自動車業界は現在、化石燃料から電気自動車への移行に対する消費者感情の高まりや規制の義務化が進む中、急速な変革が進んでいます。Fordは100年以上前にモデルTの生産と組立ラインの導入を主導した時と同じく、この変換でも先頭に立ち、2030年までに欧州での販売をEV車のみとすることを目標としています。
Ford Motor Companyは世界第6位の大手自動車メーカーで、年間400万台以上の自動車を生産し、世界中で17万5,000人以上の従業員を有する企業です。Fordの欧州事業の中心となっているのは、1930年に設立し、Ford Fiestaの組立で有名なFord Cologneです。
この工場に隣接するPD Merkenichは開発センターとして、Fiesta、Focus、Kugaをはじめ、欧州市場初の完全電気自動車としてCologne組立工場で連続生産を開始したExplorerなど、人気モデルを含む欧州市場向けの全乗用車を一から設計しています。また、英国にあるFord Dunton Technical Centreと協力し、商用車の開発もサポートしています。
しかし、激しい競争とますます短縮化が進む開発サイクルに、Fordはどのように対応しているのでしょうか?この記事では、製品開発には欠かせないラピッドプロトタイピングを担うPD Merkenich Rapid Technology Centerでの様子をご紹介します。
実物大の自動車用プロトタイプの製作をサポート
「プロトタイピングは、開発工程において非常に重要な役割を果たします。試作品を作ることで、エンジニアが設計を実物で検証できるようになるんです。射出成形用の金型や量産用の金型を作ってから後で設計変更が必要になった場合、非常にコストがかかります。金型製作には多大な時間もかかるため、最悪の場合は生産ラインでダウンタイムが発生する原因にもなります。プロトタイピングを行い、利用できる技術を全て活用することで、このような事態を避けることができます」と、FordのRapid Technology CentreのスーパーバイザーであるSandro Piroddi氏は述べています。
実物大の車両の試作品製作にはさまざまなツールが必要になります。Rapid Technology Centreは、最新の製造設備を備えた広大な施設です。独自の射出成形機や成形機の他、最大サイズのシャーシパネルも収容できるフライス盤などを含む多様なサブトラクティブマニュファクチャリングツールが揃っています。
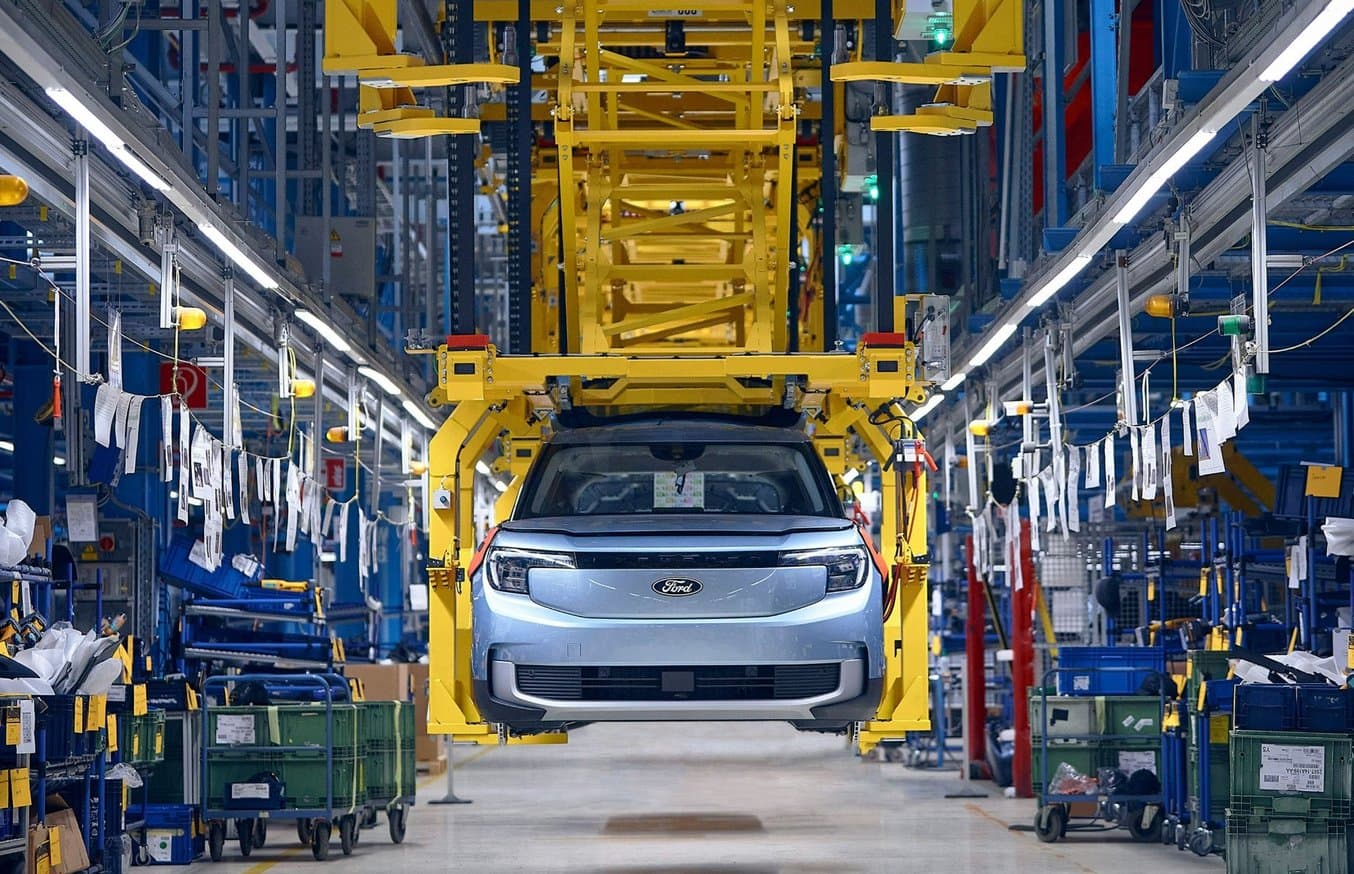
完全EVのExplorerは最近、Cologne組立工場で連続生産が開始された。
もちろん、同社の設備はアディティブマニュファクチャリングなしでは完結しません。PD Merkenichは、1994年にヨーロッパで初めてSLA光造形方式の3Dプリンタを導入して以来、FDM(熱溶解積層)方式、SLA光造形方式、SLS(粉末焼結積層造形)方式などのポリマーベースの3Dプリンタ、および金属3Dプリンタの拡張を続けてきました。
初回のコンセプトモデルは今でも粘土から作っているものの、製品開発工程が進み各コンポーネントが最終的な形状に近づくにつれ、可能な限り量産で使用する材料や工程に近い状態で形状・機能の両方をテストすることの重要性が増していきます。
「アディティブマニュファクチャリングは、開発工程において非常に重要な役割を担っています。部品を迅速かつ効率的に製作できる他、コスト削減にもつながりますし、短期間での対応が可能になります。電動製品の開発は、開発期間の短縮化が進んでいます。つまり、自動車の部品を開発し、それを検証できる時間が短くなっているのです。そのため、開発工程でアディティブマニュファクチャリングを使用できることが非常に重要で、競合他社に比べてはるかに競争力が高まります」
Ford Rapid Technology Centre スーパーバイザー、Sandro Piroddi氏
開発スケジュールの短縮化が続く中、Rapid Technology Centreでは部品の納期を短縮できるアディティブマニュファクチャリングの強化を常に模索しています。
SLA光造形3Dプリントでデザインプロトタイプを製作
同社では、SLA光造形方式3Dプリンタを主にワークショップで使用しています。主な用途は、優れた表面品質が要求され、試作・検証プロセスを高速で回す必要のあるデザインプロトタイプの製作です。PD Merkenichが最初に導入したFormlabsプリンタはForm 2でしたが、すぐに複数のデスクトップサイズプリンタと大容量SLA光造形3DプリンタのForm 3Lを追加で購入しました。最近のアップデートでは、Formlabsの最新MSLA 3DプリンタであるForm 4をいち早く導入した企業の一つでもあります。
「Form 4は非常に高速で、スピードという点ではこれまで試した中でも最高峰です。前世代機と比べてもとても優れたアップグレードだと思います。操作も簡単で、弊社のワークショップ担当オペレーターもプリンタの使い方を簡単に習得でき、高品質の部品を作ることができています」と、Fordのアディティブマニュファクチャリング・エキスパート兼金型製作スペシャリストのBruno Alves氏は言います。
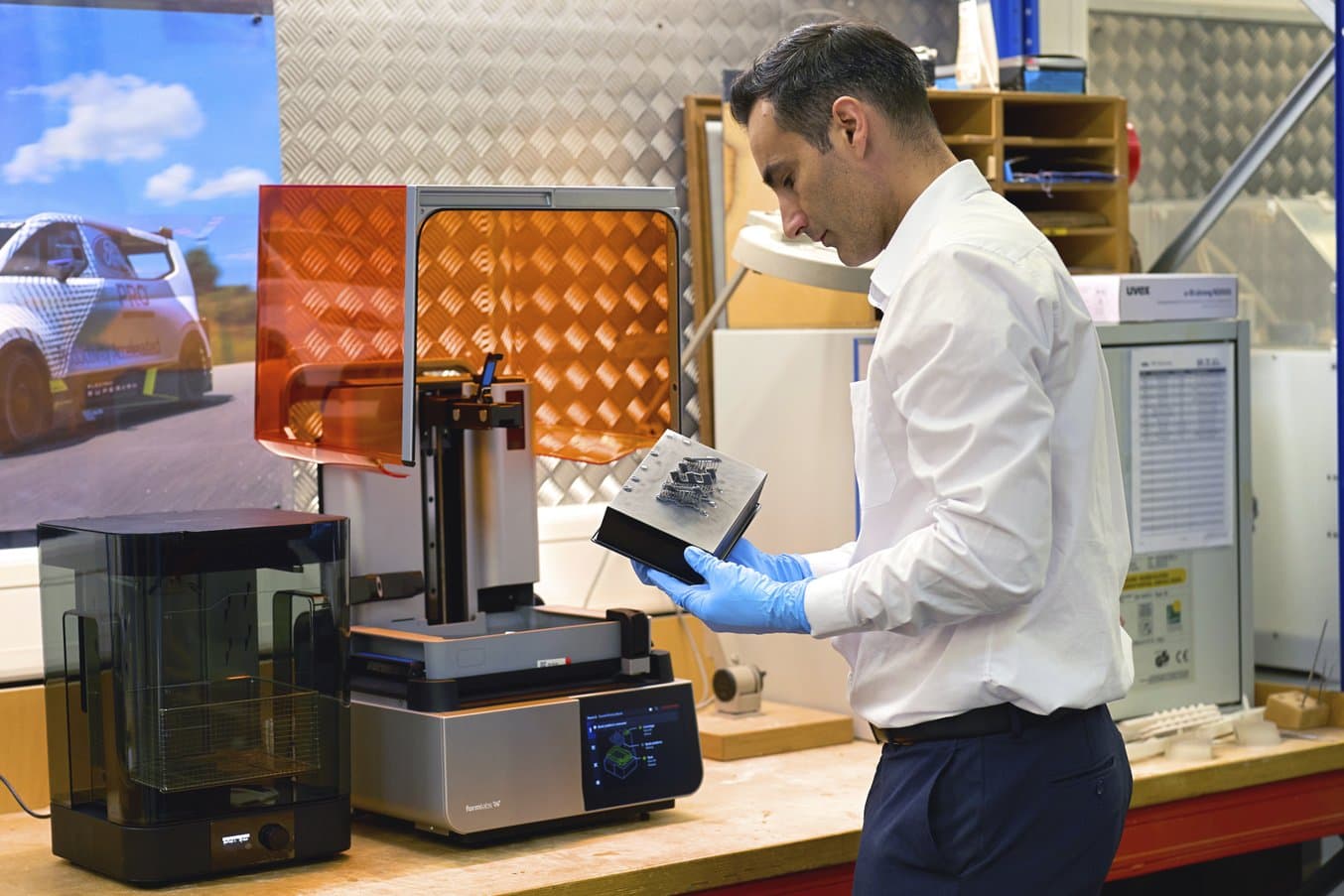
PD Merkenichは、新登場のForm 4をいち早くベータテスターとして使用した企業の一つ。新しいプリンタの驚異的な造形速度により、ワークショップでは新しいプロトタイプをわずか数時間で提供できるように。
「Form 4はまさにゲームチェンジャーです。この造形速度のおかげで、工程にも変化が出ます。生産量が上がるのでより多くの部品を提供できますし、急ぎの依頼にもより柔軟に対応できます。Form 4の導入でこれら全てが可能になりました」
Ford Rapid Technology Centre スーパーバイザー、Sandro Piroddi氏
「何年か前は何日もかけて造形していたものが、今では数分で完成するようになりました。エンジニアたちもすぐに造形品が出来上がることがわかっているので、躊躇することなく新しいデザインや試作・検証プロセスを試すことができます」と、Alves氏は付け加えます。
造形スピードが上がったことで、RTCチームはより多くの依頼を24時間以内にこなせるようになり、夜のうちに部品を発送することで迅速な納品が実現しています。
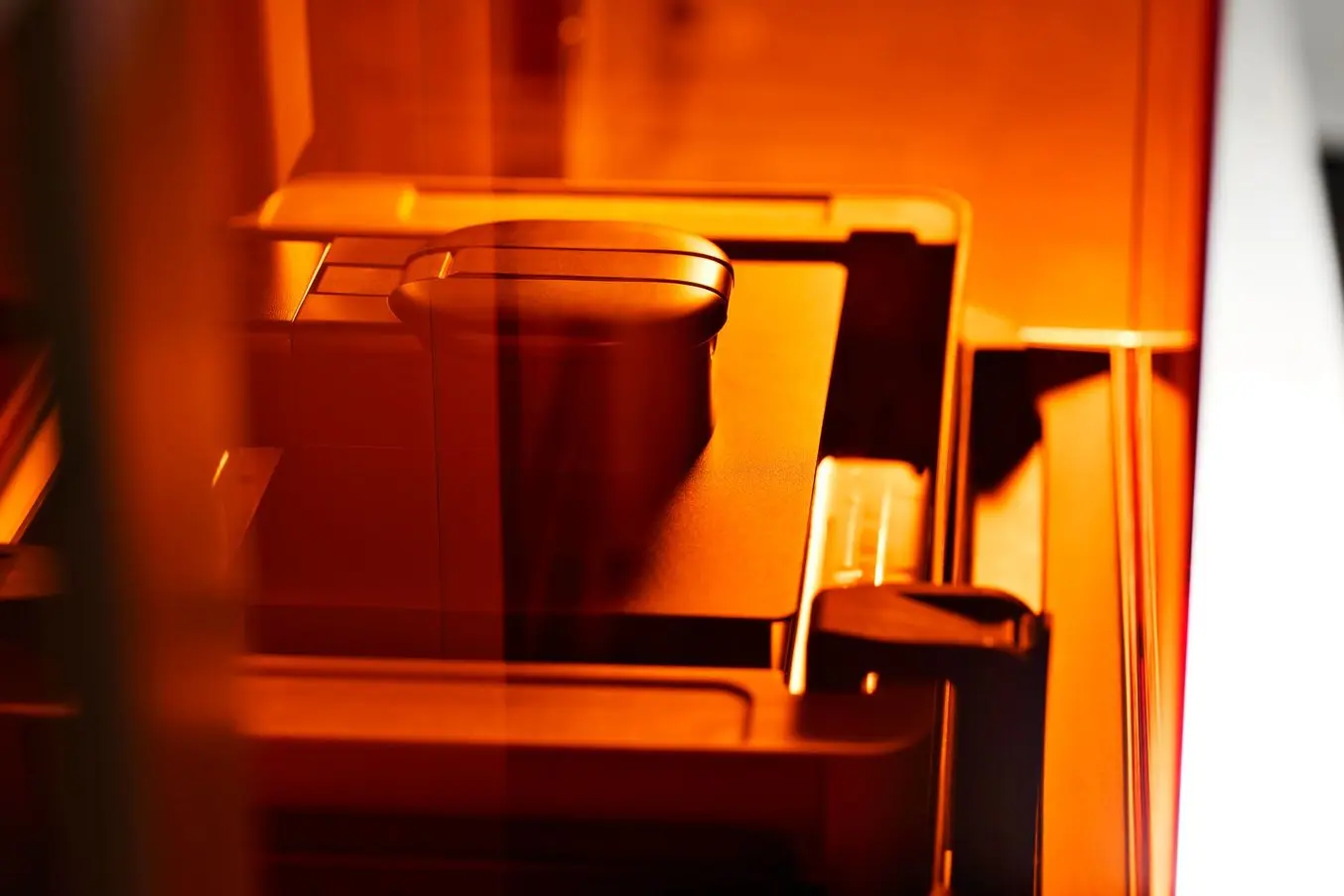
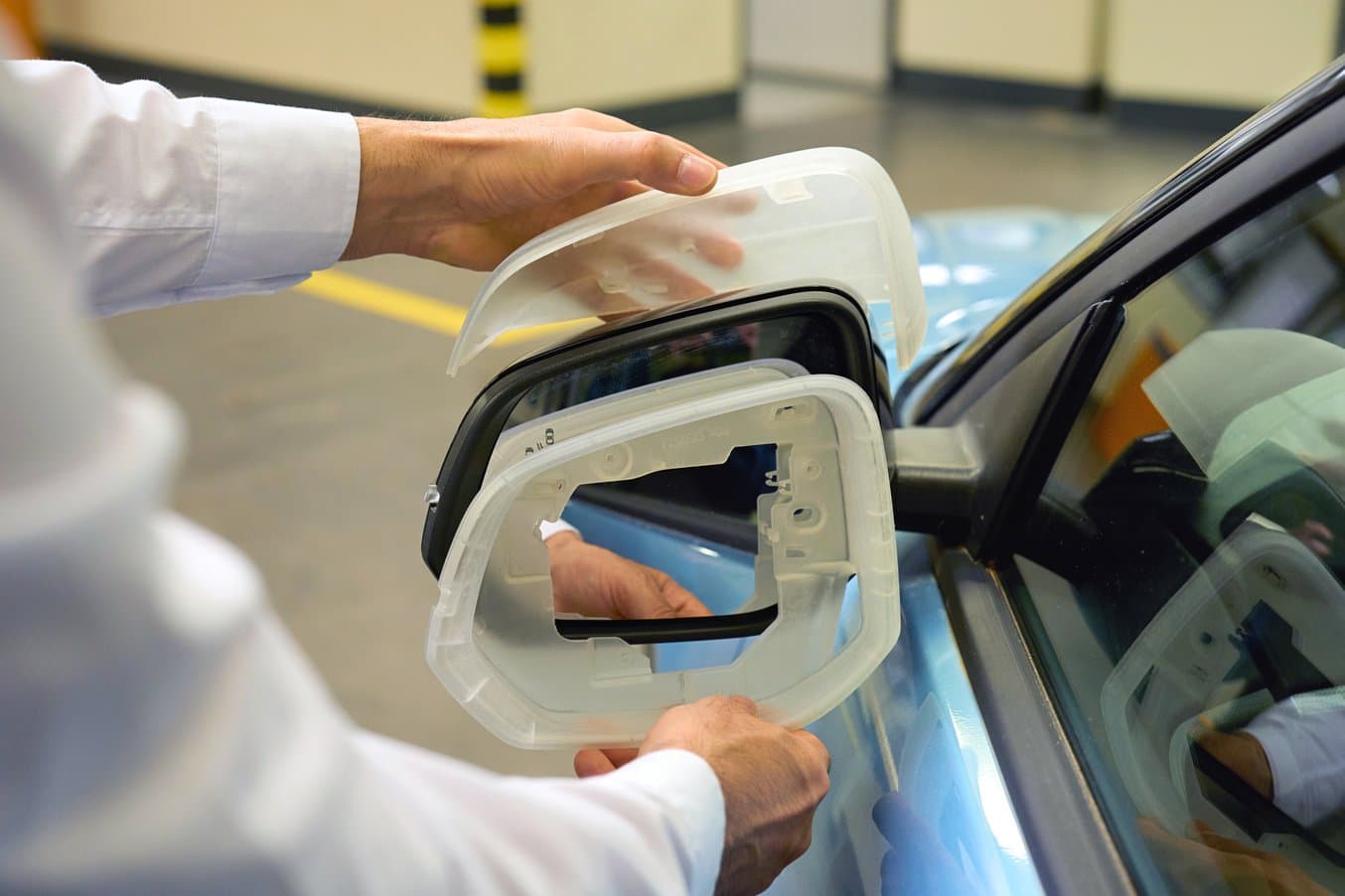
同社チームはSLA光造形3Dプリントで新型Explorerの多くの部品の試作を製作。写真のバックミラーアセンブリもその一つ。
新型Explorer向けに、同社チームはSLA光造形を活用して多くの外装および内装部品の設計検証を行いました。
Alves氏はこう続けます。「Form 3Lは、外装として車体に取り付ける部品など大型のパーツも造形が可能です。このミラーキャップは、設計検証用にプリントしたものです。高速で大量生産品に比べて非常に品質の高い造形品が出来上がるので、3Dプリントはこの用途に最適なんです」
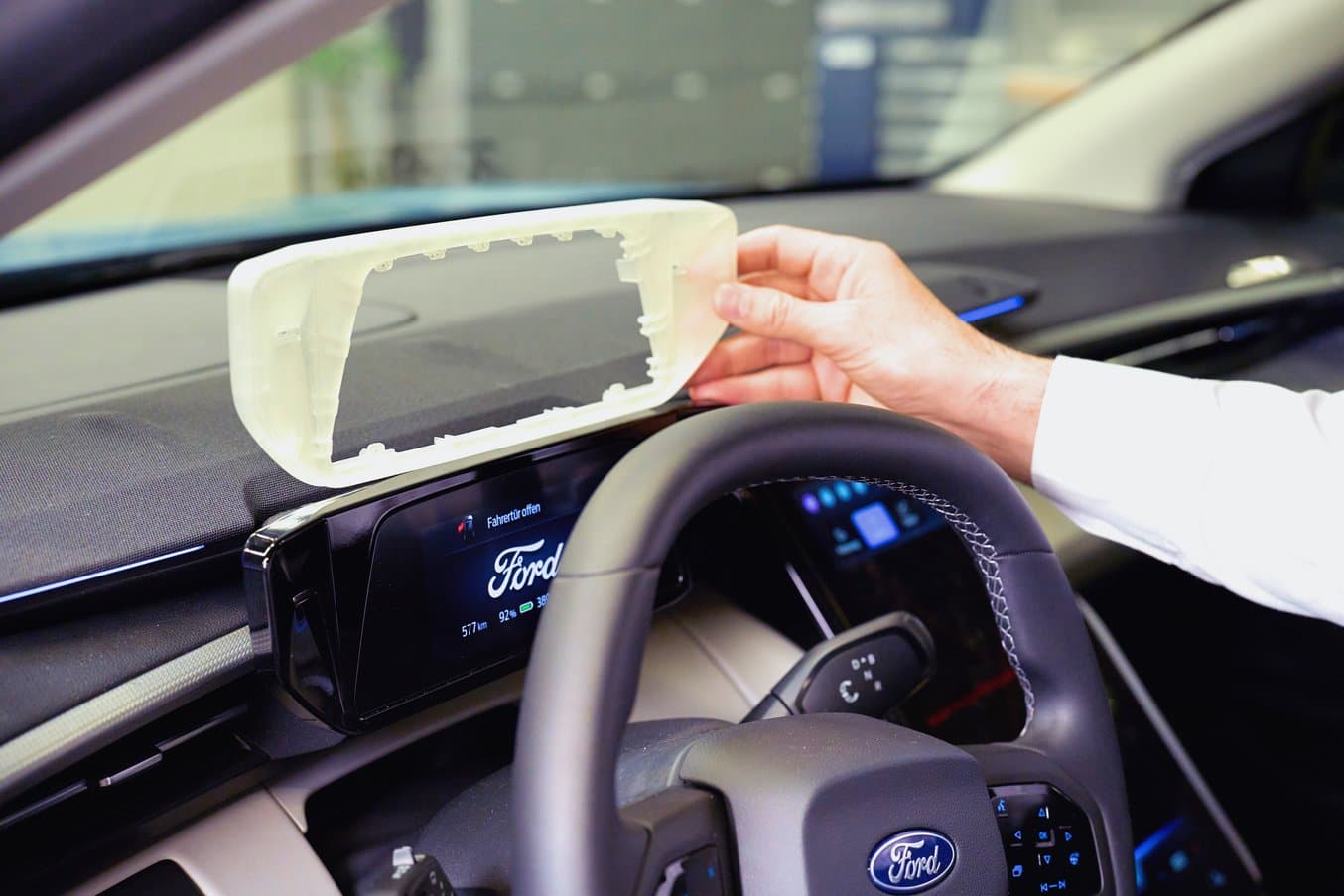
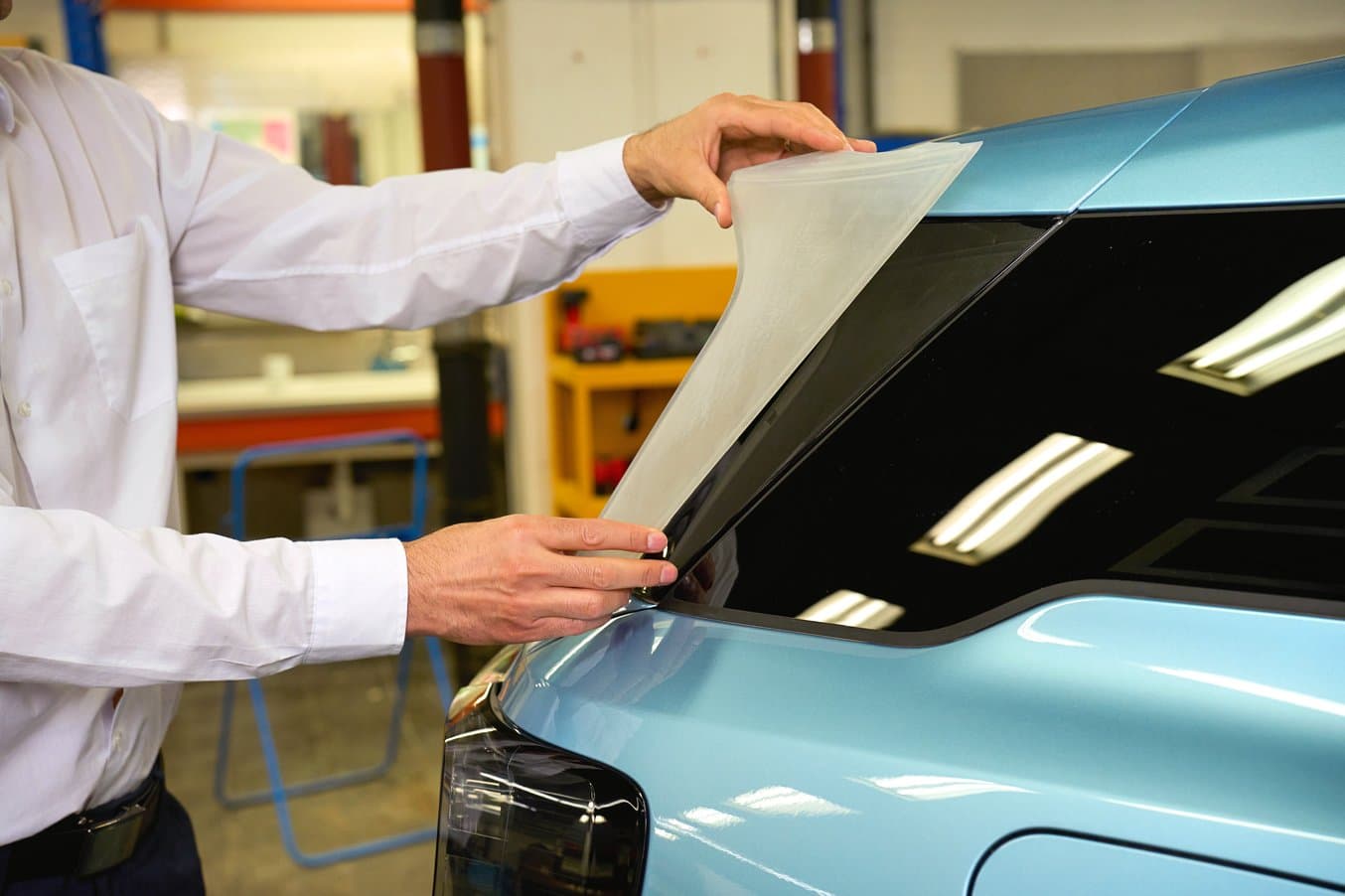
大容量Form 3Lでは、大型の試作品も分解することなく一度に造形が可能。
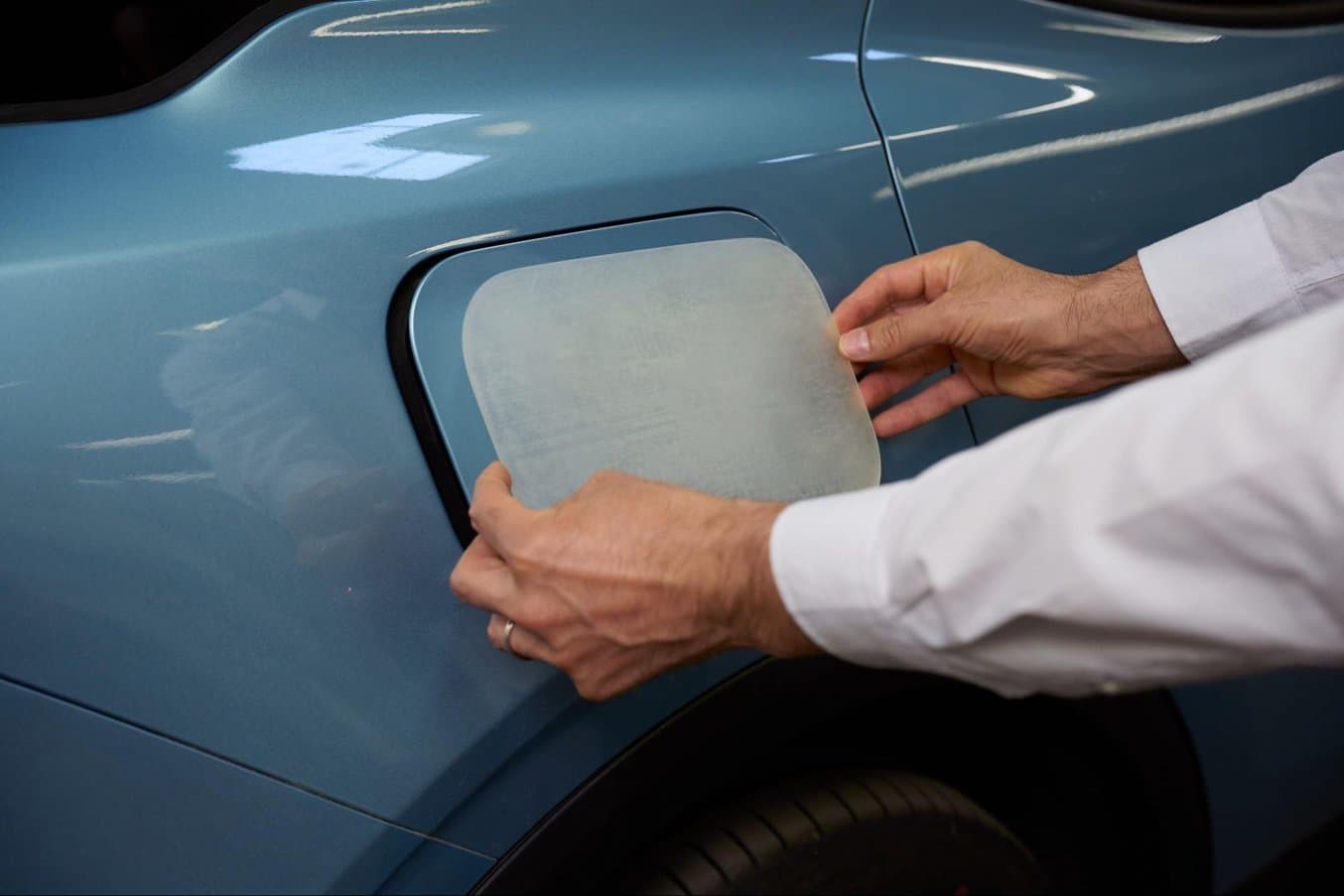
これらのパーツはClearレジンを使って造形し、Fuse Blastでブラスト処理を施したもの。
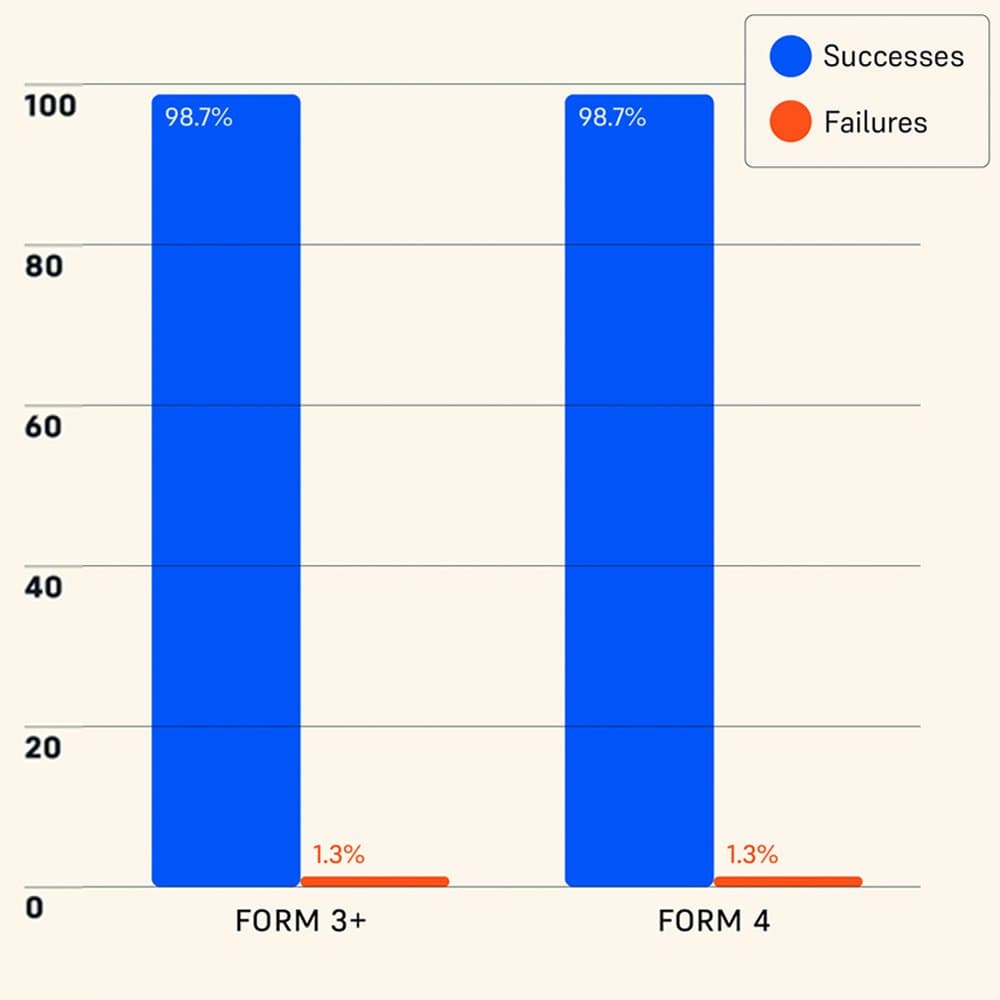
Form 4と他社製光造形3Dプリンタの信頼性に関する第三者試験
独立試験機関により、Form 4 のプリント成功率は 98.7 % と評価されました。テスト方法と結果の詳細についてはこちらの技術資料でご確認いただけます。
SLS 3Dプリントで機能部品を検証
ワークショップではSLS 3Dプリンタも複数台稼働しており、機能部品の検証用に使用しています。
「私たちは常に、大量生産で使用する材料に近い材料をテスト・検証しています。Fuse 1+では射出成形による量産部品に非常に近いPA-12[ナイロン]を使用しています」とAlves氏は述べます。
大型の車体パネルでも造形可能な大容量SLS 3Dプリンタも設置されていますが、最大造形サイズに収まるものであれば普段はFuse 1+ 30Wを使うことが多いと言います。
「Fuse 1+は競合他社の製品よりはるかに高速なんです。また非常に使いやすく、作業員も簡単に操作ができます。最終的に私たちが最も重視するのは、パーツをいかに速く納品できるか、これにつきます」
Ford アディティブマニュファクチャリング・エキスパート兼金型製作スペシャリスト、Bruno Alves氏
同社チームは、後処理を簡素化しFormlabsのSLSシリーズを完結させる粉末除去・研磨用自動化装置Fuse Blastのベータテスターでもありました。
「Fuse Blastのおかげでオペレーターが手作業で粉末除去をする必要がなくなったため、作業工程が大幅にスピードアップしました。造形品を庫内に入れて装置を作動させるだけでいいんです。以前は粉末除去を手作業で行っており、非常に時間がかかっていました。オペレーターは浮いた時間を他の作業に回せるようになり、工程全体が高速化しました」とAlves氏は言います。
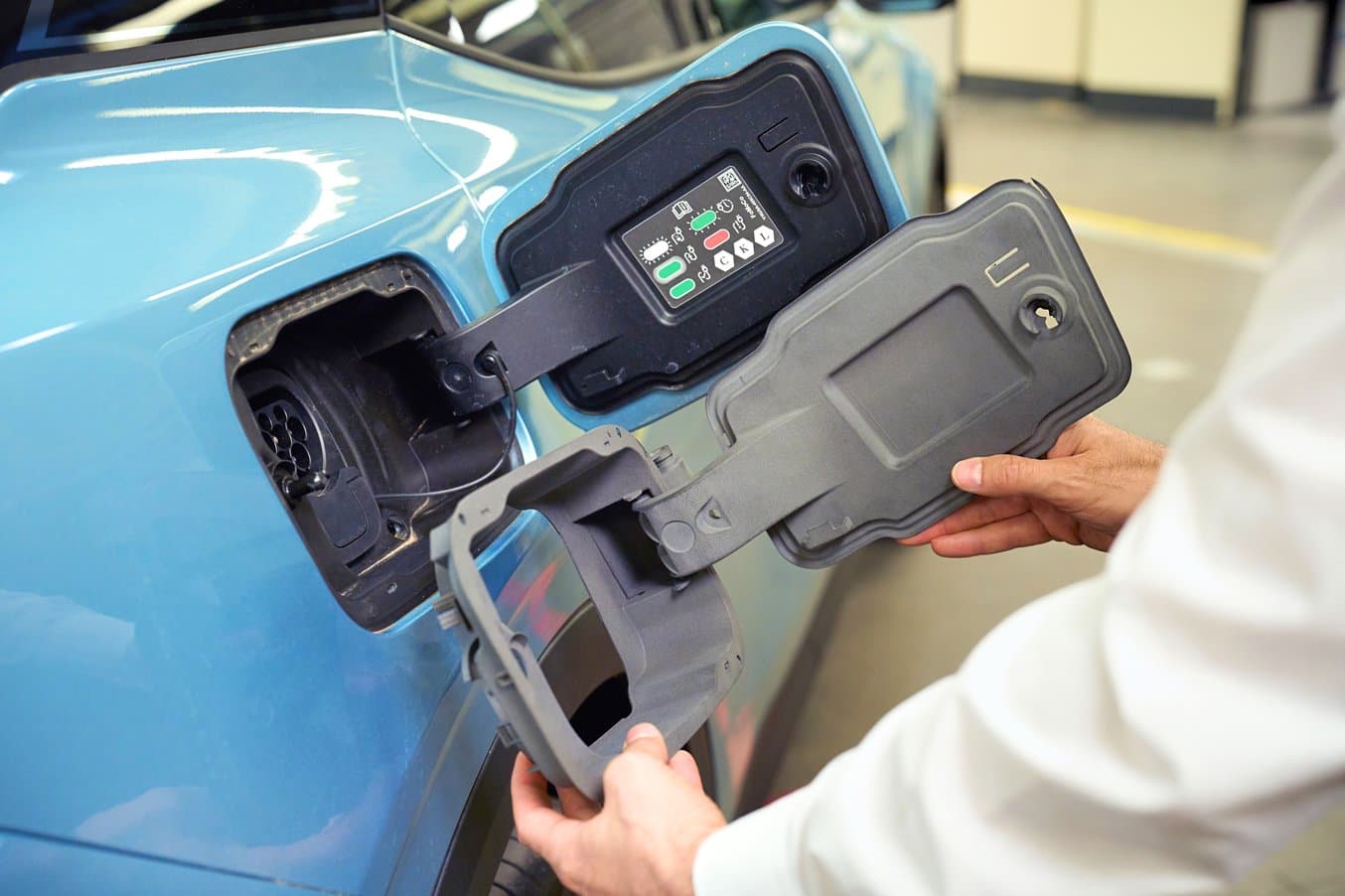
充電ポートは複雑なアセンブリで、他の方法では試作製作が不可能だった。
SLS 3Dプリントでは、造形中は未焼結の粉末が造形品を支えるため、複雑なデザインの部品でも簡単に製作できます。同社チームは、新型のExplorer用にFuse 1+ 30Wで様々な機械部品とアセンブリを製作しました。
「この充電カバーを開発した時は、メカニズムをテストできる機能部品が必要だったため、SLSで作る必要がありました。非常に複雑な設計で、他の方法では製造できないためです。例えばフライス加工することもできませんし、射出成形でサンプル品を作ることもできません。物理的にテストを行える材料で造形するのが最善の方法だったんです」とAlves氏は振り返ります。
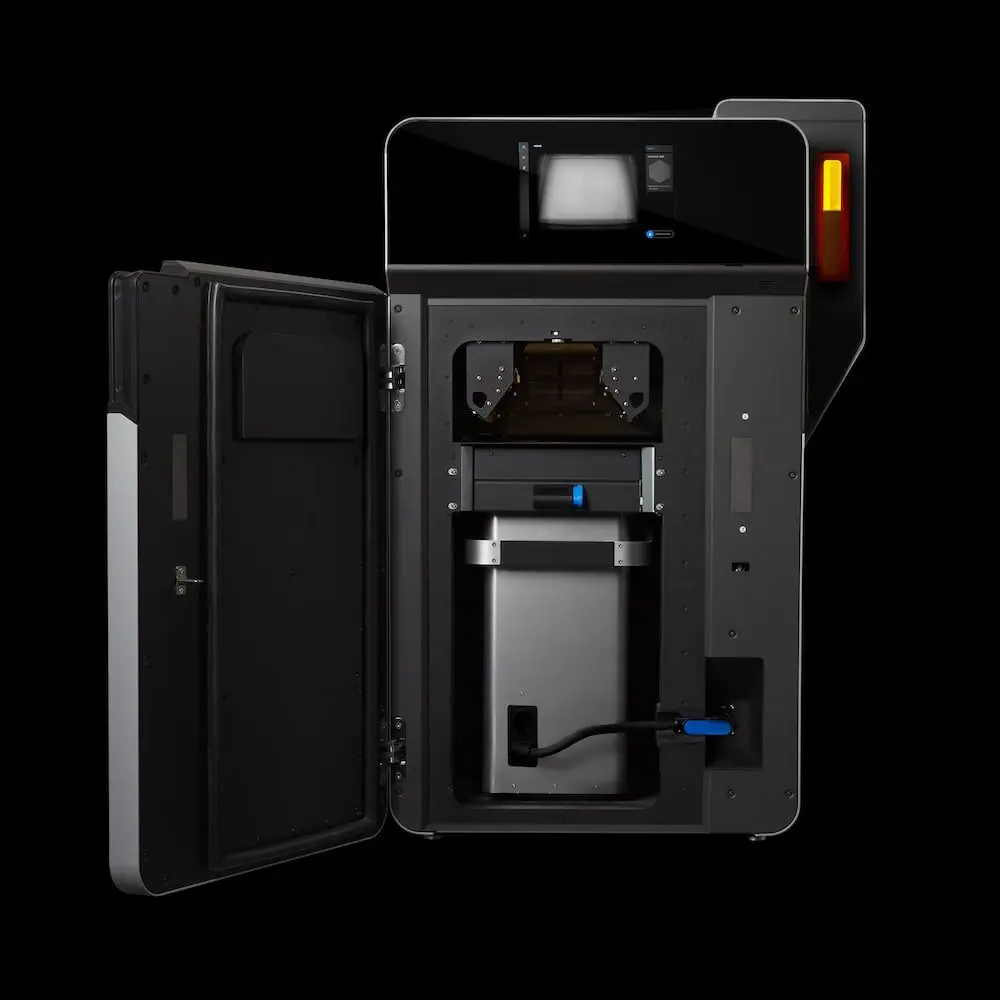
新しいSLS方式プリンタFuse 1+ 30Wで高性能部品を高速製作
本ウェビナーでは、Fuse 1+ 30Wの製品概要やSLS方式3Dプリントの概要をFormlabsのエキスパートがご説明します。
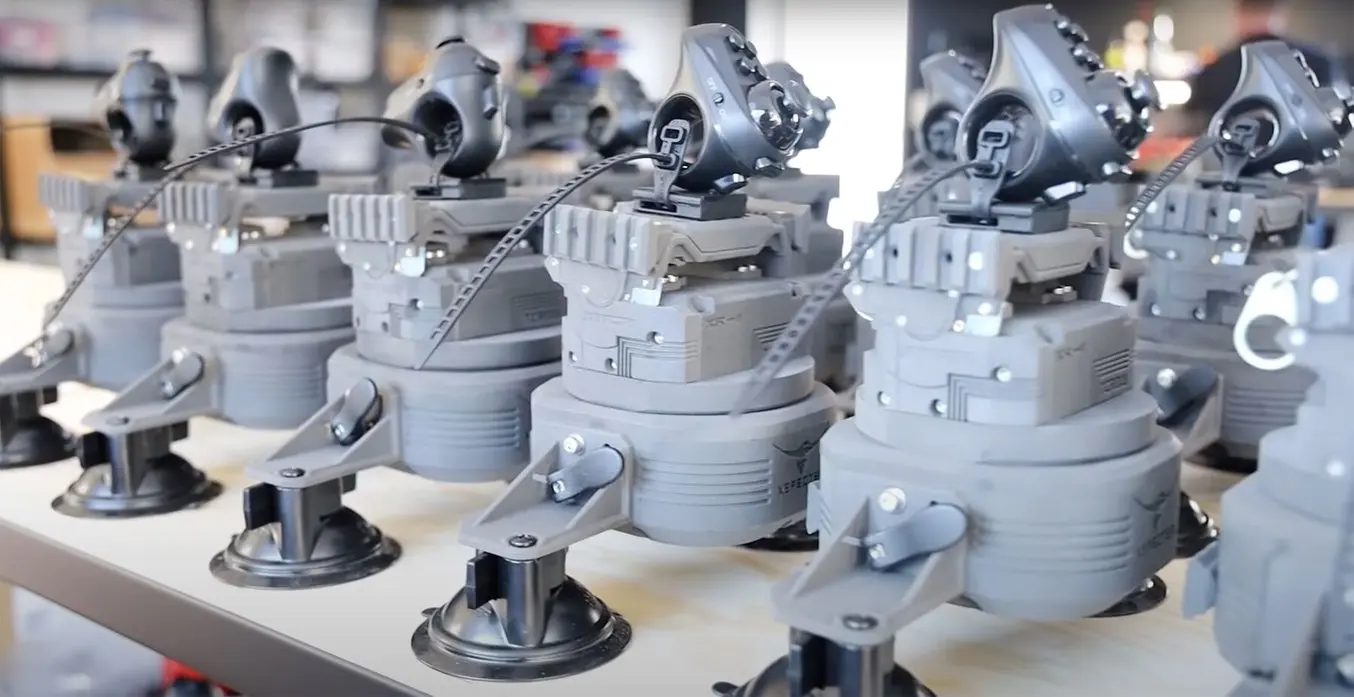
SLSを実製品の量産に活用
実製品の量産工程への3Dプリント導入は今や単に実現可能となっただけでなく、SLS Fuseシリーズを活用することでこれまでより安価かつ迅速に、そして規模の拡大にも柔軟に対応できます。量産工程におけるSLS活用事例ページにて、量産方法の比較、パウダー材料のボリュームディスカウントの詳細、現在Fuseシリーズを実際に量産工程に取り入れているメーカー15社の事例をご覧ください。
3Dプリンタ製のインサートを使用し、射出成形品を内製
Rapid Technology Centreは社内に多様な技術を導入することで、従来の製造工程と3Dプリントによるラピッドツーリングを組み合わせるなどハイブリッドな製造工程を実現しています。
同社チームはコスト、スピード、作業工程全体の高効率化を実現できるよう、用途に応じて最適な製造工程と材料を選択します。例えば、衝突試験で使用するコンポーネントは大量生産品と同じ材料・工程で製造する必要があります。プラスチック部品の場合は射出成形が用いられることが一般的で、従来であればコストと時間のかかる金型製作が必要でした。
「3Dプリント製のヘリサートを使って射出成形を行うことで設計の試作・検証工程を高速反復でき、多くの可能性を感じています。コアにキャビティを造形し、金型内で変形して射出成形で部品を作るんです」とAlves氏は言います。
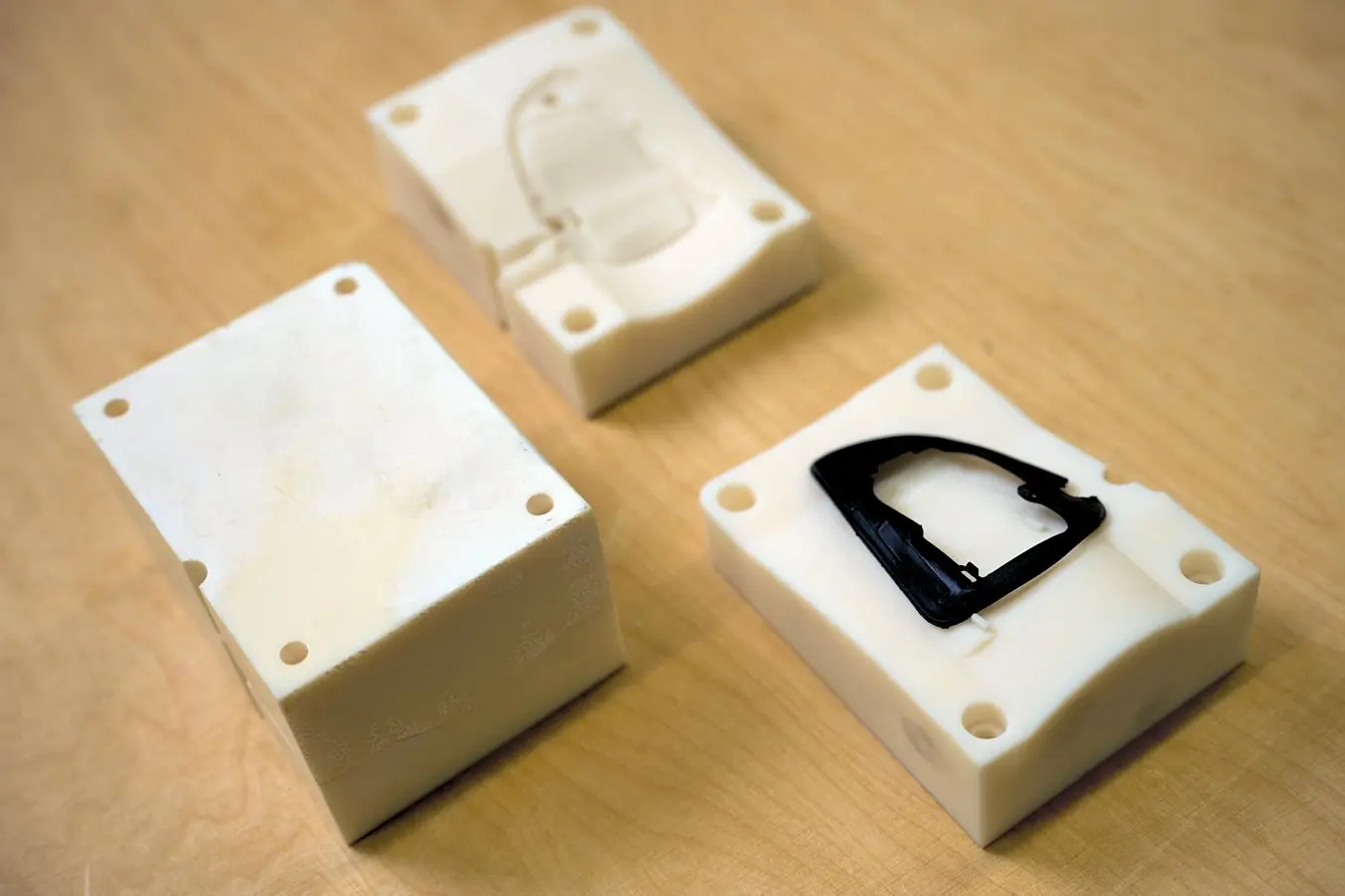
SLA光造形プリンタでRigid 10Kレジンを使用して射出成形用のヘリサートを製造。
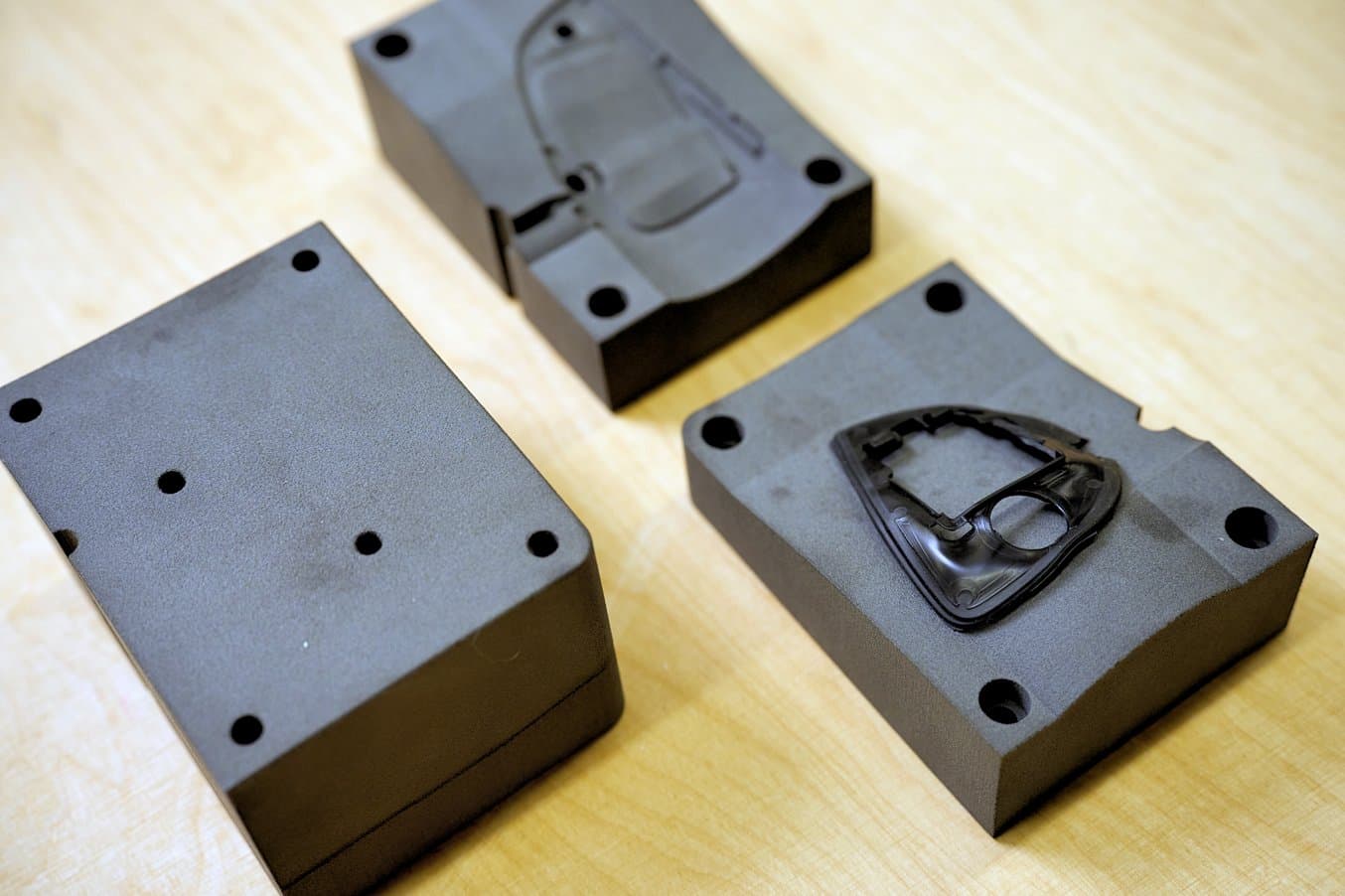
同じ用途にて、SLSプリンタでNylon 12パウダーを使って造形したもの。
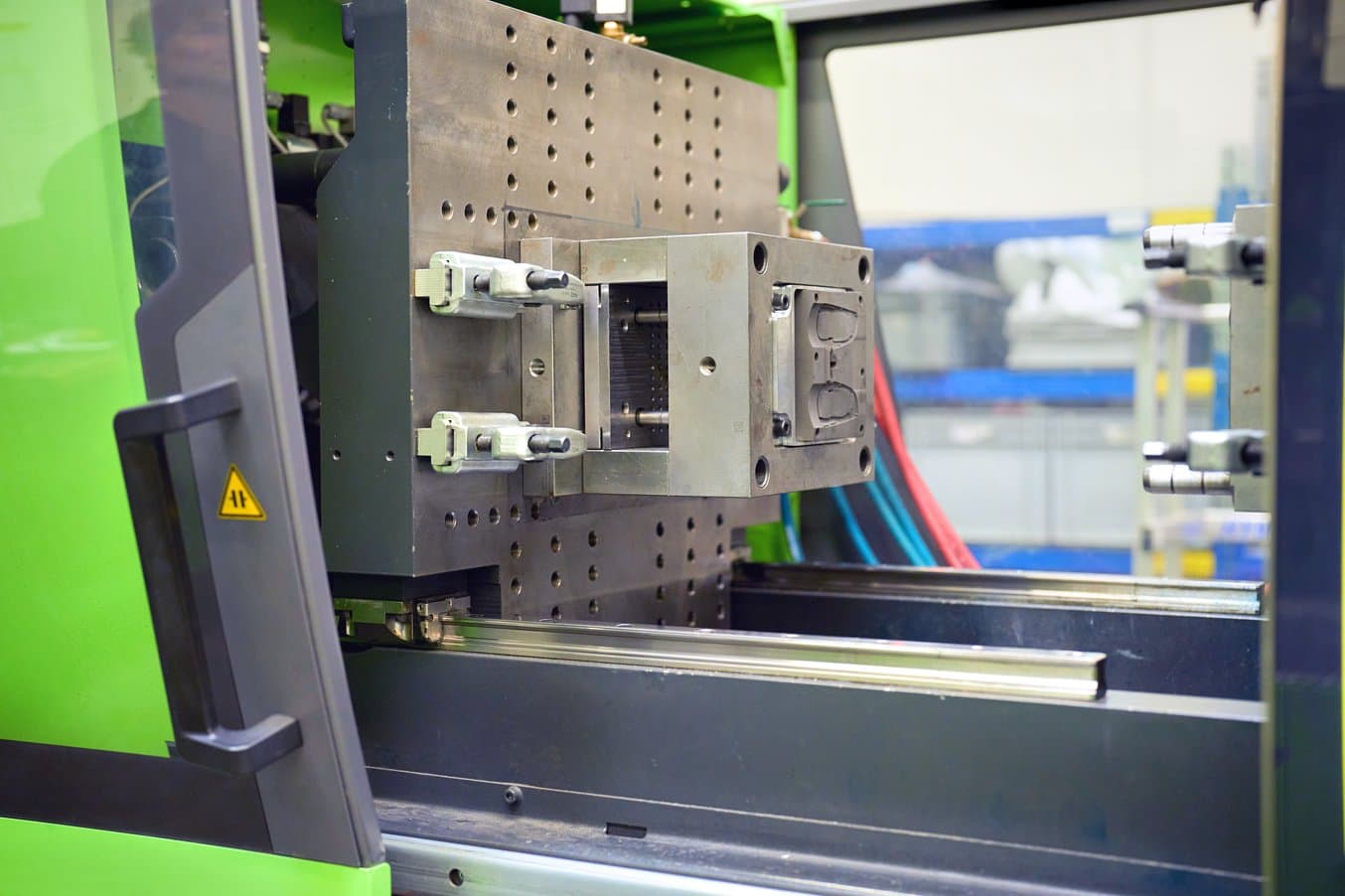
様々なデザインの成形用に3Dプリントでヘリサートを製作し、社内にある産業用の射出成形機を使って試作・検証プロセスを迅速に繰り返す。
新型Explorer向けにも、3Dプリント製のヘリサートを使って社内の射出成形機でドアハンドルアセンブリ用のゴム部品を製造しました。
「これは複雑な工程でした。もともと複数のヘリサートを使用していましたが、さらにそれぞれの種類ごとに別のデザインを複数バージョン用意していたからです。通常、射出成形を外注した場合には完成まで2~3カ月かかります。アディティブマニュファクチャリングを使用して内製することで、その工程を2週間から最大3週間程度にまで短縮することができるんです。もし外注に頼っていたらより多くの時間がかかってしまって、パーツを納期に間に合わせることができなかったでしょう」とAlves氏は言います。
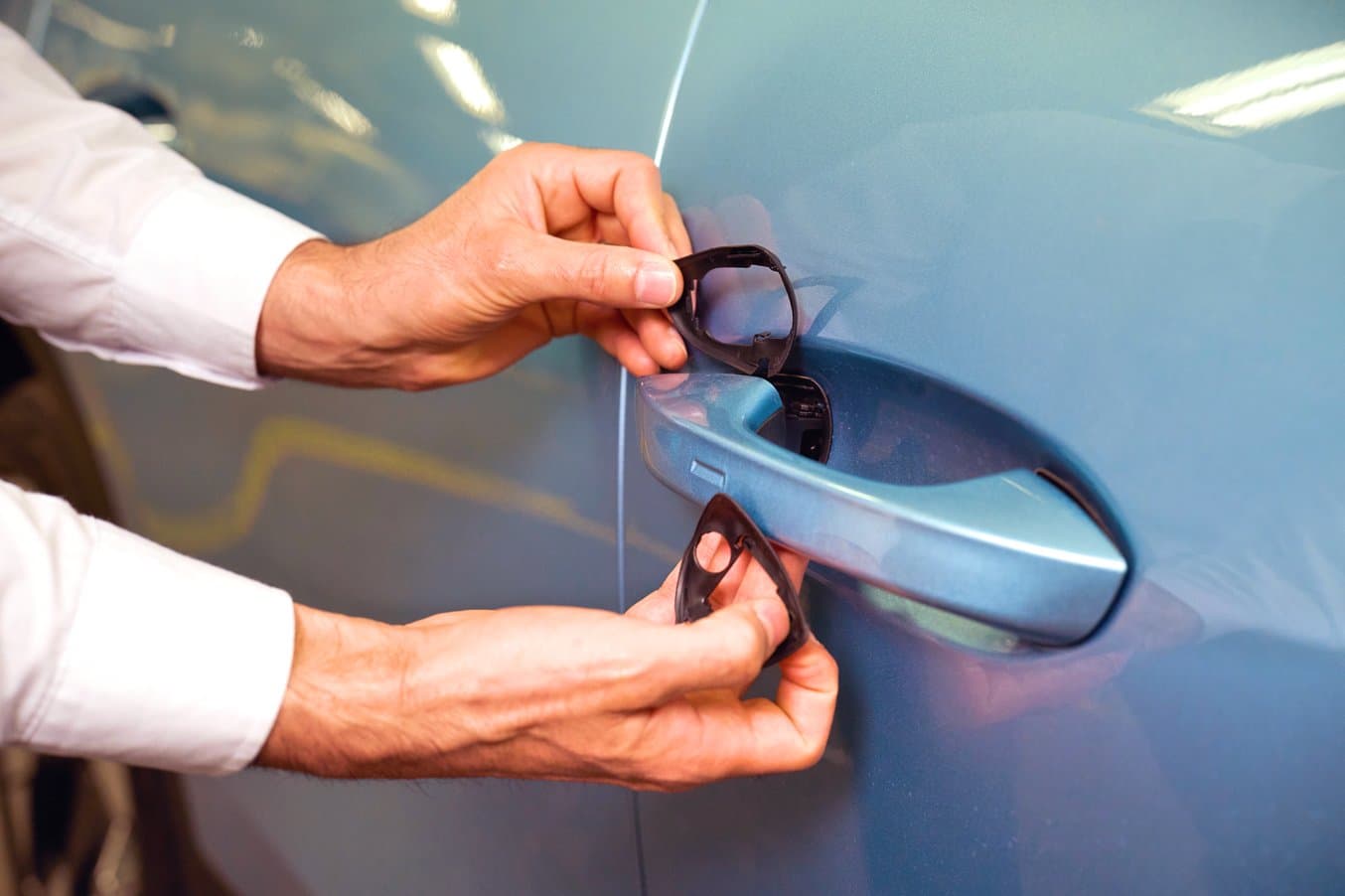
各ドアハンドルのデザインには、減衰・断熱効果のためにゴム部品が2つ搭載されている。4ドアSUVの場合、試作・検証の繰り返しを1回行うごとに異なる部品が8点必要になる。
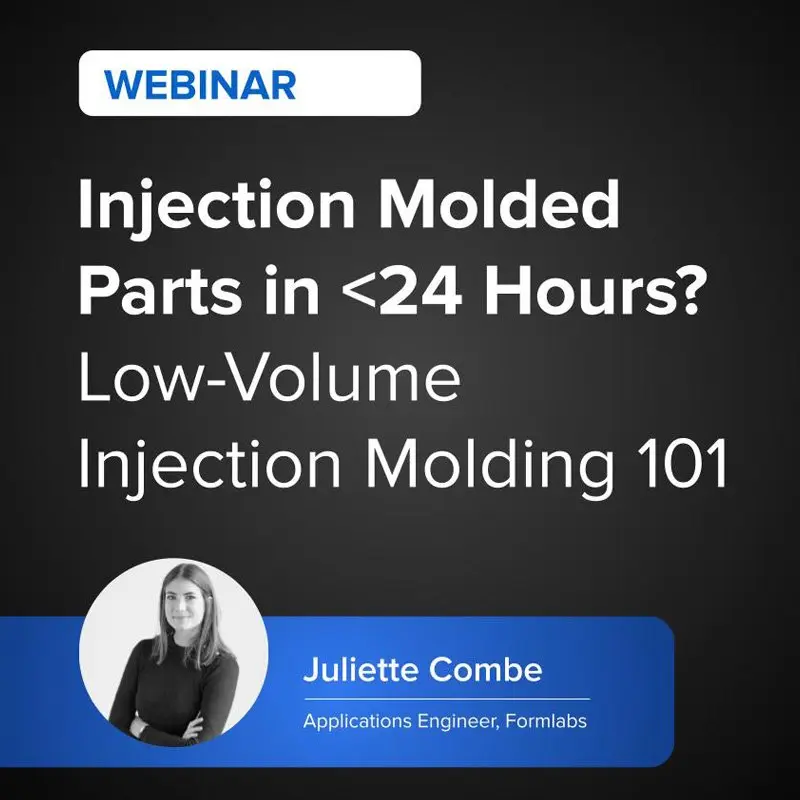
24時間以内に射出成形を完了する方法とは?小ロット量産用の射出成形 101
本ウェビナーでは、射出成形でSLA光造形3Dプリント製型を使用してコストを削減し、製作期間を短縮し、より高品質な製品を市場投入する方法を解説します。
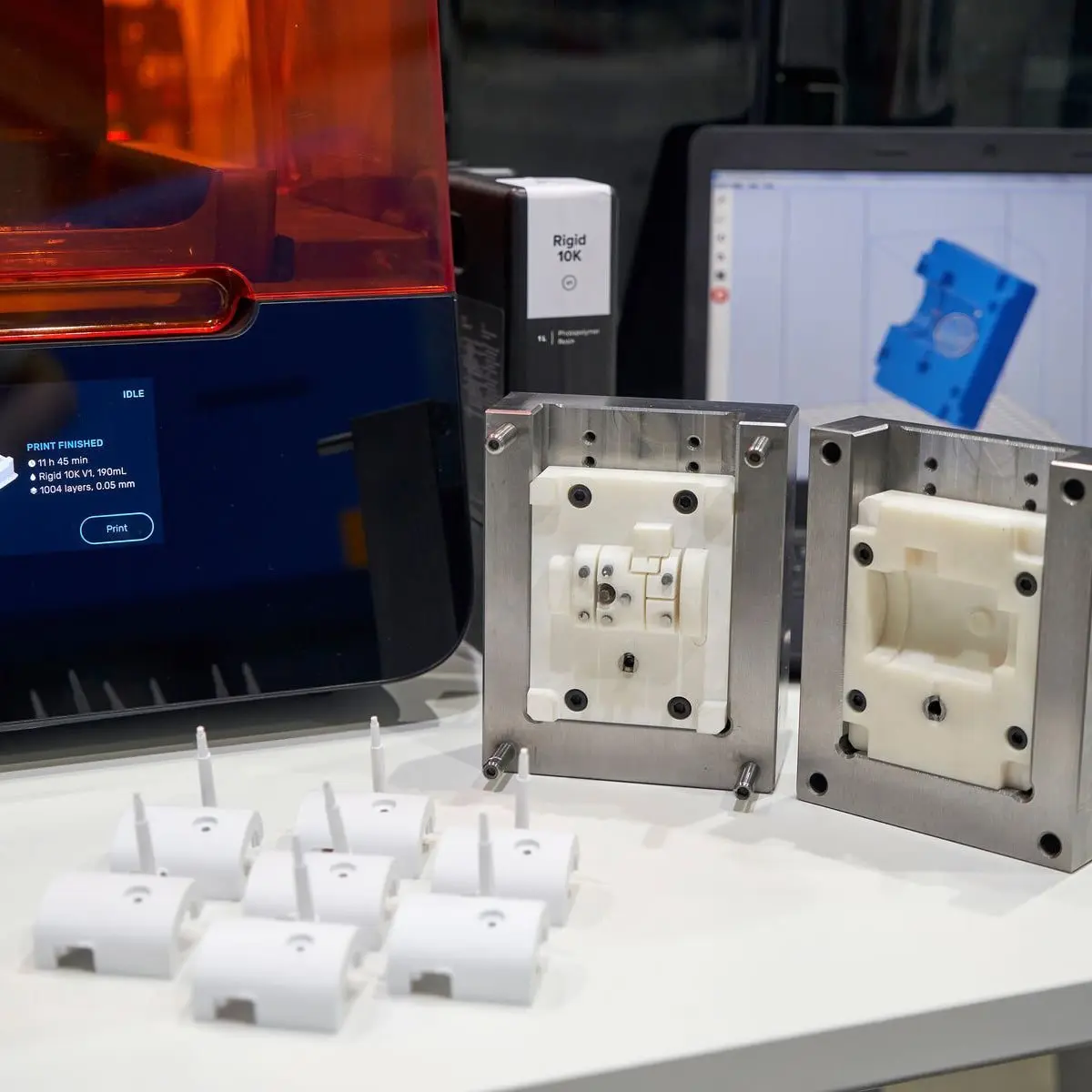
3Dプリントした金型を使った少量高速射出成形
FormlabsのWebサイトでは、3Dプリント製の型を使ってコストと時間を削減しながら射出成形を行う際のガイドライン、また実際にこの手法を導入しているBraskemやHolimaker、Novus Applicationsの事例を掲載した技術資料をダウンロードできます。
電動化を加速する
2030年までに完全EV化を実現するというFordのコミットメントは、PD Merkenichにとって大きな挑戦です。必要なマイルストーンを達成するために、同社は常に最先端の技術を取り入れ、新しい革新的な工程を試していく必要があります。競争優位性を維持するためには、限界を押し広げ、新しい材料や工程、成形型の内製や3Dプリントのような様々な機器を統合し、うまく活用することが求められています。
「競合他社が開発工程を高速化しているので、私たちも同じくスピードを上げなければなりません。その課題に対応するには、市場に新たに参入してくる材料や工程、機器を試していくことが大切です。もしアディティブマニュファクチャリングを採用していなければ、今頃競合他社に太刀打ちできなかったでしょうし、これほどのスピードも出せなかったでしょう。短時間で最高の製品をお客様に提供することができているのは、3Dプリントのおかげです」とAlves氏は言います。