
The effects of climate change are being felt across the world, and 3D printing is helping companies evolve to meet the challenge. As regulations regarding water and electricity usage are updated in response to the prolonged droughts, more frequent wildfires, and increased smog, individuals, businesses, and municipalities are scrambling to report accurate data and show improvement in water usage. As the saying goes, if you can’t measure something, you can’t change it. That’s where Next Meters come in.
Next Meters is a manufacturer of connected water metering tools with a mission to educate and reward individuals who conserve water. They create solid-state flow meters that measure water usage by residential, commercial, or municipal customers. Their challenge is creating equipment that can affix to the wide variety of utility applications currently in use. Using multiple Form 2, Form 3+, Form 3L, and Fuse 1 printers, Next Meters has been able to rapidly prototype, improve molding designs, and produce end-use parts for their equipment.
We spoke to Next Meters CMO David Clyde about the water meter market and why 3D printing is the ideal complement to their traditional manufacturing process.
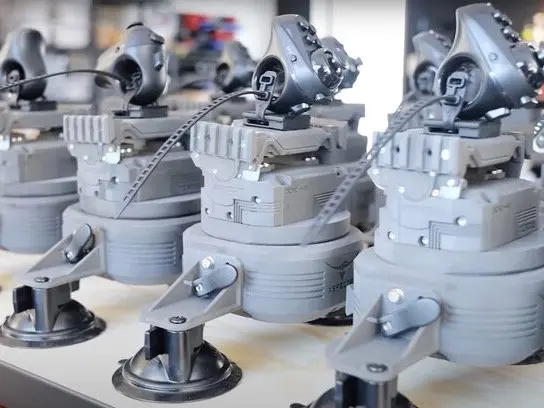
Stress Testing 3D Printed Parts for End-Use Applications
This white paper presents Formlabs 3D printing hardware and material solutions for end-use part production. It documents various users' case studies and includes stress testing results to verify the suitability of 3D printing materials for end-use applications.
Rewarding Those Who Conserve
Historically, water meters have been mechanical, relying on the flow of water to spin gears inside a tube and calculate usage from that flow rate. This presents several problems—multi-unit buildings generally only have one city utility meter, and usage is equally split across all units. This penalizes those who conserve and rewards those who waste. In addition, mechanical meters are less accurate and degrade over time, creating large discrepancies between recorded and actual usage.
Next Meters designs and manufactures extremely accurate and fully connected water meter equipment, like ultrasonic utility flow meters, leak detection sensors, and remote shut off valves. This equipment makes it possible to detect even the smallest losses in water due to issues like cracked pipes or leaky gaskets. Especially in large town or apartment building utility systems, these tiny leaks can add up to massive losses over time, costing the residents money and wasting precious water resources.

A Next Meters specialist examines a system that will soon be fitted with a water meter device printed on the Fuse 1 SLS printer.
“A lot of things are driving the demand for our products. There are new state mandates—California is pushing conservation legislation. They’ve had a drought for many years that’s wreaking havoc on many areas. States are putting laws in place that require tracking for conservation purposes, and people are generally wanting to be more informed on their utility usage.”
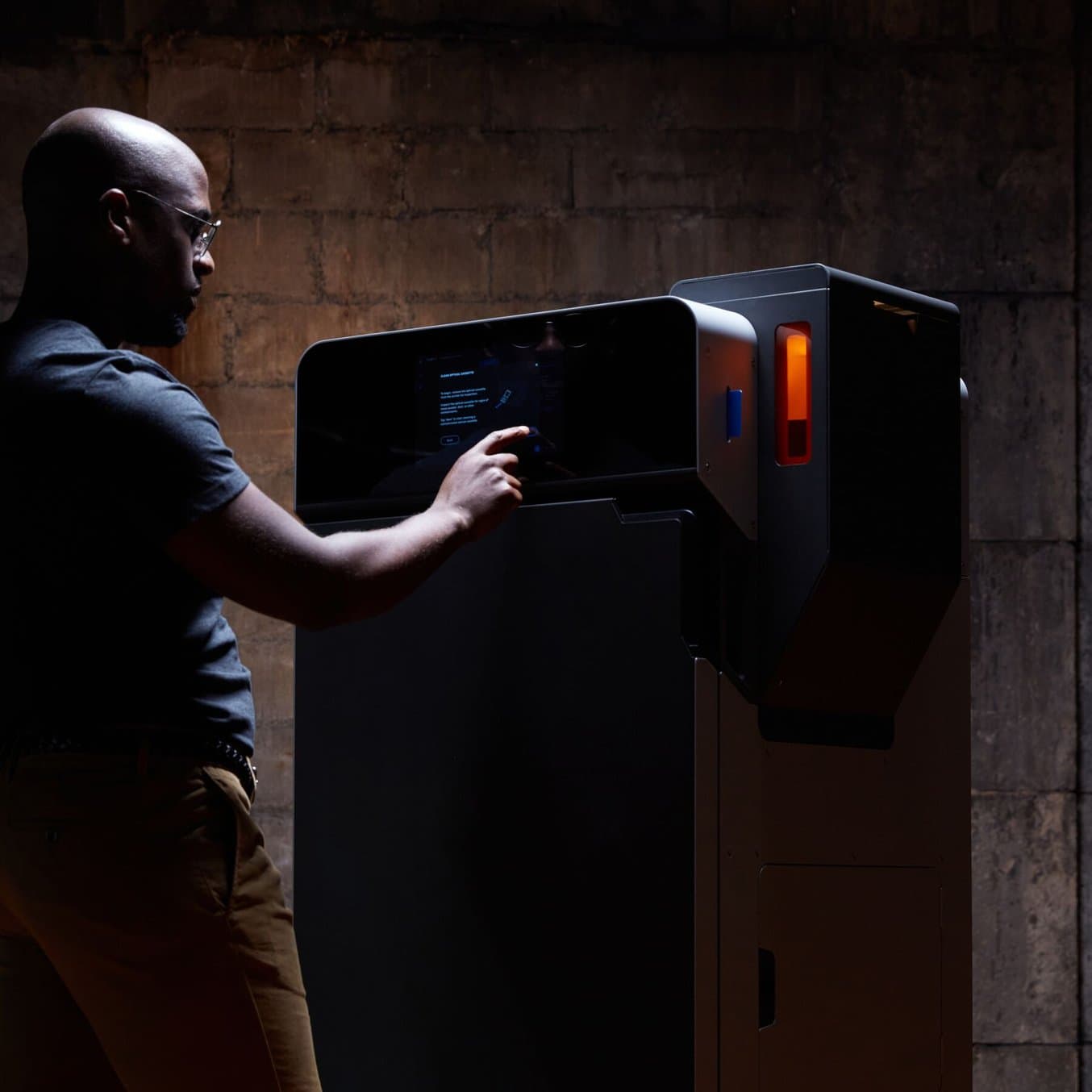
Outsourcing vs. In-House: When Does it Make Sense to Bring SLS 3D Printing In-House?
In this white paper, we evaluate the value proposition of bringing SLS 3D printers in-house, in comparison with outsourcing SLS parts from a service bureau.
One Size Doesn’t Fit All: Meters From the Last 50 Years Need Customization
Recent spike in demand exacerbates the challenge Next Meters already faces—they need to provide flow metering equipment that can mount onto a large variety of different types of water meters, each with a different installation date and OEM. To successfully provide a solution, public or private, Clyde’s team needs to identify which water meter they’re dealing with, and then determine which of their own products will fit, or create and manufacture a new one. As they grew from solely residential to municipal markets, the number of meters they needed to match increased, adding to the challenge.
“As we enter the municipal market, we’re finding many cities have a mix of multiple brands as well as the meter ages. Even in a small town of 3,000 homes, you could see six or seven different meter types. Every meter type is a different shape and size that requires a unique bracket to retrofit with our IoT devices,” says Clyde.
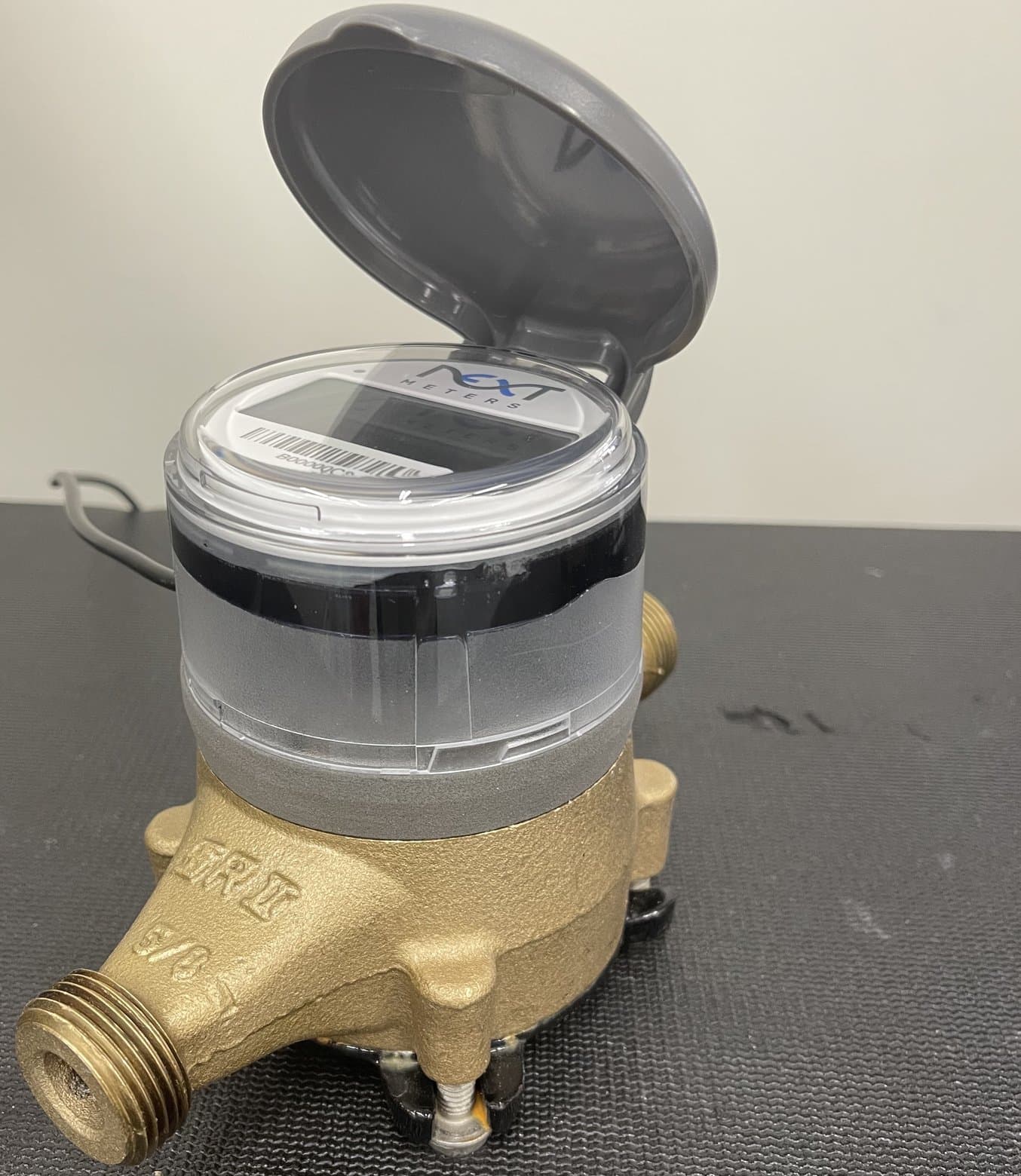
A water meter (clear casing) fitted onto a unique water system spigot (gold plated) via a custom-printed Fuse 1 SLS fixture (grey middle part).
Slow Sculpting, Expensive Tooling
To create their products Next Meters engineers historically started with clay modeling to design the general look of their devices. Once a design looked and felt right, they would move to 3D CAD modeling, and finally send them out to a mold house for a prototype molding.
“Our mechanical engineers were literally sculptors. Carving, putting that into our CAD software, sending it to a sourcing company, sourcing soft tooling, then iterating, all before even testing our prototypes. It was time consuming and expensive,” said Clyde.
One solution was to take existing tools and modify them to accommodate a new product that had very slight differences, but the Next Meter team ran into a roadblock there too. Every time they modified a tool, it weakened, and after modifying several times, it had to be scrapped, even though the cost to make them ranged from $5,000 to $50,000 and could take several months to replace.
Not only were the number of tools in the hundreds, the process to make them was labor-intensive and costly. The timelines for delivering complete solutions were getting pushed back and the company was running up huge costs. Next Meters turned to 3D printing to speed up their iterative process, starting with a Form 2 printer, and later adding a Form 3, Form 3+, and Form 3L. They use Formlabs SLA printers to design a proof of concept for molds, and iterate quickly, taking their design process from months to days.
To CNC these tools, on a good day, would take five to six weeks. Sometimes it took us a year to go from proof of concept design to the first prototype. A year and several hundred thousand dollars in cost. Adopting 3D printing allows us to make those design choices quickly, and only send out for hard tooling after we’ve validated every part.
David Clyde
Injection Molding for the Many, SLS for the Few
Roughly 80% of utility systems in the field belong to a couple major players. The equipment for those can be injection molded efficiently. But what about the 20% of customers left, represented by over a dozen additional small manufacturers? Next Meters still has to provide a total solution to their customers. If a town or city needs to update their metering system and pull usage data to satisfy new regulations, they need everything covered, not just what’s convenient, or the data set is useless.
“It doesn’t make sense for a city to only be able to only read 80%. We need to address the outliers, to provide the customers with a total solution and not a partial solution,” says Clyde.
In addressing the last 20% of the market, Next Meters ran into another challenge. While the SLA printers had sped up their mold design and iteration process, with low production quantities of each part necessary, injection molding would still be prohibitively expensive. Though Next Meters utilized the range of Formlabs resins available on their fleet of SLA machines, the 3D printed resins weren’t able to be used for production parts with the 15 year life span the parts require on average. Next Meters needed a cost-effective solution for producing production parts in small quantities.
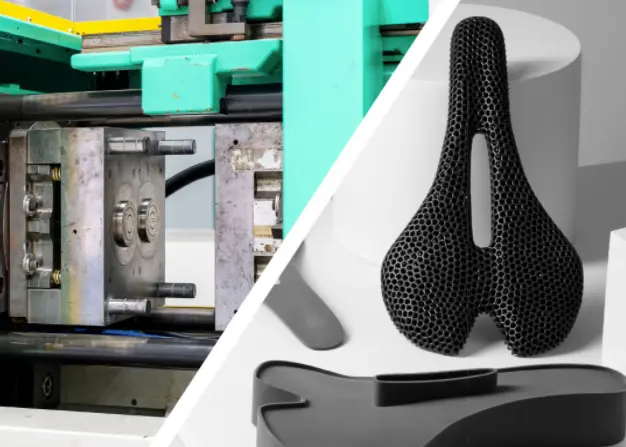
SLS 3D Printing vs. Injection Molding: When to Replace Molded Parts With 3D Printing?
This white paper showcases the cost-dynamics for real-life use cases, and presents guidelines for using SLS 3D printing, injection molding, or both.
In late 2021, Clyde’s team purchased a Fuse 1 selective laser sintering (SLS) 3D printer, a Fuse Sift post processing unit, along with Nylon 12 Powder, then later adding Nylon 11 Powder as well to their material library. They use Nylon 12 Powder for prototyping the brackets that hold the meter together, and Nylon 11 Powder for the parts in the field.
“There are dozens of meter models out there with quantities so low we’d never recover tooling costs. So, for those specific meters, we’re printing the parts on the Fuse 1 as needed. We can now deliver equipment for both the commonly found meters as well as the other 20%, and we can do it much faster and cheaper with the SLS printer,” says Clyde.
Turbulence Ahead: Self-Supported Printing Solves Flow Issues
The Fuse 1 provides another benefit in the self-supporting nature of the print bed. For parts in the ultrasonic water meter itself, friction is the enemy—water needs to flow through the meter uninhibited in order to produce an accurate reading. For complicated parts, Next Meters uses the Fuse 1 so that the part can be built with internal features without supports.
A mold for a complicated part like this would take months to tool and hundreds of thousands of dollars to set up manufacturing, but having in-house SLS capabilities means that Next Meters is able to produce a functional device in only a few days.
“For more complex prints we print them on the Fuse 1, recover them with the Fuse Sift, and then sandblast them. We can get better detail when you don’t have to account for supports, and the parts can slide and interact well together as functional assemblies. In the example of a water meter, with a seven inch flow tube, we can’t be cleaning supports out of that. Bumps from supports would affect the water flow, creating turbulence and messing up the reading”, says Clyde.
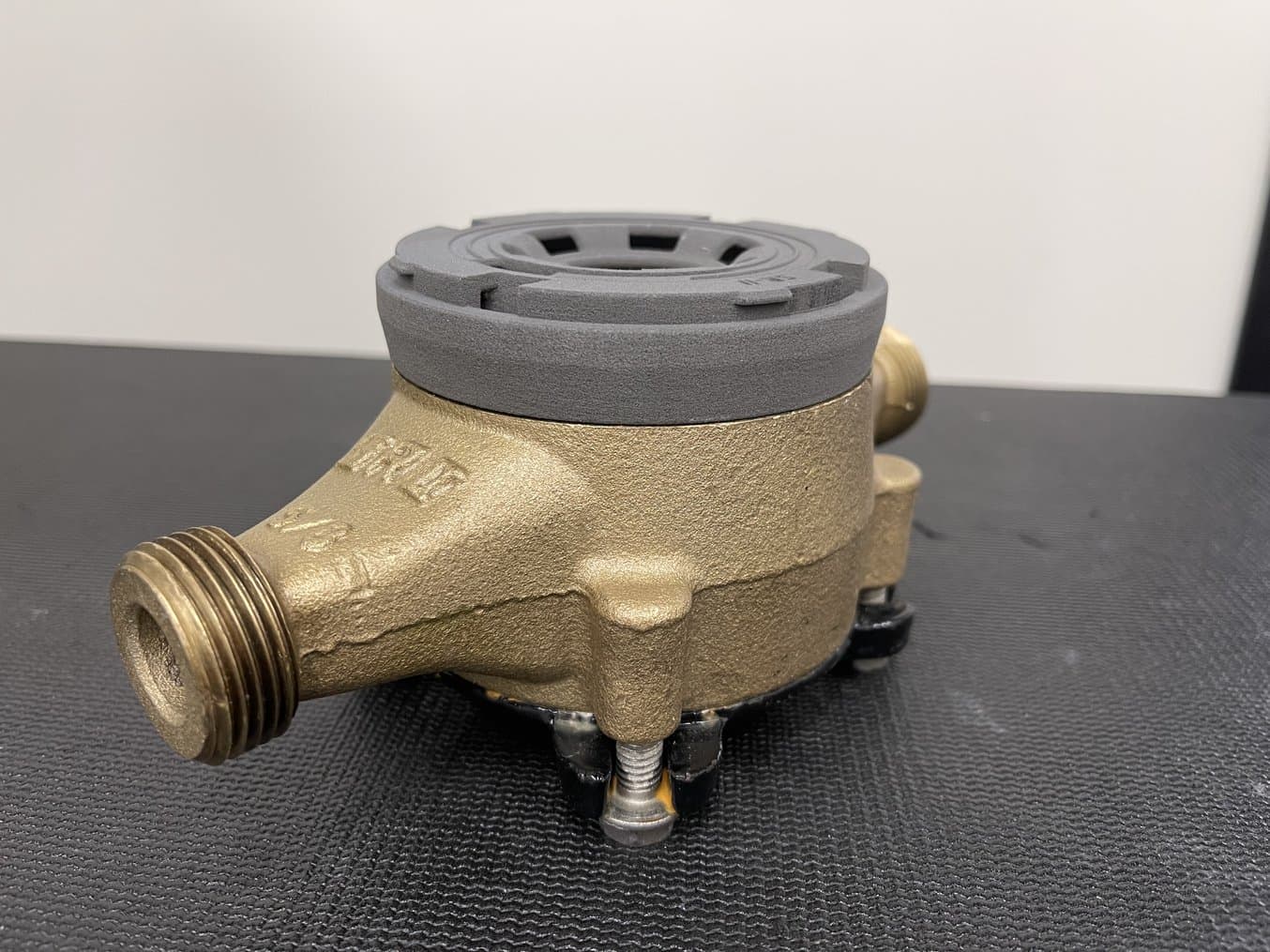
The Fuse 1 printed component of Next Meters' custom water maters.
Stress Testing to Mimic Conditions in the Field
To ensure that their end-use parts would be able to withstand the demands put upon them in the field, Next Meters has their own in-house testing team. The bracket they print in Nylon 11 Powder to affix their tech to the existing water meter does not have to go through external regulatory testing, so Next Meters conducts their own extensive certification process to ensure their parts perform in the field.
Using a state-of-the-art environmental chamber, they take the brackets from 70C down to 0C and back up multiple times a day for over three months, simulating 15 years in an outdoor environment. The success of the tests allowed them to start producing these end-use parts with their Fuse 1 printer and have upgraded to using two materials.
"There are about 250 Fuse 1 printed brackets currently in the field, made to fit three different manufactured meters and printed in Nylon 11. We prototype them in Nylon 12 [Powder] because its got the better refresh rate, and then clean the machine and switch to Nylon 11 for parts to be deployed in the field."
David Clyde
3D Printing Enables Expansion and Education
As the Fuse 1 has made it cost-effective to manufacture production parts on demand, as well as reduced costs in the development and prototyping stages, the Next Meters team can expand their business and reach more communities. Part of the company’s growth is due to their internal training and career development programs as well. As more companies take advantage of advanced manufacturing, the workforce needs to develop the skills to implement the technology, and Next Meters has found a solution in-house. Every employee has the benefit of using the 3D printers on demand, and many have utilized this opportunity to learn more about product design and advanced manufacturing.
“We’ve had multiple employees outside our engineering department teach themselves mechanical engineering skills and move on to advance the company with these new skills. It’s fun to see the creativity of our staff, as well as support those with the desire to learn and grow professionally,” says Clyde.
Additionally, Clyde partners with a local 3D printing club to provide access and education to middle school students. Every month, students come to the Next Meters prototyping lab and have a chance to print their own designs out on the FDM, SLA, and SLS printers. Clyde sees it as an opportunity to help increase adoption of the technology, and improve the industry as a whole by educating the future of the workforce.
“It’s fun to watch them think through this process. 3D printing in manufacturing will absolutely grow—the kids embrace it and they’re designing parts purposely suited for it, as opposed to traditional mechanical engineers, who need to change the way they design. That’s why we do what we do supporting these youth groups, this young group of engineers will grow up to change the future of manufacturing,” says Clyde.
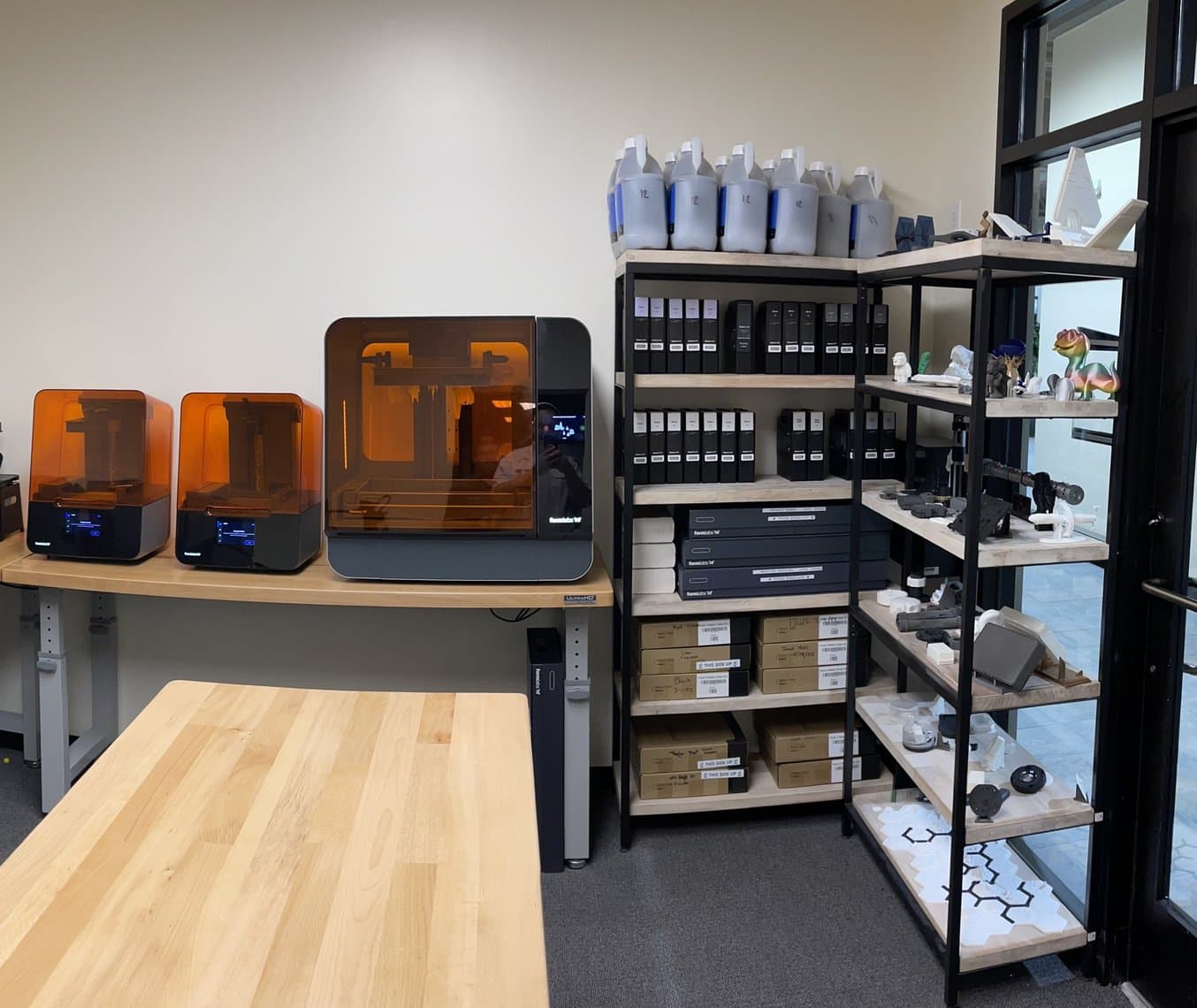
The Form 3L allows employees and student members of the 3D printing club to print large prototypes and models.
Improving Access
Relying on their new complementary workflows of injection molding and 3D printing, Next Meters can now tackle any situation, and continue enabling communities to accurately track their water usage and reward those who conserve this increasingly precious natural resource. 3D printing has sped up their prototyping and development timelines, reduced costs in the tooling phase, and enabled the production of end-use parts, along with providing education and training tools to their employees and community.
“The investment we’ve made in our 3D print lab has not only provided us with a quicker and more cost effective method of manufacturing, it’s also enabled us to further maintain our high standards for quality by bringing more of the process back in-house within our control. We look forward to continuing to grow our 3D printing capabilities, and we’re excited for the future it brings."
David Clyde