In partnership with Autodesk, we are excited to announce that Formlabs Nylon 12 Powder and Tough 2000 Resin have been introduced to the Fusion 360 Material Library! Along with our newest design, visualization, and production tools, we are expanding on a shared mission to make digital fabrication more accessible.
The updated material library is the result of an extensive study by Autodesk to research their customers’ most used materials as well as probing the properties of printed parts. The Autodesk team 3D printed dozens of samples and sent them off to their materials testing lab in Australia, where they measured thermal, mechanical, and physical properties (shown in image below).
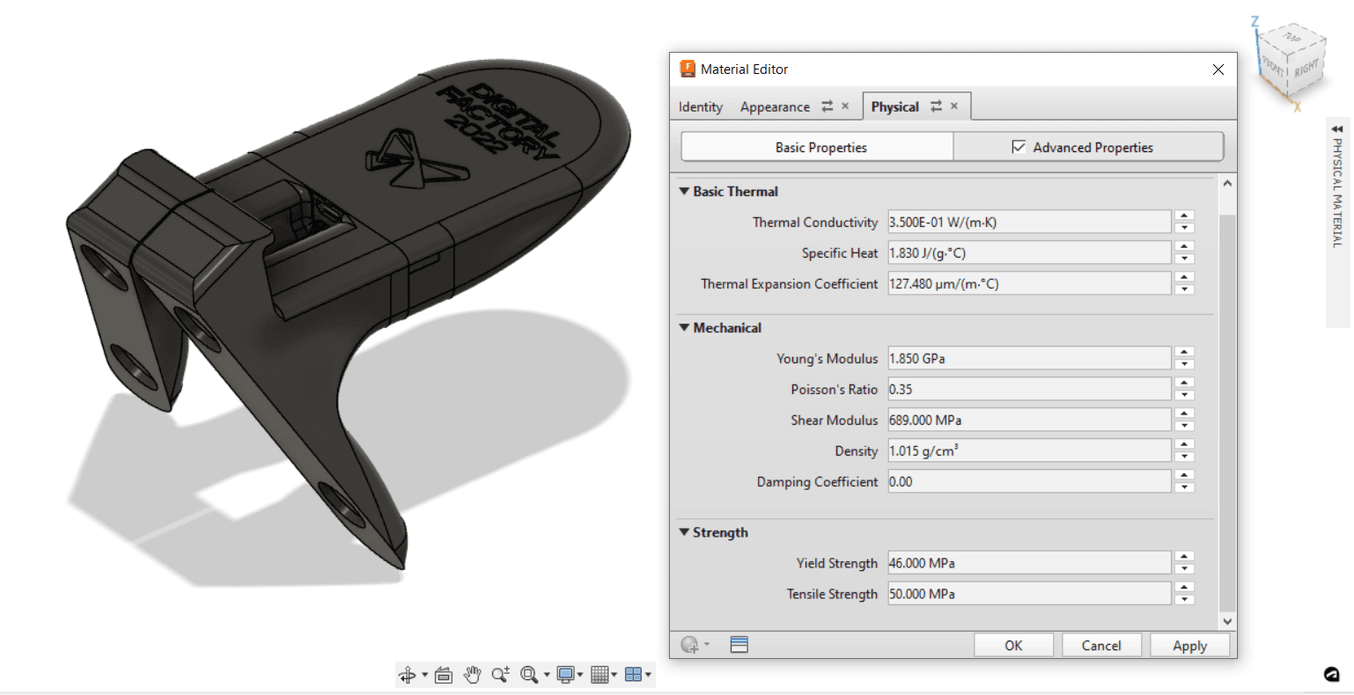
Wireless phone charger represented in Nylon 12 Powder. Designed by Evan Fisher of Formlabs.
Nylon 12 Powder and Tough 2000 Resin are now available in the Design, Simulation, and Generative Design workspaces. You can apply these materials to your design to accurately represent your part’s mechanical properties and appearance.
According to Senior Product Manager at Autodesk Sualp Ozel, 3D printing allows designers to explore more ambitious ideas than ever before, but determining how these unique geometries perform in the field is a new challenge. “Today, designers can create previously unimaginable forms with technologies like generative design, and leverage additive manufacturing to turn those ideas into reality. By combining both technologies, form and function can be considered simultaneously, and manufactured rapidly. With this new addition, Fusion 360 users are now able to design and simulate their ideas before printing with their Formlabs materials and hardware, and be confident that their printed parts will perform in the field right the first time.”
"With this new addition, Fusion 360 users are now able to design and simulate their ideas before printing with their Formlabs materials and hardware, and be confident that their printed parts will perform in the field right the first time."
Senior Product Manager at Autodesk, Sualp Ozel
Many Formlabs customers are already taking advantage of the additive manufacturing tools within Fusion 360. Here you can read how Vertiball, maker of an accessible wall-mountable muscle massager, prototypes parts on the Form 3 using Tough 2000 Resin as a mimic for injection molded plastics. Furthermore, the founders of Michigan-based KUHMUTE use Nylon 12 Powder on the Fuse 1 SLS printer to produce end-use parts for their universal micromobility charging stations.
Case Study: Wireless Phone Charger for The Digital Factory
At this year’s Digital Factory conference in Boston, attendees assembled their own Qi wireless phone chargers using 3D printed parts and a flexible circuit board. They followed along with interactive instructions at a Vention workstation powered by software from Tulip. The final assembly came together with a satisfying “click” of interlocking SLS nylon components.
Formlabs’ 3D model manager Evan Fisher designed the charger using Fusion 360, and also oversaw the production of over 500 units for our one-day conference. Various features within Fusion 360 aided his process from prototype to final production on the Fuse 1 printer.
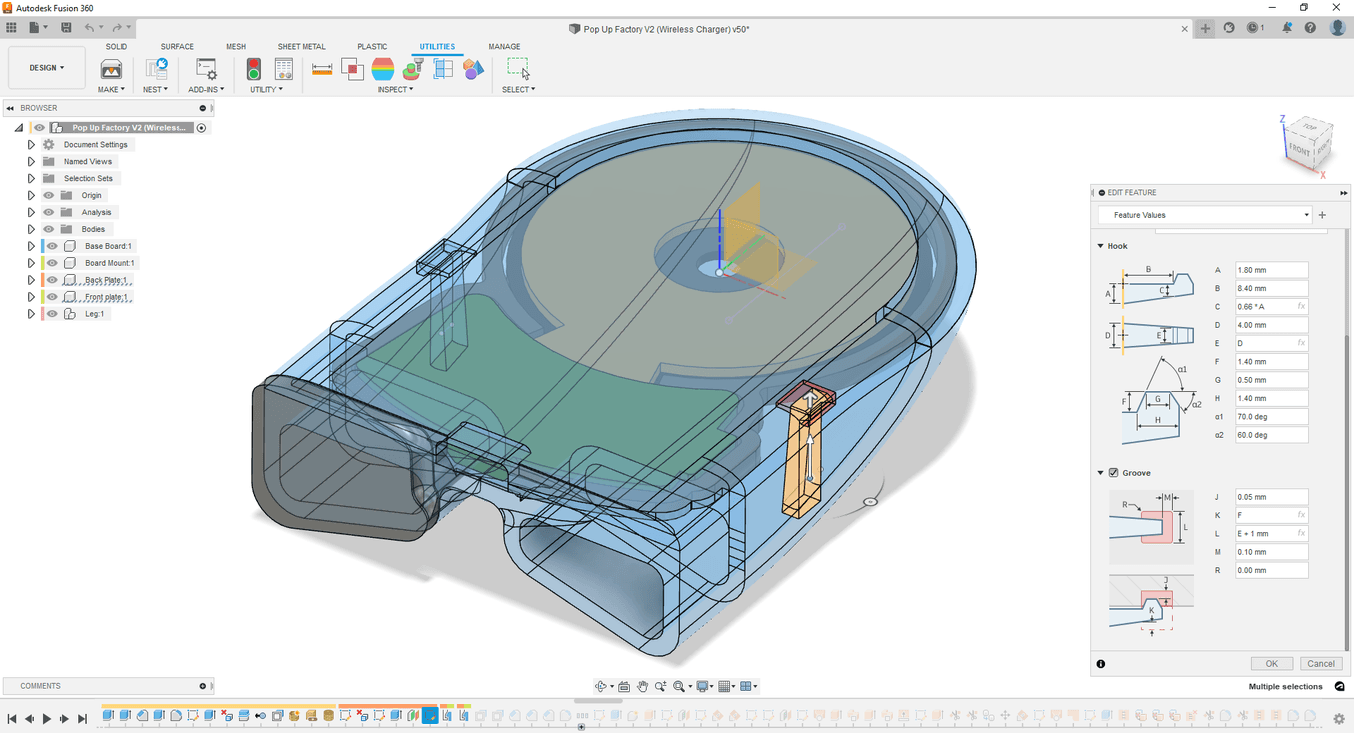
Visualization of flexible PCB within the Nylon 12 shell. We also took advantage of the Snap Fit Generator tool from Fusion 360.
The charger is composed of four individual shell components that fit around one flexible PCB assembly. Evan started by importing the geometry of the circuit board to design and visualize the shell around this PCB geometry. In order to connect shell components together without needing external hardware, he designed a robust snap fit mechanism using the Snap Fit Generator in the product design extension of Fusion 360. Ultimately, the team chose Nylon 12 for the final production parts because these delicate features require a balance of compliance and strength.
Evan quickly printed his first iteration in Tough 2000 Resin to get a general sense for the shape of the model and how the internal electronics and 3D printed shell would come together. He then moved on to prototyping in Nylon 12 Powder to lock in the action of the snap fits and check part clearances. In total, his team developed four versions of the charger before landing on a final design.
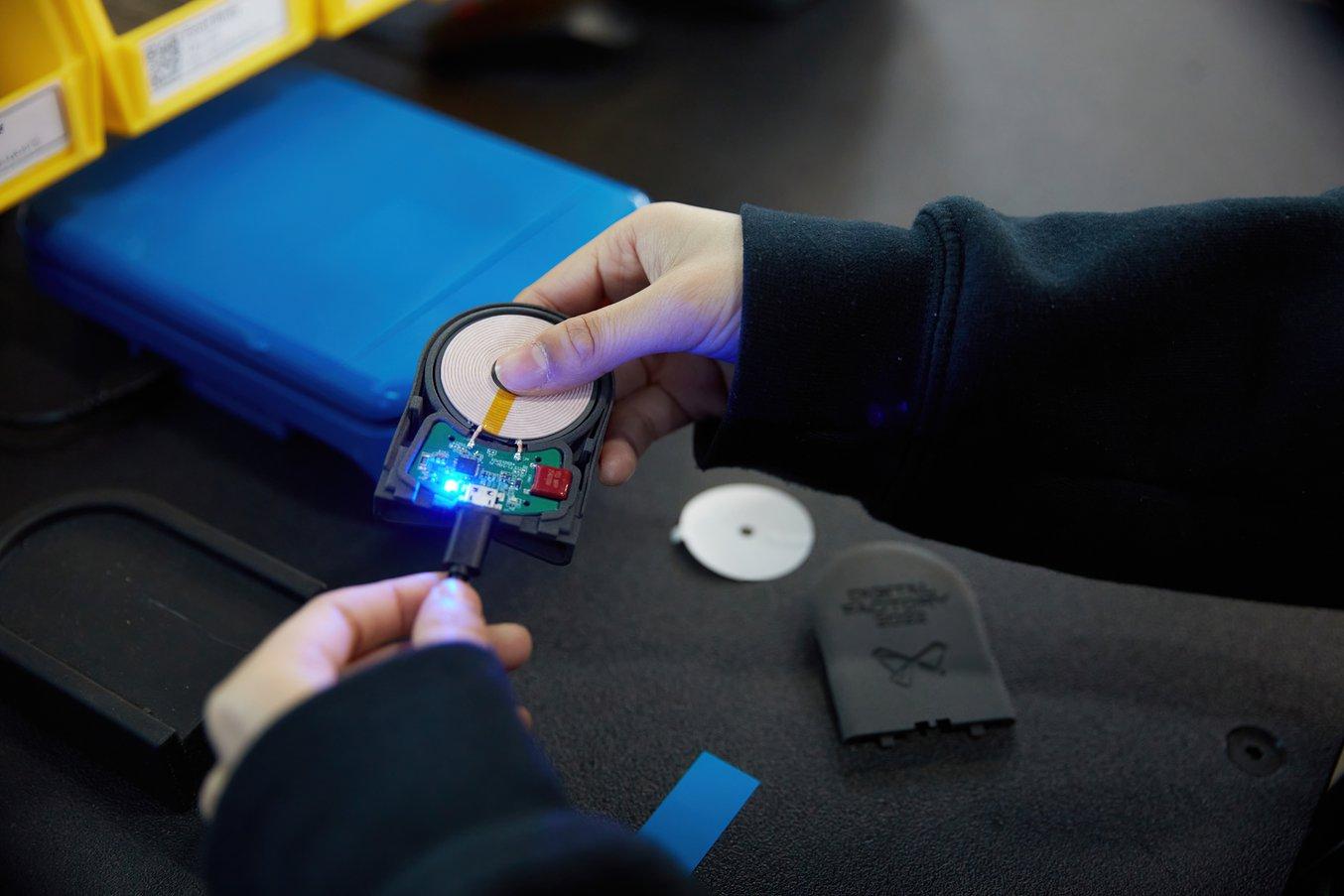
The final charger assembly. Interactive instructions, assembly line workstations, and QA tools were provided by Vention and Tulip.
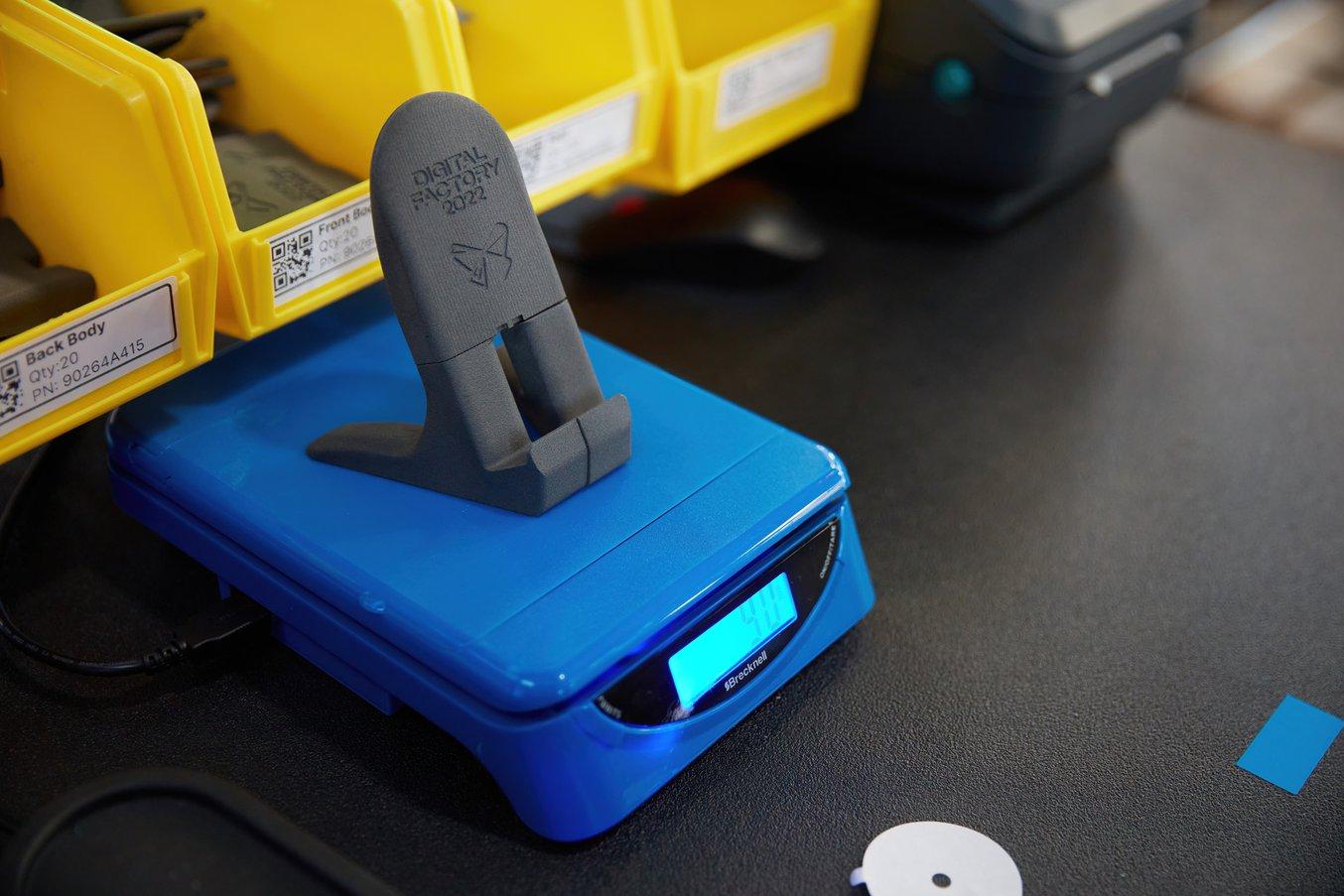
Finally, the team efficiently nested 27 copies of the charger shell (108 individual parts) into a Fuse 1 build volume. The total batch production required 19 separate print jobs, run over multiple Fuse 1 printers at the Formlabs Massachusetts and Ohio offices. The Autodesk team continues to make improvements to Fuse 1 packing features to aid efficient batch production for these types of projects. We’re excited to see how our customers leverage the newest tools within Fusion 360 to aid every step from prototyping to production.
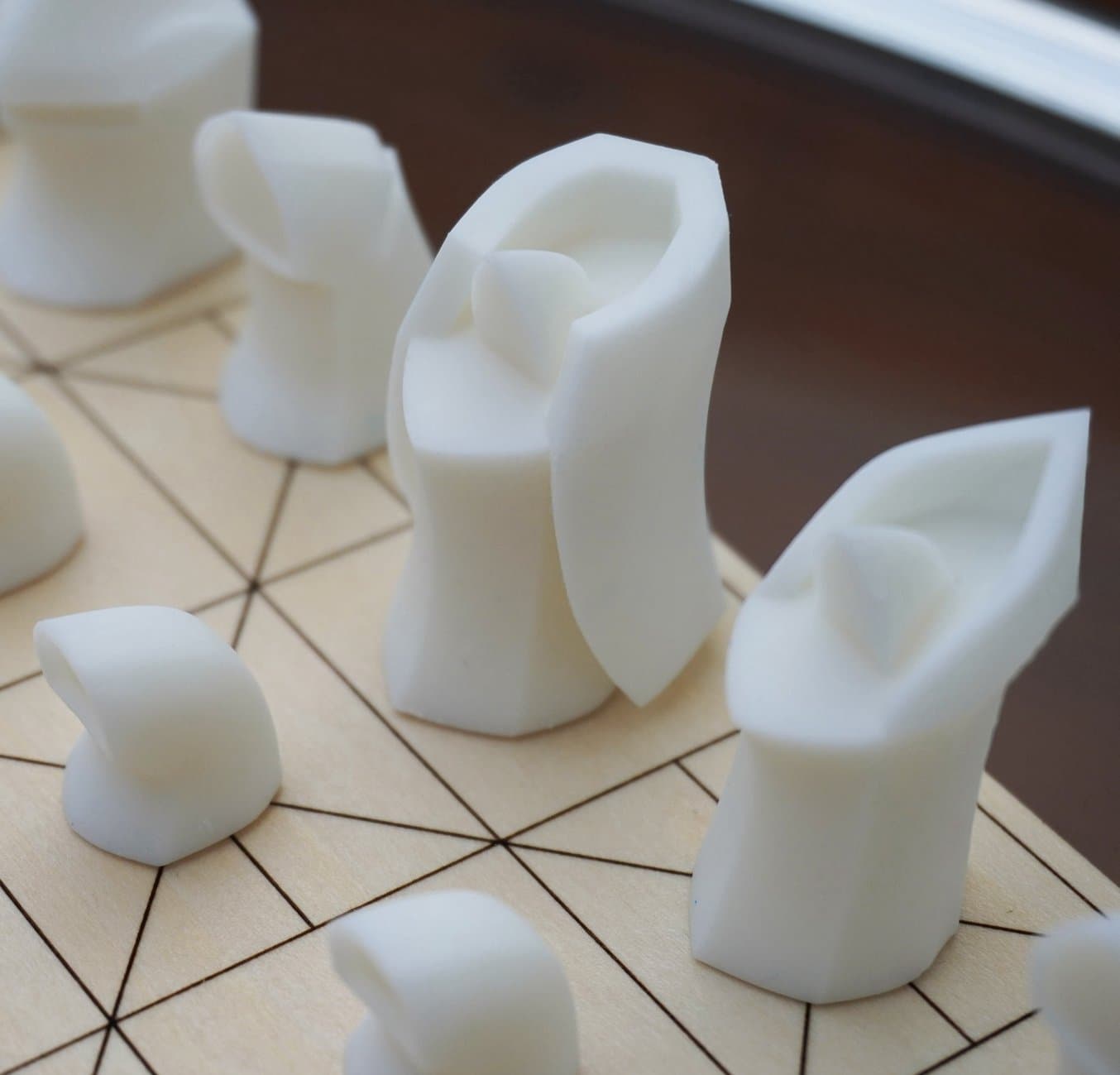
Formlabs Integration with Fusion 360
Formlabs and Autodesk’s Fusion 360 have partnered to streamline your digital workflow with a new CAD software for 3D printing integration. Visit our integration hub to learn about the newest Fusion 360 features for SLA and SLS, read more user stories, and download our design guide. (Pictured: chess set by Will Qiu)