Per anni, il clamore suscitato dalla stampa 3D ha catturato l'attenzione del pubblico sulla stampa. Si parlava di un futuro in cui ogni casa avrebbe avuto la sua stampante 3D, ma queste previsioni erano povere di dettagli e alla fine non si sono trasformate in realtà. Tuttavia, le potenzialità della stampa 3D erano innegabili, nonostante si trattasse di una tecnica appena nata e con un numero relativamente basso di casi d'uso disponibili fino a quel momento.
Il clamore iniziale ha celato quelle che erano le reali applicazioni aziendali della stampa 3D. Con la proliferazione sul mercato di apparecchi desktop e da banco ad alte prestazioni, moltissime aziende hanno potuto espandere la propria offerta di prodotti e fornire risultati migliori ai clienti.
Cosa si può fare con una stampante 3D? Scopri 25 usi (spesso insoliti) della stampa 3D che ne testimoniano l'ampio campo di applicazione.
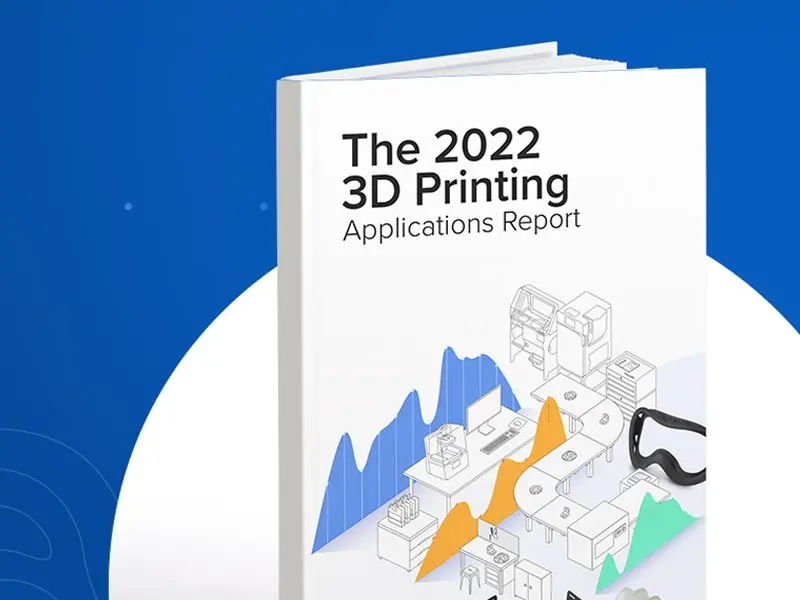
Rapporto 2022 sulle applicazioni della stampa 3D
Un nuovo rapporto che confronta l'utilizzo della stampa 3D nelle aziende da parte degli utenti nuovi e di lunga data, e studia le tendenze future di questa tecnologia.
Progettazione delle automobili di domani
La stampa 3D può aggiungere un enorme valore alle catene di fornitura, offrendo l'accesso a un ampio spettro di applicazioni produttive. La tecnologia sta diventando sempre più praticabile e conveniente, e alcune aziende riescono a introdurre la produzione additiva in-house per supportare i processi in fabbrica. Nuovi materiali di stampa 3D resilienti offrono opportunità inedite di produrre stampe 3D funzionali e ad alta precisione, in grado di sostituire le parti finali. Grazie a nuove soluzioni di personalizzazione, i designer potranno ridefinire gli standard delle automobili ad alte prestazioni. Lo studio di progettazione industriale Vital Auto sfrutta tutta la tecnologia a sua disposizione per creare prototipi estremamente fedeli e concept car, eseguendo rapidamente diverse iterazioni utilizzando una serie di strumenti avanzati, tra cui una vasta flotta di stampanti 3D in-house.
"Utilizziamo la stampa 3D sin dal primo giorno. Volevamo introdurla nel nostro processo di produzione, non solo per ridurne i costi, ma anche per offrire ai clienti maggiore diversità per i loro design e le loro idee", ha detto l'ingegnere di progettazione Anthony Barnicott.
Il settore automobilistico ha colto il valore che la produzione additiva può aggiungere a moltissimi aspetti della creazione di automobili. Ciò significa andare oltre la prototipazione rapida, arrivando a includere anche:
- Creazione di parti complesse, personalizzate e ad alte prestazioni
- Realizzazione di ausili per attrezzature e produzione
- Produzione di parti sostitutive e parti di ricambio su richiesta
- Riduzione dei costi e dei tempi di realizzazione fino al 90% rispetto all'esternalizzazione
Cuffie dall'aderenza perfetta
I progressi recenti della tecnologia di stampa 3D stanno modificando radicalmente il settore dell'audiologia. Infatti, la stampa digitale di dispositivi auricolari su misura per i settori dell'audiologia e della protezione dell'udito non è mai stata così affidabile. Negli ultimi anni, i produttori in ambito di stampa 3D hanno lanciato sul mercato materiali biocompatibili e sicuri per la pelle, consentendo la produzione in-house di modelli auricolari e gommini per le cuffie.
La personalizzazione offre a ogni cliente un'esperienza di ascolto unica, data dalla perfetta aderenza degli auricolari alle orecchie. Questa caratteristica, oltre a offrire un comfort e un isolamento acustico migliorati, fa sì che gli auricolari non cadano dalle orecchie.
"Siamo davvero entusiasti di questo concept di personalizzazione. In questo modo possiamo offrire un'esperienza esclusiva per tutti i clienti, che possono godersi un ascolto immersivo. Formlabs condivide il progetto di innovazione di Sennheiser, e il miglioramento dell'esperienza dei clienti attraverso questo prototipo ne è la prova."
Veronique Larcher, direttrice AMBEO Immersive Audio di Sennheiser
I problemi legati alla produzione personalizzata possono essere affrontati combinando la rivoluzionaria tecnologia di stampa e scansione mobile di Formlabs con il machine learning. Ciò significa che è possibile ridurre drasticamente i tempi di realizzazione, generalmente di quattro giorni, e permettere ai clienti di ottenere i loro auricolari personalizzati il giorno successivo all'ordine o persino il giorno stesso.
L'ultima generazione di strumenti chirurgici stampati in 3D
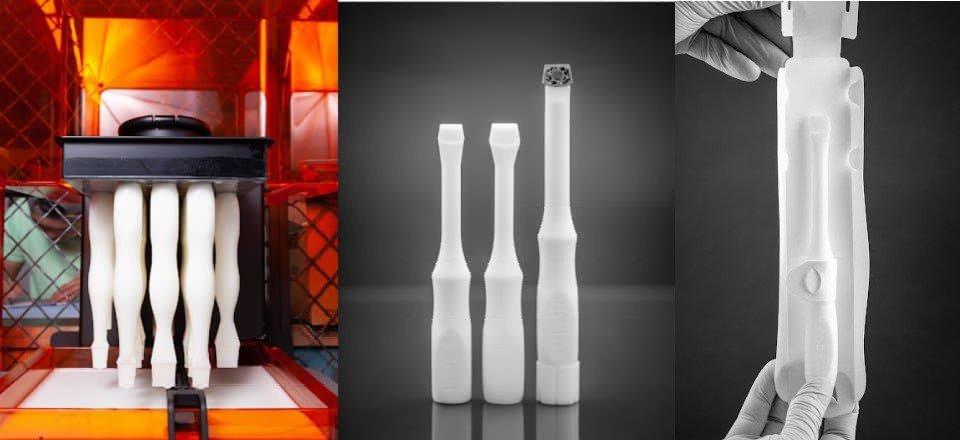
Strumenti restor3d in fase di stampa accanto alla loro forma finale.
Dieci anni fa si parlava ancora poco del forte impatto che la stampa 3D avrebbe potuto avere sul settore medico, dalla creazione di dispositivi medici avanzati a dime chirurgiche su misura per i pazienti. Sorprendentemente, restor3d è stata tra le prime aziende a sfruttare le potenzialità della stampa 3D, e ha migliorato notevolmente la fornitura di trattamenti chirurgici stampando strumenti polimerici specifici per impianti della spina cervicale.
Con una linea di produzione che conta più di 25 stampanti 3D Formlabs, i suoi team sono già al lavoro per stampare la prossima generazione di strumenti chirurgici. Per i chirurghi, l'utilizzo di questo sistema di strumenti sterili, in confezioni singole e specifici per ciascun intervento significa:
- Sostituzione dei grandi e costosi vassoi chirurgici.
- Possibilità di eseguire iterazioni dei design e introdurre rapidamente nuovi strumenti o caratteristiche a seconda delle esigenze.
- Drastica riduzione dei costi legati alla catena di fornitura e alla sterilizzazione per gli ospedali.
Accelerazione della ricerca in ambito di ingegneria tissutale
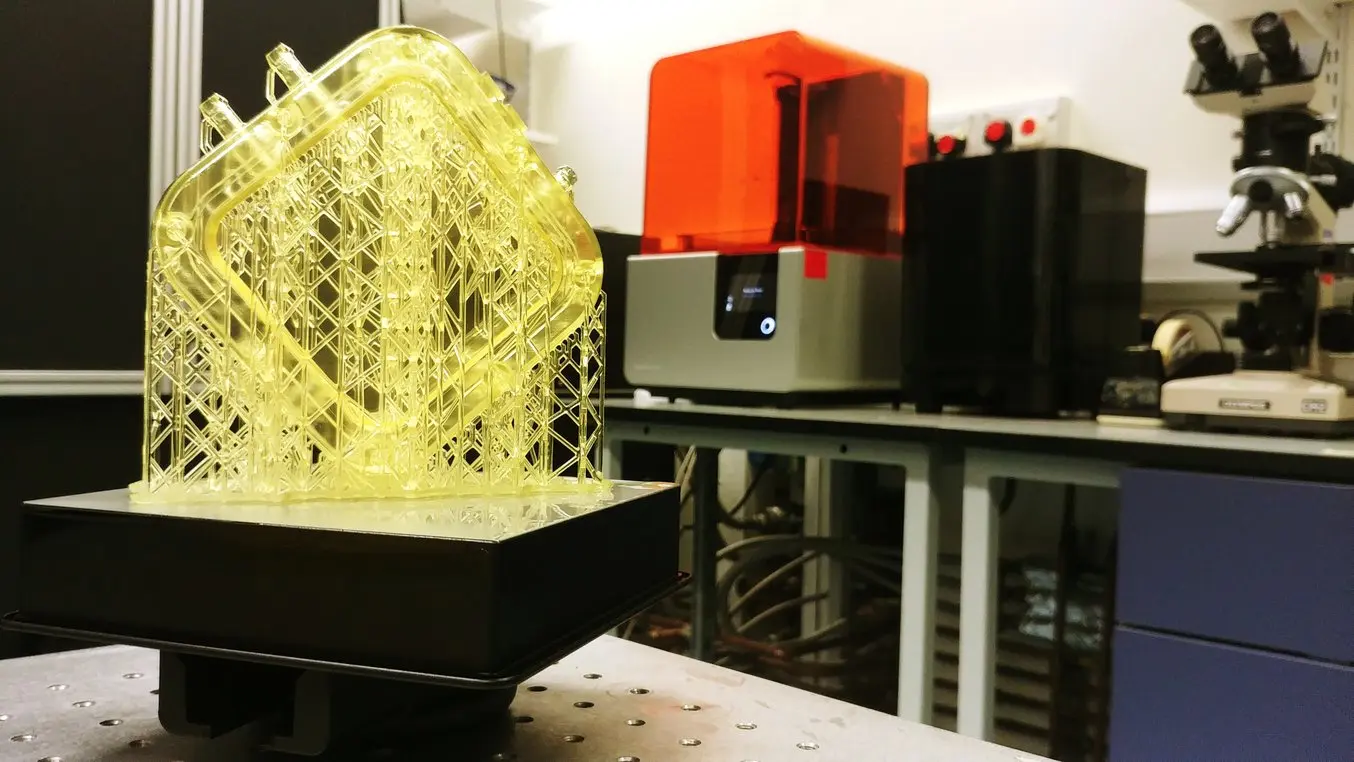
Per quanto la tecnologia di stampa 3D si sia evoluta nel corso degli ultimi anni, ci sono ancora altri casi di utilizzo ad alto impatto attualmente in fase di sviluppo, come la stampa 3D di organi.
Riuscire a creare con facilità nuovi organi è da tempo il sogno degli scienziati che lavorano nel campo della medicina rigenerativa. Sebbene ancora in fase embrionale, l'uso del flusso di lavoro 3D per produrre tessuti organici idonei al trapianto sta dando i primi frutti.
Il Dott. Sam Pashneh-Tala, ricercatore dell'Università di Sheffield, sta facendo da apripista. Per le sue ricerche usa la stampa 3D stereolitografica (SLA) desktop ad alta precisione, che permette la produzione di vasi sanguigni in un'ampia gamma di forme geometriche. Questo renderà possibile la progettazione di trapianti vascolari creati su misura per il paziente, maggiori opzioni chirurgiche e una piattaforma sperimentale per nuovi dispositivi medici vascolari dedicati alle persone affette da malattie cardiovascolari, che sono la prima causa di morte al mondo.
"La cosa più importante è che posso creare vasi sanguigni con geometrie più simili a quelle presenti nel corpo. Perciò ci sono maggiori possibilità di ottenere migliori opzioni chirurgiche e potenzialmente di consentire persino la progettazione di vasi sanguigni specifici per ogni paziente. Senza l'accesso alla precisione e all'affidabilità offerte della stampa 3D, ciò non sarebbe possibile," afferma il Dott. Pashneh-Tal.
Riportare in vita le città
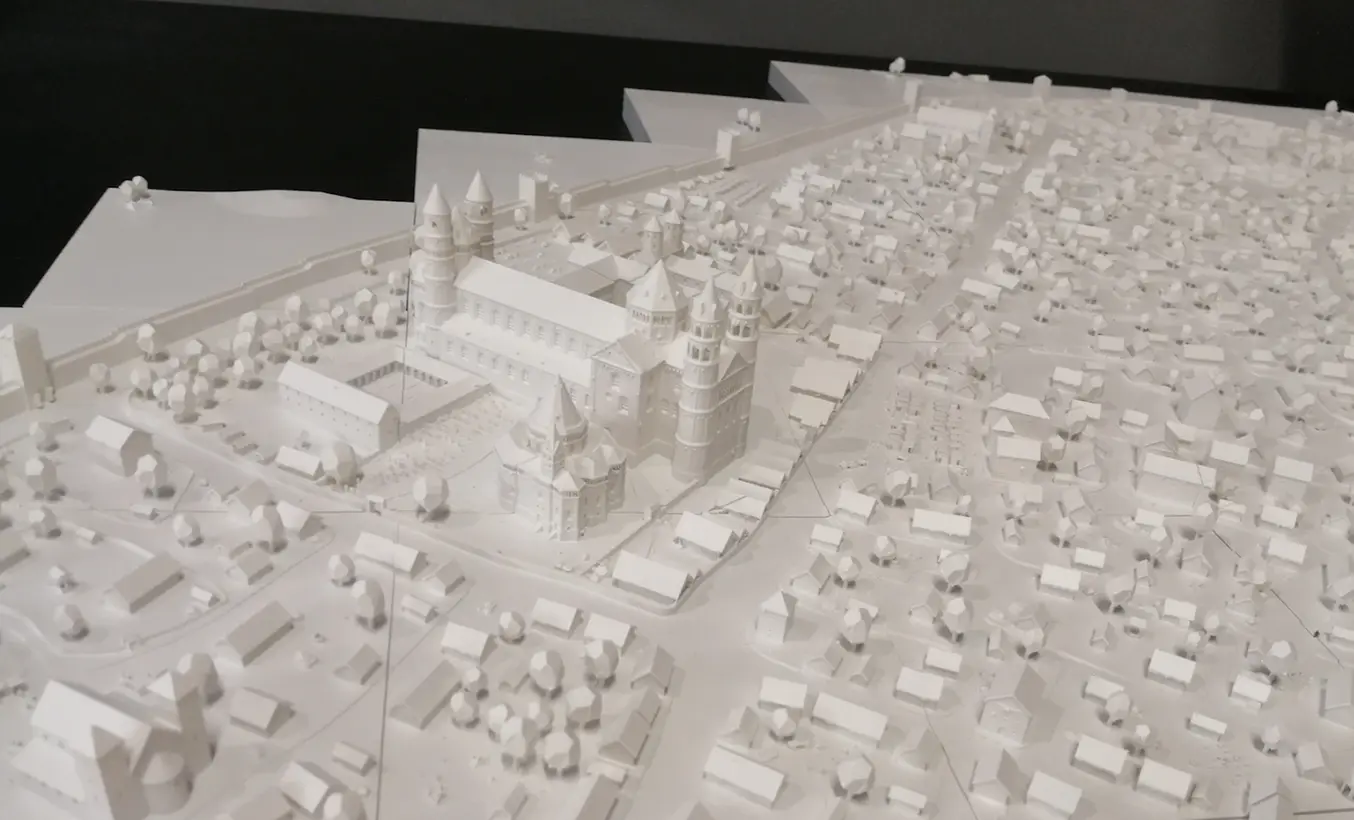
La ricostruzione delle tre città nei due diversi periodi storici ha richiesto più di 650 segmenti, ciascuno di 12x12 cm e stampato usando la White Resindi Formlabs.
Essendo un settore per sua natura fondato sul disegno geometrico, sulla prototipazione e sulla modellazione, l'architettura si appresta a trarre enormi vantaggi dai progressi della tecnologia di stampa 3D.
Oltre a ridurre i tempi di produzione del modello, i modelli stampati in 3D permettono agli architetti di prevedere con maggiore sicurezza gli effetti concreti di alcune caratteristiche di progettazione: osservando un plastico prodotto con una gamma completa di materiali, sarà possibile misurare con estrema precisione aspetti come la distribuzione della luce all'interno della struttura.
Ma il caso d'uso della stampa 3D va oltre i singoli modelli: alcune aziende stanno ricreando intere città. Come ad esempio l'Istituto di Architettura di Magonza, Università di scienze applicate (Hochschule Mainz). Il risultato è un'esposizione straordinaria in cui sono presentati sei modelli su larga scala delle città, negli anni 800 e 1250. I modelli sono costituiti da 650 parti, che sono state tutte create con la tecnologia di stampa 3D SLA.
Parti per utilizzo finale per calzature ad alte prestazioni
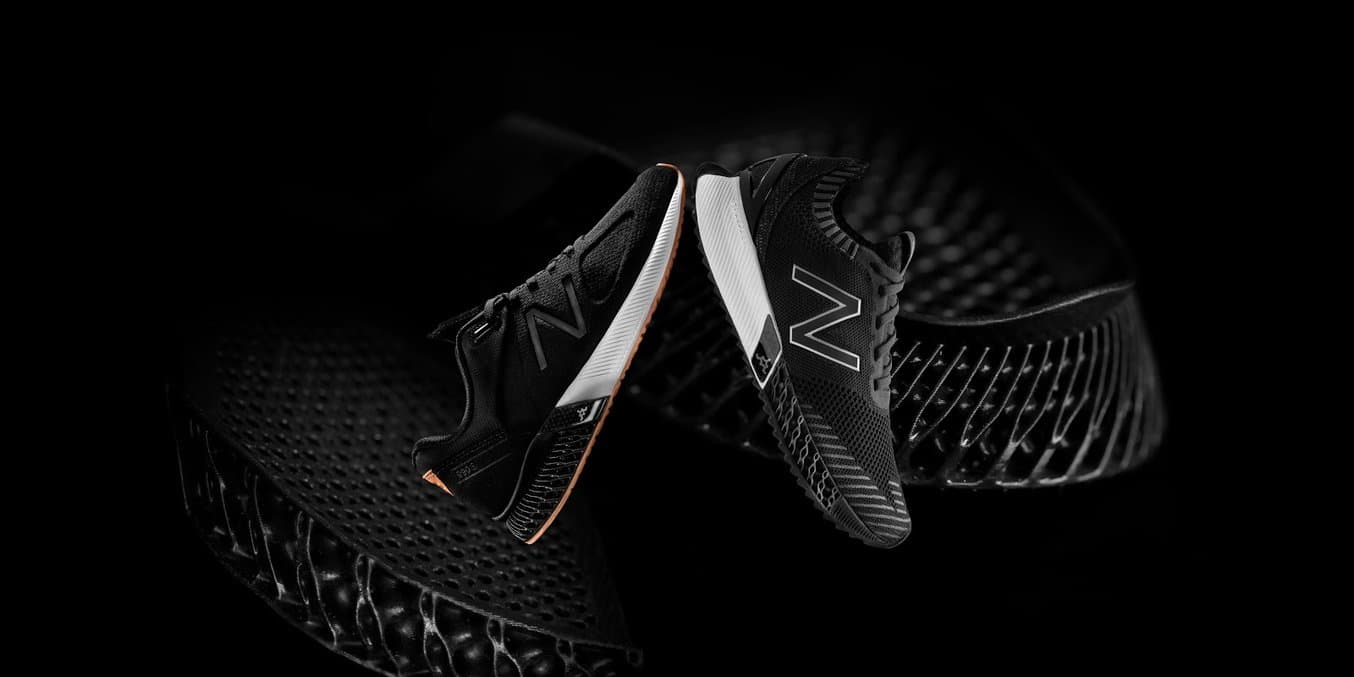
Le 990S TripleCell e le FuelCell Echo Triple.
Il settore delle calzature sportive si affida da tempo alla tecnologia per ottimizzare le prestazioni dei propri prodotti e ora, con l'avvento del workflow digitale, ha a disposizione ulteriori opzioni di personalizzazione.
Alcuni grandi marchi come New Balance, Adidas e Nike, avendo riconosciuto il potenziale della produzione additiva, intendono produrre in massa intersuole personalizzate a partire da materiali stampati in 3D. Come in altri settori, il workflow digitale affiancherà i metodi tradizionali di produzione: i componenti essenziali e altamente personalizzati di ciascun prodotto saranno affidati alla stampa 3D, mentre i rimanenti saranno realizzati secondo le tecniche convenzionali.
New Balance produce calzature dalle proprietà uniche, per questo ha collaborato con Formlabs per creare un materiale di stampa personalizzato in grado di resistere all'usura quotidiana a cui va incontro una scarpa sportiva. I materiali per calzature devono affrontare una varietà di ambienti, a cui va aggiunta la necessità di resistere a diversi livelli di pressione migliaia di volte al giorno. La Rebound Resin è progettata per creare strutture reticolari elastiche e resilienti, con un ritorno di energia, una resistenza alla lacerazione e un allungamento molto superiori agli altri materiali di Formlabs. La Rebound Resin è abbastanza resistente da poter essere utilizzata in guarnizioni e interni per auto, ma è abbastanza leggera e flessibile per l'uso nella suola di una scarpa.
"Una delle cose di cui siamo davvero orgogliosi è il fatto che questo prodotto offre ai corridori un'esperienza davvero differente."
Katherine Petrecca, direttrice generale del dipartimento calzature presso l'Innovation Design Studio di New Balance
Reinventare la narrativa moderna
La stampa 3D ha già trovato il proprio posto all'interno della produzione cinematografica hollywoodiana ed è ampiamente utilizzata per effetti visivi e costumi.
Se una volta la realizzazione di fantastiche creature immaginarie presupponeva un minuzioso lavoro manuale, la crescente pressione e le tempistiche stringenti imposte dalla moderna industria cinematografica hanno portato allo sviluppo di un metodo più rapido per la creazione di tali effetti. Gli studi di progettazione ed effetti visivi come Aaron Sims Creative ora usano un approccio ibrido basato sulla realizzazione di effetti concreti potenziati poi dal workflow digitale, in modo da creare nuove opportunità di collaborazione e ridurre i tempi di consegna necessari per dare vita ai progetti.
“Il Demogorgone è stato una delle prime stampe che abbiamo realizzato usando le nostre stampanti 3D Formlabs, e siamo rimasti sbalorditi. Prima di allora avevamo sempre esternalizzato le stampe. L’abilità di stampare in-house e vedere il design che avevamo contribuito a creare fin dall’inizio prendere forma davanti ai nostri occhi è stata una sensazione incredibile. È stato come tornare ai tempi in cui scolpivamo i personaggi nella creta,” ha dichiarato Aaron Sims.
Un tipo diverso di danza e musica
Il potenziale artistico della stampa 3D non si limita al mondo delle opere d'arte fisiche, ma ha il potere di svelare dimensioni totalmente nuove ad altre forme d'arte come la danza e la musica. Grazie alla libertà di design che offre la stampa 3D è possibile modificare o creare strumenti unici o molto complessi partendo da zero, a una frazione del costo degli strumenti prodotti in maniera tradizionale.
Essendosi conservata nei secoli senza grandi cambiamenti, la forma del violino è nota a tutti. La sua musica si è evoluta a un punto tale che lo strumento ha acquisito uno status quasi leggendario nella nostra cultura. Brian Chan, ingegnere di Formlabs, ha voluto creare un violino acustico perfettamente funzionante usando la White Resin su una stampante 3D di Formlabs.
Restauro artistico: riportare in vita pezzi di storia
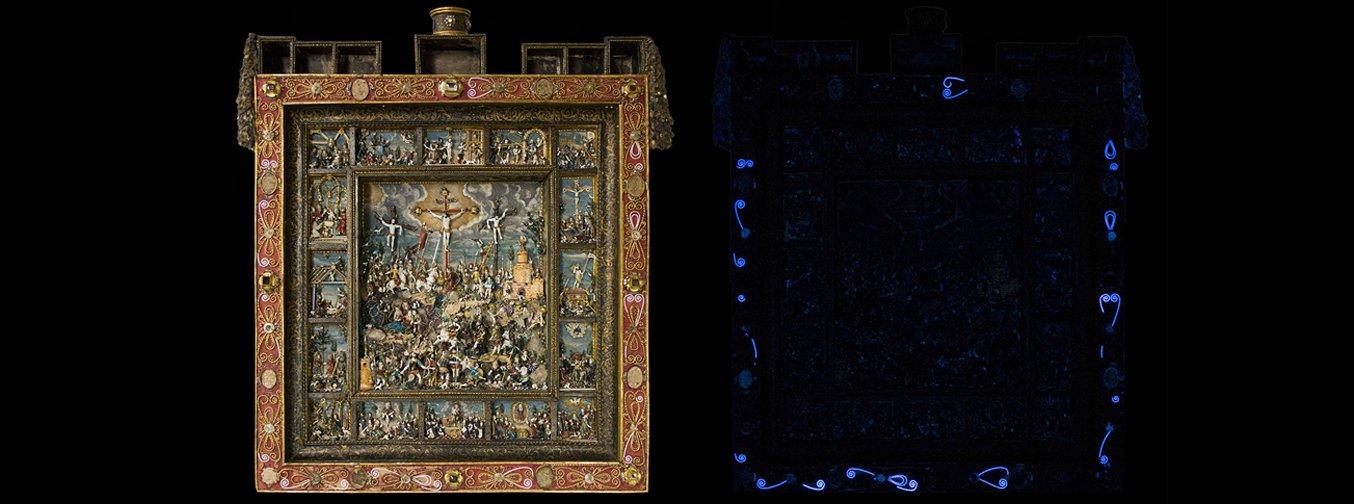
La scansione 3D, i programmi CAD e la stampa 3D hanno consentito di restaurare i lavori di alcuni tra i più grandi artisti della storia, riportando le opere di Michelangelo e Da Vinci alla loro bellezza originaria.
I progetti di restauro artistico possono essere migliorati combinando la stampa 3D e la scansione 3D, due potenti tecnologie che permettono ai modellisti di prendere un oggetto fisico, trasformarlo in una forma tridimensionale, modificarlo o restaurarlo e infine ristamparne le parti.
Mattia Mercante usa la riproduzione 3D per sostituire pezzi mancanti di sculture e altre opere d'arte presso la rinomata fondazione Opificio di Firenze, permettendo quindi ai visitatori del museo di vedere le opere d'arte così come erano state immaginate dagli artisti.
Per un reliquiario del XVII secolo, Mattia Mercante ha usato uno scanner 3D a luce strutturata HP per scansionare i complessi dettagli della cornice, che erano rimasti intatti in altre parti dell'oggetto, e ha poi riprodotto i pezzi mancanti con una stampante 3D di Formlabs. Le parti stampate sono quindi state verniciate in modo da apparire identiche alle decorazioni originali. E la cosa più sorprendente è che questo intervento di restauro ha richiesto una modellazione CAD minima ed è stato completato in modo rapido ed economico rispetto alla lavorazione manuale.
Piani, crani e valigie: risolvere il delitto perfetto
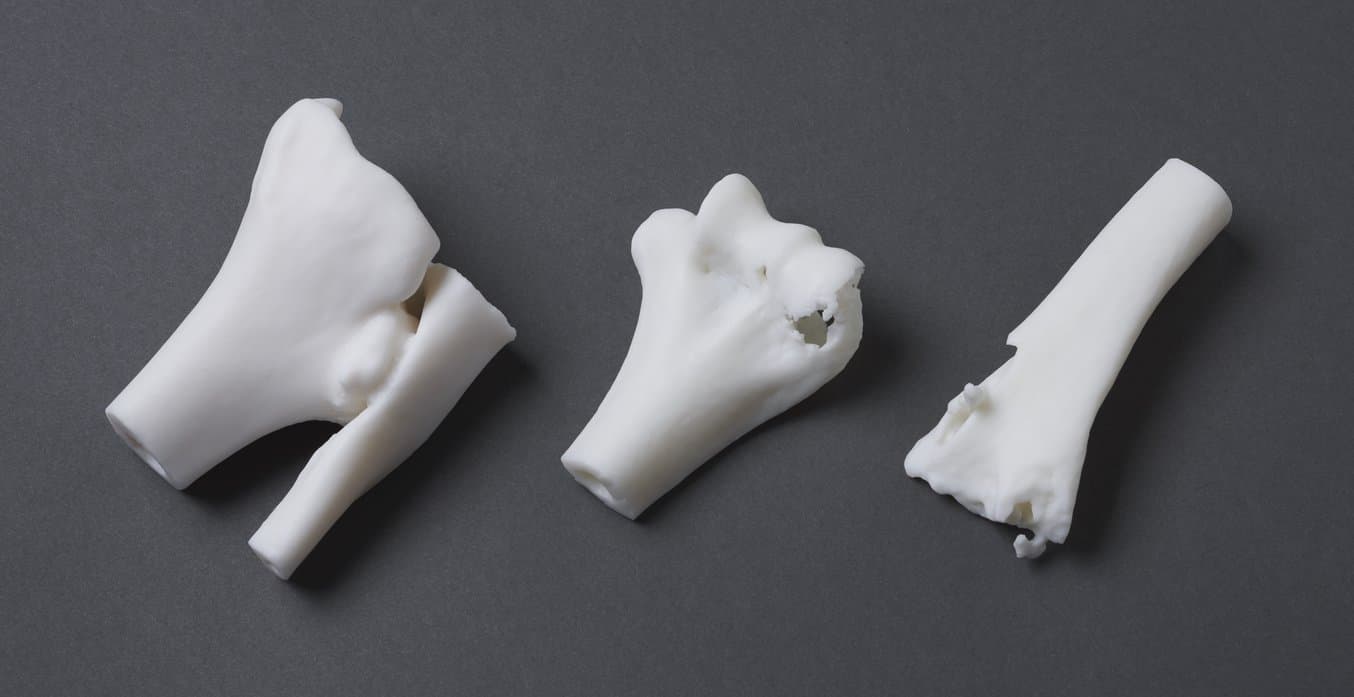
L'utilità potenziale della stampa 3D non si esprime solo in termini di produzione, ma anche di ricostruzione. Il lavoro dei periti legali è spesso complicato dall'assenza di prove esaurienti. Le tecnologie digitali possono rivelarsi estremamente utili durante le inchieste legali e facilitare il lavoro di ricostruzione di modelli accurati delle persone indagate o delle vittime.
In questo caso, il workflow digitale consiste nel convertire TAC in stampe 3D destinate al processo di identificazione. Ad esempio, se gli investigatori riescono a reperire come prova solo una parte di un cranio, una stampante può modellare e replicare il campione completo.
Le ricostruzioni dell'aspetto delle vittime hanno già svolto un ruolo chiave nel conseguimento della giustizia, dimostrando ancora una volta l'utilità della stampa 3D non solo in termini di design ed efficienza produttiva.
Così come la stampa 3D può essere usata per la pianificazione preoperatoria, le TAC delle vittime di un crimine possono aiutare i detective a osservare le ossa più da vicino. I dati ottenuti dalle TAC digitali e dalle radiografie eseguite sui resti possono essere usati per produrre repliche in 3D di varie parti del corpo. In seguito, il medico legale sarà in grado determinare le circostanze esatte di un crimine, dal numero di partecipanti al tipo di arma usata.
Come costruire protesi migliori
L'impatto della stampa 3D non si limita a migliorare i workflow o a consentire la prototipazione rapida, ma può anche cambiare la vita delle persone in modo diretto. Al mondo ci sono 30 milioni di persone in attesa di tutori e arti artificiali; la speranza è che la stampa 3D riesca a fornire nuove soluzioni fino a oggi ostacolate da fattori quali il costo e la specificità.
La stampa 3D può rappresentare un'alternativa economica in grado di fornire, come in altri casi di medicina, una soluzione su misura che sappia rispondere in modo più mirato alle esigenze dei pazienti. L'accessibilità e la personalizzazione delle tecniche di stampa 3D possono cambiare in modo radicale la qualità della vita di coloro che presentano lesioni o disabilità, come nella storia di questo padre e di suo figlio.
Abbiamo visto questo tipo di innovazione in prima persona con Matej e suo figlio Nik, affetto da paralisi cerebrale. Matej si fissò un semplice obiettivo: permettere a Nik di camminare. Sono seguiti mesi di ricerca e sviluppo, da cui sono nate delle ortesi su misura stampate in 3D, che forniscono supporto e correzione esattamente dove Nik ne ha bisogno, consentendogli così di muovere i primi passi in maniera indipendente. Guarda il video completo sopra e leggi la loro storia.
Oltre a protesi in grado di ripristinare la funzionalità di un arto, è possibile stampare in 3D dispositivi che, da un certo punto di vista, sono migliori degli arti che devono sostituire. Grazie alla stampa 3D, le parti del corpo bioniche non saranno più un concetto futuristico, ma l'ultima frontiera della produzione protesica. Alcune aziende, come Psyonic, hanno già iniziato a produrre protesi avanzate.
Nuovi tipi di abitazioni ed edilizia
Alcune persone pensano che la stampa 3D serva esclusivamente a produrre articoli di piccole dimensioni che possono essere afferrati con una mano. Ma di recente le aziende hanno sviluppato workflow additivi su scala industriale in grado di produrre componenti funzionali molto più grandi. Negli ultimi anni sono state avviate diverse iniziative per la creazione di case e altre grandi strutture interamente costruite per mezzo della stampa 3D, aprendo nuove frontiere nel campo delle abitazioni e dell'edilizia sostenibile.
La tecnica di stampa 3D dona agli architetti la libertà di sperimentare con le forme, anche quando si tratta di materiali edili fino a oggi risultati meno malleabili come il calcestruzzo. In generale, consente di costruire case totalmente eco-sostenibili ed efficienti sotto il profilo energetico, secondo i moderni canoni di comfort. In questo modo l'edilizia può evitare del tutto gli sprechi e diventare meno costosa rispetto ai metodi tradizionali, riducendo anche l'impatto sull'ambiente.
Probabilmente dovrai aspettare ancora un po' di tempo prima di poterti trasferire in una casa stampata in 3D, ma puoi comunque vedere in prima persona alcuni progetti edili realizzati con una stampante 3D. Il ponte MX3D di Amsterdam è attualmente aperto al traffico pedonale. Secondo dezeen.com, "per la struttura sono stati necessari 4500 kg di acciaio inossidabile, che è stato stampato in 3D da robot nell'arco di sei mesi, prima di essere trasportato nella sua posizione sopra il canale con una gru".
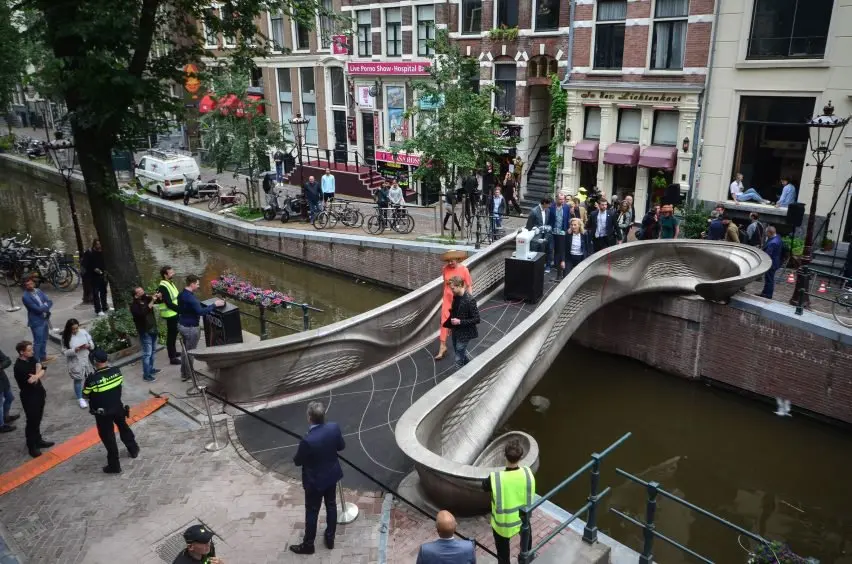
Fonte: www.dezeen.com
Una grande spinta alla corsa allo spazio
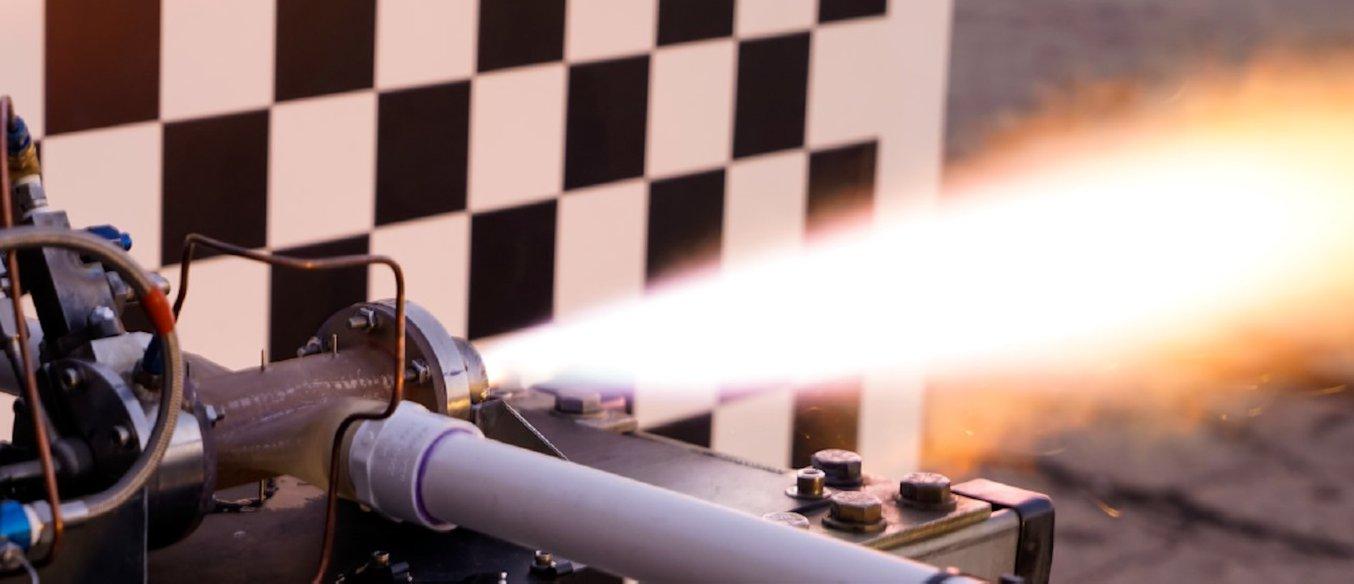
Con una delle maggiori barriere all'ingresso tra le industrie mondiali, i viaggi spaziali sono ormai pronti per l'applicazione delle innovazioni di stampa 3D. La riduzione dei costi di prototipazione per strumenti e macchine costose e specifiche per lo spazio permetterà alle piccole aziende di risparmiare e dare il loro contributo all'innovazione in ambito aerospaziale.
La startup aerospaziale Relativity Space ha eseguito diversi test per la creazione di motori a razzo in alluminio usando la produzione additiva. In caso di esito positivo, questa applicazione ridurrebbe in modo netto i costi e le difficoltà pratiche dei viaggi spaziali, aprendo la strada a nuove possibilità commerciali e a un vasto potenziale di crescita.
Masten Space System è un'altra azienda che, grazie alla stampa 3D, ha innovato il settore aerospaziale: fondata nel 2004, è specializzata in missilistica e in particolare nel decollo e nell'atterraggio verticale. L'azienda lancerà una missione lunare nel 2022 come parte del progetto Commercial Lunar Payload Services (CLPS) della NASA. Masten ha utilizzato le stampanti 3D di Formlabs per produrre motori di razzi in plastica per svolgere test in ambito di ricerca e sviluppo.
Inoltre, ha sperimentato la stampa 3D sia con le plastiche sia con i metalli, arrivando persino a sviluppare nuovi metalli personalizzati per il progetto Tipping Point della NASA. "Siamo davvero soddisfatti dei motori per razzi stampati in 3D, perché possiamo fare molte cose che non sarebbero possibili con il processo di produzione tradizionale. Per ridurre i costi e aumentare l'efficacia, abbiamo iniziato a pensare a come utilizzare le stampanti stereolitografiche, specialmente dopo il lancio della Ceramic Resin e della High Temp Resin. Questi materiali hanno delle proprietà ingegneristiche davvero interessanti ed eravamo curiosi di scoprire se fosse possibile usarli in un razzo," ha affermato Matthew Kuhns, ingegnere capo di Masten.
La High Temp Resin e la Rigid 10K Resin di Formlabs sono esempi di materiali con proprietà ingegneristiche ottimali per applicazioni aerospaziali. La High Temp Resin è progettata per la prototipazione funzionale in applicazioni a calore elevato, mentre la Rigid 10K Resin è il materiale più rigido del nostro catalogo per l'ingegneria, il che la rende adatta per prototipi di qualità industriale.
Trasformare il design generativo in realtà
Ildesign generativo è l'ultima frontiera della progettazione CAD per i team ingegneristici che lavorano in modo virtuale in tutti i settori della produzione. Sfrutta il potere dell'intelligenza artificiale (AI) per sviluppare nuove iterazioni di design ad alte prestazioni che contribuiscono a risolvere sfide complesse, a ridurre il peso dei componenti e i costi di produzione, a incrementare la personalizzazione e a ottimizzare le prestazioni.
Con la stampa 3D è possibile creare oggetti organici e complessi dalle proprietà eccellenti. Con un'ampia gamma di proprietà dei materiali pensate per applicazioni aziendali specifiche, preparati a vedere strutture di design senza precedenti. I team ingegneristici possono servirsi dell'intelligenza artificiale per scoprire e testare nuove iterazioni di design complessi in modo rapido ed efficiente e su larga scala, riducendo drasticamente i tempi di ricerca e sviluppo per i nuovi prodotti. Successivamente, con la loro stampante 3D in-house, possono produrre la forma complessa, toccarla con mano e ispezionarla.
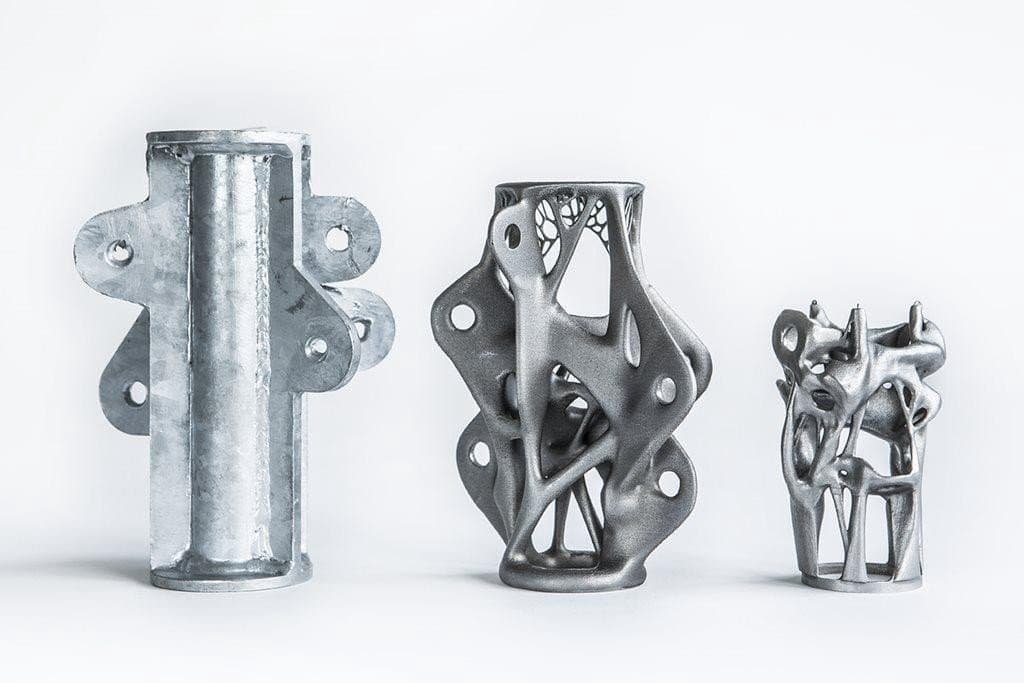
Attacchi e supporti in cui le forze in gioco sono ben definite sono le parti più comuni per cui ci si serve del design generativo.
Vuoi saperne di più sul design generativo? Guarda il nostro webinar gratuito e scoprirai: perché vedi così tante staffe quando cerchi "design iterativo" su Google, come impostare un problema di progettazione in Fusion 360 di Autodesk, come un'azienda è riuscita ad alleggerire del 40% la staffa di una sedia a rotelle usando un processo di design iterativo per la prima volta e molto altro.
Formare la forza lavoro di domani
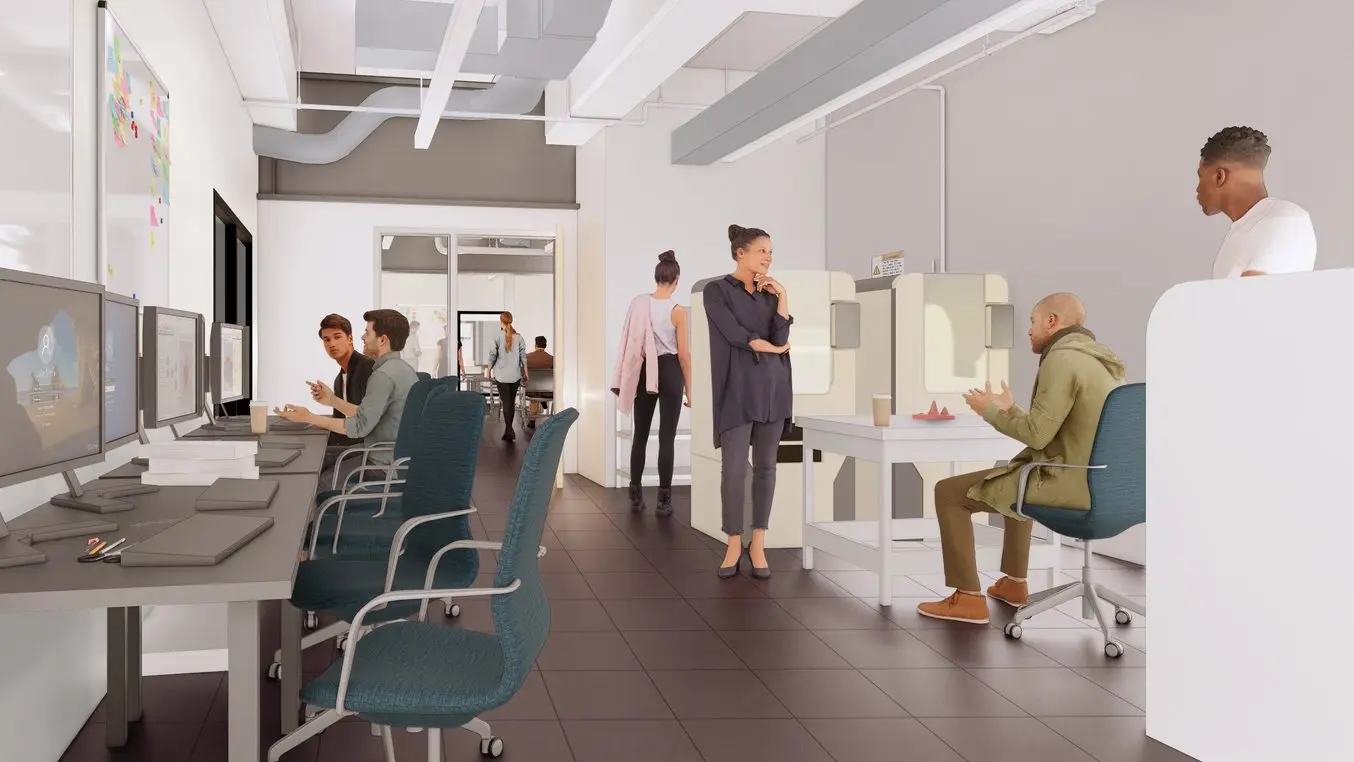
Origin Labs, all'interno del suo polo per l'innovazione, avrà un'area dedicata alla stampa 3D per gli studenti e i membri della comunità.
La maggior parte degli istituti di educazione superiore si dedica alla preparazione degli studenti affinché diventino la forza lavoro del futuro. La Pennsylvania State University pensa anche alla forza lavoro attuale, e ha recentemente investito milioni di dollari per la costruzione del polo per l'innovazione dedicato a Eric J. Barron, aperto sia agli studenti sia ai membri della comunità universitaria.
La catena montuosa degli Appalachi, nella Pennsylvania occidentale e centrale, è sempre stata il principale centro dell'industria carboniera del Paese e per questo ha goduto di un'economia solida e prospera nella prima metà del ventesimo secolo. Quando quest'attività è stata dismessa, la regione degli Appalachi ne ha sofferto molto e il tasso di disoccupazione è aumentato, facendo sì che i redditi delle famiglie fossero tra i più bassi del Paese, come riportato dalla Appalachian Regional Commission.
Negli ultimi due decenni, la dirigenza a livello locale e statale ha cercato di cambiare la situazione tramite investimenti nei settori della produzione, dell'educazione e della tecnologia. La Appalachian Regional Commission offre borse di studio per un valore totale di un milione di dollari per "supportare le opportunità educative e le istituzioni, in particolare coniugando lo sviluppo delle competenze e la formazione della forza lavoro con gli interessi e le opportunità delle aziende locali e regionali".
Mentre la produzione additiva si espande rapidamente nelle aziende (come abbiamo visto in questo articolo di blog), i responsabili delle assunzioni si dedicano alla ricerca di impiegati formati per lavorare con le tecnologie digitali e con una buona padronanza della progettazione CAD. Anche le università stanno cercando di rispondere a questa esigenza di mercato, e per questo hanno iniziato a creare poli per l'innovazione spaziosi e sostenuti da finanziamenti adeguati.
Miglioramento dei programmi d'insegnamento tradizionali
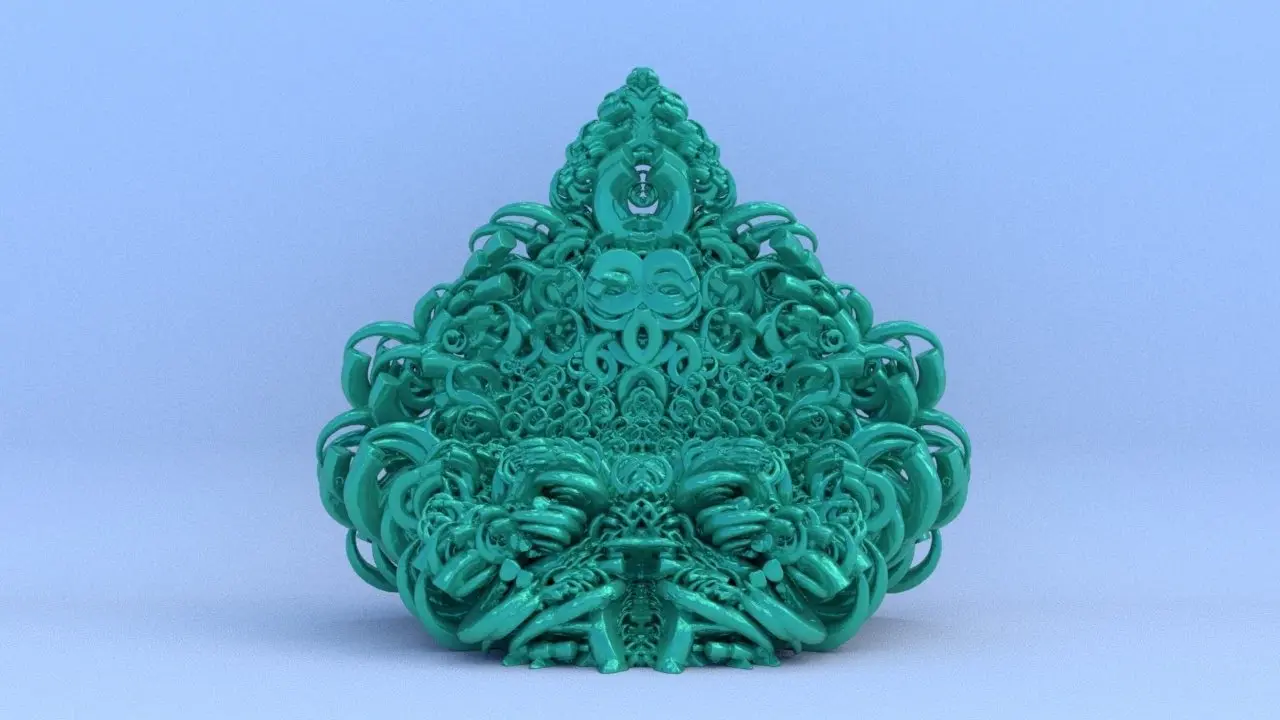
Oltre a formare la forza lavoro di domani in materia di progettazione CAD e stampa 3D, le università hanno anche iniziato a focalizzarsi sui vantaggi della stampa 3D in un'ampia gamma di discipline educative.
Alla UMass Lowell questo si è tradotto nella modernizzazione dei corsi di scultura e design 3D per aggiornarli al ventunesimo secolo. Ed è stato proprio questo il ruolo di Yuko Oda, che lavora nell'ateneo dal 2017 e che, non appena arrivata, ha ordinato una serie di stampanti 3D, tra le quali un apparecchio SLA Formlabs.
Yuko riesce a portare in aula la sua passione per l'arte e la tecnologia e attualmente insegna scultura, modellazione e animazione 3D, nonché media interattivi. La maggior parte degli studenti sa di dover comprendere l'animazione e la modellazione 3D per la futura carriera in vari campi, tra cui il design di sculture per il cinema. Per gli artisti, la modellazione 3D è diventata una competenza essenziale.
"Gli studenti realizzano un modello scolpito in 3D, lo importano in Zbrush e poi lo stampano in varie resine, tra cui la Clear Resin. La capacità delle macchine Formlabs di mostrare dettagli elaborati che sono stati modificati in Zbrush è a un livello di gran lunga superiore rispetto a quello delle altre stampanti in laboratorio."
Yuko Oda
Uno degli sviluppi più promettenti nella scultura è l'integrazione della stampa 3D e della realtà virtuale (VR). Questo è particolarmente importante per gli studenti che hanno difficoltà con il design 3D. La realtà virtuale riduce sempre più le barriere del design 3D e permette ad artisti e studenti di creare con le proprie mani utilizzando programmi come Oculus Medium. Yuko ha insegnato ad alcuni studenti delle scuole medie a creare un oggetto in 3D in 30 minuti con la realtà virtuale e poi a stamparlo con una stampante 3D. Anche per gli scultori più esperti, la realtà virtuale riduce il tempo necessario per passare dall'idea all'oggetto fisico, aprendo potenzialmente nuove strade all'arte sperimentale.
Salvataggio di un uccello a rischio di estinzione
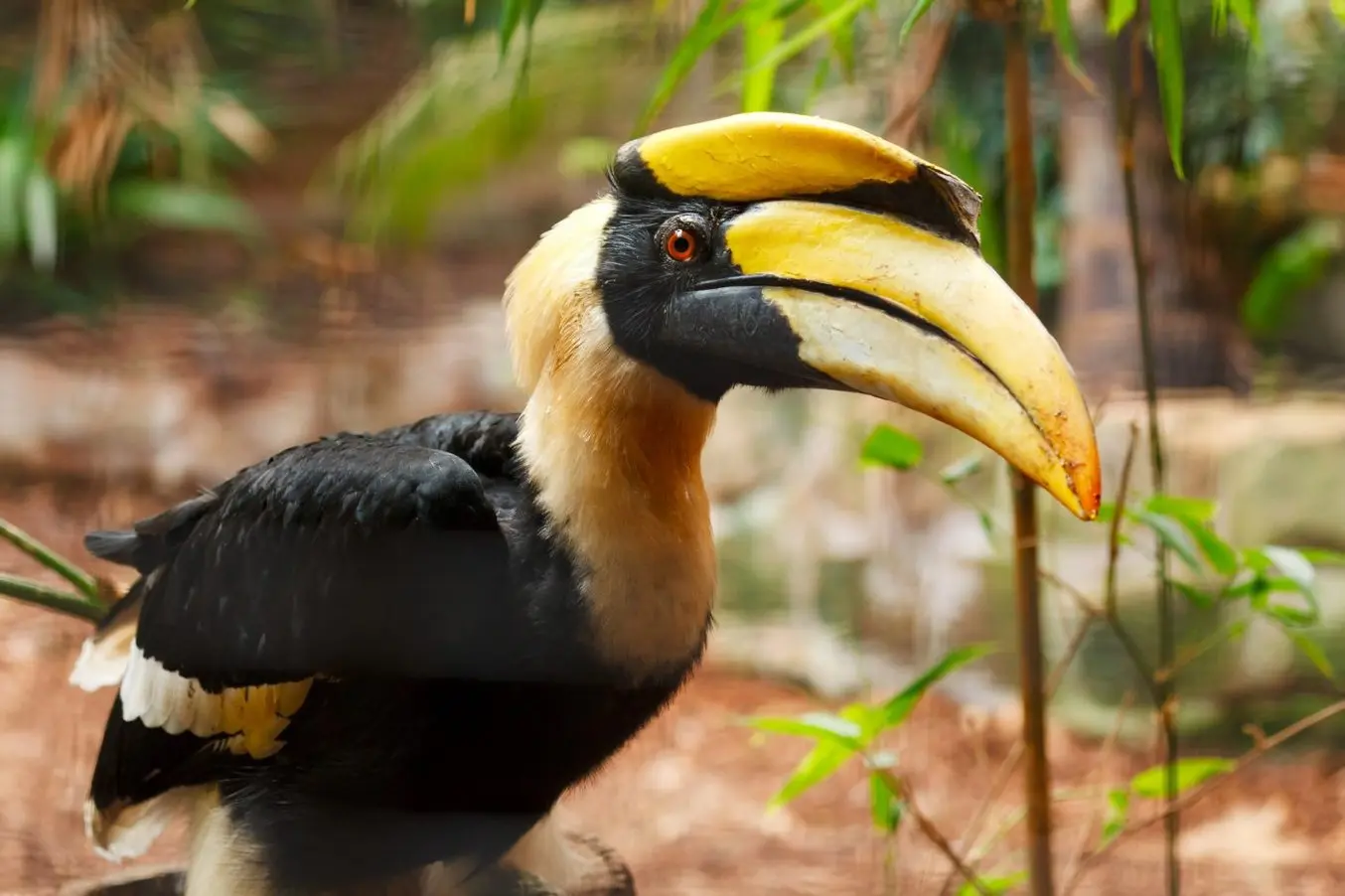
Nel corso di un controllo di routine su un bucero maggiore di 25 anni, i custodi dello ZooTampa hanno scoperto una lesione alla base dell'elmo dell'uccello, ovvero la parte di colore giallo che assomiglia a un casco e che si trova sulla testa del volatile. Ulteriori esami di approfondimento hanno stabilito che Crescent, questo è il nome dell'uccello, aveva un cancro potenzialmente fatale.
Il cancro, individuato vicino al cranio, non poteva essere rimosso, in quanto ospitava parte dei seni paranasali dell'uccello. Il team ha cercato di capire se fosse possibile rimuovere l'elmo e sostituirlo con una riproduzione stampata in 3D e realizzata appositamente per il volatile. Protesi e dispositivi su misura per i pazienti sono già stati utilizzati in passato per interventi sull'uomo, ma mai su buceri maggiori. Sarebbe possibile un intervento di questo tipo? E se sì, quali sono i materiali più sicuri per l'animale?
Lo ZooTampa afferma che il "becco sostitutivo" stampato con successo in 3D è stato realizzato con la BioMed White Resin. Si tratta di un materiale bianco opaco per applicazioni biocompatibili destinate al contatto a lungo termine con la pelle o a breve termine con le mucose. Questo materiale per uso medico è unico all'interno del catalogo di materiali Formlabs per la stampa 3D SLA, in quanto è adatto per il contatto a breve termine con tessuti, ossa e dentina.
Come risolvere i problemi della catena di fornitura
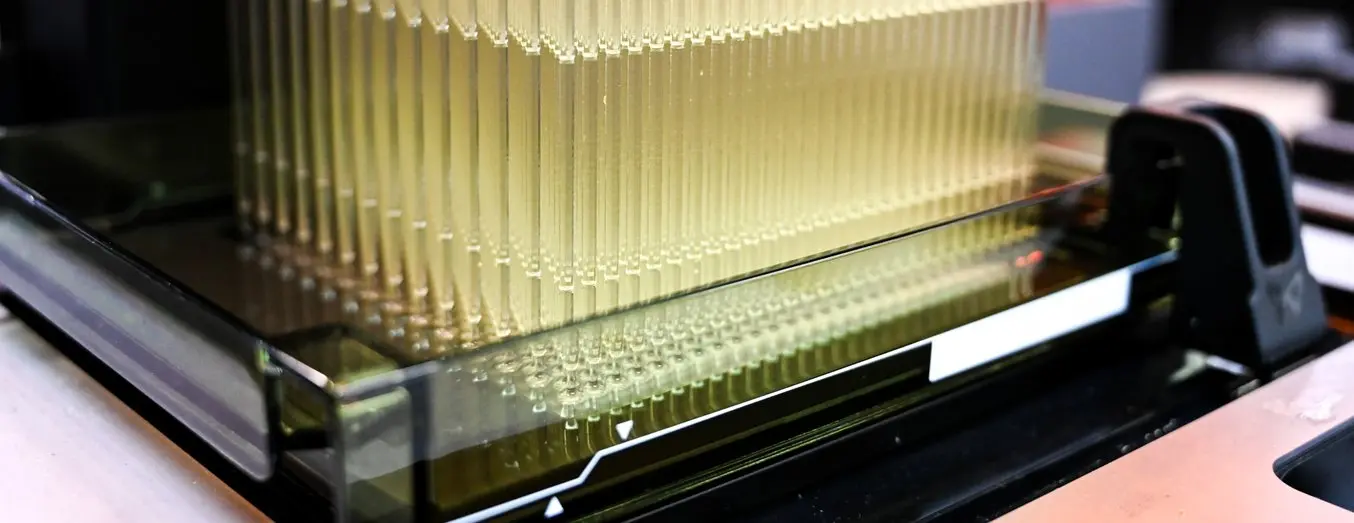
Durante la pandemia di COVID-19 e in seguito alla crisi delle catene di fornitura del biennio 2021/22, molte aziende si sono rivolte alla stampa 3D per mantenere le macchine in attività e far sì che i prodotti continuassero a uscire dagli stabilimenti di produzione. L'uso diffuso della stampa 3D in-house per la creazione di parti per utilizzo finale, come parti sostitutive per macchine, ha reso la produzione additiva uno strumento fondamentale per affrontare i problemi legati alla catena di fornitura.
Formlabs ha commissionato il Rapporto 2022 sulle applicazioni della stampa 3D per comprendere meglio se e cosa è cambiato di recente tra gli utenti della stampa 3D. Il rapporto dimostra come la stampa 3D sia passata dall'essere uno strumento destinato alla prototipazione e ad attività di ricerca e sviluppo a essere considerata una tecnologia di produzione irrinunciabile, necessaria per soddisfare le esigenze in continua evoluzione dei clienti e per superare i problemi della catena di fornitura. Che serva per risolvere i problemi della catena di fornitura, creare prodotti in numeri limitati o personalizzare dispositivi, le aziende si sono trovate a dover rivedere il loro metodo di produzione per soddisfare le richieste dei clienti.
Stampa 3D di stampanti 3D
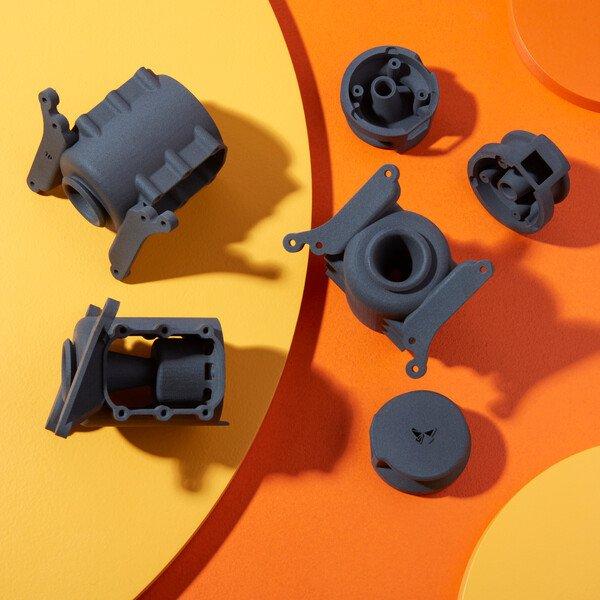
Parti per utilizzo finale stampate con la Fuse 1.
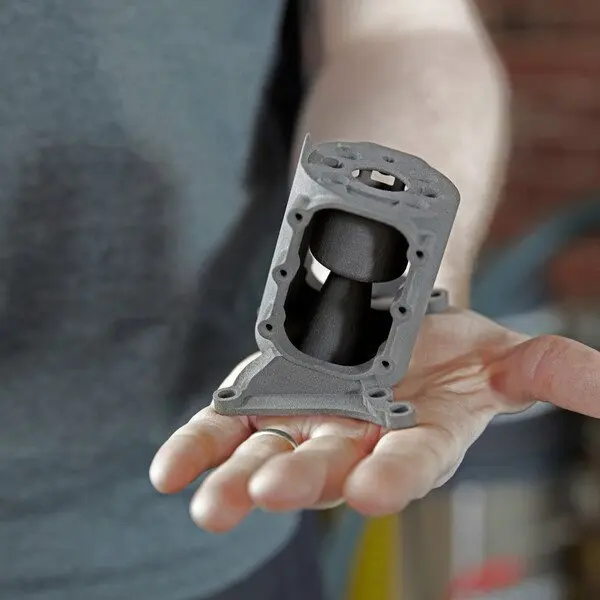
Uno spurgo per sensore IR stampato sulla Fuse 1 con la Nylon 12 Powder.
La costruzione di stampanti 3D è una vera e propria sfida ingegneristica. Ci sono voluti anni di progettazione e ingegneria per riuscire a implementare prestazioni di livello industriale in un apparecchio desktop a un prezzo accessibile. Questo è stato il caso della stampante 3D a sinterizzazione laser selettiva (SLS) di Formlabs, la Fuse 1.
Uno degli strumenti usati dagli ingegneri di Formlabs per realizzare i prototipi delle parti è stata proprio la Fuse 1. Ma l’uso della stampa 3D non si è limitato alla prototipazione. Oggi, ogni unità Fuse 1 spedita ai clienti contiene diverse parti di produzione stampate direttamente sulla Fuse 1 utilizzando la Nylon 12 Powder.
L'utilizzo della stampante SLS Fuse 1 per la prototipazione e la creazione di parti per utilizzo finale ha comportato principalmente tre vantaggi, come ci racconta Seth Berg, l'ingegnere responsabile dello sviluppo della Fuse 1:
- Libertà di progettazione nel creare parti complesse senza strutture di supporto interne.
- Accorciamento della catena di fornitura mediante la prototipazione e la creazione in-house di parti per utilizzo finale.
- Eliminazione dell’esternalizzazione e creazione di una soluzione conveniente per la produzione di piccoli lotti con un materiale in Nylon 12 Powder collaudato e versatile.
Per scoprire come il team è riuscito a fare tutto ciò, e quali parti per utilizzo finale ha prodotto sulle stampanti 3D, guarda il seguente video.
Materiali per l'emergenza COVID-19: tamponi nasali
A maggio 2020, Forbes ha pubblicato un articolo dal titolo: In che modo la stampa 3D aiuterà gli Stati Uniti a contrastare la scarsità di tamponi per il COVID-19. Come riportato, aziende specializzate nella stampa 3D come Formlabs, HP, Origin, Carbon, Desktop Metal e molte altre hanno fatto fronte comune per affrontare la carenza di tamponi e ne hanno incrementato la produzione.
L'impatto della pandemia ha richiesto una risposta ben pianificata e globale. Grazie alla collaborazione con USF e Northwell, Formlabs ha ideato una soluzione che è stata utilizzata in tutto il mondo. Con un design accessibile, un'attrezzatura poco costosa e processi collaudati, la progettazione del tampone ha consentito la realizzazione di oltre 40 milioni di test COVID in 25 Paesi. Durante l'ultimo anno, le stampanti 3D di Formlabs sono state usate senza sosta dai governi e dagli organi sanitari per migliorare i test e la cura dei pazienti. Questa soluzione globale è semplicemente un esempio di come l'agilità della stampa 3D possa essere utile a livello pubblico.
A Singapore questa soluzione ha toccato livelli mai visti: la Eye-2-Eye Communications, infatti, ha incrementato la produzione di tamponi per mantenere i cittadini al sicuro, superando le 30 000 unità al giorno.
"Si è trattato di un'opportunità eccellente per presentare i vantaggi della stampa 3D in ambito di progettazione rapida e sviluppo, ma non solo. Formlabs ha dimostrato una capacità davvero formidabile di produrre in massa in brevissimo tempo. Inoltre, visti i picchi di casi in tutto il mondo, è rassicurante sapere che, se necessario, possiamo incrementare la produzione in modo relativamente semplice per soddisfare la domanda," afferma Miles Podmore, amministratore delegato di Eye-2-Eye Communications.
Produzione agile: parti personalizzate e per il mercato post-vendita
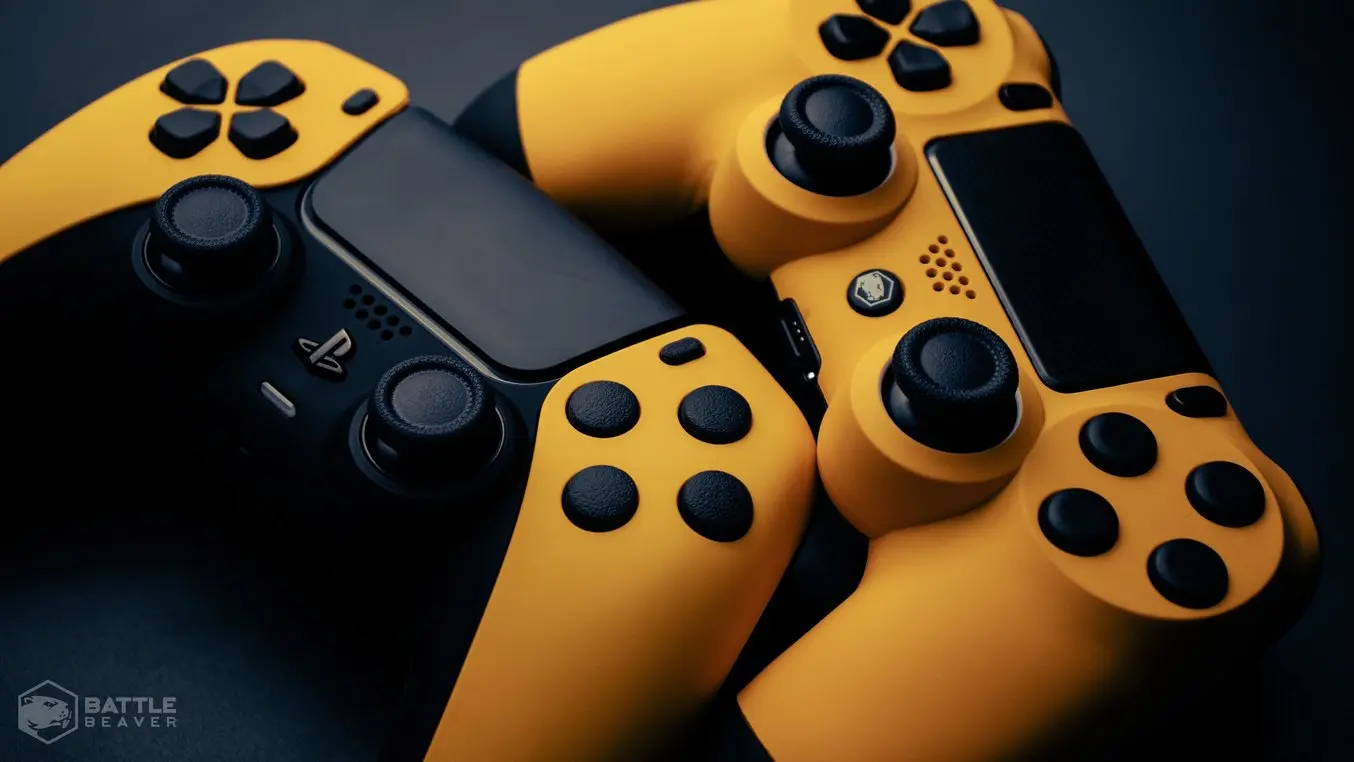
Un controller con pulsanti stampati con la Fuse 1 (a sinistra) e un altro con tasti realizzati tramite stampaggio a iniezione (a destra).
Un problema legato alla creazione di parti per il mercato post-vendita è che questi ordini hanno solitamente volumi ridotti e devono evolversi in risposta agli aggiornamenti dei prodotti da parte dei produttori originali. Ma, con l'avvento della stampa 3D in-house, la produzione personalizzata si sta diffondendo in moltissimi settori diversi.
BattleBeaver Customs ha l'obiettivo di fornire un'esperienza di gioco di alto livello con controller personalizzati. Grazie alle modifiche, i controller sono più reattivi e competitivi e permettono ai giocatori di aumentare il loro potenziale e raggiungere prestazioni eccellenti in un'ampia varietà di giochi. La prototipazione rapida con la stampante 3D SLS Fuse 1 consente a Battle Beaver Customs di cambiare velocemente il design di attacchi e tasti. Nella costruzione di prodotti personalizzati per il consumatore, i tempi di esecuzione possono fare la differenza per le aziende che vogliono essere un passo avanti rispetto alla concorrenza. Secondo Michael Crunelle, responsabile di ricerca e design presso Battle Beaver Customs, "la Fuse 1 è stata fantastica, perché ci ha consentito di apportare modifiche velocemente dal concept alla parte per uso finale. La concorrenza non riesce a stare al passo".
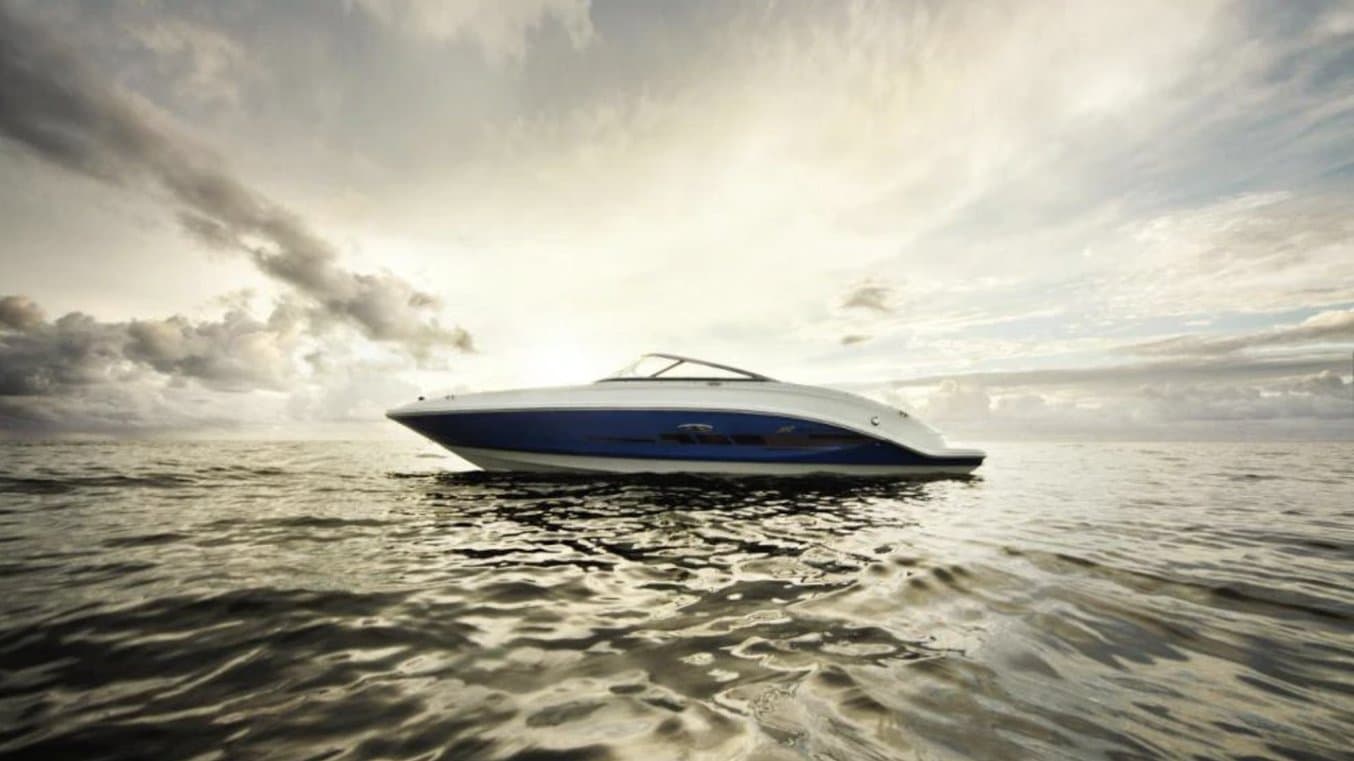
JetBoatPilot, azienda produttrice di parti e accessori per la navigazione, è diventata leader nel settore grazie alla creazione di prodotti per il mercato post-vendita che migliorano le prestazioni e la manovrabilità a bassa velocità delle barche a idrogetto.
JetBoatPilot utilizza le stampanti 3D stereolitografiche (SLA) Form 3 e quelle a sinterizzazione laser selettiva (SLS) Fuse 1 per prototipare e produrre parti per il mercato post-vendita. Il Lateral Thruster 2.0, prodotto concepito di recente e dalle prestazioni eccezionali, è stato progettato e realizzato con la Fuse 1. Grazie alla Fuse 1 e alla Nylon 12 Powder, JetBoatPilot ha potuto ridurre i costi di sei volte rispetto ai metodi di produzione precedenti. "Probabilmente il prezzo al dettaglio della versione in alluminio sarebbe stato di 400 $, o addirittura di 600 $, se avessi voluto esagerare. Ma a quel prezzo non ne avrei venduti così tanti. Adesso invece lo vendo a 199 $ e i clienti ne sono entusiasti. E guadagno venti volte il costo delle materie prime", dice Will Owens, fondatore di JetBoatPilot.
Creazione delle migliori bombe da bagno sul mercato
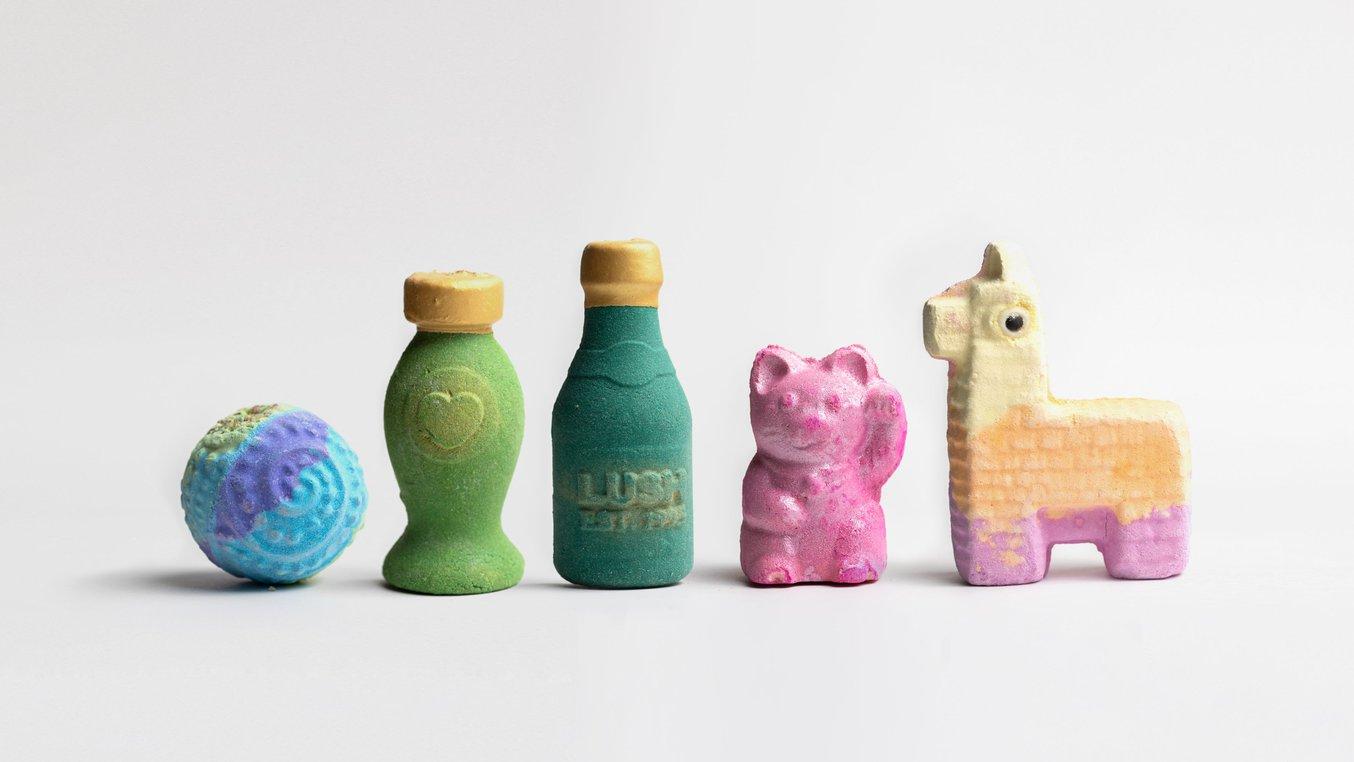
Dall’alto dei suoi 928 punti vendita sparsi in 48 Paesi, Lush Cosmetics è un gigante dei cosmetici conosciuto per prodotti come olio da massaggi solido, burro per il corpo, bombe da bagno e molto altro, e attribuisce il proprio successo all’abilità di rispondere rapidamente alle tendenze e alle esigenze dei clienti.
Per realizzare nuovi cosmetici altamente dettagliati e unici nel settore, Lush si è rivolta alla stampa 3D per la prototipazione di nuove forme, ma non solo. L'azienda ha investito in un centro di produzione additiva di nuova generazione dedicato alla creazione di stampi, attrezzature e parti per utilizzo finale.
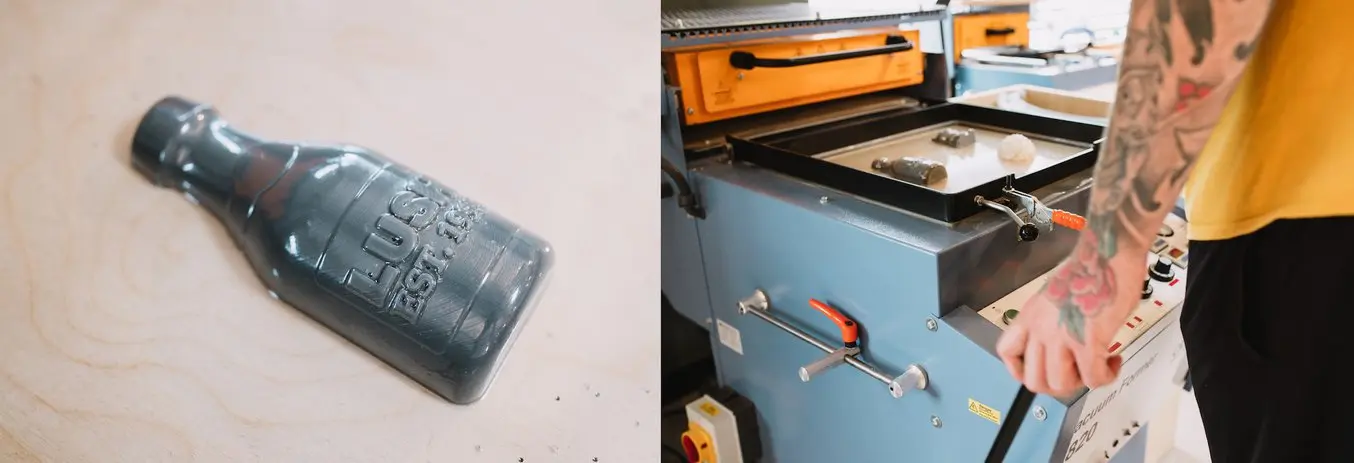
Il team di Lush Cosmetics realizza in-house la formatura sottovuoto delle parti stampate in 3D.
"Usiamo le stampanti 3D Formlabs per creare stampi, attrezzature personalizzate e parti per utilizzo finale. Siamo un’azienda che risponde alle esigenze del mercato, e avere la possibilità di eseguire queste operazioni in-house significa che non dobbiamo condividere i design all’esterno e che possiamo mantenere il controllo completo sul processo di sviluppo del prodotto,” afferma Damien Carter, responsabile del laboratorio di innovazione di Lush Cosmetics.
La vera personalizzazione di massa per la prima volta
La stampa 3D apre le porte a nuove possibilità e opportunità commerciali, come la personalizzazione di massa. Oggetti che prima risultavano troppo complessi, costosi o poco pratici da produrre con i metodi tradizionali, ora possono essere realizzati senza costi aggiuntivi grazie alle tecnologie digitali. Questo permette ai designer di assumere il controllo completo e apre la strada all'introduzione di prodotti di consumo interamente personalizzabili.
Un ottimo esempio è Razor Maker™ di Gillette, che dà ai clienti la possibilità di personalizzare l'impugnatura del loro rasoio scegliendo tra vari design e colori o aggiungendo un testo personalizzato
"Per Gillette, Razor Maker™ rappresenta un passo cruciale nel nostro percorso di personalizzazione, in cui tecnologie innovative si uniscono a nuovi modelli aziendali per offrire prodotti unici come i nostri consumatori" spiega Donato Diez, responsabile globale del marchio Gillette e Razor Maker™.
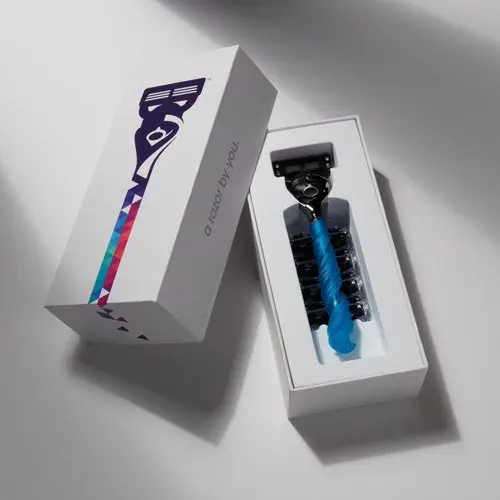
Guida alla personalizzazione di massa
Questa guida fornisce alle aziende produttrici un approfondimento sui diversi approcci alla personalizzazione, su come scegliere quello più adatto e molto altro.
Stampa dentature su misura
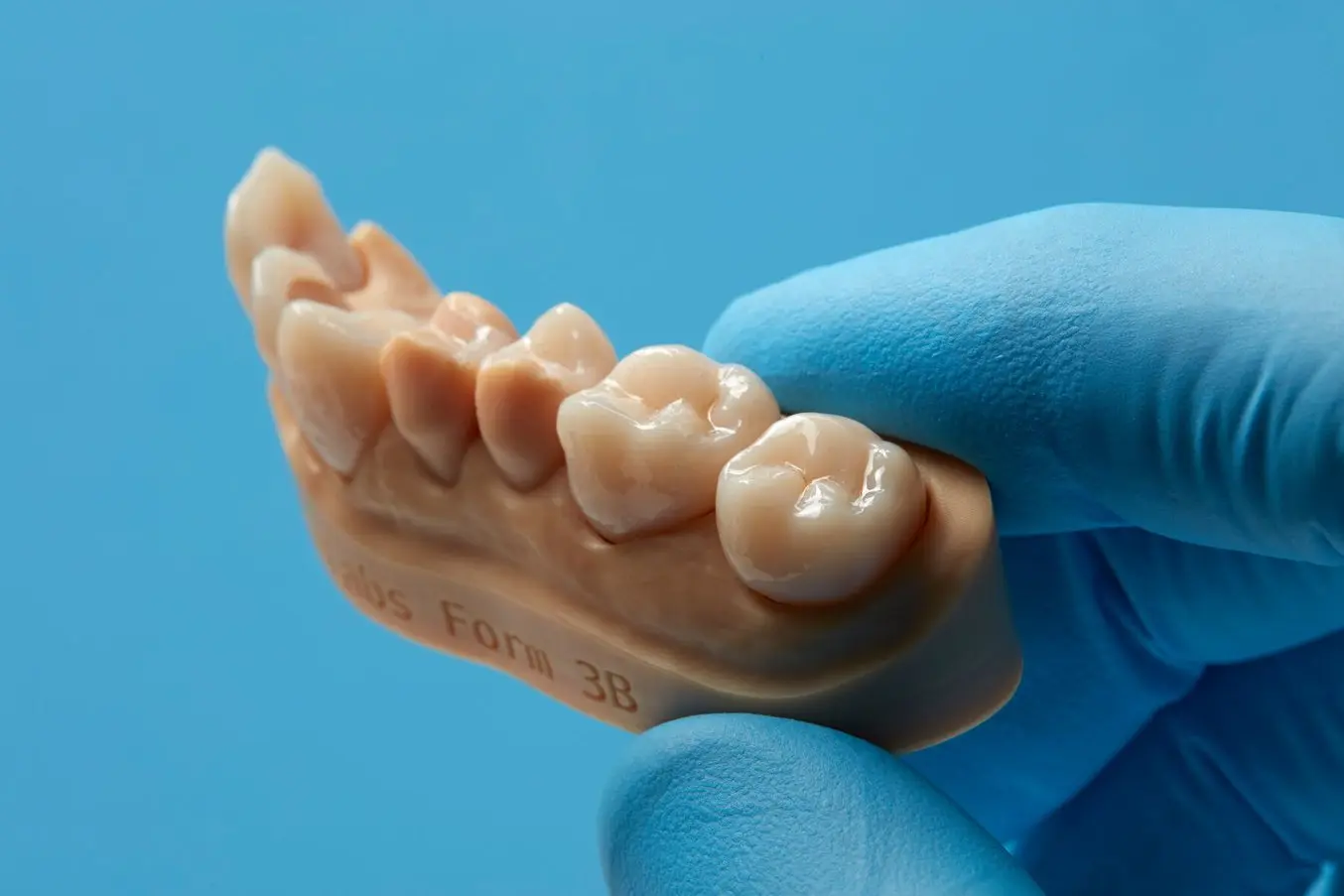
Anche l'odontoiatria ha investito fortemente nella stampa 3D: sempre più laboratori e studi odontoiatrici hanno deciso di adottare stampanti 3D desktop. Ad esempio, i popolari allineatori trasparenti termoformati a partire da modelli stampati in 3D al momento sono probabilmente l'applicazione più riuscita.
Negli ultimi dieci anni, la stampa 3D ha compiuto enormi progressi nel settore dell'odontoiatria, e oggi quasi nessun laboratorio odontotecnico decide di aprire senza prima essersi dotato di una tecnologia di odontoiatria digitale. I materiali sono talmente ben concepiti che è possibile stampare in 3D corone permanenti, protesidentali e molto altro.
Le tecnologie di stampa 3D si inseriscono in un ambiente in cui le caratteristiche fisiche uniche di ogni individuo richiedono soluzioni personalizzate. Di conseguenza, il settore odontoiatrico sta subendo una rapida trasformazione da quando i workflow digitali migliorano l'efficienza, incrementano la qualità e riducono i costi per i laboratori odontotecnici e gli studi dentistici.
Occhiali di lusso stampati in 3D
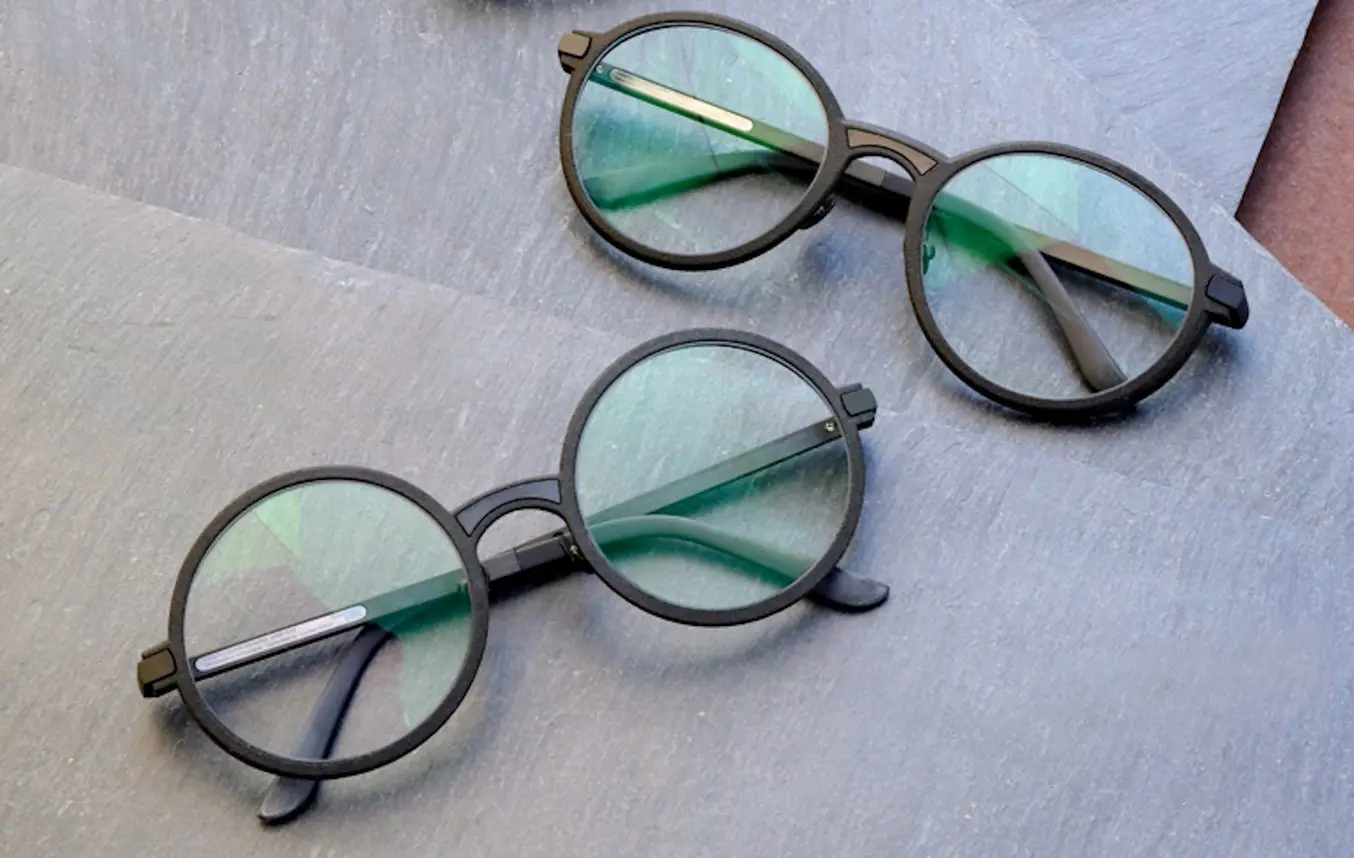
La prossima volta che esci per una serata in città, tieni gli occhi ben aperti per il nostro prossimo caso d'uso: la stampa 3D per montature di occhiali personalizzate.
Le montature di occhiali di Marcus Marienfeld AG si distinguono da quelle tradizionali grazie all'uso di tecniche di produzione diverse e uniche. Di recente hanno iniziato a integrare la stampa 3D a sinterizzazione laser selettiva (SLS) nella linea di produzione delle montature nel loro laboratorio svizzero, sia per la stampa di parti per uso finale, sia per la produzione rapida di attrezzature per la formatura del titanio.
"Con una stampante 3D in-house è possibile avere molta inventiva e fantasia. Riesco a realizzare con poco sforzo cose che altrimenti non avrei mai provato," ha affermato Marcus Marienfeld.
Infinite possibilità
Oggi, ipotizzare futuri cambiamenti dei metodi di produzione ad opera della stampa 3D non richiede più un grande sforzo di immaginazione. Nel corso degli ultimi anni, con lo sviluppo dei flussi di lavoro e il conseguente riconoscimento ottenuto nei settori più svariati, l'iniziale potenziale rivoluzionario della stampa 3D sta iniziando a trovare riscontri nel mondo reale.
Dall'odontoiatria, passando per l'intero settore sanitario, fino all'industria dei beni di consumo, all'architettura e alla produzione, i punti di contatto tra il pubblico e i prodotti finali della stampa 3D continuano ad aumentare in modo costante. La produzione di parti personalizzate in modo conveniente, la riduzione dei tempi di consegna e delle spese generali, nonché la possibilità offerta ai clienti di ottenere esattamente i prodotti che desiderano, sono solo alcuni dei fattori che ci spingono a pensare che l'influenza della stampa 3D continuerà a crescere anche in futuro.