Fast, cheap, good. The age-old quest in manufacturing is achieving speed and quality at a low cost, and it’s a common belief that it’s impossible to achieve all three. When manufacturing plastic parts, most engineers would say injection molding is the best solution for all three, with quick cycle times, strong materials, and inexpensive cost per part. But with recent innovations in 3D printing, is that really still the case?
In April 2024, we pitted Form 4 against injection molding to show how far 3D printing has come: that it can compete with, or even beat, injection molding when it comes to speed and quality at a low cost. The comments were wild with questions. Now, with the release of Form 4L, which has 4.6x the build volume of Form 4, we decided to run this test again, producing the Form 4 Resin Mixer Latch. With two Form 4L masked stereolithography (MSLA) 3D printers and injection molding, we set out to prove that the blazing speeds of Form 4 Series 3D printers can outpace traditional injection molding.
Below, we break down the costs, time, and mechanical properties for producing the end-use parts, addressing viewers’ questions about cost, post-processing, and mechanical properties of 3D printed parts.
Manufacturing the Form 4 Resin Mixer Latch
Production Process: Injection Molding vs. 3D Printing
The Form 4 Resin Mixer Latch is a component of the Form 4 Mixer, an accessory that attaches to the Resin Tanks in Formlabs Form 4 Series printers and improves material performance by keeping resin homogenous in the tank during the printing process. For this test, we timed two production operations in a race to 1,000 end-use parts: the actual contract manufacturer using injection molding, and two Form 4L large-format resin 3D printers.
The mixer latch secures the Resin Mixer in place on the Form 4.
For injection molding, we worked with a contract manufacturer based in Taiwan that has produced components for multiple generations of Formlabs 3D printers, including tanks, cartridges, and mixers. The two-cavity mold used for this test is the real one used in serial production of Form 4 Resin Mixer Latches.
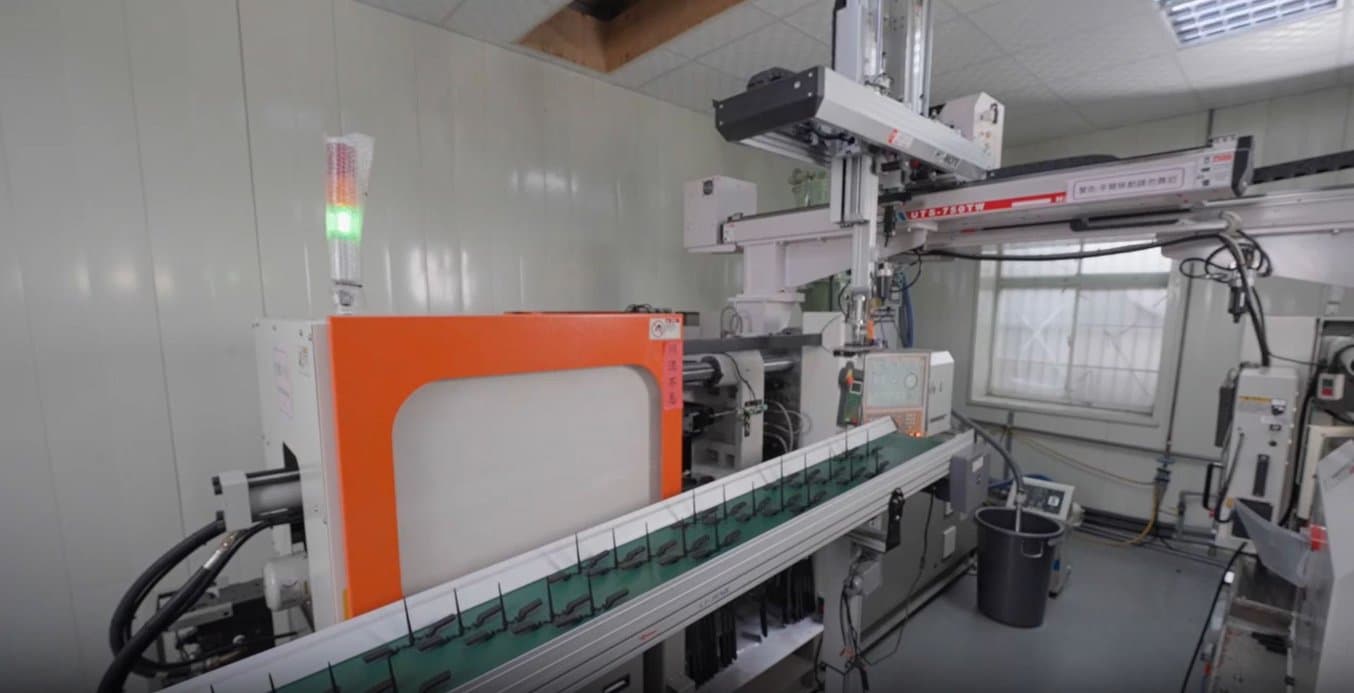
The injection molding machine at the contract manufacturer takes up 10 square meters of floor space.
For the 3D printing comparison, we used two large-format Form 4L 3D printers, which are designed for high-throughput production, with a large build area and fast print speeds. The setup also included one Form Wash L and one Form Cure L for post-processing. For the material, we chose Black Resin V5, a stiff and strong general-purpose material that produces matte, presentation-ready parts.

Form 4L Manufacturing Setup
The 3D printing setup takes up approximately three square meters of floor space and includes:
- 2x Form 4L
- 2x Resin Pump
- 2x Black Resin 5 L containers
- 1x Form Wash L
- 1x Form Cure L
In the real injection molding environment, each cycle takes 50 seconds and yields two parts. The speed could be increased by having a mold with more cavities, which would produce more parts per cycle, or by decreasing the cycle time with process changes, but this is the process we and our contract manufacturer decided was the optimal one for our production needs. As we’ll discuss shortly, injection molding does take over as the cheaper production method for this part in volumes over about 13,000 units.
With Form 4L, we printed 78 parts per print job, meaning 13 print jobs are needed to produce 1,000 parts. The proprietary Low Force Display™ print technology used in Form 4 Series printers enables fast print speeds, and adjustments were made in PreForm’s Print Settings Editor to increase speed even further. A custom print setting with a layer height of 150 μm reduced the number of layers needed to complete the print, and increased irradiance and exposure to reduce the time needed for each layer. Learn how to use Print Settings Editor here.
Part Production Times
Injection Molding | 3D Printing | |
---|---|---|
Parts per cycle/print | 2 | 78 |
Time per cycle/print | 50 sec | 48 min |
Number of cycles/prints | 500 | 13 |
Total parts | 1,000 | 1,014 |
Total time | 6 h 59 min | 5 h 56 min |
Both injection molded and 3D printed parts require some post-processing. Injection molded parts need sprues and runners removed. Resin 3D printed parts must be washed and cured, and supports removed. In both cases, post-processing can be done by operators during production, meaning post-processing only increases production time for the last cycle of parts.
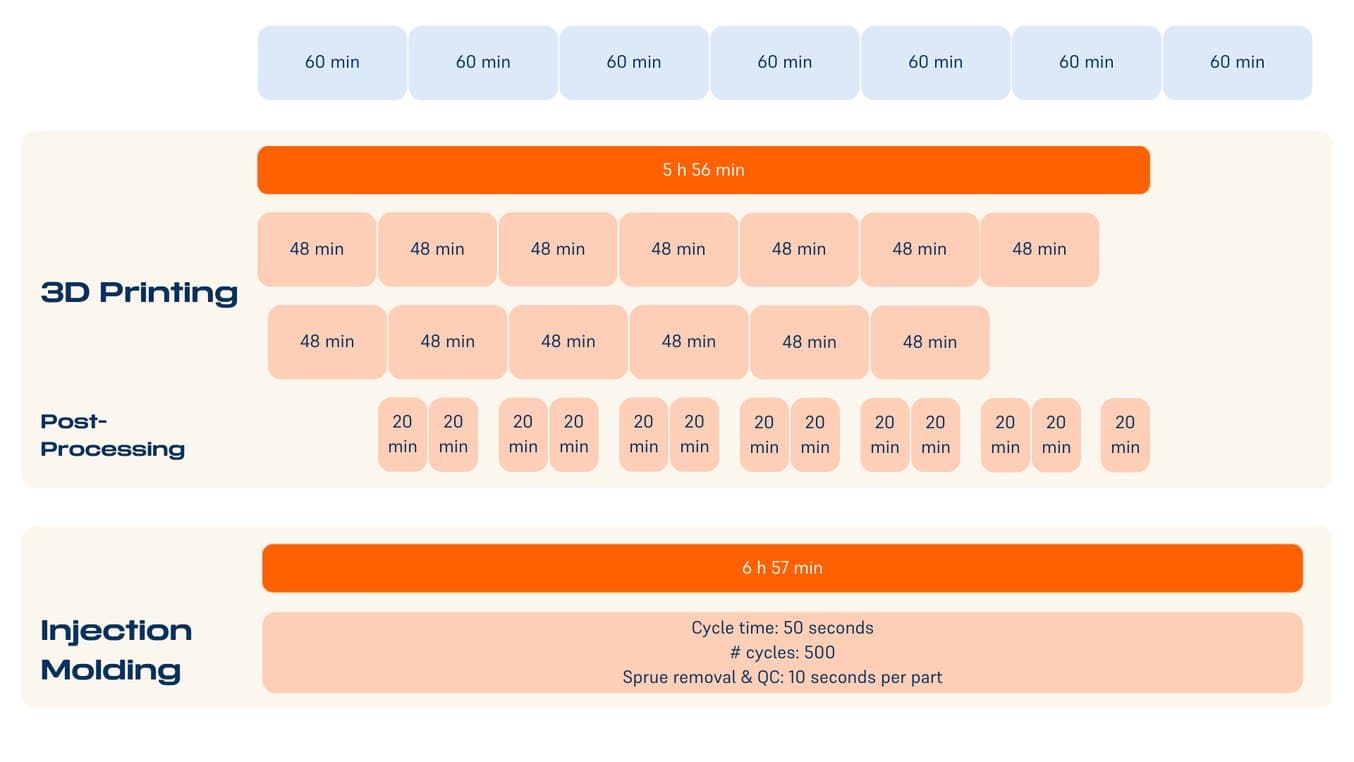
Lead Time Comparison: Six Weeks vs. Same-Day
While our head-to-head race focused only on production time, the timeline to production arguably starts with the fabrication of the mold used for injection molding. Getting a mold of this size and complexity made can typically take several weeks, which can only be expedited by paying a 2-3x premium. From finalized part design to finished parts, a typical lead time would be 4-6 weeks, accounting for design for manufacturability, tool cutting, production, and processing.
In contrast, 3D printing requires no tooling, and parts can be printed same-day at no additional costs. This means a short production run with 3D printing can be completed before injection molded tooling designs are even finalized.
Cost Per Part Breakdown: 85% Lower Costs
With no tooling costs, 3D printing is well established as an inexpensive way to produce a small number of parts. This well-earned reputation applies in this case as well: at 1,000 parts, 3D printing costs 85% less than injection molding. We broke down the numbers, finding that the breakeven point between the two methods is 13,050 parts.
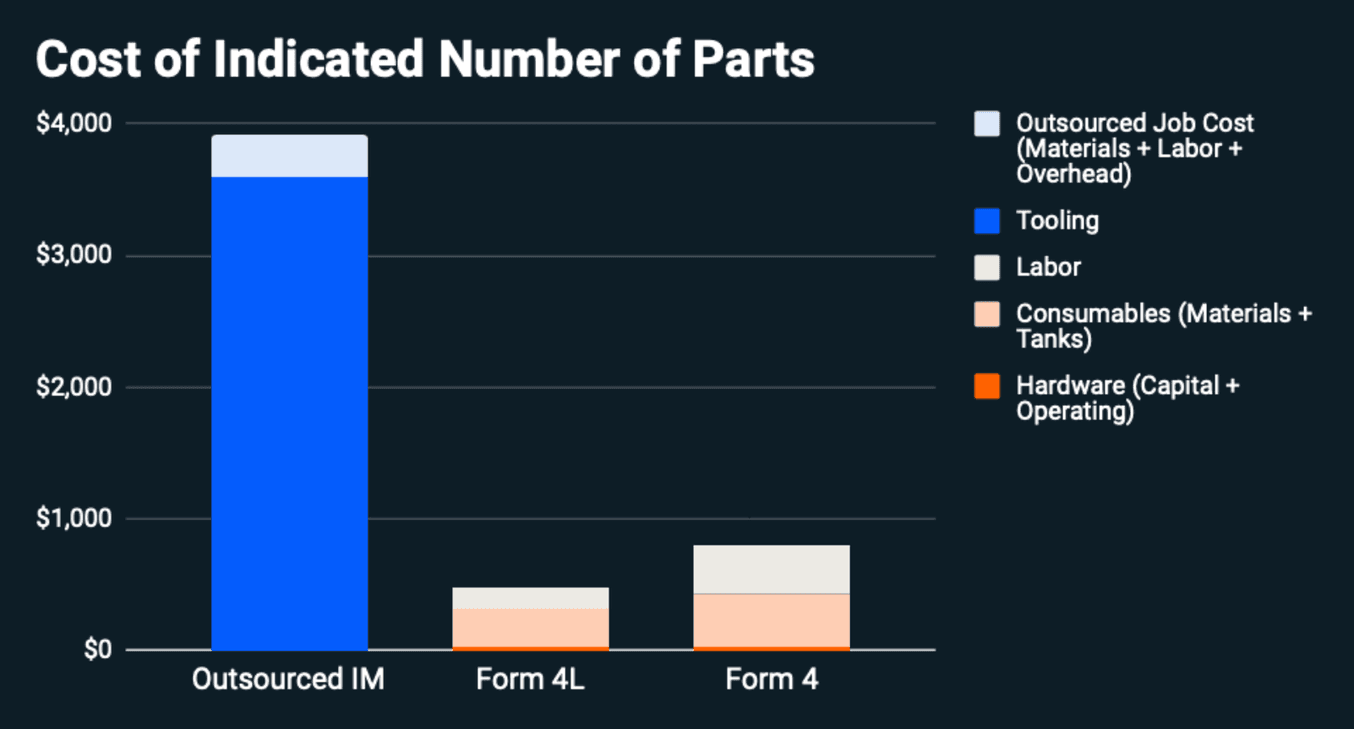
Manufacturing 1,000 parts with outsourced injection molding costs $3,920, while in-house 3D printing with Form 4L is only $600.
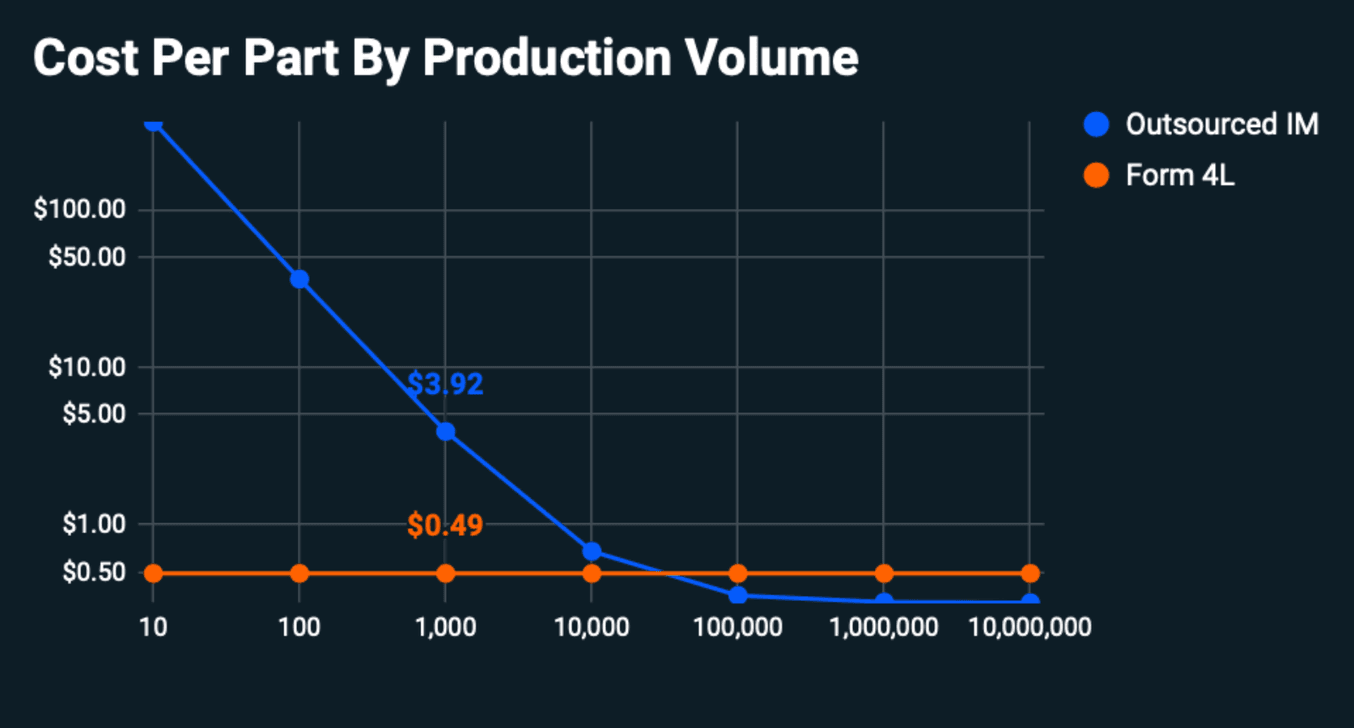
Cost per part as a function of unit volume. 3D printing is the more cost-effective solution for up to 13,050 parts. Discounted bulk resin purchases could drive down cost per part for 3D printing even further, putting the break-even point at over 40,000 parts depending on the amount of resin purchased.
Injection molding cost per part varies significantly with production volume due to the substantial upfront financial investment in tooling. The injection molding tool used to mold the mixer latch cost $3,600. In addition, the contract manufacturer charges 32 cents per part for materials, labor, and overhead.
On the other hand, 3D printing requires no tooling, so the cost per part varies less with production volume and consists of hardware, consumables, and labor.
For this comparison, we amortized the costs of the entire setup over three years, including both the capital investment in the printer purchase and the operating costs, including space, power, maintenance, and solvents for washing parts. At high volumes, the contribution of hardware costs to the cost per part is almost negligible.
When it comes to material costs, the Form 4 Resin Mixer Latch uses 6 mL of Formlabs Black Resin, which is now $65 per liter when purchased in a five-liter container, meaning the material cost per part is 40 cents. As a vertically integrated manufacturer, Formlabs offers substantial volume discounts as low as $35 per liter for resins, so for large production runs, the cost per part could be up to 50% less. Contact sales to learn more about bulk resin pricing and get a custom cost per part breakdown for your specific application.
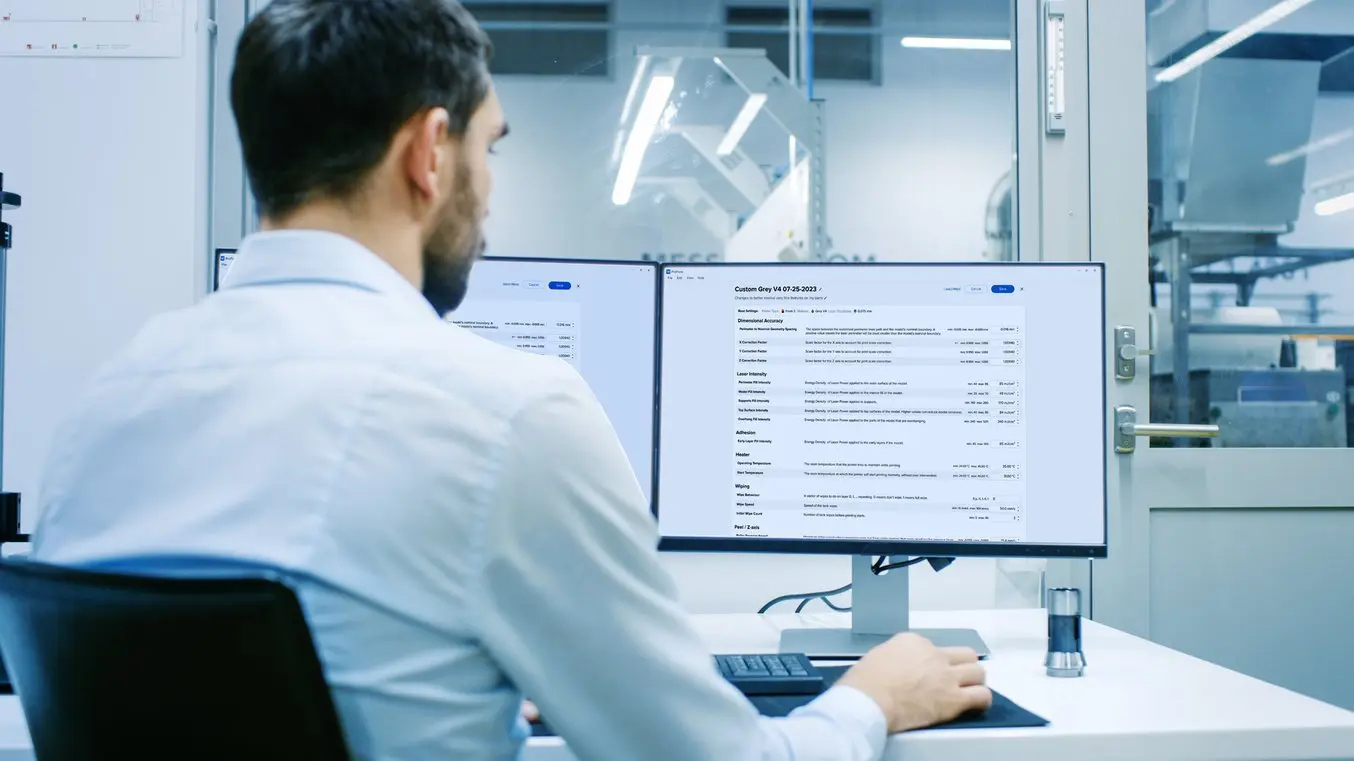
Talk to Our Sales Team
Whether you need to prototype at speed, or are producing end-use parts, we’re here to help. The Formlabs Sales team is composed of dedicated specialists who know exactly how to support you and your company's needs.
With Form 4, the biggest cost factor is labor. Form 4’s smaller build area can fit half the parts per print job than Form 4L, which means more than twice the number of print jobs are needed to reach the target number of parts. As a result, operators would spend more than twice the amount of time preparing and post-processing parts printed with Form 4 than with Form 4L, and hourly labor costs are correspondingly higher. We assumed a $30 hourly labor cost in our model; this is adjustable in the cost per part calculator.
Total Cost at Indicated # Parts
Cost Category | Outsourced IM | Form 4L | Form 4 |
---|---|---|---|
Hardware (Capital + Operating) | $0 | $29 | $22 |
Consumables (Materials + Tanks) | $0 | $408 | $409 |
Labor | $0 | $163 | $370 |
Tooling | $3,600 | $0 | $0 |
Outsourced Job Cost (Materials + Labor + Overhead) | $320 | $0 | $0 |
There are many ways to calculate cost per part — this breakdown is just one. For example, we omitted shipping and tariffs from our calculations, as this cost is site-specific. In the case of injection molding, this would probably be an additional $500-1,000, whereas 3D printing in-house incurs no shipping costs.
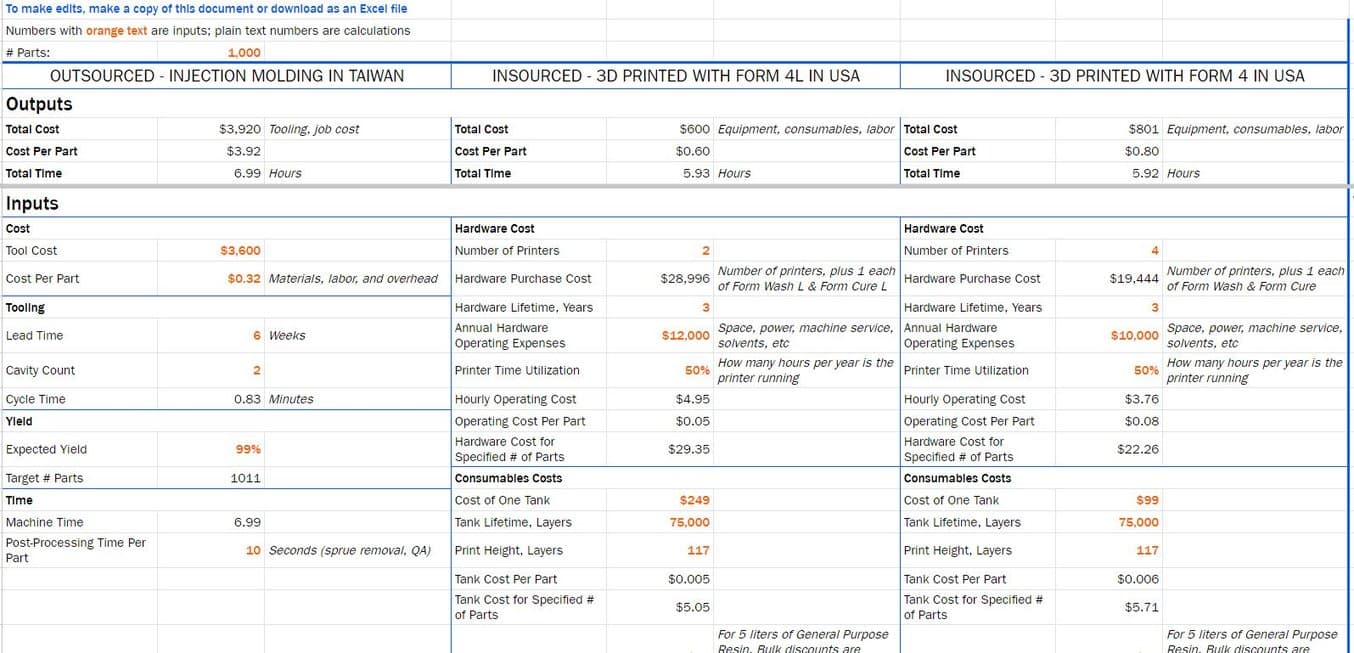
Skeptical? See For Yourself
We’ve published a cost per part calculator for this use case. Dive into the numbers to see for yourself.
Material Selection and Mechanical Properties: Fit for End-Use Application
Viewers of the April 2024 video questioned whether the 3D printed parts would hold up to serious use. Historically, SLA resins have been so brittle as to be unsuitable for end-use parts, but the new generation of General Purpose Resins from Formlabs have comparable strength and stiffness to PET. We selected Black Resin V5 for this test as its strength and stiffness meet the requirements for part usage. Additionally, the smooth matte black color meets the aesthetic preferences for this part.
Black Resin V5 | PET | |
---|---|---|
Ultimate Tensile Strength | 54 MPa | 58 MPa |
Tensile Modulus | 2500 MPa | 2400 MPa |
Flexural Strength | 91 MPa | 84 MPa |
Flexural Modulus | 2450 MPa | 2500 MPa |
The latch design requires a balance of stiffness and compliance: it must be stiff enough to act as a lever, and compliant enough to click in and out of place. The mechanical properties of Black Resin V5 meets the physical requirements of normal use for this part. To see additional properties of this material, download the technical data sheet for Black Resin V5.
A cycle tester was built to latch and unlatch the part several hundred times. The 3D print part was still in working order at the end of the test.
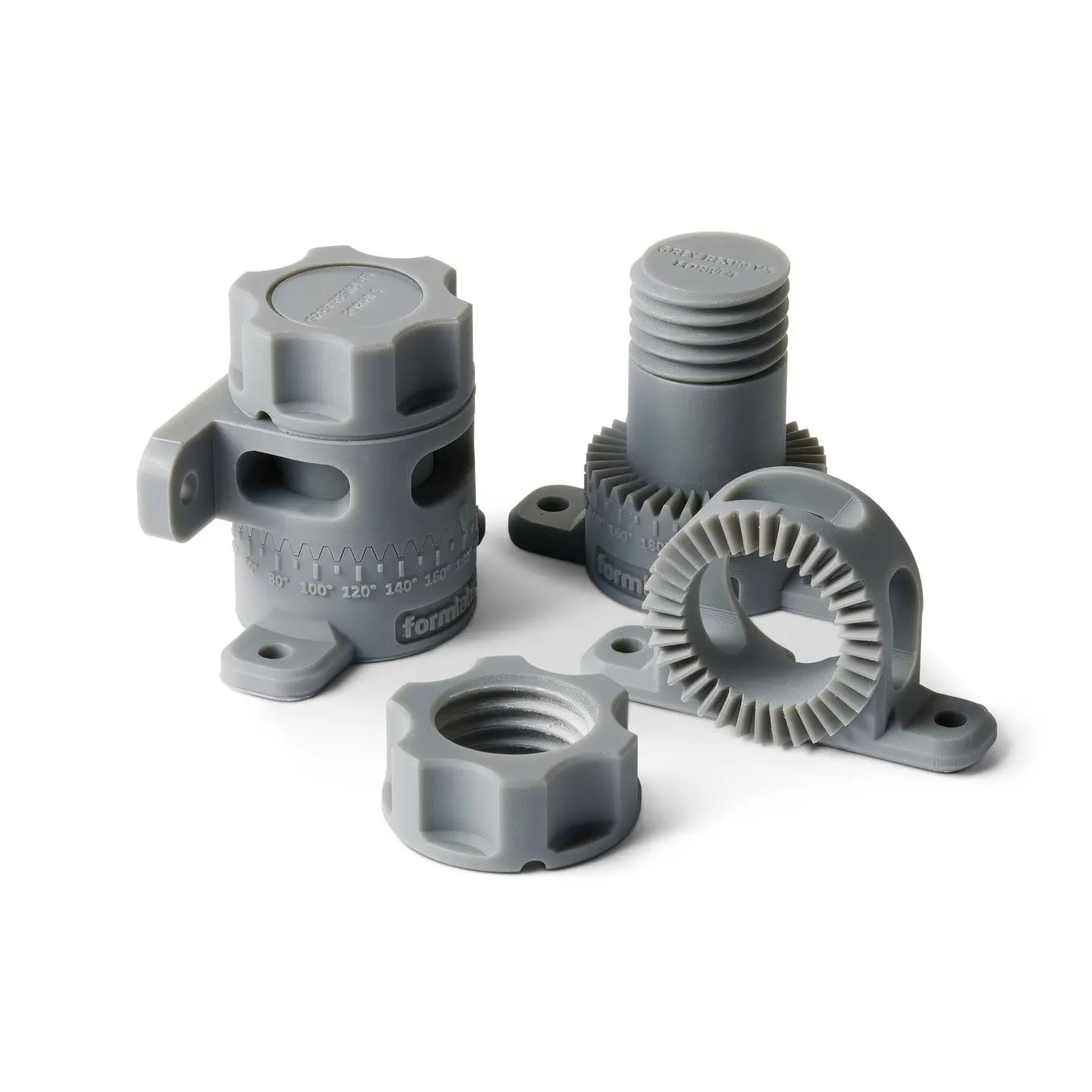
Request a Free Sample Part
See and feel Formlabs quality firsthand. We’ll ship a free 3D printed sample part to your office.
The Winner: 3D Printing With Form 4L
Whether you’re including lead time or not, 3D printing wins the race to 1,000 parts against injection molding, either by one hour, or by six weeks. 3D printing is also 85% less expensive for 1,000 parts and is the more cost-efficient solution for up to 13,050 parts. Lastly, Black Resin V5 offers the mechanical properties required to be suitable for our end-use application.
We’re not saying that 3D printing will win at all times — the equation is dependent on your design, application, and many other factors. But once considered too slow, costly, and low performance for end use parts, 3D printing is now a viable manufacturing option for a wide range of applications.
We know skeptical readers will still have questions. Use our interactive cost calculator to explore the time, cost, and quantity trade-offs of 3D printing vs. injection molding for yourself, or talk to a 3D printing expert to learn how 3D printing can meet your manufacturing needs.