Additive Synthesis: KORG Berlin Makes Innovative Sound Generation a Reality With 3D Printing
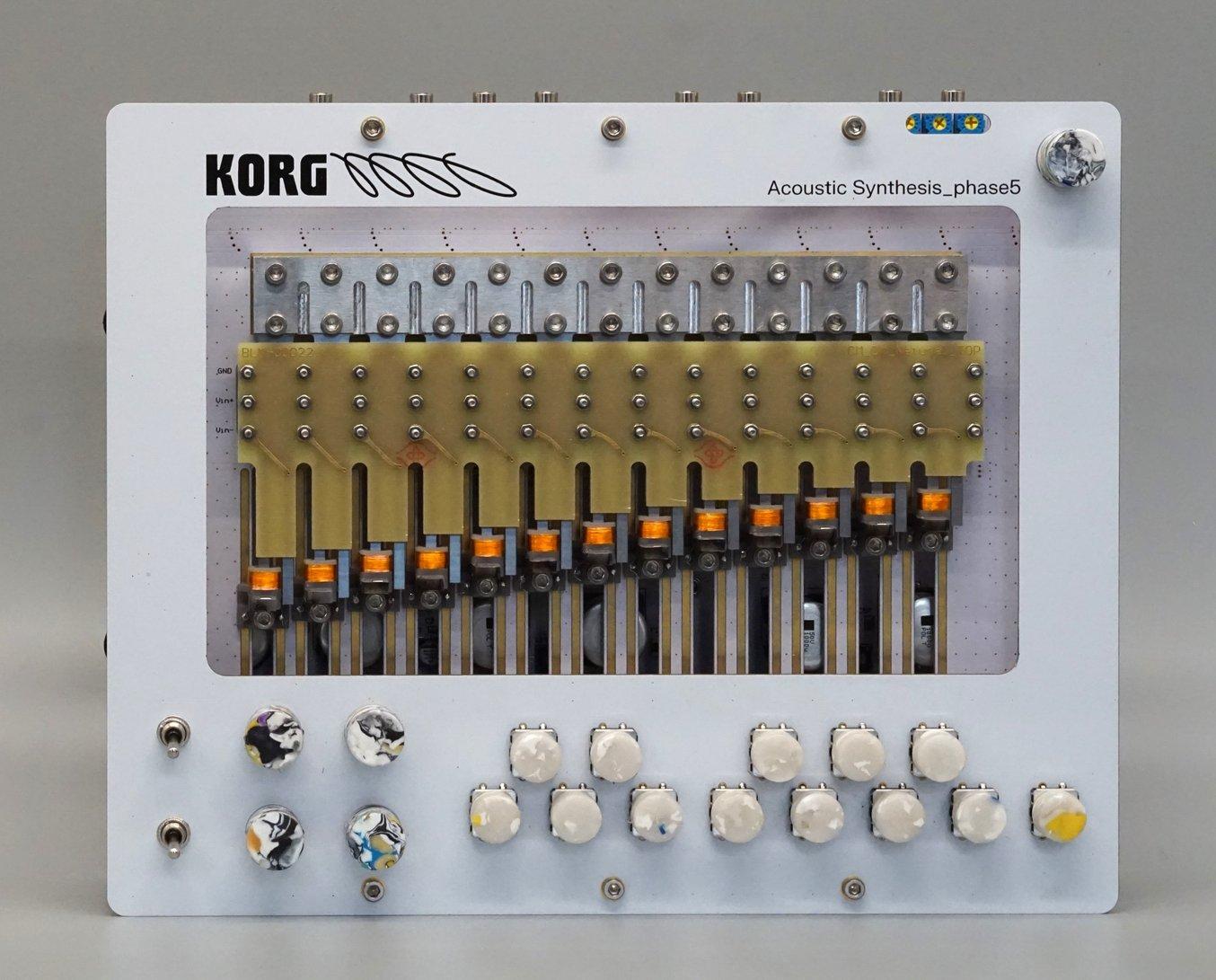
Digital advancements have revolutionized music production — even a laptop can turn a bedroom into a recording studio. But the team at KORG Berlin believes that the physical sensitivity and unpredictability of real instruments invite musicians to experiment intuitively, offering advantages that cannot be replaced by software.
KORG Berlin is an independently operating subsidiary of the world-renowned instrument manufacturer KORG INC. Together with CEO Tatsuya Takahashi, the pioneer behind iconic synthesizers such as Minilogue, Monotron, and Volca, ten employees are working to revitalize the synthesizer industry, which is threatened by software-generated instrumentation.
The challenge for KORG Berlin is to explore new, innovative ideas with just a small team. They not only developed a new synthesizer, but also a completely new form of synthesis, which they presented with their prototype Acoustic Synth Phase5 at the Superbooth 2023 trade fair.
We spoke to Hardware Developer Lukas Hartmann and Sustainability & Communications Designer Samantha Melnyk about the importance of rapid prototyping for the exploration of innovative ideas.
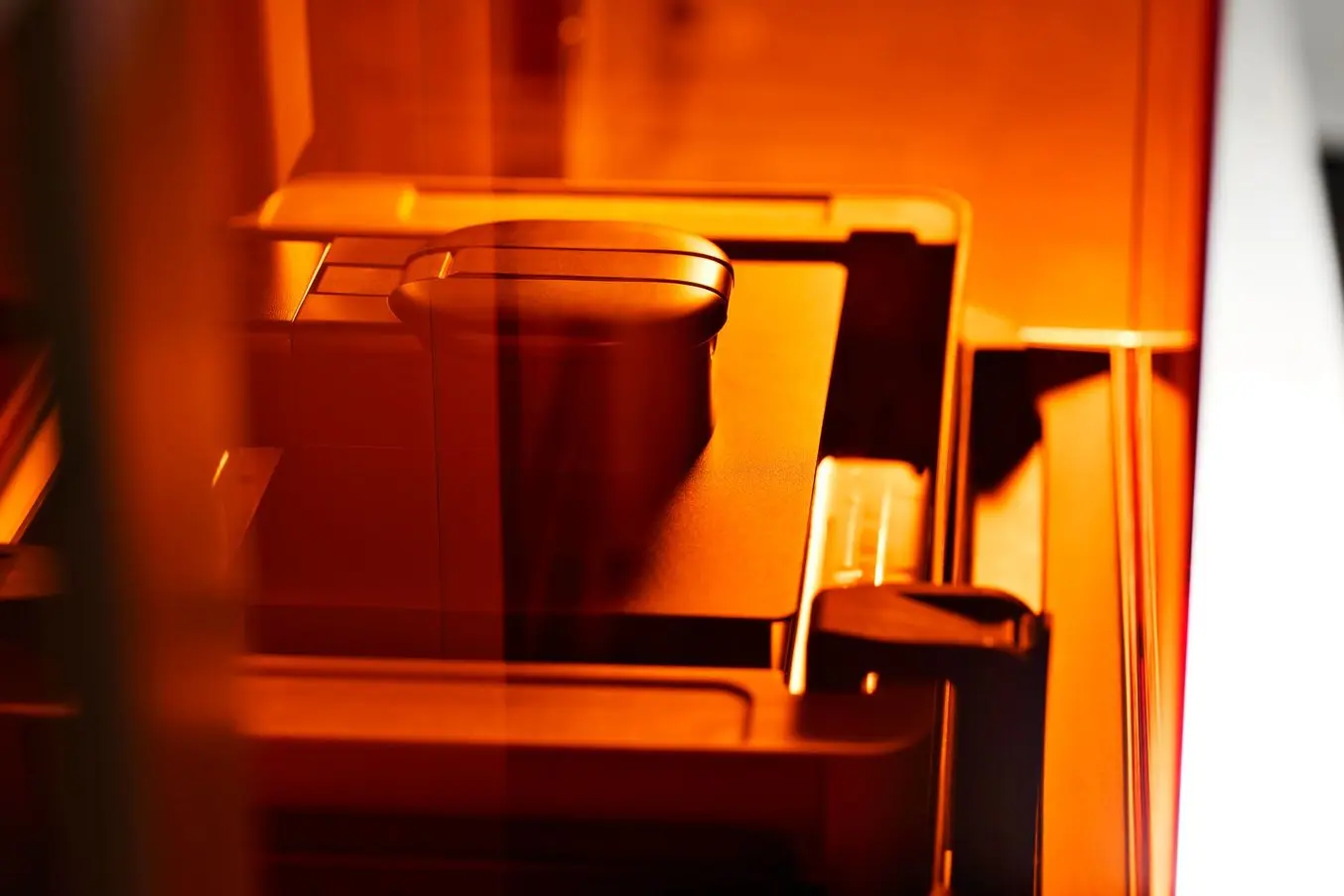
Product Demo: Form 4
See how Form 4 can enable new levels of productivity and innovation through its unmatched speed, accuracy, and reliability.
Acoustic Synth Phase5: The First Acoustic Synthesizer
Instruments and effects that are produced by ensembles can now largely be replaced by digital equivalents. Most manufacturers have recognized this trend and are increasingly focusing on the development of musical software solutions rather than physical instruments and synthesizers.
With the Acoustic Synth Phase5, KORG Berlin combines the controllability of synthesizers with the organic rawness of acoustic instruments by using tuning forks as sound generators that are set in motion by magnetic fields.
The Acoustic Synth Phase5 invites musicians to move from the digital to the analog, physicality of instrumentation. Tuning forks that interact with their spatial environment can be plucked or muted with fingers and, like a guitar, form feedback loops when their signal is reflected back to them by walls or amplifiers. "The mechanical parts react to the room temperature, for example, and sound different in every studio. There are complex physical processes at work that you can't simply replicate in software," explains Hartmann.
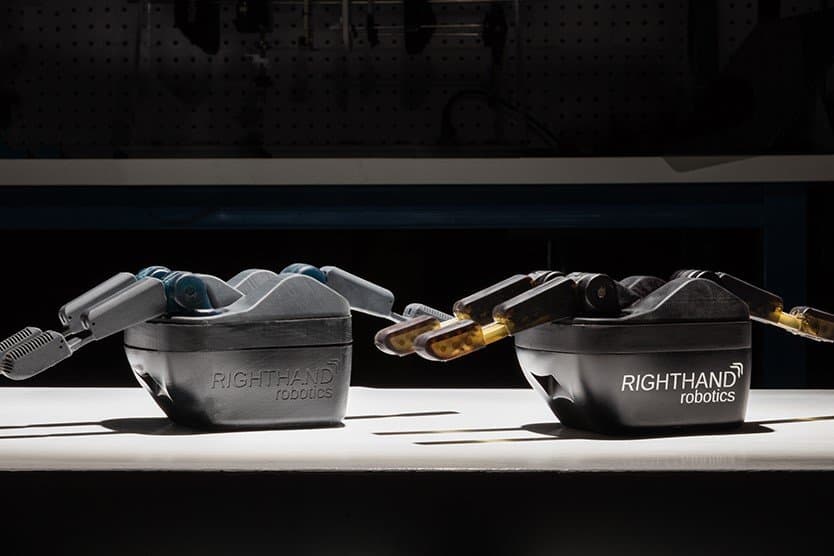
Guide to Rapid Prototyping for Product Development
In this guide, you’ll learn how rapid prototyping fits into the product development process, its applications, and what rapid prototyping tools are available to today’s product development teams.
Prototyping With In-House 3D Printing
"If we want to produce physical objects that users enjoy, then we as designers must also enjoy making them and physically interacting with them," says Lukas.
Since the founding of KORG Berlin, 3D printing has been essential in the development of the Acoustic Synth Phase5. "When we started thinking about what machines we wanted to buy for our prototyping, it was immediately clear that we needed 3D printers," Melnyk recalls. For the young team, additive manufacturing is no longer an innovation, but the fastest, easiest, and cheapest way to prototype.
"Most of our team were already familiar with 3D printing from their studies. For a workshop like ours that is trying to innovate, it's super important that we have a cost-effective option like 3D printing to produce prototypes."
Samantha Melnyk, Sustainability & Communications Designer, KORG Berlin
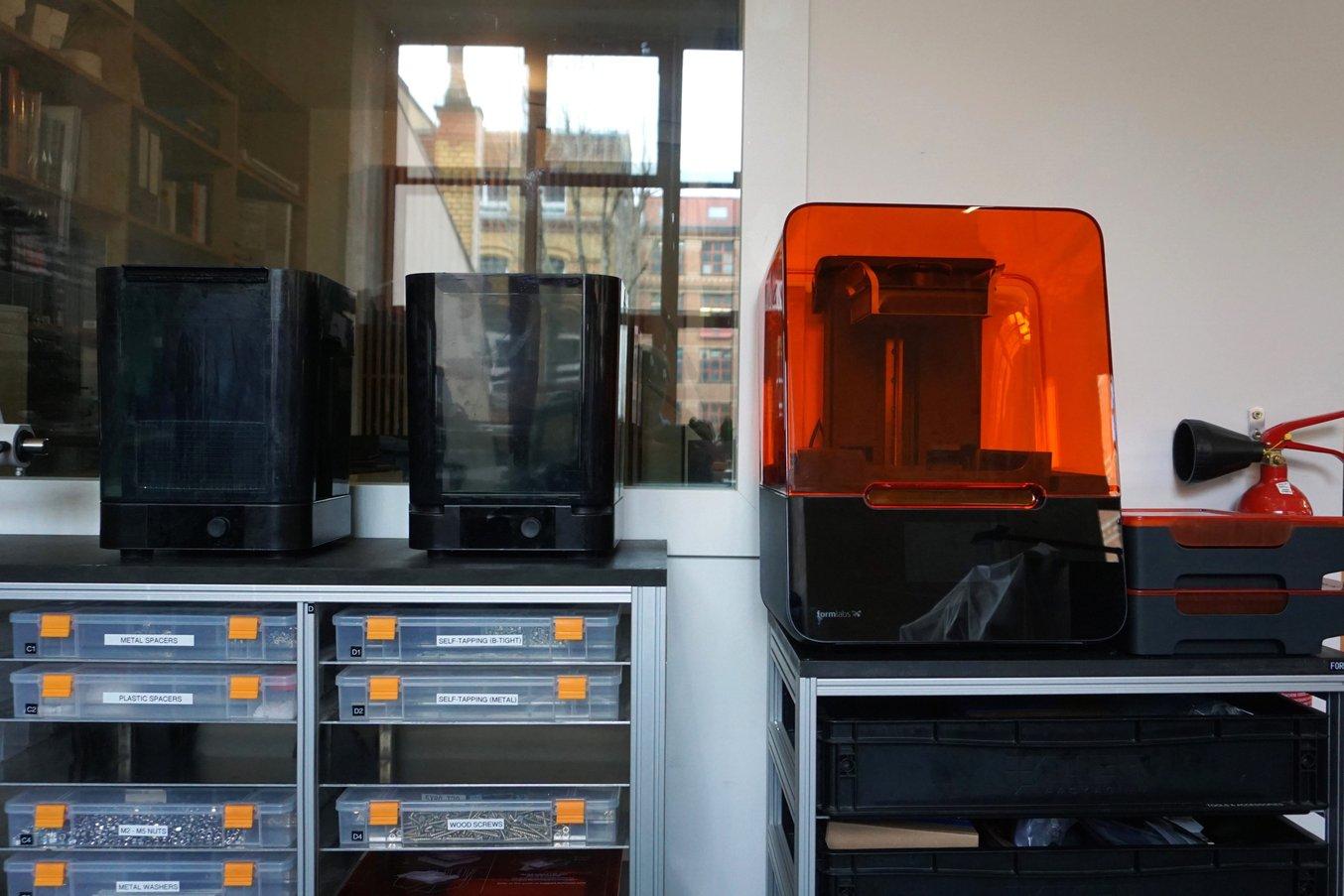
For the development of analog instruments, it’s essential to evaluate a feels-like prototype. KORG Berlin uses the Form Series ecosystem to quickly iterate.
Custom, 3D In-House 3D Printing Reduces Wait Times by 90%
For KORG Berlin, 3D in-house additive manufacturing empowers Hartmann to focus on his concepts, moving beyond the existing portfolio of components and iterating at the speed of printing, not at the speed of external manufacturers.
"The 3D printers give us greater creative freedom because we don't have to orient ourselves to existing parts and existing standards. No matter what we have in mind, we can simply print it instead of spending hours searching warehouses for parts in stock."
Lukas Hartmann, Hardware Developer, KORG Berlin
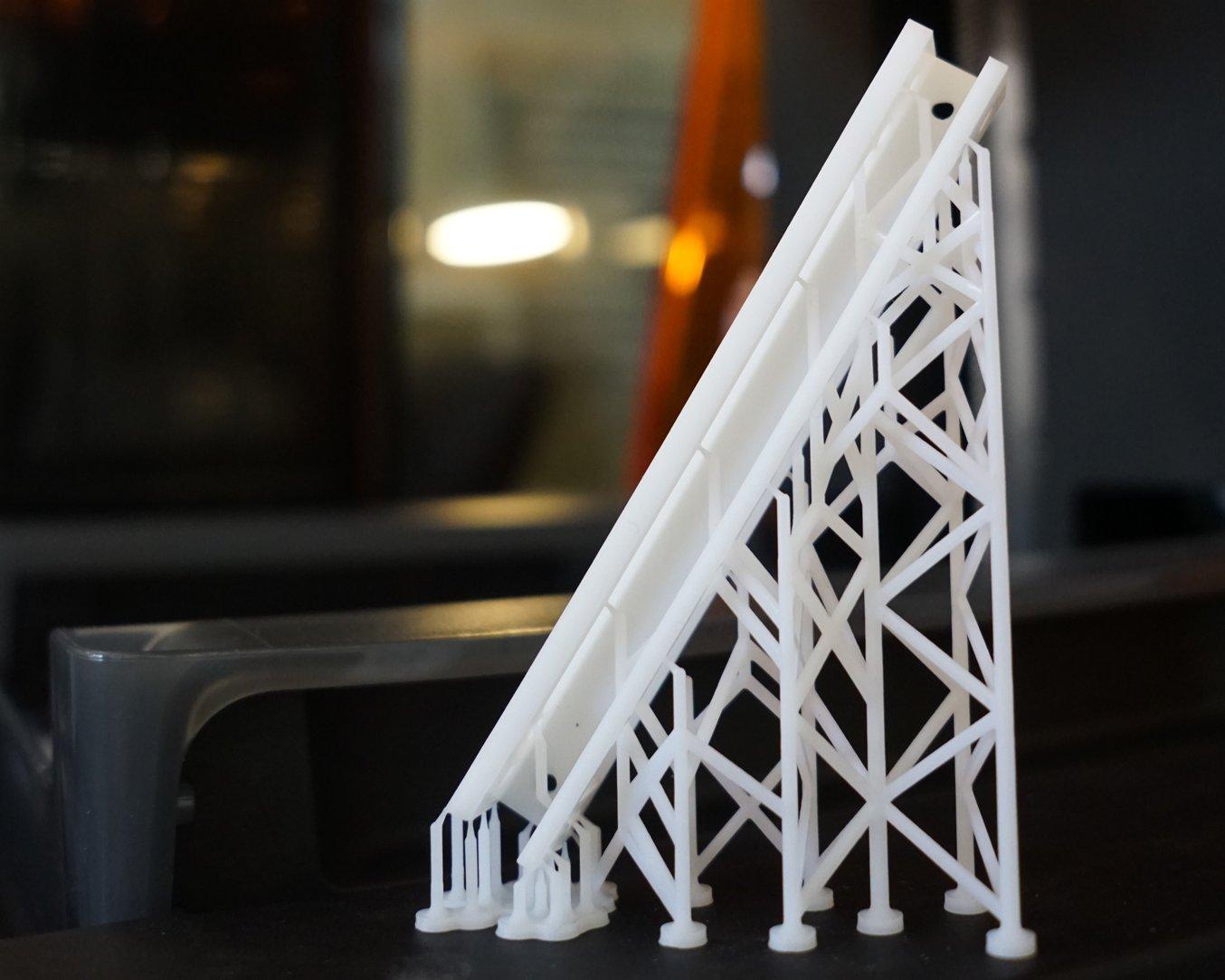
KORG Berlin relies on the precision of Formlabs resin 3D printers to produce the custom parts of functional prototypes, such as this slider guide printed in Rigid 4000 Resin.
Wait times for outsourcing parts can be three days, compared to the few hours or less of in-house 3D printing. This keeps Hartmann and Melnyk in the creative flow.
"With 3D printing, we not only save delivery times, but are also in constant interaction with our developments. If we want to build instruments that musicians can connect with, then we have to have a relationship with them ourselves instead of outsourcing every step of production."
Lukas Hartmann, Hardware Developer, KORG Berlin
Average lead time per part (external order) | Average printing time per part with Form 3+* | Reduction of lead time with 3D printing |
---|---|---|
3-4 days | 5-7 hours | 90% |
*With Form 4, speeds are significantly faster. Learn more here.
For Melnyk, producing analog instruments comes with a great responsibility that she believes has been ignored by the synthesizer industry for too long. Every physical instrument requires natural resources in both manufacturing and development. KORG Berlin therefore tries to make its instruments as sustainable as possible. By 3D printing parts on site, the team saves CO2 emissions from transportation.
"Printing parts in-house and with material we already have on site, rather than having different components delivered that may not work at all, can really make a difference in terms of sustainability.”
Samantha Melnyk, Sustainability & Communications Designer, KORG Berlin
The Advantages of Formlabs Resin 3D Printers Over FDM & CNC
For a long time, KORG Berlin only had access to fused deposition modeling (FDM) 3D printers. Since the acquisition of a Form 3+ stereolithography (SLA) 3D printer, the FDM printers are hardly used.
"I use our SLA printers much more often than the FDM printers simply because of their resolution, the smooth surface, and the large selection of materials. With SLA, I can do so much that would be impossible with FDM. I can't say the same the other way around."
Lukas Hartmann, Hardware Developer, KORG Berlin
The first major advantage of Formlabs SLA 3D printers is their accessibility: intuitive user experience, easy workflows, and validated settings. In contrast to FDM printing, Form 3+ does not require any previous experience or lengthy experimentation with print settings, but enables even beginners to achieve absolutely reliable and fast results. "The Form 3+ gives us total reproducibility and prints the same part perfectly every time," explains Lucas.
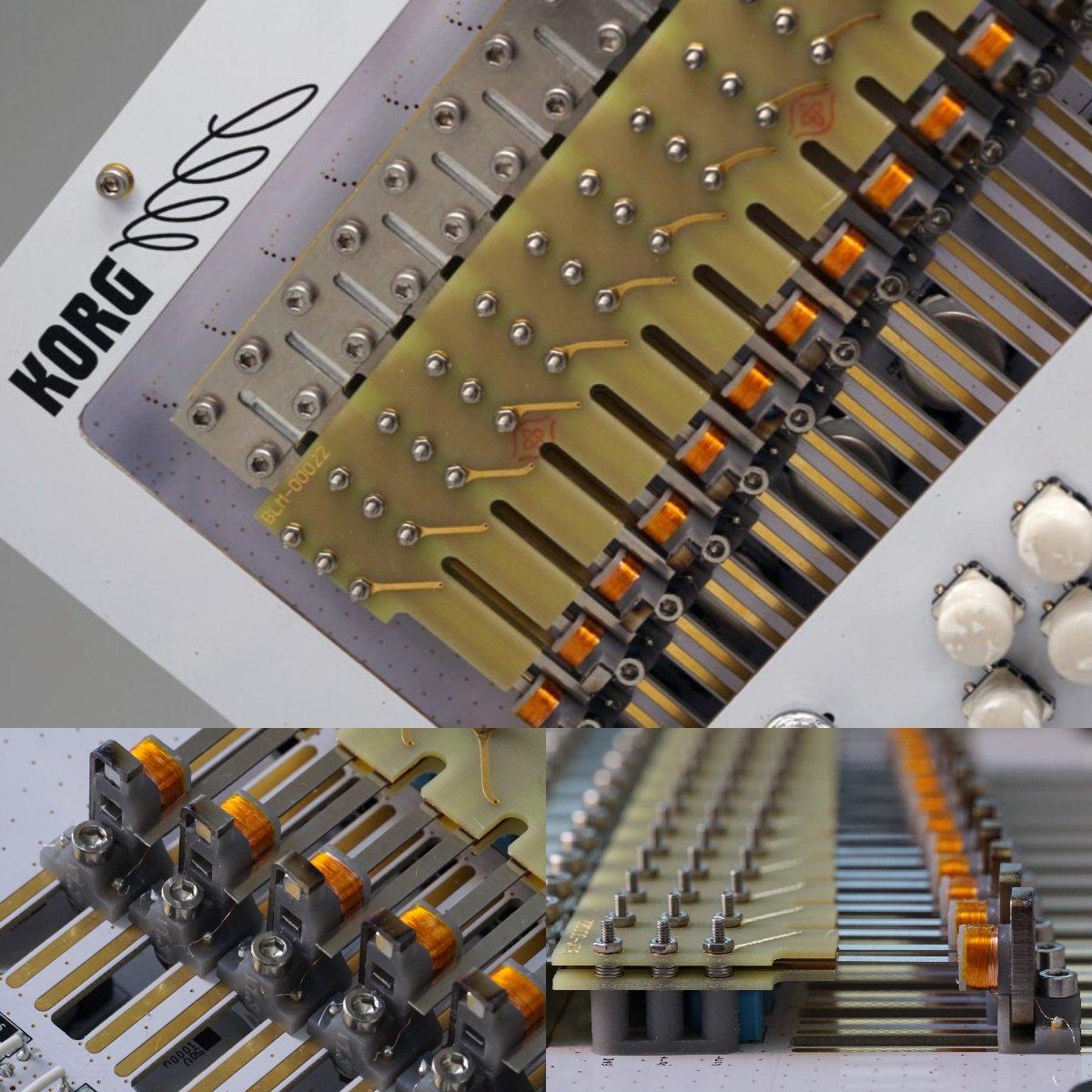
Complex small parts can be 3D printed precisely, cost-effectively, and quickly with Grey Pro Resin so that development can continue without interruption.
Print setup, too, is easy as the ideal parameters, the orientation of the part, and the necessary supports are automatically generated in PreForm. At KORG Berlin, all team members can easily print with Form 3+, giving the small team flexibility and speeding up development time.
Build Platform 2, with quick-release technology, helps to minimize post-processing time. "Build Platform 2 is a huge advantage. We can now completely do without support structures and print directly on the build platform. We can now print parts such as spacers, which have to be absolutely precise, in the XY plane. This means that tight tolerances on the micron level can be printed much more easily," says Hartmann.
"The Form 3+ is incredibly easy to use. With SLA 3D printing, we don't have to worry about the geometry of our parts and post-processing, for example, because the printed part is oriented automatically. This makes the workflow very fast. Especially for a small team like ours, it is extremely valuable to be able to produce aesthetic parts with minimal post-processing."
Samantha Melnyk, Sustainability & Communications Designer, KORG Berlin
Synthesizers consist of a multitude of small parts that have to be perfectly positioned to enable the tuning forks to vibrate. Therefore, Hartmann had to produce parts with complex geometries that were unattainable via milling or FDM 3D printing. "The high printing accuracy of Form 3+ has helped us enormously in the production of all our small and geometrically complex parts," says Lukas.
"The advantage of SLA is that I hardly have to adapt my design, thanks to the simple printing of the supports, which offers large tolerances. For FDM or CNC, I regularly have to make adjustments and disassemble parts into several components in order to manufacture them. I simply don't have these problems with SLA."
Lukas Hartmann, Hardware Developer, KORG Berlin
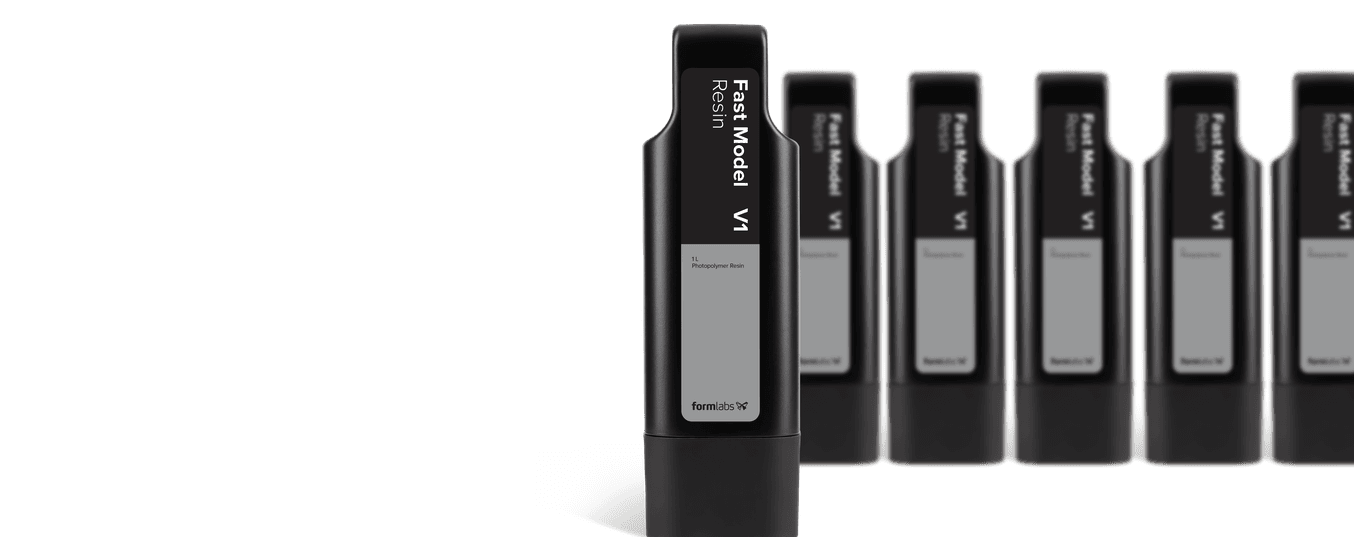
Form 4 Materials Guide
Learn more about all the high performance materials available on Form 4 and how to leverage the right material for your application.
Creative Freedom Through Material Diversity
What particularly excited the team at KORG Berlin about resin 3D printing with Formlabs was the wide variety of materials available, which gave them the freedom to try out different conceptual approaches without additional entry costs. Not only can they print precise spacers for their prototypes cost-effectively with Grey Pro Resin or Rigid 4000 Resin, but they can also experiment with high-quality materials such as ceramic and quickly test various control elements such as drum pads made of Elastic 50A Resin.
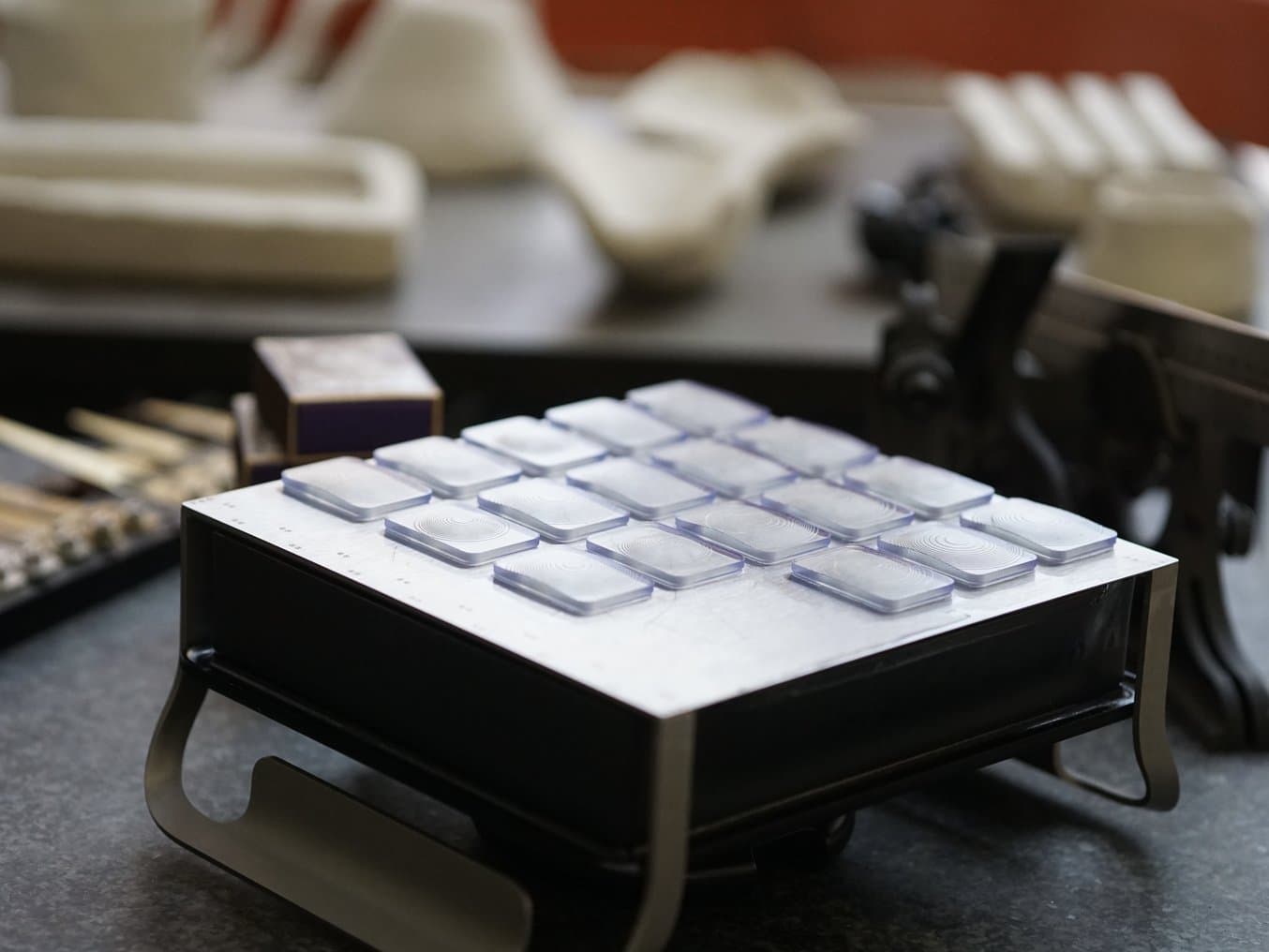
The Formlabs material library includes materials with a range of material properties. These pads are printed with Elastic 50A Resin.
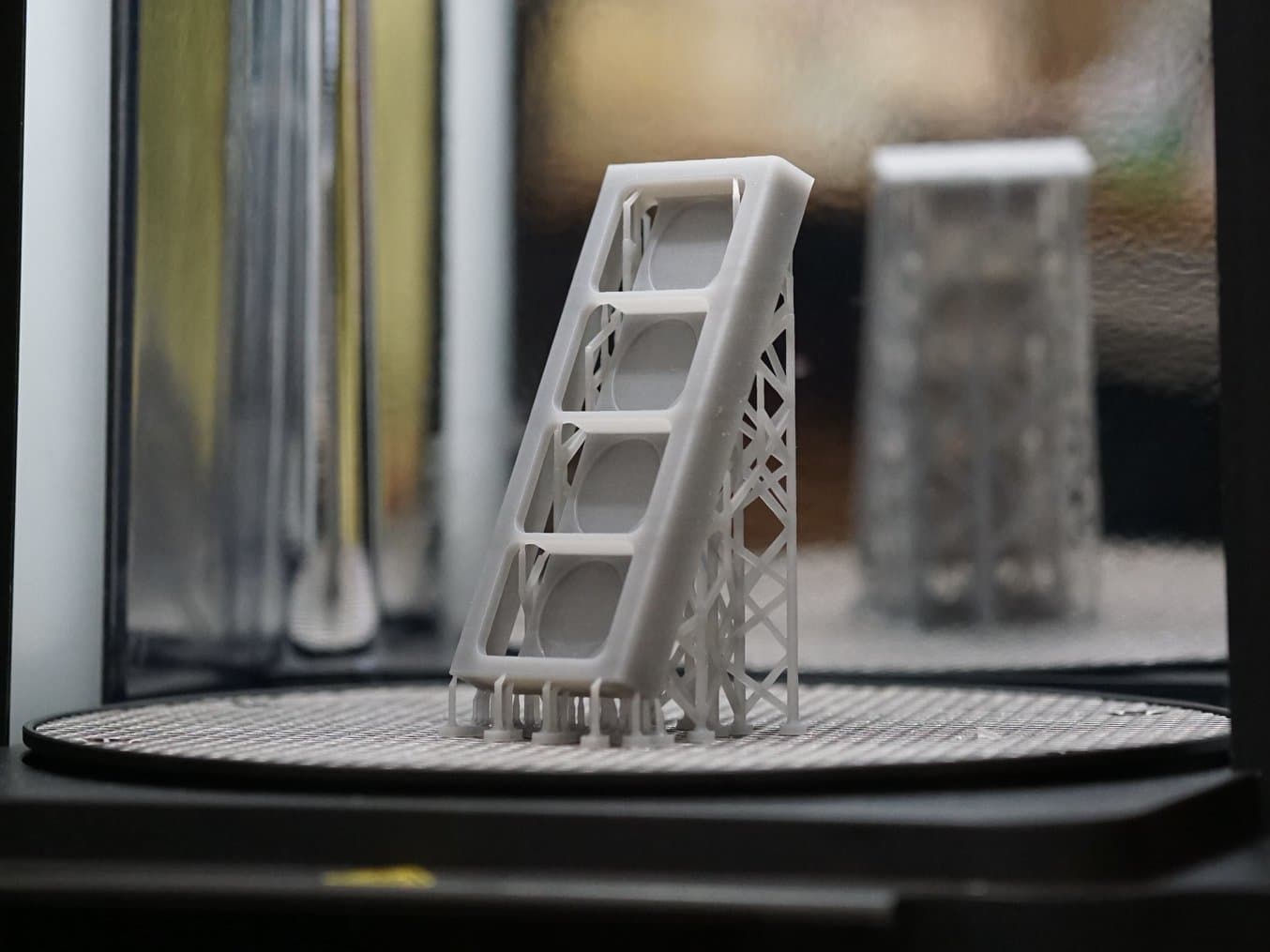
A pad holder prototype must be stiffer and more robust, and is printed with Grey Resin Pro.
Instead of having to buy different equipment to use different materials, Formlabs resins can be changed in a matter of seconds. This gives the KORG Berlin team the agility to react flexibly to new requirements and customer feedback.
"The fact that we can easily experiment with so many materials helps us to remain open to new possibilities. Other devices only work with specific materials and are limited in the way we use them. The Form 3+ has no such limitations and new resins are constantly being developed that are similar to materials we would use for end applications. That's the great thing about SLA."
Samantha Melnyk, Sustainability & Communications Designer, KORG Berlin
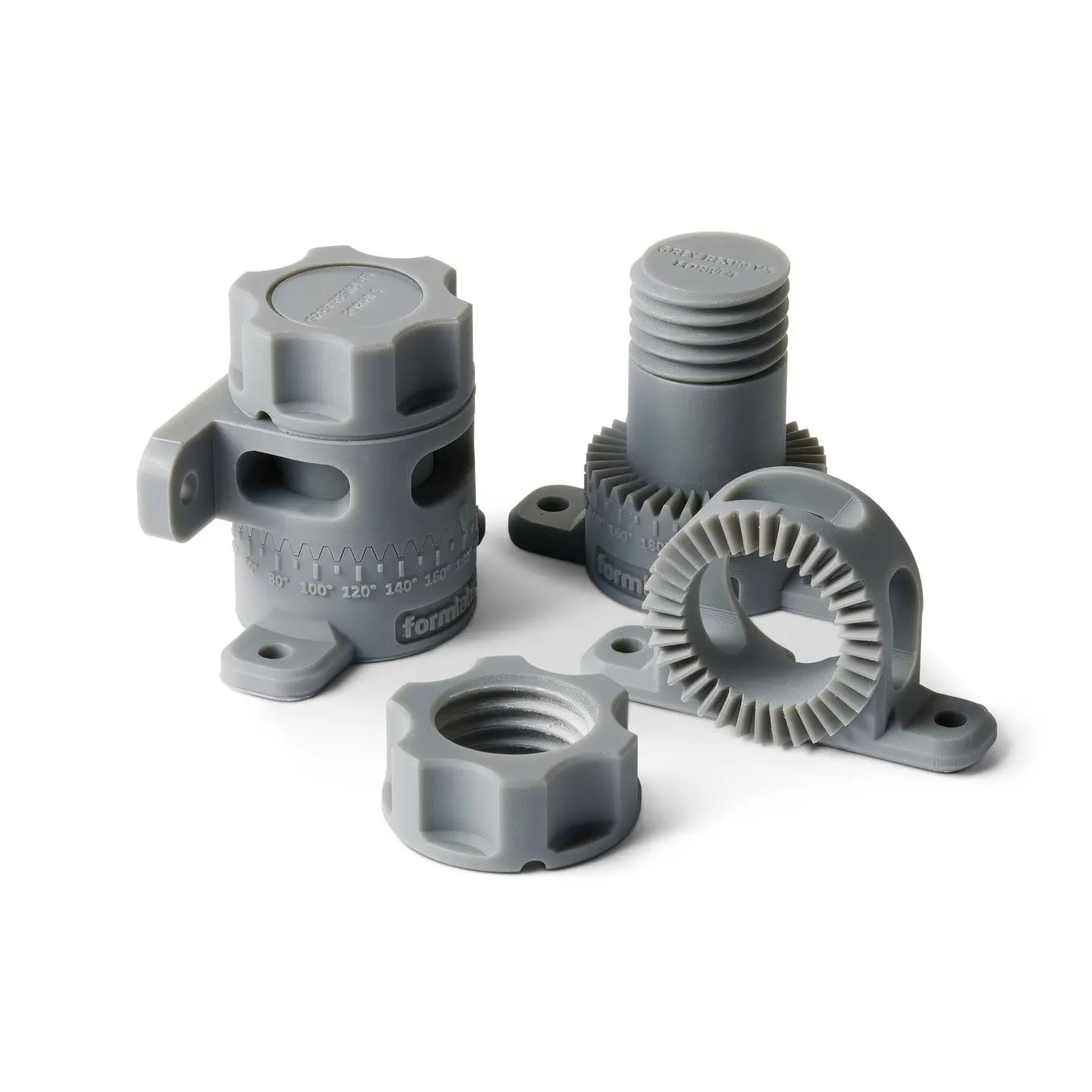
Request a Free Sample Part
See and feel Formlabs quality firsthand. We’ll ship a free 3D printed sample part to your office.
Future Developments With Resin 3D Printing
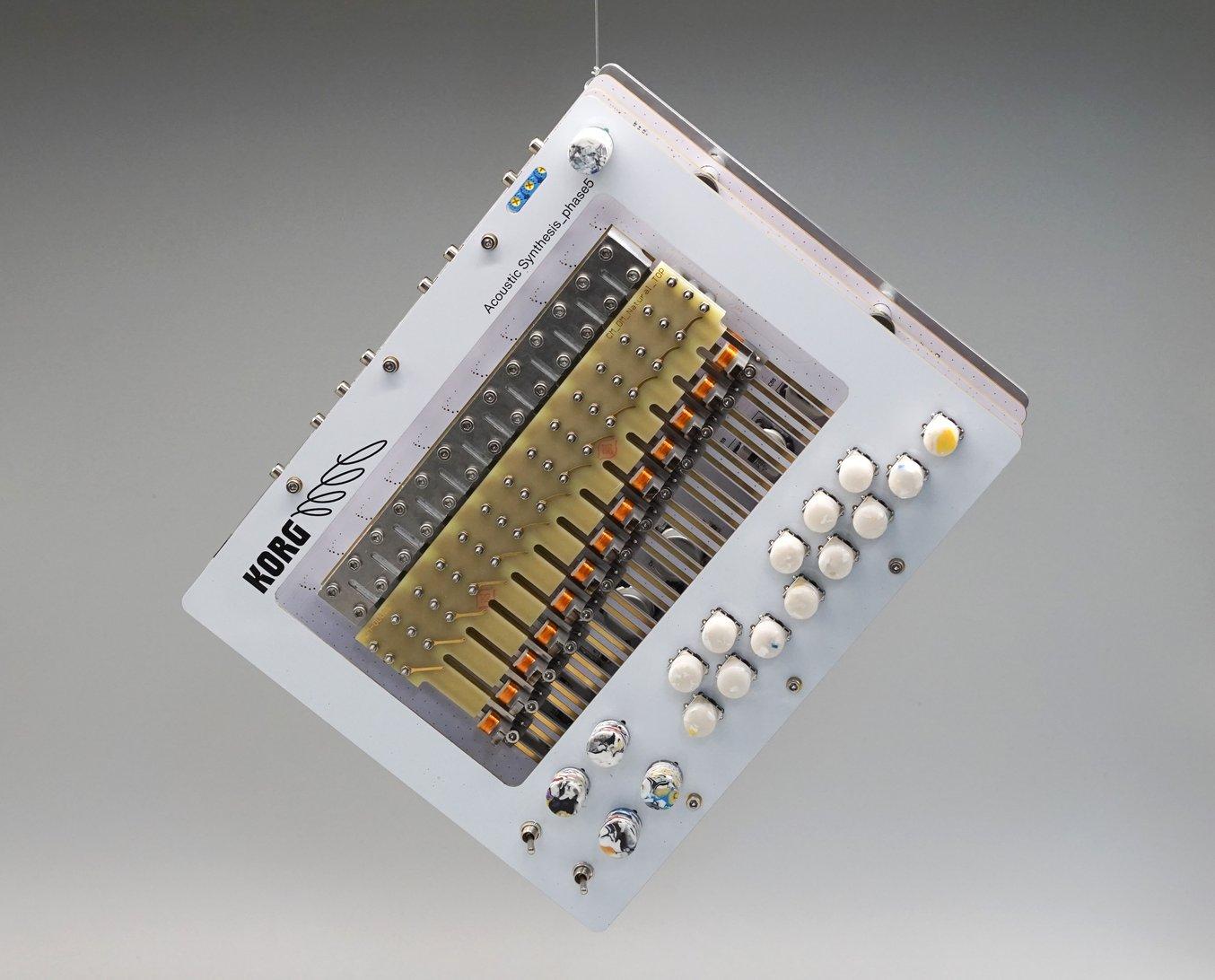
Creativity often hangs by a thread and must be pursued before inspiration is lost. With the flexibility of in-house resin 3D printing, KORG Berlin will continue to produce innovations such as the Acoustic Synthesis_phase5 in the future.
KORG Berlin will continue its search for innovative approaches to analog synthesis — 3D printing is an indispensable part of this process. Currently, Formlabs resin 3D printers are being used to develop the Acoustic Synthesis_phase5. Hartmann says, “It is an enormous privilege that we can now access technologies such as 3D printing. Such rapid iterations were previously unthinkable and now open up a whole new range of products and ideas for us to work on.”
Explore Formlabs resin 3D printers to learn more, or contact an expert to see how 3D printing can help you meet your goals.