組立ラインから出荷される新車の3台に1台は、Broseが製造した部品を搭載していると言っても過言ではありません。家族経営の自動車サプライヤーとして世界5大企業の一つに入るBroseは、100年以上も前にMax Broseによってベルリンで創業を開始し、自動車用アクセサリーの商社からメカトロニクスシステムのマーケットリーダーへと成長しました。Broseは、BMW、Volvo、Ford、Mercedes、Jeepなど、自動車業界の有名企業向けにシート、リフトゲート、ドアアセンブリを中心とする製品を設計・製造しています。
Broseの着実な成長と、これら大手OEMとの長期的なパートナーシップの成功は、継続的な革新と改善に対する同社のコミットメントの表れとも言えます。そんなBroseの設計および実製品用部品の製造プロセスでは、3Dプリントが中核的な役割を果たしており、めまぐるしく変化する自動車業界への適応・対応をサポートしている。
私たちは、ミシガン州オーバーンヒルズにある本社Brose North Americaを訪れました。本社であると同時に同社最大の実製品用部品の製造拠点の1つでもあるこの拠点で、パワフルなSLA光造形およびSLS(粉末焼結積層造形)3Dプリンタがどのように実用化されているのか、お話を伺いました。リージョン内でAdditive Technologyチームの責任者を務めるシート部門プロトタイピングマネージャーのMatthias Schulz氏が、Broseが設計から製造に至るまで、OEM向けに厳しいスケジュールが求められる工程を通して3Dプリンタをどのように活用しているのかを教えてくれました。
「自動車業界では、特にここ5年で急激な変化が起こっていると感じます。新製品の開発期間は大幅に短縮されました。それに合わせて迅速に対応するために、これまで以上にアディティブテクノロジーを実装していく必要がります。アディティブテクノロジーは、金型製作などにかかる時間を短縮し、その後の工程でも部品をより早く生産する助けになっています」
Brose North America シートプロトタイピングマネージャー、Matthias Schulz氏
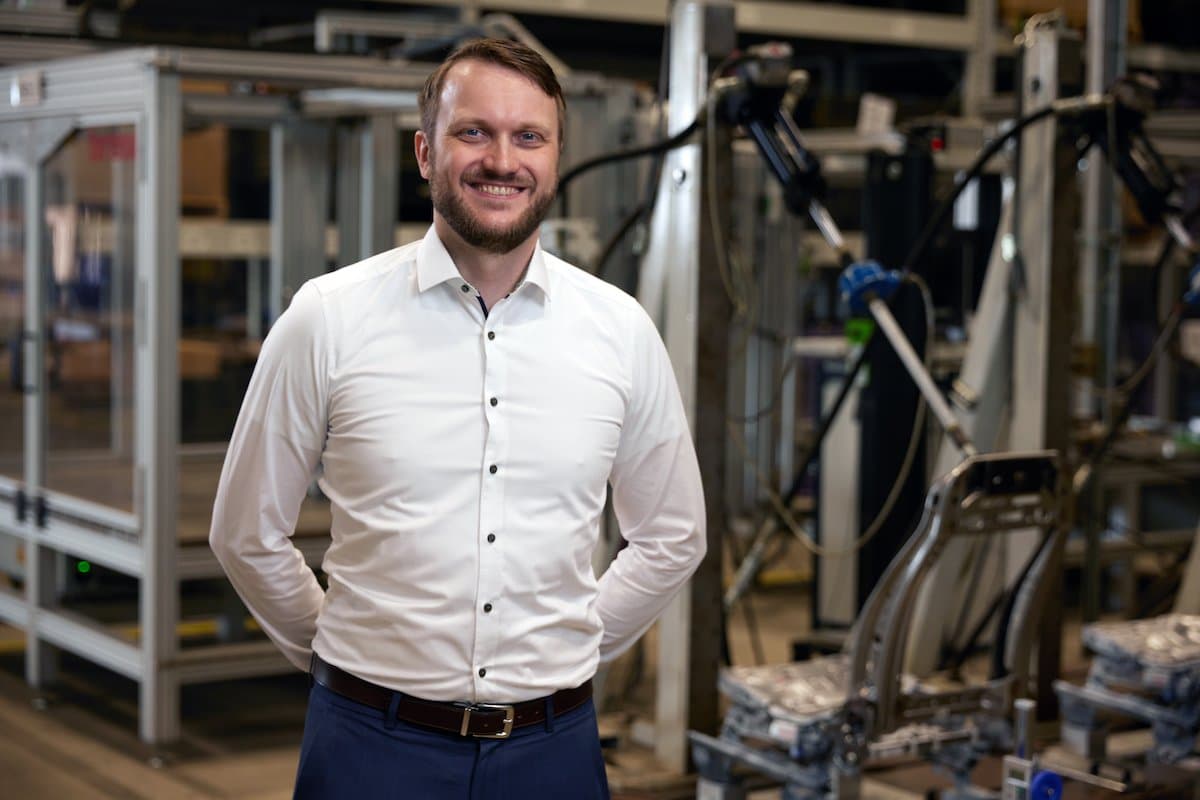
オンデマンドウェビナー:BroseでSLSを活用して自動車部品を生産
このオンデマンドウェビナーでは、Brose North AmericaのシートプロトタイピングマネージャーであるMatthias Schulz氏が、Broseで溶接用の治具から250,000点もの実製品用部品の生産まで、あらゆるものにSLA光造形・SLSを活用している方法を紹介します。
一回限りのプロトタイピングのその先へ
プロトタイピングは3Dプリントの活用方法として最適で、実績も多くあります。Broseは、プロトタイピング用に様々なFDM(熱溶解積層)、SLA光造形、SLS 3Dプリンタを採用していますが、その生産量は必ずしも概念実証(PoC)の期待に応えられるとは限りません。Broseの場合、一般的なプロトタイプの数量は500〜1,000点に上ります。
「かなり大規模に3Dプリンタを活用しています。私たちが言う『プロトタイプ』とは、数百点ものパーツをプリントすることなんです。そのほとんどがテストに使用されます。そのため、社内外の基準だけでなく連邦政府の要件も満たす必要があります。通常、プロトタイプ用にプリントしなければならない部品は700~800点になります」とSchulz氏は言います。
海外の最低発注量をきっかけにSLA光造形に転換:ゴム製シートの長さ調整アジャスターダンパー
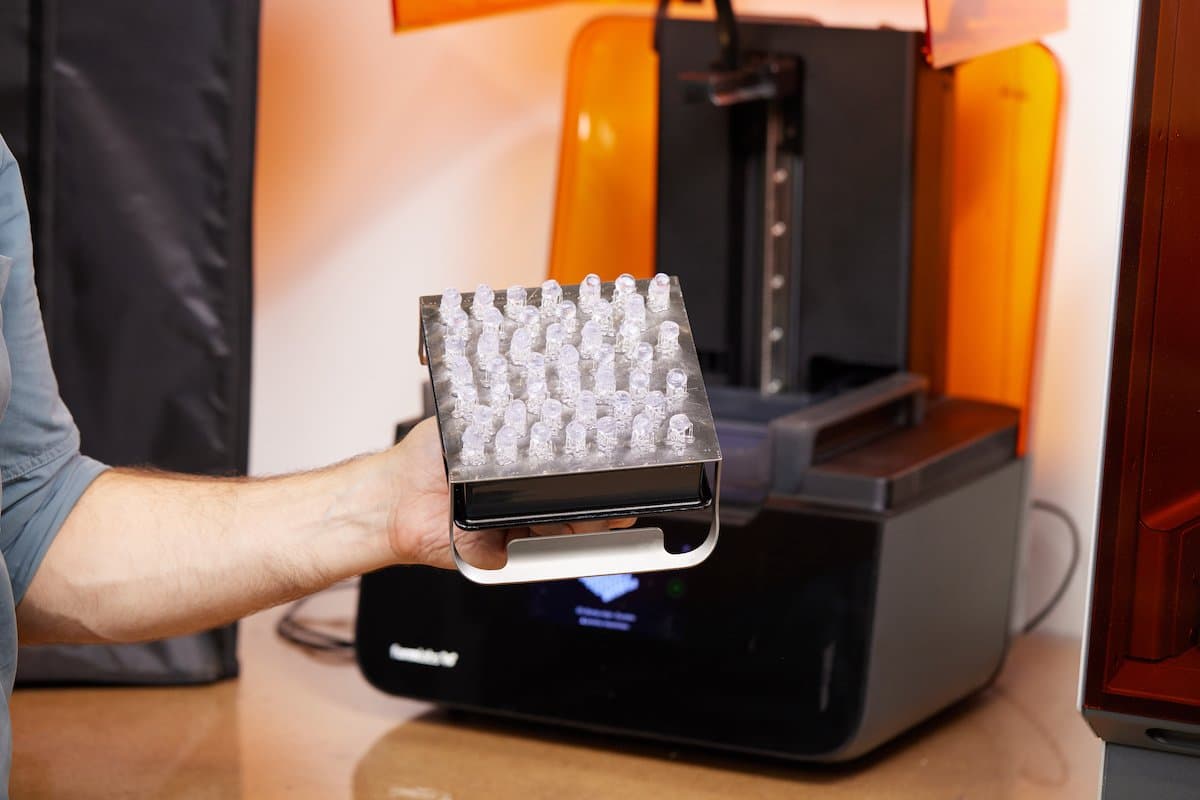
写真の試作品は、金属製のシートアセンブリがシートフレームに当たる音や感触を軽減するための小さなダンパー。海外から取り寄せるには数百万個の最低発注量を満たす必要があり、Schulz氏率いるチームはテスト用にFormシリーズのプリンタで造形した。
あるプロジェクトで、プロトタイプチームはシートアセンブリに取り付ける柔らかいシリコンダンパーを必要としていました。シートがフレーム上で前方に動くと、このダンパーが音を軽減し、シートアセンブリが動いた時の感触や音響のフィードバックを改善します。Broseがよく外注している海外のサプライヤーに注文する場合、数百万個もの最低発注数量を満たさなくてはなりません。
数百万個の部品を注文して海外から輸送するのではコストが高くつくうえに、届くまでに数週間もかかり、実際に使わなかった残り数百万個もの部品は一度保管した上で最終的に廃棄しなければなりません。そこで、部品を注文する代わりに既存のCADツールを使ってForm 4で数百個のみ素早く3Dプリントすることにしました。一週間後には全て完成し、おかげでプロジェクト全体のコストや製作期間を削減することができました。
「数百万個という最低発注数量を満たすために必要のない数を注文し、さらにそれを空輸するよりも、はるかに安いコストでForm 4でプリントすることができました。すぐに部品が揃ったので待ち時間もほとんどありませんでした」
Brose North America シートプロトタイピングマネージャー、Matthias Schulz氏
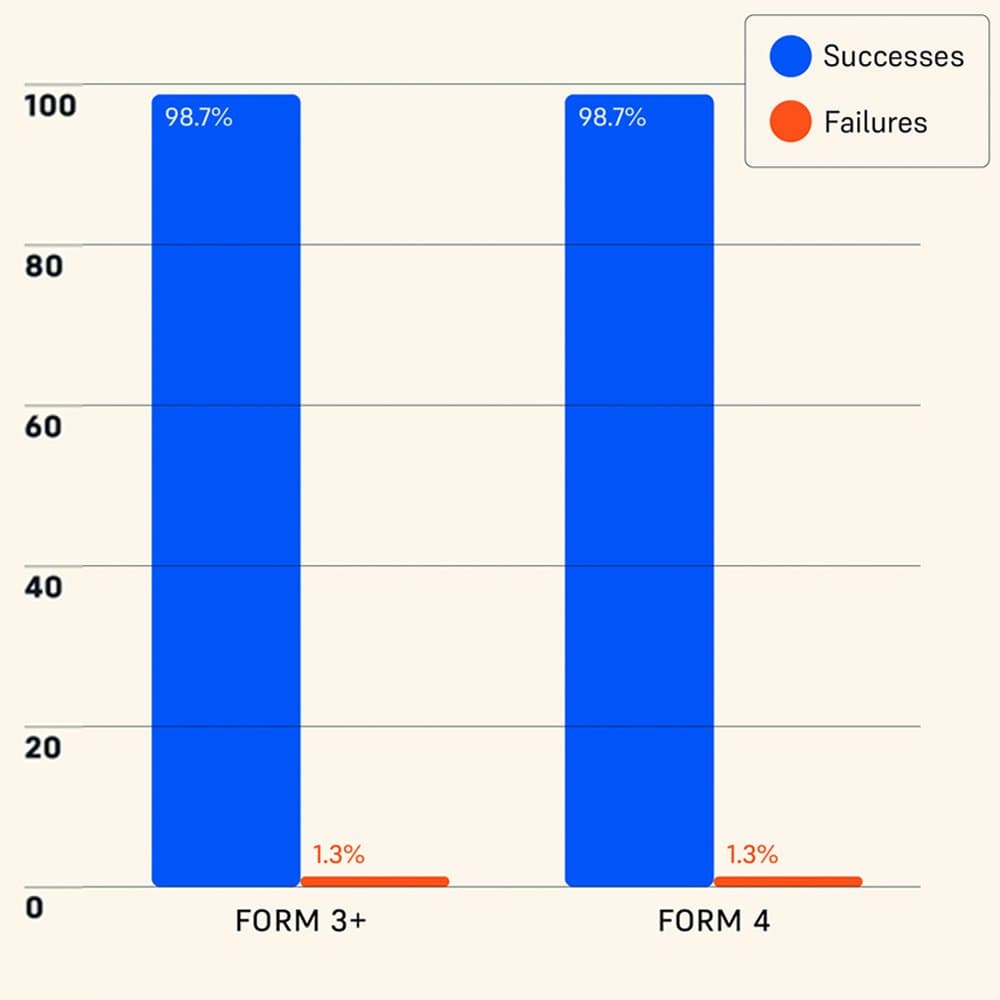
Form 4と他社製光造形3Dプリンタの信頼性に関する第三者試験
独立試験機関により、Form 4 のプリント成功率は 98.7 % と評価されました。テスト方法と結果の詳細についてはこちらの技術資料でご確認いただけます。
SLA光造形とSLSを組み合わせて高い生産量に対応
アセンブリのコンポーネントがより複雑でサイズが大きく、必要な体積も大きくなる場合には、Broseは3台のFuseシリーズ SLS 3Dプリンタを使ってプロトタイプや生産を行います。SLSは造形中に未焼結パウダーが造形品を支えるため、ビルドチャンバーをいっぱいにした状態での大量の造形が可能でありながら、焼結したナイロンの強度と機械的特性を活かせるため実製品用のコンポーネントの生産に最適です。最近のプロジェクトで、BroseのAdditive TechnologyチームはSLA光造形とSLSの両方の技術を使用して、シートサスペンションマットを試作しました。
半透明で柔軟性のあるパーツはFormシリーズ SLA光造形プリンタでDurableレジンを使って造形し、マットのコネクションチューブはFuseシリーズでNylon 12 GFパウダーを使って造形しました。マットのプロトタイプ1つあたりSLSパーツが6つ、光造形パーツが3つ搭載されており、合計で150点もの組み立て済みのマットをテストしました。
ラピッドプロトタイピングツールを社内に導入したことで、Broseはシートアセンブリ製品の重要コンポーネントの設計、テスト、検証・改善の反復プロセスを金型や外注なしで行うことができました。「このシートサスペンションマットのように、SLA光造形とSLSの両方を組み合わせることで解決できることもあります。オーバーモールドの金型は非常に複雑で高価なため、SLSではワイヤーにパーツをはめ込むように設計し、SLA光造形ではワイヤーに『グリーン状態』といっていわゆる未処理・未加工状態のパーツを取り付けて硬化させました」とSchulz氏は言います。
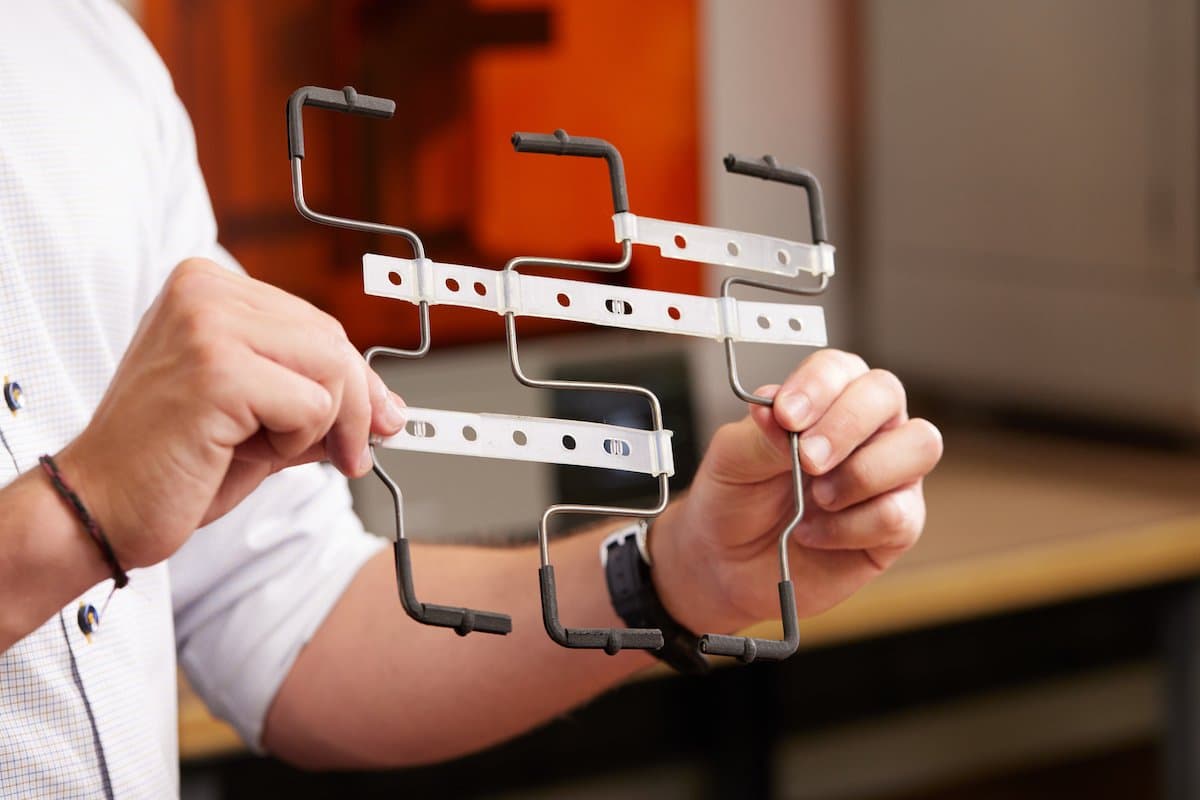
このシートサスペンションマットには、光造形パーツ(半透明材料のDurableレジンで造形)とSLSパーツ(ダークグレー材料のNylon 12 GFパウダー)の両方が使われている。試験には、SLSパーツ900個と光造形パーツ450個を搭載した計150個のフルアセンブリが必要。
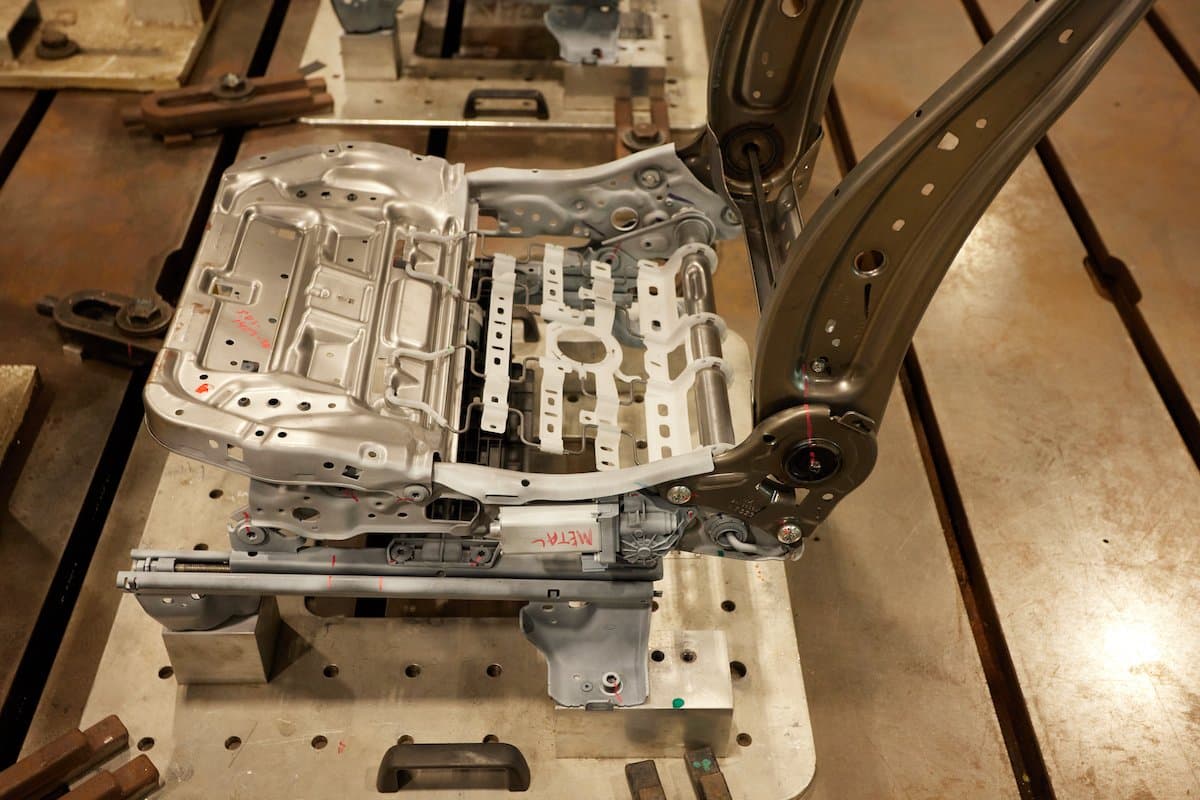
試作品・実製品用の量産部品(上図参照)は、数年にわたる使用を模した疲労試験を受ける。
生産を補助する治具で工程を合理化
Broseでのアディティブマニュファクチャリングの活躍の場は、プロトタイピングだけにとどまりません。同社では2022年から始まったPlant Goes Additive(製造拠点全体のAM移行)という取り組みの一環で、あらゆる部署でAM技術の導入が進んでいます。自動車製造工程は、高度に制御された状態でノンストップで稼働しています。プロセスの全ての箇所が高効率化、安全性と製品品質の向上のために最適化されています。
Form 4Lで溶接ロボット用の治具を同日製作
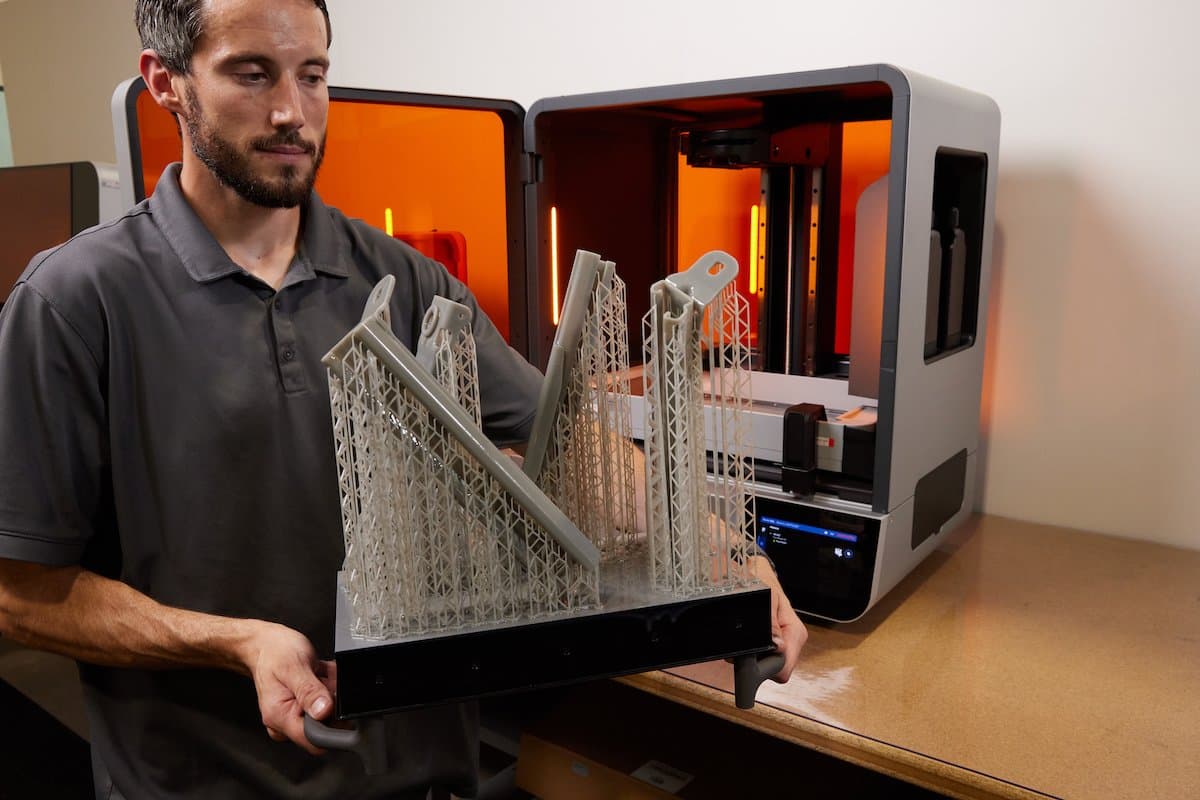
Form 4Lが大容量パーツの同日製作を可能に。写真はFast Modelレジンで造形した溶接用の固定具。
自動車のサプライチェーンのあらゆる段階において金属部品が製品の重要なコンポーネントになるのと同じく、溶接は組み立て工程で大部分を占める作業です。BroseのAdditive TechnologyチームがSLA光造形およびSLSプリンタを複数台運用するBrose North Americaでは、溶接ロボットは様々な製品ラインを常に行き来する必要があります。工場では、溶接機は1つの製品ラインに特化してプログラムされていますが、本社には2台の溶接ロボットが様々な製品ラインでシートのプロトタイプの溶接を担当します。
ロボットが新しい製品ラインに移るたびに、溶接部門はロボットのパラメータを再プログラムする必要があります。溶接ロボットのプログラミングにプロトタイプの金属レールを使用すると高額になるうえ、溶接ステーションで学習用の準備が整うまでにレールが間に合わないことがよくあります。スピードと寸法精度の両方が求められるこれらのセットアップ部品には、高速で低コストな代案として3Dプリントが活用できます。
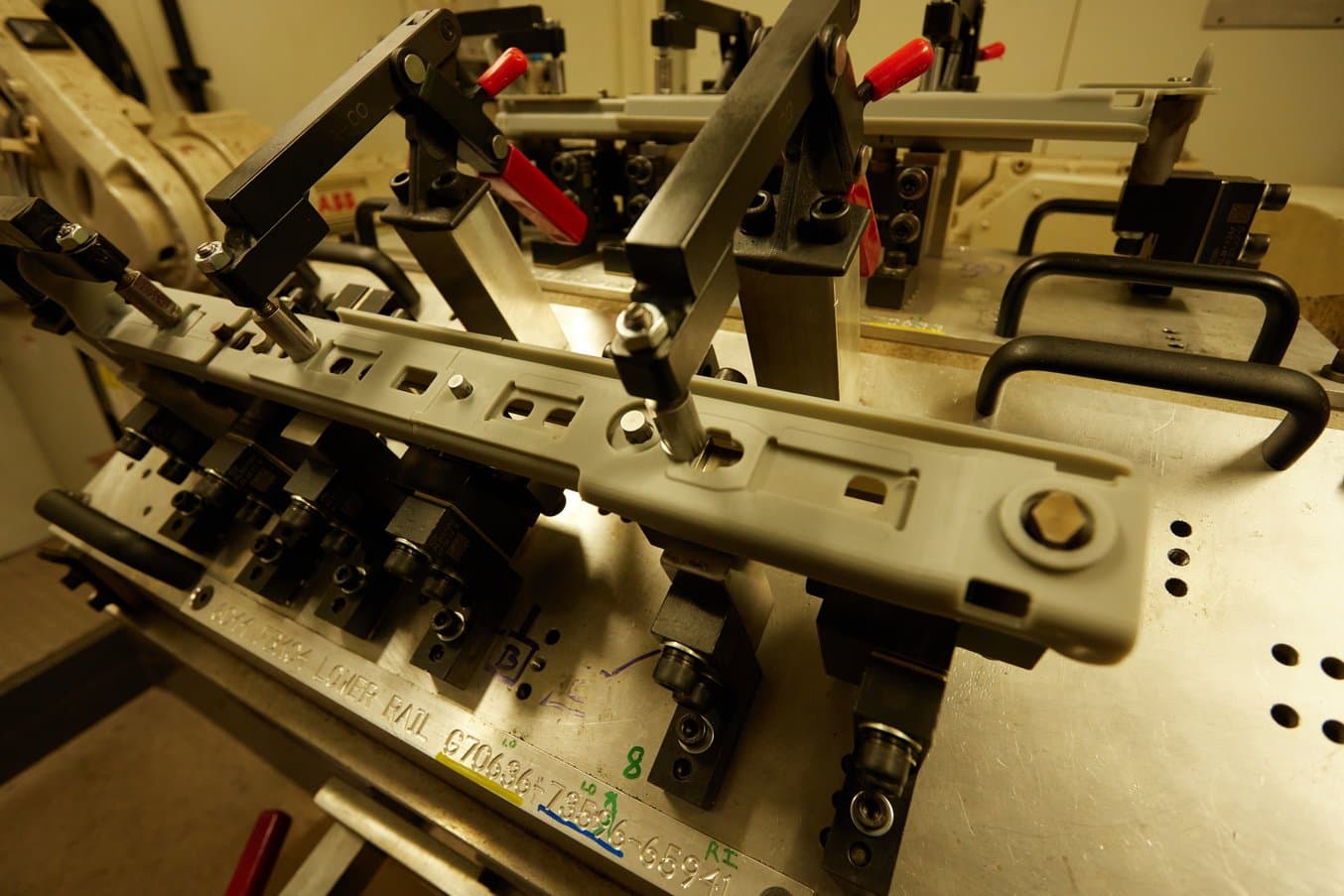
このシート用パーツはForm 4LでFast Modelレジンを使って造形。洗浄・二次硬化後に組み立てて溶接ロボットに装着。これらすべての工程が3時間以内に完了した。これで溶接ロボットに動きを迅速に学習させることができる。
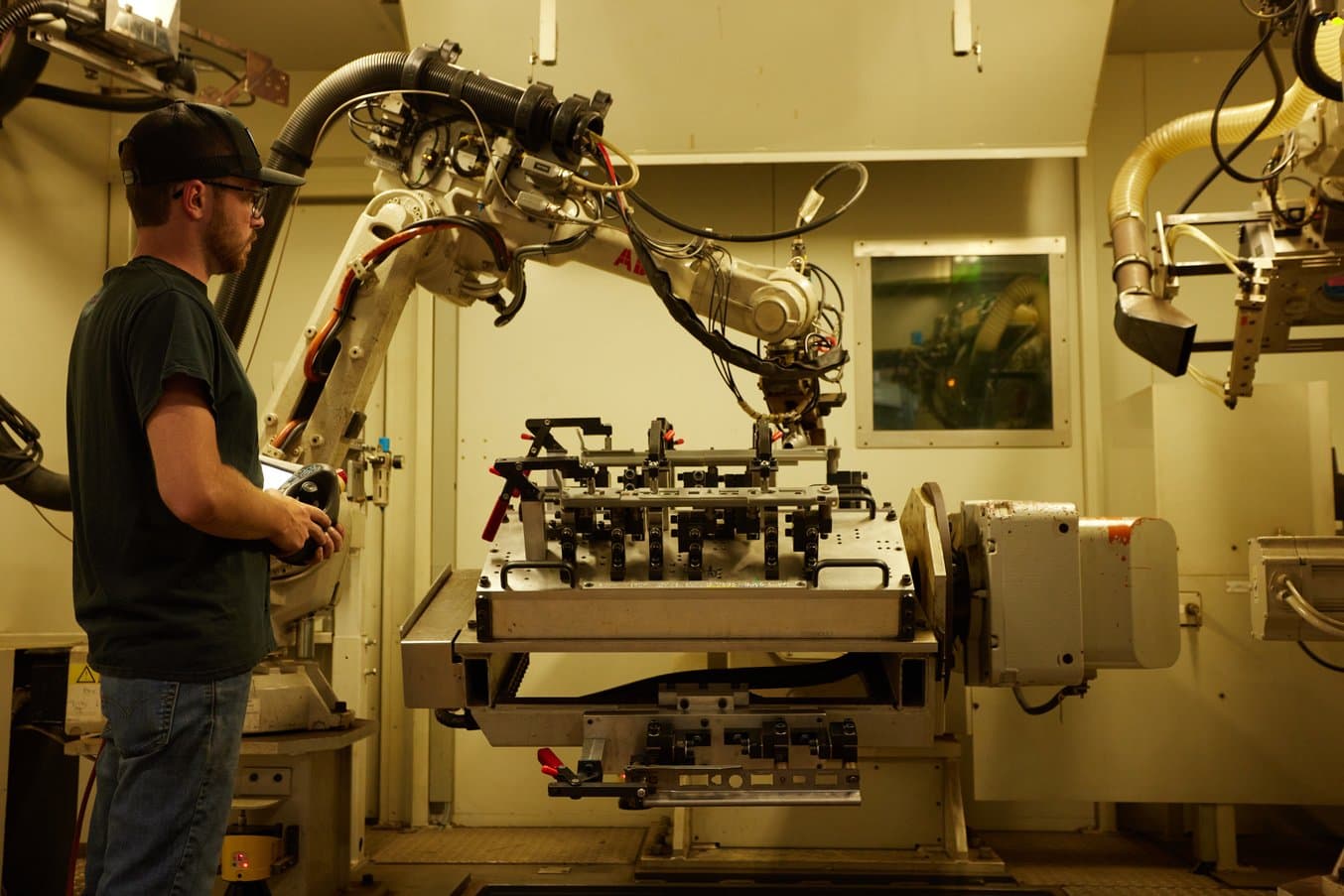
こういった治具は、溶接チームがマシンを一つの製品ラインから別の製品ラインへと迅速かつ効率的に切り替えるのに役立つ。非常に精度が高く価格も手頃なため、変更や交換が必要な場合に備えて無数の複製を用意しておくことができる。
火曜日の朝、Broseのもとに新発売となる大容量の光造形3Dプリンタ Form 4Lが届くと、チームは早速開梱に取り掛かります。セットアップにかかった時間はわずか30分。その後はすぐにFast Modelレジンを使って大型の溶接セットアップパーツを造形し始めました。4回に分けてプリントしたパーツは最大造形サイズをほぼ埋め尽くすほどの大きさであったにもかかわらず、Form 4Lはわずか2時間以内に造形を完了。取り出した造形品を素早く洗浄して二次硬化を行った後、わずか45分後には溶接ロボットに治具を取り付けることができました。
「新しいForm 4Lのおかげで大型パーツを高速造形できています。例えば、Form 4Lを使って溶接セルのセットアップパーツをプリントしていますが、一夜どころかたった数時間で完了するので、金属プレス部品が届く前にBroseの溶接エキスパートたちがロボットを事前にプログラムできるようになりました。新しいFast Modelレジンでは、これまでより短い時間で、求められるディテールや剛性を満たすことができています」
Brose North America シートプロトタイピングマネージャー、Matthias Schulz氏
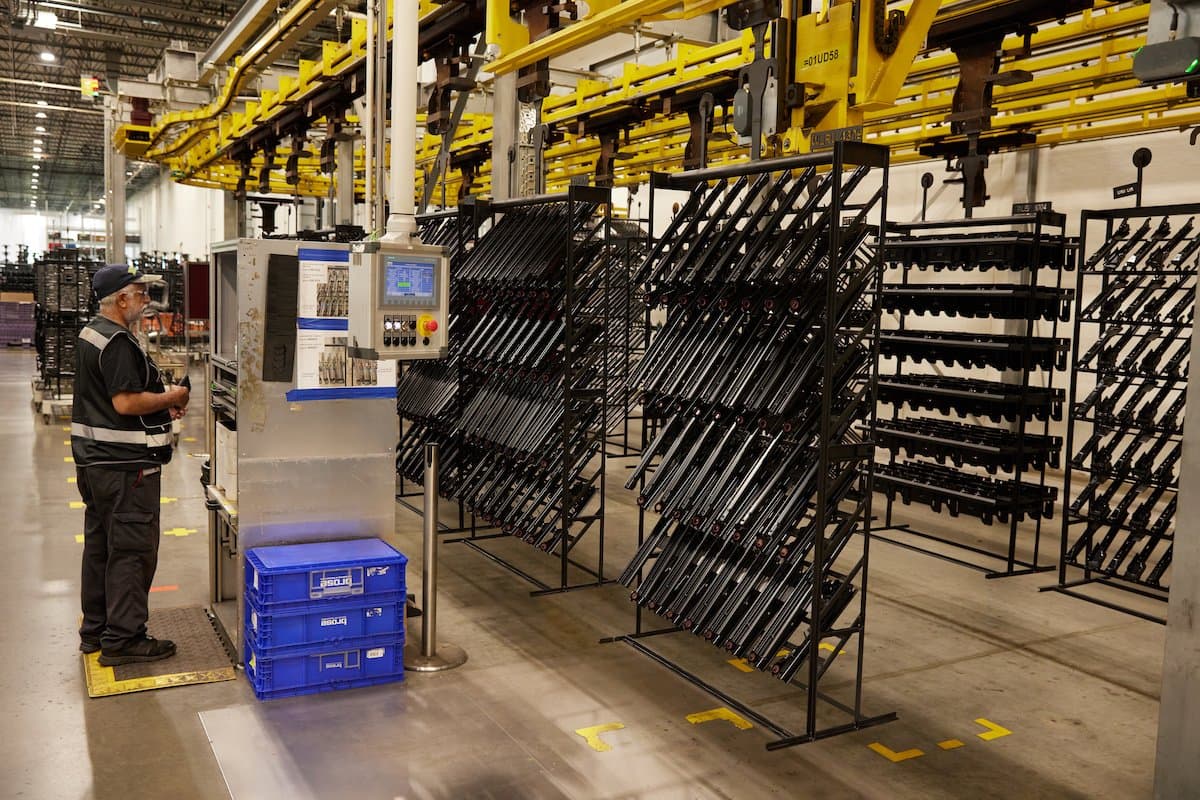
Brose New Bostonでは、写真のように何千点ものシートレールが溶接されてシートアセンブリのベースを形成する。そのため、溶接パラメータのテストは製造プロセスに欠かせない。
プロトタイプや3Dプリント製のセットアップパーツを使ってBrose North America本社で決定された溶接パラメータは、溶接シートフレームの大量生産に使用されます。写真のシートレールは、Brose New Bostonで大型の溶接ロボットを使って組み立てられます。
Brose New Boston、終端(EOL)コネクタで運用コストを削減
デトロイトのダウンタウンから西に30分ほど行った場所に位置するBroseのNew Boston工場では、組み立て工程を合理化するカスタム治具を3Dプリントで製作しています。3Dプリント製のパーツは量産に使用される前に厳しいテストを受け、そこで承認されると、廃棄物の削減や生産スケジュールの改善、機械の連続稼働を支える役割を果たします。
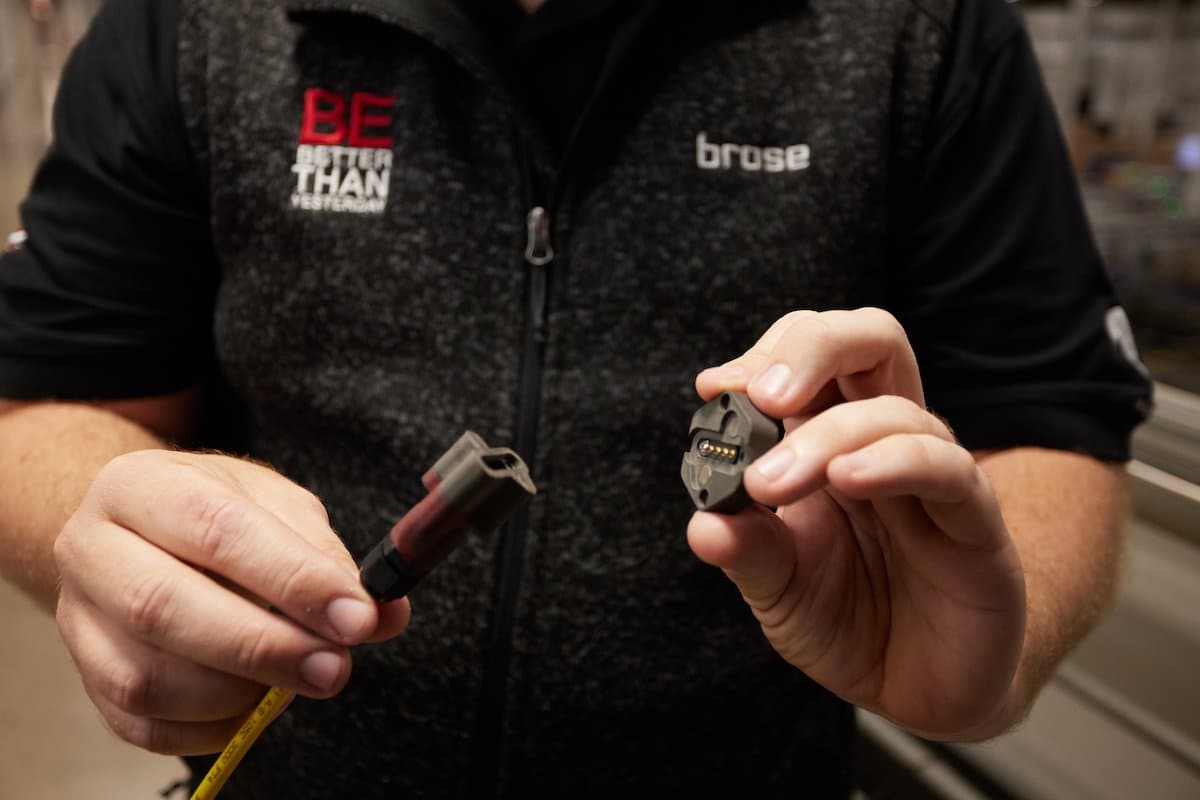
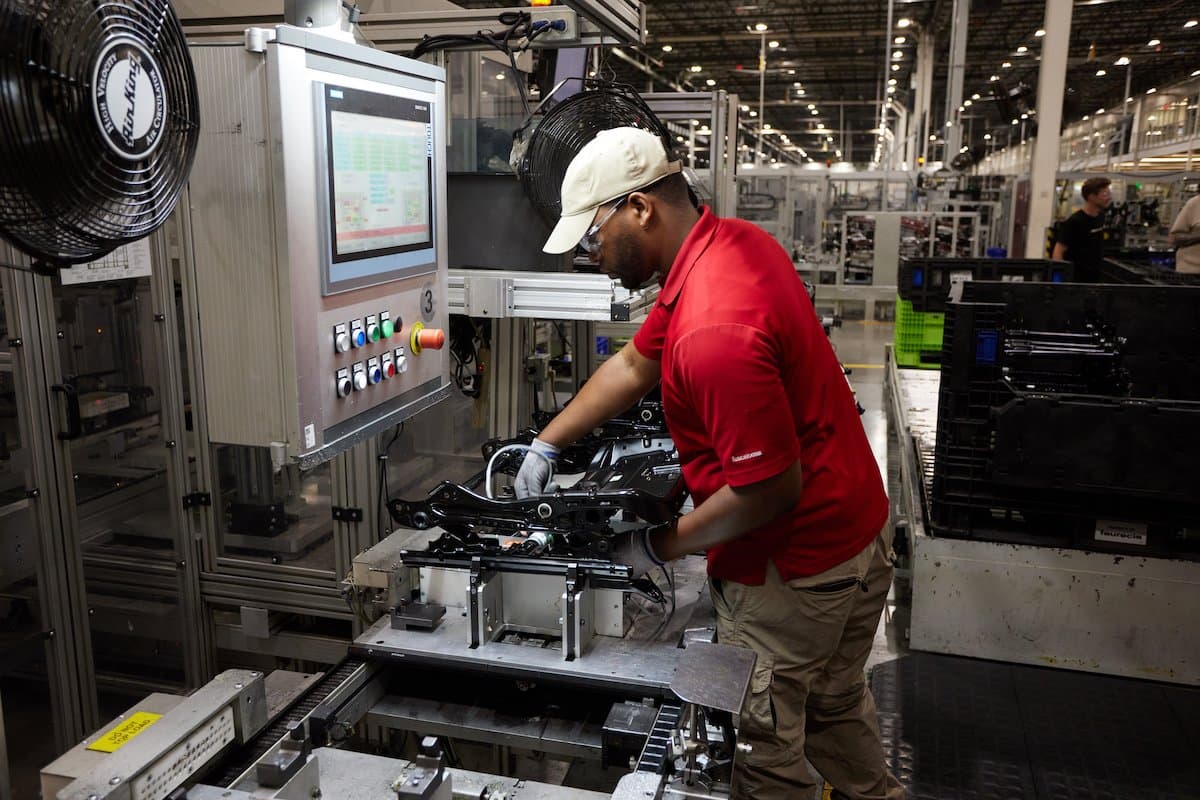
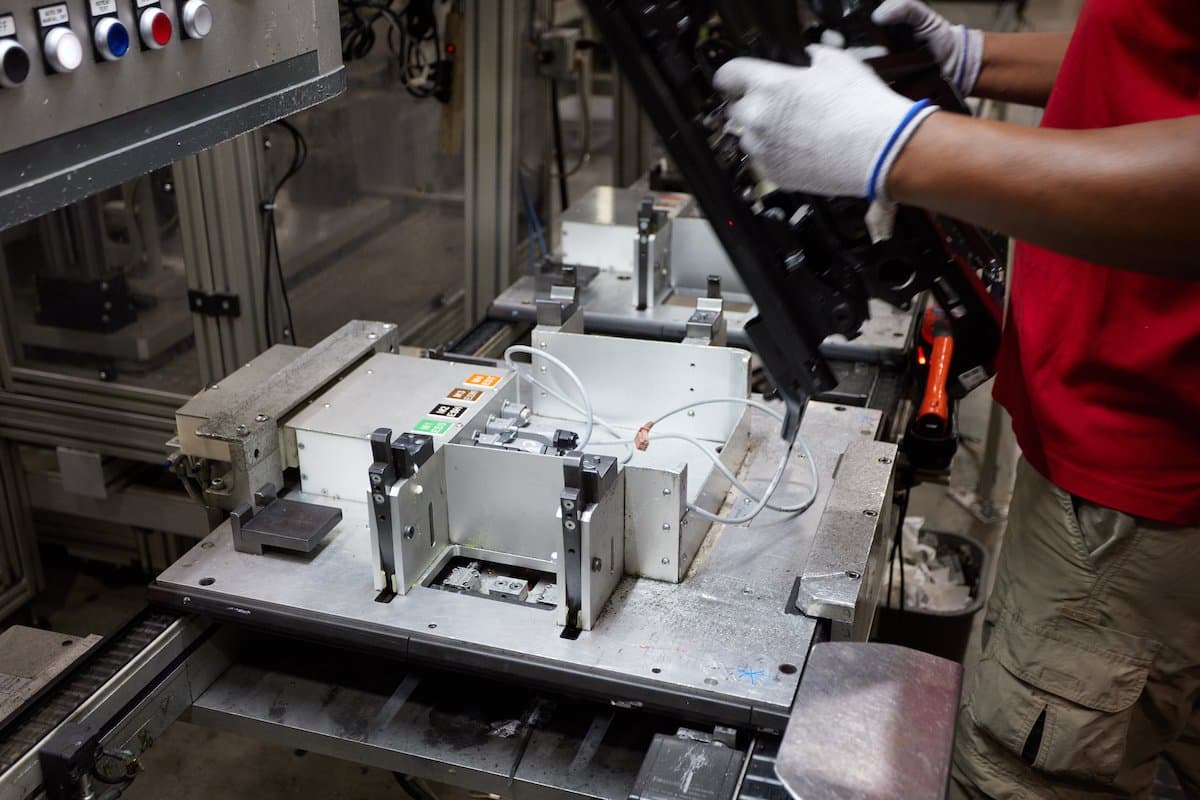

写真の終端コネクタは、シートアセンブリ工程の最終段階で実装される。技術者がシートフレームを電源に接続して最終チェックを実行した後、電源を抜いて次のプロセスに移動するが、これを失念してしまうケースが多く、シートを取り外す際にコードが切断され、組立ラインに数百ドルの損傷を与えたり生産の一時停止を余儀なくされることがある。
Additive TechnologyチームはNew Bostonチームと協力し、磁気で接続できるタイプのコネクタラインを設計しました。ラインとシートフレームに簡単に取り付けられるだけでなく、技術者がコードを手動で取り外さずにシートフレームを引き離すとその勢いで簡単に外れ、損傷を避けることができます。「3Dプリント製の治具を使用して機械を摩耗などから守っています。こうすることで、生産ラインの迅速な修理が可能になります。結果的にダウンタイムが短縮され、全体的な生産量を増やすのにも役立っています」と、Schulz氏は言います。
自動車部品の量産移行前の連続テスト生産
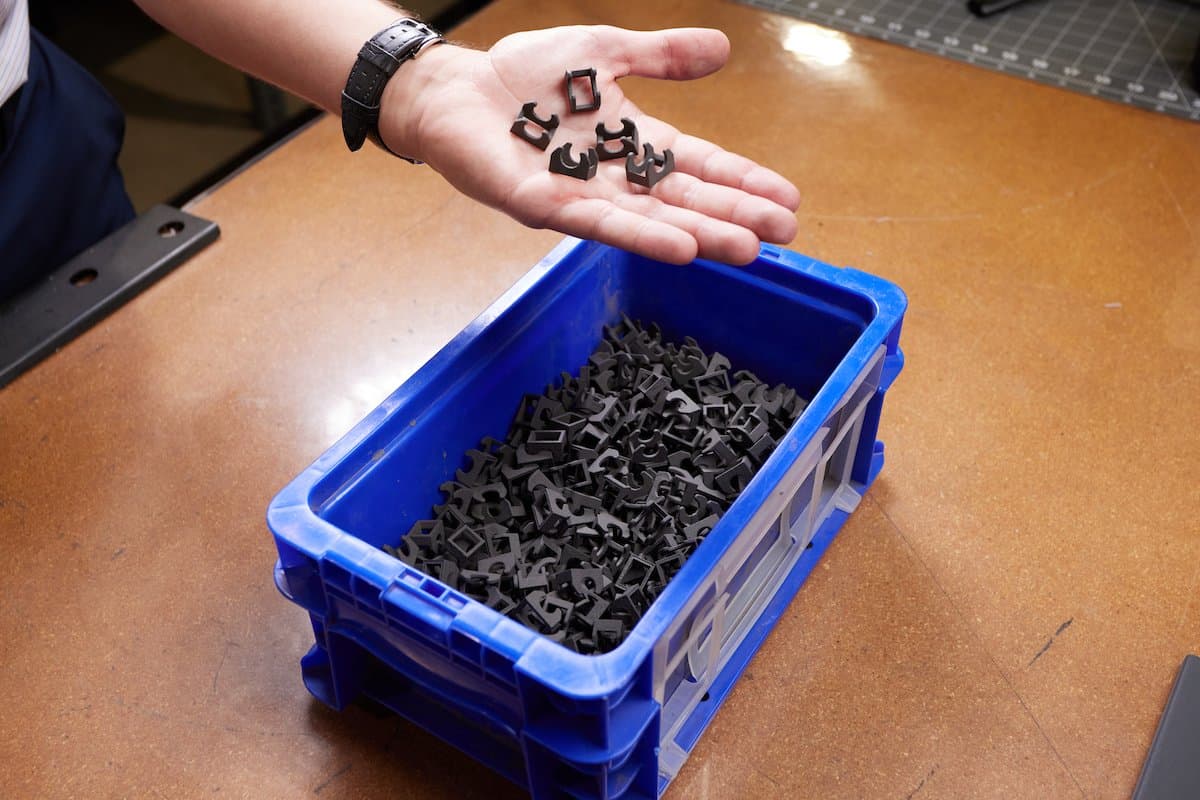
Broseは、BMW X7のシートアセンブリ用に写真のクリップを250,000点も3Dプリントした。
冒頭でSchulz氏が述べた通り、自動車産業は特に過去5年間で急速に変化しています。EVの台頭やカスタム機能に対する需要の高まり、サプライチェーンへの懸念により、OEMは信頼できる生産手段としてアディティブマニュファクチャリングに多額の投資を行うようになりました。
「アディティブテクノロジーの使用を求めるお客様がますます増えていきています。また、エンドユーザー向けの顧客インターフェースとしても一役買っています。お客様は一人一人に合わせたカスタム機能をもっと車両に搭載したいと考えていますから、OEMのアディティブテクノロジーに対する需要も高まります」と、Schulz氏は現状を教えてくれました。
実製品用部品の3Dプリント、特に高度に規制された自動車業界向けの3Dプリントは、これまでなかなか実現できませんでした。Broseのアディティブマニュファクチャリングチームは、ハードウェアと材料の品質が高機能部品を確実に提供できる場合にのみ、実製品用部品の量産に移行することに決めました。
「そのタイミングで、Formlabsの船に飛び乗ることにしたんです。入手できる材料が豊富なこと、そしてプリントの一貫性が大幅に向上したことで、この技術を遂に自動車業界に活かせる時が来たと感じました。私たちにとっての課題は、特にOEMに関しては、安全性と耐久性の面で懸念が存在することです。私たちは、それを排除しようとしています。そこでFormlabsと協力し、現在のBMW X7に使っているようなパーツを実装できるということを証明しました。
Brose North America シートプロトタイピングマネージャー、Matthias Schulz氏
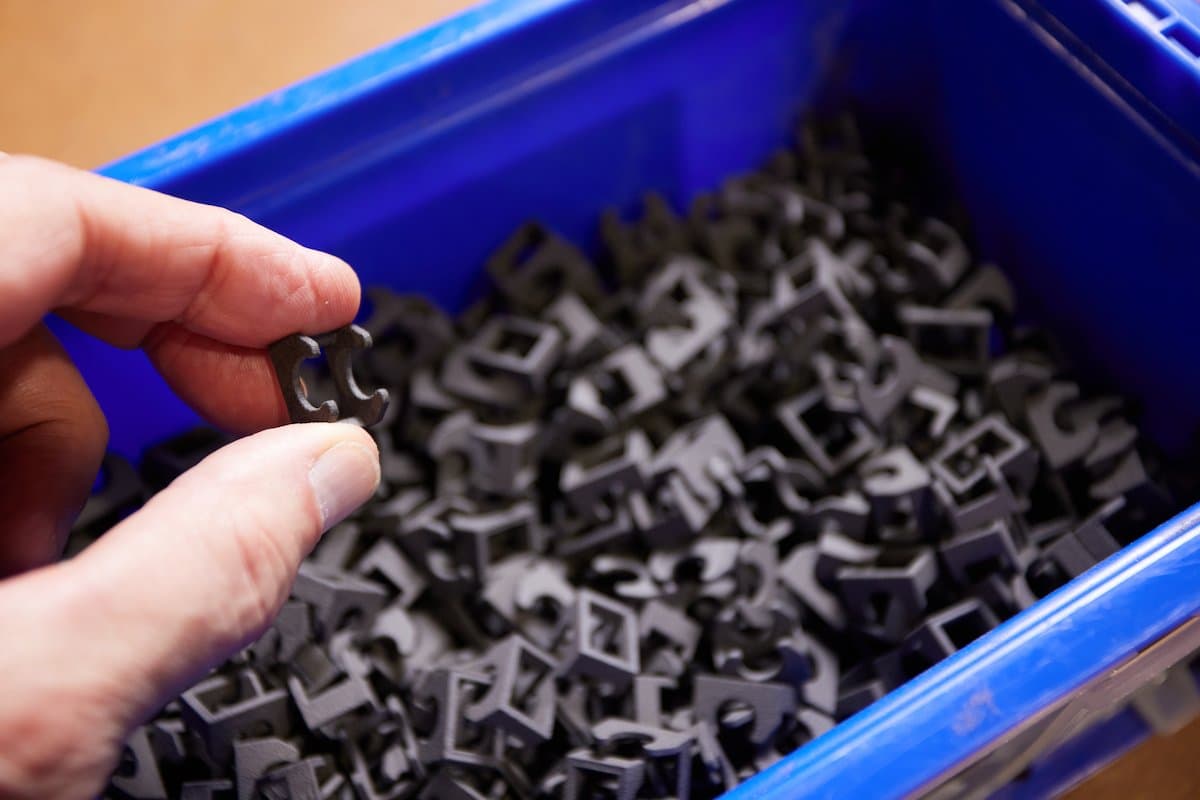
活用例:BMW X7のシート部品
作業工程:3Dスキャン、試作・検証を経て、Fuseシリーズ SLS 3Dプリンタで実製品用部品を3Dプリント
生産量: 250,000点
造形の詳細:
- プリンタ:Fuse 1、Fuse 1+ 30W
- 材料:Nylon 12 GFパウダー
- 造形量:1回あたり144点
- 造形量/月:16,000点
3Dプリントの活用目的
- 金型製作に移る前のテスト生産
Broseは、従来の製造方法に代わる手頃かつ迅速な方法として、実製品用部品の量産に3Dプリントを活用しています。OEMから、金型製作や大量生産をしていては間に合わない部品の製造や既存部品の変更を依頼されると、Broseのアディティブ部門は3Dプリントが活かせるかどうかを評価します。評価の中核となっているのは、リバースエンジニアリングと既存コンポーネントのスキャンです。
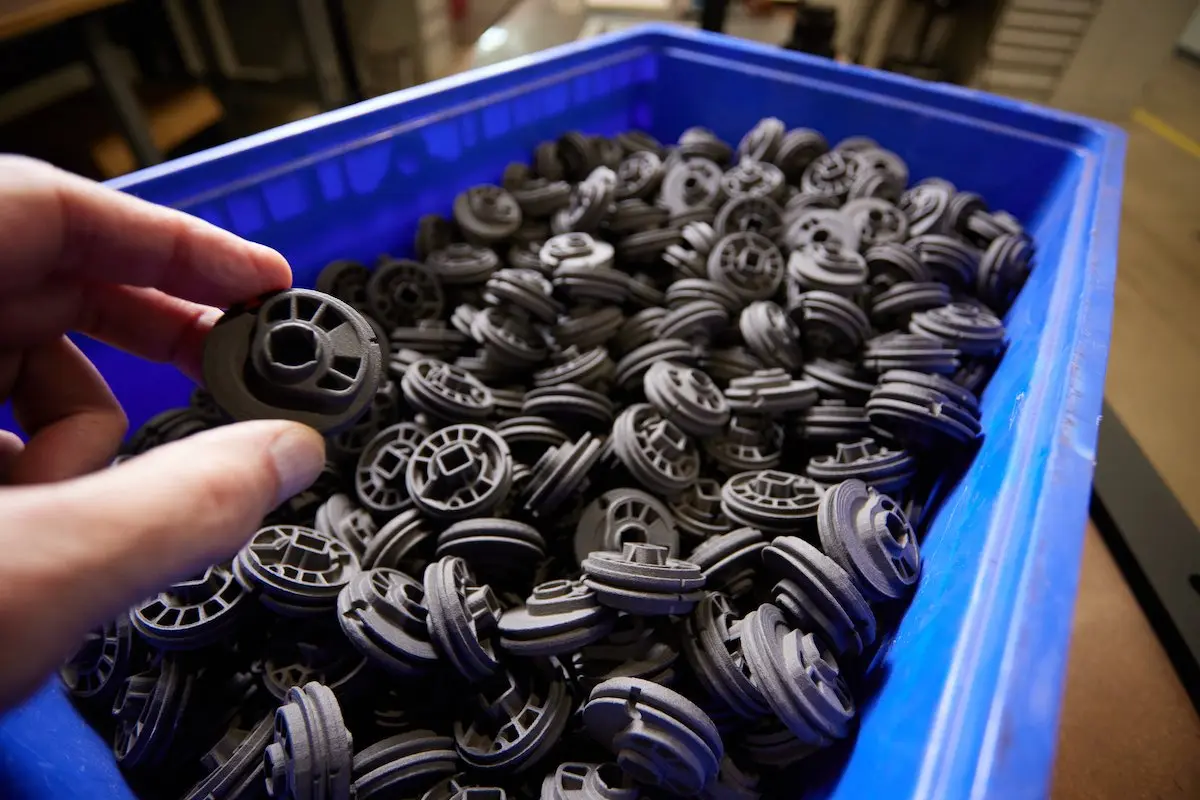
活用例:Bowdenリリース
作業工程:3Dスキャン、試作・検証を経て、Fuseシリーズ SLS 3Dプリンタで実製品用部品を3Dプリント
生産量:20,000点
造形の詳細:
- プリンタ:Fuse 1、Fuse 1+ 30W
- 材料:Nylon 12 GFパウダー
- 造形量:1回あたり144点、週に1,000点
3Dプリントの活用目的
- 金型製作に移る前のテスト生産
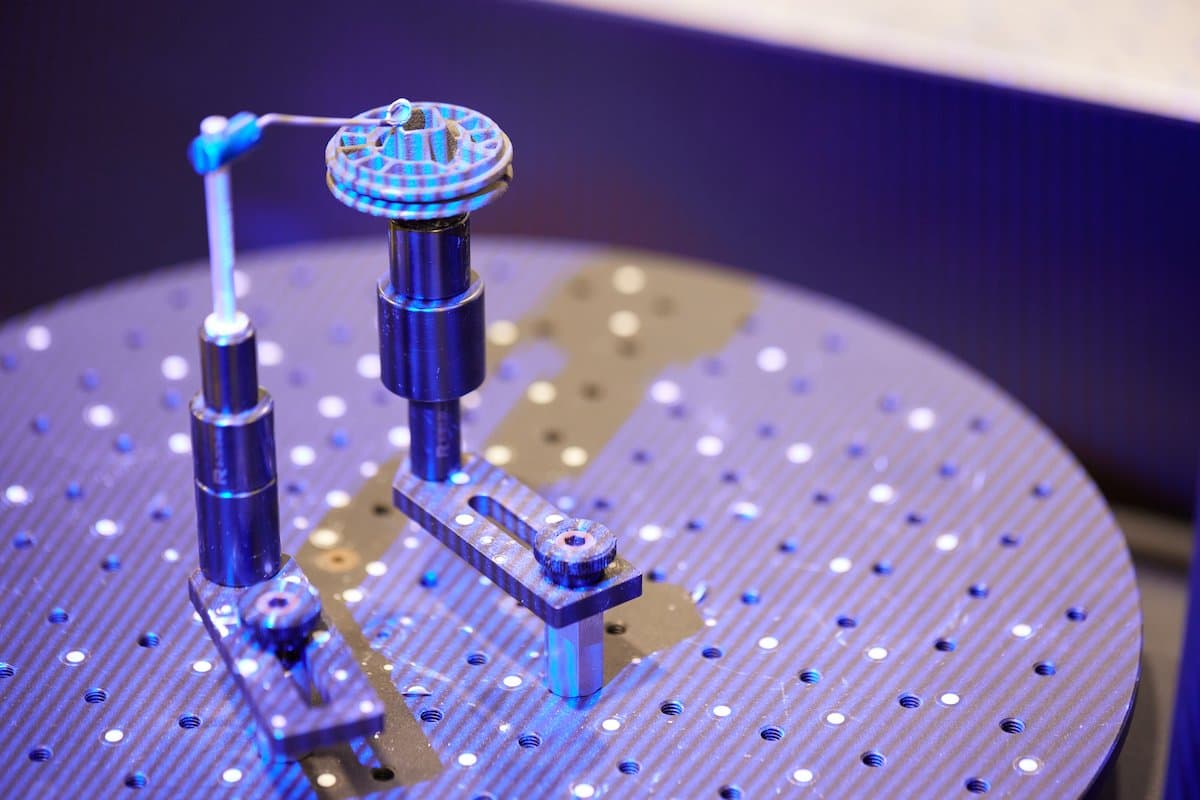
Broseはよく、既存コンポーネントや以前の試作品をスキャンし、CAD上で変更を反映して最新バージョンを同日に3Dプリントしている。
写真のコンポーネントはBowdenリリースで、Broseが所有する複数台のFuseシリーズ SLS 3Dプリンタで20,000点造形し、最終シートアセンブリに搭載して有名OEMに納品します。
「SLSはSLA光造形よりも後処理の要件が少なく、迅速に3Dプリント品を用意することができるので、Formlabsの製品で導入を決めました。大量の造形が可能で、量産移行前のテスト生産やその他OEM関連の消費者向け実製品用部品の製造に役立っています」と、Schulz氏は言います。
3台のFuseシリーズ SLS 3Dプリンタがノンストップで稼働し、プロトタイプ、治具、数十万点にのぼる実製品用部品を製造する同社では、信頼性と一貫性が重要な要素になります。同社は、寸法精度の高さと射出成形品に似た性質から、Nylon 12 GFパウダーを使用して量産レベルの量を生産しています。ビルドチャンバーいっぱいの造形を1回行うごとに実施するFuse 1またはFuse 1+ 30Wのメンテナンスチェックも約15分ほどで完了し、継続的かつ効率的な生産を迅速に行えます。
「Formlabsは、メンテナンスに手間のかからないプリンタの作り方を熟知しています。プリンタは非常に信頼性が高く、造形に失敗したこともほとんどないため、私たちはより生産量を高めることだけに集中し、自信を持って量産に進むことができます」と、Schulz氏は評価します。
3Dプリントが自動車業界の加速をサポート
継続的な改善に対するBroseの飽くなき取り組みが、アディティブマニュファクチャリングや自動化などの新たな技術に同社を向かわせ、プロセスを合理化して顧客に革新的なソリューションを提供できるようになりました。同社における3Dプリントの重要性が高まるにつれ、早期に導入を決めたSchulz氏たちは、そのスピードと(ほとんどの場合に)低コストで生産できるこの技術を活用する、新たな方法を模索しています。
Form 4、Form 4L、Fuseシリーズなどの高速で強力なプリンタを使用することで、プロトタイピング、治具、および実製品用部品を、数時間または数日で生産することができます。数週間も数ヶ月も待つ必要は、もうありません。「Formlabsは最高のパートナーです。エンジニアリングサポートがそこまで必要なく、より多くの部品を迅速に生産できるすぐに利用可能なソリューションを探していました。Formlabsのソフトウェア、サポート、プリンタは、どれもこの要件に完璧にフィットしているんです」
自動車業界における3Dプリントの活用例については、FormlabsのWebサイトをご覧ください。SLA光造形またはSLS 3Dプリントの品質を実際にお確かめになりたい場合は、無償サンプルパーツのリクエストも受け付けています。お気軽にお申し込みください。