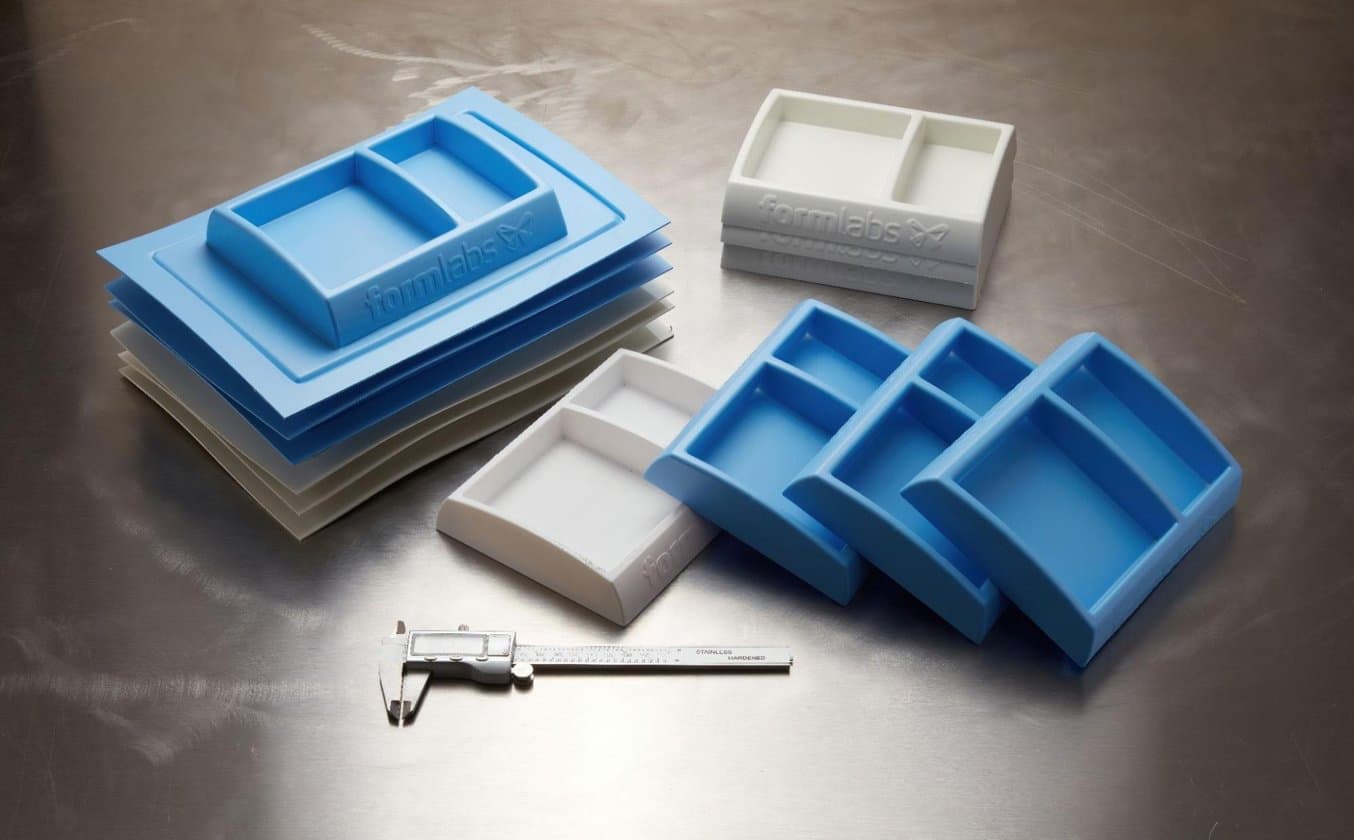
Formech, a designer and manufacturer of vacuum forming machines, evaluated the viability of using 3D printed molds on their vacuum forming machinery, and shared their results with us.
Download our white paper that documents the fabrication steps and trials thermoforming with 3D printed molds, as well as three more case studies, design recommendations, and molding conditions for forming common thermoplastics.
Why 3D Print Molds for Thermoforming?
Traditionally, thermoforming tools—also referred to as molds, forms, or bucks—are fabricated by CNC machined metal for large production, or wood or composite board (foam or fiberglass) for smaller batches. These processes all require expensive equipment and labor for CAM settings and machine operation. Outsourcing the mold comes with weeks of lead time and can cost thousands of dollars. As a result, producing limited quantities of thermoformed parts—for prototypes or low-volume batches—is usually not a viable option.
Desktop 3D printing is a powerful solution to fabricate tools rapidly and at a low cost. It requires minimal equipment, saving CNC time and skilled operators for other high-value tasks in the meantime. With in-house 3D printing, manufacturers and product designers can introduce rapid tooling into the product development process to validate design and material choices prior to transitioning to mass production. They can iterate quickly, accelerate product development and bring better products to market.
Stereolithography (SLA) 3D printing technology is a great choice for molding. It is characterized by a smooth surface finish and high precision that the tool will transfer to the final part and that also facilitates demolding. Molds produced by SLA 3D printers are chemically bonded such that they are fully dense and isotropic, producing functional molds at a quality not possible with other common 3D printing technologies, such as fused deposition modeling (FDM). SLA 3D printing also offers unmatched design freedom to create complex and intricate molds.
Desktop SLA printers, such as the Form 3+, can seamlessly be integrated into any workflow as they are easy to implement, operate, and maintain. While being compact enough for an office, the large format 3D printer Form 3L enables the fabrication of large-scale parts and molds. Additionally, Formlabs offers a wide range of engineering materials with mechanical and thermal properties that pair well with tool manufacture.
Research by Formech, a Leading Designer and Manufacturer of Vacuum Forming Machines
Formech is a leading designer and manufacturer of vacuum forming machines, with 40 years of experience in delivering complete solutions including consultancy, equipment, installation, and training throughout the globe. Their machine range runs from manual machines right up to fully automatic machines.
Formech is exploring innovative techniques to help their community be successful; gaining flexibility with on-demand tooling is one particular interest. One of their latest research studies involved evaluating the viability of using 3D printed molds on their vacuum forming machinery.
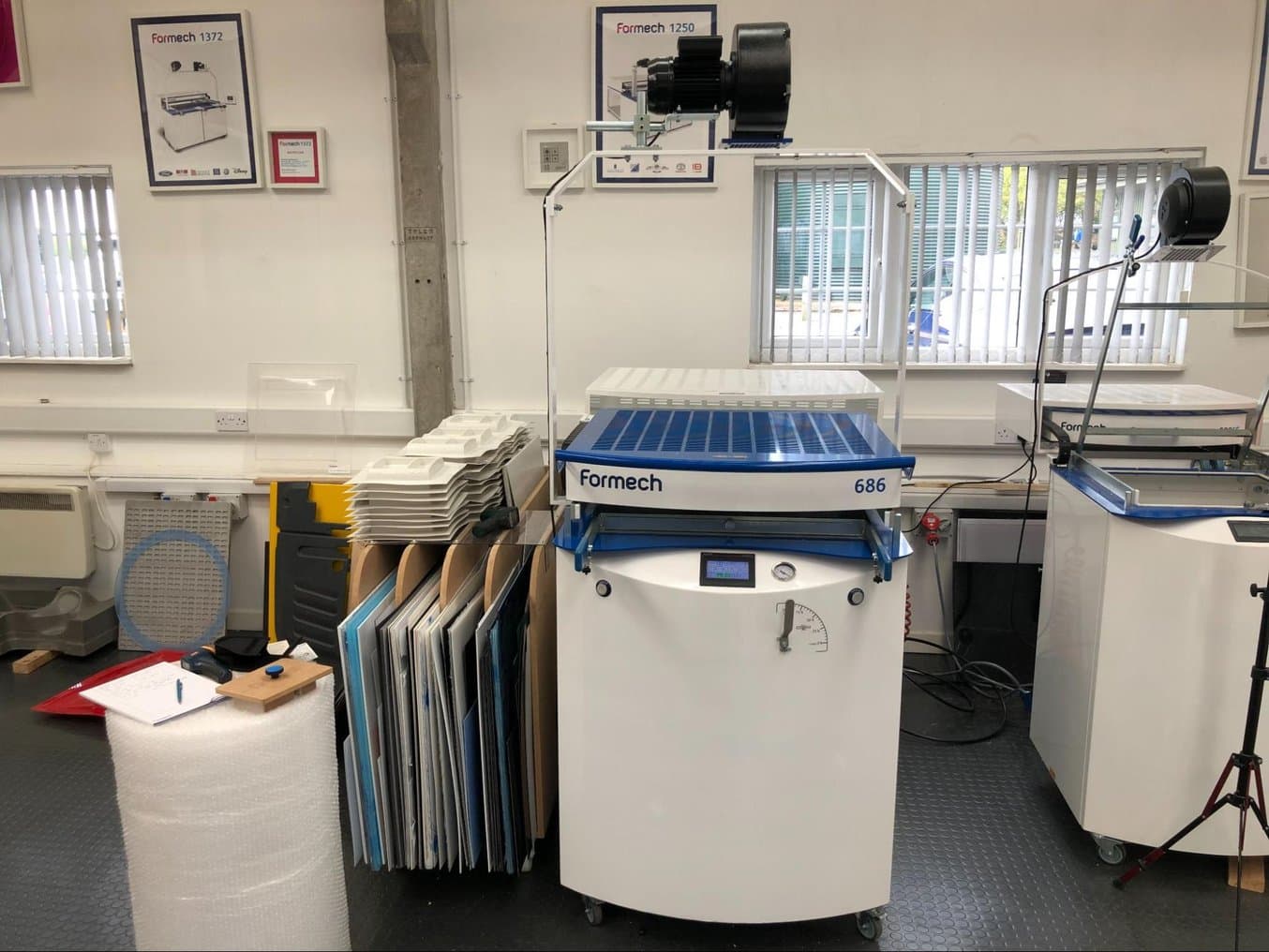
The Formech 686 vacuum former used in the study and the finished formed sheets (left).
Study Details and Benchmarks Geometries
To reflect a common thermoformed item, Formech designed a pocket tray with the following specifications:
- Part dimension at 200 mm x 160 mm x 42 mm.
- Presence of embossed writing of 20 mm x 130 mm x 0.4 mm sizes, the logos followed the curvature of the tray face, and contained a small undercut.
- 6 mm wall thickness and 3 degrees draft angles.
- 1 mm diameter vacuum holes.
- The mold was drawn up hollow with a 3 mm wall thickness at the base to limit resin consumption. Additional ribs were placed on the underside for better mechanical support and improved airflow.
- Presence of four flat stips on the underside in the grid area to fix the tool on the baseboard of the vacuum forming machine with double-sided foam tape or by the use of screws.
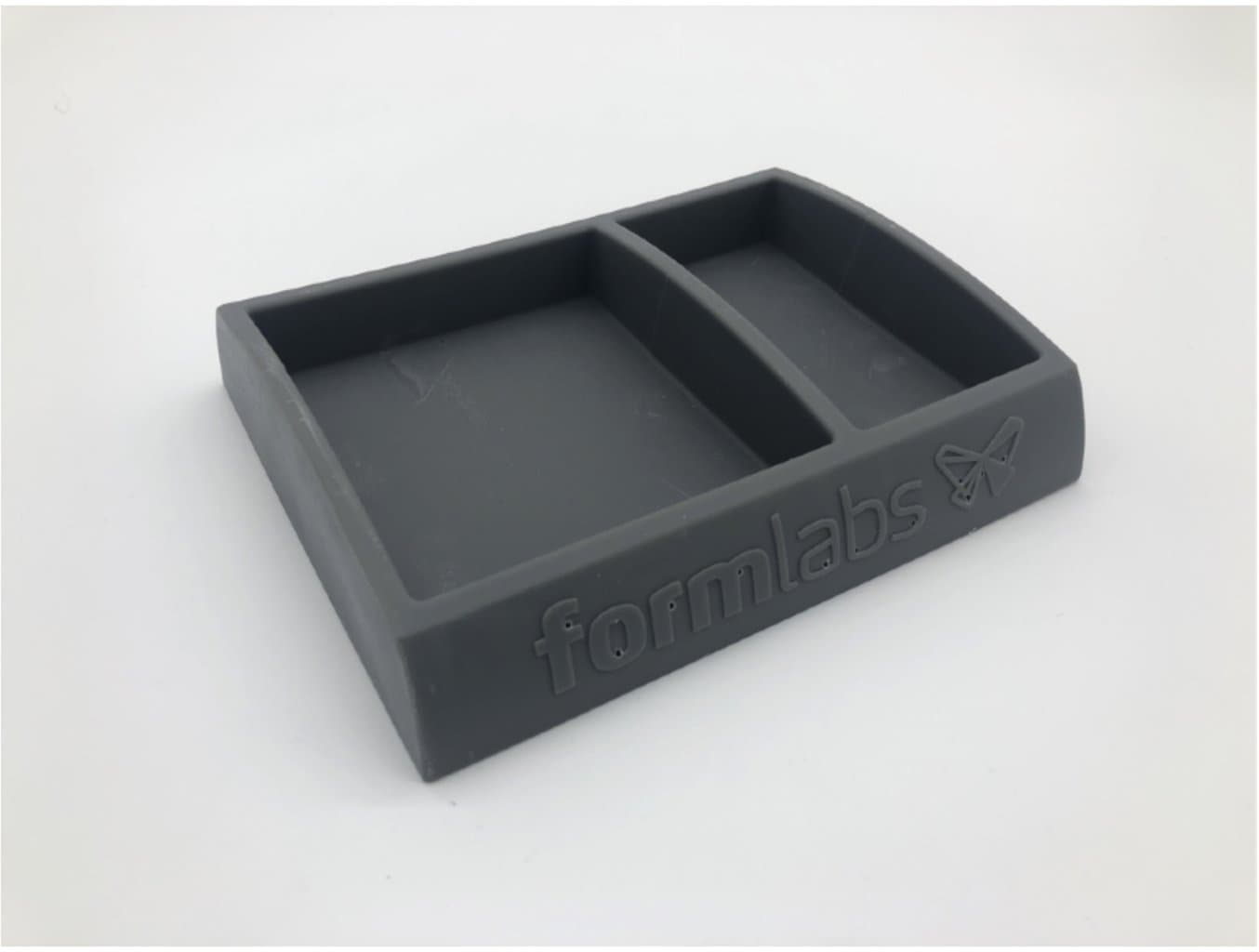
The test part was a pocket tray, a common thermoformed item. The mold was printed in Grey Resin on a Form 3L printer.
Results
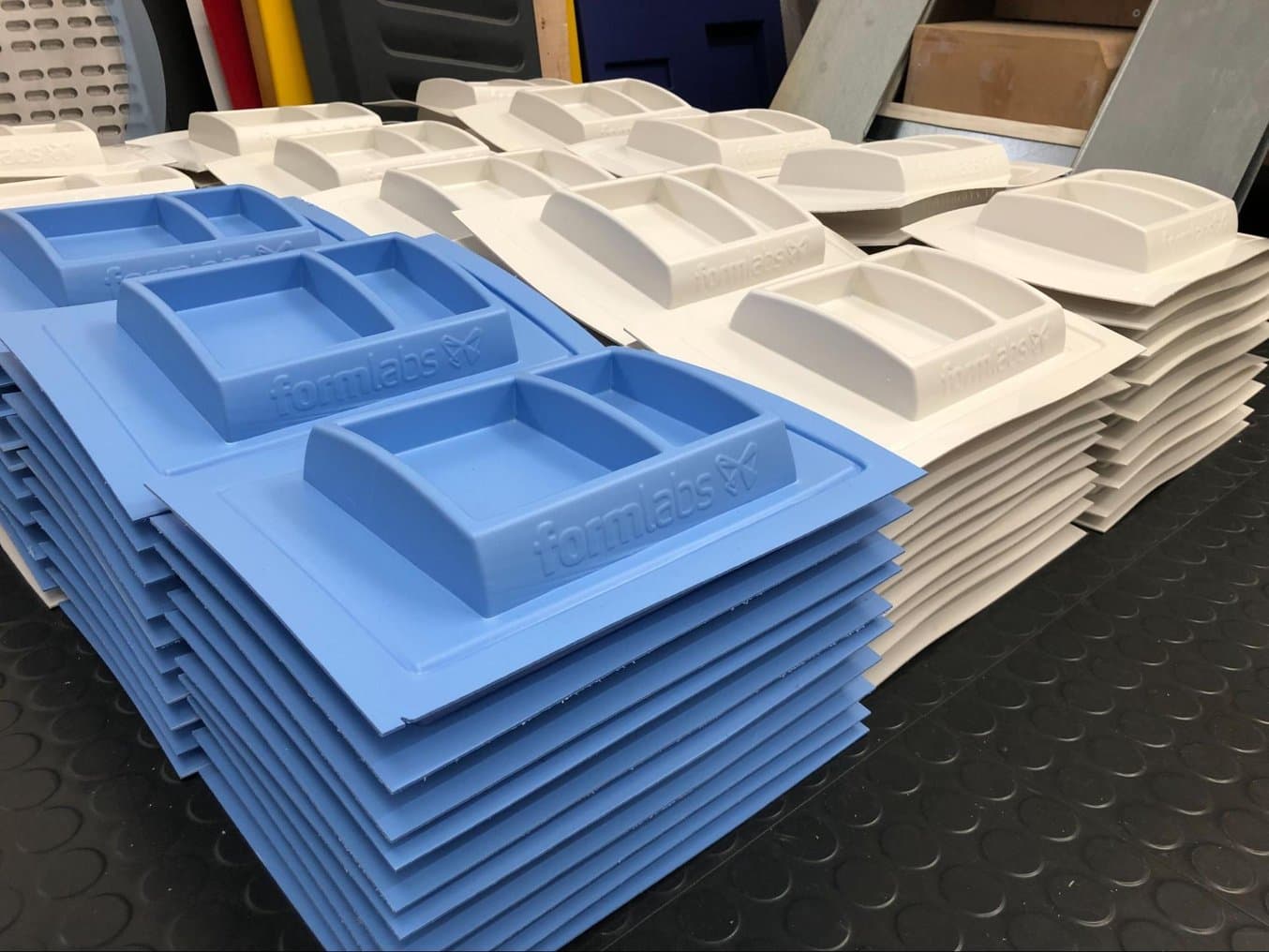
Molds printed in Grey Resin and Rigid 10K Resin were successfully used to thermoform 1.5mm thick ABS and HIPS sheets.
Formech’s team formed 50 parts of 1.5mm thick ABS and HIPS sheets on each printed tool. The vacuum formings were produced in a similar fashion to conventional production methods with no allowance for the tooling overheating. Consistent cycle times were used. The quality of the formed parts was similar to those achieved with traditional tooling.
Download the full report to see the details of the study, including 3D printing guidelines and insights on the mold assembly and process conditions.