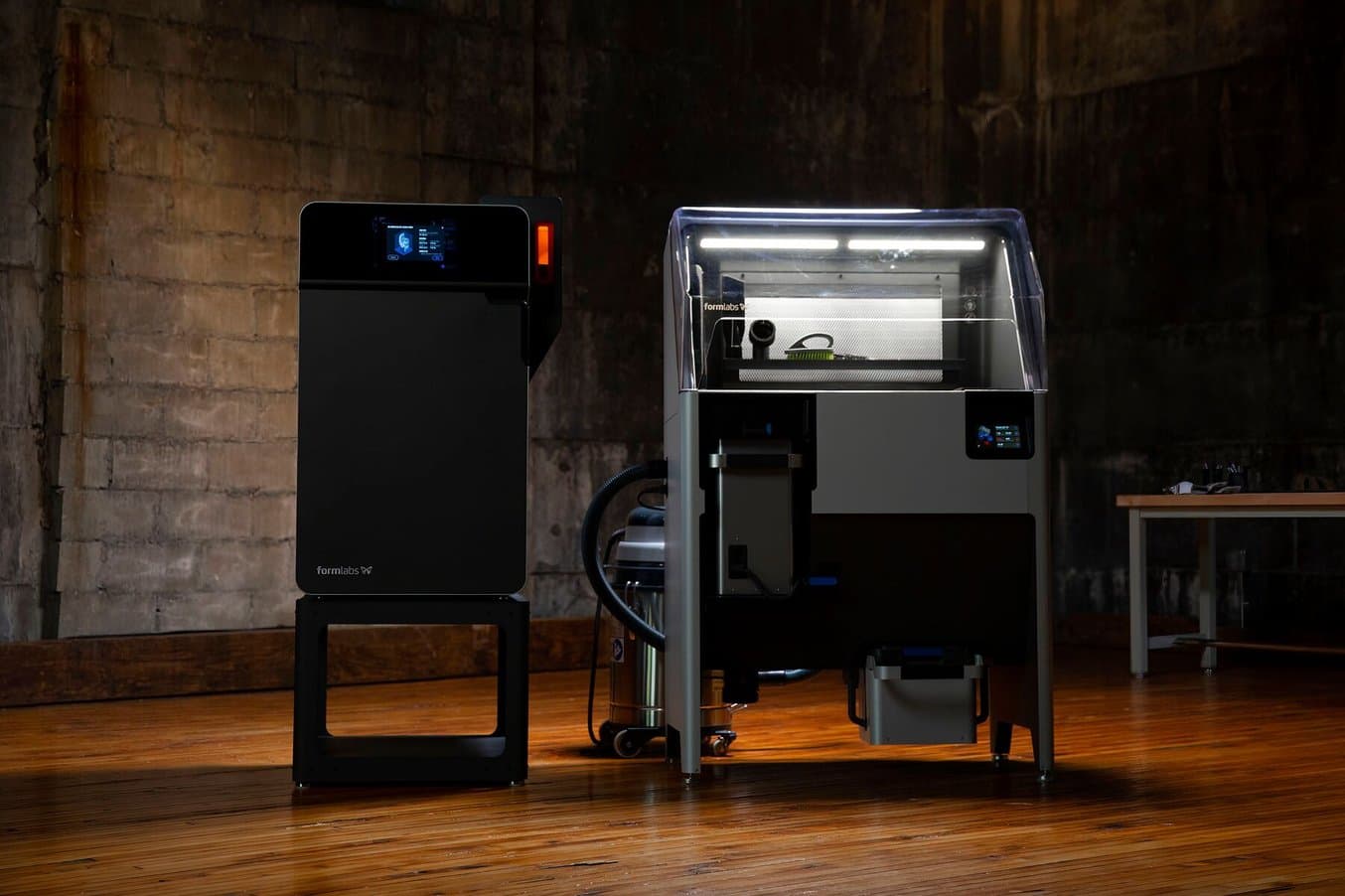
FormlabsのSLS方式3Dプリンタ、Fuse 1+ 30W。
1980年代にその技術が開発されて以来、SLS(粉末焼結積層造形)方式3Dプリンタは大手メーカーの試作品製作や少ロット量産向けに導入されてきました。しかし最近になりようやく、SLS方式の3Dプリンタが中小メーカーにも手の届きやすい価格になりました。SLS方式3Dプリンタの導入台数が世界的に増加しているという事実が、このプリント技術の造形品質の高さ、造形単価の低さ、量産に向けた準備のしやすさを物語っていると言えるでしょう。
SLS方式は、高出力レーザーを照射することで粉末状の樹脂材料を焼結し、3Dモデルをもとに造形するアディティブマニュファクチャリング技術です。造形スペースとなるビルドチャンバーにパウダー材料による薄い層を1層ずつ作り、造形品の断面をレーザーで焼結して積層する工程を繰り返してプリントします。SLS方式の3Dプリンタでは、造形品以外の部分は焼結対象とはならず、粉末状態のまま造形品の周囲や隙間に残されます。この未焼結パウダーが造形品を支えるため他の方式の3Dプリンタで必要となるサポート材が不要で、オーバーハング、内部チャネル、ラティス(格子)構造などの複雑な形状も造形できます。サポート材が不要なため後処理も簡単で労力がかからず、より大規模な生産でも安定して部品を量産することができます。
SLS方式では高出力のレーザーと高い精度、プリント工程全体の厳密な管理が必要で、これが最も安価なSLSプリンタであってもほとんどのFDM(熱溶解積層)方式プリンタやSLA光造形方式プリンタより高額になってしまう理由です。他の方式に比べると初期費用は高くなりますが、工業クラスのパワーをベンチトップサイズで実現したプリンタの生産性、そして価格がさらに手頃になったことにより、SLS方式3Dプリンタで内製化が実現できればわずか数ヶ月で投資金額をペイすることができます。
本記事では、初期購入価格から継続的なメンテナンス、材料の購入に至るまで、さまざまなSLS方式3Dプリンタの価格を比較し、SLS方式プリンタ導入にかかる全体的なコストを詳しく解説します。
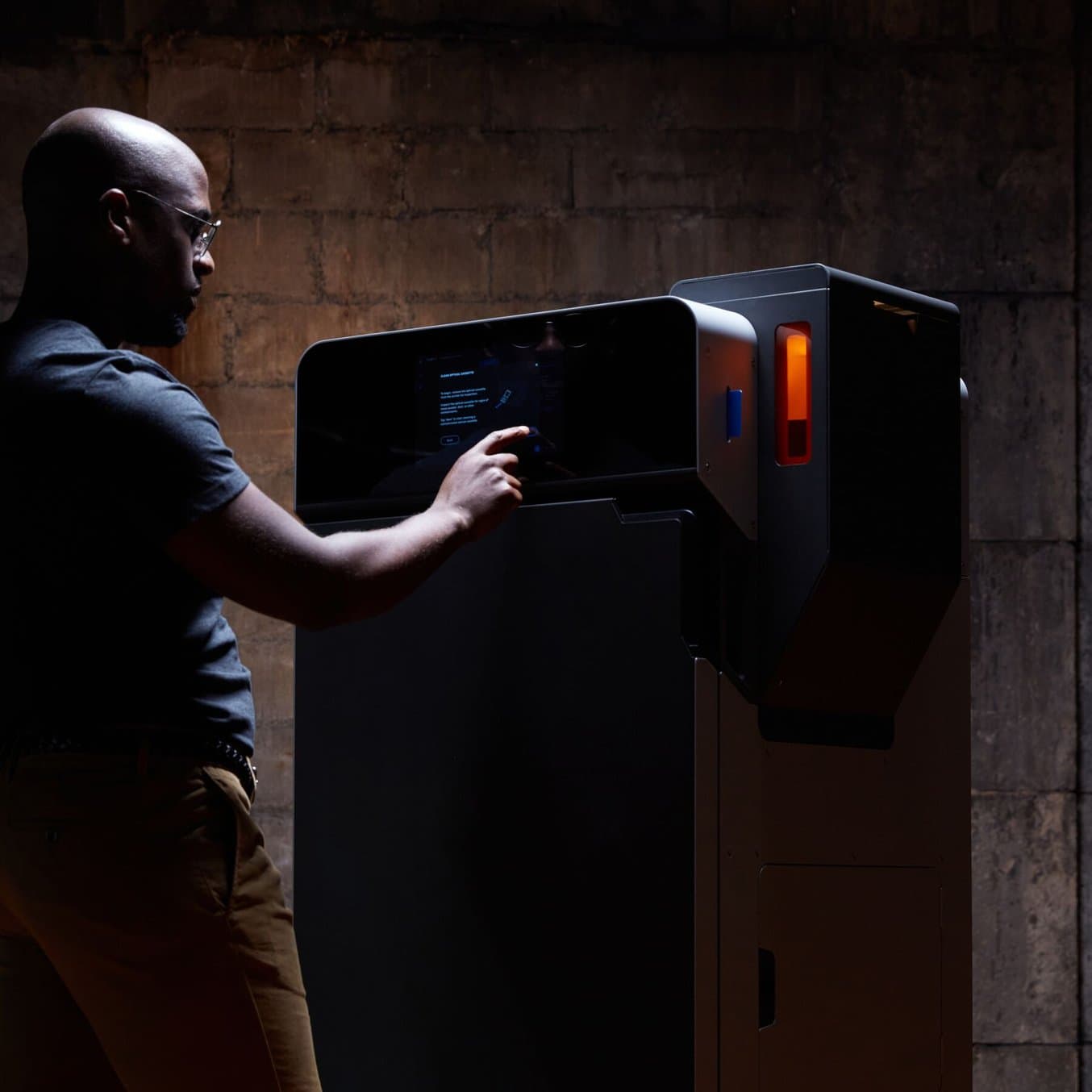
外注か内製か:SLS方式3Dプリントが適するケースとは?
本技術資料では、SLS方式3Dプリンタでの内製と、SLSプリント品を外注で製作した場合を比較し、SLS 3Dプリンタの導入の費用対効果の評価を行います。
SLS方式3Dプリンタの価格: ベンチトップ型と工業用プリンタ
SLS方式プリンタはこれまで、仕組みが複雑なうえに設置面積が大きく価格も高額なため、導入できるのは大規模な製造設備を持つ業界大手企業に事実上限定されていました。しかし過去5年間でベンチトップサイズのプリンタが登場したことで、中小メーカーでもSLSプリンタの導入が現実的な選択肢となったのです。
FuseシリーズのようなベンチトップサイズのSLS方式プリンタを従来の工業用プリンタと比較する場合は、購入価格、サイズ、使いやすさ、インフラ要件、継続的にかかるコストなど、いくつかの要素を考慮する必要があります。以下の表では、ベンチトップサイズの工業用SLSプリンタ(Formlabs Fuse 1+ 30W)と従来のSLSプリンタ(EOSや3D Systemの製品群を基準)との間でこれらの要素を比較したものです。
Fuse シリーズ: ベンチトップサイズの工業用SLS方式3Dプリンタ | 従来型の工業用SLS方式3Dプリンタ | |
---|---|---|
価格 | Fuse 1+ 30W:$28,989〜 | $200,000〜$500,000以上 |
造形サイズ | 最大165 x 165 x 300mm | 最大550 x 550 x 750mm |
長所 | 手頃な価格 造形品質の高さ 高いスループット 複数の材料が使用可能 簡素化された作業手順 狭い設置面積 省メンテナンス | 大きなビルド容積 造形品質の高さ 高いスループット 複数の素材オプション |
短所 | 造形量が少ない | 機器が高額 設置面積が大きい 設備要件 高メンテナンス 専任のオペレータが必要 |
SLS方式のコストに含まれるもの
設備所有コスト:
SLSプリンタの設備所有にかかるコストを考える際、プリンタの本体価格だけではなく、周辺機器、メンテナンス、サービスなども考慮が必要です。プリンタ自体の価格は、$10,000程度から購入が可能な格安DIY SLSプリンタから、最も高価なものであれば大容量の工業用プリンタで$500,000以上など、種類によって価格帯が大幅に異なります。
Formlabsは、工業品質での造形を手頃な価格で提供することに成功した最初のメーカーです。Fuse 1+ 30Wは$28,989という価格帯でありながら、従来の工業クラスSLSプリンタに匹敵する造形品質を実現します。しかし、どのプリンタを購入しても造形品を部品として使用可能な状態にするには、プリント後の後処理が欠かせません。
SLS方式プリンタはサポート材が不要なため、サポート材を取り除く手間がかかりません。ただし、造形品の周囲に残る未焼結パウダーを取り除く工程があり、そのための専用機器が必要になります。SLS方式プリンタを扱うメーカーのほとんどが後処理や粉末回収ステーションも合わせて提供していますが、その価格帯は大きく異なります。FormlabsのFuse Depowdering Kitなら$999と手頃な価格で導入が可能で、コンパクトで高効率なパウダー回収ステーションのFuse Siftは$9,999です。高価格帯の製品としては、$50,000のEOSソリューションなどがあります。
造形品から大まかにパウダーを除去した後は、ブラスト処理(サンドブラストとも呼ばれます)でパウダーを徹底的に除去することをおすすめします。手動ブラストキャビネットは$500以下で購入可能で、自動ブラスト装置を初めて手頃な価格で実現したFuse Blastなら$10,999という価格で作業時間の大幅削減が実現できます。
また、Fuse 1+ 30W SLS 3Dプリンタ、そしてパウダー除去・回収・再利用を一台で可能にするFuse SiftとFuse Blastがセットになった工業品質の造形を叶えるエコシステム一式が$60,000以下でご利用いただけます。この価格帯を実現したことで、中小企業や個人、教育機関などより多くの人々に、パワフルなSLS 3Dプリントを使った内製の可能性を追求いただけるようになります。
現在市場に出ているSLSプリンタにはすべて、任意または必須でサービスプランと保守契約オプションがついています。従来型の工業用プリンタの場合、サービス契約料が本体価格の10%程度、つまりFuseシリーズのプリンタを毎年追加購入できてしまうほどの金額に設定されていることがほとんどです。さらに、工業用プリンタのサービスプランは毎年更新が義務付けられていることが多く、継続的なコストが発生し続けることになります。
材料と消耗品
SLS方式の材料として最も一般的なのはナイロンです。ナイロンは高機能エンジニアリング系熱可塑性プラスチックで、硬度が高く軽量な機能部品の主要材料として使用されています。ナイロン複合材料も広く使用されており、TPUのように柔軟性のある材料を提供しているメーカーもあります。これらの材料費はメーカーによって異なりますが、ナイロン材料の価格はほとんどが1kgあたり$100ドル前後で、大量購入で割引が適用されるケースもあります。
原材料の価格はどのメーカーでも大体同じですが、これらの材料にかかる継続的なコストは作業手順の効率性によっても変動し、その効率性を左右するのがパッキング率とリフレッシュ率です。
FuseシリーズのようなベンチトップサイズのSLSプリンタの場合、パッキング率30%を実現できることが多く、粉末のロスが最小限で済みます。無駄のないプリント手順の実現可否は、パッキング率とリフレッシュ率のバランスを合わせられるかどうかにかかっています。リフレッシュ率とは、プリントを行う度に必要となる未使用パウダーの量を指します。SLSプリンタのリフレッシュ率は30%~50%が主流ですが、一部のプリンタでは20%程度しか実現できないケースもあります。
しかし、リフレッシュ率だけが消耗品にかかる継続的なコストを左右するわけではなく、最も重要なのはリフレッシュ率とパッキング率のバランスなのです。リフレッシュ率とパッキング率のバランスが取れている、もしくはパッキング率がリフレッシュ率より高い場合は、使用済みパウダーと未使用パウダーを同量で入れ替えれば良く、最終的にすべてのパウダーが使用されることになるため無駄が最小限に抑えられ、資金を効率的に使うことができます。
人件費
SLS方式の場合は未焼結パウダーが造形品を支えるため、FDM方式やSLA光造形方式で発生するサポート材の取り外し工程が不要です。ただし、後処理として造形品から余分なパウダーを取り除く必要があるため、手作業をゼロにすることはできません。また、一部のプリンタは仕組みが非常に複雑で、プリントを1回行うごとにメンテナンスや手間のかかる準備作業が必要になる場合があります。
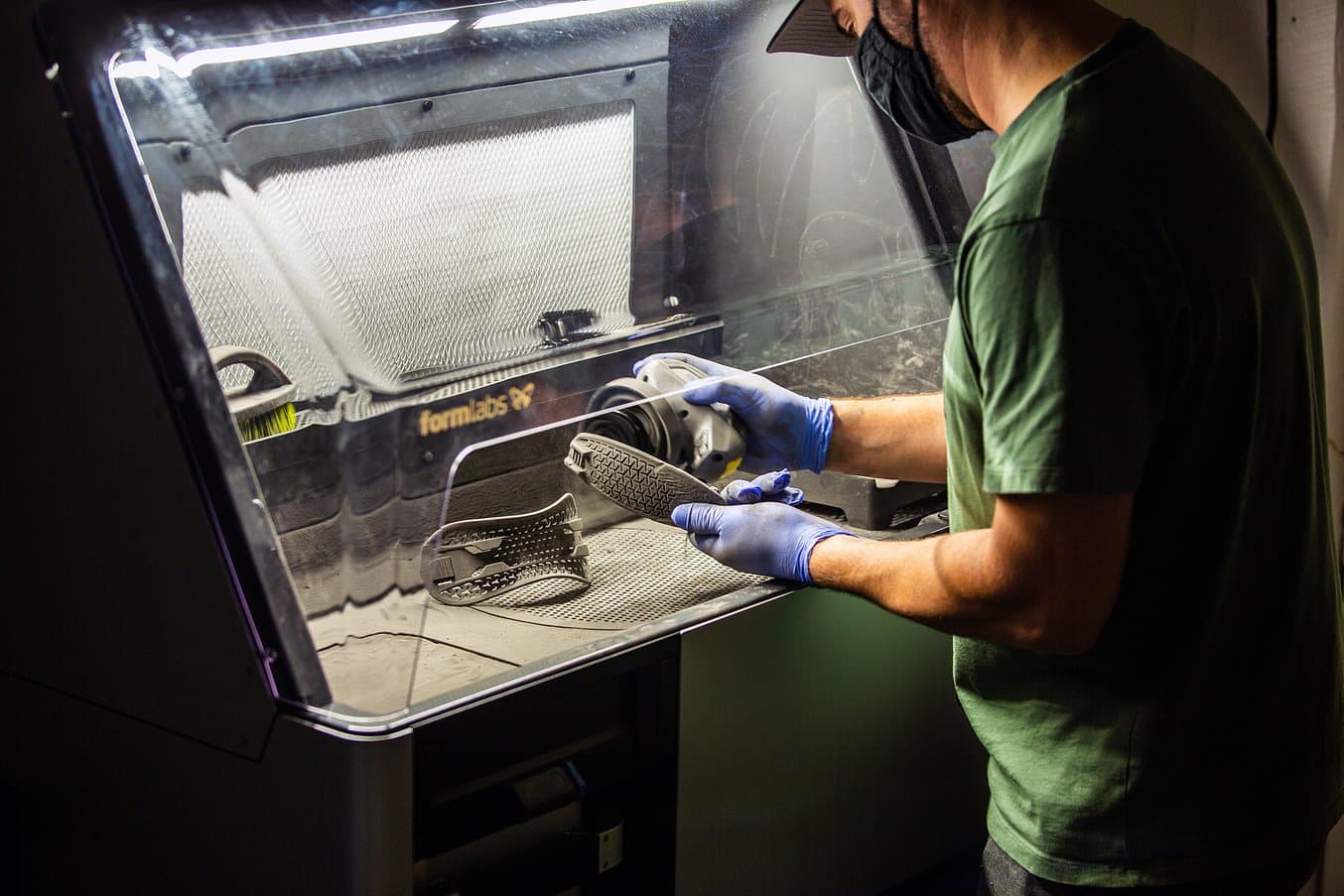
Fuse Siftは、パウダーの除去、回収、再利用、ミキシングを一貫した手順で行える後処理装置です。
従来の大型SLSプリンタの場合、プリンタ本体と後処理装置の操作には専任の技術者が必要で、場合によってはパウダーの再利用工程で別の機器が必要になることもあります。このような従来型のSLSプリンタでは、使用するパウダーを別のものに切り替えたい場合、プリンタと後処理装置のクリーニングやパウダー除去に少なくとも丸1日かかることがあります。コストの計算をする際は、このような作業にかかる追加の人件費のほか、洗浄中にプリンタが使えないことによる潜在的な生産機会の損失も考慮する必要があります。FormlabsのFuseシリーズの場合、Nylon 12パウダーとNylon 11パウダー間の切り替えに必要な時間はわずか4時間で、Nylon 12パウダーとNylon 12GFパウダーなど、ベースとなる成分が同じ材料間の切り替えはさらにその半分程度の時間で済みます。
DIYプリンタなど低価格SLSプリンタの場合は、後処理に必要な周辺機器が付属しておらず、オペレーターがパウダー除去やパウダーの混合、再利用、その他作業に費やす時間が長くなります。作業手順が直感的でないことも、多くの手作業が必要になる原因です。
FormlabsのFuseシリーズは、従来型のSLSプリンタの合理化された作業手順と低価格プリンタの設置面積の少なさを兼ね備えたプリンタです。FuseシリーズのプリンタとFuse Siftをセットで導入しても既存の作業環境に無理なく組み込むことができるサイズで、パウダー除去や再利用などパウダーの取り扱いに関わるすべての作業はFuse Siftで簡単かつ直感的に行えるため、オペレーターはより重要な作業に時間を割くことができます。
SLS方式3DプリンタのROI算出
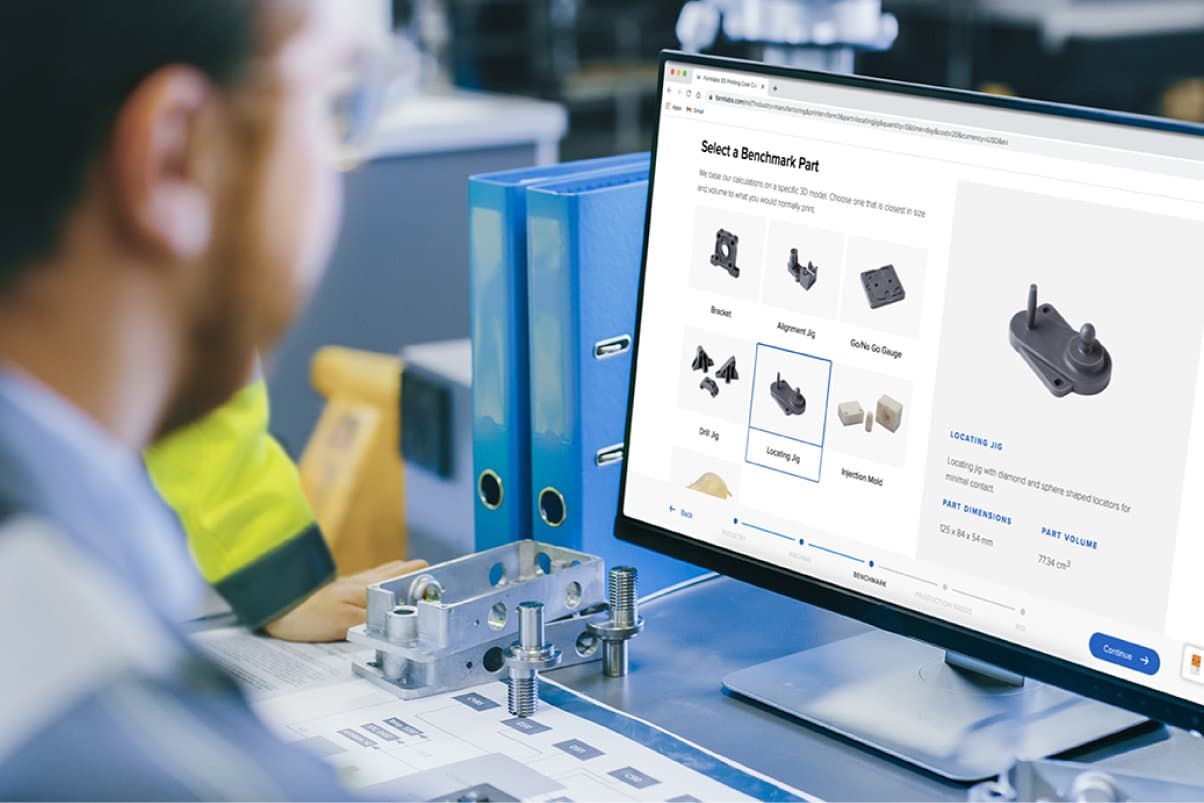
FormlabsのROI試算ツールでは、ハードウェアの購入価格、材料費、人件費、その他すべてのコストを細分化し、一定の生産量に基づいて造形単価を計算することで、SLSプリンタ導入に必要な予算を簡単に計算できます。さらに、SLSプリンタを導入した場合と外注やその他製法でかかる時間とコストも比較し、SLS導入でどれほどの削減効果が見込めるのかを確認することもできます。
SLS方式の内製化と外注
SLS方式は、機能性を備えた堅牢な工業品質の試作品を迅速かつ手頃な価格で製作したい場合や、実製品用部品の小ロット量産やカスタム生産に最適です。内製か受託メーカーへの外注かを問わず、既に多くのメーカーやエンジニア、プロダクトデザイナーがSLS方式で製作した部品に信頼を寄せています。
長い歴史を持つ技術でありながら、これまで大手メーカー以外が内製化するには価格が高すぎたため、SLS方式で部品を製造したい場合はほとんどの企業が外注に頼るしかありませんでした。現在でも、部品を1回しか生産しない場合やパワフルなSLSプリンタを導入したくても資金が足りない新興企業などの場合には、SLS方式の部品を外注したほうがメリットが得られるケースもあります。受託メーカーへ外注することで、試作品製作や小ロット量産で量産移行前の製造フェーズをカバーできることもあります。しかし、SLSプリンタを使った高品質な部品の内製が手の届く範囲になった今、中小メーカーもSLS導入のコストを検討する価値があると言えるでしょう。
Fuse 1+ 30Wプリンタの社内導入は従来のSLSプリンタの10分の1のコストで実現でき、さらに部品を内製化することで製造工程の主導権を握ることができるようになります。Fuseシリーズのプリンタを使った内製環境が整えば、量産の場合はわずか5週間、試作品製作の場合は2~3か月でROIをプラスにすることができます。企業は外注に依存する必要がなくなり、試作品製作や小ロット量産を高速化し、部品の出荷・配送時間などの変動要素を減らすことができるようになります。最新の技術資料では、6種類の異なる試作品と生産シナリオを用いて、内製化によって企業がどれくらいの期間でFuse 1+ 30Wの購入費用を回収できるかを分析しました。
試作品:電動ドリル
材料: Nylon 12パウダー
造形品:アセンブリ1つに対して2点、合計4点
Fuse 1+ 30Wで内製 | SLS受託メーカーに外注 | |
---|---|---|
造形時間 | 13時間10分 | |
冷却 | 13時間45分 | |
シフト時間(後処理の作業時間) | 40分 | |
合計時間 | 27時間35分 | 7~10日 |
材料費 | $50 | |
人件費 | $11.22 | |
コスト合計 | $61.22 | $752.50 |
造形単価 | $15.31 | $188.13 |
従来の方法で試作品製作にかかる合計時間は、SLSプリンタを使った内製を毎週5サイクル行い、2つの部品から構成されるドリル本体のアセンブリの試作・検証を10回行った場合に匹敵します。また、2週間に1回しか設計変更ができない外注の場合と比較すると、SLS方式3Dプリンタを使った内製では確実な設計改良が可能になると考えて良いでしょう。設計変更に合わせて外観を変更したり、グリップ部分のバリエーションを増やしたり、ネジの挿入深さを変えたり、内製であればすぐに試作品を作り、翌日には承認取得のために社内の担当チームに提出することができます。
このような仕組みが実現した場合、3Dプリント受託メーカーに外注する場合と比較して節約できるコストは約$700で、1サイクルあたり90%以上の節約ができることになります。つまり、Fuse 1+ 30W導入後わずか3か月あまりでROIがプラスになり、仮にプリンタを週に1回しか使用しない場合でも1年少々あれば利益を出せるようになる計算です。
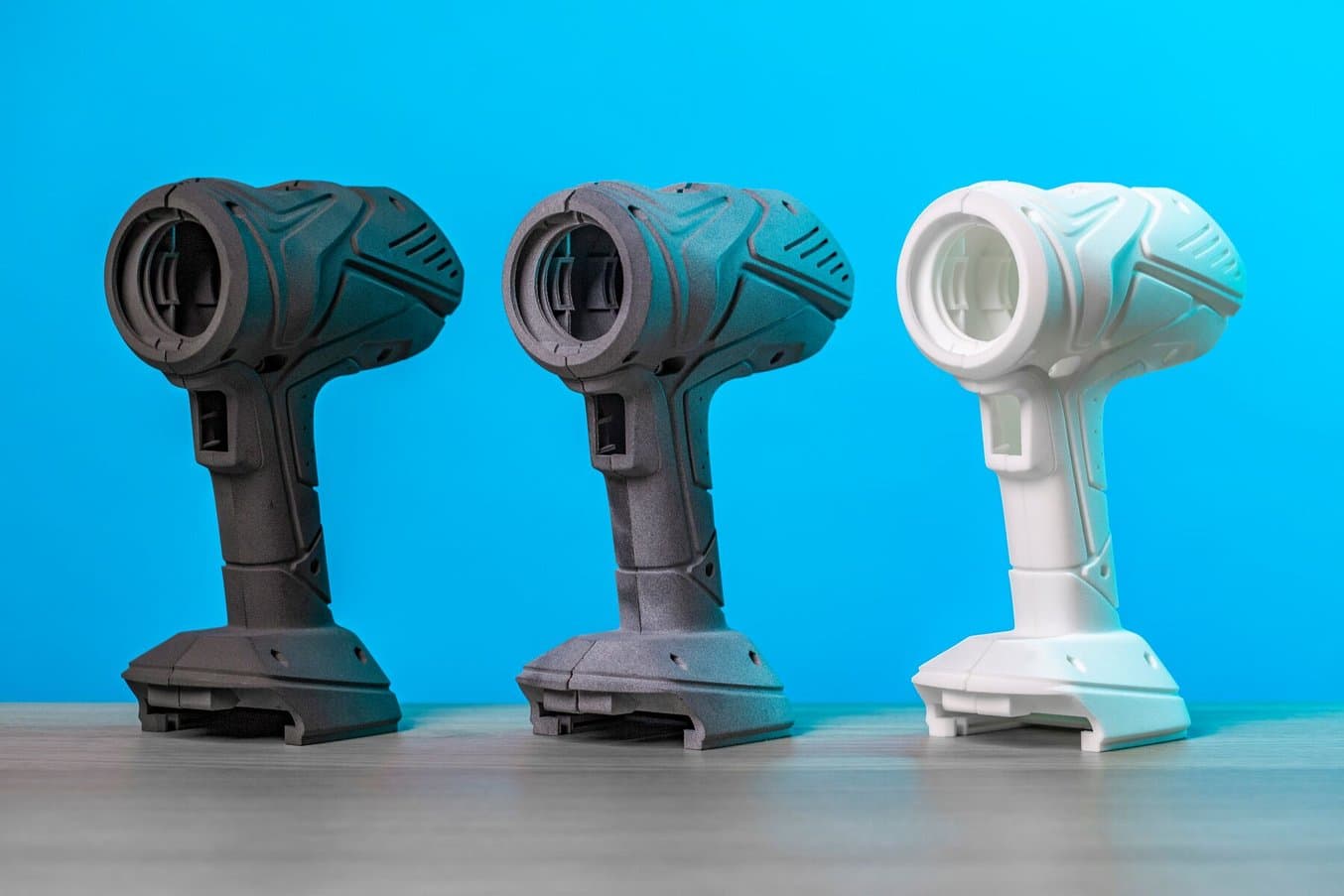
Fuse 1+ 30Wプリンタ(左)、HP MJFプリンタ (中央)、EOSの工業用SLSプリンタ(右)で造形したドリルの試作品。
ROIを短期間でプラスにできた事例は、ラピッドプロタイピングだけではありません。以下の技術資料では、実製品用部品や治具を少量だけ内製する場合にどの程度の費用削減が見込めるのかを分析し、内製化によって削減できる費用により上記のラピッドプロタイピングと同程度の期間でプリンタの購入価格を回収できることがわかっています。
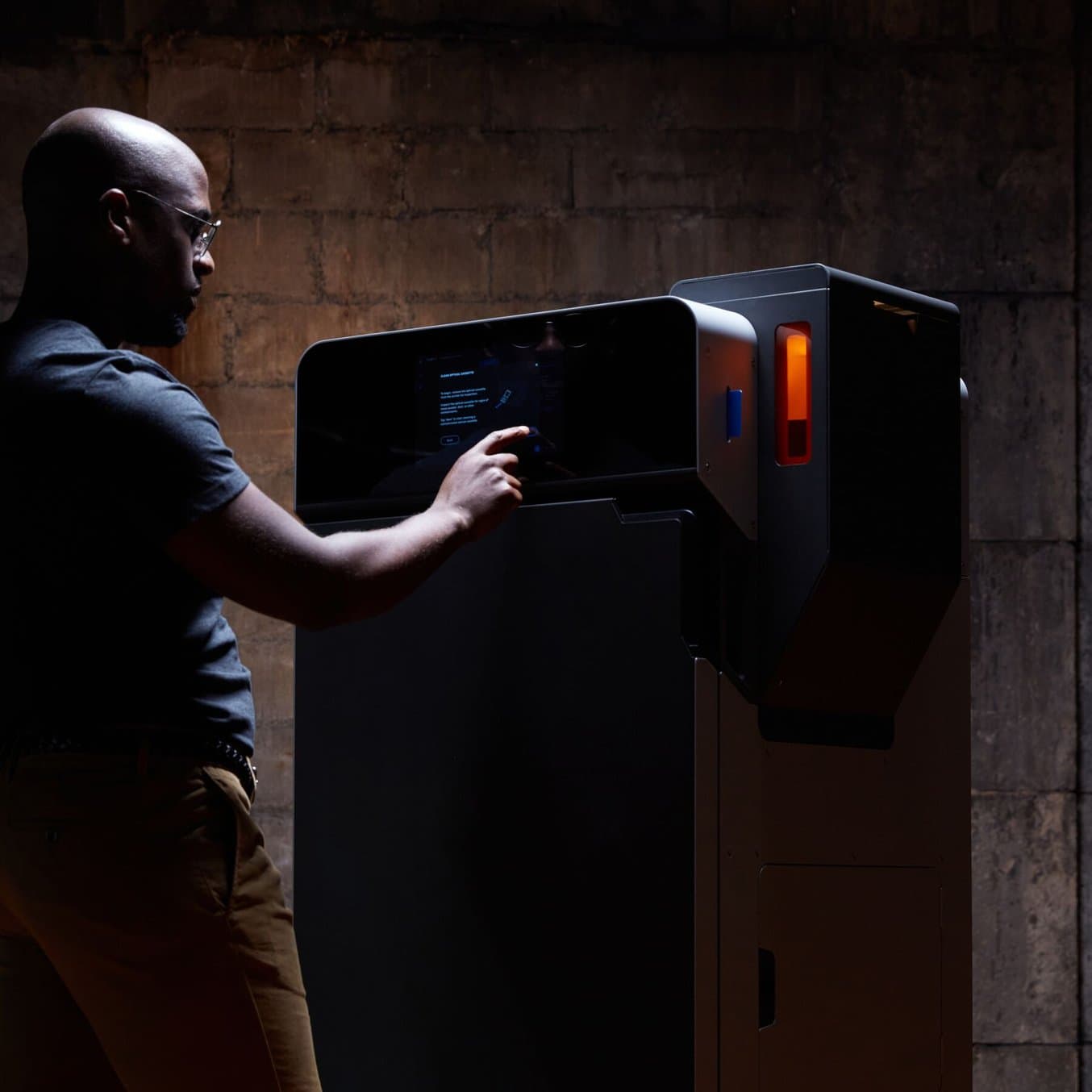
外注か内製か:SLS方式3Dプリントが適するケースとは?
本技術資料では、SLS方式3Dプリンタでの内製と、SLSプリント品を外注で製作した場合を比較し、SLS 3Dプリンタの導入の費用対効果の評価を行います。
結論
SLS方式3Dプリンタはこれまで、ハードウェア本体のコストだけでなく、継続的に発生する材料費やサービスプラン、メンテナンスなどのコストにより、ほとんどの企業には手の届かない高額なソリューションでした。
しかし、ハードウェアの価格が下がり、合理化された作業手順で運用コストも削減できるようになった今、SLSプリンタ導入の敷居がはるかに低くなりました。FDM方式やSLA光造形方式よりも高額であることには変わりありませんが、SLS方式3Dプリンタによってさまざまなメーカーが価値を提供できる可能性が広がっています。高いスループットと卓越した造形品質により、企業は試作・検証サイクルや小ロット量産プロセスを高速化して市場投入までの時間を短縮し、外注に頼ることなく金型や交換部品の製作ができるようになります。高速で効率的、かつ造形品質の高い3Dプリンタなら、特に外注などの他のソリューションと比較した場合に短期間で初期費用を回収できます。
FormlabsのFuseシリーズは、従来の大型SLSプリンタに匹敵する高品質部品を手頃な価格と使い慣れた材料、そしてこれまでより効率的なパウダー再利用システムで生産することができます。また、プリンタの本体価格と継続的なコストの両方を考慮しても、Fuseシリーズは工業クラスの高品質な部品を最も手頃な価格で内製できるプリンタです。