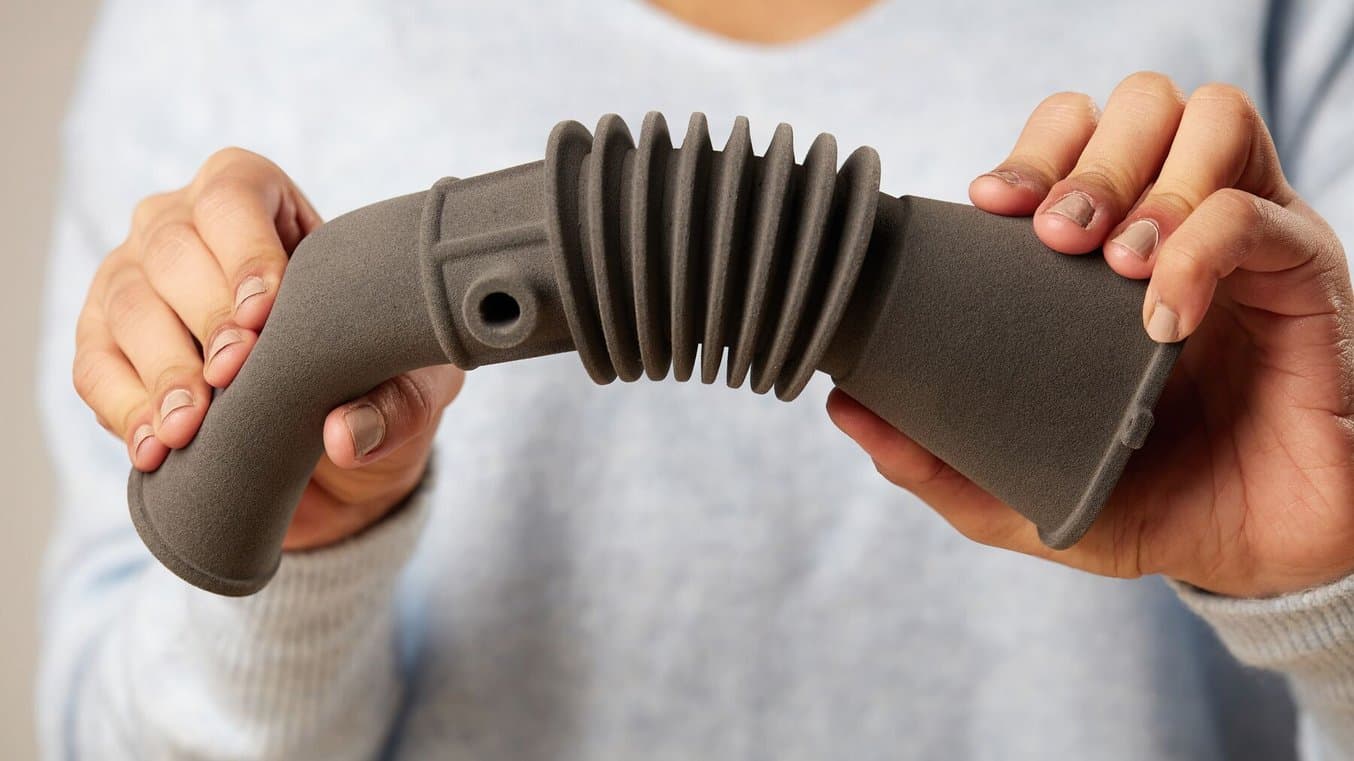
TPUとは
TPU(熱可塑性ポリウレタン)はTPE(熱可塑性エラストマー)の一種で、自動車、輸送、航空宇宙、スポーツ用品、医療機器業界のメーカーがよく使用する材料です。プラスチックの高い耐久性とゴムの弾力性を兼ね備えるTPUは、繰り返しの曲げや圧縮が発生する用途に最適です。
さらに弾力性もあるため、TPUはヘルメットや梱包の緩衝材、防振製品、ガスケットやシールなど、製品の緩衝用に使用されることの多い材料です。TPUは耐摩耗性にも優れ、自動車の内装や電気ケーブル、絶縁体のように高摩擦が発生しやすい環境でも頼りにされています。オイル(油)を使用することが多いこれらの業界では、油汚れにも強いTPUは人気の高い材料です。
TPU製品の生産方法
私たちの身の回りにはTPU製品が溢れています。その人気の高さから、従来工法の射出成形による大量生産が適しています。私たちがゴムだと思っている製品の多くも、実はTPUなのです。
射出成形は大量生産の場合にはコスト効率が高いのですが、複雑な形状やカスタマイゼーションに対応できる柔軟性がありません。数十万〜数百万という単位で生産される射出成形品は、大抵の場合は形状などが標準化されています。そのため、医療器具やスポーツ用品の製造においては少量生産やカスタマイゼーションがしやすい代替工法が求められています。
大量生産では巨大な射出成形機が必要になるため、中小企業や新興企業が市場参入しにくい点も課題として挙げられます。
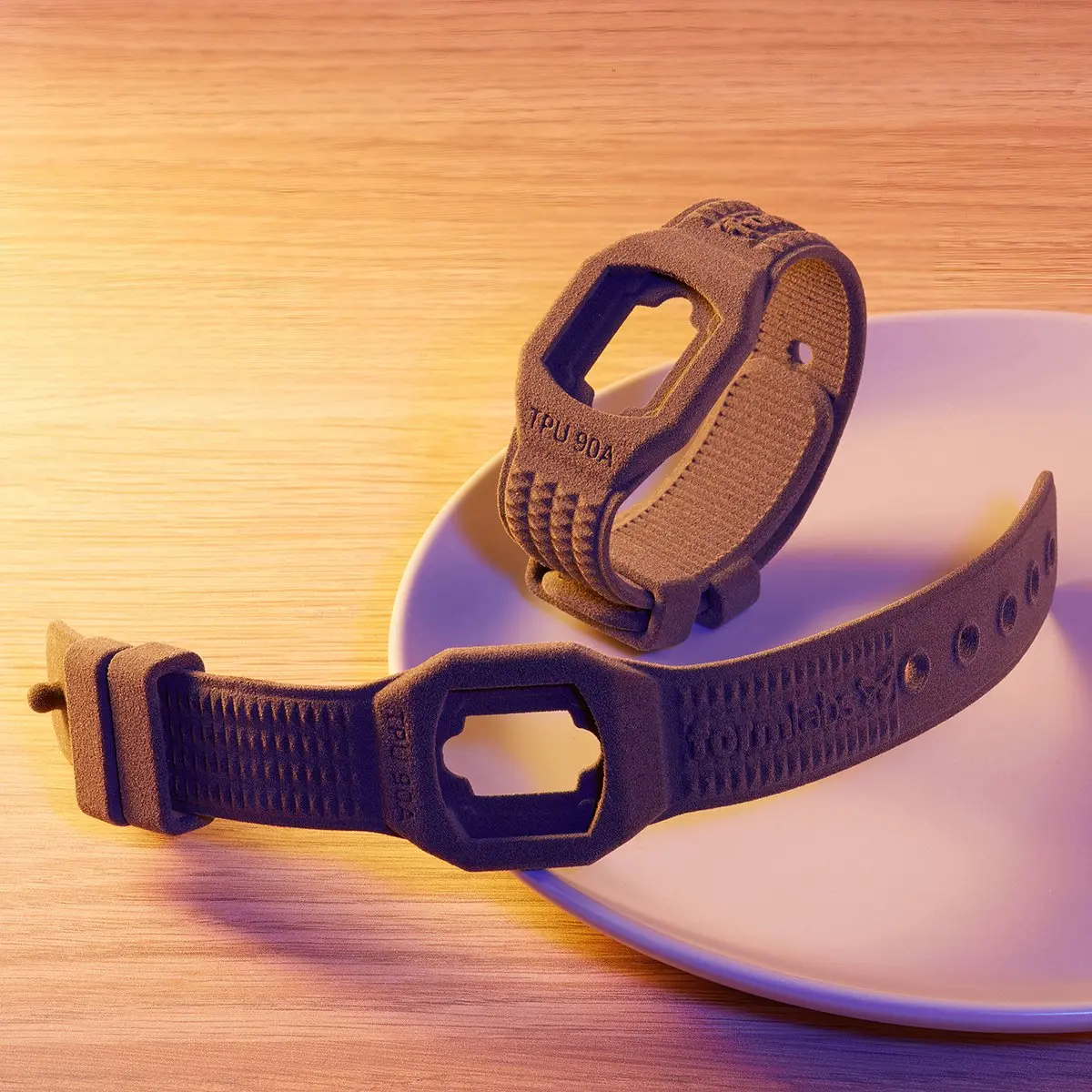
TPU 90Aパウダー:柔軟性、強度、皮膚安全性に優れたSLS 3Dプリント用材料
本ウェビナーでは、Fuseシリーズ3DプリンタとTPU 90Aパウダーの組み合わせで柔らかな手触りのゴム製品を内製する方法をご紹介します。
3DプリントでTPUを使う理由
TPUやTPE材料を使って3Dプリントすることで、これまでより遥かに複雑な形状、パーソナライズまたはカスタマイズされたデザイン、試作・検証の高速反復、コスト効率の良い少量生産が可能になるなど、従来の作業手順にはないビジネスチャンスが生まれます。
TPUを使った3Dプリントには、FDM(熱溶解積層)方式やSLS(粉末焼結積層造形)方式など、様々な選択肢があります。3Dプリント技術と材料の進歩に伴い、既存工程に3Dプリントを導入するメーカーの数は飛躍的に増加しています。
TPUの3Dプリントは、ラピッドプロトタイピングの試作・検証サイクルを短縮できるだけでなく、実製品用部品の製造でカスタマイズの可能性も広がります。製品開発プロセスのうち、これまで1つのフェーズ(通常は大量生産段階)で外注を利用していた場合には、3Dプリントの導入によって全体的な作業フローを改善し、工程の垂直統合が可能になります。
TPU製品の3Dプリントで、メーカーはカスタマイズまたはパーソナライズ製品に対する需要の高まりに応えやすくなります。Deloitteの調査によると、一部のカテゴリーでは消費者の50%以上がカスタマイズされた製品やサービスの購入に関心を示しており、さらにその大半はそういった製品やサービスに普段よりも高い金額を支払う意思があることがわかっています。ヘルメットや人工装具、矯正装具やインソールなど、一般的にTPUやゴムを使用する保護目的の用途では、マスカスタマイゼーションで作るヘルメットのパッド、矯正装具、スポーツ用品、ゴーグル、ヘッドセット、ハイテク製品の人間工学に基づくグリップ部品として、3Dプリント製のTPU部品が最適です。
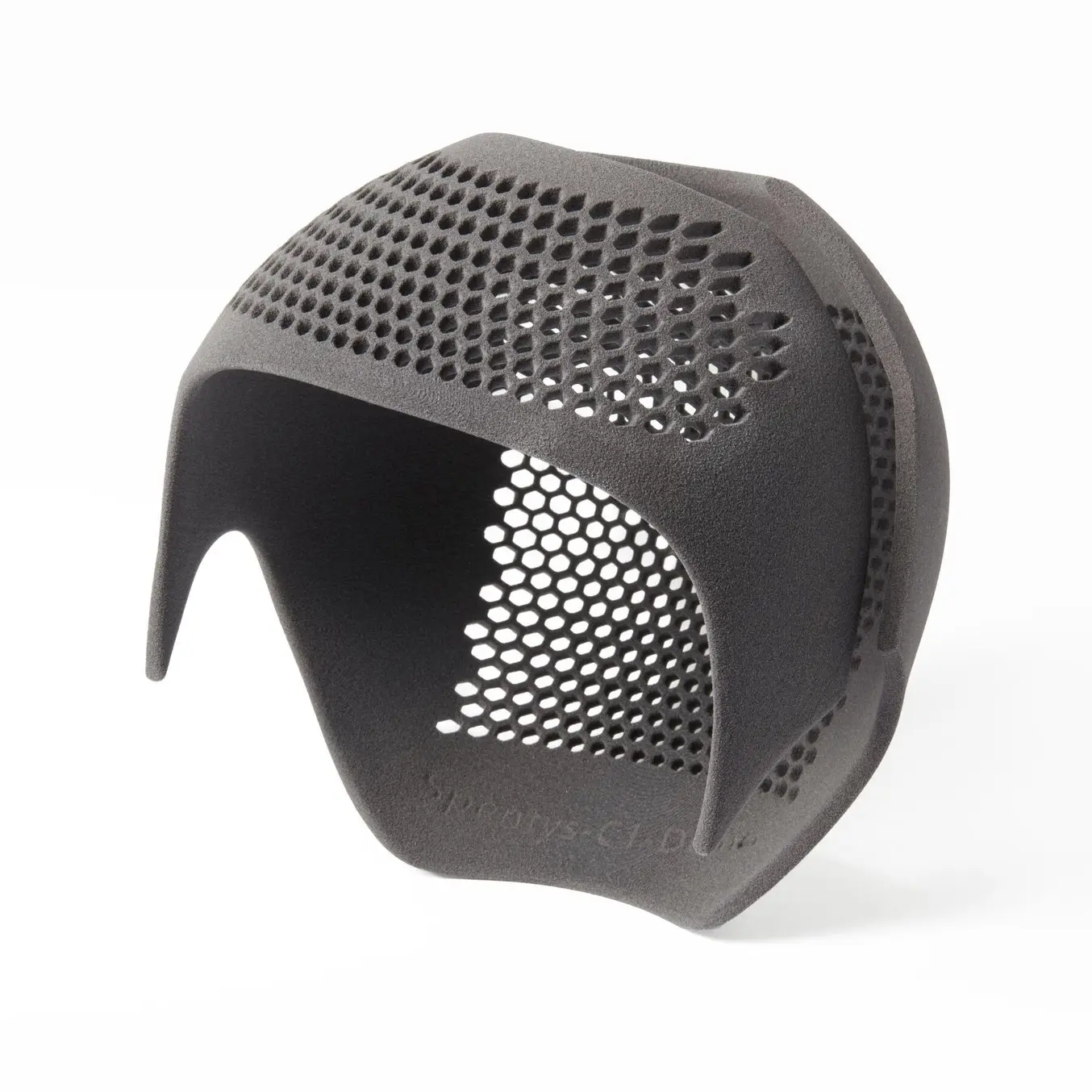
FormlabsのTPU 90Aパウダーは写真のようなカスタムヘッドカバーなど、人体測定データに基づくカスタマイズも可能にする。
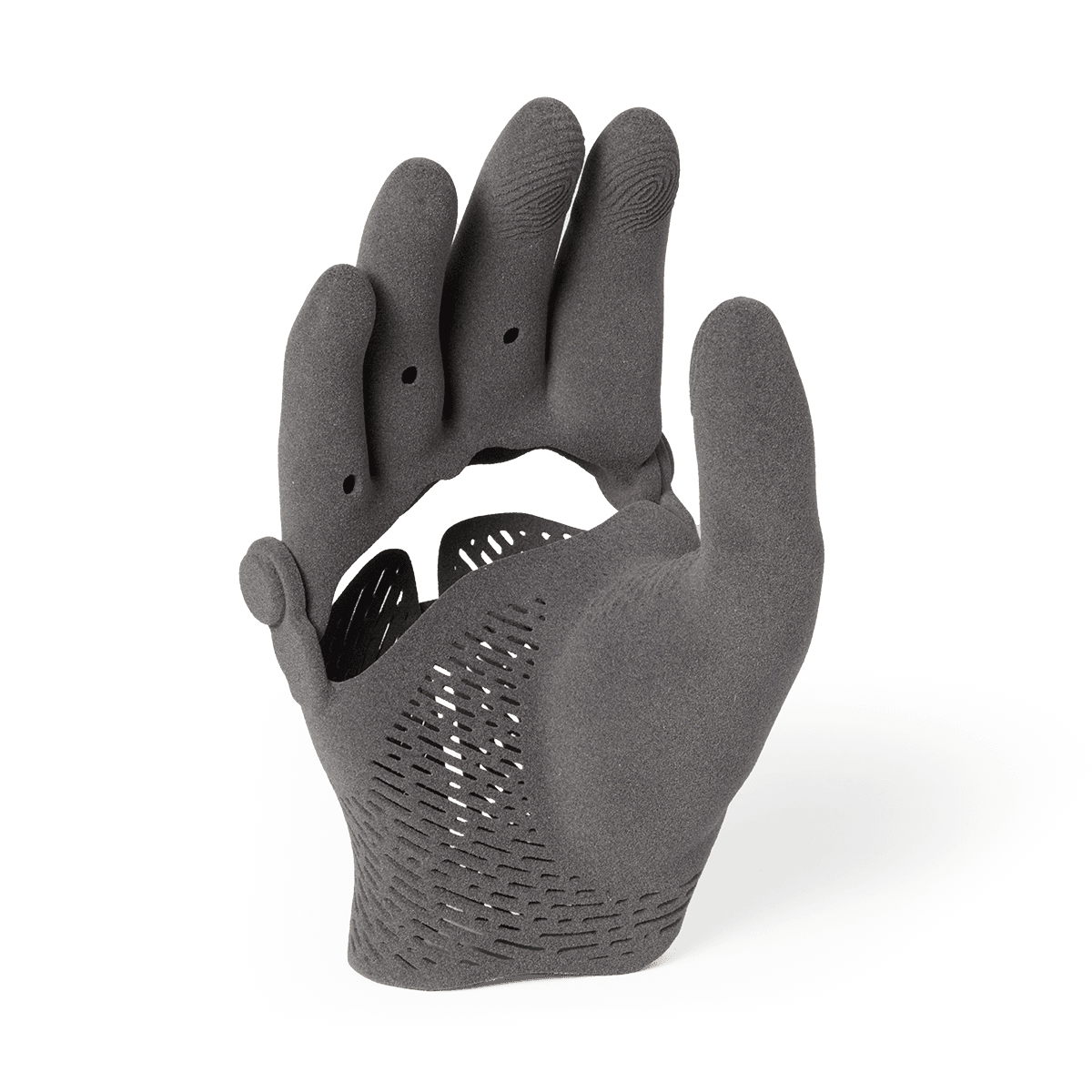
TPU 90Aパウダーで3Dプリントした義手カバー。柔軟性と強度、耐久性に優れる。
TPUを使った3Dプリント
TPUはFDM方式またはSLS方式の3Dプリンタで造形が可能です。方式ごとに異なるメリットが享受できるため、3Dプリンタを選ぶ際は既存の作業手順とビジネスニーズに最適なものを見極めることが重要です。
FDM方式3Dプリント | SLS方式3Dプリント | |
---|---|---|
機能性材料の強度 | ★★☆☆☆ | ★★★★★ |
精細度 | ★★☆☆☆ | ★★★★☆ |
精度 | ★★★★☆ | ★★★★★ |
表面品質 | ★★☆☆☆ | ★★★★☆ |
スループット | ★★☆☆☆ | ★★★★★ |
複雑な形状 | ★★☆☆☆ | ★★★★★ |
使いやすさ | ★★★★★ | ★★★★☆ |
長所 | 低価格の消費者向けプリンタと材料 シンプルな形状の小型部品なら高速かつ簡単に造形可能 | 造形品は機能的で丈夫、等方性あり 量産レベルのスループット サポート材不要 設計の自由度が非常に高い |
短所 | 造形品は異方的で、水密性や機能強度が劣る 設計の自由度が低い | 表面がややザラついた手触り |
代表的な用途 | 低コストでのラピッドプロトタイピング 基本的な概念実証モデル | 機能確認用試作 実製品用部品の少量生産:自動車用ガスケット、シール、マニファオールド、消費者製品、シューズ、補綴物、人工装具 |
FDM方式によるTPUの3Dプリント
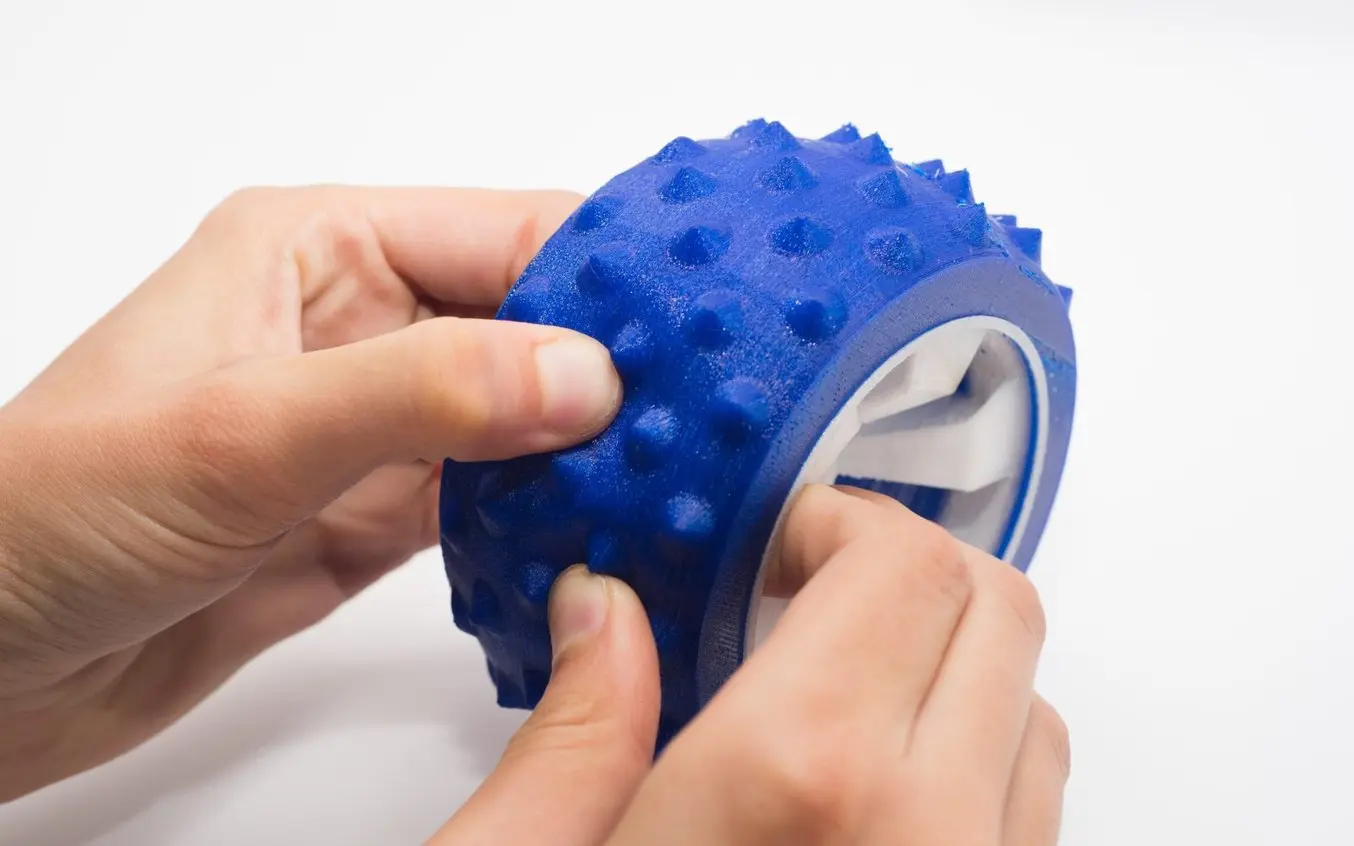
FDM方式はエントリーレベルの選択肢としてはよいが、TPUは3Dプリントが難しく設計上の制約もある。(画像出典:Hubs)
TPU部品の3Dプリントを検討中の企業にとって、低価格のFDM 3Dプリンタはエントリーレベルの用途ではよい選択肢と言えるでしょう。FDMのTPUフィラメントは安価ですし、特に最終的な部品は射出成形で大量生産するという場合であれば、デザインコンセプトの確認や外観確認用の試作品製作には向いています。
しかし、TPUは柔らかく伸縮性のあるフィラメントのため、FDMプリンタで3Dプリントするのが難しい場合があります。また、FDMプリンタでTPUを3Dプリントすると、設計の自由度が制限されるほか、造形品の寸法精度の低下、そして積層痕が目立ちやすいなどの難点がいくつかあります。
FDMプリンターで造形したTPU部品は異方的で、応力に対する強度が軸や平面によって異なります。つまり、FDMで3DプリントしたTPU部品にある向きから応力をかけた場合と、別の向きから応力をかけた場合では、部品への影響が変わります。TPU部品は引き伸ばしや圧縮、捻りなどの様々な応力がかかることが多く、プロトタイピングの段階でもしっかりとした機能性が求められる用途ではこの異方性が課題になります。
FDMプリント用のTPUフィラメント
多くのFDMプリンタメーカーや材料メーカーが様々な材料特性を持つTPUフィラメントを提供しています。FDM用のTPUフィラメントは一般的に少し硬めの弾性材料で、ショア硬度は95A前後ですが、これは造形設定や設計を工夫することで調整が可能です。
SLS方式によるTPUの3Dプリント
SLS 3Dプリント方式は、人工装具、ヘルメットのパッド、ウェアラブルなど、実製品用のカスタム部品の少量生産や機能試作の製作など、より高いスループットと機能性が求められる用途に最適です。SLS 3Dプリントのユーザーは、TPUの卓越した強度と柔軟性を活かして製品のいち早い市場投入や患者ケアの変革が可能になります。材料の引裂強さが高いため丈夫で耐久性のあるエラストマー部品が製作でき、FuseシリーズのようなアクセスしやすいベンチトップサイズのSLS 3Dプリンタを使うことで製造単価を抑えられます。Fuseシリーズは、手頃な価格、需要に応じて容易に生産規模の拡張が可能なこと、そしてリフレッシュ率が低いことが魅力です。リフレッシュ率が低いことでパウダーの使用効率を高め、新品材料への支出を抑えます。
SLS方式で3DプリントしたTPU部品は、性能の観点から複雑な形状が必須または歓迎される用途に最適です。SLS方式では造形中に未焼結パウダーが造形品を支えるため専用のサポート材が不要で、内部チャネルやラティス構造、マニホールドタイプのアコーディオン構造など、複雑形状の造形が可能です。保護用ヘッドウェアやシューズの中敷、矯正装具などの用途では、ゴム材料で作るラティス構造により圧縮強度が高まり、製品の有効性が高まります。
SLSプリント用のTPU材料
TPUのパウダー材料が利用できるSLS方式3Dプリンタは複数あります。ただし、こういったプリンタの多くは専用の換気システムや広い設置場所、複数の電気回路や電力要件など、複雑なインフラ整備が必要な大型の産業機です。Formlabs FuseシリーズのようにアクセスしやすいSLS 3Dプリンタの登場により、パウダーベッド方式によるTPUの3Dプリントがより身近で手頃なものになりました。
FormlabsのTPU 90Aパウダーは皮膚に触れても安全な材料で、安全規制によって3Dプリント部品の使用が制限されることの多いウェアラブルデバイスや医療器具としての用途にも新たな可能性を開きます。TPU 90Aパウダーを使用することで、エンジニアやデザイナーが3Dプリントの魅力である設計の自由度を存分に活かしながら、ゴムの高い引裂強さと伸び率、これまで成形で使われてきた熱可塑性プラスチックの皮膚への安全性といった様々な長所をすべて1つの工程に組み込むことができます。
FormlabsのTPU 90AパウダーとFuseシリーズSLSプリンタを使えば簡単にTPU材料を3Dプリントできます。すでにSLSを活用中の場合は既存工程への組み込みも容易に行えますし、まだの場合は初めて利用するSLS材料としてもよいでしょう。この材料は通常の空気環境で造形が可能で、一部のSLS材料で求められるような不活性雰囲気は必要ありません。
さらに、TPUを使う場合はFuseシリーズでSurface Armor(より硬度の高いパウダーによる造形品の周囲に形成される半焼結のシェル)を使用しないため、後処理装置であるFuse Siftを使ったパウダー除去作業も簡単に行えます。TPU 90AパウダーではSurface Armorが形成されないものの、造形品から余分なパウダーを完全に除去し、アセンブリの一部としてスムーズに機能する滑らかな部品にするためにはブラスト処理をお勧めしています。すでにFuseシリーズのプリンタをお持ちの場合は、もちろん既存機器にてTPU 90Aパウダーによる造形が可能です。ただし、Formlabsでは専用のFuse Siftやビルドチャンバーをご用意いただくことを推奨しています。
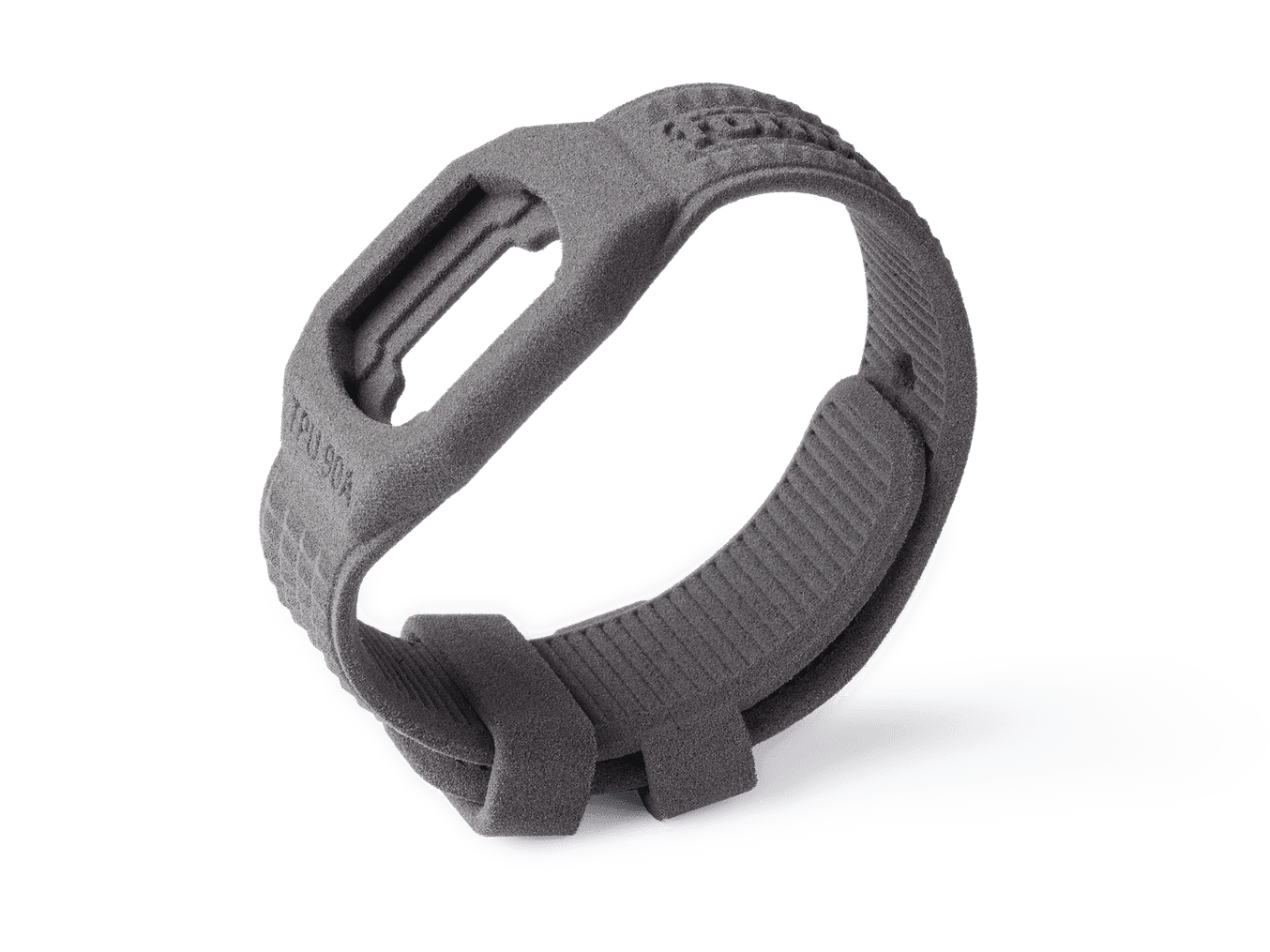
FormlabsのSLS 3Dプリント用弾性材料、TPU 90Aパウダー
SLSパウダーとしてFormlabs初となる弾性材料、TPU 90Aパウダーの品質を直接手に取ってお確かめください。本パウダーで造形した腕時計用ストラップを無償でお届けいたします。
3Dプリント製TPU部品の活用例
TPU部品の従来の製造工法は実績があり、今でもゴム製品の大量生産には理想的な方法です。一方でTPU部品の3Dプリントは、スピードや使いやすさが必須となる場合、ラピッドプロトタイピング、生産工程で使用する治具のオンデマンド生産、カスタマイゼーションなど、様々な状況でその代替案となり得ます。迅速な試作品製作が必要な設計プロセスの初期段階から、実製品用部品やマスカスタマイゼーションで作る消費者製品の最終設計に至るまで、TPU部品の製造に3Dプリントを活用することで、部品の機能特性や精度を犠牲にすることなく高速・高効率な生産を実現できます。
ラピッドプロトタイピング
3DプリントでTPU部品を作れるということは、社内でのプロトタイピングが可能になります。そのため、受託メーカーや工房に外注する場合に比べてコストや製作期間を削減できます。
例えばスポーツ用ヘルメットのプロトタイピングの場合、硬質の外郭と軟質の内部クッションの両方を生産できる能力が必要です。革新的な企業はそういったクッション用にラティス構造の新設計や衝撃吸収テクノロジーの開発に取り組んでおり、TPUはその材料として最適です。
しかし、金型を使用する従来の工法で新しいデザインや形状の試作品を作って検証しようとするとコストが非常に高く、受託メーカーへの外注の場合は製作に数週間かかってしまいます。硬質の外郭と軟質の内部クッションの両方をたった1つの工程・方法で製造できるとすれば、イノベーターたちは試作・検証プロセスを遥かに高速で反復できることになります。こういったヘルメットには広範な物理的検証が不可欠なため、1回のテストでクッションパッドが10個ほど必要になります。クッションの表面を手作業で形づくりには多すぎる数でありながら、金型を使って成形する従来のTPU製造工法では数が少なすぎてコスト効率が悪くなります。そのような場合に解決策となるのが、3Dプリントによる内製です。
Fuseシリーズ3Dプリンタがあれば、TPU 90Aパウダーを使ってゴム製のラティス構造を複数造形し、わずかに設計の異なる様々なバージョンをテストできます。壁の厚みなど部品そのもののデザインを変更することで用途に合わせて硬度の異なる部品を製造したり、検証後の設計変更が可能です。
Fuseシリーズでは幅広い機械的特性を備えた様々な材料を利用できるため、開発と製造をすべて社内で行いながら、1種類の技術だけで多岐にわたる部品の設計を管理できます。多くの方々から信頼されているFuseシリーズにてTPU 90Aパウダーを使えるようになることで、直接3Dプリント可能な全く新しいタイプの製品を生み出せるかもしれません。
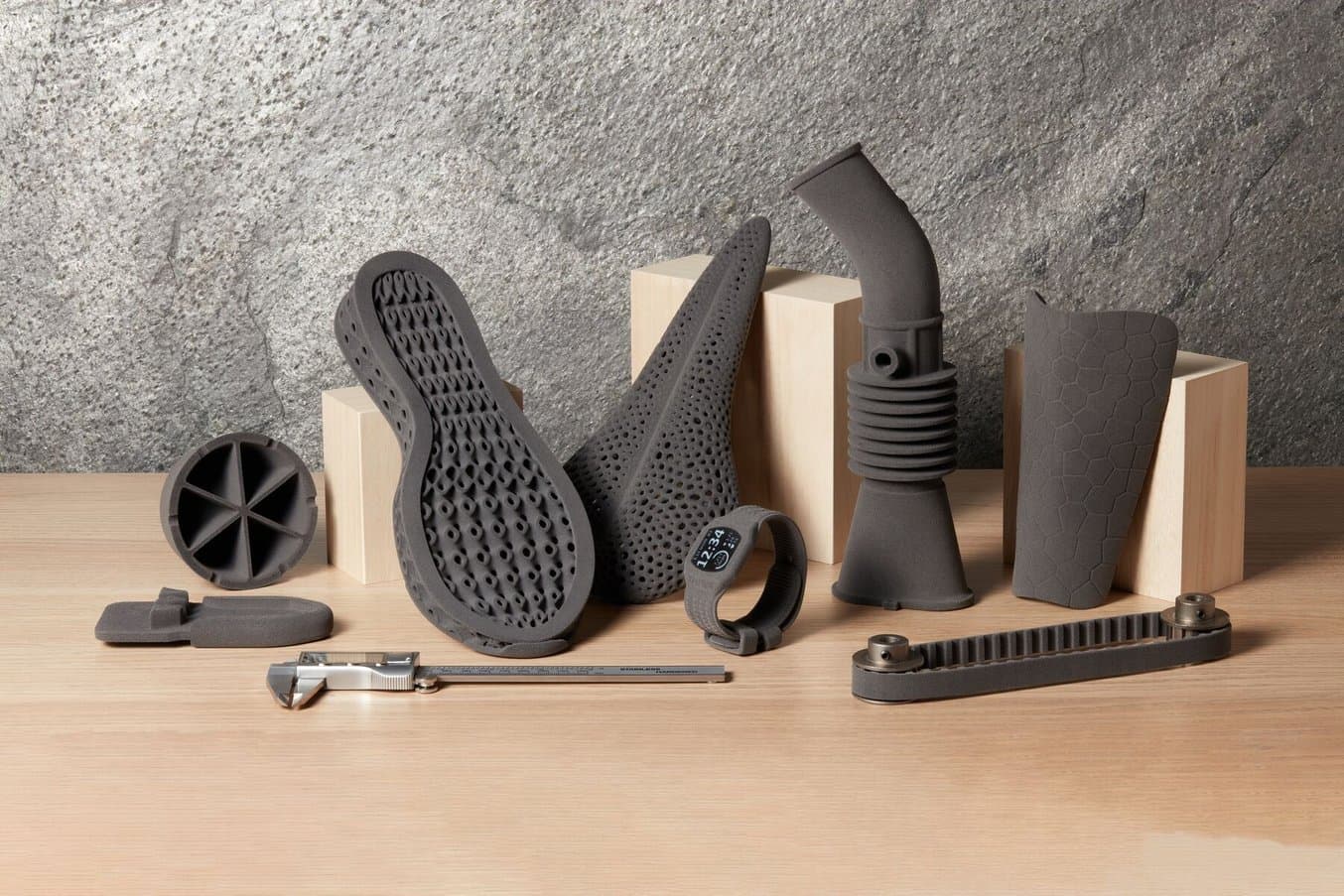
TPU 90Aパウダーは、皮膚に触れても安全なウェアラブル製品や高性能スポーツ用品、シューズのインソールなど、弾力性が求められる機能確認用試作の製造に最適な材料。
治工具
製造業に関わりがない人にとっては、治具の違いは分かりづらいかもしれません。治具でもブラケットでもエンクロージャでも、そして機器が一体になって動くその他全てのものに対して言えることですが、これらは「あれば便利」という程度のものでは決してなく、本当に必要だから製造が求められるのです。TPU 90Aパウダーは、多くのメーカーが直面する問題、つまり何百万ドルもかけて作った製造技術を数々の摩滅や破損から守ること、に対処できる材料です。
手触りの柔らかい治具は衝撃に対するクッションや完璧にフィットするグリッパとして機能し、重機の長寿命化を叶えます。長年に及ぶ繰り返しの使用によってシールやガスケットが破損してしまった場合でも、オペレーターが交換部品を3Dプリントできれば、数時間以内に製造ラインの稼働を再開できます。
新たな材料特性を付与することで、メーカーにとっては予想外の破損や機器の不具合を避けられ、生産の継続性をより確かなものにすることができます。社内でより多くの機械的特性を活用できれば、サプライチェーンの遅延やOEMによる高額な修理を避けることができます。ゴム製部品を3Dプリントすることで、導入機器のうちこれまでは不可能だった部品をオンデマンドで修理・交換できるようになり、生産ラインやプロセスの停止を防ぐことで一日に何千ドルものコストを節約できます。
TPUは、自動車や航空宇宙のテストで使用する振動ダンパーや、独自形状部品の熱成形などの工業プロセスで使用する治具の製作にお使いいただけます。自動車工場では、曲げや回転が発生するガントリーの上で大規模なロボット機器が稼働しています。カスタムのクッションや軟質のエンクロージャを使用することで、これらの機器を摩擦から守り長寿命化を図ることができます。
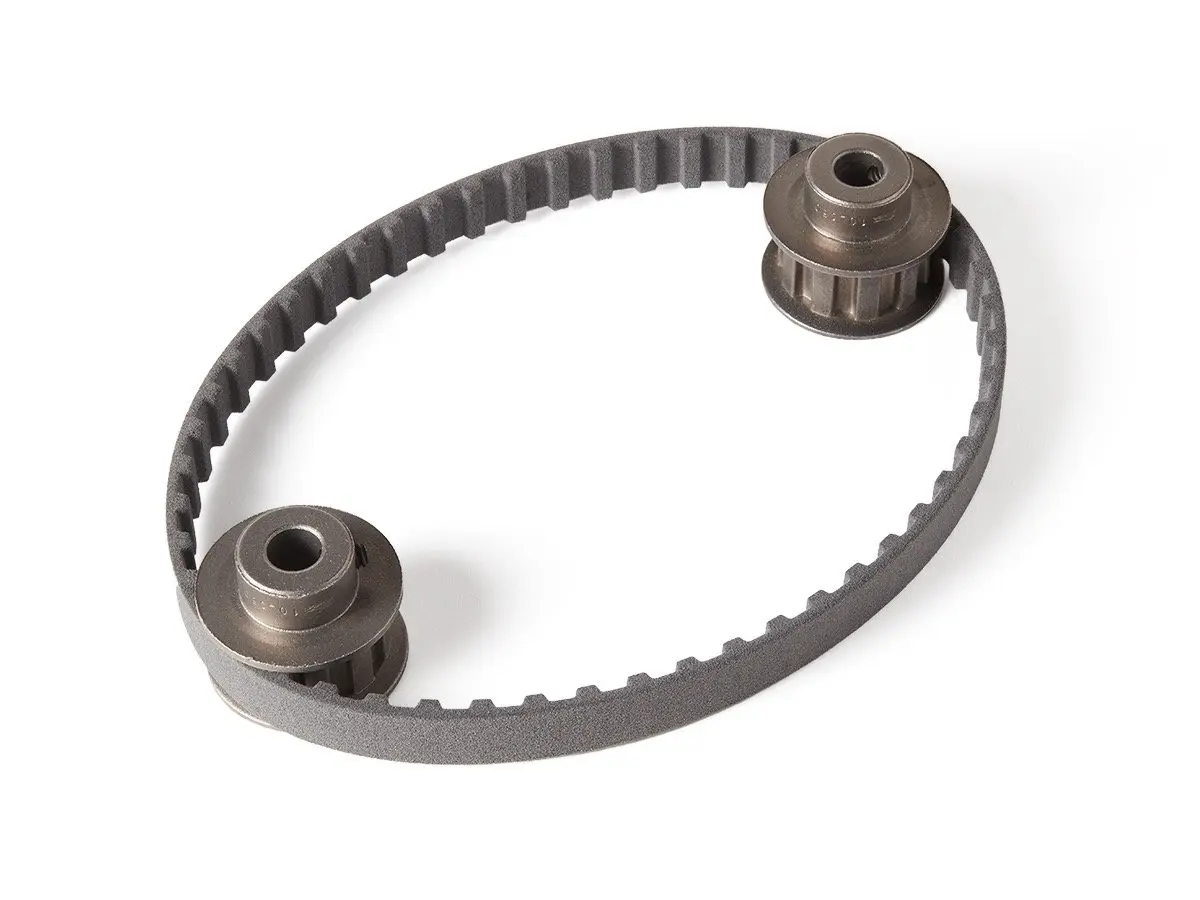
TPU材料が使用できることで、弾力のある交換部品や治具をその日のうちに設計・プリントできるため、生産ラインの停止を回避できる。
着用可能な製品の少量・カスタム生産
スポーツ、ファッション、ウェアラブル業界で市場シェアを狙うブランドにとって、パーソナライズ製品の提供は不可欠な要素です。これまで、金型製作にかかるコストを考えると少量生産や1回限りの生産というのはほぼ不可能に近いものでしたが、手頃な価格の3Dプリンタの登場で新たな可能性が生まれました。
とはいえ、3Dプリント用材料はスポーツ用品やウェアラブル業界で使用するには硬すぎるという課題がありました。それもTPUが使用できるようになったことで状況が一変し、個人の足形や重量配分に応じてカスタマイズ可能なソールや衝撃吸収に特化して開発されたフットボール用ヘルメット、ひとりひとりの手首に合わせて成形した腕時計用バンドまで、可能性は無限に広がります。
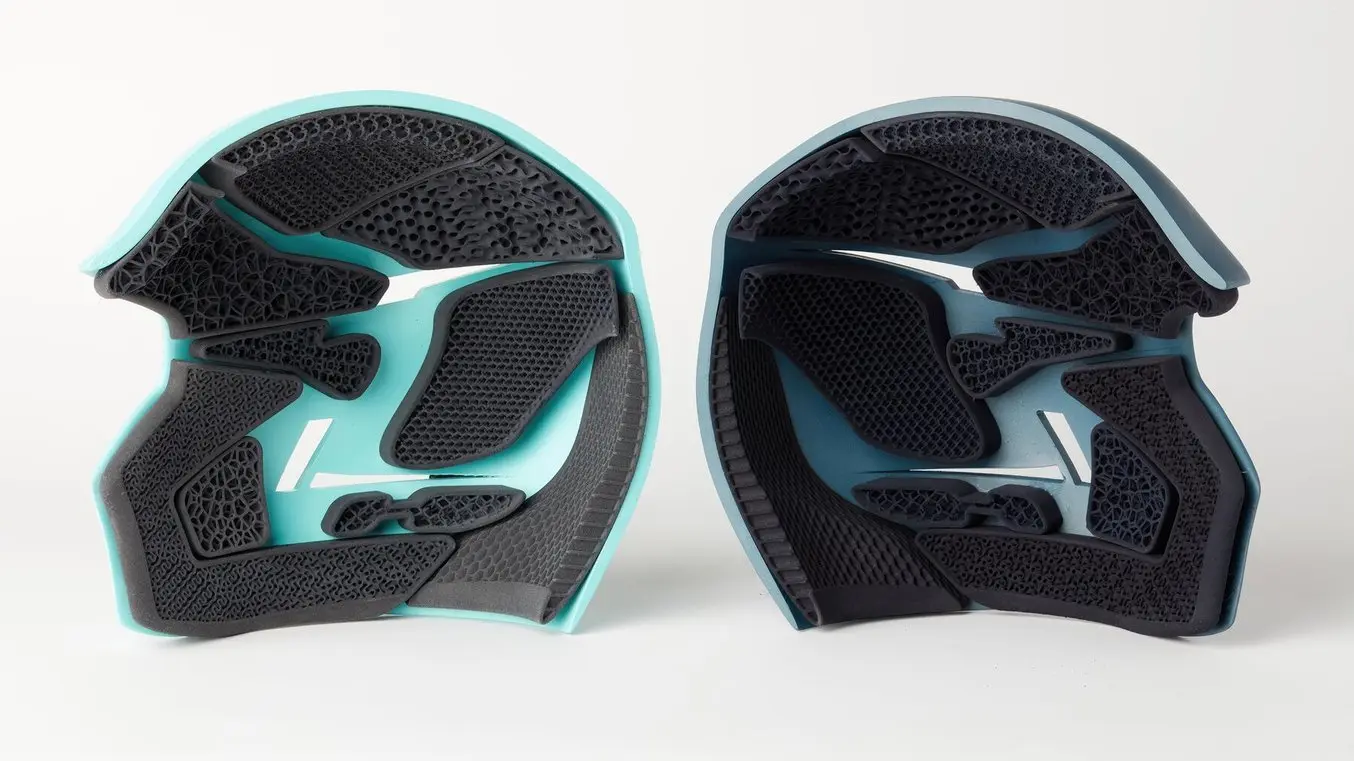
アメフト用ヘルメット。FuseシリーズSLS 3DプリンタにてTPUを使って造形したカスタムインナーパッドを装着。
医療器具
優れた耐久性と強度を備える3Dプリント製のTPU部品は、人工装具や矯正装具、患者ひとりひとりに合わせたアプライアンスや医療器具としての使用に最適です。弾力があり高強度の実製品用部品を3Dプリントする能力を社内に導入することで、医療従事者の方々がゴム材料の引裂強さと破断伸び率、そしてSLS 3Dプリントの特徴である設計の自由度と耐久性を兼ね備えた部品を製作できるようになります。
弾力性のあるエストラマー材料であるTPUは、以下のような医療器具の3Dプリントに最適です。
-
医療機器の試作品、実製品用医療器具及びその部品
-
矯正パッドや義足ライナー
-
ウェアラブル、シール、バンパー、チューブ
-
スプリント、頭蓋形状矯正ヘルメット
-
競技用及び矯正用インソール
ヘルスケア分野における3Dプリントの活用は急速に広まりつつありますが、安全性に関する認証だけでなく、強度や材料特性に対する規制など、材料に求められる厳しい要件により制約があるのも事実です。ここでも、TPUを3Dプリントできることでヘルスケア分野における様々な用途で利用可能なオプションが1つ増えることになります。
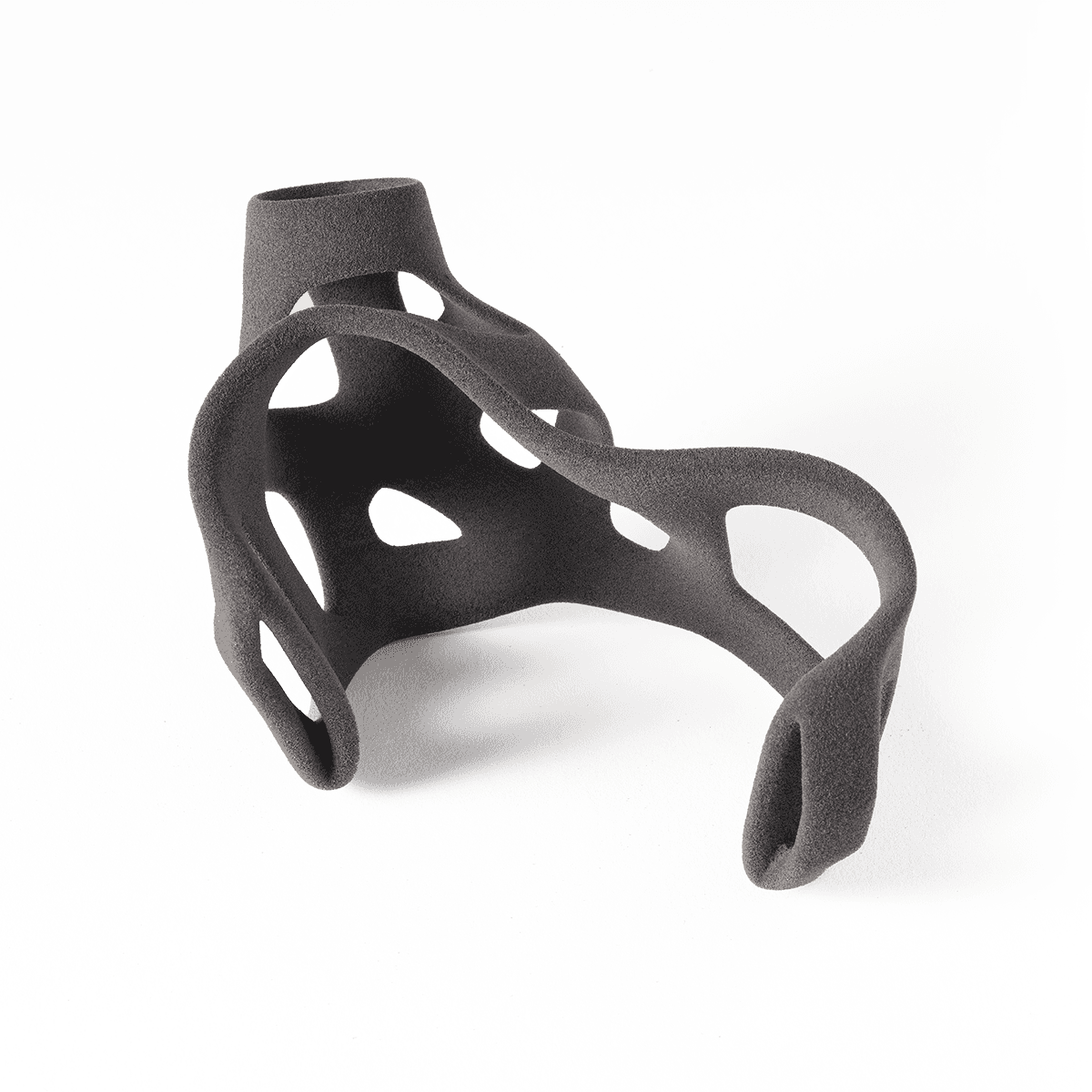
写真のカスタムサムブレースは抜群の柔軟性で従来のブレースよりさらに制御がしやすく、しっかりとしたサポートを提供しながらケガを防ぐ。
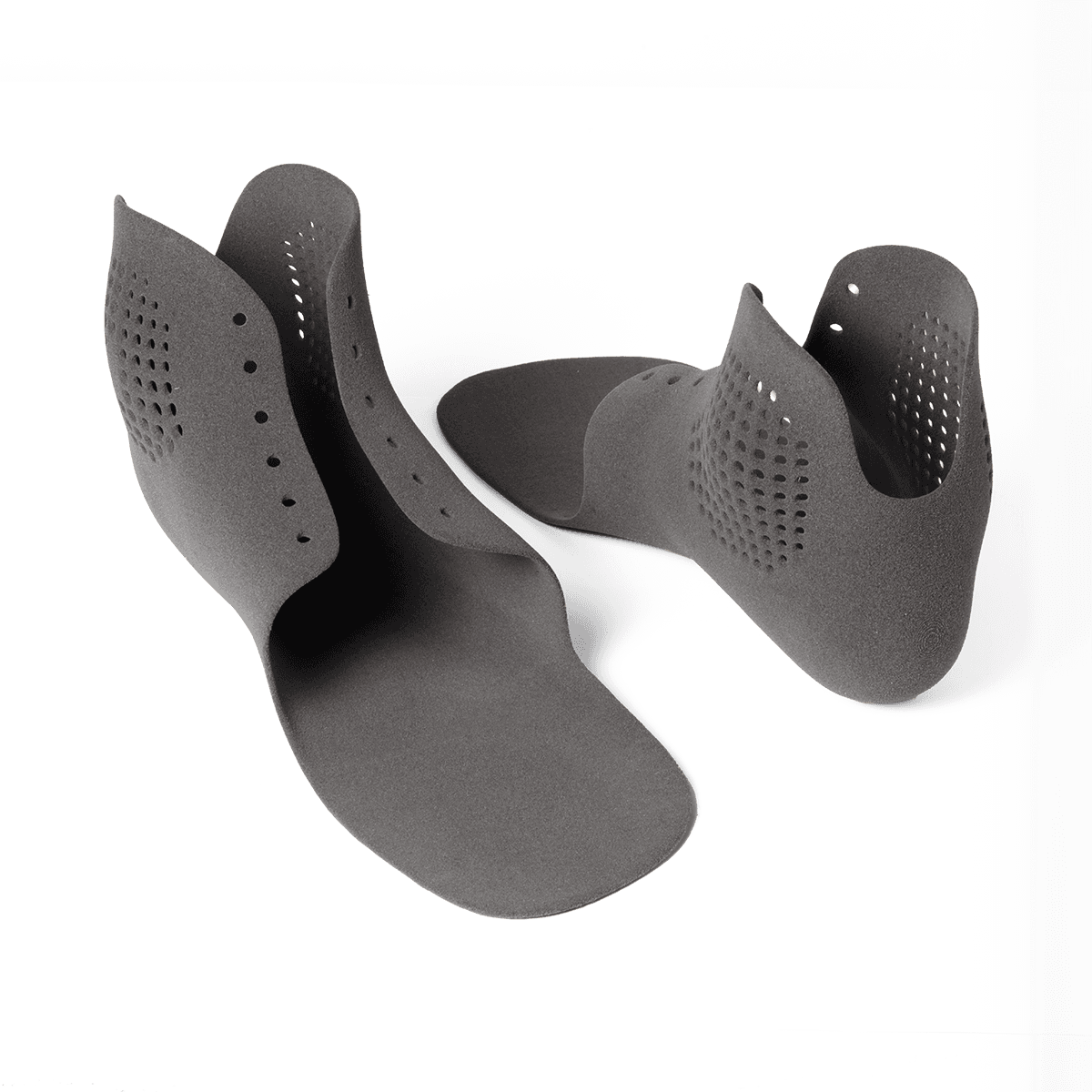
TPUはライナーや競技用・矯正用インソールなど、様々な人工装具に最適。
ケーススタディ
印刷業界の世界的リーダー、Heidelbergが機械の保護部品を3Dプリントで製作
世界大手のオフセット印刷機メーカーであるHeidelberger Druckmaschinen AGは、世界170カ国以上で10,000人近い従業員を擁する企業です。同社は、これまでにない速さで印刷可能な最大級の最新鋭印刷機から、裁断機や紙折り機に至るまで、印刷バリューチェーン全体で幅広いツールや自動化ソリューションを提供しています。
同社では、ピック&プレース用ロボットの軽量部品、紙折り機用の新たなコンポーネント、以前はスチールで製造していた交換部品など、幅広い用途で3Dプリント製部品を使用しています。TPU 90Aパウダーでは、柔軟で耐衝撃性がありながら、既存の硬質な機械部品と組み合わせての使用に適した順応性のある部品を製作できます。
交換部品や治具は既存のロボットシステムに組み込む必要があるため、製作対象となる部品の形状が特殊だったり、複雑だったりすることがよくあります。このような部品は稼働中にかかる負荷や応力に耐えられるよう特別に設計されており、繰り返しの摩耗や引張にも晒されることが見込まれます。また、金属製のベアリングやテフロンでコーティングされたコンポーネントなど、対摩擦特性を持つ部品と3Dプリント製の部品を組み合わせて使用することも一般的です。仮にここまで複雑ではない部品でも、高精度や繊細さが求められます。
TPUを使って製作した柔軟部品は、不純物の混入防止、鋭利なエッジやセンサーの保護、摩耗を防ぐために使用されています。TPU 90Aパウダーを使ったSLS 3Dプリントはこの種の部品の製作に最適で、負荷の高い使用環境で発生する様々なダメージから高価な機器を保護することができます。
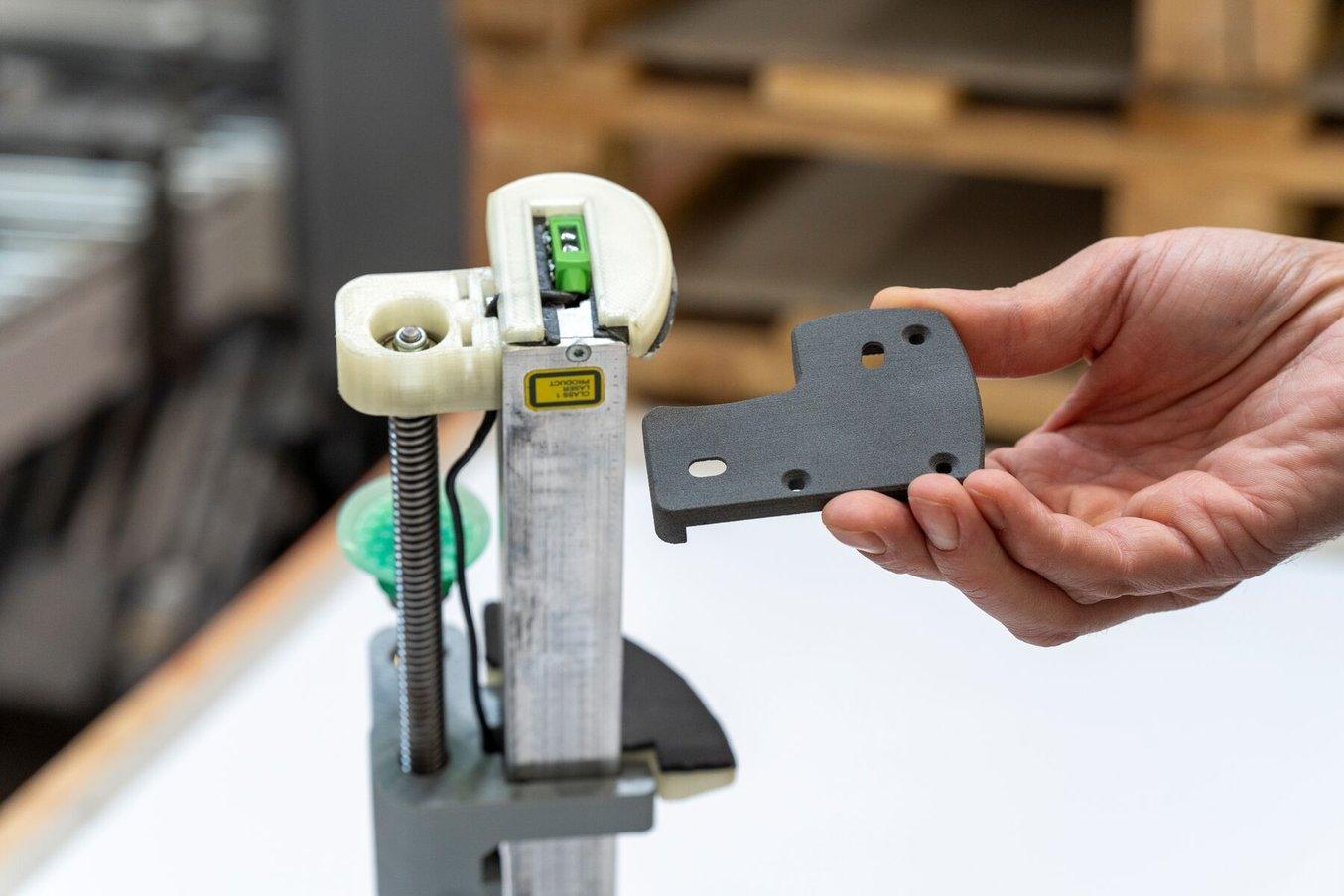
TPU 90Aパウダーで3Dプリントした柔軟性のある部品でセンサーやその他アーム先端の工具を保護する。
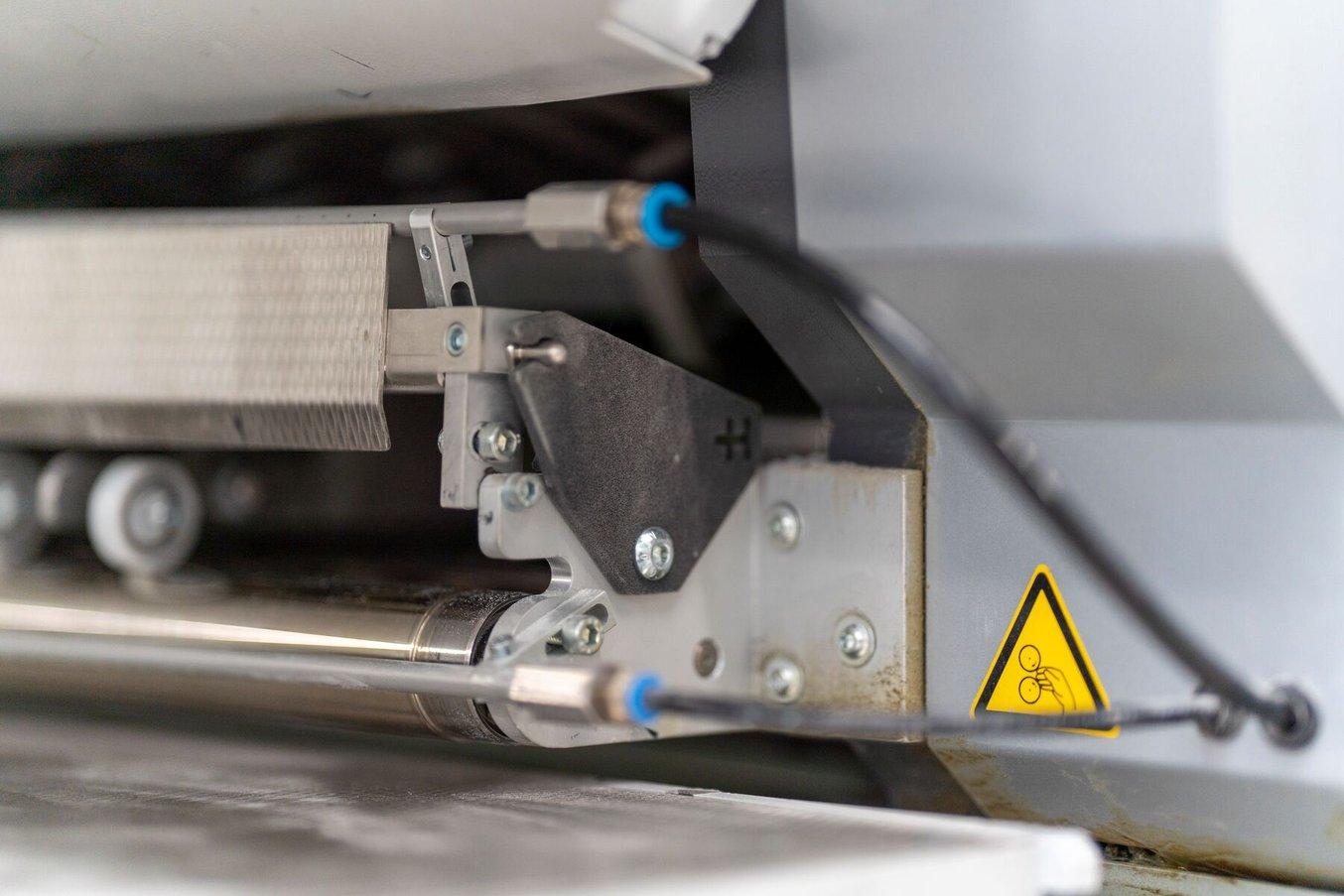
柔軟な部品は、スナップフィット設計のコンポーネントにも最適。鋭利なエッジを保護することで、オペレーターの安全も確保できる。
TPU 90Aパウダーを使って造形したケーブルガイドで機器の電源ケーブルを高い摩擦から守り、ケーブルの長寿命化とダウンタイムの最小化を図っています。これらケーブルの1本でも断線したりほつれたりすると、交換用ケーブルを発注して実際に交換するまで機器全体の稼働が止まってしまうため、ケーブルガイドなどの保護部品は工場の連続稼働には欠かせない存在となっています。
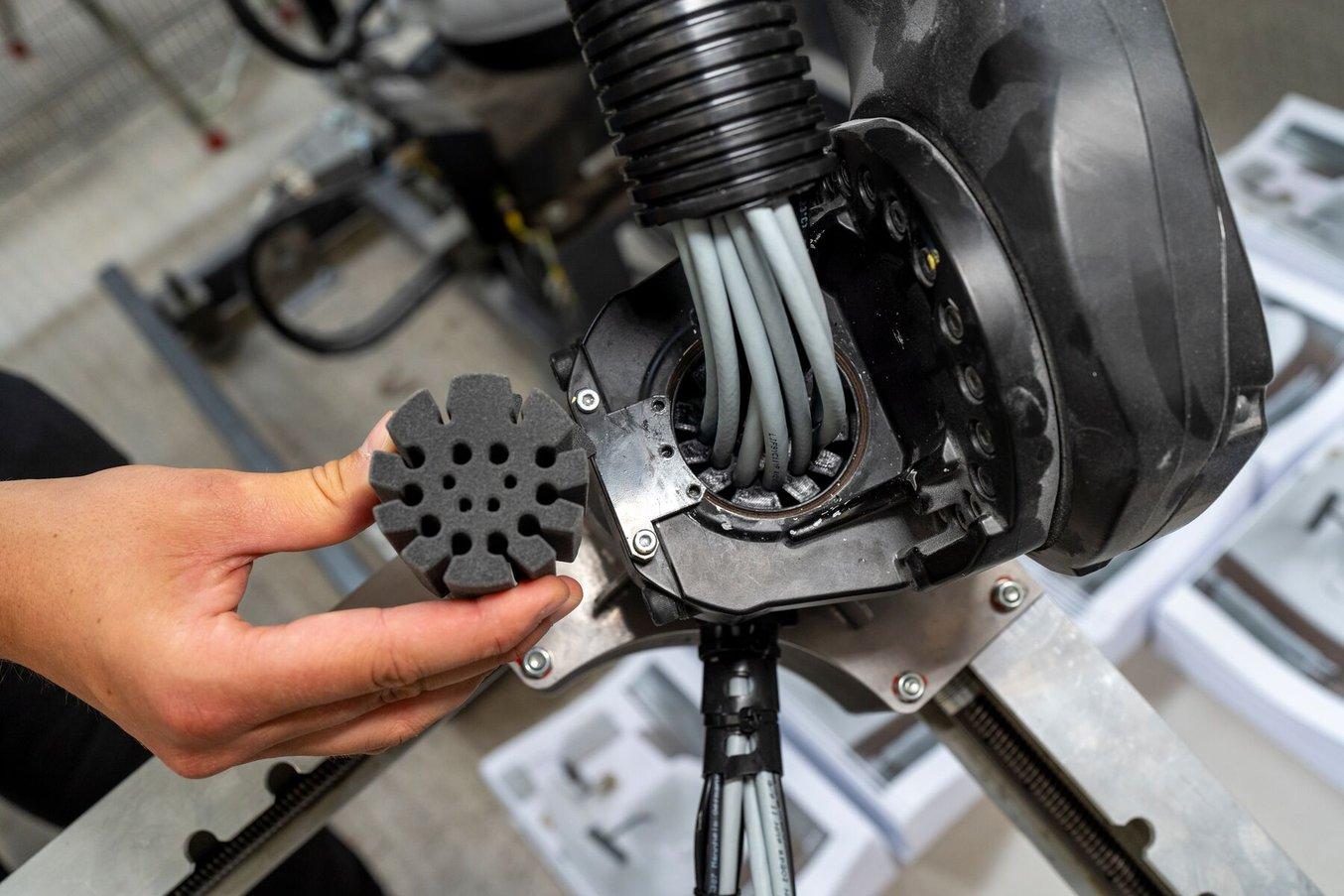
FuseシリーズSLS 3Dプリンタで製作したケーブルガイド。複雑な形状でも造形が可能で、ケーブルを摩耗から保護し、より耐久性のあるソリューションを提供する。
FuseシリーズとTPU 90Aパウダーの手頃な価格帯とアクセスしのやすさにより、企業は自社のサプライチェーンやメンテナンスのニーズを管理しやすくなります。TPU 90Aパウダーで製作した部品は、機器の保護や部品の長寿命化に最適で、ひいては運用コストの削減やダウンタイムの回避にもつながります。
TPU製の治具によりDeutsche Bahnが電車の連続運行を実現している理由
ドイツはノイミュンスターにあるDeutsche Bahnの車両メンテナンス拠点では、国内の公共電車の点検やメンテナンスを行なっています。そんな中、同社が3Dプリントによってオペレーションの高効率化を実現している様子をご紹介します。工程の中に3Dプリントを取り入れたことで、Deutsche Bahnは数百万ユーロものコスト削減だけでなく、車両を実際の運行に戻すまでの期間短縮にも成功しました。
マニュファクチャリングエンジニア兼アディティブマニュファクチャリング・エキスパートのCarsten Wolfgramm氏は、Fuse 1+ 30W SLS 3Dプリンタを2台統括しており、1台はNylon 12パウダー専用、もう1台はTPU 90Aパウダー専用で稼働させています。「Formlabsのプリンタを導入したのは、コストパフォーマンスが非常に優れていたからです。特にSLSプリンタは安定していますし、電源を入れればすぐに使えます。そのおかげで、部品に何度も改良を重ねる際の作業が格段に楽になりました。24時間365日連続稼働してくれます」と、Wolfgramm氏は言います。
一般的なメンテナンス手順の中で、技術者は車両の手荷物棚を取り外し、車両の内壁を再塗装します。手荷物棚を移動させることで壁に傷がついてしまうことがありますが、こうなるとメンテナンスチームが終えたばかりの仕事を最初からやり直さなくてはなりません。そこで、DBチームは内壁を保護するためのカスタムカバーを設計し、TPU 90Aパウダーを使って3Dプリントで造形することにしました。このカバーを手荷物棚にスライドして取り付け、角に丸みをつけます。こうすることで、手荷物棚の取り外しや再装着の際も、塗装したばかりの内装を傷つけずに済みます。
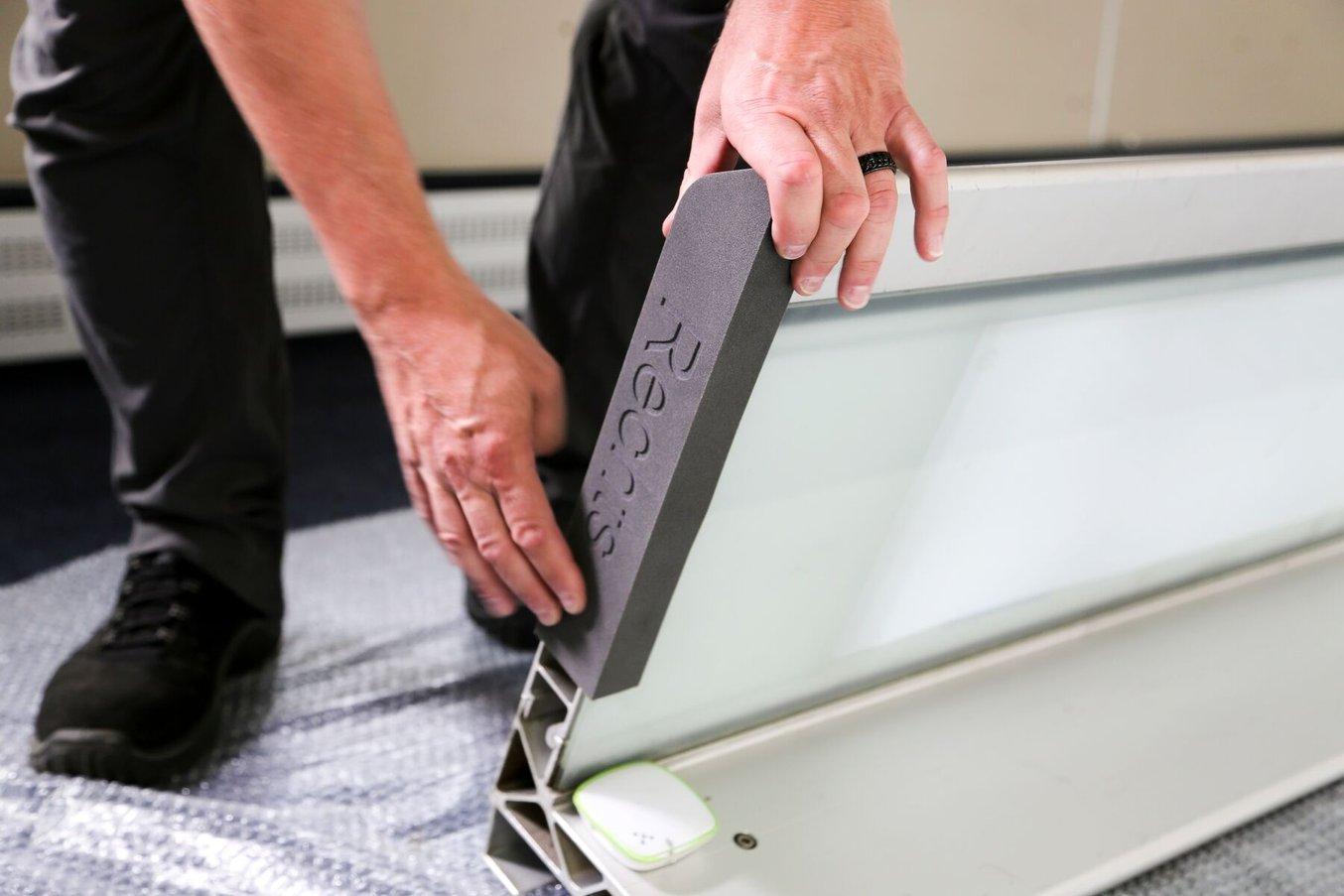
軟質材料のTPU 90Aパウダーを使って傷や衝撃から守る保護カバーを製作。
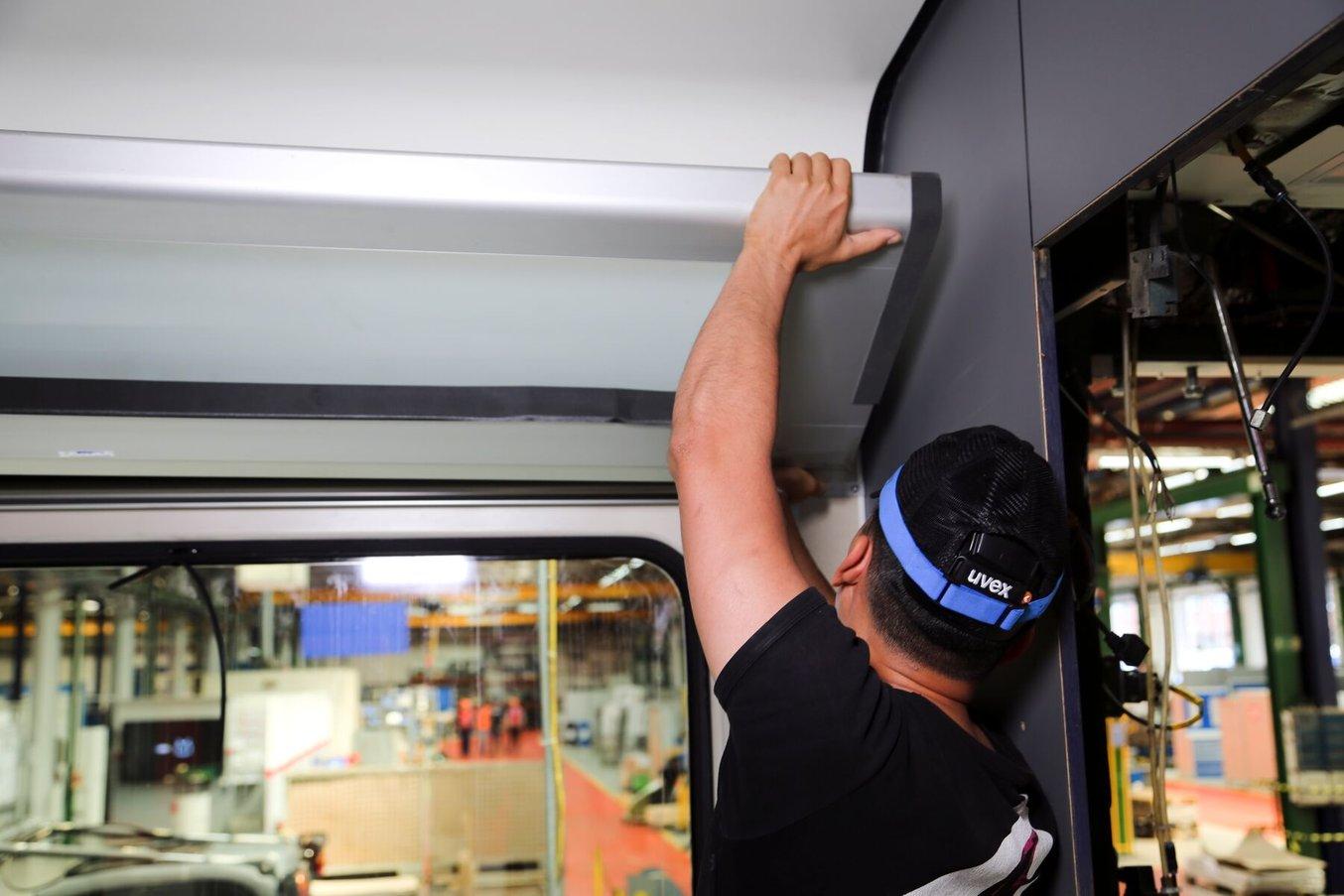
SLS 3Dプリントにより、手荷物棚と壁の隙間にフィットするスリムなデザインを実現。
「傷防止カバーを3Dプリントで製作するまでは、緩衝材や同様素材の治具を使って従来の方法でマスキングをし、傷をつけないようにしていました。でも、この方法が常にうまくいくとは限らないのです。新しく開発したTPU部品のおかげで、今回初めて傷をゼロにすることができました」
Deutsche Bahn 製造エンジニア兼アディティブマニュファクチャリング・エキスパート、Carsten Wolfgramm氏
3Dプリント製のMRO部品でコスト削減と作業量の最小化を実現したDeutsche Bahnは、大規模な輸送会社における3Dプリント導入の成功事例を示してくれました。3Dプリントの導入により、今回紹介した保護カバーなどの柔軟なカスタム部品の内製が可能になることで、Deutsche Bahnは全体のプロセスのさらなる効率化を実現し、これまでよりも早く車両を現場に戻すことができています。
米国の玩具・電動自転車メーカー Radio Flyer、TPUを使用したプロトタイプを製作
100年以上にわたり子供たちとその家族から信頼され愛され続けてきたRadio Flyerは、National Toy Hall of Fameで殿堂入りを果たしたOriginal Little Red Wagon®という有名なおもちゃの製造を手がけるメーカーです。同社は常にポップカルチャーの最前線として、そして子供たちのクリスマスプレゼントの第一候補となる製品を手がける世界トップメーカーとして、ワゴンやスクーター、三輪車、ゴーカート、電動自転車など実際に乗って遊べるおもちゃやその他多くの画期的な製品を世に送り出してきました。
そんなRadio Flyerの開発工程では3Dプリントが重要な役割を果たしています。デザインエンジニアのAgostino Lobello氏が、完璧な機能性を備えた試作品の製作にTPU 90Aパウダーが役立っていると教えてくれました。「グリップの強い表面は、これまで3Dプリントで作ってきたTPEやTPU部品とは異なります。その点では当社が射出成形しているTPE/TPU部品により近く、試作品用途でそれが実現できるのはありがたいことです。現時点でこの工程に変わるオプションとして次に優れているのは、試作品の金型に実際のTPEやその他ウレタン材を流し込んで作る方法で、コストと時間の両方の観点で効率が良いですね」とLobello氏は言います。
「将来、タイヤのトレッドやハンドグリップ、バンパー、シートクッションにもこの材料を使用したり、指定のばね定数でTPE製のバネを試作できるようになるのではと、今から楽しみにしています」
デザインエンジニア、Agostino Lobello氏
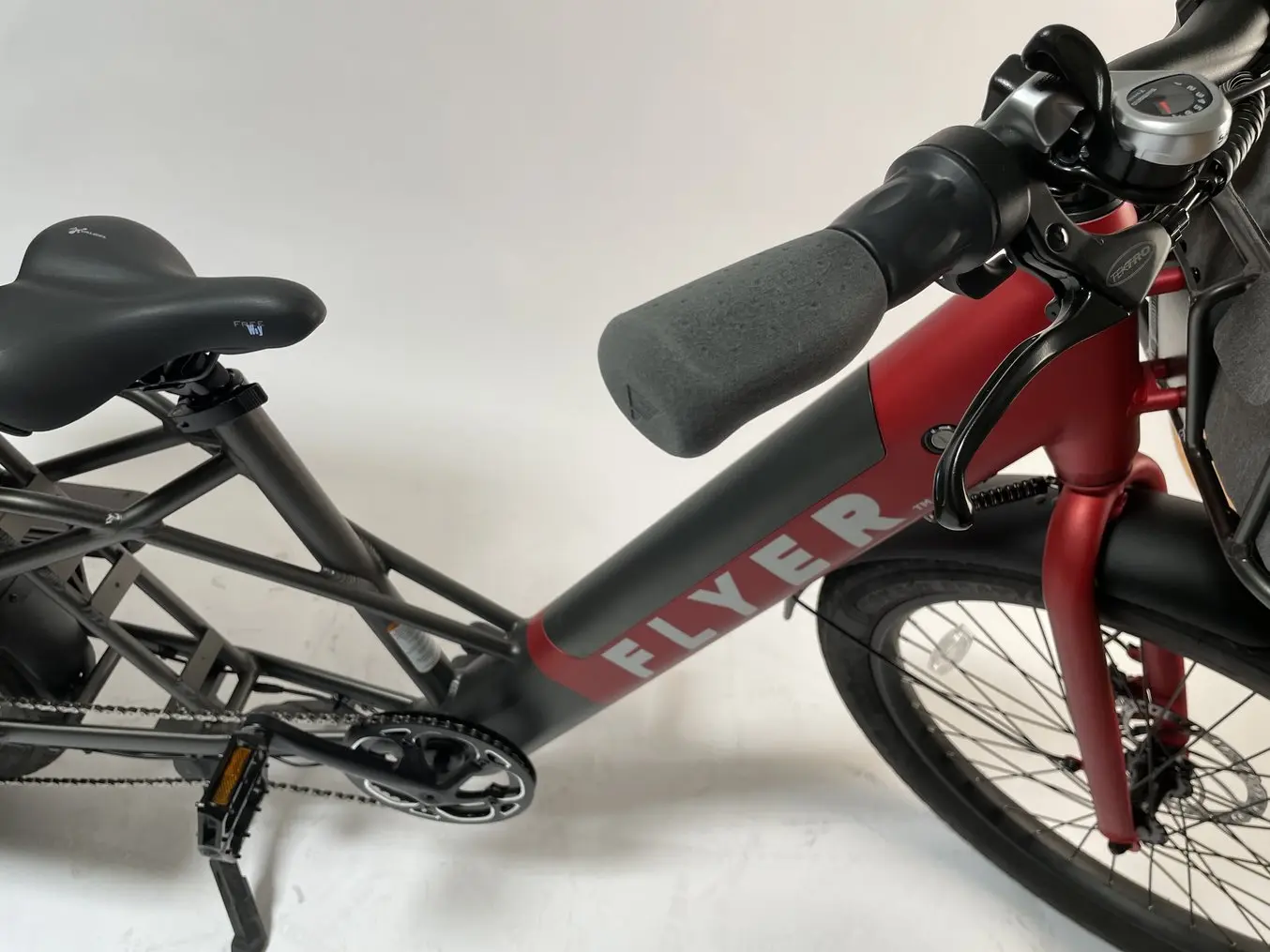
Radio FlyerはFuseシリーズにてTPU 90Aパウダー使用し、Flyer™ L885 Family Cargo eBikeに搭載するソフトグリップハンドルバーなどの機能試作を製作している。
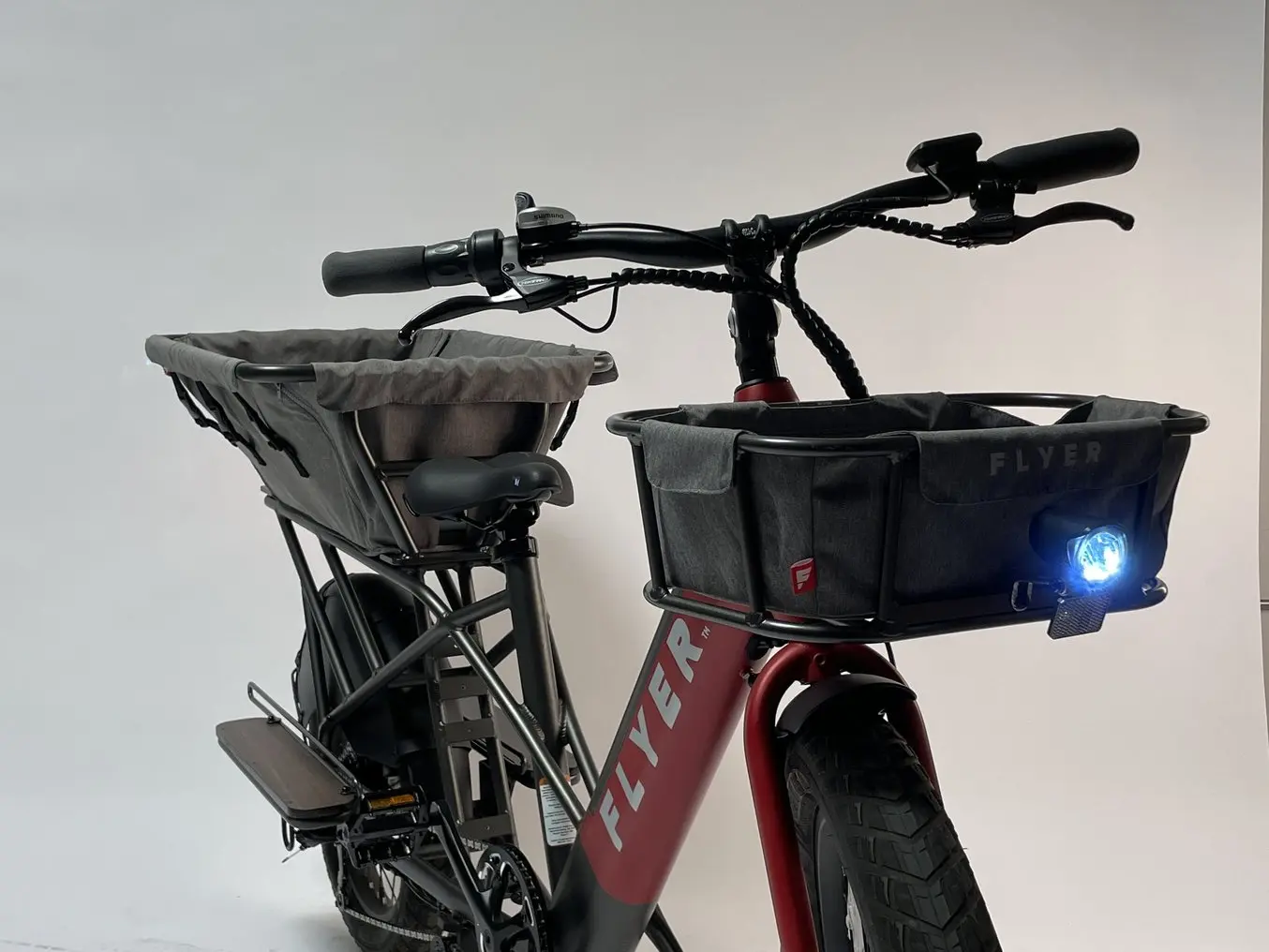
FuseシリーズでTPUの3Dプリントを開始
手頃な価格で使用できるSLS 3DプリントとTPUパウダーを組み合わせることで、メーカーは高品質の試作品で試作・検証プロセスを行うなど設計工程の質をさらに向上させたり、実製品用のカスタム部品の生産にも取り組めるようになります。
プリンタとFuse SiftがセットになったFuseシリーズは、コンパクトかつ手頃な価格でどなたにもアクセスしやすい製品となっています。FormlabsのTPU 90Aパウダーで、従来であれば成形が必要だった高強度・弾力性・等方性の全てを備えた部品を製作できることで、新しい用途の開拓や作業工程の合理化を可能にします。ゴムライクな部品の内製能力が備わることで、その用途や業界に関わらず、設計と製造プロセスをより高度にコントロールでき、かつ様々な変化に迅速に対応できる柔軟性も備わります。皮膚に触れても安全なFormlabsのTPU 90Aパウダーは、ヘルスケアやウェアラブル業界の可能性を今後も広げていくでしょう。
Formlabs SLS 3Dプリント製品を使ったTPU部品の生産に関する詳細は、TPU 90Aパウダーで造形した無償サンプルをリクエストいただくか、Formlabsまでお気軽にお問い合わせください。お客様の用途について、まずは一度お話ししましょう。