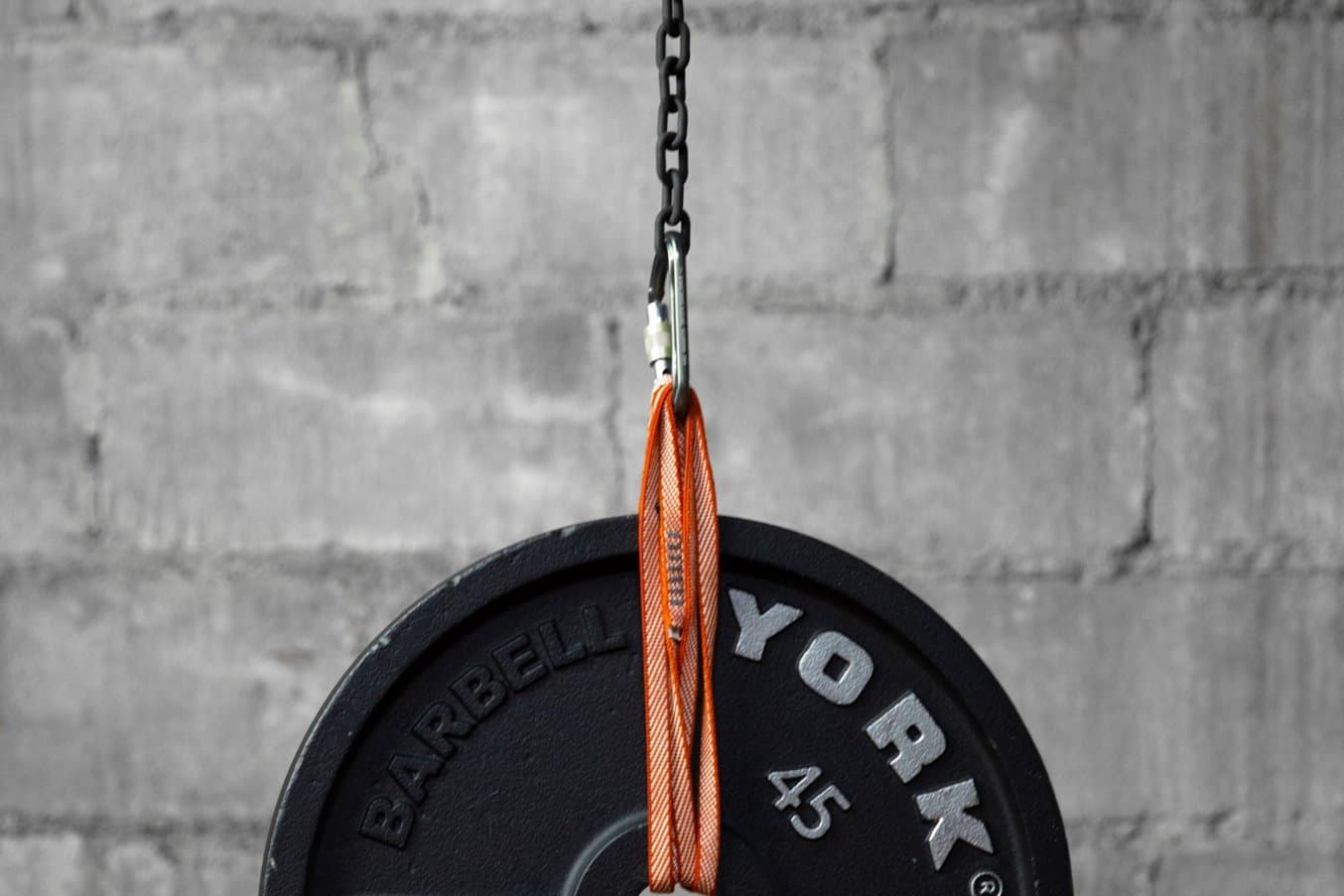
自転車、レーシングカー、ドローン、テニスラケットなど、さまざまな用途で軽量で高い強度と耐久性を備えた製品が求められています。このような組み合わせの特性を備えているのが炭素繊維複合材料であり、Fomula 1のレーシングカーから軽量ロードバイクのフレームまで、あらゆる用途で使用されています。
多くの業務用3Dプリンタでは、各種複合材料などのポリマーベースの材料を使用するため、炭素繊維の3Dプリントも可能なのか?と疑問に思う方も多いようです。
3Dプリントによる炭素繊維パーツの製作は、2通りの方法で行うことができます。1つ目は、従来の炭素繊維パーツの生産工程を3Dプリンタで補完する方法、そして2つ目が炭素繊維複合材を使用して3Dプリントで直接製作する方法です。本記事では従来の製作方法についてひととおり説明した上で、炭素繊維の3Dプリントで成形型を製作するための新たなワークフロー、そして炭素繊維複合材料を使って直接3Dプリントでパーツを製作する方法についても解説します。
従来の手法と3Dプリントを組み合わせて炭素繊維パーツを製作する
炭素繊維材料は、炭素繊維の長い撚り糸を織り合わせたものをポリマーで複合化させて生産される複合材料です。この撚り糸の織り方を工夫することで一定方向での強度を高めたり、実製品に全方向に対する強度を持たせることが可能です。炭素繊維を織り上げたものを実製品に加工するのですが、加工は基本的に、ウェットレイアップ、プリプレグ積層、レジントランスファーモールディング(RTM)の3つの方法で行います。
ウェットレイアップ
ウェットレイアップでは、炭素繊維のシートをカットして型に押し当て、その上から液体樹脂を塗布します。液体樹脂が硬化・固化する時に炭素繊維シートと結合し、意図した最終形状に成形されます。この手法は必要な設備の数が最も少なく済むため、初心者にもマスターしやすい方法です。ほとんどの工程を手作業で行えるため最も安価な手法の一つではありますが、ほかの手法で製作したものに比べて、成形品で原型通りの忠実な寸法を再現するのが難しいというデメリットがあります。
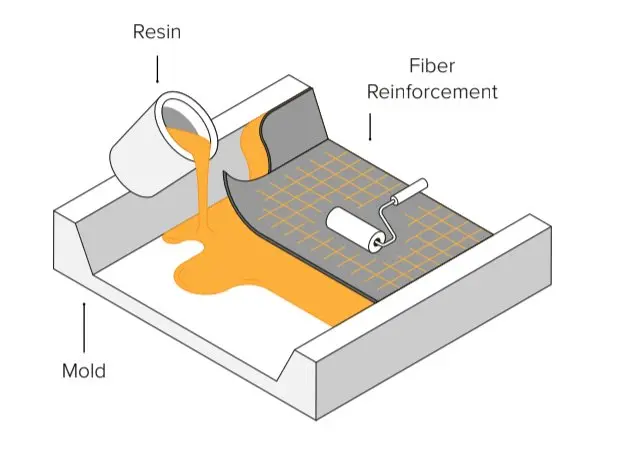
プリプレグ積層
この方式では、あらかじめ樹脂に浸漬させた炭素繊維を型に入れ、圧力と熱を与えて最終形状に成形します。あらかじめ樹脂を浸透させた炭素繊維シートを保管・処理するための専用装置や、加熱および加圧機能を備えた成形機が必要なため、この手法は最もコストが高くなります。ただし、専用装置は繰り返し安定した生産が可能でもあるので、炭素繊維パーツのバッチ生産には最適です。
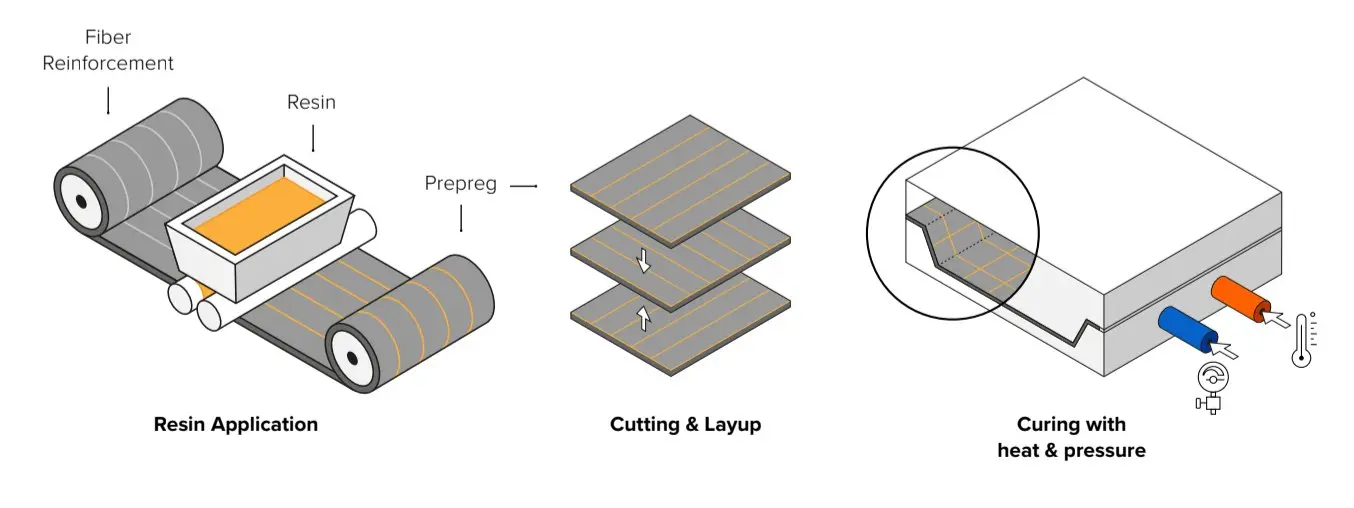
レジントランスファーモールディング(RTM)
RTMでは、乾燥した繊維を二つ割の金型の中に入れ、その後金型をクランプで閉じ、高圧をかけて樹脂をキャビティ内に押し当てます。工程が自動化されていることが一般的で、大量生産に使用されます。
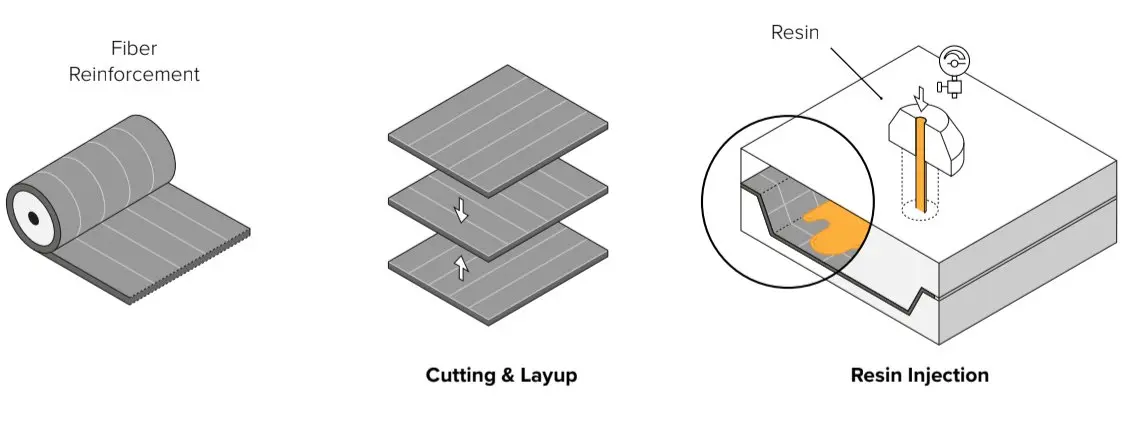
3Dプリント製の型を使用して炭素繊維パーツを製作する
先に説明した3つの方法のいずれも、3Dプリントを活用することでコスト削減や製作期間の短縮が可能です。これら3つの従来工法には、1個または複数個の成形型が必要で、この型の製作には木材やフォーム、金属、プラスチック、ワックスを切削加工する時間のかかるサブトラクティブ法が用いられてきました。3Dプリントは、このように型材料を切削して型を作る従来の方法に代わる、小量生産やカスタマイズに適したより高効率でコストパフォーマンスの高い方法です。
自動車業界や航空宇宙業界のように機能試作が必要な業界では、設計の検証や修正用に数百種類もの型が必要になることもあります。大量の型を従来の工法で製作するにはコストも時間もかかるため、このような用途には小量の型を効率よく製作可能な3Dプリントが適していると言えます。3Dプリント製の型は量産向けの金型としては向いていませんが、社内で短時間かつ安価に型を製作し、製品開発や設計検証に係る時間を短縮できるという利点があり、また、小量生産にも向いています。
炭素繊維パーツ用の型の生産手法は複数ありますが、社内で型を生産する用途では、仕上がり面が滑らかで利用できる材料も豊富なSLA光造形方式の3Dプリンタが一般的です。SLA光造形で製作した部品は基本的に積層痕や空孔が残らないため、表面がざらついた質感になることを心配せずに炭素繊維シートをしっかり型に押し当てることができます。
レーシングカーやスポーツカーを製造しているPanozでは、レーシングカーのコックピットに搭載してキャビン内の空気を排気し内部の温度を下げる、特注の排気ダクトを必要としていました。PanozはDeltaWing Manufacturingの協力のもと、FormlabsのSLA光造形プリンタでHigh Tempレジンを使って原型をプリントし、その原型の上に手作業で耐熱エポキシ樹脂を流し込んで成形型を製作するという方法を採用しました。3Dプリントの活用により、DeltaWingは炭素繊維パーツのカスタム生産に必要な高価な金型の外注を回避し、全体的なコストの低減と短納期での製作を実現しました。
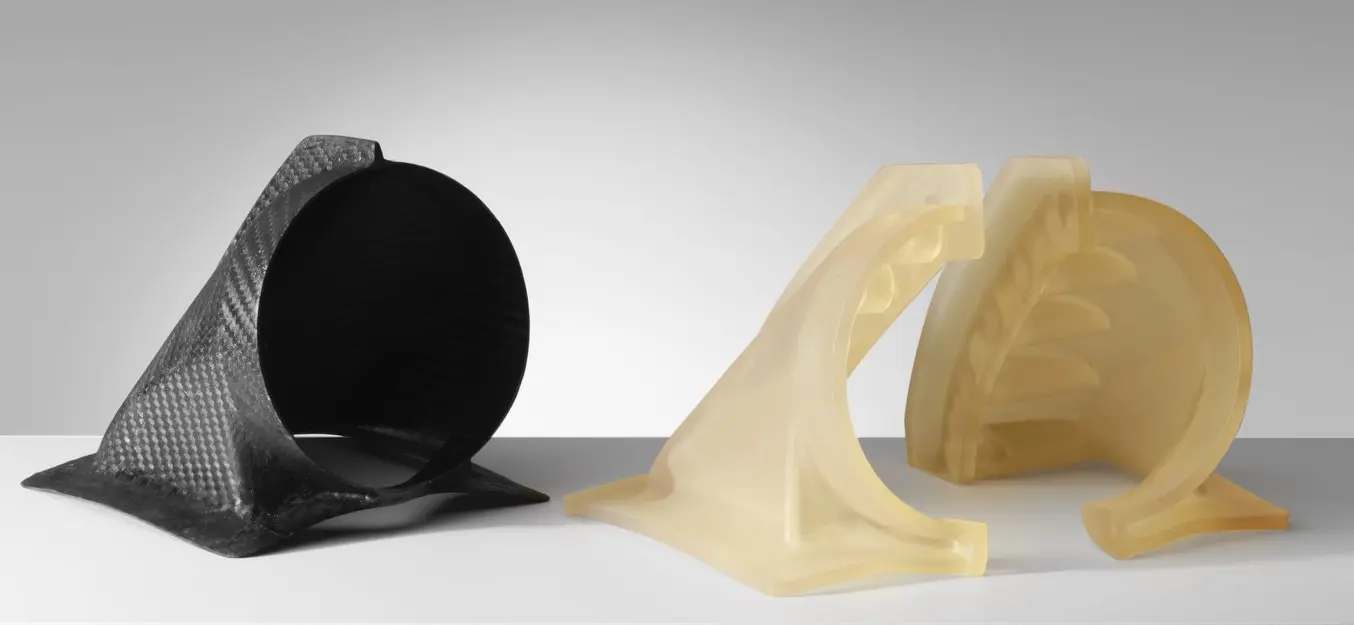
High Tempレジンでプリントした二つ割の成形型。その隣にあるのは炭素繊維で作ったフェンダーエアダクト(DeltaWing Manufacturing製)。
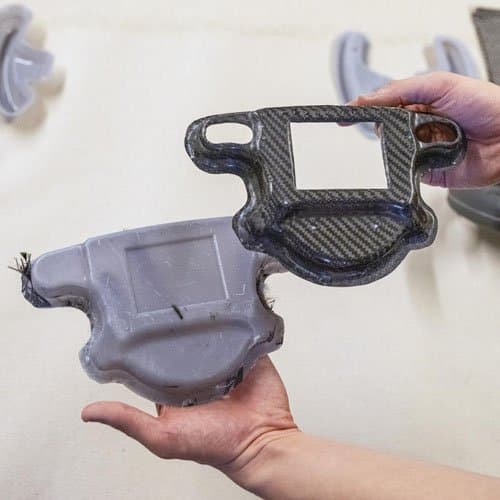
3Dプリント製の型で炭素繊維製パーツを製作
本技術資料では、複合材料を使用した成形型の設計ガイドラインや、炭素繊維部品の製造に必要なプリプレグや手作業によるラミネート成形について、手順ごとに詳しく解説しています。
炭素繊維を直接3Dプリントする
炭素繊維を使った造形が可能な3Dプリントをお探しですか?従来の炭素繊維パーツが持つ強度、耐久性、堅牢性と、3Dプリントの迅速な適応性、形状の自由度、再現性を組み合わせたワークフローには大きな需要があります。そのため、炭素繊維を使った3Dプリントサービスを提供する3Dプリント業者が多数存在し、短繊維と長繊維を使用した2種類の炭素繊維プリントを提供しています。
短炭素繊維の3Dプリント
短繊維とは、細かな炭素繊維を混ぜ合わせた3Dプリント用の複合プラスチック材料を指します。短繊維は複合材料の強度を高めるために使用され、FDM(熱溶解積層)方式の炭素繊維フィラメントやSLS(粉末焼結積層造形)方式3Dプリンタ用のナイロンパウダー等がこれに相当します。
短繊維による強化材料で3Dプリントした造形品は、ほかのポリマーベースの3Dプリント品よりも強度、軽量性、耐熱性、および耐クリープ性に優れています。従来の炭素繊維成形法で製作したパーツと比較した場合、3Dプリントした短繊維材料パーツは形状の設計自由度に優れ、特にSLS方式の3Dプリントを使用した場合には、従来の金型製作に要する多大な労力が不要になり、また、短繊維材料をワークフローに採り入れることによって新たなイノベーションが生まれる可能性もあります。
FormlabsのFuse 1+ 30W SLS 3Dプリンタでは、FormlabsのSLS用材料ライブラリの中でも最も強度の高いNylon 11 CFパウダーを使用して、この種の炭素繊維3Dプリントが可能です。Fuse 1+ 30Wは短炭素繊維を使った3Dプリントにも対応した、高性能ながら導入しやすい価格帯を実現したSLS 3Dプリンタです。従来の産業用SLS 3Dプリンタの中にも炭素繊維材料に対応したものはありましたが、これまではレジントランスファーモールディング(RTM)やプリプレグ積層と比較した場合に初期費用が高く、炭素繊維パーツの3Dプリント機能を搭載しているというメリットが打ち消されてしまっていました。
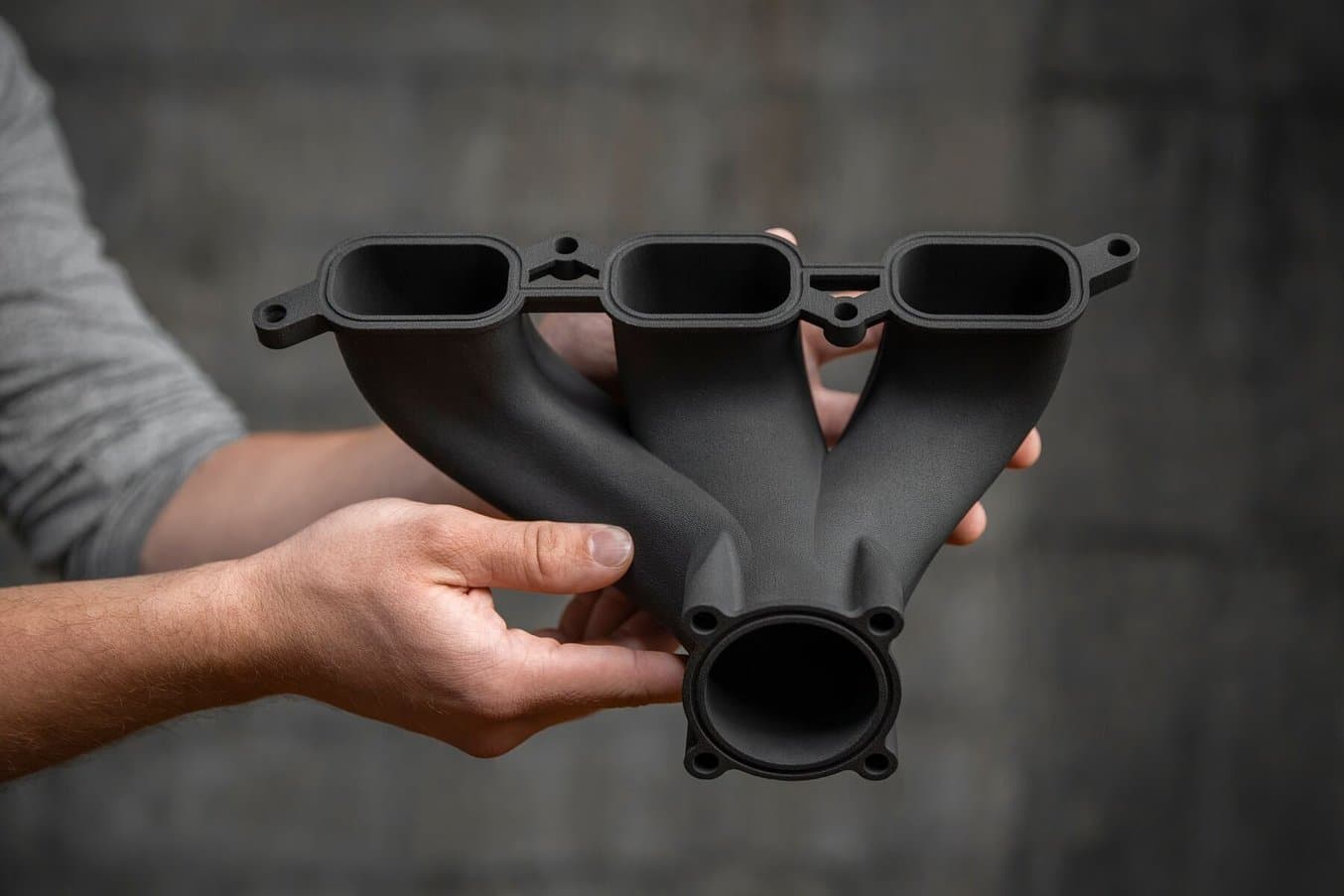
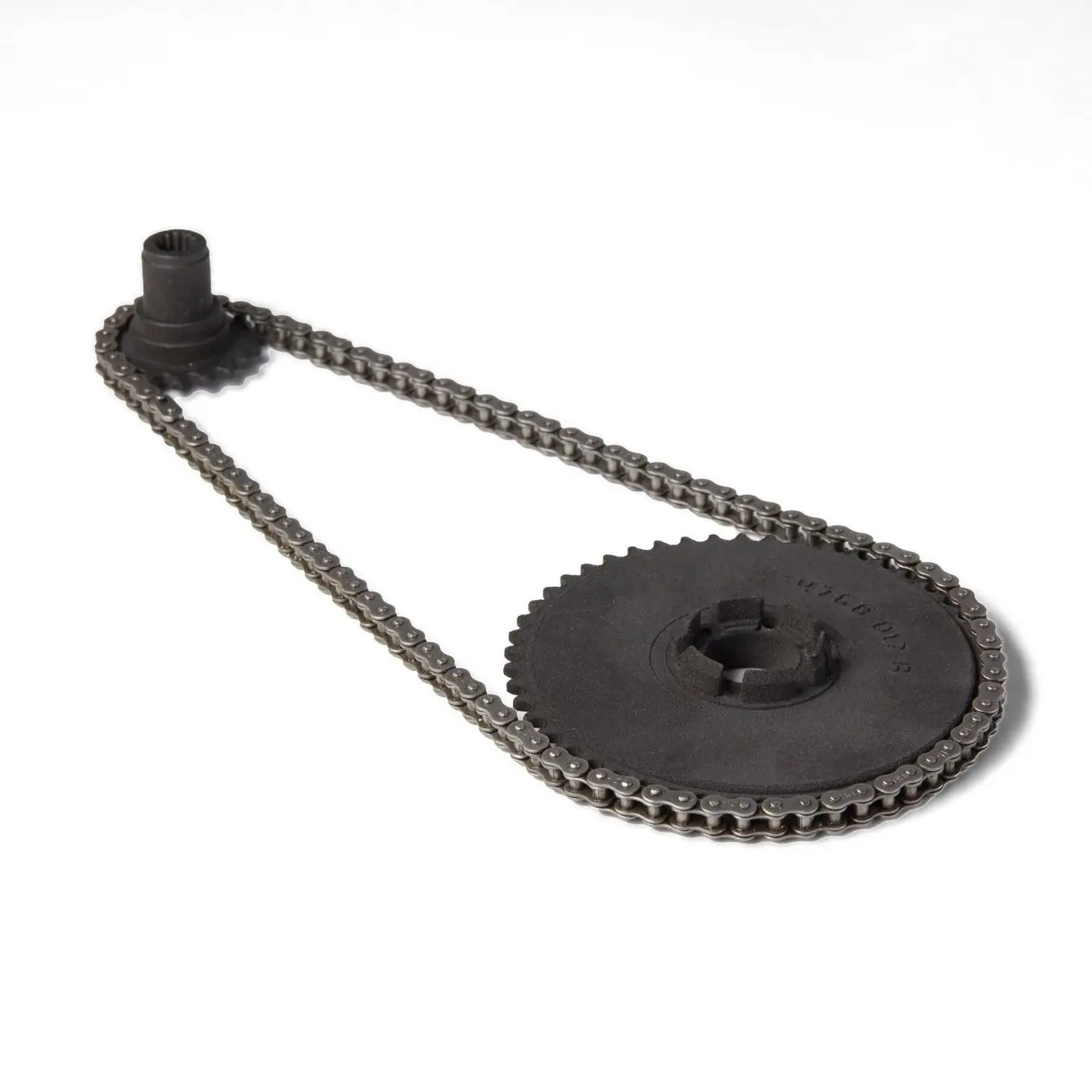
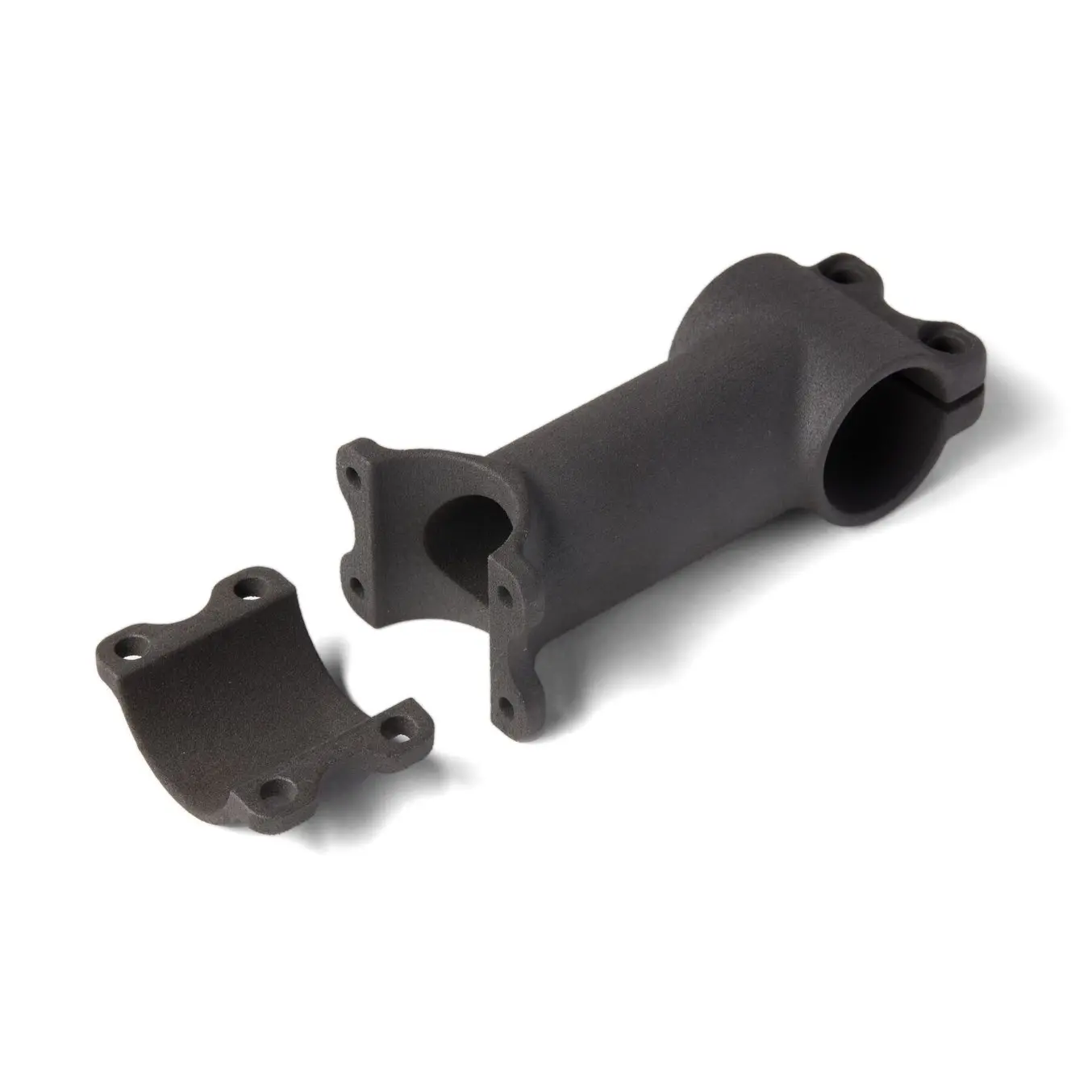
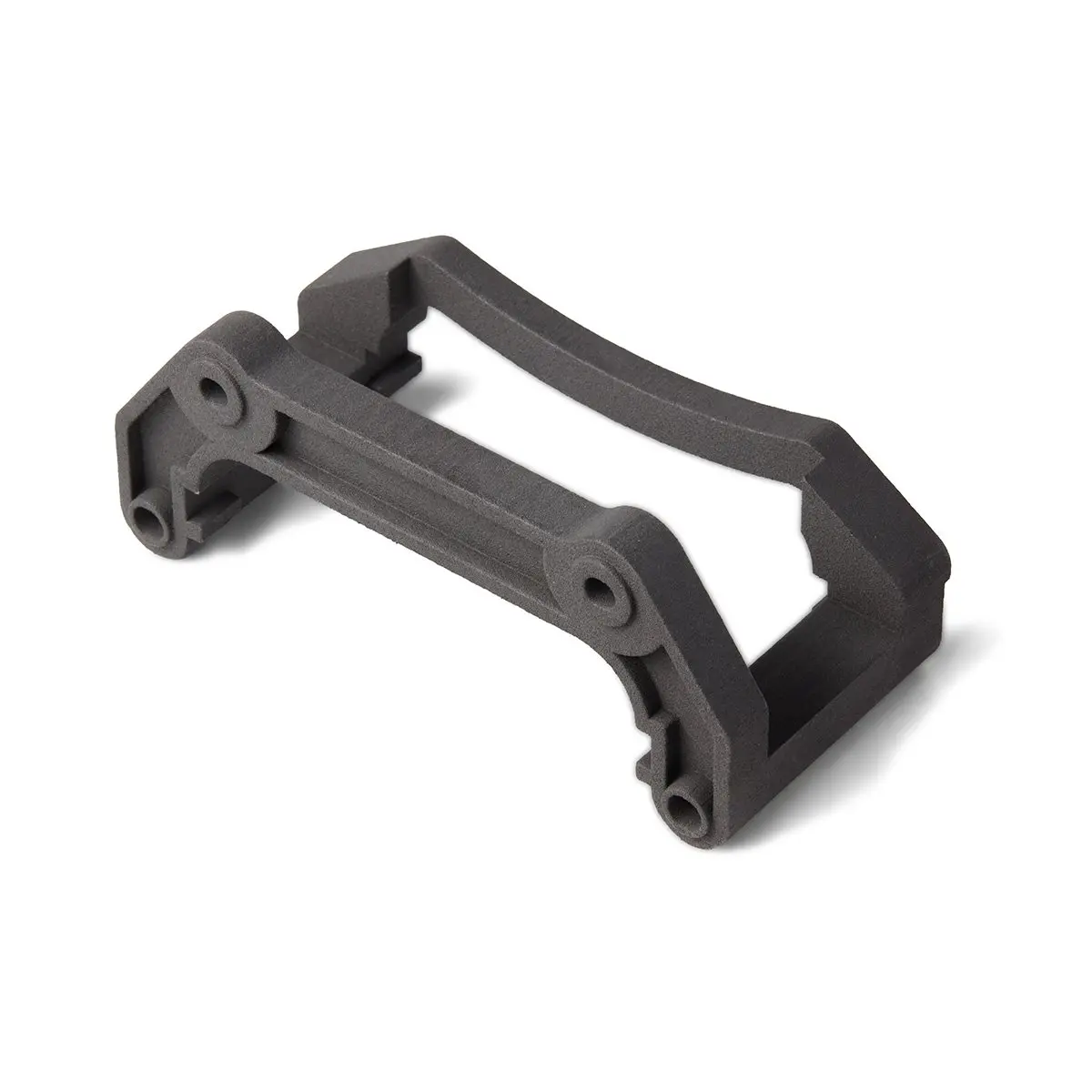
Formlabs Nylon 11 CFパウダーは強度が高く軽量で耐熱性があり、自動車、航空宇宙、製造業での用途に最適な材料。
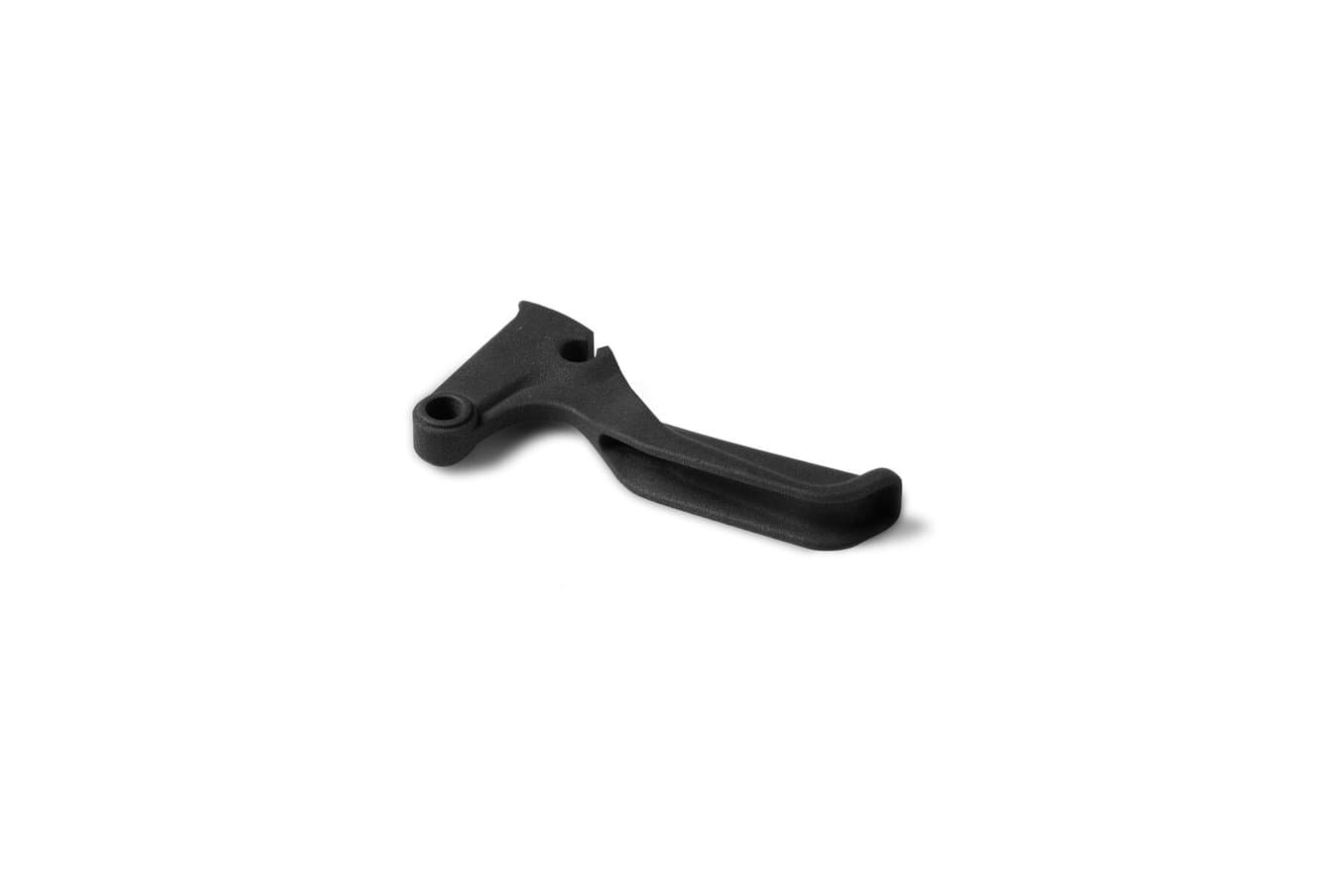
多くのFDM方式3Dプリンタが炭素繊維配合フィラメントに対応していますが、炭素繊維材料を使ったプリントは標準的なABSやPLAフィラメントよりも複雑で、詰まりが生じることも多く、さらにフィラメントが真鍮製のノズルを摩耗させるためメンテナンスも頻繁に必要になります。FDM方式の3Dプリンタの中には短炭素繊維フィラメント専用機種もありますが、価格帯は高くなります。
SLSおよびFDM方式で短炭素繊維でプリントしたパーツの主な制約は、長繊維を織った従来の炭素繊維パーツの純粋な代用品としてではなく、強度を備えた別の3Dプリントパーツとして理解しなければならない点です。また、3Dプリント中の積層方向が重要で、その方向に対する強度が最も高くなります。SLS造形パーツではX方向、FDM造形パーツではXY方向です。従来の方法で炭素繊維パーツを製作する場合、成形前の段階で複数のカーボンファイバーシートを型に慎重にセットアップすることで、多方向に強度が与えられます。
長炭素繊維の3Dプリント
長炭素繊維を使用した3Dプリントには、一部の専用FDM方式3Dプリンタが対応しており、強度の点では従来の炭素繊維パーツに近い性能を実現できますが、短繊維対応のFDM方式プリンタと同じく、強度方向はXY平面のみです。長炭素繊維対応のプリンタでは、連続した炭素繊維と熱可塑性樹脂を混合しますが、カーボンファイバーの積層方向を考慮することで、特定の面を強化したり圧力軸を設定したりといった操作が可能です。この方式のプリンタのノズルは、デュアルノズルを搭載して炭素繊維の糸とポリマーを吐出して混合する構成、もしくは、カーボンファイバーの糸を吐出するノズル1個と加熱したフィラメントを吐出するノズル1個が一体化した構成になっています。
長炭素繊維の3Dプリントは、型で成形する従来の炭素繊維パーツの代用となりますが、設計の自由度は下がります。強度は格段に高くなりますが、この強度が達成されるのはXY面に限られるため、強度が必要な方向に合わせてプリントを実行する必要があります。このような特性が適合する設計であれば、アルミニウム製パーツと置き換えることも可能で、頑丈な生産用の治具やエンドユースパーツの製作も可能です。
従来の炭素繊維加工法と炭素繊維3Dプリントのワークフローを比較
ウェットレイアップ | プリプレグ積層 | レジントランスファーモールディング | 短繊維FDM方式3Dプリント | 短繊維SLS方式3Dプリント | 長繊維FDM方式3Dプリント | |
---|---|---|---|---|---|---|
メーカー&モデル | 多数 | 多数 | 多数 | Markforged Onyx、Markforged X3 | Formlabs Fuse 1+ 30W | Markforged Mark Two、Desktop Metal Fiber、Markforged X7 |
精度 | ★★★☆☆ | ★★★★★ | ★★★★★ | ★★★☆☆ | ★★★★★ | ★★★☆☆ |
表面品質 | ★★★☆☆ | ★★★★★ | ★★★★★ | ★★★☆☆ | ★★★★☆ | ★★★☆☆ |
設計の自由度 | ★★★☆☆ | ★★★☆☆ | ★★★☆☆ | ★★★★☆ | ★★★★★ | ★★★★☆ |
軽量 | ★★★★★ | ★★★★★ | ★★★★★ | ★★★★☆ | ★★★★☆ | ★★★★☆ |
強度 | ★★★★★ | ★★★★★ | ★★★★★ | ★★★☆☆ | ★★★☆☆ | ★★★★★ |
強度方向 | XYZ | XYZ | XYZ | XY | X(Y) | XY |
スループット | ★☆☆☆☆ | ★★★☆☆ | ★★★★★ | ★★★☆☆ | ★★★★☆ | ★★★☆☆ |
設備コスト(詳細) | 多数選択肢あり、$100以上〜 | 多数選択肢あり、 $3000以上〜 | 多数選択肢あり、一般的に$100,000以上 | デスクトップタイプは$5,000~、産業用は$40,000~ | 産業用一式 $39,243~ | デスクトップタイプは$20,000~、産業用は$70,000~ |
部品単価 | $$$$ | $$$ | $$ | $$$ | $$ | $$$$ |
最適な用途 | 高性能カスタム製品、ワークフローはエントリーレベル | 小~中量生産 | 大量生産 | 迅速な設計検証、強度を備えた3Dプリントパーツ | 迅速な設計検証、複雑形状、強度を備えた3Dプリント製部品の小量バッチ生産 | 迅速な反復、3Dプリント製部品 従来の炭素繊維複合材と同等の強度(XY方向) |
メリット | 高強度 設備コスト低 | 高強度 | 高強度 精密、再現性 自動化可 | 安価 金型レス | 精度と再現性 設計の自由度 金型レス | 高強度 金型レス |
短所 | 作業負荷が高い 高品質の維持が難しい | 作業負荷が高い | 金型や装置が高額 | 強度が異方的 低強度 プリントしにくい | 強度が異方的 低強度 | 強度に異方性あり |
3Dプリント製の炭素繊維パーツの強度
炭素繊維複合材料を使って3Dプリントしたパーツの機械的特性は、強度と耐熱性の点でプラスチック材料を使ったほとんど全ての3Dプリントパーツを上回ります。参考として、短繊維と長繊維を使った3Dプリントパーツと一般的な材料で3Dプリントしたパーツの特性を比較してみましょう。
製造工程 | SLS - 短繊維 | FDM - 短繊維 | FDM - 長繊維 | FDM - 長繊維 | 射出成形 | 鋳造または切削 |
---|---|---|---|---|---|---|
材料 | Formlabs Nylon 11 CFパウダー | 炭素繊維強化ナイロンフィラメント | ナイロン6フィラメント+α 炭素繊維 | PEEKフィラメント + 炭素繊維 | ABS | アルミニウム |
引張弾性率(GPa) | 1.6~5.3 | 2.4 | 60~100 | 145 | 2.3 | 70 |
最大引張強さ(MPa) | 38~69 | 40 | 800~1000 | 2400 | 39 | 310 |
曲げ弾性率(GPa) | 4.2 | 3.0 | 51~71 | 124 | 2.4 | 70 |
曲げ強さ(MPa) | 110 | 71 | 540~800 | 1300 | 74 | 310 |
破断伸び | 5~15% | 25% | 1.5% | N/A | 6~15% | N/A |
ノッチ付アイゾット(J/m) | 74 | 330 | 960 | N/A | 200 | N/A |
荷重たわみ温度@0.45MPa(℃) | 188 | 145 | 105 | N/A | 70~107 | N/A |
炭素繊維3Dプリントパーツの用途
強度が高く軽量で、衝撃や熱、薬品に対する優れた耐性を備えた炭素繊維3Dプリントパーツは、これまで3Dプリントの活用が検討されてこなかった様々な用途で最適なソリューションとなる可能性を秘めています。レジンと炭素繊維の複合材を3Dプリントして作るパーツは、自動車や宇宙機のエンジンコンポーネントで生じる高熱にも耐え、アルミの切削加工パーツや生産用治具の代用として、高い耐久性と耐衝撃性を持った部品の生産を可能にします。
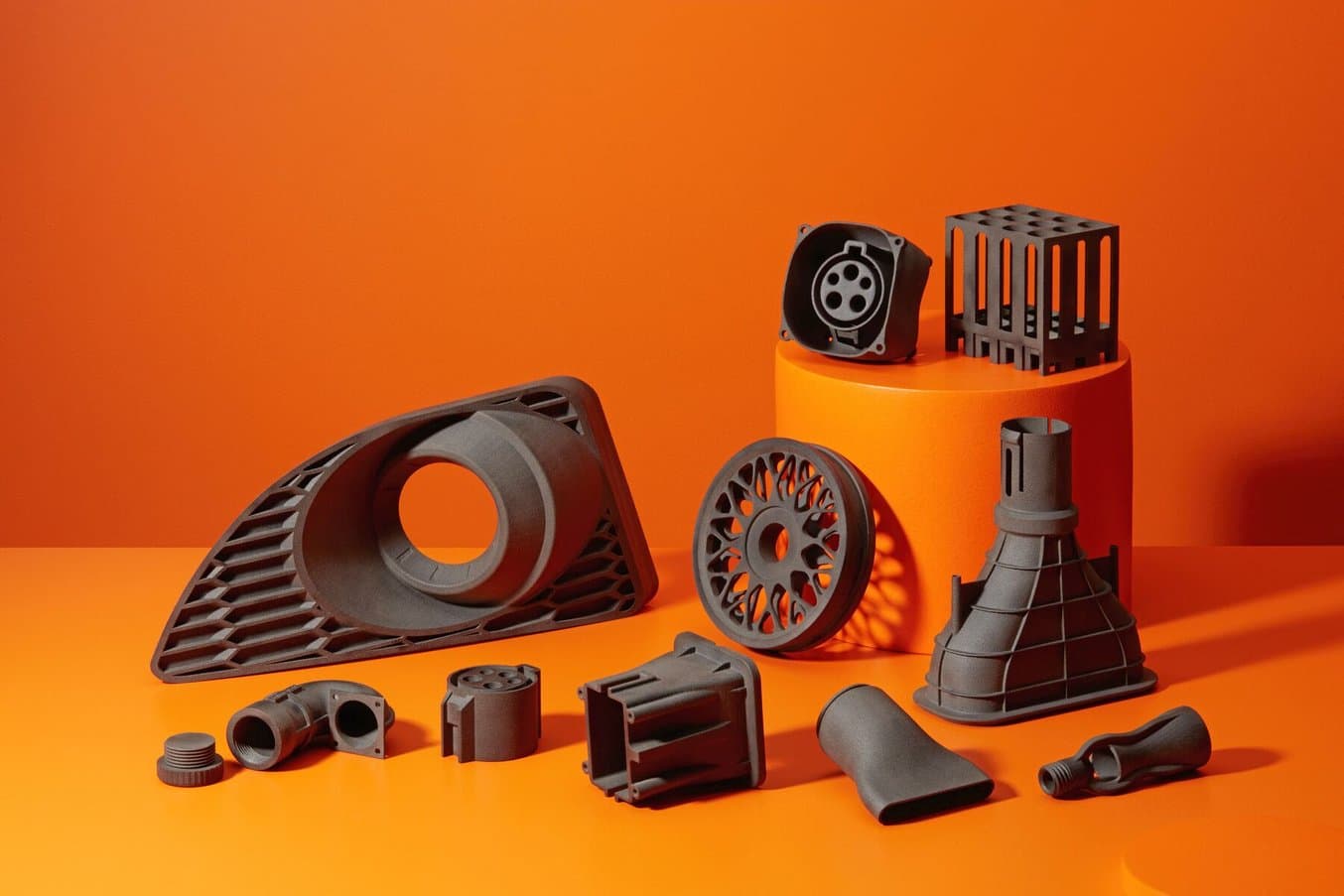
3Dプリント製の炭素繊維パーツは、形状が複雑で高い強度を持つ実製品用部品の小量生産や、耐摩耗性と耐久性を備えた治具や固定具のラピッドプロトタイピングに最適。
これまでも設計や生産の分野で新たな可能性を切り開いてきた3Dプリントですが、炭素繊維複合材料によってこの可能性がさらに広がり、自動車や航空宇宙、防衛、製造などの様々な業界において、高強度かつ耐熱性を備えた設計の自由度の高いパーツの短期かつ効率的な生産を可能にします。従来の切削加工や金型製作プロセスが不要になることで、これまでより遥かに容易に、カスタムパーツや交換部品、機能試作を製作できるようになります。強度が付加されるのは特定の面に限られるため、従来工法の完全な代替とはならないものの、3Dプリント製の炭素繊維パーツはほとんどすべてのレジンパーツよりも強度が高く、多くの用途への応用のしやすさでは唯一無二と言えるでしょう。
炭素繊維パーツの最適な生産手順は、そのパーツの用途以外にも、パーツの設計、生産数量、その他の要素によって、型を使った成形と3Dプリントによる直接製作のどちらが向いているかが変わります。短繊維を使用したSLS 3Dプリントは、頑強なパーツを作りたいメーカーにとって最適な手法ですが、従来工法で型を使用して成形した炭素繊維パーツの強度には届きません。
Formlabs Fuse 1+ 30WでNylon 11 CFパウダーを使って造形する方法であれば、コストを抑えながら、厳しい試作検証および生産スケジュールにも遅れることなく、従来の樹脂パーツと同等の強度と優れた機械的特性を備えた実製品用部品の生産が可能です。この方法であれば、繰り返しの機能試験やその結果に基づく設計変更にもCADによる微修正対応できるため、実製品の性能向上や市場投入までの時間短縮も実現できます。
以下から無料のサンプルパーツをリクエストいただくと、SLS 3Dプリントで短炭素繊維材料を使った造形品を直接ご確認いただけます。また、用途に適したプリンタの選定等に関する各種ご相談は、Formlabs担当者までお気軽にお問い合わせください。