近年では、度々3Dプリントで製作された多くのものが様々なメディアで報道されてきました。1家に1台3Dプリンタがある暮らしといった未来を予測する向きもありますが、その詳細までは未だ固まっておらず、まだ実現には至っていません。しかし歴史の浅さや実用化された事例の少なさにも関わらず、3Dプリントが多くの可能性を秘めている事実は否定し難いものです。
初期の大々的な報道の一部は、拡大解釈や誤解を生んでしまったという意味で3Dプリントが本来持っている業務用途での可能性を覆い隠してしまった側面もあります。一方で、高性能なデスクトップおよびベンチトップサイズの3Dプリンタが多数登場したことで、現在では様々な企業が活用の幅を拡大し、お客様により良い製品を提供できるようになっていることも事実です。。
では実際のところ、3Dプリンタでは何ができるのでしょうか?本記事では、3Dプリントの「意外な」活用事例25件をピックアップし、幅広い用途での3Dプリントの可能性をご紹介します。
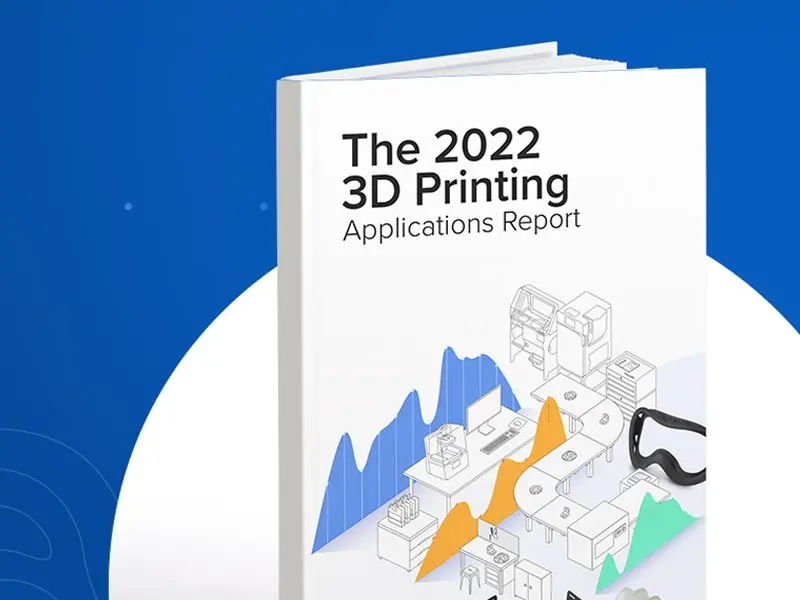
2022年 3Dプリント活用事例レポート
3Dプリント使用歴が比較的長いアーリーアダプター層となる企業と、直近3年以内に導入した企業における3Dプリントの活用法を比較し、今後のトレンドに関するインサイトも提供する業界初のレポートです。
未来の車を創造する
3Dプリントでサプライチェーンに大きな付加価値をもたらすだけでなく、より広い用途への活用の可能性も広がります。3Dプリントはますます使いやすく、価格的にも手頃になり、アディティブマニュファクチャリングによる内製で製造現場を支えています。新たに登場した様々な軟質の3Dプリント用材料は、量産品と遜色ない高精度かつ高機能な3Dプリント品の製作を可能にし、カスタマイゼーションや高パフォーマンスな生産を続々と実現しています。工業用デザインスタジオのVital Autoは、この技術のすべてを駆使して忠実な試作品やコンセプトカーを製作しています。複数台の3Dプリンタによる内製を始め、様々な高機能ツールを使って試作・検証プロセスを迅速に繰り返すことができています。
「弊社では創業当初から3Dプリントを活用しています。製造工程に3Dプリントを導入しようと思ったのは、コスト削減のためだけではなく、お客様がさまざまなデザインやアイデアを実現できるようになると考えたからです」と語るのはデザインエンジニアのAnthony Barnicott氏です。
自動車業界はこれまでも、自動車製造の様々な場面でアディティブマニュファクチャリングがもたらす価値を目の当たりにしてきました。ラピッドプロトタイピング以外にも、3Dプリントの用途は様々あります。
- カスタム品や複雑形状の部品、高機能部品の製作
- 金型や治具の製作
- 交換部品やスペアパーツのオンデマンド生産
- 外部委託に比べてコストと製作時間を最大90%削減
パーフェクトフィットのヘッドホン
近年の3Dプリント技術の進歩が、オーディオ業界に大きな変化を起こし始めています。オーディオや騒音防止、消費者向けオーディオ製品業界向けに、カスタムフィットのイヤホンのデジタルプリントがかつてないほど手頃な価格で実現できるようになってきています。近年、3Dプリントメーカーが皮膚に触れても安全な生体適合材料を市場に投入したことで、耳模型やヘッドホンのイヤーチップなどの内製が可能になりました。
カスタムフィットのイヤホンは、ユーザーの耳に完全にフィットするよう設計することで、一人一人に合わせた音楽体験を提供します。快適さとノイズキャンセラ機能の効果が向上するだけでなく、イヤホンが耳から外れない確実な装着感が得られます。
「より没入感のある音楽体験を提供する、カスタムフィットのコンセプトに期待しています。FormlabsはSennheiserのイノベーションの駆動力です。試作品でカスタマーエクスペリエンスが向上していることが、その証と言えるでしょう」
Sennheiser AMBEOイマーシブオーディオディレクター、Veronique Larcher氏
カスタム生産で発生する課題は、Formlabsの画期的な3Dプリント技術とモバイルスキャン、機械学習の組み合わせで解決できます。製作期間が4日から翌日納品、あるいは当日納品に短縮されることで、顧客がカスタムフィットのイヤホンにアクセスしやすくなります。
次世代の手術器具を3Dプリントで
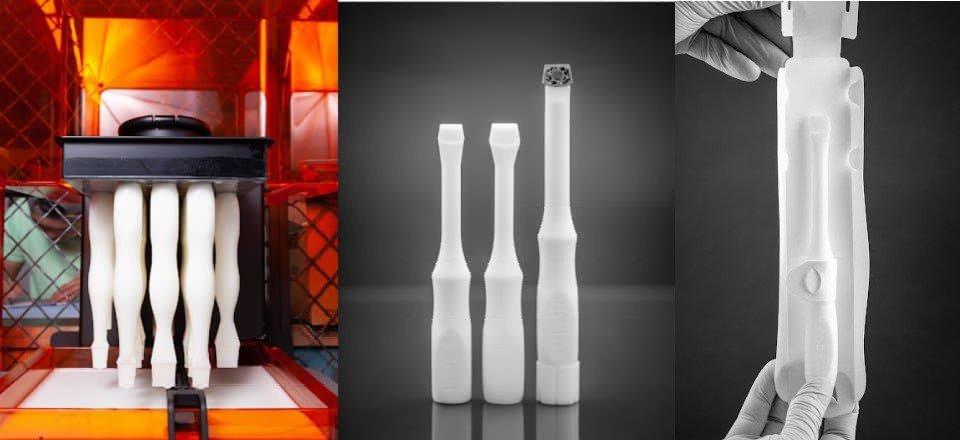
restor3Dのツールを3Dプリントしている様子。隣の写真は最終的な形状。
10年前は、高度な医療機器の製作から患者専用の手術ガイドの製作まで、3Dプリントが医療業界に及ぼす多大な影響について語る人はほとんどいませんでした。誰もが予想していなかった企業の1つに、restor3dがあります。restor3dは、3Dプリントを活用して頸椎インプラント専用に手術ごとに必要なポリマー器具を製作し、外科治療を劇的に改善しています。
restor3Dの生産ラインにはFormlabs 3Dプリンタが25台以上も設置されており、すでに次世代の手術器具を生産しています。手術ごとに専用の個別包装の無菌器具を生産できる仕組みで、実際に器具を使用する外科医には以下のようなメリットがあります。
- 大型・高額な手術用トレイの置き換え
- 設計の試作・検証を繰り返し、外科医の好みに基づいて新しい器具や機能を迅速に導入する能力
- 病院のサプライチェーンおよび滅菌コストの劇的な削減
組織工学研究の加速
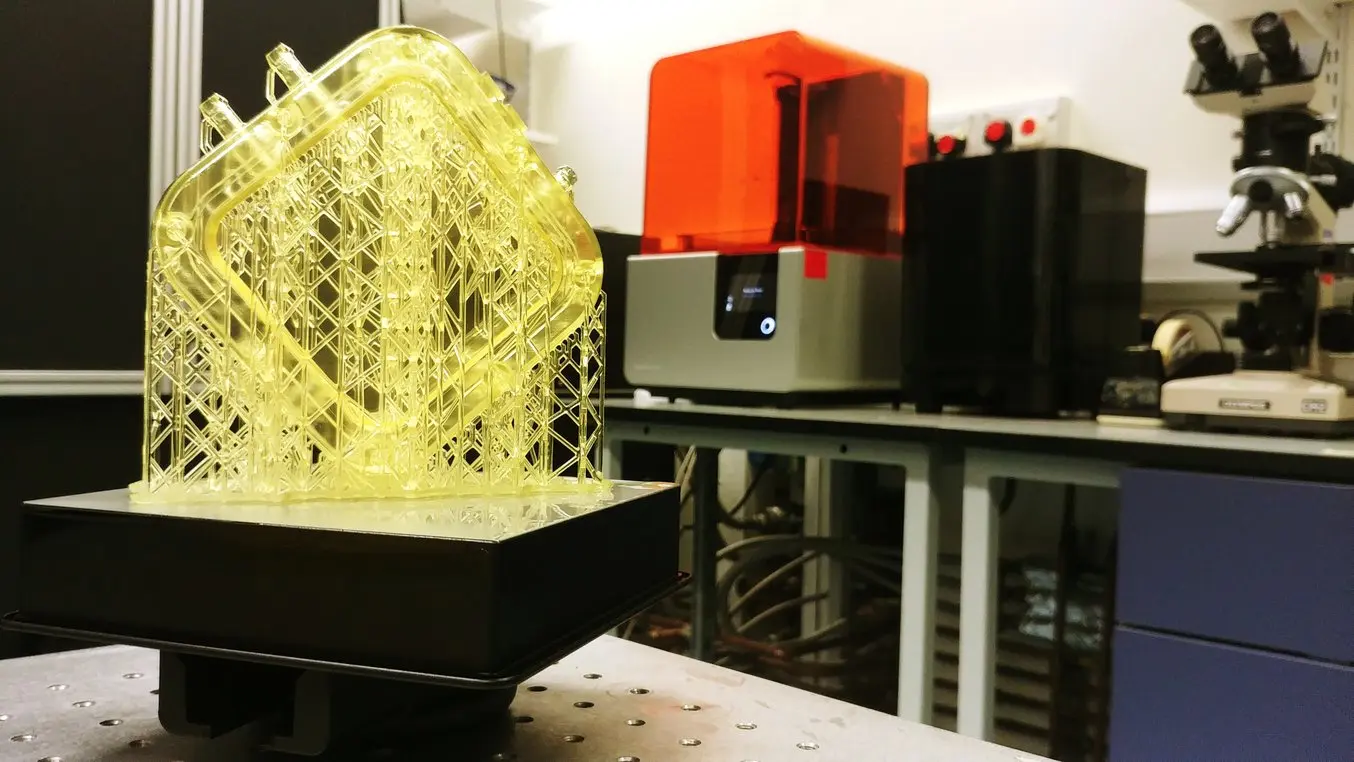
ここ数年で3Dプリント技術が進化する中で、さらに大きな影響を与える可能性のあるユースケースも現在開発が進んでいます。そのうちの1つが、3Dプリント製の臓器です。
新しい臓器を簡単に作れる。これは、再生医療に携わる科学者が何十年も夢見てきた状態です。まだ初期段階ではありますが、3Dプリントを活用した移植に適した有機組織の製作は、早くも実を結びつつあります。
率いるのは、シェフィールド大学のSam Pashneh-Tala博士です。博士の研究では、高精細なデスクトップ光造形3Dプリンタを使用して、様々な形状の組織工学的な血管の製作を可能にします。これにより患者に適した血管移植片の設計が可能になり、外科手術の選択肢が改善される他、現在世界の死因第一位である心血管疾患に苦しむ人々のために、新しい血管医療機器の個別の試験プラットフォームを提供できます。
「体内の血管により近い形状を作ることができる、というのが他と違うところです。これによって手術の選択肢が広がるだけでなく、患者一人一人に合わせた血管のデザインが可能になるかもしれません。精密な造形が可能で価格も手頃な3Dプリンタがなければ、このような形状を実現することは不可能だったでしょう」とPashneh-Tal博士は述べています。
都市に命を吹き込む
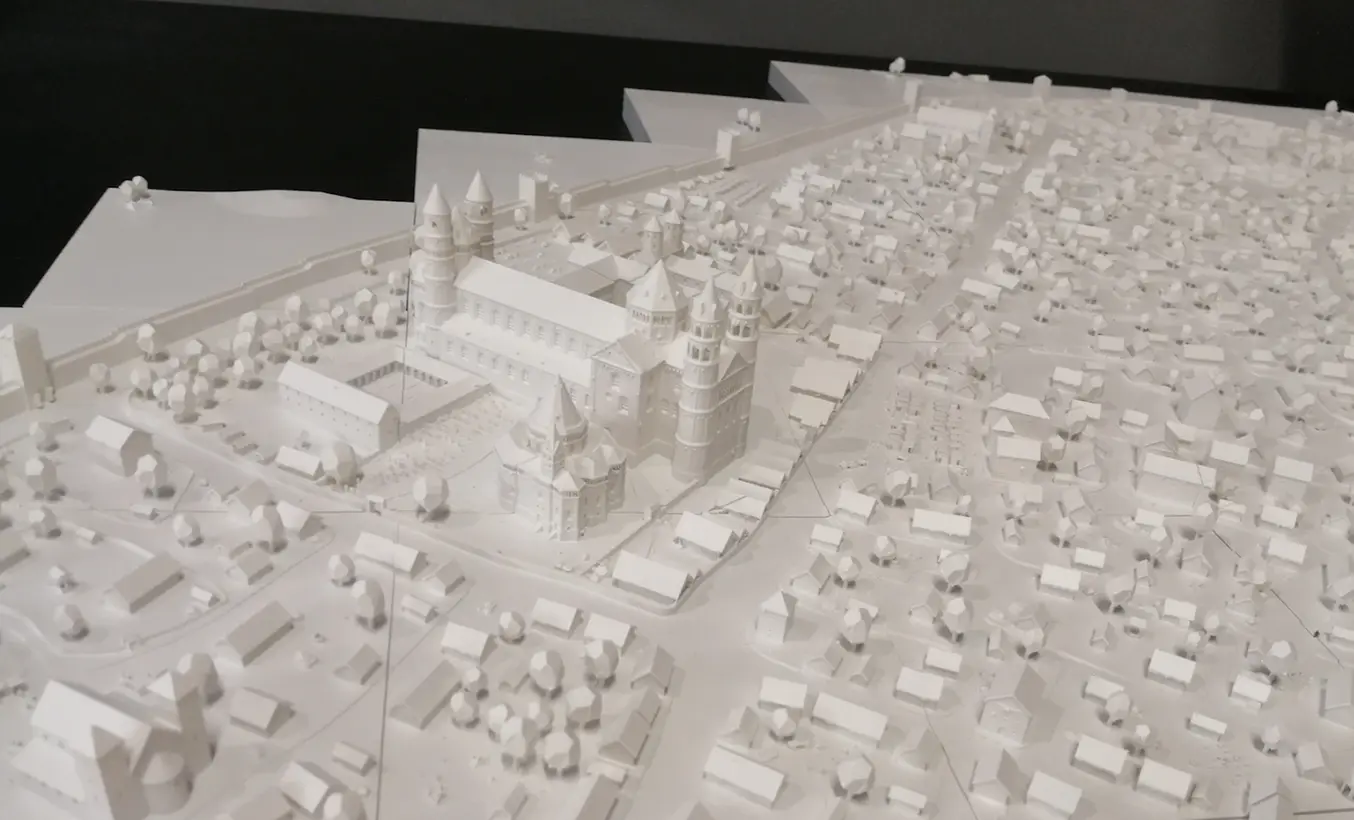
2つの時代を跨ぎ、3つの都市が復元された。650以上のセグメントを、FormlabsのWhiteレジンを使ってそれぞれ12x12cmの大きさで製作。
幾何学的デザイン、試作品製作、モデリングに基づいて進む建築業界は、3Dプリントの進歩で多大なメリットを享受しています。
模型製作にかかる時間を削減できるだけでなく、建築家は3Dプリント製の模型で特定の設計形状の効果をより確実に予測できるようになります。例えば、より多くの材料を使って製作した模型を観察することで、建物を通る光の流れなど、様々な要素を高精度に測定できるようになります。
しかし、3Dプリントが活用されるのは単一の建築モデルだけではありません。都市一体を復元している組織もあります。マインツ専門大学応用科学建築研究所です。3つの都市をそれぞれ西暦800年と西暦1250年の状態を元に復元し、計6種類の都市の見事な大規模模型が出来上がりました。模型は650以上のパーツからなり、そのすべてを光造形3Dプリントで製作しました。
高機能フットウェア用部品の制作
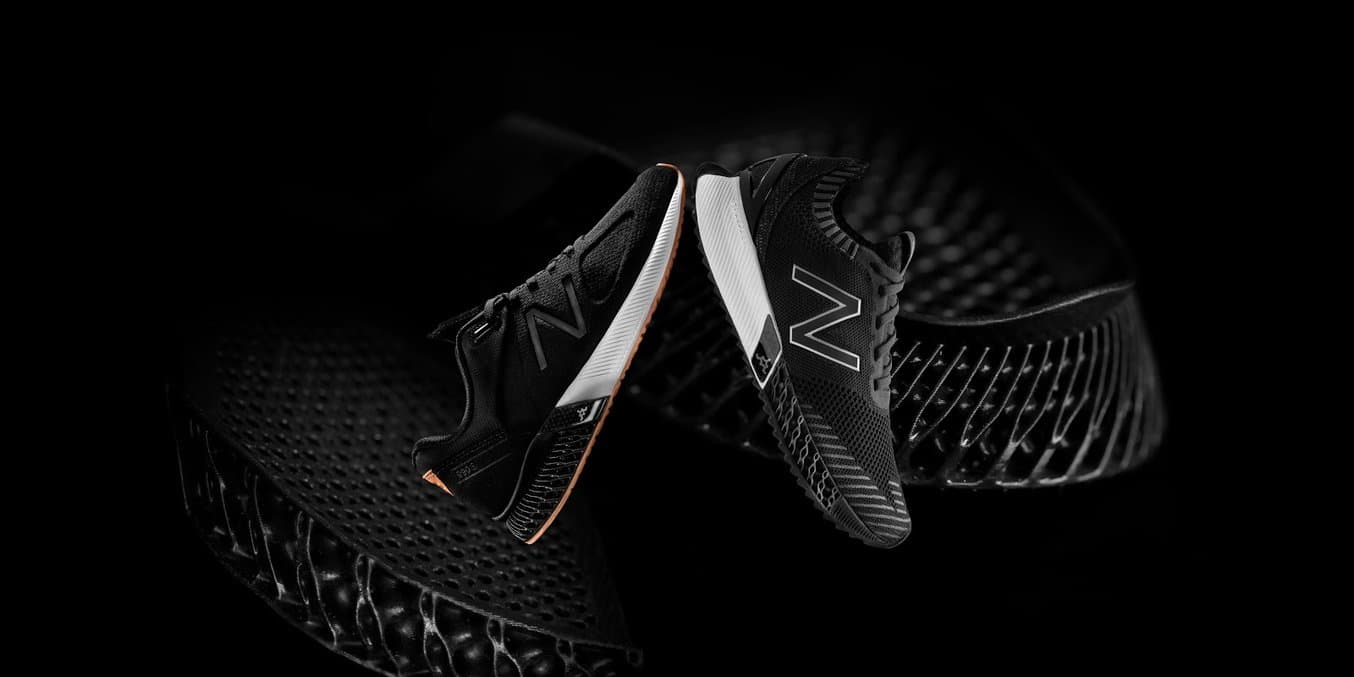
990S TripleCellとFuelCell Echo Triple 990S。
スポーツフットウェア業界は長年、製品のパフォーマンス改善のためにテクノロジーを駆使してきました。中でも、製作工程のデジタル化によってカスタマイズの幅がこれまでにないほどに広がりました。
New Balance、Adidas、Nikeといった大手ブランドがアディティブマニュファクチャリングの力に注目し、3Dプリント用材料を使ってカスタムのミッドソールを大量生産する予定です。他の業界と同様、製作工程のデジタル化により従来の製造方法を強化し、各製品の重要かつ高度にカスタマイズされた部分の製作を3Dプリントに委ね、それ以外の箇所は従来の方法で製造を行います。
フットウェアに要求されるユニークな特性を考慮し、New BalanceはFormlabsと提携して、アスレチックシューズの日々の磨耗や損傷にも耐えられるカスタムの3Dプリント用材料を開発しました。シューズに使用する材料は、様々な環境で1日に何千回も異なる圧力に晒されることになります。バネのような弾力性のある格子構造を製作できるよう設計されたReboundレジンは、Formlabsの他のどの材料よりもエネルギーリターンや引裂強度、伸び率が遥かに高くなっています。Reboundレジンは、ガスケットやシール、自動車の内装にも使用できるほどの強度と、靴底にも使用できる軽さと柔軟性を備えています。
「ランナーにこれまでとは全く違う体験を提供できることが、本当に楽しみです」
New Balance Innovation Design Studio フットウェア部門GM、Katherine Petrecca氏
現代のストーリーテリングを再考する
ハリウッド映画の制作現場では3Dプリントが既に導入されていて、実用的な視覚効果やコスチュームに広く活用されています。
かつて、映画で登場する素晴らしいクリーチャーの製作には非常に細かな手作業が必要でしたが、納期のプレッシャーと時間的な要件が厳しくなった現代の映画制作現場では、実用的な効果をより迅速に製作する方法が欠かせません。Aaron Sims Creativeなどのエフェクトスタジオは現在、エフェクト制作工程をデジタル化で強化するというハイブリッドなアプローチを用いて、新たなコラボレーションの機会を創出し、短期間でアイデアに命を吹き込んでいます。
「デモゴルゴンは、Formlabsの3Dプリンタを使った最初の造形品の1つです。その仕上がりに驚いたのを覚えています。3Dプリントはこれまで、常に外注していたんです。ですから、この工程を社内で行い、最初から携わってきたデザインが目の前で造形されるのを見て、感動しましたね。粘土で彫刻していた頃に戻ったようでした」とAaron Sims氏。
ダンス音楽の新しい形
アートとしての3Dプリントの可能性は、物理的な作品だけにとどまりません。ダンスや音楽といった形式にも、これまでにない次元が切り開かれます。3Dプリントの特徴である設計の自由度により、非常に複雑でユニークな楽器であっても、従来の製造法の何分の一の価格で既存製品の調整や一からの製作が可能です。
何世紀も前からほとんど変化していないバイオリンの形状は、誰もが一目見てわかるものです。バイオリン音楽は非常に洗練されたレベルまで進化し、楽器自体が高尚な地位を獲得するまでになっています。しかし、FormlabsのエンジニアであるBrian Chanは、3DプリンタとFormlabsのWhiteレジンを使ってアコースティックバイオリンの製作に挑戦しました。
美術品の修復で骨頂品を甦らせる
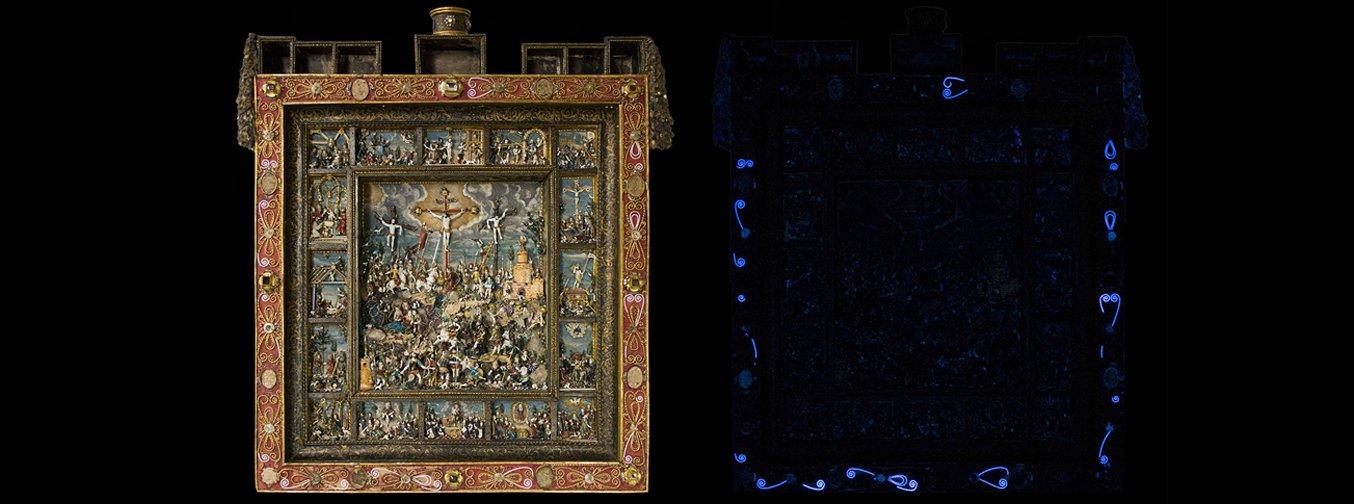
3Dスキャン、CAD、3Dプリントは、歴史上最も有名な芸術家の作品の修復にも使用されており、ミケランジェロやダ・ヴィンチなどの作品がかつての輝きを取り戻しています。
美術品の修復プロジェクトは、3Dプリントと3Dスキャンという2つの技術を組み合わせることで強化できます。これらの技術により、物理的なオブジェクトの設計、3Dモデルの作成、変更や修復、再プリントが可能になります。
Mattia Mercante氏は、フィレンツェにある世界的に有名なOpificio研究所で、彫刻品や美術品の欠損部分を3Dプリントによる複製で補修しています。
17世紀の聖遺物の修復時には、Mercante氏はHPの3D Structured Light Scannerを使って作品の他の箇所からフレームの繊細なディテールをスキャンし、Formlabsの3Dプリンタで欠損部分を複製しました。造形品には、元の装飾品と同じに見えるよう塗装を施しました。何よりも、修復に必要なCADモデリングは最小限で済み、手作業に比べて迅速かつ手頃な価格で行うことができました。
飛行機、頭蓋骨、スーツケース: 完全犯罪の解決を支援
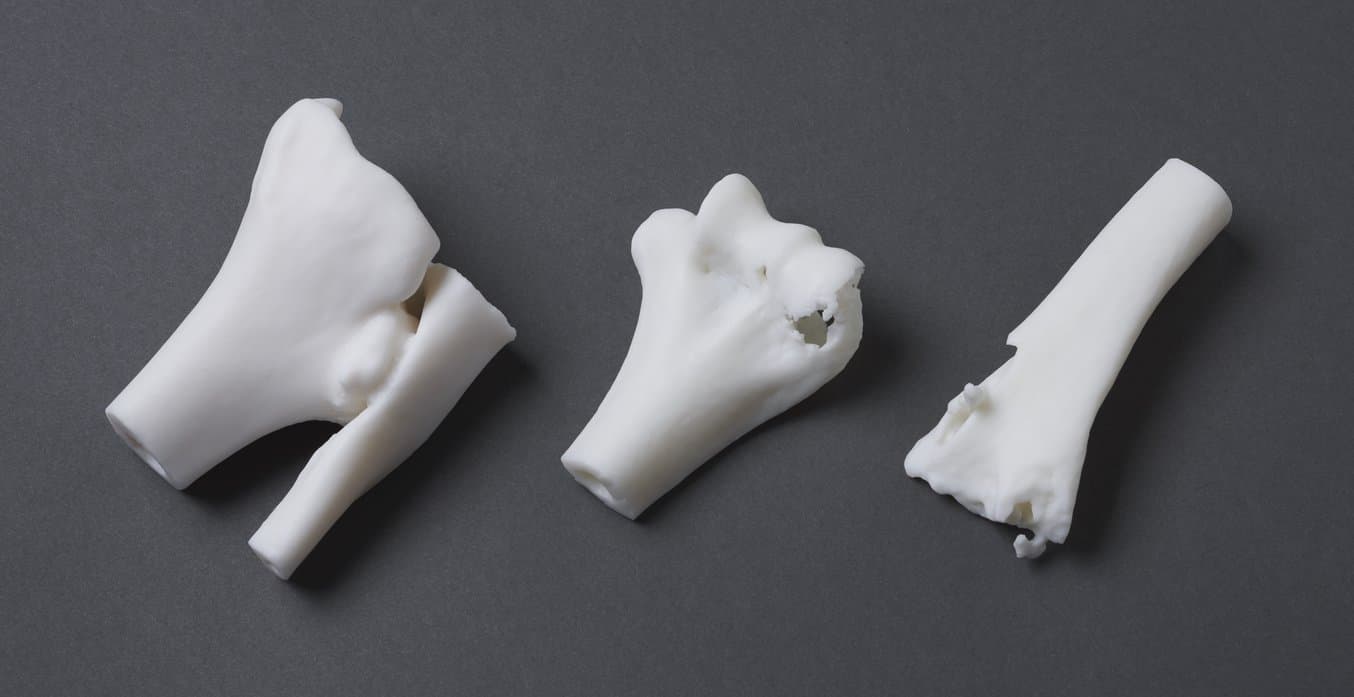
3Dプリントは、復元という目的でも生産と同様の可能性があります。法医学アーティストの仕事は、不完全な証拠によって困難を極めます。捜査ではデジタル技術が大いに役立ち、法医学アーティストによる参考人や被害者の正確なモデル復元を支援します。
このデジタル工程では、CTスキャンから3Dプリント品を作り身元確認に役立てています。例えば、捜査官が証拠品として頭蓋骨の一部だけを見つけた場合、3Dプリンタで完全なサンプルのモデル作成および複製を行います。
被害者の外見の復元モデルは既に司法の場で重要な役割を果たしており、3Dプリントの有用性はデザインの自由さや生産効率以上のものであることを改めて示す事例となっています。
術前計画に3Dプリントを活用するのと同じく、犯罪の被害者のCTスキャンを行うことで、刑事が骨を間近で観察できるようになります。遺体のデジタルCTスキャンとX線データを使用して、3Dプリントで体の様々な部位のレプリカを作成し、その後病理学者が犯罪に関わった人数から凶器の性質まで、犯罪の全容解明に努めます。
一人一人に合った義肢装具
3Dプリントの影響は、生産工程の改善やラピッドプロトタイピングの実現だけにとどまりません。人々の人生を変えることもできるのです。現在、世界では3,000万もの人々が義肢や装具を必要としていますが、従来の方法ではコストや仕様がハードルとなることが多く、3Dプリントがこの問題を解決できるのではないかという期待が高まっています。
医療界の様々な進歩と同様、3Dプリントも患者様一人一人のニーズに合わせた治療を代替手段として手頃な価格で提供できます。3Dプリント技術の価格の手頃さとカスタマイズ性は、上の動画で紹介した親子のように、怪我や障害に苦しむ人々の生活の質を大きく変えることができます。
私たちはこの種のイノベーションを、Metajさんと脳性麻痺を患う息子Nikくんの事例で目の当たりしました。Metajさんが目標とするのはただ一つ。Nikくんが歩けるようになることでした。その後何ヶ月にも渡る研究開発の結果、Nikくんが必要とするサポートと補修を的確に行えるカスタムメイドの装具を3Dプリントで製作することに成功し、Nikくんは初めて自分の力で歩けるようになりました。上の動画と特集記事をご覧ください。
3Dプリントにより、ユーザーの身体から失われてしまった機能を取り戻す義肢装具だけでなく、ある意味で元の手足よりも優れた装置を製作することもできます。これらの事例はもはやロボコップのような生体工学的な体を作るという未来的な構想ではなく、既に最先端の義肢装具製造の一部となっているのです。Psyonicなどの企業が、既に最先端の義肢装具を提供しています。
住宅と建築の新しい形
3Dプリントというと、手に持てるくらいの小さなものを造形する、というイメージが強いかもしれません。近年、様々な企業が、遥かに大きく機能的な部品を製作できるアディティブマニュファクチャリングの工程を模索しています。ここ数年では、完全3Dプリント製の住宅や大規模な構造物を生み出すべく、様々な取り組みが行われており、持続可能な生活と建設の新たな可能性が切り拓かれつつあります。
3Dプリントにより、コンクリートなどの柔軟性に欠ける建築材料でさえ、建築家が自由に設計できるようになります。大まかに言ってしまえば、現代の快適さの基準を満たしながら、完全に持続可能でエネルギー効率の高い住宅を建築することができるのです。この方法による建設は、従来の方法よりもコストや環境に与える影響を低く抑えられるだけでなく、無駄をほぼゼロにすることができるかもしれません。
実際に完全3Dプリント製の住宅に移り住む日はまだ先になるかもしれませんが、3Dプリントによる建設プロジェクトは既に始まっています。アムステルダムにあるMX3D Bridgeは、現在一般市民が歩いて渡ることができます。dezzen.comによると、「橋に使用されている4,500kgのステンレススチールは、半年かけて工場でロボットを使った3Dプリントが行われ、今年、運河の上にクレーンで設置された」とのことです。
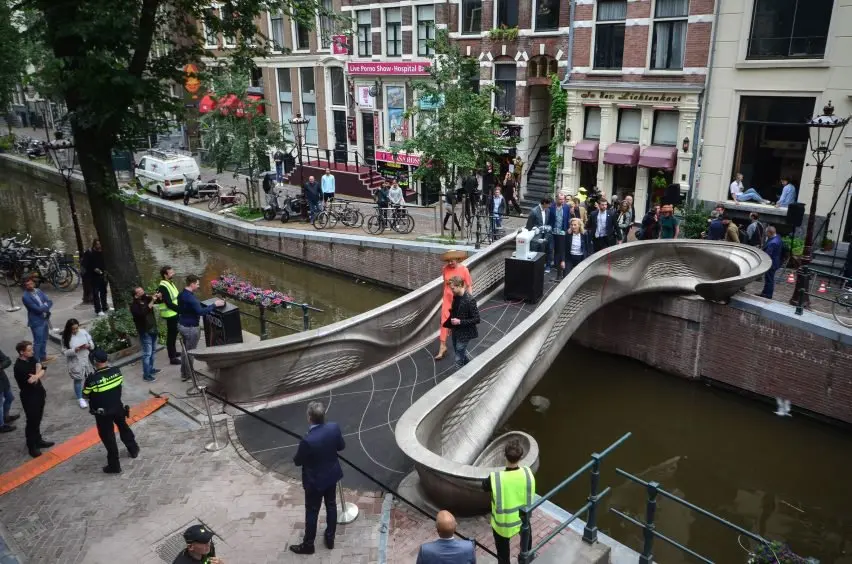
出典:www.dezeen.com
宇宙開発競争を支援
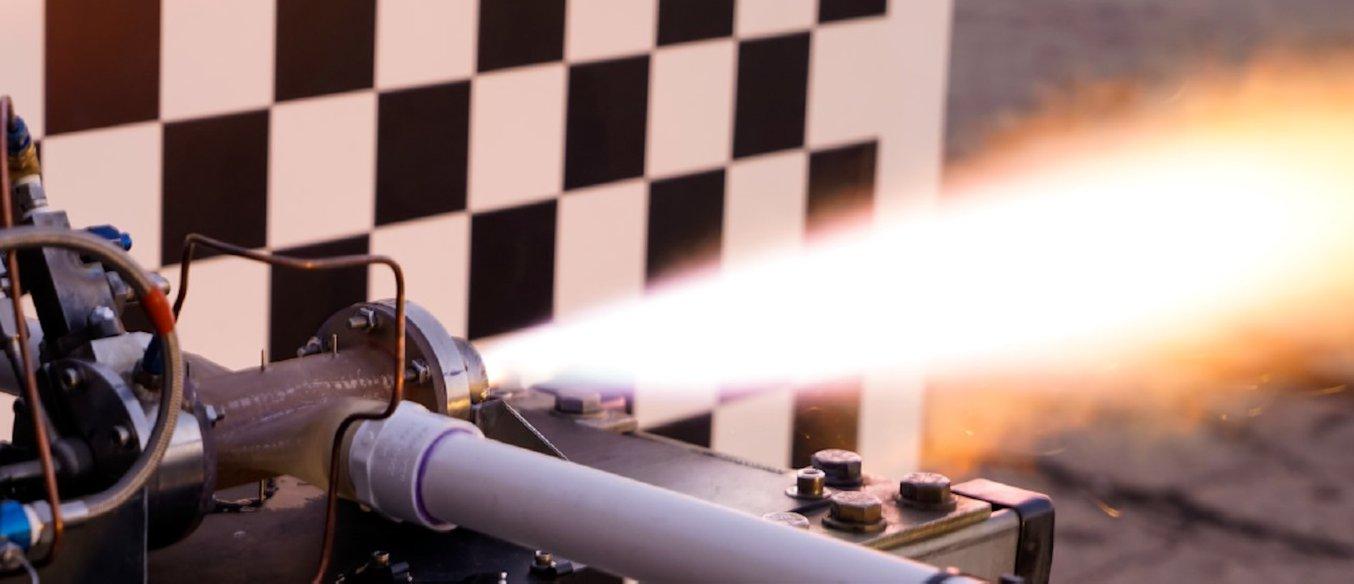
世界で最も参入障壁の高い業界の1つである宇宙旅行業界は、3Dプリントによるイノベーションの期待が高まっています。宇宙業界専用の高額な金型や機械の試作品製作コストを下げることで、中小企業による宇宙業界でのイノベーションを促進できるようになります。
航空宇宙のスタートアップ企業、Relativityは、アディティブマニュファクチャリングを使用したアルミニウム製ロケットエンジンの製作を検証しました。成功すれば、宇宙旅行のコストと実用面での障害を大幅に削減することができ、業界全体で新たなビジネスと成長の可能性が大きく広がります。
航空宇宙業界における3Dプリント活用法に変革を起こそうとするもう1つの企業に、Masten Space Systemsがあります。2004年に設立された同社は、垂直離着陸ロケットを専門としています。同社は、NASAのCommercial Lunar Payload Services (CLPS:商業月面輸送サービス)プロジェクトの一環として、2022年に月へのミッションを開始します。Mastenは、Formlabsの3Dプリンタを使用し、R&D用にプラスチック製のロケットエンジンを製作しました。
同社にはプラスチックと金属の両方を使った3Dプリントの経験があり、NASAのティッピング・ポイント・プロジェクト用に新しいカスタム金属材料の開発も支援しました。「ロケットエンジンを3Dプリント製にすると、従来の製造方法では実現できなかった様々な事が可能になるので、私たちはとても気に入っています。コストと削減と有効性の向上を目標として掲げる中、特にCeramicレジンやHigh Tempレジンがリリースされてから、SLA光造形3Dプリンタの活用方法を検討し始めています。これらレジンの工学的特性は、実際にロケットで使用できるかどうかを検討する上でかなり魅力的です」とMastenのチーフエンジニアであるMatthew Kuhns氏は述べます。
FormlabsのHigh TempレジンとRigid 10Kレジンは、航空宇宙用途に最適な工学的特性を持つ材料の一例です。High Tempレジンは高熱にさらされる機能試作の製作に最適で、Rigid 10KレジンはFormlabsのエンジニアリング系レジンの中で最も剛性が高く産業グレードの試作品製作に適しています。
ジェネレーティブデザインの実現へ
ジェネレーティブデザインは、製造業のすべての分野で働くエンジニアにとってCAD設計の新境地とも言える技術です。人工知能(AI)の力を活用し、複雑な課題の解消や部品の軽量化、製造コストの削減、大規模なカスタマイゼーション、性能の最適化を実現できる新しい高機能設計をいくつも編み出すことができます。
複雑で有機的な形状のオブジェクト製作に適した3Dプリントでは、事業用途に合わせて設計された幅広い材料特性により、これまでにはない新しい構造を設計できます。AIを活用してエンジニアが複雑な新設計を素早く効率的、かつ大量に模索することができるので、新製品の研究開発工程を大幅に短縮することができます。設計が出来上がったら、社内の3Dプリンタで複雑な形状を具現化し、手に取って確認することができます。
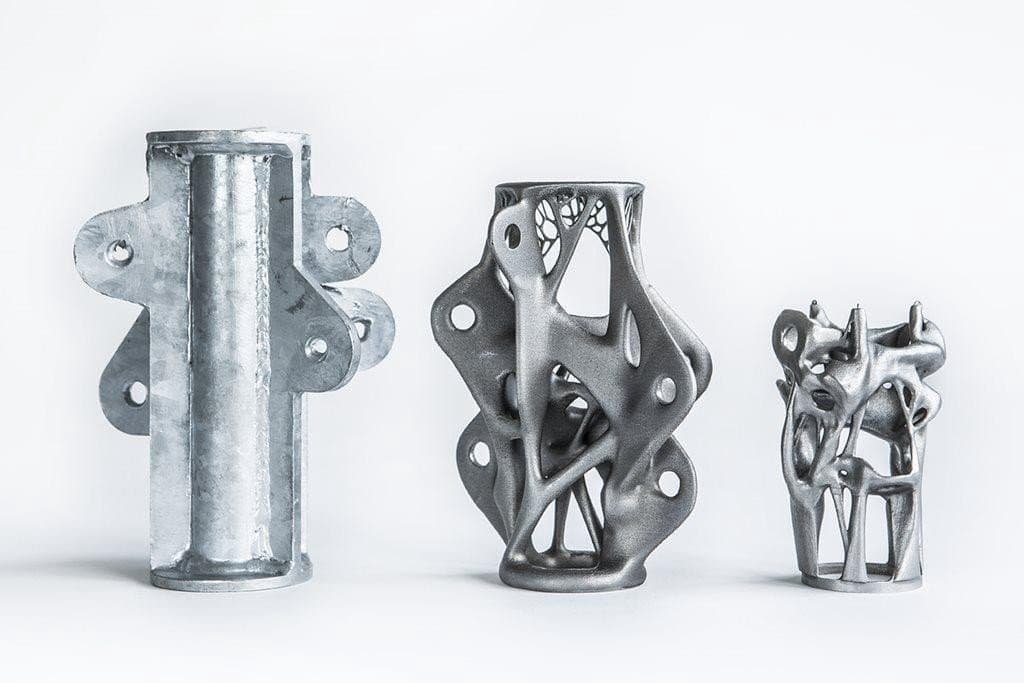
荷重がかかる箇所が決まっているブラケットやストラットは、ジェネレーティブデザインが活用されることの多い部品。
ジェネレーティブデザインにご興味がある場合は、無料ウェビナーをご覧ください。「ジェネレーティブデザイン」というキーワードで検索するとブラケットの画像が多く表示される理由、Autodesk Fusion 360 で設計の問題を設定する方法、初めてジェネレーティブデザインを活用した企業が車椅子のブラケットの40%軽量化に成功した事例などをご覧いただけます。
未来の人材を育成
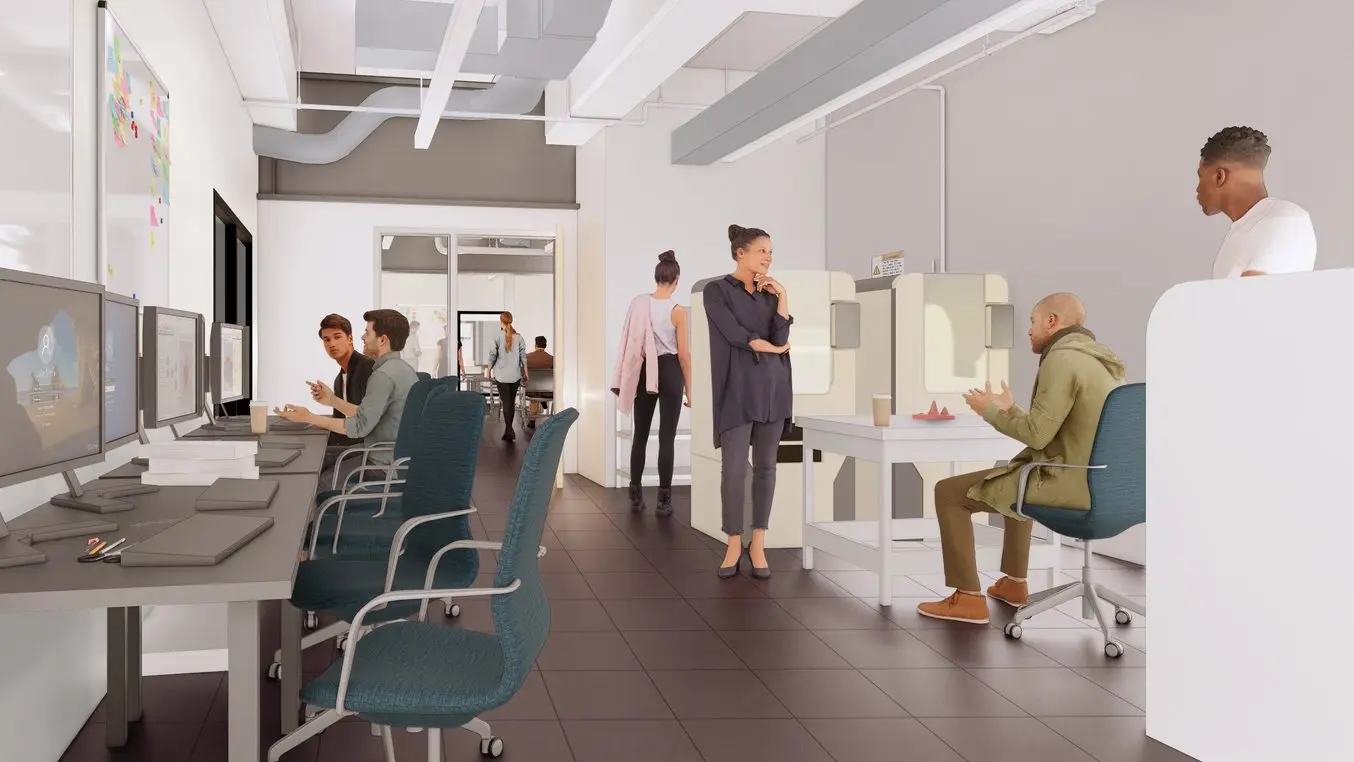
Innovation Hub内のOrigin Labsには、学生やその他コミュニティのために3Dプリント専用スペースが設置される予定。
高等教育機関のほとんどは、未来の人材を育てるべく学生の教育に力を入れています。ペンシルベニア州立大学も現代の人材に力を入れていますが、最近、大学内のコミュニティだけでなく一般市民にも公開予定のEric J. Barron Innovation Hubの建設に数百万ドルを投資しました。
ペンシルベニア州西部と中部に位置するアパラチア山脈は、歴史的に全米の炭鉱産業の中心地であり、20世紀前半にはそのおかげで堅実で豊かな経済を享受してきました。しかし、世界経済と国内経済の石炭離れが進むにつれてアパラチア地域は苦境に立たされることになります。アパラチア地域委員会の報告によると、失業率は上昇し、世帯所得率は全米で最も低い地域の1つになりました。
過去20年に渡り、この現状を変えようと地域及び州レベルで製造や教育、技術分野への投資が行われています。アパラチア地域委員会は、「特に技能開発および人材訓練を地元及び地域のビジネスニーズや機会に結びつけることにより、教育の機会や教育機関を支援する」ために100万ドルの助成金を提供しています。
この記事でもお分かりいただけるように、アディティブマニュファクチャリングが様々な事業に急速に拡大する中、採用担当者たちはデジタルでの作業に慣れ、CADを使いこなせる従業員を求めています。同州の大学は大規模かつ潤沢な資金を持つイノベーション・ハブを設立することで、この市場のニーズに応えようとしています。
昔ながらの教育カリキュラムを強化
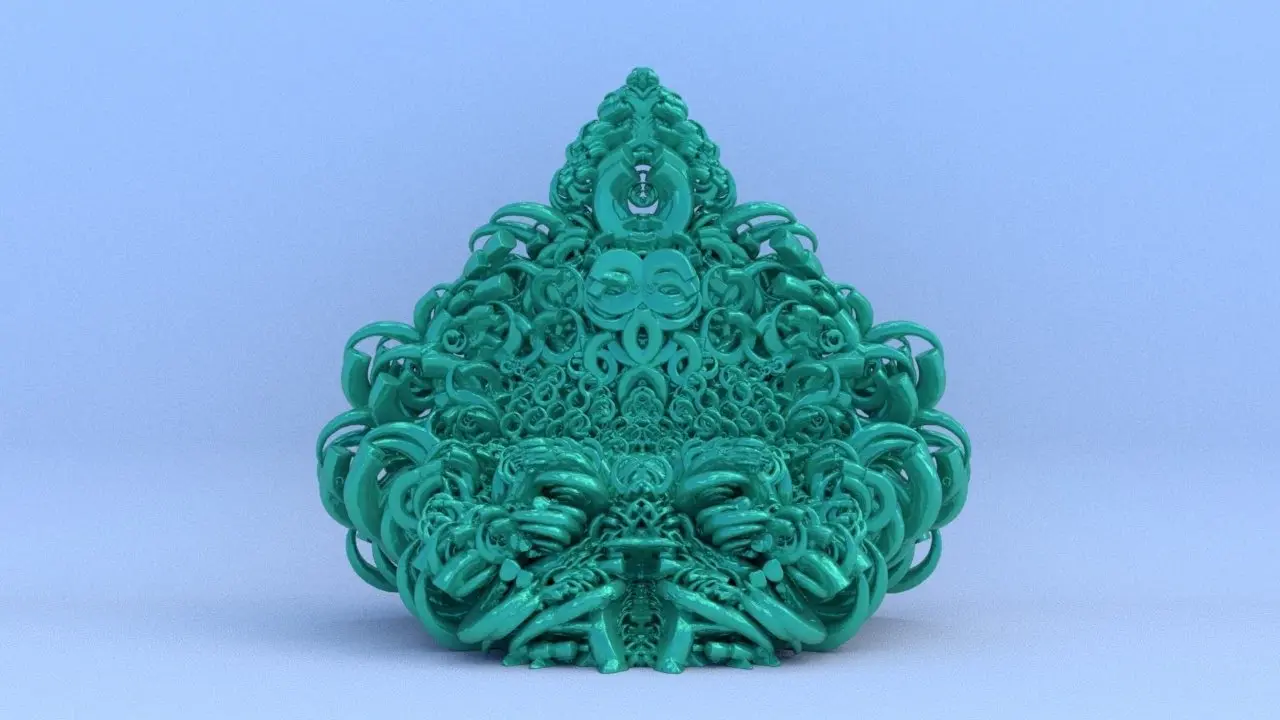
大学では、CADと3Dプリントで未来の人材を育成するだけでなく、幅広い教育分野に3Dプリンタを導入することのメリットも認識され始めています。
マサチューセッツ大学ローウェル校では、21世紀に向けて彫刻と3Dデザインのコースを近代化しています。2017年に同大学に加わったYuko Oda氏は、第一歩としてFormlabsの光造形3Dプリンタを始め多数の3Dプリンタを導入しました。
Yuko氏は、アートとテクノロジーへの情熱を教室でも存分に発揮し、現在は彫刻、3Dモデリング、アニメーション、インタラクティブメディアを教えています。将来様々な分野で活躍するためには、映画用の彫刻デザインなどを含め、3Dアニメーションや3Dモデリングの理解が欠かせないことを、ほとんどの学生が理解しています。スタジオアーティストにとって、3Dモデリングは不可欠なスキルになっているのです。
「学生は3Dモデルをスカルプトし、Zbrushにインポートし、Clearレジンなどの様々なレジンで3Dプリントします。Zbrushで修正した繊細な部分を表現できるFormlabsの3Dプリンタの能力は、研究室にある他のプリンタとは比較にならないほど優れています。
Yuko Oda氏
彫刻の未来で最も期待が高まっている要素の1つは、3Dプリントと仮想現実(VR)の統合です。3Dデザインに苦手意識を持つ学生にとっては特に重要です。VRは3Dデザインの障壁を急速に取り払い、アーティストや学生がOculus Mediumなどのプログラムを使って実際に手を使って製作できるようになります。Yuko氏は、VRを活用してわずか30分で3Dオブジェクトを作成し、作品を3Dプリンタでプリントする方法を中学生にも教えたことがあります。熟練の彫刻家にとっても、VRによってアイデアを具現化するまでの時間を短縮し、実験的なアートの新分野を切り拓ける可能性が広がります。
絶滅危惧種の鳥類を守る
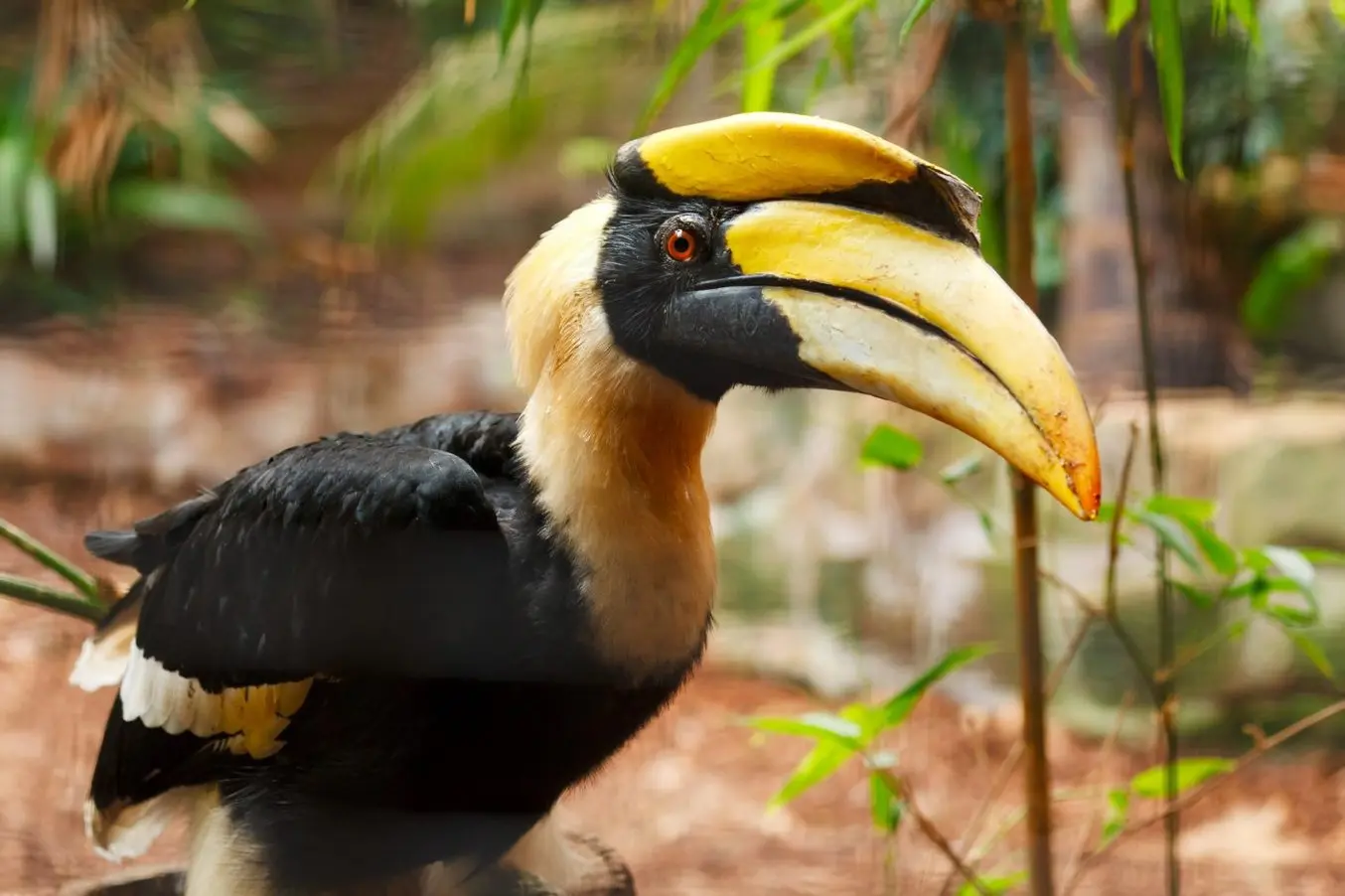
ZooTampaの飼育員が25歳のオオサイチョウの定期検査を行っていたところ、頭頂部の黄色いヘルメットのような形をしたカスクの付け根に病変を発見しました。その後の検査で、クレセントと名付けられたこの鳥は、生命を脅かすガンに冒されていることがわかりました。
ガンが発見されたのは頭蓋骨の近くで、副鼻腔の一部を収容している箇所のため、取り除くことができません。研究チームは、ガンに侵されたカスクを取り除き、この鳥専用に設計した3Dプリント製のレプリカに置き換えることができないかと考えました。患者専用の補綴物や装具は人間の手術では使われたことがありますが、サイチョウには初めてです。もし可能なら、鳥にとっても安全な材料はどれかも見極める必要があります。
ZooTampaによると、見事成功した3Dプリント製の人工嘴はBioMed Whiteレジンを使用して製作したそうです。BioMed Whiteレジンは、長期的な皮膚接触または短期的な粘膜接触が求められる生体適合性用途に適した不透明な白色の材料です。Formlabs SLA光造形3Dプリント用材料の中でも特別な医療グレードの材料で、組織、骨、象牙質との短期接触が想定される用途で使用できます。
サプライチェーンの混乱を解決
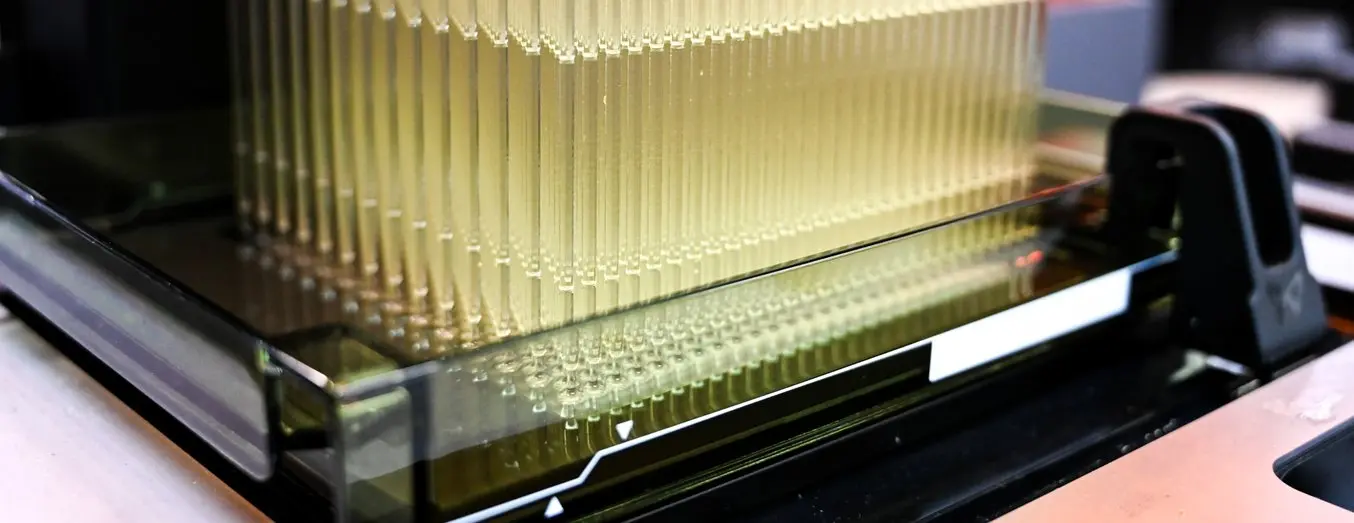
COVID-19の大流行や、それに続く2021年・2022年のサプライチェーンの大混乱の最中、多くの企業が3Dプリントを頼り、機器をオンラインに保つことで工場から製品を出荷し続けました。機器の交換部品など、3Dプリントによる実製品用部品の内製が拡大したことで、アディティブマニュファクチャリングはサプライチェーンの問題に対処する重要なツールとなりました。
Formlabsは、2022年3Dプリント活用レポートを発行し、3Dプリントユーザーの間で起きている最近の変化をまとめました。このレポートでは、3Dプリントに対する考え方が、「研究開発や試作品製作用のツール」という認識から、「常に変化する消費者の嗜好に対応しサプライチェーンの課題を克服するための重要な製造技術」という位置付けに変化していることがわかります。サプライチェーンの制約を緩和する目的であれ、限定品の生産やカスタムデバイスの生産であれ、企業は顧客の需要を満たすために製品の製造方法を再考する必要性に迫られています。
3Dプリントで3Dプリンタを製作
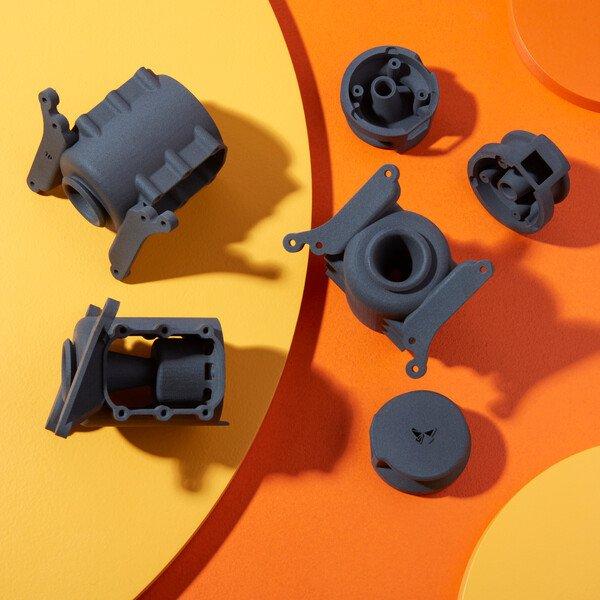
Fuse 1でプリントした実製品用部品。
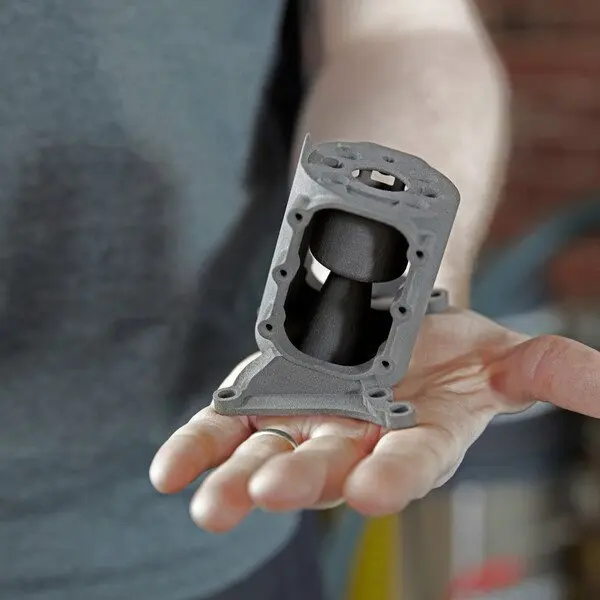
Fuse 1にてNylon12パウダーでプリントしたIRセンサー用のパージ。
3Dプリンタの製造は、常にエンジニアリングの課題です。手頃な価格で洗練されたデザインのデスクトップ型プリンタに工業グレードの性能を詰め込むには、長年に渡るエンジニアリングと設計作業が必要です。待望のFormlabs SLS(粉末焼結積層造形)方式3Dプリンタ、Fuse 1が特にそうでした。
Formlabsのエンジニアが部品の試作に使用したツールの1つは、Fuse 1そのものでした。しかし、3Dプリントの活用は試作品製作だけにとどまりません。現在、出荷されるすべてのFuse 1ユニットには、Nylon 12パウダーを使ってFuse 1で直接プリントした複数の生産部品が搭載されています。
Fuse 1を監督するエンジニア・プログラム・マネージャーのSeth Bergによると、Fuse 1 SLSプリンタで試作品や実製品用部品を製作することで得られたメリットは3つです。
- 部品内部にサポート材を使用することなく複雑な形状の部品を製作できる設計の自由度
- 試作品と実製品用部品を内製することによるサプライチェーンの削減
- 外注の必要性を排除し、実績のある万能材料Nylon 12パウダーで少量生産に適した手頃なソリューションを実現
工程の詳細、3Dプリンタに搭載されている実製品用部品、3Dプリンタの詳細については、こちらの動画をご覧ください。
鼻腔用綿棒の製作でコロナ禍の緊急需要に対応
2020年5月、Forbesは「How 3D Printing Test Swabs Will Help Fulfill America's Shortage」というタイトルの記事を掲載しました。その記事では、COVID-19の流行で在庫不足に陥っていた綿棒の増産に対処すべく、Formlabs、HP、Origin、Carbon、Desktop Metalなど3Dプリント業界の企業が一丸となって取り組む様子が紹介されました。
COVID-19パンデミックにより、世界を跨いだ協力体制が必要でした。USFとNorthwellとの提携により、Formlabsは世界中に展開されることとなったソリューションを実現しました。利用しやすい設計と手頃な価格の機器、検証済みの工程で綿棒を生産し、25カ国4,000万人以上のCOVID検査を可能にしました。昨年以降、患者の検査とケアを改善するために、Formlabsの3Dプリンタが政府や医療提供者によって使われ続けています。世界的規模のこのソリューションは、3Dプリントの俊敏性が公共の利益に貢献できたほんの一例にすぎません。
この有効性はシンガポールでは特に顕著で、Eye-2-Eye Communicationsが綿棒の生産を1日あたり3万本以上に増やし、街の安全維持に貢献しました。
「高速設計・開発が可能な3Dプリントの特徴を活かす絶好の機会であっただけでなく、非常に短期間で製品を大量生産できるFormlabsプリンタの実用性を示すものでもありました。また、世界中で感染者数が急増する中、必要であれば需要に合わせて比較的簡単に生産規模を拡大できるというのは心強いことです」と言うのは、Eye-2-Eye CommunicationsのCEO、Miles Podmore氏です。
アフターマーケット・カスタム部品を高速生産
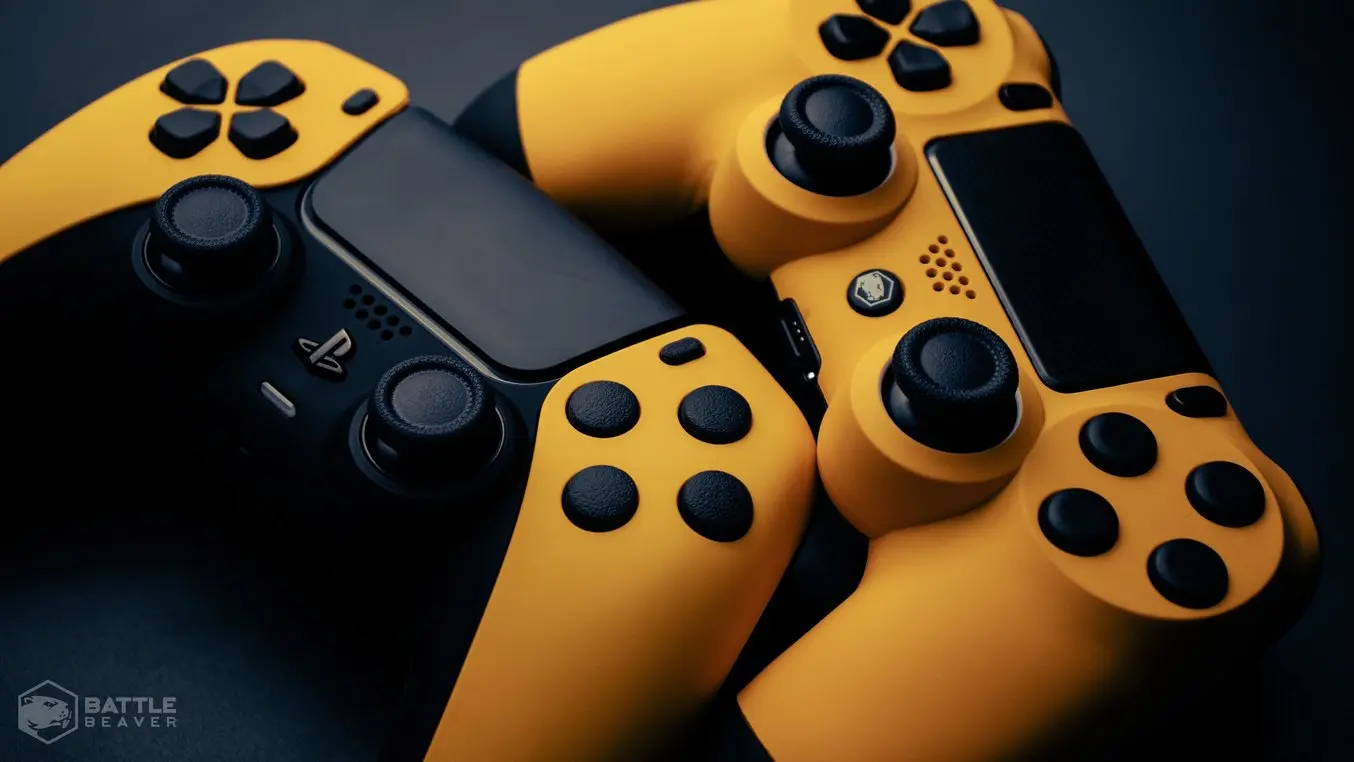
Fuse 1でプリントしたボタン付コントローラー(左)と射出成形したボタン付コントローラー(右)
カスタムアフターマーケット品の生産における課題の1つは、通常は注文数が少なく、販売元のメーカーが製品仕様を更新した場合にはそれに対処する必要があることです。しかし、3Dプリントによる内製化の拡大に伴い、複数の業界でカスタム生産が行われるようになりました。
Battle Beaver Customsは、カスタムコントローラーで最高のゲーム体験を提供することを主軸としています。同社が行う改良でコントローラーの反応速度と機能性が高まり、プレイヤーは様々なゲームでポテンシャルを向上させ、パフォーマンスを最大限に押し上げることができます。Fuse 1 SLS 3Dプリンタを使用したラピッドプロトタイピングにより、Battle Beaver Customsはマウントとボタンのデザインをすばやく変更できます。消費者製品をカスタム生産する場合、競合他社よりも優位に立つには、納期の短さが重視されます。Battle Beaver Customsの研究・設計責任者であるMichael Crunelle氏はこう言います。「コンセプトから実製品用部品まで、変更を素早く反映できることがFuse 1の魅力です。このスピードには、競合他社はなかなか追いつけないでしょう」
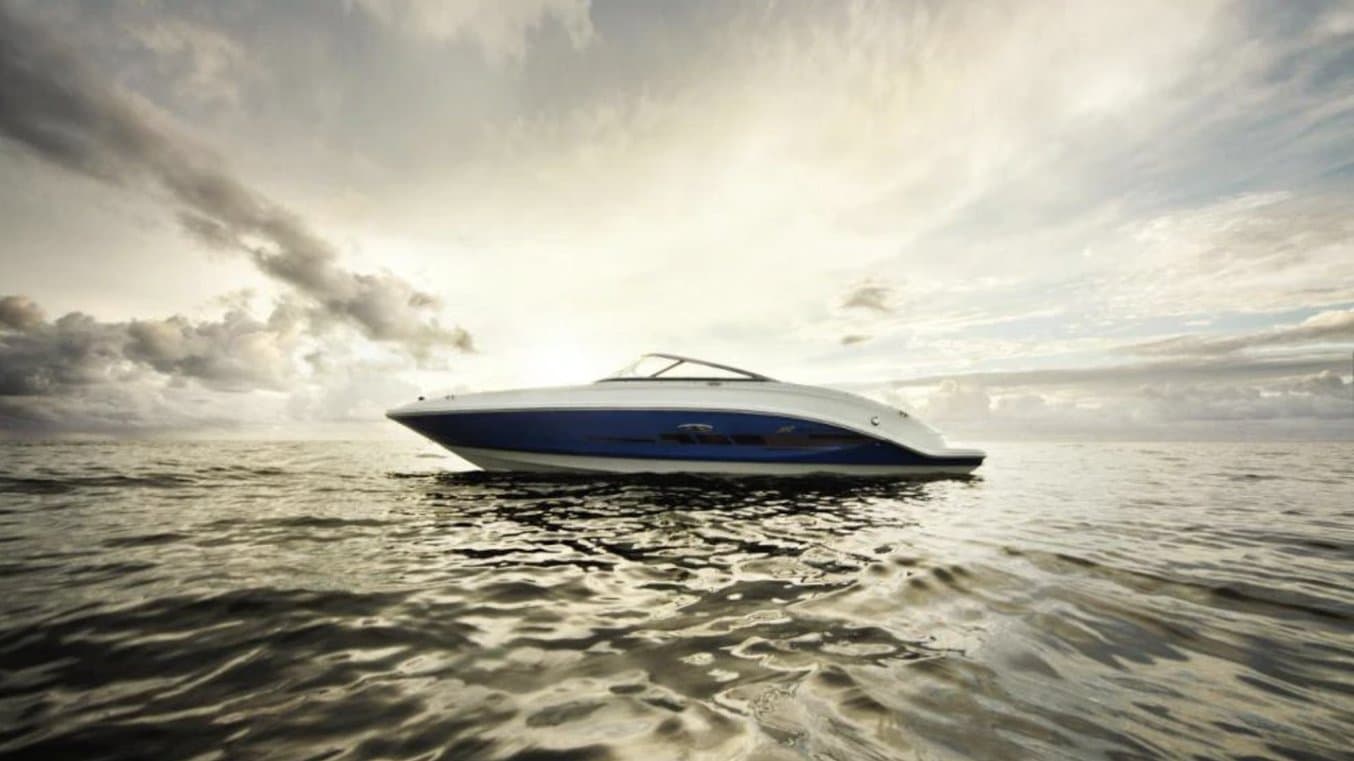
海洋用品やその周辺機器を製造するJetBoatPilotは、ジェットボートの性能と低速ハンドリングを向上させるアフターマーケット部品の開発で業界の権威としての名声を築いてきました。
JetBoatPilotは、光造形3Dプリンタ Form 3及びSLS方式3Dプリンタ Fuse 1でアフターマーケット部品の試作と製造を行っています。新たに設計され、現在最高の性能を誇る製品、Lateral Thruster 2.0は、Fuse 1でのプリントを前提に設計・製造されたものです。Fuse 1とNylon 12パウダーを活用し、JetBoatPilotは以前の製造方法と比べて製造コストを6分の1に削減することができました。「そうしようと思えば、新しい(アルミ版の)製品の小売価格を$400あたり、もっと言えば$600あたりにまで上げることができたでしょうね。でも、$600ではあまり売れなかったと思います。今は$199で販売していますが、お客様も喜んでくれていますし、この価格でも原価の20倍です」と、JetBoatPilotの創始者Will Owensは言います。
最高のバスボムを作る
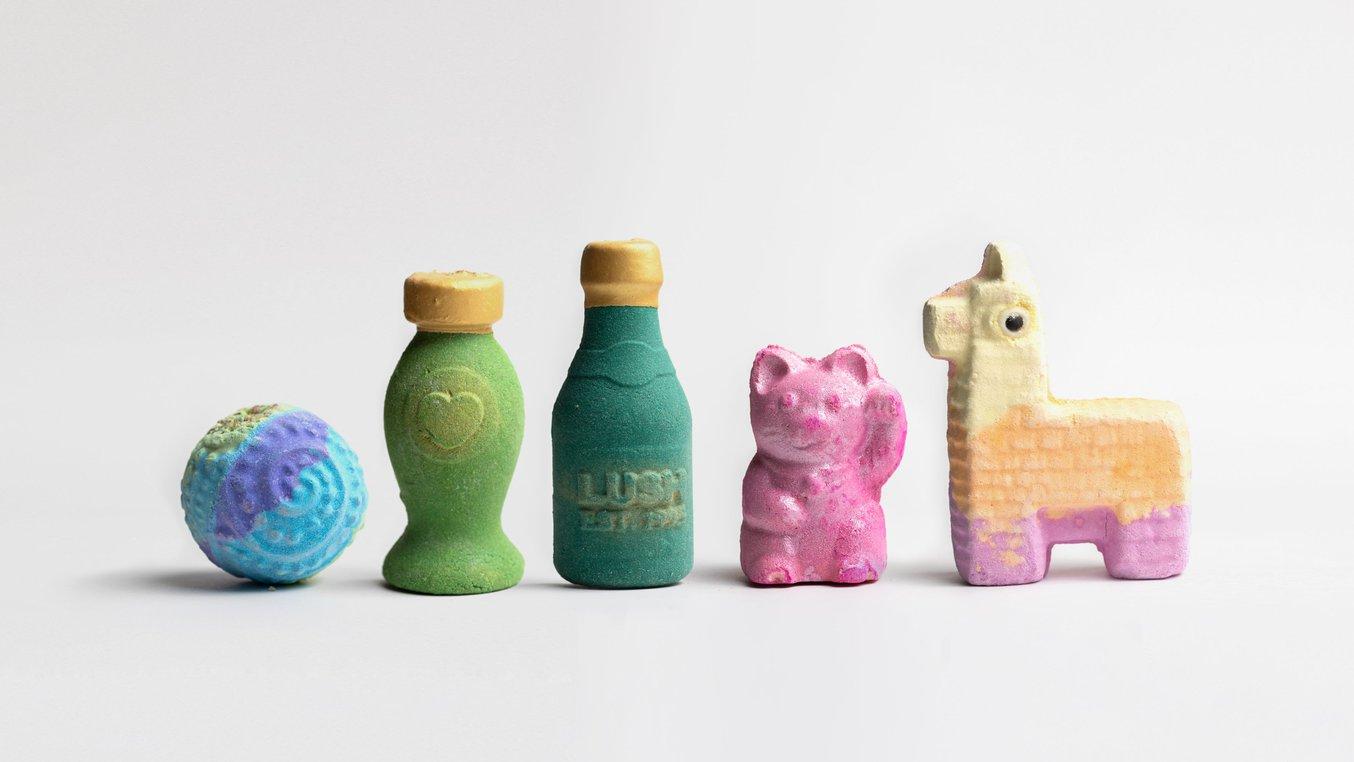
「マッサージ・バー」、「ボディ・バター」や「バス・ボム」をはじめ、消費者が喜ぶクリエイティブな商品シリーズの数々を発表し、今では世界48カ国に928店舗を展開するグローバルブランドとして大きく成長したLUSH成功の秘訣は、トレンドや顧客ニーズの変化に即応する俊敏性と柔軟性にあります。
業界を代表するような、斬新で細部までこだわった化粧品を実現するため、LUSHは3Dプリントの活用を新形状の試作品製作以外にも拡大しました。LUSHは、成形型や治具、実製品用部品の製作ができる次世代アディティブマニュファクチャリングセンターに投資しました。
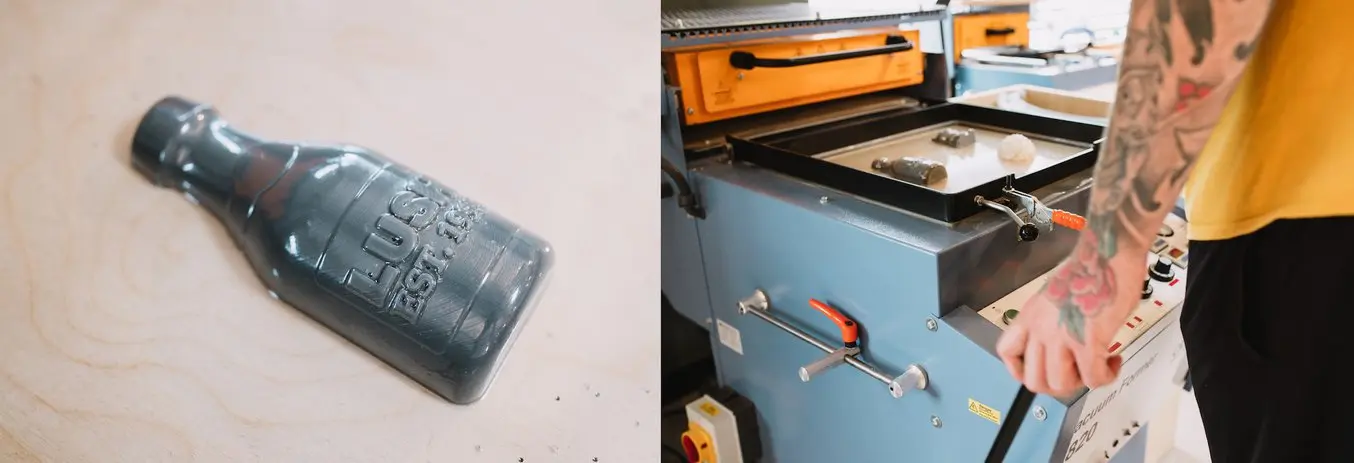
LUSHは社内で3Dプリント製の成形型を使って真空成形を行う。
「私たちは、Formlabsの3Dプリンタを活用して、成形型、カスタム治具、実製品用部品を製作しています。消費者のニーズに常に迅速に応えなければならない私たちにとって、製品開発工程をすべて内製化できると、社内で考案したデザインを外部の業者と共有する必要が無くなり、生産効率の向上に繋がっています」と、Lush CosmeticsのInnovation Labマネージャー、Damien Carter氏は言います。
真のマスカスタマイゼーションを初めて実現
3Dプリントにより、マスカスタマイゼーションなどの新たな可能性とビジネスチャンスが生まれています。デジタル技術を使用することで、従来の製造法では複雑すぎたり、高額なコストを要して非現実的だったものも、付帯コストの発生なく製作できるようになり、デザイナーが主導権を持ちながら完全にカスタマイズ可能な消費者製品が実現できる可能性が広がります。
その例がGilletteのRazor Maker™です。顧客が様々なデザインや色の中から好きなものを選んだりカスタム文字を追加したりして、カミソリのハンドルをカスタマイズできます。
「Gilletteにとって、Razor Maker™という試みはカスタマイゼーションの取り組みの中で重要なステップです。消費者一人一人が異なるように、それぞれ異なるユニークな製品をお届けするには、新しいテクノロジーとビジネスモデルを融合させる必要があります」と語るのはGilletteとRazor Maker™でグローバルブランドマネージャーを務めるDonato Diez氏です。
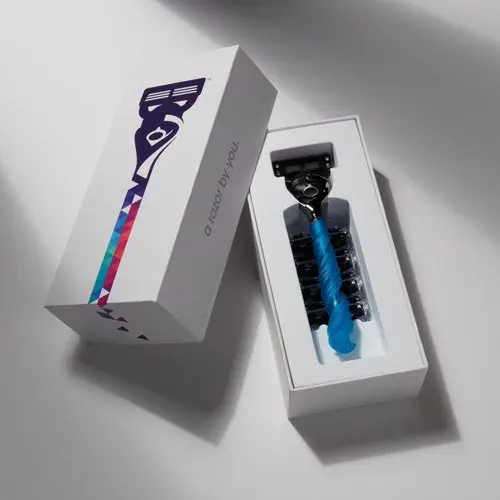
歯科医療にも3Dプリントを
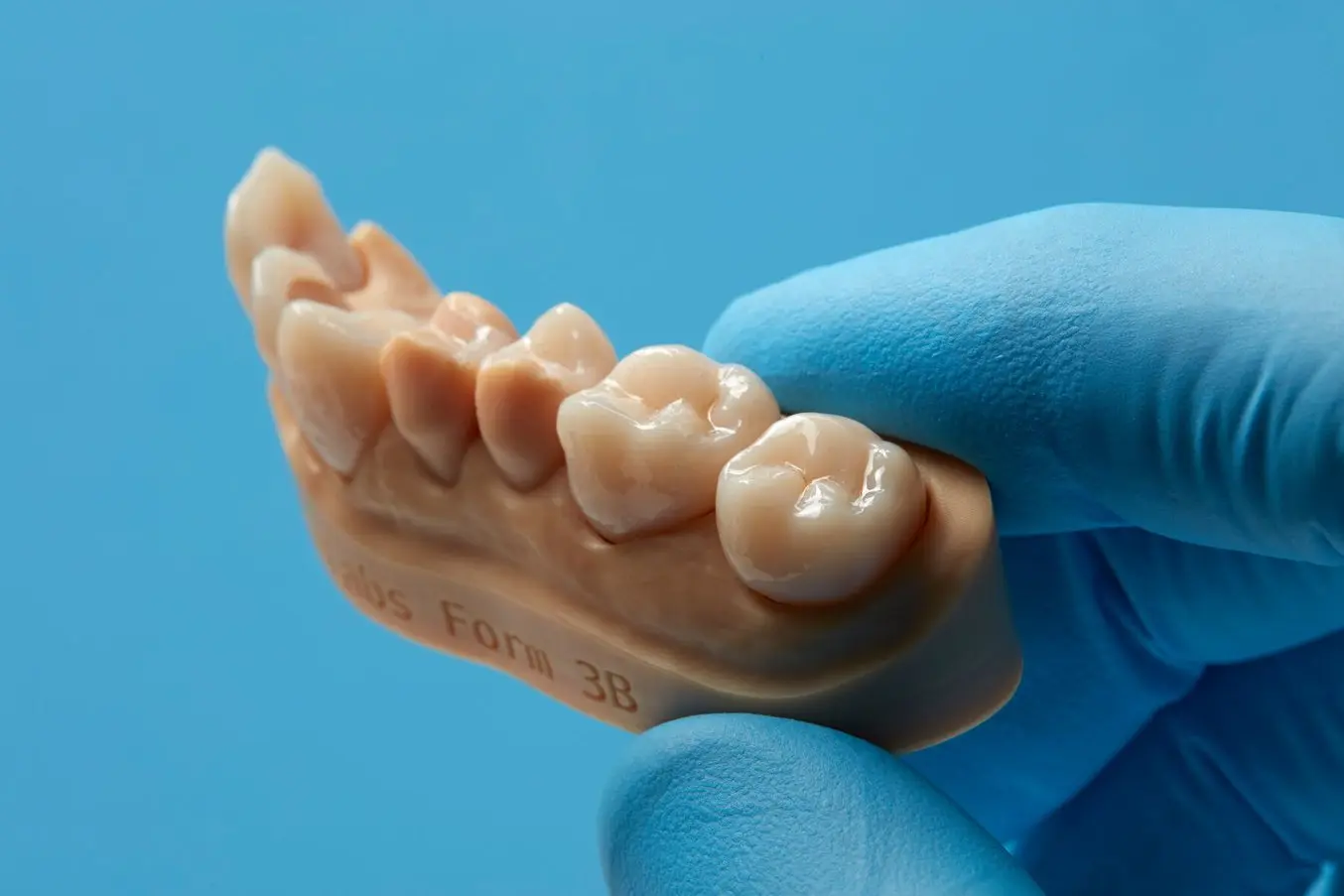
歯科医療もまた、3Dプリントに大きな投資をしている業界の1つで、デスクトップ型3Dプリンタが歯科技工所や診療所で使用される場面がますます増えてきています。3Dプリント製の型を使って熱成形したクリアアライナーは人気が高く、おそらく3Dプリントの活用事例の中で最も成功した事例と言えるでしょう。
歯科分野における3Dプリントの活用は過去10年間で大きく拡大し、現在では、新しい歯科技工所を開設する際は必ず何らかのデジタルデンティストリーが導入されています。材料が非常に優れているため、永久歯のクラウンや総入れ歯などの3Dプリントが可能です。
一人一人異なる私たちの体に合わせたカスタムなソリューションが必要とされる環境で、3Dプリント技術が広がっています。その結果、歯科業界では急速なデジタル変革が起き、工程のデジタル化によって歯科技工所や歯科診療所は効率の向上、一貫した高品質、低コストなどのメリットを享受しています。
3Dプリンタで高級アイウェアを製作
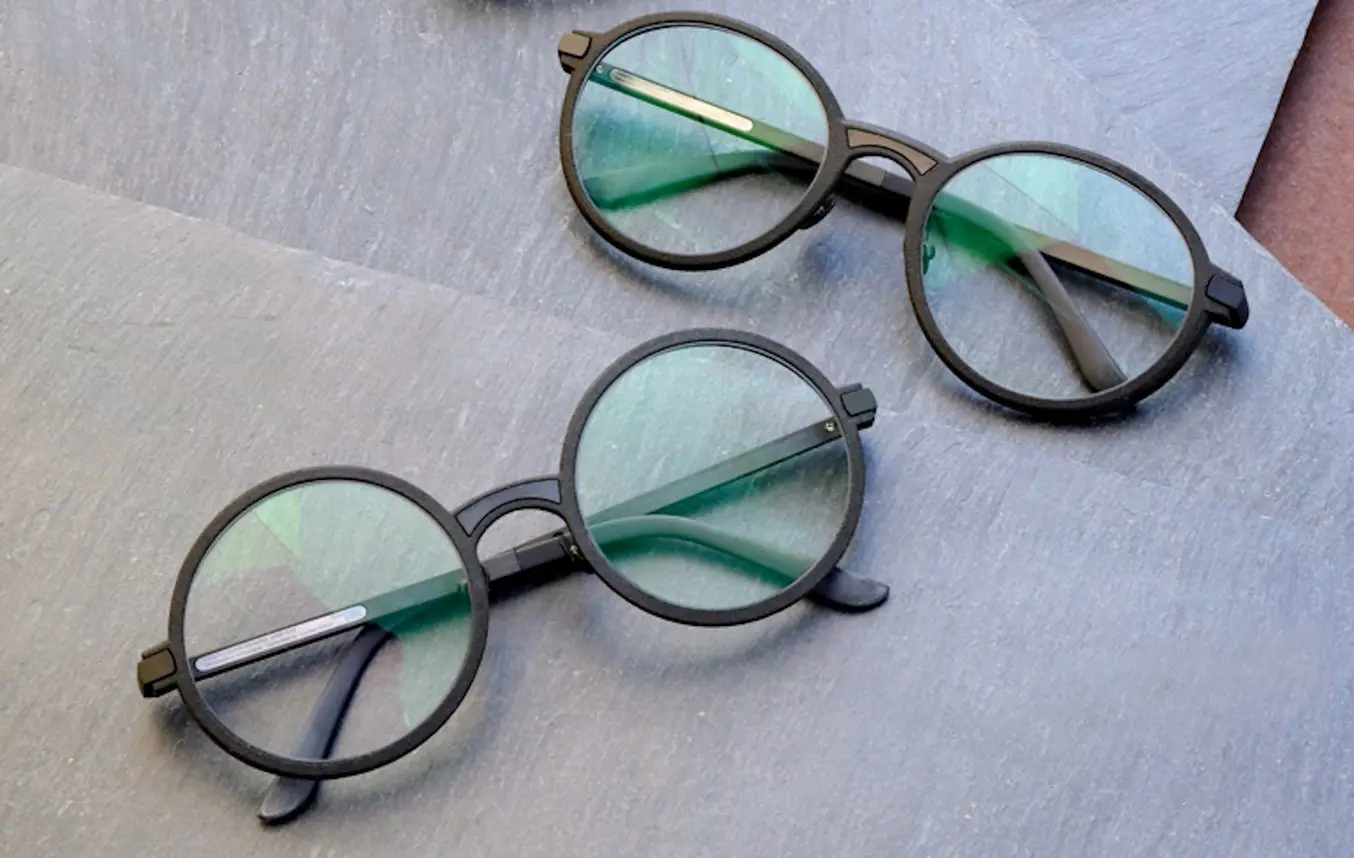
今度、夜の街に出かける機会があれば、3Dプリンタの意外な活用例が周りにないか見回してみてください。3Dプリント製のカスタム眼鏡フレームを見かけるかもしれません。
Marcus Marienfeld AGは、独自の製造法を用いて従来のガラスフレームとは一線を画すアイウェア用のフレームを製造しています。最近では、スイスの工房にFormlabsのSLS 3Dプリンタ Fuse 1を導入し、アイウェアフレームに使用する実製品用部品の製作や、チタン成形で使用する型のラピッドツーリングを始めました。
「社内に3Dプリンタがあると、想像力が膨らんでもっと工夫できないものかと考えるようになります。普段はトライしないようなことにも、気軽に挑戦できるようになるんです」とMarcus Marienfeld氏は言います。
無限に広がる可能性
3Dプリントによって製造分野に広がる変化を目の当たりにするのに、かつてのような想像力は必要ありません。ここ数年で作業工程がさらに発達し様々な業界での活用が定着してきたことで、3Dプリントの持つ革命的な可能性が実証され始めています。
歯科医療から消費者製品、建築、製造に至るまで、一般の人々が3Dプリント製の実製品に触れる機会が増えています。カスタム製品の生産効率を上げ、製造期間とコストを削減しながら、顧客が望む製品にできるだけ近いものを提供する3Dプリントの影響力は、今後も拡大し続けていくことは間違いありません。