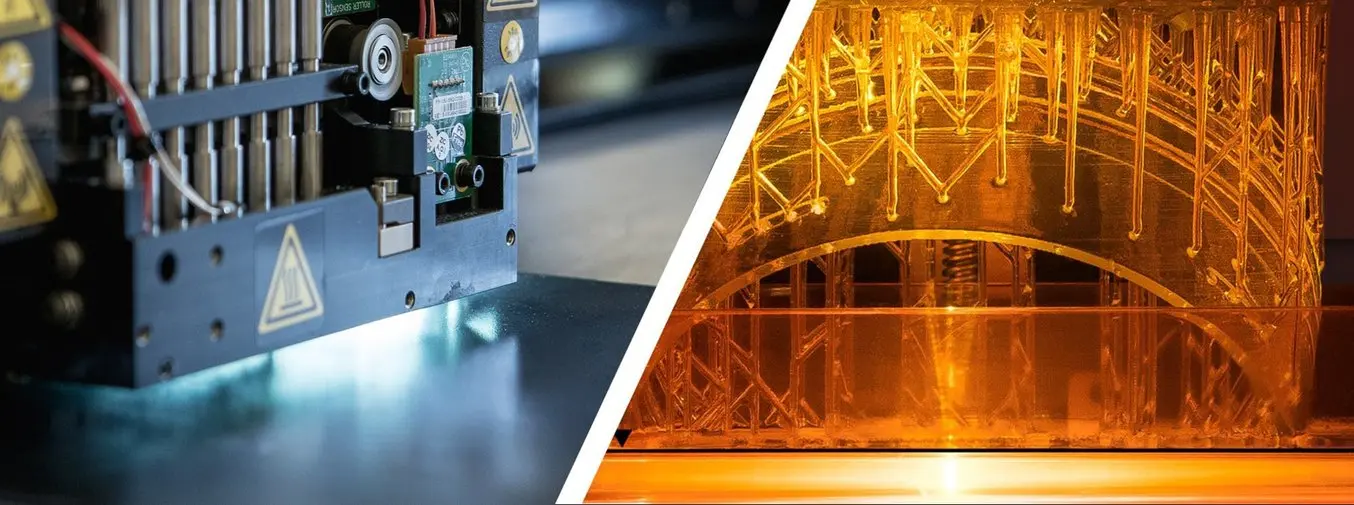
There are many 3D printing processes on the market. Getting familiar with the nuances of each helps to clarify what you can expect from final prints, initial investments, workflows, and speed, so you can select the optimal technology for your application.
PolyJet, a form of material jetting 3D printing, and stereolithography (SLA) are two common processes for resin 3D printing. Both technologies are popular for producing high-accuracy, isotropic, and watertight industrial-quality prototypes and parts in a range of advanced materials with fine features and a smooth surface finish.
In this comprehensive guide, we take a closer look at PolyJet vs. SLA 3D printers, and how they compare in terms of costs, print quality, materials, applications, workflow, speed, and more, to help you decide which technique is ideal for your business.
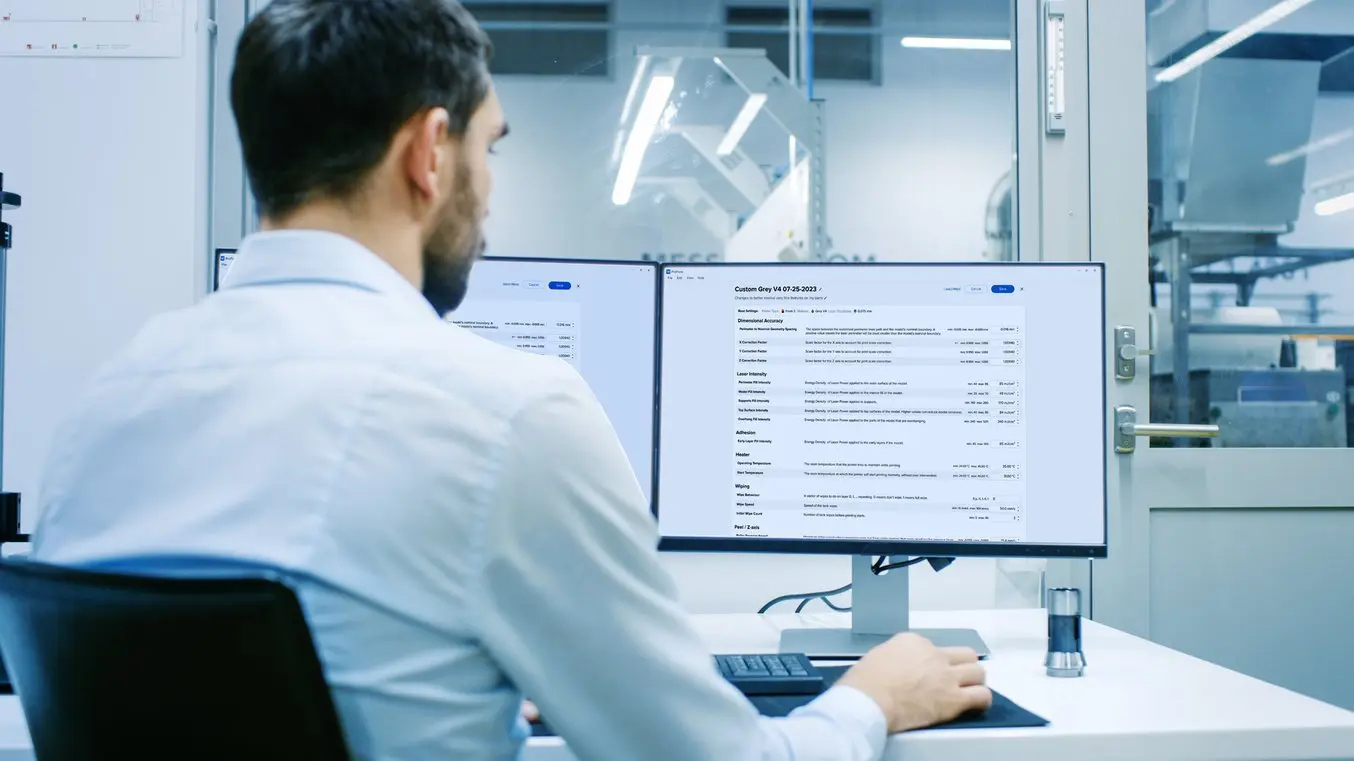
Talk to Our Sales Team
Whether you need to prototype at speed, or are producing end-use parts, we’re here to help. The Formlabs Sales team is composed of dedicated specialists who know exactly how to support you and your company's needs.
What Is Material Jetting?
Material jetting is a form of 3D printing similar to traditional inkjet printing. However, with material jetting printing, drops of photopolymer plastic are cured as they’re jetted instead of droplets of ink being jetted onto paper.
How Does Material Jetting Work?
During the material jetting process, a print head moves across the build platform along the X and Y axis, jetting out droplets of resin onto the platform. Within the same movement, ultraviolet light from the print head cures the droplets on the build platform. Once the layer is complete, the built platform moves down, so that the print head can distribute a second layer. The printed object will then continue to grow until the process finishes.
For more complex geometries such as overhangs, the 3D printer jets a removable gel-like support material. The print heads can also mix multiple material jetting materials together to achieve unique material properties and colors.
What Is PolyJet 3D Printing?
PolyJet 3D printing belongs to the family of material jetting additive manufacturing processes. PolyJet technology was developed by Objet, which was later acquired by Stratasys. There are other material jetting 3D printers on the market, but under the brand name PolyJet, they are only sold by Stratasys.
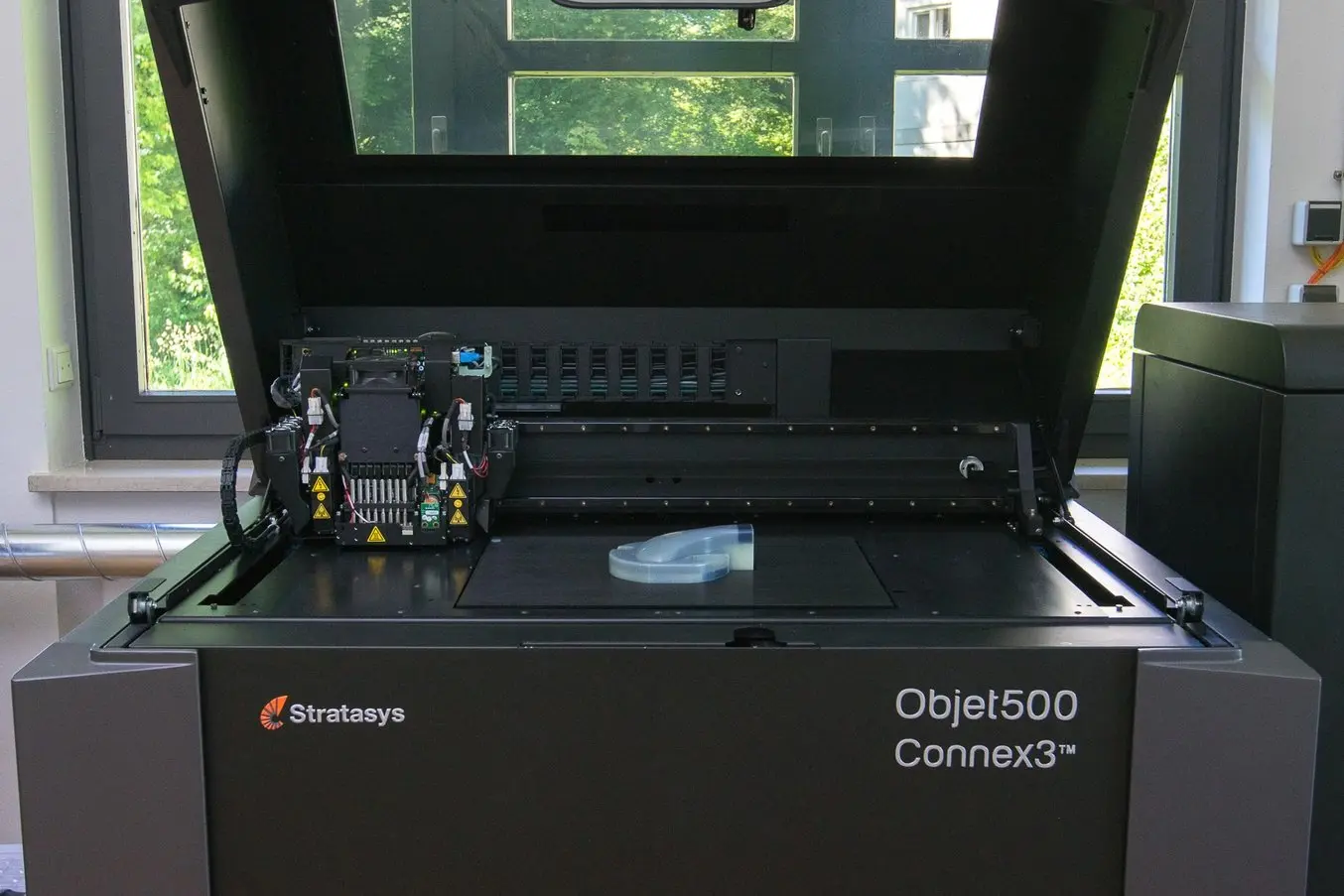
A Stratasys Connex 500 polyjet 3D printer.
What Is SLA 3D Printing?
Stereolithography was the world’s first 3D printing technology, invented in the 1980s, and is still one of the most popular technologies for professionals. SLA 3D printers use a light source to cure liquid resin into three-dimensional objects by exposing a vat or tank of resin to a light source, which hardens it.
How Does SLA 3D Printing Work?
The most common inverted SLA 3D printers contain a resin tank with a transparent base and non-stick surface, which serves as a substrate for the liquid resin to cure against, allowing for the gentle detachment of newly-formed layers.
There are multiple types of SLA or resin 3D printing processes, defined largely by the type of light source that’s used to solidify the resin. The most popular process currently is masked stereolithography (MSLA) 3D printing, where the light source is selectively covered, or masked by an LCD screen.
Form 4, and Form 4L for large-format 3D printing, are powered by the Low Force Display™ (LFD) Print Engine, an advanced form of MSLA 3D printing.
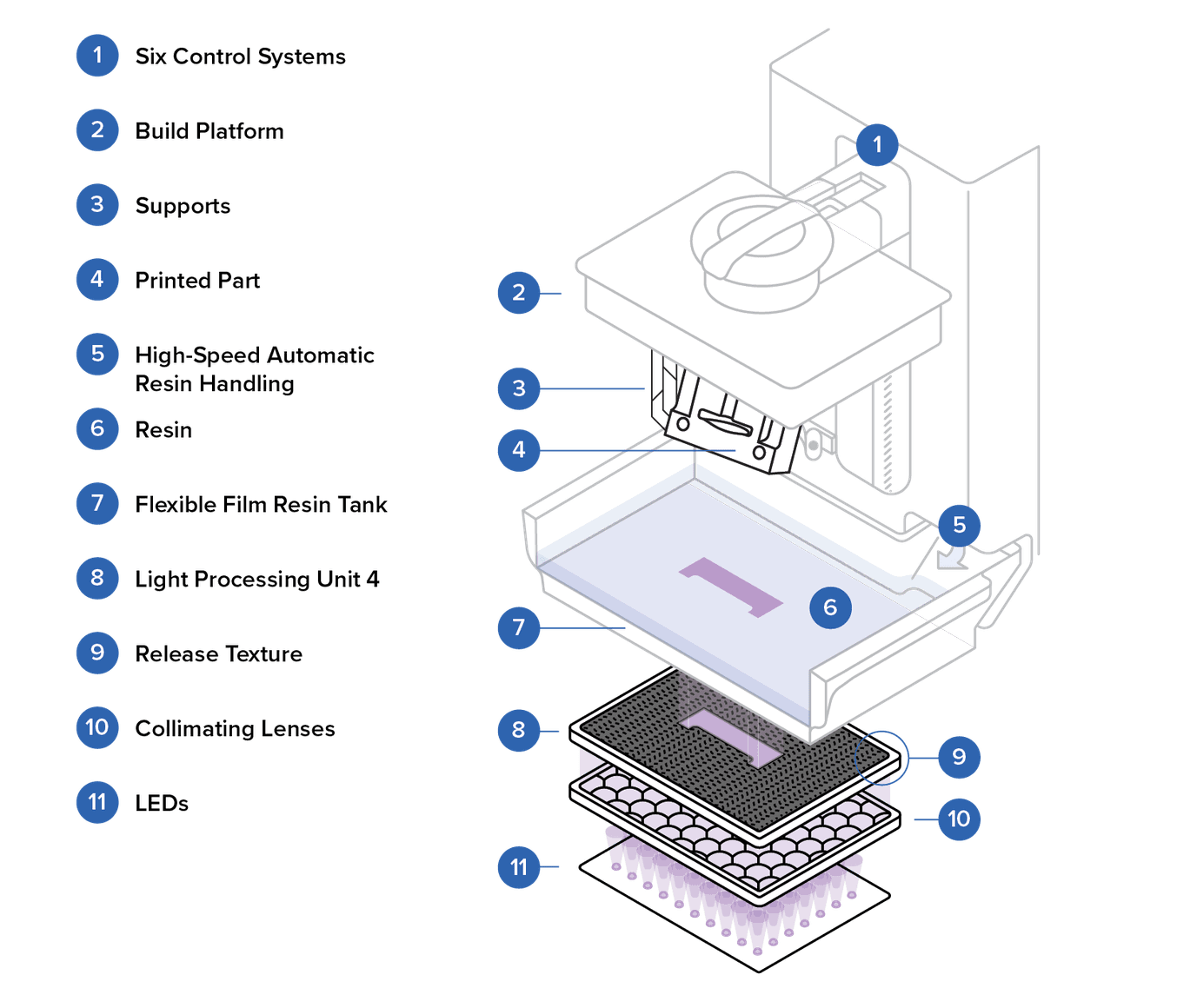
At the core of the LFD Print Engine is the Backlight Unit, an ultra-high power light source that emits a uniform area projection of light which passes through a lens array and into the Light Processing Unit (LPU) 4, where it is formed into the shape of the printed layer. Once the light reaches the liquid resin inside the resin tank, the full liquid layer immediately cures into a solid layer. The Build Platform then rises out of the resin and a precision Z-axis peels away the layer from the bottom of the resin tank.
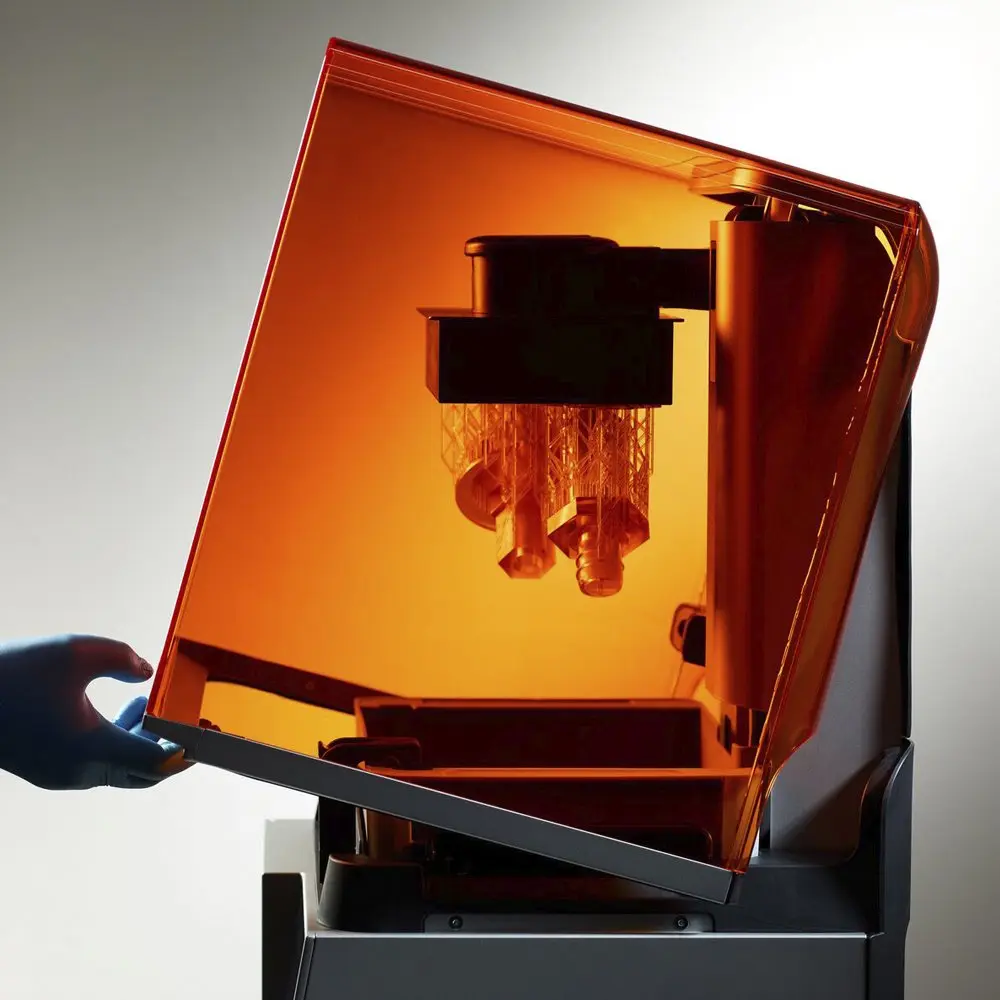
Introduction to 3D Printing With Desktop Stereolithography (SLA)
Looking for a 3D printer to produce high resolution models fast? Download our white paper to learn how SLA printing works and why it's the most popular 3D printing process for creating parts with incredible detail, high dimensional accuracy, and superior surface finish.
PolyJet (Material Jetting) vs. SLA: Detailed Comparison
While PolyJet (material jetting) and SLA 3D printers both create high-resolution resin parts, there are various benefits and drawbacks for specific applications. As such, it is helpful to evaluate their comparative strengths and weaknesses in a few key categories.
Costs and Return on Investment
One of the main differences between SLA and material jetting 3D printers involves costs. As SLA patents began to expire at the end of the 2000s, and smaller format, desktop SLA 3D printers were introduced to the market, the cost of SLA printers decreased by 100x. Today, prices for professional SLA printers start at about $2,500, while large-format benchtop printers start at $5,000.
In contrast, material jetting and PolyJet 3D printers are substantially more expensive, with prices ranging from $20,000 to $500,000+. This is only the machine cost, compulsory service plans can cost up to 20% of the price of a PolyJet printer annually, which is enough to buy a fleet of SLA printers each year.
In addition, resins for material jetting 3D printers are generally two to three times more expensive than SLA resins. As a result, the overall cost per part for PolyJet prints is many times higher than that of an SLA print. PolyJet printers also require more maintenance, increasing the amount of labor necessary to operate these machines.
Thus, unless you specifically need PolyJet for a certain application, such as full-color models or multi-material parts, you are likely to see a higher return on your investment with an SLA printer.
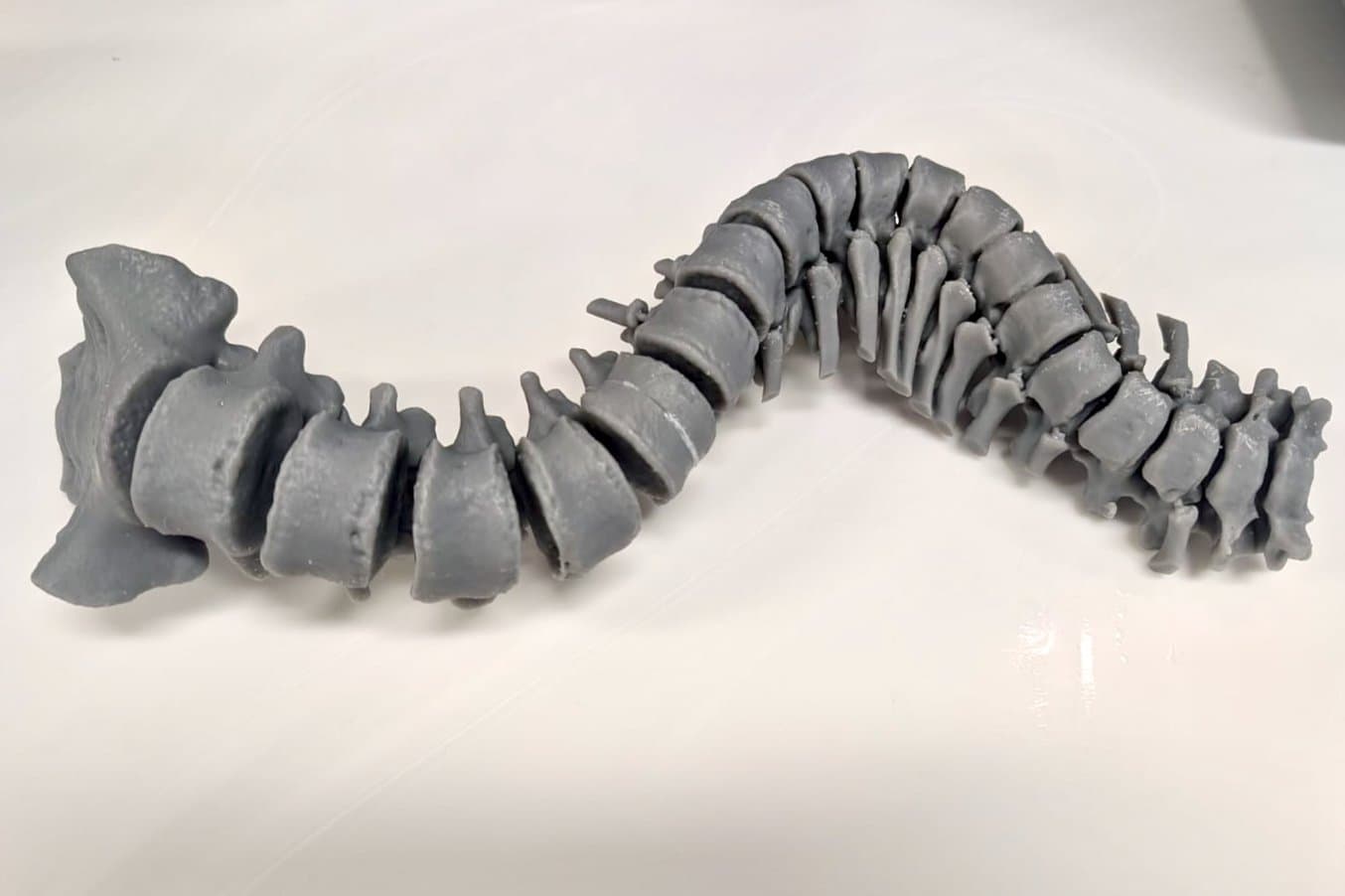
At St. Louis Children’s Hospital, anatomical models like this spine would cost about $1,600 in PolyJet resin, versus $80 in Formlabs Fast Model Resin.
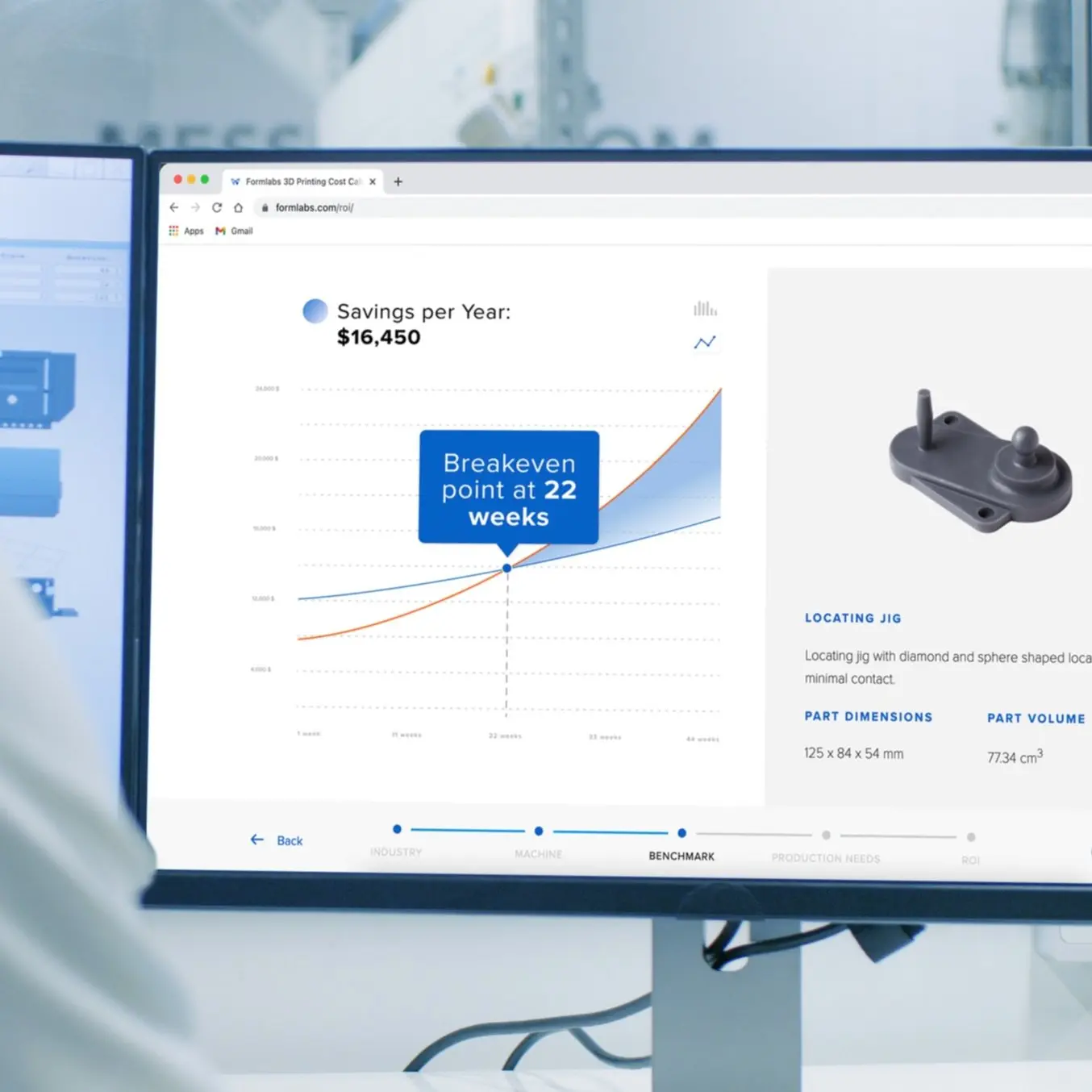
Calculate Your Time and Cost Savings
Try our interactive ROI tool to see how much time and cost you can save when 3D printing on Formlabs 3D printers.
Print Quality and Precision
Because 3D printing is an additive process, each layer introduces an opportunity for inaccuracy, and the process by which layers are formed affects the level of precision, defined as the repeatability of the accuracy of each layer. 3D printing tolerances, accuracy, and precision depend on many different factors: the 3D printing process, materials, software settings, post-processing, and more.
Both material jetting and SLA 3D printers are among the most accurate and precise 3D printing processes, with tolerances around ±0.2% (lower limit: ±0.1 mm). Thanks to the highly-precise light sources, these processes can achieve fine details and can consistently produce high-quality results.
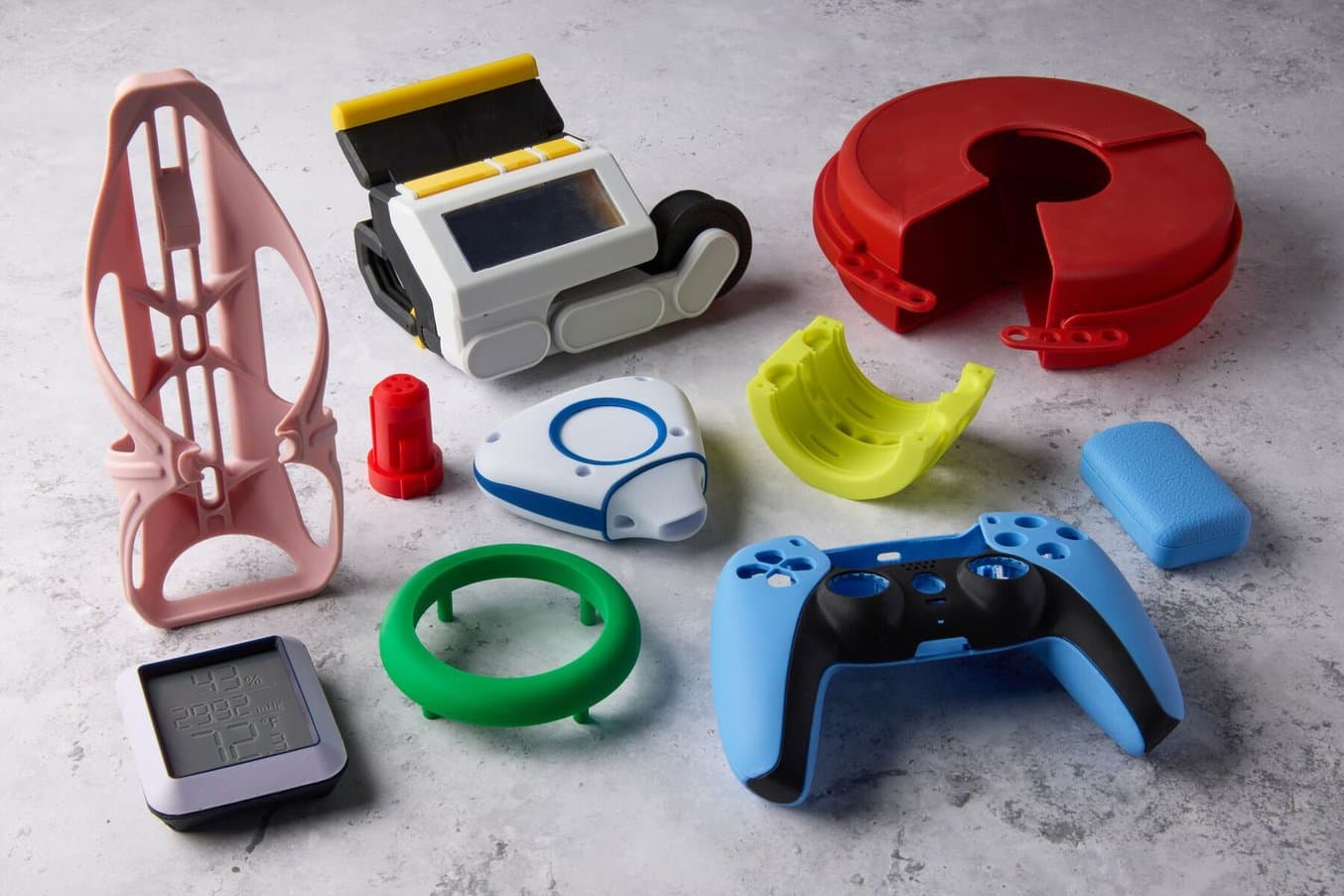
SLA parts have fine details, sleek surfaces, and minimal visible layer lines. These parts were printed in Color Resin on Form 4.
Depending on the model geometry, PolyJet and SLA 3D printed parts require support structures, which can be essential to achieve dimensional accuracy, especially with complex geometries or large and thin walls.
With SLA, supports are removed manually during post-processing. Formlabs SLA printers offer enhanced, light-touch support structures and bundled supports that detach from parts in seconds to save post-processing time. SLA printed parts are also known for their smooth surface finish, which, depending on the material, can be matte or glossy.
With PolyJet printers, support structures are washed away during post-processing with a water jet. This workflow exerts forces on the parts and can break intricate details or bend thin walls. PolyJet printers can print with a matte and glossy surface. However, glossy finish is only limited to sections of the model where support material is not used.
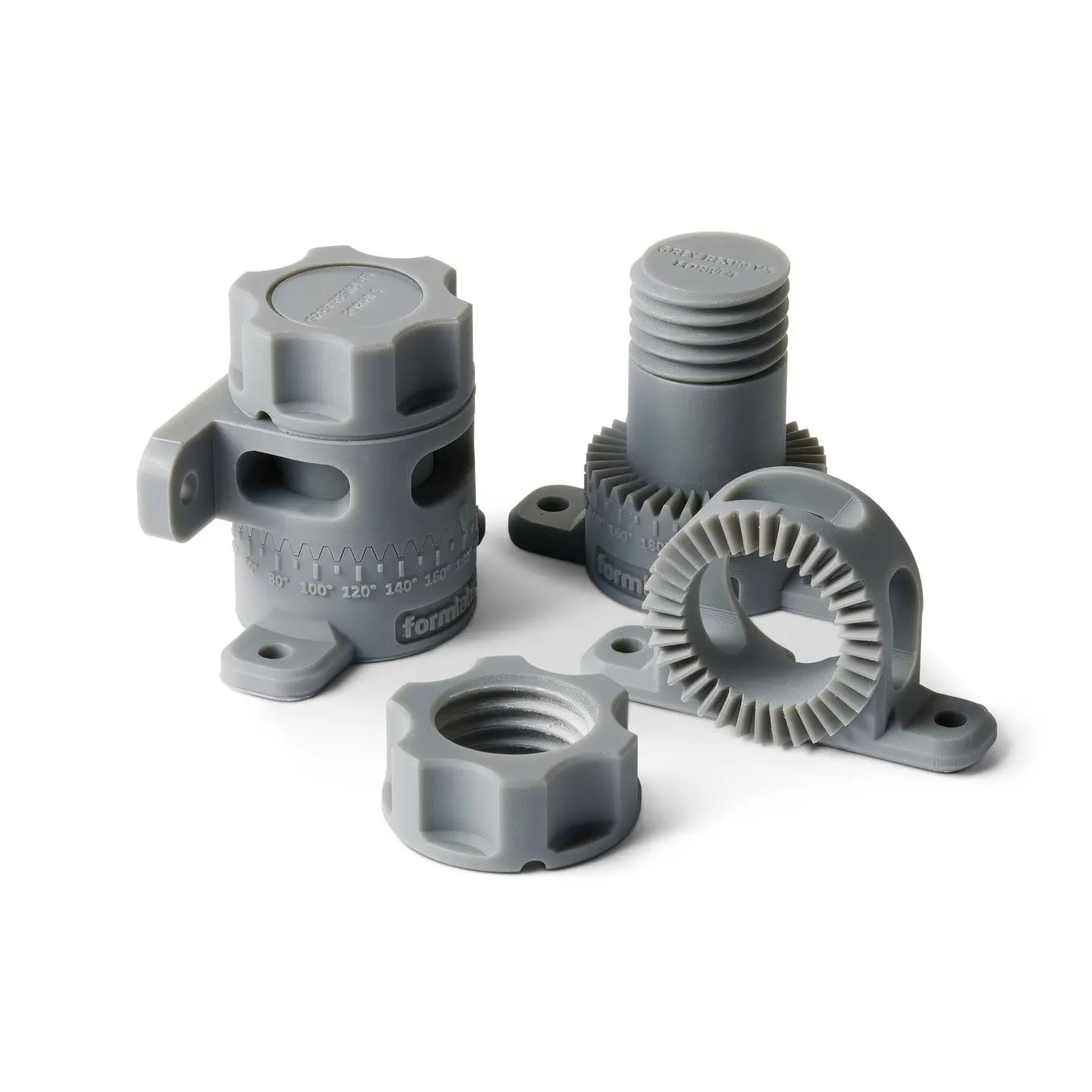
Request a Free Sample Part
See and feel Formlabs quality firsthand. We’ll ship a free 3D printed sample part to your office.
Materials and Applications
One of the biggest differences between PolyJet and SLA is the availability of materials, which also defines the possible applications for these printers.
Depending on the printer model, most material jetting and PolyJet 3D printers support around five to 10 different materials. These range from standard prototyping materials to materials in different colors, clear materials, and biocompatible materials. More high-end PolyJet 3D printers also support printing with multiple materials at the same time, enabling novel material jetting applications such as printing multicolor and multi-material prototypes.
However, PolyJet printers can only print with low-viscosity materials, which severely limits the range of mechanical properties available. PolyJet materials also have a low heat deflection temperature (HDT), generally around 45-50 °C, which means that they can even start to creep and lose shape under strong light. As a result, PolyJet printing is only ideal for concept modeling and non-functional prototyping applications, as well as some dental and medical applications that require biocompatibility.
SLA 3D printers support a much wider range of materials than a typical material jetting 3D printer, with up to 45+ materials for Formlabs 3D printers, including 15+ biocompatible materials. SLA resins offer a much wider range of material properties: They can be flexible or stiff, clear or opaque, heavily filled with secondary materials like glass, wax, or ceramic, or imbued with mechanical properties like high heat deflection temperature, impact resistance, or chemical resistance. Due to this, SLA materials can closely match common end-use thermoplastic materials for rapid prototyping.
While SLA doesn’t offer multicolor 3D printing, it is the only other 3D printing technology that offers custom colors for professional applications with Color Resin. Color Resin is custom-manufactured and enables fast, easy, and affordable production of color parts that range from nuanced neutrals to saturated, bold colors for realistic prototypes, color-coded jigs and fixtures, or custom-colored end use parts.
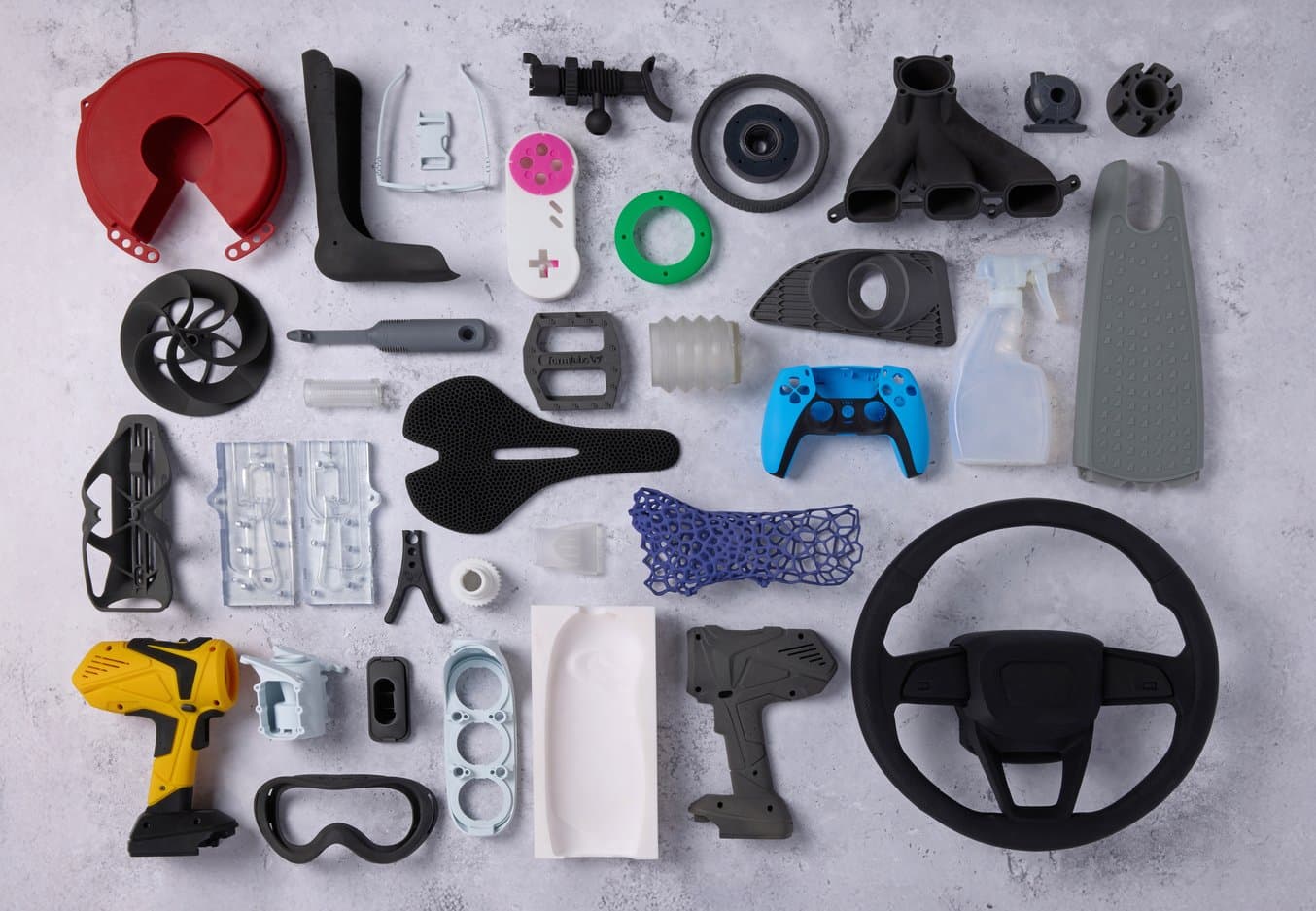
SLA 3D printers offer the widest range of materials for engineering, manufacturing, and healthcare applications.
Formlabs also offers Open Material Mode (OMM), which unlocks the ability to print with any 405 nm photopolymer resin, empowering researchers and expert users with full access to third-party materials or material development.
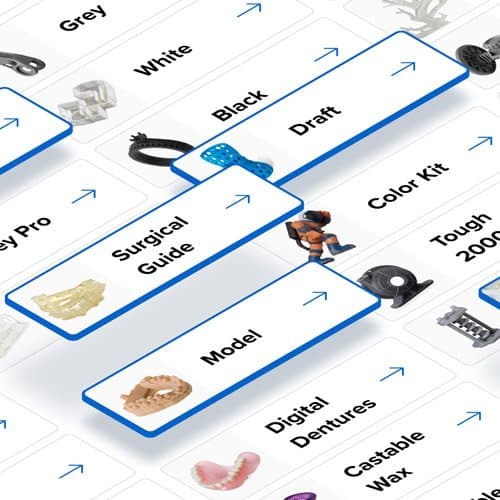
Find the Right Material for Your Application
Need some help figuring out which 3D printing material you should choose? Our new interactive material wizard helps you make the right material decisions based on your application and the properties you care the most about from our growing library of resins.
Ease of Use
Workflow
The workflow for both PolyJet and SLA 3D printing consists of three steps: designing, 3D printing, and post-processing.
Both PolyJet and professional SLA 3D printers come with their own proprietary software and predefined settings for each material that have been thoroughly tested to ensure the highest print success rate. Setting up prints with advanced print preparation tools like PreForm is plug-and-play, with automatic orientation and support generation.
Once the 3D printing process begins, 3D printers can run unattended, even overnight, until the print is complete. Both PolyJet printers and advanced SLA 3D printers like Formlabs' Form 4 Series offer a cartridge system that refills the material automatically. Resin Pumping System can also be added to Form 4 Series 3D printers, seamlessly delivering 5 L of resin to the printer.
To post-process parts, you will need to manually remove support material from a PolyJet 3D printed part using a water jet or a combination of chemical baths and peeling for thick supports. This can bend parts with thin walls and also easily break delicate features. PolyJet parts don’t require post-curing — the models come off the printer fully cured.
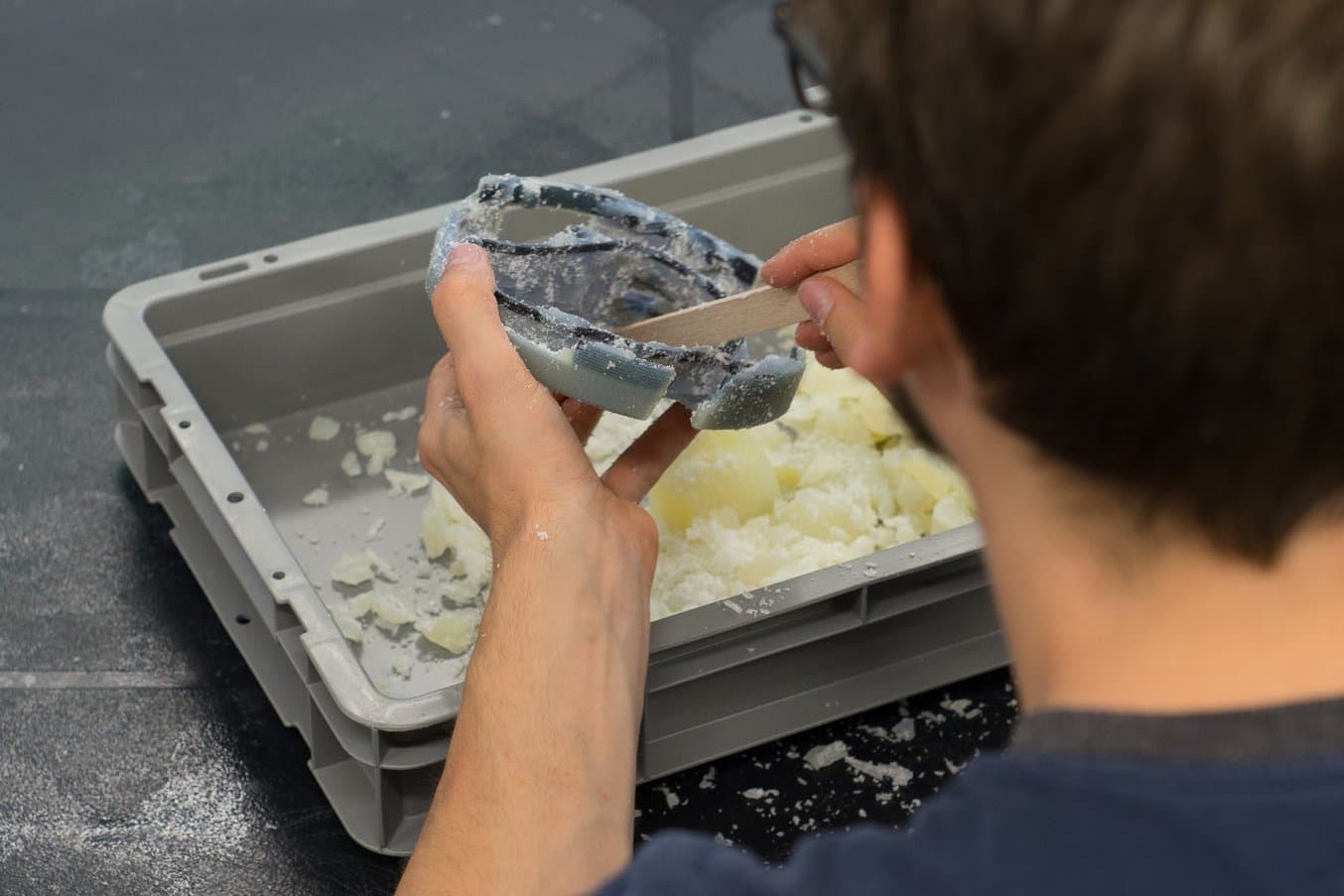
PolyJet post-processing includes a combination of chemical baths, peeling, and water jetting, which can damage intricate features.
SLA parts require rinsing in isopropyl alcohol (IPA) or alternative solvents to remove any uncured resin from their surface. Using the standard workflow, this involves first removing parts from the build platform, then manually soaking them in a bath of solvent to clean off excess resin.
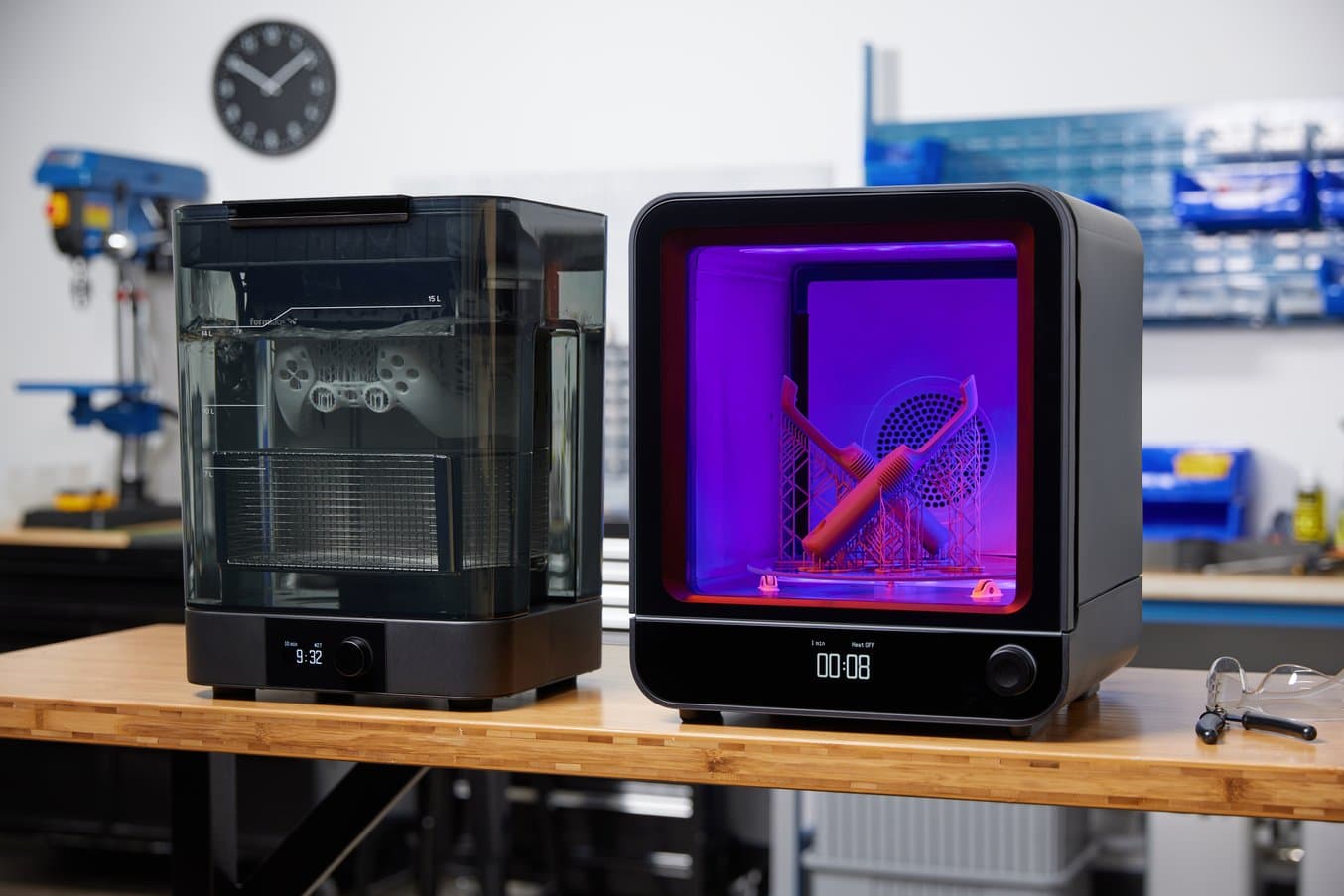
SLA post-processing can be mostly automated with washing and curing solutions.
Professional solutions such as the Form Wash and the Form Wash L automate SLA post-processing. Parts can be transferred directly from the printer to Form Wash or Form Wash L, which agitates the solvent around the parts to clean them and automatically raises parts out of the alcohol bath when the process is finished.
After rinsed parts dry, some SLA materials require post-curing, a process that helps parts to reach their highest possible strength and stability. This can also be automated with curing solutions like the Form Cure and the Form Cure L.
Support removal for SLA parts requires cutting away the support structures and lightly sanding the parts to remove support marks. Formlabs technology offers light-touch supports, which allow an entire object to be torn away from its support base in seconds, leaving minimal markings and reducing time spent post-processing. Additional support features and settings in PreForm, including bundled supports shown below, can optimize how supports are placed, minimizing support removal.
When further post-processing is required, both PolyJet and SLA parts can be machined, primed, painted, and assembled for specific applications or finishes.
Maintenance
PolyJet printers often require more maintenance than a typical SLA printer. You will need to clean the print head, build tray, and roller after every use. In addition, you will need to clean the UV lamps and wiper daily and perform regular tests to ensure that your printer remains in working condition.
Material jetting 3D printers also generally require setup and training with on-site installation. The more complex workflow and the steeper learning curve mean that the system requires a skilled technician in-house to operate and maintain.
Besides keeping the printer and the work area tidy, professional SLA 3D printers generally don’t require regular maintenance. Smart sensors on Form 4 Series 3D printers also offer debris detection, control resin levels, and more. Plus, the easy workflow empowers anyone at a company to use an SLA printer independently after less than one hour of training.
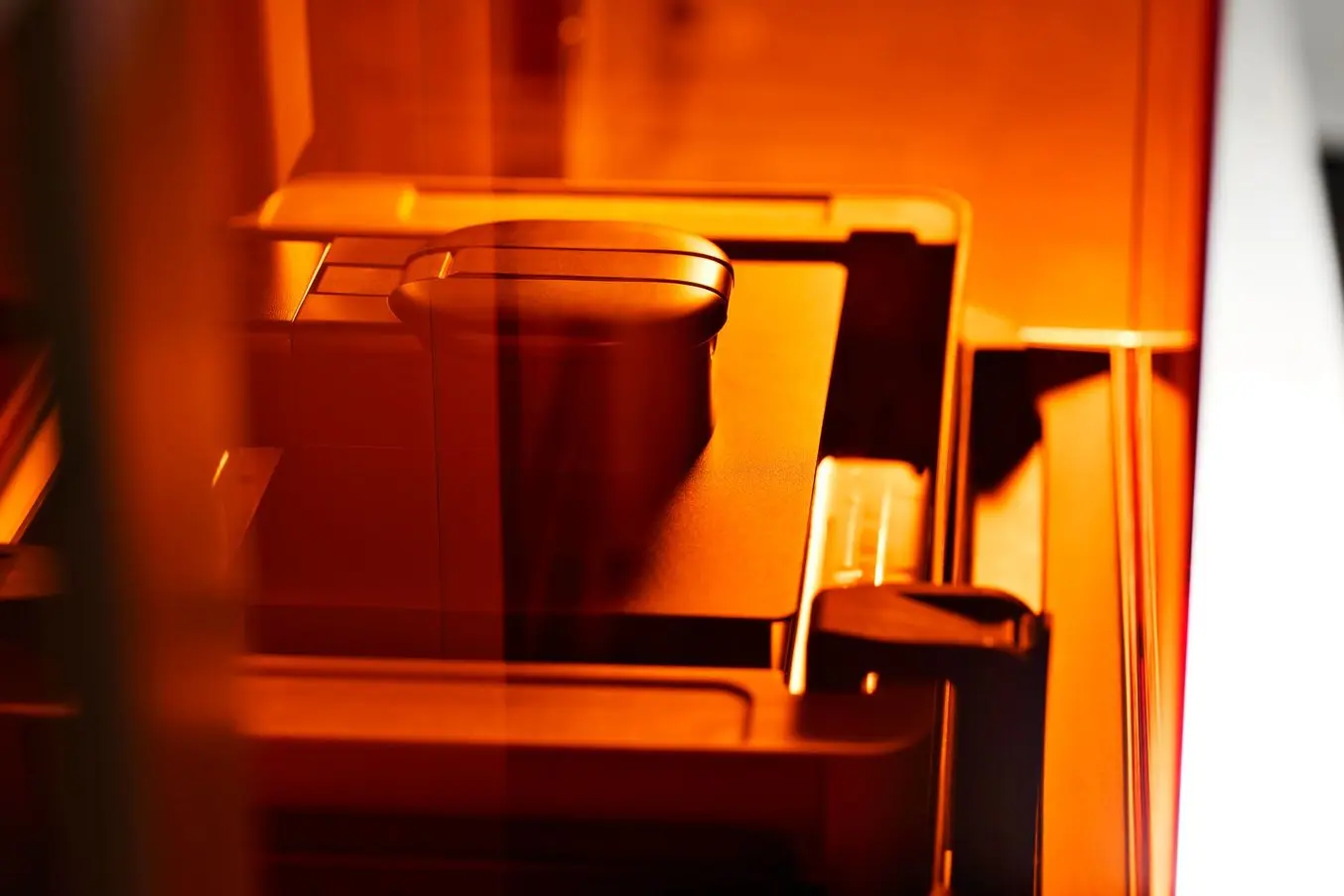
Product Demo: Form 4
See how Form 4 can enable new levels of productivity and innovation through its unmatched speed, accuracy, and reliability.
Build Volume
PolyJet printers are available in various sizes, from smaller benchtop models to large, multi-ton industrial machines. Due to the differences in technology, developing larger PolyJet machines is less complex.
The first SLA 3D printers were mainly large industrial machines that offered large build volumes, but often at an even higher cost than PolyJet and with a much more complex workflow. However, thanks to the rapid development of the SLA printing technology, SLA printers are now available in both compact desktop and large format benchtop forms at much lower cost than PolyJet printers.
The inverted SLA process behind more accessible desktop and benchtop SLA printers reduces footprint and cost, but heightened peel forces introduce limitations around materials and build volume, and larger parts support structures to print successfully.
With the introduction of the Low Force Stereolithography (LFS) print process of Form 3 generation 3D printers, Formlabs re-engineered the approach to resin-based 3D printing to drastically reduce the forces exerted on parts during the print process. Additional updates for Form 4 Series 3D printers, including a Release Texture and Flexible film Tank, further minimized peel forces enabling fast print speeds and reliable printing.
For large format SLA 3D printing, Form 4L leverages the same technology as Form 4, while removing size restrictions that sometimes hinder workflows on smaller desktop devices and maintaining a competitive price point.
Printing Speed
Both PolyJet and SLA are considered some of the fastest 3D printing technologies.
PolyJet 3D printers provide fast printing speeds within a five-inch cube, but for larger models and builds, the print speed slows down significantly as the print head has to travel farther, which causes the layers to take a longer amount of time to complete.
MSLA printers cure an entire layer of resin at once, meaning it takes a similar time to print a full build platform or a single part, enabling users to pack a build platform and still achieve fast print speeds.
PolyJet printers also have a limited range of automated post-processing solutions available, so while the actual printing process may be faster, post-processing is often slower and more labor-intensive with a PolyJet printer.
Speed can also depend on the material choice. Formlabs Fast Model Resin was developed to leverage the technology of Form 4 Series and is capable of printing at speeds of over 100 mm per hour for dental models in minutes or large prototypes in less than two hours.
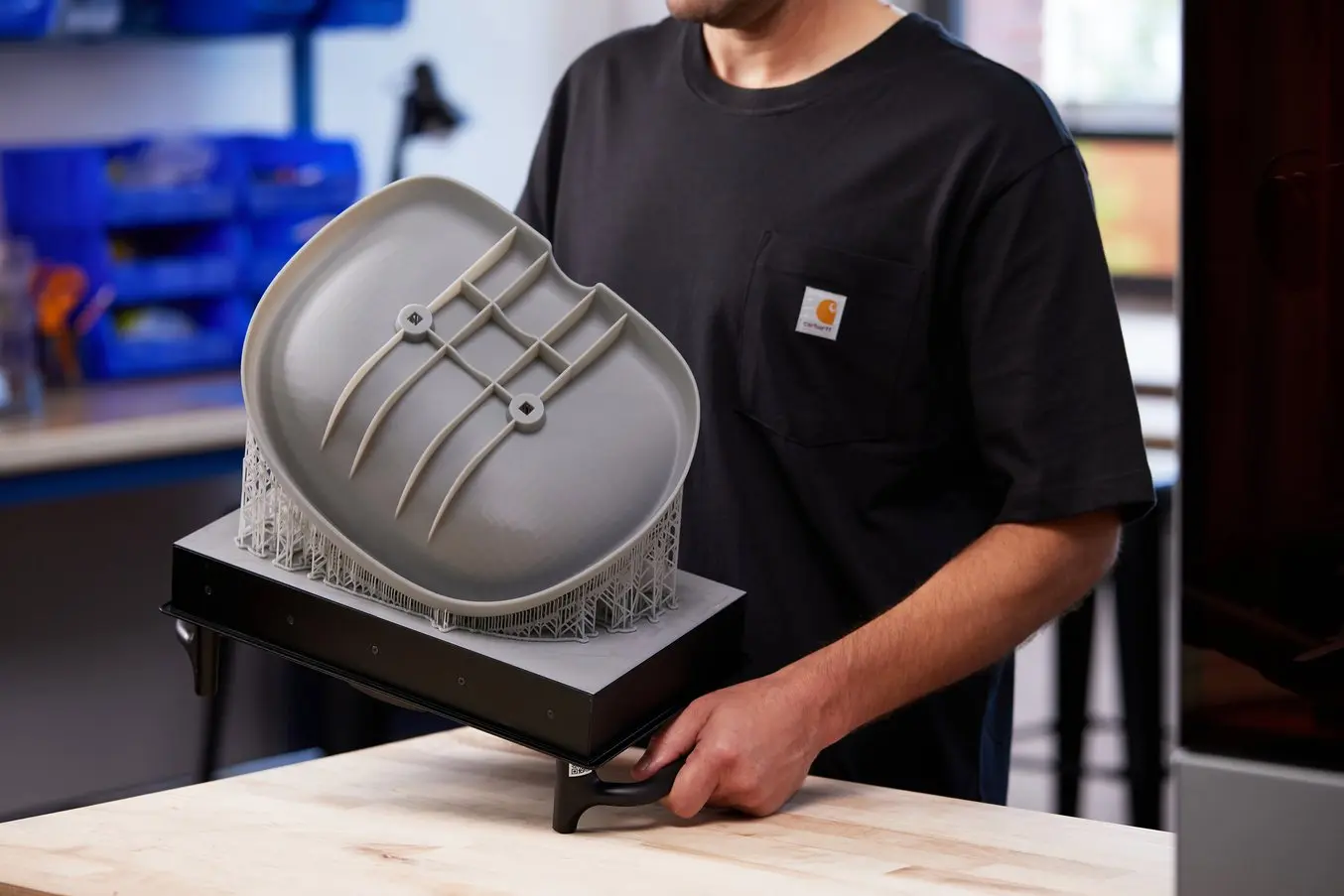
Print Speed Comparison: Radio Flyer Seat Prototype
FDM 3D Printing | SLA 3D Printing | |
---|---|---|
1 prototype | 42 hr 3 min | 2 hr 37 min |
Compared printers and printing parameters:
- FDM 3D printer: Ultimaker S7, PLA, 100 microns layer height, 20% infill density
- SLA 3D printer: Form 4, Fast Model Resin, 200 microns layer height
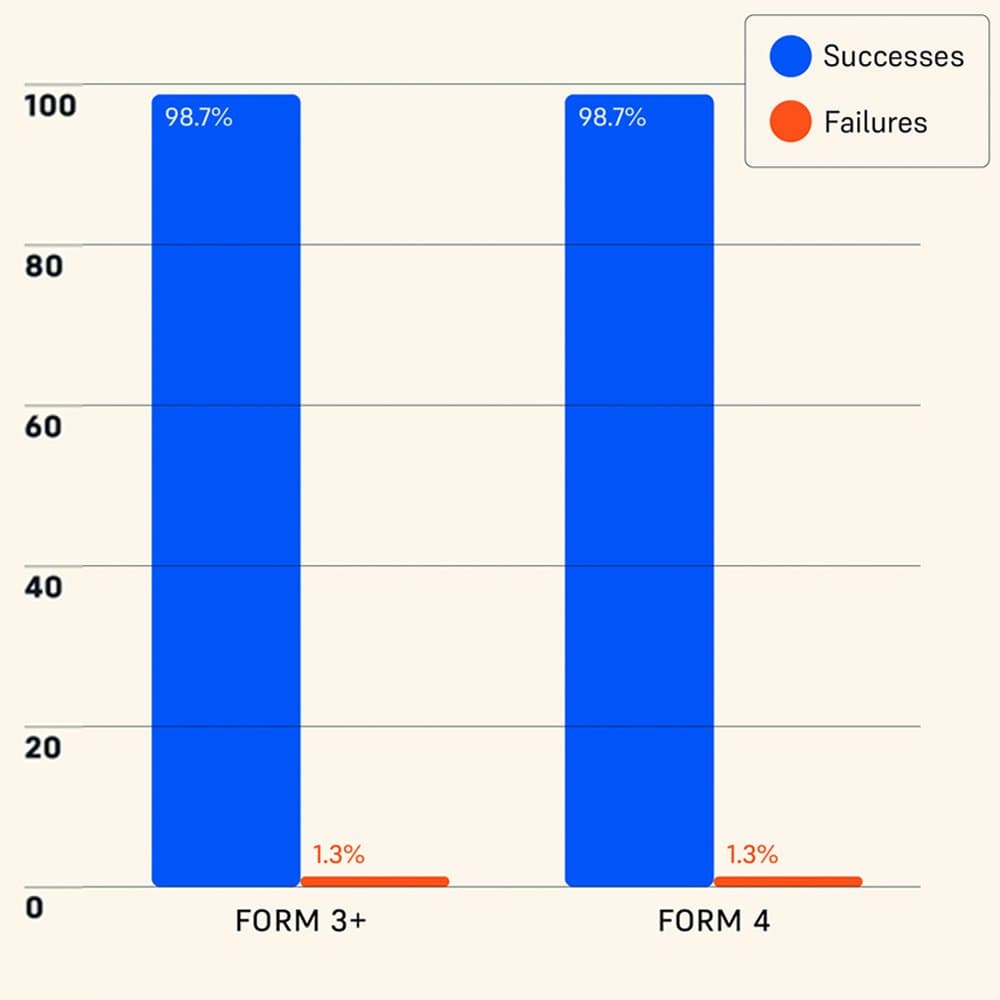
Independently Tested Reliability of Form 4 and Other Resin 3D Printers
Formlabs Form 4 was measured to have a 98.7% print success rate by an independent global leader in product testing. Read a complete description of the test methodology and see the results in our white paper.
PolyJet (Material Jetting) vs. SLA: Side by Side Comparison
Each 3D printing technology has its own strengths, weaknesses, and requirements, and is suitable for different applications and businesses. The following table summarizes some key characteristics and considerations when comparing PolyJet vs. SLA 3D printers.
PolyJet | Stereolithography (SLA) | |
---|---|---|
Resolution | ★★★★★ | ★★★★★ |
Accuracy | ★★★★★ | ★★★★★ |
Surface Finish | ★★★★★ | ★★★★★ |
Throughput | ★★★★☆ | ★★★★☆ |
Complex Designs | ★★★★☆ | ★★★★☆ |
Ease of Use | ★★★★☆ | ★★★★★ |
Pros | High accuracy Smooth surface finish Multicolor 3D printing Multi-material properties Fast printing speeds (for small parts) | Great value High accuracy Smooth surface finish Fast printing speeds Wide range of functional applications |
Cons | Expensive machinery and materials Limited material options Parts are sensitive to heat and long exposure to UV light. Requires maintenance and a dedicated operator | Some materials are sensitive to long exposure to UV light |
Applications | Concept modeling Rapid prototyping Dental and medical applications | Concept modeling Rapid prototyping Functional prototyping Rapid tooling Manufacturing aids Low volume, bridge, or custom manufacturing Dental models and appliances Medical models and medical devices Jewelry prototyping and casting Models and props |
Build Volume | 294 x 192 x 148.6 mm for benchtop printers, up to 1000 x 800 x 500 mm large-scale printers | Up to 353 x 196 x 350 mm (desktop and benchtop 3D printers) |
Price | Benchtop printers start around $20,000, large-scale industrial machines can cost $500,000+. | Low-cost resin 3D printers are available for $200 to $1000, professional SLA 3D printers are in the $2,500 to $10,000 range, and large-format resin 3D printers are in the $5,000 to $25,000 range. |
Materials | Varieties of resin (thermosetting plastics). Standard (opaque, clear, colors), engineering, dental and medical (biocompatible) | Varieties of resin (thermosetting plastics). Standard (opaque, clear, colors), engineering (ABS-like, PP-like, flexible, heat-resistant, rigid glass-filled), castable, and dental and medical (biocompatible). Pure silicone and ceramic. |
Choosing the Right 3D Printers for Your Needs
Both material jetting and SLA 3D printing technologies have unique benefits, from high accuracy and precision to a smooth finish, fast prints, and a variety of materials. However, SLA technology has evolved faster and provides unique benefits, especially considering the cost, ease of use, and the possible range of applications.
Formlabs Form 4 Series resin 3D printers deliver a 99% success rate, a growing library of specialized materials, intuitive print preparation and management software, and professional services — all in one package. Curious to see the quality firsthand? Order a sample part shipped to your office.