3D Printing Miniatures and Custom Figurines: A Guide to Bringing Digital Models to Life
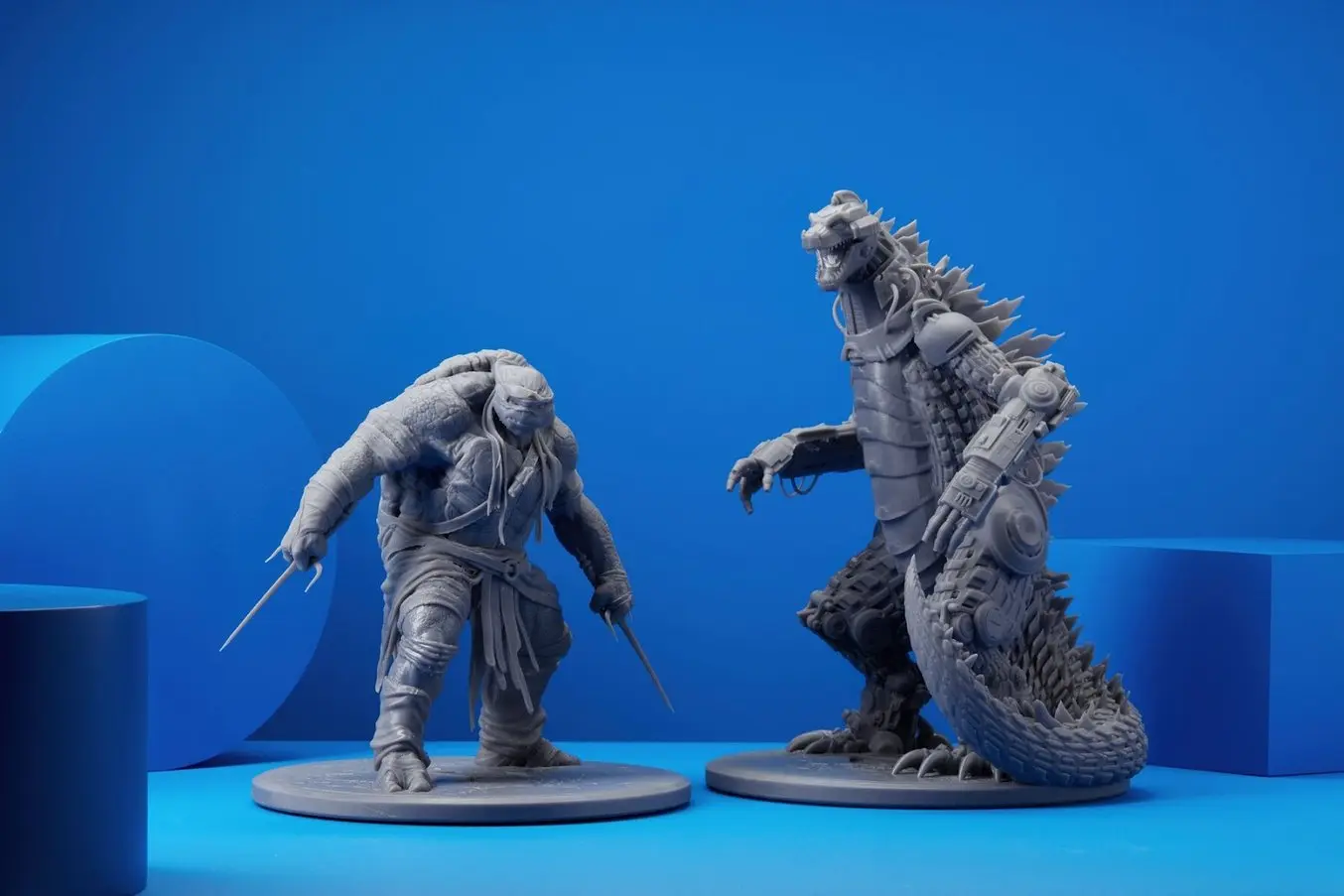
Over the last few years, 3D printers have become more affordable, easier to use, and more reliable. As a result, professionals in the entertainment industry, game designers, and hobbyists have embraced these technologies to create 3D printed miniatures.
This comprehensive guide to 3D printing miniatures and custom 3D figurines will show you how to bring your hyperrealistic digital models to life, which processes to use, how to post-process and paint your 3D prints, and where you can source 3D models for miniatures. Plus, the post will highlight other companies already using 3D printing to bring their digital models to life.
3D Printing in Entertainment and Gaming
In several industries, 3D printing is emerging as a go-to technology for creating custom models. In the model-making and entertainment fields, 3D printing allows designers to create realistic, detailed, unique, and replicable figurines, miniatures, action figures, character models, sculptures, film props, stop-motion models, art, and decoration, all at a sustainable cost and with a fast turnaround.
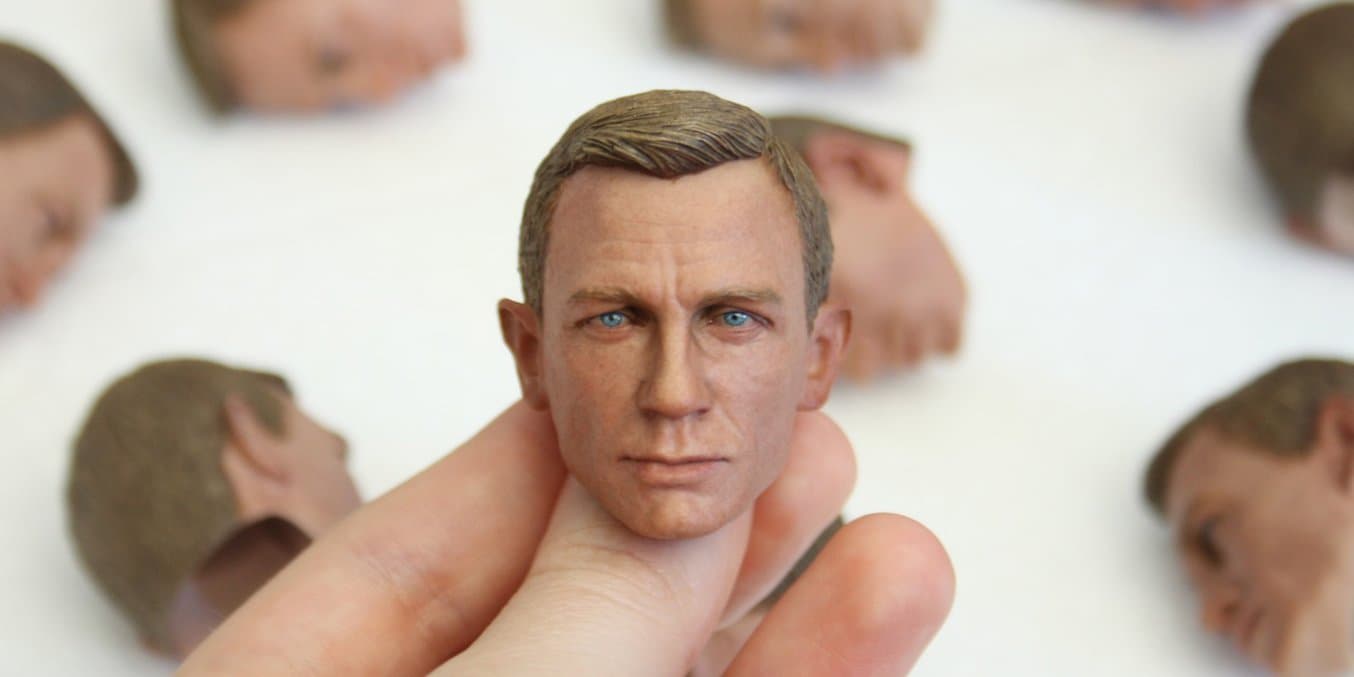
The artists from Modern Life Workshop create hyper-realistic sculptures of actor Daniel Craig with ZBrush and 3D printing.
3D printing is also playing a transformative role in the movies and series industry. Props masters, such as Russell Bobbitt for Marvel movies and Jaco Snyman for the first season and the second season of the Raised by Wolves series, as well as visual effects (VFX) and design studio Aaron Sims Creative for Stranger Things, have adopted the technology, as it significantly saves time in prop making and fuels creativity in the design process. The creation becomes more flexible and fluid, and props and models can be created in an efficient manner.
A behind-the-scenes look at visual effects (VFX) and design studio Aaron Sims Creative’s process to design of Stranger Things’ Demogorgon.
“The Demogorgon was one of the first prints that we did. The first results were just amazing. The level of detail was something that I couldn't even imagine that you could get in a printer”
—Aaron Sims, Founder of Aaron Sims Creative
In gaming, online communities have sprung up around tabletop games like Dungeons & Dragons, for which gamers use 3D printers to create one-of-a-kind D&D 3D printed miniatures, figurines, terrains, landscapes, and other board game accessories.
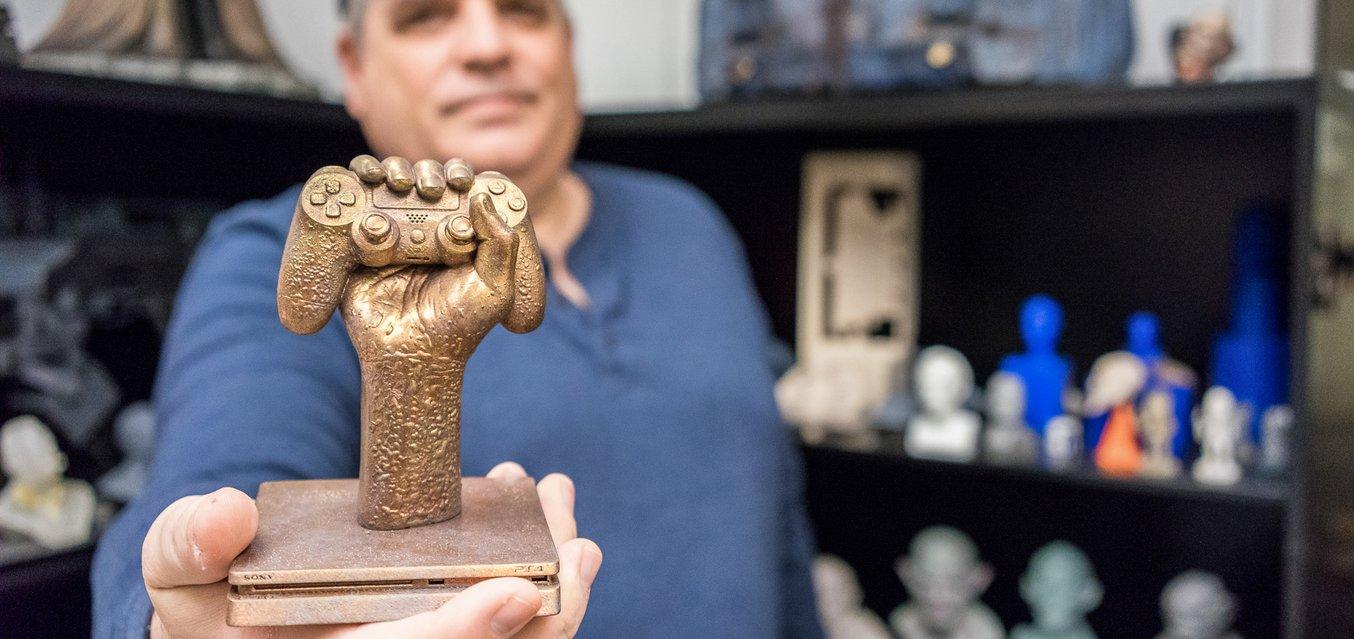
A half-scale hand gripping a PlayStation controller designed and printed for an internal awards event at Sony Fabrication Arts.
Global play and entertainment company Hasbro also uses the technology to create Hasbro Selfie Series figures—a groundbreaking endeavor to use 3D printing to manufacture personalized action figures at scale. For the first time, fans are now able to scan their face with a smart device and have a custom-made look-a-like action figure delivered to their door.
Additive manufacturing offers great design and engineering opportunities for professionals and miniature-making enthusiasts, who will be thrilled to see the designs of their imaginations come to life in a 3D printer.
Best 3D Printers for Miniatures
All 3D printing technologies use a process called additive manufacturing. 3D printers create three-dimensional parts from computer-aided design (CAD) models by successively adding material layer by layer until a physical part is created. Prop makers, game designers, and hobbyists can use the following 3D printer technologies to create various props, miniatures, and figurines.
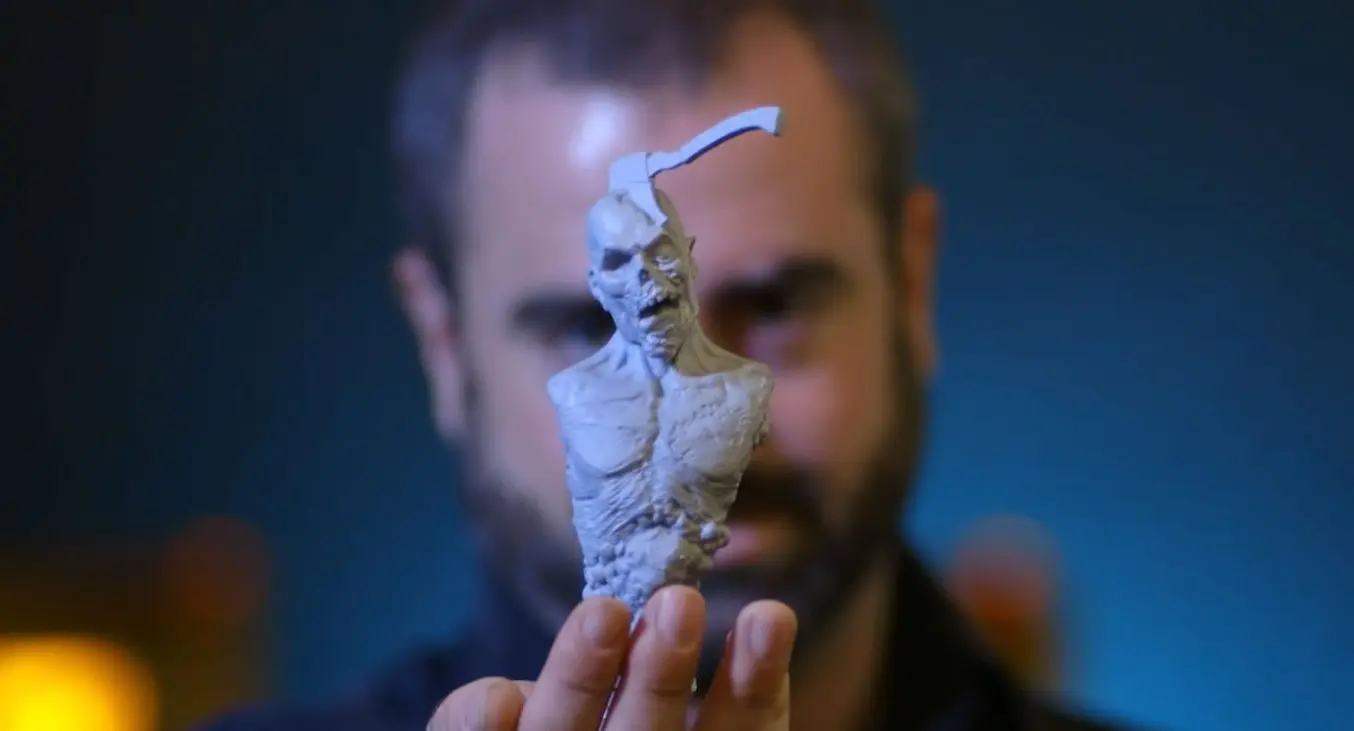
Creature and concept designer Jared Krichevsky uses a stereolithography (SLA) 3D printer to facilitate bringing digital models to life at Aaron Sims Creative.
Fused Deposition Modeling (FDM)
Fused deposition modeling (FDM), also known as fused filament fabrication (FFF), is the most widely used form of 3D printing at the consumer level, fueled by the emergence of hobbyist 3D printers. FDM 3D printers build parts by melting and extruding thermoplastic filament, which a printer nozzle deposits layer by layer in the build area.
Compared to other 3D printing processes, FDM creates larger and more visible layer lines, leading to less-detailed end products. An FDM 3D printer is good for cheaply and quickly 3D printing miniatures for applications where fine surface details are less important.
Depending on your model, post-processing for FDM printing might only require support removal. However, complex figurines printed with an FDM printer require extra support structures, which can be difficult to remove and require sanding to get support marks off finished miniatures.
FDM printers are the least expensive option. A low-end hobbyist desktop FDM printer can cost less than $500, while a more professional FDM printer for 3D printing figurines can cost on average from $2,000-4,000.
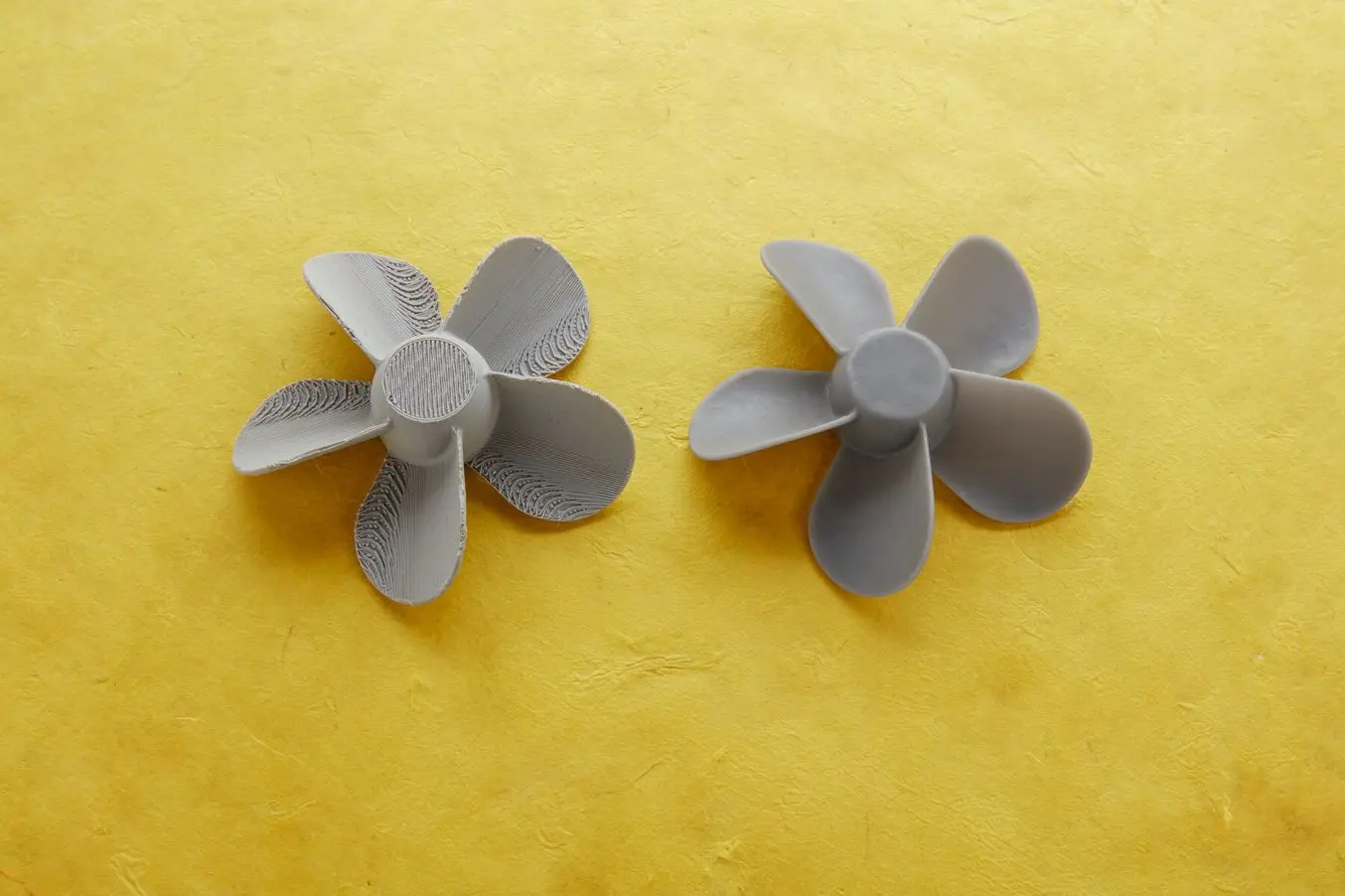
A side-by-side comparison on FDM vs SLA 3D printed parts.
Stereolithography (SLA)
Stereolithography (SLA) printers are the most versatile and precise desktop 3D printers on the market. SLA printer technology uses vat photopolymerization, or resin printing, to cure liquid resin into hardened plastic using a laser. Resin 3D printing produces finely detailed miniatures and figurines with high surface quality using a range of advanced materials.

SLA 3D printers can create finely detailed miniatures and figurines with a smooth surface finish. Part printed on a Form 3 SLA 3D printer.
Resin 3D printers bring high-resolution for miniatures, figurines, and models. Even the smallest prints have a high level of detail.
A 3D printed figurine from an SLA printer will require a medium-length post-curing process, but automated post-curing options are available. Support structures from SLA printers, especially from low force stereolithography (LFS) printers like the Formlabs Form 3 and large scale 3D printer Form 3L, are easy to remove.
SLA 3D printers also offer a wide range of materials, empowering applications outside of traditional 3D printing like silicone molding, pewter casting, or lost-wax casting.
A high-resolution quality desktop SLA 3D printer from Formlabs for miniatures and figurines price starts at $3,499, while large-format SLA 3D printers start at $10,999.
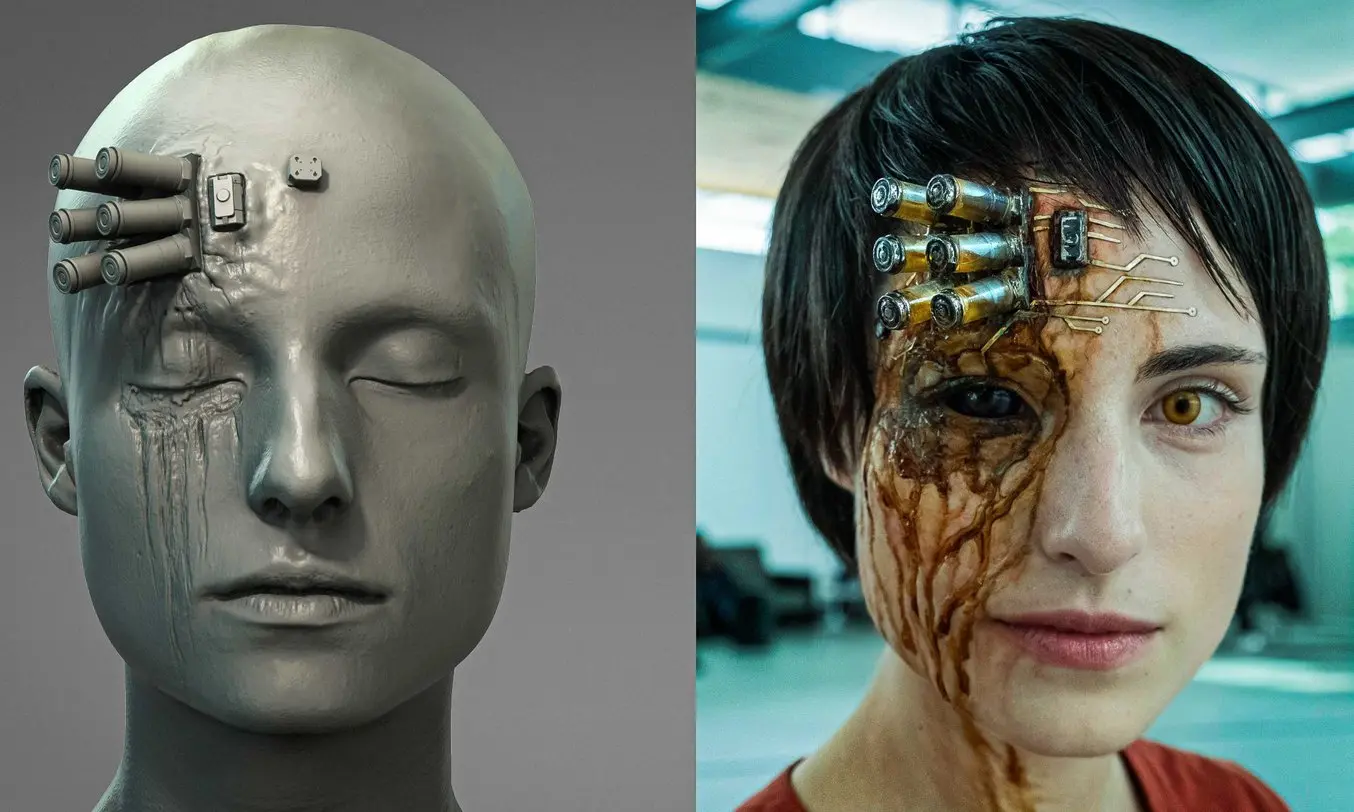
Jaco Snyman, founder of Dreamsmith Studio, shows how he used 3D printing behind the scenes for the HBO Max’s Raised by Wolves series.
“For bigger, less detailed things or as part of mold-making workflows, I use FDM 3D printers. I mostly use Formlabs [SLA] 3D printers to print final parts, because you get such a nice finish.”
—Jaco Snyman, founder of Dreamsmith and lead Prosthetics Designer of the Raised by Wolves series
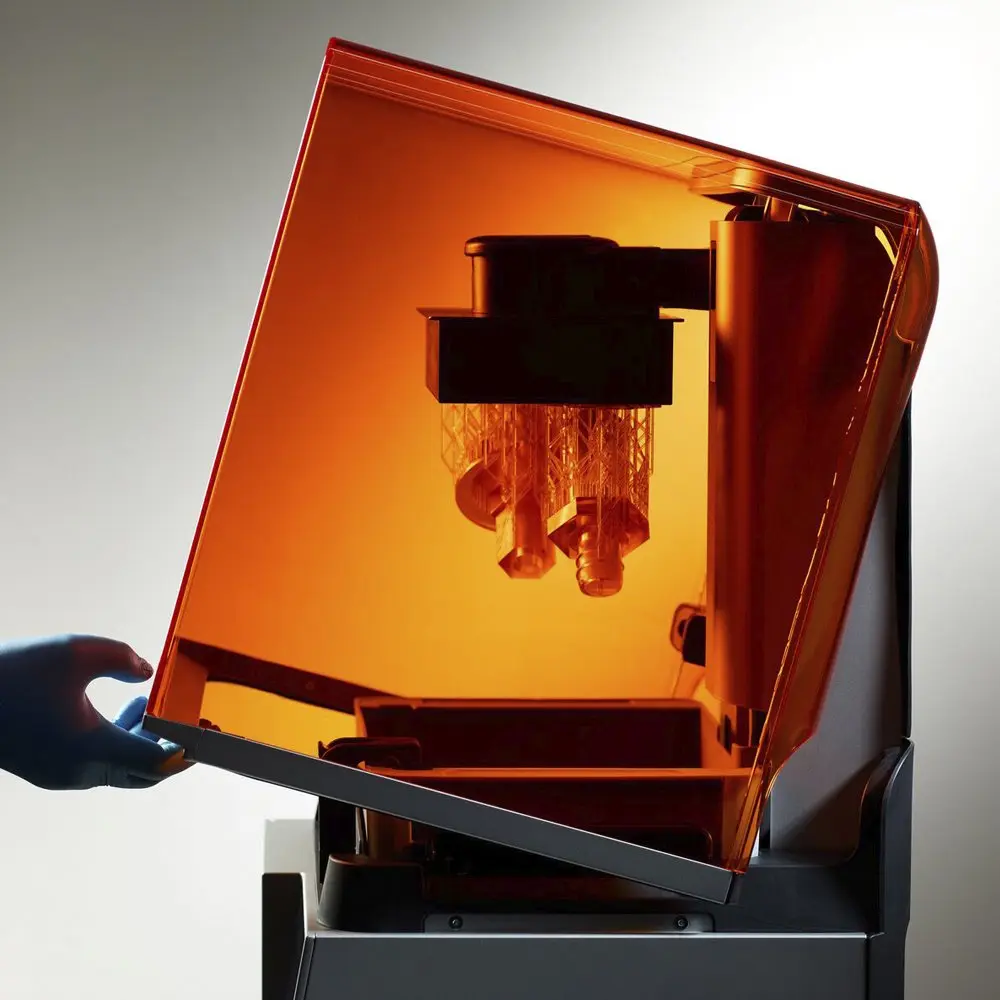
Introduction to 3D Printing With Desktop Stereolithography (SLA)
Looking for a 3D printer to produce high resolution models fast? Download our white paper to learn how SLA printing works and why it's the most popular 3D printing process for creating parts with incredible detail, high dimensional accuracy, and superior surface finish.
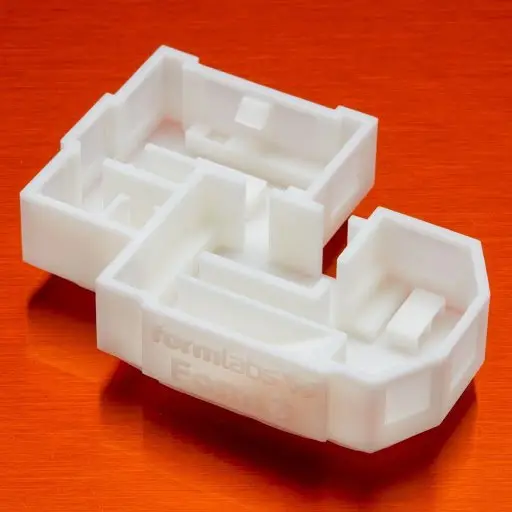
Request a Free Sample Part
White Resin is one of the most popular resins for model making. See and feel White Resin for yourself by requesting a free sample part.
Selective Laser Sintering (SLS)
Selective laser sintering (SLS) uses a high-powered laser to fuse small particles of polymer powder. As the unfused powder supports the part during printing, there’s no need for dedicated support structures. This makes powder 3D printing ideal for intricate models and complex geometries, including interior features, undercuts, thin walls, and negative features.
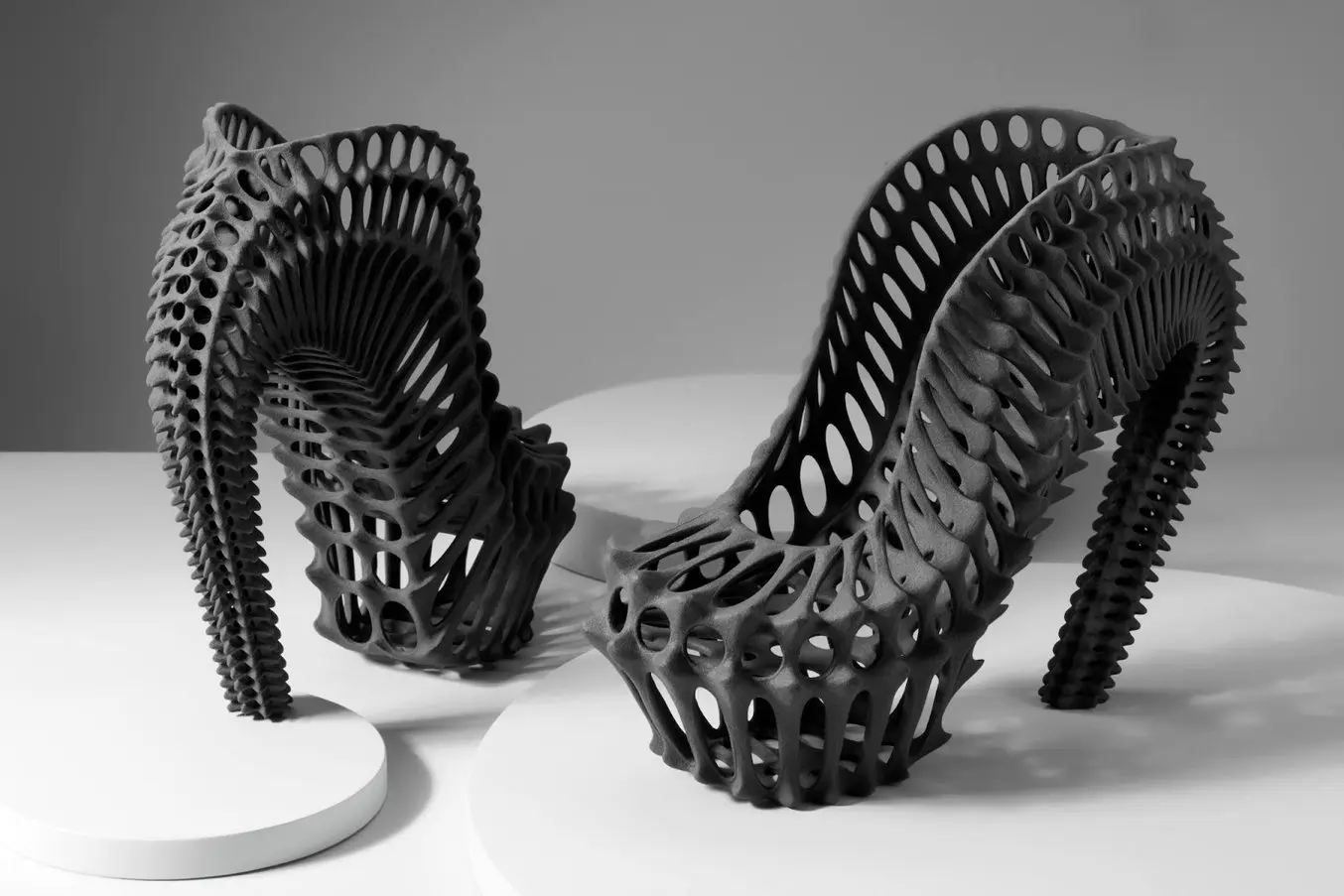
SLS 3D printing is ideal for intricate models and complex geometries. Part printed on a Fuse 1 SLS 3D printer.
SLS parts have a slightly grainy surface finish, but almost no visible layer lines. The most common material for selective laser sintering is nylon, a highly capable engineering thermoplastic for both functional prototyping and end-use production.
Because SLS printers are industrial machines, the entry price used to be higher, starting at around $100,000 and making it inaccessible for many businesses. However, Formlabs has recently introduced the Formlabs Fuse 1 to bridge this gap with the first benchtop industrial SLS 3D printer that offers high quality at a fraction of the cost of traditional industrial SLS systems, starting at $18,499.
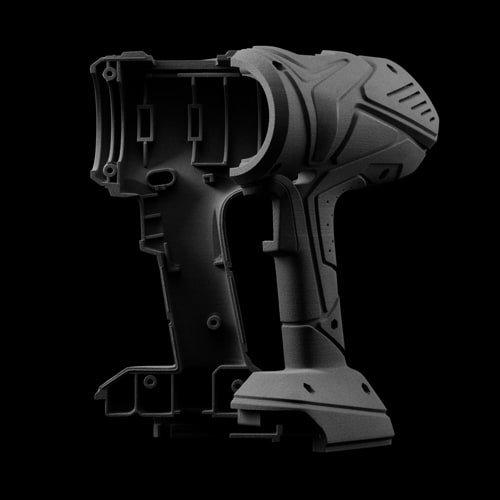
Introduction to Selective Laser Sintering (SLS) 3D Printing
Looking for a 3D printer to create strong, functional parts? Download our white paper to learn how SLS printing works and why it's a popular 3D printing process for functional prototyping and end-use production.
Binder Jetting
Binder jetting is similar to SLS printing, but uses a binding agent to bond the powder material instead of heat. In model making, binder jetting is most commonly used for creating full-color 3D printed figurines and miniatures out of sandstone material.
Just like SLS, binder jetting requires no support structures, as the surrounding powder provides the necessary model support. However, parts that come off a binder jetting printer are very brittle and have high porosity. This means that the process is not ideal for complex designs, as the parts may fracture in the post-processing due to the brittleness of the material.
Binder jetting 3D printers are expensive industrial machines, with prices ranging from $30,000 to $100,000+.
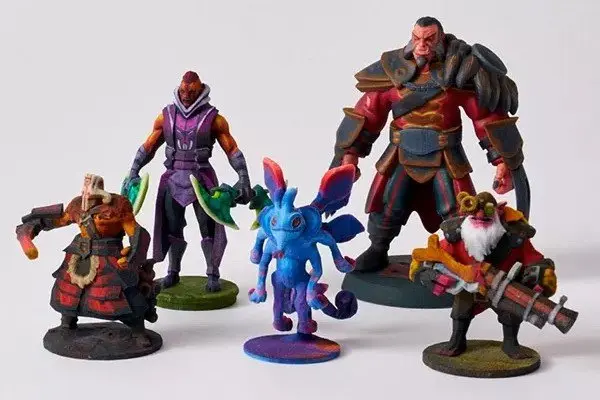
Figurines 3D printed with binder jetting. (source: Shapeways)
Comparing Different Types of 3D Printers for 3D Printing Miniatures
Fused Deposition Modeling (FDM) | Stereolithography (SLA) | Selective Laser Sintering (SLS) | Binder Jetting | |
---|---|---|---|---|
Resolution | ★★☆☆☆ | ★★★★★ | ★★★★☆ | ★★★☆☆ |
Surface Finish | ★★☆☆☆ | ★★★★★ | ★★★★☆ | ★★★★☆ |
Complex Designs | ★★★☆☆ | ★★★★☆ | ★★★★★ | ★★★☆☆ |
Ease of Use | ★★★★★ | ★★★★★ | ★★★★☆ | ★★★☆☆ |
Ideal for | Low-cost, simple models with less details | Finely detailed miniatures and figurines with high surface quality at an affordable price | Complex geometries and durable end-use parts | Full-color 3D printed figurines out of sandstone |
Cost | $500-$2,000 starting equipment cost | $3,750 starting equipment cost | $18,500 starting equipment cost | $60,000 starting equipment cost |
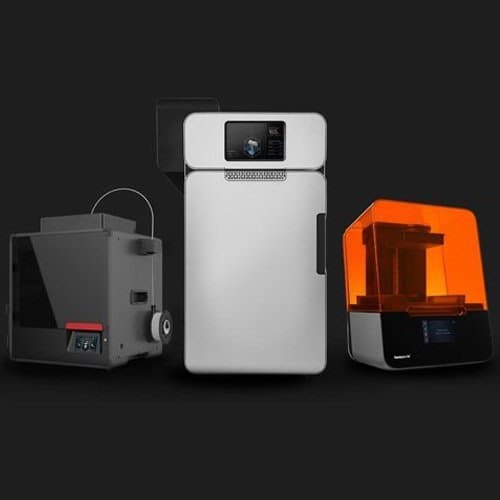
How to Choose a 3D Printing Technology
Having trouble finding the best 3D printing technology for your needs? In this video guide, we compare FDM, SLA, and SLS technologies across popular buying considerations.
Tips for 3D Printing Miniatures
The level of detail and precision needed for printing miniatures can be challenging. Beyond the printing process, post-processing will have a high impact on the final miniature. Here are some tips on how to better 3D print and prepare miniatures.
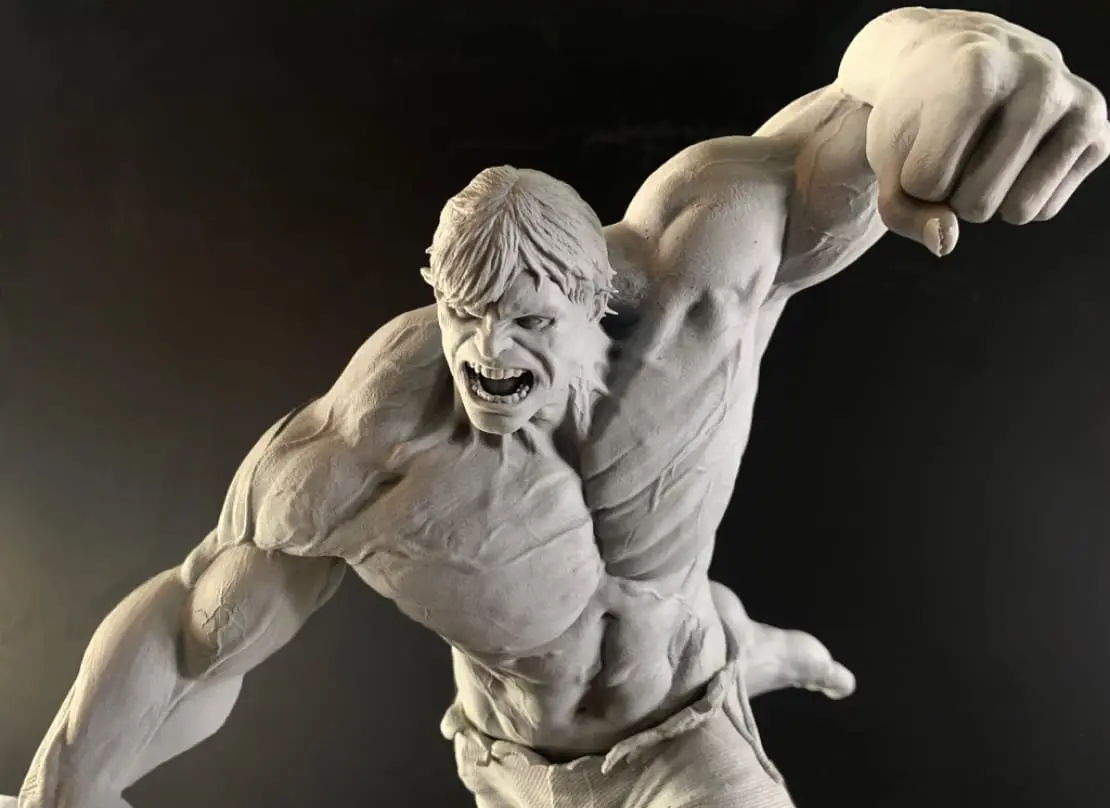
Highly detailed Hulk figurine done with 3D printing by Aarom Sims Creative.
Improving the Quality of Your 3D Prints
Two major factors impact the quality of your 3D prints: layer lines and support structures.
The thicker the layers you use for your 3D printed figure, the more visible your layer lines will be. Thick layer lines create a “staircase” effect on a flat or slanted surface or cause round surfaces to appear “pixelated.” Smaller layer thickness will lead to higher surface quality and more polished prints.
FDM printing tends to use thicker layers and the layer lines are more visible even at the same layer height due to the way the parts are formed. SLA printers can print at a variety of layer thicknesses, including incredibly thin 25-micron layers, depending on the desired print quality, which makes it the ideal choice for showcasing the best details. SLS and binder jetting printers print at around 100-110 micron layers, but the layer lines are mostly invisible on final parts.
In FDM and SLA printers, 3D prints include support structures to scaffold the part during the print process. You will need to remove these support structures, which can be difficult for FDM prints and fairly easy for SLA prints (depending on part orientation). A more complicated support removal will leave marks on the finished product, which you must sand and polish for high-quality finishes.
Support removal with a part printed on the Form 3 SLA 3D printer.
Post-Processing 3D Printed Miniatures
Your models will not be complete without the perfect finish. After printing, post-processing the miniatures with priming and painting will give a final flawless touch and the customization to make them truly unique.
Preparing Your Miniatures for Painting
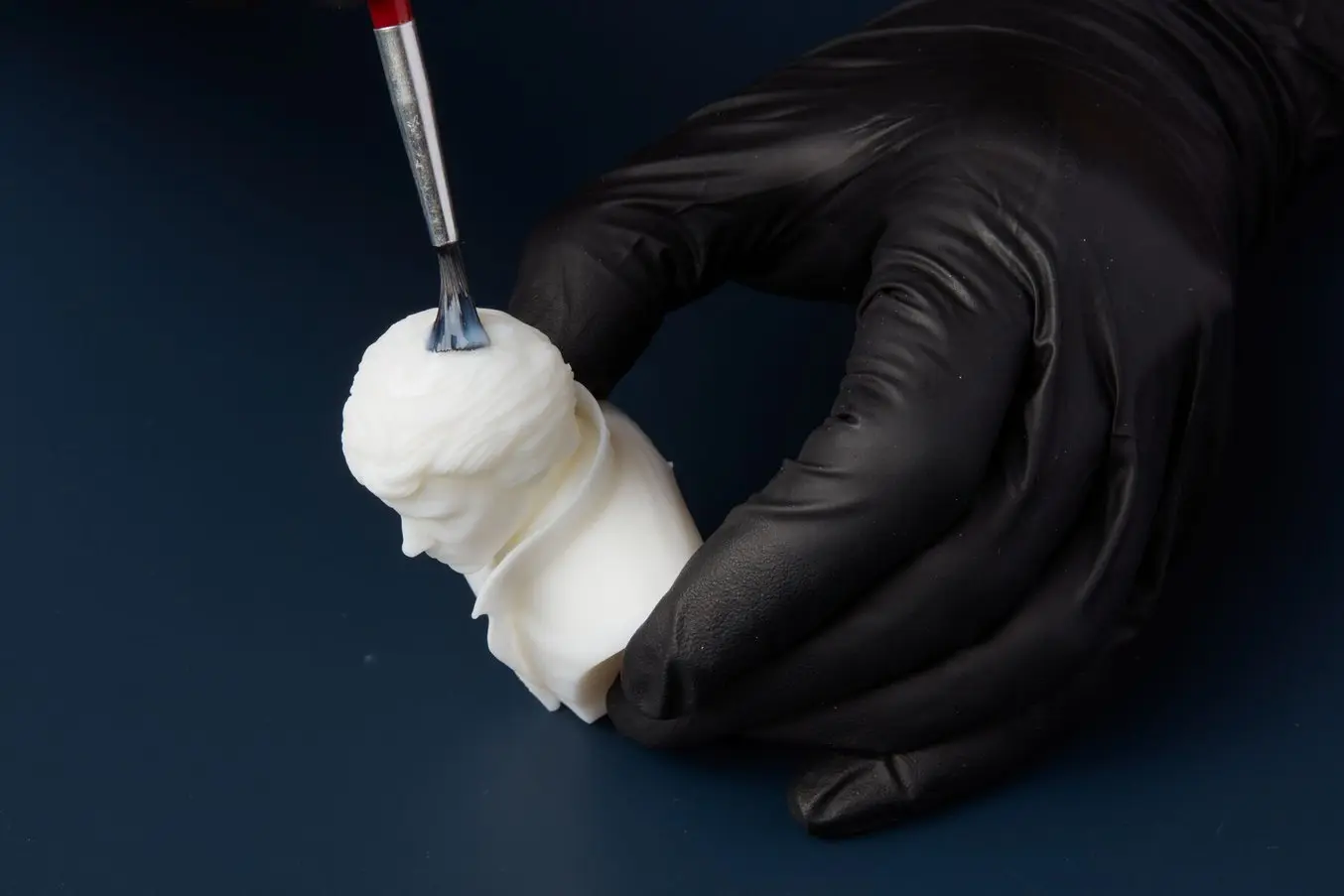
Priming a 3D printed miniature before painting.
You can finish a 3D printed figurine in whatever way supports the end goal of your 3D print. Many models look great straight out of the printer, but you can enhance your miniatures by painting them.
Before you paint, remove all support structures from your 3D printed figurines, and then sand the figurines to eliminate support-structure marks. The amount of sanding and polishing will depend on the object’s finish. For FDM prints, you may have to do some extra sanding to reduce the “staircase” effect of layer lines, while SLA prints should have a smooth surface right away.
After you sand your 3D miniature, we recommend applying a primer. Choosing the right primer will help your 3D printed miniature achieve a professional-grade finish.
See why priming makes painting 3D printed parts effortless and helps create a flawless final surface.
Types of Paint for Your 3D Miniature
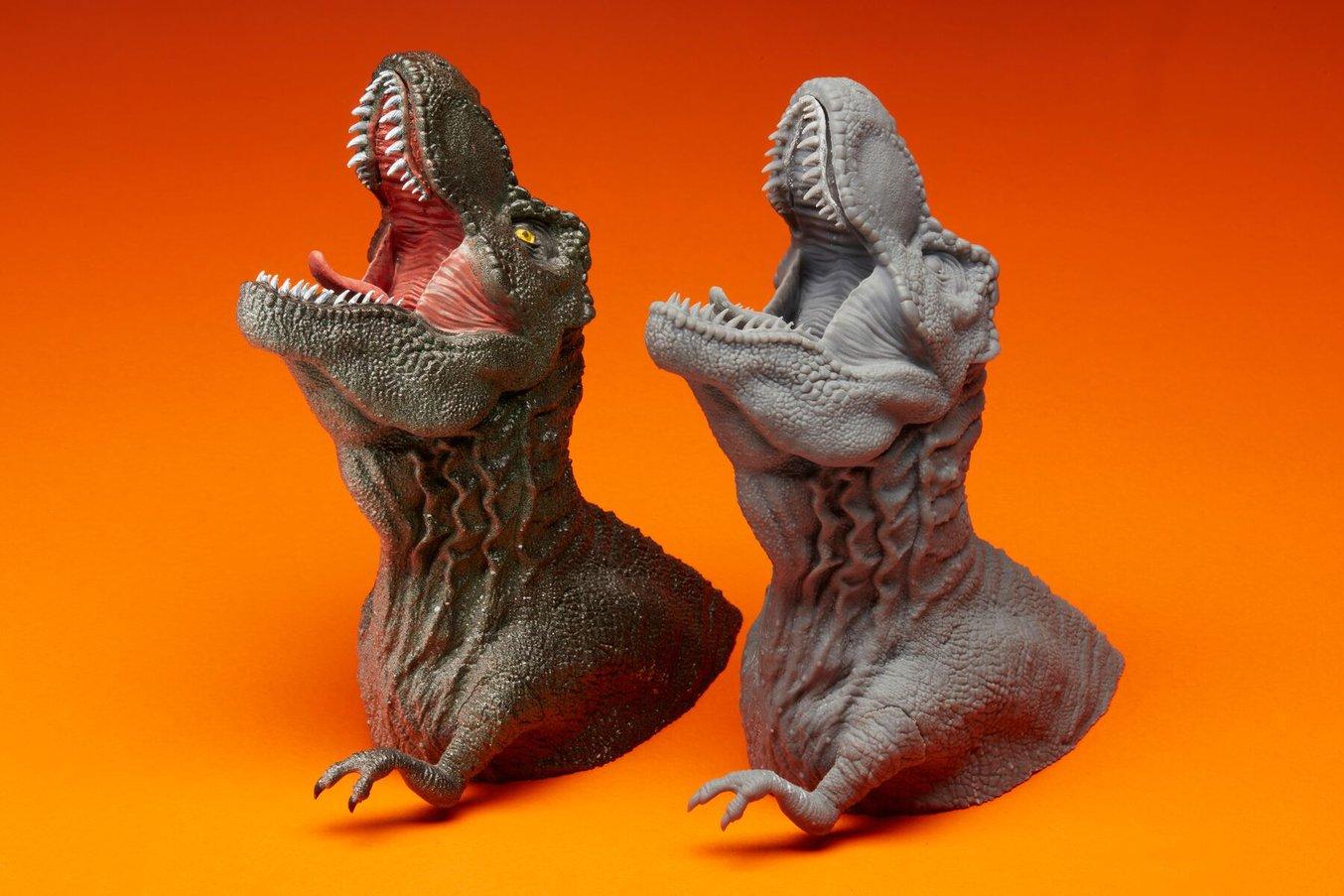
Side by side comparison on the before and after painting a 3D printed dinosaur miniature.
For detailed hand painting of your 3D printed miniature, acrylic paint is a versatile option. Acrylic paint usually binds well to plastic, but always check that the paint you have selected lists “plastic” or “multisurface” functionality, and always prime before you paint.
Spray paint, when applied correctly, can also give your custom miniature a smooth, glossy, and consistent finish. Your spray paint finish can approach professional quality if you apply a good primer and a thick undercoat for color consistency. Always finish with a blemish-resistant topcoat.
See how to transform your miniature from a simple 3D print to a colorful model ready to display with spray painting.
Sourcing 3D Models for Miniatures
3D printing always starts with a digital model. You can download a free or paid miniature model, design the model yourself, or even scan an existing object and turn it into a 3D file.
Miniature Model Files to Download
If you are at the beginning of your 3D printing journey, downloading premade designs can make printing easy. Huge online communities exist around gaming miniatures, such as Dungeons & Dragons figurines. Checking communities like Pinshape, MyMiniFactory, Cults, or Thingiverse is a great way to find free 3D miniature model designs for your own prints.
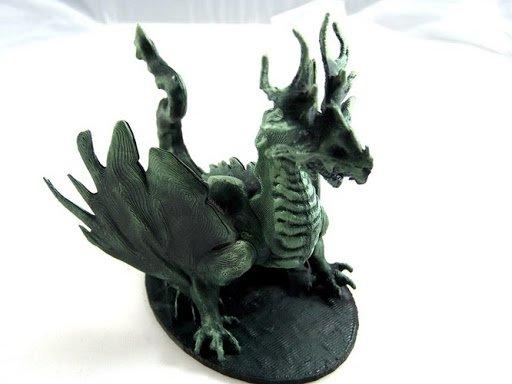
Forest Dragon 3D model, available for free download in Pinshape (Design by Dutchmogul).
Design Software for 3D Printing Miniatures
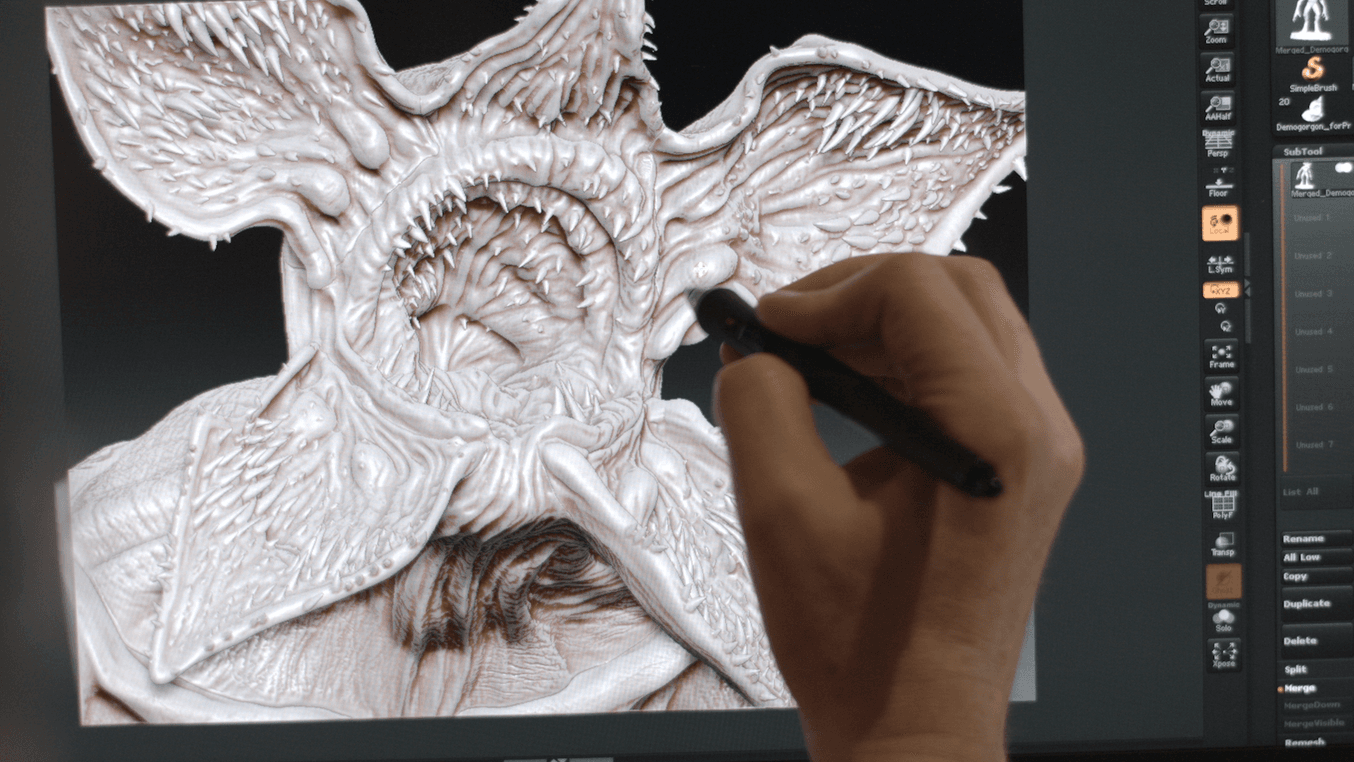
Aaron Sims Creative creating the Stranger Things’ Monster digital 3D assets for 3D printing.
The right 3D modeling software will help you design your own custom miniatures that are ready for 3D printing. If you are creating miniatures, you need detailed design capabilities. CAD software that specializes in video game design or animation often provides the granular tools necessary for creating realistic miniatures.
For example, ZBrush is a digital sculpting tool that combines multiple artistic techniques to create high-resolution models. Users mainly design for movies, games, and animations on ZBrush, making it ideal for realistic figurines. You can learn more about how ZBrush is used for digital sculpting, modeling, and rapid visualization in this webinar.
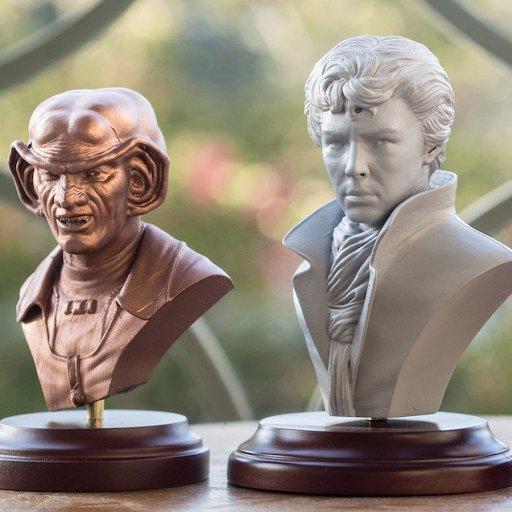
Powerful Tools, Seamlessly Integrated: One-Click 3D Printing for Digital Sculptors
ZBrush gives artists the freedom to push the limits of digital modeling. Until recently, the power to bring complex concepts beyond the computer screen has been inaccessible and cost-prohibitive.
Scanning Your Miniatures for 3D Printing
A custom 3D print does not need to be based on a completely original digital design. Instead, you can also 3D scan an existing object. There are many scanning options available, from low-cost depth-sensing cameras and photogrammetry to high-definition professional scanners.
Before 3D printing a part, you’ll often need to adapt, optimize, and finalize 3D scans. With Meshmixer, it’s not only possible to optimize a triangle mesh but also to resculpt entire sections, stylize the model, or add useful features to it.
Get Started with 3D Printing Miniatures
Whether you are a professional sculptor, a model maker, an enthusiastic hobbyist, or a gamer, SLA 3D printing is an ideal tool to bring hyper-realistic digital models to life in a matter of hours, right on your desktop.
Start 3D printing your own custom miniatures and figurines with the Form 3 with incredible detail at an affordable price point, and bring your biggest ideas to life with the Form 3L.