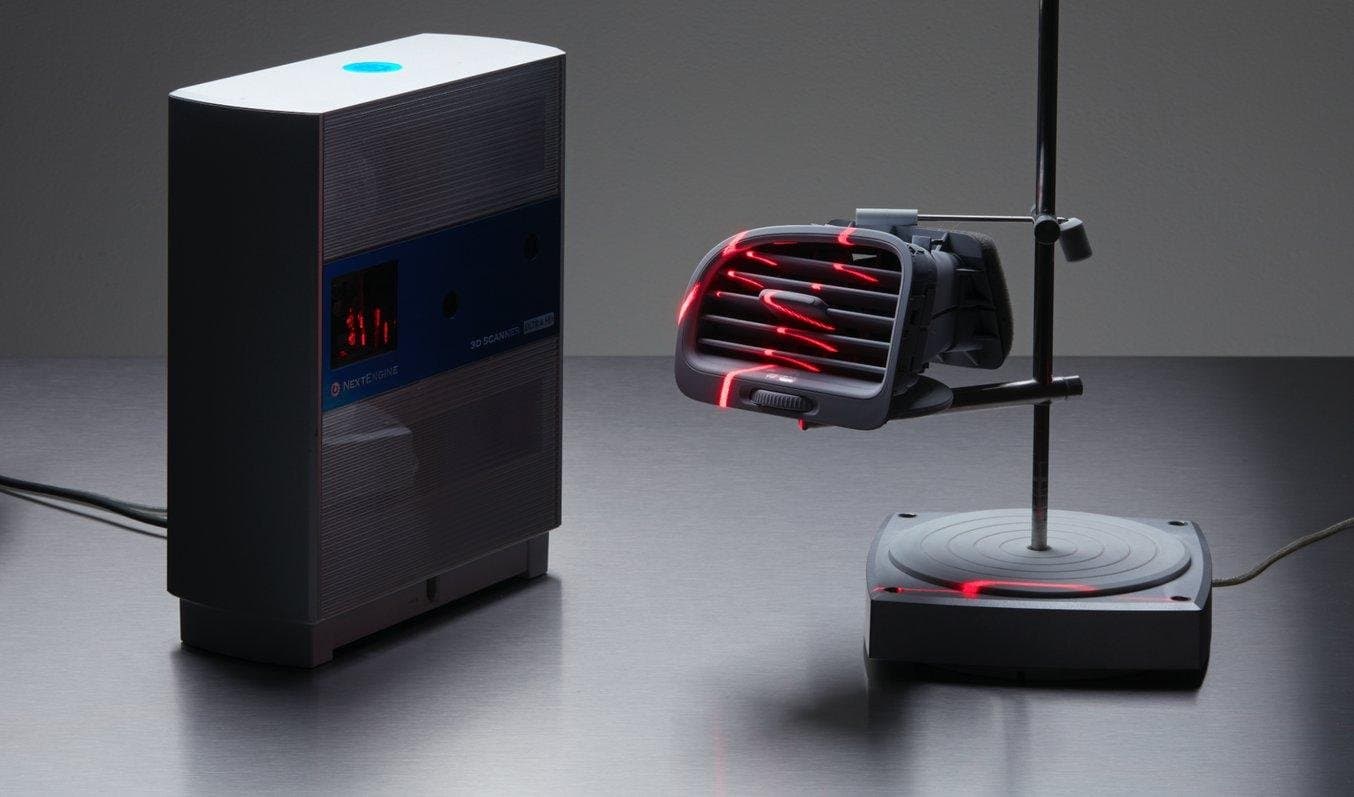
Reverse engineering is a popular method of digitalizing product design so manufacturers can easily reproduce parts on-demand, create and maintain a digital inventory, and avoid issues caused by obsolescent tooling or designs. This technique is common in industries like automotive, aerospace, biomedical engineering, design for manufacturing, and industrial design.
In this in-depth guide, we will explain the reverse engineering process, highlight the best tools for reverse engineering, and showcase real-life case studies in various fields.
What Is Reverse Engineering?
Reverse engineering is the process of dismantling and investigating a product to discover the concepts involved in its fabrication, with the goal of producing a similar product or improving upon an existing one.
While this is an accepted reverse engineering definition, there are plenty of other reasons to take the backwards engineering approach. Innovation is often borne of nothing more than a slight tweak or addition to a finished product: in chemistry to create new molecular compounds or vaccines, in electronics to replicate printed circuit boards, and in software development to recreate firmware, back-end architectures, and user interfaces.
With technologies like 3D scanners and digital fabrication tools like 3D printers, (reverse) engineers have better tools at their disposal today than ever before.
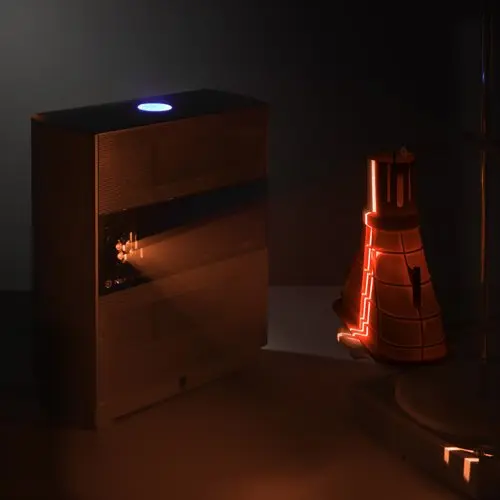
3D Scan to 3D Print: Rapid Reverse Engineering for Machine Restoration, Assembly Jigs, and Aftermarket Products
Watch this webinar for a detailed look at how to start using 3D scanning to improve part design and production when paired with reverse engineering CAD and 3D printing.
Reverse Engineering of Hardware
The reasons to reverse engineering mechanical parts are manifold.
Add-ons: In product development, existing components are often remodeled to create complementary or aftermarket items, customizations, repairs, or to fit them into a new assembly.
Product improvements: Existing components may be deconstructed, scanned, and scrutinized to improve their manufacturing and assembly processes. Cost reduction can occur in the following ways:
-
Loosening geometric dimensioning, tolerances, and constraints.
-
Lightweighting by optimizing structural geometry like ribs, wall thicknesses, radii, and other transitions.
-
Redesign for changes in the manufacturing process to aid assembly, disassembly, moldability, function integration, or end-of-life processing.
-
Refining key functional features, ergonomics, and usability.
-
Improving product performance such as overall strength, snap features, living hinges, electronic component mounting points, durability, and ingress protection (IP) for water and dustproofness.
Kick-starting innovation: Taking apart existing devices to understand their inner workings and design intent in great detail can be a spark for radical innovations.
Revisiting engineering challenges of the past precludes the need for reinventing the wheel. The field of biomimicry is notable for this, where biological systems such as grasshopper legs, gecko feet, whale hydrodynamics, ant colony behavior, mantis shrimp arms, spider webs, and ammonite shell formations have been researched as input for novel inventions.
By dismantling existing devices, companies can also learn about the components ‘under the hood’ of competitors’ products and how they were assembled. They can then use this information to evaluate if the company is truly delivering value for money, and where they may improve on the level of supply-chain integration and business strategy.
Resurrection: In case an OEM manufacturer goes out of business without having published any blueprints or CAD data, reverse engineering is the go-to method to revive otherwise lost items. For example, antique or retrocars that have run out of suppliers for replacement parts can be driven again thanks to reverse-engineering efforts on essential subsystems like engines, gearboxes, and drivetrains.
Reverse engineering is also a great way to bring back discontinued product lines with expired patent protection that were once popular and modify them to serve current-day audiences.
Reverse engineering also serves historical purposes by creating a digital archive of long-lost objects. Companies that only have physical instances of products they manufactured before the age of computers and CAD can now recreate these lost items by creating digital twins and this way keep their complete product legacy intact.
Knock-offs: The least ethically sound application of reverse engineering is the widespread copycat practices we are witnessing around the world today to create replicas, often simplified, awkwardly rebranded, or disproportioned, of bestselling products.
While in many cases this involves patent infringement and legal action should be taken, on the upside it can also be seen as a compliment to the original developers and a tolerable means to spread a design to markets that aren’t being served by the original inventor’s scope of distribution and intellectual property.
Here are some examples of reverse engineering applications:
Industry | Applications | |||
---|---|---|---|---|
Automotive | Bumpers, roofs, aerodynamic mods, kit cars, exhaust manifolds, spare parts, clay model digitization | |||
Biomedical Engineering | Anatomical models, implants, surgical tools, prosthesis/orthoses, orthopedics | |||
Consumer Goods | Add-ons, prototypes, packaging | |||
Mechanical Engineering | Replacement parts, part improvement, value engineering, machine conversion, failure analysis | |||
Furniture | Ornamentation, legs, moldings, trims, replacement parts | |||
Jewelry | Replicas, molds, made-to-fit items, preservation |
Is Reverse Engineering Legal?
Reverse engineering is generally legal under the U.S. Defense Trade Secrets Act (DTSA) to gain a commercial or military advantage over competitors, provided this is done without breaching contractual agreements and after obtaining the original product in accordance with the law.
It is considered a lawful means to discover trade secrets different from theft or espionage, as long as this does not interfere with patent protection, end-user licensing, or other contractual obligations.
In some cases, however, competitors replicating products can have severe consequences to the business of an OEM and companies often take active measures to prevent their products from falling into the wrong hands.
Reverse Engineering of Software
Software reverse engineering has the same purpose yet differs fundamentally from hardware replication because commercial applications typically are closed-source. That is, the source code is purposely made inaccessible to third parties.
There are specific tools called disassemblers that can lay bare the inner workings and algorithmic structure of the target application. These software reversing solutions decompile into their own platform-specific assembly language without plagiarizing the original code.
Because of this inner conversion, the resulting machine code is unique, which makes the process entirely legal. It’s in a similar fashion that manufacturers like AMD create Intel-compatible microprocessors. This way, businesses can also legally customize new software environments to integrate into their existing IT systems.
In one famous case, Google’s Project Zero discovered a critical weakness in microprocessors by reverse-engineering them. They found that it’s possible to create readouts of pre-cached memory chunks, which may contain sensitive information like passwords. This led to a new idea: performing memory storage in a separate system-on-a-chip (SoC) where it is secured from interception.
One fundamental distinction between how to reverse engineer software versus hardware is that code, as opposed to physical matter, can be encrypted. Cybercriminals often make use of this in creating malware, which is exceptionally hard to reverse engineer even with tools like the NSA’s Ghidra.
To improve corporate cybersecurity, an internal ‘hacker’ team will often create virtual attacks on their own network, while another ‘protector’ team monitors and reverse-engineers the attacks in order to find new solutions.
Reverse Engineering Process Overview
The exact process for reverse engineering differs by the type of the object. In this guide, we’ll focus on reverse engineering of hardware.
Reverse engineering of hardware is a four-step process. It happens in a backward fashion compared to regular new product development processes. Reverse engineers start with the finished product and subsequently deduce the requirements that drove its development.
The methodology typically follows these steps:
-
Data acquisition: The 3D scanner is calibrated, and the scene is set up for optimal results in terms of background and lighting. This results in a point cloud up to several gigabytes in size. It is often not enough only to digitize the model; reverse engineers will also want to learn first-hand about the design intent and assembly features by taking the product apart and subjecting it to a variety of tests.
-
Post-processing: The original point cloud is converted into a conceptual mesh model. Most software tools offer automatic functions but may still require manually filling gaps and removing irregularities. The purpose of this step is to study and break apart the current system and its constituent components.
-
Modeling: The mesh representation of the object is converted into a parametric model based on solids and surfaces. We are now working back from the implementation level to recover the underlying design intent. In this stage, engineers can easily alter dimensions and add improvements.
-
Review: This stage involves dimensional comparisons between the scan and the resulting reproduction. It subsequently entails proofing, prototyping, testing, and iterating in various scenarios to ensure the reverse-engineered product meets the new requirements.
Reverse engineering is intrinsically different from forward engineering. Because we have worked back from an existing implementation, the reworked product is never 100% accurate, on-spec, or ‘correctly‘ modeled in terms of CAD procedures.
Since reverse engineering is inherently inaccurate in dimension, ambiguous in interpretation, and odd in surface construction, we have to be satisfied with the closest possible approximation. In very little time, we can still create significant value with useful parts that would have taken 10-100 times the resources if developed from scratch. This is a different mindset than forward development which is usually characterized by a striving toward perfection.
Best Reverse Engineering Tools
3D Scanners for Reverse Engineering
There is a range of available methods to turn a physical object into its digital twin. 3D scanners are the most commonly accepted capturing device and come in various forms.
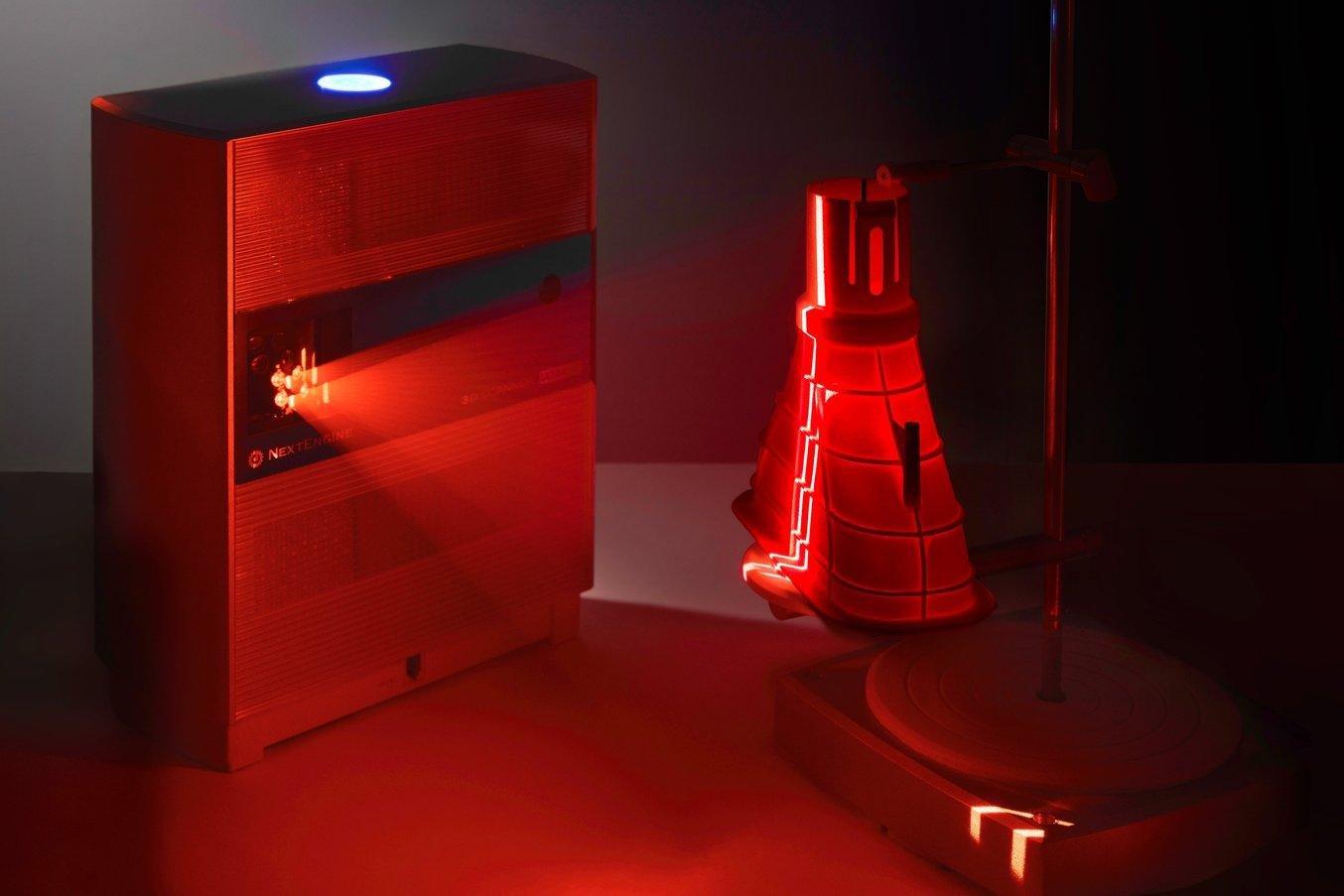
3D scanners are the most commonly used capturing devices for reverse engineering.
Structured light scanners project a light pattern across the object and use two cameras to capture how the object deforms the light. The resulting images are stitched together into a 3D representation.
Commonly used in handheld and non-invasive medical applications, some well-known entry-level models include the Shining3D Einstar, Creality CR-Scan Lizard, and Structure Sensor Pro. Advertised precision levels need to be taken with a grain of salt though; the average deviation is roughly 1% for these types of devices.
More advanced scanning solutions include the Peel3D, Calibry, and Artec Eva handheld 3D scanners. These have higher accuracy, inbuilt processing software, and real-time feedback to guide the scanning process, plus different modes including stick-on marker-based scanning. That is great for flat objects up to several meters in size. The increase in quality, however, typically comes with an exponential increase in price.
Laser triangulation scanners shoot millions of laser dots per second onto the target object, which typically needs to be enhanced with markers. For opaque parts with fine details such as filigree meshes, convex surfaces, and lattice structures, this category of 3D scanners is the best pick.
Popular products like the Matter and Form 3D scanner, Creaform HandyScan, Zeiss T-Scan Hawk, and FARO Freestyle can scan entire vehicles. For complex scanning projects, professionals will often use a hybrid method using both a portable CMM system and a stationary non-contact scanning arm.
For beginner enthusiasts who can accept compensating the imperfections of their scans with their superstar reverse-engineering CAD abilities, there are some low-budget alternatives.
Depth-sensing infrared cameras and LiDAR sensors provide less accurate mesh models, but may still be satisfactory for simple scans in some cases and can be found on the latest models of the Apple iPhone and iPad.
Photogrammetry is based on regular photography where the reverse engineer has to shoot a sequence of images from various angles around the object. The process then relies on computation-intensive software such as Meshroom, RealityCapture, Regard3D, Trnio, RecFusion, or Zephyr, to stitch the images into a 3D reconstruction.
Despite the perk that some apps are available for free, it takes a bit more skill and patience to derive workable models from photogrammetry, regardless of the application.
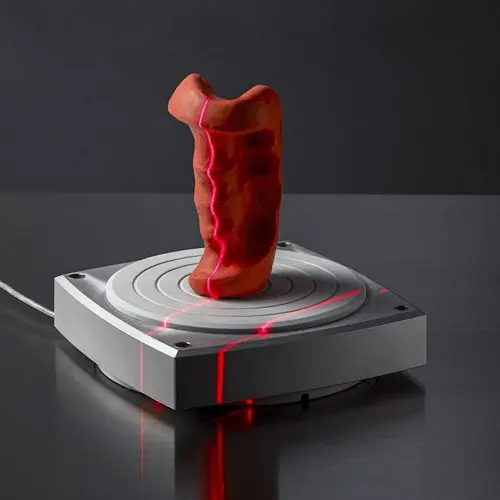
3D Scanning and 3D Printing for Reverse Engineering and Other Applications
3D scanning and 3D printing workflows can be applied to replication and restoration, reverse engineering, metrology, and more. Download our white paper to explore these applications and learn how to get started.
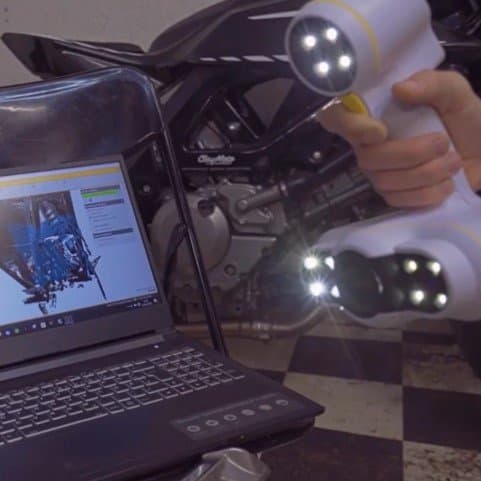
How 3D Scanning Supports the Modern Product Development Process
Watch this webinar with Peel 3D to explore how to integrate 3D scanners into your 3D printing workflow to elevate your product development process.
Software for Reverse Engineering
The relative ease of a 3D scan to CAD workflow often depends on an arsenal of separate software tools that have varying degrees of compatibility. To streamline the pipeline, however, it is best to choose a software solution that takes the reverse engineer all the way from the raw scan data to a complete high-quality reconstruction of the original design.
The best software tools for reverse engineering will load a point cloud in various formats such as .ply, .asc, .ptx, .pcg (Autodesk), .e57, .xyz, .fls (Faro), .pcd, .las, and .obj. These programs will auto-generate and auto-repair the resulting mesh object, and offer a host of smart tools for reconstructing NURBS surfaces to fit the mesh. This prevents having to measure every little detail with a caliper to manually reconstruct it, as used to be the case before the advent of 3D scanning.
Some virtual design studios even let users prepare the result directly for prototyping through CNC, 3D printing, or casting. And since a tenth of a millimeter can make all the difference in how two fabricated parts fit together, precision is key throughout the entire reverse engineering process.
To ensure accuracy, a reverse engineering tool has to be able to do the following:
-
Interference checking to ensure parts will operate smoothly together in an assembly, and that external components will fit snugly.
-
Wall thickness analysis to optimize moldability and lightweight design
-
Draft analysis to ensure correct draft angles, prevent undercuts, and validate parting lines
-
Surface analysis such as zebra striping and curvature control ensures suitability for large complex shapes such as those required in consumer products and automotive.
-
Dimensional verification such as mass, volume, and bounding box.
Here are some of the top choices when it comes to the best reverse engineering software tools.
Mesh2Surface
Mesh2Surface is an end-to-end solution that enables product developers to convert their point cloud to a mesh directly for Rhinoceros or SolidWorks reverse engineering.
The 3D designer can then extract reference planes and points on the mesh to fit complex geometry. Mesh2Surface contains smart tools for creating 3D sketches, cross sections, and outlines. It provides deviation analysis, auto-surfacing with custom precision settings, and the ability to draw best-fit freeform surfaces.
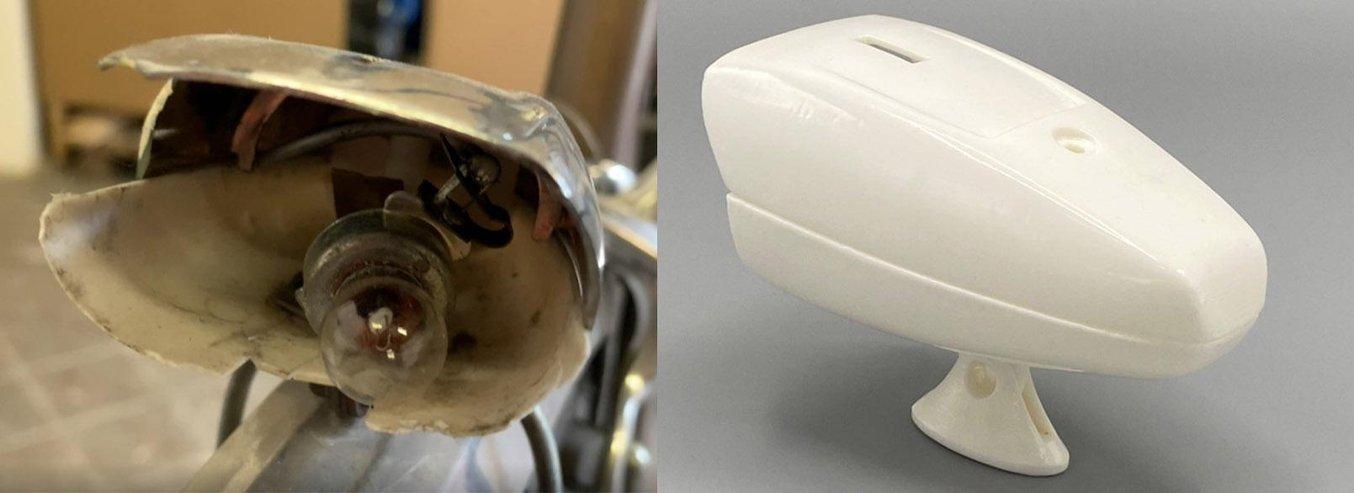
Mesh2Surface performs outstandingly in creating replacements for heavily damaged parts such as this motorbike headlamp.
Artec Studio
Artec is another contender at the top of hardware reverse engineering tools. It focuses on ease of use and boasts maximum speed in the Scan-to-CAD conversion process. Because the software provides real-time feedback on the movement of the device, and even allows overlaying multiple scans for richer data integration, an entire car can be digitized in roughly 15 minutes.
Even though Artec does not offer a full CAD experience, users can still create accurate models using primitive fitting, top-notch texture and geometry tracking algorithms, and the Auto Surface tool that turns organic shapes into a solid model.
Artec Studio also includes an Autopilot Mode that automates a substantial part of the modeling process.
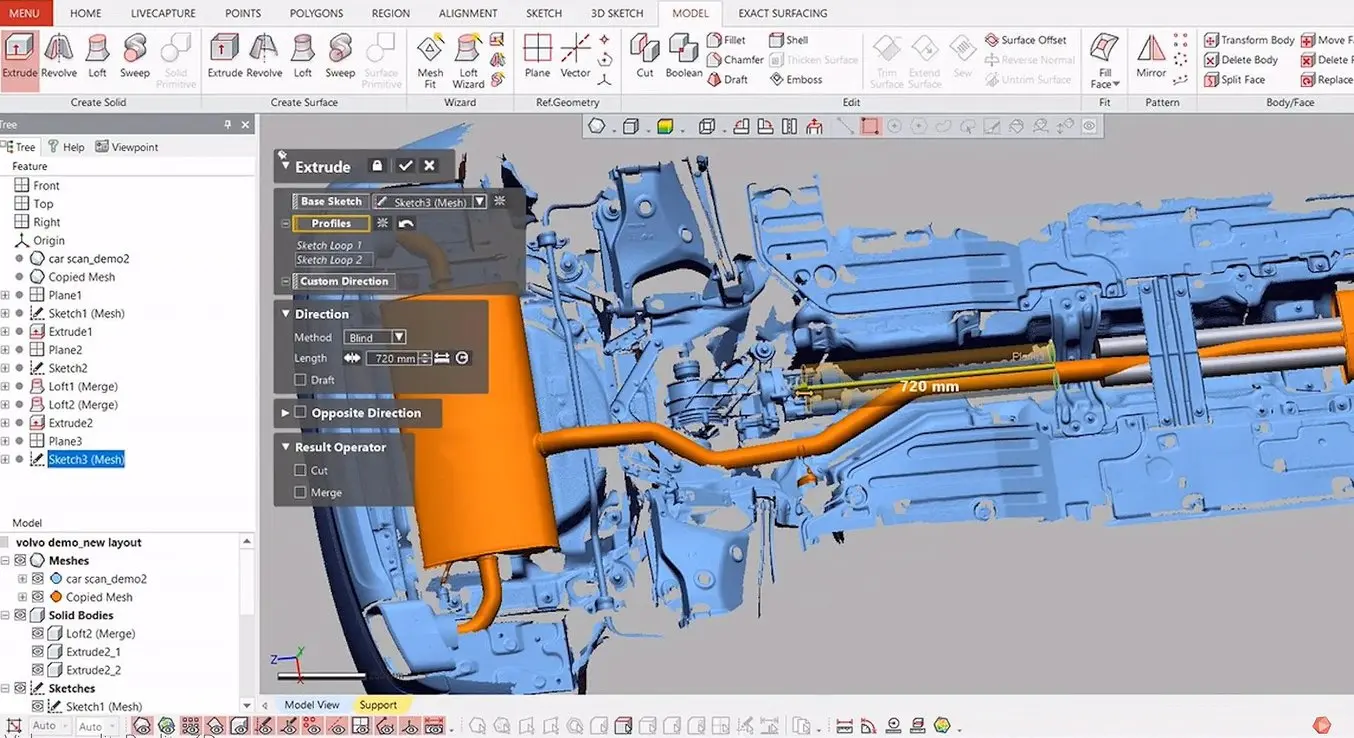
Artec Studio allowed a reverse engineer to 3D scan and reproduce parts of a Volvo XC90 underbody in under an hour for developing a new exhaust system.
Fusion 360
Autodesk Fusion 360 is one of the popular reverse engineering tools. It is a cloud-based CAD system that offers an intermediate solution as it can only handle lightweight meshes and offers a limited suite of geometrical operations when compared to the industry leaders.
Fusion offers various methods for the mesh-to-solid workflow, such as obtaining contours in the Mesh workspace. It also has numerous analysis tools for stress simulation and topological optimization in its various workbenches. As it is integrated with Meshmixer, it also provides more and more reliable mesh repair tools.
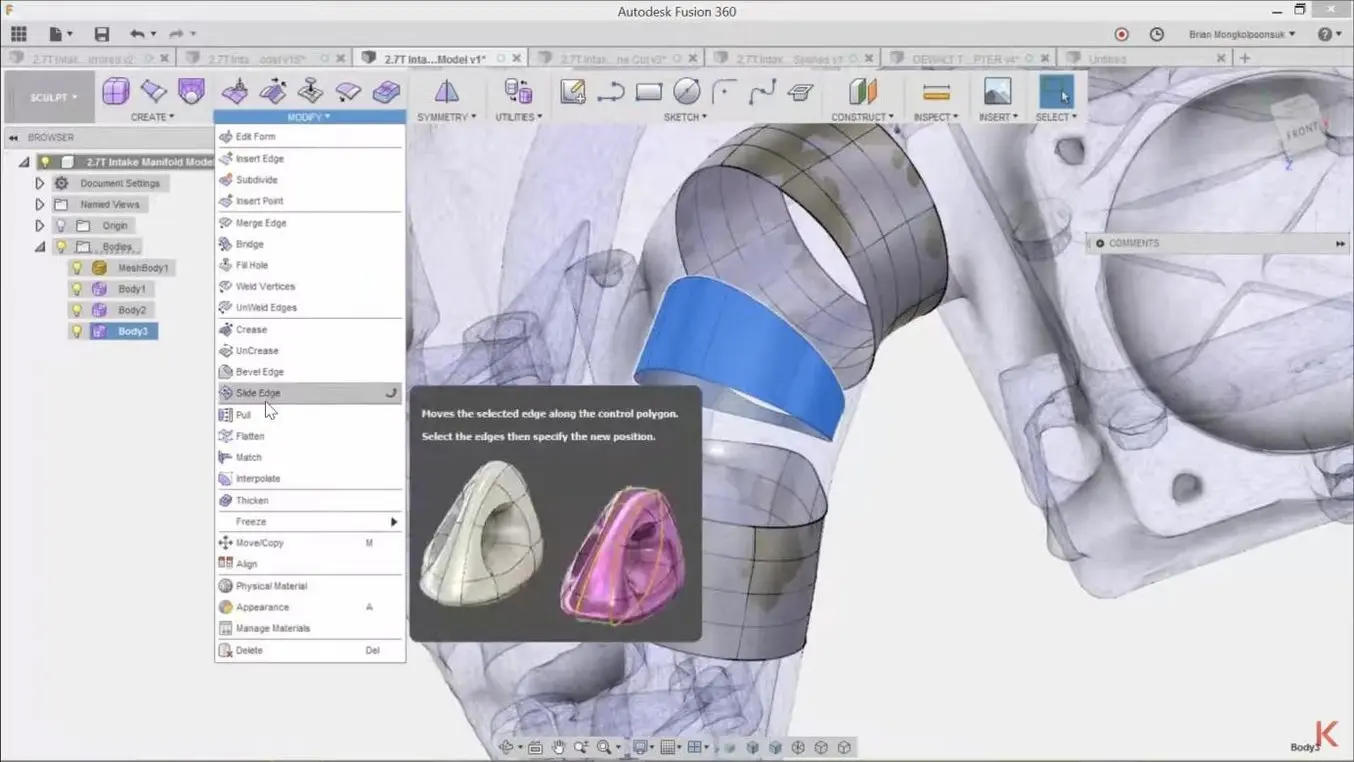
Fusion 360 is a great mid-level solution that carries a broad arsenal of polygonal modeling tools to fit mesh geometry.
Geomagic Design X
Geomagic is the top-shelf solution for turning 3D scan data into feature-based CAD models. Precise reconstruction is guaranteed by tracing outlines based on different sections of the mesh. Brush selection allows you to include and exclude specific areas for the various steps in the reconstruction process. It also offers a powerful Autosurface function that takes some of the hassle off the hands of engineers.
What’s more, the user interface feels familiar as it resembles SolidWorks. In fact, the ‘Live Transfer’ tool allows designers to export the history tree to a dedicated CAD modeling environment such as NX, Creo, Inventor, Pro/Engineer, and SolidWorks.
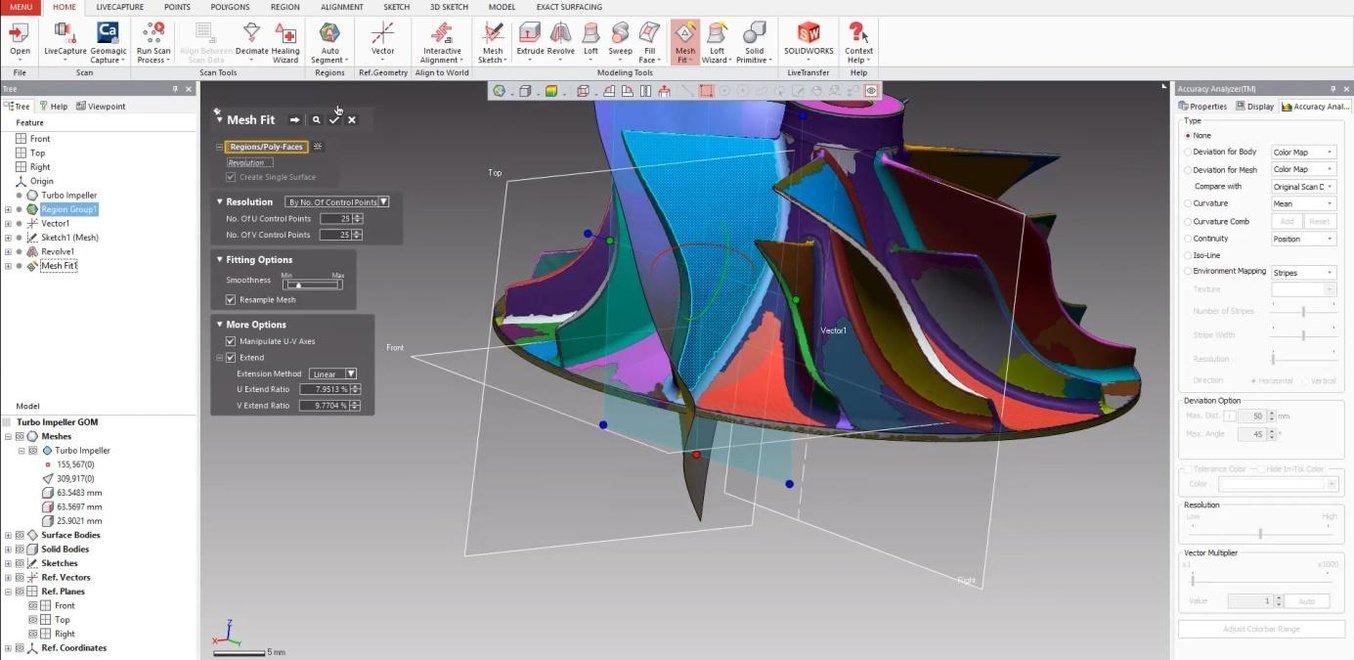
With advanced surface reconstruction tools, Geomagic DesignX can handle complex reverse-engineered designs, such as this 3D scanned turbocharger impeller.
Xtract3D
For designers and engineers who prefer to keep their reverse engineering efforts within the walls of SolidWorks, Xtract3D is an essential plugin. It allows direct importing of meshes or point cloud data, yet since it’s mostly geared to simpler geometry, it is a lightweight alternative to more powerful reverse engineering packages.
Still, its tools are commendable. Xtract3D serves the user with powerful slicing, sketch fitting, and snapping tools. This enables designers to trace right on top of 2D cross-sections of the 3D scan data to create parametric models with ease.
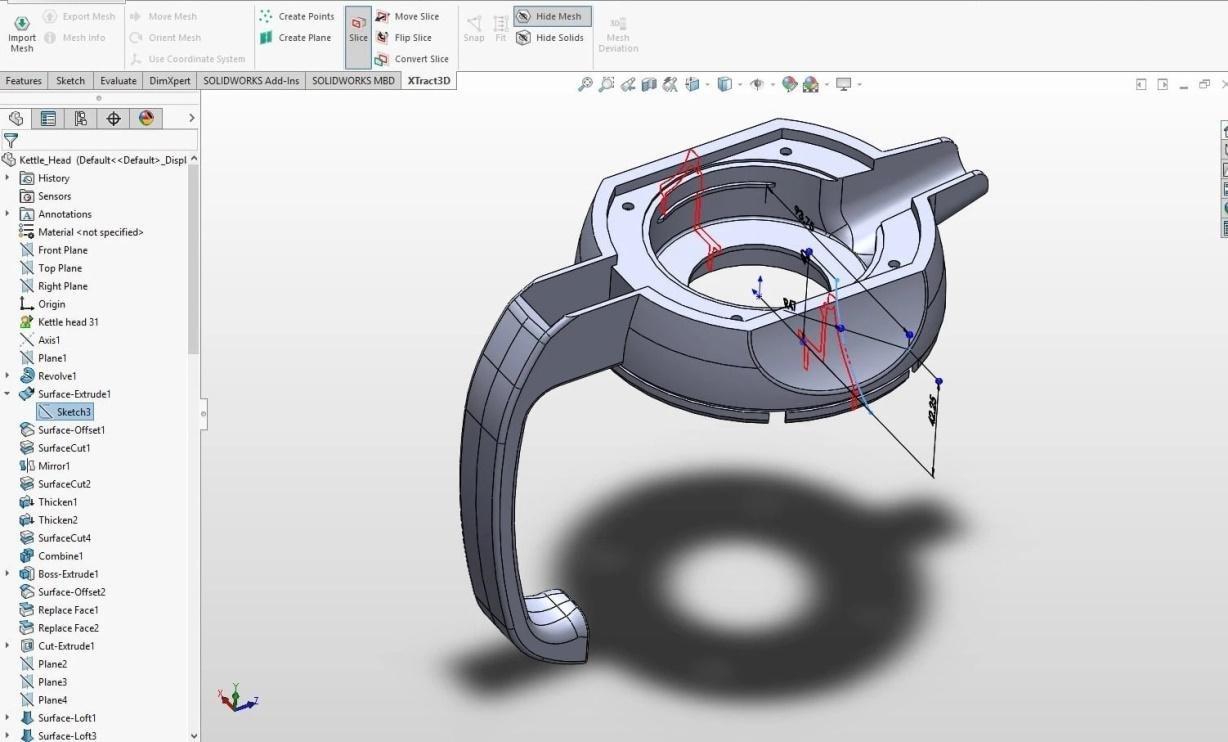
Xtract3D for SolidWorks offers enough functionality to replicate consumer products such as this kettle head based on 3D scan data.
Ansys SpaceClaim
SpaceClaim is a renowned and innovative CAD package with advanced reverse-engineering capabilities. It is the preferred solution for direct modelers who prefer freedom and speed over the complexities of having to tightly define geometry in parametric history-tree based modeling environments.
Smart functionalities like feature identification, Skin Surface, and push/pull manipulation are what make SpaceClaim stand in its own right when it comes to streamlining the reverse engineering workflow. In the reconstruction process, the software will automatically detect desired modeling operations and make suggestions for optimal remodeling toward highly accurate results.
What’s more, by working with SpaceClaim, engineers can easily link their model up to other Ansys modules such as those for CFD or mechanical simulations.
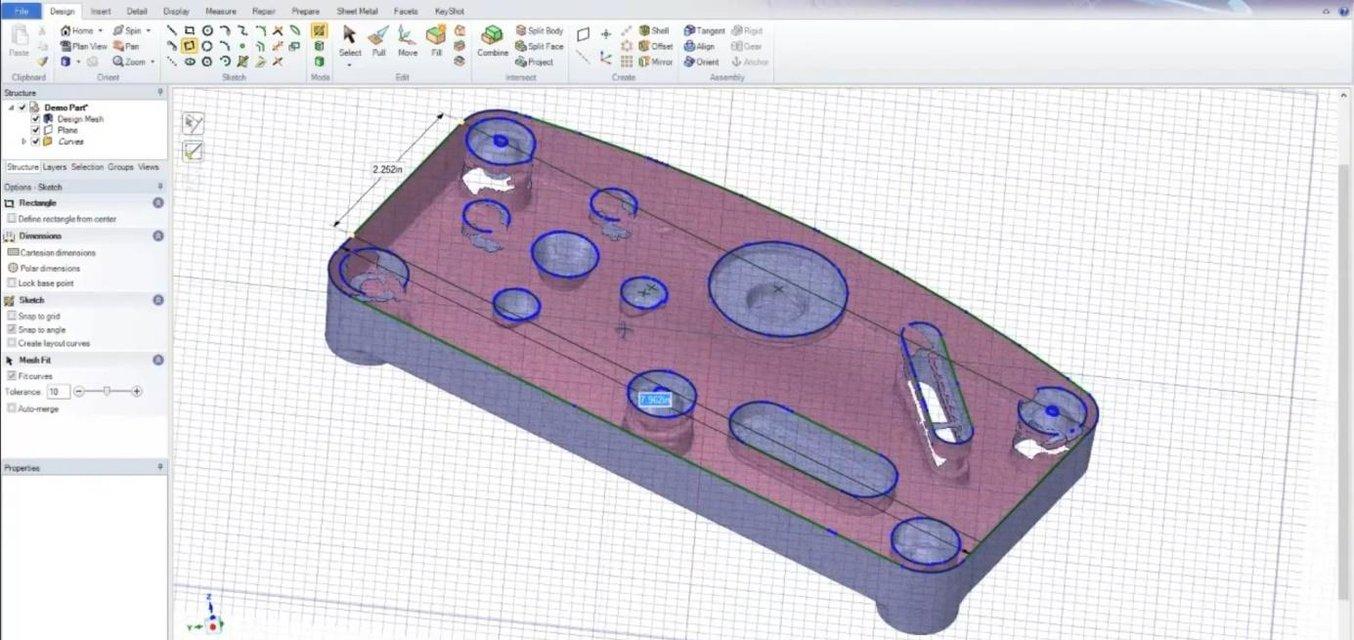
SpaceClaim automatically detects features and snaps new geometry to the original mesh for quick and accurate remodeling.
Tebis Reverser
Tebis offers a specialized reverse engineering environment for automotive designers. It was developed in collaboration with BMW Design Group to facilitate the Clay-to-CAD workflow. This way, designers can take the manual design process further before stepping into 3D.
The Reverser software package analyzes mesh data and has designers create a wireframe structure that is then used to generate individual surfaces. These surfaces are then analyzed and smoothed up to A-class quality as per the industry standard.
Next to offering a slew of manual control parameters, surfaces can automatically be calculated and transitions controlled in great detail, without requiring the user to obtain a deep expertise. The associative surface technology keeps the mesh and generated surfaces linked to ensure tangentially constant transitions and smooth surface progressions.
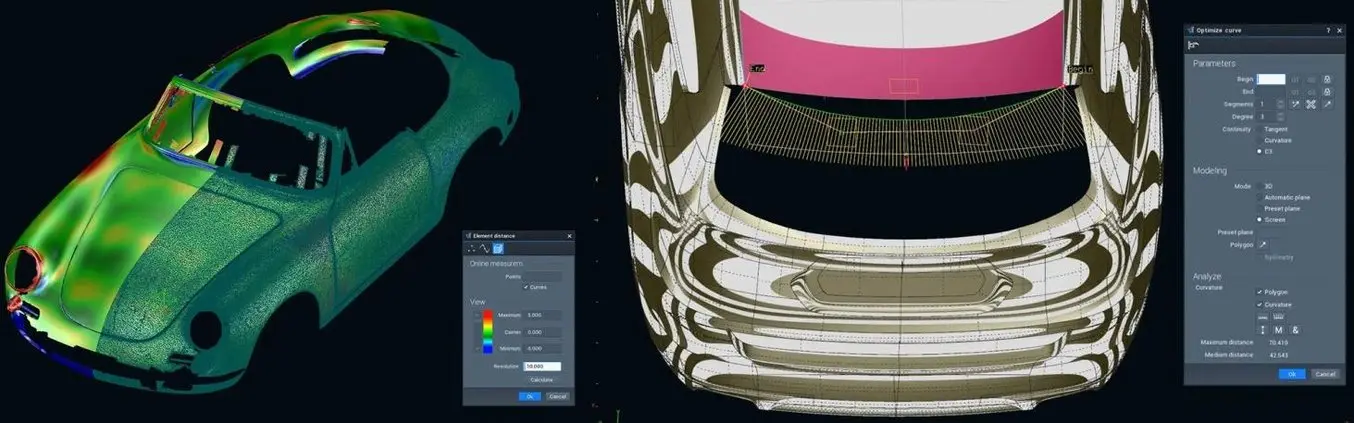
Tebis Reverser is a surefire solution to generate high-quality surface models from 3D vehicle scans.
PTC Creo
Creo is a parametric modeling package suitable for working for assemblies of over 1,000 parts. It is increasing in popularity in the consumer product as well as mobility sector and has been adopted by industry stalwarts like Aston Martin, John Deere, Volkswagen, Toyota, and Amazon.
Professional engineers will benefit from investing in the Advanced Plus package which includes advanced surfacing, a 3D printing slicer, GD&T, mold design, and simulation.
PTC has now also released a Reverse Engineering Extension for both Pro/Engineer and its professional version, Creo. After importing point cloud data and creating the facet mesh, it can be cleaned and its modeling features automatically extracted with the Restyle feature. Creo then offers powerful synthesis and analysis tools for building a highly accurate, curvature-continuous model.

The Reverse Engineering Extension for Creo and Pro Engineer offers advanced tools for professional and accurate results.
VXElements
The VXElements suite by Creaform offers a collection of modules for the scan-to-CAD workflow. Most notable is the VXModel software, which acts as a virtual assistant to turn raw mesh data into a high-quality solid model.
Highlights of the program are the auto- and manual-surfacing tools, mesh cleaning functionality, snap align, Boolean combine operations, and the ability to extract and edit boundaries and cross sections. VXModel also has a 3D printing export function and provides the opportunity to directly transfer reverse engineering models to Inventor, SolidWorks, and SolidEdge for further processing.
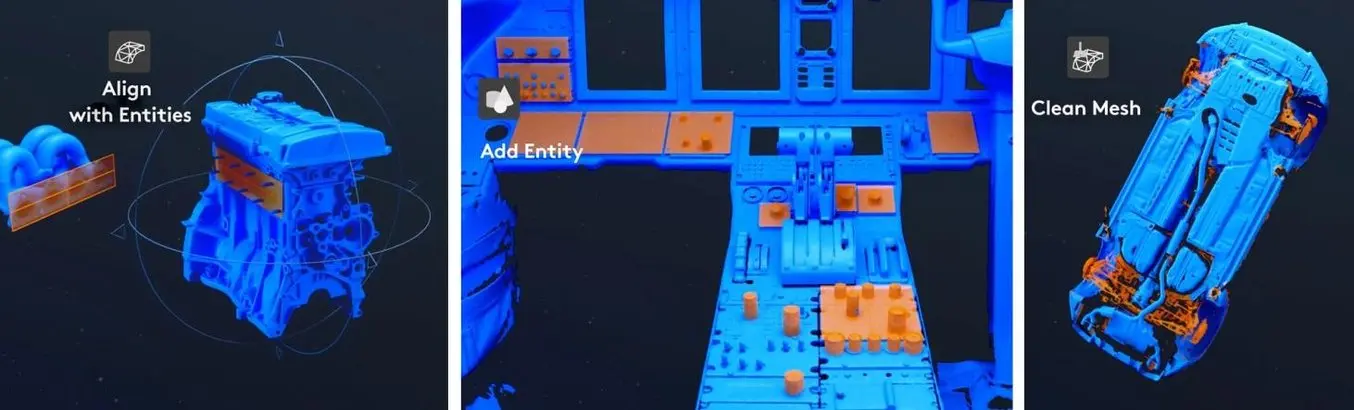
VXModel offers a wide arsenal of reverse engineering tools.
3D Printers for Reverse Engineering
By 3D printing reverse engineering parts, designers develop an in-depth understanding of all the features and parameters that drive the success of their creation. What’s more, it enables them to go through rapid improvement cycles and even 3D print end-use parts.
Stereolithography (SLA) resin 3D printers use a laser to cure liquid resin into hardened plastic in a process called photopolymerization. SLA parts have the highest resolution and accuracy, the clearest details, and the smoothest surface finish of all plastic 3D printing technologies, and SLA printing also offers the widest range of materials.
SLA is a great option for highly detailed prototypes requiring tight tolerances and smooth surfaces, such as molds, patterns, and functional parts. SLA is widely used in a range of industries from engineering and product design to manufacturing, dentistry, jewelry, model making, and education.
Desktop SLA 3D printers like the Formlabs Form 3+ offer a powerful, yet affordable solution for most reverse engineering projects, while large resin printers like the Formlabs Form 3L can support even the largest projects.
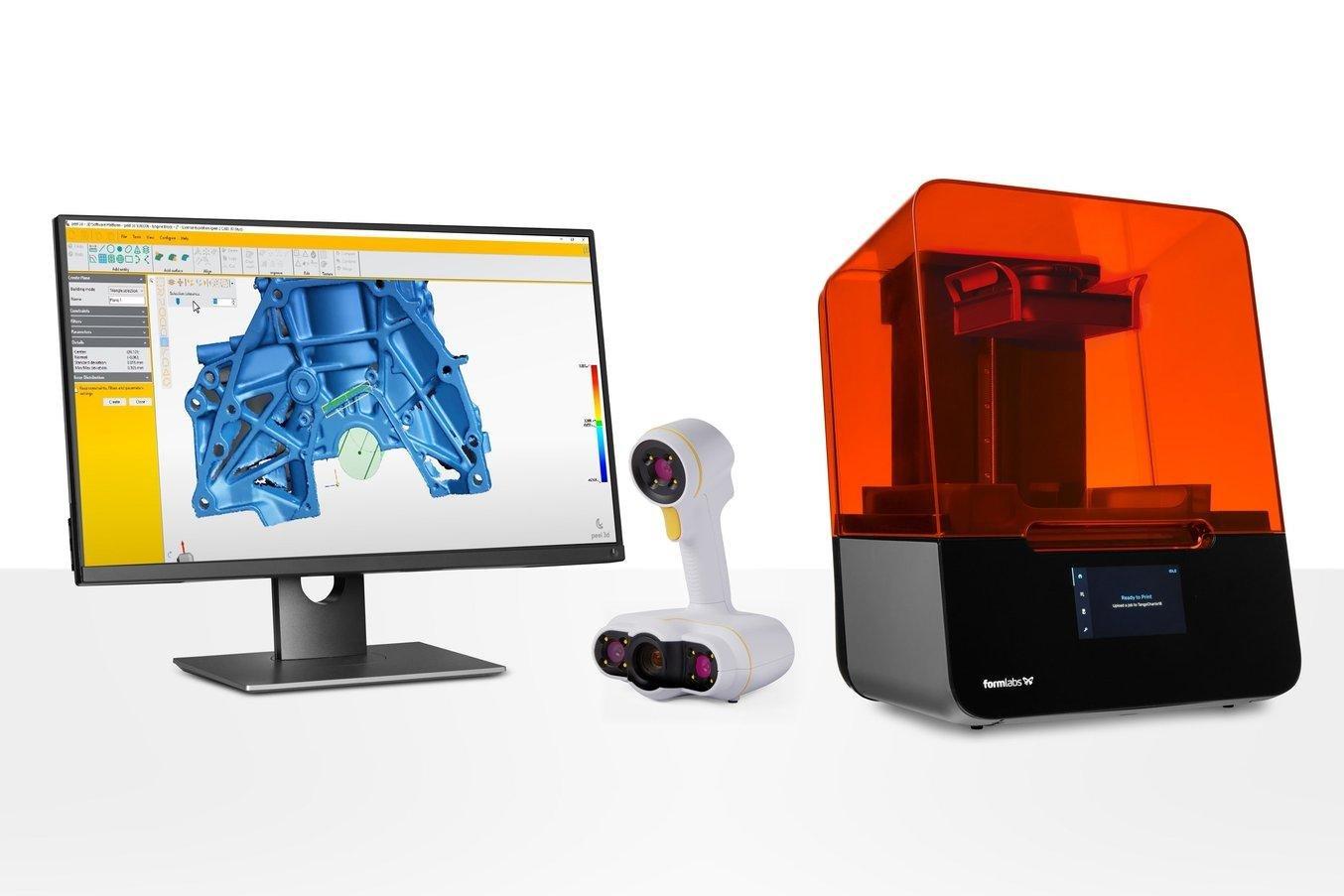
Desktop SLA 3D printers are ideal for turning reverse-engineered designs into physical parts.
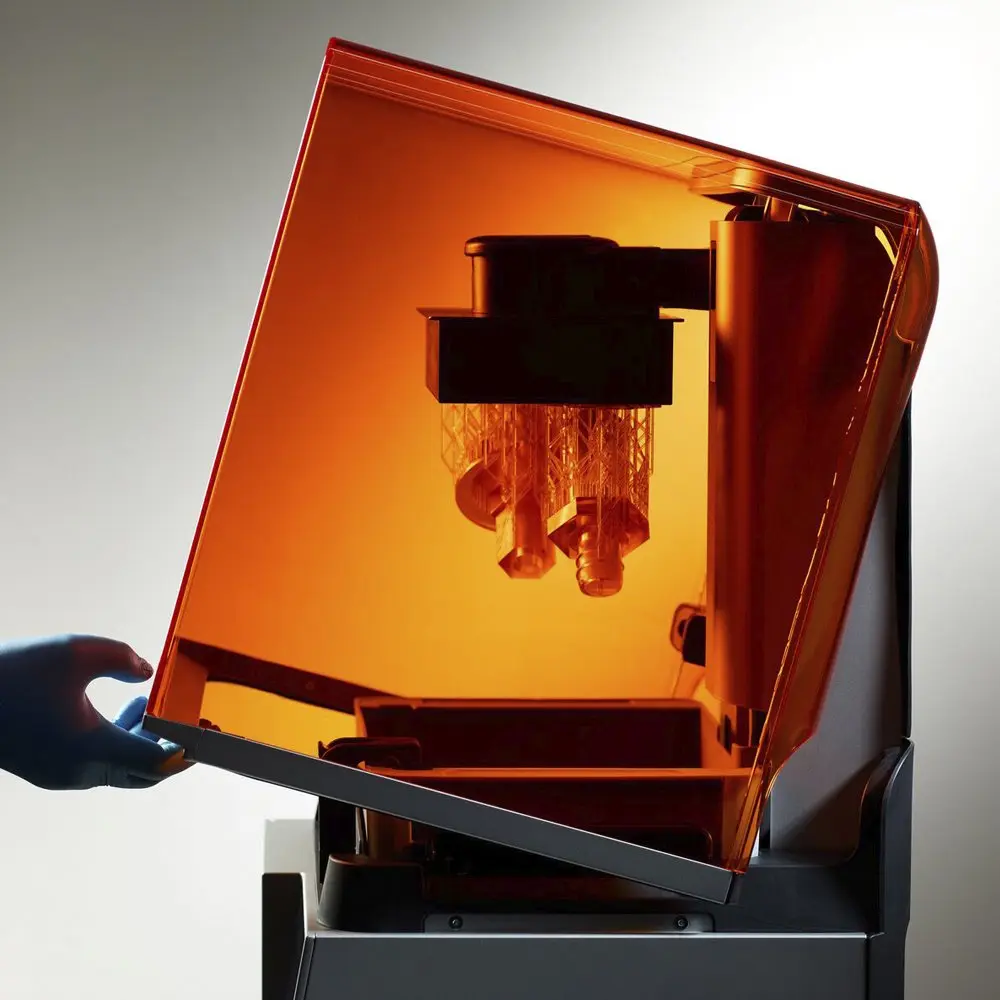
Introduction to 3D Printing With Desktop Stereolithography (SLA)
Looking for a 3D printer to realize your 3D models in high resolution? Download our white paper to learn how SLA printing works and why it's the most popular 3D printing process for creating models with incredible details.
Selective laser sintering is the most common additive manufacturing technology for industrial applications, trusted by engineers and manufacturers across different industries for its ability to produce strong, functional parts.
SLS 3D printers use a high-powered laser to fuse small particles of polymer powder. The unfused powder supports the part during printing and eliminates the need for dedicated support structures. This makes SLS ideal for complex geometries, including interior features, undercuts, thin walls, and negative features. Parts produced with SLS printing have excellent mechanical characteristics, with strength resembling that of injection-molded parts.
The combination of low cost per part, high productivity, and established materials make SLS printers, like the Fuse Series from Formlabs, a popular choice among engineers for functional prototyping, and a cost-effective alternative to injection molding for limited-run or bridge manufacturing.
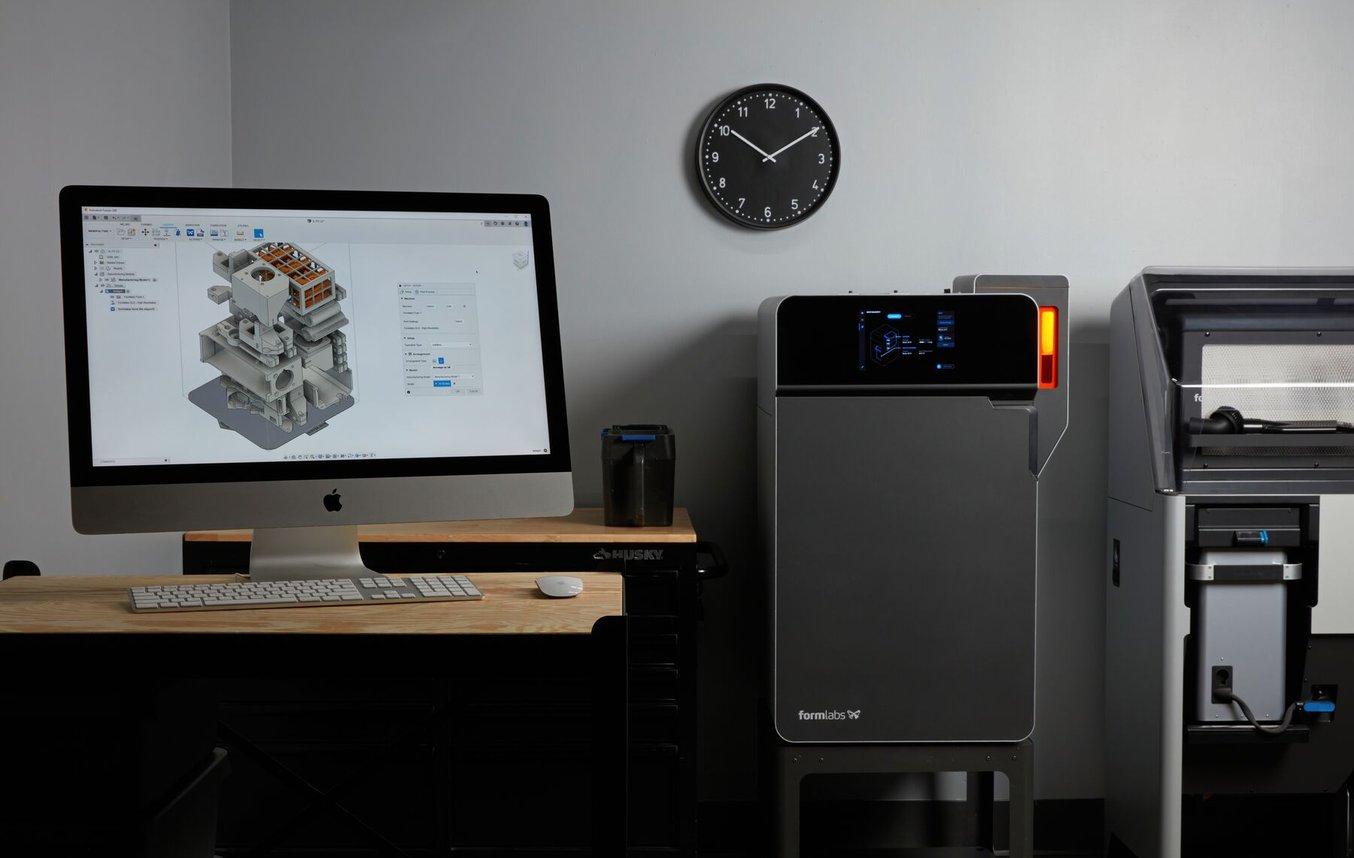
SLS 3D printers are ideal for reverse engineering complex geometries.
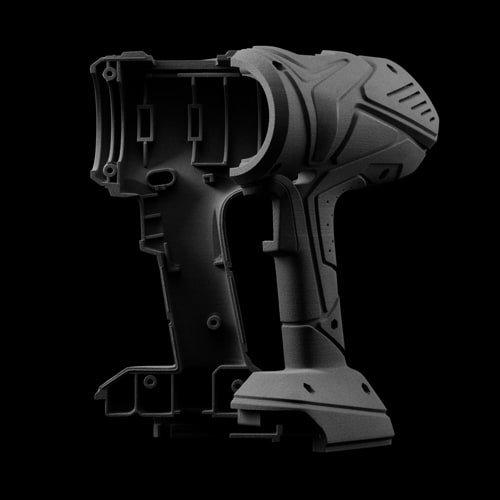
Introduction to Selective Laser Sintering (SLS) 3D Printing
Looking for a 3D printer to create strong, functional parts? Download our white paper to learn how SLS printing works and why it's a popular 3D printing process for functional prototyping and end-use production.
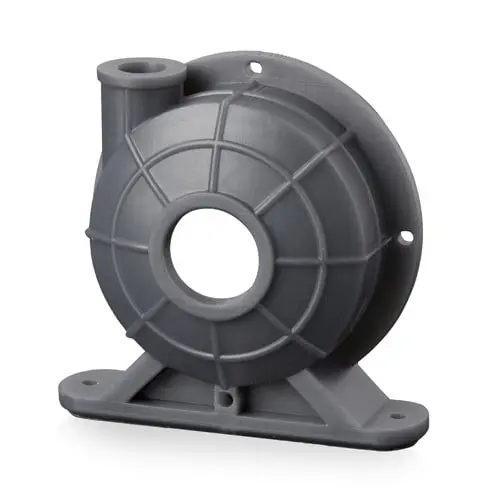
Request a Free Sample Part
See and feel Formlabs quality firsthand. We’ll ship a free sample part to your office.
Case Studies: Reverse Engineering With 3D Scanning and 3D Printing
Reverse engineering has a variety of applications. Let’s look at some real-life case studies where the entire workflow from 3D scanning to 3D printing was used to create custom parts, replacement parts, aftermarket parts, and more.
For the industry giant in automotive aftermarket parts, Dorman Products, reverse engineering is the core of their business model. Dorman analyzes OEM part failures, and reverse engineers the product, in some instances completely rethinking and improving the design. They will often go out and find the original part, sometimes purchasing whole cars in order to fully understand the entire vehicle system and validate the improved design.
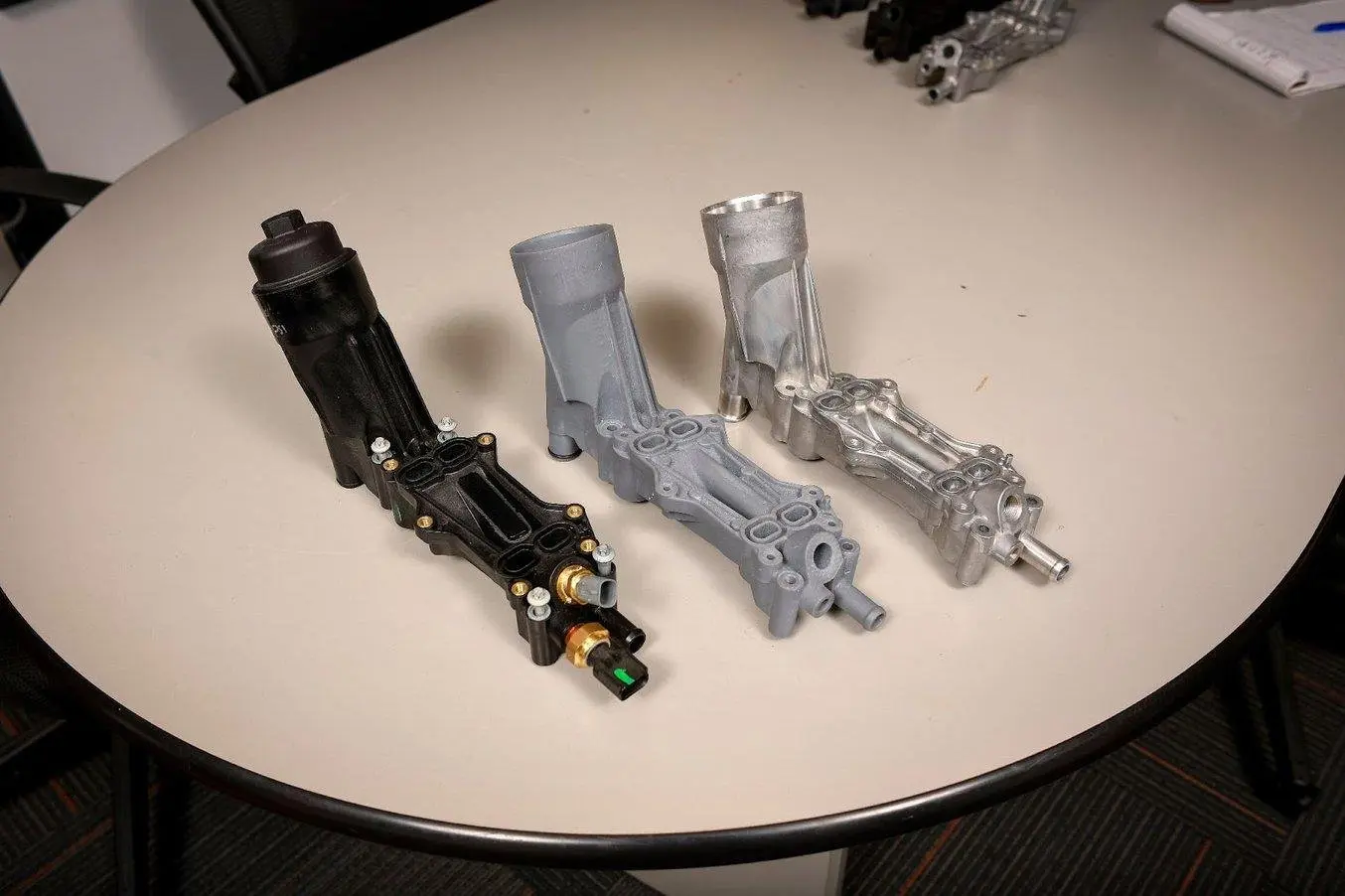
Dorman Products uses Formlabs SLA 3D printers to produce prototypes of their aftermarket products.
Engineers at STS Technical Group used a Creaform 3D scanner and VX Elements software to create a custom gripper for a pick-and-place robot to improve compatibility with a specific fuel injector. The results turned out far superior to the commercial product itself.
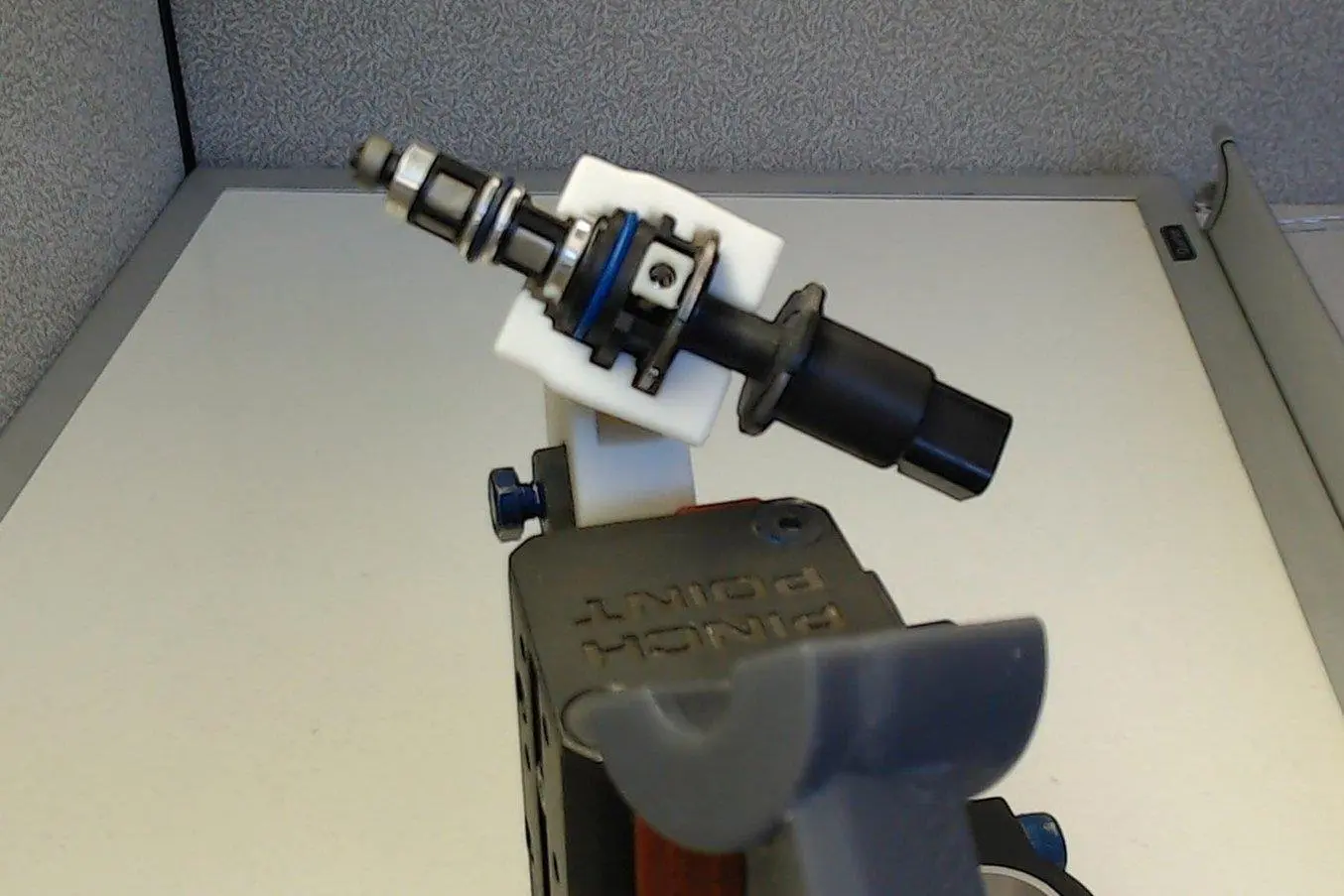
STS Technical Group’s team used SLA 3D printing to produce the custom robot grippers.
In another project, Help3D’s team developed a custom intake manifold for a professional racing bike. They used 3D scanning to generate an accurate model of the four-stroke engine and surrounding assembly and then turned to Fusion 360 to reverse engineer the design. The airtight 3D printed result was created using the Formlabs SLA printer in Rigid 10K Resin and delivered a 10% increase in power output.
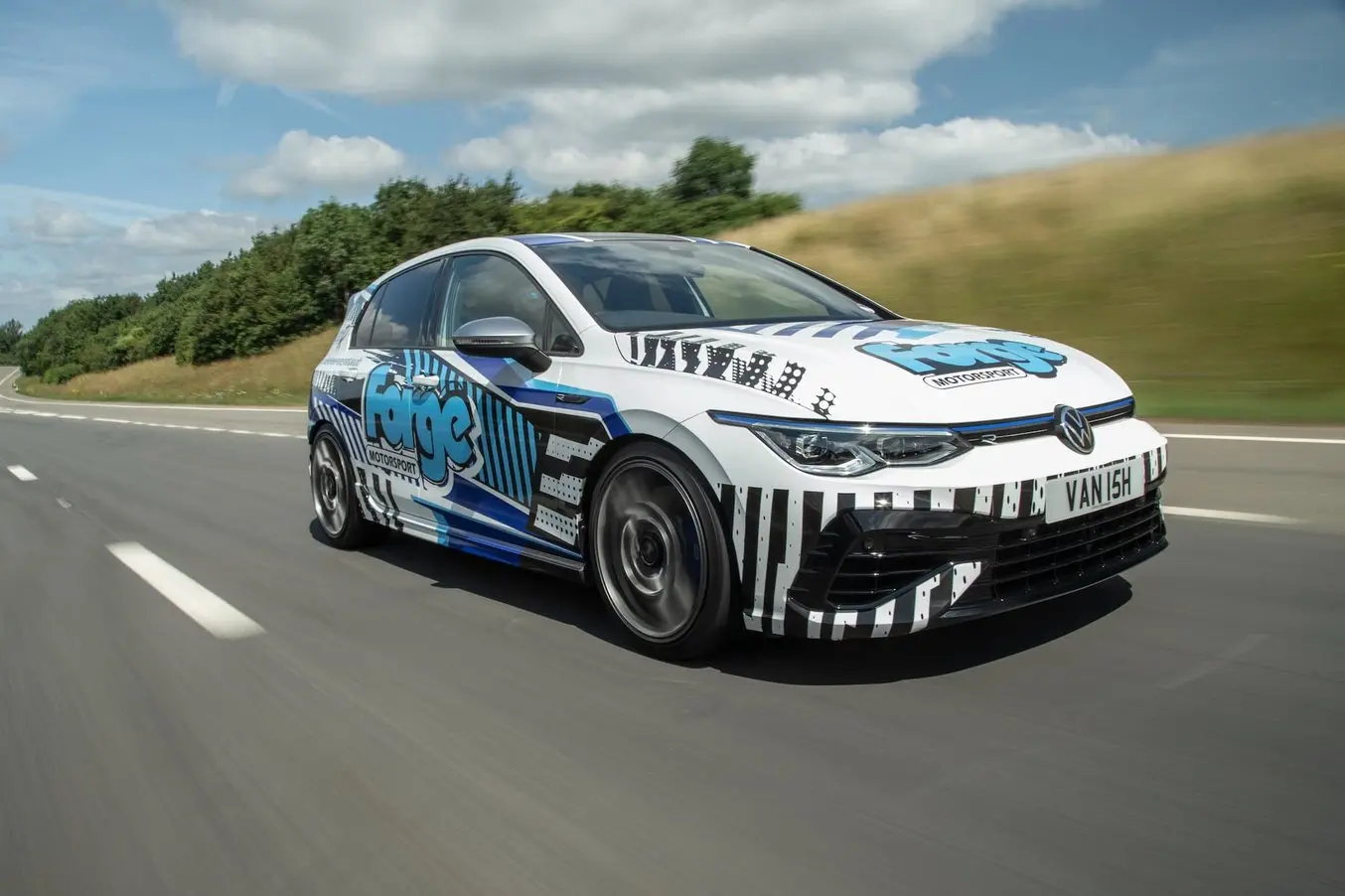
3D Scanning and 3D Printing in the Automotive Industry with Forge Motorsport
In this webinar, Forge Motorsport, manufacturer of performance upgrades for the aftermarket automotive industry, talks about the ways they use 3D printing and 3D scanning technologies to augment their workflows.
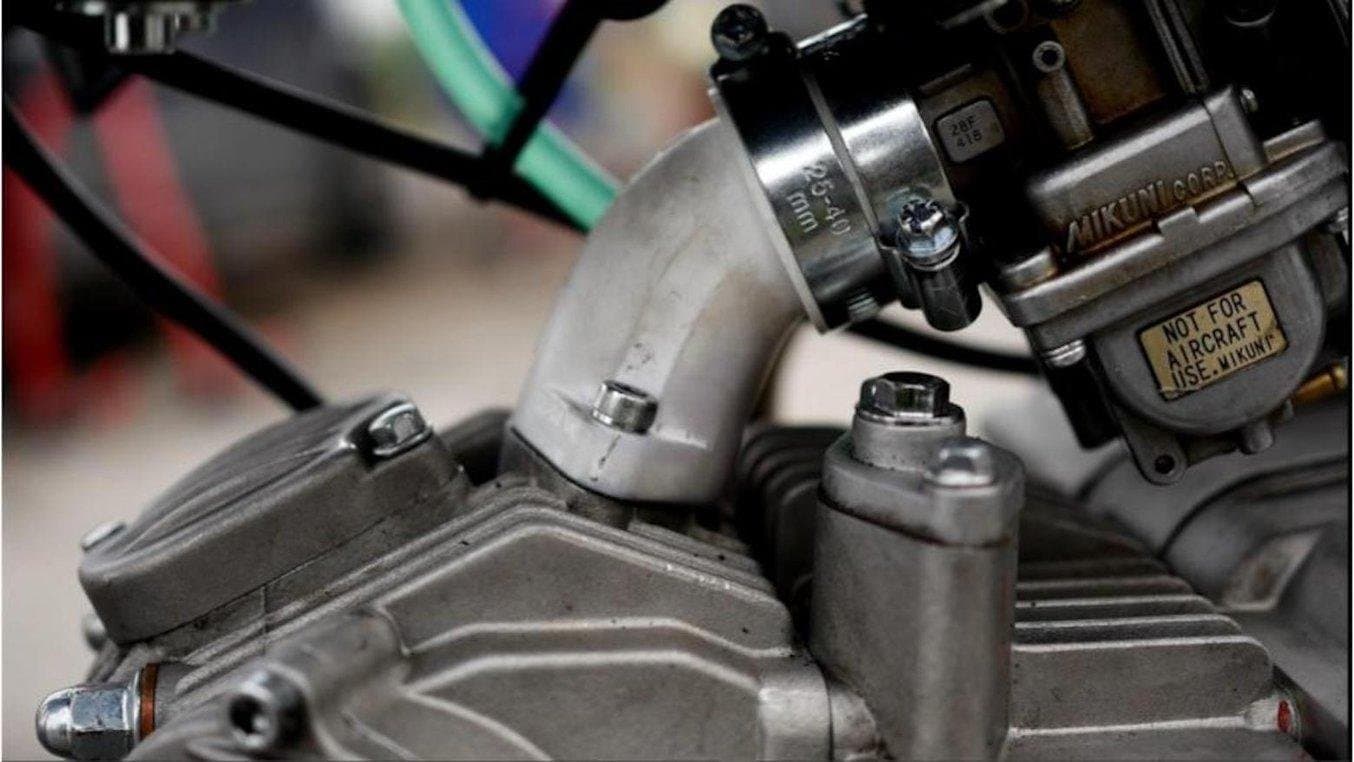
The reverse-engineered manifold was 3D printed using a heat-resistant material.
Reverse engineering capabilities also come in handy for creating replacement parts for industrial production equipment. In one case, Productive Plastics managed to reverse engineer an impeller for a thermoforming machine. They 3D printed a durable replacement part on a Fuse Series SLS printer that was used as a stop-gap solution, helping the company avoid downtime.
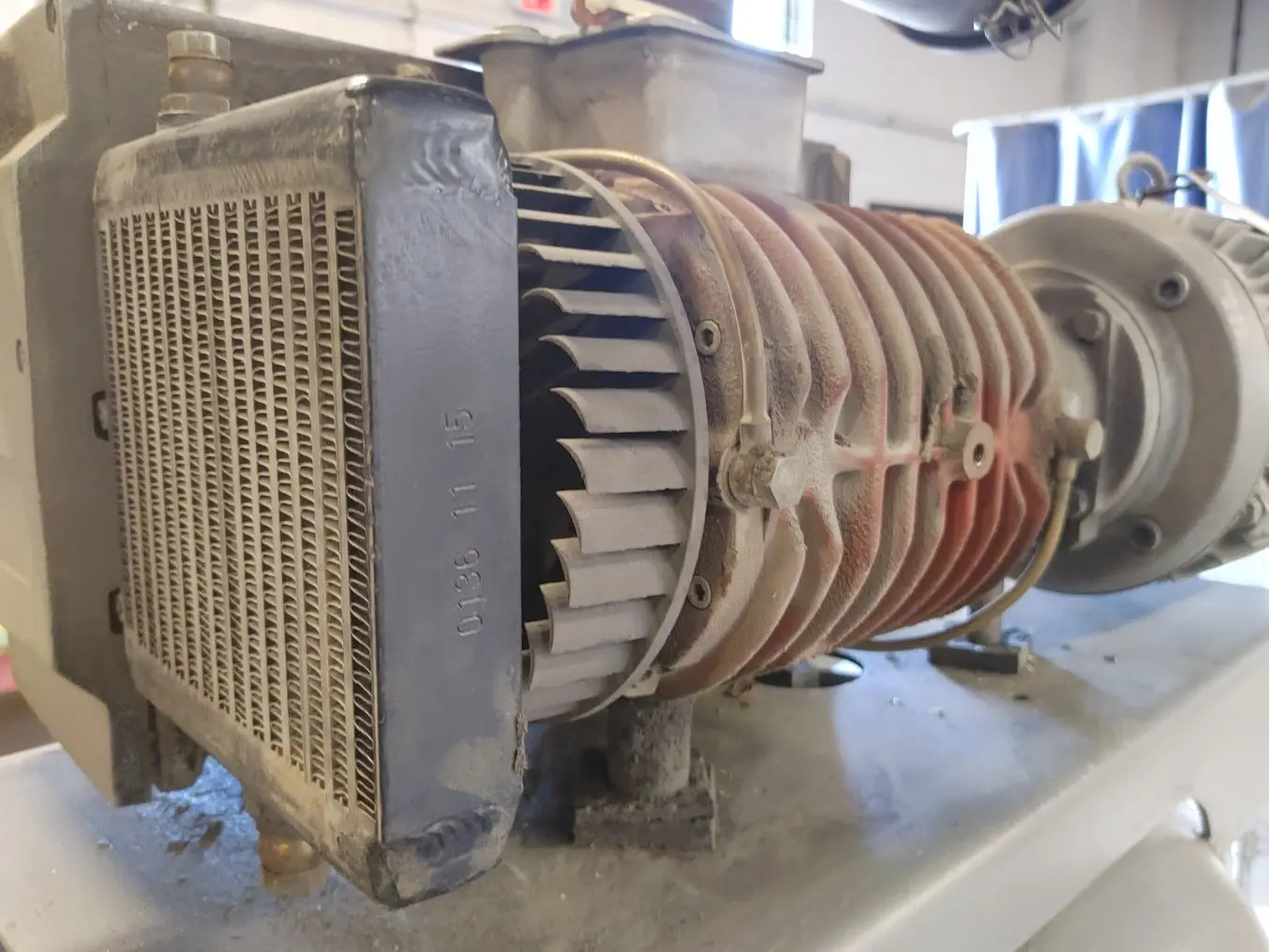
A close up (right) and expanded view (left) of the 3D printed impeller, fitting seamlessly into the industrial thermoforming vacuum pump.
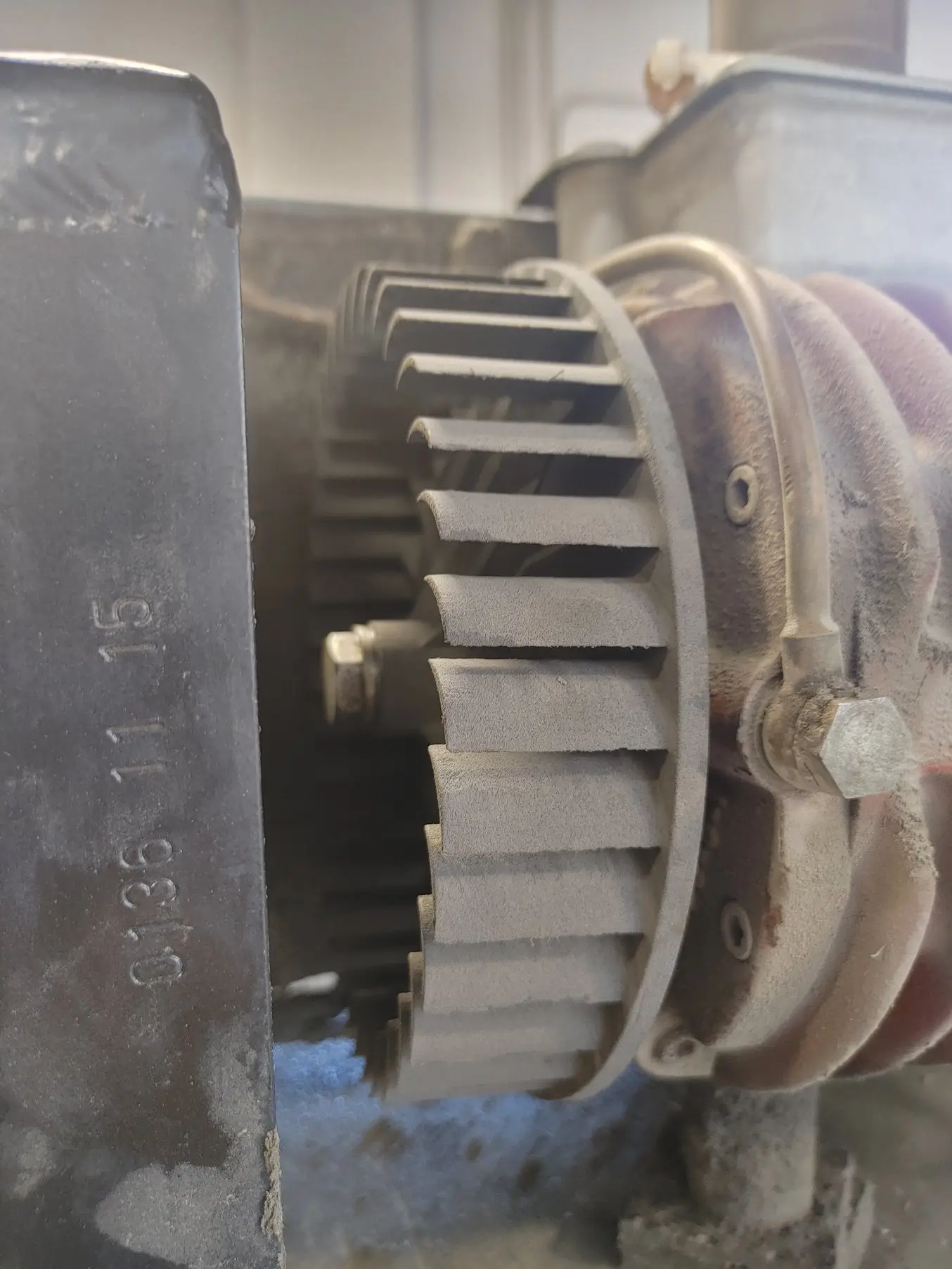
Get Started With Reverse Engineering
Equipped with only a caliper, a pencil, and drafting paper, manual reverse engineering even a simple component used to be a monumental task. Thankfully, those days are over. Modern day reverse engineers possess an impressive array of tools to accomplish awe-inspiring feats.
As we have learned, the contemporary reverse engineering process begin with creating a high-quality 3D scan. The data is then translated into a wireframe that is used for surface remodeling in a state-of-the-art CAD environment where designers and engineers can tweak and improve the part to perfection.
This is especially helpful if engineers have to work with objects that are organic in shape, costly to obtain, lack a digital representation, are in need of revision, or require repair, aftermarket, or replacement parts. With outstanding reverse engineering skills on board, designers are also empowered to scrutinize existing solutions without having to reinvent the wheel.
In all those cases, cutting-edge SLS and SLA 3D printers such as the Fuse Series and the Form 3+ have proven their game-changing worth by delivering same-day professional-quality prototypes and end use parts, enabling companies in all industries to speed up their product development and boost new innovations.