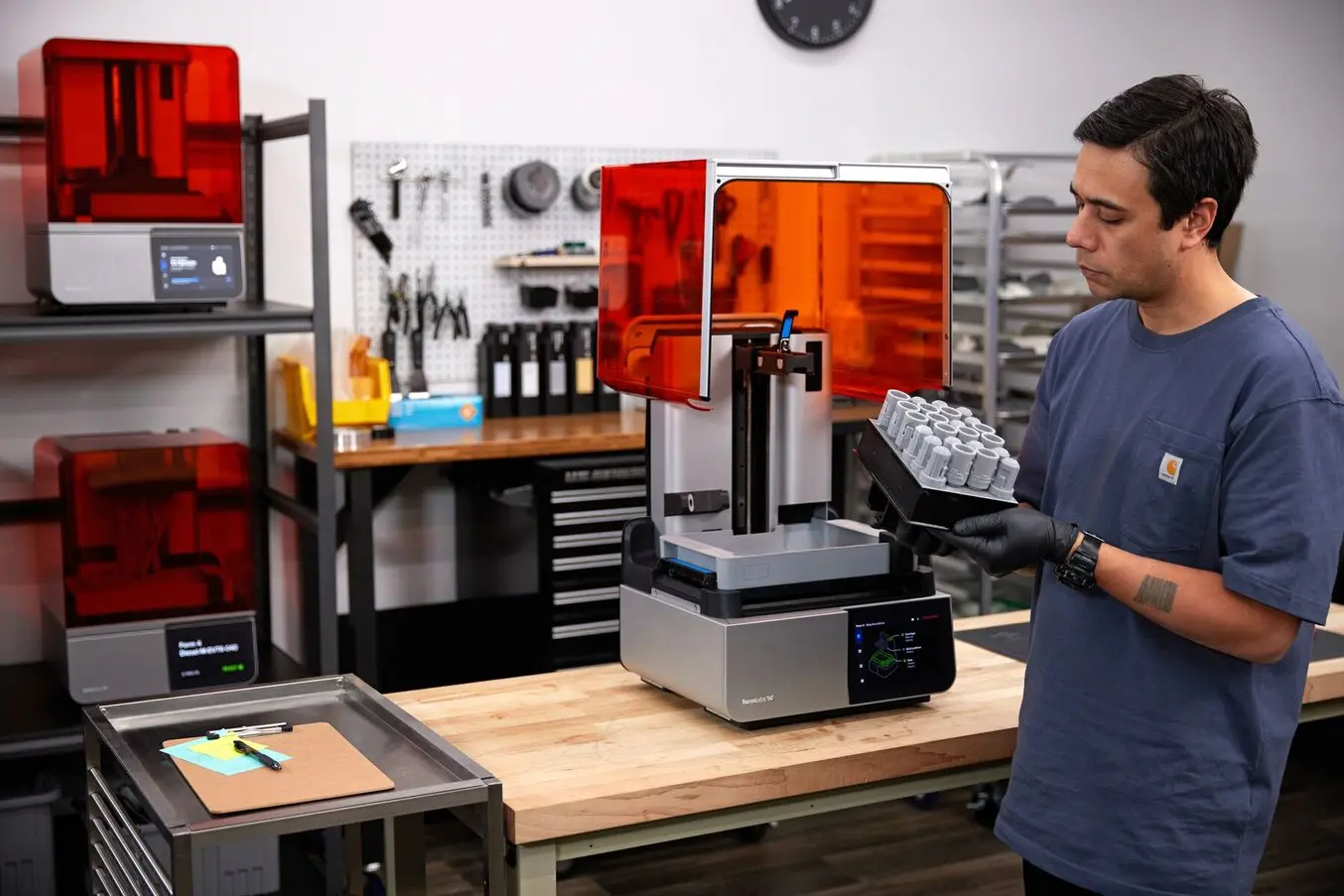
In-house 3D printing is a versatile solution for a wide range of applications, from high-resolution models to rapid prototyping, rapid tooling for traditional production processes, manufacturing aids, and even end-use parts in manufacturing.
When you consider investing in a 3D printer, however, viability typically boils down to a simple question: does it make economic sense for your business? How much does a 3D printer cost and how much time and cost can you actually save with it for your business?
3D printer prices range from about $200 to $500,000+ depending on the printing process, materials, and the level of sophistication of the 3D printing solution.
In this guide, we’ll walk you through the 3D printing costs for different technologies, compare outsourcing with in-house production, lay out the various factors you should account for to calculate cost per part, and look at considerations beyond cost when comparing various 3D printing solutions and other production methods.
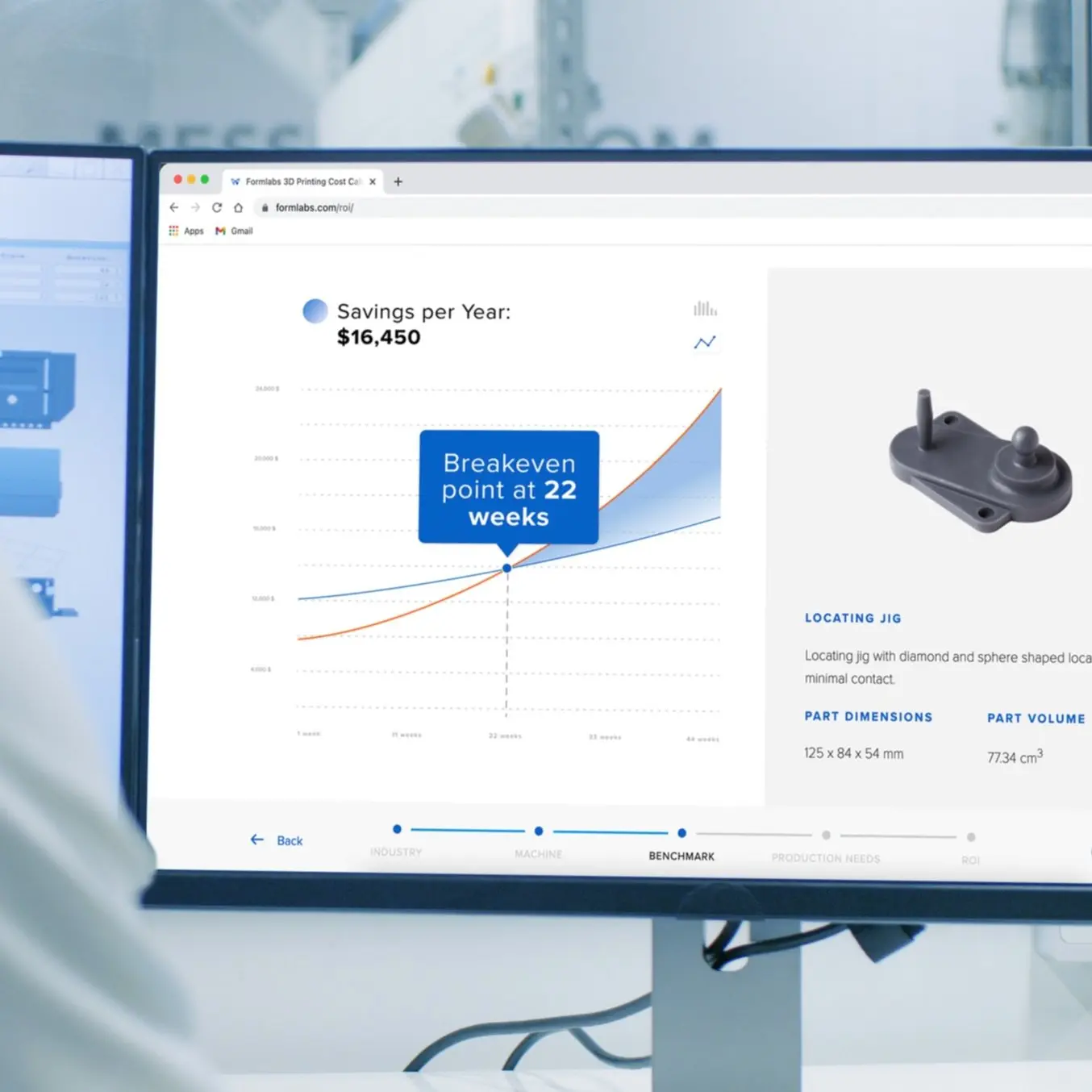
Calculate Your Time and Cost Savings
Try our interactive ROI tool to see how much time and cost you can save when 3D printing on Formlabs 3D printers.
Cost and Considerations for Different Types of 3D Printing Processes
Plastic 3D Printer Costs
The three most established plastic 3D printing processes today are fused deposition modeling (FDM), stereolithography (SLA), and selective laser sintering (SLS).
Each 3D printing technology has its pros and cons — watch our video below for a quick comparison or check out our in-depth FDM vs. SLA vs. SLS guide.
3D printer prices have dropped significantly in recent years, and today, all three technologies are available in compact, affordable systems.
As a rule of thumb, FDM 3D printers will create the cheapest parts if you’re printing only relatively simple prototypes in limited numbers. SLA resin 3D printers offer higher resolution, better quality, and a wide variety of 3D printing materials at a slight premium, but the difference quickly diminishes when you print complex designs or larger batches due to the less labor-intensive post-processing. Lastly, SLS 3D printing is the most cost-effective process for producing medium to large volumes of high-quality functional parts.
Comparing the overall cost of different 3D printers goes beyond sticker prices -- these won’t tell you the full story of how much a 3D printer costs and how much your printed part will cost. 3D printing material and labor costs have a significant influence on cost per part, depending on the application and your production needs.
Let’s look at all the different factors and costs for each process.
Fused Deposition Modeling (FDM)
FDM, also known as fused filament fabrication (FFF), is a printing method that builds parts by melting and extruding thermoplastic filament, which a printer nozzle deposits layer by layer in the build area.
FDM is the most widely used form of 3D printing at the consumer level, fueled by the emergence of hobbyist 3D printers. Professional and industrial FDM printers are, however, also popular with professionals.
The lowest cost 3D printers are almost exclusively FDM printers. Prices for the cheapest entry-level DIY FDM 3D printer kits start at around $200. However, most of these models are more like toys or DIY projects themselves that require you to spend a considerable amount of time assembling, tweaking, and calibrating the printer. Print quality is highly dependent on the success of these steps and still, these machines will require you to do repairs and regular maintenance to keep them running, so they are only recommended for anyone with an (in progress) engineering degree and lots of time and patience.
Hobbyist FDM 3D printers which cost around $500-$1,500 might come as a kit or assembled, require slightly less tweaking, but they still share much of the same disadvantages as the lowest-cost 3D printers. Some models closer to the top of this range will offer bigger build volumes and also more material options beyond low-temperature materials like PLA.
Professional FDM 3D printers start around $2,000, and large-format professional FDM printers start around $4,000, while the most advanced industrial FDM printers can easily cost more than $15,000. Most of these printers will come assembled and calibrated out of the box, or they can auto-calibrate themselves. Printers in this category offer better print quality, a wider range of materials, larger build volumes, better reliability, and are easier to use and maintain. Unlike lower-cost printers, manufacturers of professional 3D printers also offer customer support to troubleshoot issues.
Regarding materials, FDM 3D printing material costs range from around $20 to $150/kg for most standard and engineering filaments and $100-200/kg for support materials.
Lastly, FDM printing can be highly labor-intensive. Many designs, especially complex models, require support structures for successful printing, which need to be removed manually or by dissolving the structures in case of soluble supports. To obtain a high-quality finish and remove layer lines, parts require lengthy manual post-processing, such as sanding.
Stereolithography (SLA)
SLA 3D printers use a laser to cure liquid resin into hardened plastic in a process called photopolymerization. SLA is one of the most popular processes among professionals due to its high resolution, precision, and material versatility.
SLA parts have the highest accuracy, the clearest details, and the smoothest surface finish of all plastic 3D printing technologies, but the main benefit of SLA lies in its versatility. SLA resin formulations offer a wide range of optical, mechanical, and thermal properties to match those of standard, engineering, and industrial thermoplastics.
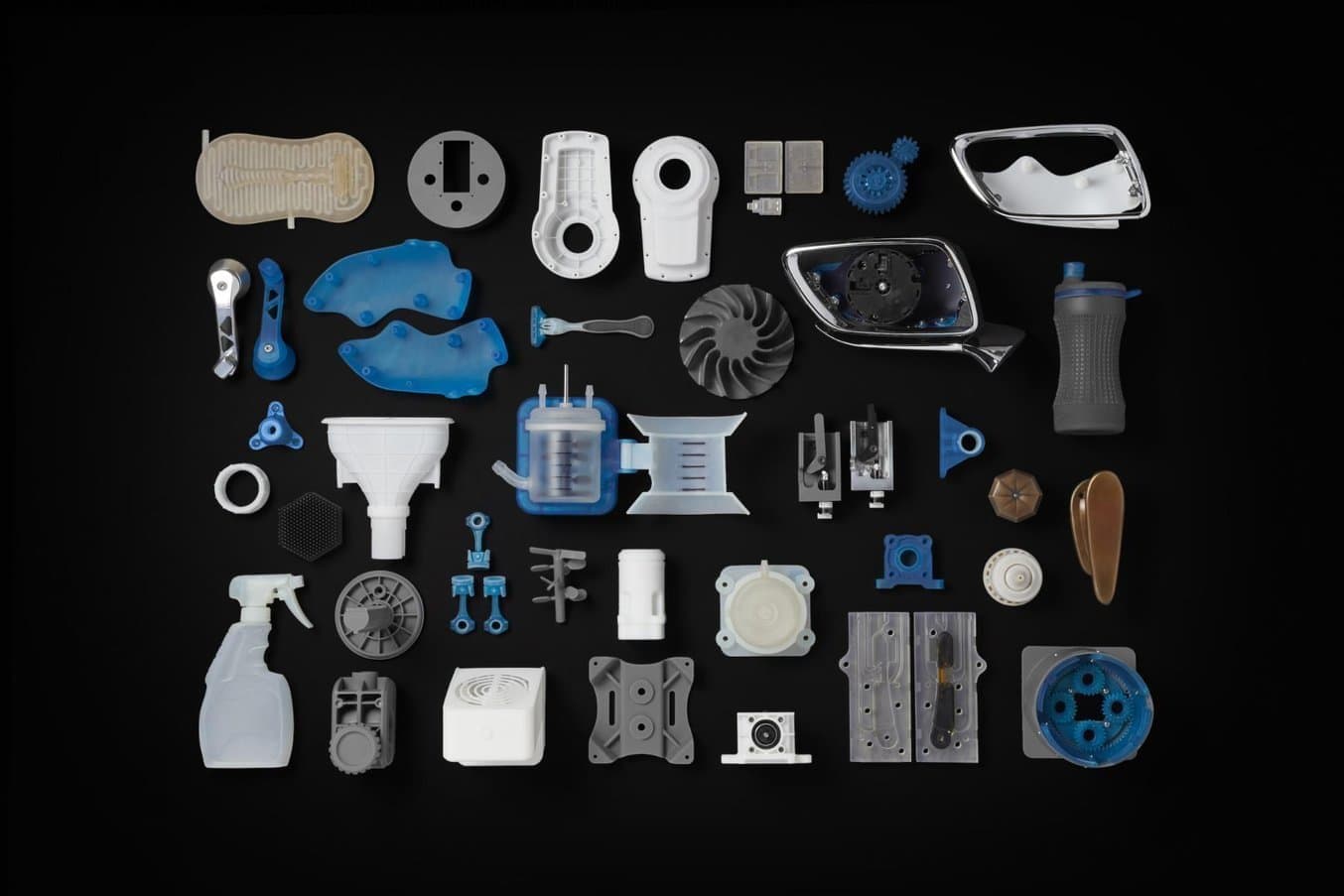
SLA 3D printing offers a wide range of materials for a variety of applications.
While SLA technology used to be available only in large, complex industrial 3D printers that cost more than $200,000, the process has become much more accessible.
At the lower end of the range, low-cost LCD 3D printers are available for $200 to $1000. These machines might be suitable for hobbyists or beginners, but they require calibration and fine-tuning for each resin type, and they are generally not reliable or durable, which will often lead to higher costs in terms of maintenance, sunk time, failed parts, and wasted material.
Professional resin 3D printers include SLA technologies including laser-powered SLA, DLP, or LCD/MSLA. Prices are generally in the $2000 to $10,000 range, while large-format resin 3D printers are typically more in the $5,000 to $25,000 range. There are many factors that influence the price in this range, from the more reliable and powerful light sources (whether LEDs, lasers, or projectors) to the light processing solution, overall build quality, software, accessories, and service plan.
With the Formlabs Form 3+, businesses now have access to industrial-quality SLA for just $2,499, while the latest generation blazing fast Form 4 MSLA 3D printer starts at $3,499. For printing bigger parts, the large-format resin 3D printer Form 4L starts at $9,999.
Professional resin 3D printers will come assembled and calibrated out of the box. They’re reliable also for production and require barely any maintenance. Customer support is also readily available to troubleshoot issues in the unlikely event that something goes wrong.
In terms of material costs, SLA resins cost around $79-$250/L for most standard and engineering resins, with discounts available when printing higher volumes. Low-cost options exist, but often contain potentially harmful chemicals and have limited options for material properties.
SLA printers are easy to use and many steps of the workflow like washing and post-curing can be mostly automated to reduce labor needs. Printed parts have a high-quality finish right off the printer and require only simple post-processing to remove support marks.
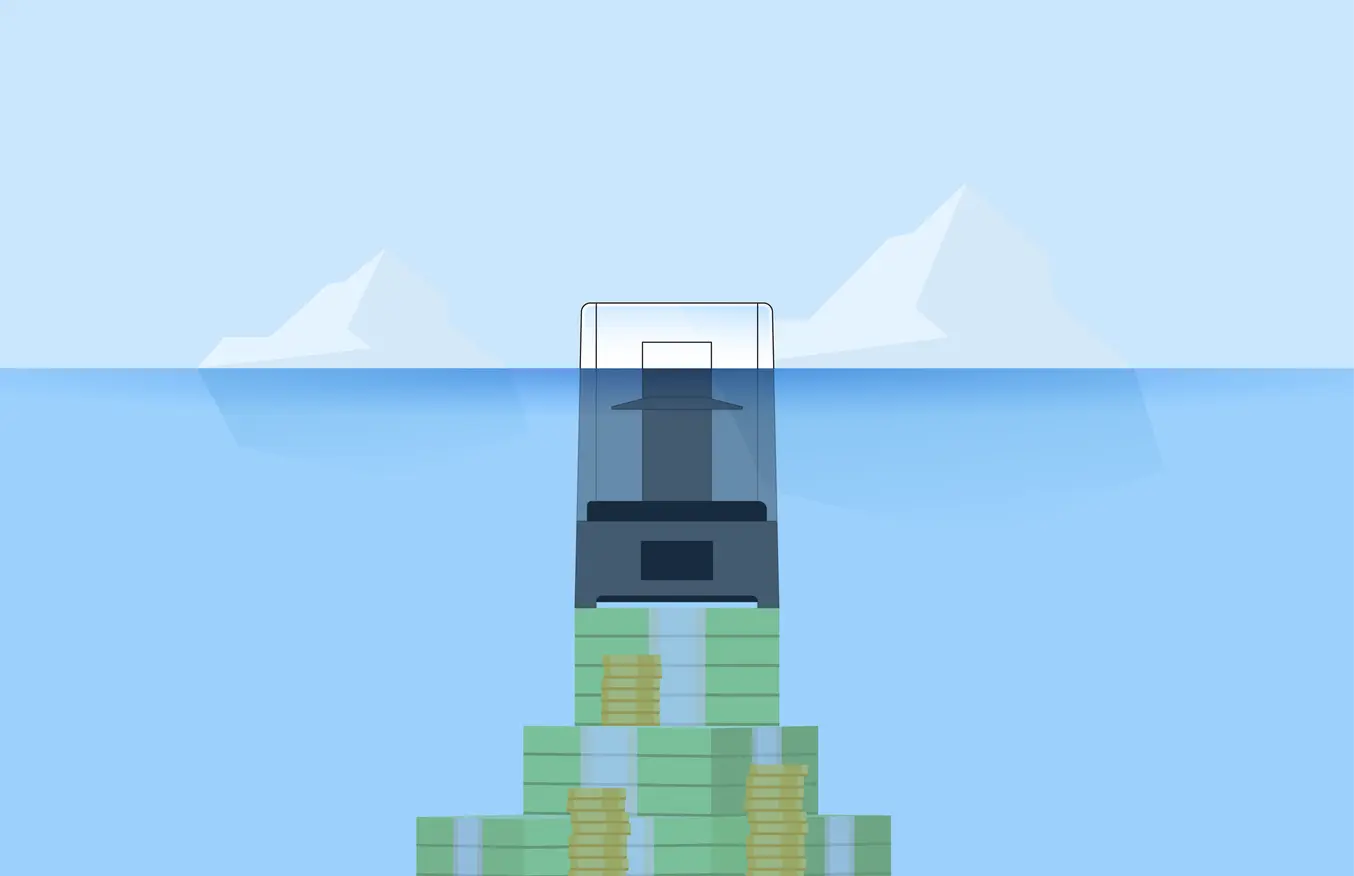
Uncovering the Hidden Costs of Low-Cost Resin 3D Printers
Compare costs and experience of low-cost resin printer and Formlabs Form 3+ SLA printer, revealing stark differences in hidden expenses.
Selective Laser Sintering (SLS)
SLS 3D printers use a high-powered laser to fuse small particles of polymer powder. The unfused powder supports the part during printing and eliminates the need for dedicated support structures, which makes SLS ideal for complex geometries, including interior features, undercuts, thin walls, and negative features.
Parts produced with SLS printing have excellent mechanical characteristics, with strength resembling that of injection-molded parts. As a result, SLS is the most common plastic 3D printing process for industrial applications.
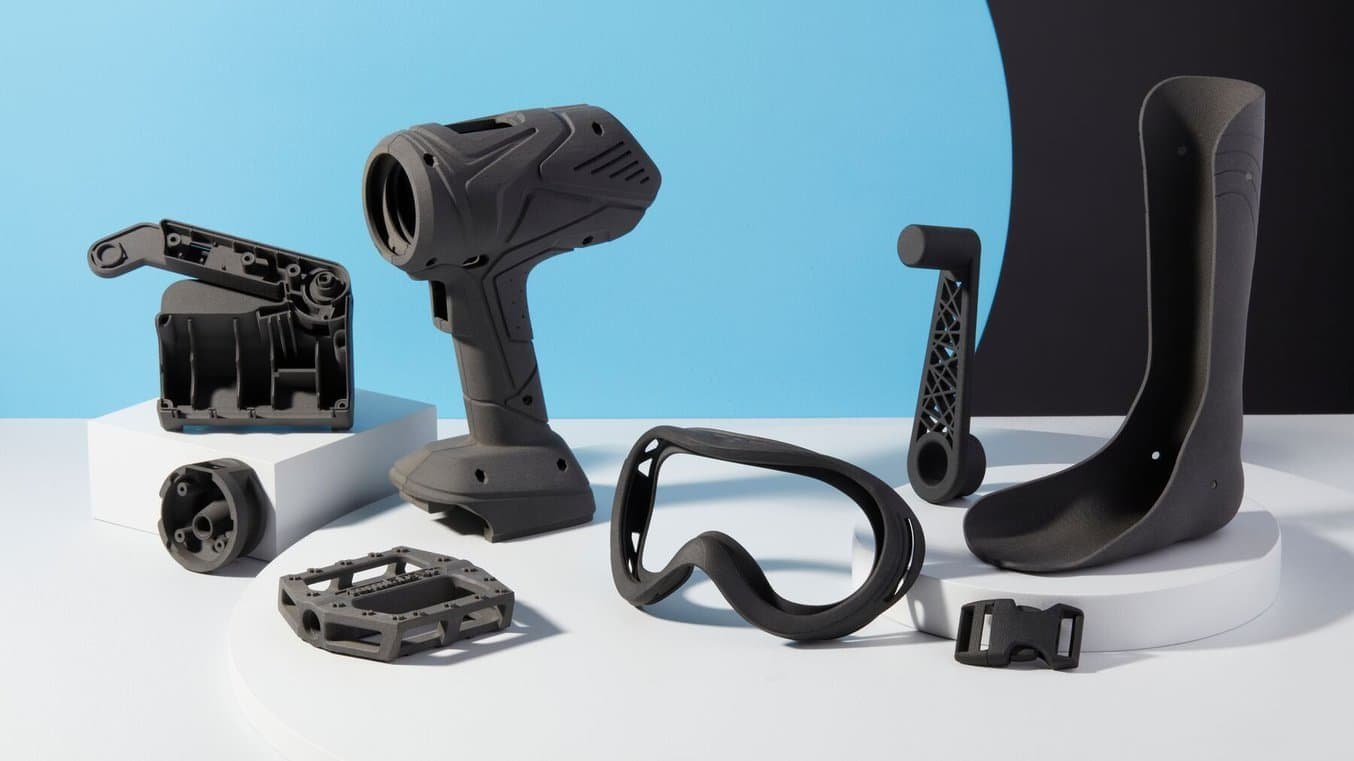
SLS nylon parts are ideal for a range of functional applications, from engineering consumer products to healthcare.
Just like SLA, SLS used to be only available in large-format, complex 3D printing systems starting at about $200,000. With Formlabs’s Fuse 1+ 30W SLS printer, businesses can now access industrial-quality SLS starting under $30,000 (printer and depowdering kit) and under $60,000 for a complete setup that includes a compact and efficient powder management station and a fully automated cleaning and polishing solution.
Also similar to SLA printers, SLS printers will come assembled and calibrated out of the box. They are reliable and developed for 24/7 production, and come with advanced training and fast customer support.
Nylon materials for SLS printing cost around $100/kg, but bulk pricing discount can reduce it by more than 50% for production volumes. SLS requires no support structures, and unfused powder can be reused, which also lowers material costs.
SLS is the least labor-intensive plastic 3D printing process in a production setting as parts have great quality right out of the printer and require only simple cleaning to remove excess powder.
Metal 3D Printers Costs
Beyond plastics, there are multiple 3D printing processes available for metal 3D printing.
-
Metal FDM
Metal FDM printers work similarly to traditional FDM printers, but extrude metal rods held together by polymer binders. The finished “green” parts are then sintered in a furnace to remove the binder.
-
Selective Laser Melting (SLM) and Direct Metal Laser Sintering (DMLS)
SLM and DMLS printers work similarly to SLS printers, but fuse metal powder particles together layer by layer using a laser instead of polymers. SLM and DMLS 3D printers can create strong, accurate, and complex metal products, making this process ideal for aerospace, automotive, and medical applications.
While metal 3D printer prices have also begun to decrease, with costs ranging from $100,000 to $1 million, these systems are still not accessible to most businesses.
Alternatively, SLA 3D printing is well-suited for casting workflows that produce metal parts at a lower cost, with greater design freedom, and in less time than traditional methods.
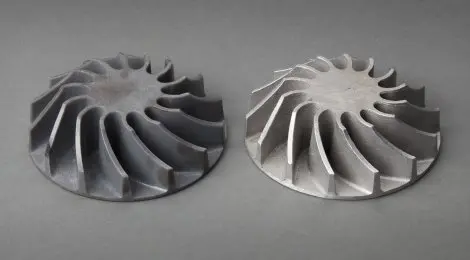
Fabricating Metal Parts With 3D Printing
Get design guidelines for creating 3D printed patterns, walk through the step-by-step direct investment casting process, and explore guidelines for indirect investment casting and sand casting.
3D Printer Price Comparison by Process
The various plastic and metal 3D printing processes have unique qualities that make them suitable for different applications. Here's a quick breakdown.
Fused Deposition Modeling (FDM) | Stereolithography (SLA) | Selective Laser Sintering (SLS) | Metal FDM | Selective Laser Melting (SLM) and Direct Metal Laser Sintering (DMLS) | |
---|---|---|---|---|---|
Resolution | ★★☆☆☆ | ★★★★★ | ★★★★☆ | ★★☆☆☆ | ★★★★☆ |
Accuracy | ★★★★☆ | ★★★★★ | ★★★★★ | ★★★☆☆ | ★★★★★ |
Surface Finish | ★★☆☆☆ | ★★★★★ | ★★★★☆ | ★★☆☆☆ | ★★★★☆ |
Throughput | ★★★★☆ | ★★★★☆ | ★★★★★ | ★★★☆☆ | ★★★★☆ |
Complex Designs | ★★★☆☆ | ★★★★☆ | ★★★★★ | ★★★☆☆ | ★★★★★ |
Ease of Use | ★★★★★ | ★★★★★ | ★★★★☆ | ★★★★☆ | ★☆☆☆☆ |
Build Volume | Up to 300 x 300 x 600 mm (desktop and benchtop 3D printers) | Up to 353 x 196 x 350 mm (desktop and benchtop 3D printers) | Up to 165 x 165 x 300 mm (benchtop industrial 3D printers) | Up to 300 x 200 x 200 mm | Up to 400 x 400 x 400 mm |
Price Range | Budget FDM printers and 3D printer kits start at around $200. Professional desktop FDM printers range from $2,000 to $8,000, and industrial systems are available from $15,000. | Low-cost resin 3D printers are available for $200 to $1000, professional SLA 3D printers are in the $2,500 to $10,000 range, and large-format resin 3D printers are in the $5,000 to $25,000 range. | Benchtop industrial SLS 3D printers start just under $30,000 for the printer and $60,000 for the entire ecosystem, including powder management and cleaning stations. Traditional industrial SLS printers start at around $200,000. | Metal FDM printers start from $100,000, but the full solution that includes a furnace goes well beyond that. | DMLS/SLM solutions start around $200,000. These printers also come with stringent facility requirements which may increase the costs further. |
Material Costs | $20-$150/kg for most standard and engineering filaments, and $100-200/kg for support materials. | $30-$250/L for most standard and engineering resins. | $50-$150/kg for nylon. SLS requires no support structures, and unfused powder can be reused, which lowers material costs. | Depends on the material and the technology. Significantly higher than plastics. | Depends on the material and the technology. Significantly higher than plastics. |
Labor Needs | Manual support removal (can be simplified in some cases with soluble supports). Lengthy post-processing is required for a high-quality finish. | Washing and post-curing (both can be mostly automated). Simple post-processing to remove support marks. | Simple cleaning to remove excess powder. | Washing and sintering (both can be mostly automated). Optionally machining and other surface treatments. | Stress relief, support removal, heat treatment, as well as machining, and other surface treatments. |
Materials | Standard thermoplastics, such as ABS, PLA, and their various blends. | Varieties of resin (thermosetting plastics). Standard, engineering (ABS-like, PP-like, silicone-like, flexible, heat-resistant, rigid), castable, dental, and medical (biocompatible). | Engineering thermoplastics, typically nylon and its composites (nylon 12 is biocompatible + compatible with sterilization). | Stainless steel, tool steel, inconel, copper, titanium. | Stainless steel, tool steel, titanium, cobalt chrome, copper, aluminum, nickel alloys. |
Ideal applications | Basic proof-of-concept models, low-cost prototyping of simple parts. | Highly detailed prototypes requiring tight tolerances and smooth surfaces, molds, tooling, patterns, medical models, and functional parts. | Complex geometries, functional prototypes, short-run or bridge manufacturing. | Strong and durable parts, tooling, and manufacturing aids. | Strong, durable parts with complex geometries; ideal for aerospace, automotive, and medical applications. |
Cost Per Part: Calculating 3D Printing Costs
Calculating cost per part requires accounting for the costs of equipment ownership, material, and labor. It’s helpful to understand the factors that influence each of these cost components, and the questions to ask to evaluate alternative production methods and uncover hidden costs.
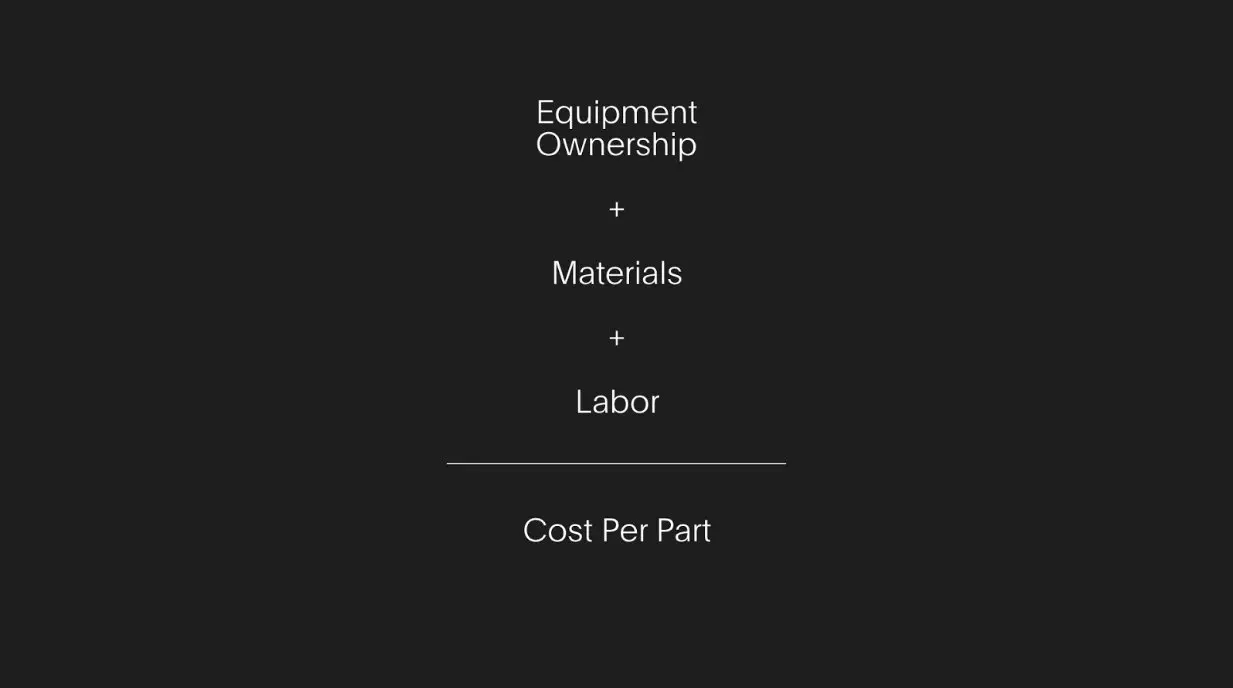
Equipment Ownership
Fixed costs, such as the 3D printer cost, service contracts, installation, and maintenance, together make up the equipment ownership cost. These expenses occur regardless of whether your 3D printer stands idle or produces dozens of parts a week.
Distribute equipment ownership costs over individual parts by adding up all of the forecasted fixed costs over the lifetime of the machine and divide the sum by the number of parts that it is expected to produce. As a rule of thumb, the higher the productivity and utilization of your 3D printer, the lower the equipment ownership cost on a per-part basis.
Desktop 3D printers have achieved tremendous progress in recent years in lowering equipment ownership costs. With a price point 10-100 times lower than traditional industrial 3D printers and the capability to produce thousands of parts over their lifetime, the equipment ownership cost can become negligible.
Questions to ask:
-
Are there installation, training, or further initial expenses beside the cost of the machine?
-
Is there a (mandatory) service contract? What does it include?
-
Beyond the machine, what accessories and tools are required to create final parts?
-
What are the maintenance needs of the machine within the normal range of activity? What’s the expected annual cost of maintenance? How does it change if production levels rise?
Materials and Consumables
Raw 3D printing materials and other consumables required to create parts are variable costs. These costs are highly dependent on the number of parts you’re producing.
Measure material cost by calculating the amount of 3D printing material that’s required to create a single part, and multiply it by the cost of the material. Calculate in waste and any other consumables that are needed. While equipment ownership costs decrease as production grows, material costs for 3D printing tend to flatten out quickly. To make 3D printing cost-efficient for higher volumes, some manufacturers like Formlabs offer a substantial volume discount on materials.
Make sure to clarify what materials you’ll need to create the given parts, as the cost of consumables for 3D printing varies. Also note that some 3D printers only work with proprietary materials, and thus limit your third-party material options.
Questions to ask:
-
What is the cost of each type of 3D printing material?
-
How much material is required to create a given part, including waste?
-
What’s the shelf life of the materials?
-
Are there other consumables required to create the parts?
-
Can the machine work with third-party materials?
Labor
While 3D printing can replace the complex workflows of traditional manufacturing methods and lead to substantial time savings, depending on the 3D printing technology, it can still be a fairly labor-intensive process.
Professional desktop 3D printers are generally optimized for ease of use. DIY 3D printers and hobbyist printers often require more tinkering to get the settings dialed in, whereas regular maintenance or changing materials on traditional industrial machines can involve time-consuming tasks that require a skilled operator.
Post-processing workflows vary by 3D printing process, but in most cases include cleaning parts and removing supports or excess material. There are solutions to automate some of these tasks; for example, Form Wash and Form Cure simplify the washing and post-curing workflow for SLA 3D printers, and Fuse Sift offers a turnkey post-processing and powder recovery system for Fuse Series SLS printers.
To achieve high-quality parts, more advanced processes like SLA and SLS don’t require time-consuming steps, but FDM parts will need lengthy manual post-processing to improve the quality and remove layer lines.
Questions to ask:
-
What is the entire workflow for producing parts? What are the specific steps required to set up a print, change materials, and post-process parts?
-
How much time does it take to post-process a given part?
-
Are there any tools or devices available to automate some of these tasks?
Outsourced Production vs. In-House 3D Printing
Outsourcing production to service bureaus or labs is recommended when you require 3D printing only occasionally, and for parts that are large or call for non-standard materials. Bureaus generally have several 3D printing processes in-house such as SLA, SLS, FDM, and metal 3D printers. They can also provide advice on various materials and offer value-added services such as design or advanced finishing.
The main downsides of outsourcing are cost and lead time. One of the greatest benefits of 3D printing is its speed compared to traditional manufacturing methods, which quickly diminishes when an outsourced part takes multiple days or even weeks to arrive. With growing demand and production, outsourcing also rapidly becomes expensive.
Desktop 3D printers are great when you need parts quickly. Depending on the number of parts and printing volume, investment into a professional 3D printer can break even within months.With desktop and benchtop machines, you can pay for just as much capacity as your business needs, and scale production by adding extra units as demand grows without making a significant investment in a large-format 3D printer. By using multiple 3D printers, you also get the flexibility to print parts in different materials simultaneously. Service bureaus can still supplement this flexible workflow for larger parts or unconventional materials.
Try our interactive 3D printing ROI calculator to see how much time and cost you can save when 3D printing on Formlabs 3D printers compared to outsourcing.
Considerations Beyond Direct Costs
Investment, materials, and labor costs are relatively easy to calculate. But what about indirect costs and factors that are hard to quantify, but still influence your business? Let’s look at some of the key considerations when comparing desktop 3D printing to outsourcing or other production methods.
Time savings: What if you could bring products to market months faster? Or cut the lead time for your products by days or weeks? 3D printing simplifies traditional prototyping and production workflows, helping you to save time and outpace the competition.
Better results: 3D printing allows you to create more iterations, fail faster, and achieve better end products. Finding and fixing design flaws early also helps to avoid costly design revisions and tooling changes in production.
Communication: Having high-quality prototypes and parts allows you to better communicate with customers, clients, suppliers, and other stakeholders. Avoid confusion and costly mistakes.
IP protection: Do you work with sensitive information? Creating parts in-house means you won’t have to give away intellectual property (IP) to third parties, reducing the risks of leaks or IP theft.
3D Printing Cost Calculator
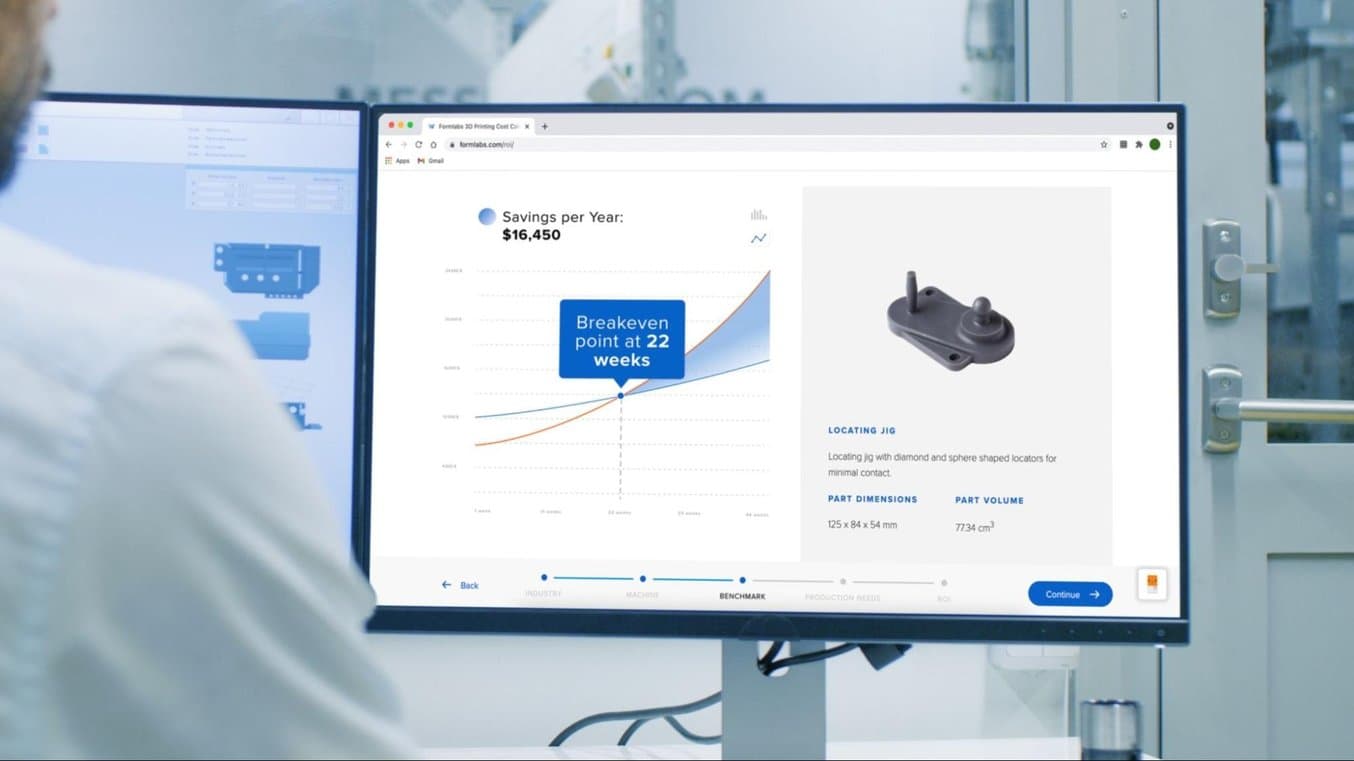
Calculating cost per part, lead time, and comparing alternatives to figure out if a solution makes sense for your business would normally be the strenuous task of creating an elaborate spreadsheet and trying to gather all of the—often hidden—information from a manufacturer.
To skip this hassle, try our simple, interactive 3D printing cost calculator to calculate 3D printing cost and lead time on Formlabs' professional 3D printers, and to compare time and cost savings to other production methods.