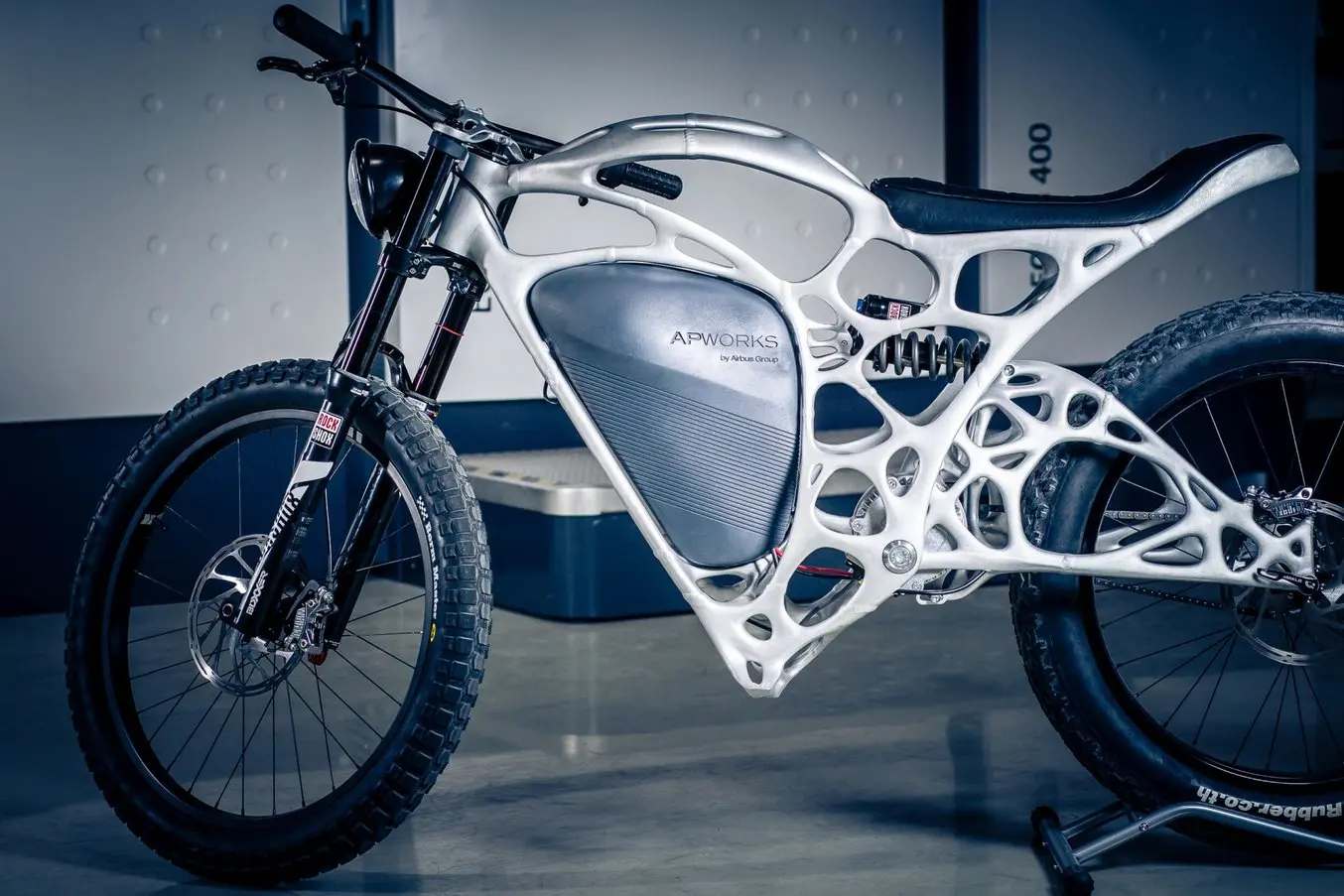
Generative design is the next frontier in CAD design for engineers working in virtually all manufacturing industries. It harnesses the power of artificial intelligence (AI) to develop new high-performance design iterations that help solve complex challenges, reduce component weights and manufacturing costs, scale customization, and optimize performance.
While highly latticed designs with extraordinarily intricate features might seem exotic, generative design has an increasing number of practical applications today.
In this comprehensive guide, find out how generative design works, learn about its benefits, applications, and the important role 3D printing plays in bringing its incredible design to life. Through real-life case studies and practical tips, see how you can get started now.
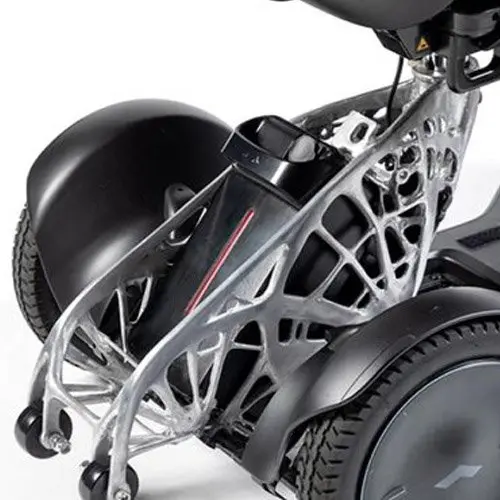
An Introduction to Generative Design for Producing Lightweight Parts With 3D Printing
In this webinar, Formlabs Product Marketing Lead Jennifer Milne will provide a simple overview explaining what generative design is, framed in a way that is applicable to mechanical part design, including a step-by-step tutorial of Fusion 360 where she’ll produce a lightweight bracket.
What Is Generative Design?
Generative Design Defined
Generative design is an iterative design exploration process that uses an AI-driven software program to generate a range of design solutions that meet a set of constraints. Unlike traditional design, where the process begins with a model based on an engineer’s knowledge, generative design begins with design parameters and uses AI to generate the model.
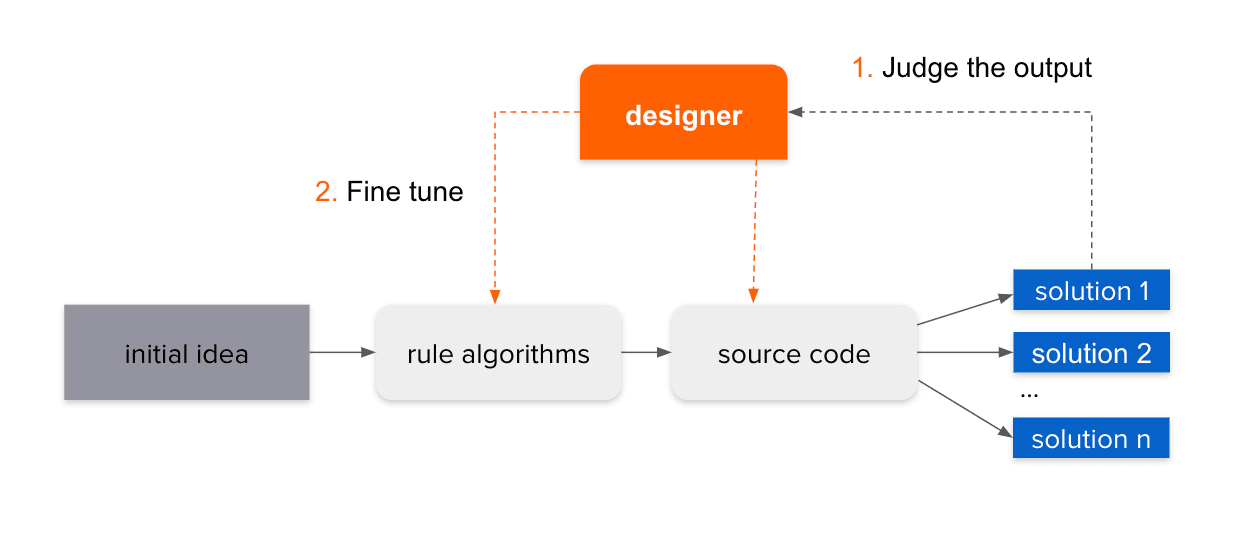
Generative Design Process. Adapted from “Generative Design” by H Bohnacker, J Laub, B Groß, and C Lazzeroni, 2009, Princeton Architectural Press.
By modifying the design parameters in an increasingly refined feedback loop, engineers can find highly optimized and customized design solutions to a wide range of engineering challenges, such as making product components lighter, stronger, and more cost-effective.
The Difference Between Topology Optimization and Generative Design
Generative design and topology optimization have become buzzwords in the CAD design space, but it’s a common misconception that they’re synonymous.
Topology optimization isn’t new. It has been around for at least 20 years and has been widely available in common CAD software tools. The start of its process requires a human engineer to create a CAD model, applying loads and constraints with project parameters in mind. The software then generates a single optimized mesh-model concept ready for an engineer’s evaluation. In other words, topology optimization requires a human-designed model from the outset to function, limiting the process, its outcomes, and its scale.
In a way, topology optimization serves as the foundation for generative design. Generative design takes the process a step further and eliminates the need for the initial human-designed model, taking on the role of the designer based on the predefined set of constraints.
The Changing Role of the Engineer in Generative Design
The role of the engineer has evolved alongside technology. As design has come to rely more heavily on computer software, understanding how to manipulate digital tools to solve design challenges has become a central requirement for engineers working in all industries. Before generative design, engineers would conceptualize and test iterations using hands-on sketching and modeling.
Now, using generative design software, engineers specify high-level performance requirements and general design frameworks and then relegate the details to the software. The process of defining these parameters can be particularly complex when characterizing novel materials or modeling hard-to-define problems and solution spaces.
In a fundamental shift from traditional design processes, engineers will no longer need to create design solutions themselves. Instead, through generative design, they articulate and refine the environment in which design solutions can succeed. By letting computers do the “thinking,” generative design lets engineers focus on innovation and high-level problem-solving.
Applications of Generative Design
Generative design applications exist across many industries—from aerospace and architecture to manufacturing and consumer goods. Engineers who use generative design are often trying to solve complex engineering challenges. Such challenges include reducing component weights and manufacturing costs, scaling component customization, and optimizing performance.
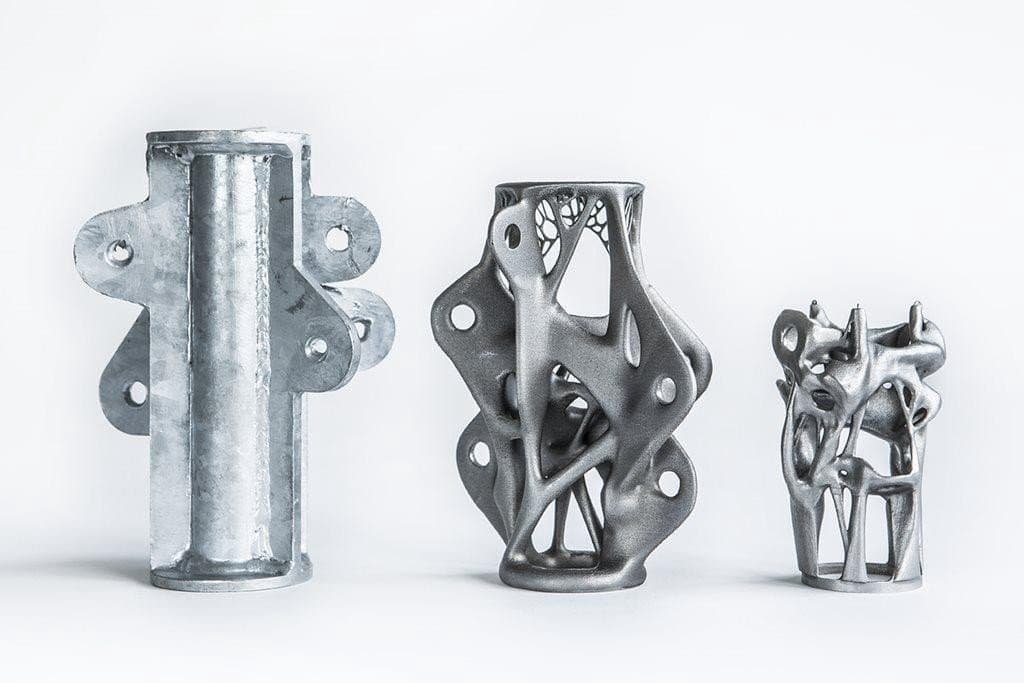
Brackets and struts where the forces are well-defined are common parts for generative design.
For example, in the automotive manufacturing industry, engineers utilize generative design to reduce component weights, improve weak design areas, decrease production costs through component consolidation, and reduce the time to market for new products.
Similarly, in the sports equipment industry, designers leverage generative design to achieve new levels of product performance while minimizing production costs. In the aerospace industry, generative design enables airline manufacturers to reduce the weight and improve the strength of plane components, helping airlines reduce fuel consumption to lower costs and emissions as a result.
Benefits of Generative Design
Simultaneous exploration: A notable benefit of generative design is that it allows the simultaneous exploration, validation, and comparison of hundreds or thousands of design options. The software can display and compare design options in a way that enables engineers to quickly and efficiently find the ones that best meet a project’s parameters and needs.
Accelerated design timeline: When engineers leverage AI to discover and test new complex design iterations quickly, efficiently, and at scale, they can drastically shorten research and development timelines for new products. As a result, companies utilizing generative design can gain a competitive edge in accelerating products’ time to market.
Leverage advanced manufacturing processes: Generative design can create complex designs like organic features and internal lattices to leverage the unique design freedom offered by additive manufacturing technologies. It also offers the ability to consolidate parts, so a single complex geometry created by a generative algorithm and 3D printed can often replace assemblies of dozens of separate parts.
Software Tools for Generative Design
Individuals who have experience with CAD can easily make the leap to generative design software. In addition to generative design-specific software, many CAD programs now offer integrated generative design tools or plug-ins.
Generative design software, however, offers users more than the traditional functionality of CAD software. These tools enable users to input information on forces, materials, costs, and the like into design profiles as well as prioritize and refine parameters based on graphical representations of design solutions.
By no means an exhaustive list, the following are popular software programs offering generative design capabilities:
-
Fusion 360 from Autodesk: Fusion 360 offers users a powerful set of modeling tools, including sketching, direct modeling, surface modeling, parametric modeling, mesh modeling, rendering, and much more. Its generative design capabilities enable users to identify design requirements, constraints, materials, and manufacturing options to generate manufacturing-ready designs, all the while enabling users to leverage the power of machine learning and AI to review cloud-generated design outcomes based on visual similarities, plots, and filters.
-
Creo Generative Design from PTC: Leveraging the cloud, this software enables users to create optimized design concepts and simultaneously explore and test numerous design iterations quickly. It highlights the iterations that best match a user’s objectives based on design parameters the user sets. Within the Creo design environment, this software promises to generate high-quality, lower-cost, and manufacturable designs, all in less time than leading competitors.
-
nTop Platform from nTopology: The nTop Platform software promises users complete control over every aspect of the optimization process and its outputs. Leveraging advanced generative tools, users can create custom, reusable workflows tailored to an application’s unique requirements. Featured capabilities of this program include unbreakable modeling and latticing operations, topology optimization, reusable design workflows, field-driven design, and mechanical-thermal finite element analysis simulations.
-
NX from Siemens: Beyond generative design, the main feature that NX offers is the digital twin technology, which promises users a flexible, powerful, and integrated solution to help them streamline the design and delivery of better products. NX combines design interoperability, validation, model-based definition, and more to help users move products through research and development faster and at lower costs while improving product quality.
-
MSC Apex Generative Design from MSC Software: This program promises users an end-to-end solution for making high-precision metal components more quickly and with less human intervention than its competitors. MSC Software reports that users experience reductions in initial design and setup time by as much as 80 percent. At a glance, the software combines simplicity, automated design, import and validation, and direct output in one process.
Generative Design and 3D Printing
Why Generative Design and 3D Printing Work Well Together
Generative design algorithms often create highly efficient organic shapes with supporting latticework that are costly or even impossible to fabricate with conventional manufacturing technologies such as injection molding or subtractive manufacturing tools like CNC machining. Advanced manufacturing tools like 3D printing—also known as additive manufacturing—are essential for the types of performance-sensitive applications where this optimization is compelling.
3D printing works well with generative design because it provides a flexible, fast means of producing a three-dimensional, high-resolution model of one or more design iterations for a cost-effective final product. Generally, in economic terms, the cost-effectiveness of 3D printing increases alongside the complexity of a design iteration.
3D printing is more cost-competitive at lower production volumes because you do not need to reach an economy of scale to offset setup costs. Therefore, it facilitates the mass customization that generative design makes possible. As the cost of 3D printing continues to decrease and the variety of materials increase, 3D printing is becoming practical for small and mid-volume parts for more and more applications.

How to Choose a 3D Printing Technology
Looking for the best 3D printing technology for your needs? In this video guide, we compare FDM, SLA, and SLS technologies across popular buying considerations.
Case Studies: Generative Design and 3D Printing in Action
Let’s look at three examples of how generative design and 3D printing work well together in real-life applications.
IGESTEK is a leading company specializing in the development of lightweight solutions for the automotive industry using plastics and composite materials. The company develops and integrates different hybrid processing techniques to manufacture composite components, which can then be implemented by Tier 1 automotive suppliers and original equipment manufacturers (OEMs) to produce parts for high-end cars and motorcycles.
One of IGESTEK’s latest innovative projects is a Suspension Shock Absorber Support (Top Mount). These components are part of a car’s suspension system that aim to reduce the vibrations produced by the rolling of the vehicle to improve comfort for the passengers.
The shock absorber support was developed with Autodesk’s Fusion 360 generative design software, which provided multiple solutions based on a limited series of requirements.
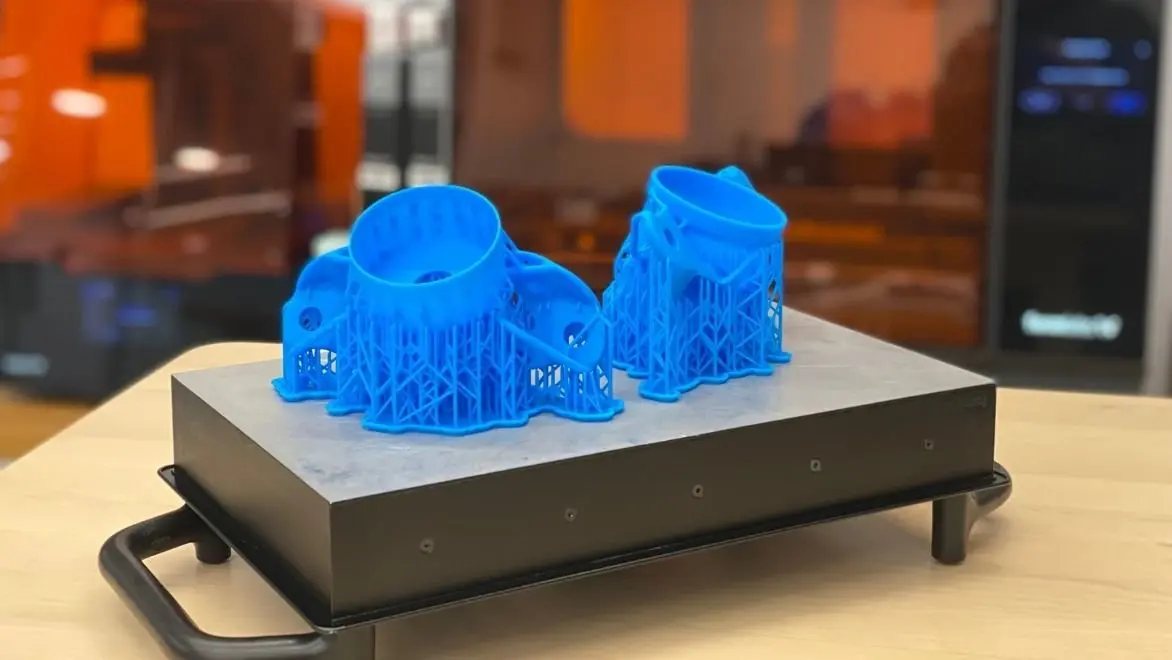
The large build volume of the Form 3L empowered IGESTEK to print multiple iterations of the component at the same time.
The team then 3D printed the most promising designs on their Form 3L large-format resin 3D printer in-house to validate the geometry, leveraging its large build volume to print up to three different iterations at the same time. SLA 3D printing made it feasible to realize the complex geometries obtained through generative design and validate assembly and kinematic processes with functional prototypes without investing in expensive tooling.
The end result of the R&D process was a multi-material architecture that combines metal 3D printing based on generative geometries and lighter composite materials to offer the best performance, in a 40% lighter package than current solutions on the market.
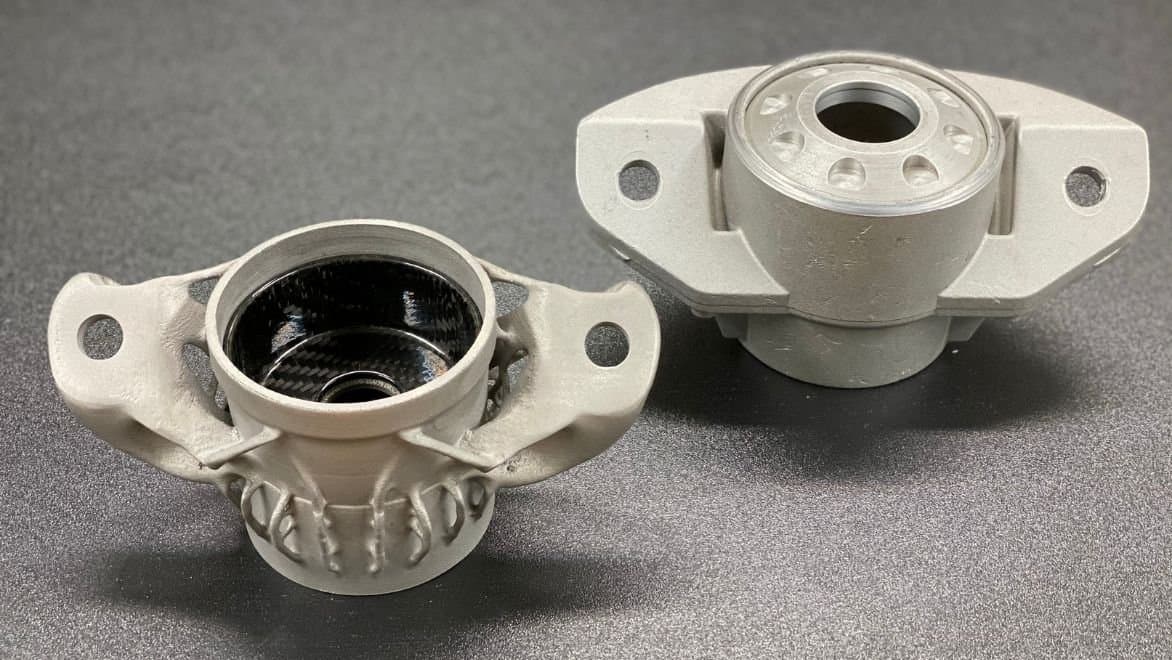
The end result, built using a combination of metal 3D printing and composite materials.
WHILL, a Japanese electric vehicle manufacturer, challenged itself to make a more portable motorized wheelchair by reducing the weight of its heaviest part—the battery case. Using Autodesk’s Fusion 360 generative design software, WHILL engineers were able to create a new design that reduced the battery case weight by 40%.
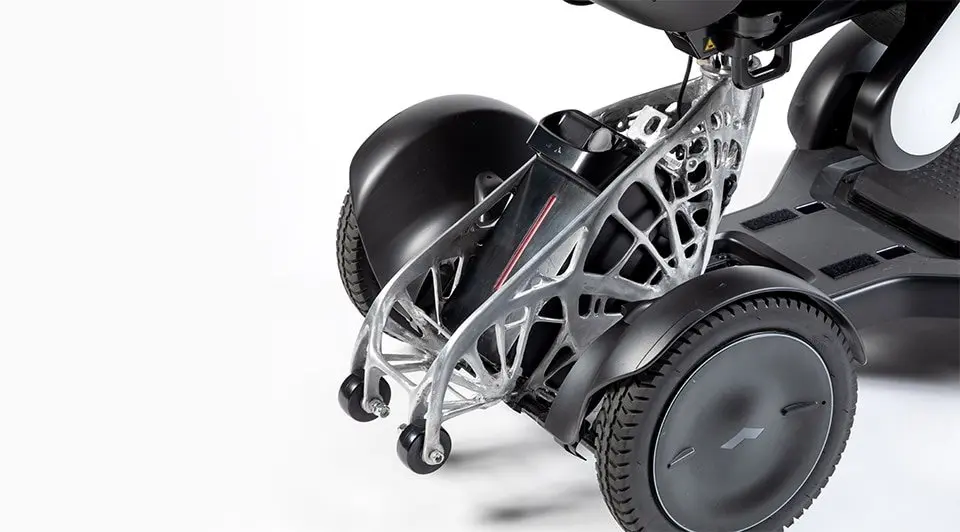

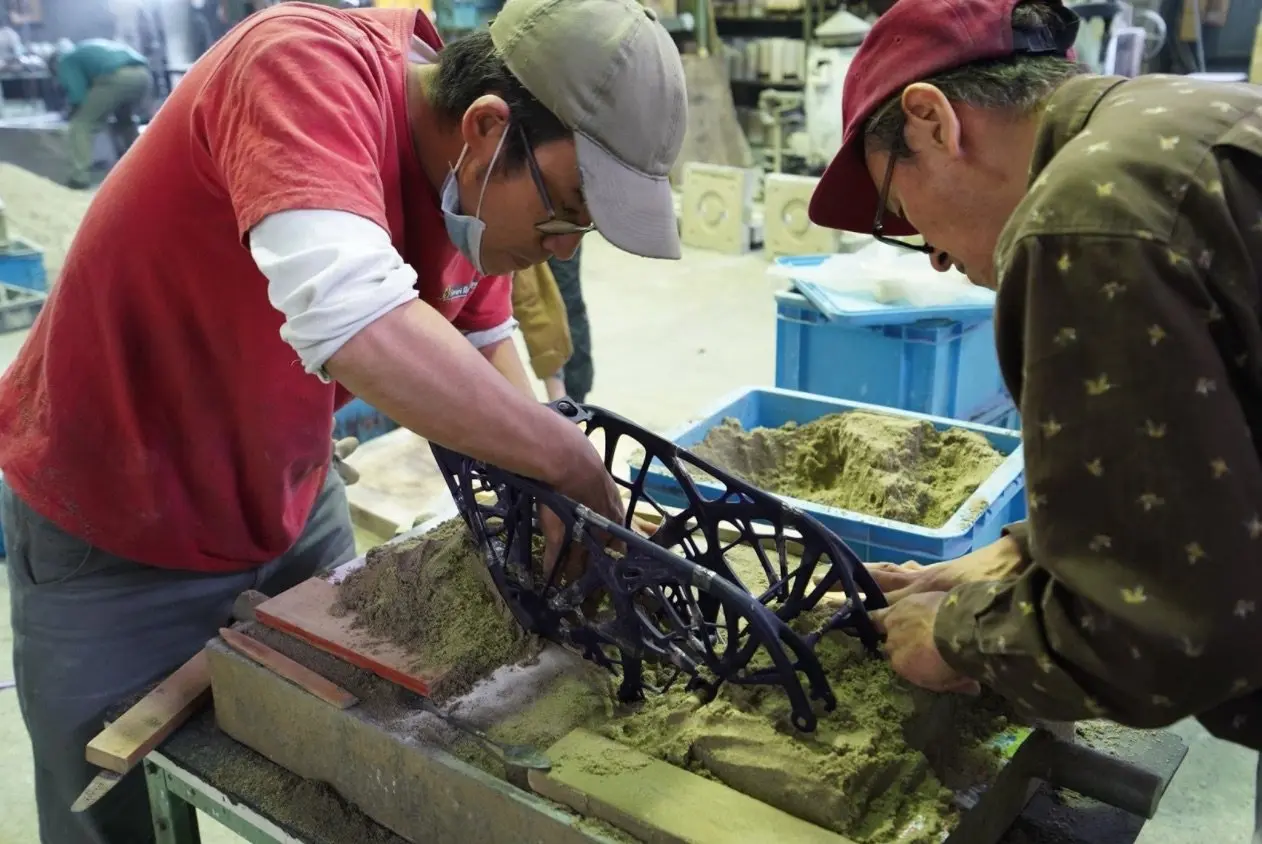
WHILL, a Japanese electric vehicle manufacturer used generative design to reduce the weight of a battery case, the heaviest part of a portable motorized wheelchair.. WHILL’s team used a desktop stereolithography 3D printer to manufacture the pattern for investment casting.
The product development team then used a novel manufacturing process to bring the design to life. The team split the design into four parts to be able to fit it inside the build volume of a Formlabs desktop stereolithography 3D printer and then printed the parts in Castable Wax Resin for investment casting. The engineers then connected the parts and sand cast the design for a final metal cast part. Ultimately, the team achieved a major breakthrough as a result of in-house 3D printing and generative design, reducing the final manufacturing cost of the WHILL wheelchair by decreasing the total number of parts in the product.
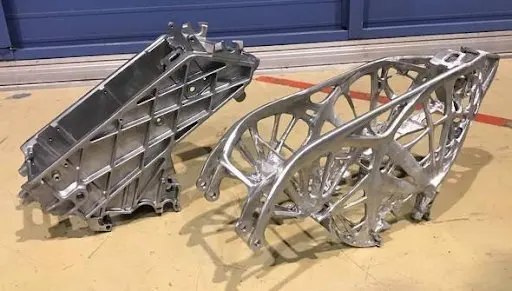
The part produced with generative design reduced the battery case weight by 40%.
Like WHILL, New Balance, a footwear manufacturing company, has made important breakthroughs through generative design and 3D printing. With a long-term vision for innovation in its customized shoe line, New Balance partnered with digital design studio Nervous System in 2015 to engage in a generative design process to develop a midsole that would better adapt to performance data from a runner.
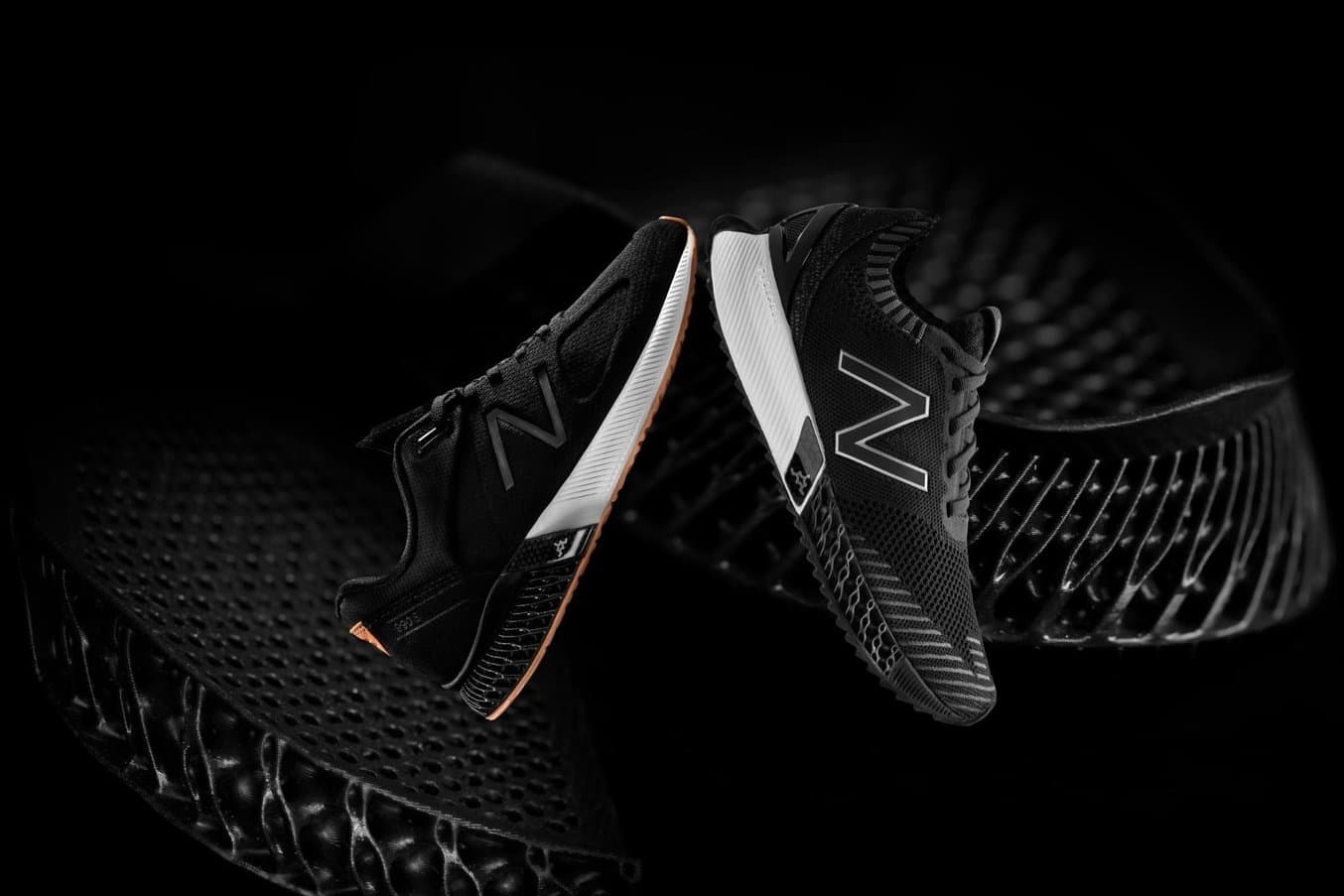
New Balance collaborated with Formlabs to develop a completely new material from the ground up for customized, high-performance shoes with generatively designed midsoles.
Then, in 2017, New Balance partnered with Formlabs to develop Rebound Resin, a proprietary production-ready photopolymer resin with five times the tear strength, three times the tensile strength, and two times the elongation of other production-grade elastomeric 3D printing materials on the market. Together, New Balance and Formlabs have made notable advancements in shoe manufacturing and helped deliver better products for end-users.
The two companies continue to work together with the ultimate goal to mass-produce custom running shoes tailored to each customer through generative design and novel 3D printing materials.
Getting Started With Generative Design
Wondering where to start? Here are a few key takeaways to help you find the right track:
It’s easy to start. If you know CAD, there isn’t a huge learning curve to try generative design. Generative design is easy to play around with for well-defined, closed problems. It is now integrated into many CAD packages that offer 30-day trials.
Lightweighting an existing part is a great starter project. Lightweighting is a good starting point to optimize for reduced weight while maintaining performance assuming loads are well understood.
Break the long term vision down into smaller R&D projects. Generative design and additive manufacturing require different mindsets and workflows to take advantage of. You won’t get to a performance-optimized, custom 3D printed product, available globally and at scale, overnight. Most successful projects look like a series of iterative, strategic projects over time.
Look to technology partners for expertise and support. Many software and additive companies have dedicated teams to support you, such as Formlabs Factory Solutions. Look for ways to take advantage of this expertise to get started and learn quickly.
Generative Design: Innovating the Future
Generative design plays an increasingly central role in the design of products across a wide range of industries. Whether a company aims to reduce the weight of an aircraft engine bracket, make an electric wheelchair more portable, or customize a running shoe, generative design and 3D printing are paving the way for a fully optimized and customized future.
As advancements in AI and additive manufacturing continue to extend the horizon of possibility for generative design, more applications and benefits of these innovative and cutting-edge technologies will emerge.
Curious to learn more about generative design? Watch our webinar “An Introduction to Generative Design for Producing Lightweight Parts With 3D Printing for more examples and a step-by-step tutorial of Fusion 360 for producing a lightweight bracket.