Concept to Commercialization in Four Months: How Arbutus Medical Utilized 3D Printing for Rapid Device Development
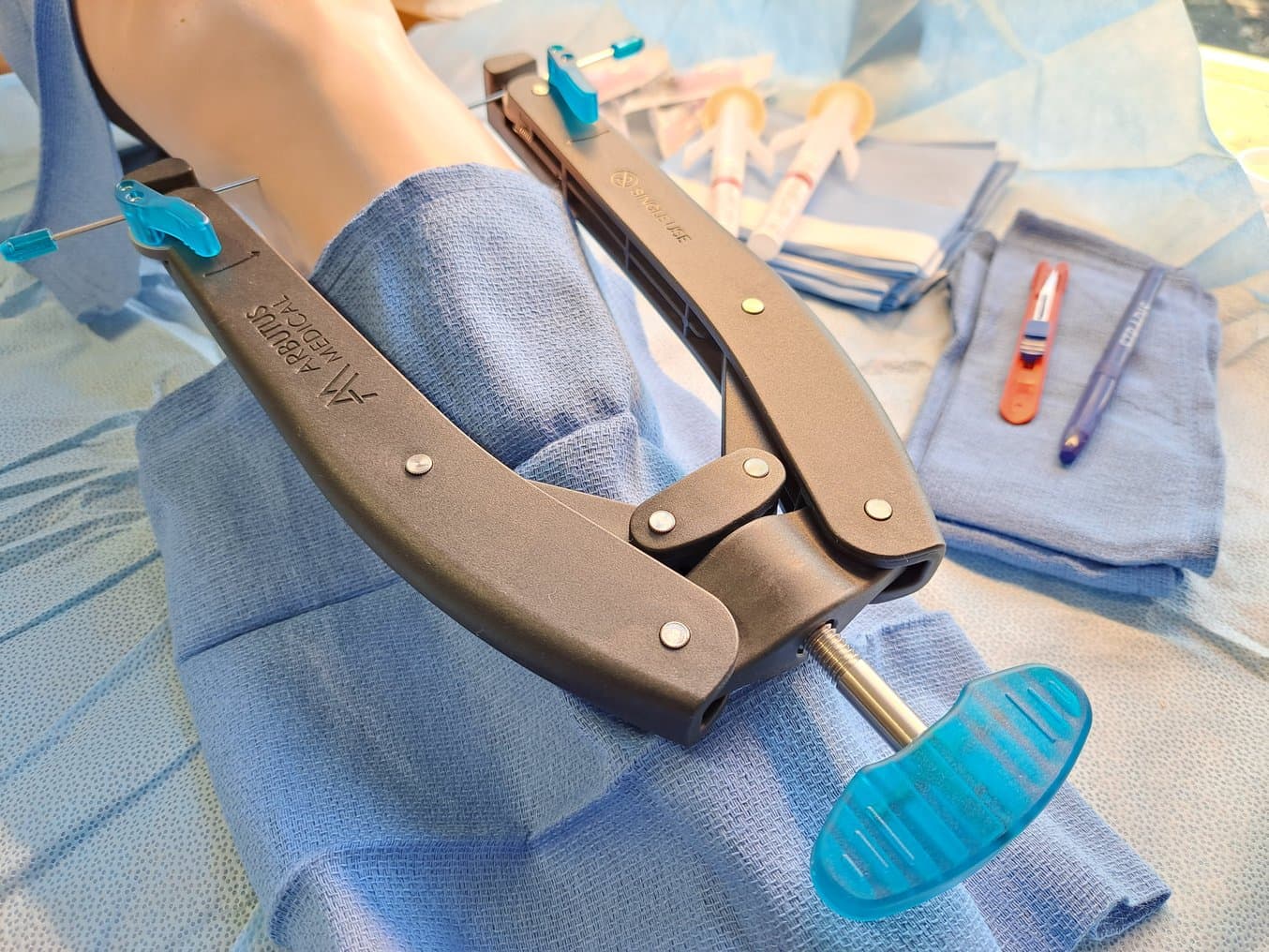
Surgeons performing minor surgeries in the emergency rooms (ERs) of trauma facilities often have limited access to the tools they need, having to track down medical devices in other areas of the hospital, causing delays in treatment times. Arbutus Medical seeks to change this, responding to the pain points of surgeons and residents by creating specialized procedure kits. These kits often require high-performance single-use instruments to help streamline specific procedures, so patients can receive treatment faster and doctors can spend their time treating instead of tracking down tools.
3D printing is key to design and production at Arbutus Medical. Radu Postole, Product Design Lead at Arbutus Medical, uses Formlabs resin 3D printers to not only prototype medical devices, but to manufacture devices for human factors testing and pilot production. For the latest device, a Kirschner Bow, Postole worked with Phil Tsao, a Formlabs ambassador and founder of Ember Prototypes, a rapid prototyping, consulting, and product design firm, to leverage 3D printing to sprint from idea to commercialization in one year, even utilizing 3D printing for stopgap production, producing over 800 parts a month.
For Arbutus Medical and Ember Prototypes, reliability and the vast material library of the Formlabs ecosystem have enabled the development and production of medical devices in record time.
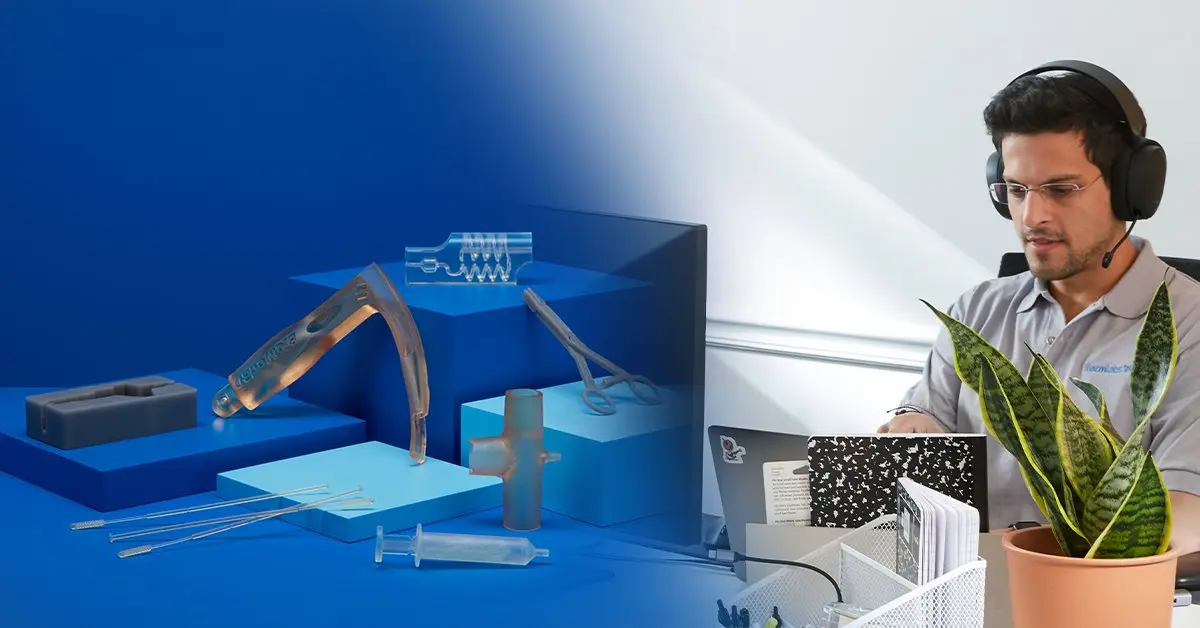
Talk to Our Medical Sales Team
Whether you need to make patient-matched surgical tools or are prototyping for a cardiac medical device, we’re here to help. Formlabs Medical team are dedicated specialists who know exactly how to support you and your company's needs.
Solving Problems in Trauma Centers With Specialized Procedure Kits
Arbutus Medical’s TrakPak® launched in 2021. The kit is used to quickly apply skeletal traction to patients who have suffered femur or pelvis fractures, to reduce and stabilize the fractures while they await surgery. The original version of the kit featured a modified Dewalt drill with a sterile cover and an implantable pin. When Postole originally designed this device, he looked for a 3D printer to increase the speed at which he could prototype. Tsao recommended Formlabs’ Form 3. Not only were elements of the TrakPak® prototyped on the 3D printer, but Tsao and Postole were able to quickly 3D print the final designs in sufficient quantities for human factor studies and cadaver testing. Since its release, over 4,000 patients in the US have been treated using TrakPak®.
Human Factors Studies With 3D Printed Devices
Human factors testing can be a lengthy process, often due to the time it takes to procure molds and start production. 3D printing meant Postole could quickly provide functional prototypes that could not only be bench and cadaver tested, but looked like the final device as well. The aesthetics were important, removing the noise so that the feedback from surgeons was purely focused on part performance and value.
“Because this is a Class II device, an implant, the threshold for product release was pretty high. So we did have to do a very detailed human factor study, and we did that fully with the 3D printed parts. Some companies might have to wait until they actually have the injection molded parts to do human factor study, but we were able to save three to four months by 3D printing.”
Radu Postole, Product Design Lead, Arbutus Medical
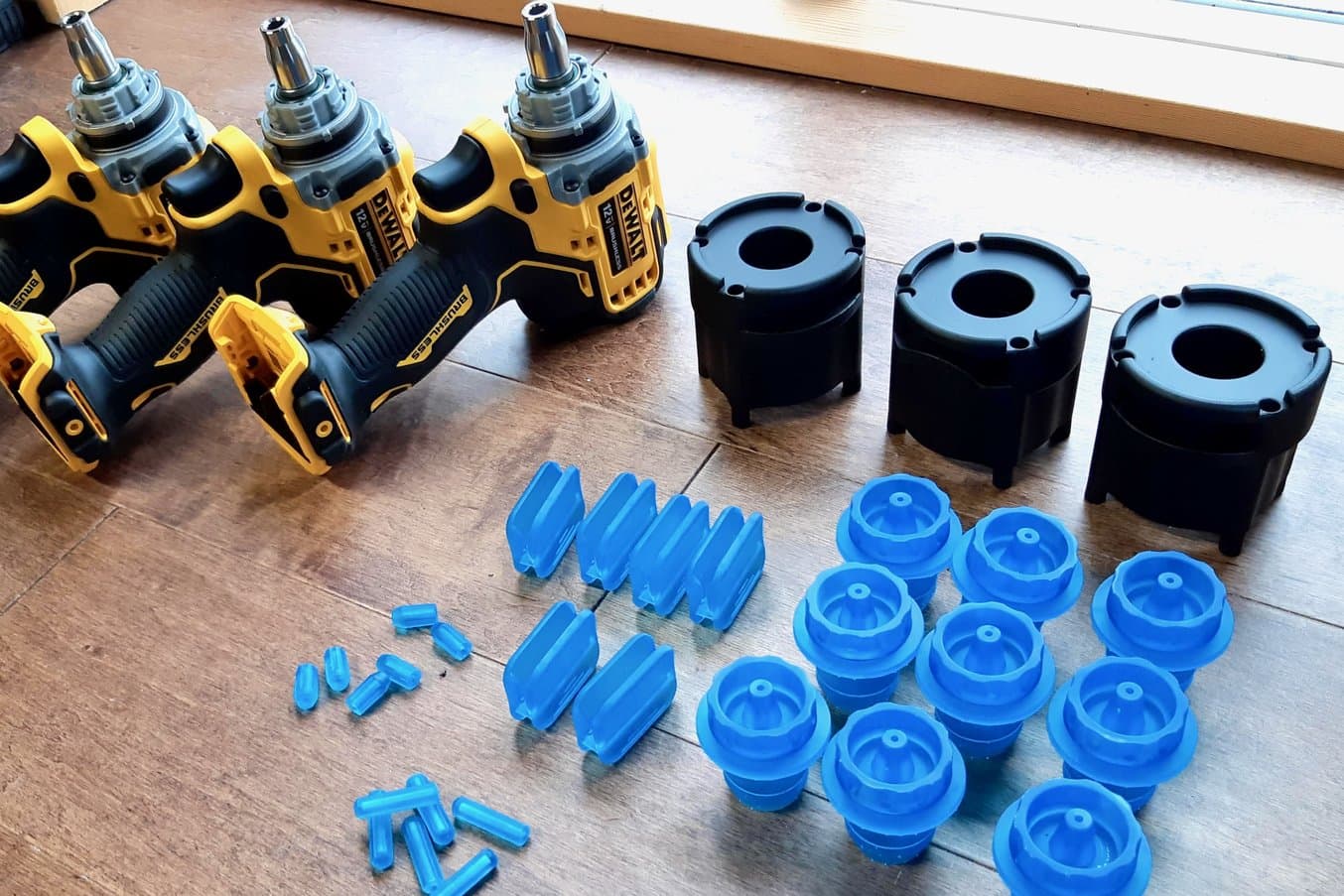
TrakPak® prototyping included 3D printing an adaptor for a power drill, as well as pin components.
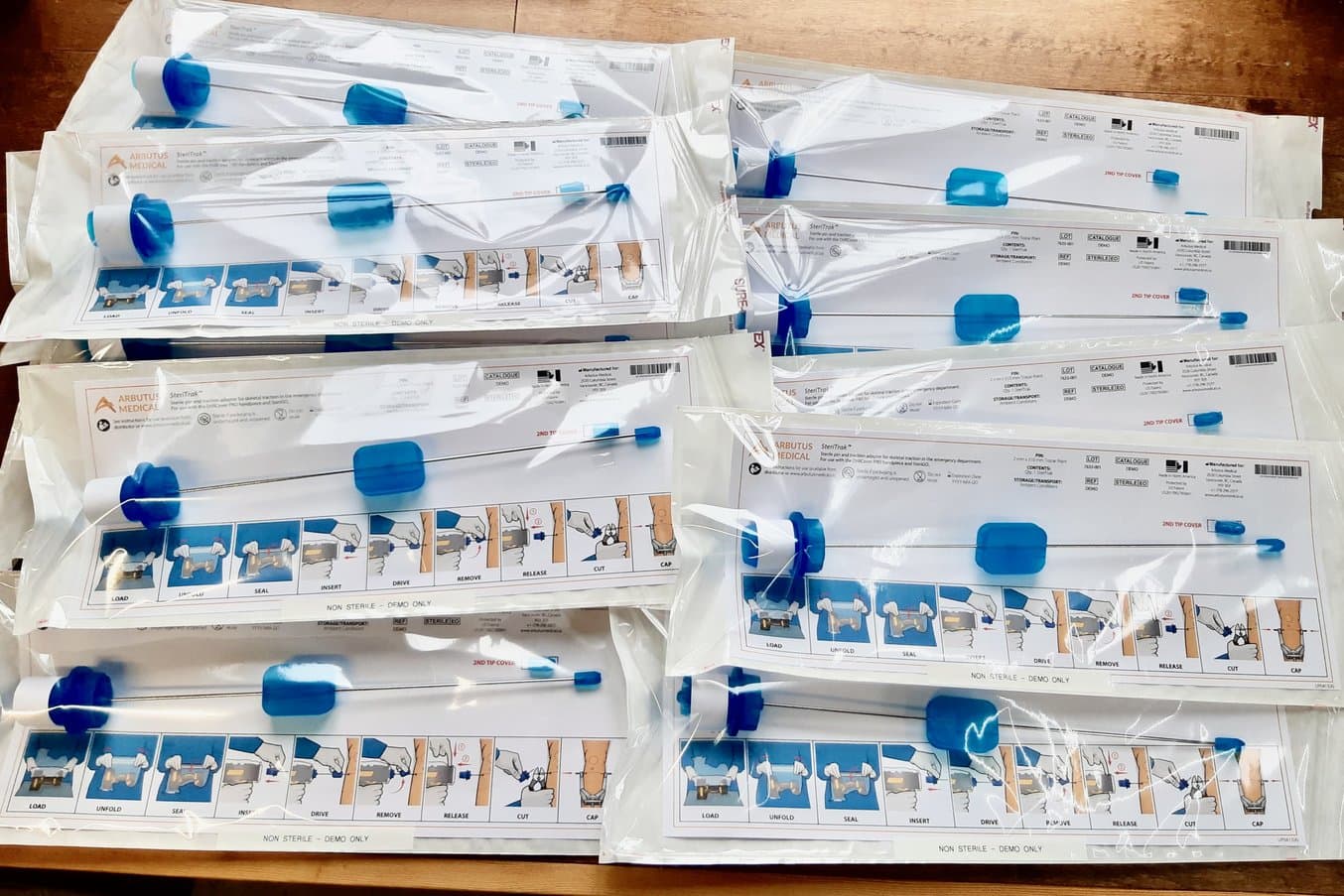
TrakPak® consists of a disposable, sterile cover for a power drill and an implantable pin. The blue components on the pin are 3D printed.
While the first version of TrakPak® solved one problem for trauma centers, working closely with surgeons and residents illuminated another issue: limited ER access to Kirschner Bow (K-bow) devices, used by orthopedic surgeons to tension the implanted pin and provide a means for applying skeletal traction. Problems include tracking them down and retrieving them, as they’re generally stored near operating rooms but applied in emergency rooms, and finding a device that actually functions, as the pin gripping teeth and tensioning mechanism often wear out. This not only leaves the patient waiting in pain while the K-bow is retrieved, but also wastes the time of emergency room doctors. Arbutus Medical’s response was the QuikBow® pin tensioner.
Launched in 2023, QuikBow® reduces reliance on Central Sterile Processing (CSP) centers in hospitals, and improves speed and quality of patient care. With the help of Form 3 printers, the printing prowess of Ember Prototypes, and the extensive Formlabs material library, the QuikBow® was designed, developed, tested, and commercialized in one year.
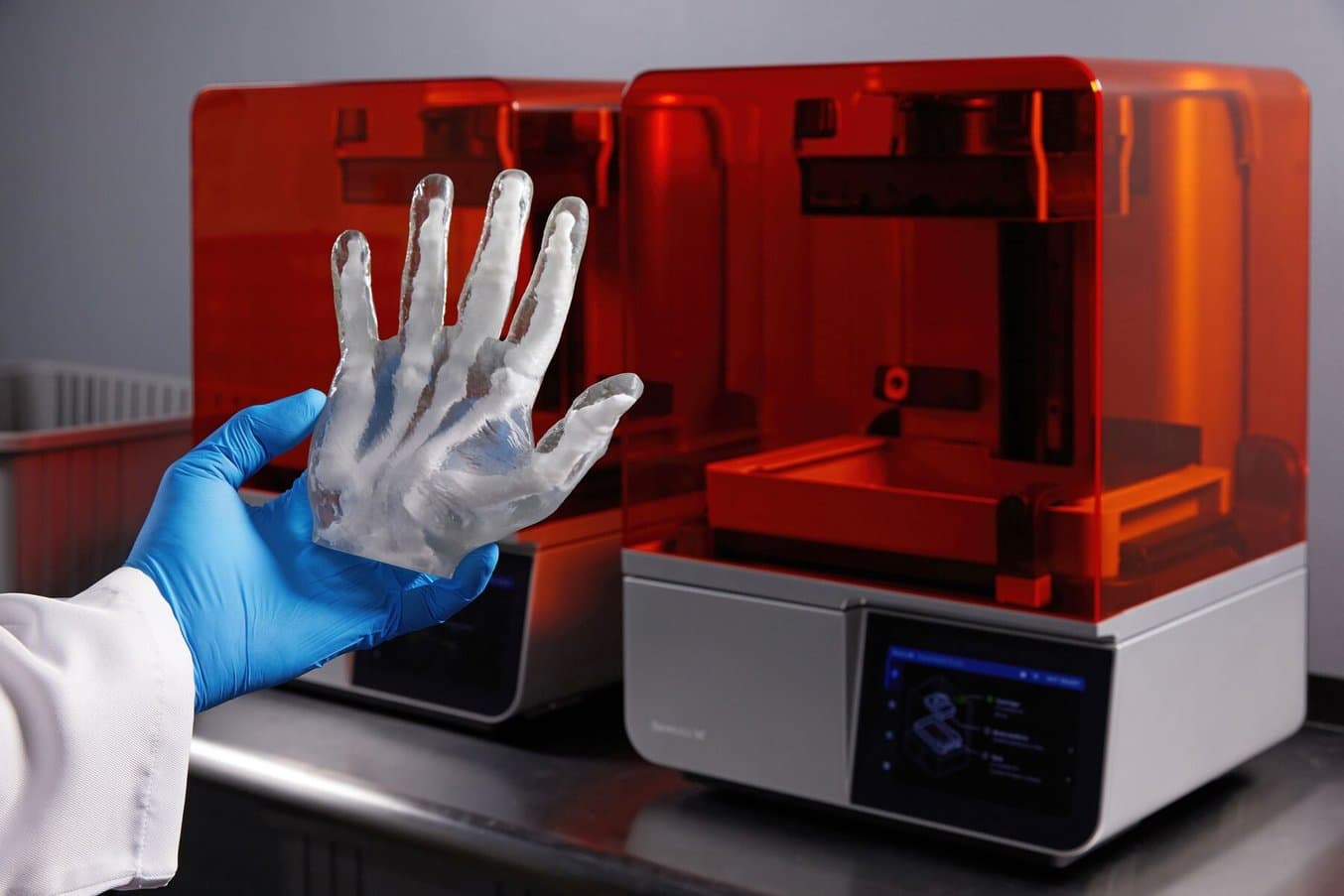
Formlabs Biocompatible Resins: A Comprehensive Guide To Choosing the Right Material
Formlabs currently offers more than 40 unique materials for stereolithography (SLA) 3D printing. This paper helps users compare and contrast our biocompatible offerings, and determine the best fit for their medical applications.
Rapid Prototyping With Form Series 3D Printers and Ember Prototypes
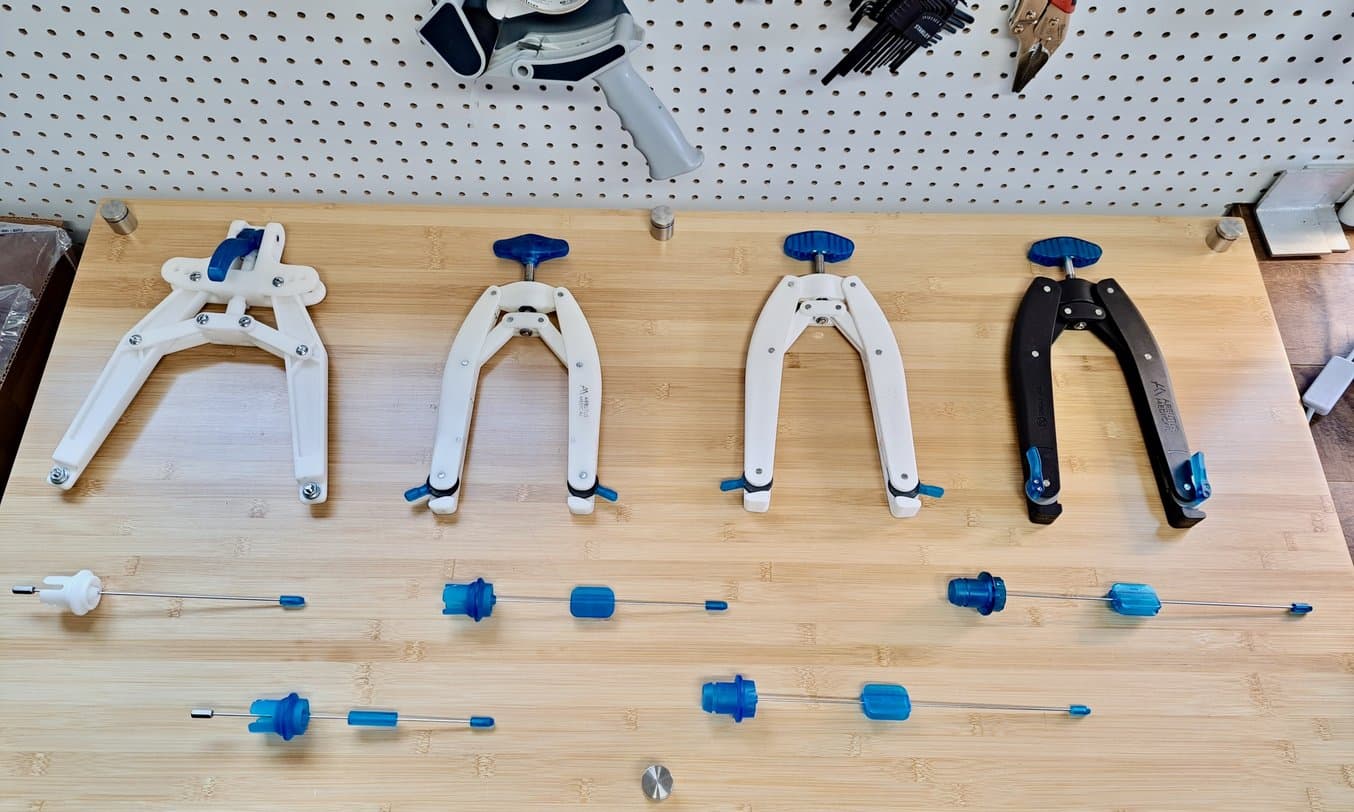
Three prototypes of the QuikBow® (white) and the final medical device (black). White and blue parts were 3D printed on Form 3 Series printers, and blue parts denote touchpoints the user will interact with.
Prototyping the QuikBow®, Postole first looked at machining for parts of the bow, including the arms. “But they're so massive and there's so much coring out, that it was actually prohibitively expensive to get the arms machined for testing, especially for the 30+ design iterations we created. 3D printing with the Formlabs 3D printer was a natural fit.”
As the design developed, Postole reached out to Tsao at Ember Prototypes, because the arms he was prototyping would only fit in Form 3L, Formlabs’ large-format SLA 3D printer. Tsao has extensive experience with 3D printing and the Formlabs material library. He worked with Postole to evaluate the best materials for the QuikBow®.
For the arms, a rigid material was required. Tsao printed the arms in multiple materials, including Tough 2000 Resin, Rigid 4000 Resin, and Rigid 10K Resin, to help Postole pinpoint the best material for his application. Ultimately, Postole selected Rigid 10K Resin as the best option available. In addition to toughness, the bow needs to tension the pin to over 100 lb and support 40 lb of traction weight. To make the prototypes stronger, Postole iteratively altered the part design to get it to withstand the rigorous testing needed.
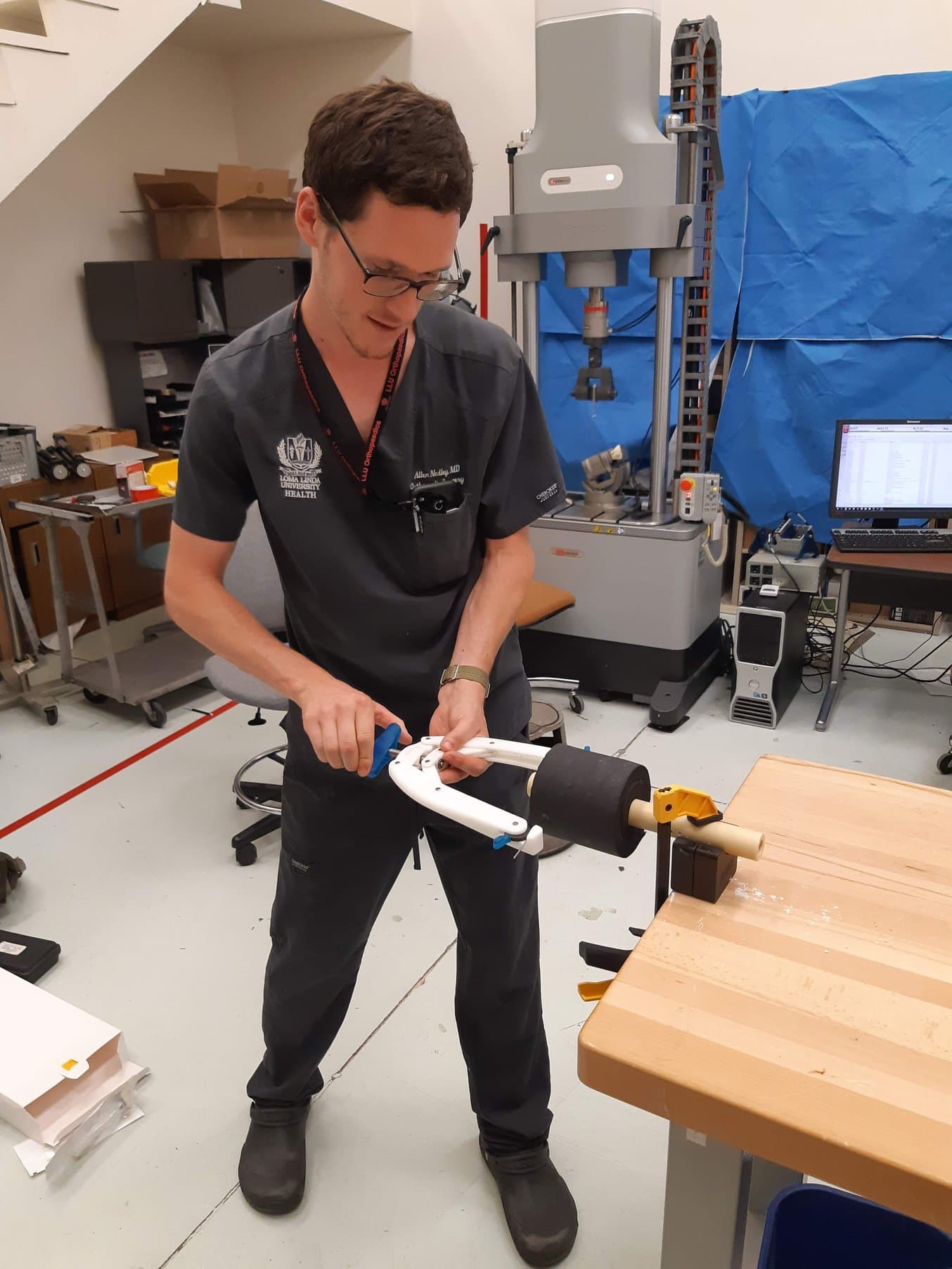
Allen Nedley, MD, Orthopedic Surgeon performing usability and strength testing on a QuikBow® prototype at Loma Linda University School of Medicine in California.
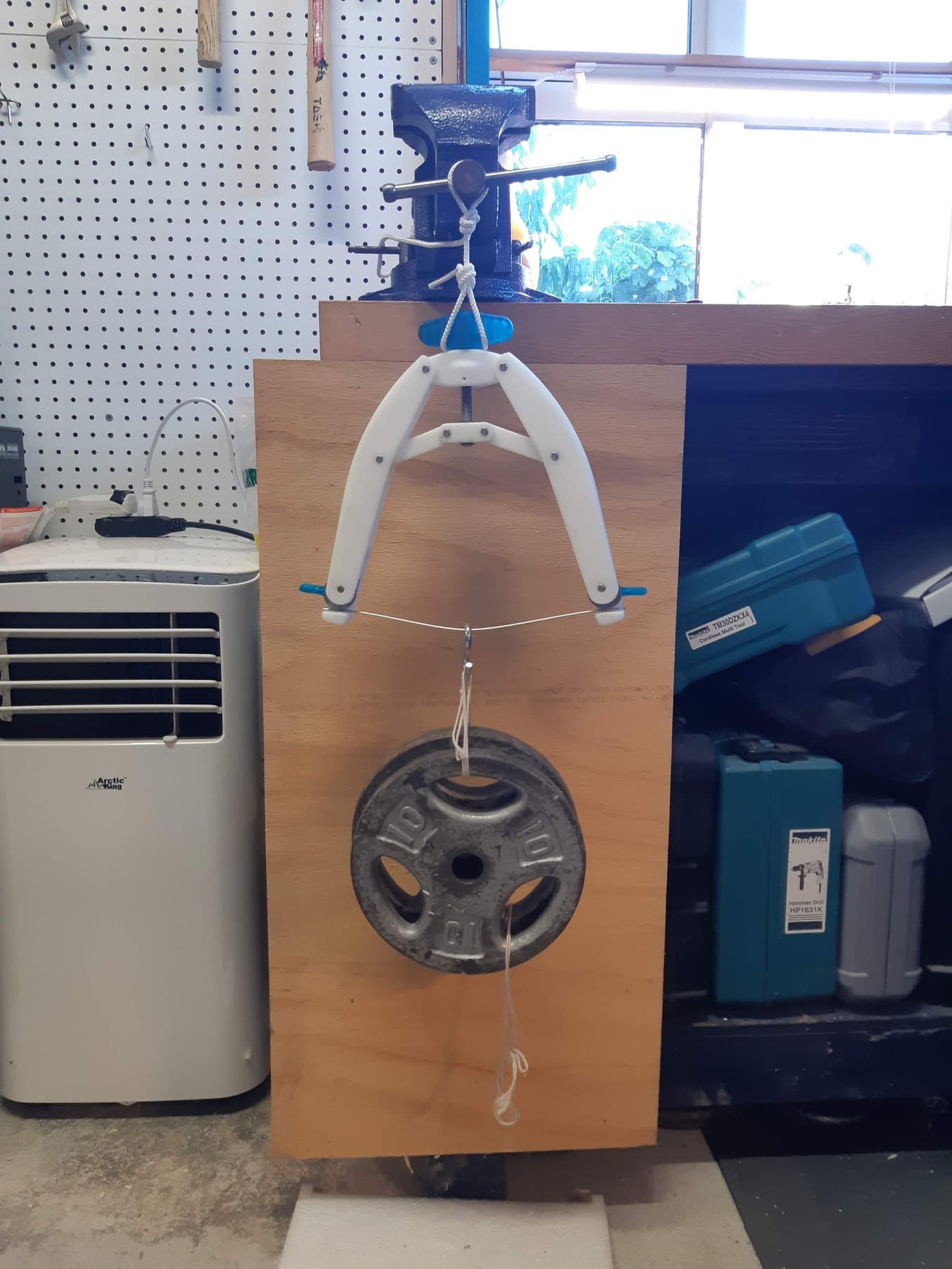
Testing the QuikBow® pin on a 3D printed prototype.
“We had very unique requirements for strength, stiffness, and aesthetics, and we were able to achieve that. Surgeons quickly realized the value and performance of the device, even though they were 3D printed prototypes.”
Radu Postole, Product Design Lead, Arbutus Medical
While the aesthetic quality of materials was a factor in selecting materials, Tsao manually placed supports and oriented files to ensure minimal post-processing was needed, so that resulting prints were as clean as possible, with a consistent surface finish.
Postole says, “Phil has done an awesome job of trying to understand the end use of the parts because that's really dictated how he sets them up in PreForm. Which are the aesthetic faces and what are the critical features?” As these prototypes were being sent out for user demos and feedback, they had to look like finished parts. By placing supports in internal areas, Tsao was able to deliver parts that were indistinguishable from injection-molded ones. In addition to specialized setup in PreForm, Tsao developed and 3D printed a jig to hold the parts when washing so they would have a uniform, aesthetically pleasing finish.
“The resolution and the surface finish with the Formlabs printer is so good that most people could not tell that it was 3D printed.”
Radu Postole, Product Design Lead, Arbutus Medical
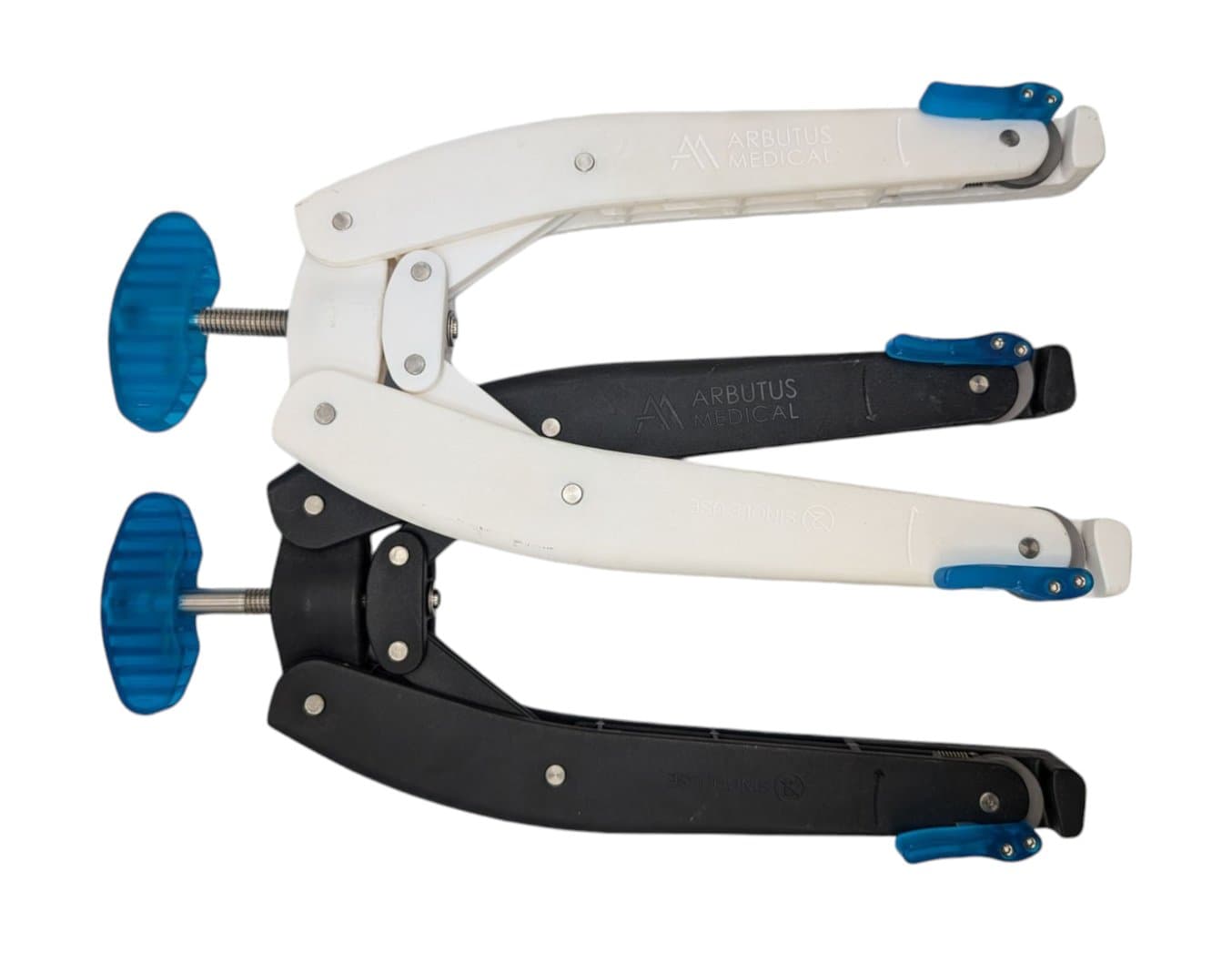
Prototype 3D printed in Rigid 10K Resin (top) and injection molded T1 (bottom). Ultimately, Arbutus Medical chose a black color for the final medical devices as it doesn’t show blood stains as easily as white does.
“I still have the Rigid 10K prototype and the injection molded T1. Every time somebody comes to my shop, I show them as an example of what we can do. People are always blown away by how good the Rigid 10K assembly looks. They can't tell the difference between that and the injection mold, other than the color.”
Phil Tsao, Founder of Ember Prototypes
During this stage of prototyping, Tsao says, “We basically iterated almost weekly. Every three or four days, Radu would send a new iteration and we'd print it and then send it over to him. It was having a rapid prototyping arm that was not part of your own company, it's just external.”
A benefit of collaborating with Ember Prototypes was time. With Tsao printing the arms, Postole’s Form 3 was freed up to print other components in-house, enabling him to continue iterating rapidly. All in all, Postole and Tsao did over 30 rounds of prototypes in four months, including some back-to-back, everyday iterations that were shipped to surgeons for feedback the following day.
Part of this process involved analyzing user responses on usability, performance, and perception of value, a key reason the 3D printed prototypes needed to look like finished, injection-molded devices.
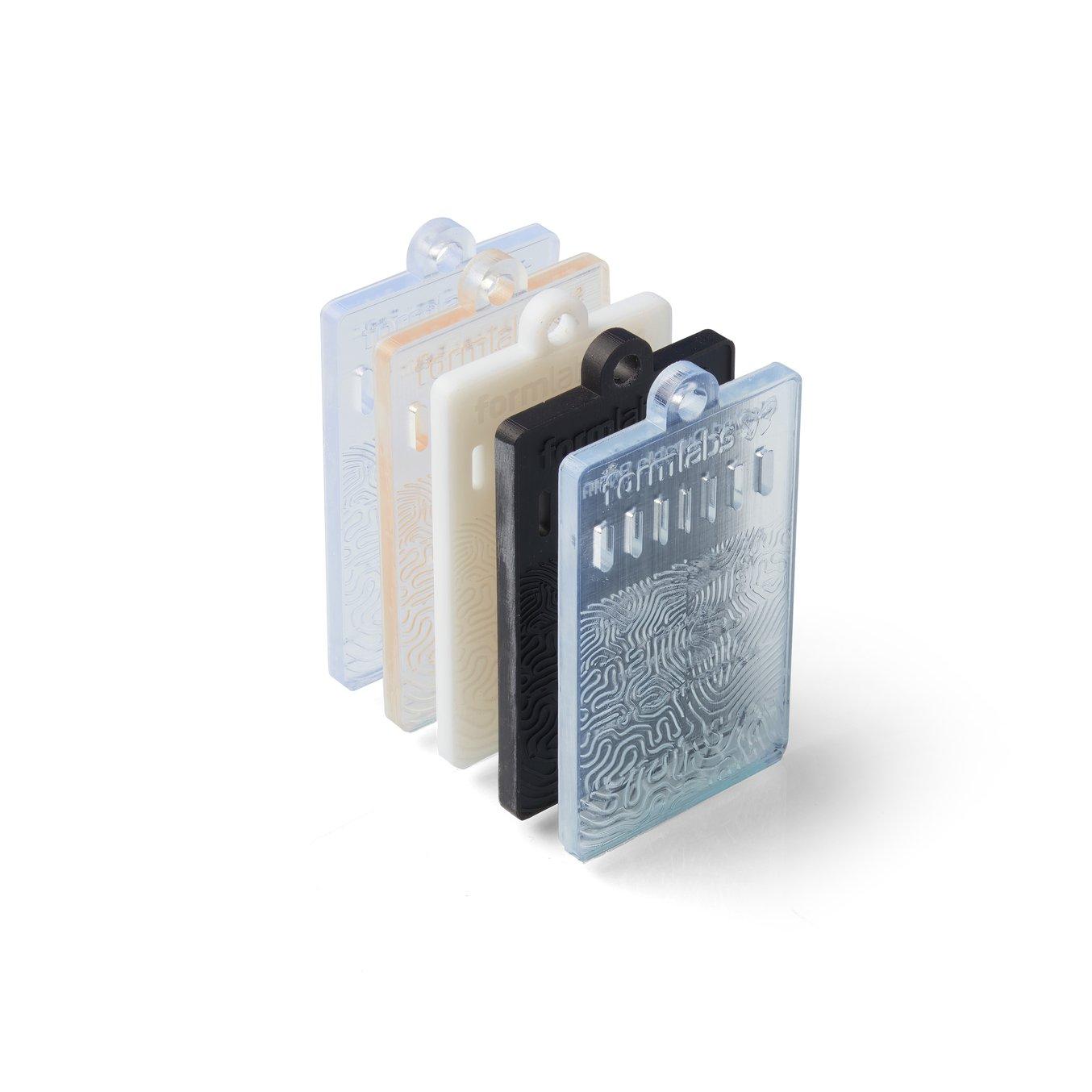
BioMed Resin Swatches
Each BioMed Resin swatch features embossed and debossed designs, 0.5-2.0 mm cutout thicknesses, as well as regulatory information unique to that resin.
Refining Commercialized Medical Devices
QuikBow® was launched in early 2023. Within a few months, Arbutus Medical received feedback that emergency room workers found the QuikBow® was making patient care faster and better. However, it still required the use of a bed frame to pull traction in an upward direction, lifting the device off the patient’s shin.
Bed frames are clunky apparatuses that require special setup, storage, and tracking, wasting time and resources in hospitals. To solve this pain point, Radu and the design team at Arbutus had a brainwave: they could design some adapters for the QuikBow® with lateral hinge points that lift up the bow so that it clears the patient’s shin. “With this innovation, we basically eliminated the need for conventional bed frames and pulley systems that can take up to two hours to procure throughout the hospital,” says Postole.
The addition of the hinge points came a full three months after the commercialization of QuikBow®. “We rapidly 3D printed different iterations of this attachment, and sent them to our trusted surgeons. They loved it so much they wanted it right away,” says Postole, “That's where Form 3B came in. We knew that if we picked the right material, we could get this new product feature into the hands of surgeons right away.”
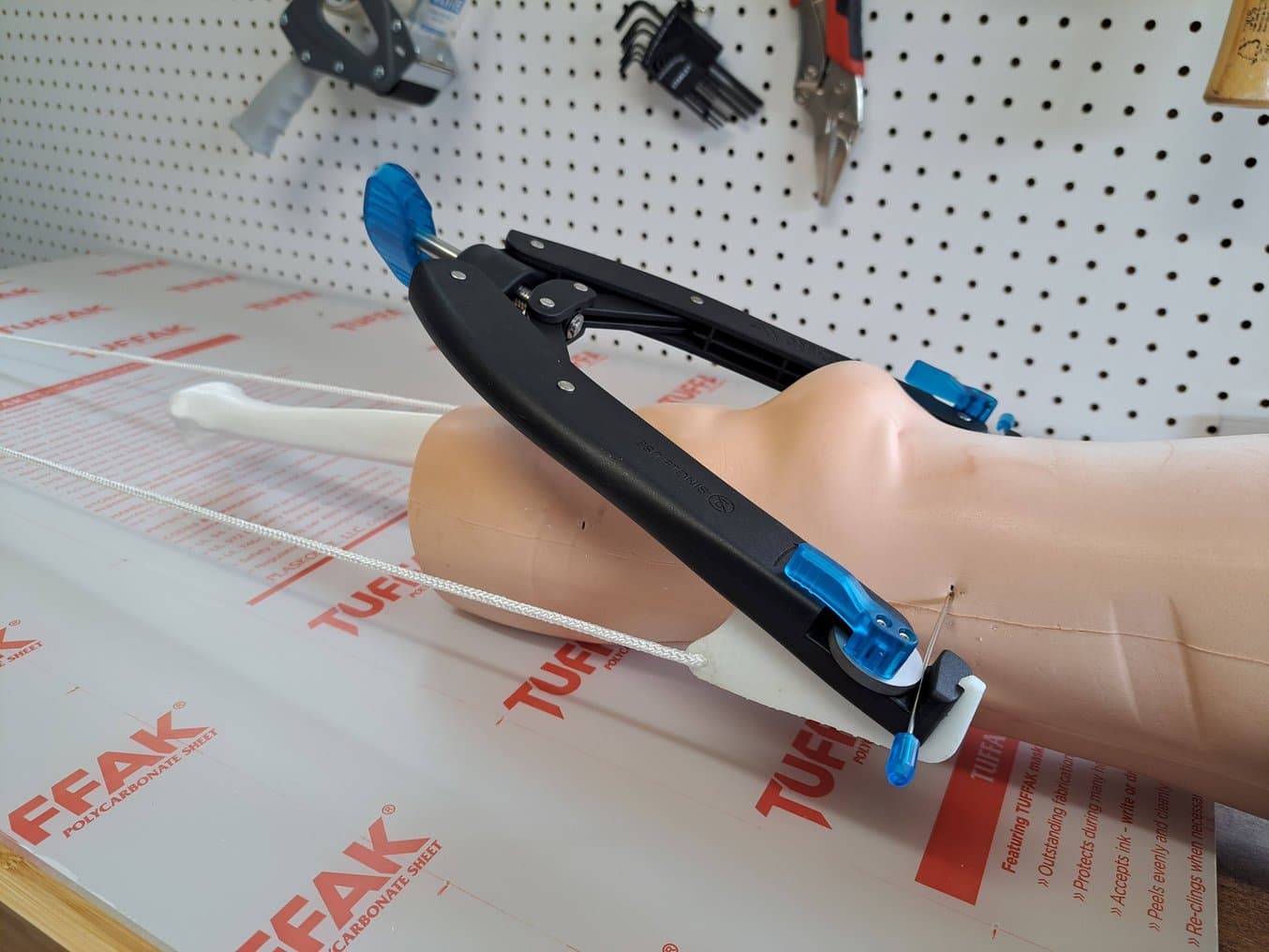
An early prototype of the hinge points for the QuikBow®. By placing tension on the hinges, the bow is lifted clear of the shin, reducing risk of pressure ulcers.
For biocompatible parts, Postole wanted a clear resin option to match the other translucent parts in the assembly, and honed in on BioMed Clear Resin and BioMed Durable Resin, ultimately selecting BioMed Durable Resin for its superior impact resistance, noting, “both materials were very strong for our application. Although BioMed Clear passed our initial impact testing BioMed Durable gave us more safety margin for repeated impacts”
Within a couple of months, Arbutus Medical was producing the first clinical units that had been cleared through their quality system.
“We did all the testing, all the verification, with 3D printed parts. It was basically a four-month project from idea to sellable part.”
Radu Postole, Product Design Lead, Arbutus Medical
For most conventional devices, it takes over three months to get molds made and start molding parts. With all the hoops a medical device has to clear to be used in a hospital, Arbutus Medical wanted to be able to implement the improvement immediately, without waiting for molds. This meant another production method was necessary.
3D Printing for Stopgap Production With Ember Prototypes
Wanting continual feedback on the new bow hinge points while continuing to provide the QuikBow® to surgeons, Postole didn’t want to commit to molds for the bow hinge points, because molds cost $25,000 and cannot be easily changed once they are produced. Postole says, “That's where Form 3B came into use because it was a stopgap for us — we just kept 3D printing them. Eventually, the demand went so high that we couldn't keep up in-house, and that's where Ember stepped in and basically took over all the 3D printing.”
3D printing enables not just rapid production, but production using the same workflows used during prototyping, for increased efficiency. Plus, by adding print batches or printers, production can easily be scaled as demand increases.
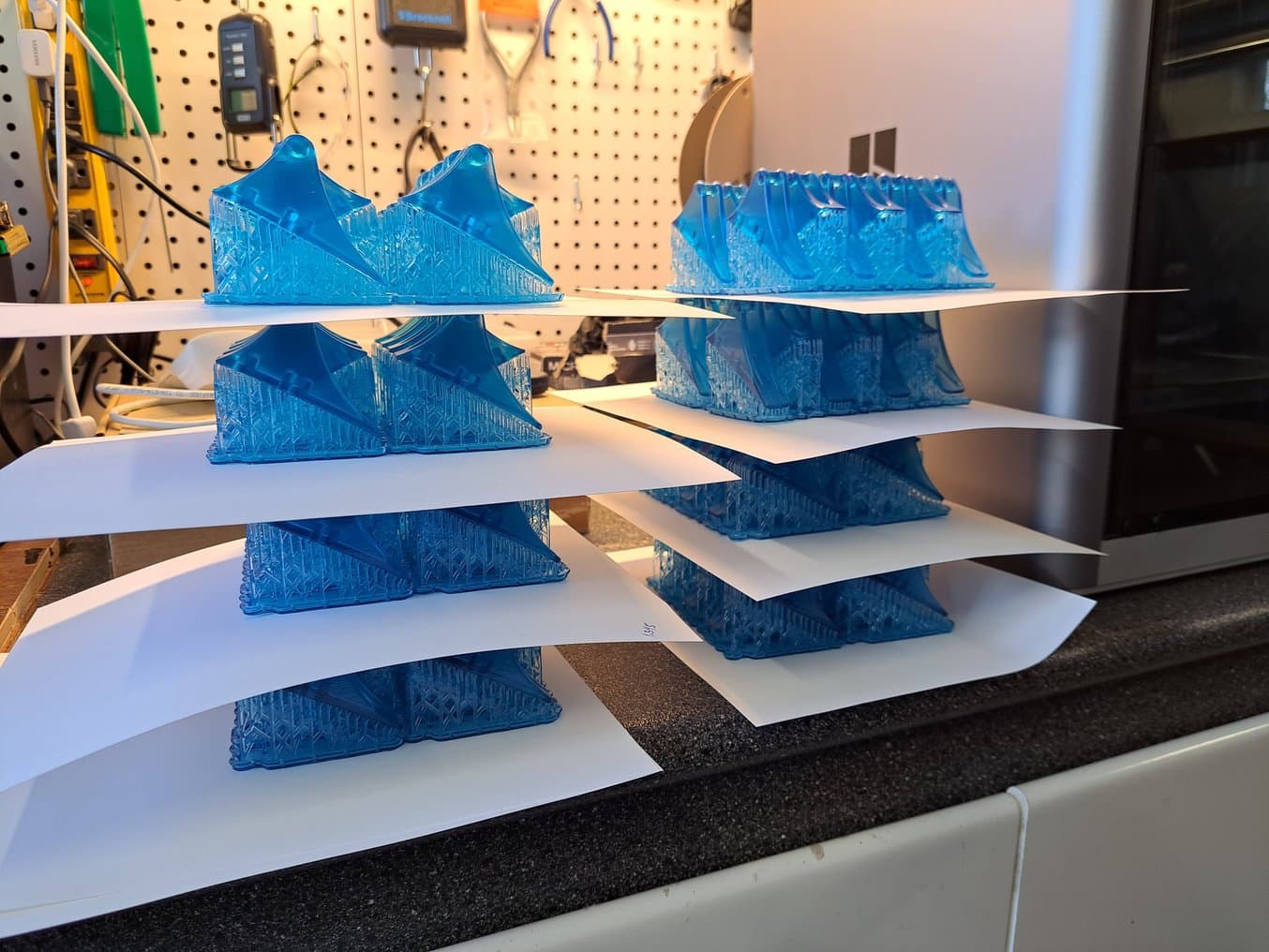
Stopgap production runs of the QuikBow® hinge were printed on Form 3B.
As demand increased, Arbutus Medical outsourced 3D print production of the hinges to Ember Prototypes, where Tsao would print two batches of parts per day. This stopgap production meant that Arbutus Medical could help improve patient care and start generating revenue from the new product five to six months earlier, while lowering the risk by not having to invest in expensive molds before receiving more clinical feedback.
At first, Arbutus Medical thought they would need 200-500 parts total, but very quickly Tsao was printing about 200 parts a week (14 parts per build, two builds a day), and delivering around 800 parts a month. 3D printing at this level of production involved special considerations, including washing and packing the parts. Tsao designed and 3D printed a custom jig to hold the parts when washing, to ensure the best aesthetic finish. When packing parts, he found that paper or other materials could leave fibers on parts, but bagging them in plastic bags kept them clean. These workflow additions enabled Tsao to deliver parts with the look and feel of injection molded parts, without the costly overhead and while still enabling design refinement.
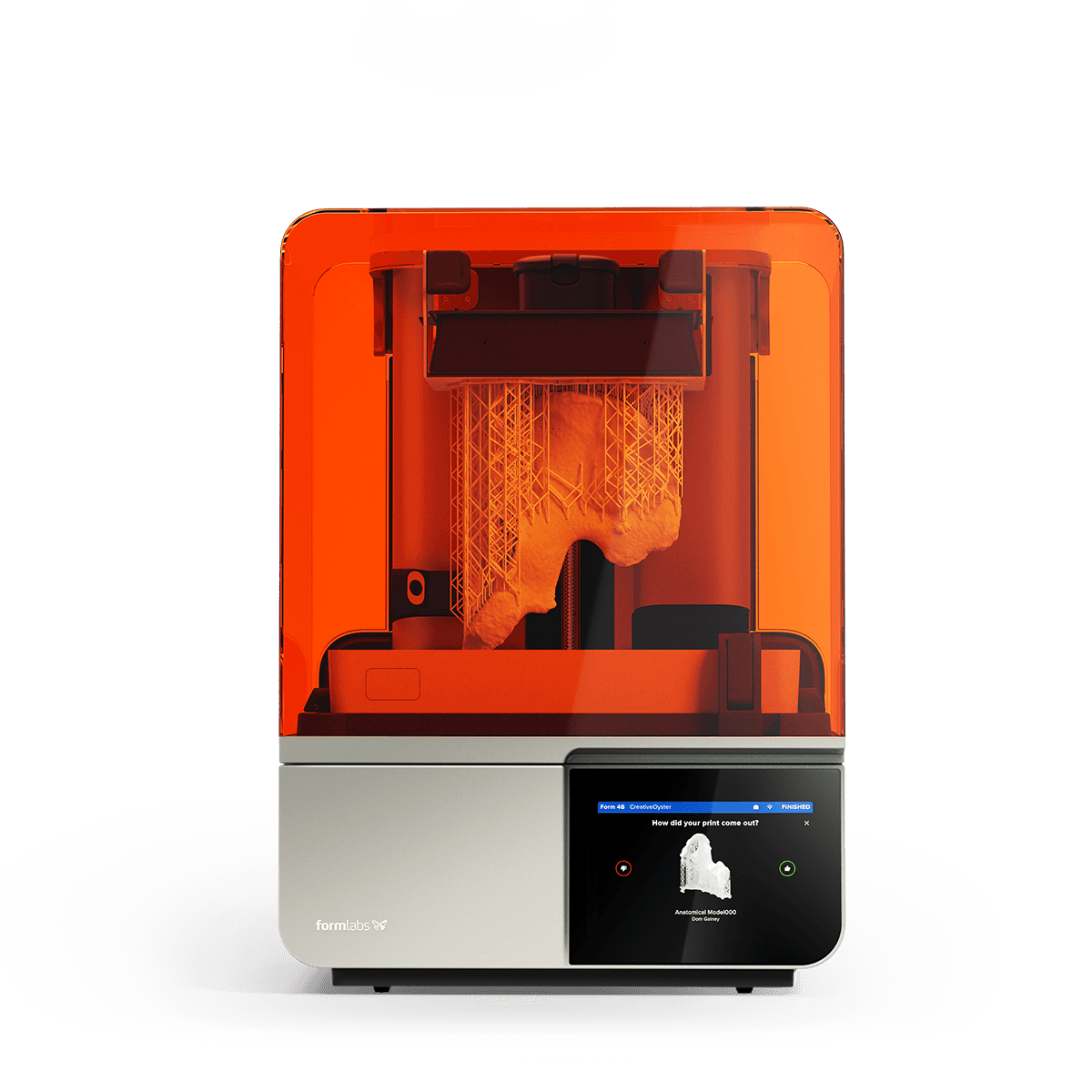
Introducing Form 4B: Faster Production, Higher Precision, Regulatory Equivalence
The Formlabs Healthcare team showcases our newest product, Form 4B. Along with a technical overview, Bradley Heil, Quality and Regulatory Lead at Formlabs, will discuss the regulatory aspects of producing medical devices with the help of Formlabs 3D printers.
The Workhorses Behind Prototyping and Production: Form Series 3D Printers

Form Wash, Form 3B, and Form 3L at Ember Prototypes. Tsao uses Form 3B for biocompatible part production, and Form 3L for large-format printing.
Tsao has been using Formlabs resin printers since the release of Form 2. Since then, he’s used Form 3, Form 3B for biocompatible printing, and Form 3L for large-format printing.
“The main driver for me is ease of use out of the box, and then material selection. Not only do I work with people like Radu, but I work with a lot of other engineering and tech startups and companies and everybody has vastly different requirements. Some people need low-friction parts. Some people only care about aesthetics. Some people need super high stiffness like Radu and Arbutus did. Being able to have this vast library of materials and know exactly what the mechanical properties are and how repeatable they are is really important for Ember.”
Phil Tsao, Founder of Ember Prototypes
Up until 2019, Postole had been using FDM printers. “We couldn't get the performance out of FDM printing. The parts weren't solid. We were having nozzles getting clogged constantly. It was just very hands-on and wasting a lot of our time,” said Postole. He asked Tsao for a 3D printer recommendation and, “As soon as he recommended the Form 3 and we got it, we were just blown away by solid parts and being able to just do repeated prints without any issues.”
Ultimately, Postole says, “being able to 3D print clinical use devices, enabled us to A, get to market fast, and B, quickly validate the value and product market fit.”
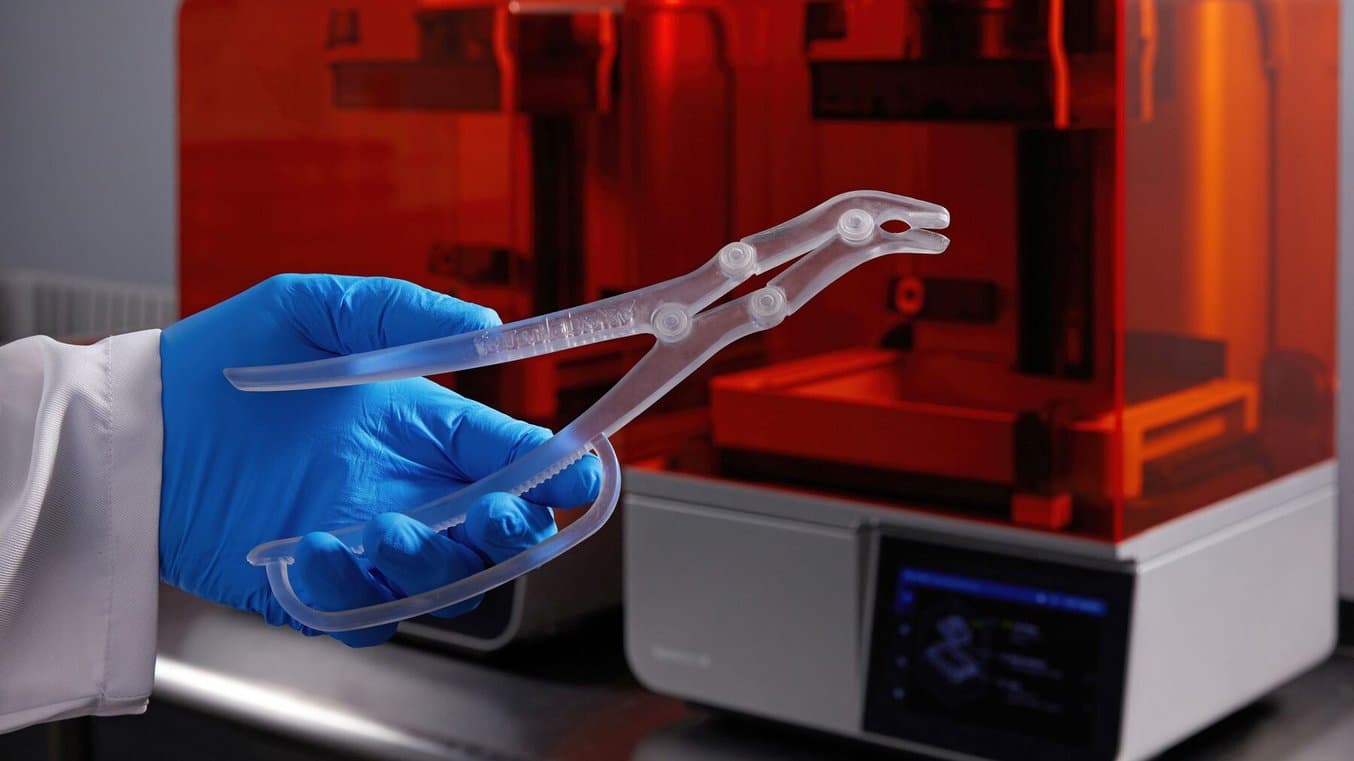
From Prototyping to Production: How In-House 3D Printing Enhances Medical Device Development
Medical devices tend to have longer development cycles than consumer goods, due in part to clinical testing, quality, and regulatory requirements. Reducing the number of prototyping cycles or even directly 3D printing end-use devices can have a significant impact on speed to market.
What the Future Holds
Initially, Postole thought Arbutus Medical would 3D print the adaptive hinge points for QuikBow® indefinitely. However, when he realized they were on track to produce on the order of 10,000 per year, Arbutus Medical did a cost analysis and opted to move to injection molding once surgeons confirmed the design did not need to change. For the next device Radu is developing, he’s considering 3D printing for production, weighing material properties, options, and costs.
“As the properties of materials get better, as the costs come down and the speed of printing goes up, I definitely see how we would, for a lot more devices, just 3D print longer, until we need 10,000 a year.”
Radu Postole, Product Design Lead, Arbutus Medical
For Arbutus Medical, 3D printing and injection molding are both important manufacturing methods. With 3D printing, it’s possible to produce looks-like and feels-like prototypes, continue to refine the product in the early stages of commercialization, and do stop-gap production while awaiting molds.
“We've got a playbook that works now. We use the Form 3 to build rapid, high-fidelity prototypes that our end-user surgeons are impressed by. We've got something that works really well for us and we're just going to keep iterating and keep finding new ways to help improve patient care.”
Radu Postole, Product Design Lead, Arbutus Medical
Arbutus Medical and Ember Prototypes continue to work together. The diversity of projects Tsao works on at Ember Prototypes reveals pain points in manufacturing and production, and he’s determined to solve these as he helps his clients, including Arbutus Medical.
“We've made internal products that specifically solve pain points in manufacturing and 3D printing and production. We're now starting to turn those into our own products. The Formlabs ecosystem is a pretty big part of that.”
Phil Tsao, Founder of Ember Prototypes
Explore resources on 3D printing for medical device development, or talk to a 3D printing expert to learn more about leveraging 3D printers for your prototyping, manufacturing, and production needs.