Flexible 3D printing has traditionally been more complicated than 3D printing with rigid materials, but it’s becoming more common as 3D printer manufacturers make advances in both hardware development and materials science. The possibilities for 3D printed flexible parts are nearly limitless — flexible materials are required in almost every part of our daily lives, and 3D printing can open up new opportunities for customization and optimization within these applications.
The main plastic 3D printing technologies, fused deposition modeling (FDM), stereolithography (SLA) or resin 3D printing, and selective laser sintering (SLS) each offer flexible 3D printing materials. Due to the inherent differences in these technologies, some of these materials may be better suited for certain applications than others.
In the following article, we’ll cover the various types of flexible 3D printers, flexible 3D printing materials including flexible filaments, resins, and powders, and the advantages and disadvantages of each.
Comparison: Flexible 3D Printing Processes
FUSED DEPOSITION MODELING (FDM) | STEREOLITHOGRAPHY (SLA) | SELECTIVE LASER SINTERING (SLS) | |
---|---|---|---|
Resolution | ★★☆☆☆ | ★★★★★ | ★★★★☆ |
Accuracy | ★★★★☆ | ★★★★★ | ★★★★★ |
Surface Finish | ★★☆☆☆ | ★★★★★ | ★★★★☆ |
Throughput | ★★★☆☆ | ★★★★☆ | ★★★★★ |
Complex Designs | ★★★☆☆ | ★★★★☆ | ★★★★★ |
Ease of Use | ★★★★★ | ★★★★★ | ★★★★☆ |
Materials Available | TPU, TPC, TPA, TPE, Soft PLA | Flexible resins Biocompatible resins True silicone | TPU |
Shore Hardness | 60-100A | 40-90A | 90-95A |
Price | Budget FDM printers and 3D printer kits start at around $200. Professional desktop FDM printers range from $2,000 to $8,000, and industrial systems are available from $15,000. | Low-cost resin 3D printers are available for $200 to $1000, professional SLA 3D printers are in the $2,500 to $10,000 range, and large-format resin 3D printers are in the $5,000 to $25,000 range. | Benchtop industrial SLS 3D printers start just under $30,000 for the printer and $60,000 for the entire ecosystem, including powder management and cleaning stations. Traditional industrial SLS printers start at around $200,000. |
Advantages | Inexpensive consumer machines and materials | Accuracy Smooth surface finish Wide range of flexible materials Biocompatible materials available | Strong functional parts Design freedom No need for support structures Biocompatible materials available |
Disadvantages | Lower quality Parts are not isotropic Limited design freedom | Sensitive to long exposure to UV light | Rough surface finish Limited material options |
Applications | Basic prototyping | Functional prototyping Short-run, bridge, or custom manufacturing Rapid tooling (molds, patterns) Manufacturing aids (jigs, fixtures) Dental and medical applications | Functional prototyping Short-run, bridge, or custom manufacturing Manufacturing aids (jigs, fixtures) |
FDM 3D Printing With Flexible Filaments
FDM 3D printing, where a nozzle melts a spool of hard plastic filament and extrudes it through a nozzle to build the shape layer by layer, is perhaps the most well-known type of 3D printing due to its low entry-level price point and easy-to-grasp technology. There are many different types of FDM materials available, including several flexible filaments.
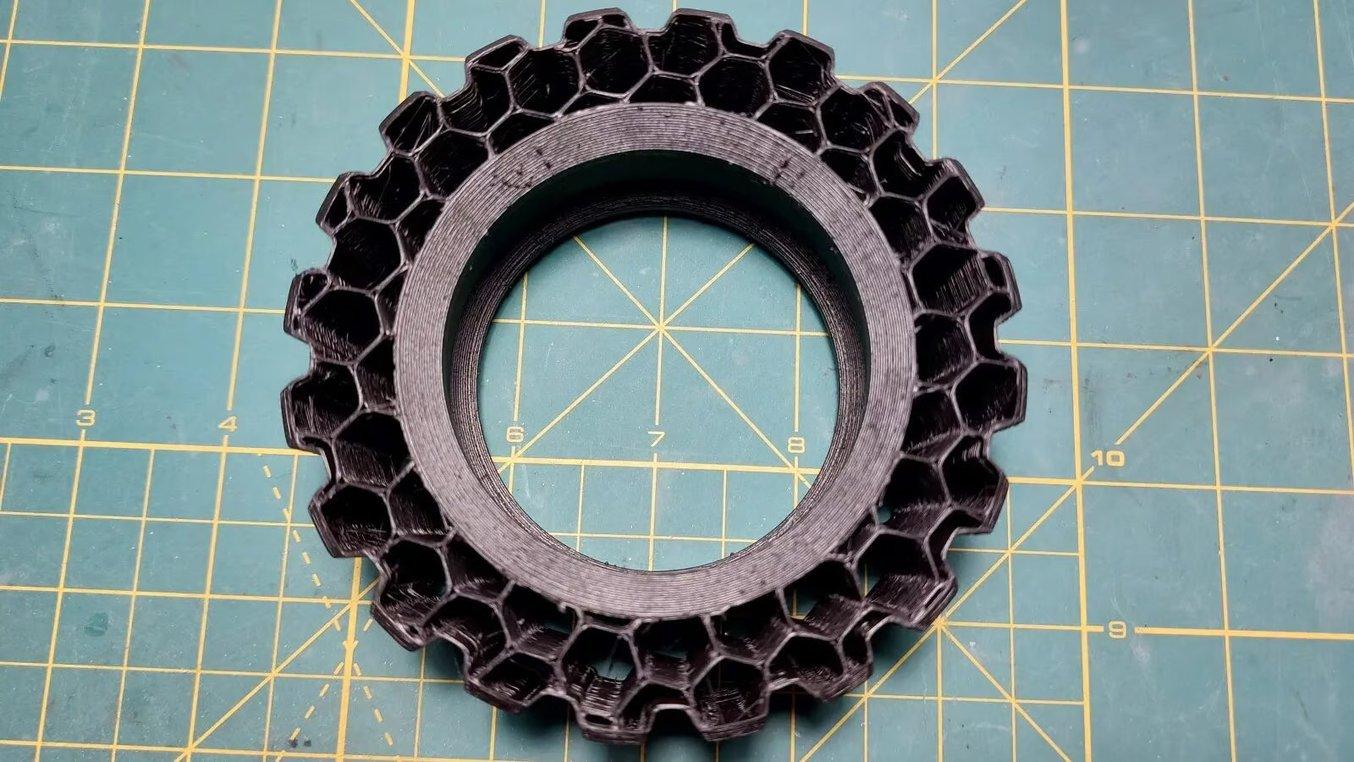
Flexible filaments for FDM 3D printers are good for early-stage prototypes and simple designs, but come with a few limitations. (Source: All3DP)
Pros and Cons of 3D Printing With Flexible Filaments
The benefits of FDM 3D printing with flexible filament are that you can easily and inexpensively produce simple flexible parts or prototypes. Flexible FDM 3D printed parts have good elasticity, impact resistance, vibration or shock absorption, and elongation. These qualities make FDM 3D printing flexible filaments ideal for early-stage prototypes of dampeners, actuators or end-of-arm tooling, soft casings, and stretchable enclosures.
However, because the flexible filament retains some of these stretchy properties even in its melted state during extrusion, there are often print quality issues when FDM 3D printing flexible materials. Design features such as overhangs and bridges often lead to issues like stringing, uneven surface finish, clogged extruders, and poor mechanical performance. Because FDM 3D printed parts are not chemically isotropic in the Z-axis direction, layers can separate during elongation. If the part’s purpose is to stretch and bounce back, that separation will often result in part failure.
Additionally, any jerkiness or accidental deviation from the programmed path of the extruder can negatively impact the way the flexible filament sets — these flexible filaments are more prone to poor adhesion than rigid filaments, so users should be aware that the printer has to to remain perfectly steady and the nozzle and extruder should move very slowly to give the flexible filament adequate time to extrude and set.
3D Printers for Flexible Filaments
Most FDM 3D printers are compatible with some type of flexible filament. A good practice to narrow the search for an FDM printer that is more suited to flexible materials is to look for one that is capable of heating the extruder up to around 220 °C and has a heated bed, a direct drive extruder (to minimize stringing), controllable feed rates (to modify the speed at which the flexible filament is extruded), and a cooling fan.
Compare Popular Flexible Filaments for FDM 3D Printing
Flexible 3D printing filaments can all be classified as thermoplastic elastomers (TPE) because they are altered by heat and display elastomeric properties, though TPE can also refer to a specific type of filament. The five most common flexible 3D printing filaments are:
TPU (thermoplastic polyurethane): TPU is one of the most common types of flexible filament. It is strong, can handle shocks and general wear and tear from use, and can come in various colors. Many products that may seem to be rubber are actually made from TPU. TPU is slightly more rigid than other thermoplastic elastomers, and is, therefore, the easiest flexible 3D printing filament to print with, as there is less chance of it stringing or oozing. FDM 3D printing with a flexible TPU filament is helpful in early-stage prototyping, but for functional prototypes and end-use parts, its anisotropic qualities can lead to inferior performance.
TPC (thermoplastic co-polyester): TPC is a polyester-based flexible 3D printing filament with good thermal stability and chemical resistance, but is less flexible than other TPEs. Some common examples of TPC parts are bumpers, flexible air-ducting, and softer casings, covers, and enclosures made to protect from compression or shock. When printing with TPC, it’s important to bring the material to an ambient temperature before loading the printer, use a direct-drive extruder, and make sure to have an extruder temperature capability of at least 230 °C.
TPA (thermoplastic polyamide): TPA is a chemical co-polymer of TPE and flexible nylon that is smooth and highly flexible. This combination of two commonly known flexible 3D printing materials leads to a filament that is smooth, soft, and flexible. TPA can withstand repeated shock or pressure, and is very durable. Parts that need to be repeatedly twisted, bent, or stretched can be printed in TPA — these properties make TPA ideal for functional prototypes, wearables, and engineering components. Most TPA filaments have a shore hardness of around 80A, which is similar to what you might often think of as rubber.
TPE (thermoplastic elastomer): As mentioned above, TPE can refer to the entire group of elastomeric thermoplastics, or a specific material. TPE filament is very elastic and soft, and is harder to print with than its more rigid counterpart, TPU. The TPE flexible filament is prone to oozing, or becoming overheated and unable to hold the nozzle shape, and should therefore be printed very slowly with a 3D printer that can easily and precisely control extruder temperature. TPE flexible filament is a good material choice for 3D printing wearables like wristbands or consumer goods like phone cases that can be stretched around the device.
Soft PLA: Soft PLA is a flexible filament made from organic fibers treated with chemicals. It can hold a rigid shape easily, but will return to its original shape after experiencing pressure. For this rigidity, it’s commonly used for items like tire prototypes or tough rubbery parts that need to maintain their shape and format the majority of the time. While soft PLA is one of the easiest flexible filaments to print with, it's more prone to jamming the extruder, and printing speed should be reduced.
Material | Shore Hardness | Elongation at Break | Ideal For |
---|---|---|---|
TPU filament | 60-98A | 300-600% | Prototyping of rubber-like parts |
TPC filament | 85-100A | 350-530% | Prototyping, tooling, harder flexible parts |
TPA filament | 70-95A | 350-500% | Soft and stretchy flexible parts and prototypes |
TPE filament | 70-95A | 150-900% | Soft and stretchy flexible parts and prototypes |
Soft PLA | 90-95A | 300% | Prototyping of rubber-like parts |
Resin 3D Printing With Flexible Materials
Resin 3D printers, such as stereolithography (SLA) 3D printers, use a laser or other light source to cure a liquid vat of plastic one layer at a time, and offer many options for flexible 3D printing materials.
Resin 3D printer manufacturers mostly manufacture their own materials — so they aren’t as easy to identify and group as FDM 3D printing flexible filaments. However, they all share similar characteristics and printing considerations, and can be used for a wide range of applications in many industries.
Pros and Cons of 3D Printing With Flexible Resins
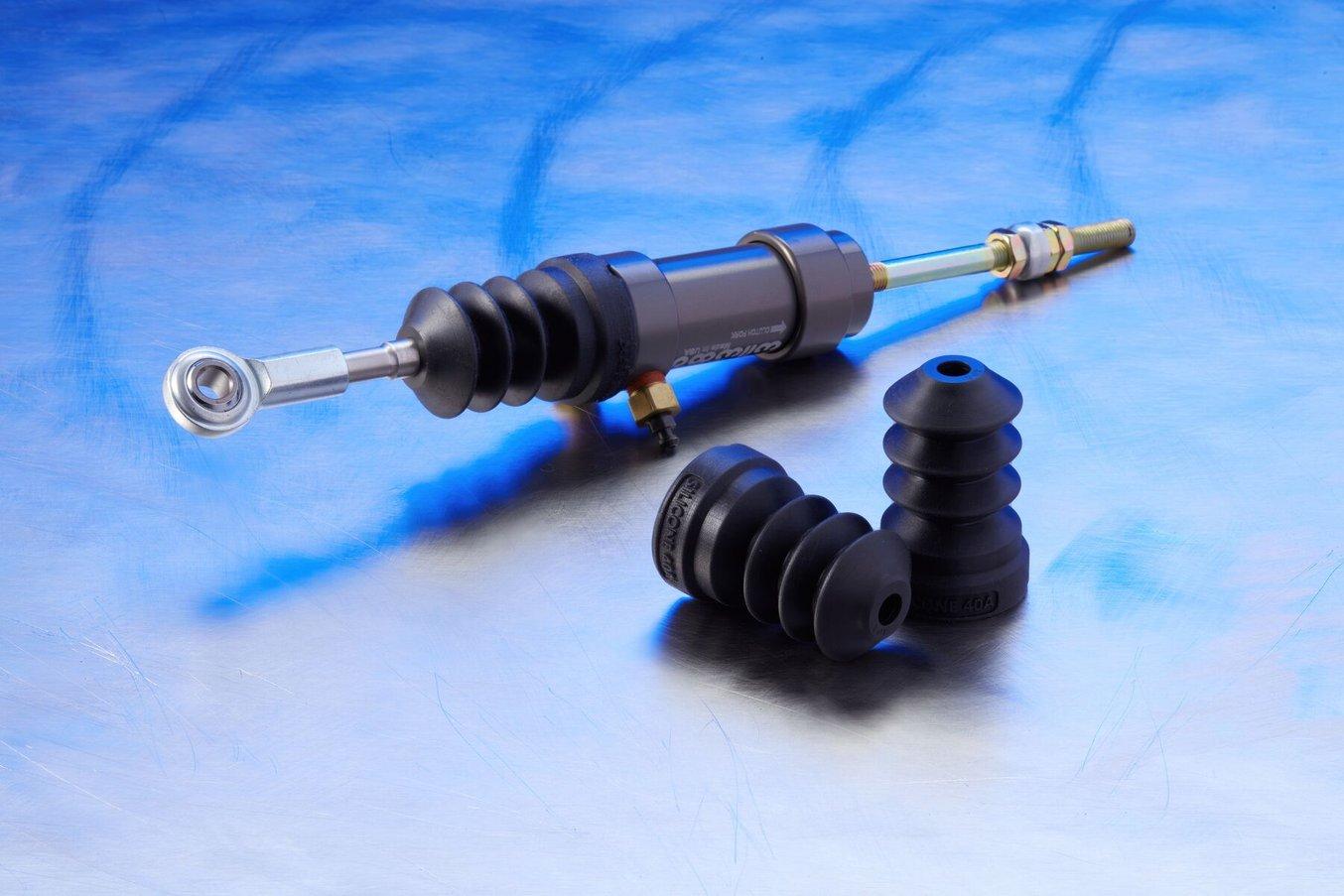
Formlabs Silicone 40A Resin is a 100% silicone material that is ideal for parts that will undergo repeated or prolonged compression, bending, or flexing.
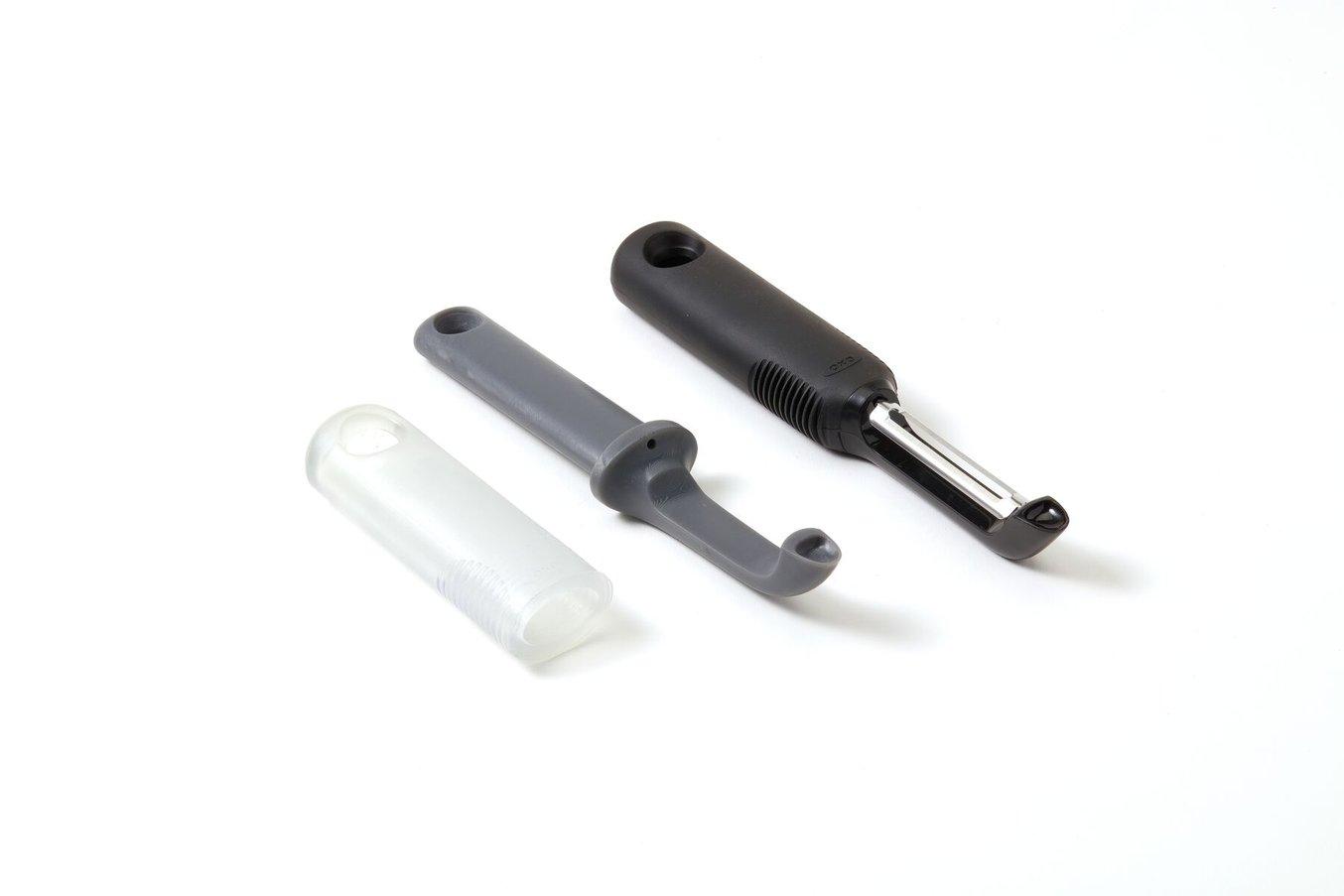
Formlabs' Flexible 80A Resin is a flexible material that works well for prototyping parts like grips or handles.
There are dozens of resins available, specifically designed by manufacturers for different applications. They range from soft durometer materials that closely resemble industrially molded silicone to harder durometer materials that are closer to hard rubber.
Because resin printers cure liquid plastics with a light source, the layers are chemically bonded to each other in all directions, meaning the parts have isotropic mechanical properties, and aren’t prone to shearing along the Z-axis like FDM parts are. Resin 3D printed parts are also waterproof and airtight, and can be relied upon for seals and gaskets in underwater robotic applications, fuel gauges, and other situations where parts like complex tubing needs to be printed.
The process also lends itself to smooth surface finishes, few or nearly invisible layer lines, and a high degree of accuracy and precision. Flexible 3D printing resins are ideal for applications like functional prototypes, end-use parts for bridge production or customization, and jigs, fixtures, and tooling parts that require tight tolerances.
A disadvantage of 3D printing with flexible resins is that printed parts are more sensitive to UV light and like other flexible 3D printing materials, they can be more difficult to work with than stiffer resins.
3D Printers For Flexible Resins
Material availability for resin 3D printing is highly dependent on the type of printer. Unlike with FDM 3D printing, where common types of plastic are available for different types of printers, SLA manufacturers often formulate and create their own, proprietary materials.
Formlabs offers the widest variety of flexible resins for its line of desktop and large-format resin 3D printers, including biocompatible materials that enable a range of applications in healthcare and medical device manufacturing. There are multiple types of resins spanning a range of shore hardnesses, and offering mechanical properties that can mimic popular plastics such as silicone or rubber.
Compare Formlabs Elastic and Flexible Resins
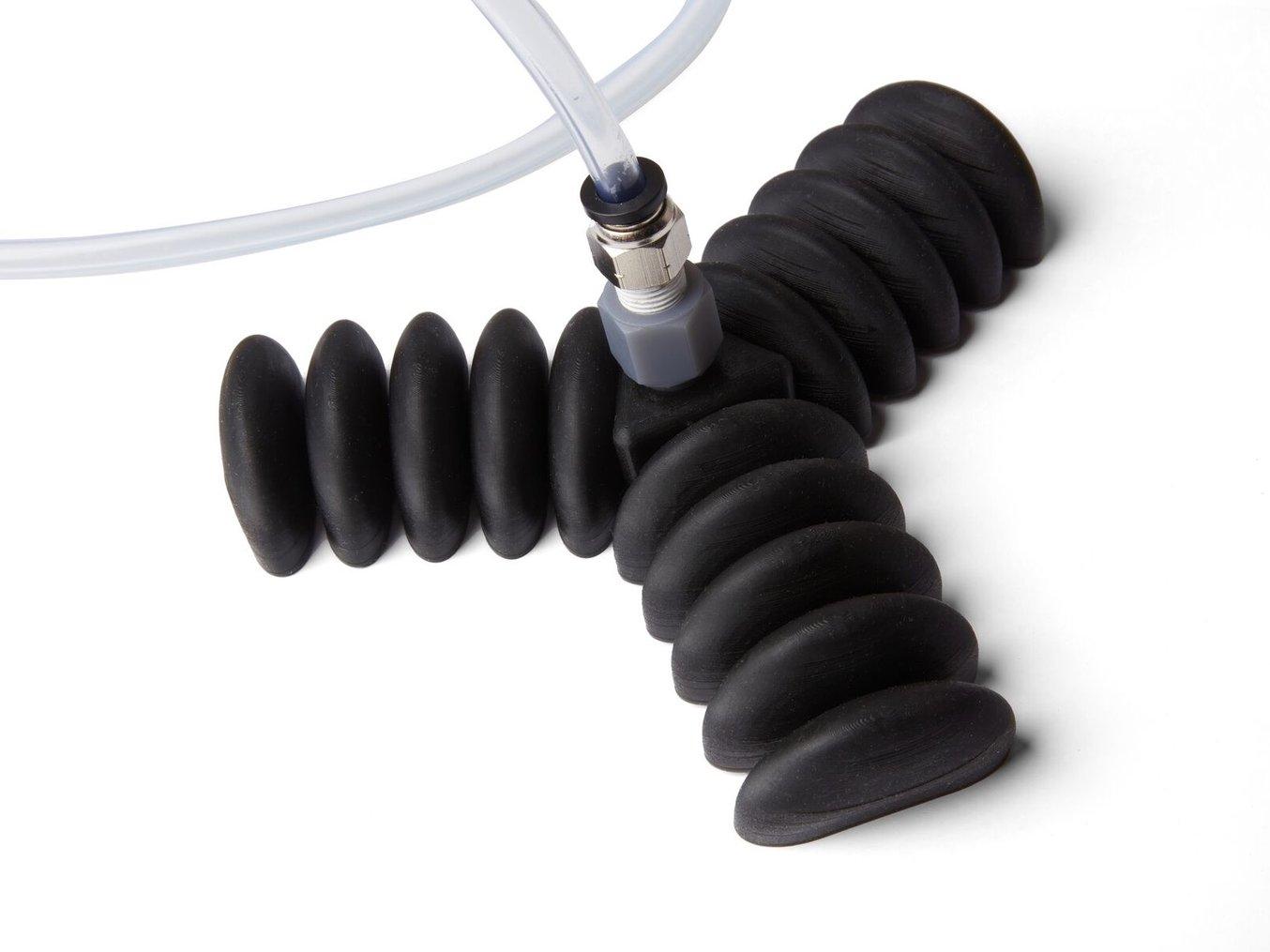
Silicone 40A Resin uses Formlabs’ patent-pending Pure Silicone Technology™ to 3D print pure silicone parts in-house, in a matter of hours.
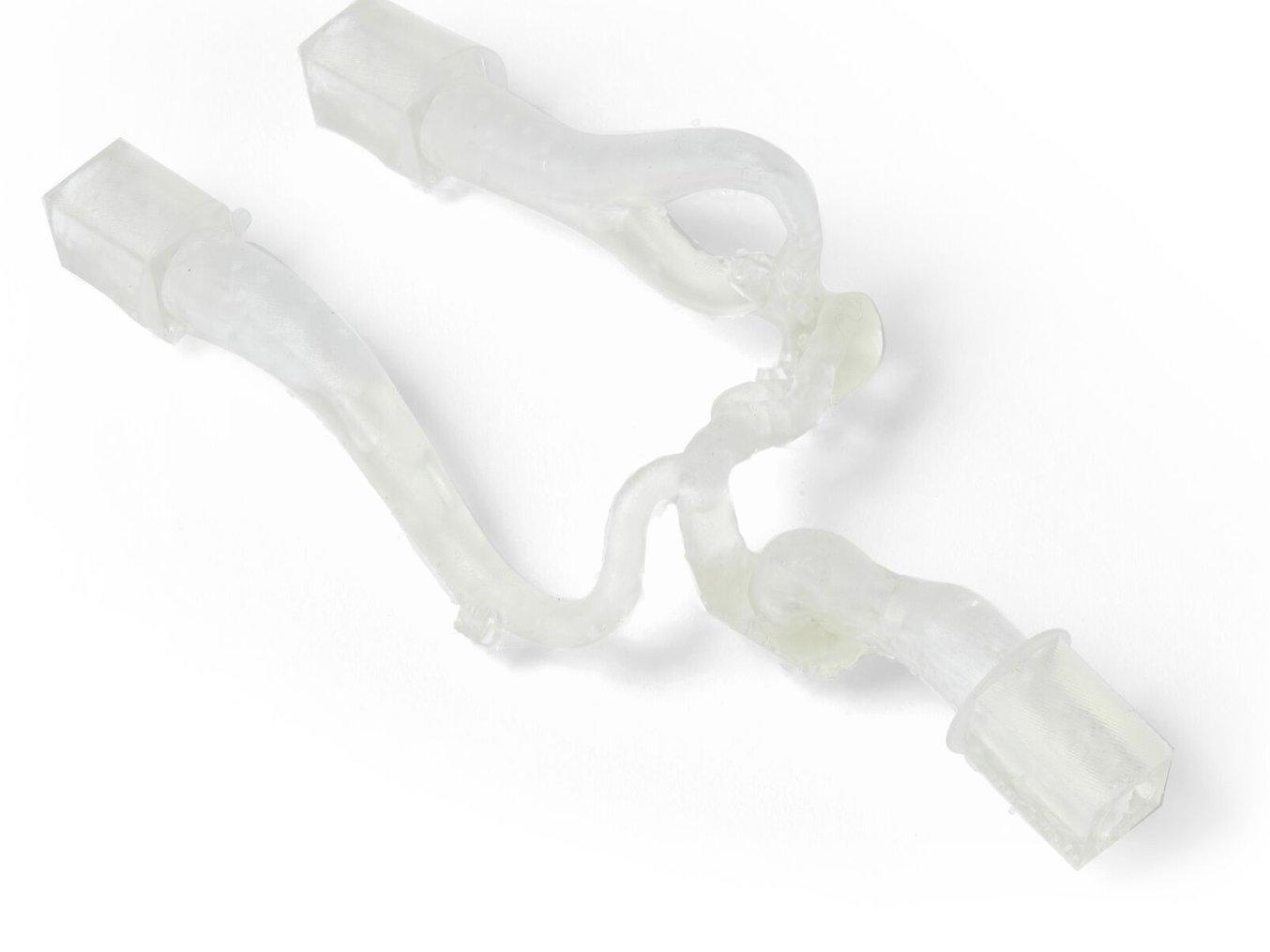
BioMed Elastic 50A Resin is a soft, elastic, medical-grade material for applications requiring comfort, biocompatibility, and transparency.
-
Silicone 40A Resin is the first accessible 100% pure silicone 3D printing material. With 40A Shore durometer, 230% elongation at break, and 12 kN/m tear strength, it is ideal for applications requiring pliability and durability even through repeated stretching, flexing, or compression. Parts made with Silicone 40A Resin have a rebound resilience of 34%, excellent chemical and thermal resistance (-25 °C to 125 °C), and can have fine features as small as 0.3 mm and complex shapes that are challenging to achieve with traditional manufacturing methods. Silicone 40A Resin is ideal for rapid prototyping, low-volume or custom manufacturing of indoor end-use parts, custom manufacturing aids and tooling, medical device components, patient-matched prosthetics, audiology applications, and complex geometry parts that are difficult to manufacture with traditional methods.
-
Elastic 50A Resin is a soft material that’s suitable for prototyping parts normally produced with silicone. This 50A Shore material is ideal for parts that will bend, stretch, compress, hold up to repeated cycles without tearing, and spring back quickly to their original shape. Choose Elastic 50A Resin for applications like wearables (straps), stretchable enclosures and casings, and compressible buttons.
-
Flexible 80A Resin is a stiff soft-touch material with an 80A Shore durometer to simulate the flexibility of hard silicones, as well as rubber or TPU. Balancing softness with strength, Flexible 80A Resin can withstand bending, flexing, and compression, even through repeated cycles. It is ideal for prototyping applications like handles, grips, overmolds, cushioning, damping, shock absorptions, seals, gaskets, and masks.
-
Rebound Resin is an 86A Shore elastic 3D printing material that offers unique properties for end-use applications. With five times the tear strength, three times the tensile strength, and two times the elongation of other production-grade elastomeric materials on the market, Rebound Resin is perfect for 3D printing springy, resilient parts. Rebound Resin’s high elongation makes it perfect for tactile, stretchy parts such as handles and grips. It is strong enough to handle constant compression or tension, which is ideal for manufacturing complex gaskets and seals that last.
-
BioMed Elastic 50A Resin and BioMed Flexible 80A Resin are flexible biocompatible materials that are ISO 10993 and USP Class VI tested and produced in an FDA-registered, ISO 13485-certified facility, ensuring that medical professionals can use these products with the utmost confidence. They're ideal for the direct 3D printing of elastomeric, biocompatible medical devices and models.
Material | Shore Hardness | Elongation at Break | Ideal For: |
---|---|---|---|
Formlabs Silicone 40A Resin | 40A | 230 % | Functional prototypes, validation units, small batches of silicone parts, customized medical devices, flexible fixtures, masking tools, and soft molds for casting urethane or resin |
Formlabs Elastic 50A Resin | 50A | 160 % | Prototyping of wearables (straps), stretchable enclosures and casings, and compressible buttons |
Formlabs BioMed Elastic 50A Resin | 50A | 150 % | Flexible and biocompatible applications such as study or practice operating modes of soft tissue, medical device prototyping and manufacturing of silicone-like parts |
Formlabs Flexible 80A Resin | 80A | 120 % | Prototyping of handles, grips, overmolds, cushioning, damping, shock absorptions, seals, gaskets, and masks |
Formlabs BioMed Flex 80A Resin | 80A | 135 % | Flexible and biocompatible applications such as study or practice operating models of cartilage or ligaments, medical device prototyping and manufacturing of rubber-like parts |
Formlabs Rebound Resin | 86A | 300 % | Specific applications, mid-sole shoe prototypes |
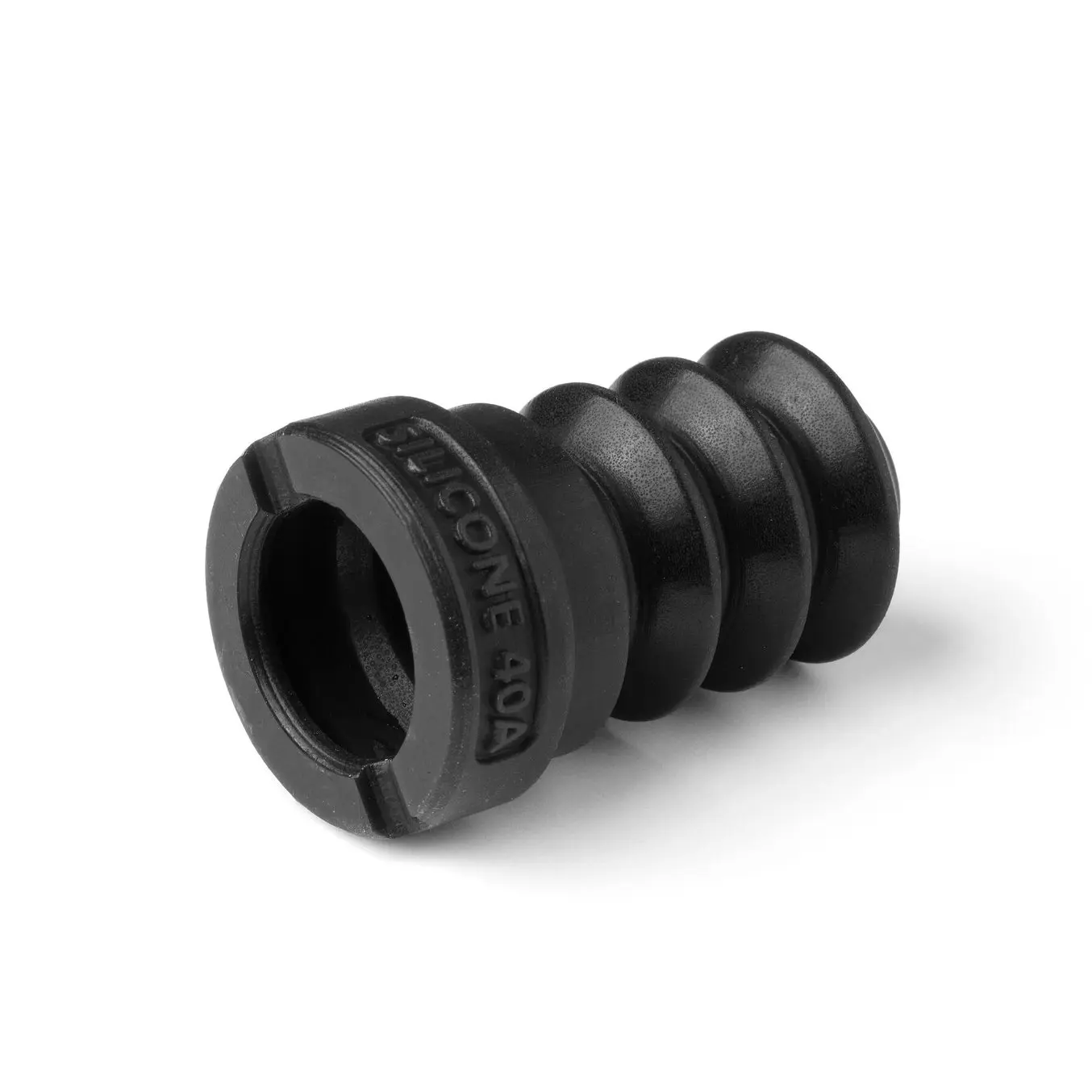
Request a Free Sample Part
See and feel Formlabs quality firsthand. We’ll ship a free flexible resin 3D printed sample part to your office.
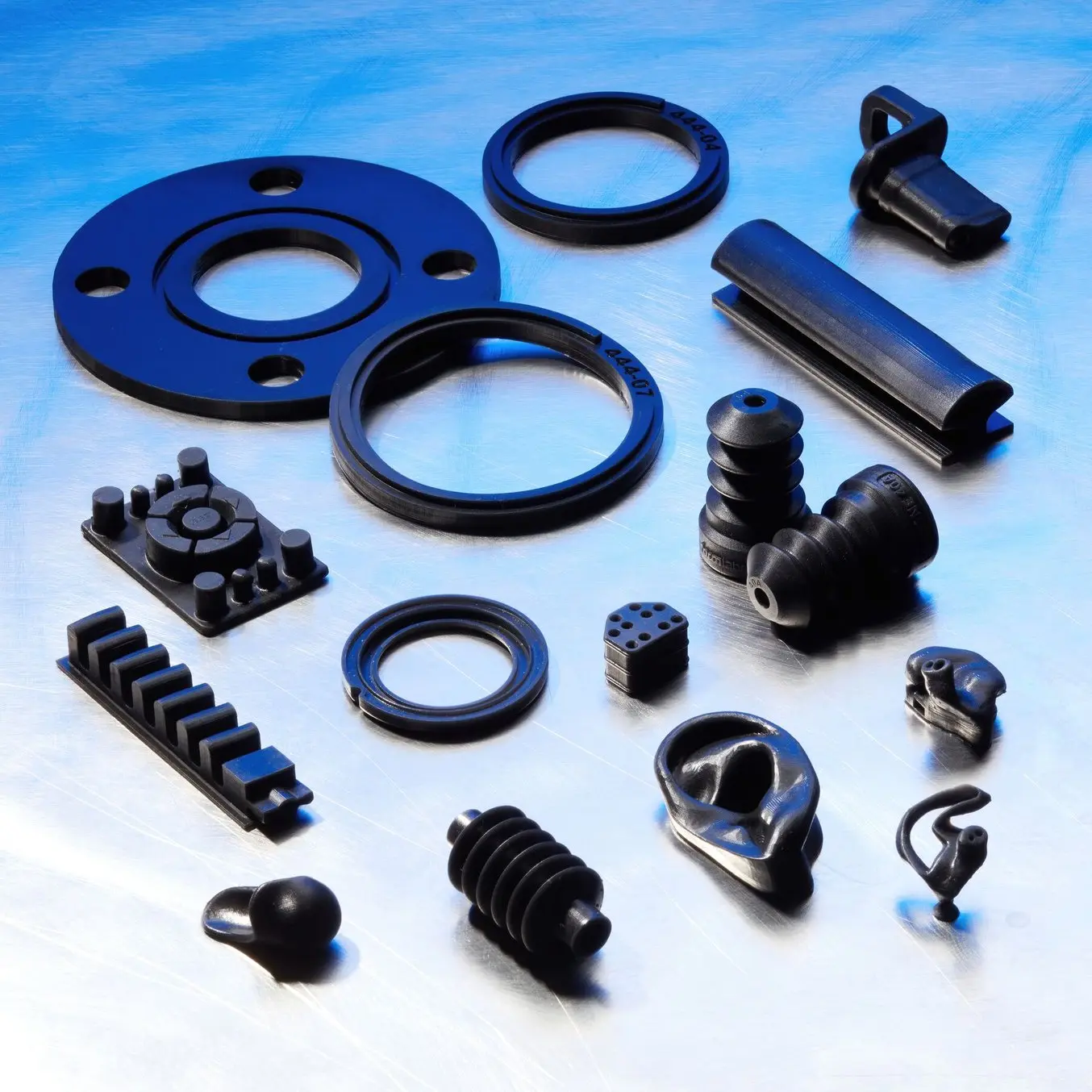
Introducing Silicone 40A Resin
In this webinar, our 3D printing experts walk you through the key benefits and applications of Silicone 40A Resin and present the material properties and the workflow for this resin.
SLS 3D Printing With Flexible Powders
Selective laser sintering (SLS) refers to the powder bed fusion 3D printing process where a laser fuses powder particles layer by layer. The unused material supports the parts during printing so you can create complex, interconnecting designs with no need for support structures. Much like with FDM 3D printing, SLS 3D printing manufacturers offer powders that are familiar and well-understood in the engineering world, such as nylon and TPU.
Pros and Cons of 3D Printing With Flexible Powders
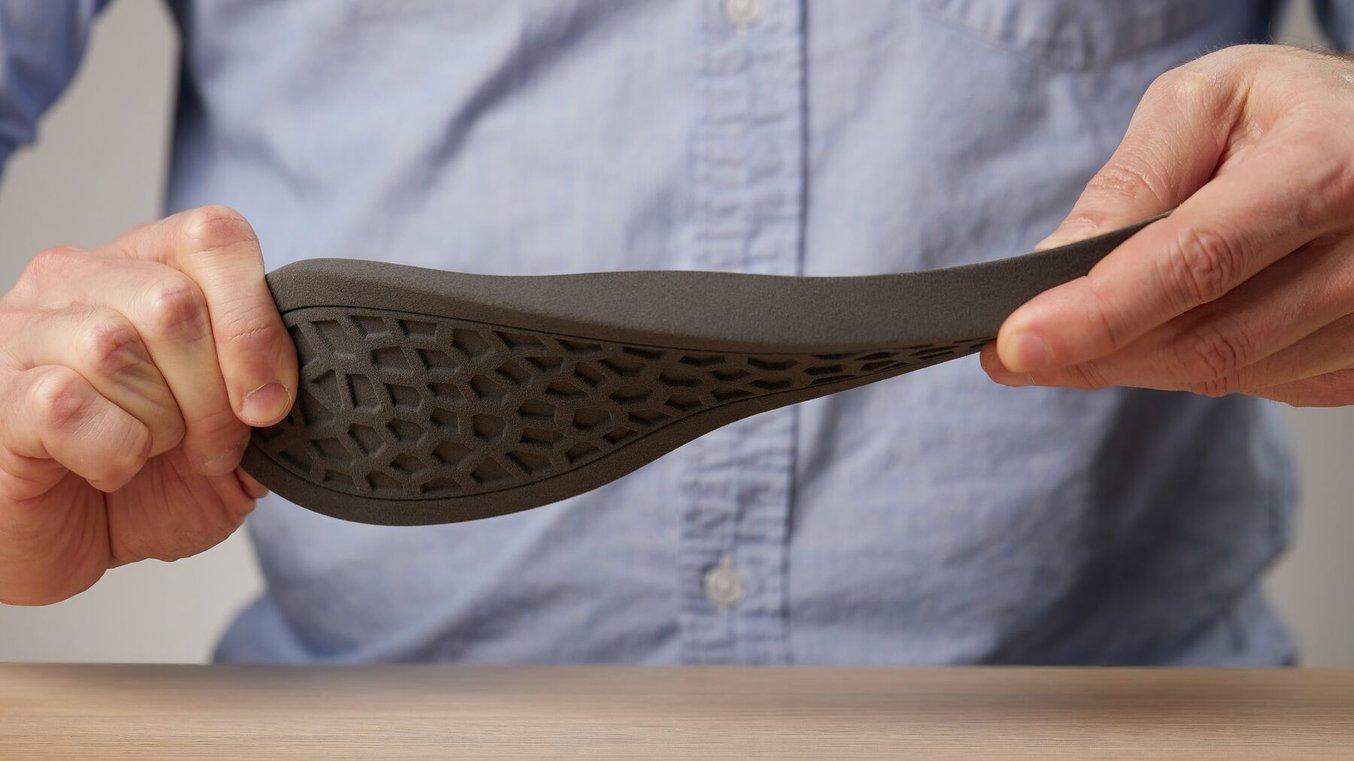
Shoe sole printed in TPU 90A Powder on the Fuse Series.
There are many advantages to printing with SLS powders for flexible, strong, and geometrically complex parts. The self-supporting nature of the powder bed makes it possible to print parts without supports, enabling quicker post-processing and the possibility of shapes that would be difficult to print with SLA or FDM technology. SLS ecosystems like the Fuse Series can recycle powder, leading to higher efficiency and lower cost per part.
Flexible SLS powders are strong, flexible, and extremely durable, opening up the possibility of end-use consumer goods or industrial-grade parts in industries like automotive, aerospace, or medical device manufacturing. SLS printing also creates parts that are mechanically bonded to each other within layers, so flexible SLS parts won’t tear along layer lines.
However, some of limitations of SLS 3D printing also extend to printing with flexible powders. SLS 3D printers are more limited in their ability to achieve very low Shore hardness materials, so the range of elasticity is smaller than traditional manufacturing. Printed parts also have a slightly rough surface finish, however, this can be easily improved using post-processing solutions.
3D Printers for Flexible SLS 3D Printing
Most SLS printer manufacturers offer a flexible material that is compatible with at least one model of their SLS technology. Not all manufacturers, however, offer the ability to switch between materials, or provide workflow considerations for doing so. Because many of the SLS powders on the market are some version of a type of nylon, switching between these is often possible, though not advised. However, switching between nylon types and TPU powders is often impossible.
The workflow of Formlabs' Fuse Series SLS 3D printers does allow switching between nylon powders and TPU 90A Powder after a thorough cleaning of the printer and accompanying post-processing unit. Trying new SLS powders doesn’t have to be impossible or exorbitantly expensive — with the Fuse Series and Fuse Sift, users can try printing with different flexible SLS powders, without having to purchase a completely new ecosystem.
Compare Formlabs Flexible SLS Powders
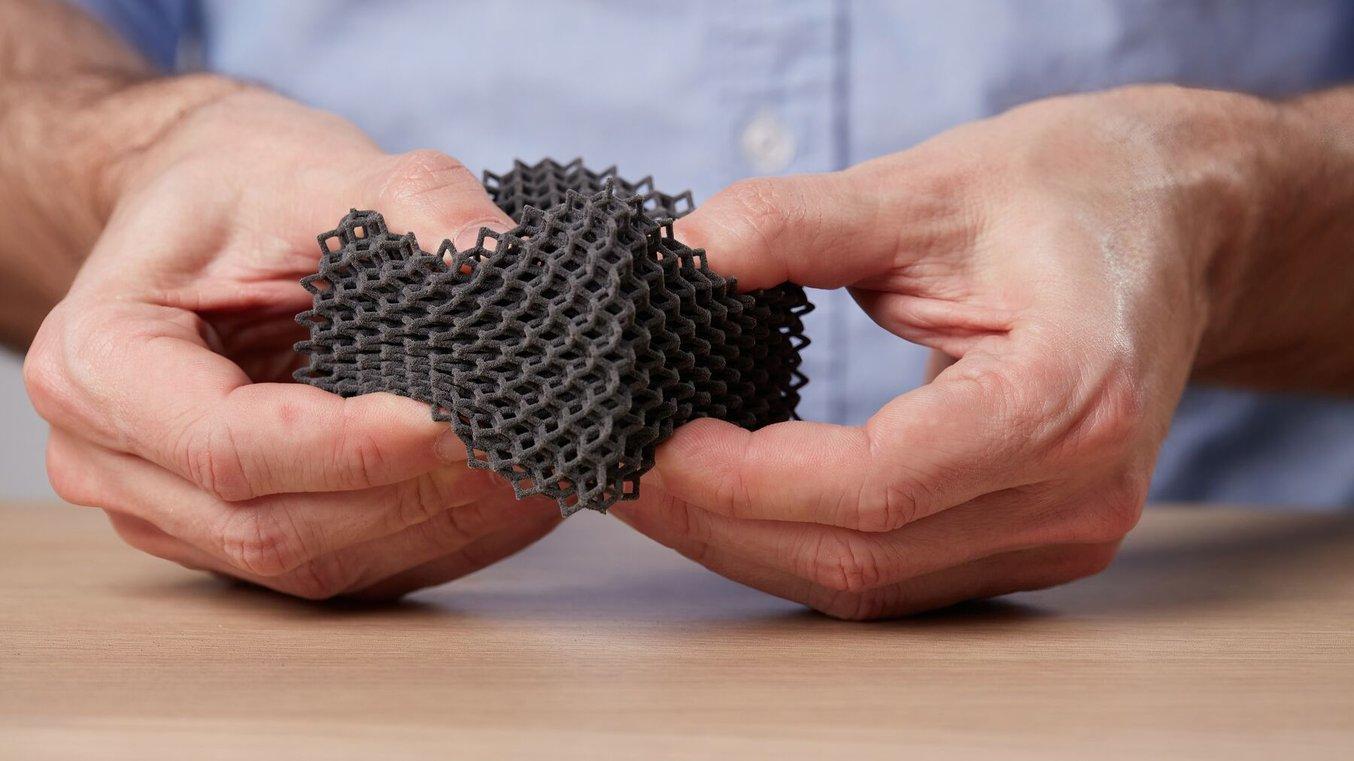
Latticed structure printed in TPU 90A Powder on the Fuse Series.
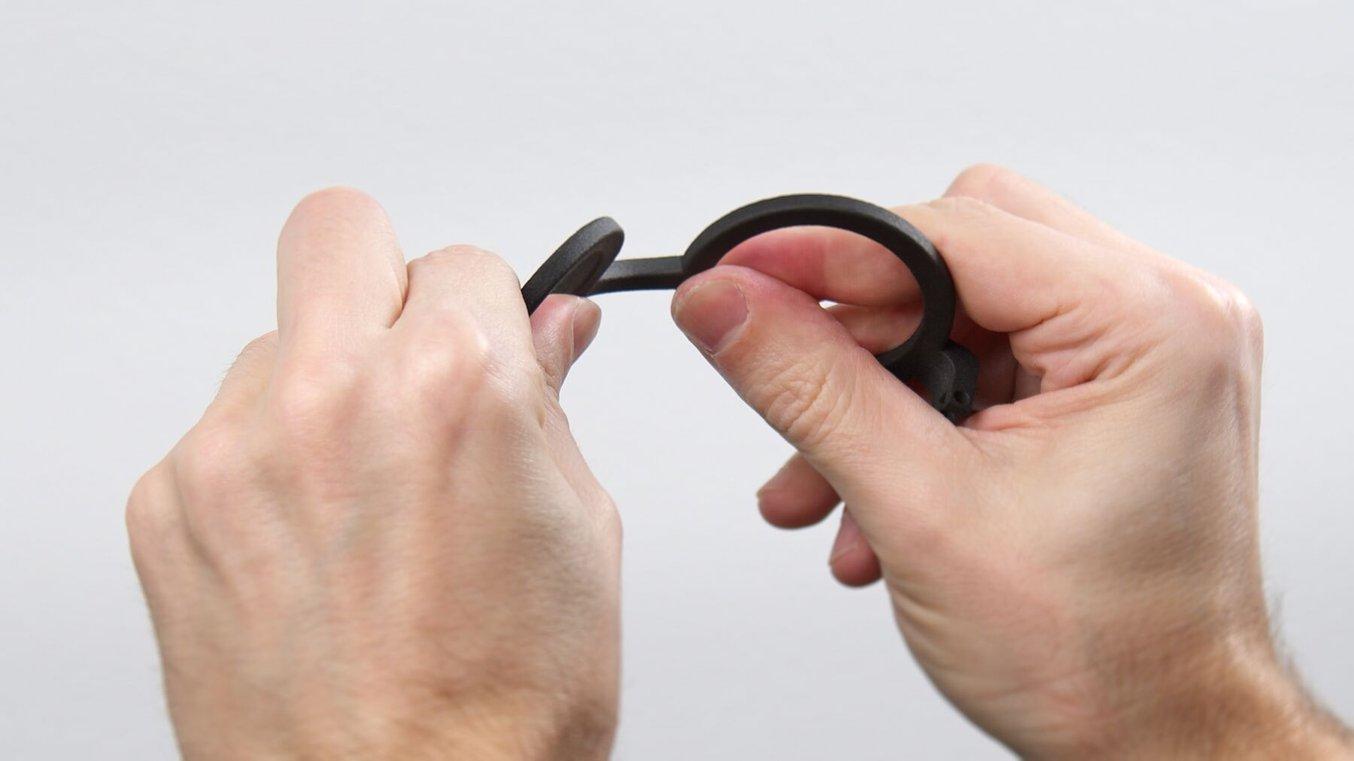
Flexible eyewear frames printed in Nylon 11 Powder on the Fuse Series.
SLS 3D printing offers many of the same flexible materials as FDM printing. The most common in flexible SLS powder is TPU, but TPA, TPC, TPE are all available in powder form, though not for every manufacturer’s system. In addition to these elastomeric powders, more rigid materials like nylon 11 can also bend and return to their original form when printed in thin shapes.
Material | Shore Hardness | Elongation at Break | Ideal For: |
---|---|---|---|
Formlabs TPU 90A Powder | 90A | 310 % (XY) 110% (Z) | Wearables, orthotics, prosthetics, gaskets, seals, masks, belts, plugs, tubes, padding, dampers |
Formlabs Nylon 11 Powder | n/a | 40 % | Thin-walled consumer products, automotive components, orthotics, prosthetics |
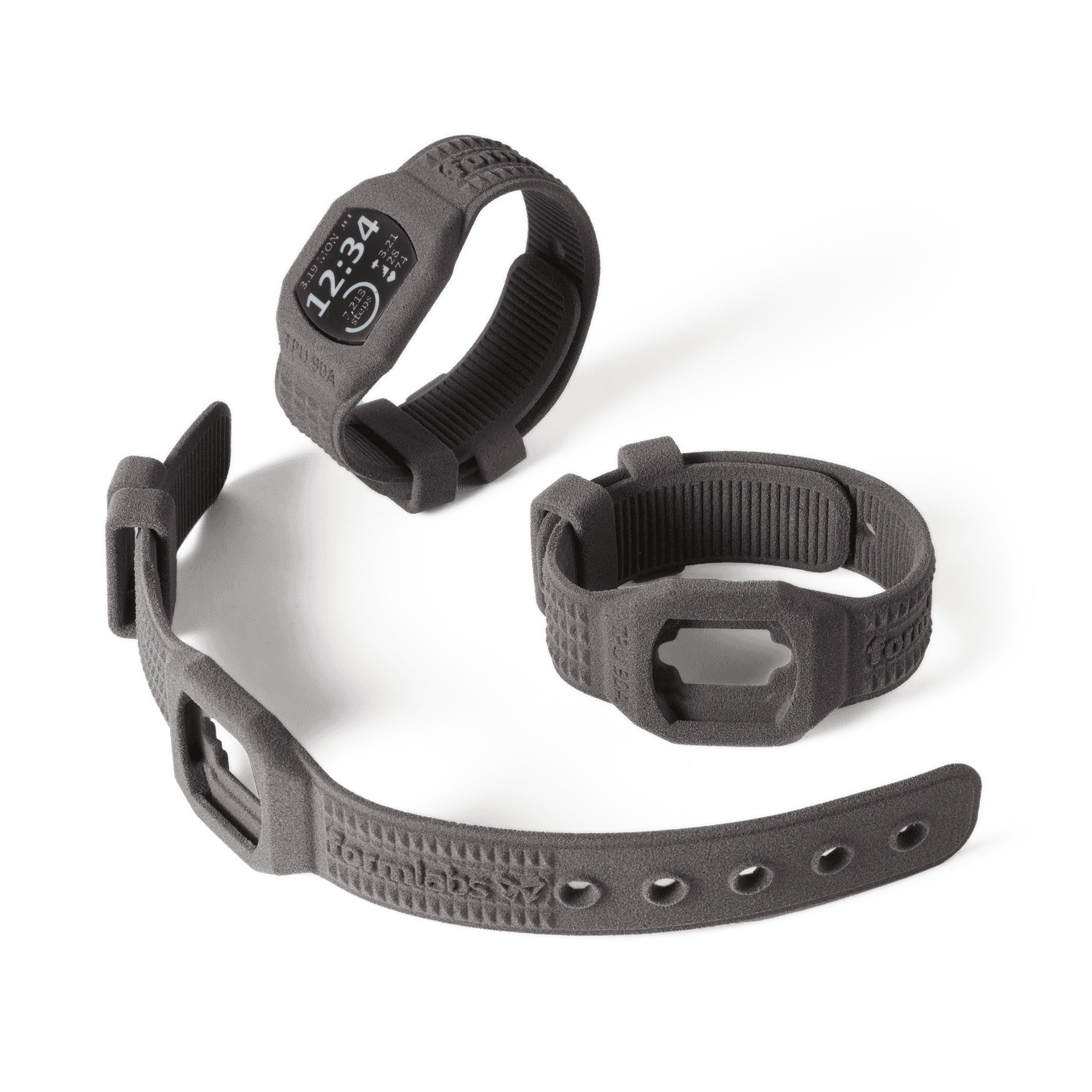
Request a Free SLS Sample Part
See and feel Formlabs quality firsthand. We’ll ship a free flexible SLS sample part printed on the Fuse 1+ 30W to your office.
Get Started With Flexible 3D Printing
One of the advantages to additive manufacturing is the ability to choose a material for your specific application — there are so many different filaments, resins, and powders available. For flexible 3D printed parts that behave like traditionally fabricated rubbers, silicones, or thermoplastic elastomers, there are multiple technologies, manufacturers, and materials to choose from.
The Formlabs SLA ecosystem makes flexible resin 3D printing easy and intuitive through the combination of reliable hardware and specialized, advanced materials developed for targeted applications and industries. There are a wide range of flexible materials available for the Form 3/B/+ and Form 3L/3BL ecosystems — including biocompatible materials that enable new applications in healthcare and medical device manufacturing. The post-processing steps are also handled cleanly and simply by automated post-processing solutions, making flexible resin 3D printing easy and clean.
SLS 3D printing technology is ideally suited to both functional prototyping and production workflows. Before the Fuse Series however, there were few accessible options for either small and medium businesses or for scaling SLS ecosystems. With materials purpose-built for flexible, rubber-like printing, such as TPU 90A Powder, as well as powders that can be designed for flexibility, such as Nylon 11 Powder, there are multiple options available to SLS 3D print flexible parts.
Flexible 3D printed parts unlock possibilities in new industries, whether they’re printed in flexible filaments, resins, or powders. 3D printing can help engineers, designers, manufacturers, and healthcare professionals reduce costs, improve their products, and increase efficiency in their workflows. For parts that have not been possible until now, such as flexible gaskets, seals, bumpers, tubing, or others, systems like the Fuse Series SLS or Form Series SLA printers are now possible solutions. Request a free flexible SLA or SLS printed sample part or talk to an expert to discuss your application and requirements.