
45種超のFormlabs製材料から最適な材料を選ぶ
Formlabsは3Dプリンタメーカーでありながら、3Dプリント用材料のメーカーでもあります。2023年11月時点で45種超の材料がご利用いただけ、各材料の特徴に応じて幅広い要件に適用できる点もFormlabs製品をお選びいただく際の大きなメリットになっています。
それぞれの材料が高機能で、他社製材料以上の強度、剛性、靭性、耐熱性、耐薬品性、絶縁性などを高水準で備え、特許技術による100%純シリコン材料や4Nグレードの工業用セラミック(アルミナセラミックス)、そして医療グレードの生体適合性材料にも豊富な種類があり、時には「自分の作りたいものに合った材料を選ぶ」となると迷ってしまう方もいらっしゃいます。
本記事では、多くのお客様が材料選定の際に指標とされる「高強度」「高耐熱」「ゴムライク」など物性ごとに材料をご紹介し、更に金属と樹脂の特性の違い等に起因する誤解されがちな点を整理して皆さまにより良くFormlabsの3Dプリント製品をご活用いただくヒントをご提供します。また、記事末尾には質問に答えていけば最適と思われる材料を提案する材料選定支援ツールもご紹介いたします。
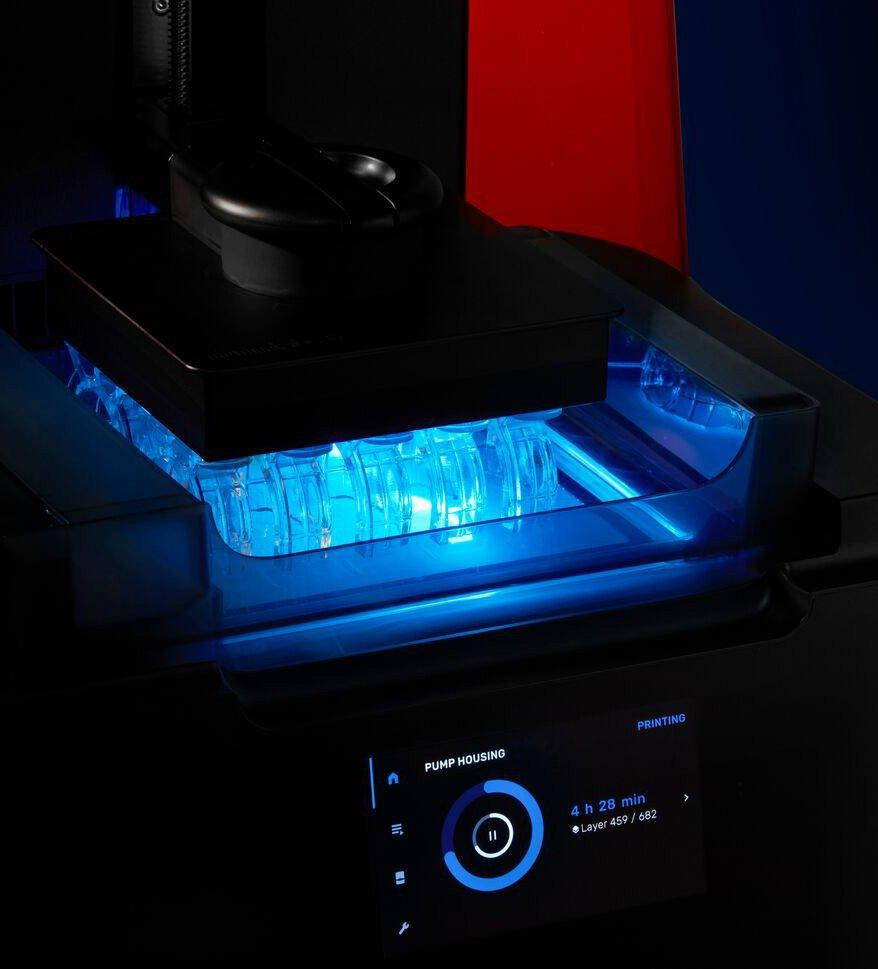
Formlabs光造形製品総合カタログ
本総合カタログでは、FormlabsのSLA光造形方式3Dプリント製品、極高精度を実現する特許技術LFS(Low Force Stereolithography™)技術の解説、各レジンの一括比較と詳細、使い方ガイド等光造形の情報を総合的にご紹介しています。
Formlabs デスクトップ光造形3Dプリンタ
Form 3+ / Form 3B+デモ動画
金属と樹脂の違いと2種に大別される樹脂の種類
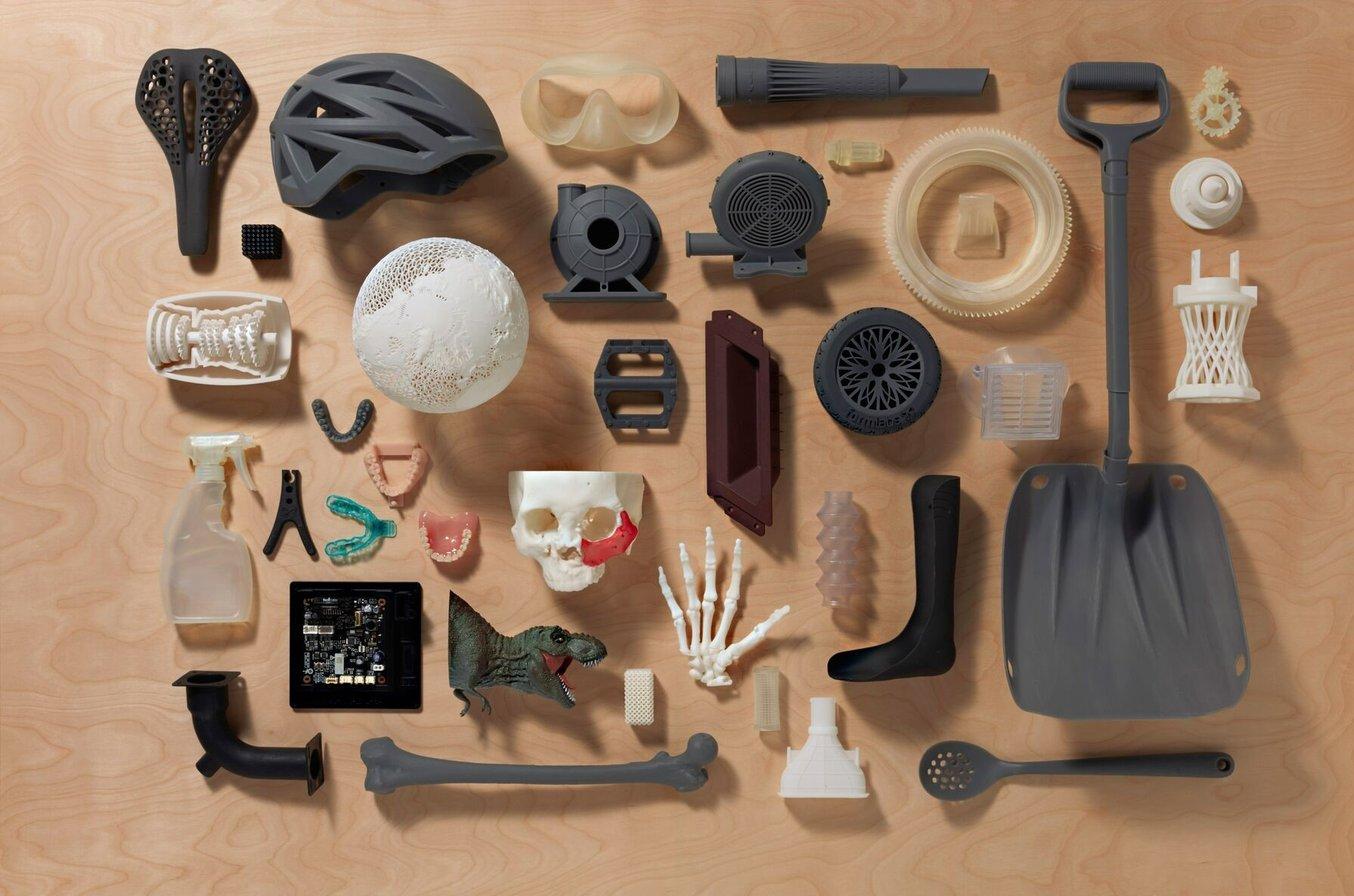
Formlabsでは、強度、剛性、靭性、耐熱性、耐薬品性、絶縁性など各材料特性を高水準で備えた高機能材料が利用できる。
日本のものづくりの歴史は、ほぼイコール金属加工でのものづくりの歴史です。そのため日本の技術者の多くは樹脂材料より金属材料の扱いに慣れているという方も多くいらっしゃいます。こと材料選定となった際に念頭に置くべきことはいくつかありますが、ここではまず金属材料と樹脂材料の特徴の差を整理した上で、必要な特徴を持つ材料を選ぶ際のヒントを見ていきましょう。
押さえておくべき金属と樹脂の主な違い①
まず1つ目は、材料選定に限らず製品設計、特に強度計算に関わる違いです。一般的に金属は、合金であってもその機械的特性は非常に安定しており、例えばシート状の材料の端から端までがすべて同等の特性を備えていると考えられています。一方で、3Dプリント用材料に限らず樹脂の一般的な特徴として、よく「樹脂は練りもの」と言われるように多数の化学物質を混ぜ合わせて狙った材料特性を発揮できるよう調合して作られます。そのため、金属と比較すると材料の機械的特性にはばらつきが発生しやすく、シート状の材料でも端から端まですべて同じ特性を備えているとは限りません。もちろん特性のばらつきは大きなものではありませんが、製品設計を行う際の注意点として「その材料特性の限界値ギリギリで使用する」という使用方法にはリスクが伴います。上述のように僅かであったとしても材料特性にはばらつきがあるためです。
金属材料使用時に、その強度や硬さの限界を把握してギリギリ耐えられる地点で使用するという考え方には、強度が高く硬い材料になるほどコストが上がってしまうという点が理由となっているケースも多く見受けられます。当然構造部など安全に直接関係する箇所の設計にこの考え方は適用されないまでも、安全バッファーを設けずに設計を行う場合はその部品や材料の挙動が完全に把握、あるいは管理できる場合に限られるかと思います。樹脂材料の場合は、強度や硬さ、耐熱性などがより高い材料でもコストに大きな差が無いケースもあります。また、既に安定した状態の材料を加工する切削や圧造等とは違い、3Dプリントでは材料が安定する前に必要な形状を造形し、形ができた後に安定させることとなります。そのためユーザー側の作業によっても寸法精度や強度等の特性に差が出るという点も把握しておきたい点で、例えば機械的特性においても靭性が高い(柔らかい)材料であるほどプリント時のクセがあり、そのクセを把握して材料とモデルの形状に合った造形設定を行ってプリントを行うという点が、まさに3Dプリントを使いこなす上でのノウハウとなります。Formlabsではこの点で悩みをお持ちのお客様へのご相談窓口を設けています。個別相談ご希望のお客様は、以下よりご連絡ください。
押さえておくべき金属と樹脂の主な違い②
2つ目は、変形に関する違いです。一般的に、金属材料の変形には弾性変形と塑性変形があります。加わる荷重の大きさが弾性限界以下の弾性域内での変形であれば、荷重を取り除けば元の状態に戻ります。反対に弾性限界を超えた塑性域内での変形であれば、形状が元に戻らない塑性変形となります。わかりやすい例は、ボルトでしょう。ボルトは締め込むと、ねじ部のボルト軸が引き伸ばされます。引き伸ばす力が降伏点を超えるまでは元に戻ろうとする力が働くため、これが軸力と呼ばれる締結力になりますが、トルクをかけ過ぎる(過度に締め過ぎる)とボルトが降伏して(荷重が降伏点を超えて)しまい、ボルト軸の元に戻ろうとする力が失われ、締結力が消失してしまいます。
樹脂材料では、この塑性変形は起こりません。ゴムやシリコンなどの軟質材が最もイメージしやすいですが、樹脂材料は塑性変形できないため、曲げても引っ張っても破断しない限りは元の状態に戻ろうとする力が働きます。しかし樹脂材料の場合は粘弾性と言い、例えばPPやABSの薄板を折り畳むと元に戻ろうとする力は働いても完全に元の状態には戻らない場合もあります。この違いは、上で取り上げたねじ部など要素部品やその使用部位の設計など、幅広い箇所で関係してきます。ねじ部の場合は強度に懸念がある場合はインサートを使用する等の対策は可能ですが、試作品の場合はねじ部にこだわって全体の進行を遅らせる必要はないため、ねじでなくともピンやリベット等での暫定的な締結で事足りる場合も多くあるでしょう。
樹脂材料にも2種類ある
樹脂材料には、熱可塑性樹脂と熱硬化性樹脂の2種類があり、この2種は全く異なります。3Dプリンタには7種類の造形方式がありますが、方式の違いによってこの2種のうちどちらの材料を使用するかも違ってきます。私たちの身の周りにある殆どのプラスチックは熱可塑性樹脂で、射出成形のペレットのように加熱することで溶けて液状になります。対照的に、熱硬化性樹脂は架橋結合という非常に強固な分子構造となっているため加熱しても分子の運動量が一定以上に大きくならず、液状に溶けてしまうことがありません。
3Dプリントでは、光造形方式とPolyJetやインクジェットとも呼ばれるマテリアル・ジェッティング(MJ)方式の2方式でこの熱硬化性樹脂の1種である光硬化性樹脂を使用します。光硬化性樹脂は液体で、レジンとも呼ばれ、紫外線(UV)光に反応して光重合という化学反応を起こして固化します。光造形とMJの2方式はこの光重合を利用して3Dプリントを行う方式で、他の5方式は熱可塑性樹脂を溶かすかレーザーで焼結する、あるいは凝固剤を併用して固めることでプリントを行います。そのため光硬化性樹脂を使用する光造形とマテリアル・ジェッティングでは、材料がABSライク、PPライク、あるいはゴムライクといった熱可塑性樹脂同等の機械的特性が発揮できるよう開発された相当材となります。
Formlabsでは、光造形3Dプリント用材料として他では得られない高機能な高強度材料やゴムライク材料、特許技術で実現した100%純シリコン材料などを提供し、そして小ロット量産に対応するSLS(粉末焼結積層造形)方式のFuseシリーズ用には高強度工業用ナイロン材や軟質材のTPUなど、高機能材料を提供しています。
「光造形の良いところは、中まで材料がしっかり詰まるところと、材料特性が優秀なところです。〇〇ライクと呼ばれますが、本当にそれに近い性質がしっかりあります。ゴムライクなんかは特に優秀で、インクジェットではこれほどのゴムのような質感は表現できません。」
西野 晃一氏 株式会社エポック社 シルバニア本部技術室 マネージャー
「光造形のForm 3では、Grey、Grey Pro、Tough 2000(ABSライク)、Rigid 10K(ガラス分高配合材)レジンでマネキンの手先などを作っています。マネキンよりも慎重な扱いが求められるサービスロボットの外装部品は、特に輸送中や倒れた時に破損しない高強度材料が必要です。その点SLSのFuse 1で使えるNylon 12は高強度ながらある程度の靭性があり、すごく破損しにくい材料です。」
西田 真人氏 吉忠マネキン株式会社 東京店 マネキン・モデリング部 事業企画部
幅広い用途に:スタンダードレジン
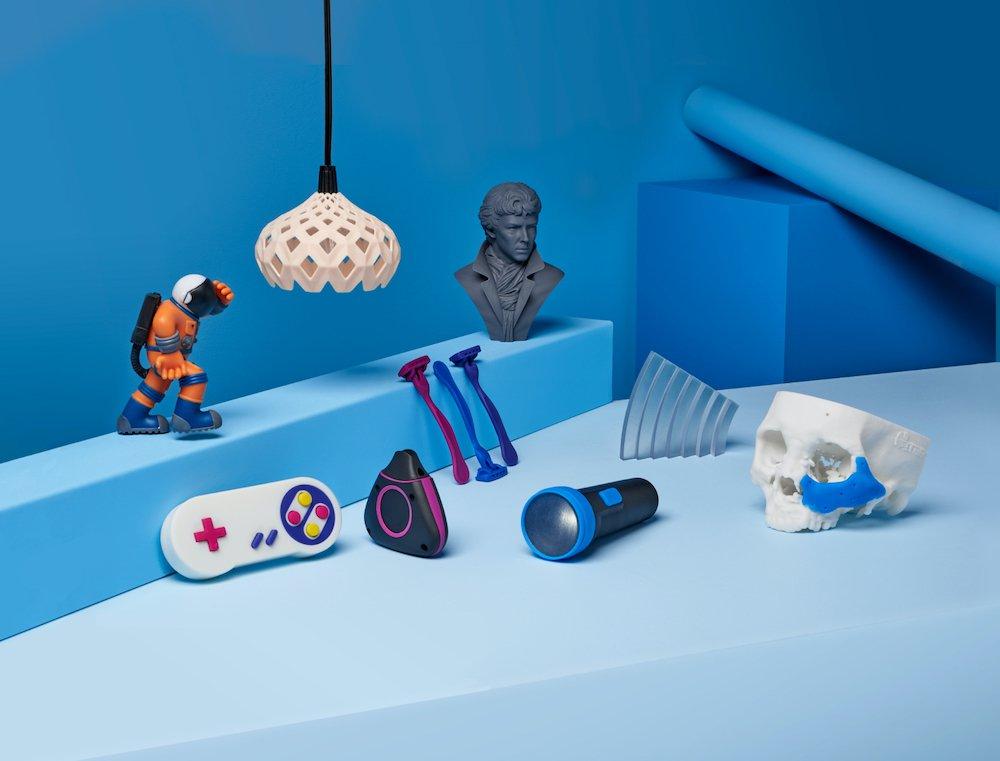
白・黒・グレーのモノトーン色レジン3種は機械的特性は同じだが、プリント時の特徴は異なる。他にも高速プリント用レジンや高靭性高耐久材料、自在にカラーリングが行えるものも。
Formlabsのスタンダードレジンには、7種のレジンがあります。これらスタンダードレジンは、他社製の汎用材料やFDM(FFF)で汎用材として一般的に提供されるPLA(ポリ乳酸)等よりも十分に高い強度があります。また、光造形という造形方式の特徴により、強度の異方性(荷重方向によって強度が変わること)がない点もFDMとの違いとなります。幅広く活用できるスタンダードレジンですが、各レジンごとに特徴があるため選定の際には以下情報を選定時の参考にご確認ください。
Greyレジン
光造形では材料色による光の吸収・反射もどこまでの精密表現が可能か等のパフォーマンスに影響します。GreyレジンはWhite、Black、Clear、Color Baseレジンと強度や靭性、耐熱などの材料特性は同じですが、他のレジンより精密表現や精緻な寸法精度を出したい場合におすすめします。
Blackレジン
やや光沢のある黒色であるため、陰影をはっきりと確認したい場合におすすめです。また、多くの製品での仕上げ時の質感に近い発色であり、特に外観にこだわる試作品や模型製作では人気のある材料です。White、Grey、Clear、Color Baseと強度や靭性、耐熱などの材料特性は同じで、精密表現度はGreyにやや分があります。
Whiteレジン
こちらはモノトーン3色の中ではプリント時のクセがあります。非常に微細な表現が必要なモデルではサポート材無しのビルドプラットフォーム上での直接プリントを行うより(デザインにより異なりますが)45~70℃の傾きでプリントすることをおすすめします。一方で塗装を施したい場合はそのまま塗装でき、最も扱いやすい材料です。
Clearレジン
光造形の特徴を活かした透明度の高い造形品が製作できますが、プリントしただけでは半透明の状態です。透明度を重視する場合、表面処理で透明度を向上できます。研磨での透明度向上とトップコートの併用が最も効果的ですが、研磨を避けたい場合は一般的なクリアラッカー等で2~3層のクリアコートを行えば、一切の研磨なしで筐体の内部機構が確認できるレベルの透明度は得られます。そうした試作が目的の場合は筐体にそれほど高い強度は必要ないケースも多いため、紫外線によって黄色がかってしまうのを避けるため、強度を出すことが主目的の二次硬化は行わず、洗浄後はクリアコートなどの表面処理に進みましょう。
Draftレジン
Formlabsの光造形用材料におけるトップセラーの一角で、他レジンと比べて最大4倍速でのプリントが行える高速造形材料です。紫外線に反応する成分を多く含むことで高速プリントを実現しますが、その分日光が当たる場所に置いた場合の劣化も早く進むため、2~3年以上の長期間使用するものを作る場合は他のレジンの方が良い選択肢となります(逆に言えば日光に当たらない環境であれば、多くの場合で1~2年程度なら大きな劣化はありません)。一方でDraftレジンは強度や精度も一定以上の水準で発揮できるため、高速で試作・検証サイクルを回したい場合は最高のソリューションです。使い方の詳細はサポートページをご覧ください。
Grey Proレジン
Greyレジンの精密表現度と寸法精度といったプリントのパフォーマンスを維持しつつも機械的特性(特に靭性と耐久性)を向上した材料で、クリープ耐性が高い点や、光硬化性樹脂でありながら耐光性が高いためプリント後の劣化に強く、中長期の使用にも対応できる点も特徴です。機能確認用試作や耐久性を要する治具製作、中長期で使用する模型や展示用途のモデル等におすすめします。詳細情報はサポートページをご覧ください。
高強度材料:Tough、Durable、Rigid
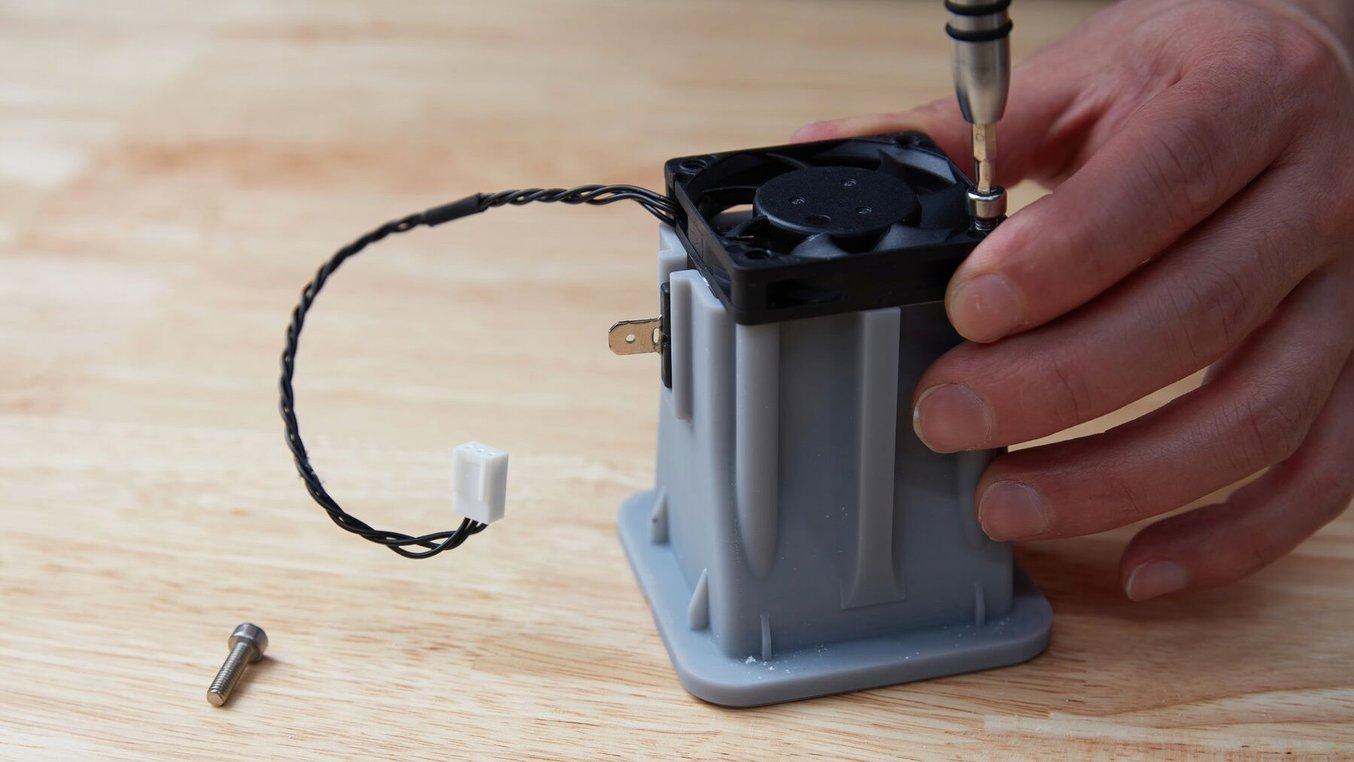
高強度材料のニーズは非常に多い。一方で、強度という言葉は非常に曖昧な言葉でもあり、材料選定時には硬さ(剛性)が必要なのか破断・破壊への強さ(靭性)が必要なのかは区別して考えることが必要。
材料選定の際に強度を考える場合、念頭に置くべきは強度という言葉は非常に曖昧な言葉で多彩な意味合いの強度を包括的に示す言葉であることを認識しましょう。例えばWikipediaで「強度」のページを見てみると、様々な意味合いでの強度が解説されています。そのため強度が重要な選定基準である場合は、材料選定の際に念頭に置くべき重要事項があります。
その重要事項とは、イメージしている「強度」が、例えば圧や荷重を受けても変形しないといった硬さ(剛性)を重視しているのか、あるいは衝撃や繰り返しの荷重を受けても壊れないといった耐久性(靭性)を、あるいは剛性と靭性のバランスを重視しているのかということです。意外にメーカーで設計に携わる方でもこの2つを混同して「強度」という言葉を使われるケースは多く、社内でも単に「高強度」という曖昧な表現が浸透しているケースも散見されます。部門内のメンバーが共通の目的を共有していたり、それを熟知する既存取引先とのコミュニケーションは問題なくとも、一歩外に出て新たな相手とコミュニケーションを取ったり材料選定の相談をする場合は、硬さと耐久性の違い、剛性と靭性のバランスはどの程度必要なのか等の「要件定義」を明確に行う必要があります。
Tough 1500レジン
ポリプロピレン(PP)同等の機械的特性を発揮できるよう開発されたTough 1500レジンは、PP同様にある程度の剛性はあるものの、靭性に優れた高耐久性材料です。製品名の「1500」はヤング率(引張と曲げの弾性率)の大まかな値を示しており、他のFormlabs製材料で名称に数値が入っている場合、高強度材料ではヤング率のおおよその数値とご理解ください。量産時にPPを使用する部品や、ばねをプリントして繰り返し使用することも可能です。また、一定の要件を満たした後処理を行えば皮膚接触に対応する生体適合性材料として使用できます。詳細はサポートページをご覧ください。
Tough 2000レジン
ABS同等の機械的特性を発揮できるよう開発されたTough 2000レジンは、日本国内でも最もよく使われている材料の一つです。ヤング率2GPaでありながら50%近い破断伸びを備え、割れにくく一定の硬さもバランス良く備えた高強度材料です。圧力や衝撃にも高い耐性がありますが、靭性が重要となる場合は荷重を受ける箇所の厚みなど設計面での配慮と材料特性を併せて考慮してください。他材料との比較を含めた詳細はサポートページをご覧ください。また、樹脂型のように高温環境下で圧を受けても変形しないという特性が必要な場合はRigidシリーズをおすすめします。
Durableレジン
ポリエチレン(PE)同等の機械的特性を発揮できるよう開発されたDurableレジンは、例えば洗剤のスプレーボトルのように圧をかけると凹み等の変形を起こしても即座に元の状態に戻る性質、そして摩擦係数の低い独特の触感が特徴です。ゴムライク材料と違い、ある程度の剛性がありながらも柔らかい材料をお求めの場合は是非ご検討ください。食品安全や生体適合性が不要な用途であれば、ガスケットやパッキンのような用途にも対応し、こちらも国内外で非常に多くの企業で活用されています。詳細はサポートページをご覧ください。また、BioMed Durableという生体適合性を備えたバージョンもご用意しています。
Rigid 4000レジン
Rigidシリーズのレジンは、ガラス充填によって剛性を強化した材料です。一般的に光造形方式の3Dプリントでは、剛性が高いほど微細表現に優れ、また突出形状(オーバーハング)でもサポート材なしでプリントできる度合が大きくなります。Rigid 4000はTough 2000の2倍程度のヤング率を備えた高剛性材料で、靭性を高水準に兼ね備えるToughシリーズ以上に微細形状の表現などプリントの自由度が高い材料です。また、他のレジンより耐光性にも優れています。一方で、高剛性材料であるため、特に薄肉形状では限界以上の衝撃や圧が加わると割れてしまいます。詳細はサポートページをご覧ください。
Rigid 10Kレジン
Rigid 4000よりも更にガラス充填率を上げた極高剛性材料です。ガラス分の高配合によって、圧や荷重を受けてもほぼ全く変形せず、極めて高い耐熱性も備えることから樹脂型・簡易型のプリントにも数多く採用されています。また、耐光性、耐薬品性にも優れており、ガラス繊維強化プラスチック(GFRP)並みの剛性と強度があることから、工業用途で多く選ばれる材料です。詳細はサポートページをご覧ください。
高い強度と他の特性を併せ持った材料
材料選定時に高強度が条件となるケースでは、強度の他にも耐熱性、耐薬品性などを兼ね備えた材料が求められるケースも多くあります。上で紹介したRigid 10Kレジンは、極めて高い剛性に耐熱性と耐薬品性、耐光性を備えた高機能材料の好例です。Formlabsでは、例えば以下のような材料もご用意しています。
- Flame Retardant(難燃性)レジン:FRレジンはUL 94のV-0認証を取得した難燃性材料で、当然ながら高い耐熱性も備えています。また、直接造形品にタップを切っても割れない強度を持ち、電子機器を中心とした機能確認用試作や難燃部品の小ロット量産で使用されています。サポートページはこちらです。
- ESDレジン:光造形では非常に珍しい、静電気散逸性(静電気拡散性とも)材料で、特に基板実装前のICチップトレイや電子部品の保管・運搬用品、治具や固定具などに使用され、静電気による損傷から電子部品を保護します。FDM(FFF)方式ではABS系の材料でESD材料が販売されていますが、FormlabsのESDレジンはABS系材料を超える強度を備え、電子部品製造工程のあらゆる治工具に採用されています。サポートページはこちらからご確認ください。
ゴムライク/軟質材:Flexible、Elastic、Silicone
Formlabsのゴムライク材料は、何年も前から非常に高く評価され、世界的に非常に多くの企業で活用され続けています。また、2023年9月には、独自の特許技術Pure Silicone Technology™によって実現した100%純シリコン材料であるSilicone 40Aレジンが、続く10月には従来のFlexible 80AとElastic 50Aの生体適合性バージョンであるBioMed Flex 80A、BioMed Elastic 50Aレジンが発売され、3Dプリンタの中では最多の軟質材の選択肢を提供しています。
ユーザー側に求められるプリントのノウハウという点では「硬いほどいろいろな形状に対応しやすい」という原則の通り、比較的ノウハウが求められる度合いは高くなります。導入前のご相談や導入後にサポートを必要とされるお客様は、以下よりFormlabsまでご連絡ください。
Flexible 80Aレジン
推奨値での二次硬化後、ショアA硬度80Aとなる硬質ゴムライク材料です。Formlabsのゴムライク材料は、二次硬化時間を調整することで硬さをある程度調整することも可能です。硬質ゴムやシリコン製品の試作品、製造や組立ラインにおけるワーク受け治具の表面、ロボットのエンドエフェクタ、ハンドルやグリップ部、シール材やガスケットなど多彩な試作品に対応します。プリント時の注意点を含む詳細は、サポートページをご覧ください。
Elastic 50Aレジン
推奨値での二次硬化を経て、ショアA硬度50Aとなる軟質ゴムライク、あるいはシリコンライク材料です。曲げ、伸び、圧縮等の負荷に強く、それらの環境下でも割れずに元の形状に戻ることができます。シリコン部品の試作品や衝撃吸収部材、ワーク受け用の治具、ピックアンドプレースロボット等のエンドエフェクタ、ウェアラブルデバイスの試作品など幅広く活用されています。詳細はサポートページをご覧ください。
Silicone 40Aレジン
Formlabs独自の特許技術 Pure Silicone Technology™で実現した、100%の純シリコン材料です。Form 3シリーズの価格帯で純シリコン材料が使用できるという点自体が大きなメリットとなるため、シートからの切り出しや成形を行うことなく手軽にシリコン部品の試作や実製品用部品の製造が行えます。1mm厚程度までのプリントは問題なく行えますが、複雑形状の場合はサポート材の除去に少し労力と時間を要します。その場合は軟質材の利点を生かし、CAD上で土台やサポートを自身で付加してプリント後に切除する等の対策が行えれば、後処理時間は大きく削減可能です。サポートページはこちらです。
BioMed Flex 80Aレジン
Form 3Bシリーズ(Form 3B, 3B+, 3BL)でご使用いただけるショアA硬度80Aの生体適合性硬質ゴムライク材料BioMed Flex 80Aレジンは、ISO 10993およびUSP Class VI認証取得済み材料で、米FDA登録済みのISO 13485認証取得済み工場で製造されています。長期皮膚接触(30日以上)と短期粘膜接触(24時間未満)にて生体適合性認証を取得しており、硬質ゴムライクの模型製作やウェアラブルデバイスの部品、医療機器や器具にてご使用いただけます。詳細はサポートページをご覧ください。
BioMed Elastic 50Aレジン
BioMed Flex 80A同様に、Form 3Bシリーズ(Form 3B, 3B+, 3BL)で使用可能なショアA硬度50Aの生体適合性軟質ゴム/シリコンライク材料BioMed Elastic 50AレジンもISO 10993およびUSP Class VI認証取得済み材料であり、米FDA登録済みのISO 13485認証取得済み工場で製造されています。長期皮膚接触(30日以上)や短期粘膜接触(24時間未満)を含むあらゆる用途で装着時の快適性と視覚的な透明度が必要なウェアラブルデバイスの部品、医療機器や器具にてご使用いただけます。詳細はサポートページをご覧ください。
高耐熱材料:High Temp、Rigid 10K、FR、Alumina
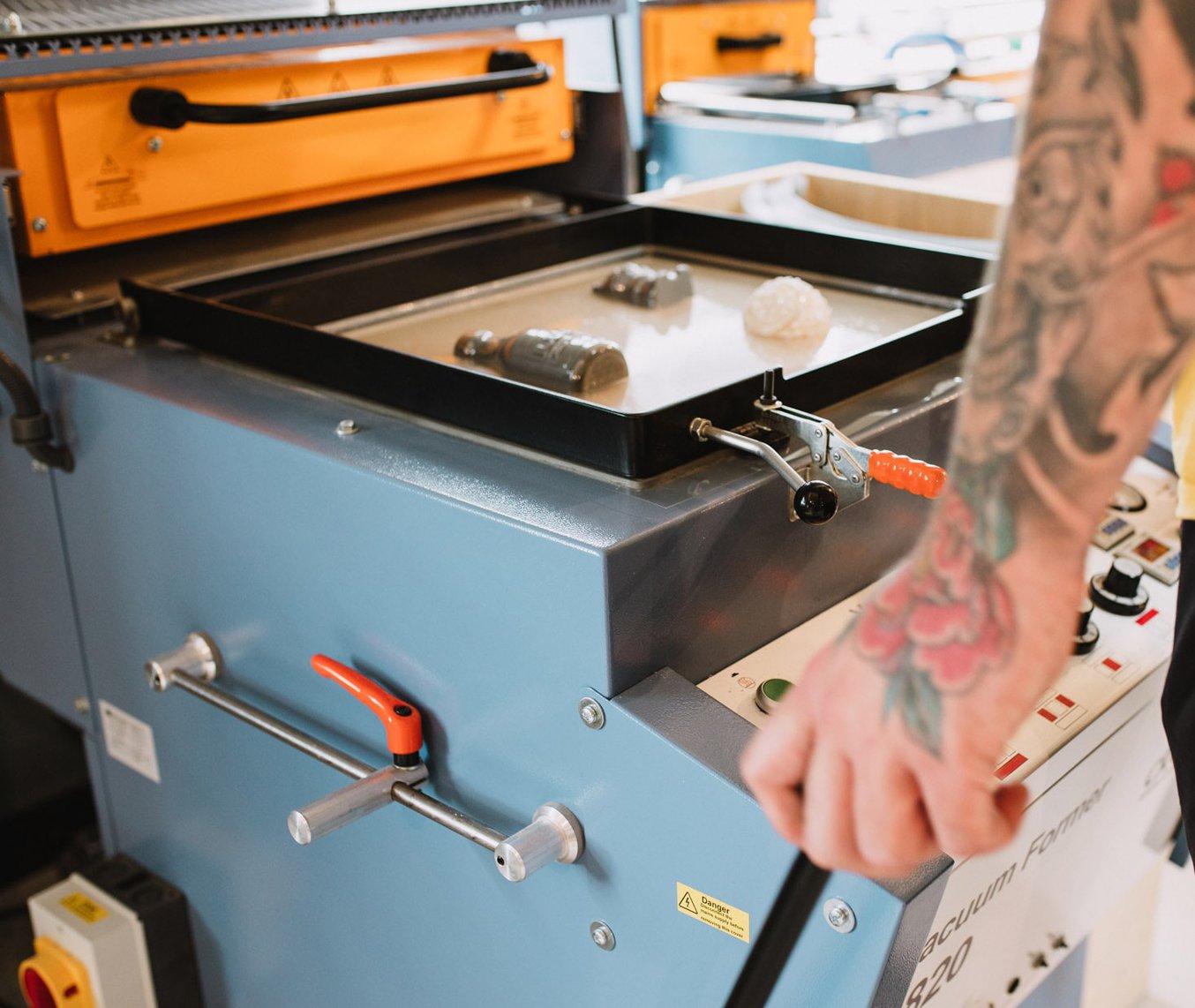
コスメブランドLUSHは真空成形の金型にFormlabsの各種レジンを使用する。先述の通り光造形で使用される光硬化性樹脂は加熱によって溶けることはない。樹脂材料で耐熱性(温度安定性)の指標となる荷重たわみ温度(熱たわみ温度とも呼ばれる)は「対応温度帯」とは全く異なることを知っておく必要がある。
Formlabsに寄せられる高耐熱材料についてのご相談では、単に高温に強いだけの材料では用を成さないケースが殆どです。製造業において高温環境に晒される製品・部品の殆どは高温環境下で一定の荷重に晒され、高温だけでなく「高温環境下での荷重」に耐える必要があります。そこで思い出したいのが、光造形方式で使用する光硬化性樹脂は熱硬化性樹脂の一種で、冒頭で触れたように熱可塑性樹脂のように加熱によって溶けることはないということです。
そのため樹脂材料の耐熱性(温度安定性)の目安となる指標、荷重たわみ温度(熱たわみ温度とも呼ばれる)を金属部品の対応温度帯と同様に受け取ってしまう誤解をされる方が非常に多くいらっしゃいます。実際には、規格で定められたサイズの試験片に圧力子で既定の圧(高圧:1.8MPa、低圧:0.45MPa)を加えた状態で昇温させ、たわみが一定の程度に達した時点での温度が荷重たわみ温度です。くどいようですが、光硬化性樹脂である光造形用レジンは荷重たわみ温度を超える高温に晒されても溶けて液状化することはありません。従って、モデルの形状が当該試験での試験片以上の厚みがあれば、それ以上の温度にも十分耐え得るということを理解しておきましょう。
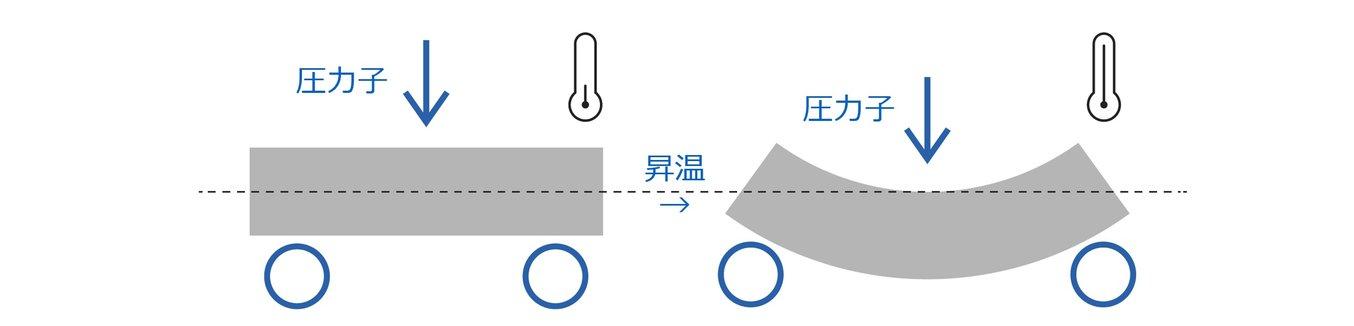
荷重たわみ温度試験の概念図。荷重たわみ温度(HDT/Heat Deflection Temperature)は、厚み6.4mm(ASTM D 648-16)等の既定の試験片が1.8Mpaまたは0.45MPaの圧を受けた状態で既定の変形を起こした時点での温度を測定する。材料の対応温度帯とイコールではない点に注意したい。
High Tempレジン
High TempレジンはFormlabsの光造形用材料の中で最高の耐熱性を備え、洗浄後にForm Cureにて80℃で120分間の二次硬化を行い、更に工業用オーブン等の炉に入れて160℃で180分加熱する熱硬化処理を行うことで、238℃の荷重たわみ温度(0.45MPa時)を発揮します。剛性が非常に高い一方で靭性が低いため、高い荷重や圧力が加わると割れてしまうことがあります。高い荷重や圧に晒される用途で使用する場合はRigid 10Kレジンをおすすめします。High Tempレジンの詳細はサポートページをご覧ください。
Rigid 10Kレジン
高強度材料のセクションでご紹介の通り、Rigid 10Kはガラスを高い割合で充填することで剛性と耐熱性を向上しており、高い荷重や圧にも割れずに耐えることができます。そのため射出成形や熱成形/真空成形での金型(樹脂型)としても使用され、他には流体解析用の試験用モデルなどにも頻繁に使用されます。Rigid 10Kは、洗浄後にForm Cureにて70℃で60分の二次硬化を行った後、更に工業用オーブン等の炉に入れて90℃で125分加熱する熱硬化処理で218℃の荷重たわみ温度(0.45MPa時)を発揮します。詳細はサポートページをご覧ください。
Flame Retardantレジン
UL 94のV-0グレードの難燃性を持つFlame Retardantレジンは、高い耐熱性も備えています。Form Cureにて80℃で120分間の二次硬化を行うことで0.45MPa加圧時の荷重たわみ温度で111℃の耐熱性となり、厚みが大きくなればそれ以上の高温環境下でもご使用いただけます。火炎に直接触れる場合や防火上の配慮が必要な部品および治具での使用をおすすめしています。詳細はサポートページをご覧ください。
Alumina 4Nレジン
純度99.99%の4Nグレードのアルミナセラミックスを3DプリントできるAlumina 4Nレジンは、セラミック粉末をバインダー(凝固剤)代わりの光硬化性レジンに充填した材料です。プリント後に工業用オーブン等の炉に入れ、樹脂を飛ばす脱脂とセラミック成分を焼成する焼結の2段階の焼き入れにより純粋なセラミック部品を得ることができ、対応温度帯上限は1,500℃となります。樹脂のバインダーを使用する金属3Dプリント同様に、炉で樹脂を飛ばすことで収縮が発生するため、CAD上でXY軸を121.8%、Z軸を126%に拡大して寸法精度を調整しますが、そこから更に微調整を要するケースもあります。詳細はサポートページをご覧ください。
用途によっては他の選択肢も
何度も触れてきた通り、熱硬化性樹脂の一種である光硬化性樹脂を使用する光造形方式の3Dプリント用材料(レジン)は、どれだけ高温に晒されても溶けて液体になることはありません。そのため汎用材料であるスタンダードレジンでも、以下のような用途で活用しているお客様がいらっしゃいます。
- Clearレジン:2液シリコンでのシリコン成形用の注型を製作
- Draftレジン:真空成形の金型をプリント
- Greyレジン:真空成形、熱成形の金型として、または卓上射出成形機で使用する簡易型を製作
生体適合性材料BioMedシリーズのオートクレーブ滅菌
医療グレードの生体適合性材料であるBioMedシリーズレジンは、オートクレーブでの滅菌処理に対応しています。新製品で検証が未完了のものもありますが、オートクレーブでの滅菌処理に関するレポートとガイドラインをお求めのお客様は、以下よりFormlabsまでお問合せください。
電気的特性:絶縁性と静電気散逸性
殆どの樹脂材料は非常に大きな電気抵抗を持ち、絶縁性材料に分類されます。例えば、電子部品の製造現場において重要な静電気に関する特性では、IEC 61350-5-1の規定では、表面抵抗率PSが、1×102~1×105Ω/sq未満であれば静電気導電性、1×105~1×1011Ω/sqの間であれば静電気散逸性(静電気拡散性とも呼ばれる/アース線のように接地していれば静電気を消散する)、1×1011以上であれば静電気絶縁性に分類されます。一般的な絶縁性を示す指標は体積抵抗率や誘電率、誘電正接などがあります。
材料の自社開発を行うFormlabsでは、ESDレジンのように非絶縁性を達成することが目的となった材料以外は、社内標準にて全ての光造形用レジンが以下の基準を満たすよう開発されています。
- 表面抵抗率:2 x 1014(Ω/sq.)以上
- 体積抵抗率: 1.7~1.8 x 1014(Ω・m)間
※ESDレジンを除く
ESDレジン:静電気散逸性 / 静電気拡散性材料
特に基板実装前の電子部品やICチップの取扱において重要な静電気対策。ESDレジンは、近傍の作業台などに接地させて使用することでアース線のように静電気を逃がし、電子部品を静電気による損傷から保護します。強度は他社製品やFDM方式のABS系ESDフィラメントよりも高水準で、治具や工具、実装作業ロボットのエンドエフェクタや光造形ならではの精度を活かしたチップトレイなど、電子部品/電子機器の上流工程で幅広く使用されます。詳細はサポートページをご覧ください。
Flame Retardantレジン
V-0グレードの難燃性を持つFlame Retardantレジンは、15.1 kV/mmの絶縁耐力、ASTM D150/1 MHzにて3.82の誘電率と0.025の誘電正接を備えた絶縁性にも優れた材料です。材料特性の詳細情報はデータシートページより「Flame Retardantレジン」を検索ください。また、使用方法の詳細についてはサポートページをご覧ください。
Alumina 4Nレジン
工業用セラミックの代表格であるアルミナセラミックスを純度99.99%の4Nグレードにて3Dプリントが行えるAlumina 4Nレジンは、焼成後に樹脂が飛ばされ、完全なセラミック品となるため非常に優れた絶縁性と耐熱性を発揮します。Alumina 4Nレジンの造形品の対応温度帯上限は1,500℃となり、1x1014(Ω・m)以上の体積抵抗率、1 MHzにて9.8の誘電率と9x10-5の誘電正接を備えています。詳細はサポートページをご覧ください。
電気的特性は表面処理で向上することも
実製品用パーツの量産時はもちろん、機能確認用試作や製品試作においても製品同様の電気的特性を備えた部品製作が求められます。本セクション冒頭で触れた通り、一般的に樹脂材料は元来絶縁性であり、Formlabs製3Dプリント用材料も社内標準にて表面抵抗率や体積抵抗率が標準化されています。もし材料の絶縁性や導電性が目的を満たしていない場合は、表面処理で電気的特性を補強することも検討してみるのがおすすめです。導電性を付加または強化するには、金、銀、銅、ニッケル等のめっき処理や蒸着が可能です。逆に絶縁性を向上したい場合はセラミックコーティングやPEEKコーティング等を施せば、より高い絶縁性を得ることができます。
耐薬品性材料:Rigid 10K、Silicone、Alumina
耐薬品性が材料選定の要件となる場合、考えておきたい点があります。これは耐薬品性に限ったことではありませんが、もし現在検討中の用途が金属部品との置き換えである場合、既設の金属部品と同等の耐薬品性が本当に必要かという点です。樹脂材料の耐薬品性は、一般的にはSUS等の合金に比肩する水準に達するのは難しく、無加工の樹脂材料をそのまま工業水準で見た場合の「高い耐薬品性」を発揮できる材料は非常に限られます。
そのため、樹脂3Dプリント品を高い耐薬品性が求められる用途で使用する場合は、併せて以下の使用方法を検討されることをおすすめします。耐薬品性が求められる用途の多くは、当該部品が化学物質や薬品による劣化で破断した場合、設備機器自体の不具合につながる、あるいは異物混入リスクを抱えることとなります。一方で、上手く3Dプリント品を活用できればすぐにその場で当日中に必要な部品がプリントできるというスピードとコスト両面の利点があります。それらを総合的に判断し、以下を検討しつつ導入を進めるのが良いと思われます。
- 表面処理による耐薬品性の向上
- 当該部品の交換サイクルの検証と見直し
- 対象となる化学物質や薬品に浸漬または晒される時間の見直し
Rigid 10Kレジン
マットで美しい白に仕上がる独特の質感を持つRigid 10Kレジンは、ガラスを高い割合で充填することで剛性と耐熱性だけでなく、耐薬品性も非常に高水準で備えています。機械的特性の特徴は、極めて高強度高剛性である一方で靭性が僅かである点で、射出成形の金型(樹脂型)として使用しても型締めや射出の圧に耐える強さはありますが限界を超えると脆性破壊により割れが生じてしまいます。詳細はサポートページをご覧ください。
Silicone 40Aレジン
独自の特許技術 Pure Silicone Technology™により100%の純シリコン材料での光造形3Dプリントを実現した本材料では、シリコンそのままの高い耐薬品性を発揮することができます。サポートページはこちらです。
Alumina 4Nレジン
プリント後に樹脂を飛ばして焼成することで、4Nグレードとなる純度99.99%のアルミナセラミックス品が得られる本材料では、工業用セラミックとして多用されるアルミナセラミックスの特徴である1,500℃までの対応温度帯、絶縁性、そして耐薬品性を活用いただけます。詳細はサポートページをご覧ください。
ロストワックス鋳造マスター
ロストワックス鋳造またはインベストメント鋳造と呼ばれるワックス(蝋)でマスターを製作して鋳造を行う方法で、宝飾や歯科だけでなく製造業においてもアルミなどのダイキャスト品を製造する際に使用されます。また、光造形用材料ではセラミックのAlumina 4Nレジン同様にプリントと洗浄が完了した後、二次硬化が不要である点も特徴です。Formlabsでは、ワックス充填率が異なる2種の材料をご用意しています。作業工程の詳細はサポートページをご覧ください。
- Castable Waxレジン:ワックス充填率20%の紫色の材料です。ワックス充填率を低めに抑えることで硬さを維持し、非常に繊細な形状を表現することができます。Form 3シリーズのすべてのプリンタでご使用いただけます。
- Castable Wax 40レジン:ワックス充填率40%の青色の材料です。石膏インベストメントにも対応し、Castable Waxよりもやや劣りますが複雑なデザインにも対応します。Form 3Lと3BLの大容量プリンタには対応しておらず、デスクトップサイズのForm 3, 3+, 3B, 3B+のみの対応です。
小ロット量産対応SLS方式
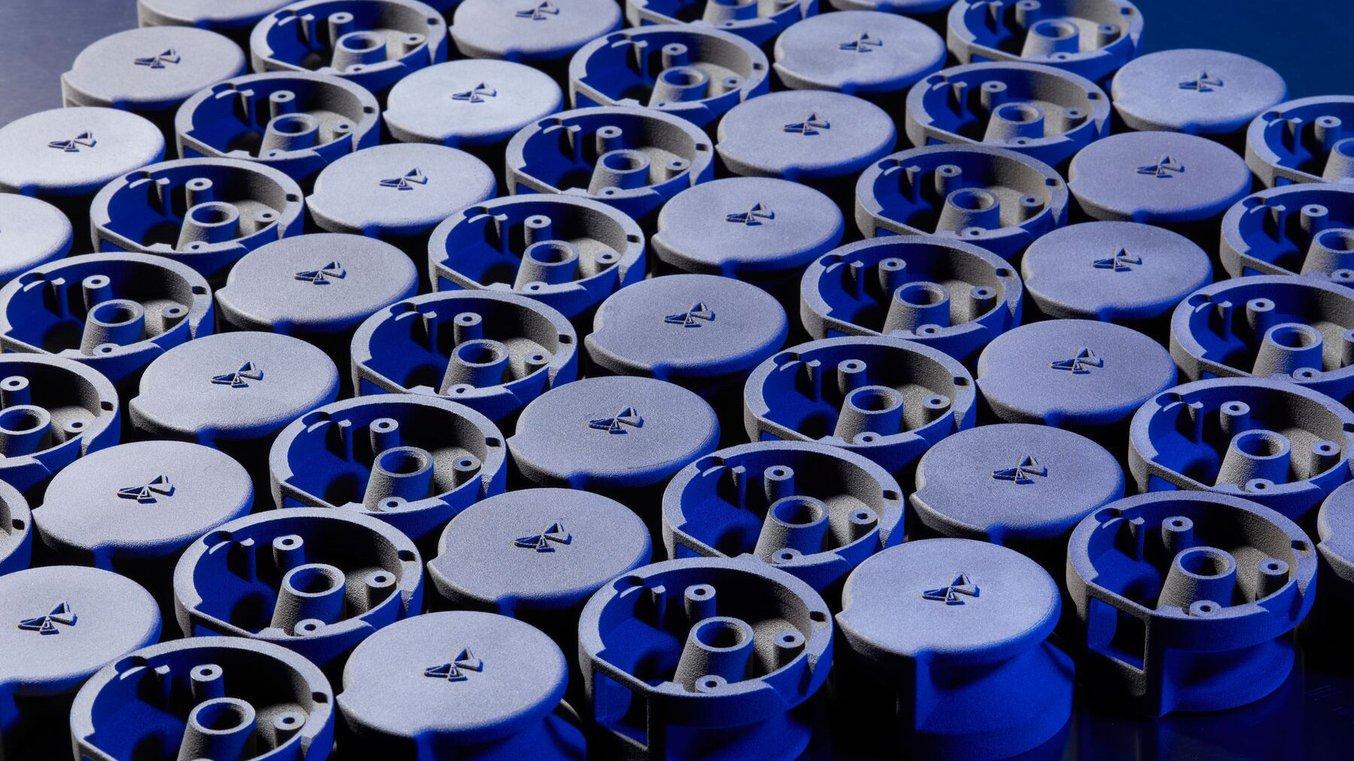
小ロット量産に対応するSLS方式Fuseシリーズでは、1,000万円以下のシステムで3Dデザインさえ行えれば月産200~500程度の量産が内製化できる。
量産対応のSLS(粉末焼結積層造形)方式であるFuseシリーズは4,000万円以上の価格帯でしか入手できなかったSLS方式を1,000万円強の価格帯に低価格化・小型化しつつ独自の特許出願中技術でそうしたハイエンド機と同等以上の造形品質を実現し、2023年11月には作業時間と労力を要する粉末除去やブラスト、研磨までの後処理をワンストップで行う自動仕上げ装置Fuse Blastもラインナップに追加。SLSでの3Dプリントを劇的に効率化しています。
以下ではFuseシリーズで使用可能な材料をご紹介します。Fuseシリーズプリンタはビルドチャンバーと呼ばれるチャンバー内のスペースでプリントを行います。ビルドチャンバー内寸はW165×D165×H300mm(四隅はアール形状)ですが、各材料の特性によって使用可能なスペースサイズが僅かに異なります。以下では各材料ごとの使用可能な最大スペース寸法もご紹介しますが、各材料の最大寸法を極限まで使用するのではなく多少の安全バッファーを見込んだプリントを行うことを推奨します。
Nylon 12パウダー
Nylon 12パウダー使用時の最大造形サイズ:W159.8×D159.8×H295.5mm
※今後のソフトウェアアップデート等により僅かに変動する可能性があります
工業水準の高い強度と一定の靭性を持ち、硬さと破断に対する耐性を兼ね備えた万能材料であるNylon 12は一般的にPA12とも呼ばれています。ナイロン材の中では耐熱性にも優れ、高温環境下においてもその特性を発揮できることから既に幅広く工業用途で使用されています。また、プリント時のクセも少なく微細表現にも高い性能を発揮します。3Dプリントならではの形状や外観上のデザイン、表面のテクスチャ(シボ)や文字入れ等にも多彩な選択肢が担保できます。また、皮膚接触に対応する生体適合性材料であるため、直接肌に触れる用途にもご使用いただけます。そういった多彩な利点から、国内外で最も多く採用されているSLS用材料です。
また、SLSでは材料の再利用が可能ですが、再利用時に未使用の新品パウダーを混合する比率である材料リフレッシュ率に関しては、30%で経済的に運用いただけます。詳細はサポートページをご覧ください。
Nylon 11パウダー
Nylon 11パウダー使用時の最大造形サイズ:W158.6×D158.6×H294.4mm
※今後のソフトウェアアップデート等により僅かに変動する可能性があります
ある程度の剛性は備えながらも、高水準の靭性を備えた一般的にPA11とも呼ばれる高耐久性材料で、PA12とは対照的に低温環境でもその特性を発揮するとされています。PPの強度と耐久性を一歩向上させたようなイメージで使用でき、100%生物由来のバイオ材料である点からも、特に近年消費者向け製品やウェアラブルデバイス、義肢装具などを中心に採用数が増えています。また、皮膚接触の生体適合性も備えています。デザイン面では高い靭性を有するため、微細表現性能はNylon 12と比較するとやや低くなり、細かな凹凸や穴あけ、あるいは設計上のクリアランスには余裕をもった寸法が必要です。プリントにおいては空気環境では50%の材料リフレッシュ率ですが、窒素環境でプリントすることでリフレッシュ率を30%に抑えてコスト効率を向上することが可能です。詳細はサポートページをご覧ください。
Polypropyleneパウダー
PPパウダー使用時の最大造形サイズ:※新製品のため確認中
※近日中に本ページおよびこちらの設計仕様ページにてお知らせいたします
汎用プラスチックのポリプロピレン(PP)で、軽量で耐薬品性が高く、靭性に優れた材料です。3Dプリント品同士だけでなく、成形品も含めてPP品同士の溶着が可能であるため、最大造形サイズに収まらない自動車のバンパーのような大型品でも分割してプリントした後に溶着で一体化することが可能です。0.7mm程度の薄肉構造の表現も可能で、一般的なPP同様に折り畳んだ際にもすぐに割れることはなく、白い折線が入ってぐにゃりと曲がります。Nylon 11と比較してやはり強度は落ちますが、衝撃や曲げ荷重で割れにくいため、用途によってはPPパウダーの方が安全性は高いという考え方もあるでしょう。汎用プラスチックのため材料費がFormlabsの全パウダー中最も安価です。
靭性が高い材料であるためパウダーが凝集してダマになりやすく、ご使用時にはFuse Siftのシーブを既設の150μmシーブから別売りの300μmシーブに交換してご使用いただく必要があります。詳細はSLS設計ガイドラインやサポートページをご覧ください。
TPU 90Aパウダー
TPU 90Aパウダー使用時の最大造形サイズ:W152.1×D152.1×H294.9mm
※今後のソフトウェアアップデート等により僅かに変動する可能性があります
ショアA硬度90Aの高強度軟質材です。SLS方式での軟質材では珍しく、高水準の引裂強さを備えながら高い破断伸びも有しています。TPU 90Aも皮膚接触の生体適合性材料であるため、スポーツ用品や義肢装具などの衝撃吸収部材やウェアラブルデバイスのベルトや肌に当たる部分の保護部材、生産/組立用治具やマスキング治具など幅広くご使用いただけ、20%という最少の材料リフレッシュ率でコスト効率も非常に高い材料です。また、設計面においてもプリント設定においても、軟質材にはクセがあるという原則が本材料にも当てはまります。詳細はSLS設計ガイドラインやサポートページをご覧ください。
Nylon 12 GFパウダー
Nylon 12 GFパウダー使用時の最大造形サイズ:W160.1×D160.1×H297.3mm
※今後のソフトウェアアップデート等により僅かに変動する可能性があります
Nylon 12にガラス充填を行うことで、元来の強度と耐熱を向上した複合材料です。ガラス成分由来の高い剛性と耐熱性があるだけでなく、Nylon 12の特徴でもある微細表現能力も引き継いでおり、剛性を活かしてねじ部を直接プリントすることもできるため、ねじ部を備えた部品が3Dプリントで直接量産いただけます。一方で、剛性が非常に高いため薄く長い壁や板状の形状は一定以上の負荷に晒されると割れる恐れがあります。プリント面では複合材料であることからクセがあり、一定の習熟期間を設けて運用を開始することをおすすめします。詳細はSLS設計ガイドラインやサポートページをご覧ください。
Nylon 11 CFパウダー
Nylon 11 CFパウダー使用時の最大造形サイズ:W162.0×D162.0×H287.6mm
※今後のソフトウェアアップデート等により僅かに変動する可能性があります
Nylon 11をベースにチョップドファイバーの炭素繊維を複合した材料です。比強度(強度重量比)に非常に優れるだけでなく耐熱性も高水準で兼ね備え、モビリティ製品やドローンや産業機械、重機の非構造部の高強度部品にご使用いただけます。炭素繊維の3Dプリント材料は、軽金属並みの強度(この場合は剛性を指します)が謳われる反面、靭性に乏しいため衝撃が加わると割れてしまうものが多い中で、Formlabsでは靭性に優れたNylon 11をベースにすることで、耐衝撃性や耐久性も高水準に発揮できるよう開発しています。一方で、炭素繊維の特性により生体適合性はありません。
複合材であるためNylon 12 GF同様にプリント時のクセがあるため、一定の習熟期間を設けて以降の運用開始をおすすめします。また、プリントプロセスによって繊維がX軸方向に向けられることでX軸方向の強度が最も高くなり、強度に異方性が生じます。詳細はSLS設計ガイドラインやサポートページをご覧ください。
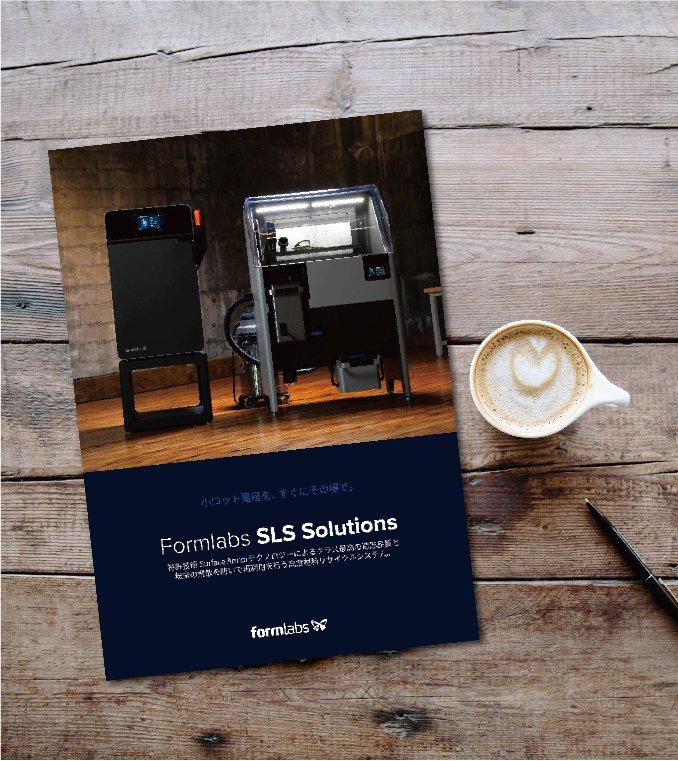
Formlabs SLS製品総合カタログ
本総合カタログでは、FormlabsのSLS方式3Dプリントシステム、Fuseシリーズ独自の特許技術や詳細の解説、各パウダー材料の一括比較と詳細、使い方ガイド等SLSの情報を総合的にご紹介します。
材料選定支援ツール Material Selector
Formlabsでは、アンケート形式でお客様側の用途や要件を回答していくだけでAIが最適と思われる材料を提案する材料選定支援ツール、Material Selectorを無料で提供しています。本ページの材料情報を参考に選定いただきつつ、こちらのツールで選定された材料も比較検討するという使い方にもご活用いただけます。
材料選定でお困りの場合やお客様のお手元にある3Dデータでのテストプリントをご希望の場合はFormlabsまでお問合せください。お見積のご依頼は正規代理店までご連絡をお願い申し上げます。
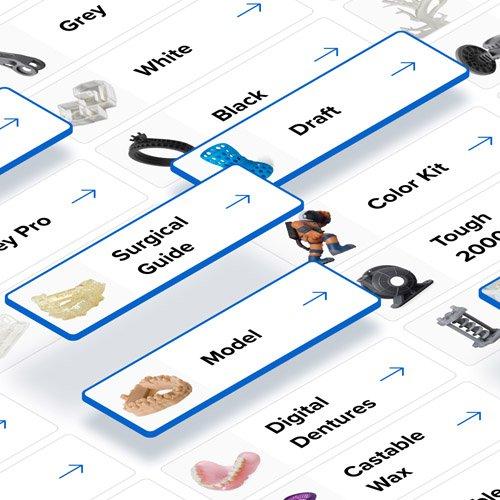
Material Selectorで条件に合う材料をチェック
Formlabsでは、いくつかの質問に答えるだけで最適な条件をAIが提案する材料選定支援ツールをご用意しています。