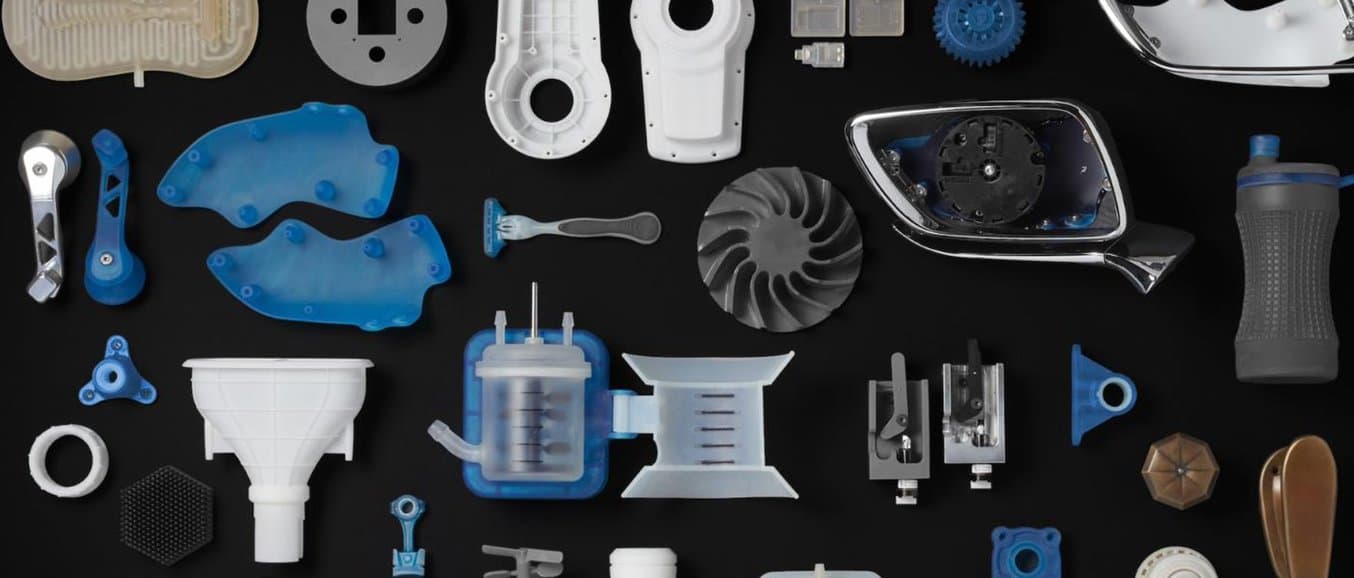
アディティブマニュファクチャリングとも呼ばれる3Dプリント技術は、物理的に一つの部品が出来上がるまで材料を層状にして重ねていき、コンピューター支援設計(CAD)モデルから3次元のパーツを製作する手法です。
アディティブマニュファクチャリングの技術自体は1980年代から存在していますが、この業界が最も話題になったのは2010年代初頭でした。プロモーターたちがこぞって消費者製品としての活用や、ホームデポやUPSなどからの再注文事業などに広く活用できると銘打ったことがきっかけでした。
過剰なまでの熱狂状態が落ちついたのが数年前。そこから、工業品質を叶える3Dプリント技術はより明確な形で急速に成長を続けてきました。近年の3Dプリントのハードウェアや材料、ソフトウェアの発展により、さらに幅広い業種にも応用できるようになった今、これまでは数えるほどのハイテク産業にしか導入できなかった高度なツールを導入する企業が増えてきています。
昨今では、製造業や歯科・ヘルスケア分野、教育、エンターテインメント、ジュエリー、オーディオ業界等、様々な分野で工業品質3Dプリンタがイノベーションを加速し、多くの企業を支援しています。
この記事では、アディティブマニュファクチャリング業界を決定づけた5つの主要トレンドと今後の動向について詳しく解説します。
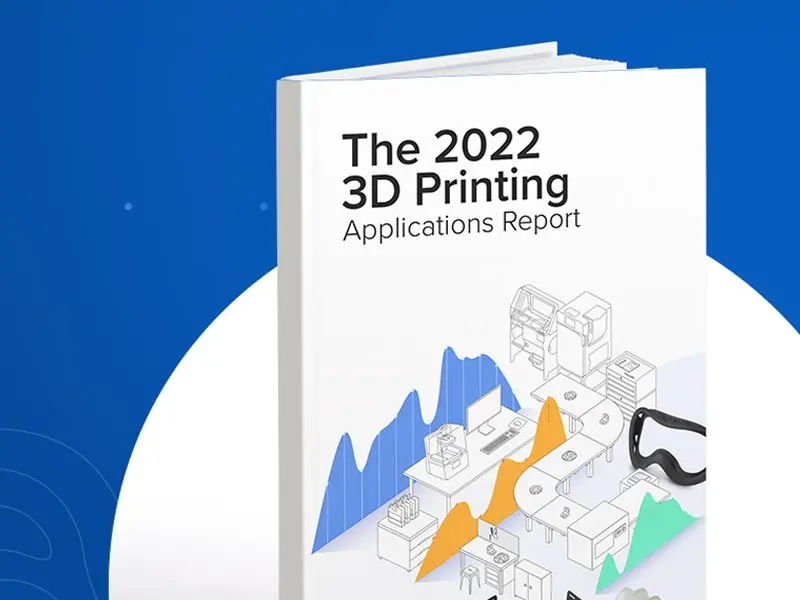
2022年 3Dプリント活用事例レポート
3Dプリント使用歴が比較的長いアーリーアダプター層となる企業と、直近3年以内に導入した企業における3Dプリントの活用法を比較し、今後のトレンドに関するインサイトも提供する業界初のレポートです。
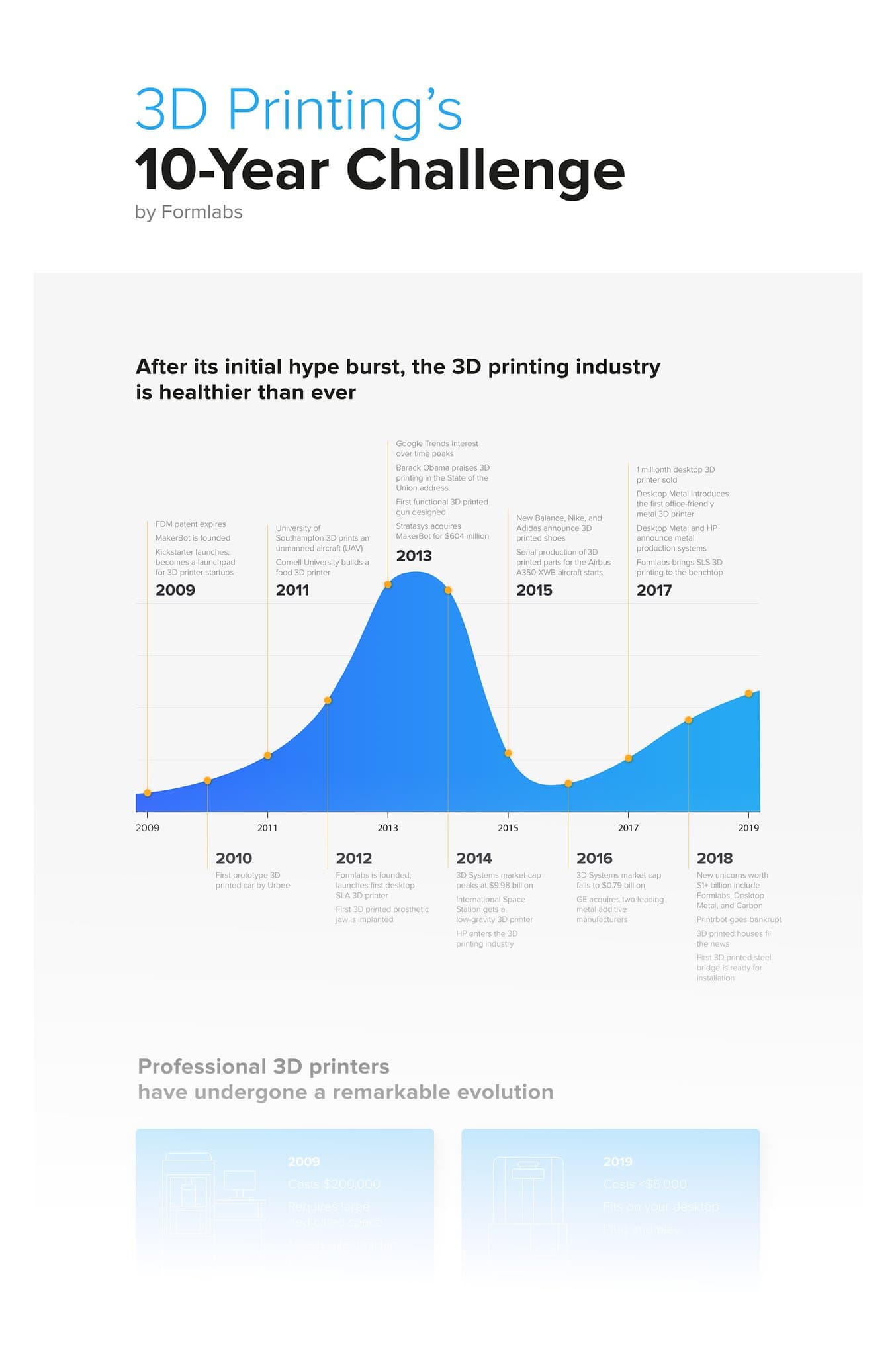
元記事はDigital Factory Report掲載。製造業におけるデジタルトランスフォーメーションに関する詳細なインサイトについては、レポート全文をダウンロードしてご覧ください。また、2019年5月7日にボストンで開催されるThe Digital Factoryにお申し込みいただくと、最先端の製造技術を取り入れて事業の革新を続ける業界リーダーたちの最新情報をご覧いただけます。
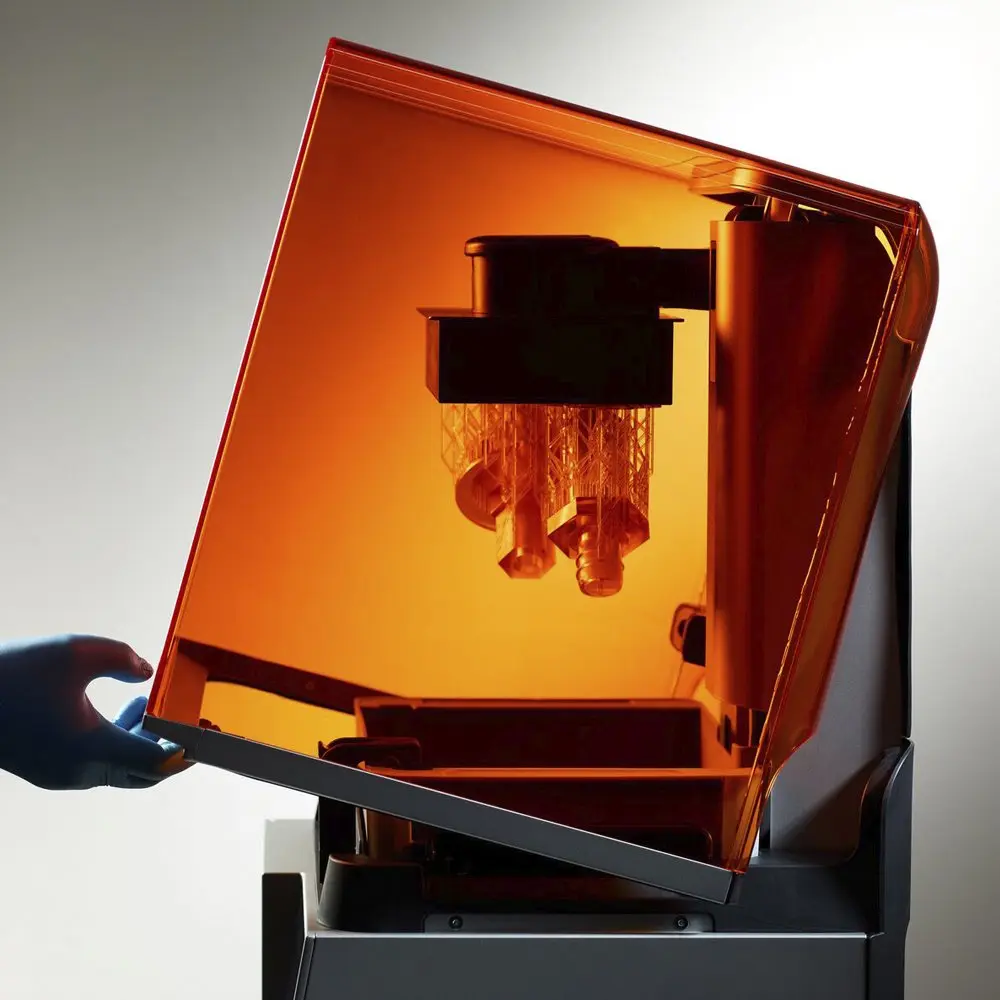
デスクトップサイズSLA光造形方式3Dプリンタの概要
高精細3Dモデルを製作できる光造形3Dプリンタをお探しですか?技術資料をダウンロードして、高精細なモデルを製作できる3Dプリント方式として、SLA光造形方式がどれほど広く活用されているかをご覧ください。
アディティブマニュファクチャリング業界の現状
2017年の売上高が60億ドルだった3Dプリント市場は、年平均成長率30.2%で成長を続け、2022年には市場規模が220億ドルに達すると予測されています。
- 何十年もの間、3Dプリントは試作品製作や製品開発などで活用されることが一般的でしたが、技術の成熟に伴い量産でも幅広く使用されるようになってきています。
- 技術向上によって高い生産性と実製品用部品の高品質造形が可能になったこと、そして幅広い高機能材料が開発されたことで、3Dプリントは小規模から中規模製造において実用的な方法となり、時には数万点もの部品を製作するケースも出てきています。
- 3Dプリントは、実製品用部品の直接製造のほか、成形型や治具、原型、固定具等、従来の製造工程と組み合わせる「ハイブリッド製造」でそのメリットを発揮します。
- コンパクトで入手しやすいデスクトップサイズ3Dプリンタの性能が向上し、複数台を並行稼働させることでコストと生産量の両面で高額な産業用3Dプリンタを上回ることができます。
- 製造業者は、3Dプリントを中規模から大規模な製造にも活用するべく、アディティブマニュファクチャリング(AM)工程にかかる作業量の集約率の低減に取り組んでいます。
- 金属AMは作業工程の改善と新技術の導入で造形単価が下がったことから、投資する企業が急増しています。
アディティブマニュファクチャリングのキートレンド
プラスチックを使用するコンパクトなモジュラー型
3Dプリンタが登場してからの最初の30年間は、高額なコストや工程の複雑さから、導入できるのは実質大企業や受託メーカーに限定されていました。2010年代初頭、より高性能な組み込みハードウェアの登場、特許の失効、および技術の成熟という様々な背景が後押しとなって何百もの企業が市場に参入し、新たな3Dプリンタが続々と登場して瞬く間にバブル状態となりました。
デスクトップで利用可能になった最初の技術はFDM(熱溶解積層)方式でした。プラスチックを溶かして選択的に積層していく3Dプリンタは本当の意味で消費者にとって手頃な価格となったものの、その機能はまだ限定的なままでした。一気に高まった期待はその勢いのままに期待はずれ感が漂い、「3Dプリンタが各家庭に欠かせないものになる」という夢はついに叶わぬままでした。
それ以降3Dプリントの消費者市場では目立った動きは見られなかったものの、その間もアディティブマニュファクチャリングの技術は急速に進歩し続けてきました。エンジニアリング、プロトタイピング、製造で使用される産業用3Dプリンタが、造形品質、信頼性、コスト構造において重要な閾値を超え始めたのです。
手頃な価格で、かつコンパクトで使いやすいフォーマットで登場した2番目の技術は、SLA光造形方式でした。2013年、FormlabsはForm 1の発表によりそれまで80,000ドル以上の3Dプリンタでしか実現できなかった高精細3Dプリントを3,300ドルで産業市場に導入し、3Dプリントへアクセスできるユーザー層を拡大しました。さまざまな高機能材料が使用できるこの方式は、製品設計やエンジニアリング、歯科や宝飾業界における3Dプリントの活用事例を広げていくこととなります。
ベンチトップサイズで登場した第3の3Dプリント方式は、工業品質を求めるユーザーにとっては欠かせない技術であるSLS(粉末焼結積層造形)方式です。他のデスクトップサイズのAM技術とは異なり、SLSではナイロンなどの熱可塑性プラスチックを使って射出成形品とほぼ同等の強度を持つ非常に丈夫な部品を製作できます。造形中は未焼結のパウダーが造形品を支えるため、効率的なパッキングで生産量の拡大が見込め、同時に後処理にかかる作業もこれまでより削減できます。
3年前までは、最も安価なSLSプリンタでも200,000ドルという価格帯で、最大級の産業用プリンタとなると数百万ドルにもなっていました。それが現在ではナイロン部品を製作可能なベンチトップサイズのSLSプリンタが1万ドル台で入手できるようになり、より多くのユーザーがこの技術にアクセスできるようになったほか、設備の総所有コストを考えると製造コストを大幅に削減できるようになりました。ベンチトップサイズのSLSは、ラピッドプロトタイピングにとどまらず実製品用部品の製造まで活用範囲を拡大する可能性を秘めています。
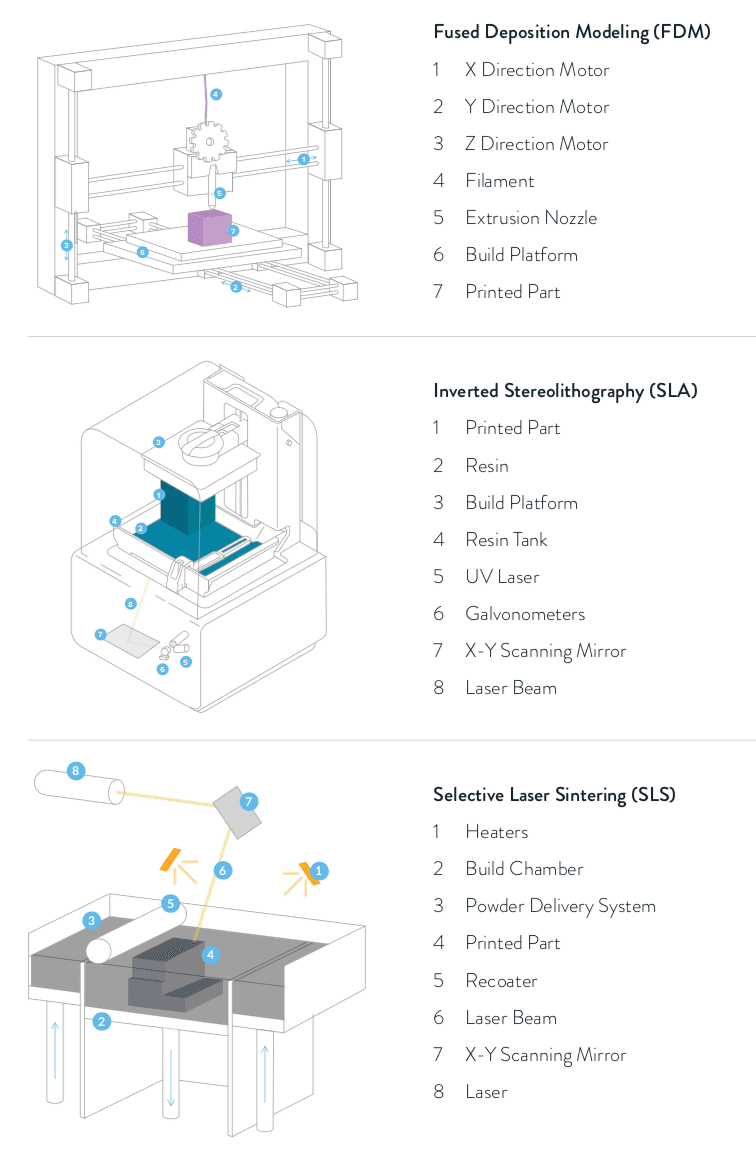
プラスチックを使った3Dプリントで最も一般的な方式。FDM(熱溶解積層)方式3Dプリンタは熱可塑性プラスチックのフィラメントを溶かしノズルから射出することで造形する。SLA光造形方式はレーザーを照射することで液体レジンを固め、SLS(粉末焼結積層造形)方式は高出力のレーザーをパウダー状のポリマー粒子に照射し焼結させる。
金属3Dプリント
常にアディティブマニュファクチャリング市場の上位に位置してきた金属3Dプリント市場は、ここ数年でも投資が飛躍的に伸び続けています。
金属3Dプリントは、航空宇宙や医療機器のような要求の厳しい高価値産業にとって、エキゾチックな形状を持つスチール、チタン、ニッケル合金、アルミニウム製の非常に高機能な部品を製作できることが魅力です。これらの業界においては、3Dプリントを金属部品の製造に最大限活用できます。特にジェネレーティブデザインを活用した高度な格子状設計や、材料の必要量と部品重量を削減するその他の複雑形状部品を製造できます。
従来の金属プリントで最も一般的なのは、SLM(レーザー溶融)方式とDMLS(直接金属レーザー焼結)方式です。プラスチックを使用するSLSと同様、これらのプロセスでも粉末材料を薄く敷き詰め、熱源を使用して粉末を選択的に溶融させることによって造形します。しかし金属の融点が高いため、より強力なレーザーと工業レベルの作業環境が必要になります。
このような金属3Dプリンタは非常に高価で工程が複雑なため、ごく最近までは高価値な少量生産が求められるやや限られた範囲以外の用途ではあまり実用的ではありませんでした。DMLSおよびSLM金属プリンタは40万ドル〜100万ドルをはるかに超える価格で、高度な熟練技術を持ったオペレーターと慎重に制御された環境が必要になります。プラスチックを使ったSLSプリントとは異なり、レーザー焼結で金属部品を作る場合はサポート材が必要です。後処理には多くの作業が必要となり、最終的な要件を満たすためにそこからさらに機械加工が必要になる部品もあります。
金属3Dプリント分野はここ数年、活発な投資の対象となっています。2016年、GEは金属AMのリーディングカンパニーであるConcept LaserとArcamの2社を買収しました。Desktop Metal、Markforged、Xjetなどのベンチャー企業数社は新たな金属3Dプリントの開発を模索中で、造形単価を下げ、幅広い用途で手頃な価格で金属3Dプリントを使えるようにすることを目標としています。
ローエンドから市場に新たな基準を打ち立てることを目指すDesktop MetalとMarkforgedは、FDMと同様の仕組みを持ち、プラスチックマトリックスに金属粉末を結合させた複合材料を使用する、コンパクトで利用しやすい金属プリンタを開発しました。プリント後は造形品を洗浄し、炉で焼結することでバインダーを除去し金属粉末を融合させ、固体の金属部品にします。必要な設備一式の価格は約10万ドルからで、従来のレーザーベースの金属AM設備よりもはるかに安価になっています。
Desktop Metalの2番目のハイエンド生産システムは、金属射出成形で実績のある材料とバインダージェッティングに似た技術を組み合わせ、エコシステムを飛躍的に発展させコストを大幅に削減するものとなっています。XJetのメタルジェット技術は、液体の中に金属粒子を保持し熱で放散させることで、固体の金属やセラミック部品を形成します。
これらの技術は、金属3Dプリントを大衆に普及させることはまだ不可能であるものの、小規模から中規模製造が求められる様々な業界でアディティブマニュファクチャリングの活用範囲を大幅に拡大し、金属部品のプロトタイピングや製品開発プロセスを近代化するものとなるでしょう。

Desktop MetalのStudio SystemはFDMと同じ仕組みだが、プラスチックマトリックスに金属粉末を結合させた複合材料を使用する。プリント後は造形品を洗浄し、炉で焼結することでバインダーを除去し金属粉末を融合させ、固体の金属部品にする。画像提供:Desktop Metal
作業工程の自動化と高効率化
これはいささか非直感的かもしれませんが、AM工程の中で最もコストがかかるのは実は人件費なのです。3Dプリンタはボタンを押すだけで完成品を製作できる魔法の道具ではありません。オペレーターが造形品をプリンタから取り出し、ある程度の後処理を行う必要があります。この後処理には、粉末を軽く取り払うだけで済むものや溶剤による入念な洗浄が必要になるもの、熱による処理や研磨、コーティングが必要になるものまで様々な種類があります。製造現場を支える基盤としてAM技術が活躍するためには、この作業量を減らし既存の作業工程に容易に組み込めるようにする必要があります。
現在は作業工程と技術の改善により、人件費の削減が見込めるようになりました。デュアルノズルを備えた一部のFDMプリンタは、溶剤で簡単に洗い流せる可溶性のサポート材が使用できます。SLA光造形製品の中には、洗浄と二次硬化の自動化装置で後処理作業を簡素化します。プラスチックベースのSLSプリントではサポート材が不要なため、後処理にかかる作業は他の方式に比べて少なくなる傾向にあります。さらに、1回のプリントでより多くのモデルをパッキングして造形可能なため、造形品一点ごとに求められる作業も削減できます。金属AMメーカーは、粉末の管理や造形品の取り出し、熱処理、造形品の取り外しといった一連の後処理作業を簡素化する、半自動化装置を提供するところが増えています。
1980年代にコンピューティングがメインフレームからデスクトップPCに移行したように、3Dプリントもモノリシックから分散型に移行しています。Formlabs、Stratasys、3D Systems、Mass Portalはいずれも、プラスチック専用の自動化されたコンパクトなモジュール型プリンタを導入しています。ロボットアームとガントリー・システムが造形品の取り外しを行いオペレーターの作業を軽減する一方、1日24時間の稼働が可能なことで営業時間外での連続生産も可能にします。プリントキューを最適化するスマートセル管理ソフトウェア、リモート監視、工場のCRM、ERP、MESシステムとの統合なども可能です。多数のセンサーが造形失敗を検知し、オペレーターを保護します。モジュラーシステムは冗長性の観点でもメリットがあり、1台のプリンタが故障しても他のプリンタが作業負荷を分散することで、中断することなく生産を継続できます。
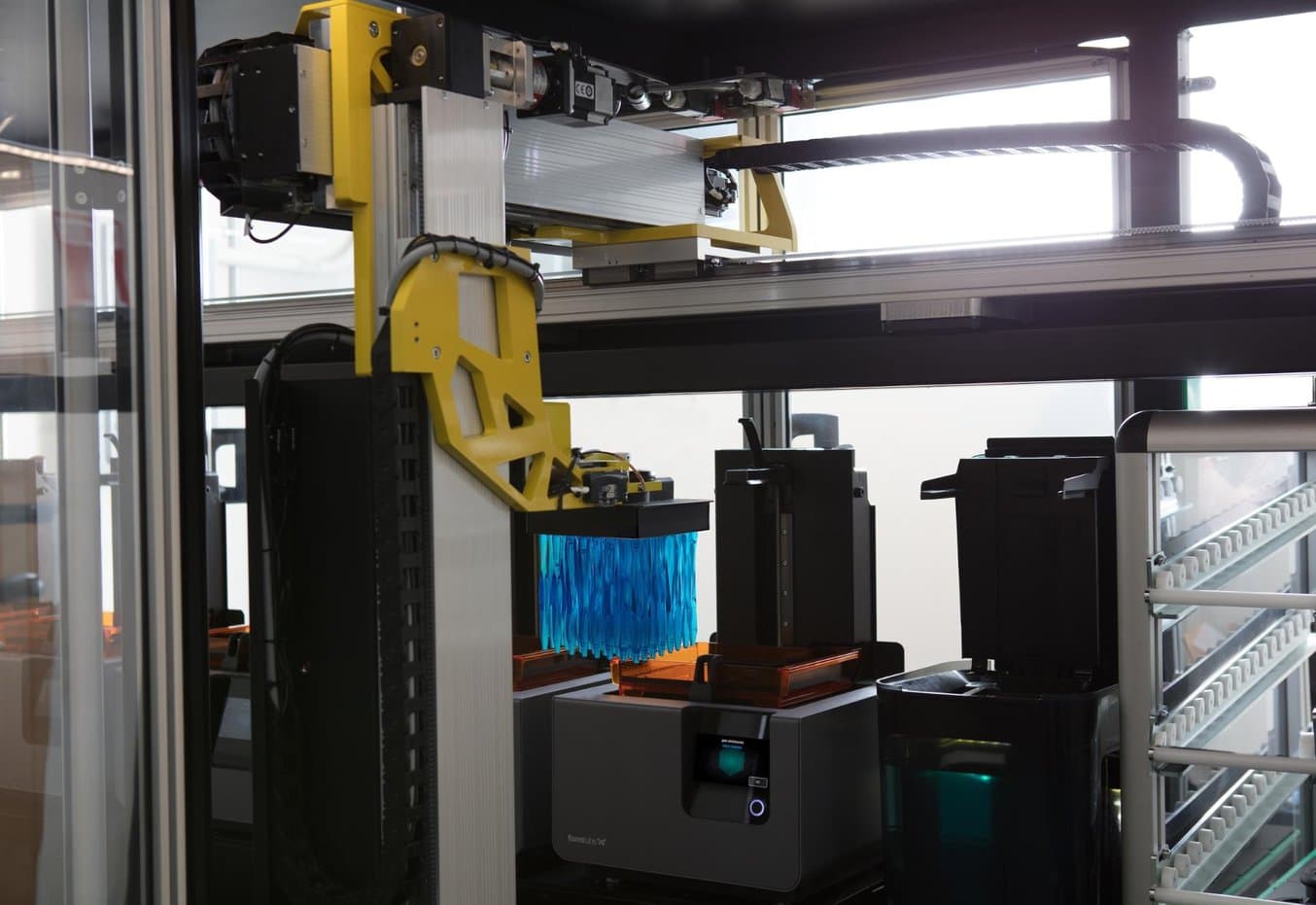
Formlabsが開発したモジュール式生産セル、Form Cellは、ロボットアームとガントリー・システムを使用して造形品を取り外し、洗浄装置で洗浄してからラックに載せて後処理の準備を行うことで、人の手による作業を大幅に削減できる。
これらの自動化製品によってデスクトップサイズのプリンタ群を量産マシンに変えることができ、3Dプリントの経済性を高め、低コストで高い生産性を実現します。さらに、エンジニアとデザイナーが同じ3Dプリントプラットフォームでプロトタイピングと製造の両方を行えることで、コストのかかる製造性を考慮した設計プロセスを削減し、製品開発サイクルを短縮できます。
自動化製品が改善され、不規則形状や1点ものの造形品でも処理できるようになれば、3Dプリントの他の工程も自動化がさらに進んでいくでしょう。ロボットがサポート材の取り外しやコーティングを行い、接着剤を使用して複数の3Dプリント品と従来の部品を組み合わせる、デジタルファブリケーションを超えた「デジタルアセンブリ」が実現できるかもしれません。
材料の進化
アディティブマニュファクチャリングは、製造におけるスイスアーミーナイフと言われています。幅広い材料に対応しているため、材料を変えることで1台のプリンタで様々な用途に向けた部品を製造できることが理由です。
この万能性を示す最たる例の1つが、SLA光造形方式のようなレジンベースのポリマー3Dプリントです。コンパクトなデスクトップサイズのSLA光造形3Dプリンタにより、小さな歯科医院では生体適合性のあるスプリントやサージカルガイドを、自動車工場では治具や固定具、耐熱成形型を製造できます。
その他の3Dプリント用高機能材料も同様に、これまでアナログだった工程のデジタル化を可能にします。高温レジンは低圧のプラスチック射出成形に使用でき、ピューターのような柔らかい金属の鋳造にも使用できます。成形品質は硬い金型と全く同じにはならないかもしれませんが、3Dプリント製の成形型の導入により、金型製作コストの回収が難しい小規模または中規模生産の現場では重要なニーズを満たせる手段となっています。
SLA光造形、SLS、FDMは工業生産ラインで使用する治具や固定具を製造することで、機械加工などコストのかかるサブトラクティブマニュファクチャリングの代替案となります。FDM用のPEEK、ULTEM、エンジニアリング用強化熱可塑性プラスチックは、機械的特性と耐熱性の高さから金属部品に代わる役割まで果たすことができます。また、新しいセラミックのSLA光造形用材料は、非常に優れた耐熱性と対薬品性を備えています。
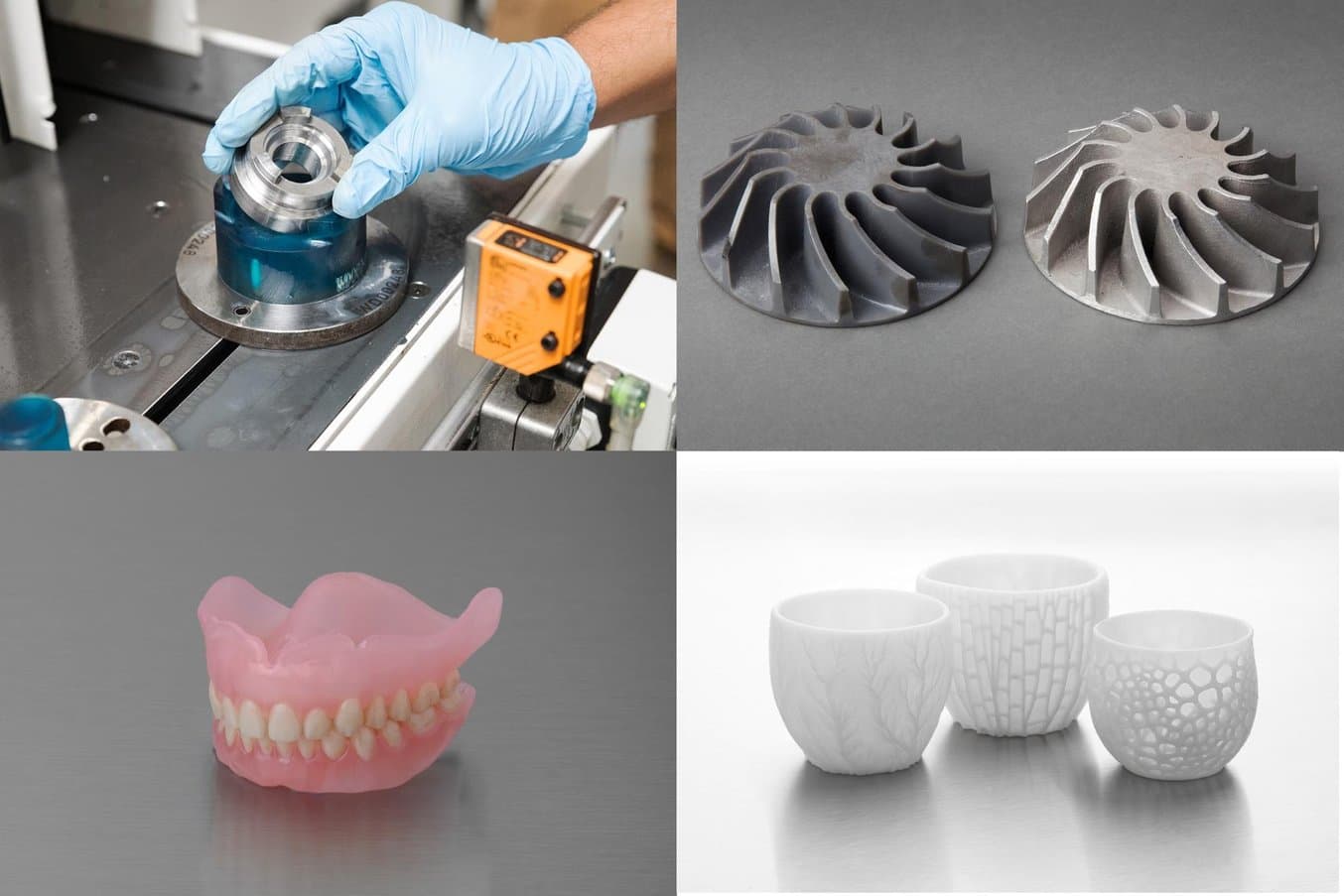
同一のSLA光造形3Dプリンタを使って4種類の造形品を製作。写真左上から右下にむかって、自動車メーカーの自動生産ラインで使用する固定具、3Dプリント製の原型を使って鋳造した金属部品、生体適合性を備えたデンチャー、セラミックの器。
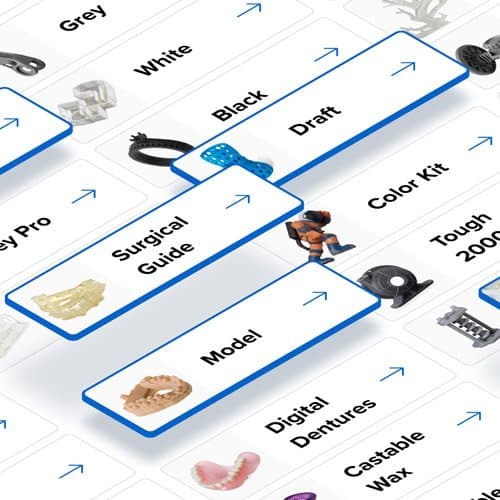
用途に合った最適な材料選定をサポート
どの3Dプリント用材料を選ぶべきか、お困りですか?最適な材料は、用途や求める特性に応じて変わります。インタラクティブなマテリアルセレクターは、拡大を続けるFormlabsの豊富な材料ライブラリからお客様にあった最適な材料の選定をサポートします。
生産のコスト効率を高める
3Dプリントは、あらゆる製造ニーズに対応できる万能薬ではありません。これまで3Dプリント導入の恩恵を最も受けられるのは、最も価値が高く、高度にカスタマイズされた少量生産の場面だということがわかっています。大量生産の場合、従来の製造方法を使った方がコスト効率が高いことに変わりはありません。そうはいっても、3Dプリントの価格が手頃になるにつれて造形単価も変化してきました。より低価格で大量生産を行う用途でも、3Dプリントの導入が現実的になってきています。技術と材料特性の進化により、アディティブマニュファクチャリングは今後ラピッドプロトタイピングにとどまらず実製品用部品や大量生産用途でも導入されていくでしょう。
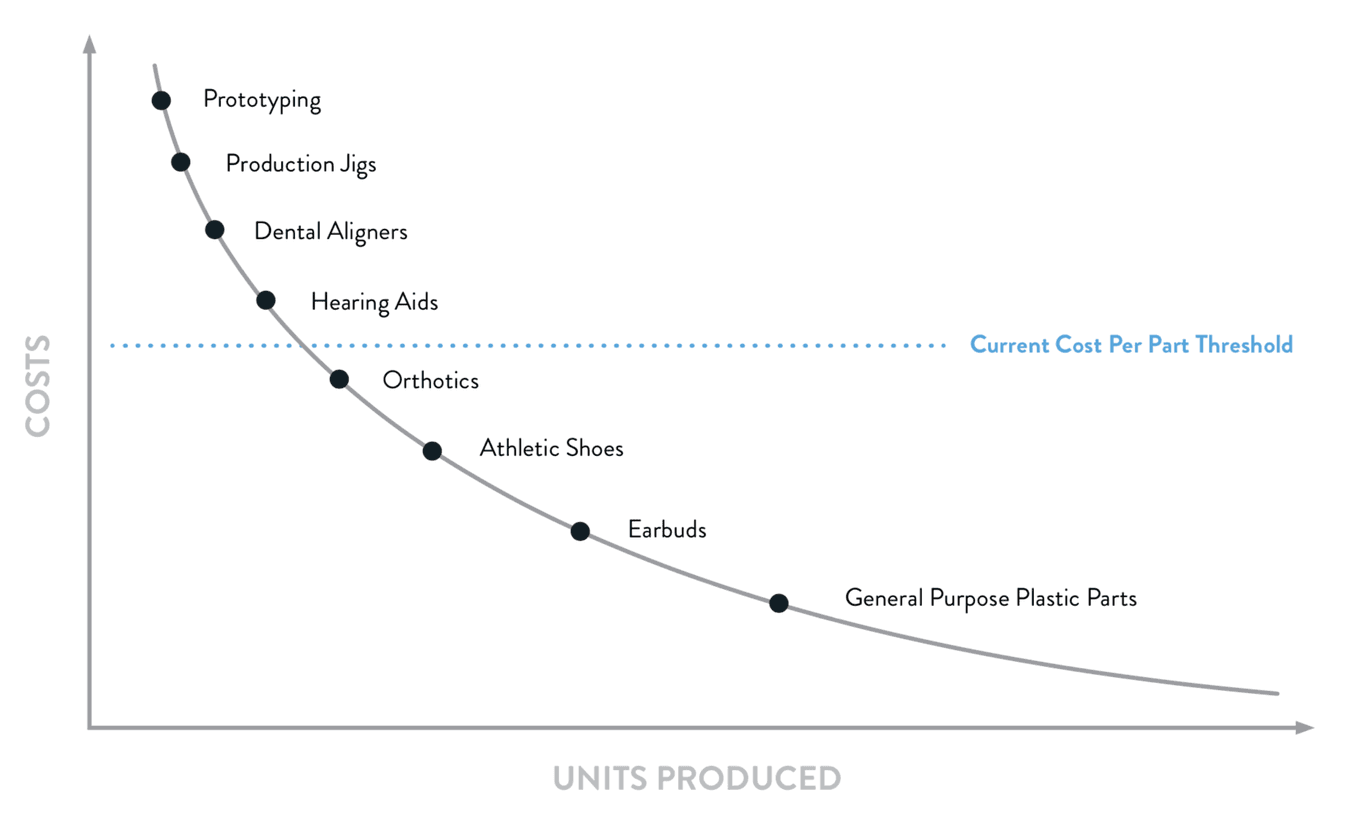
3Dプリントの価格が手頃になるにつれ、部品1個あたりの造形単価も変化してきた。より低価格で大量生産を行う用途でも3Dプリントの導入が現実的になってきている。
現在は、従来の製造方法に組み入れる形で3Dプリントを取り入れるハイブリッド生産が主流です。例えば宝飾業界では、インベストメント鋳造工程の一部として3Dプリントが活用されています。ジュエリーメーカーはまずデジタルで作品をデザインし、鋳造可能なレジンを使って3Dプリントします。その後、砂に似たインベストメント材料に浸し、宝石職人がワックスで作る通常のものと同様、オーブンで綺麗に焼き切ることで貴金属用の鋳型が完成します。
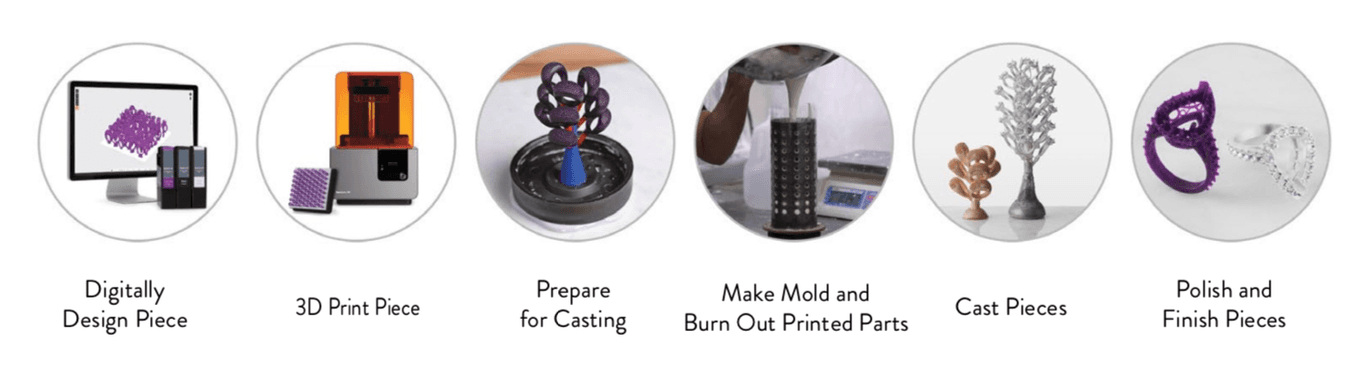
3Dプリントを取り入れたハイブリッド生産で手頃な価格のカスタムイヤホンも製造できます。このプロセスでは、3Dスキャナを使用して利用者の外耳道を素早くデジタルスキャンすることから始まります。技術者がデジタルファイルを3Dプリント可能な型に編集し、SLA光造形3Dプリンタに無線で送信します。プリント完了後は造形品を洗浄し、その中に生体適合性のあるシリコンを流し込みます。その後、3Dプリント製のシェルを取り外し、実製品の仕上げとコーティングを行います。このように、実製品自体は3Dプリントされていないにもかかわらず、3Dプリントがこれら伝統的な職人技が光る製造工程に欠かせない一部となっています。
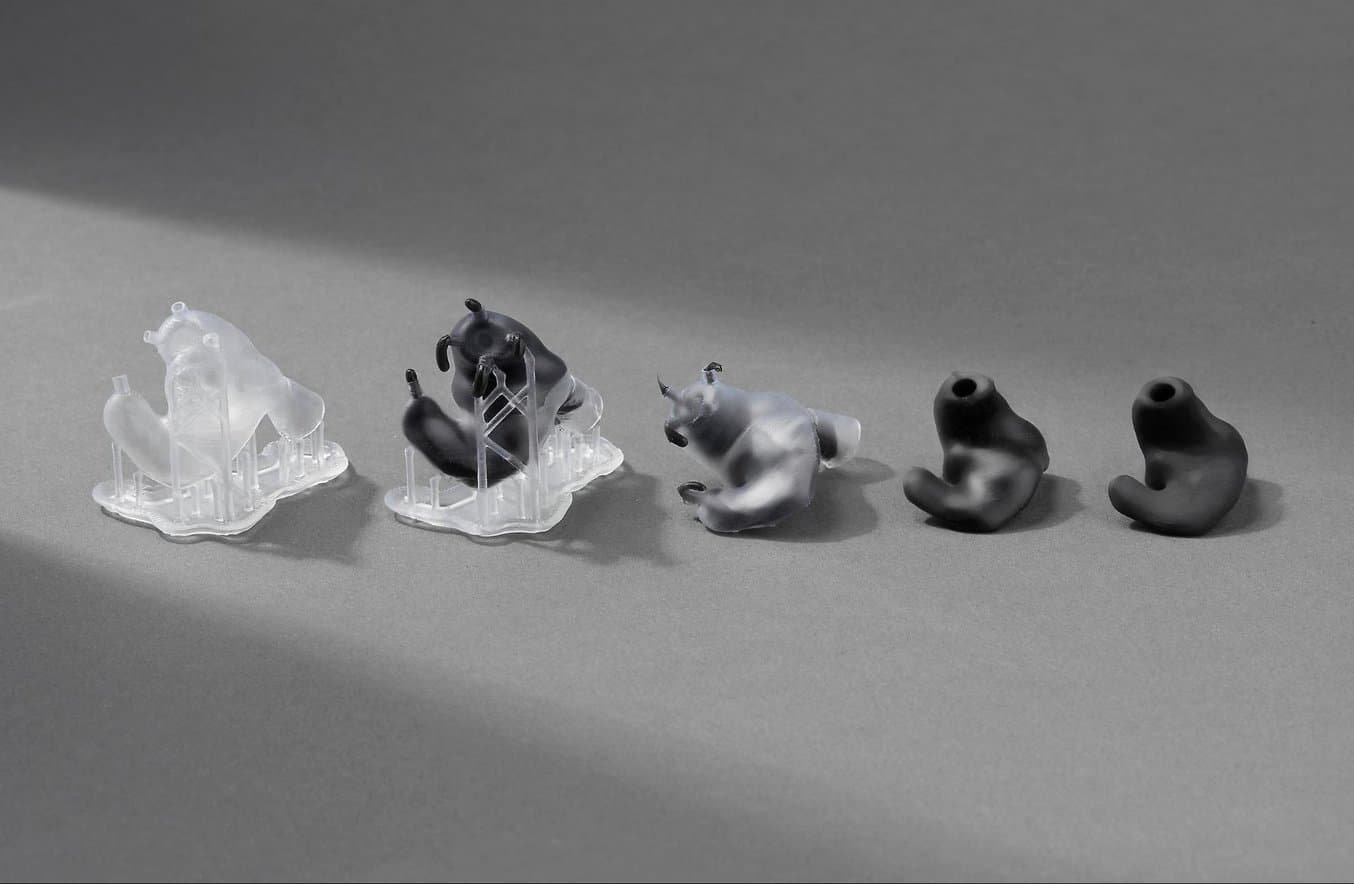
カスタムイヤホンは、3Dプリントされた中空の鋳型に生体適合性のあるシリコンを流し込んで作られる。3Dプリント製成形型の1つあたりのコストはレジンが0.40~0.60ドル、最終的に製品となるイヤホンの製造工程全体では原材料費が約3~4ドル。
歯科、医療器具、オーディオ製品などの生産を担う業界では、患者一人ひとりに合わせた実製品を製造するために3Dプリントの導入が急速に進んでいます。歯科診療所や歯科技工所での3Dプリントの使用が一般的になると、生体適合性材料でスプリントや義歯を直接製造するなど、ますます活用範囲が広がっていくでしょう。オーディオ機器の分野では、すでにカスタム補聴器のほとんどが3Dプリントで製作されています。より広い医療市場にも大きな可能性があります。例えば、丈夫で生体適合性のあるSLS品は、カスタム装具や皮膚接触のあるその他装具の製造に使用できます。
コストが下がるにつれ、アディティブマニュファクチャリングは従来型の消費者向け製品の製造にも活躍の場が広がると見込まれています。例えば家電業界で最も生産量の多い分野では現在、射出成形がプラスチック部品を製造する唯一の実用的な方法です。しかし、エレクトロニクス業界の中規模製造セグメントでは3Dプリントが定着し始めています。射出成形の代わりにアディティブマニュファクチャリングを使用することで、電子機器メーカーは製品設計と生産を合理化し、柔軟性を維持することができます。また、3Dプリントを取り入れた工程では金型製作が不要なため、生産量が1万点を超える場合は射出成形との損益差がなくなります。
New BalanceやAdidasなどのシューズメーカーは、今後数年以内に硬質ポリウレタン(RPU)を使って3Dプリントしたカスタムシューズのミッドソールを量産する計画を発表しています。ここでも3Dプリントは他の製造方法と組み合わされ、製品の中で最も重要かつ高度にカスタマイズされた部分の製造を担い、他の部分はコスト効率の高い従来の製造方法や加工が用いられることになります。
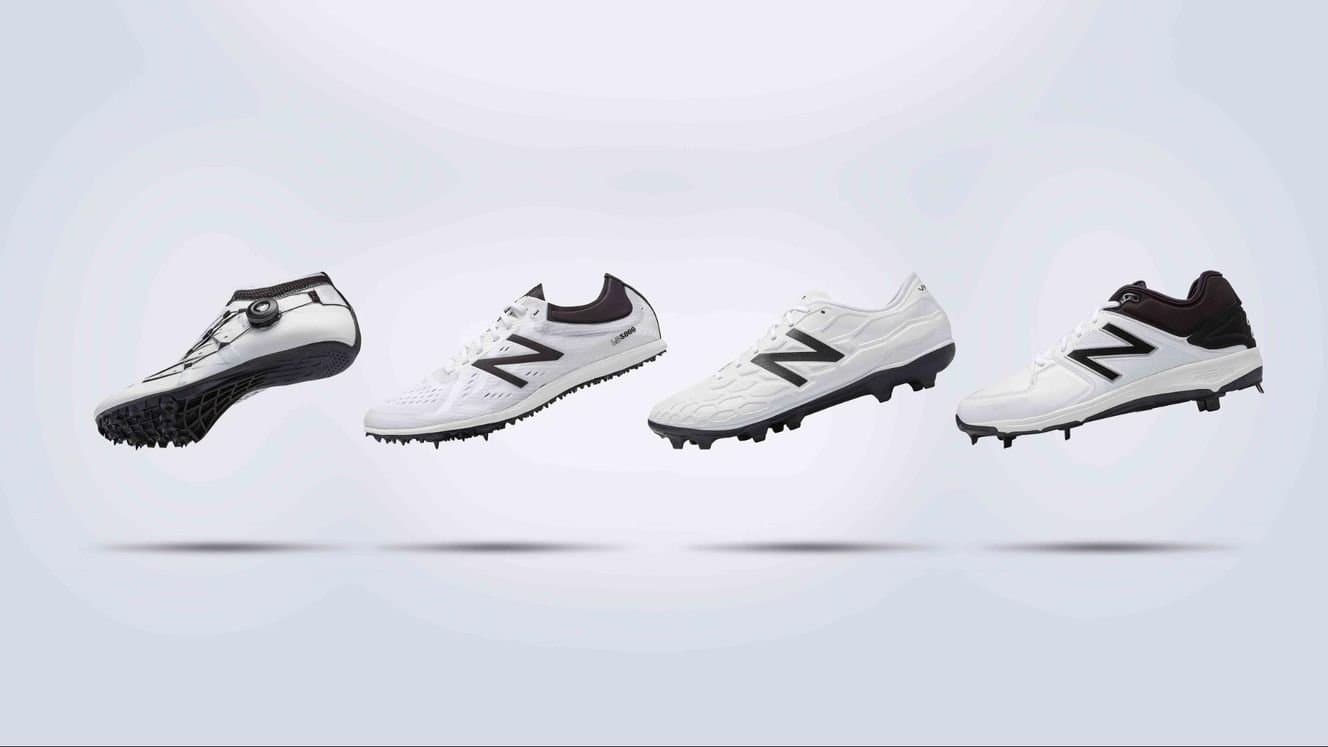
3Dプリント製ミッドソールを採用したNew Balanceのシューズコンセプト。
エンジニアリング・製造業界に変革を起こす3Dプリントとデジタル技術
こちらから2022年 3Dプリント活用レポート「Digital Factory Report」をダウンロードいただけます。また、こちらのポッドキャストでは製造業界におけるデジタルトランスフォーメーションのほか、アディティブマニュファクチャリングやAI、ロボティクス、オートメーションといった様々な技術に関するインサイトを共有しています。次回Digital Factoryカンファレンスの最新情報もお見逃しなく。Align Technologies CEO、FedEx CIO、GE CTO、Desktop Metal CEO、Form Motorの製造部門ヘッドなど、前回カンファレンスのスピーカーを含むデジタルマニュファクチャリングを牽引するリーダーたちが講演予定です。
アディティブマニュファクチャリングのハードウェアや材料は今もなお急速に進化を遂げており、造形単価も大幅に低下していることから、少量や中規模の生産プロジェクトでも広く活用できる道が開かれつつあります。業界をリードする主要なメーカーがいかにアディティブマニュファクチャリングを取り入れ、コストやリードタイムの削減、複雑な問題の解決やプロトタイピングから量産までのプロセス改善に役立てているかを直に学べるこの絶好の機会を、どうぞお見逃しなく。