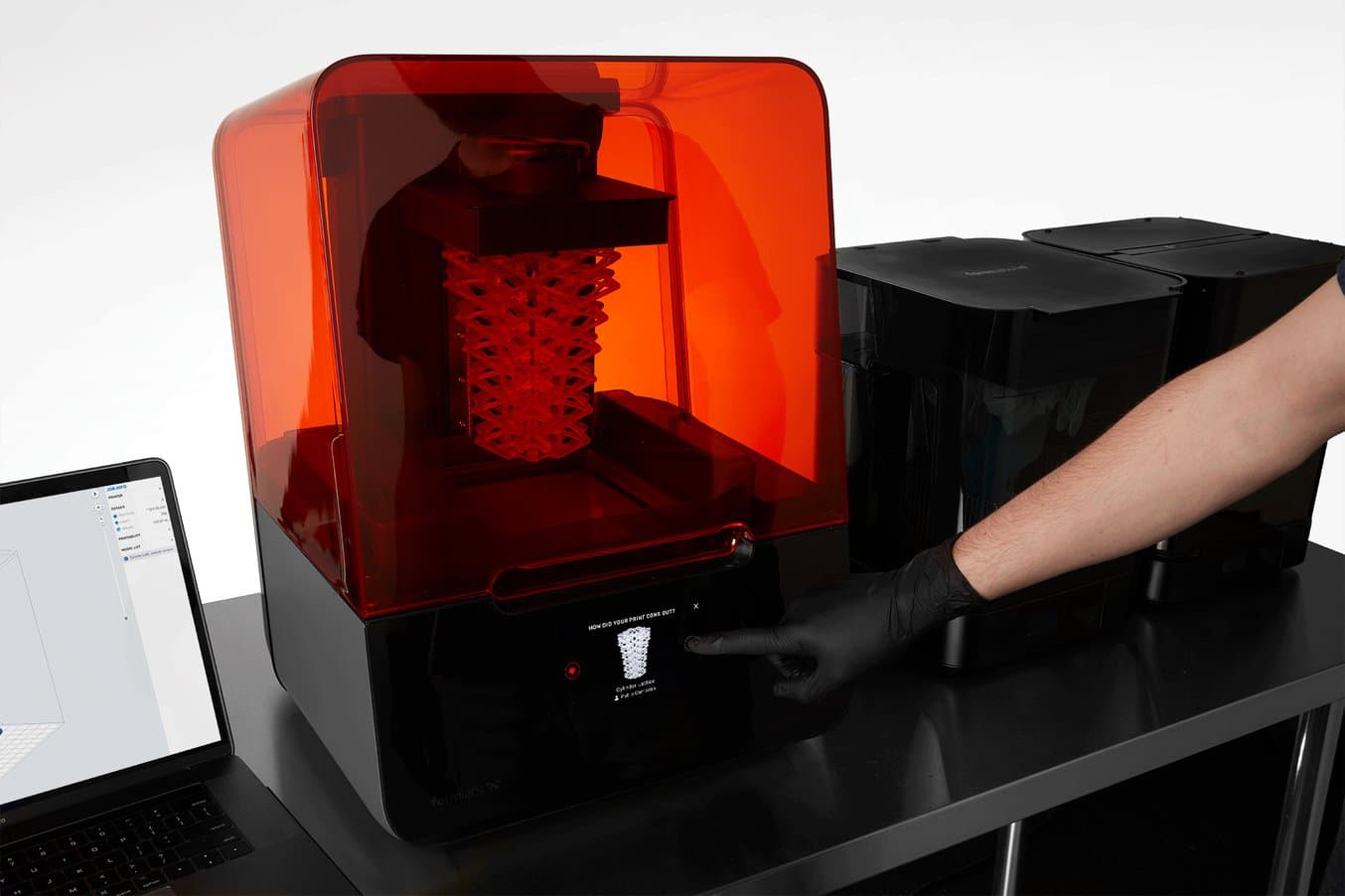
At Formlabs, our line of professional, affordable 3D printers, our software, and our materials are a cohesive ecosystem designed to function optimally together. We believe the best hardware products are those that grow better over time, and we’re committed to continually evolving our hardware through software improvements.
In this post, we’ll break down how we approach software improvements, walk through the many evolutions of the Form 2 3D printer since its release in 2015, and explore what this means for the Form 3 and Form 3L, our latest products that launched this year.
Try PreForm: 3D Print Preparation Software
Hardware Products That Improve Over Time
Perhaps the most familiar examples of hardware that evolves through software are the smartphones that most of us carry in our pockets and purses every day. The Google Pixel makes improvements to their camera over time through software, adding new features like Night Sight, Time Lapse, and Playground, in addition to general improvements to their operating system. Apple’s iOS updates are their own news category at this point.
As the ecosystem of “smart” objects expands into more areas of life, so does the potential for the physical world around us to evolve through software updates. Tesla drivers “feel like they got a new car” with over-the-air software updates that add updated audio and visual prompts, new modes like Enhanced Autopilot, Ludicrous Acceleration Mode, and Track Mode, and improvements to user experience, for example, a software update that responded to reports of issues with door handles in cold weather. Clearmotion replaces a car's shock absorbers with fast-acting software and actuators that evolve based on road input data to predict what’s coming and react more quickly.
Continuous Software Improvement at Formlabs
Since the Form 2 launch in September 2015, we’ve released over 40 versions of our free 3D print preparation software, PreForm. Our software ecosystem also includes the web-based Dashboard, which allows users to remotely track and manage their printers and materials, and the firmware (and touchscreen interface) included with each printer.
Our commitment to continually improving the software behind all of our products is, at its core, a commitment to improving product performance and extending product lifetime and usage. Users shouldn’t need to replace their hardware to expand its range of applications (within the realm of possibility) and to experience updates and improvements. Our products should be able to adapt to a rapidly changing market and respond to emerging patterns and trends, without quickly facing obsolescence and prematurely ending up in a landfill.
We decide which updates to move forward with based on three main areas:
- Performance metrics from printers in the field.
- Direct user requests, one source of which is the Formlabs Forum. Some examples of this include object mirroring (PreForm 3.0), Spacemouse support (PreForm 2.13), Z compression compensation (2.20.0), and intelligent pre-heating (firmware 1.14.21).
- Updates we think will strategically move Formlabs forward, for example, making our printers useful for new industries and customers. For example, we added a login to Dashboard within PreForm to connect a username to print jobs in multi-user environments.
The Form 2: From 2015 to 2019
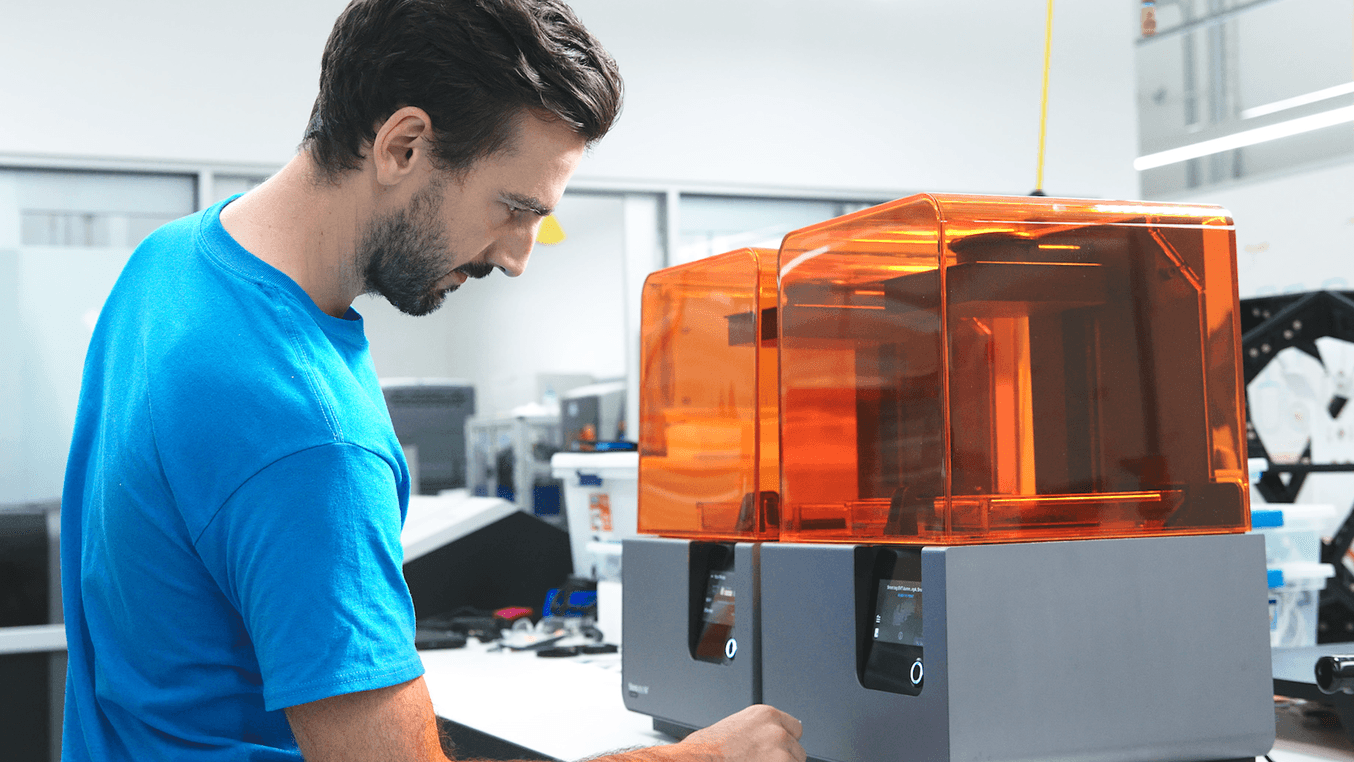
Formlabs was the first to bring high-resolution stereolithography 3D printing to the desktop in 2013. The Form 2, the second major iteration of our printer, was released in 2015, and has since become the industry-leading desktop SLA 3D printer, with over 40 million parts printed in the field by engineers, designers, manufacturers, dentists, jewelers, and more—all the while expanding its functionality and applications through regular software updates.
Read on for specific examples of how we’ve improved hardware performance across the following areas on the Form 2 through software updates:
- Materials and print settings
- Faster printing
- Support structures (structures that support the part as it prints)
- Rafts (the structures that assist in build platform adherence)
- User interface and design
- New ways to work (for example, starting prints from the cloud)
Materials: Success Is in the Settings
Each new resin we release expands the capabilities of our machines, and, more importantly, what’s possible with desktop 3D printing. Our resins are developed in house to work seamlessly with our printers, and materials development is a collaborative process between our materials science team and the print process team that develops unique print settings:
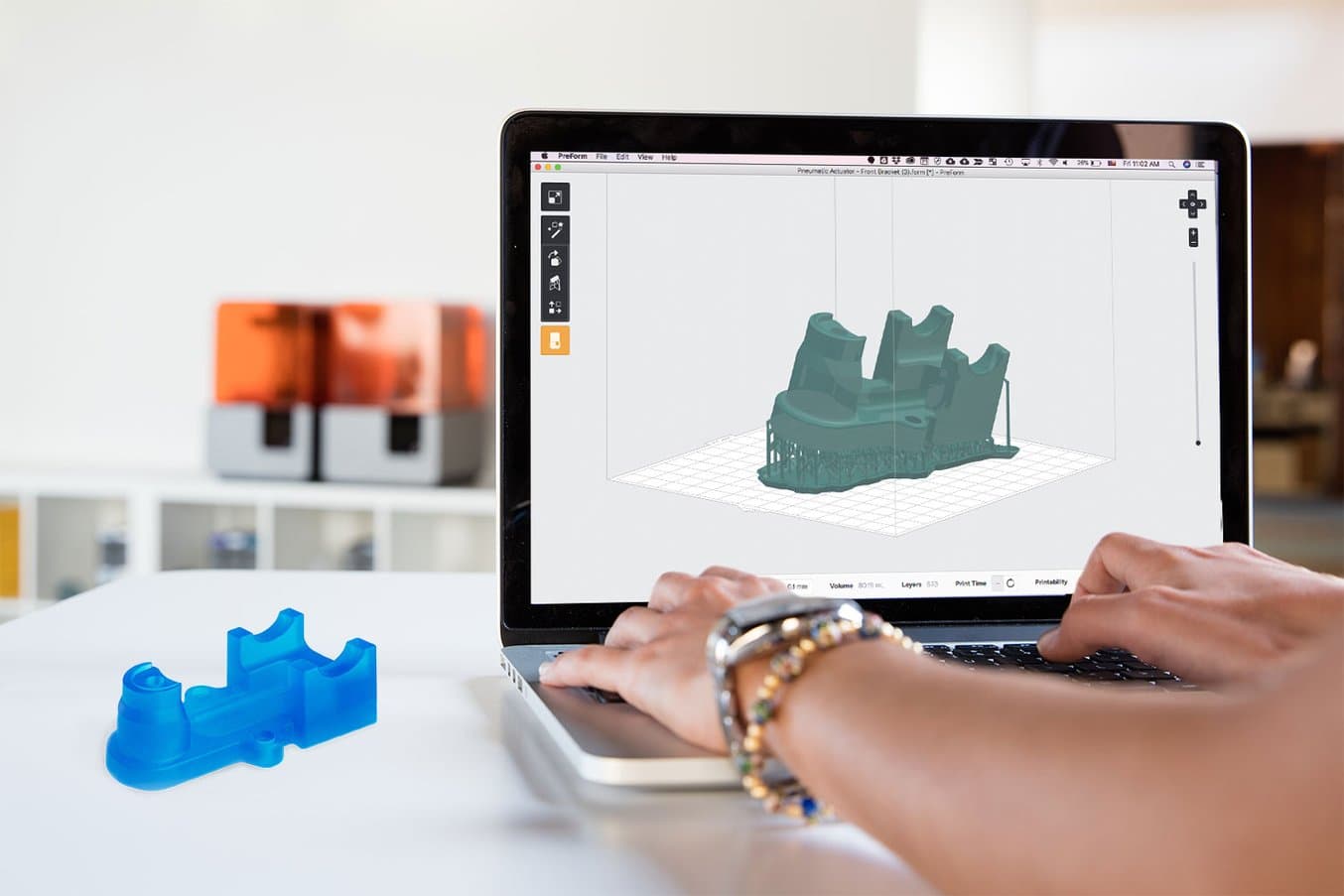
“A different resin might require algorithmic changes in the software, or motor movements in the printer itself; That all needs to be customized for each resin. The process team optimizes the printer for the resins we make and we do the same. You get a combo that’s pretty superior to what you could get with an off-the-shelf resin, or another company using our material on their printer.”
—Alex McCarthy, Materials Scientist, Formlabs
For Ceramic Resin, an experimental material that can be fired in a kiln to create a fully ceramic piece, the team developed special filleted supports to support a highly filled resin, as well as accommodating for shrinkage that occurs during firing.
For two of our advanced engineering materials, Rigid Resin and Grey Pro Resin, we combined software settings development with the development of Resin Tank LT (PreForm 2.14.1). For softer materials like Elastic Resin (PreForm 2.19.2), we tweaked the force and speed of the peel process to enable printing with a more viscous material.
Faster Printing for High Throughput and Fast Iteration
In production settings, gains in throughput can be crucial to staying competitive. When making speed improvements for our 3D printers, we prioritize supporting faster iteration while striking a balance with quality and accuracy.
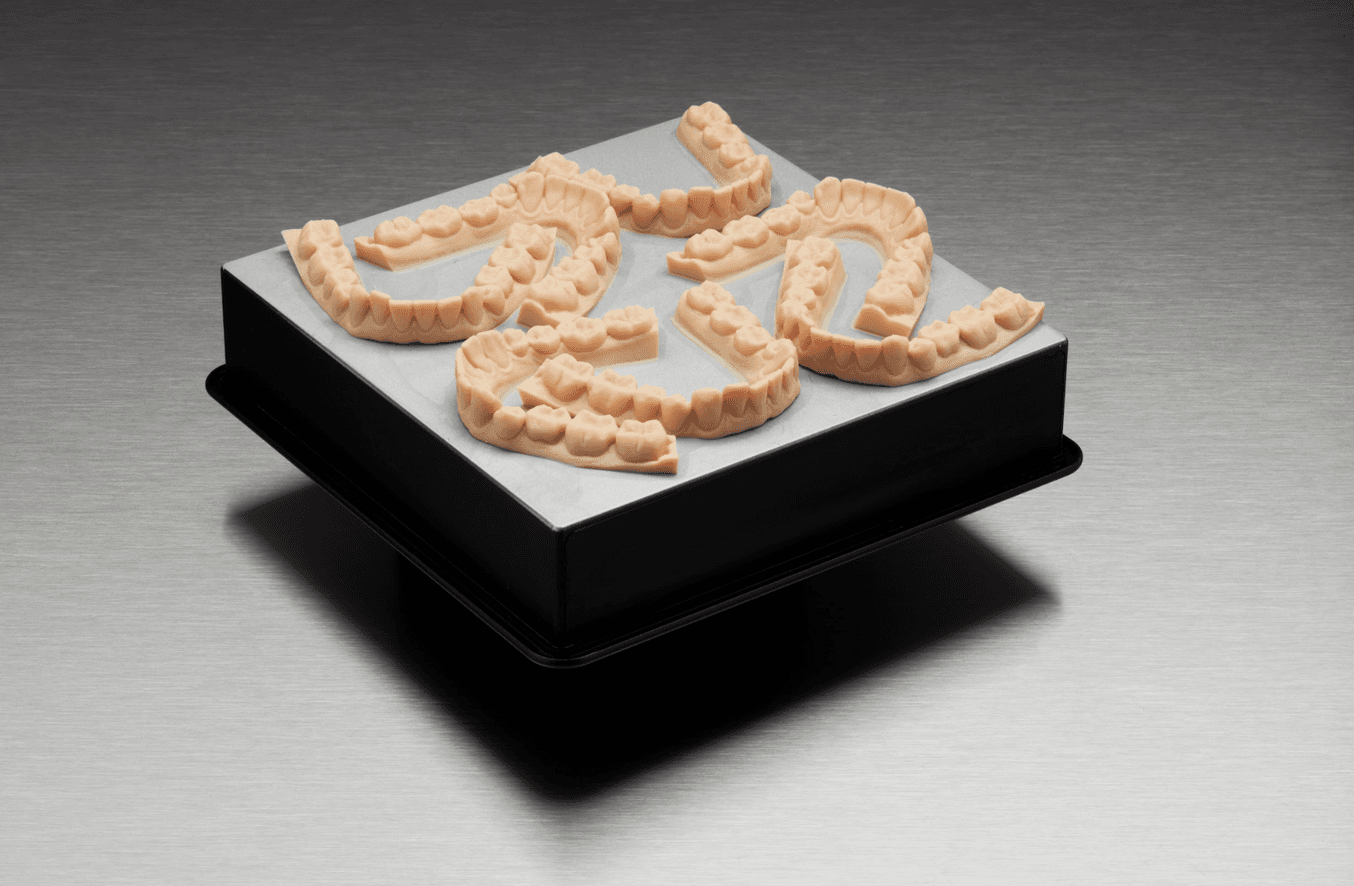
In PreForm 2.20.0, we introduced a 140 micron print setting for Dental Model Resin, enabling faster printing of orthodontic models for clear aligner and retainer production, reducing print time for one model in 37 minutes compared to 75 minutes at 100 microns. In PreForm 3.0.0, Draft Resin, a material that prints at 300 microns to save time in rapid prototyping, was introduced. In PreForm 3.0.3, it became possible to print Grey Resin at 160 microns.
In future versions of PreForm for the Form 2 and the Form 3, we’ll be introducing a new mode called Adaptive Layer Thickness, which selectively varies layer thickness throughout printing to balance high detail and high speed. This feature is now available in beta.
Support Structures: Consistent Print Success, Less Material Usage
Support structures are critical to keep the part in place as it prints, and they influence a number of aspects of the print process. Reliable support structures lead to consistent print success. If the supports are easier to remove, post-processing time is reduced (smaller touchpoints, increased trussing, and other factors can simplify removal). More efficient support structures can help save print material.
Over the course of the last several years, we’ve worked to develop lighter, stronger, and more efficient supports:
- Smaller touchpoints, which leave behind less support material for easier post-processing while still ensuring successful printing.
- More and better-placed cross-braces or trussing to ensure the supports are stiff for printing while using less material and making them easier to remove from the part.
- Smaller pillars to help save print material.
- Improved algorithms to specifically address small features, local minima, etc.
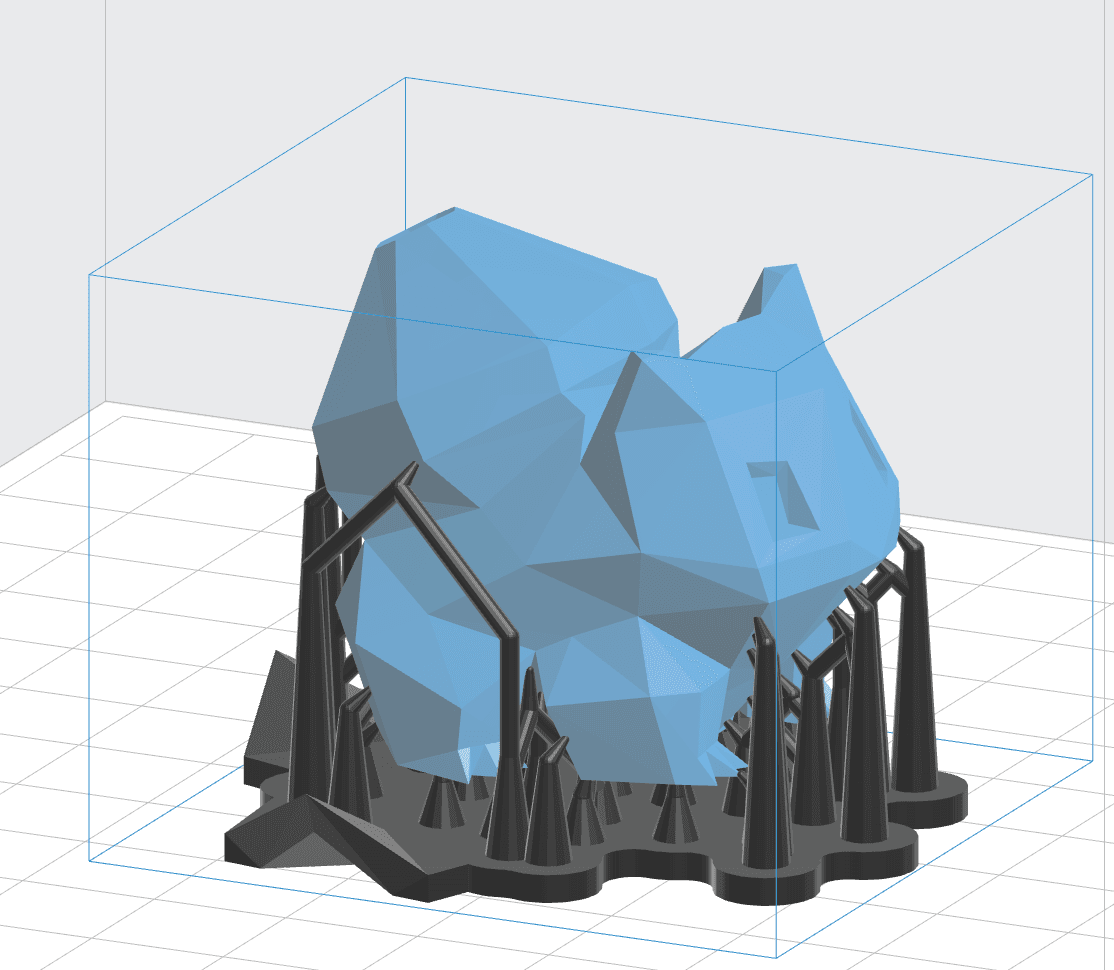
PreForm 2.0.0: The first version of PreForm for the Form 2.
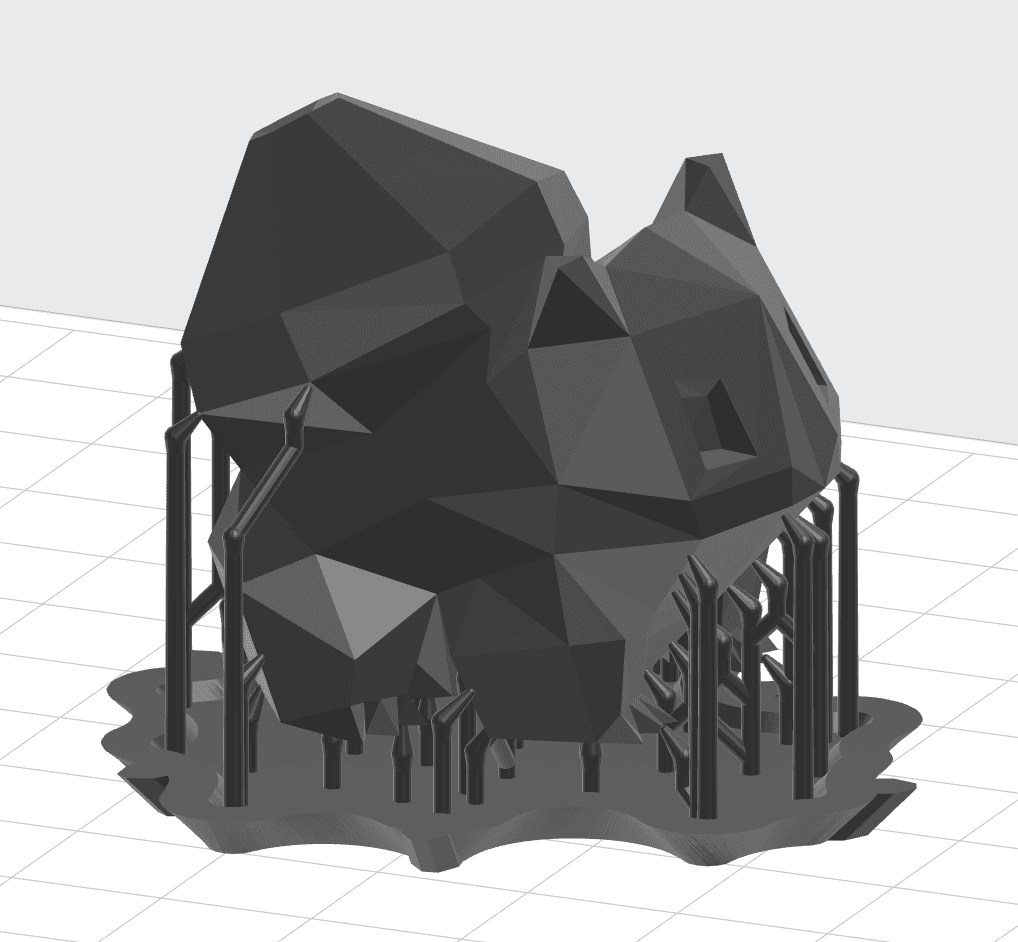
PreForm 2.10.0: Smaller pillars, chamfered raft for easier removal from the build platform.
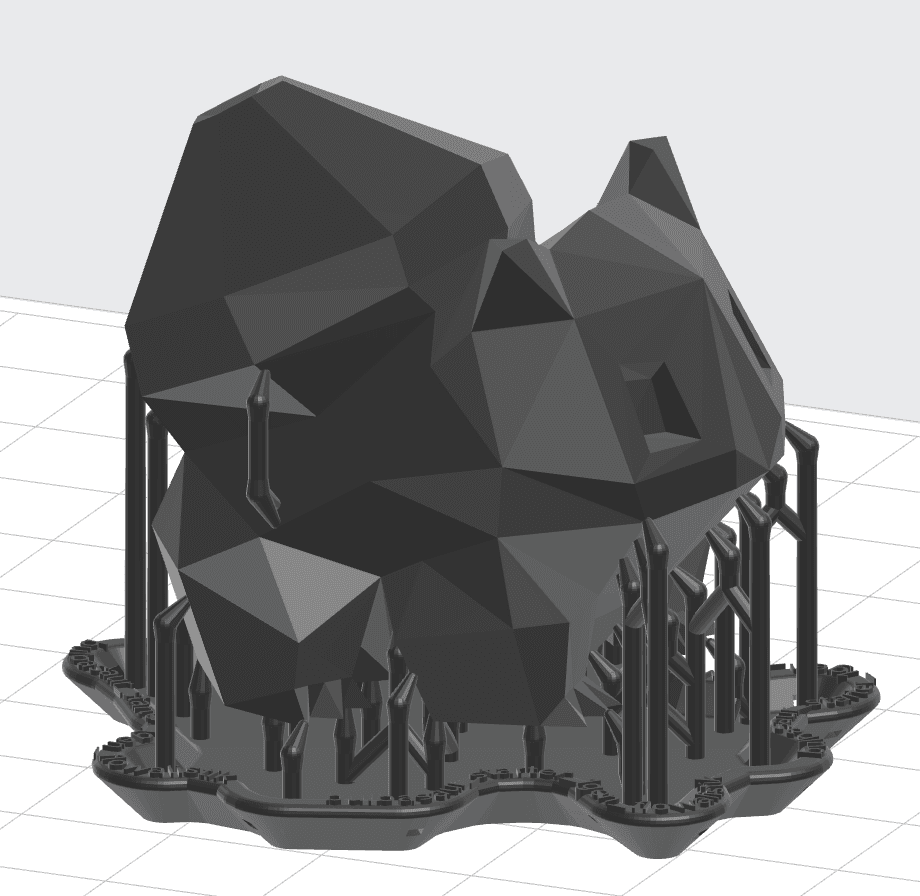
PreForm 2.15.0: Raft labels, filleted raft for easier handling.
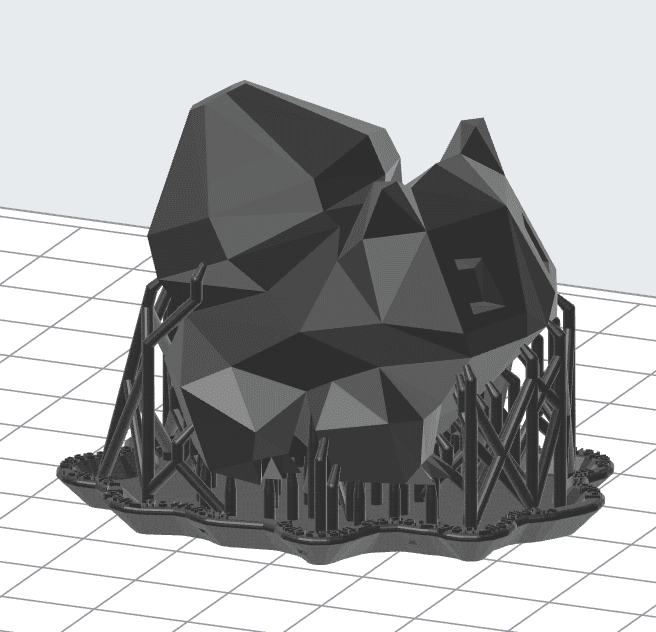
PreForm 3.0.0: Additional cross-trussing, tipped pillars for additional stiffness.
“Low Poly Bulbasaur” model courtesy of Thingiverse user FLOWALISTIK.
New Options for Support Rafts
The raft portion of the support structure generated by PreForm forms a base that improves adherence to the build platform. For some parts and geometries, it’s possible to save print time and material by changing the shape of the raft or removing it altogether.
PreForm 2.14.0 included a number of improvements to the raft, which we found through extensive testing ensure better adherence. This version also added the option to print the name of the model around the edge of the base, useful for identification when printing large numbers of similar looking parts.
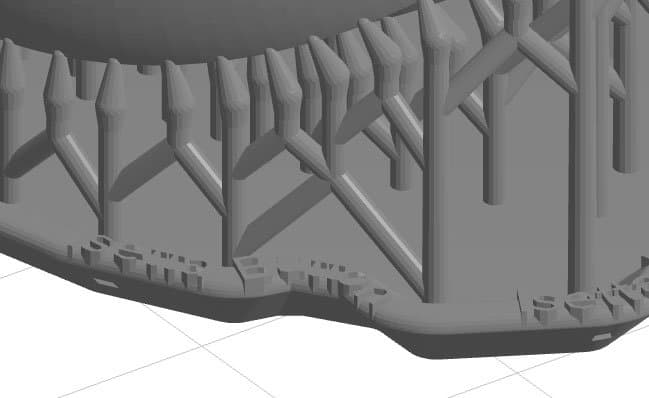
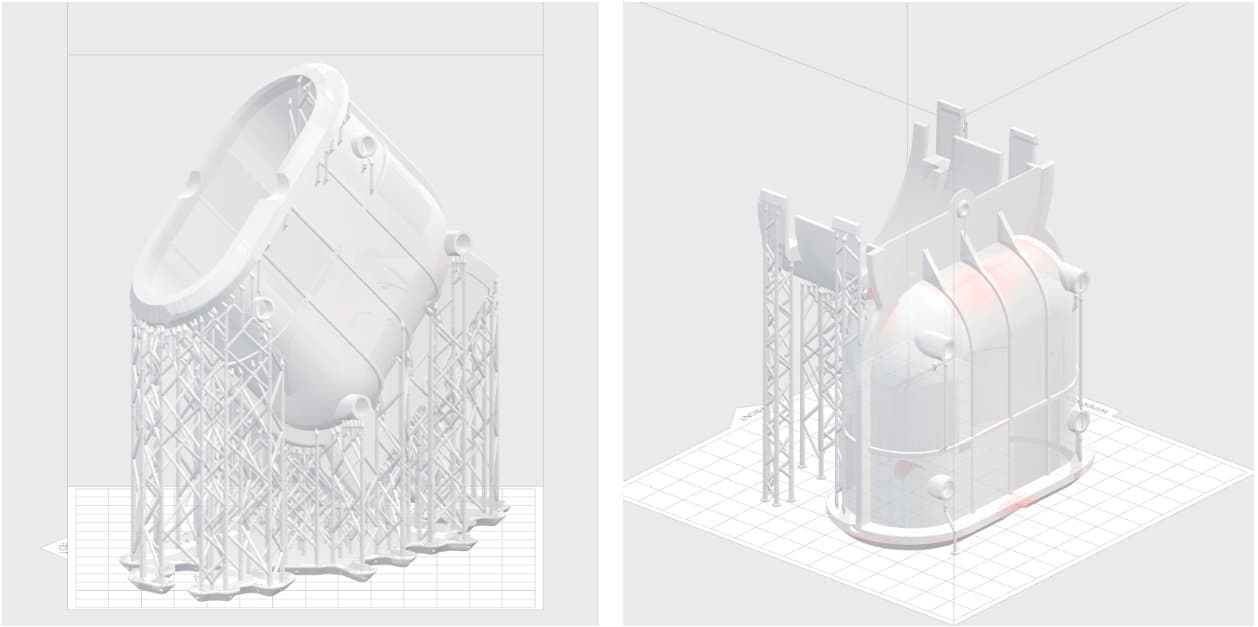
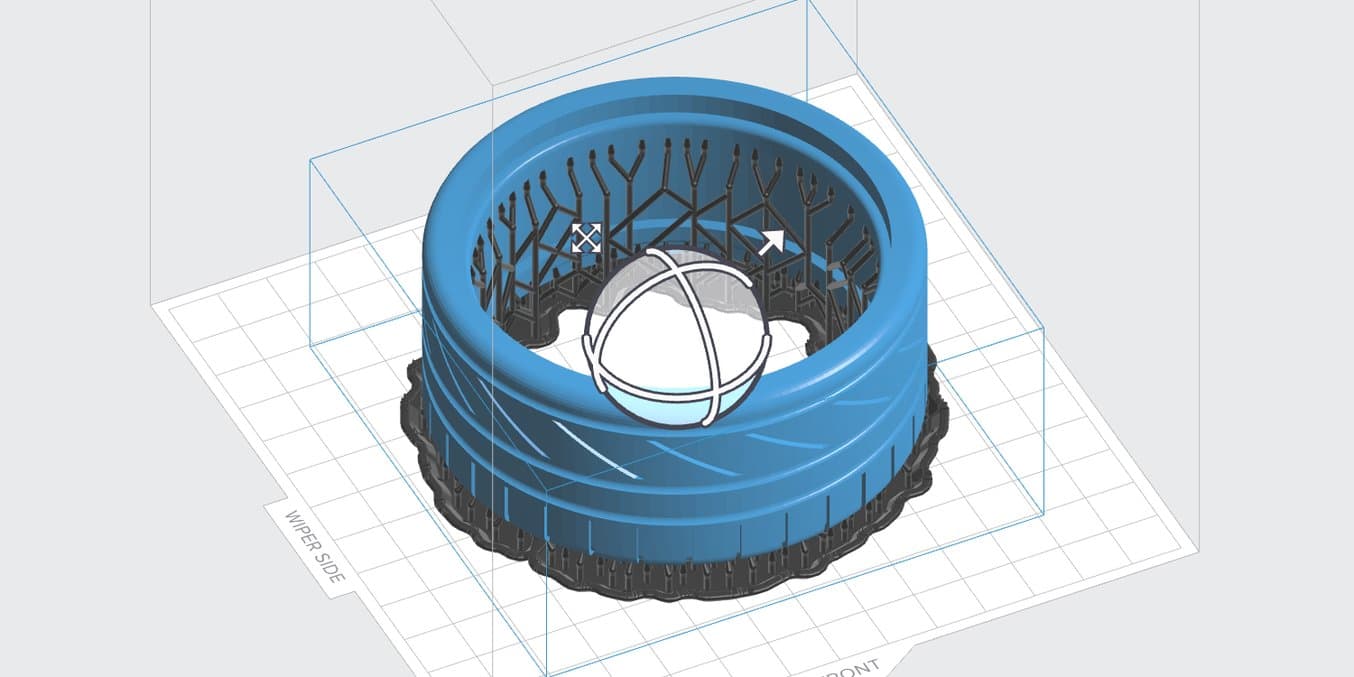
A Simple Interface for Powerful, Evolving Functionality
Our products are very complex—hardware, software, and a wide array of materials need to operate in harmony. Making that process easy and intuitive for the end user starts with a friendly, simple interface.
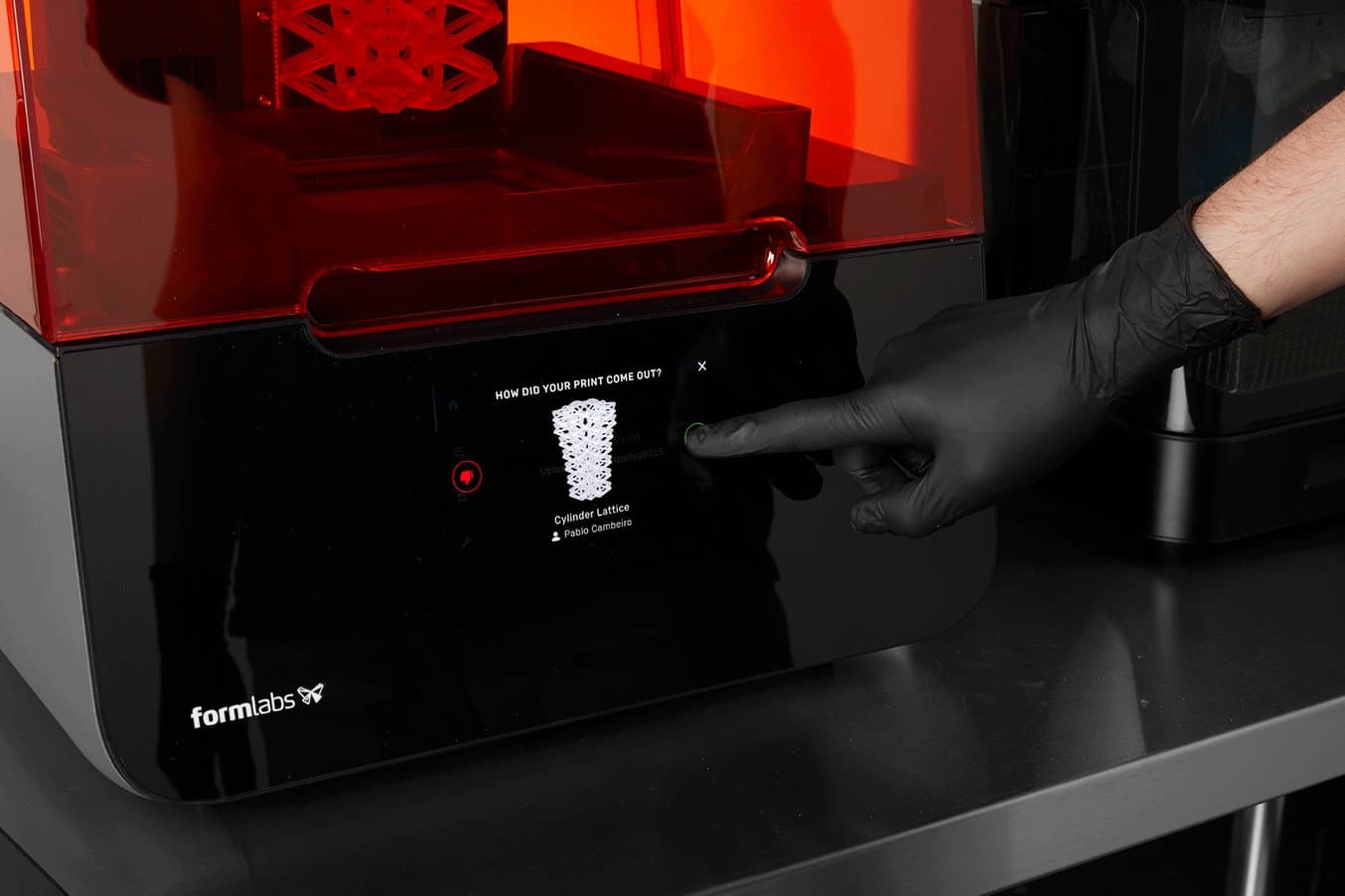
Some of the people using our printers have never touched CAD software before. Others are among the best engineers on earth and require fine-tuned control over their machinery. The trade-off between these two use cases is one of the primary challenges we face: we aim to design an interface anyone can understand and start a print from day one, without limiting the granular control required by advanced users.
The Form 1 started with a single button for printing. As our ecosystem grew and expanded, we found ourselves adding more and more features (like groups and notifications) to accommodate new workflows, and we introduced a new touchscreen for the Form 2.
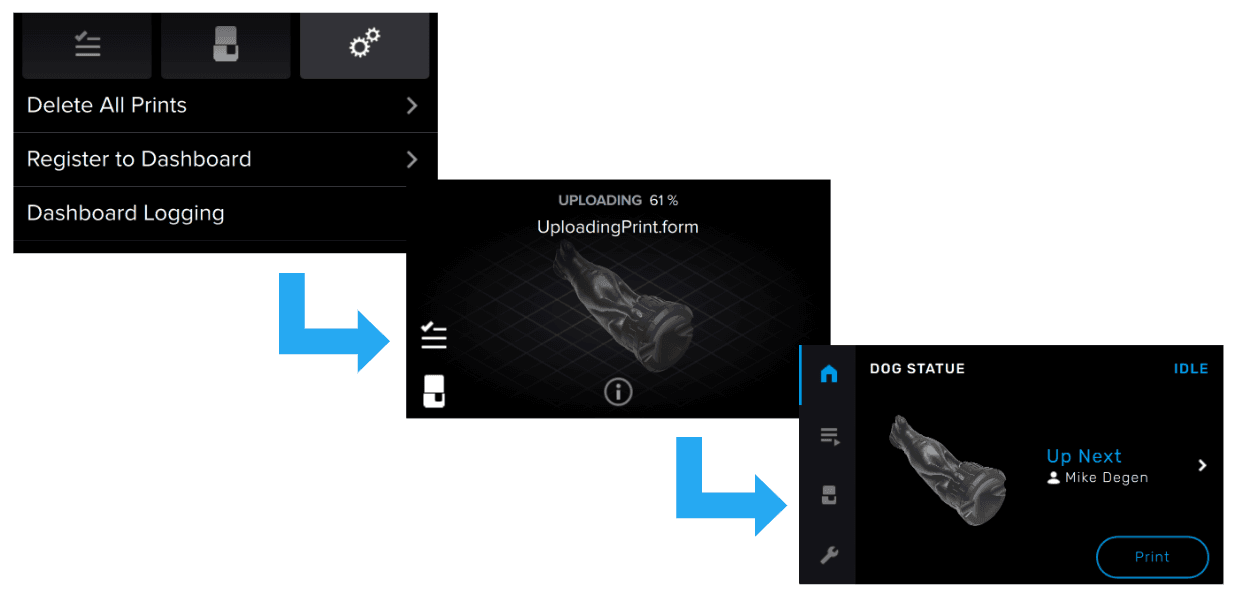
As capabilities increase, we’ll continue updating our interface to accommodate the latest innovative workflows, while ensuring that our 3D printers are accessible to engineers, designers, manufacturers, and creators at every skill level.
Changing the Ways People Work
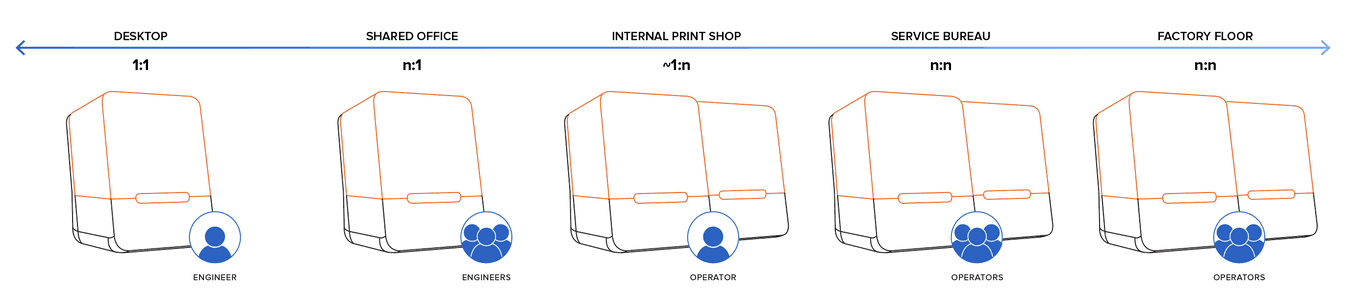
Software updates can play in role in changing the way work is done and opening up new modes of collaboration for businesses of all shapes and sizes. Over time, we’ve added numerous features to our software that allow collaboration across teams, printers, and locations.
- We added an optional login to PreForm so a username is tracked with each print job. For shared printers, this means notifications will only be sent for your own jobs, instead of for any colleague using the same printer.
- The Groups and Timeline features in the Dashboard help facilitate management of multiple people and printers in a single company.
- Remote Print allows users to start prints from anywhere via the cloud.
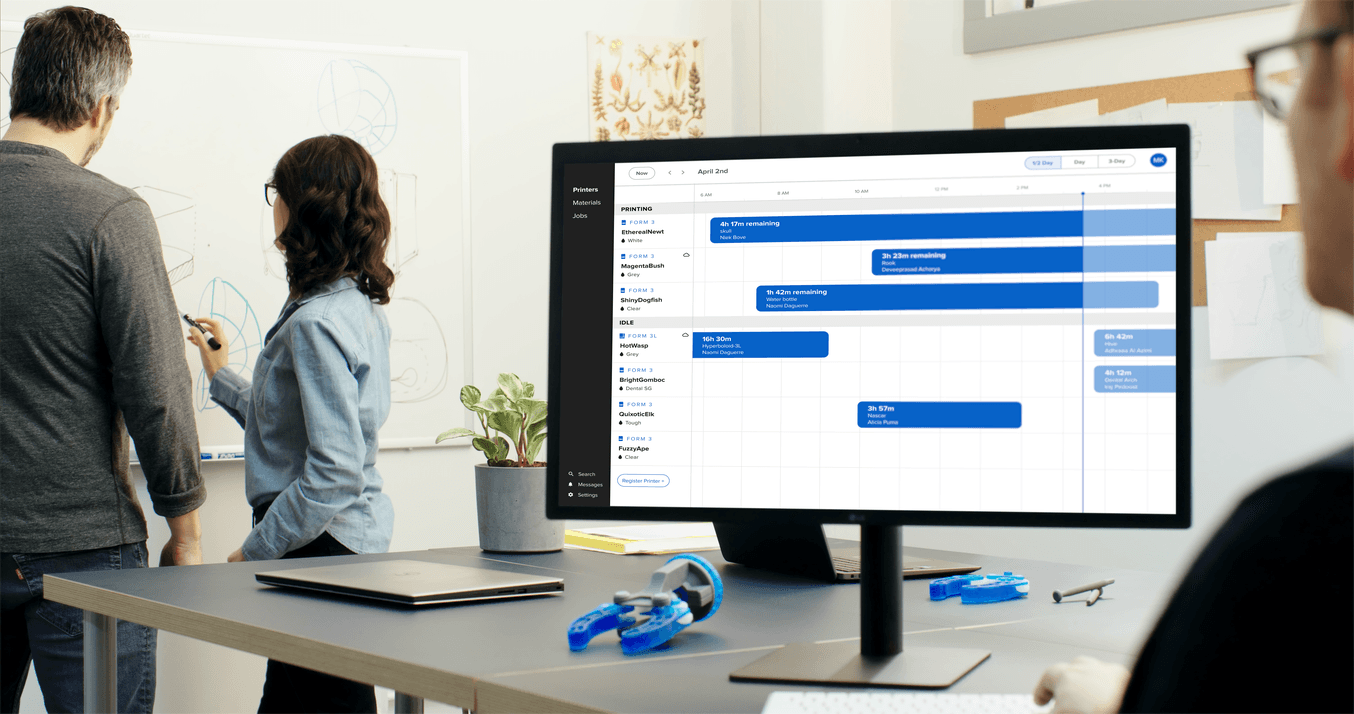
Next-Generation Hardware, New Possibilities
Over the course of its life so far, the Form 2 has evolved through print quality and speed improvements, expanded materials and applications, and entirely new workflows, all through incremental updates to software. We’ll continue updating the Form 2’s software whenever possible.
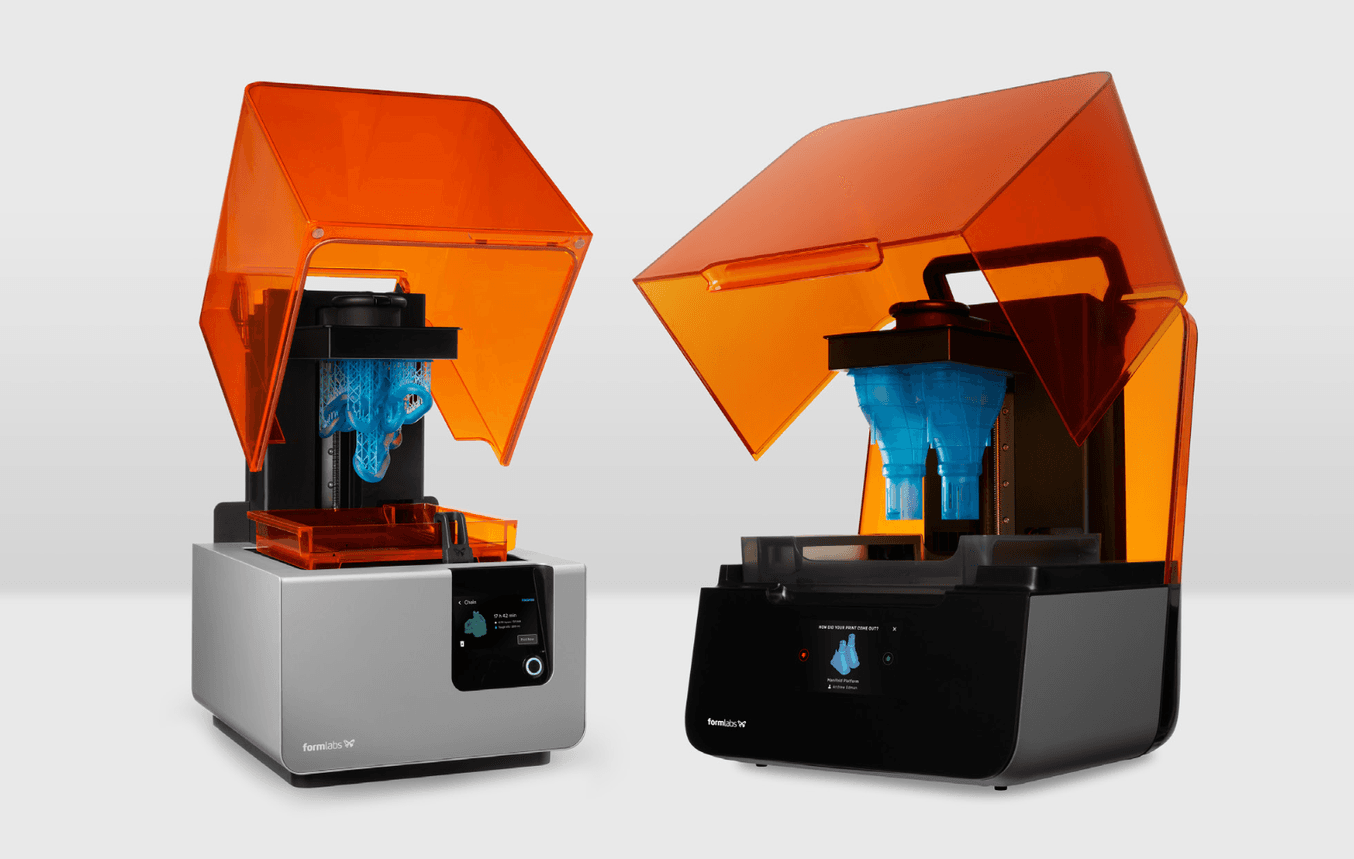
With the release of the new Form 3, we’ve updated our hardware to open up even more possibilities. The significantly lower peel forces of Low Force Stereolithography open up new possibilities in the realms of print quality, materials development, and support removal. More sensors across the printer enable more control and smarter alerts, even remotely.