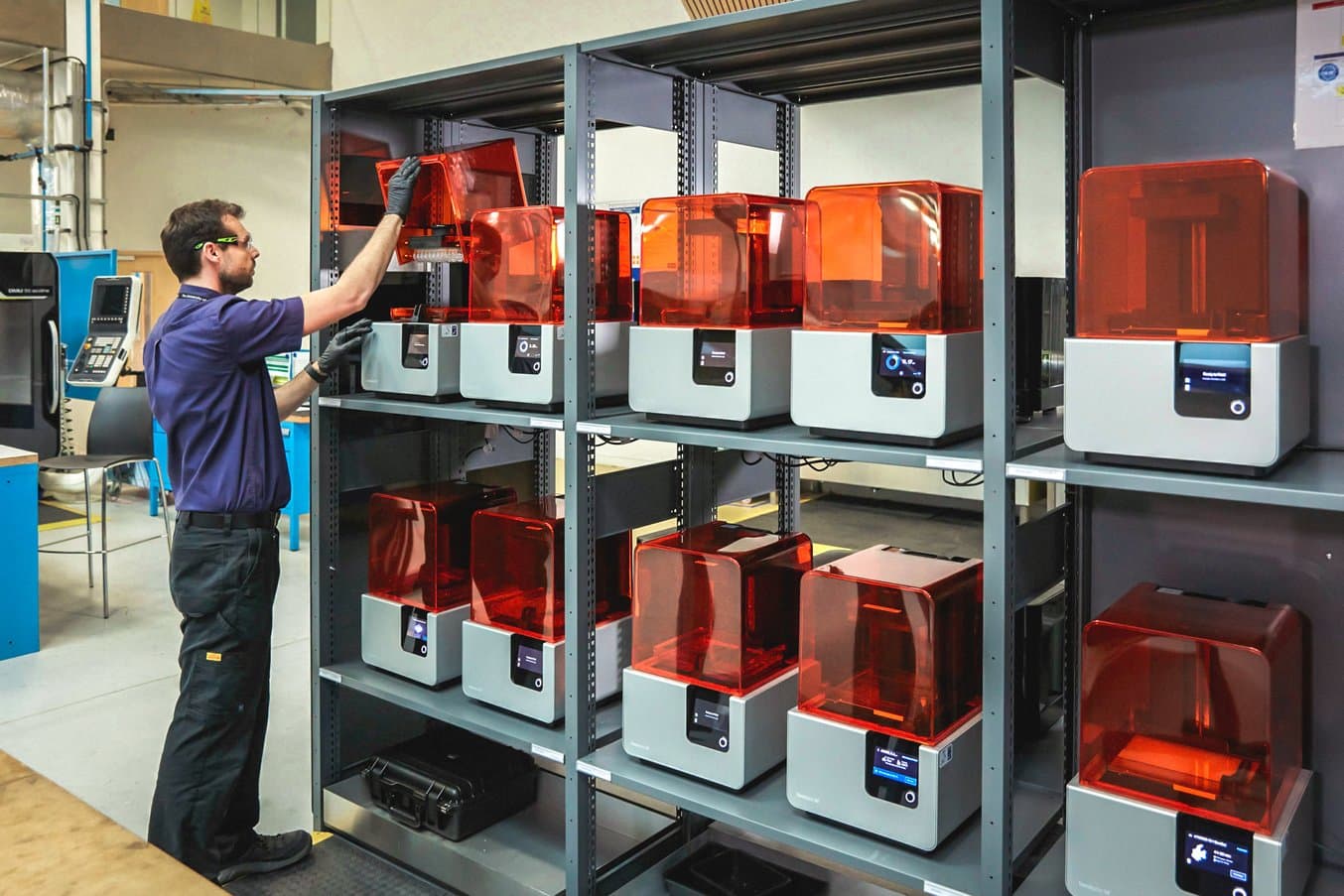
A former opencast coal mine might sound like an unlikely place to define the future of industry, but a 100-acre reclaimed land in the outskirts of Sheffield is home to the highest concentration of skills and expertise in manufacturing technology in the United Kingdom.
The University of Sheffield Advanced Manufacturing Research Centre (AMRC) conducts world-leading research in advanced machining, manufacturing, and materials, helping over 100 industrial partners ranging from global giants like Boeing, Rolls-Royce, BAE Systems, and Airbus to small companies who want to become more competitive. These business partners approach the AMRC with specific challenges, and AMRC researchers use the newest technologies and processes to develop concepts and solutions to the point where the partners can implement them in their factories.
Additive manufacturing has long been among the set of tools that researchers could use to turn around concepts and ideas quickly, but the complex and expensive machinery limited the accessibility and the use of the technology. Their challenge is not unique. Often companies buy expensive state-of-the-art equipment that promises to drive innovation, but then fail to integrate it into their workflows and efficiently use it.
The AMRC’s objective is to lead the way in how to integrate technology in ways that accelerate innovation, and they found a recipe for 3D printing that companies can replicate. Recently, the AMRC’s Design and Prototyping Group installed a new additive manufacturing station with a fleet of 12 Form 2 stereolithography (SLA) 3D printers that provides open access to 3D printing to hundreds of engineers working on diverse projects across the site.
“It has vastly streamlined our operations. [At any point in time], we have hundreds of projects live with hundreds of engineers. Now that staff has access to 3D printing, for every project that requires additive manufacturing, the time to produce components has been streamlined from probably around a week and a half to hours,” said Mark Cocking, the polymer additive technical lead at the Design and Prototyping Group at the AMRC.
Watch the video story to look inside the AMRC and learn from Cocking and engineers working across the research center about the various applications that 3D printing facilitates in a manufacturing environment.
Open Access 3D Printing to Empower Innovation and Shorten Lead Times
The AMRC Design and Prototyping Group works with researchers across the AMRC site to develop everything from conceptual designs to fully functional prototypes for a range of industries.
“Some of the parts that we create are just concept demonstrators but very often we also create jigs, fixtures, and other bespoke components that are fitted to machinery for different research programs,” Cocking said.
To fulfill the wide range of needs from nuclear to composites research, the facility is equipped with different bits of equipment including industrial laser cutting systems, CNC milling machines, CT scanners, and multiple metal laser sintering units, as well as fused deposition modeling (FDM) and SLA 3D printers.
Learn more about the three most established technologies for 3D printing plastics today, FDM, SLA, and selective laser sintering (SLS).
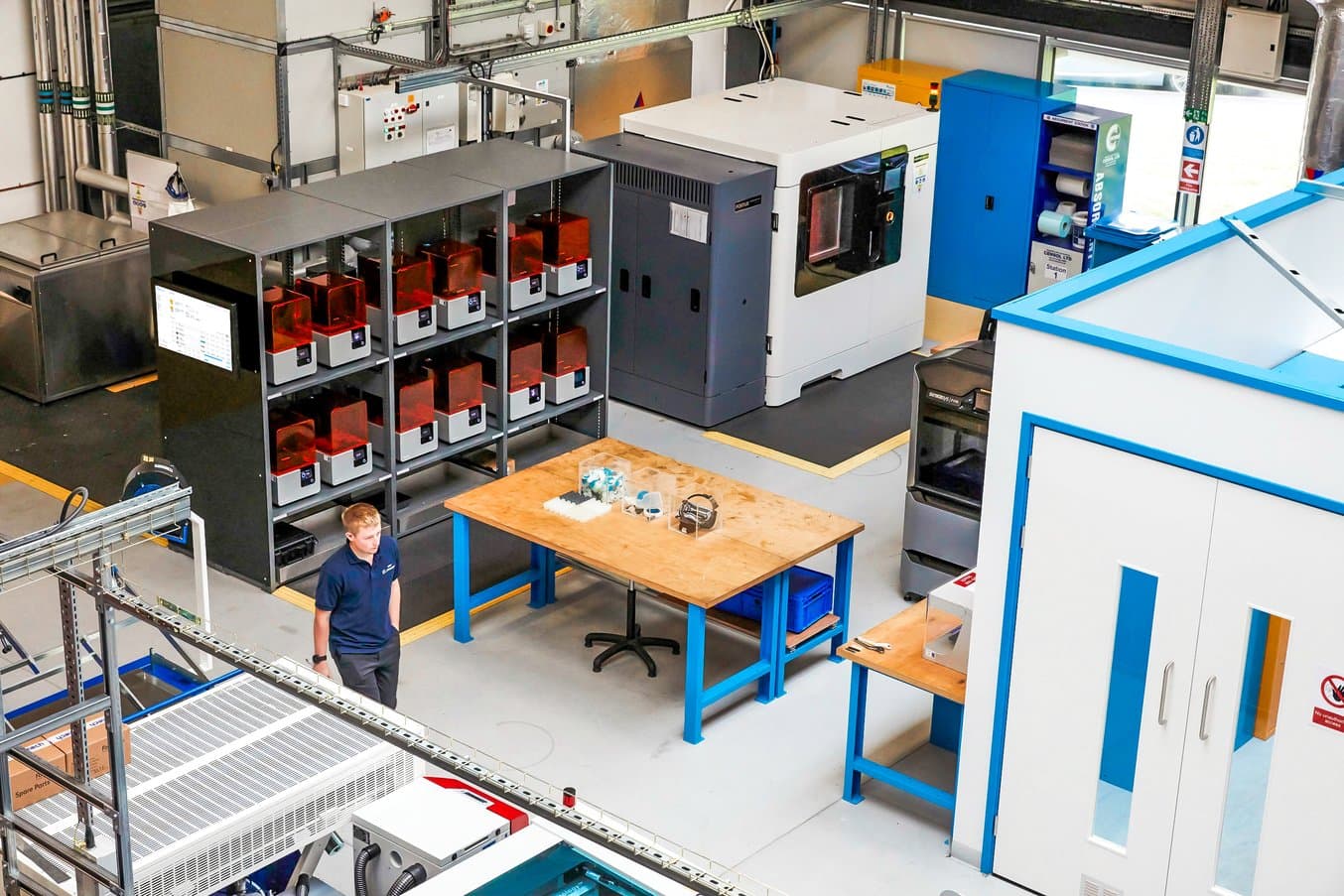
Previously, the center used a single industrial SLA 3D printer that only a couple of people were trained to use due to the complexity of the process. All jobs at the AMRC that required additive manufacturing would pass through these individuals, which slowed down the workflow and hindered innovation.
“It was far better for our site to open that knowledge up, to train many users and allow them to use the system and then increase their knowledge based on use. We found that if they have the opportunity to use the units, they're able to come up with more and more concepts for additive manufacturing components,” Cocking said.
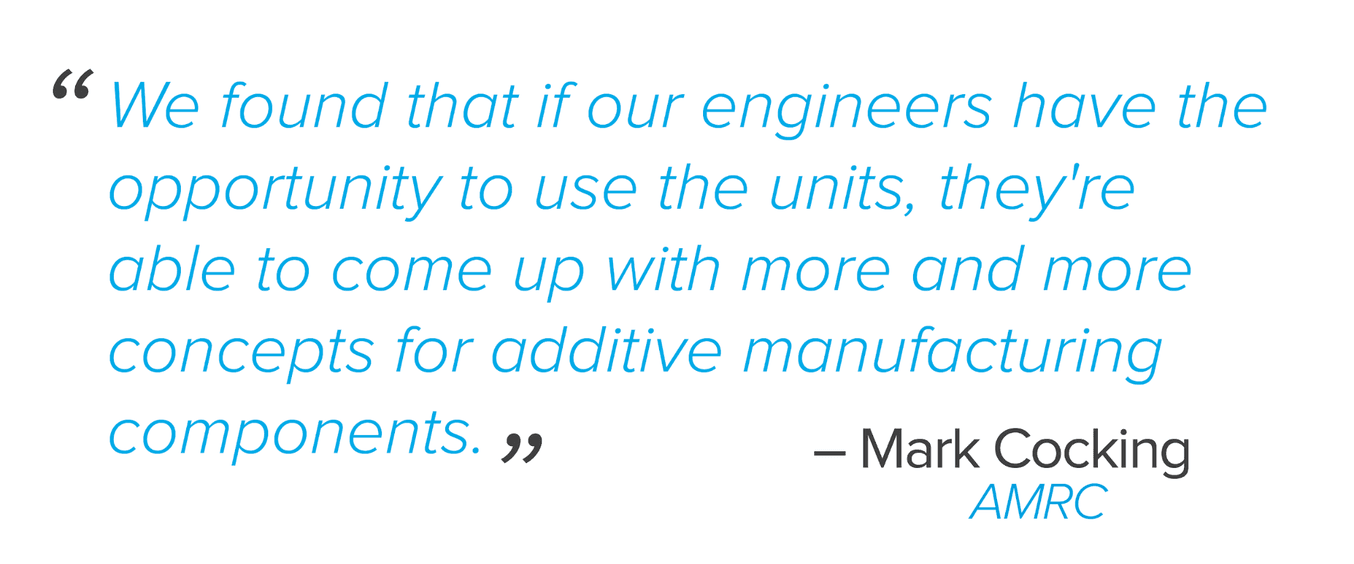
“Engineers no longer have to go through the procedure of paperwork to be able to turn an idea into a printed part; they can just come down here and do that straight away. It breaks down barriers in terms of internal concept development and there's more innovation that can take place. They can produce components within hours that can be on the meeting table for a partner the same day or maybe the next afternoon.”
How to Set Up and Operate a Print Farm for Hundreds of Engineers
The Design and Prototyping Group currently has 12 Form 2 3D printers set up in a station. Cocking arranged the printers on one side to provide easy access to all of the different resins and the prints, and set up a wet area on the other side with four Form Wash and four Form Cure units for cleaning and post-curing. There's a section on the side that has storage for build platforms, PPE, instructions, risk assessments, and also a buffer zone for prints that are passing through the system.
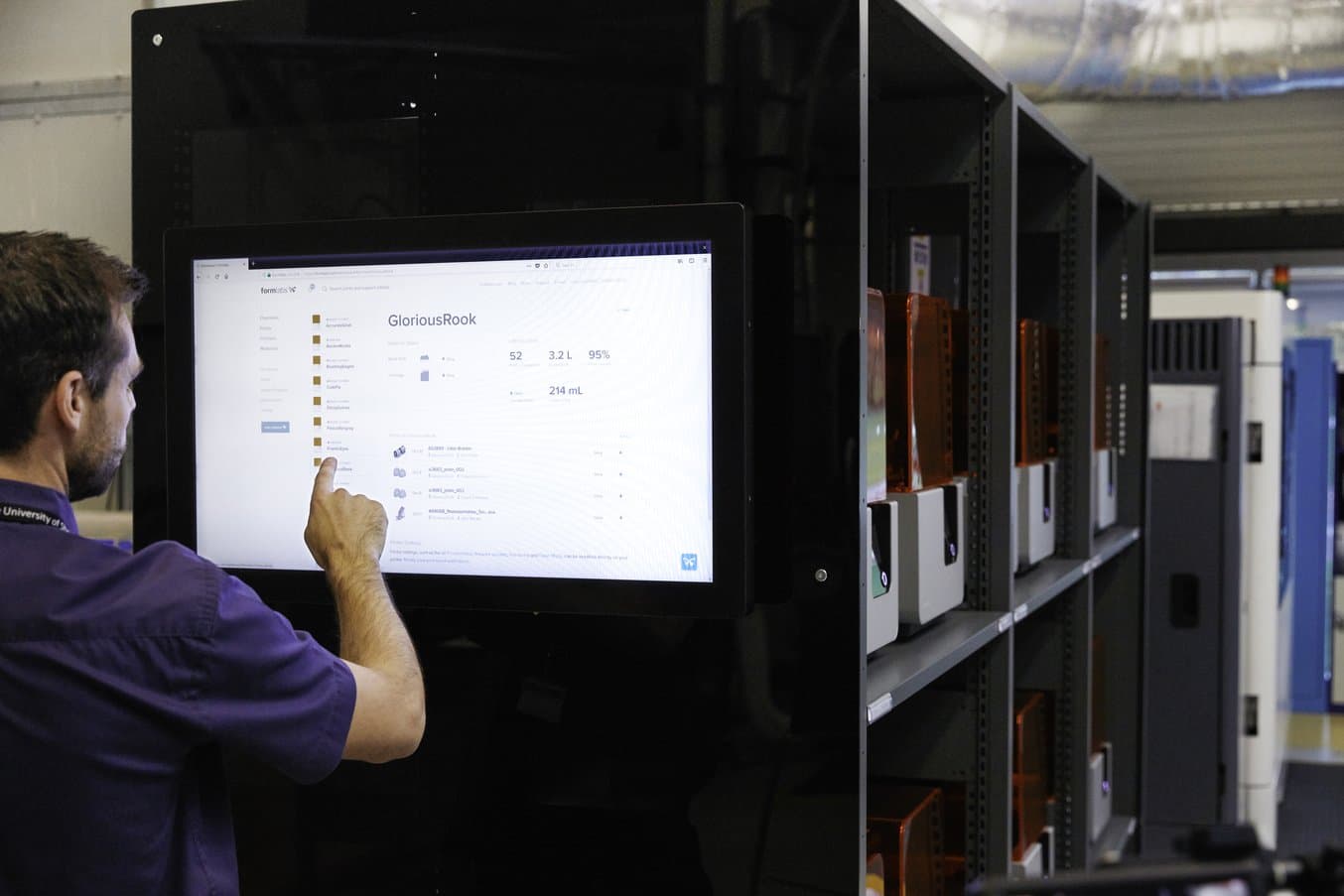
A single technician manages the area and looks after all of the printers. The technician interfaces with the 12 machines via a touchscreen on the side wall of the station that runs Formlabs’ Dashboard software and provides information on the status of prints and the material levels. When the staff comes to the center to use the machines, all they have to do is press the print button.
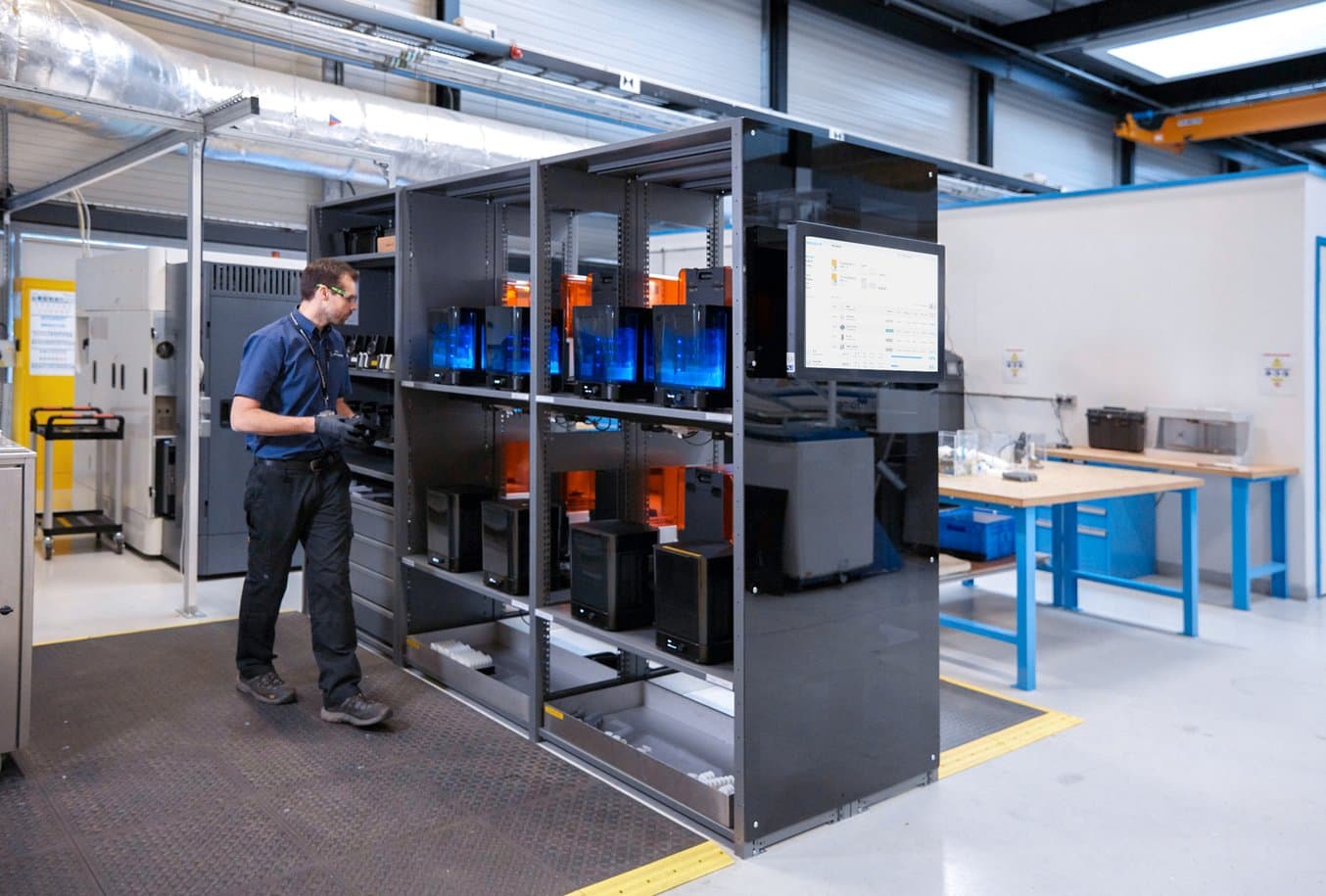
Staff members can sign up for a training course and come to the center to spend around 45 minutes to one hour going through the software and the printing process. By the end of that training, they will have started their first print job. After training, when the job is complete, they come back, take the build platform with the printed parts off the printer, pass it through the cleaning and post-curing system, use the post-processing station for support removal, and read the risk assessments. Once they're finished with that single print process, they are signed off to use the units whenever they like.
“I needed units that staff members can be easily trained on and be successful with so that they want to use them again. The Form 2 is the first small SLA machine that I've used where I thought, ‘yeah, this is a game changer.’ In terms of machinery, it's so simple to use,” Cocking said. “The software is very intuitive, engineers can pick it up very quickly. It's easy for them to understand and grasp the basics, and from there on, they can learn themselves and can push their additive experience themselves. Currently, we have just over 100 engineers trained to use the Form 2 bank.”
PreForm prepares 3D models for Formlabs 3D printers. Download and try the software now; no printer needed.
Knowledge sharing is mostly organic, through word of mouth. Engineers who start using the 3D printers take components back to their departments and use them on concept models, prototypes, or fit them onto machinery. Fellow engineers in their department learn how the parts were made, become interested, and inevitably, the center gets more and more requests for training.
A Variety of Applications Supported by 3D Printing Across the AMRC
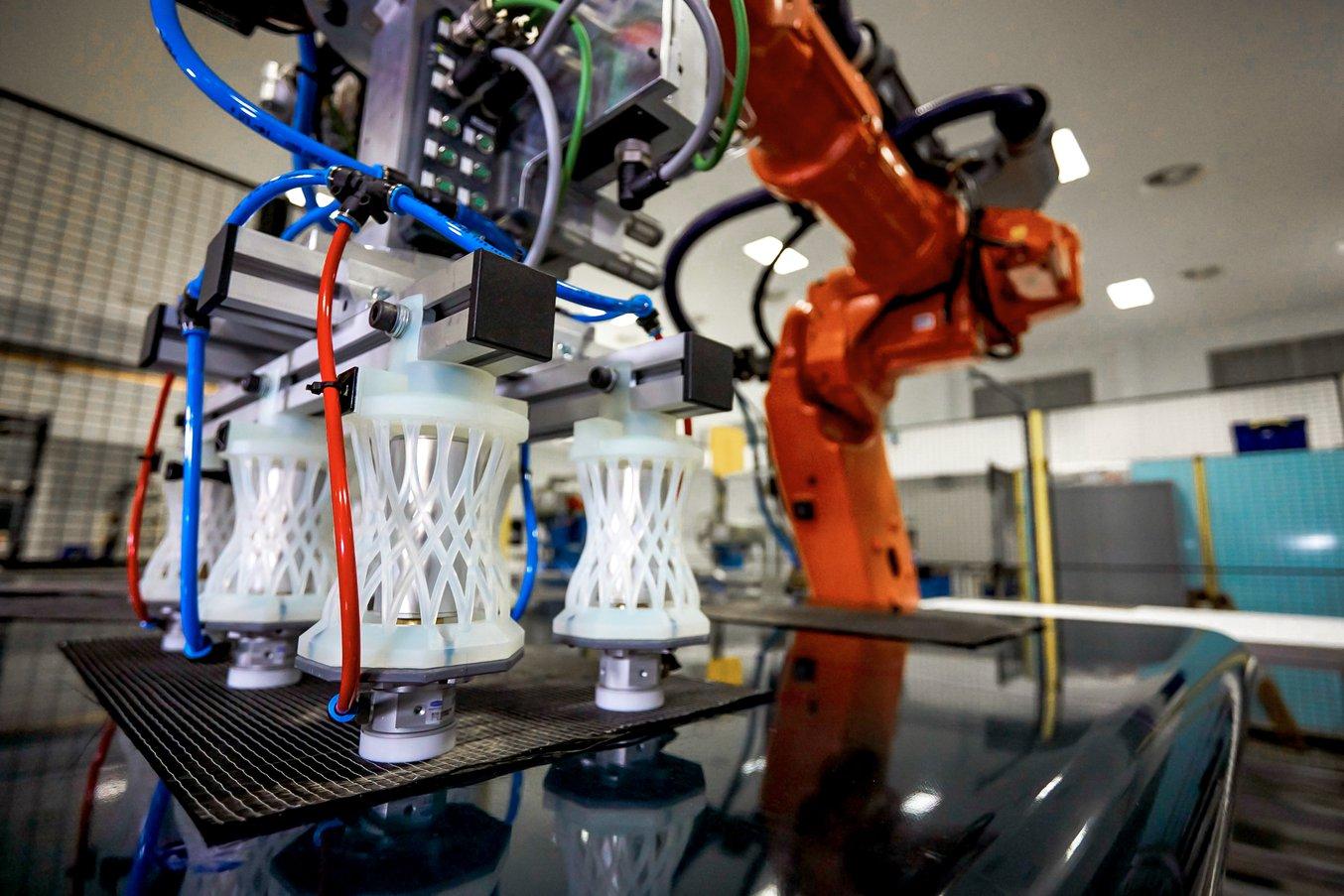
Since it’s been installed, the 3D printing station has supported dozens of research projects across the site.
Explore some of these applications in detail:
- Protective caps for drilling: The station of 3D printers produced 500 high-precision drilling caps that were critical to prevent cross-contamination during the drilling trials for Airbus, cutting the lead time from weeks to only two days.
- Robot gripper bracket: Researchers developed and printed highly intricate brackets that would be challenging to produce with any other production method for a pick and place robot that automates composites manufacturing.
- Temperature sensor bracket: In an autonomous welding project for the nuclear industry, researchers produced a dozen 3D printed parts like washers, brackets, and a sensor mounting system that needed to withstand the elevated temperatures in close proximity to the welding.
- Filament winding roller: Composites researchers created custom rollers for a filament winding machine that produces pipes, tubes, vessels, and shafts for the aerospace and for automotive industries.
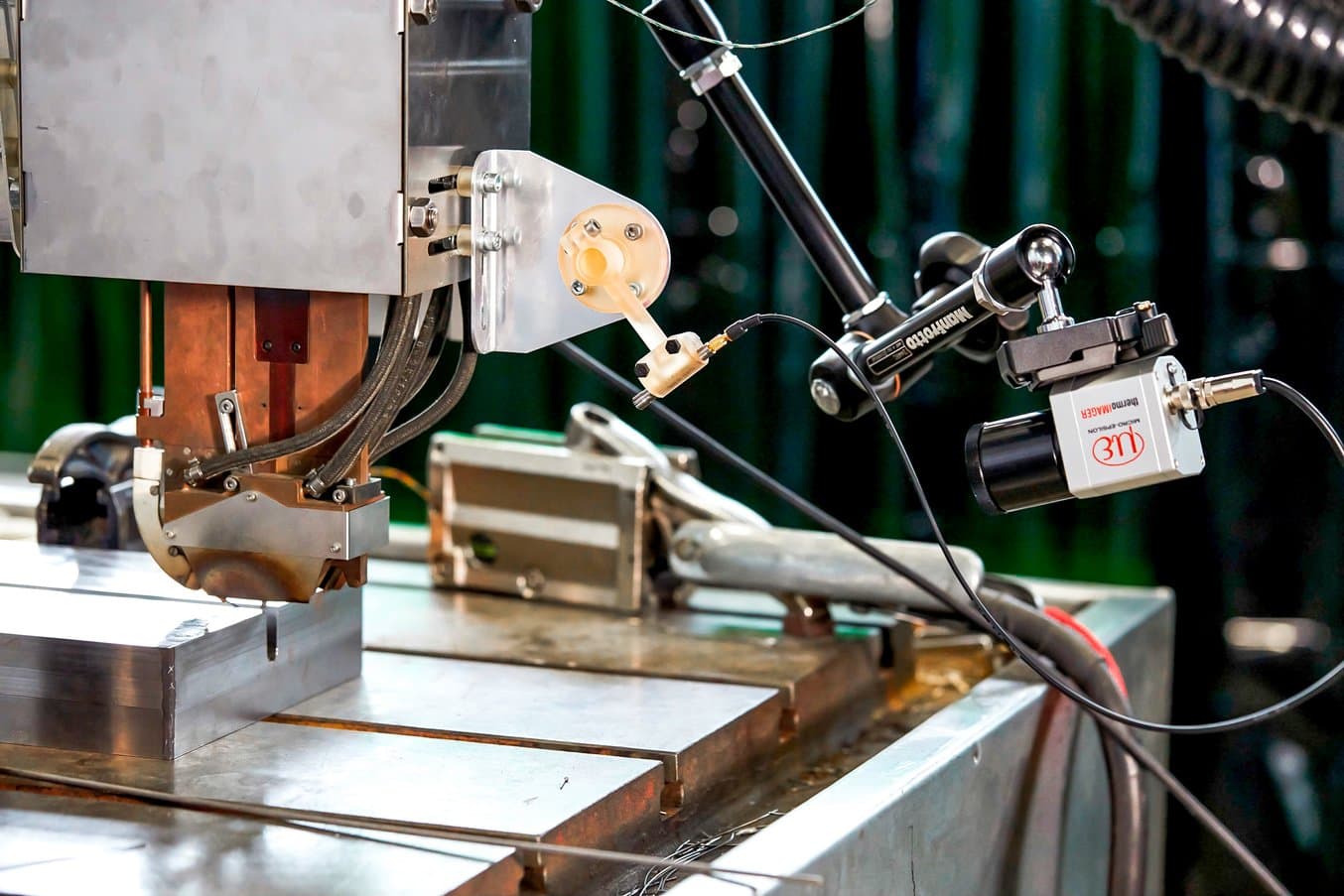
Using the 3D Printing Station’s Recipe at New Sites and Industrial Partners
Cocking and the Design and Prototyping Group is already planning to expand additive manufacturing capabilities at the AMRC.
“Some of our buildings are more remote, located further away from this main hub. We plan to use the model of this station, replicate it, and place satellite units in different buildings across the site so staff members have printers available right within their own department rather than having to make the journey down here,” Cocking said.
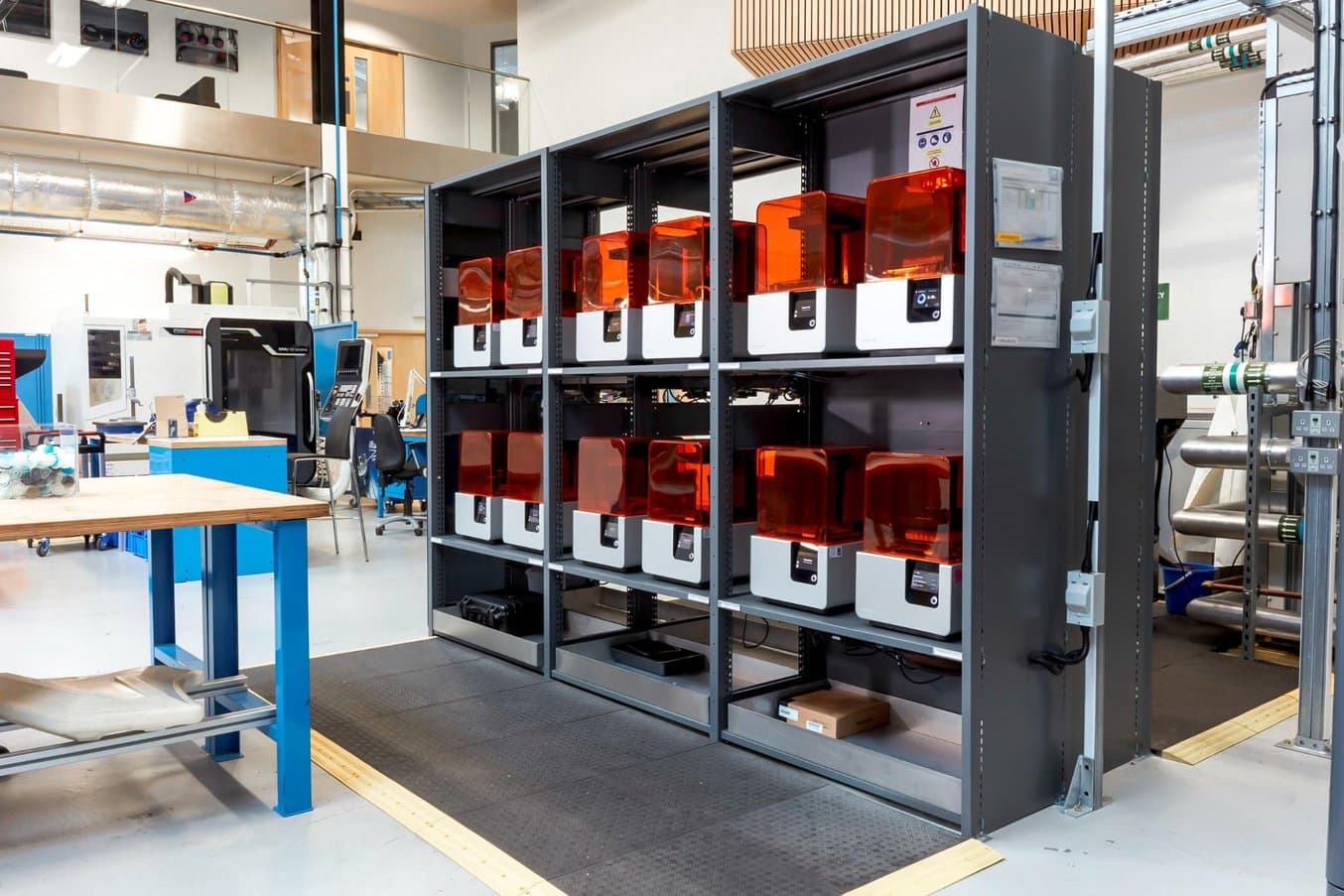
“Having worked in the industry for 12 years, I found that it would be highly beneficial for the industry to have additive manufacturing units on-site so their engineers have ease of access,” Cocking said.
“They could reduce turnaround time on custom components from weeks down to hours. Having ordered custom components myself, I understand the lead times and I understand the impact it can have on innovation, but also, ultimately, on the release date of a product. You can bring the release date of your product forward by months just by having access to additive manufacturing.”
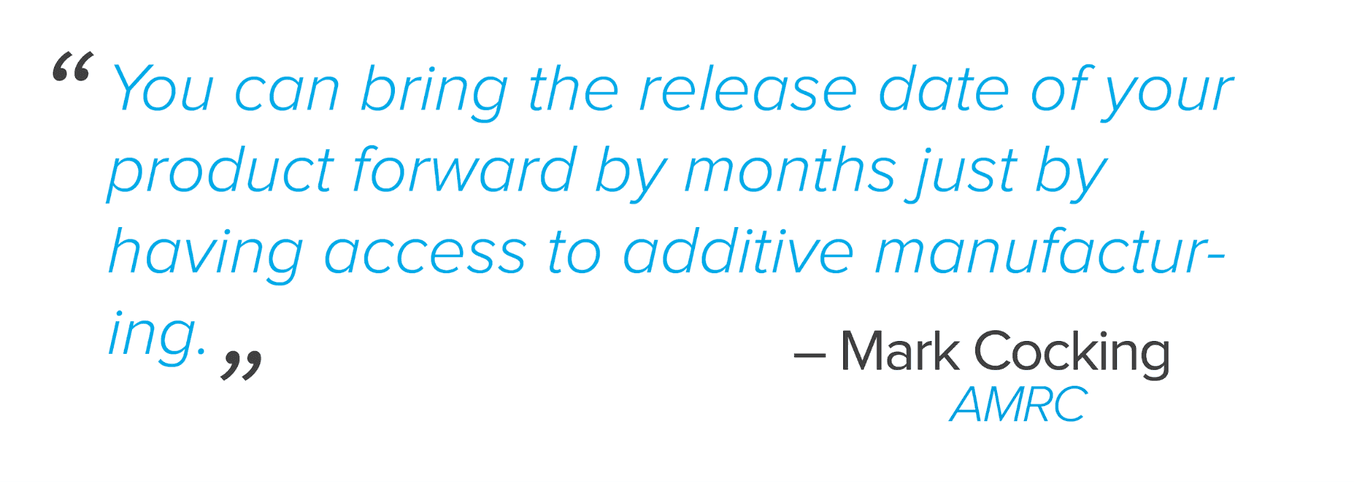
The AMRC’s industrial partners seem to agree, as the success of the open-access platform has also grabbed their attention.
“Some of our partners have become more interested in taking an exact replica of this station and introducing that into their own facility. They want something that's easy to use and something that they can scale. You can start off with 12 printers, but you can quite easily replicate that into many different stations as demand increases. Batch-quantity additive manufacturing is possible through multi-platform printers. It's possible right now, and at a good price point,” Cocking said.
Explore the Formlabs 3D Printers for Engineering and Manufacturing Applications
“What I'm seeing is a change from creating just small concept demonstrators to more and more final-use components being created. Right now we're printing many geometries that are undergoing the same tests as an injection-molded part would go,” Cocking said.
Different projects and challenges call for parts with various material properties. Engineers at the AMRC have a wide range of engineering resins at their disposal from high strength to elastic or temperature resistant material properties to solve complex problems and improve processes from prototyping to production.
Explore Formlabs latest SLA 3D printers, the Form 3 and the large format Form 3L, and Formlabs collection of engineering resins for your own project, or request a free sample 3D printed part to see materials firsthand.