3D Printing Changing the Game: How TUM Boring Printed Strong Parts for their Tunnel Boring Machine
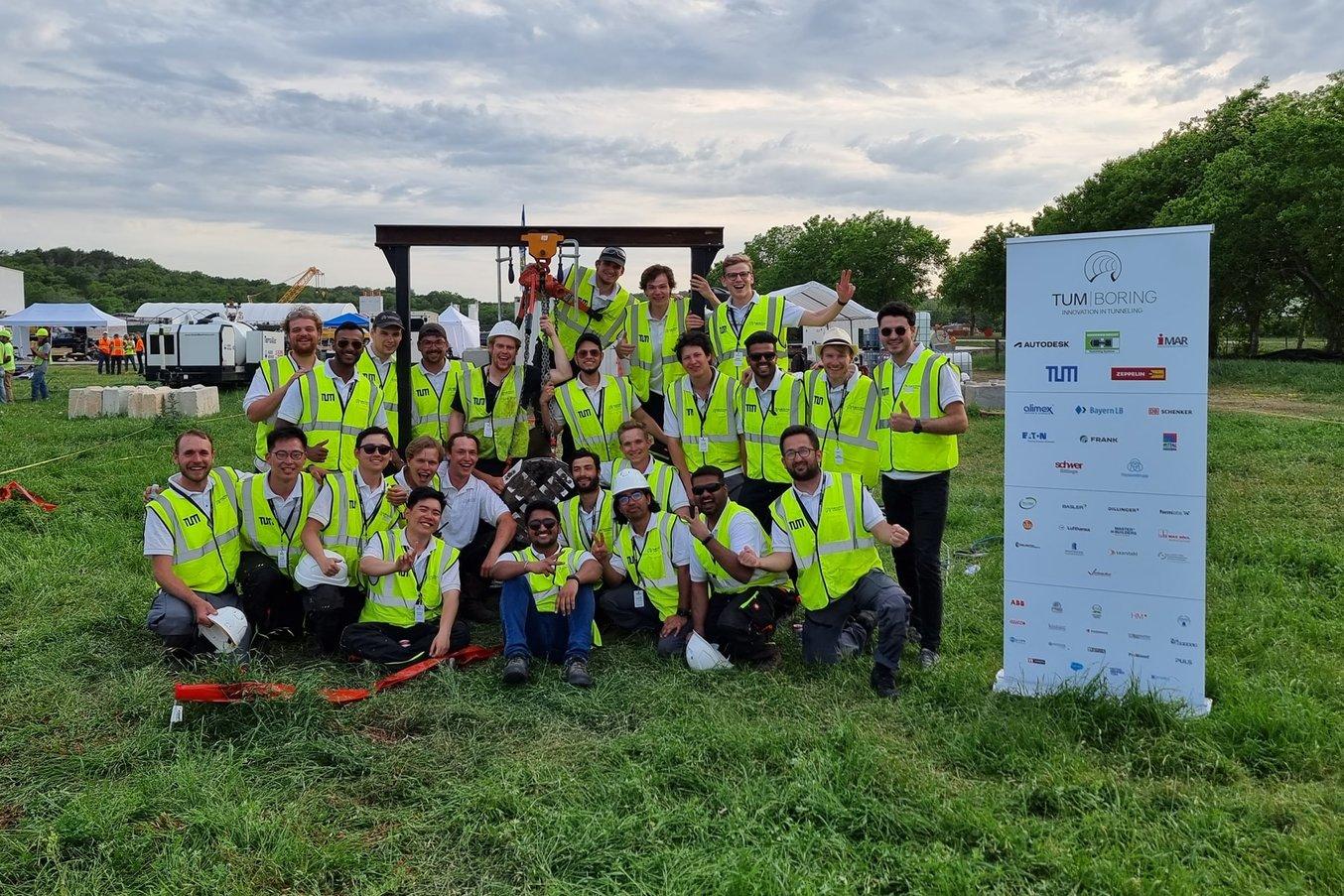
TUM Boring team in Bastrop, Texas in April 2023.
TUM Boring is a student organization from the Technische Universität Munchen composed of more than 60 students originating from 16+ countries. The group came together in 2020 to participate in the Not-a-Boring Competition 2021 from Elon Musk’s The Boring Company (TBC).
The student-led team is dedicated to the future of mobility and aims to build one of the fastest micro tunnel boring machines (TBMs) in the world to drive innovation in the tunneling industry. The competition provided the perfect place to see how their project compares to innovations from around the world.
After winning the competition in 2021, the TUM Boring team got their hands on a Form 3+ stereolithography (SLA) printer and also got to work with Fuse 1+ 30W selective laser sintering (SLS) printed parts. The newly acquired 3D printing technology significantly improved the team’s work processes. From rapid prototyping to end-use parts, the Form 3+ transformed TUM Boring’s day-to-day operations, and helped the team win the second edition of the Not-a-Boring Competition in April 2023.
Discover how TUM Boring made use of 3D printing to create strong, durable parts for their tunnel boring machine, and beat the competition to take home first prize for the second year in a row.
Speeding Up Design Iterations with SLA 3D Printing
Bringing the Form 3+ in-house enabled the TUM Boring team to improve their iterative abilities by a significant margin. To understand how to connect the different pipes within the TBM, the team turned to the Form 3+ to print miniature-scale prototypes of different concept ideas using Grey Resin. This allowed them to visualize the mechanics up close without having to work on the life-size machine immediately, improving efficiency and saving time.
“We could throw something together and by the evening we already have a prototype that’s ready to look at. And based on that, we could make iterations.”
Tom Luca Reinhardt, executive board member at TUM Boring and co-lead of the mechanical engineering team
The students were also able to perform multiple functional testing rounds on a 3D printed cutter wheel component. Printing miniatures of the cutter wheel with slightly different structures in Flexible 80A Resin enabled the team to visualize the product much better than simply through a computer aided design program. Tom Luca Reinhardt affirms, “We have the CAD program but that will only show you so much. It’s always way better to have the physical product in our hands and look at it from different perspectives.”
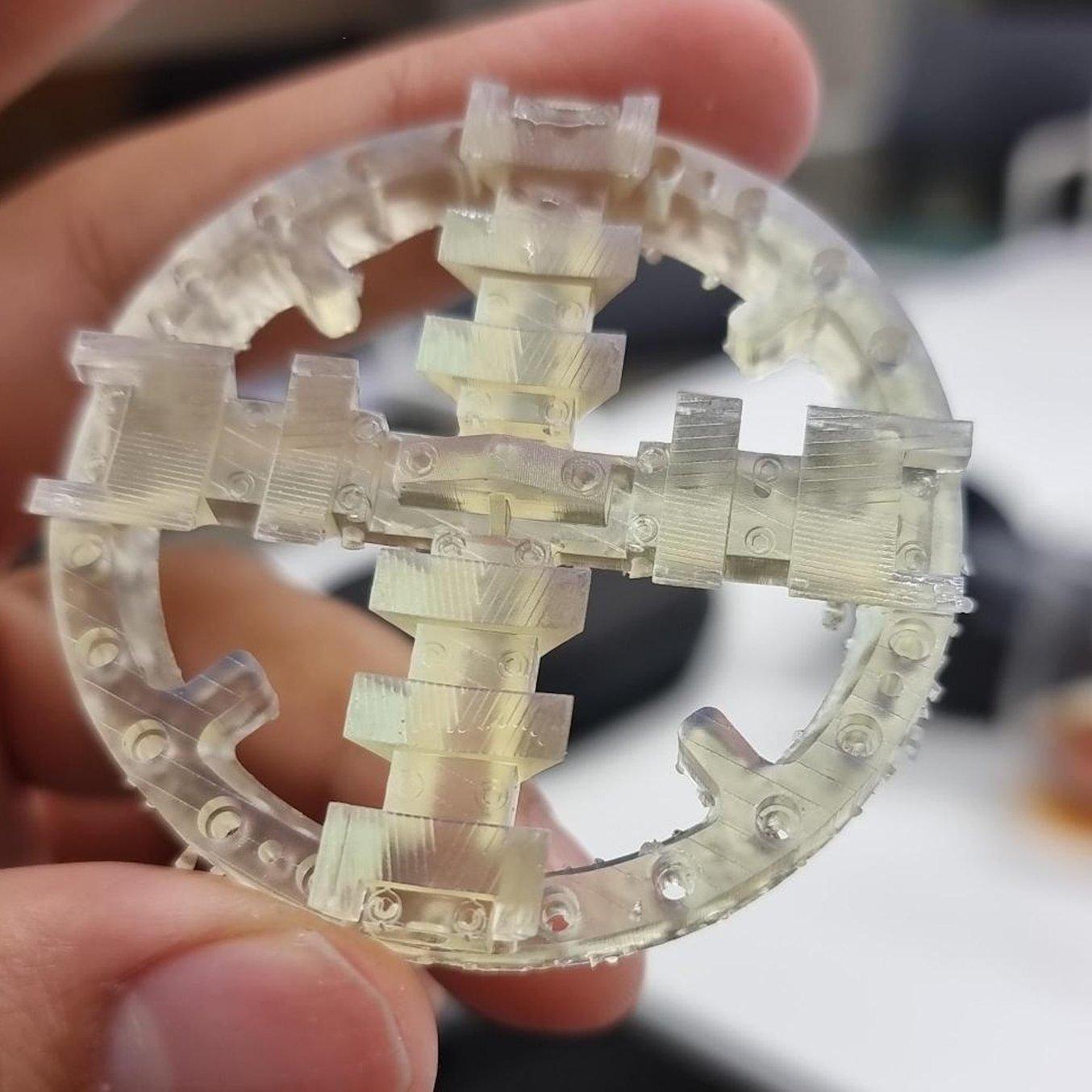
SLA 3D printing allowed the team to visualize different concepts and make iterations quickly and smoothly.
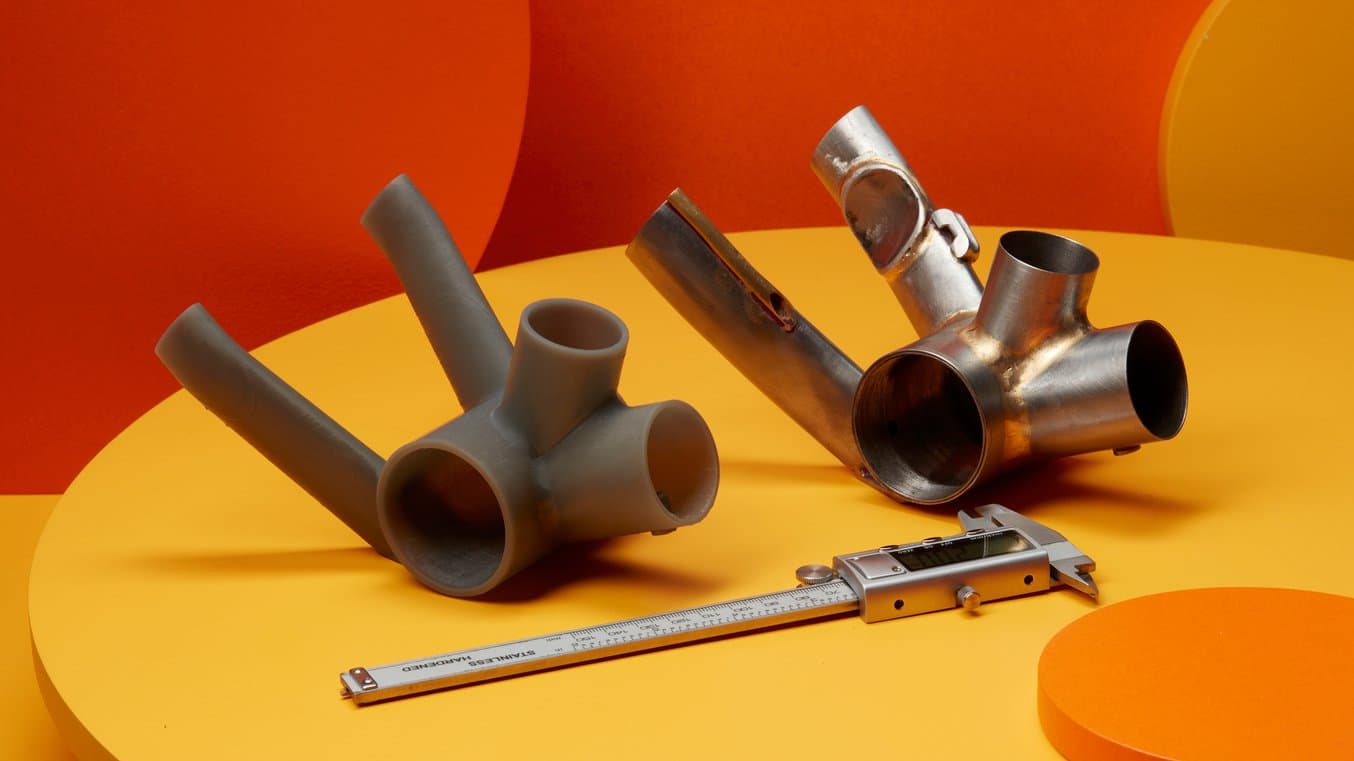
Rapid Prototyping: Choosing the Right Process and Materials
In this webinar, discover how you can create concept models and functional prototypes faster than ever before, as well as execute quick revisions of your designs based on real-world testing.
Manufacturing End-Use Parts with SLA: Efficient and Cost Saving
In addition to prototyping, TUM Boring also used SLA technology to print end-use parts such as screw hole covers and sensor mounts.
On the outer enclosure of the TBM, there are several screw holes that need to be easily accessible in case the cutter-head needs to be disassembled, but also covered to protect the machine from dirt and clay. 3D printing screw hole covers makes it cost-efficient to produce customized parts in low volume that are easily removed and still protect the machine from debris.
Reinhardt noted that this was “quite a big efficiency improvement.” After trying different engineering materials, the team decided to use Grey Resin which requires no additional post-processing and is characterized by its superior surface finish.

The screw hole covers, printed in Grey Resin, allow for easy access to the screws, saving the team time during maintenance.
The low-volume production workflow, the versatility of materials and the superior surface finish of SLA 3D printing enables other types of end-use application as well. The TBM has a large number of sensors and it is crucial that they don’t move out of alignment during operation. This means that each sensor required a custom mount that is strong enough to endure pressure and not break on impact.
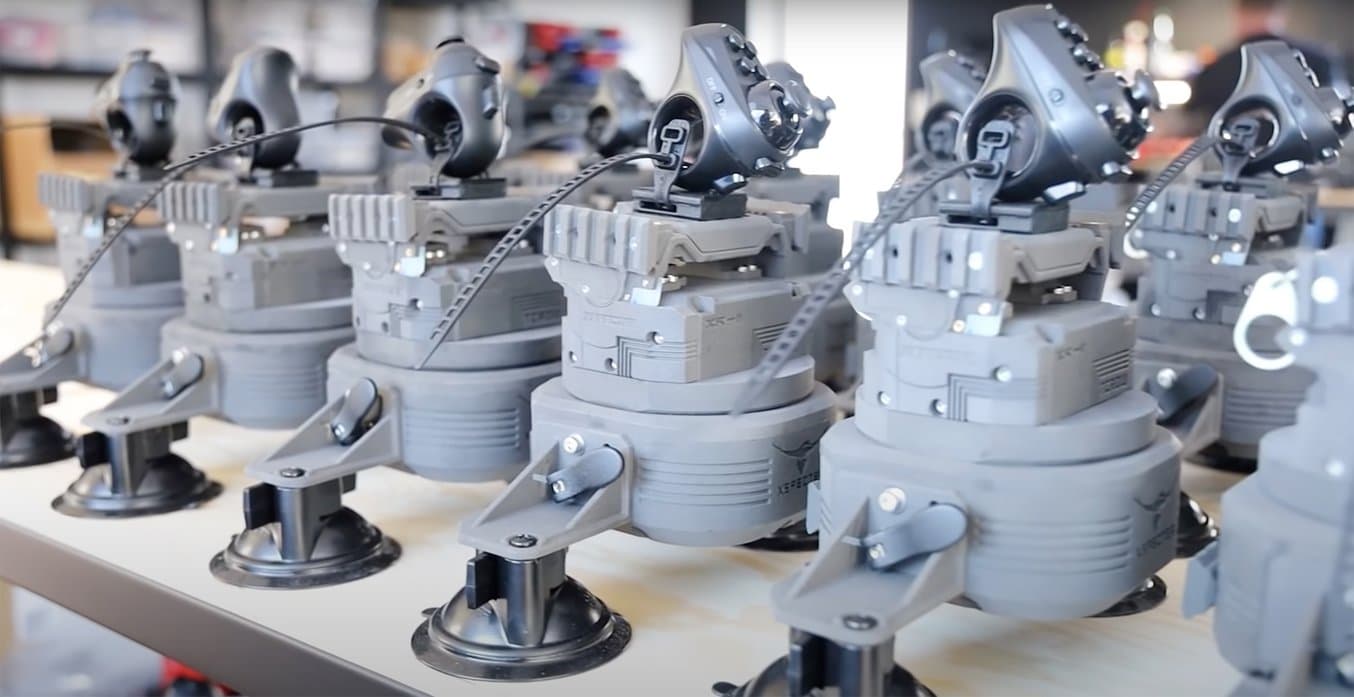
Stress Testing 3D Printed Parts for End-Use Applications
This white paper presents Formlabs 3D printing hardware and material solutions for end-use part production.
Previously produced in stainless steel by a third-party manufacturer, the team optimized this process by printing the sensor mounts on the Form 3+ in Tough 2000 Resin. Outsourcing the parts often took several days, if not weeks, and the costs were much higher than in-house fabrication. Through the use of 3D printing, the team can now simply send the file to the Form 3+ and print the mounts in about four and a half hours.
“With 3D printing, we could just upload the STL file and within a couple of hours we had the finished bracket and could mount the sensor.”
Tom Luca Reinhardt, executive board member at TUM Boring and co-lead of the mechanical engineering team
Among the resins the team tried out, Tough 2000 Resin was the clear winner for this particular application due to its sturdiness and reliability. Indeed, after running some tests, the TUM Boring team established that “it could experience some load” and that it wouldn’t break on impact.
SLS 3D Printed Cutting Tools Stress Tested at High Pressure
In addition to SLA parts, TUM Boring also tested out different cutting wheel structures with SLS printed cutting tools. The Fuse 1+ 30W enabled the team to produce different iterations before establishing the optimal geometry for the competition. The selected design included cutting tools with sharper edges, to cut smoothly through the ground, and flat-edged tools, to withstand more resistance during the boring process. The final geometry was then sent to a third-party manufacturer and produced in stainless steel.
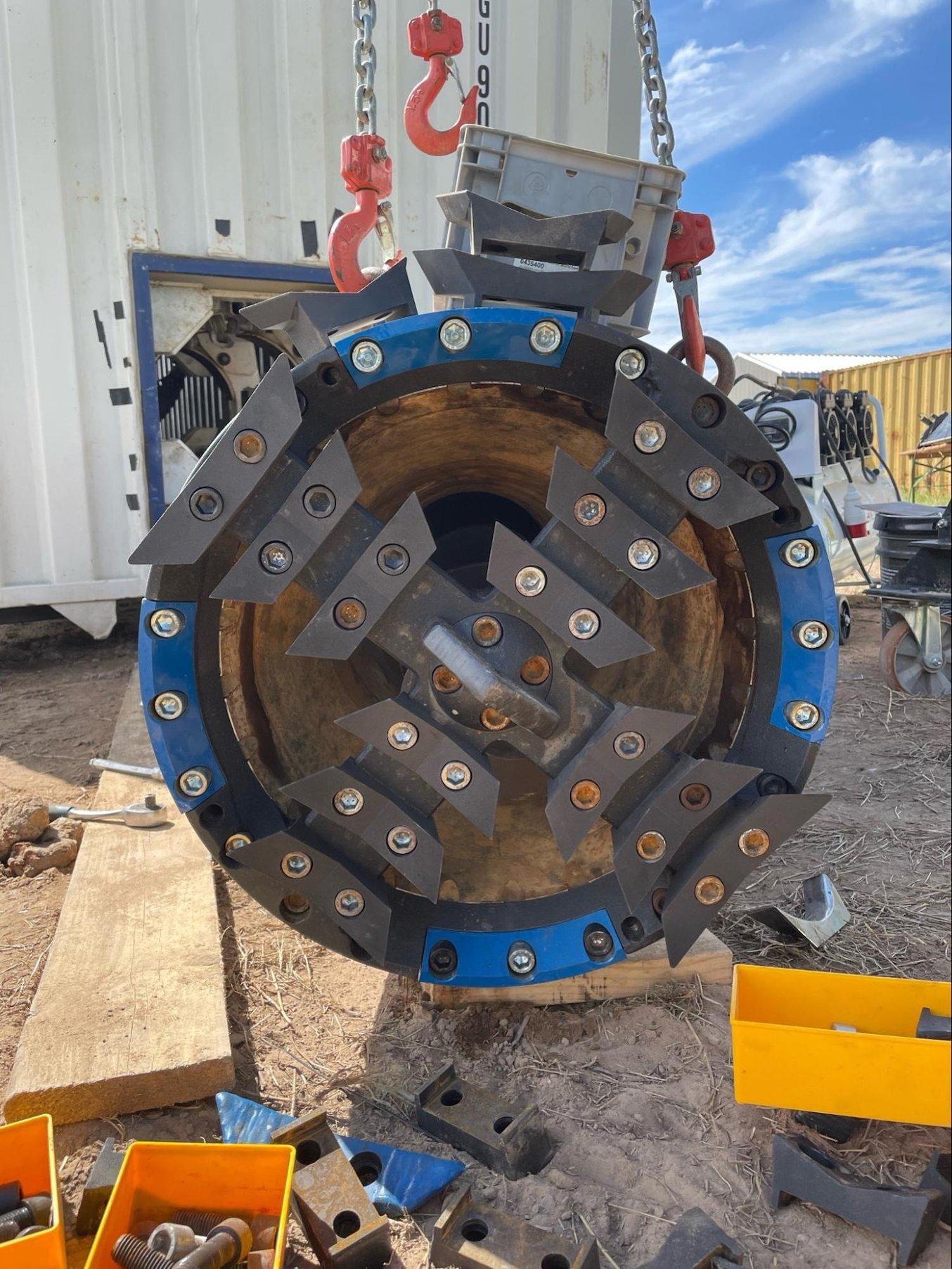
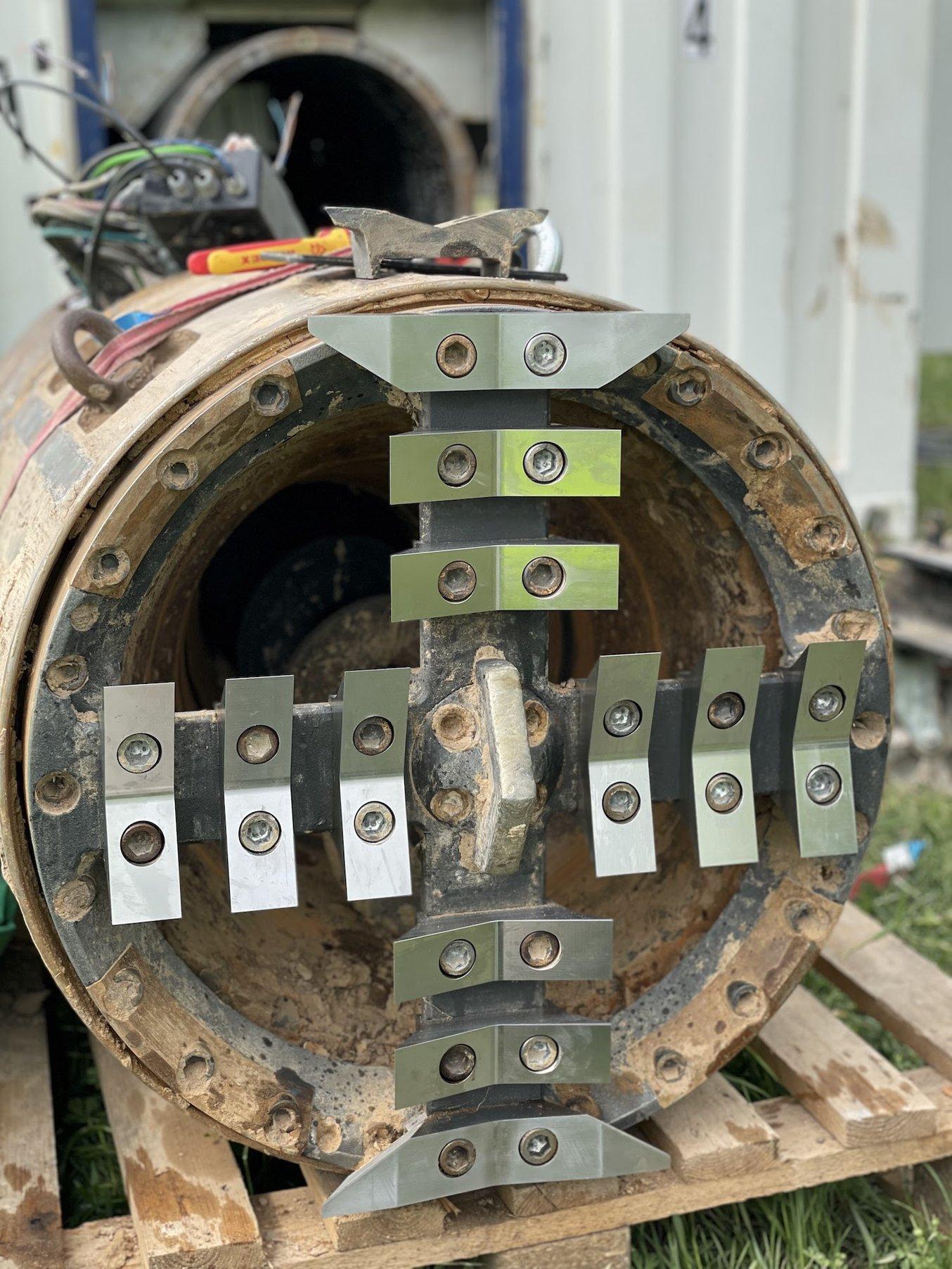
Nylon 11 CF Powder (left) proved to be a lot stronger than the team expected and allowed them to test different versions of the cutting tools on the machine before the stainless steel parts (right) arrived.
Among the various SLS Powders offered by Formlabs, they found Nylon 11 CF Powder to be the best material for this application since durability, stiffness, and impact resistence were crucial requirements. During functional testing, the parts undergo high amounts of pressure and impact force.“We applied so much force against the ground with these parts, that we were able to move our 15 ton container, and we didn’t see any breakage on them,” Reinhardt adds. In fact, the team was pleasantly surprised when these very light parts stood the test of force; there was no sign of cracks or breakage.
After running a couple tests, the team observed slight signs of wear on the carbon fiber printed cutting tools but much less than what the team expected. Additionally, after the competition they noted that the carbon fiber prototypes and the end-use stainless steel parts had about the same signs of wear and damage, showing the strength and durability of Nylon 11 CF Powder. “It surprised a lot of the members, especially the ones that didn’t believe in 3D printing, or didn’t really trust the 3D printing process that much. So, it was good to prove them wrong,” says Reinhardt.
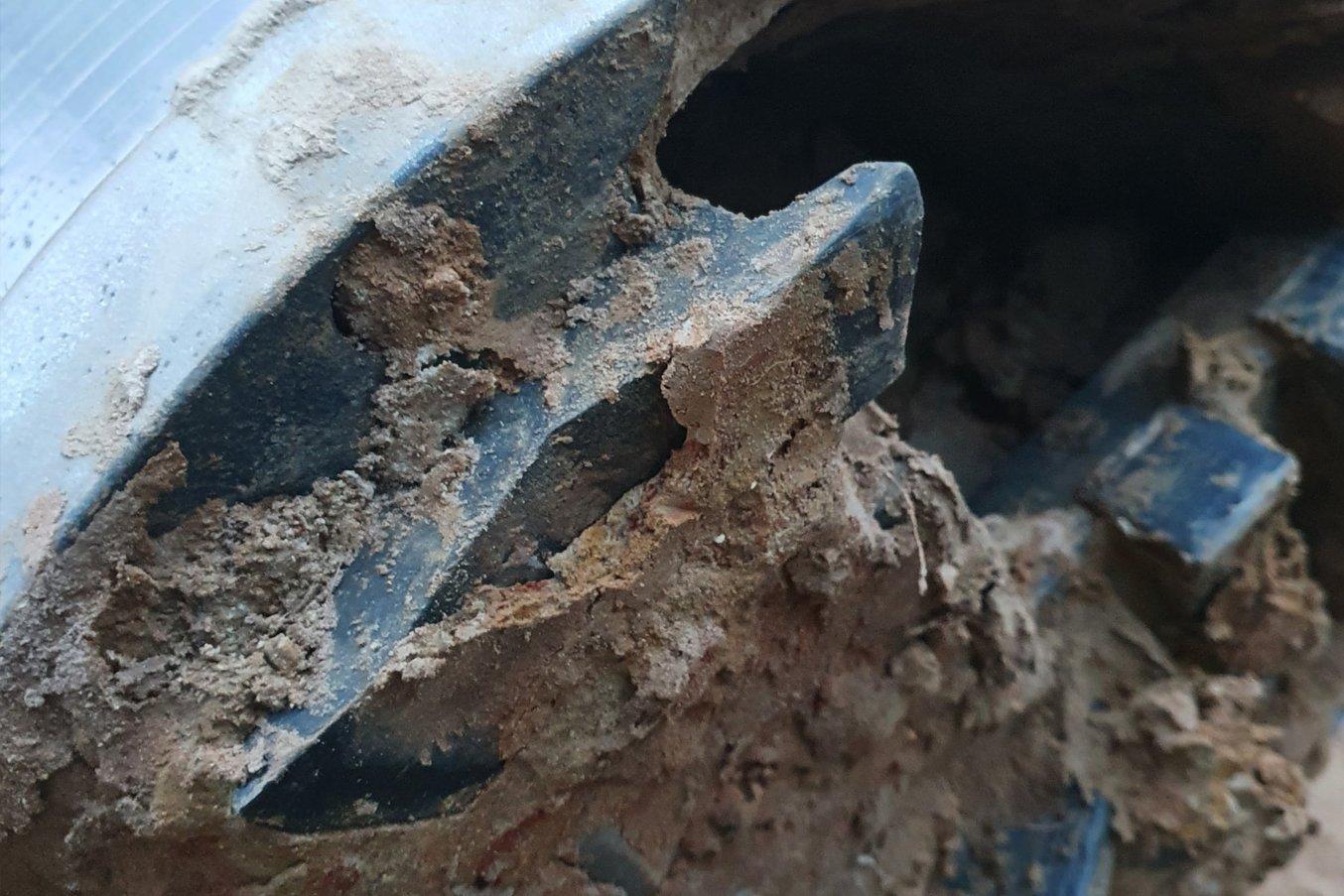
The carbon fiber 3D printed prototypes (pictured here) and the end-use stainless steel parts had about the same signs of wear and damage.
In the tunneling industry, the clay that is excavated can create a major problem by sticking to the cutting wheel of the boring machine. The clay will harden and completely block the wheel, leading to significant delays in the tunneling process. Additionally, if the cutting tools suffer from corrosion, they will impact the quality and precision of the machine. In such a demanding context, the corrosion resistance and anti-stick properties of Nylon 11 CF Powder was an unforeseen and impactful benefit.
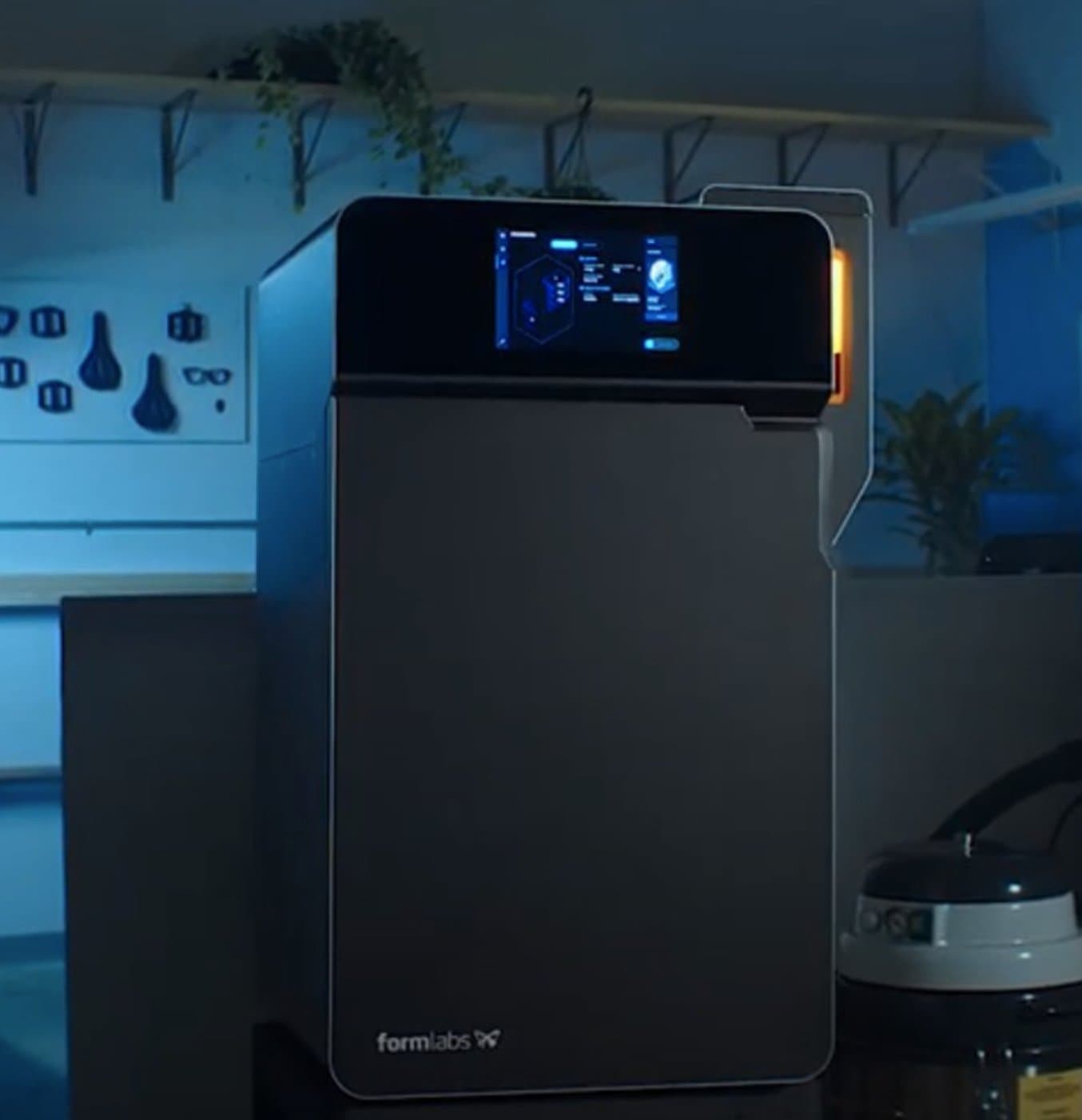
Outsourcing vs. In-House: When Does it Make Sense to Bring SLS 3D Printing In-House?
In this whitepaper, we evaluate the value proposition of bringing SLS 3D printers in-house, in comparison with outsourcing SLS parts from a service bureau.
Redefining Efficiency in the Tunneling Industry
“[This experience] gave us quite a bit of confidence to try different things in the future, and relying more on 3D printing as well.”
Tom Luca Reinhardt, executive board member at TUM Boring and co-lead of the mechanical engineering team
After winning twice in a row, it hasn’t been confirmed yet whether the team will be participating in the next edition of The Boring Company’s Not-a-Boring Competition. If one thing is certain, it’s that the team will strive to continue developing its use of 3D printing and incorporate it into their future projects.