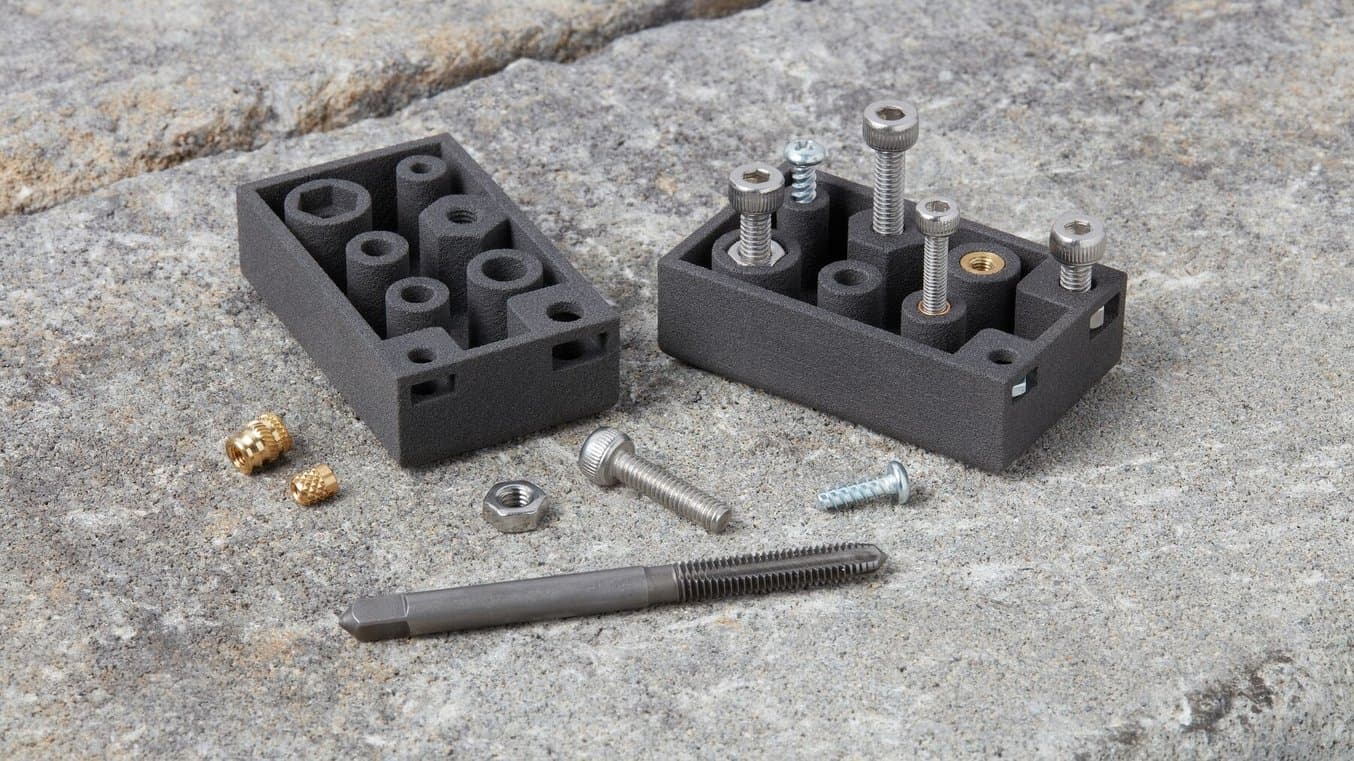
ヘリサートやタップなど、3Dプリント製部品にねじを取り付ける方法は多数ある中、ねじ山を直接3Dプリントすることも可能。
ねじは、材料を問わず最も一般的な締結具の一つです。市販のねじは、3Dプリント製部品にも使うことができるのでしょうか?答えは間違いなく、イエスです。SLA光造形とSLS(粉末焼結積層造形)のいずれの方式で造形した部品にも、市販のねじを使用できます。
この技術記事では、様々な金属製ねじと3Dプリント製部品との相性や使用法について解説するとともに、部品の3D設計時に直接ねじを組み込むためのヒントもお伝えします。
上の活用事例動画では、ねじを直接3Dプリントしたり、3Dプリント製のプラスチック部品にヘリサートを挿入する方法を紹介しています。

最適な3Dプリント方式の選定方法
ニーズに適した3Dプリント方式選びでお困りですか?本動画ガイドでは、FDM、SLA光造形、SLSの3方式の比較を行います。購入前の検討材料として、是非お役立てください。
3Dプリント製のねじ山の設計方法
お客様からのフィードバックをもとにFormlabsが数年かけて収集してきた、3Dプリント製のねじ山の設計方法についてご紹介します。テストパーツの設計には、すべての方法を一つの部品で説明できる以下を採用しました。
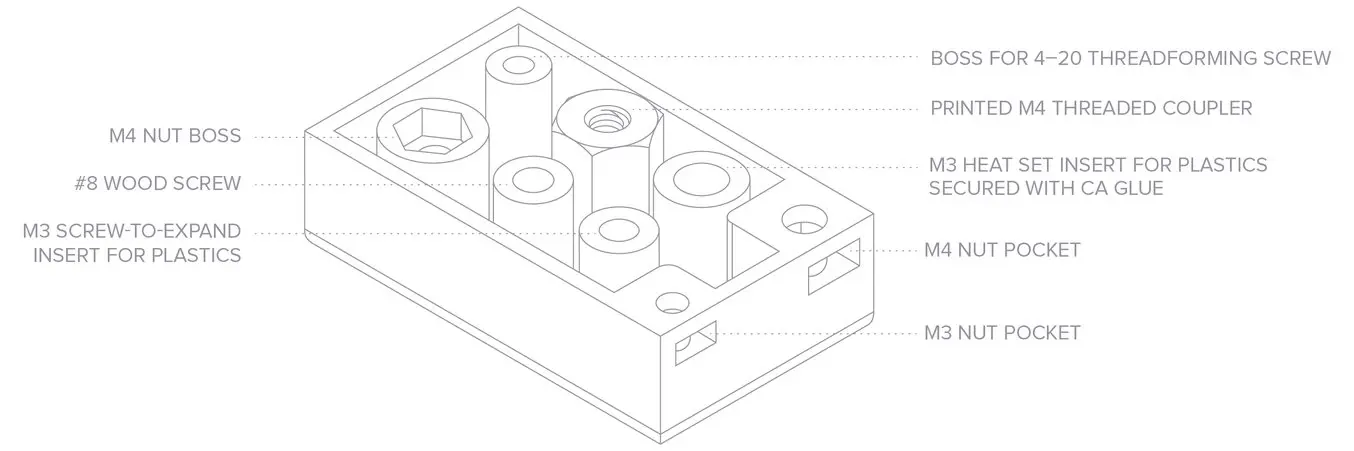
締結部品の種別ごとに組み合わせをグループ化し、それぞれの長所と短所を以下にまとめました。
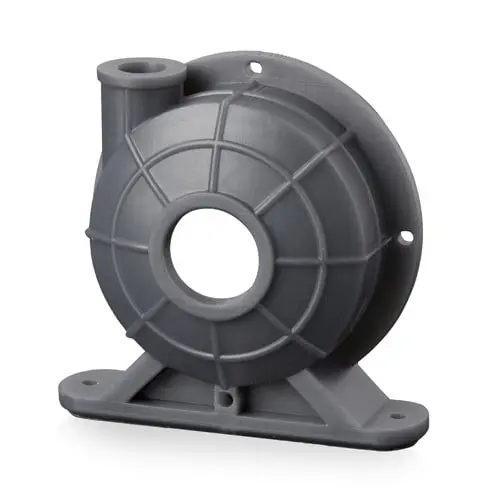
無償サンプルパーツのお申込
Formlabsの品質を直接手に取ってご確認ください。工業品質のSLA光造形・SLS 3Dプリンタで造形したサンプルパーツを無償でお届けいたします。
金属製のねじを金属製のねじ山に締結
このセクションでは、3Dプリント製の部品にヘリサートやナットを使用し、組立や分解の繰り返しにも耐えられる高強度・高耐久な締結を実現する方法をご紹介します。
拡張式ヘリサート
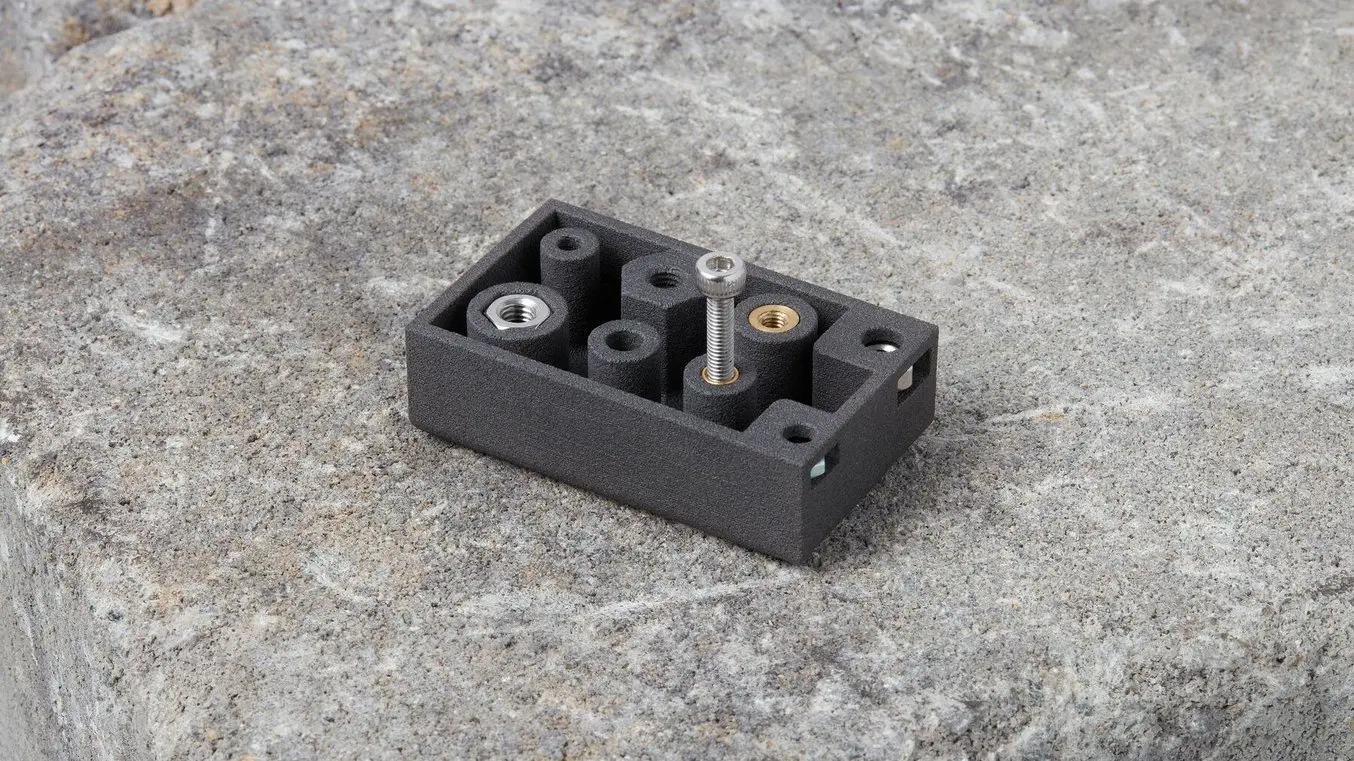
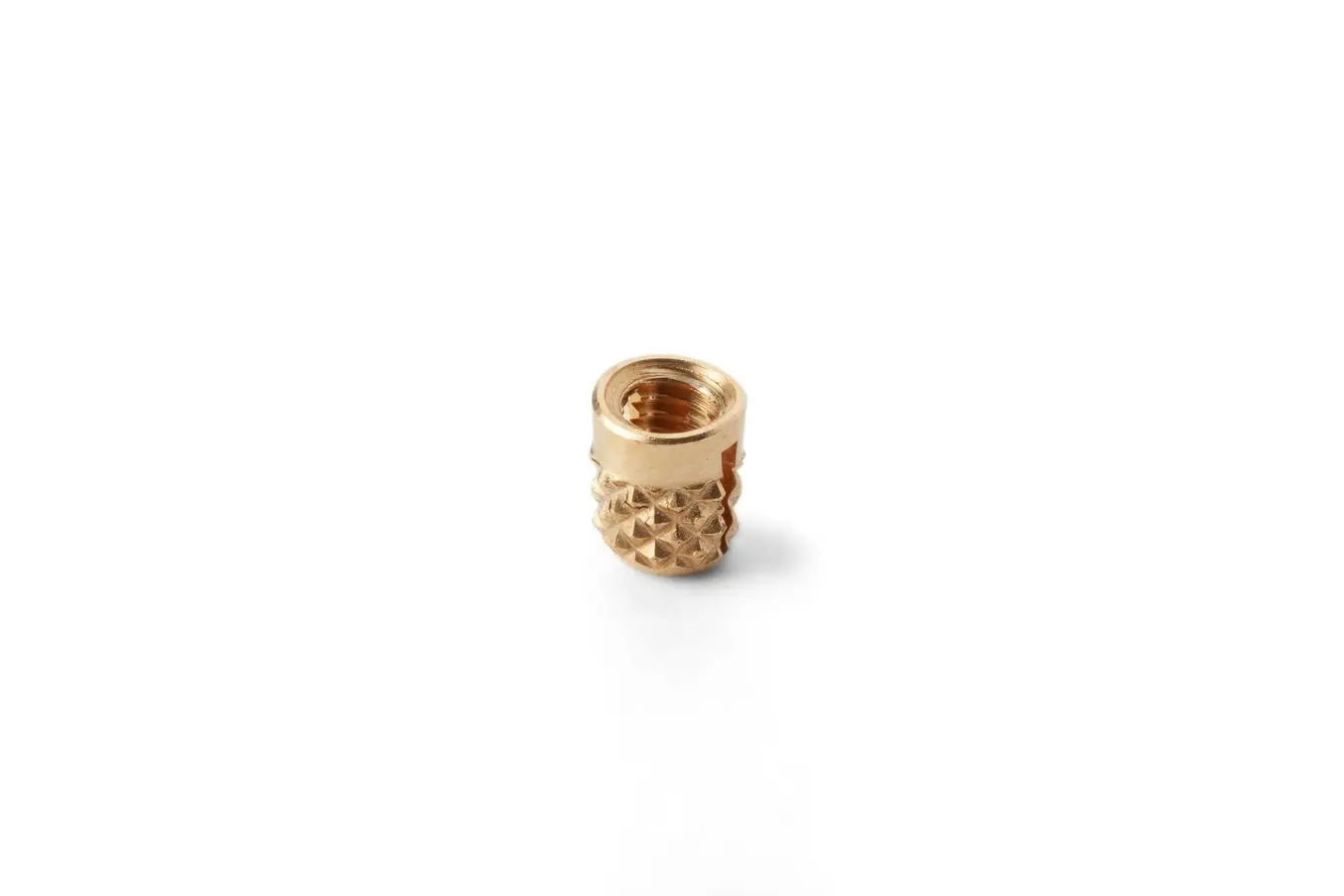
長所
-
3Dプリント製部品に対する優れた結合力
-
金属ねじで高強度で耐摩耗性を実現
-
簡単に圧入可能
短所
-
高温でヘリサートが緩むことがある
拡張方式ヘリサートの嵌合部は円筒形で、わずかに先細りになった部分の外側がローレット加工になっています。設計段階では、ヘリサートの仕様に基づいたボスの深さと穴径で部品を設計します。SLA光造形またはSLS方式プリンタの基本的な手順に従って部品をプリントし、後処理を行います。材料がキャビティ内に残っていないことを確認した後、単純に圧入してヘリサートを取り付けます。ねじを付けると、押されたヘリサート先端のローレット部が周囲の材料にしっかり食い込み、確実に締結された状態になります。
SLA光造形方式による3Dプリント製部品に拡張方式ヘリサートを使用する場合、通常どおり造形品を洗浄した後に拡張方式ヘリサートを圧入し、ねじを挿入した状態で造形品を二次硬化します。このステップを最後に行うことで、ヘリサートが相手材を圧迫した際に亀裂が入る可能性を軽減できます。
熱圧入式ヘリサート
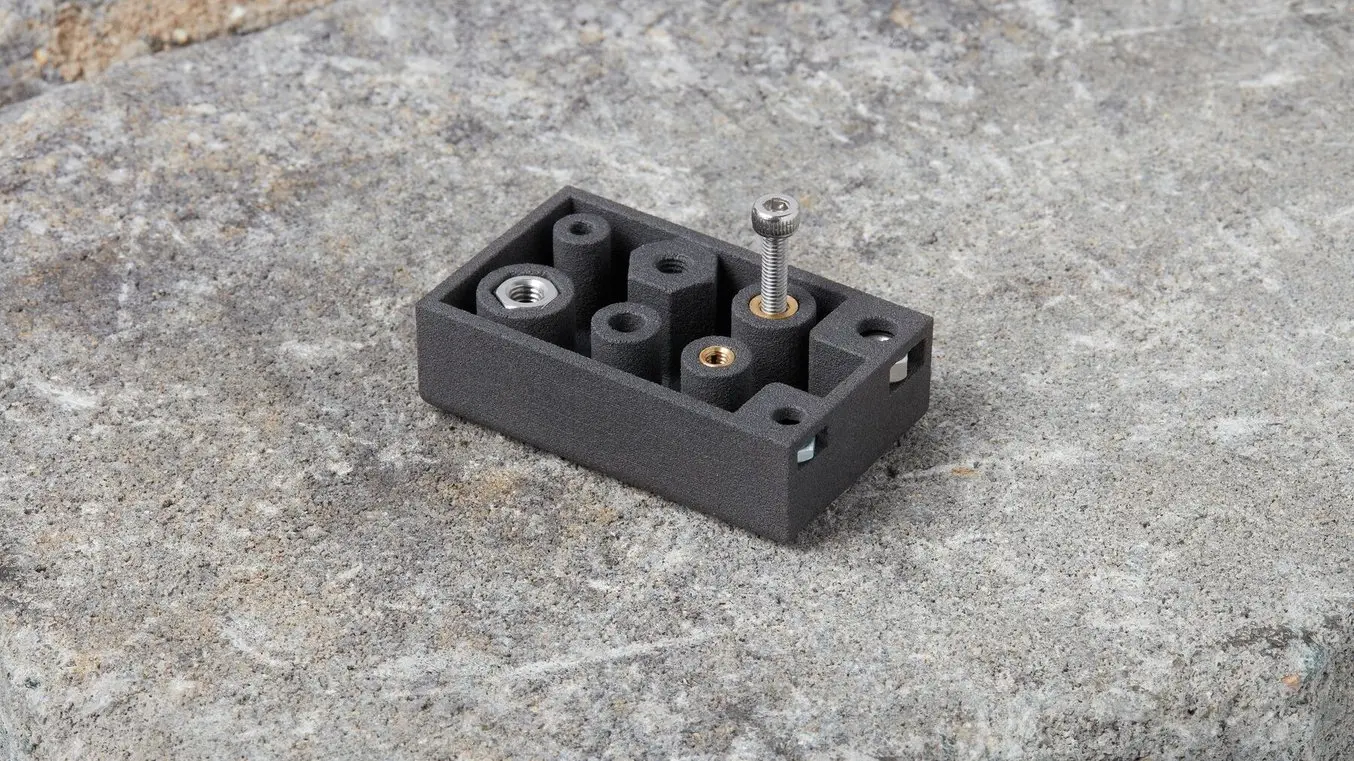
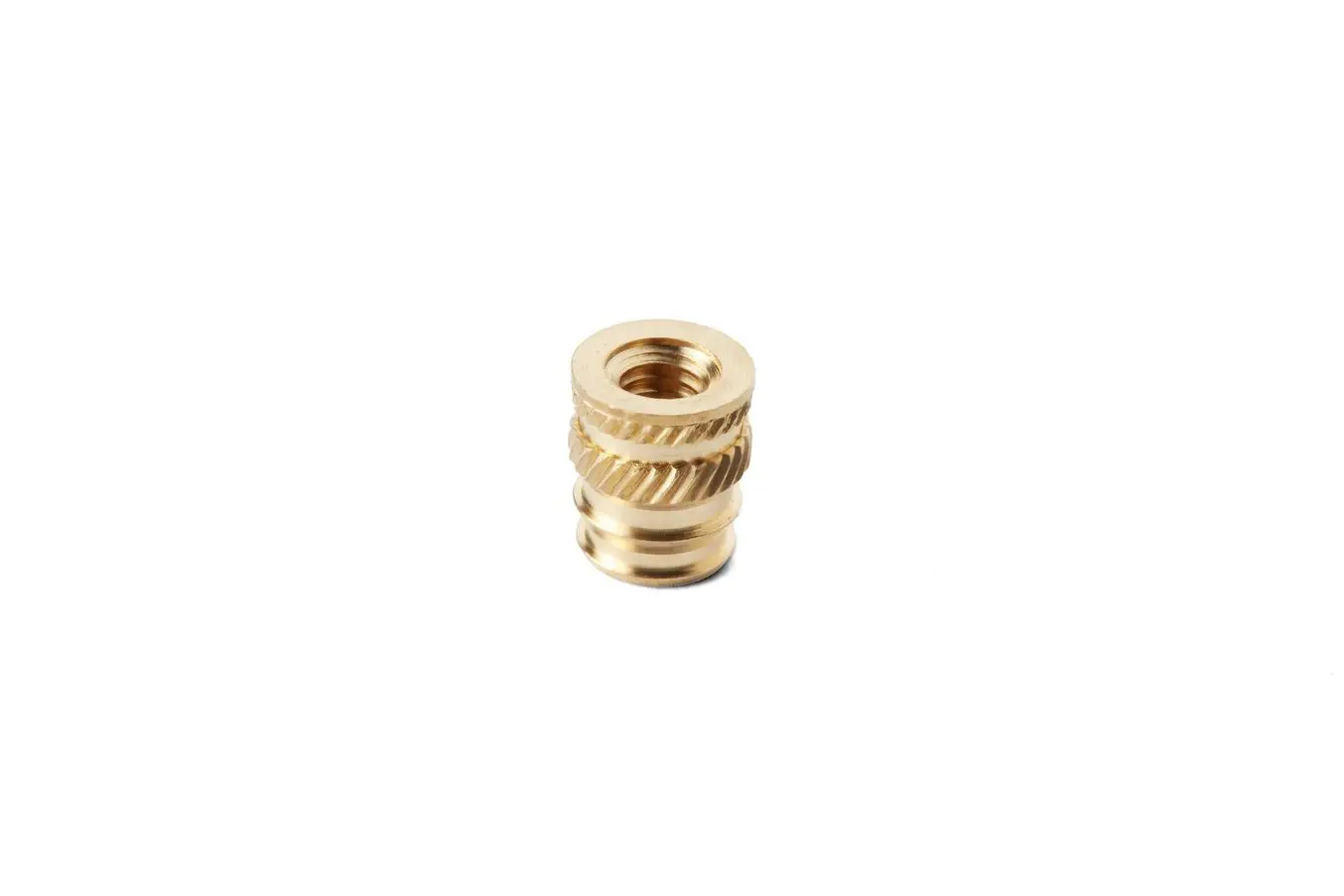
長所
-
3Dプリント製部品に対する優れた結合力
-
金属ねじで高強度で耐摩耗性を実現
短所
-
SLS部品(熱可塑性):はんだごてと冷却時間が必要
-
SLA光造形部品(熱硬化性):接着剤と硬化時間が必要
熱圧入方式のヘリサートは、専用のこて先を付けたはんだごてで熱可塑性樹脂材に溶接します。SLA光造形品のように相手材が熱硬化性材料の場合は、接着式のヘリサートとしても使用可能です。
SLSパウダーを使った造形品など、熱可塑性樹脂部品に取り付ける場合は、取り付けに使用する器具の指示に従ってください。一般的には、専用アタッチメントの有無を問わずはんだごてを使ってヘリサートを熱し、その熱を周囲の樹脂に伝導します。ヘリサートを囲む材料が熱で軟化するので、はんだごてをやや押し付けるようにしてヘリサートを3Dプリント製部品に圧入していきます。相手材が十分に冷めて強度が回復するのを待ってから、ねじを取り付けます。
SLA光造形レジンを使った造形品など、熱硬化性部品には、熱圧入式ヘリサートでも接着剤を使った取り付けが可能です。従来の取り付け方法とは異なり、ボスをヘリサートの最大径に合わせて設計し、取り付け時はシアノアクリレート(CA)系またはエポキシ系の接着剤を使用して確実に固定します。ねじを挿入する時は、十分な時間を置いて接着剤が完全に乾いたことを確認してからにしてください。
注:本記事で使用しているSLS造形品の写真では、ボスの寸法は熱硬化性樹脂に推奨される圧入方式に合わせてあります。熱可塑性樹脂の部品には、接着剤またはエポキシ系接着剤を少量塗布することでも取り付けが可能ですが、熱圧入方式ほどの強力な結合は得られません。
はんだごてを使った加熱や接着剤の使用といった追加の手順が必要にはなりますが、SLSおよびSLA光造形方式でプリントした部品を確実かつ強固に結合できる点で、熱圧入方式インサートは拡張方式インサートよりも優れていると言えます。多少の手間と工具が必要ですが、拡張方式よりも高い結合力と強度を得るには最適な方法です。
ナットを設計に取り込む
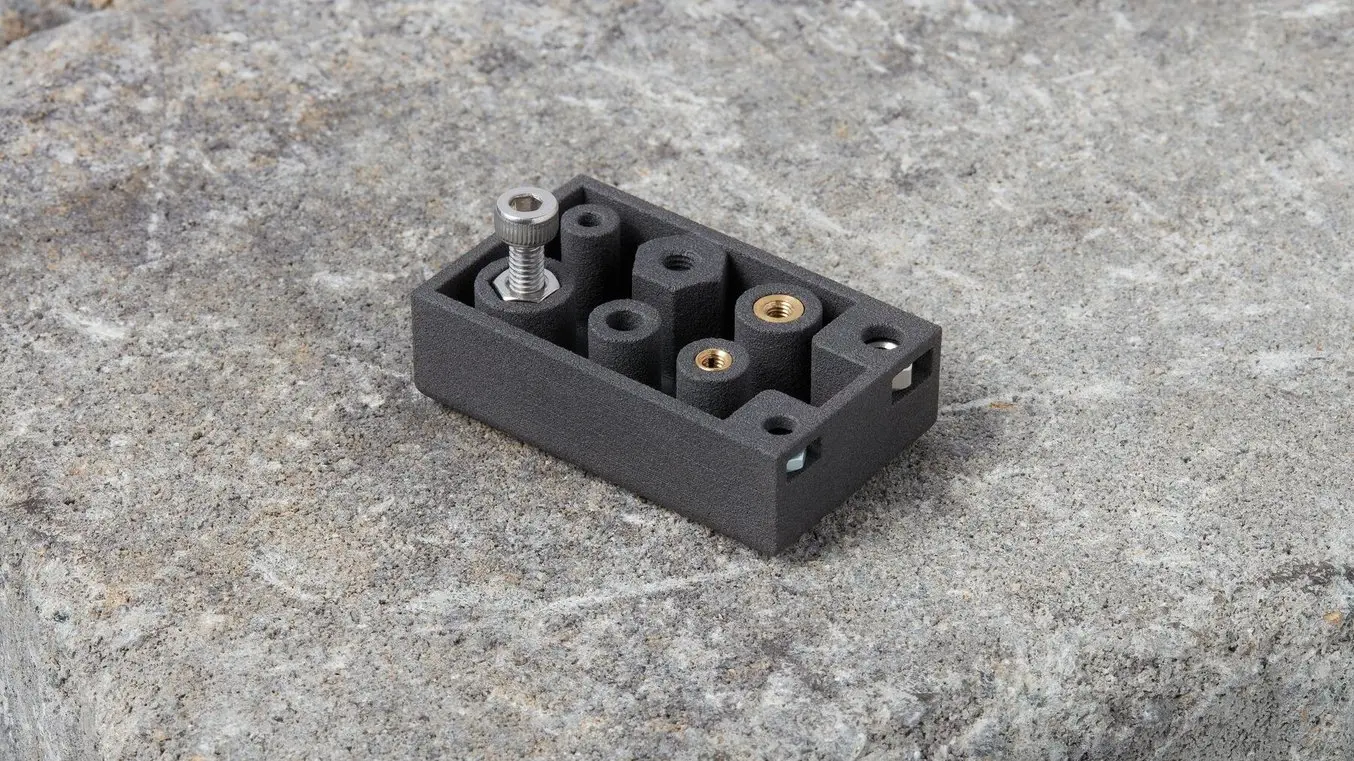
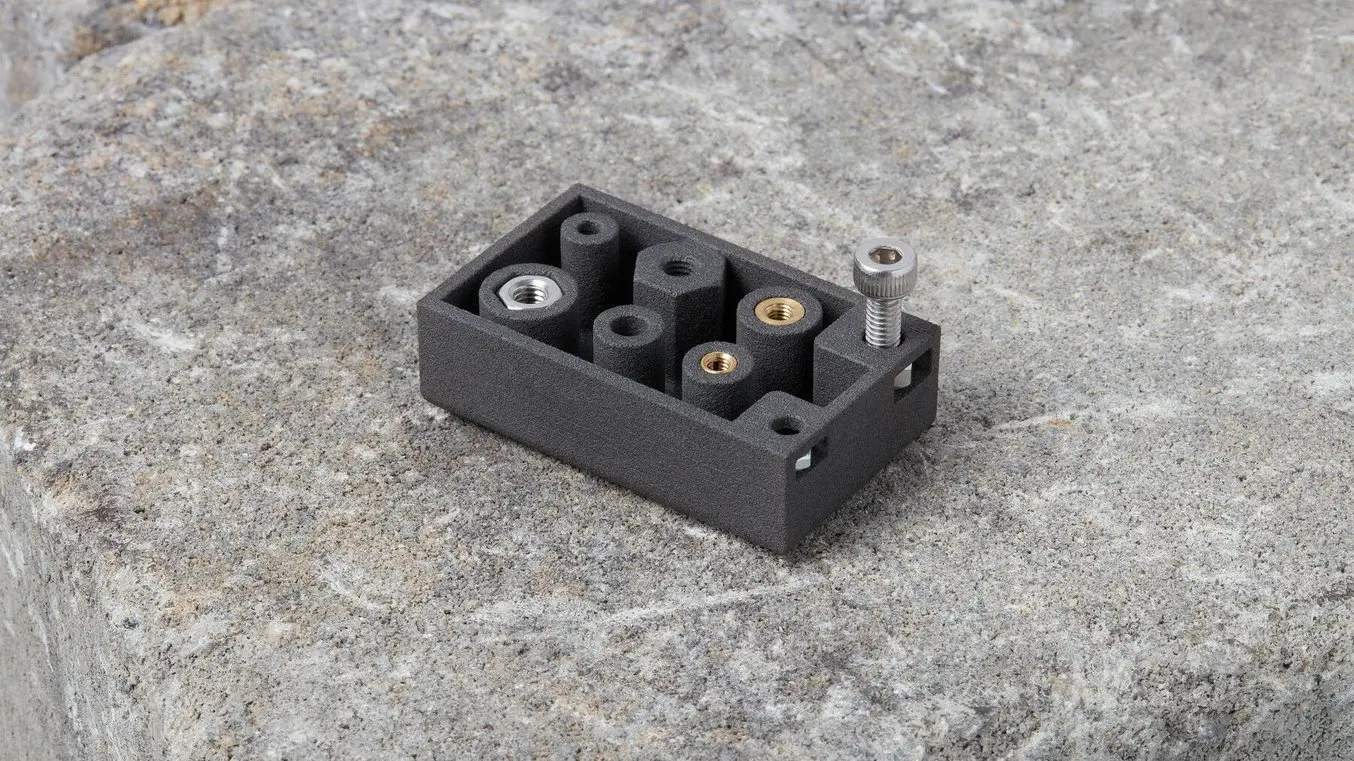
長所
-
3Dプリント製部品に対する優れた結合力
-
金属ねじで高強度で耐摩耗性を実現
短所
-
部品上にポケットやボス穴を設計し、プリント後にアクセスできる必要がある
-
形状によっては接着剤と硬化時間が必要
金属同士を強固に結合するためには、ナットを部品本体に確実に嵌合できるようポケットやボス穴を先に設計しておくことも有効です。六角または四角ナット、場合によってはロックナットが使用可能です。この手法では多様な設計が可能ですが、ナットの取り付けを可能にするためにポケットやボス(内面以外)にアクセスしやすい状態を確保することを心がけてください。ナットをより確実に固定するためには、シアノアクリレート(CA)系の接着剤を少量使用することをおすすめします。
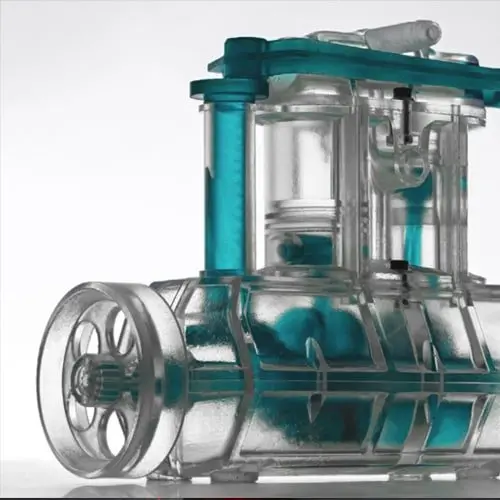
機能的な3Dプリントアセンブリの設計を最適化
Formlabs Form 3+などのSLA光造形方式3Dプリンタは、正確性と精度が非常に高く、幅広いエンジニアリング系材料が使用できます。本技術資料をダウンロードして、推奨される公差設計の詳細をご確認ください。
金属製ねじを3Dプリント製部品に締結
スピードと手順のシンプルさを優先する場合は、ヘリサートやナットを使用せずに3Dプリント製部品に直接ねじを挿入する方法が好まれることがあります。プラスチック用に設計されたタッピングねじやセルフタッピングねじ等、市販の締結部品は、レジンや熱可塑性パウダーといった3Dプリント用材料との相性が良好です。
3Dプリント製部品にタッピングねじを挿入
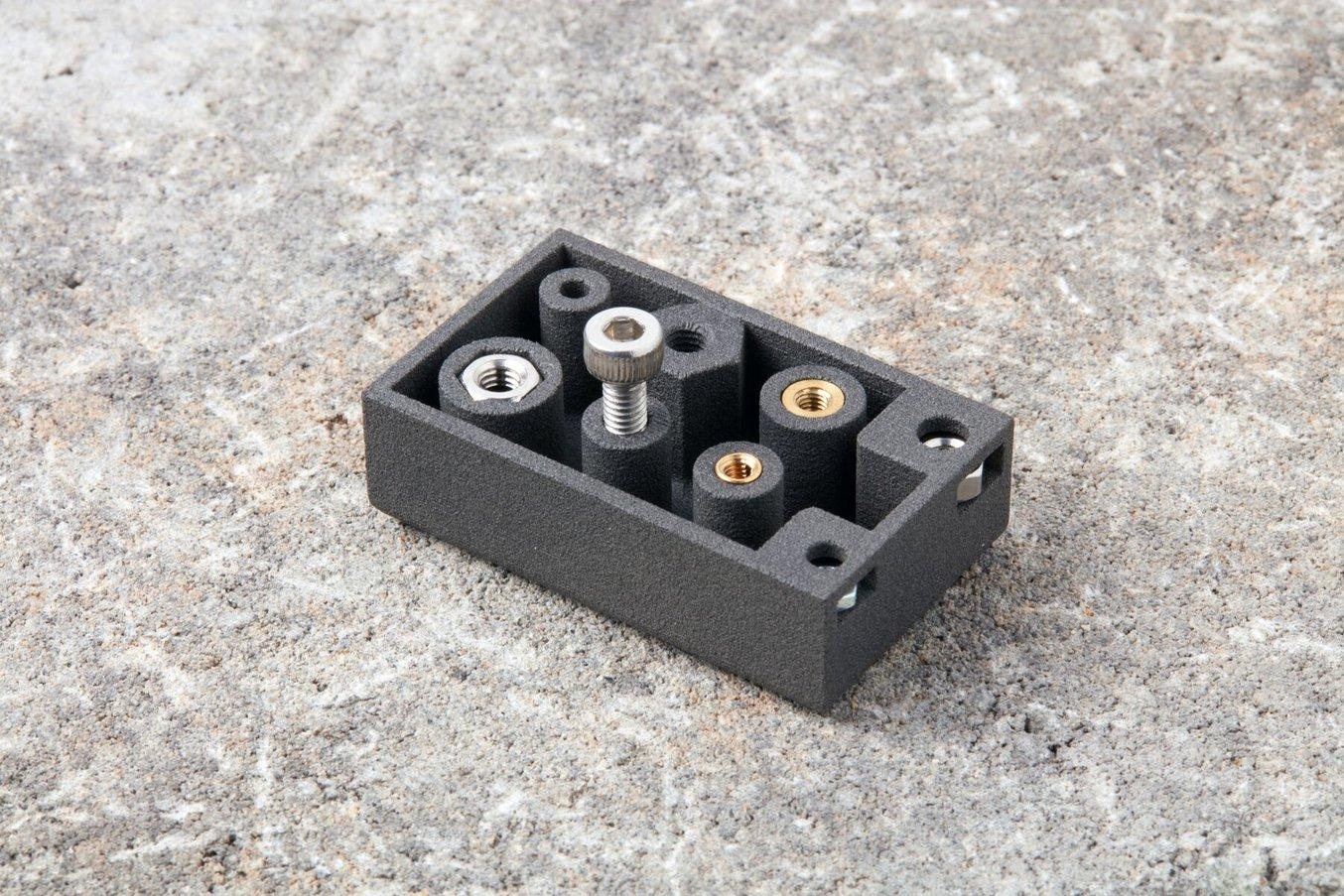
長所
-
3Dプリントパーツに対する優れた締結力
-
シンプルで迅速に作業が可能
短所
-
組立と分解を繰り返す場合、金属ほどの耐久性がない
-
窪み構造が多いパーツでは、作業時間が長くなる場合がある
プラスチック用に設計されたタップを使うことで、作業時間と費用を削減しながらねじ山を3Dプリント製部品に追加することが可能です。余分な設計手順も不要で、すでにプラスチックを取り扱っている工場であればプラスチック加工用の機器は揃っているでしょう。
めねじ成形、またはセルフタッピングねじ
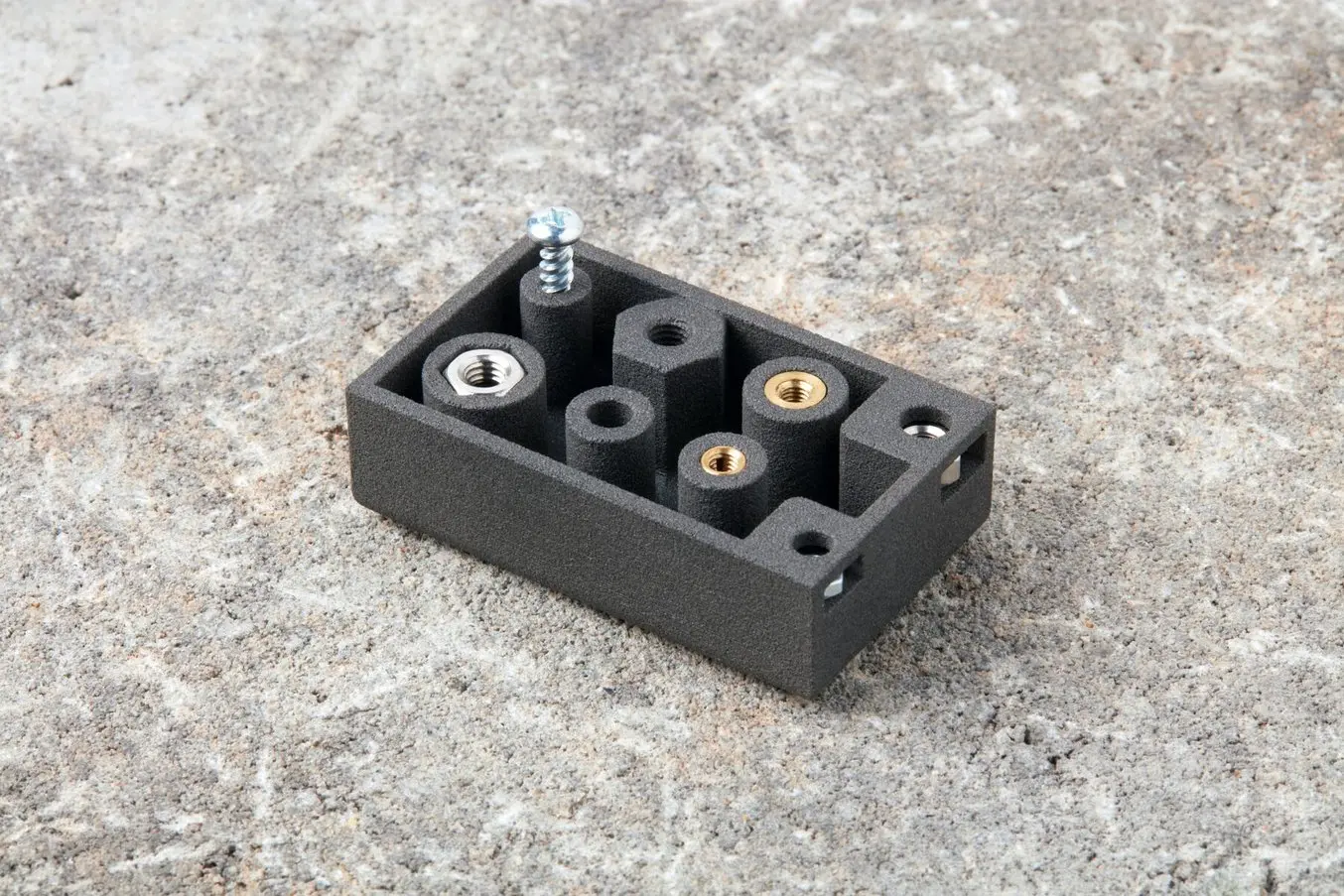
長所
-
3Dプリントパーツに対する締結力に優れる
-
極めてシンプルで迅速に作業が可能
短所
-
組立と分解を繰り返す場合、金属ほどの耐久性がない
セルフタッピングねじは、めねじ成形ねじとも呼ばれ、部材を予備加工することなく窪み構造(穴)に挿入できるねじです。ボス穴の寸法については、各メーカーの基準に従ってください。
この組み合わせには、延性や引張特性に優れた材料の使用をおすすめします。FormlabsのSLA光造形用材料ファミリーの中でも、剛性と耐久性に優れたNylon 11パウダーやNylon 12パウダーは、この用途に適しています。脆性材料や低延性材料(FormlabsのSLA光造形用材料Rigidレジンなど)は、セルフタッピングねじと一緒に使用すると割れるおそれがあるため、使用時は取り扱いに注意し、保護メガネを着用してください。
3Dプリント製のねじ山
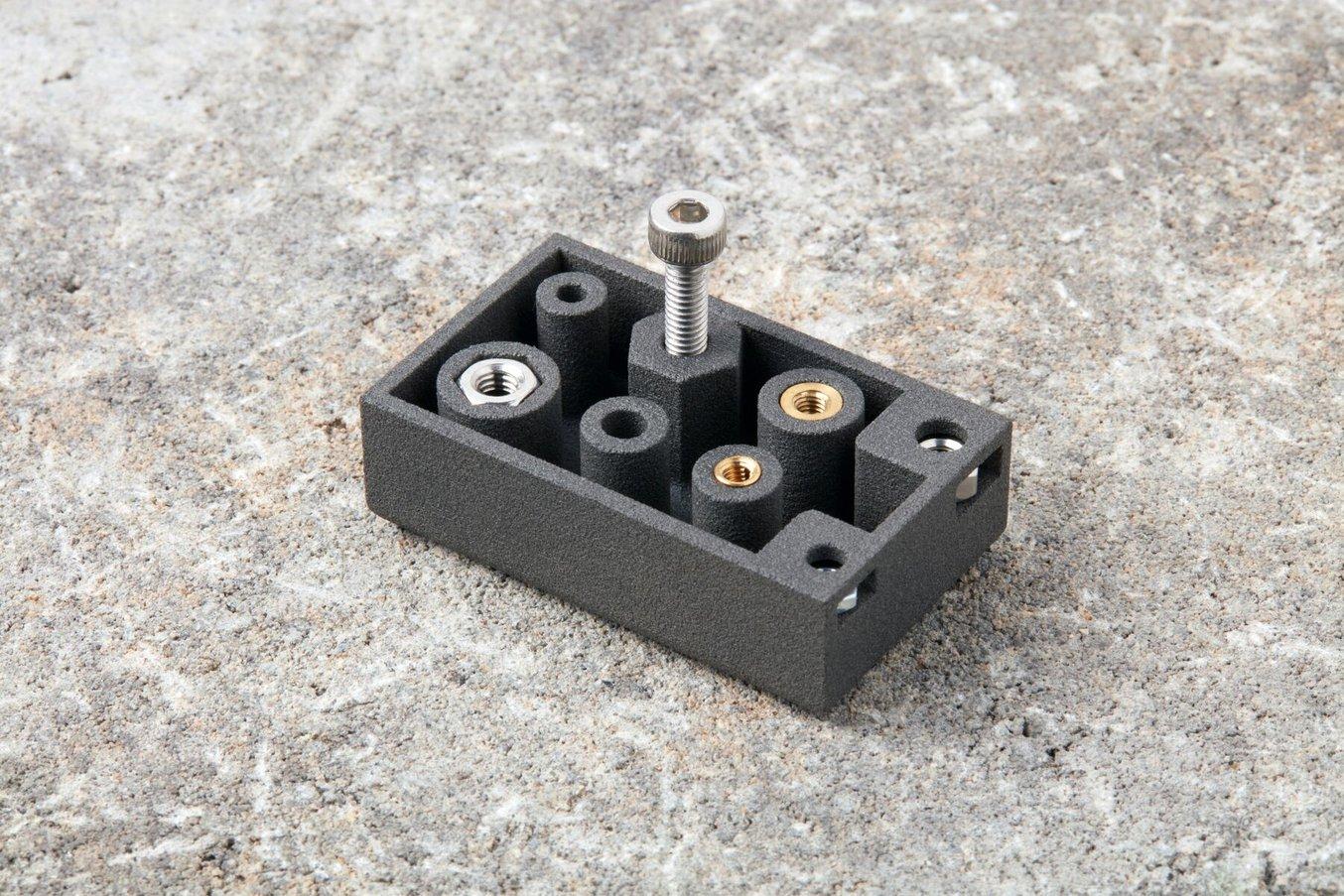
長所
-
プラス、マイナス両方の形状要素をカスタム設計可能
短所
-
組立と分解を繰り返す場合、金属ほどの耐久性がない
-
サイズの大きなねじにのみ有効
特定のガイドラインに従うことで、3Dプリント製の部品にねじ山を直接組み込むことも可能です。その場合、ねじのサイズは¼~20(インチねじ)またはM6(メートルねじ)以上で、フィレット部への応力の集中を軽減し、プラスチック用に設計されたねじプロファイルを使用する、という条件に従う必要があります。ねじのサイズがこれより小さい場合は、締結性能を上げるためにねじ山をカスタマイズする必要があります。例えば、半円形のねじプロファイルを(ねじとナット上に)プリントし、0.1mmのオフセットを付与すると、ねじの嵌合が良くなると共に耐摩耗性も上がります。
SLA光造形およびSLS 3Dプリントは精密で滑らかな表面仕上げが可能なため、基本的にこの方法にはFDM方式よりも適しています。表面の摩擦係数が特に低いDurableレジンなどを使用すると、挿抜を繰り返しても摩耗が少なく済みます。
余分な後処理をしなくても部品がスムーズに結合するよう、3Dプリント準備段階でねじ山面につけるサポート材を最小限に抑えることが重要です。
3Dプリント製のねじ山とヘリサートで複数コンポーネントを組み立てる
3Dプリント製の複数コンポーネントを、ねじとねじ山付き締結部品を使って組み立てる方法は多数あります。この記事では、ねじ山を直接3Dプリントする方法や市販のヘリサートを使用する方法をご紹介してきましたが、使用する材料や予想される組立・分解回数、求められる強度、許容可能な追加作業などに基づいて最適な方法をご検討ください。
お客様の用途に最適な3Dプリント用材料を探すには、弊社のインタラクティブなウィザードがおすすめです。また、3Dプリント製部品の品質をお確かめになりたい場合は、サンプルパーツのお申し込みも承っております。お気軽にご利用ください。