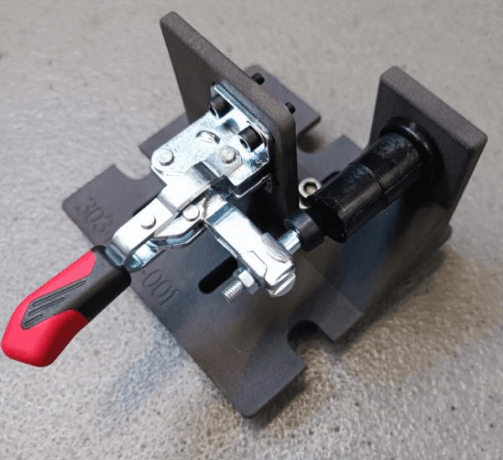
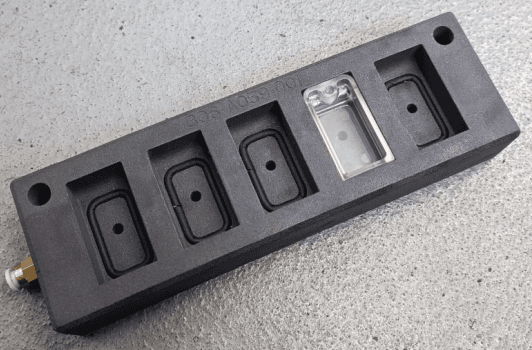
Machining jigs and fixtures. With the Fuse Series, the team 3D prints workholding devices to machine parts right after injection molding. The parts are often still hot from the process and in contact with the 3D printed tool for about 10 seconds. Cylindrical fixture for cutting a PC part at 100 °C (top left), machining tool for the injection molding sprue (top right), drilling tool (bottom left), and tapping tool for the injected part (bottom right).

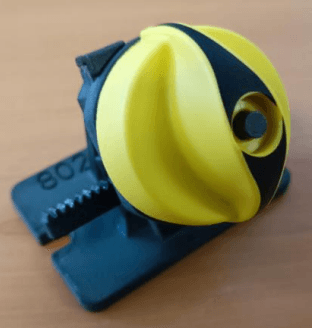
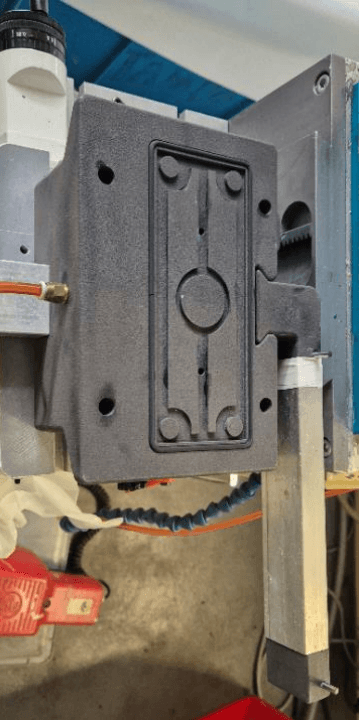
Tampography tools. The team also leverages the chemical resistance of Nylon 12 Powder to 3D print tooling for tampography. The printed parts are exposed to the standard tampography solvents without deterioration.
Global Automotive Supplier 3D Prints Welding Setup Fixtures With Fast Model Resin
Brose is one of the five largest family-owned automotive suppliers in the world. At every stage in the automotive supply chain, metal parts are key components of the overall product. Welding is, understandably, a huge part of the assembly process. At Brose North America, where Brose’s Additive Technology team operates the fleet of SLA and SLS printers, their welding robots need to switch between different product lines constantly. Programming a welding robot using prototype metal rails is expensive, and they are very often not available at the time the weld station is ready to teach the equipment. 3D printing offers a fast and inexpensive solution, as speed and dimensional accuracy are needed for those setup parts. The team 3D prints large welding setup parts using Fast Model Resin on the Form 4L printer. Read the full case study for more information.
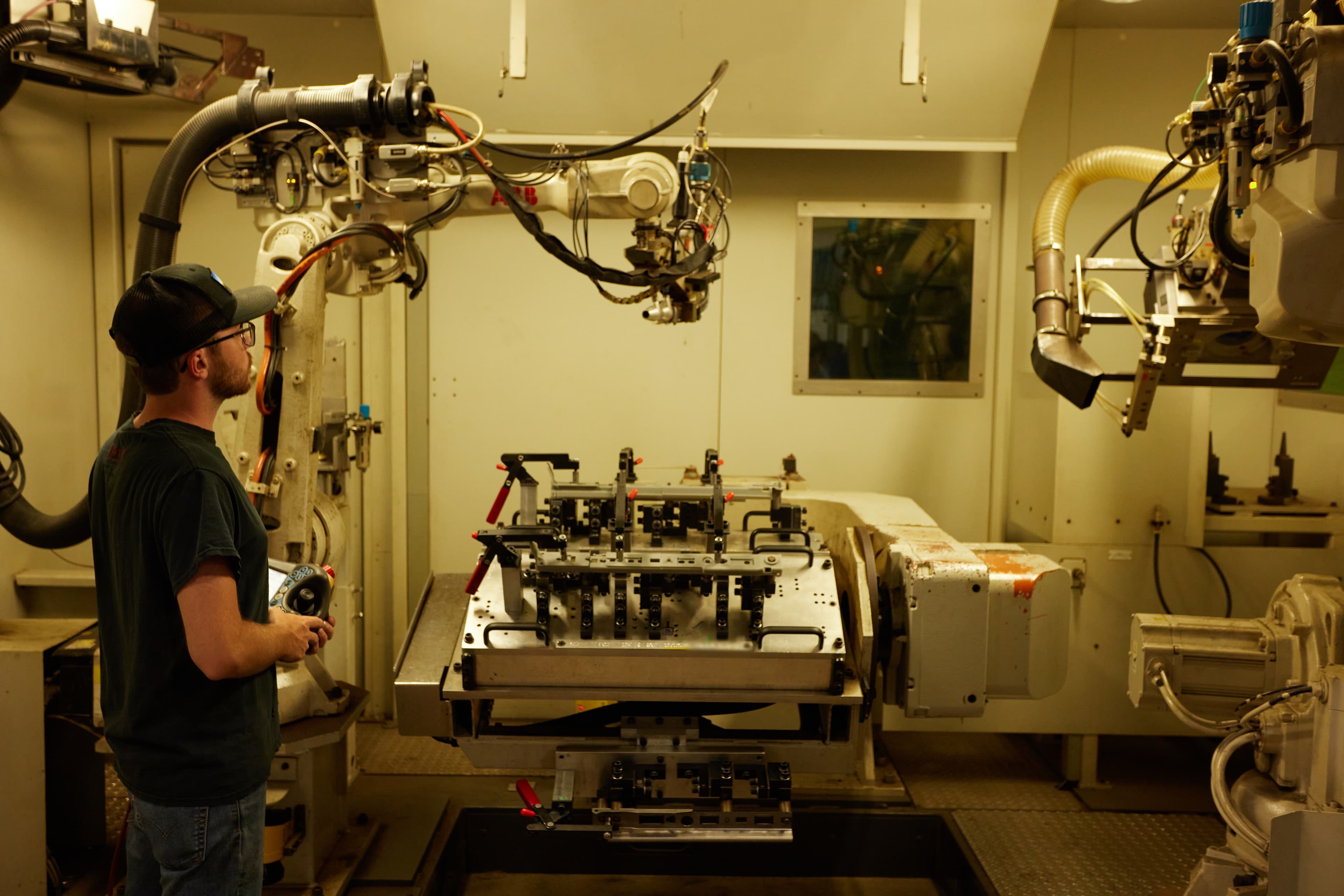
This seat part was printed on Form 4L in Fast Model Resin, washed, cured, and assembled onto the robotic welding machine in under three hours. This allows the team to teach the robot movements quickly.
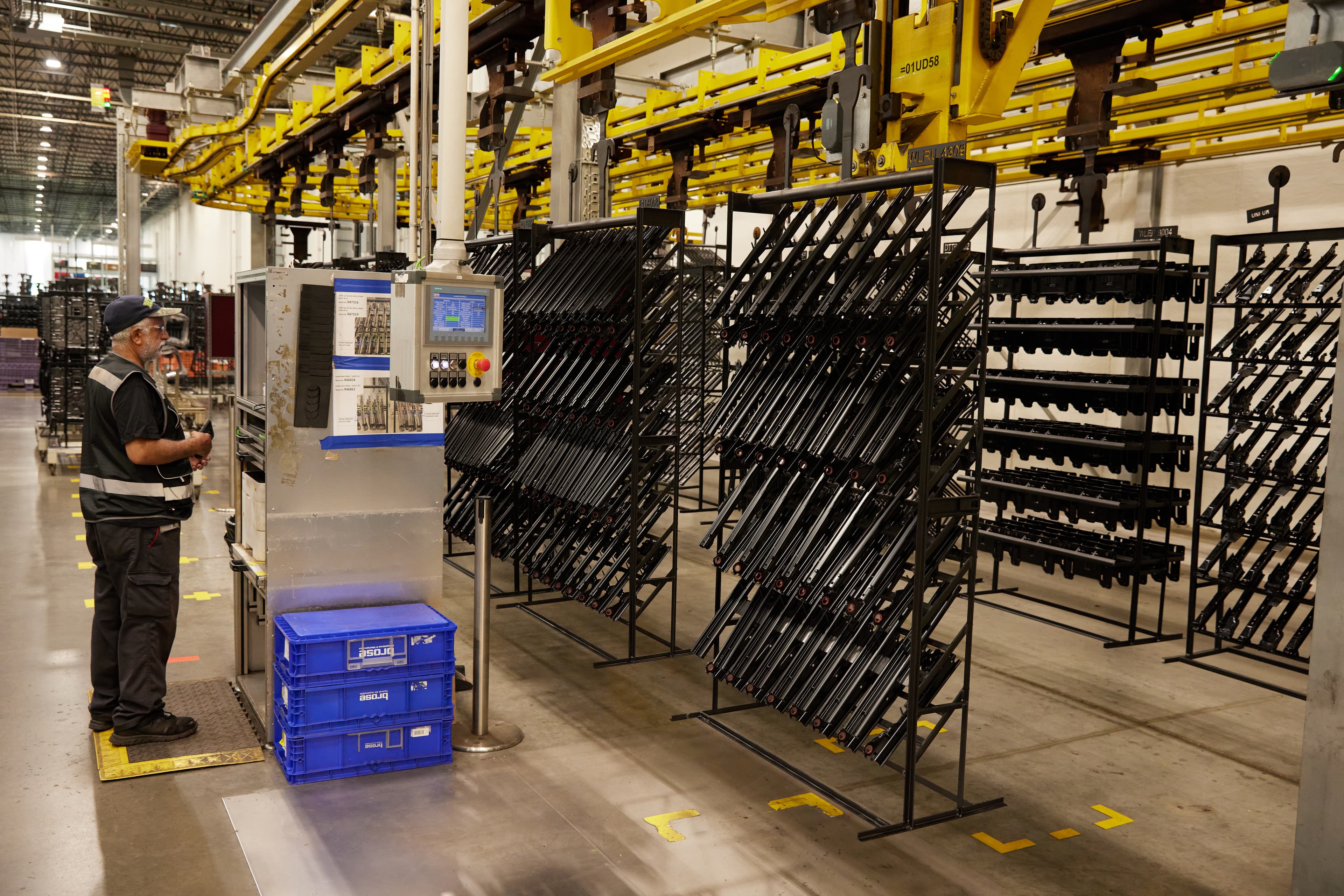
At Brose New Boston, thousands of seat rails, shown above, are welded together to form the base of the seat assembly. Testing welding parameters is integral to the manufacturing process.
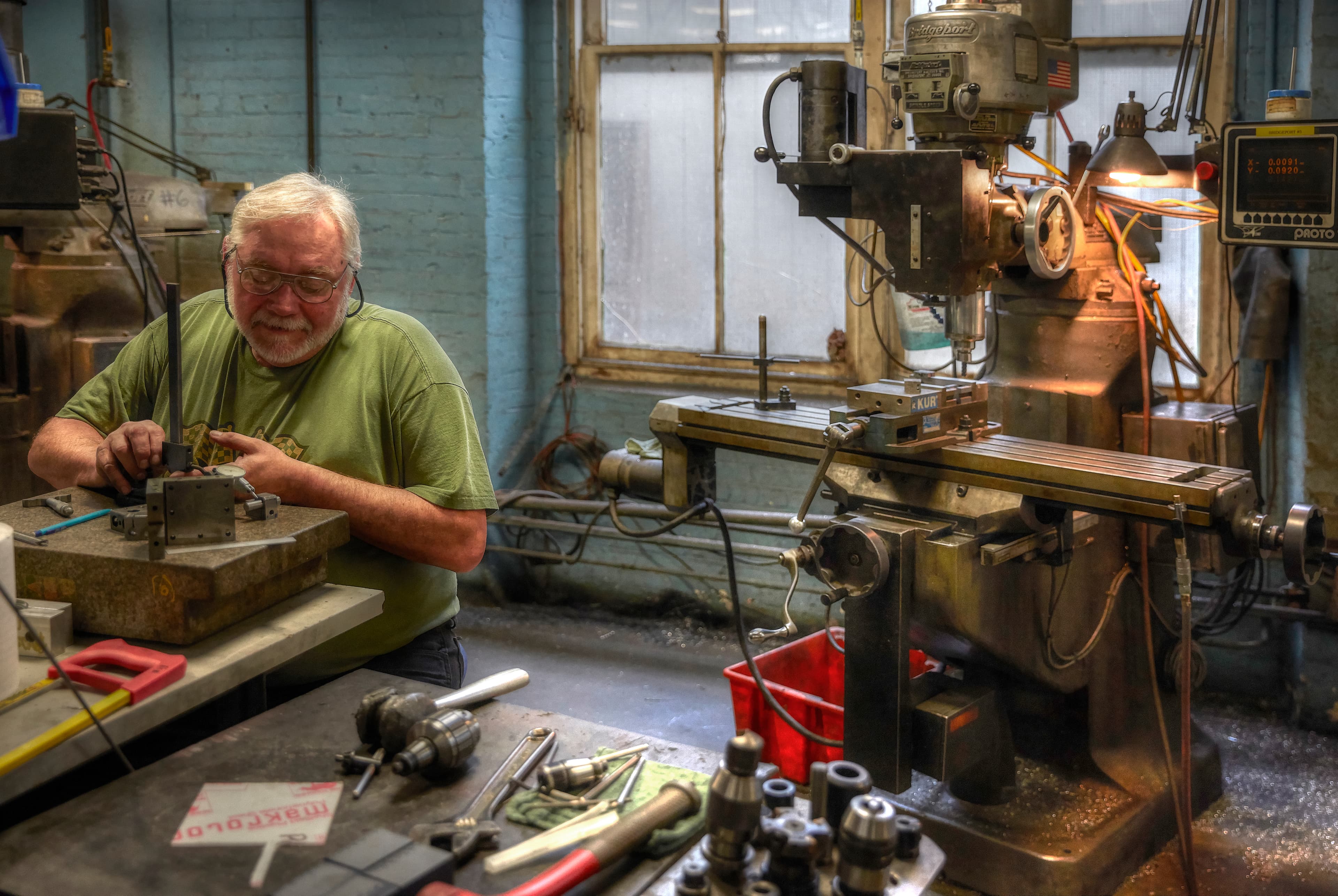
A&M Tool and Design’s machine shop includes a vast range of technologies, from Bridgeport CNC machines to large-scale manufacturing automation equipment to Formlabs SLA 3D printer.
Conclusion
3D printing jigs and fixtures provides a practical solution to the challenges of traditional tooling in metalworking. It enables faster fabrication, reduced costs, and greater design flexibility. This is particularly beneficial for custom tools in processes like machining and welding, where precision and durability are critical. Unlike traditional methods, 3D printing allows on-demand manufacturing and minimizes physical inventory through digital storage.
This white paper showcases the feasibility of using Formlabs' SLA and SLS printers for producing highquality metalworking jigs and fixtures. Case studies highlighted significant results: over 90% reduction in costs and lead times for CNC machining fixtures and welding jigs using chemical-resistant and heatresistant materials, and $10,000 in savings per year with robotic grippers. These examples demonstrate the ability of Formlabs’ technology to meet the rigorous demands of industrial environments.
For companies ready to integrate 3D printing for tooling, this white paper serves as a practical guide to getting started, from selecting the right materials and printers to optimizing design and developing a digital inventory strategy for maximum flexibility and efficiency.
Request a free sample part to see Formlabs 3D printed materials firsthand and contact our 3D printing specialists to find the right solution for your application.
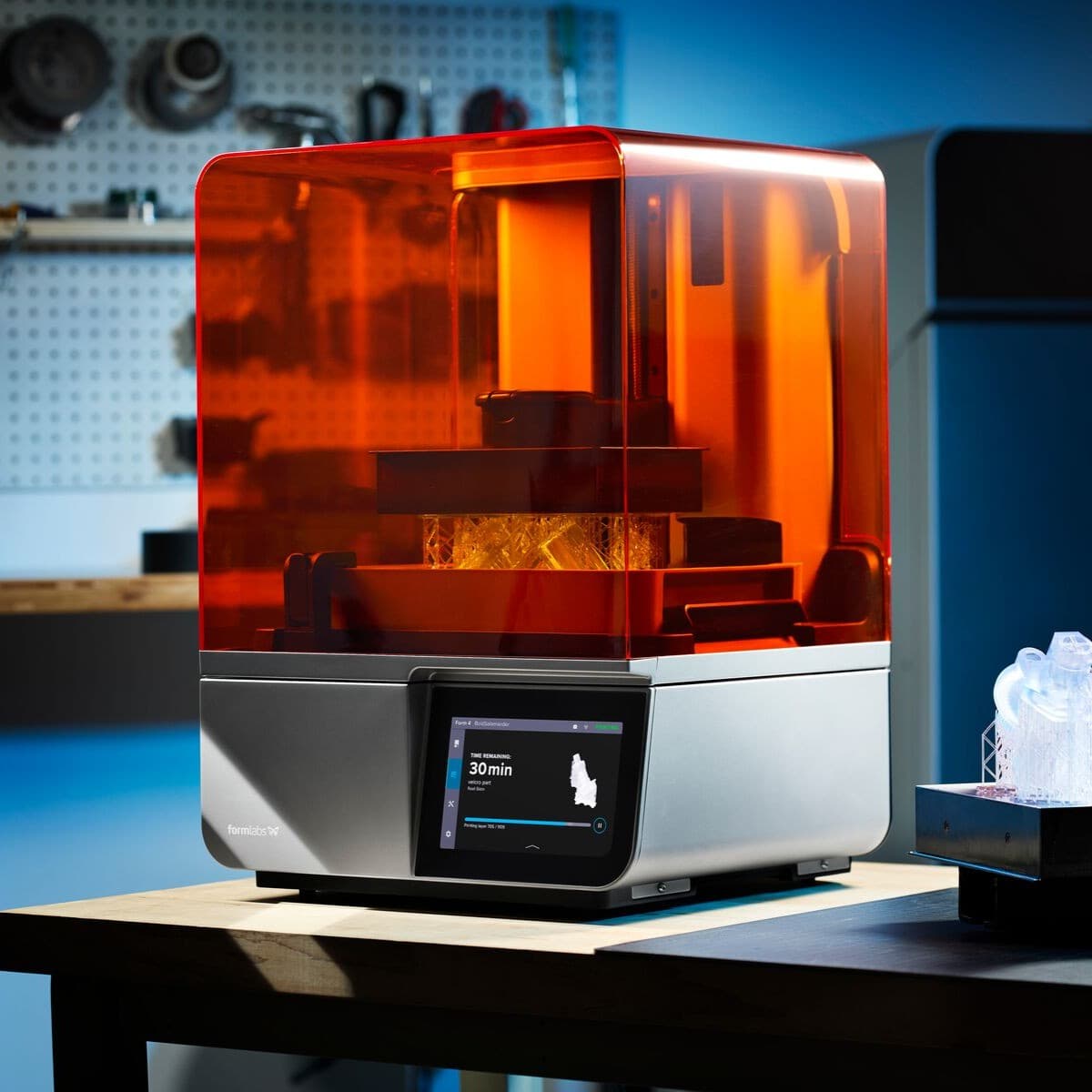
Book a Consultation
Get in touch with our 3D printing experts for a 1:1 consultation to find the right solution for your business, receive ROI analyses, test prints, and more.
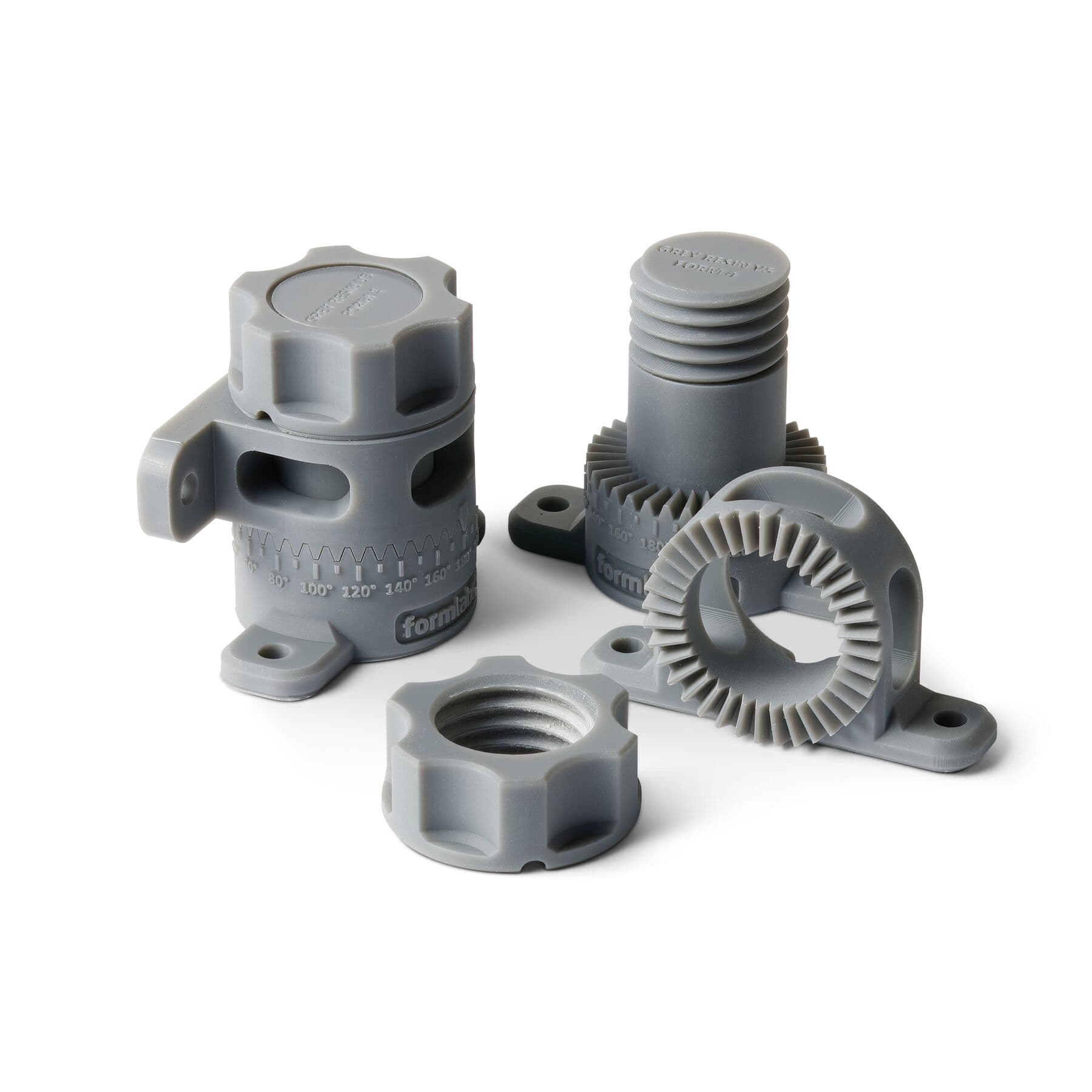
Request a Free Sample Part
See and feel Formlabs quality firsthand. We’ll ship a free 3D printed sample part to your office.
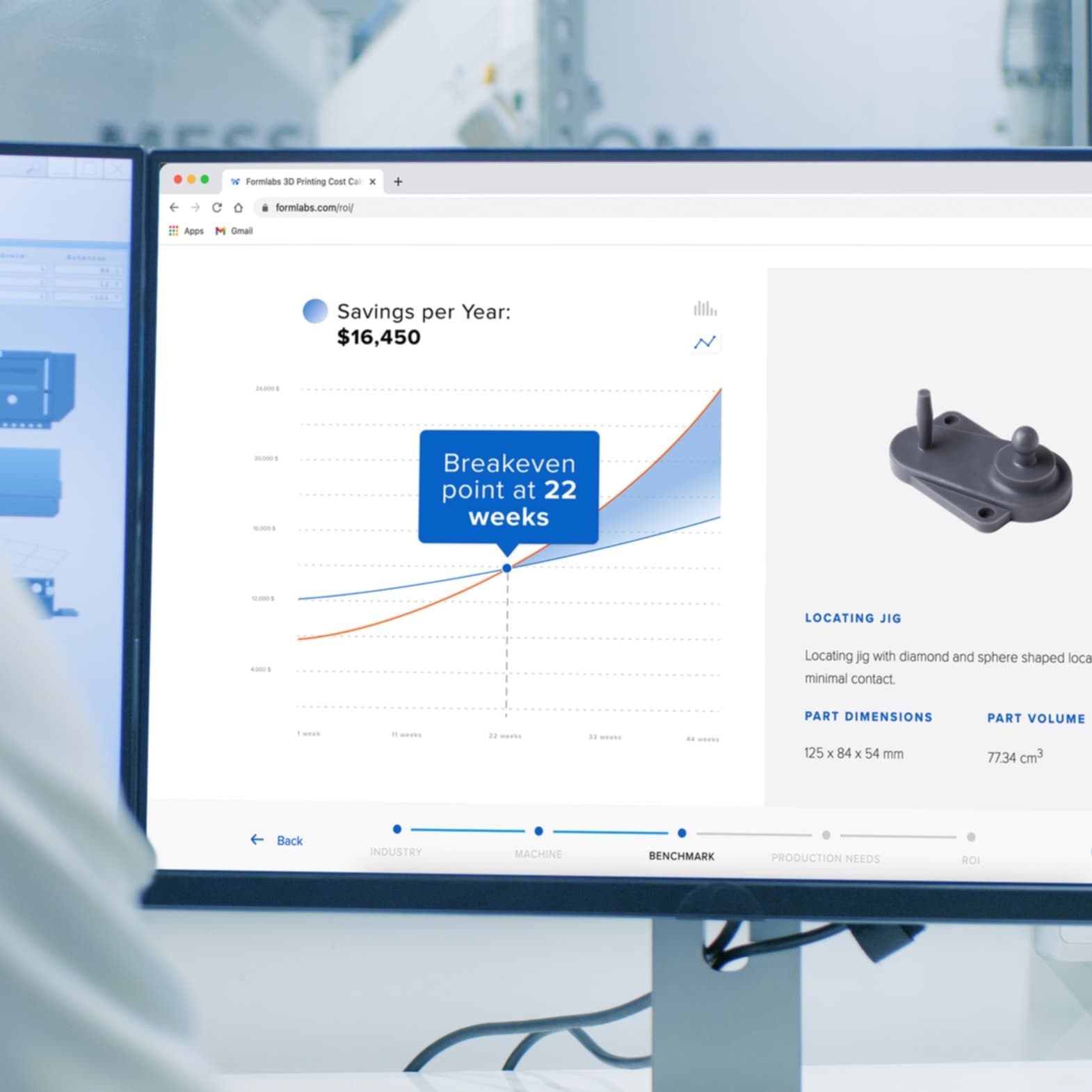
Calculate Your Time and Cost Savings
Try our interactive ROI tool to see how much time and cost you can save when 3D printing on Formlabs 3D printers.