世界最大の日用品(FMCG)メーカーの1つであるUnileverは、パーソナルケアやホームケア、栄養、その他の日用品の新製品を常に開発しています。Dove、Domestos、Cif、Knorr、Axe (Lynx)、Ben & Jerry's、その他多数のグローバルおよびローカルブランドを展開していることから、おそらくどなたのご自宅にもUnileverの製品が少なくとも1つはあることでしょう。
FMCGは、消費者の需要に応えるべく絶えず熾烈な競争が繰り広げられている激戦市場です。その中で、各ブランドは製品戦略を革新し、適応させ続けていく必要があります。その中で、イノベーションの主要分野の1つとなるのがパッケージングです。製品の中身と同じくらい、ボトルそのもののデザインが消費者の印象に大きな影響を与えるのです。Unileverのようなブランドは、自社が抱える膨大な種類のパッケージや製品について、材料の使用量や審美性、安全性、持続可能性を考慮しなければなりません。しかし、一見「シンプル」に見えるプラスチックボトルでも、コンピュータ上のデザイン製作から生産ラインで中身を充填するまで、従来は何ヶ月もかかっていました。
「Unileverのような日用品メーカーは、できるだけ早く、競合他社より先に製品を市場に投入しなければなりません。最高の製品を最短かつ最良の価格で消費者に提供する必要があるので、3Dプリントが工程の高速化に役立ちます」
Unilever CAD&プロトタイピングオーナー、Stefano Cademartiri氏
UnileverのCAD&プロトタイピングオーナーであるStefano Cademartiri氏とSerioplast Global ServicesのR&DデザインマネージャーであるFlavio Migliarelli氏が協働し、3Dプリント製の型を使って少量の延伸ブロー成形(SBM)を行う場合の実現可能性を検証し、試作品製作やパイロットテストの工程を高速化することで製作期間を6週間、コストを最大90%削減した方法をご紹介します。
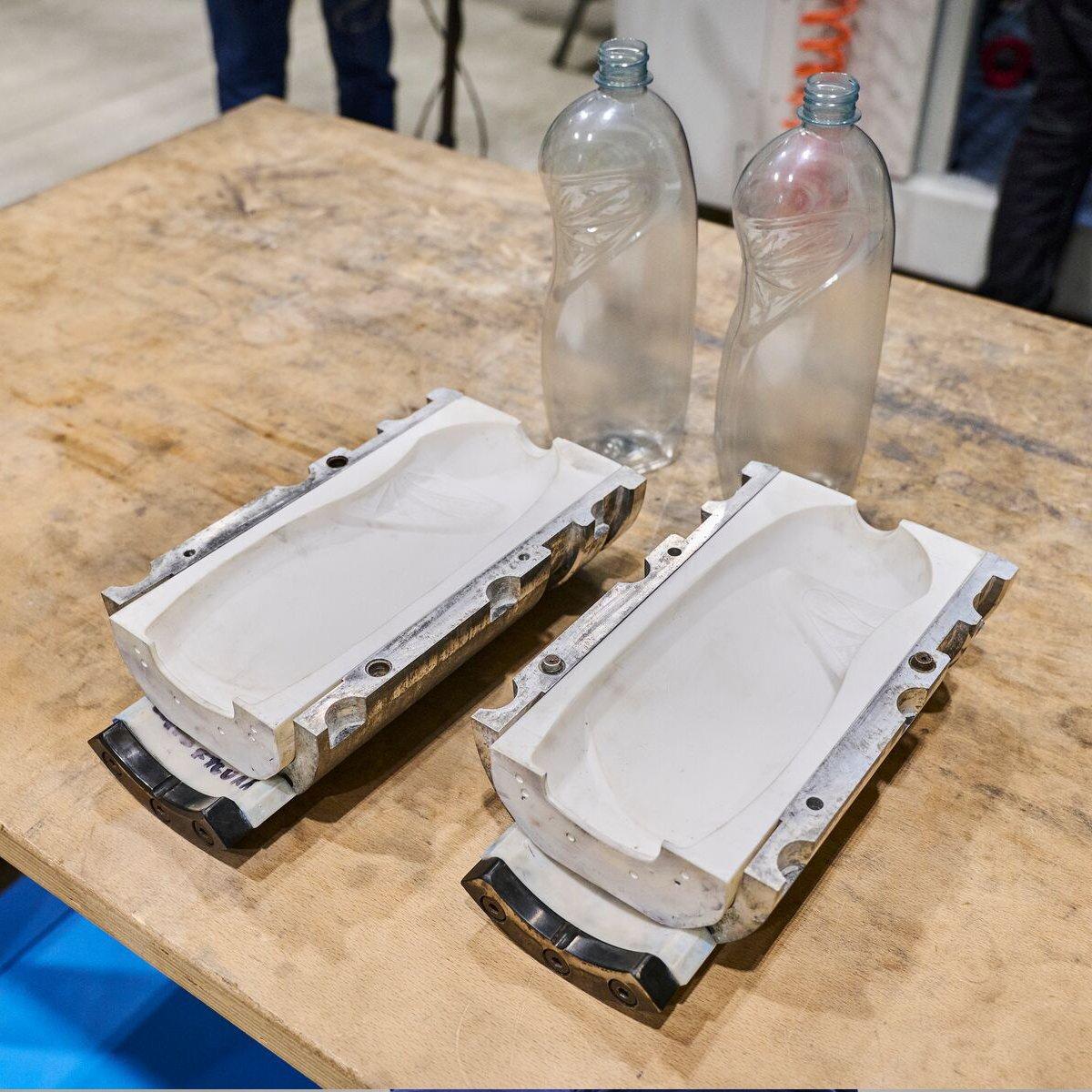
3Dプリント製の型で延伸ブロー成形品を少量・高速製作
本製品仕様では、SLA光造形方式で3Dプリントした型をSMB工程で活用するためのガイドライン、およびプリプロダクションにおけるコストや製作期間の削減方法を解説しています。設計や工程における考慮事項から成形条件に至るまで、UnileverとSerioplastという業界のエキスパート2社が行なった様々な実現可能性調査について詳細をご紹介します。
従来の新ボトル開発・検証工程
食品・飲料製品の容器、化粧品や医薬品のパッケージなど、プラスチック製品の生産には一般的にブロー成形が用いられます。ブロー成形とは、長年に渡って薄肉構造の製品を高品質かつ高速に大量生産するために用いられてきた製造方法です。ブロー成形のサイクルタイムは通常1〜2分と非常に短く、大量生産をする場合に非常にコスト効率の良い方法で、通常は形が同じ製品を低単価で何百万個と生産する場合に採用される製造方法です。
ブロー成形では、パリソンやプリフォームと呼ばれる、熱で溶かしてパイプ状にしたプラスチック材料を金型内で膨らませることで製品を成形します。ブロー成形には、押出ブロー成形(EBM)、射出ブロー成形(IBM)、延伸ブロー成形(SBM)と大きく分けて3つの工程があります。高品質でガラスのように透明なPETボトル容器(飲料水のボトルなど)の製造には、一般的にSBMが用いられます。
Serioplastは、FMCG業界向けに硬質なプラスチックパッケージを提供する世界的メーカーで、Unileverの主要パートナーの1つとしてホームケアおよびパーソナルケア市場向けの製品パッケージの開発・製造を支援しています。「PET、HDPE、PP材料で年間40億本のボトルを生産しています」とMigliarelli氏は言います。
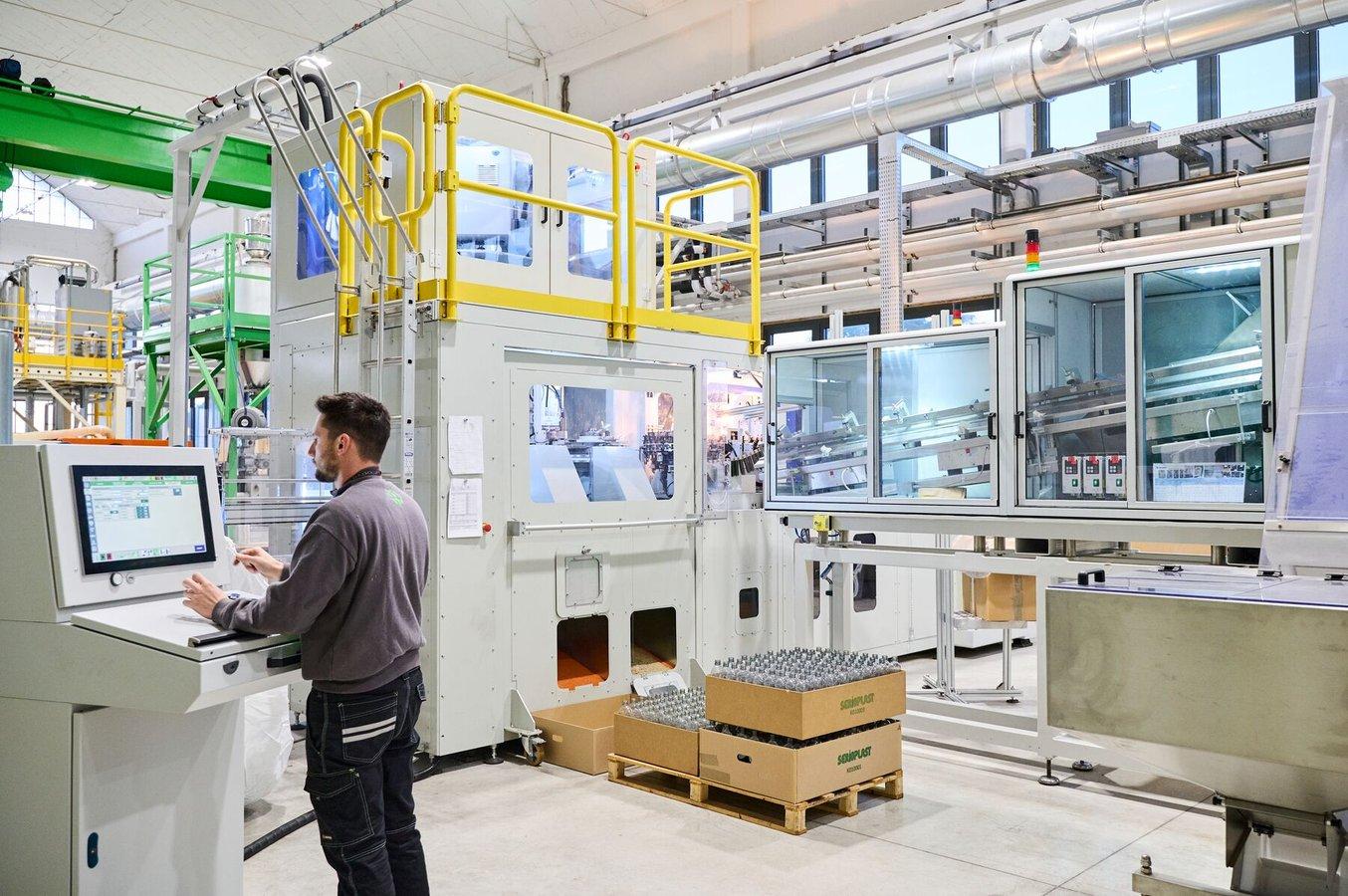
イタリアにあるSerioplastのR&D施設に設置されているSeriomac UNIX 4 Cavities SBM機。同社はUnileverと協働で、工業向けの大規模生産設備で3Dプリント製の型を使用する新たなワークフローを開発しました。
Serioplastはこれまで、試作品用のモックアップを直接3Dプリントするか、ブロー成形で製造していました。今まで、3Dプリント製のモックアップは実製品の手触りや透明性を忠実に再現できず、消費者テストに出せるほどの信頼性がありませんでした。しかし、SBMで量産品質のサンプル品を製作するには高価な金型が必要で、工程の複雑さや外注の必要性により、一般的なパイロットテストフェーズにさらに6~9週間ほど余分な時間がかかっていました。
「お客様に実物のサンプルをお渡しできるまでに6〜12週間は待たなければならず、新ボトルのデザインを確認するだけで何週間も無駄になってしまっていました。再設計が必要になることもありますから、この工程は非常に大変でフラストレーションの溜まるものでした」とMigliarelli氏は言います。
SBMで使う成形型はこれまで、CNC加工で作る金型が一般的でした。この製作には専用の機器やCAMソフトウェア、熟練のオペレーターが必要です。こういった金型は通常、受託メーカーに外注して製作されることが多く、製作期間は4〜8週間ほど、コストは$2,000〜$100,000以上と成形品の複雑さや1つの成形型に必要な部品数に応じて大幅に変動します。金型を社内で加工する場合でも、材料を発注してから届くまでの時間やCAMと機械のセットアップ、手動で行う研磨作業、機械が稼働するまでの待ち時間など、いくつかの工程が必要なために通常は6週間ほどかかってしまいます。
そのため、試作品製作やパイロットテスト用にブロー成形で少量生産する、というのはこれまで金額的に現実的ではありませんでした。Unileverのような企業は、長期的なタイムラインで計画を立て、様々な材料で作った外観確認用の試作品を元に最終的な決定を下しますが、そのためには旧式の方法で金型製作が必要で、莫大なコストがかかります。
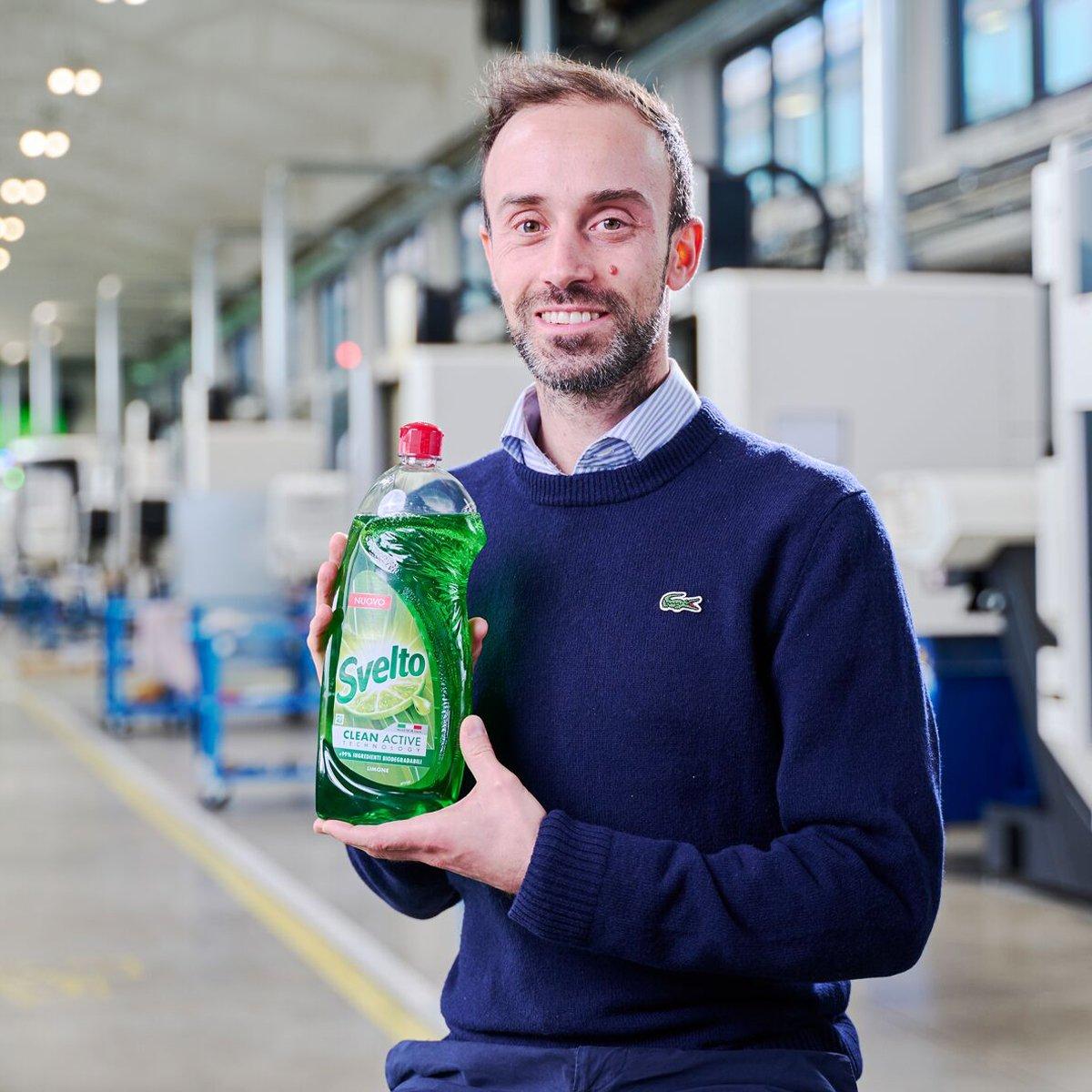
高速ブロー成形でパッケージのパイロットテストにかかるコストと時間を削減
本ウェビナーでは、ブロー成形のエキスパートであるFlavio Migliarelli氏をお招きし、ブロー成形の工程や手法をステップバイステップで解説いただくと共に、高速延伸ブロー成形における3Dプリント製の型の活用例やそのメリットをご紹介します。
実製品と同じ材料を使ったボトルのブロー成形で、時間を70%、コストを90%削減
3Dプリントは、成形型を高速かつ低コストで製作できる強力なソリューションです。3Dプリントの活用でごく限られた設備での製作が可能になり、CNC加工機を占領することなく、熟練のオペレーターも他の重要な作業に集中できるようになります。成形型を3Dプリントで内製化することで、メーカーやプロダクトデザイナーは製品開発工程にラピッドツーリングを取り入れ、大量生産前に設計や製造工程を検証できるようになります。3Dプリント製の型は既に射出成形や熱成形で活用されており、試作・検証プロセスを迅速に繰り返すことで製品開発工程を高速化し、より良い製品を市場に届けています。
SLA光造形方式3Dプリントは、成形型の製作に最適です。滑らかな表面と高精細さが特徴の光造形方式で作る型は、形状がしっかりと成形品に反映されるため離型も容易です。大容量3DプリンタForm 3Lを使って、大型の部品や金型を製造することができます。
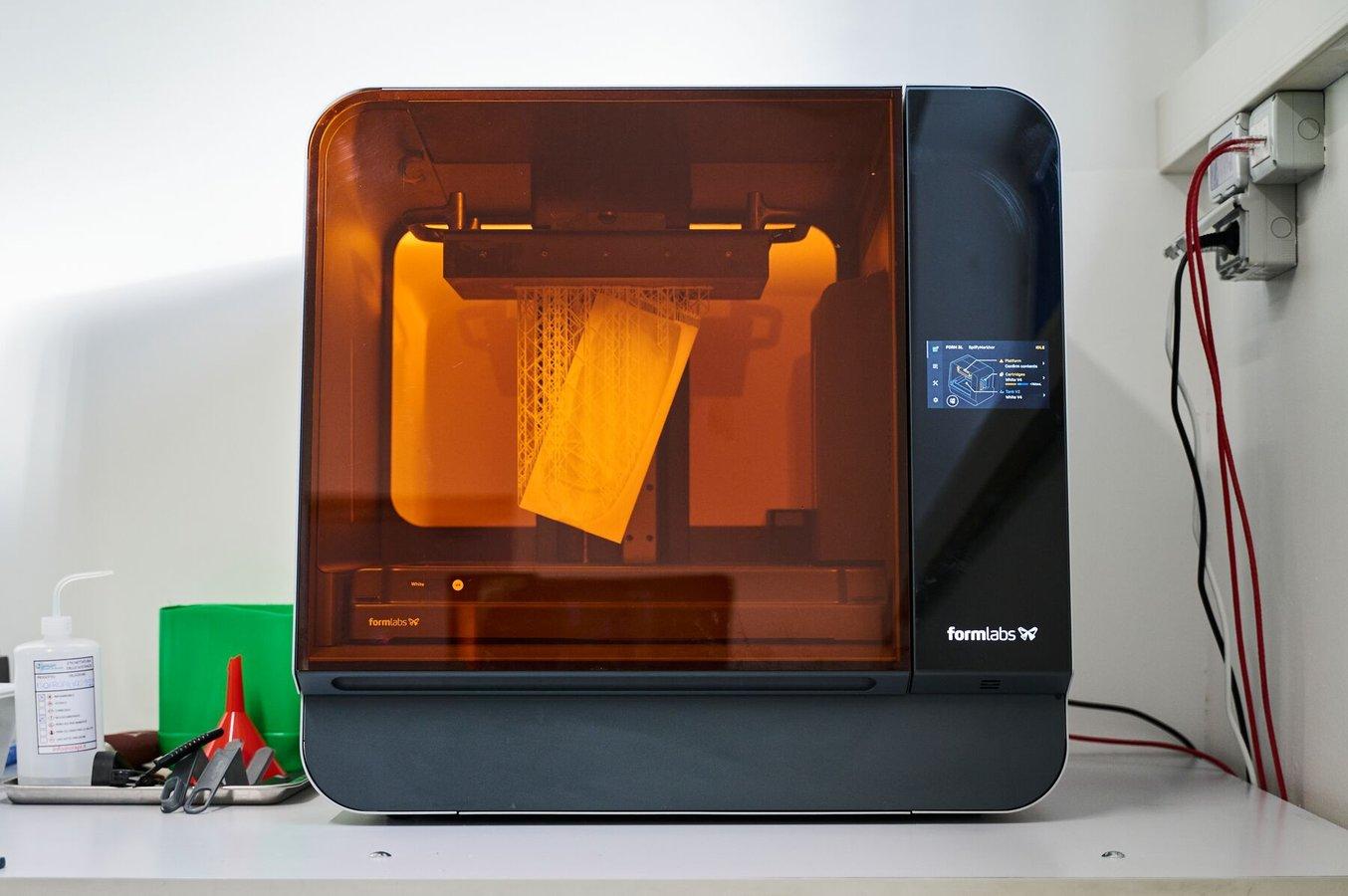
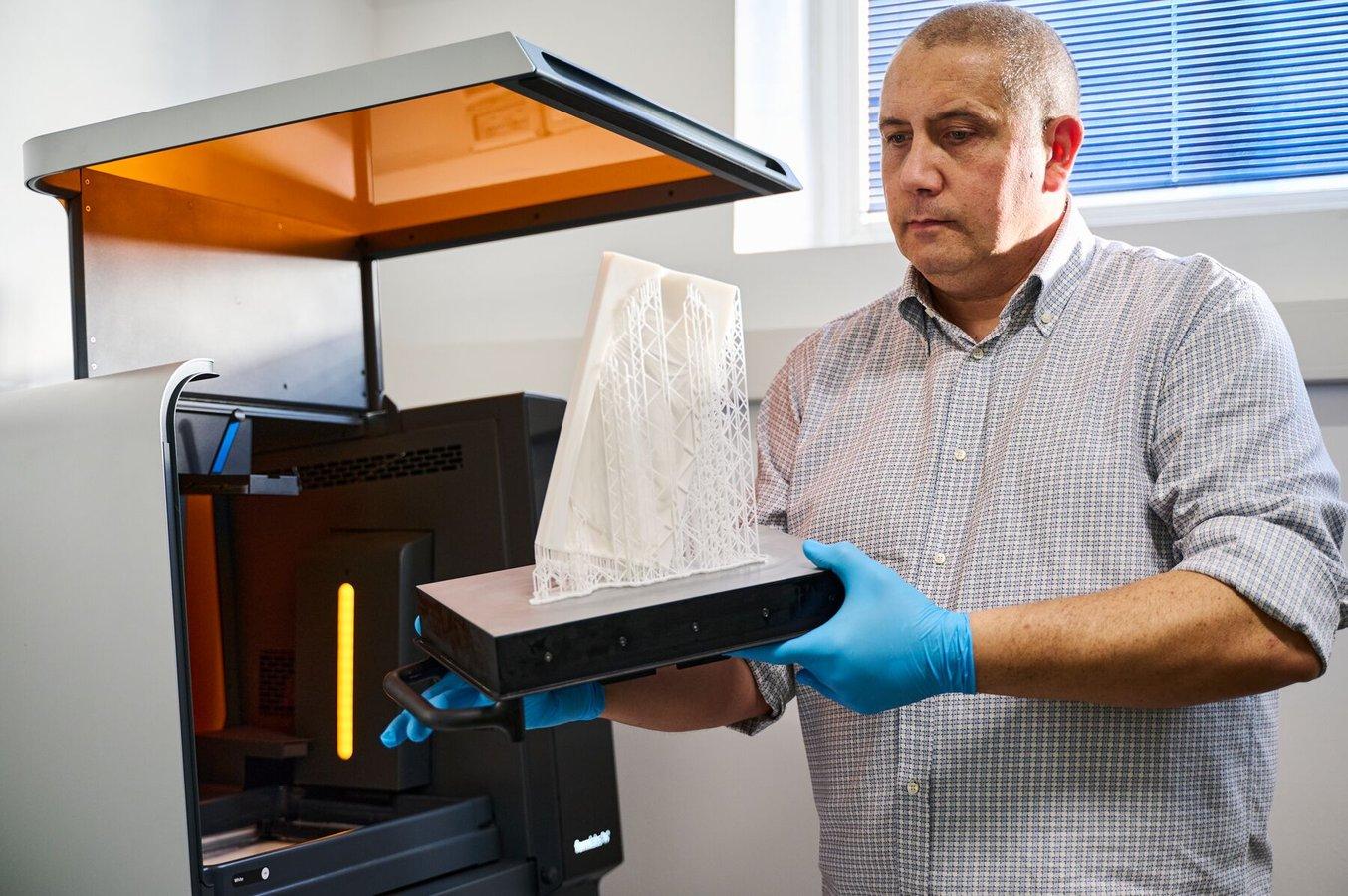
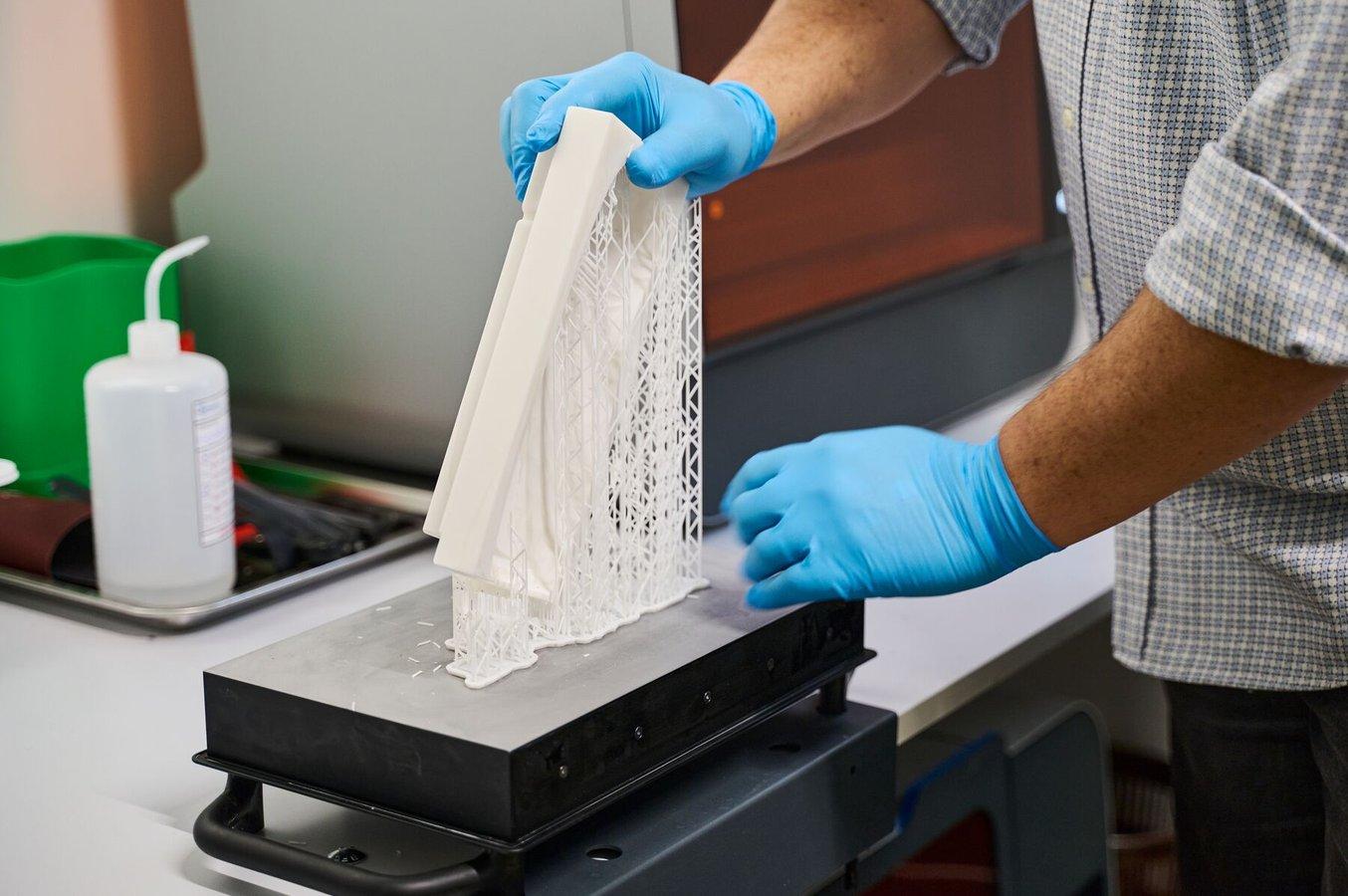
Form 3LにてRigid 10Kレジンで成形型をプリント。
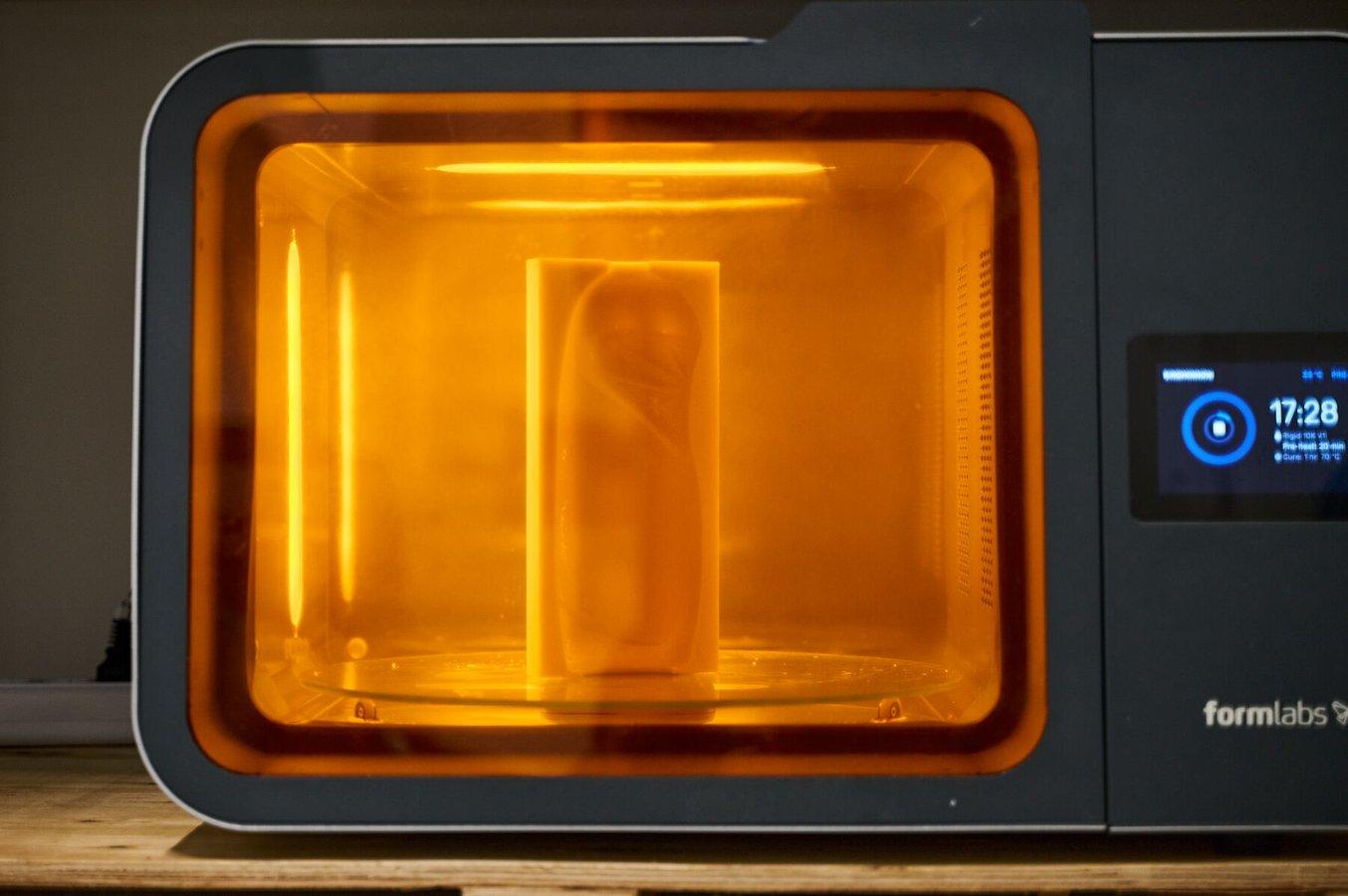
洗浄後はサポート材を取り除き、二時硬化をする。
成形型を製作する際は、材料選びが非常に重要です。UnileverとSerioplastには、高い寸法精度と安定性を備え、SBM工程でかかる内圧や高温にも耐えられる材料が必要でした。
Cademartiri氏は「Formlabのスペシャリストにアドバイスをもらいながら、テスト用に実際の材料でボトルを用意できる可能性のある材料を特定することができました」と言います。
FormlabsがSBM向けに推奨するのは、高い強度と剛性、耐熱性を備えたRigid 10Kレジンです。218°C @ 0.45 MPa の荷重たわみ温度と 10,000 MPa の引張弾性率を備えた工業グレードの高度なガラス充填材料で、Rigid 10Kレジンで3Dプリントした成形型は寸法安定性に優れ、常に均一な品質で数百回にも渡るブロー成形サイクルに耐えられます。
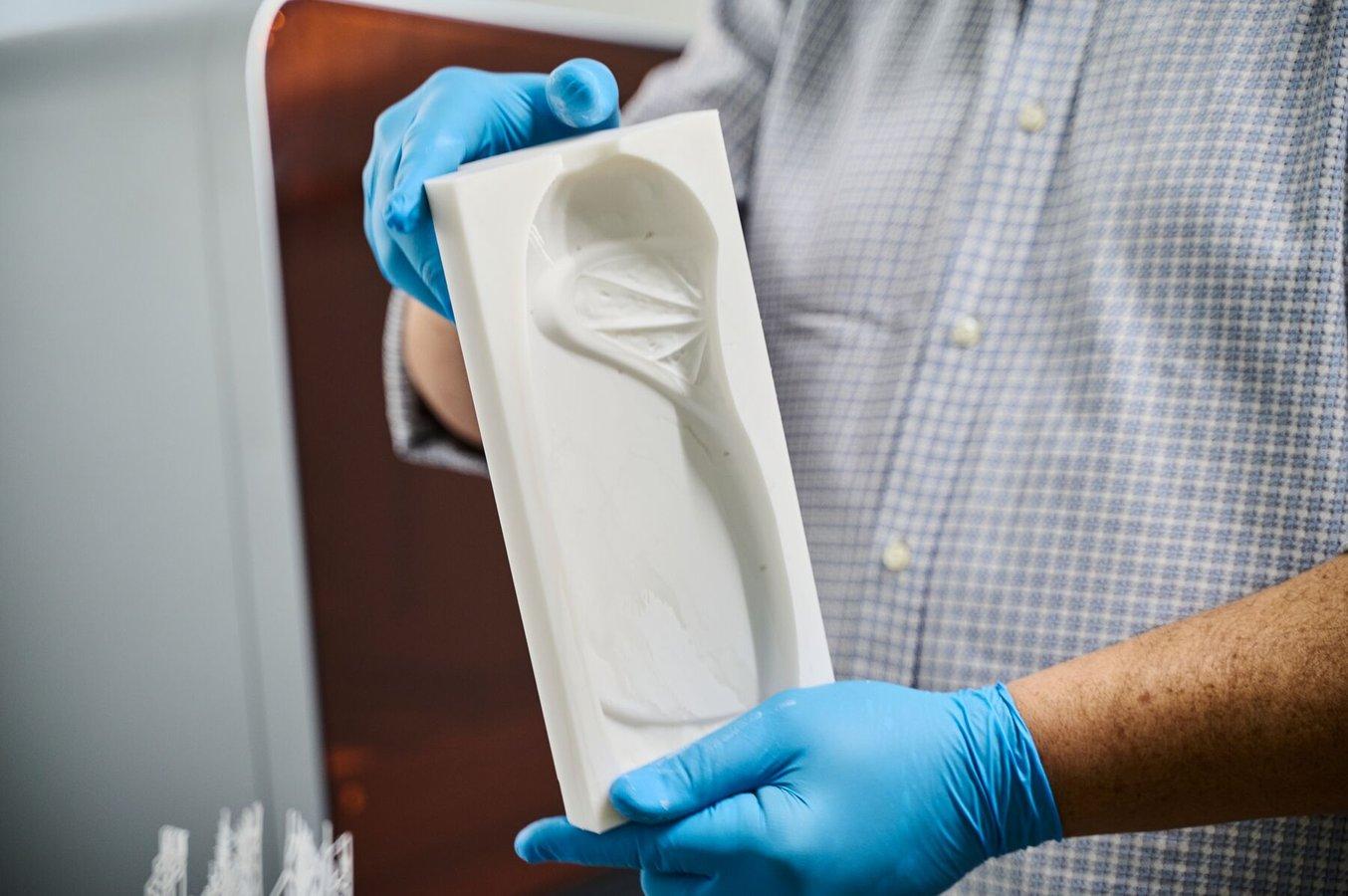
Rigid 10Kレジンを使用することで、Serioplastは表面が滑らかで0.5mmほどの極小の穴など細かなディテールも正確に表現できる成形型の製作に成功。さらに研磨機や手作業によるやすりがけで成形型に表面処理を施し、重要な寸法も仕様内に収めることができた。表面のテクスチャはキャビティのCADモデルに直接反映したもの。
「成形型用にディテールを綿密に調整しました。特にロゴが入っているものやレモンの模様が入っているものなどは、高精細さが求められます。Formlabsのプリンタを使ってRigid 10Kレジンで3Dプリントすると、詳細まで非常に高度に表現でき、成形品のボトルにもしっかりと反映できます」とCademartiri氏は言います。
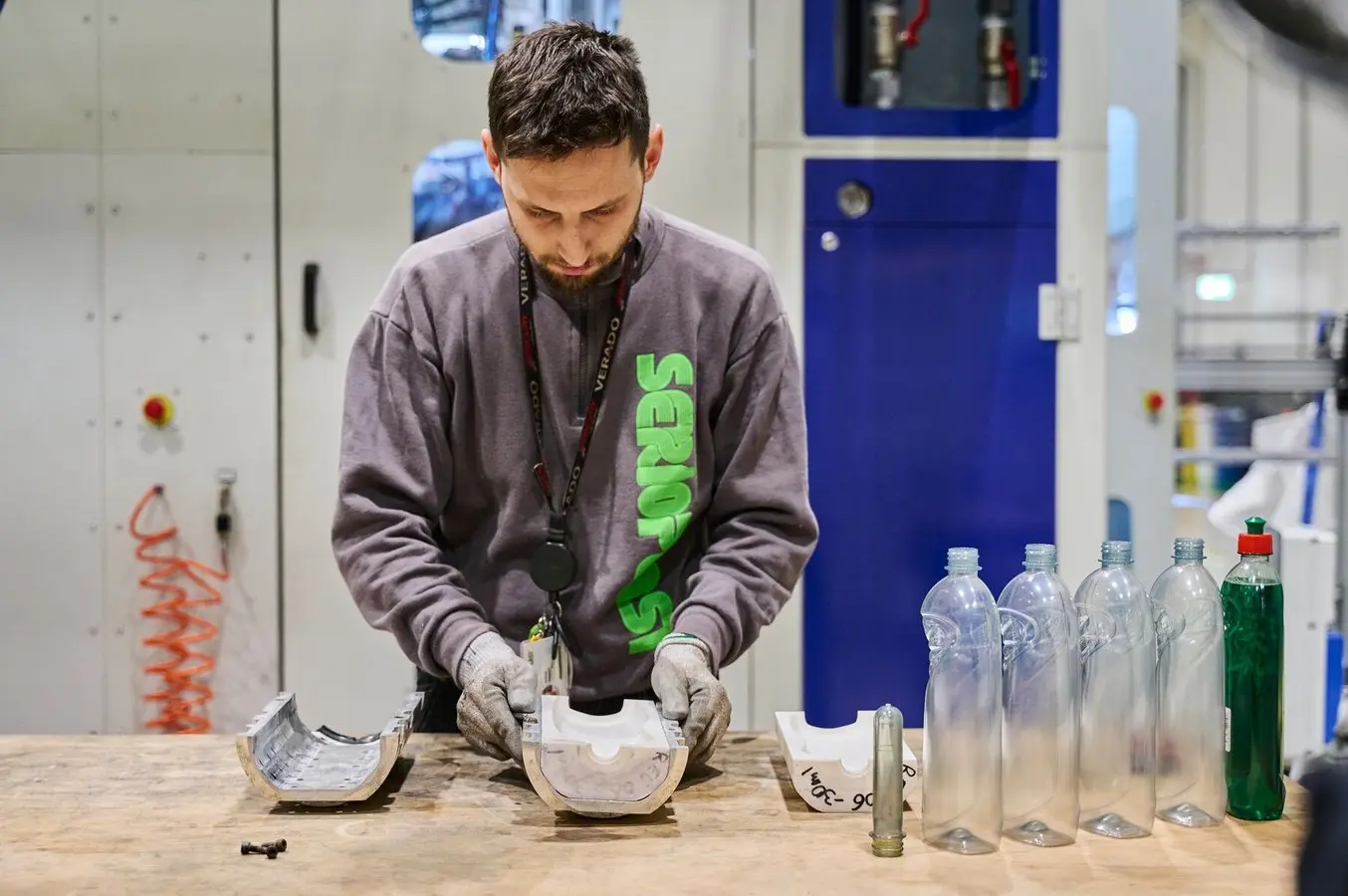
Rigid 10Kレジンで3Dプリントした型を手作業で研磨し、金属フレームに組み入れる。
SLA光造形3Dプリントを活用することで、成形型を僅か2日で製作することができます。成形型を3Dプリント製にすることでパイロットテスト開始までの時間を6週間から2週間に短縮し、量産品質に限りなく近いプリプロダクション品を最終的な量産品と同じ材料や機械を使って成形できます。さらに、3Dプリント製の型があればオペレーターはパイロットテストで複数の設計を同時に検証することができます。
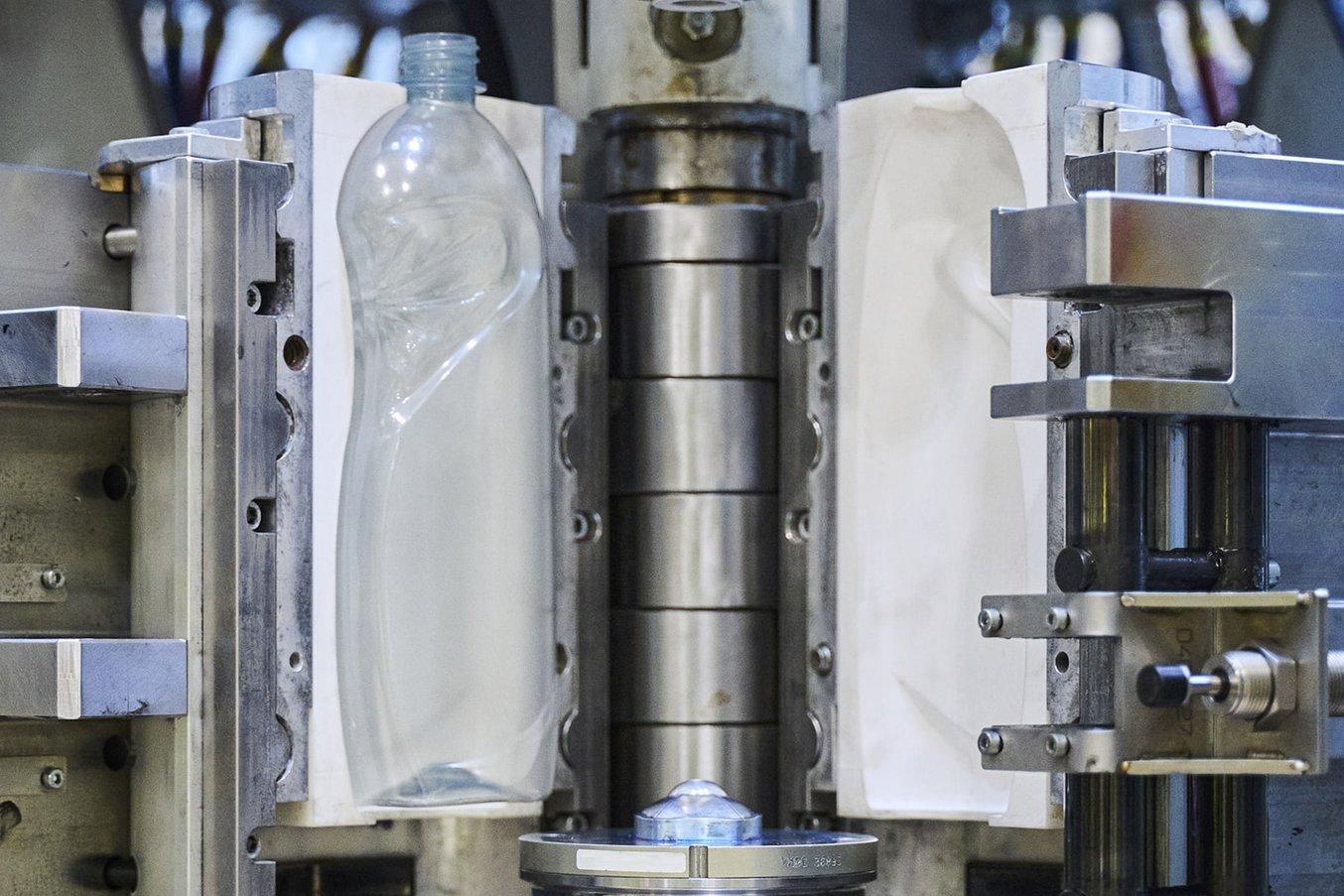
Unilever Slice 750 mLボトル用にRIgid 10Kレジンを使って3Dプリントした成形型。機械のシェルホルダーの上に設置している。標準のパイロット型と同じプロセスウィンドウで、最終的な工程をしっかりとテストすることができた。
「3Dプリント製の型を使う場合でも、ブロー成形機に設置されているシェル内部の標準レイアウトを使用するので型の設計時間を大幅に削減できますし、3Dプリントのスケジュール管理も非常に簡単です」とMigliarelli氏は言います。
200ユニットの生産 | 加工で製作した金型 | 3Dプリント製の成形型 |
---|---|---|
設備 | CNC加工機による内製または外注 | Form 3L Rigid 10Kレジン |
パイロットテストの時間 | 6〜8週間 | 2週間 |
製作コスト | $2,500〜10,000 | $500〜1,000 |
「3Dプリント製の型を使えば、標準的な金型と比較して製作時間を最大70%、コストを最大90%削減できます。これまでは1つのデザインの製作に[お客様を]12週間も待たせなければなりませんでしたが、今では同じ期間で5種類ものデザインを製作できます」
Serioplast Global Services R&Dデザインマネージャー、Flavio Migliarelli氏
従来の方法では、このような広範なテストはほぼ不可能です。デザインの種類ごとに金型を製作しなければならず、規模の経済によるメリットが得られないため金型製作費用を回収することもできません。
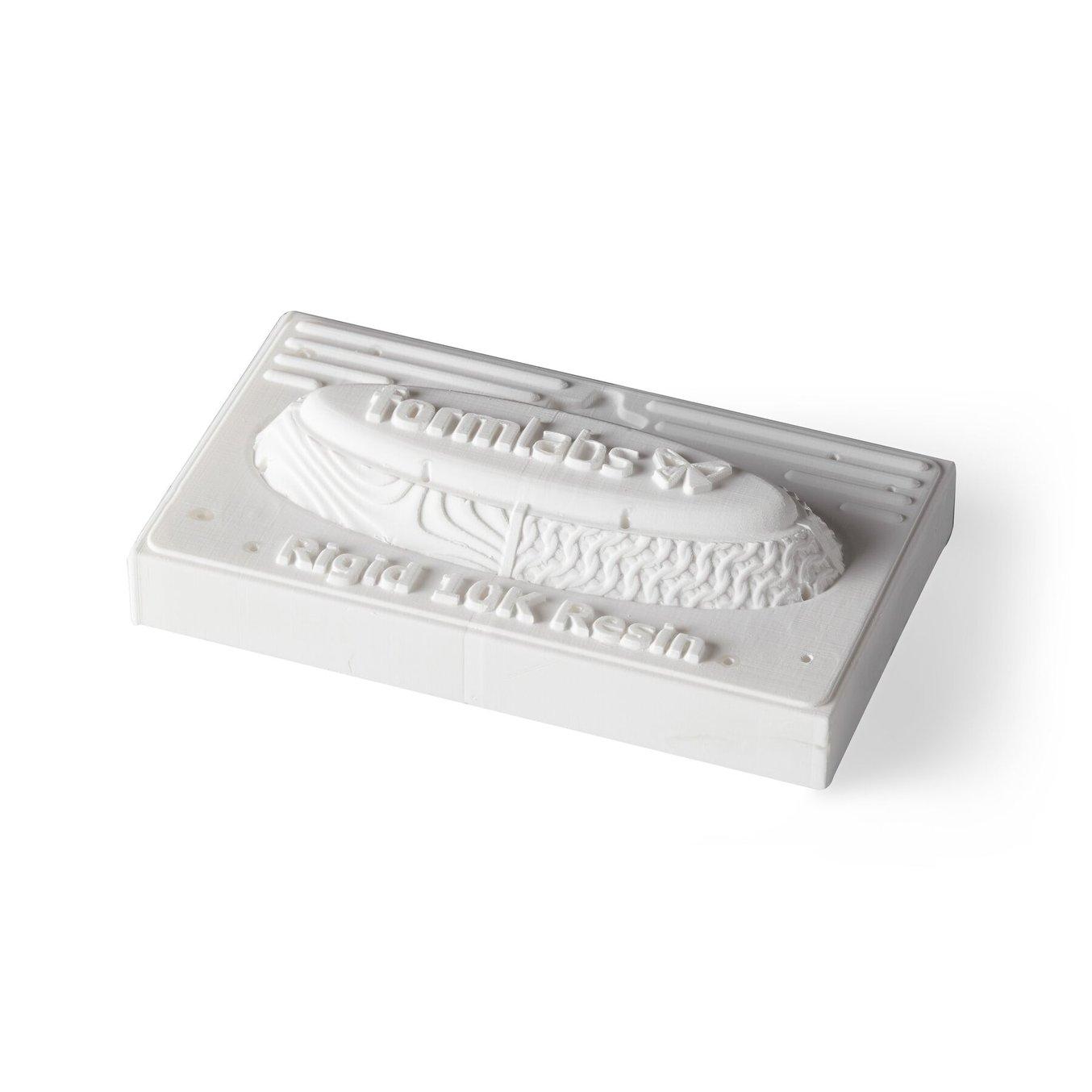
顧客テストから生産ラインへ
3Dプリント製の型は主に、消費者テスト用のサンプル製作で使用しました。手触り、審美性、使い心地の点で実製品を忠実に再現し、消費者の目には実際の製品として映ります。
生産用の金型を作る前に実物のボトルを確認できるので、開発の方向性が正しいか、それとも何か変更が必要かを即座に見極めることができます。
Unilever CAD&プロトタイピングオーナー、Stefano Cademartiri氏
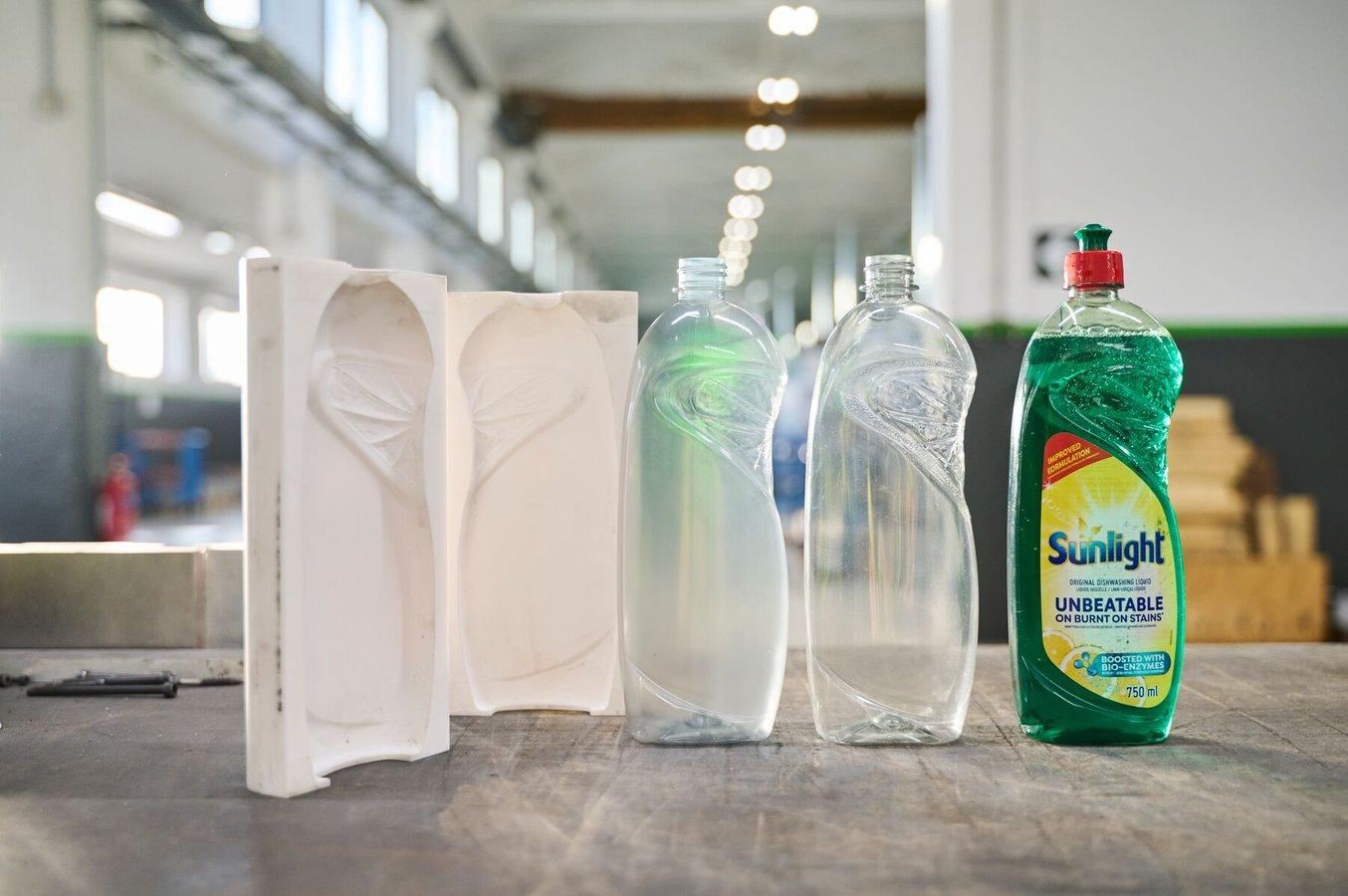
3Dプリント製の型で成形したボトルは、従来の金型で成形した実製品とほとんど変わらない。(写真左から)Rigid 10Kレジンで3Dプリントした二つ割の型、Rigid 10Kレジンで3Dプリントした型で成形したボトル、金型で成形したボトル、顧客テスト用にラベルをつけた試作ボトル。
モジュラー型のもう1つの用途は、SBM工程の検証と、空気を吹き込んで膨らませるPET材料のプリフォームの検証で、プロセスウィンドウや延伸率、実現可能な材料の分配などを確認します。Serioplastは射出成形でプリフォームを社内生産しています。プリフォームの中には特定のボトル用にカスタム生産されているものもありますが、通常はユーザーが変更できない標準品を使用しています。Serioplastでは、この標準的なプリフォームで何をどこまで実現可能なのかを確かめたいと考えていました。この情報を知ることで、使用予定のプリフォームが製作予定のボトルのブロー成形に適しているかどうかを量産移行前に判断することができるためです。
「標準のパイロット型と同じプロセスウィンドウを使用できることがとても助かっています。実際のプロセスウィンドウでテストし、ボトルの状態を確認できるためです。最大30バールもの圧力にも耐えられ、非常に安定感のある優れた材料です。また、100℃という高温でプリフォームを加熱しますが、3Dプリント製の型のキャビティが摩耗することはありません。毎日最大100本から200本ものボトルを生産していますが、さらに時間をかければ最大1,000本まで生産量を伸ばすことができます」とMigliarelli氏は言います。
3Dプリント製の型の3つ目の用途は、生産ラインでの検証を一部、早期実施することでした。3Dプリント製の型を使って成形したボトルは量産ユニットに非常に近いため、3Dプリント製の型を使用して充填ラインの一次検証を行い、ラインの動きやボトル充填機のスターホイールの動作、キャッピング、ロボット式ケースパッカーの動作などを確認できます。生産ラインの早期パイロットテストが可能になることで、工場は必要になりそうな予備部品の予測、大量生産用のラインの準備、市場投入までの時間短縮を実現できます。
より良い製品を、いち早く市場へ
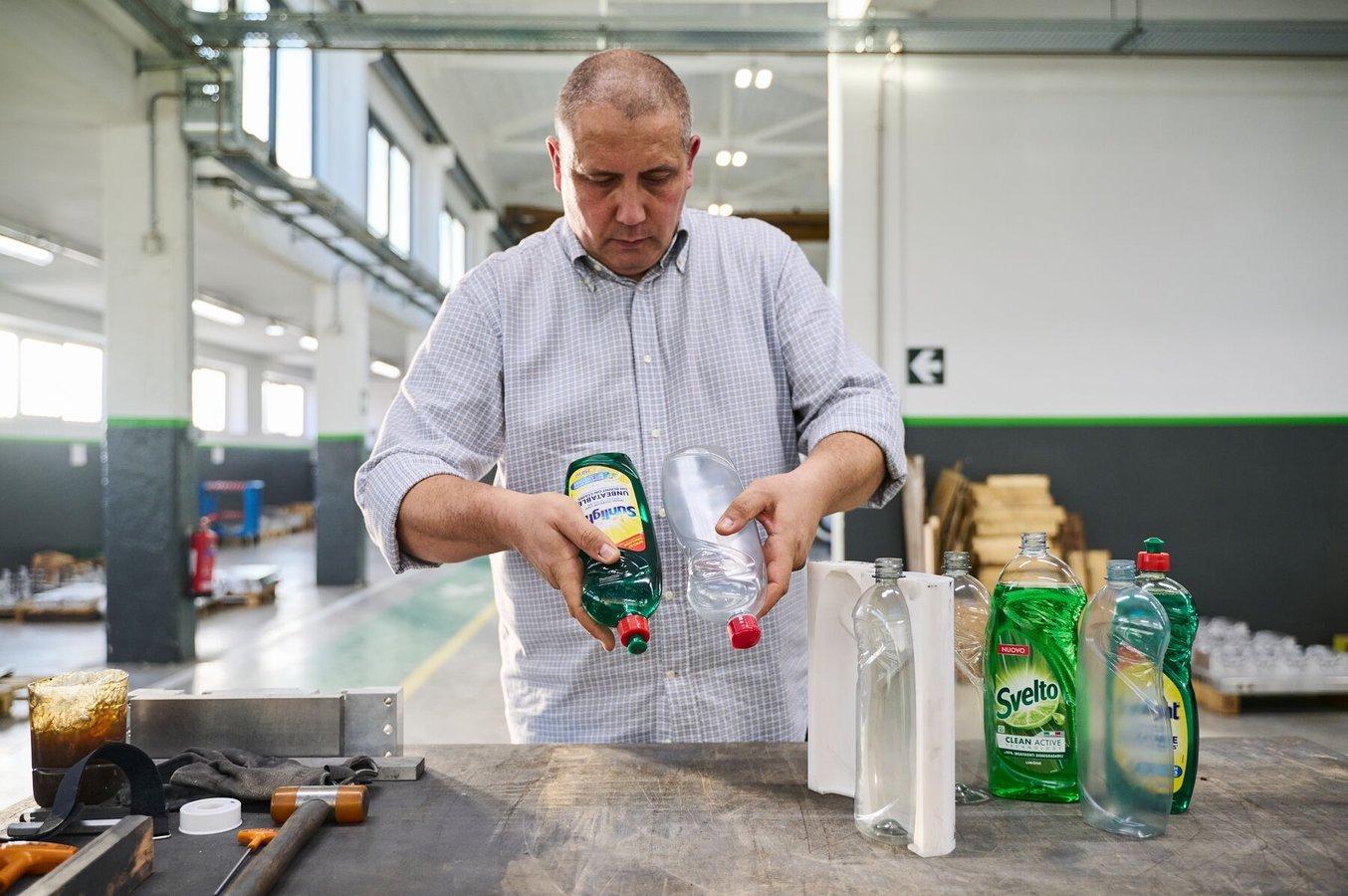
Cademartiri氏とSerioplastは、新しい工程で既に15種類ものボトルの型をテストしている。
UnileverとSerioplastは、FormlabsのSLA光造形3DプリンタとRigid 10Kレジンを活用することで、製作期間の最大70%短縮と製作コストの最大90%削減を実現し、200個ものパイロット品を僅か2週間で製作することに成功しました。
「Formlabsは、素晴らしいパートナーです。単に自社製品を販売するためだけでなく、私たちが求める特性を備えた材料の選定をサポートしてくれました。このパートナーシップのおかげで、生産工程に3Dプリント製の型を取り入れるという可能性を見出すことができました」とCademartiri氏は振り返ります。
新しい工程により、Unileverではより良い製品をより早く市場へ投入しながら、パッケージ開発のリスクやコストを劇的に削減できるようになります。
その影響は、Cademartiri氏はこう語ります。「3Dプリントを導入したことで、夢が現実になるという可能性を感じています。コンピュータの画面で見ていたものが、僅か数週間で本物のボトル、本物のキャップ、本物のラベルをつけた本物の製品となって、手元に具現化されるんです」
ブロー成形やその他エンジニアリング用途、製造用途でのSLA光造形3Dプリンタの導入についてご不明点がある場合は、製品仕様をダウンロードして工程の詳細をご覧いただくか、弊社スペシャリストまでお気軽にお問い合わせください。また、サンプルパーツをリクエストいただくことで、Rigid 10Kレジンで3Dプリントした無償サンプルパーツを直接手に取ってご確認いただけます。