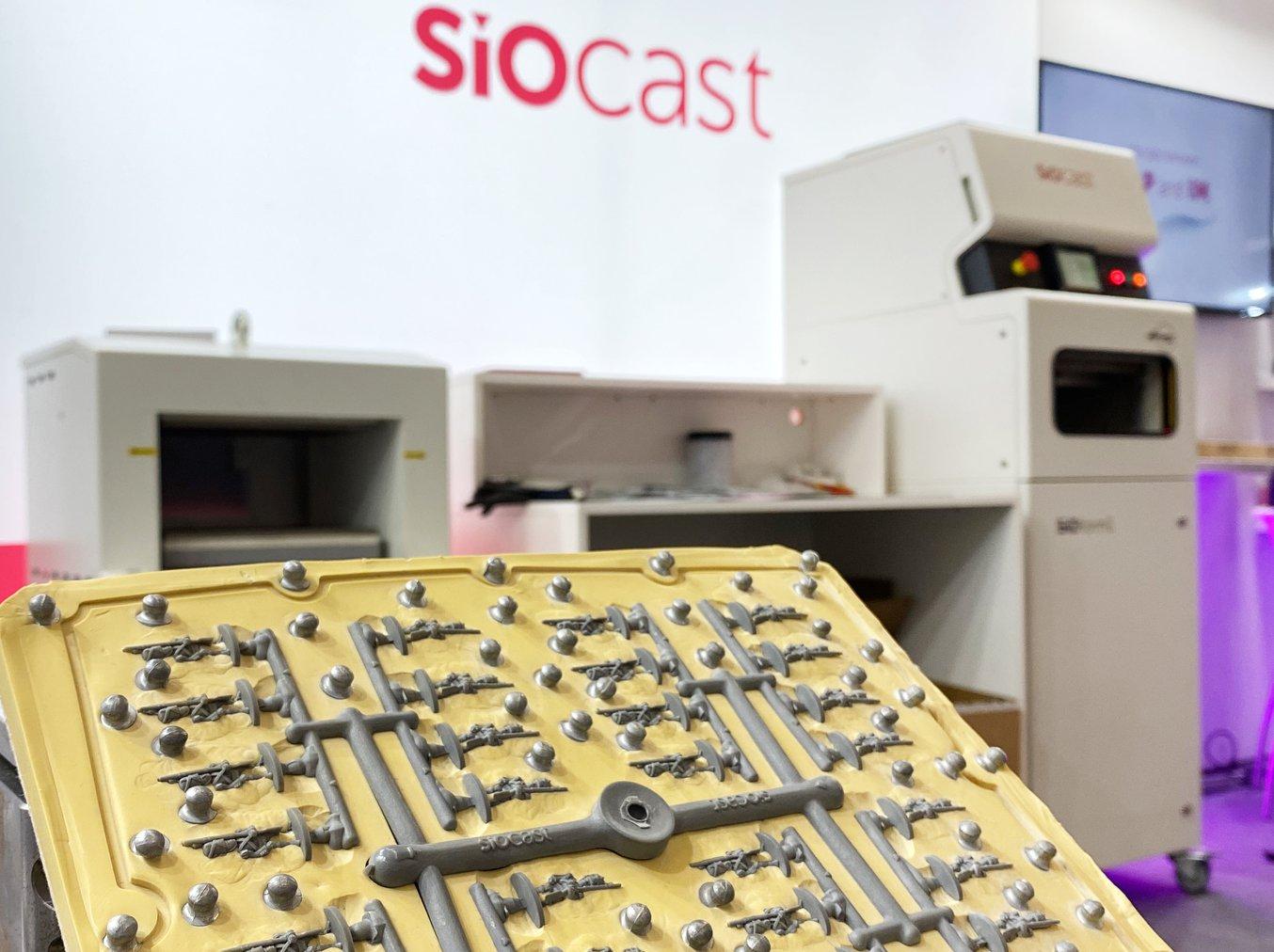
SiOCAST is set to shape the future of miniatures manufacturing by supplying their own agile production system, machinery, and materials to make high-quality non-toxic parts in-house at a reasonable price.
Using 3D printed masters to make silicone molds for a unique process that combines the benefits of 3D printing, silicone molding, and injection molding, SiOCAST’s technology has already been adopted widely, from small studios to the biggest miniatures manufacturers in the industry, such as Monster Fight Club (The Witcher, Cyberpunk RED), Reaper Miniatures (Bones), and Warlord Games (Blood Red Skies, Bolt Action).
In this article, Ferran Navarro, CEO and Co-Founder of SiOCAST, navigates us through their miniature and small part thermoplastic making technology, called the Alemany System, and how they use Formlabs 3D printers in their process.
SiOCAST’s New Technology Bridges the Gap Between 3D Printing and Injection Molding
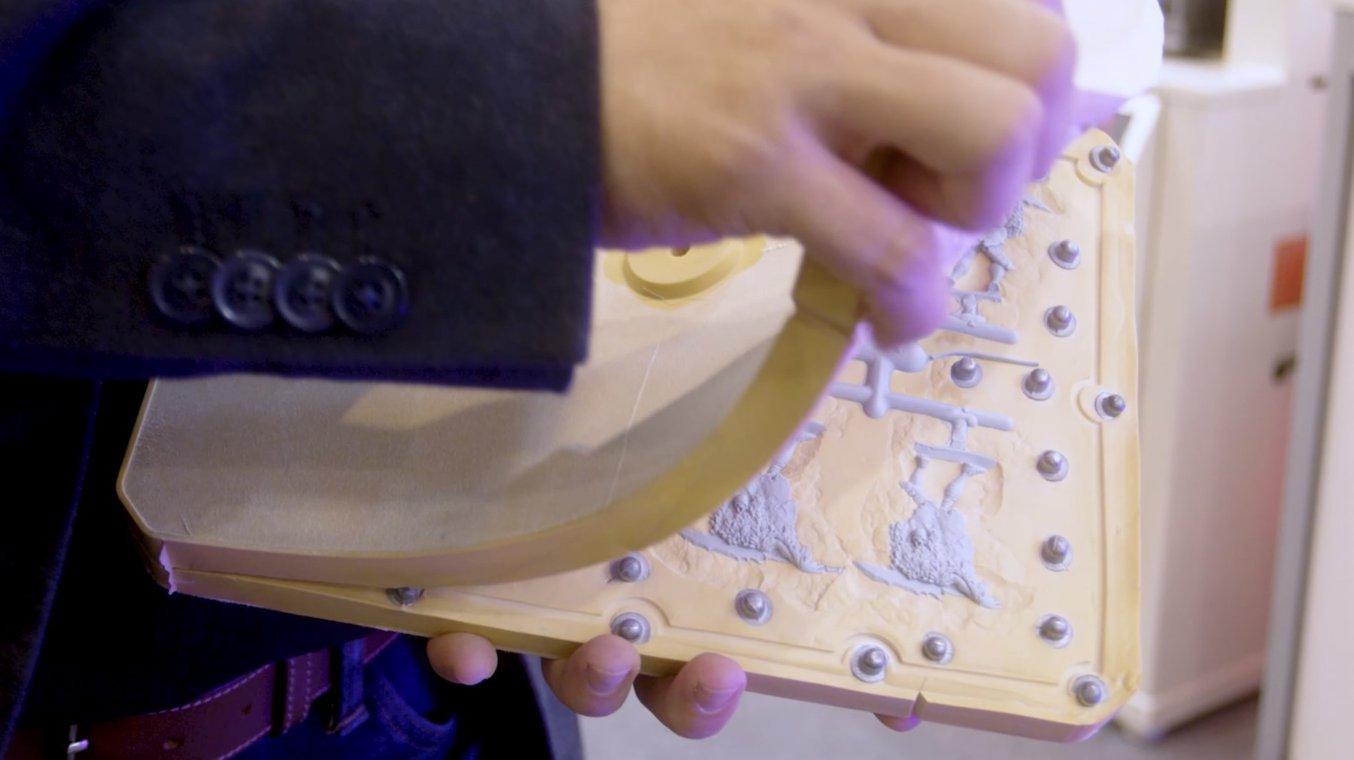
The traditional technologies to make high volumes of miniatures could be costly, lacking in quality, and hard to scale. One of the most popular of such processes, injection molding, can achieve up to millions in volume, but it is notorious for high tooling costs and long lead times, making the initial investment and large volumes needed to break even massive barriers for smaller companies to enter the market. This also represents a major barrier for bigger players in miniature-making, due to the significant risk of launching new miniature designs.
Directly 3D printed miniatures are on the opposite side of the coin: With technologies such as stereolithography (SLA) 3D printing, it’s possible to achieve extremely high details with a low barrier to entry. However, the 3D printing is not competitive with injection molding for larger volumes of parts. Miniature makers generally use 3D printing for one-offs, extremely low-volume batches, or mass-customized parts.
Other established miniature-making technologies, such as spin casting or resin casting, are often labor-intensive, messy, hard to scale, and use toxic materials, making them also complicated technologies to adapt to industrial-level production.
SiOCAST was founded to tackle these challenges. As a spin-off company of the Spanish group Coniex, that has specialized in solutions for the spin casting and silicone molding industries for more than 35 years, SiOCAST is the result of 8 years of internal research and development to bridge the productivity gap between 3D printing and injection molding, being able to achieve production volumes from 50 to 50,000 unique parts, and go even as high as 400,000 parts.
SiOCAST offers a patented thermoplastic resin injection system that operates with high-temperature vulcanized silicone rubber molds, made from high-detailed 3D printed masters, to produce fine quality small parts in a toy-safe durable material.
The whole process is eco-friendly and can be done locally, without the need to rely on overseas suppliers. In less than four years, the SiOCAST system has proven to be profitable and is already adopted by companies in several countries and regions, including the United States, the United Kingdom, Asia, and the European Union.
It’s a new technology that is in between spin casting, resin casting, and injection molding. We've done lots of progress in order to make it as simple as possible, so anyone can adopt the technology. With automation, we are able to achieve the same productivity as a very big injection molding machine, with the advantage that our silicone is really low-cost, safe, and locally made.
Ferran Navarro, CEO and Co-Founder of Siocast
Silicone Molding Process With 3D Printed Rapid Tooling
Silicone mold-making historically involves developing molds from a physical master model or pattern, which would traditionally be made by hand sculpting, spin casting, or CNC machining.
However, with the advances in high-quality and affordable SLA 3D printing, such as Formlabs 3D printers, SiOCAST was able to reliably introduce high-detailed 3D printed masters into their workflow.
The SiOCAST moldmaking process.
The SiOCAST process consists of the following steps:
1. Digital Moldel Design
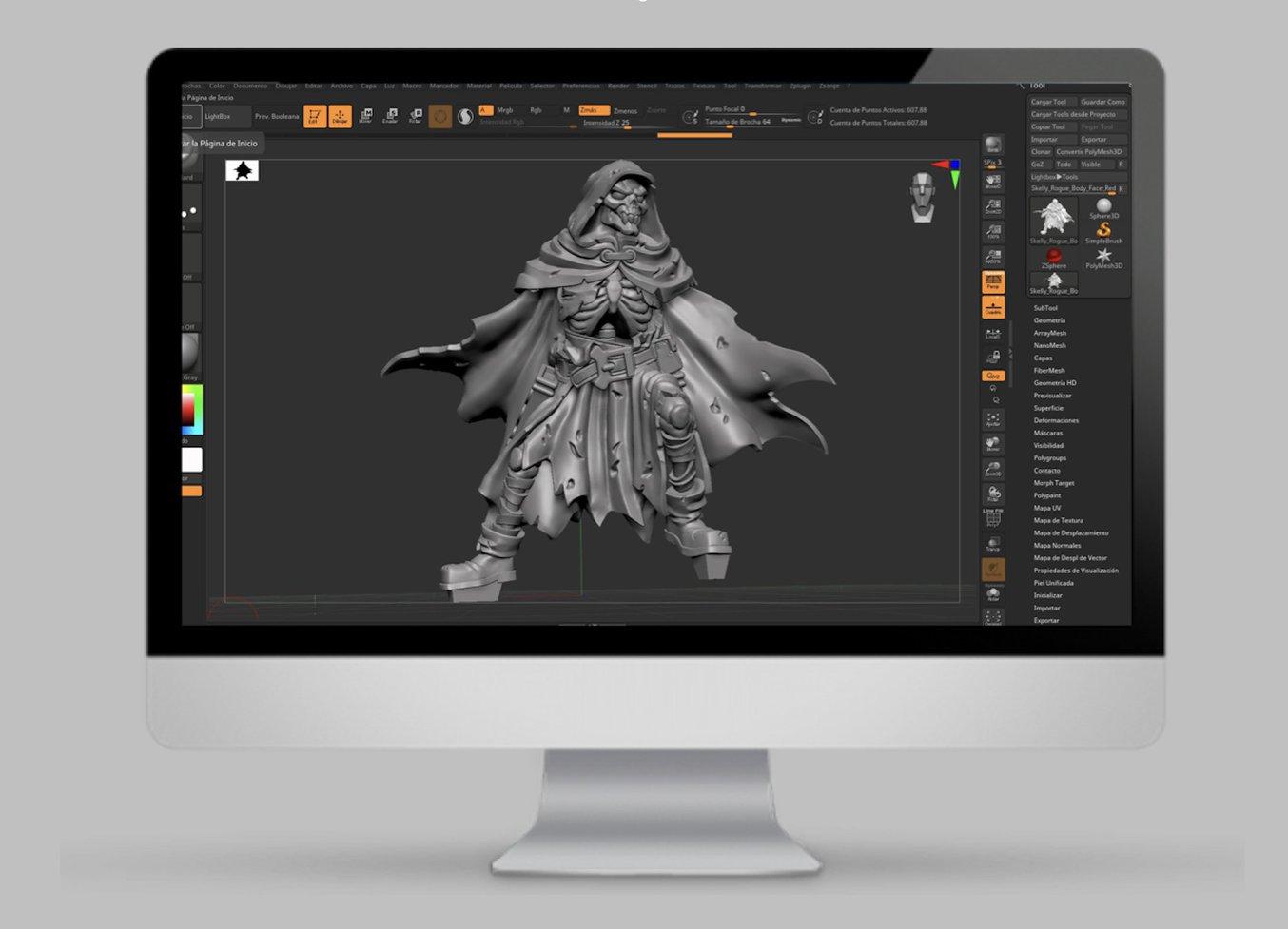
3D model design from Broken Anvil Miniatures.
Using CAD software, the designer models the parts in as much detail as possible, as those will be reflected in the 3D printed part, and then later transferred to the SiOCAST mold, and further to the molded parts. Designs with heavy undercuts are also possible to manufacture with the SiOCAST process. Currently, the maximum thickness of the final parts done with the SiOform1 is 40 mm. During the process, the injection molding gates are also added from their standardized file library.
2. 3D Printing the Masters and Runners
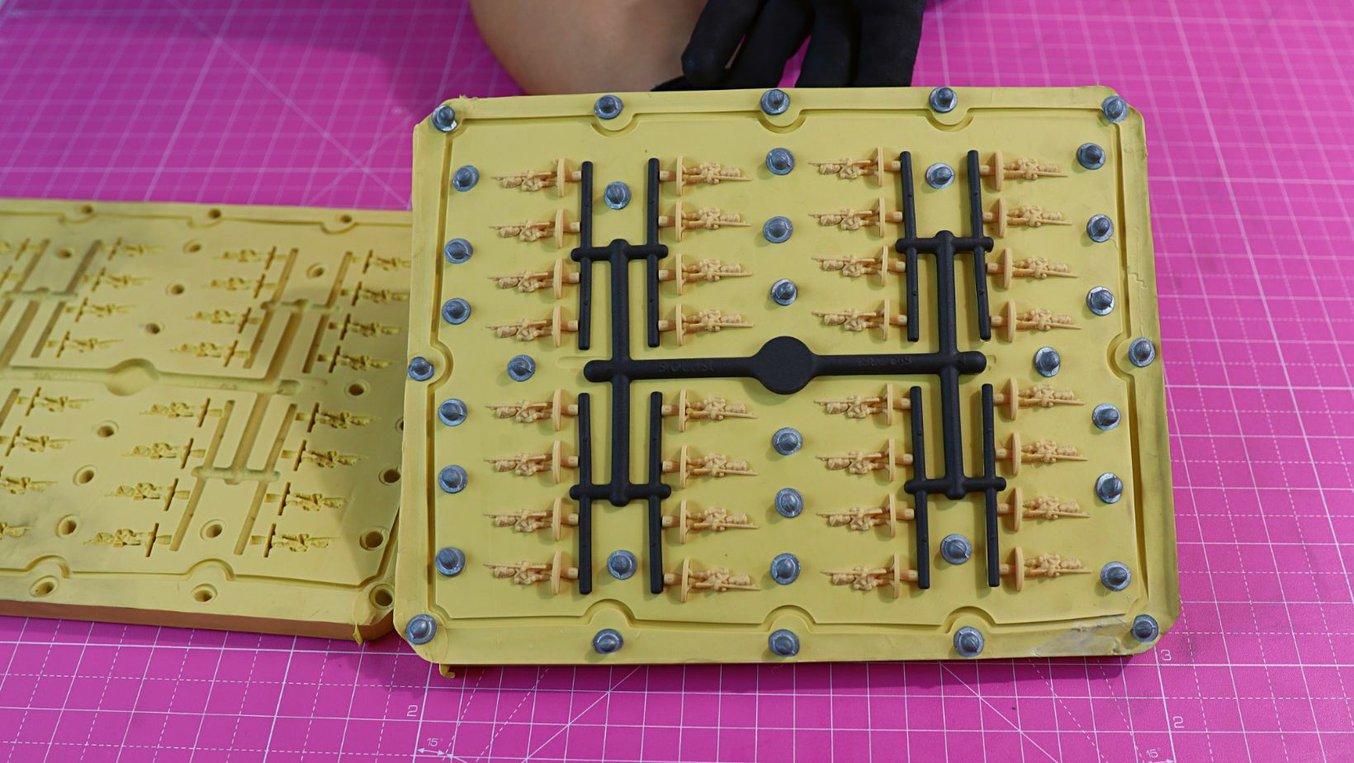
3D printed masters printed on the Form 3+ and runners printed on the Fuse 1.
Once the digital mold is finalized, SiOCAST uses Formlabs print-preparation software, PreForm and the Form 3+ SLA 3D printer to print the master mold using Model V2 Resin as it can withstand high temperatures and provide good mechanical properties in the vulcanization process.
They orientate the pieces at around 45 degrees. When flat surfaces are attached to the build platform, they use chamfering in the edges to prevent the spatulas from breaking the parts.
“We have four Formlabs printers and they are working continuously. Our customers as well—they get the SiOCAST system, and they need one or two Formlabs printers in order to cover the demand they have for masters. Some customers have up to four Formlabs machines, as they have a huge demand for printing,” says Ferran.
With the Form 3+ SLA 3D printer, making inexpensive, high-quality masters is possible in just a few hours. To get the maximum amount of detail, the company prints miniatures at 25 microns layer height.
We have tried different techniques and 3D printing machines before, DLP, SLA, and SLS. Some customers go to DLP technology for finer details, but the resins may not be so durable. We mostly use Formlabs SLA machines for these applications that require a high level of detail and vulcanization durability. And now that we are expanding to technical parts, the Form 3+ 25 micron layers are absolutely enough for those types of masters.
Ferran Navarro, CEO and Co-Founder of Siocast
After printing the parts, they are post-processed with Formlabs automated cleaning and curing system, Form Wash and Form Cure.
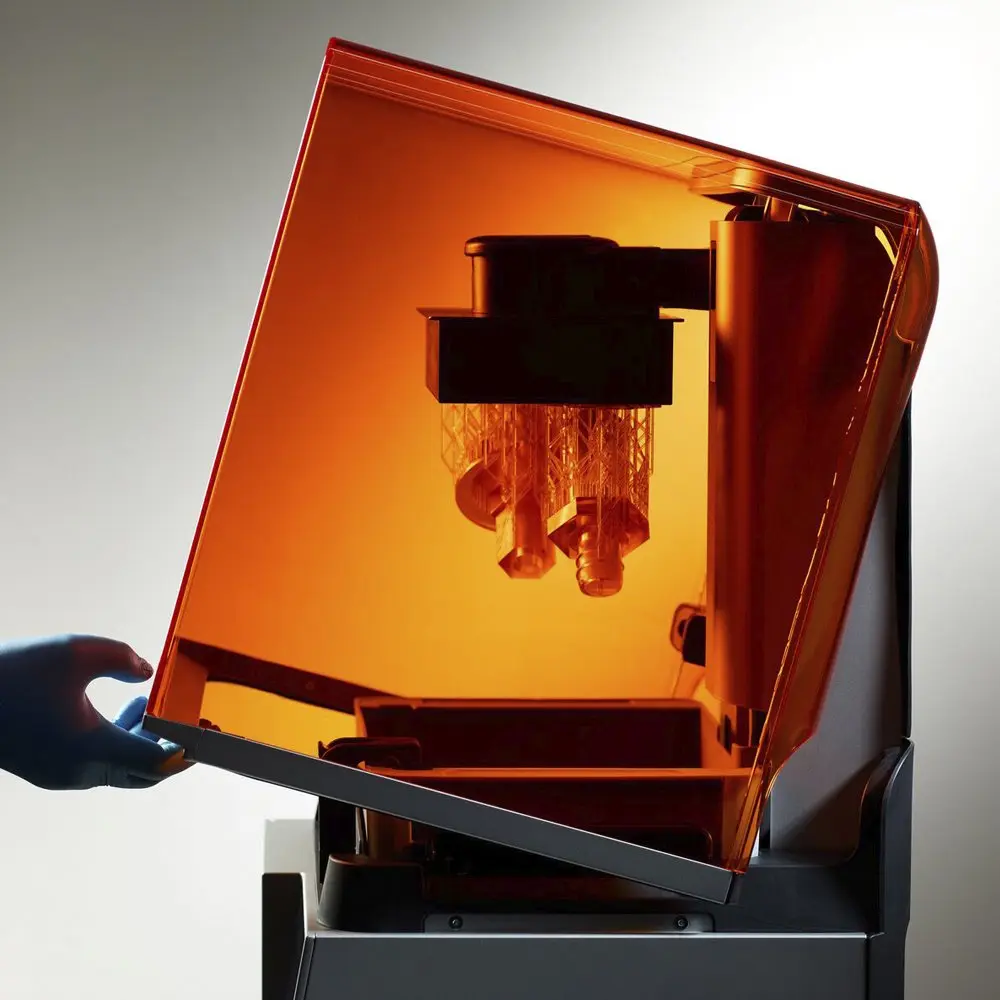
Introduction to 3D Printing With Desktop Stereolithography (SLA)
Looking for a 3D printer to realize your 3D models in high resolution? Download our white paper to learn how SLA printing works and why it's the most popular 3D printing process for creating models with incredible details.
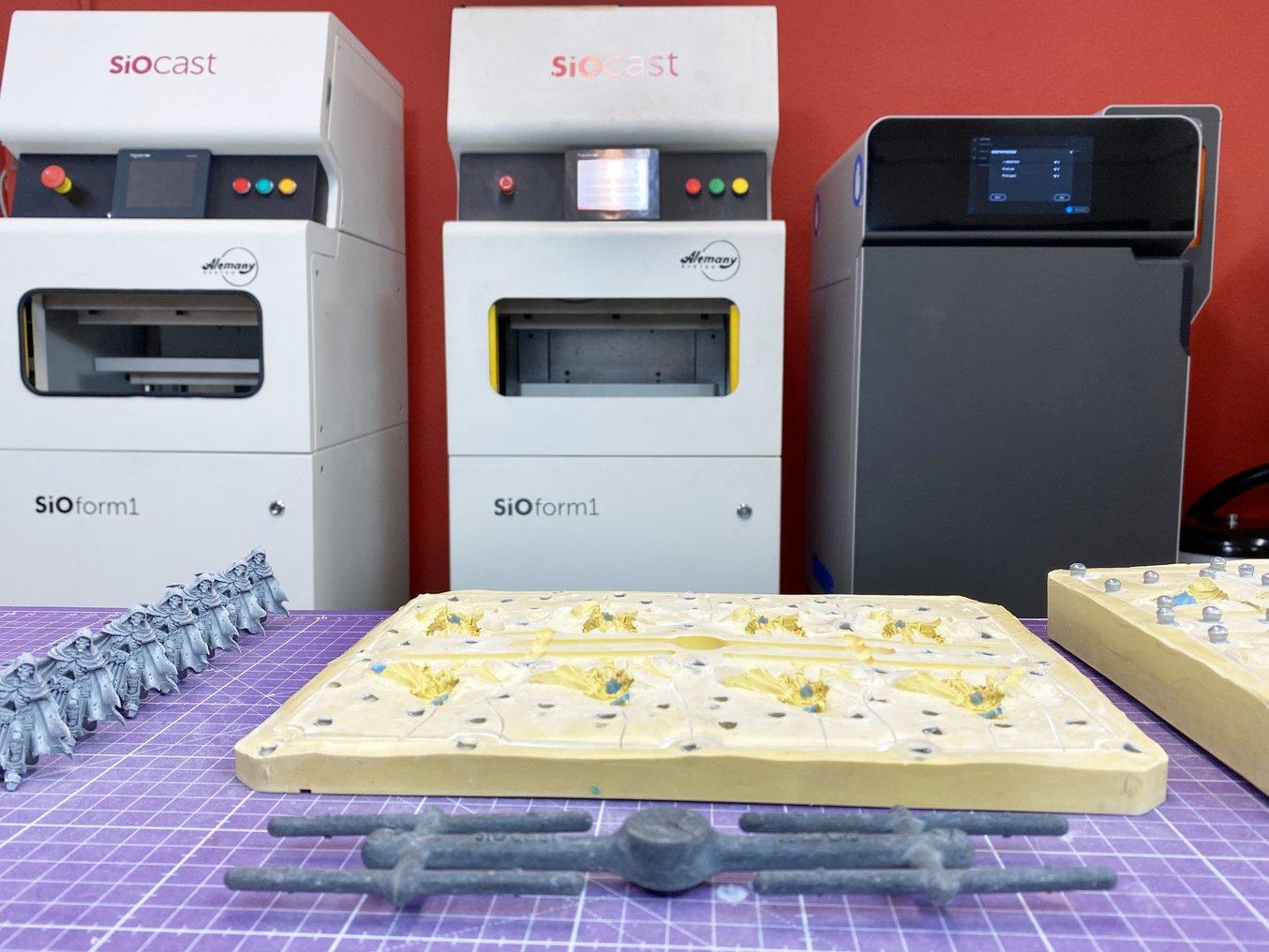
3D printed runners printed on the Fuse 1.
SiOCAST is using 3D printing not only for making the masters but also for the runners needed in the casting process. For this application, they use a Formlabs selective laser sintering (SLS) 3D printer, the Fuse 1. SLS runners are durable and several can fit in the build chamber without supports, allowing SiOCAST to supply these runners to their users worldwide.
The Fuse 1 accelerates the designs we do, making it possible to do a lot of iterations for runners. In an internal R&D project, we advanced more in the last two weeks than in the last two years.
Ferran Navarro, CEO and Co-Founder of Siocast
The 3D printing process with SLS is similar to the SLA process: The printing file is prepared with PreForm, and then printed in Nylon 12 Powder on the Fuse 1 3D printer. Later, the post-processing steps are done with the Fuse Sift. SiOCAST also uses Coniex’s Abrast post-processing solution for surface cleaning, designed for additively manufactured parts.
3. Silicone Mold Making With Vulcanization
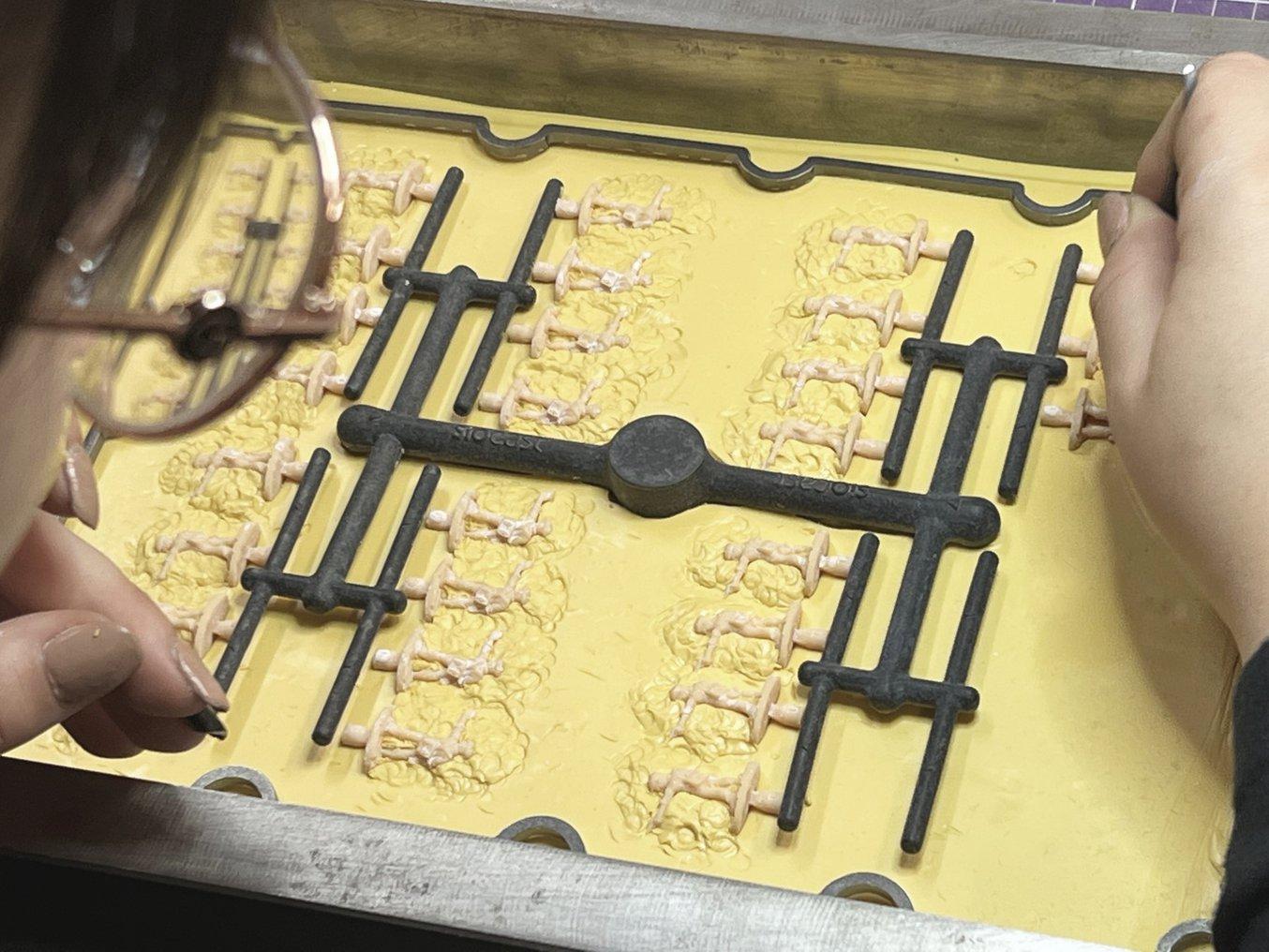
Mold preparation for vulcanization.
With the 3D printed masters and runners in hands, the next step is to create the molds with the SiOmold silicone rubber. They are SiOCAST’s hard HTV (high-temperature vulcanization) silicone material with 65 or 80 Shore A hardness, composed of an elastomer custom-made by the CONIEX group with extraordinary thermal and mechanical resistance. The silicone laminate is placed inside a stiff and precise metal frame, made with CNC machining, and then the 3D printed masters are evenly set on top of the silicone and carefully settled by adding more silicone around it to find the desired parting line. The 3D printed SLS runners are also added and pressed into a nascent slab.
The centering guides are added to hold the two parts of the mold together. Then talcum is spread on top as a releasing agent that will prevent both sides of the silicone from sticking to each other. The top layer of silicone is added, and the metal box frame is closed. Depending on the mold complexity, this process can take from ten minutes to two or three hours.
The metal box then goes inside the vulcanizing press SiOpress, in which the silicone and 3D printed masters are pressurized at 10 bars to release the air, and heated at 120 degrees Celsius. During the 40-60 minutes vulcanization process, the silicone will become liquid, and at this moment, it is copying every single detail from the 3D printed masters before bonding the elastomer chains and becoming a vulcanized mold.
After cooling off, the mold is opened and the 3D printed masters are removed from the cavities, resulting in the final mold that will be used in the SiOCAST machine. The 3D printed masters can then be re-used in additional rounds of vulcanization.
We use a special releasing agent so the 3D printed masters won’t stick into the silicone after the vulcanization and they can be re-used to make the next mold. In general, a Formlabs 3D printed master is able to make three to four vulcanizations in total or several more.
Ferran Navarro, CEO and Co-Founder of Siocast
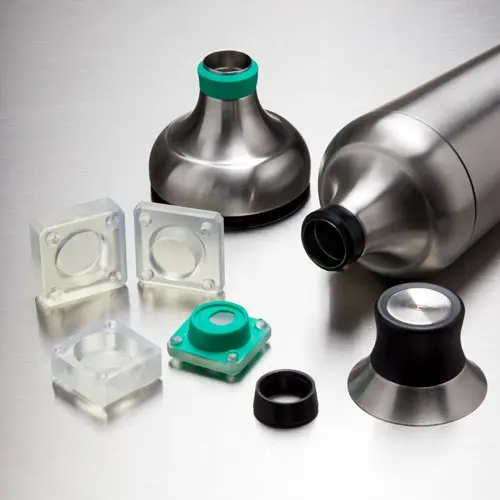
Silicone Molding For Product Design
Download this report for case studies featuring OXO, Tinta Crayons, and Dame Products that illustrate three different implementations of silicone molding for product design and manufacturing, including overmolding and insert molding.
4. Miniature Production With the SiOform1
In the SiOform1, the two halves of the vulcanized rubber mold are fitted together and placed inside, the injection recipe is selected, and after the click of a button, the machine is already working: It removes the air from the mold and injects the liquified thermoplastic resin at 240 degrees Celsius.
Once the mold cools off, it can be removed from the machine. This whole part of the process takes only about 30 seconds (up to 1 minute if it’s a thicker mold), and a new mold can be inserted right away for the next batch.
After a few seconds of cooling off outside the machine, the first batch of miniatures can be removed from the mold and unsprued. The combination of SiOCAST’s thermoplastic resin with their internally developed silicone rubber makes the miniatures come out of the mold easily.
Each cast produces on average 4 to 64 miniatures, depending on the size of the parts and the volume, which is limited to 100g per shot, and the whole process is about 10 to 20 times faster than traditional resin casting.
You can rotate molds while you let them cool off before using them again in the machine. Normally you work with three to nine different molds that are rotating. You can do 25-40 castings an hour. And if there is an automation system, we can go up to between 60-80 injections per hour, making from 100 to 1000 parts per hour, all with the same detail level of the original 3D printed master.
Ferran Navarro, CEO and Co-Founder of Siocast
Each silicone mold is 210 x 270 millimeters and can be up to 50 millimeters thick, which would accommodate final parts of up to 40 millimeters thickness. The molds can withstand about 300-500 castings, making this a viable option for both short-run and series production.
SiOCAST clients can either buy the final silicone molds directly from them with the readyCAST service or make their own molds in-house which is the standard preferred solution. The company offers a complete training package to capacitate beginners each step of the way.
Industry Game-Changer System
Directly making miniatures with 3D printing is still a great option for hobbyists’ one-offs or low quantities, but SiOCAST has set the standard for professional miniature making.
Final consumers claim they are getting more durable, much more detailed, and easier to paint parts, that they can’t get with resin casting, metal miniatures, or injection molded parts.
Companies such as Monster Fight Club (The Witcher, Cyberpunk RED), Warlord Games (Blood Red Skies, Bolt Action), Reaper Miniatures (Bones USA), Titan Forge Miniatures, Corvus Belli (Infinity the Universe), Yedharo Models and Creature Caster are a few of the players that have adopted SiOCAST’s system.
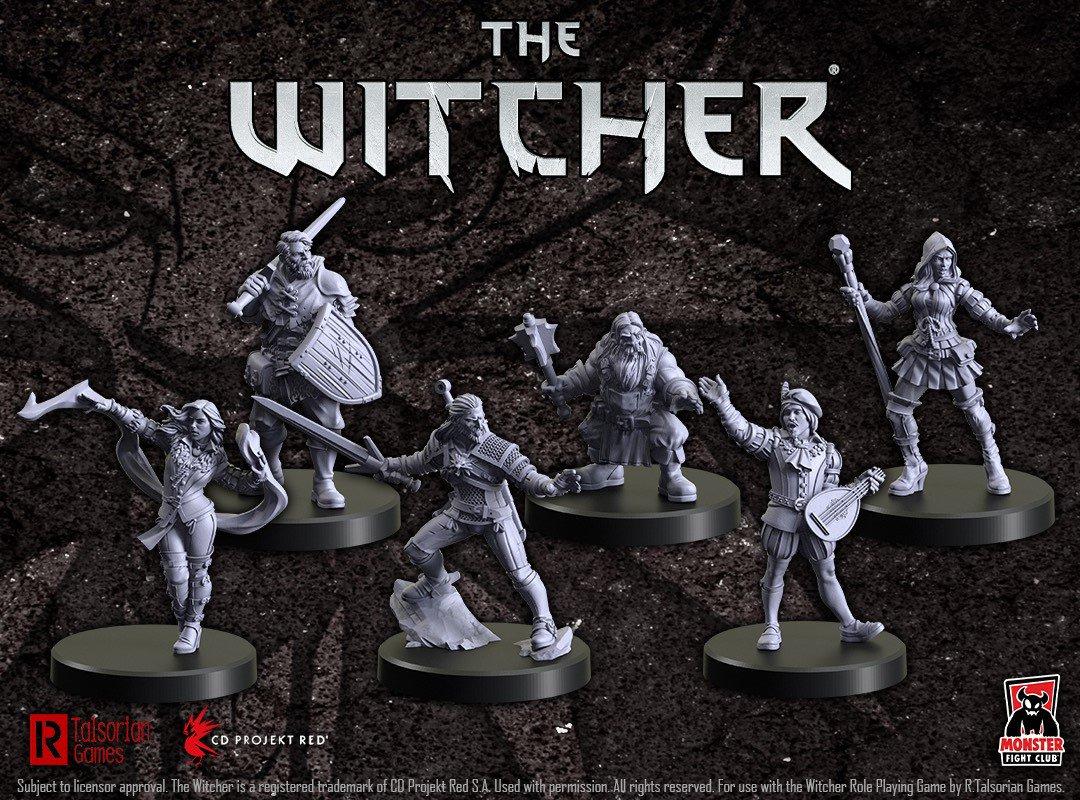
Monster Fight Club’s miniatures of The Witcher.
SiOCAST’s system reception in the miniature market has been great but also in the Anime and Manga industry.
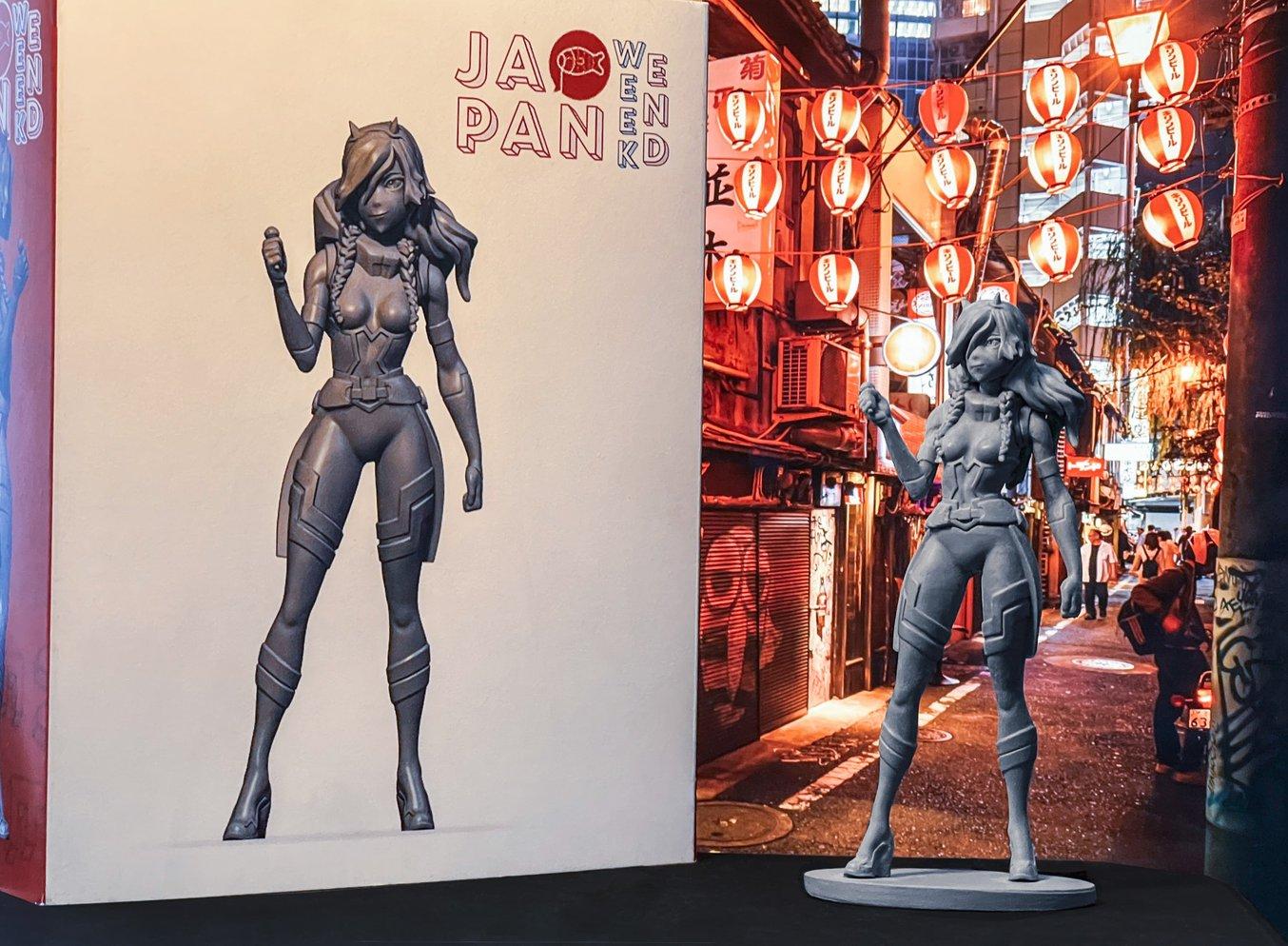
Japan Weekend’s miniature made with SiOCAST.
The company is also expanding into the model landscape market and has already worked with some of the main manufacturers of landscape modeling.
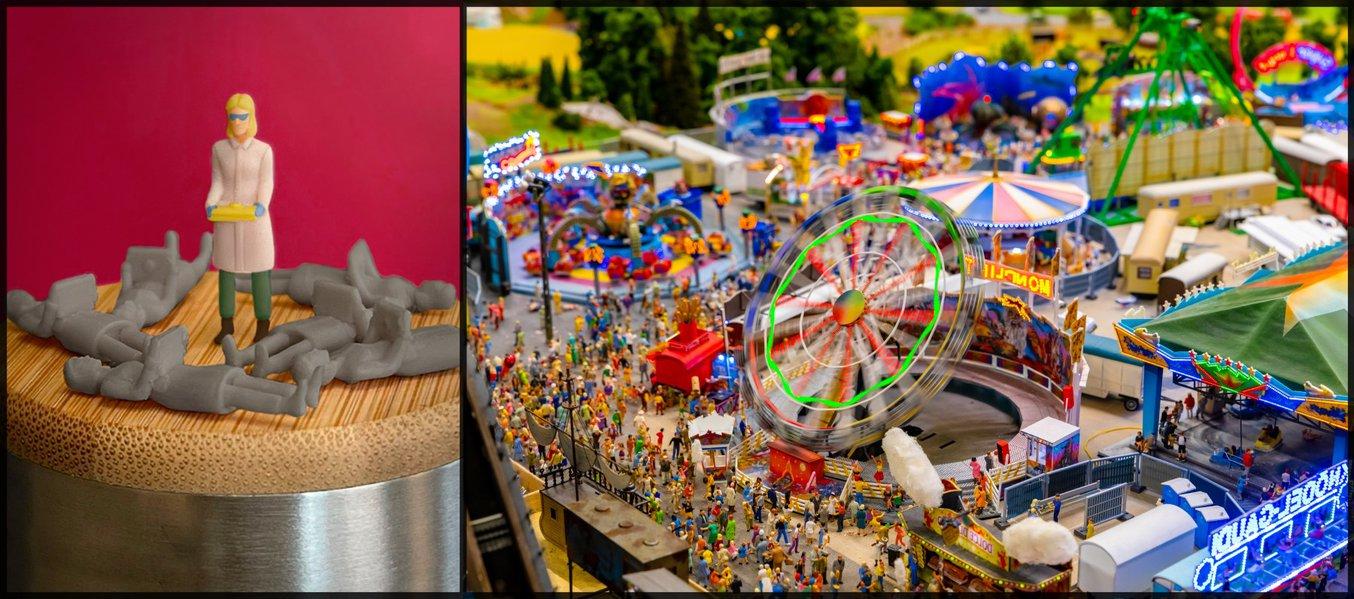
Model landscape from Miniatur Wunderland.
Some manufacturers of role-playing games, like Galladoria Games, expand the benefits of the SiOCAST system to the terrain and scenography market. The examples of companies that are moving to the SiOCAST system from out of the miniature market are growing every day.
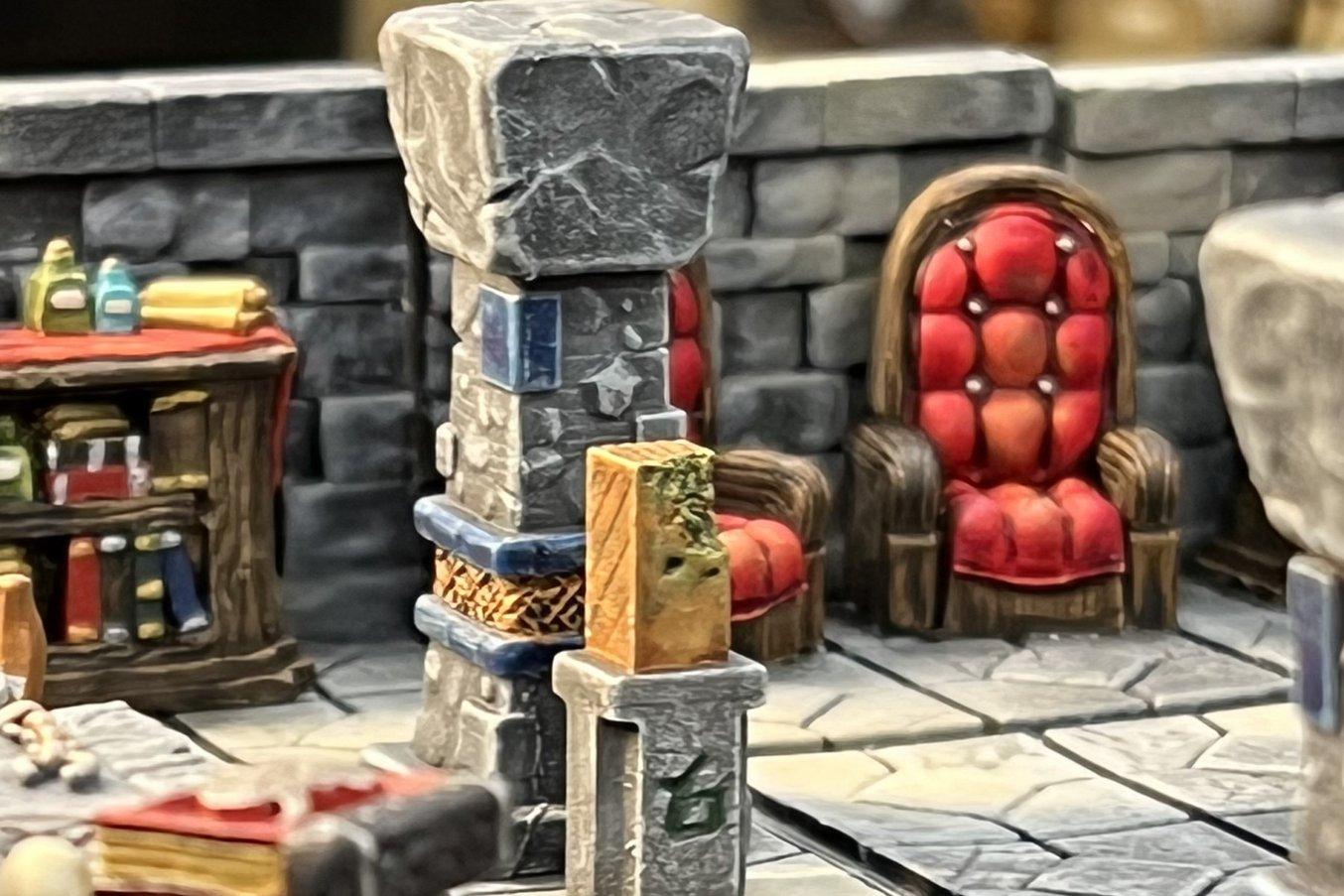
Galladoria’s D&D terrain.
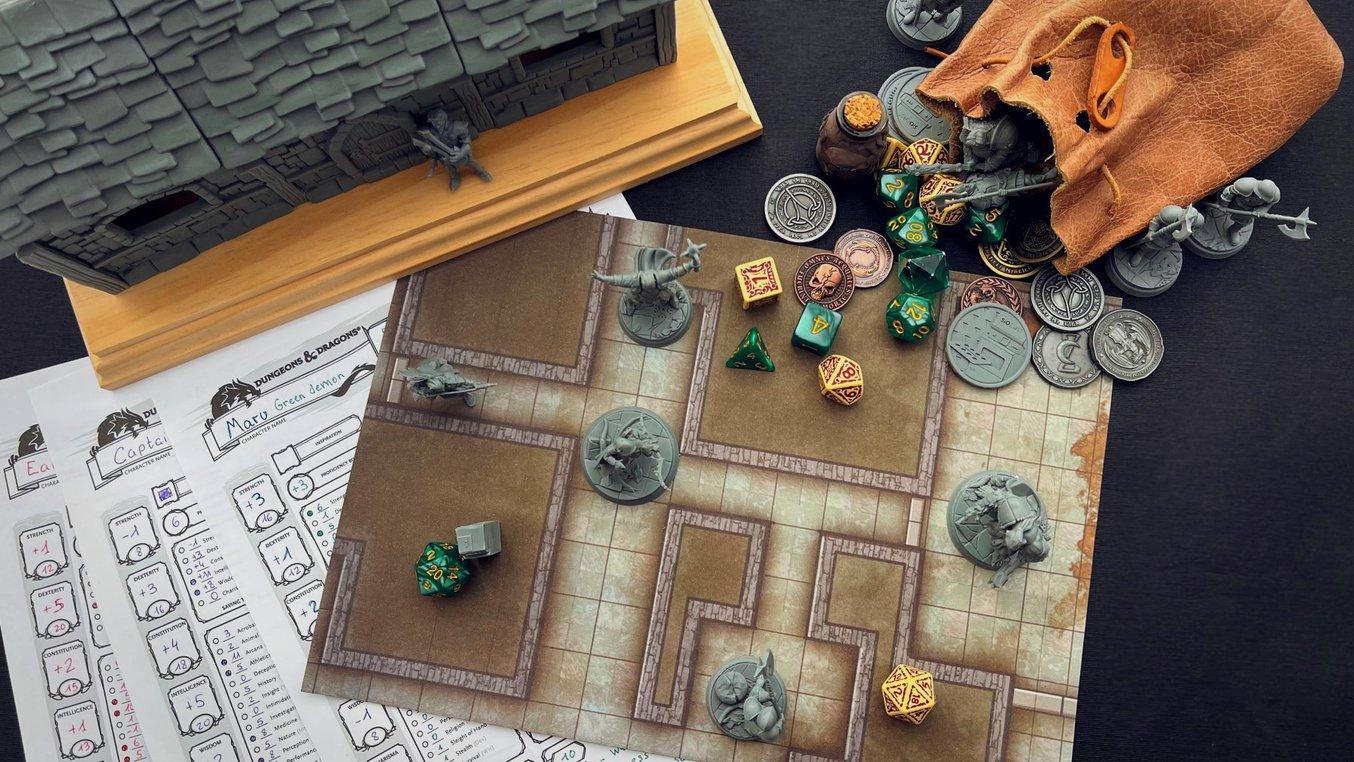
Dungeons & Dragons parts made with SiOCAST.
Locally Manufactured
The new production system is really moving the wheels in the industry. Ferran points out that only a few miniature-making companies in the world can have plastic production done 100% in-house when using traditional methods. Most companies rely on sourcing from China, which tends to come with high logistics costs, as well as long lead times and high minimum order quantities (MOQ). But now with SiOCAST, businesses of any size can bring production in-house.
For example, Reaper Miniature’s Bones USA collection not only moved from making metal miniatures to thermoplastic miniatures with SiOCAST, but also shifted its production line from China to the United States.
Eco-Friendly, Zero Waste Making
SiOCAST also highlights the fact that their proprietary plastic SiOres are non-toxic, EN-71 Toy Safe certified and their production system is eco-friendly. The resin cast to make miniatures is reusable so any miss cast or runners are ground and mixed with new material, making it a zero-waste plastic system.
By producing locally and with a system adaptable to demand, there is no need for stocking or waste due to unsold products. This, aligned with the compact machines needed to produce the miniatures, enabling a small footprint.
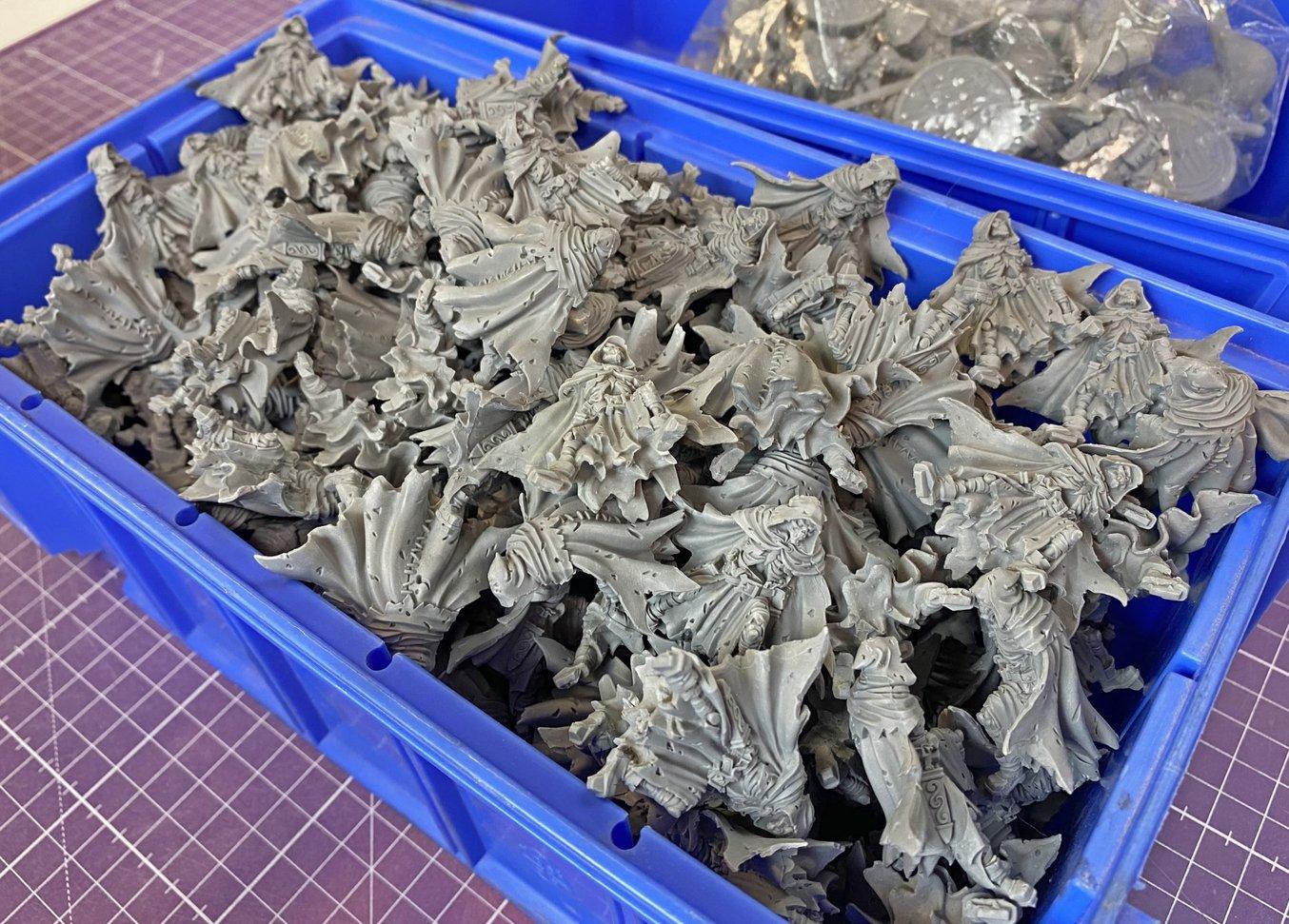
Locally produced high-quality miniatures from Broken Anvil Miniature.
Ferran says that, in a room as small as 10 square meters, “you can have your own high volume manufacturing capacity. You cannot do that with manual bench press injection molding machines, which are really nice machines but are limited in terms of size or capacity”.
“With injection molding sprues you have a lot of waste. About 20% of the plastic goes to the bin. The miniatures are generally manufactured abroad and have to travel to the United States. Also, the manufacturer has to make 20,000 units and maybe will sell half of it, they will have to throw away the rest. So injection molding is nice for a high volume, it’s cost-effective, but it’s not so eco-friendly and has a high carbon footprint. In the resin casting systems, they create 20 times more silicone residues than SiOCAST, and also 30-40% of the toxic resin is wasted in form of runners that are never used ”, adds Ferran.
High-Quality Detailed Parts at a Reasonable Price
When asked what players want in a miniature, the level of detail is always the number one answer from consumers.
However, to have such a level of detail at a reasonable price is the “holy grail”. As Ferran explained, “what everyone really wants in any application is to have the advantages of low-cost tooling, very high detail that you can copy with the silicone, but with the productivity of industrial technologies such as injection molding”.
Another successful case is Warlord Games, in which they were able to produce over 400,000 units of the plane for Blood Red Skies, using SiOCAST’s process in 4 different colors. Traditionally, this type of big batch production would only be feasible with injection molding, and the level of detail wouldn’t be the same.
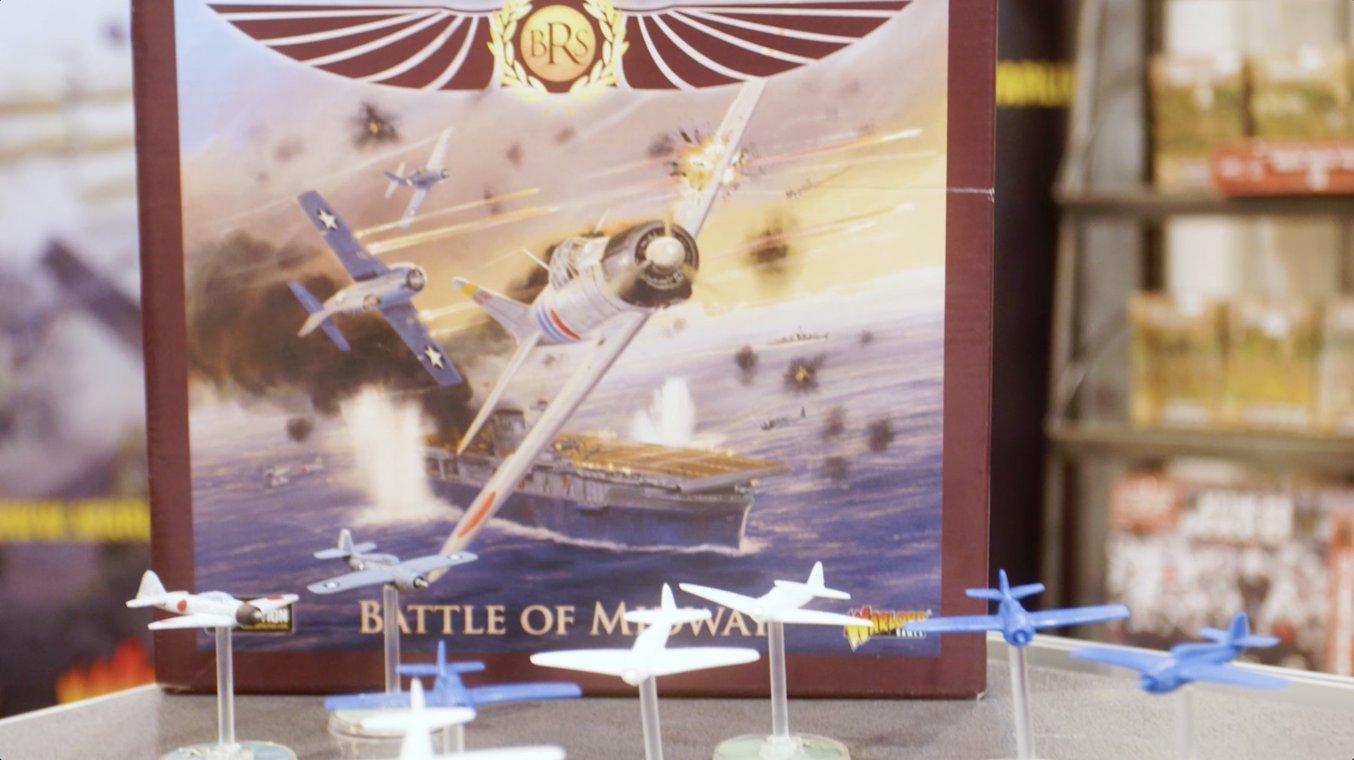
Over 400,000 units of the Red Blood Skies plane were produced with SiOCAST.
With injection molding, the breakeven point will be around ten to 15 thousand units of a single product, as the mold can cost from five to ten thousand euros. Of course, injection molding plastics are really cheap, but then you have to add lead time, availability, and level of detail. Even if you look at the highest quality miniature makers in the market that uses injection molding, they don't get the same details that you get with silicone. It’s quite a steep difference.
Ferran Navarro, CEO and Co-Founder of Siocast
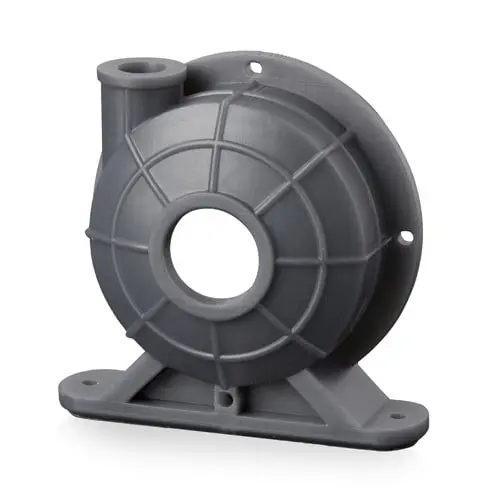
Request a Free 3D Printed Sample Part
See and feel a high-resolution 3D printed master firsthand. We’ll ship a free sample part to your office.
Expanding to New Applications
The SiOCAST system was also well received by other industries and applications, such as footwear, keycaps, medical connectors, overmolding components, and different types of soft and durable parts. For example, one of their customers made wheels and switches for a flight simulator, using masters printed on the Fuse 1 and Form 3+. The advantages of SiOCAST for this company allow the production of end parts, with excellent surface quality at low cost in a quick turnaround local manufacturing. No other technology currently meets those requirements.
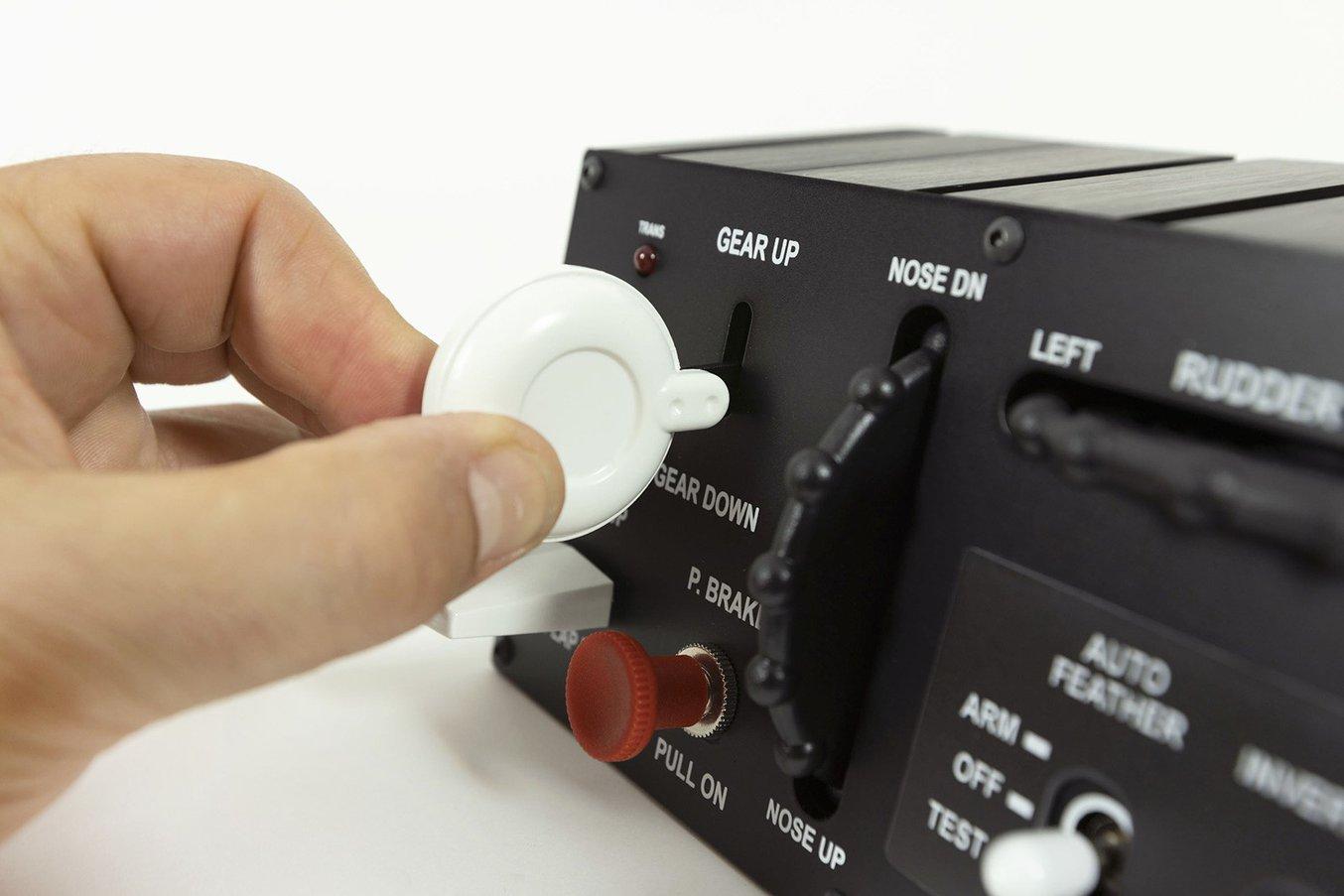
Aplica Design’s flight simulator part made with SiOCAST.
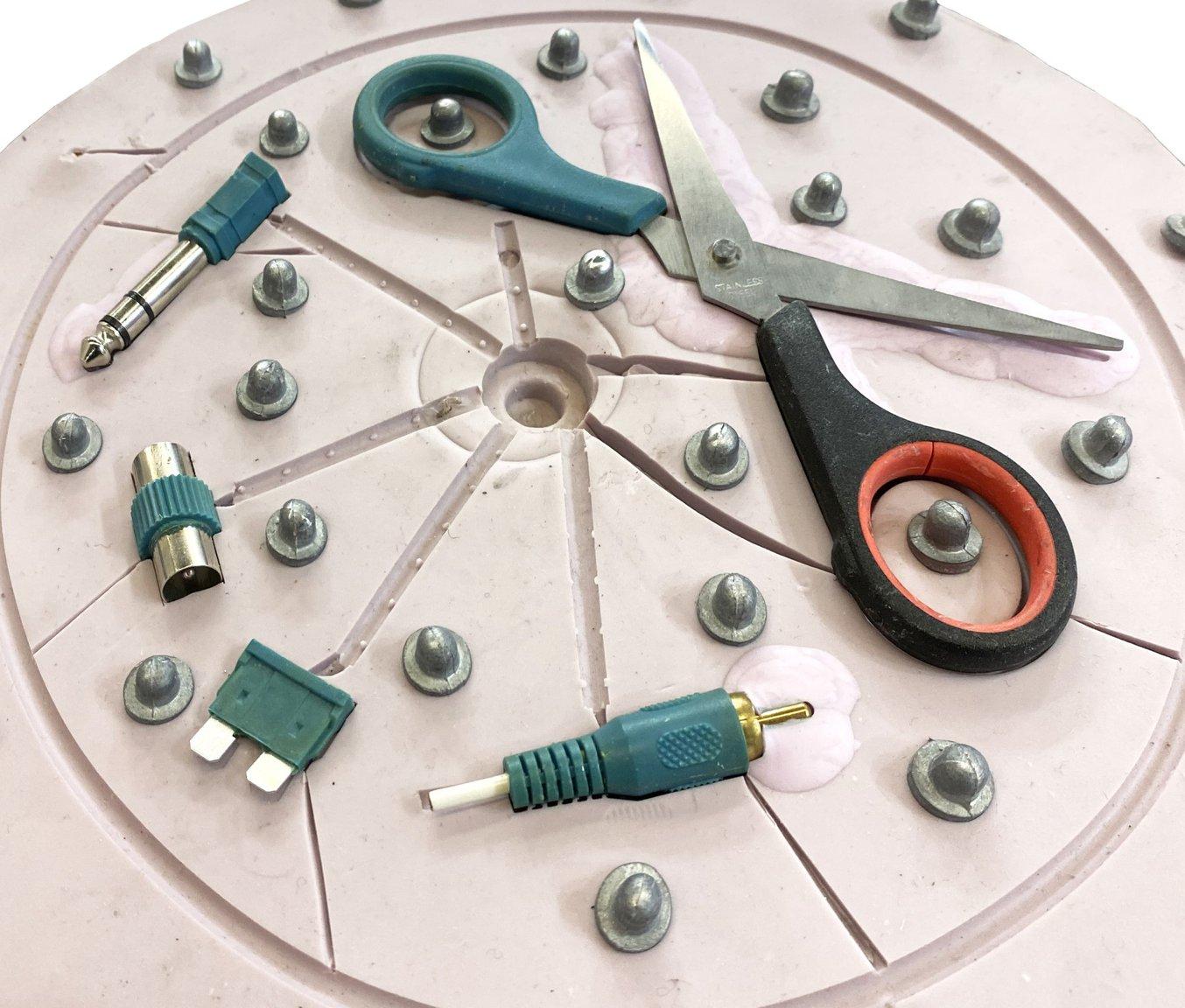
Overmolding with SiOCAST molds.
“The fact that miniature was our first business sector was because that’s the one we knew already, but there are thousands of applications out there”, says Ferran.