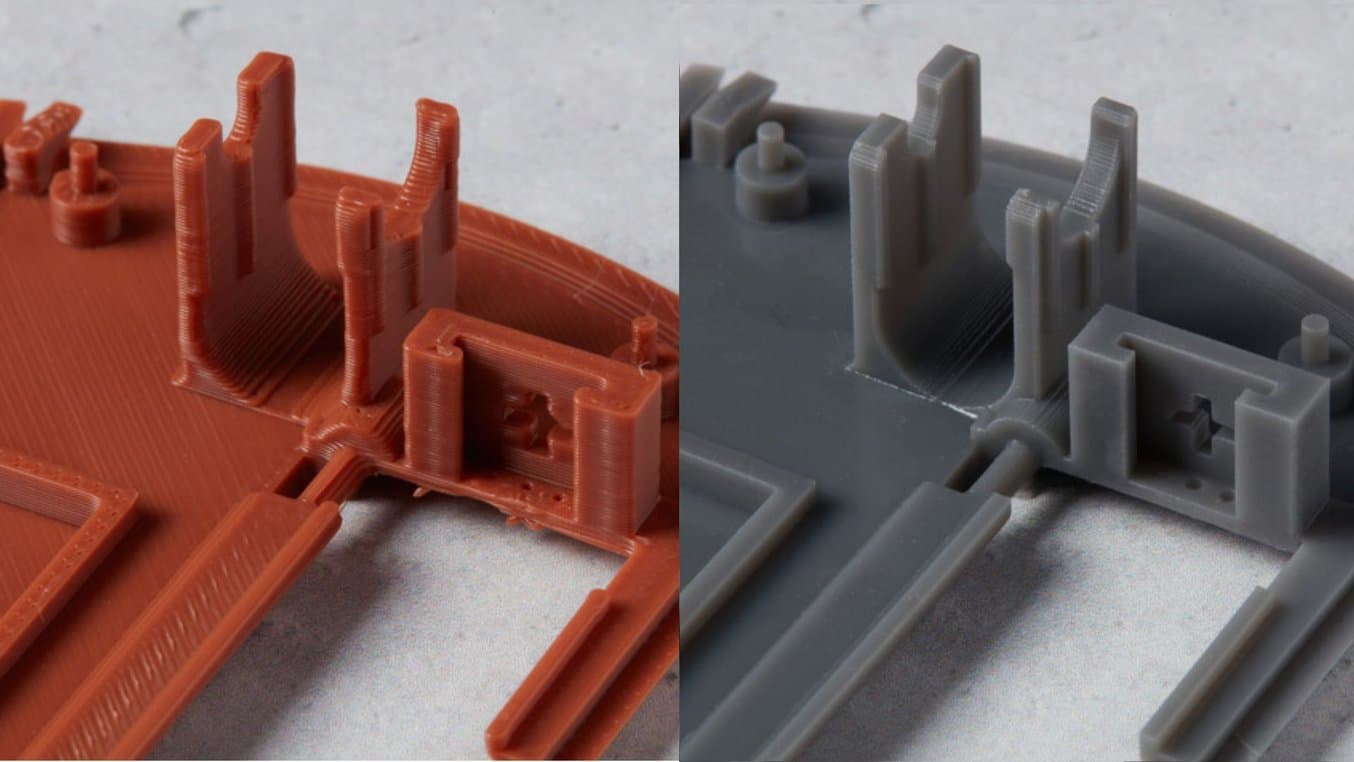
FDM 3D prints (left, printed in PLA on a leading prosumer FDM printer) tend to have a rougher surface finish than SLA prints (right, printed in Grey Resin V5 on a Form 4).
All 3D printing technologies have advantages and disadvantages, so how do you know which one is right for a given application? When choosing between two of the most commonly used 3D printing technologies, fused deposition modeling (FDM) and stereolithography (SLA), it can come down to particulars of workflow and material characteristics.
FDM is the most widely used type of 3D printer, with several million units sold since 2018. These printers tend to be easy to learn and inexpensive to operate. SLA 3D printers, once considered suitable only for delicate parts, are now widely used for producing parts with high-performance materials. With the ability to produce parts that are highly accurate, isotropic, 100% dense, and have superior mechanical properties, SLA can open up new opportunities and step up where FDM falls short.
It would be an oversimplification to say that either technology is universally better or worse than the other. In many cases, the two printer types complement each others’ strengths, and it can be useful to have both in the same workshop. Read on to learn the thought process behind selecting one technology or the other.
Where FDM is better | Where both are competitive | Where SLA is better | |
---|---|---|---|
Workflow | Material cost Low mess + hazard | Print speed Ease of support removal | Scalability/throughput |
Part properties | Color variety Lightweight, hollow parts Carbon fiber inlay Actual thermoplastics | Toughness Chemical resistance Flame retardance (self-extinguishing) ESD safety Stiff elastomerics (durometer > 80A) | Temperature resistance Fine feature resolution Fully dense parts Clarity Isotropy Smoothness Watertightness Soft elastomerics (durometer < 80A) Low moisture absorption Biocompatibility |
When To Choose FDM Over SLA
Material Cost
One of the primary considerations when deciding between FDM and SLA 3D printing is material cost. FDM materials, such as PLA or PETG, are significantly more affordable than SLA resins, with filament prices often ranging between $20 and $50 per kilogram. By contrast, SLA resin costs can start around $50 per kilogram and go much higher, depending on the type and quality of the resin. For projects requiring a lot of material, FDM’s lower cost per kilogram can make it a more budget-friendly choice.
Additional material cost savings can come from adjusting infill with FDM prints, as these are very rarely printed 100% solid. This means you can create parts that are partially hollow, saving material and reducing weight, but with some compromises on structural integrity. SLA printing, on the other hand, typically produces fully solid parts, making it less material-efficient for applications where strength is not a primary concern.
Note that some SLA print preparation software programs, such as PreForm, have a built-in part hollowing tool that achieves the same material cost reduction as sparser infill.
Color Variety
FDM offers far more flexibility than SLA when it comes to color variety. PLA filament, in particular, comes in a vast range of colors, including multi-color filament and specialty finishes like silk, matte, and even glow-in-the-dark. This variety eliminates the need for painting in many cases.
SLA resins are available in a more limited set of colors than PLA, in part because the photo-reactive components in 3D printing resins can be sensitive to pigment concentration. SLA 3D prints can be painted or coated, and some specialty products exist to mix your own color resin, but in general, FDM offers more color options than SLA.
No Washing or Curing
Another advantage of FDM is the simplicity of post-processing. With FDM, parts come out of the printer ready to use — there’s no need for washing or curing, as is required with SLA prints.
SLA prints must be washed in isopropyl alcohol (IPA) or other specialized cleaning solutions, such as Formlabs Resin Washing Solution. IPA is extremely effective at cleaning resin-coated parts, but has an odor, and the gases are flammable, which can make it an inappropriate choice for some environments such as homes or schools with young children present. Formlabs Resin Washing Solution is a non-flammable alternative to IPA that can be used with resin 3D prints for the required washing step.
SLA parts also may require curing under UV light and heat to reach their final strength or, if relevant, biocompatibility. Learn more about post-processing resin 3D prints.
However, it’s important to acknowledge that FDM post-processing isn’t always faster. Removing supports from FDM prints can be tricky, and achieving smooth surfaces can require lengthy manual sanding, particularly for complex geometries. But for those who value the convenience of pulling a part straight out of the printer and skipping the chemical-intensive workflow, FDM is often the better choice.
When To Choose SLA Over FDM
High Quality 3D Printed Parts
For projects that demand fine detail, smooth surfaces, and exceptional accuracy, SLA is often the best choice, even if the higher material cost and additional post-processing steps are necessary. Its ability to deliver professional-grade results makes it a valuable tool for specialized applications where FDM might fall short.
Accuracy
SLA is often the preferred choice when accuracy is critical. SLA printers use a light source such as a laser or LEDs to cure liquid resin layer by layer, resulting in highly precise and consistent prints. This process produces parts with tight tolerances, making it ideal for applications like dental models, jewelry prototypes, and engineering parts that require exact dimensions. In comparison, FDM printing extrudes molten filament, which can lead to slight inconsistencies due to nozzle movement, layer adhesion, and material shrinkage. When precision is non-negotiable, SLA outshines FDM.
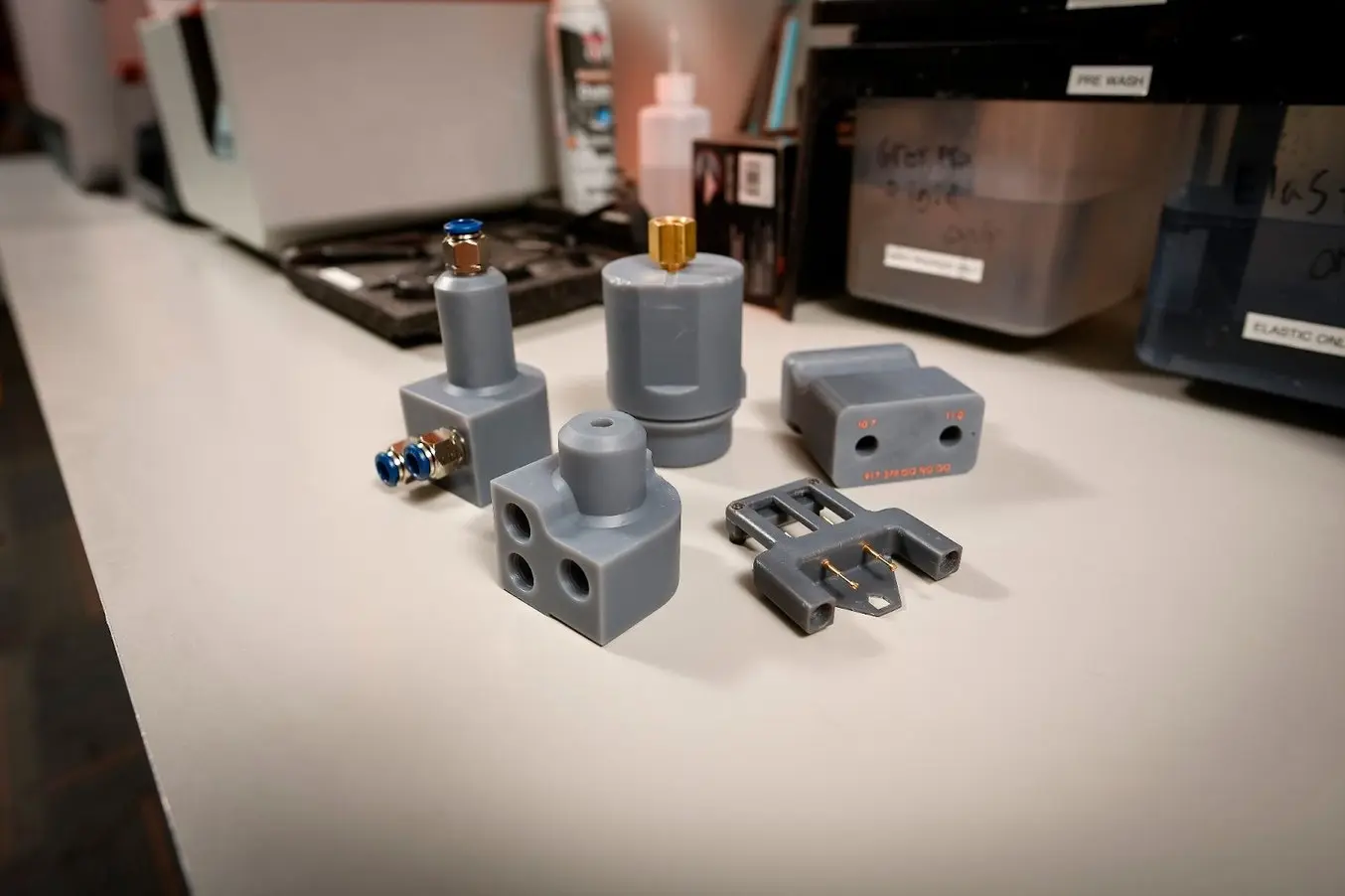
Dorman Products achieves tolerances as tight as 0.025 mm on their Form 3L SLA 3D printer without extra steps like machining.
Aftermarket automotive supplier Dorman Products uses Formlabs SLA 3D printers for prototyping and quality control because of the accuracy they offer. Before their products are put on shelves and installed in customers’ cars, the team at Dorman needs to know exactly what kind of dimensional variation these parts can tolerate, so they do dimensional analysis to determine if a part is a ‘go’ or a ‘no-go.’ This could require tight tolerances in some cases, which they weren’t sure would be possible to hold on a 3D printed gauge, before getting their Form 3+ and Form 3L printers. Now, they can achieve impressive 0.025 mm tolerances on 3D printed parts.
“The engineer came down and said that we had a +/-.05 mm tolerance that we needed to hit, on a diameter. We were able to get it printed with a diameter that had a .025 mm tolerance on a run-out. I couldn’t believe that I was able to get a tolerance like that on a Form 3L.”
Chris Allebach, Additive Manufacturing Lead, Dorman Products
With Form 4 and Form 4L printers, this tolerance is even tighter, with ±0.15% dimensional tolerances on 1-30 mm features (lower limit: ±0.02 mm) and ±0.3% on 81-150 mm features (lower limit: ±0.15 mm).
Independently Tested Reliability of Form 4 and Other Resin 3D Printers
Formlabs Form 4 was measured to have a 98.7% print success rate by an independent global leader in product testing. Read a complete description of the test methodology and see the results in our white paper.
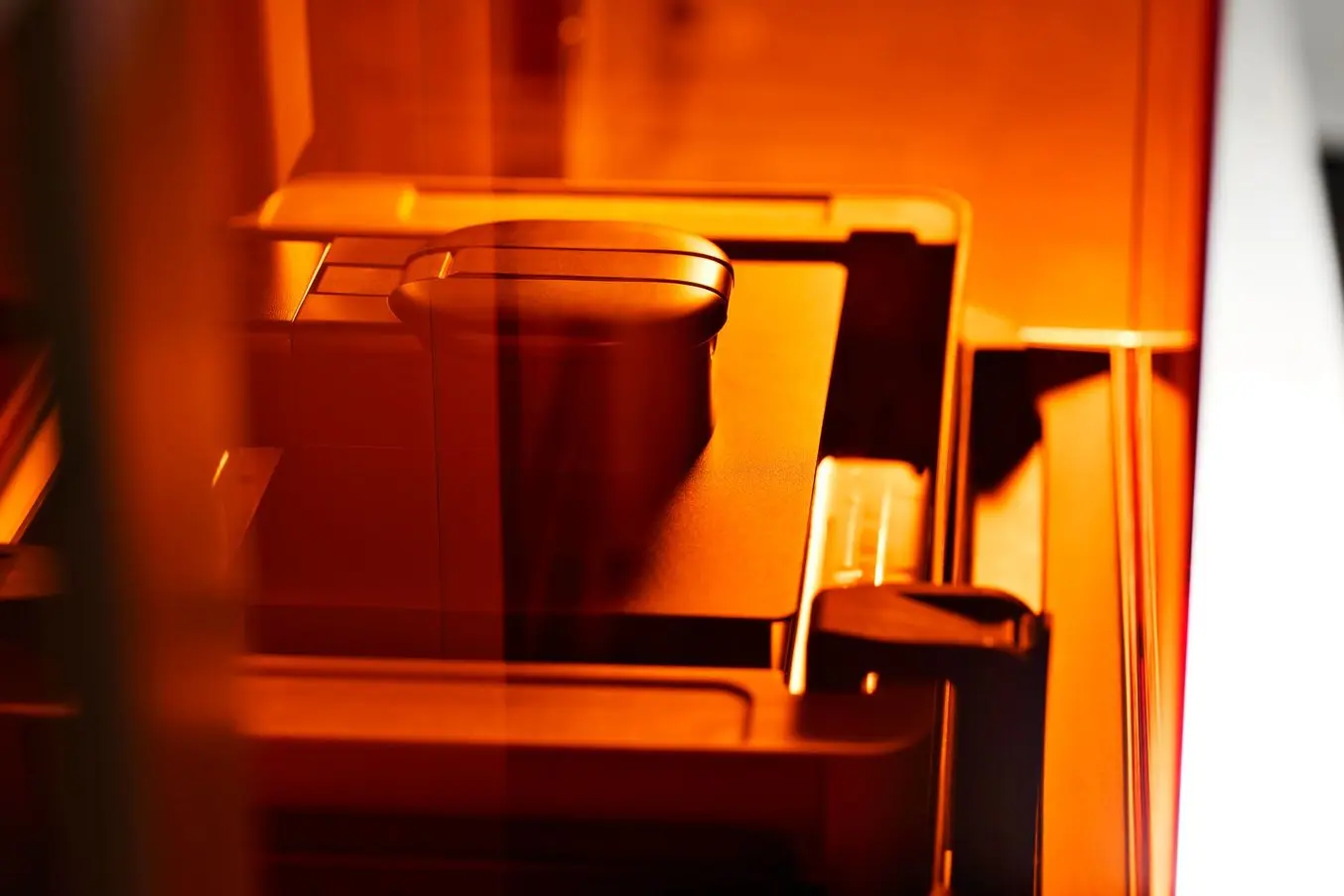
Product Demo: Form 4
See how Form 4 can enable new levels of productivity and innovation through its unmatched speed, accuracy, and reliability.
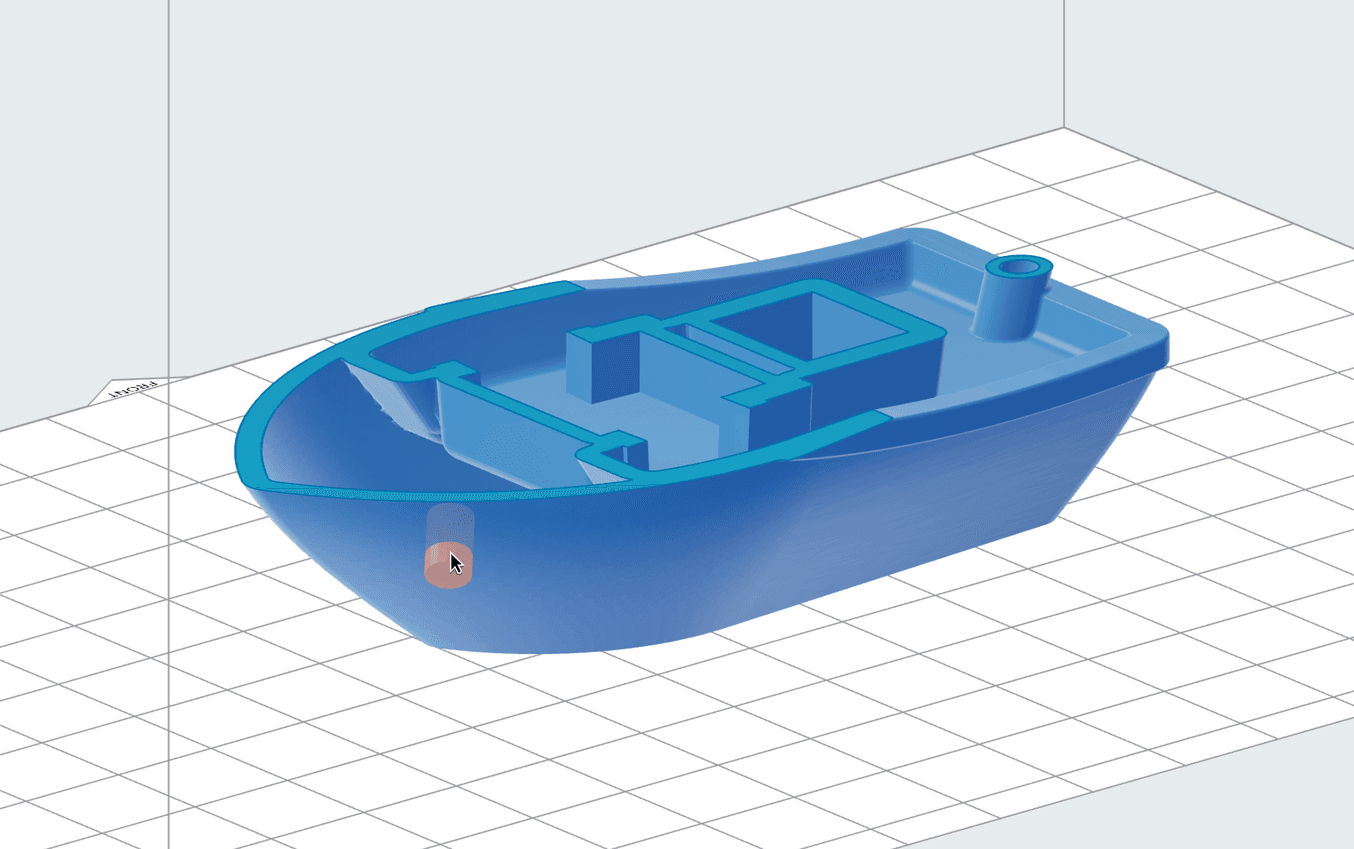
Form 4 Series Design Guide
A successful 3D print starts with a well-designed model. Follow our best practices to optimize designs and reduce failures.
Surface Finish
Another significant advantage of SLA is its superior surface finish. SLA printed parts have a smooth, semi-matte finish straight out of the printer. This smoothness is particularly advantageous for aesthetic parts, such as product prototypes, and for applications like medical devices, where surface quality can impact functionality. FDM prints, by contrast, tend to show visible layer lines, especially on curved surfaces, and often require extensive sanding or post-processing to achieve comparable results.
Smooth surfaces can be critical for some applications, such as silicone molding and wind tunnel testing. It can also be a helpful element of the 3D printing workflow, as is the case at Archer Aviation. As design manager Julien Thiebaud says, “I love the fact that we can remove all the support pieces only with a finger, not even using a tool. Wash them, cure them, and then slap them onto the prototype. There's very little, if any, hand finishing to be done. The overall quality is incredible.”
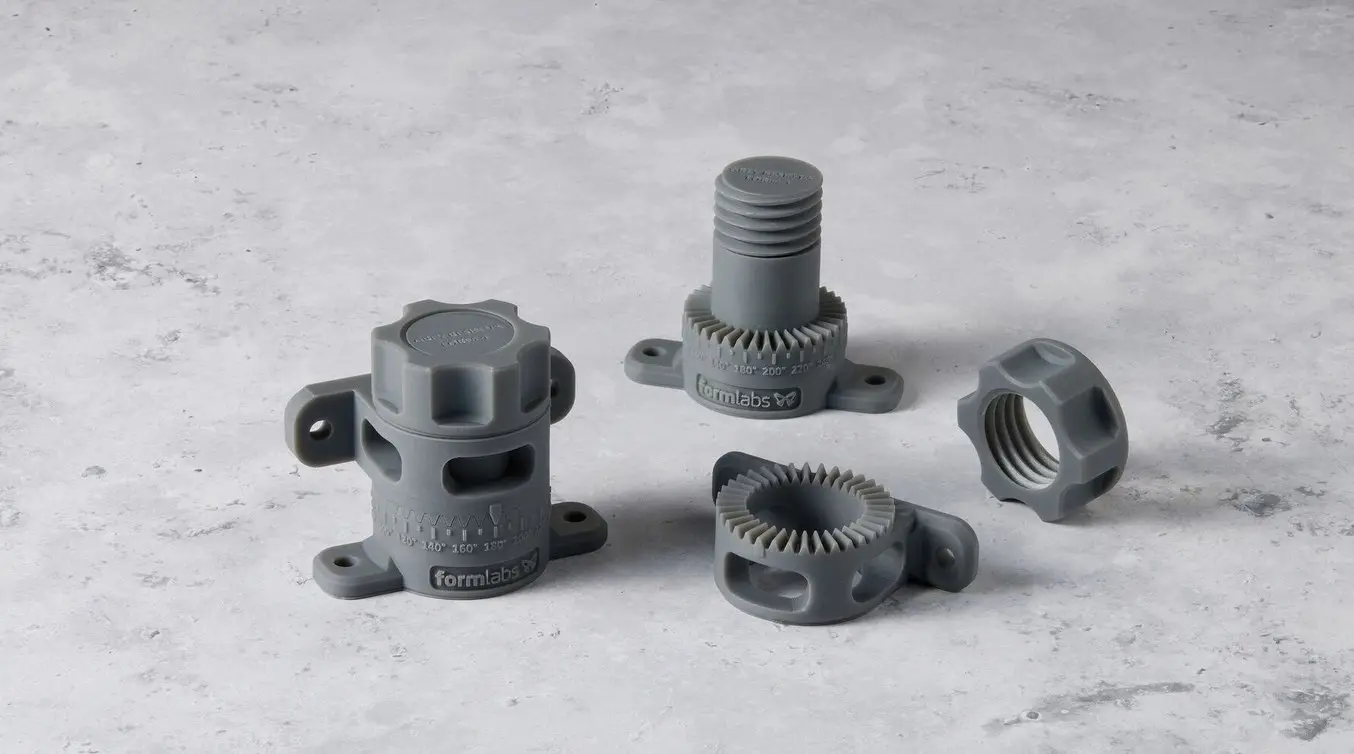
Request a Free Sample Part
See and feel Formlabs quality firsthand. We’ll ship a free SLA sample part to your office.
Small Features
SLA excels at producing small, intricate features. The XY resolution of SLA printers allows for the creation of extremely fine details, such as thin walls, sharp edges, and complex geometries. While FDM can print small details, it is limited by the size of its nozzle and the behavior of melted filament, which can result in unresolved or smoothed-over features.
Microsoft’s Advanced Prototyping Center uses many 3D printers, including SLA and SLS printers from Formlabs, to produce both iterative design prototypes and proof-of-concept short production runs. Their parts can be large, like cases for Surface laptops, or small, like the electrical connectors pictured below. While FDM could theoretically be suitable for the large parts, even the most sophisticated FDM printers would struggle to resolve the tiny negative and positive features in a part like a connector.
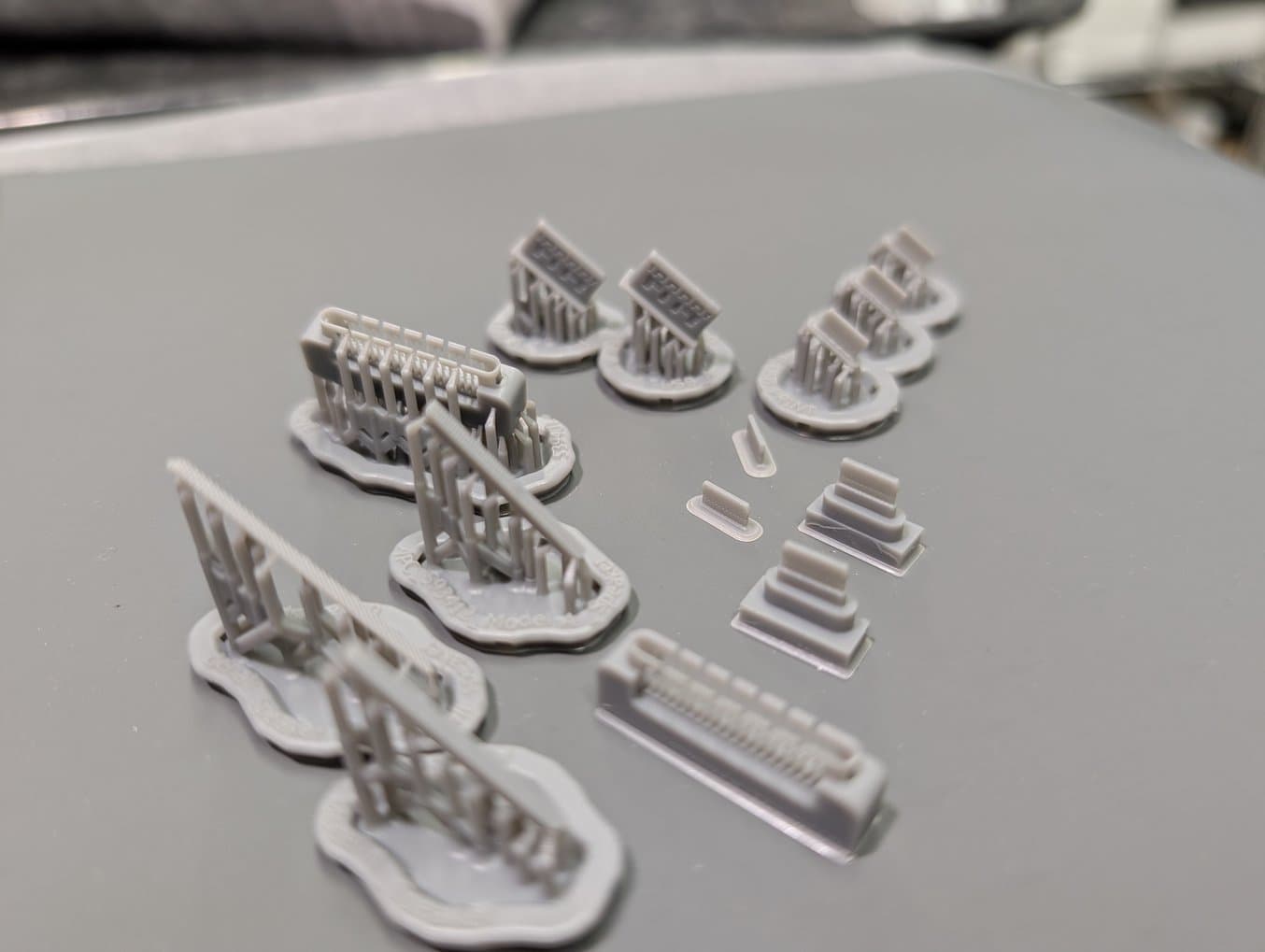
Microsoft prototypes tiny components like these electronic connectors with Formlabs SLA 3D printers because they can resolve the fine features accurately.
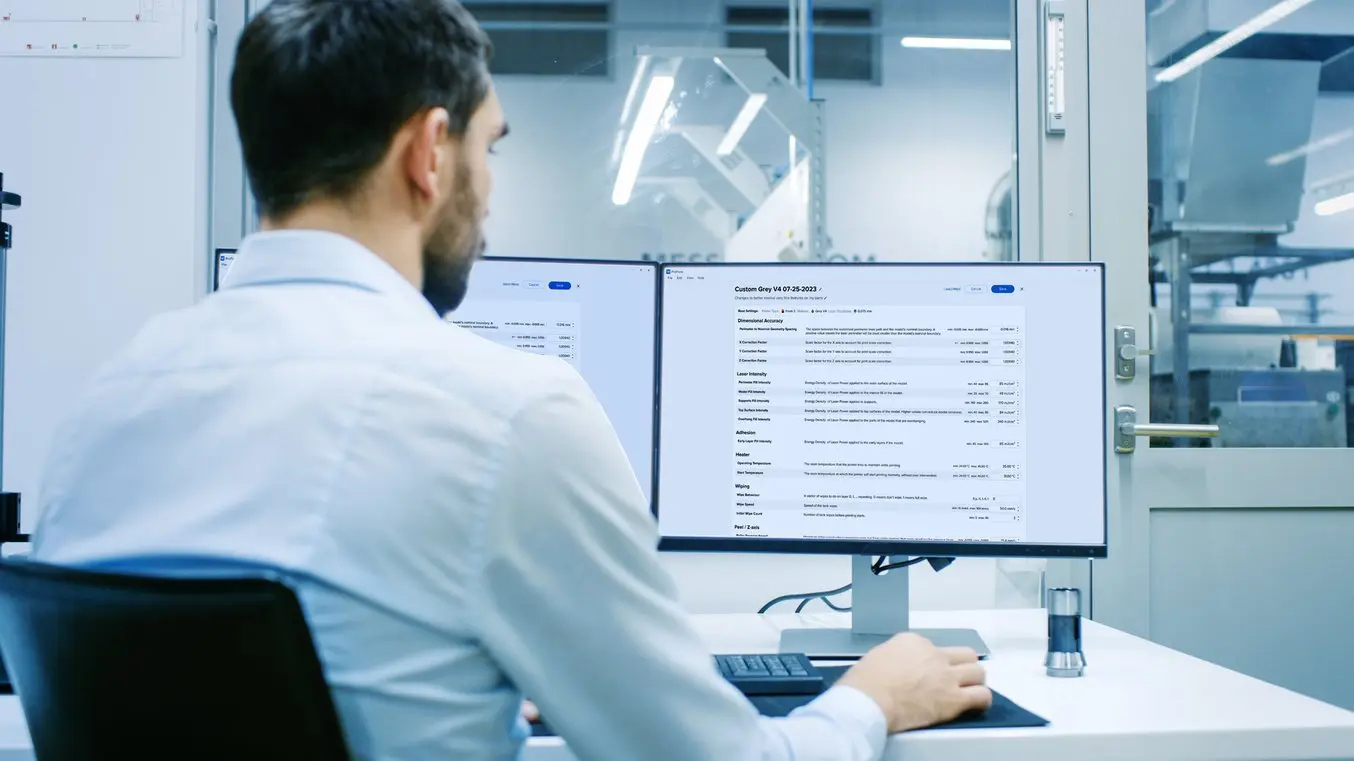
Talk to Our 3D Printing Experts
Whether you need to prototype at speed, or are producing end-use parts, we’re here to help. The Formlabs Sales team is composed of dedicated specialists who know exactly how to support you and your company's needs.
Fully Dense 3D Printed Parts
SLA creates fully dense parts, which FDM cannot do. Even at 100% infill, and even with print settings configured to over-extrude material, parts printed with FDM have tiny voids where the extruded plastic does not flow. As a result, FDM cannot create watertight, isotropic, or optically clear parts — but SLA can.
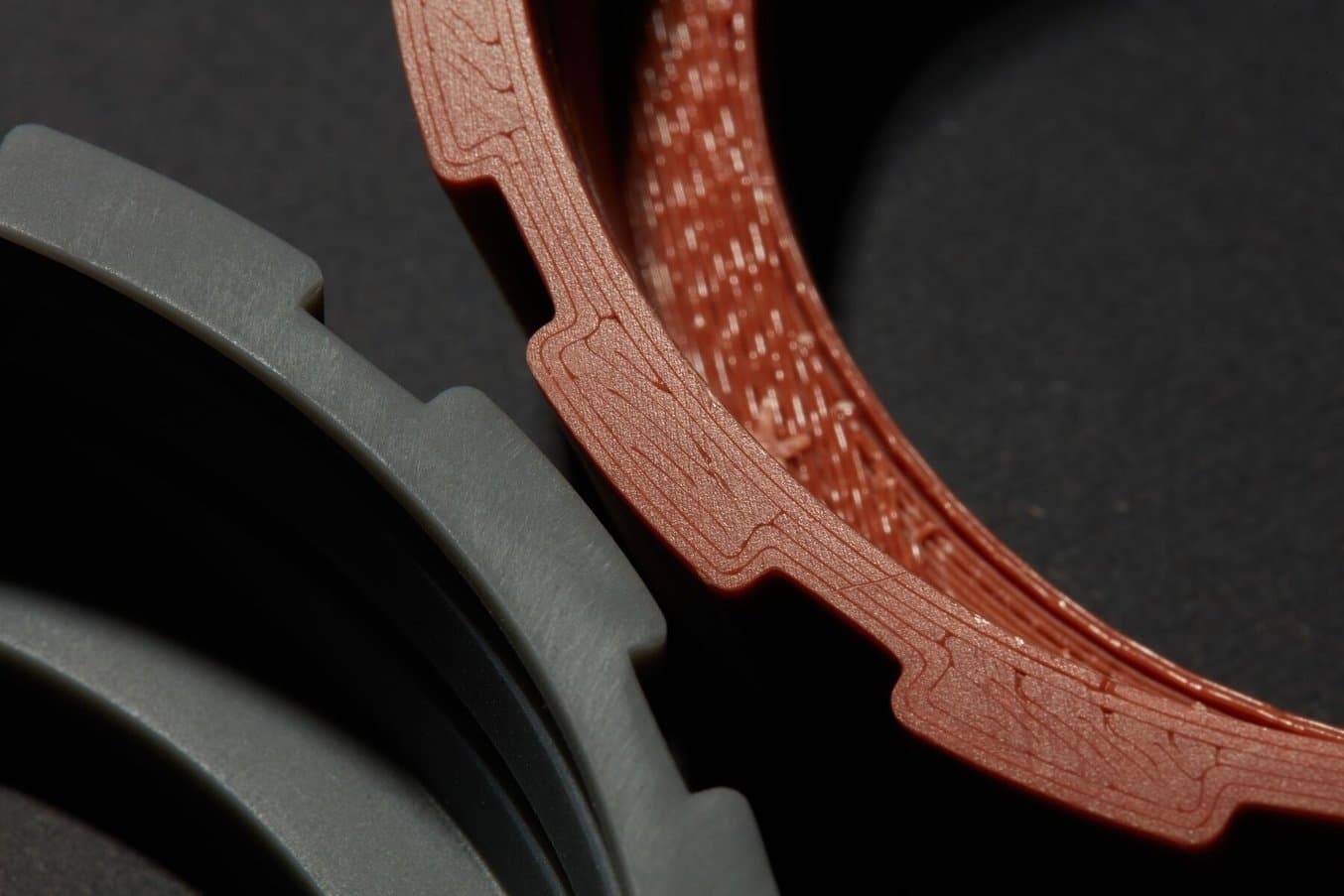
SLA 3D prints (left) are fully dense, while small air pockets remain in all FDM prints (right), even when printed at 100% infill. The part on the left was printed in Grey Resin V5 on a Form 4, and the part on the right was printed in PLA on a leading prosumer 3D printer.
Watertightness and Airtightness
Many parts that handle liquids and gasses, from engine manifolds to deep-sea robots, need to withstand pressure without leaks. The fully dense parts created with SLA 3D printing can be watertight, as opposed to FDM parts, which have air gaps that would need to be filled or otherwise sealed to prevent leaks.
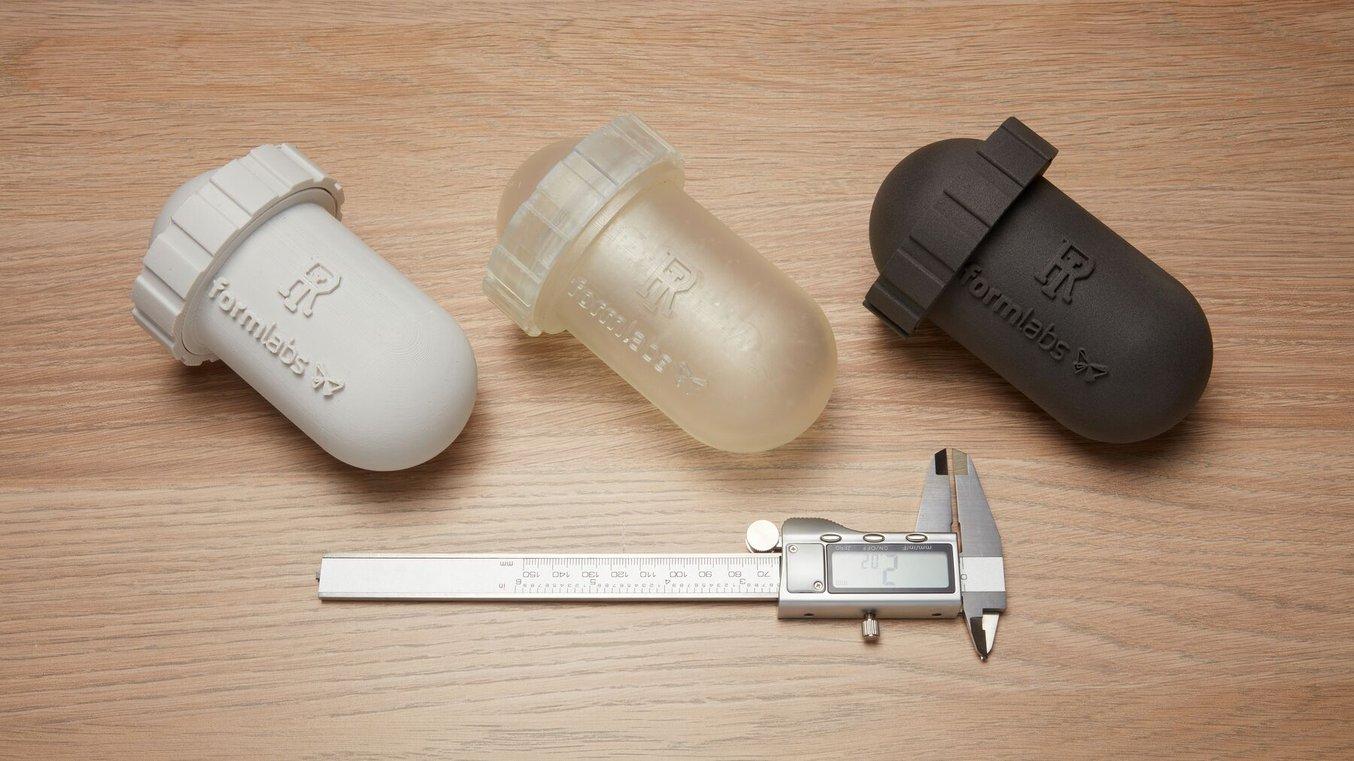
3D Printing Watertight Enclosures and Pressure Testing Results
3D printing can consistently produce enclosures that are watertight, can be deployed in highly pressurized environments, and that the workflow for creating them is accessible and affordable. In this white paper, we will provide the testing results and clear guidelines on how to affordably 3D print customized watertight enclosures.
Researchers at the University of Rhode Island tested printed pressure vessels in different materials and found that SLA printed parts withstood over 1500 PSI, or 100 bar. Glass-filled engineering material Rigid 10K Resin withstood more than 5500 PSI, or 379 bar, before imploding. For full details on the experiment and results, read the white paper.
The Atlantic Oceanographic and Meteorological Laboratory (AOML) at the US National Oceanic and Atmospheric Administration (NOAA) wanted to use 3D printing to quickly and inexpensively manufacture custom research tools. Some parts, like electronics housings, needed to keep water out, while others, like a water sampling system, needed to keep water in. They started with an FDM 3D printer, but quickly found that liquid could seep in or out of their printed parts. They switched to Formlabs SLA 3D printers and have since been able to use 3D printed parts with off-the-shelf components like PVC pipe to create low-cost, custom waterproof sampling systems.
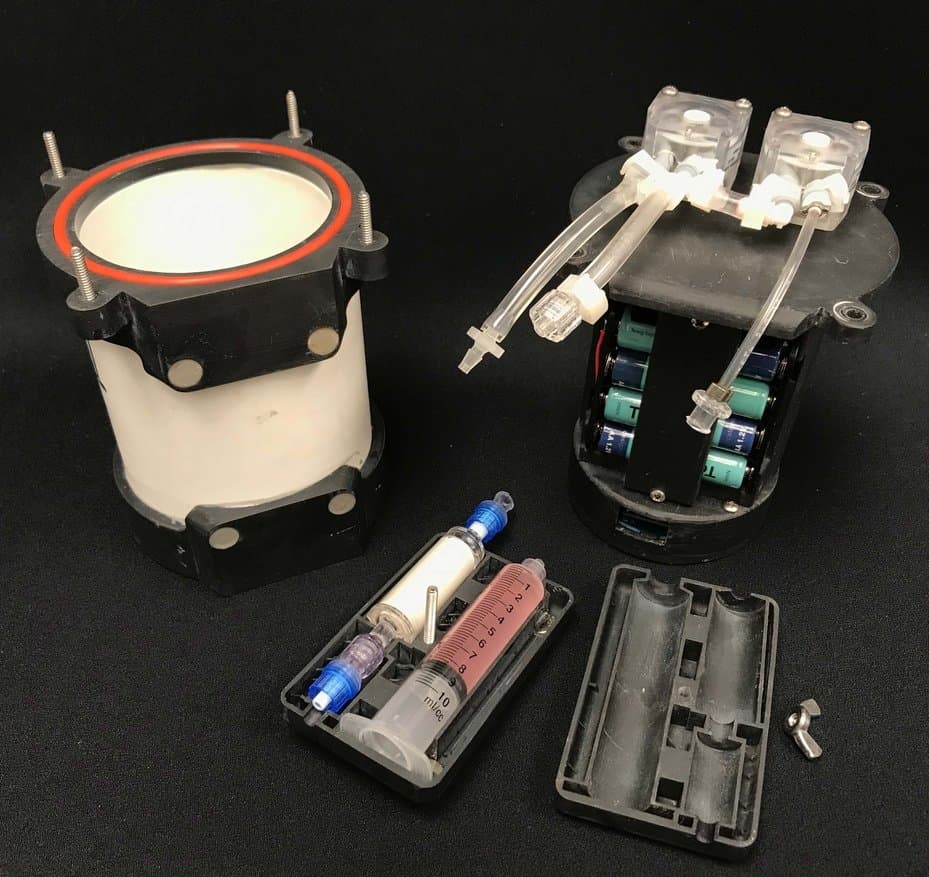
Subsurface Automated Sampler for eDNA (SASe) with SLA end-caps, sample cartridge, and internal armature. (image courtesy of NOAA)
Isotropy
In addition to not being fully dense, FDM prints are significantly weaker in the Z axis than in the X and Y axes. On the other hand, SLA prints are isotropic, meaning they are equally strong in all directions.
Australian company Foil Drive, which makes recreational electrified foiling equipment for marine use, puts their 3D printed end-use propellers through extreme forces. Their propellers spin at 3000 rpm, under extra torque as they plunge in and out of the water. “It is a brutal expectation of a propeller blade, to be able to cope with these forces,” says founder and CEO Paul Martin.
“Having these parts break was not an option going forward.”
Paul Martin, Founder and CEO, Foil Drive
After trying FDM printers, where parts broke under the strong shear forces, and low-cost SLA printers, where a bad batch of material caused part failures, Martin began using a large-format Formlabs SLA printer and a high-performance glass-filled resin to manufacture the propellers. “It wasn’t until we tried the Rigid 4000 Resin that it all worked,” Martin says. “It allowed us to make thousands of them and send them all over the world for people to use as an end-use propeller blade.”
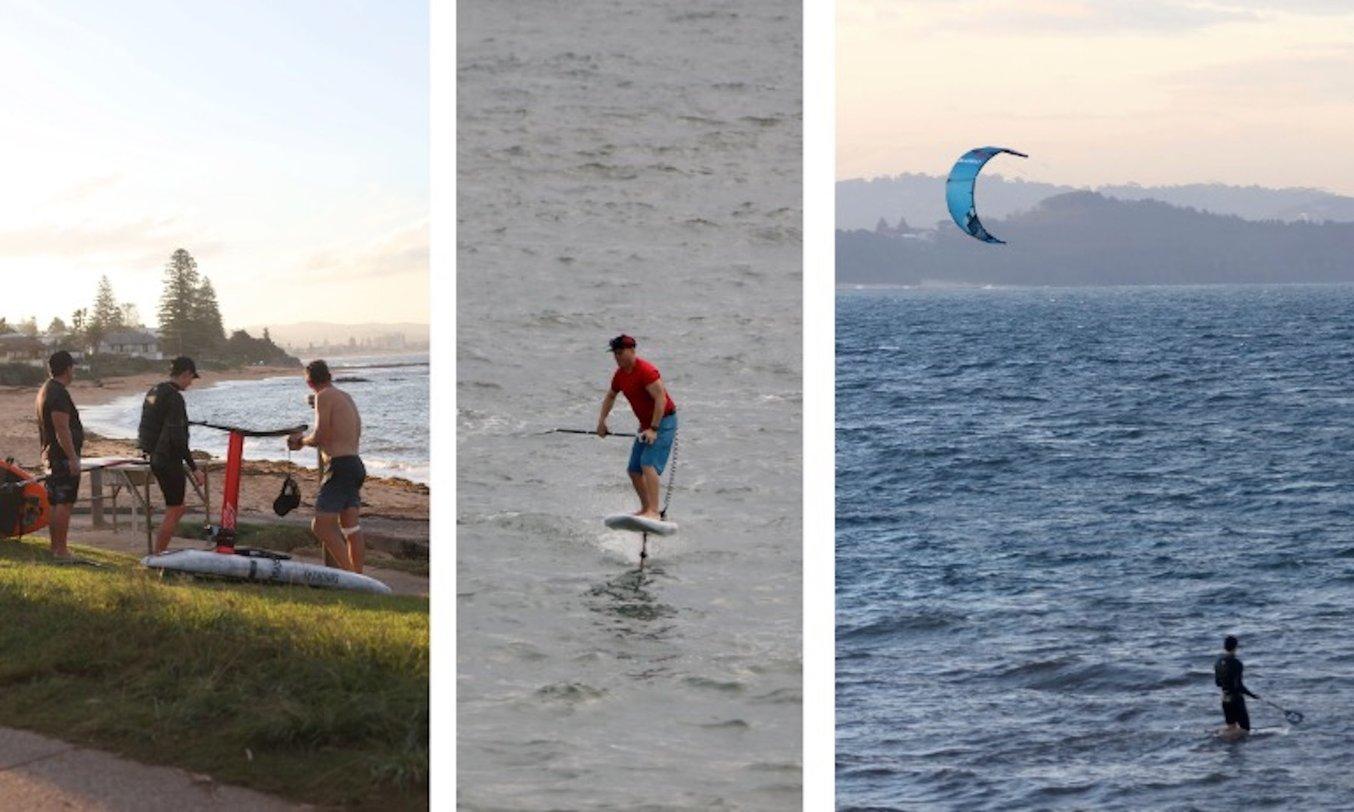
Foil Drive uses SLA to manufacture end-use parts for use in extreme marine environments.
Clarity
Clear filaments are available for use with FDM printers, but the small voids left between extruded filament in printed parts make them look hazy or frosted. Users have found that reduced cooling and slower extrusion can increase translucency, but there will still be air trapped between layers that limits part clarity.
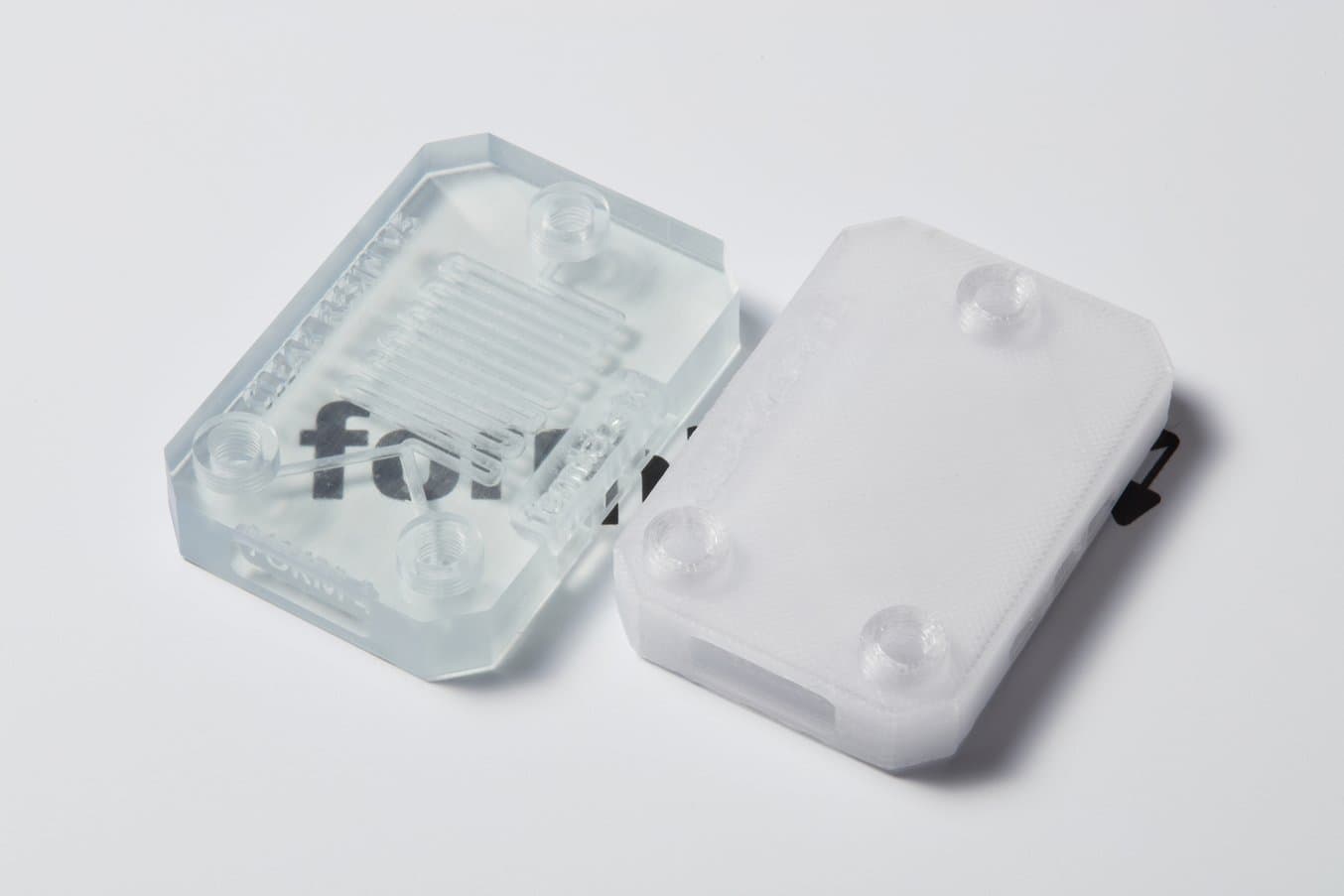
Left, a print in Clear Resin V5 on a Formlabs SLA printer. Right, the same part printed with clear PETG at 100% infill on a leading prosumer FDM printer.
Part clarity has practical applications that allow users of the parts to observe areas that would be obscured in an opaque part. Drone manufacturer Skydio uses Clear Resin to make translucent prototypes that allow engineers to route electrical wires through complex geometry, and neurotechnology company OpenBCI uses Clear Resin to prototype tooling that allows designers to observe material flow during molding to optimize vent positions.
After printing, clear parts can be polished, coated, or otherwise treated to increase clarity and protect against yellowing from UV exposure. Read our guide to transparent 3D printing to see best practices and examples.
Temperature-Resistant 3D Printed Parts
All FDM prints, even those made with specialty high-temperature filament, will melt at a high enough temperature. Most FDM materials are amorphous thermoplastics, meaning they gradually deform as viscosity decreases past their glass transition temperature (often written Tg). Some FDM materials like nylon and TPU are semi-crystalline thermoplastics, meaning they hold their shape until near their melting point, and then deform quickly and significantly. Either way, FDM parts will always melt.
On the other hand, SLA materials are thermoset plastics, which will never melt at high temperature. They may deform under load at high temperature, but this is different from melting. This makes SLA parts particularly well-suited, more than FDM or even SLS, to high-temperature applications. Read our guide to high-temperature 3D printing for more information.
SLA | FDM | SLS | |
---|---|---|---|
Types of plastics | Thermosets | Thermoplastics Amorphous (usually) | Thermoplastics Semi-crystalline (usually) |
Example materials | UV acrylate Polyurethane Silicone | PLA ABS PETG | Nylon Polypropylene TPU |
Behavior at elevated temperature | Will not melt once cured; may deform under high temperature and pressure | Gradually deforms as viscosity decreases past glass transition temperature (Tg) | Holds shape until near melting point, then deforms quickly and significantly |
Stability at High Temperature
Stability at high temperature, even if for a short time, can allow engineers to test combustion reactions for engine and rocket components on plastic 3D printed prototypes, saving significant time and money compared to metal parts.
Aerospace engineer Sam Rogers used SLA 3D printing to prototype the igniter design for a vortex-cooled rocket engine. Even with the vortex cooling, FDM parts would have deformed too much for the test to be useful. With Clear Resin, not only was he able to observe the ignition pattern, but he was able to see the geometry was stable enough for at least a few seconds per test firing.
“If we were to 3D print this on an FDM printer in thermoplastic, the parts would melt and become unusable as soon as they became warm or hot. Under a blow torch, the resin part ablates, which means it burns away a surface layer but remains mostly intact.”
Sam Rogers
Watch the video below to see the details of Rogers’s work with the Clear Resin prototype.
Sterilizability
Temperature resistance also means SLA parts can be sterilized for use in medical and dental treatments. SLA printed parts can hold up to both gamma sterilization and steam sterilization using an autoclave.
Medical device manufacturer restor3D uses Formlabs SLA 3D printers to make end-use surgical tools. Plastic is typically not used in surgical tools because it would melt under the heat and pressure of autoclaving. The tools made by restor3D combine both metal and polymer parts, making them less expensive than the typical all-metal tools, but still able to withstand autoclaving.
Note that the ability to withstand the conditions of sterilization is only one requirement for a material used in medical settings. Biocompatibility is a complex topic; read the Formlabs guide to biocompatible 3D printing resins for a thorough explanation.
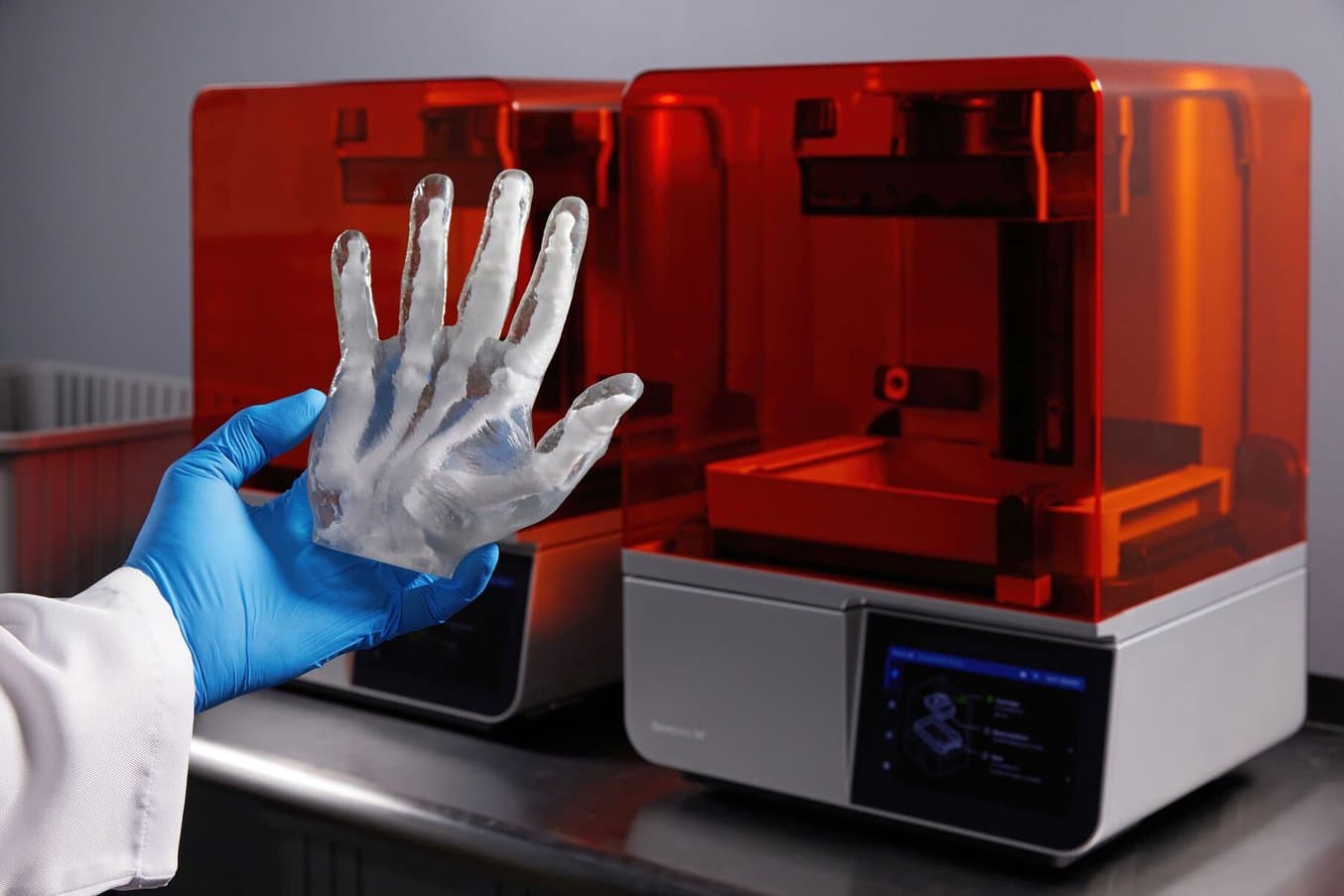
Formlabs Biocompatible Resins: A Comprehensive Guide To Choosing the Right Material
Formlabs' expansive material library was designed to address a wide range of applications and functionalities across industries, including a series of biocompatible resins created with healthcare applications in mind. This paper aims to help users compare and contrast our biocompatible offerings, and determine the best fit for their medical applications.
Molds, Dies, Tooling, and Manufacturing Aids
Many molding processes, including injection molding, blow molding, and thermoforming, occur at high temperatures. Tooling for these operations is commonly made of metals like aluminum for high strength and temperature resistance, but machined metal molds and dies can be prohibitively expensive. 3D printing can reduce lead times and costs associated with tooling, especially for prototype tooling or short production runs, as long as the materials can hold up to the process conditions in question.
Manufacturing aids like jigs and fixtures are critical in metalworking to ensure precision, repeatability, and efficiency. But producing jigs and fixtures with traditional methods can take a couple of weeks, cost upwards of $1,000, and limit geometries. Red Oak Fabrication is a machine shop in Southwest Iowa that uses SLA 3D printing to produce custom jigs in hours, for a tenth of the price of CNC machining, and in complex geometries and organic shapes.
Welding operations typically reach temperatures of a few thousand degrees Celsius, but the jigs are not directly in contact with the weld, and the processing time is only about 10 seconds. The Red Oak team prints their jigs with Rigid 10K Resin, a stiff, glass-filled material offering a heat deflection temperature (HDT) of 238 °C @ 0.45 MPa. Some blackening occurs on the white material, but it does not affect performance.
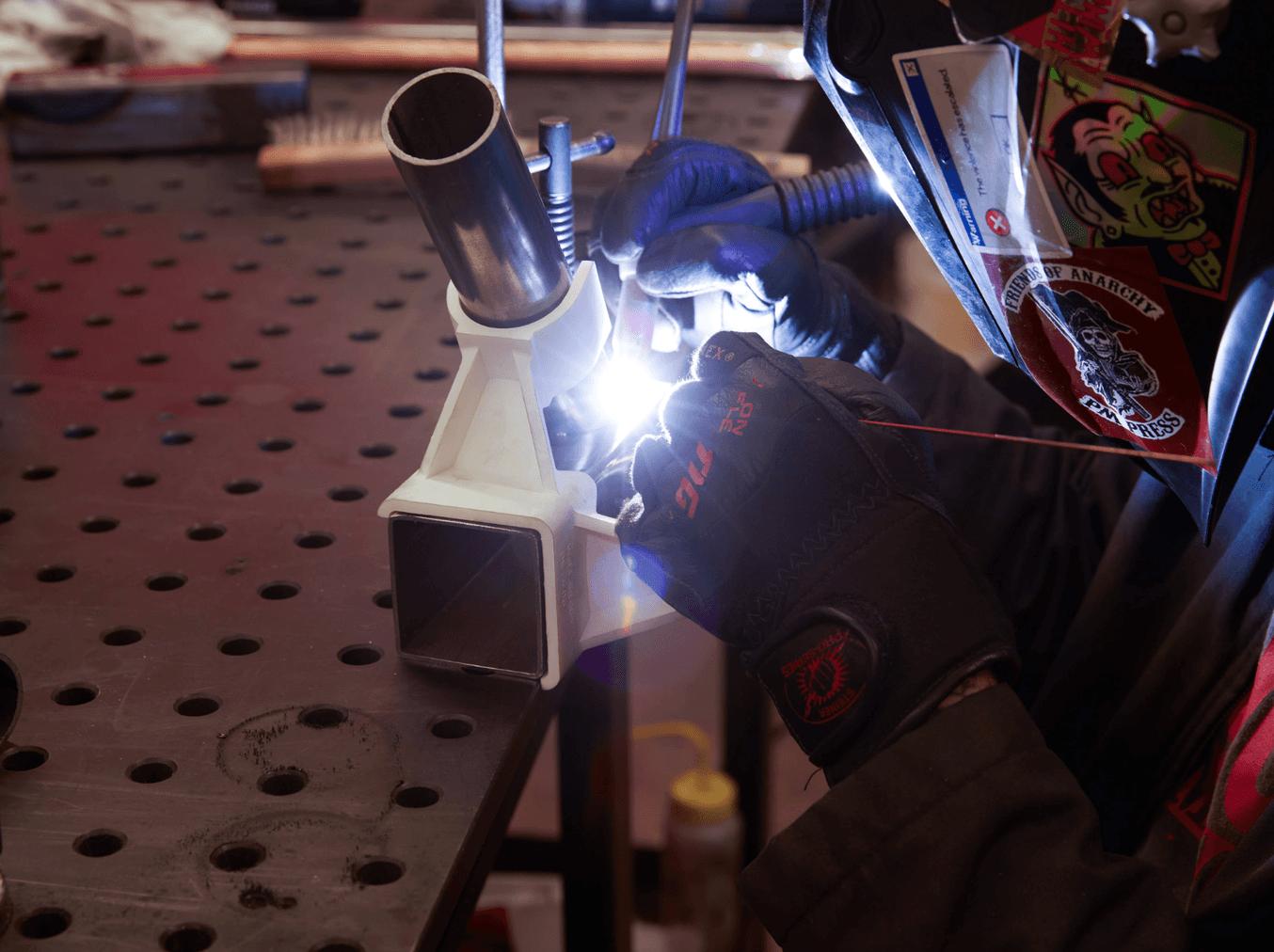
Low-Cost and Rapid Jigs and Fixtures for Metal Fabrication
This white paper outlines a methodology for using 3D printers to produce jigs, fixtures, and other tools for metalworking. Real-world case studies show how Formlabs printers create durable, precise, and heat-resistant tools that perform well in demanding environments. It highlights how companies can cut lead times and costs by up to 90% while improving tool customization and complexity.
Conclusion
While neither FDM or SLA is universally better than the other, the advantages and disadvantages of each can make them more or less suited to different applications. While the SLA materials of 10 years ago were brittle, today’s materials are strong, tough, and offer special properties. When you need high-quality, high-performance parts, SLA steps up where other tools may fall short.
“With SLA, I can do so much that would be impossible with FDM. I can't say the same the other way around.”
Lukas Hartmann, Hardware Developer, KORG Berlin
Request a free sample printed on a Formlabs SLA printer to see and feel the difference for yourself.