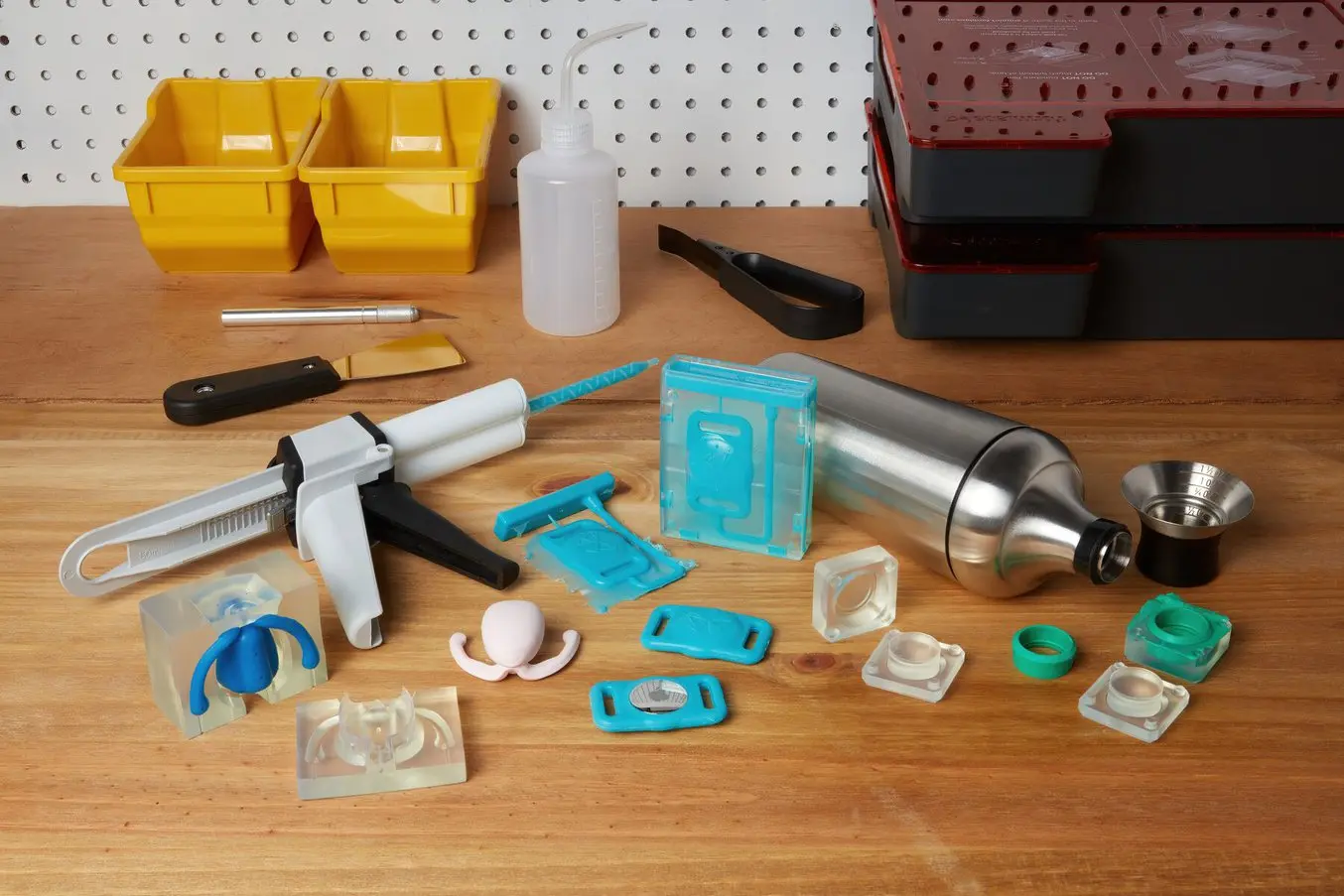
シリコンは軟質の実製品用部品の材料として人気が高く、カスタムメイドの補聴器、映画やテレビ番組撮影用の小道具、補装具、消費者製品のハンドルやグリップ、その他様々な用途で利用されています。
このガイドでは、二つ割の型、オーバーモールド、圧縮成形、エッグシェルモールドなど、シリコン部品の製造に使用する3Dプリント製の型の概要をご紹介します。これらの成形方法は、軟質のシリコン製品の試作、ベータ品の少ロット量産、カスタムメイドの実製品の生産に用いられることがあります。
本ガイドでは、Formlabsのお客様であり、実際に製品設計に関わる方々から共有いただいた金型設計のベストプラクティスを取り上げながら、Apple AirTag用のカプセル型シリコンキーホルダーの製造手順を解説します。材料の使用手順やシリコンとレジンの互換性、離型の推奨手順など、さらに詳細な情報については技術資料をダウンロードしてご覧ください。
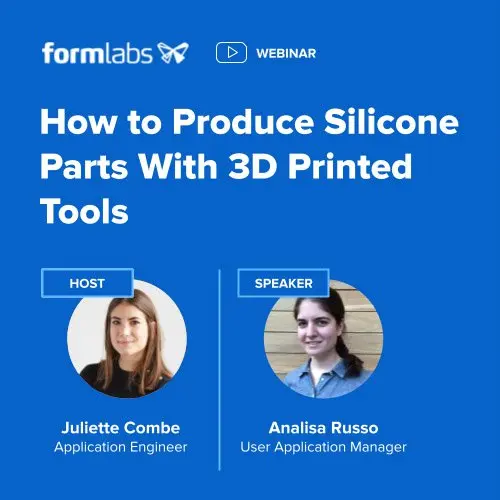
3Dプリント製の成形型を使ったシリコン部品の製造方法
シリコン鋳造用の型をSLA光造形方式で製作する際の設計について、詳細なケーススタディと共にFormlabsのお客様によるベストプラクティスをご紹介します。
3Dプリント製の型でシリコン鋳造
シリコン部品の生産に必要な金型は従来、アルミニウムやスチールの塊をCNC加工して製作していました。従来の金型には、液状シリコンゴム(LSR)を鋳造するための二つ割の型や複数部品からなる射出成形型、そして圧力と高温で硬化させる熱硬化ゴム(HCR)用のシングルキャビティ圧縮成形型などがあります。
この種の金型は大量生産で使用するのが一般的です。試作品製作で使用する場合は、製作に数週間、そして数百〜数千ドルという高額なコストがかかるため、金型の設計に細かな変更を加えて繰り返し検証を行うことが難しいのです。
金型を低コストで短期製作できるデスクトップ型3Dプリンタは、こうした問題に対処できる強力なソリューションです。大掛かりな設備が不要なため、熟練のオペレーターがより付加価値の高い作業に集中できます。3Dプリントによる内製が実現すれば、メーカーやプロダクトデザイナーは製品開発工程にラピッドツーリングを導入し、大量生産に進む前により確かな設計と材料を検証して選択できるようになります。製品開発と反復検証プロセスを高速化し、より良い製品を市場に投入できるようになるのです。
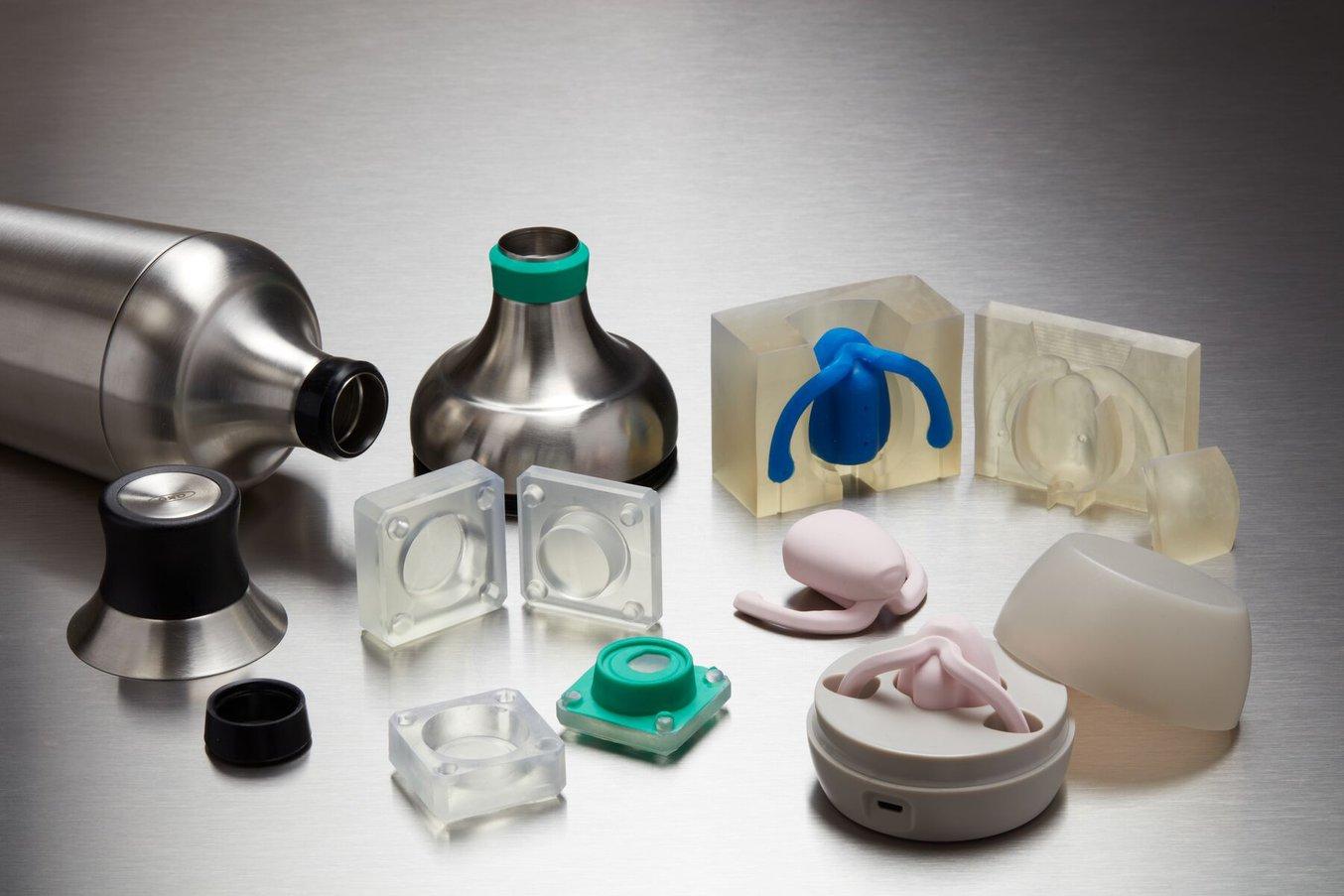
FormlabsのSLA光造形3Dプリンタで製作した型を使って成形したシリコン部品。
SLA光造形方式3Dプリントは、シリコン鋳造用の型の製作に最適です。SLA光造形方式で製作した部品は、滑らかな表面品質と高精細さが特徴です。室温加硫シリコンゴムは表面の細かなディテールまで表現可能なため、成形型の表面品質がそのまま実製品用部品の表面品質として再現されます。そのため、例えばFDM(熱溶解積層)方式で製作した型を使用した場合、型に残っている積層痕がそのままシリコン部品にも表れてしまうのです。
Formlabsの透明材料であるClearレジン(またはBiomed Clearレジンなどその他透明レジン)で作った型の場合、シリコン充填時に中身が見えるため、デザイナーは気泡やボイドが発生していないかをチェックし、コーナーフィレットの場所やエアベントを設けるべき場所を決めることができます。
また、SLA光造形3DプリントならCNC加工では不可能、もしくは製作費用が嵩みやすいアンダーカットやその他複雑な形状の型も製作が可能になります。
FormlabsのClearレジンは、幅広い機械特性を備えています。カスタムメイドのシリコン部品製作に使用する極薄のエッグシェルモールドも、ガスケット製造で繰り返し使用する頑丈な圧縮成形用型も、同じ材料で作ることができます。また、手頃な価格のベンチトップ型3Dプリンタを使用すれば部品の製造時間を削減することも可能で、デザイナーが型を3Dプリントした翌日にはシリコン鋳造を開始できるようになります。
3Dプリント製の型で室温加硫シリコンゴムを成形すると、エンボス加工など表面の細かいディテールも表現できます。加えて、鋳造可能なシリコンのほとんどは化学的に粘着性が無いため、硬化後に型から簡単に剥がすことができます。織布のように表面に無数の穴が空いている型で鋳造すると機械的結合が可能になり、専用の結合剤を使って化学的結合を促すこともできます。
OXOのシニアプロダクトエンジニアであるMack Mor氏が3Dプリントで本物のシリコン部品を高速生産する様子を動画で紹介。シリコン鋳造のデモンストレーションも。
シリコンなど鋳造用の材料が3Dプリント製の型と接触する場合、事前に2つの材料の化学反応性も確認しておく必要があります。使用可能なシリコン、レジン、保護コーティング、離型剤の組み合わせは豊富にあります。様々な業界で活躍するFormlabsのお客様にヒアリングした作業手順の成功例を、こちらの技術資料にまとめました。
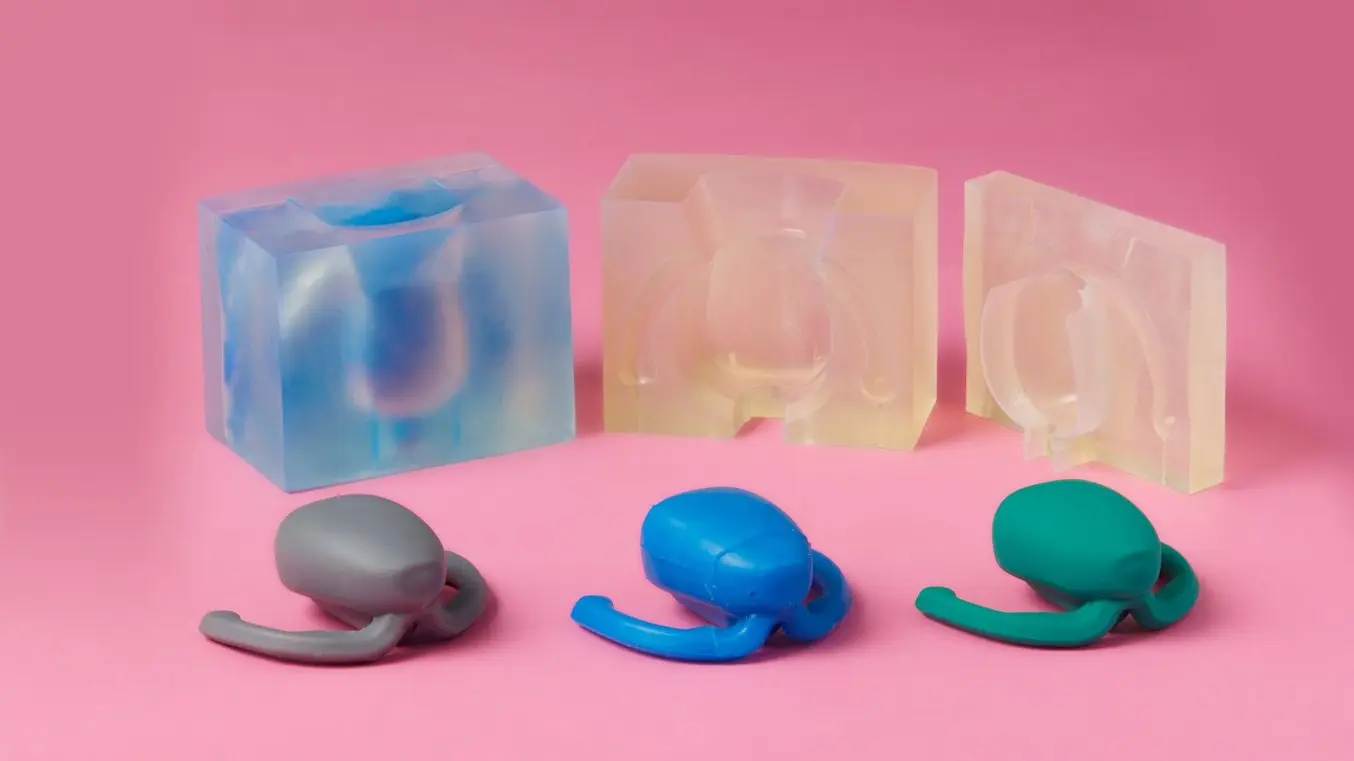
Creating Silicone Medical Devices
This guide aims to help the user decide on the best method of silicone part production for their intended use, and provides step-by-step instructions for both printing with Silicone 40A, and molding silicone using SLA 3D printed tooling (including two-part injection molds, overmolds, and compression molds).
シリコン鋳造型の製作方法
室温加硫シリコンなら鋳造工程で高温や圧力による硬化が不要なため、試作ラボの限られた設備でも簡単に成形でき、必要な初期費用を抑えながら軟質部品を製品ポートフォリオに加えることができます。
シリコン部品の製造には、目的に合った方法を取り入れることが大切です。代表的な製造方法には以下のようなものがあります。
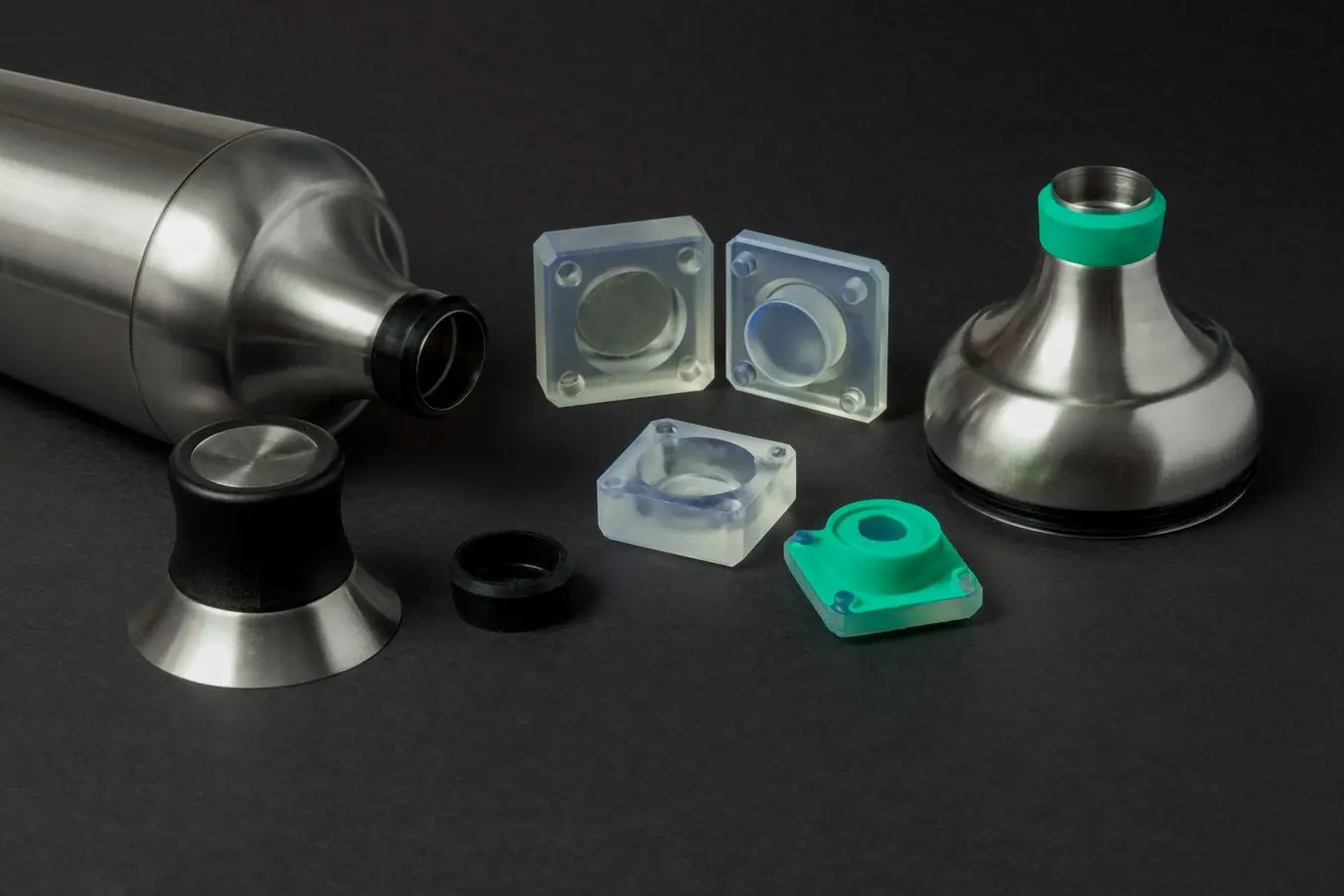
OXOは、水密ガスケットなど軟質部品の試作品を圧縮成形で製作。
圧縮成形
圧縮成形では、3Dプリント製の型の中に硬化の速いシリコンパテをはめ込み、小型の万力で締め付けます。これはガスケットの試作品製作によく用いられる方法で、大量生産用の金型を精密に再現しています。
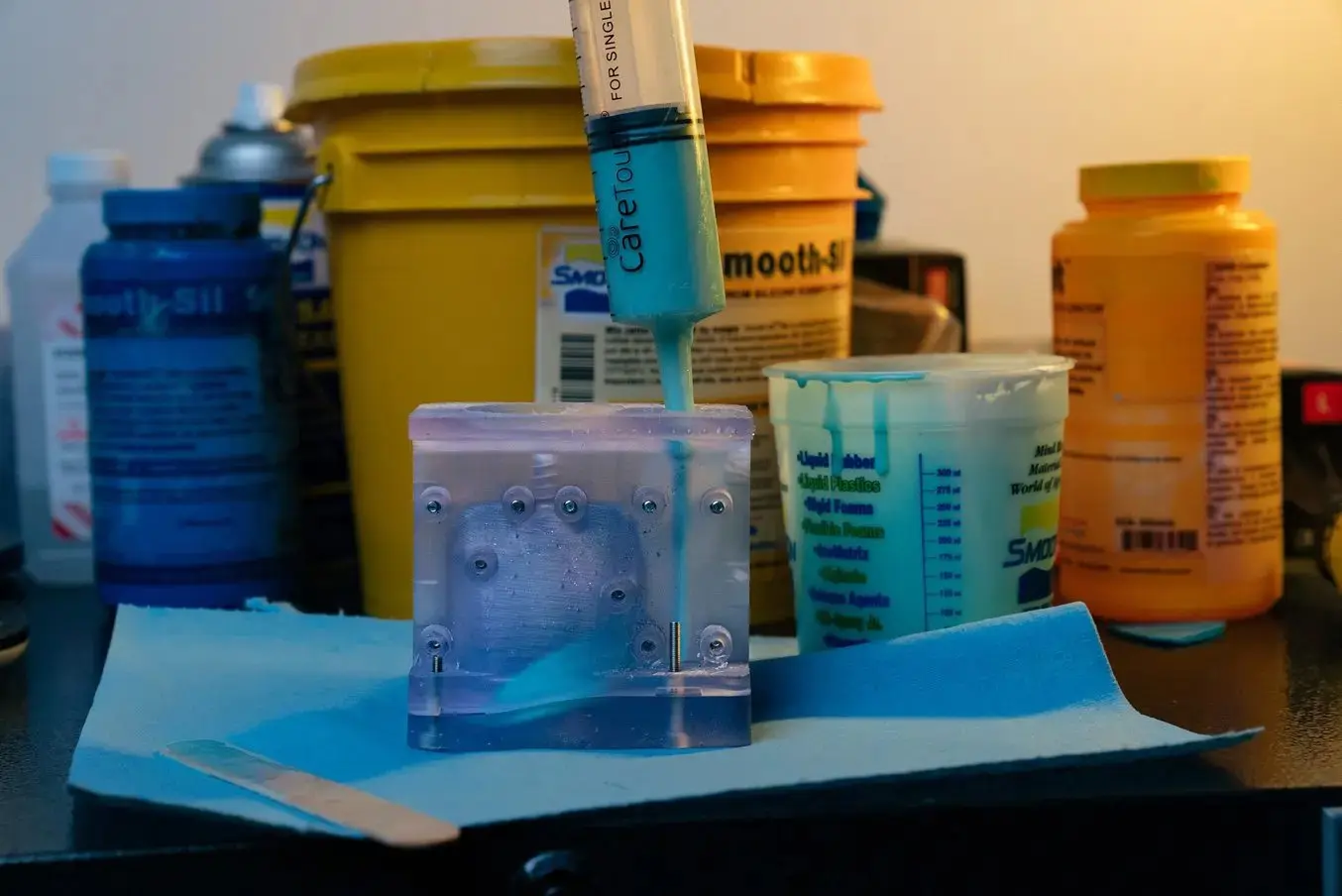
Glassboardは、シリコン製の重力射出成形型を用いてシリコン月経カップやカスタムメイドの装着具など多岐に渡る製品の試作品を製作。
射出成形
射出成形は、2つまたは複数の部品で構成される型を使って1つのシリコン試作品を製作する方法です。重力でシリコンを充填できるような設計が一般的です。型の上部からシリコンを充填すると、キャビティが下から徐々に埋まっていきます。その後、余分な液状シリコンは型上部の抜け穴と空洞から外部に出ていきます。
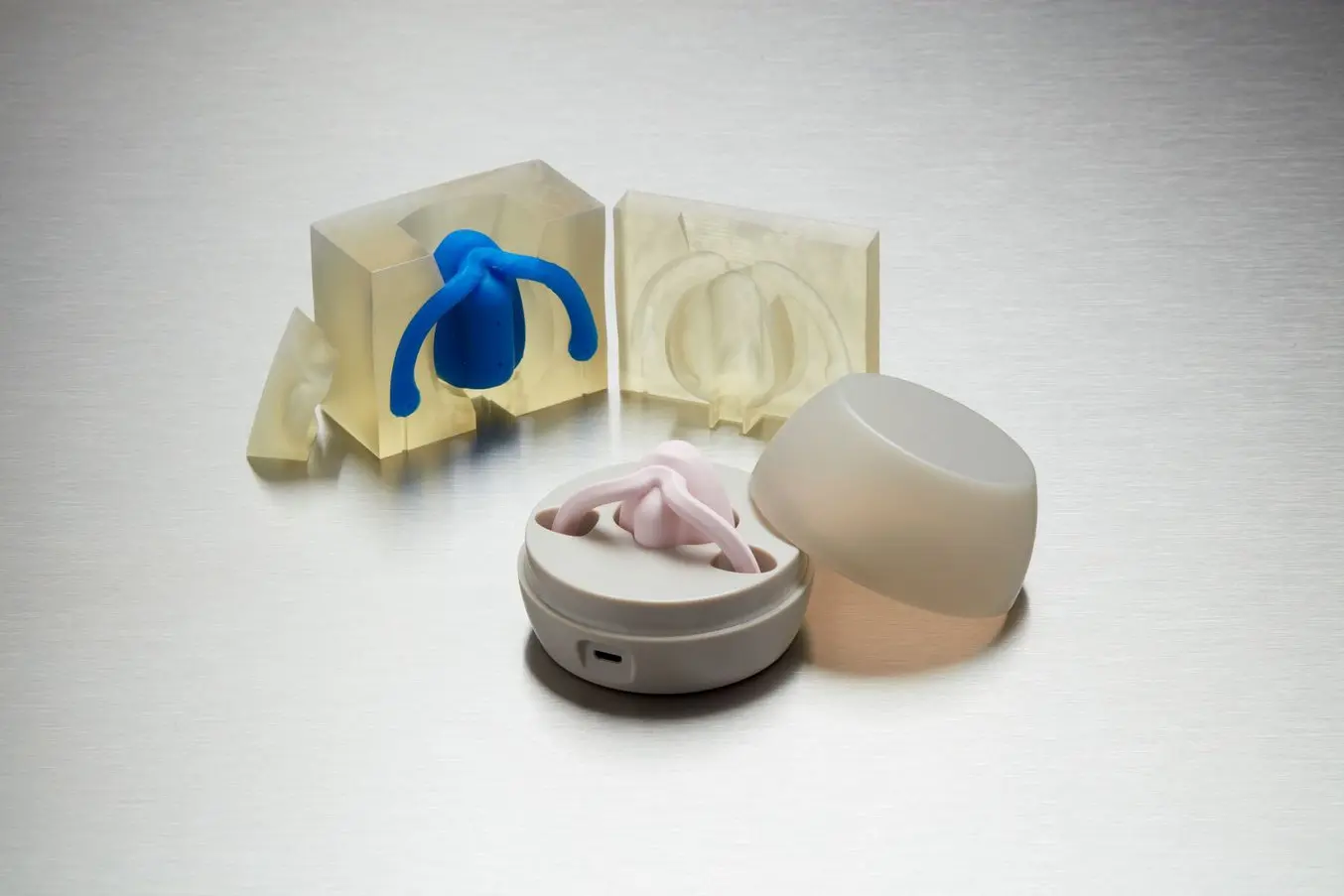
Dama Productsは、3Dプリント製の型を使ってシリコンオーバーモールドを行い、顧客用のベータ品を製作。
オーバーモールド成形
オーバーモールドは、ハードウェア筐体の一部に使用されるシリコン部品の製作に最適です。二つ割または分割式の型の間にハードウェア部品を挟み込み、外側を完全または部分的に覆うようにして液状シリコンを型のキャビティに充填します。
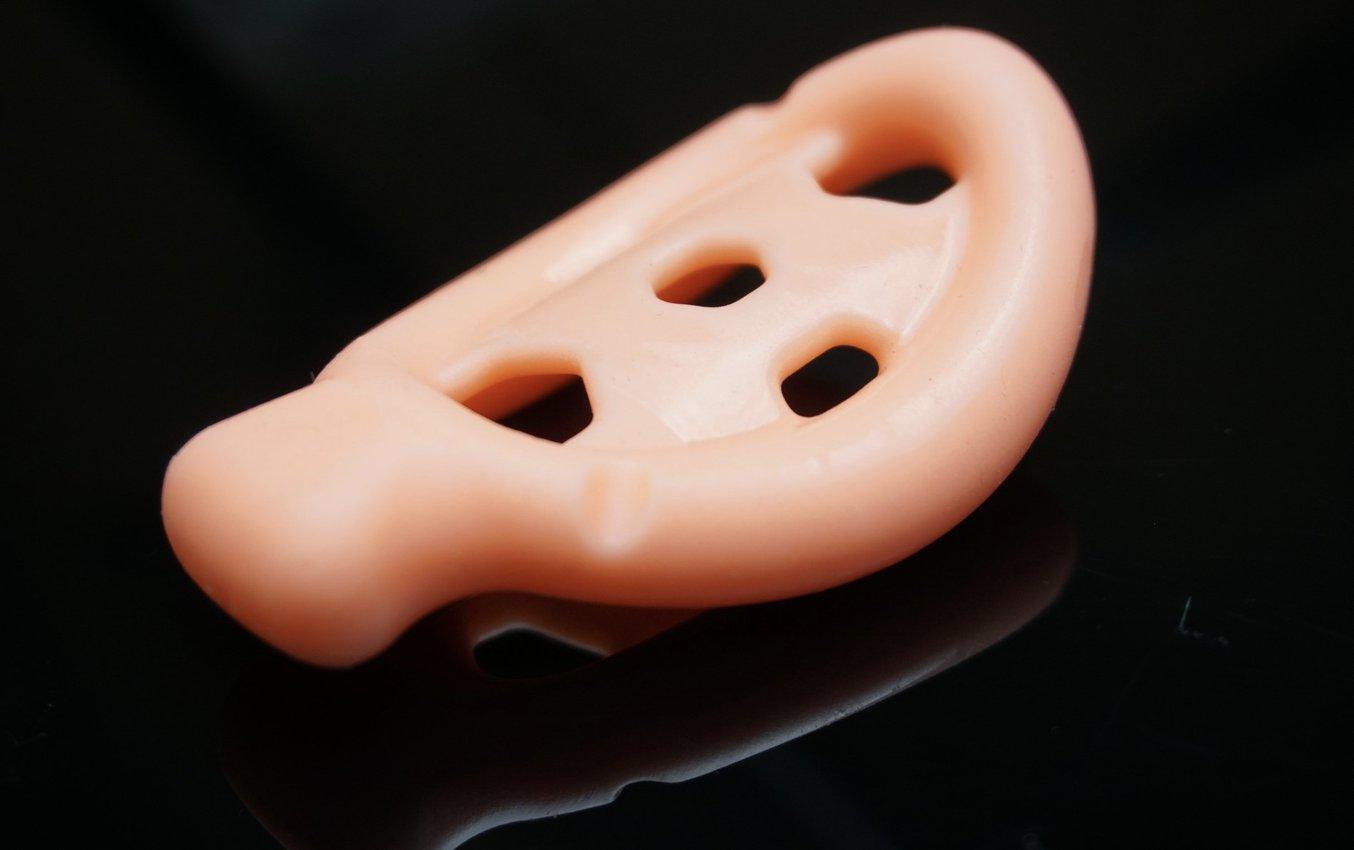
Cosmは、エッグシェルモールドで患者に合わせたシリコン製インプラントを製作。エッグシェルモールドの中に医療グレードのシリコンを充填し、完成後は型を砕いて剥がすことでカスタムメイドの部品も製作が可能。
エッグシェルモールド
この型は厚さ1mm以下と非常に薄く、砕いて剥がすことができるためカスタムメイドの部品製作に適しています。<1 mm) shell that conformally envelopes the target silicone injection cavity. After the silicone is cured, the 3D printed shell-like mold is cracked away to reveal a silicone part. Since this is a sacrificial mold that cannot be reused, this technique is used to create one single custom part. >
エッグシェルモールドの詳細については、Formlabsの補聴器製作に関する技術資料3Dプリント製の型でカスタムメイドのシリコン製補聴器を製作で詳しい手順をご覧いただけます。
完成品には成形工程ごとの違いはあまり見られないとしても、型に使用する材料を選ぶ際に考慮すべき点がいくつかあります。例えば、成形品の形状、アンダーカットや穴のあるデザインへの対応可否、生産規模、鋳造する部品に使用する材料などです。以下の表に考慮点をまとめています。
成形法 | 部品の形状 | 材料 | 生産規模 |
---|---|---|---|
圧縮成形 | アンダーカット無し | 高デュロメータ、シリコンパテ | 鋳造で数十点を製作 |
射出成形 | 小さなアンダーカット | 二つ割の液状シリコン | 鋳造で数十点を製作 |
オーバーモールド | 内部ハードウェアの包み込み、小さなアンダーカット | 二つ割の液状シリコン | 鋳造で数十点を製作 |
エッグシェルモールド | 大きなアンダーカットおよび穴のあるデザイン | 二つ割の液状シリコン | 一回限り |
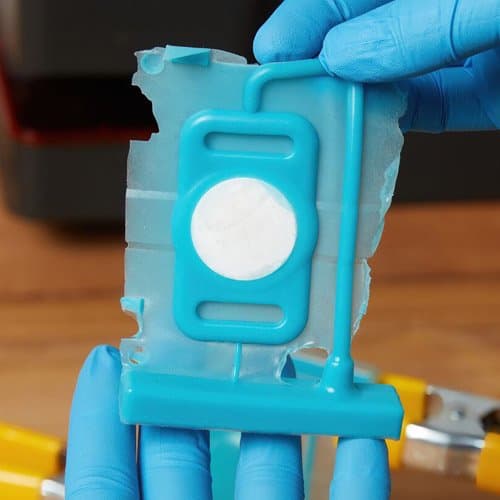
3Dプリント製の成形型でシリコン部品を生産
本製品仕様では、ベストプラクティスや導入事例など、3Dプリント製の型でシリコン部品を製造するための詳細なガイドをご覧いただけます。
シリコン鋳造型の製作方法
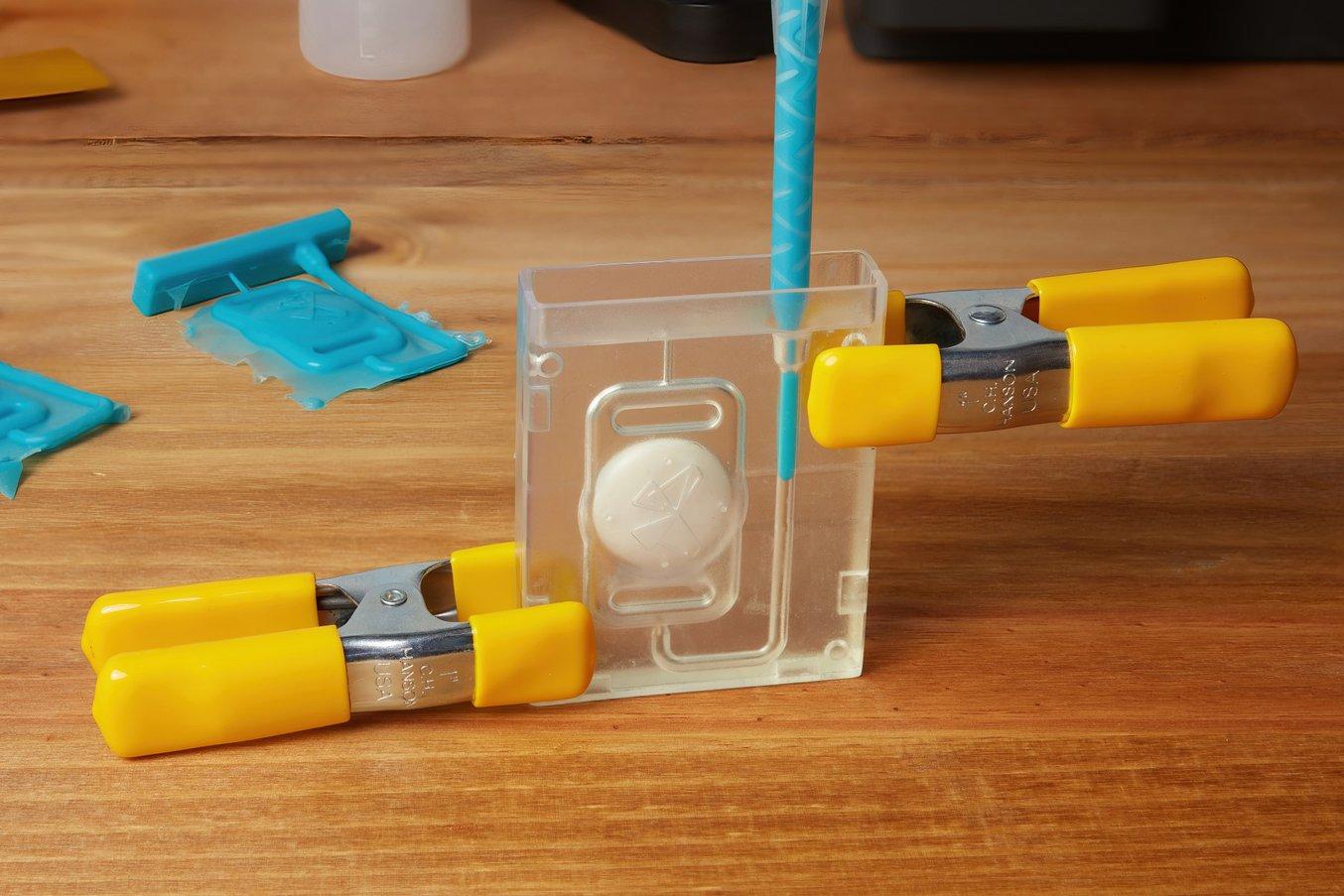
3Dプリントで高速かつ手頃な価格でシリコン部品の小ロット量産を内製化するための、シリコン鋳造用の型の製作方法をステップごとにご説明します。
この例では、AppleのAirTag用キーチェーンの型を製作します。
必要な材料と設備
材料
-
Smooth-On Dragon Skin 20(二次硬化後)
-
Silc-Pig着色顔料
-
Krylon高光沢アクリルスプレー
-
Ease Release 200
-
埋め込み型のハードウェア。今回の場合はApple Airtag。
使用機器・材料
-
エポキシカートリッジ(50:50)
-
エポキシ充填ガン
-
ミキシングノズル
-
万力
-
陰圧ブースとポンプ*
-
圧縮容器 *
*オプション
1. CADによるモデル設計
まずは成形品のCADモデルを作成します。CADソフトウェアを使用するか、既存製品を3Dスキャンしてリバースエンジニアリングで作成できます。
この例では、AppleのAirTagデバイスが埋め込まれたキーチェーン用の型を製作しますので、AirTagのデジタルレプリカを使用しました。
2. シリコン鋳造型の設計
こちらの技術資料では、このプロジェクトで用いた3Dプリント製の型の設計方法をステップごとに解説しています。ここでご紹介する基本的な設計工程やベストプラクティスは、重力で充填をする射出成形やオーバーモールドにも適用できます。
-
埋め込み型のハードウェアを含めたベースボリュームの設計
-
割り線を定め、上型と下型に分離
-
型からベースボリュームの取り外し
-
シリコンを流し込む充填ゲートを設計
-
エアベントの場所を決定
-
埋め込み型ハードウェア用に固定箇所を追加
-
上型と下型の嵌合部を追加
-
シリコン用のスプルーを設計
-
シリンジ用に充填ゲートを修正
-
型の外部に離型用の穴を作成
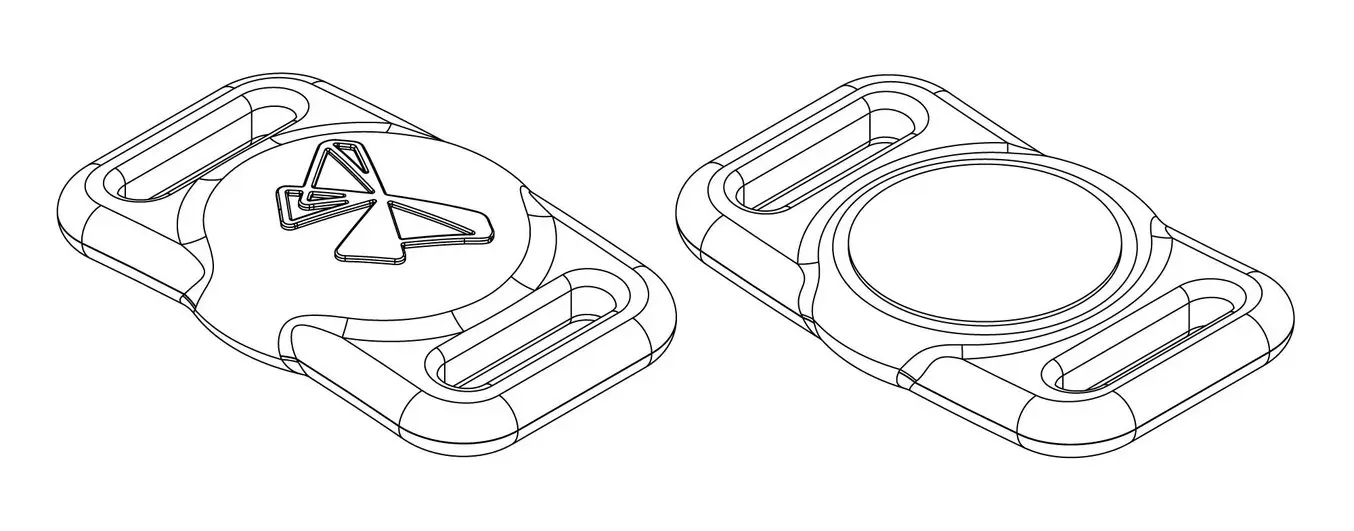
埋め込み型ハードウェアを装着した3Dモデルベース。

CADで作成した型の最終設計。
型の設計に関する詳細については、「3Dプリント製の型でシリコン部品を製作」技術資料で手順をご確認いただけます。
3. 型を3Dプリント
小さめの型ならFormlabsのSLA光造形プリンタForm 3+、大型品ならForm 3Lなど、成形品のサイズに応じて適切なプリンタを選びます。
レジンの選択肢はたくさんありますが、鋳造中にシリコンの流れを確認したい場合は透明材料のClearレジンやBiomed Clearレジンが最適です。
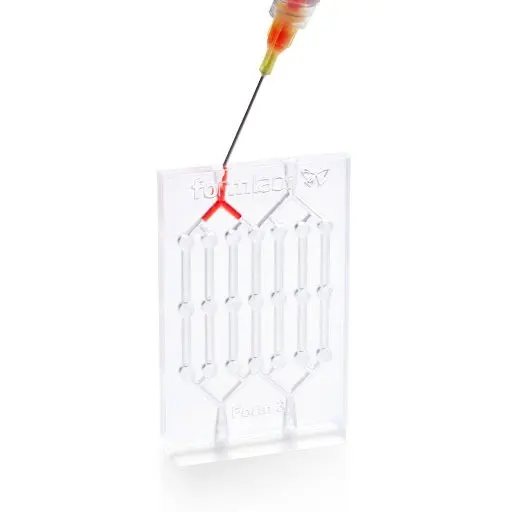
Formlabsの無料造形準備ソフトウェアPreFormを使って、モデルの造形準備やプリンタへの送信を自動化できます。滑らかな表面品質を保ちながら高速造形を実現するには、積層ピッチを50ミクロンに設定することをおすすめします。
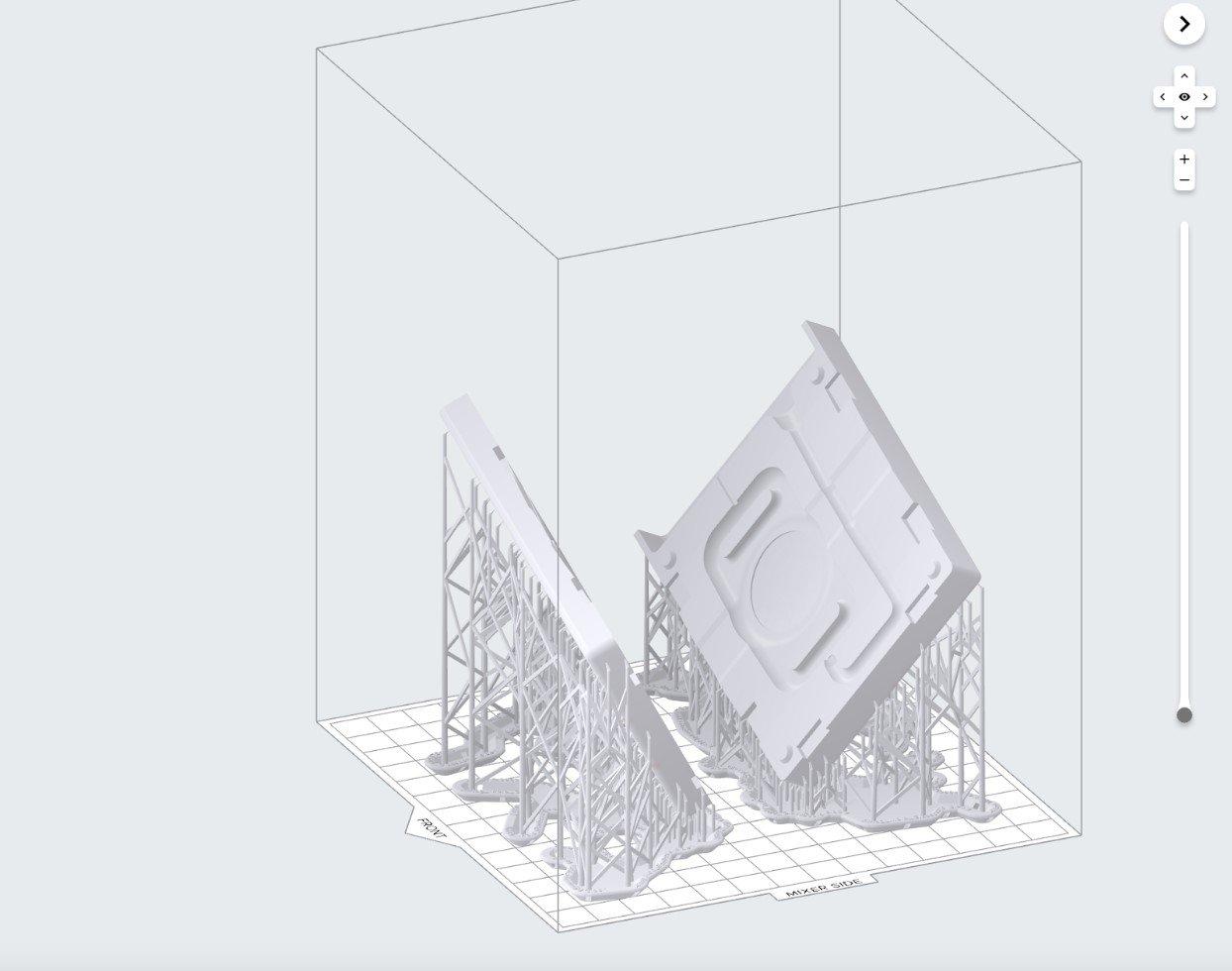
シリコン鋳造型の造形準備。PreFormでサポート材を自動生成できる。
シリコン材料は積層痕も含めて表面の細かいディテールをすべて表現できるため、外観が重視される用途では積層ピッチを25ミクロンにする必要があるかもしれません。ビルドプラットフォーム上で造形品の向きを調整し、重要な内側の表面にサポート痕が残らないようにします。ビルドプラットフォームに型を水平に置くと最適にプリントできる場合もあります。
プリントが完了したら、造形品を洗浄・二次硬化してサポート材を取り外します。
4. 型の組立と充填
鋳造前の準備として、型に保護用コーティングと離型剤を塗ります。2つの異なる材料が接触し合う時は、離型剤の使用をおすすめします。例えば、オーバーモールドで成形したシリコン製の筐体カバーに埋め込む着脱可能なハードウェアなどがこれに当てはまります。推奨手順については、技術資料で弊社お客様の作業手順をご覧いただけます。
材料ごとのガイドラインに従い、コーティングが完全に硬化・乾燥したら次の手順に進みます。
絞り方向に向かって慎重に型を固定し、型と埋め込む対象の位置がしっかりと合うようにします。
型を万力で締め付けながら、シリコンを流し込む。
使用するシリコン材料を準備し、型に流し込みます。使用するシリコン材料の選択については、こちらの技術資料をご確認ください。
5. 離型と後処理
次に、離型をして成形品から余分な部分を切り落とします。成形では、分割線の内側から周りにかけてバリができます。まずは型の外側に溢れ出た余分なシリコンを取り除きます。離型用の穴にマイナスドライバーや平らな工具を挿入し、角度をつけることで徐々に型をこじ開けていきます。型が開いたら、シリコン部品を取り出します。この時、シリコンの一部がエアベントに入り込んでいる場合は丁寧に切り取ります。
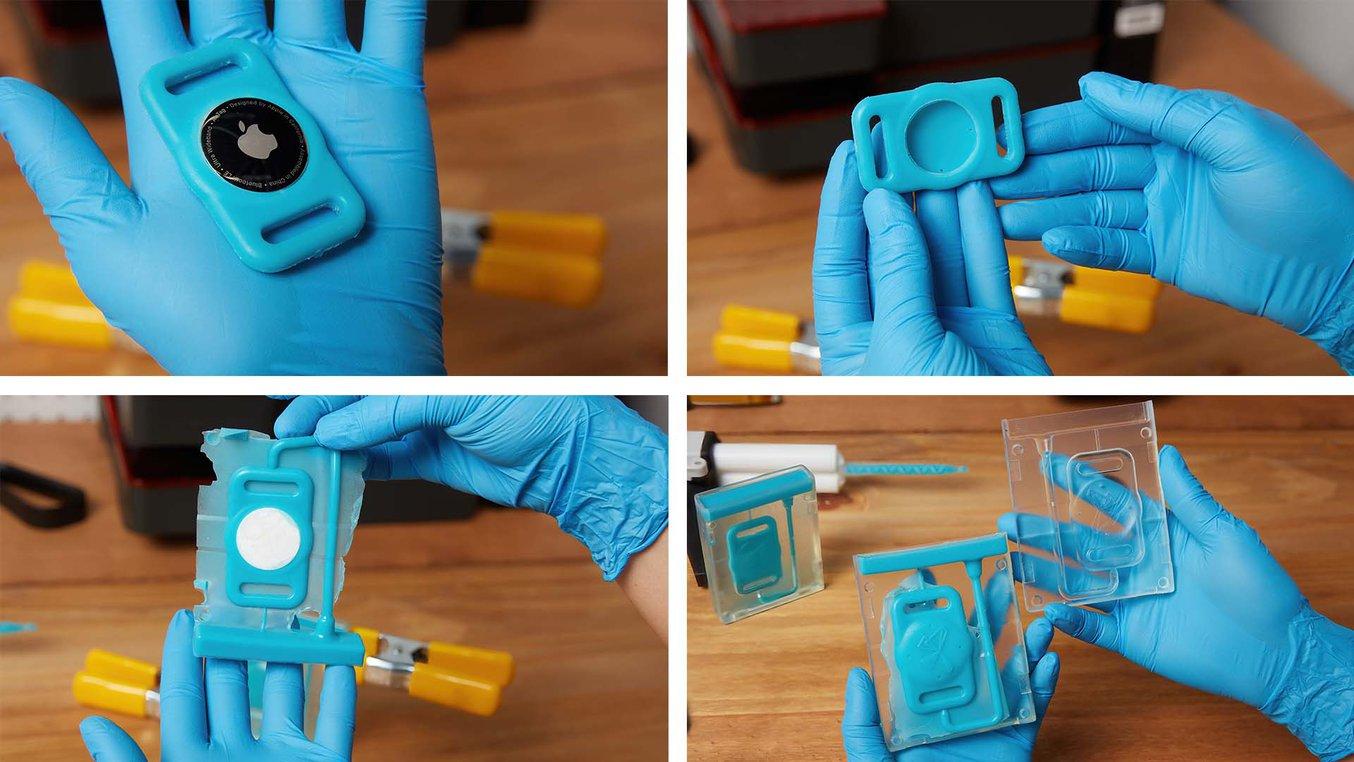
離型後に余分なシリコンを切り取ったら、3Dプリント製の型で成形したApple AirTagデバイス用のシリコンキーチェーンが完成。
型から成形品を取り出したら、鋭利なカミソリやバリ取りカッターを使って成形品からエアベントとゲートを切り落とします。残った突起などは、目の細かいウェットサンドペーパーで優しく取り除いていきます。最後に、石鹸と水で成形品を洗浄し、サンドペーパーや離型剤の残留物を除去します。
型の種類によっては繰り返し使用も可能です。もう一度シリコンを流し込む前に、鋭利な工具を使ってベントの中を掃除し、離型剤を再度塗っておく必要があるかもしれません。
手順を最初から最後まで通した後も、型の調整が何度か必要になることが一般的です。こういった調整には、嵌合部分間のオフセットの長さ調整や、埋め込む対象を確実に固定するための位置合わせピンの移動、シリコン充填中に気泡が発生しやすい場所へのエアベントの追加、などがあります。
3Dプリントでシリコン部品の製造を始める
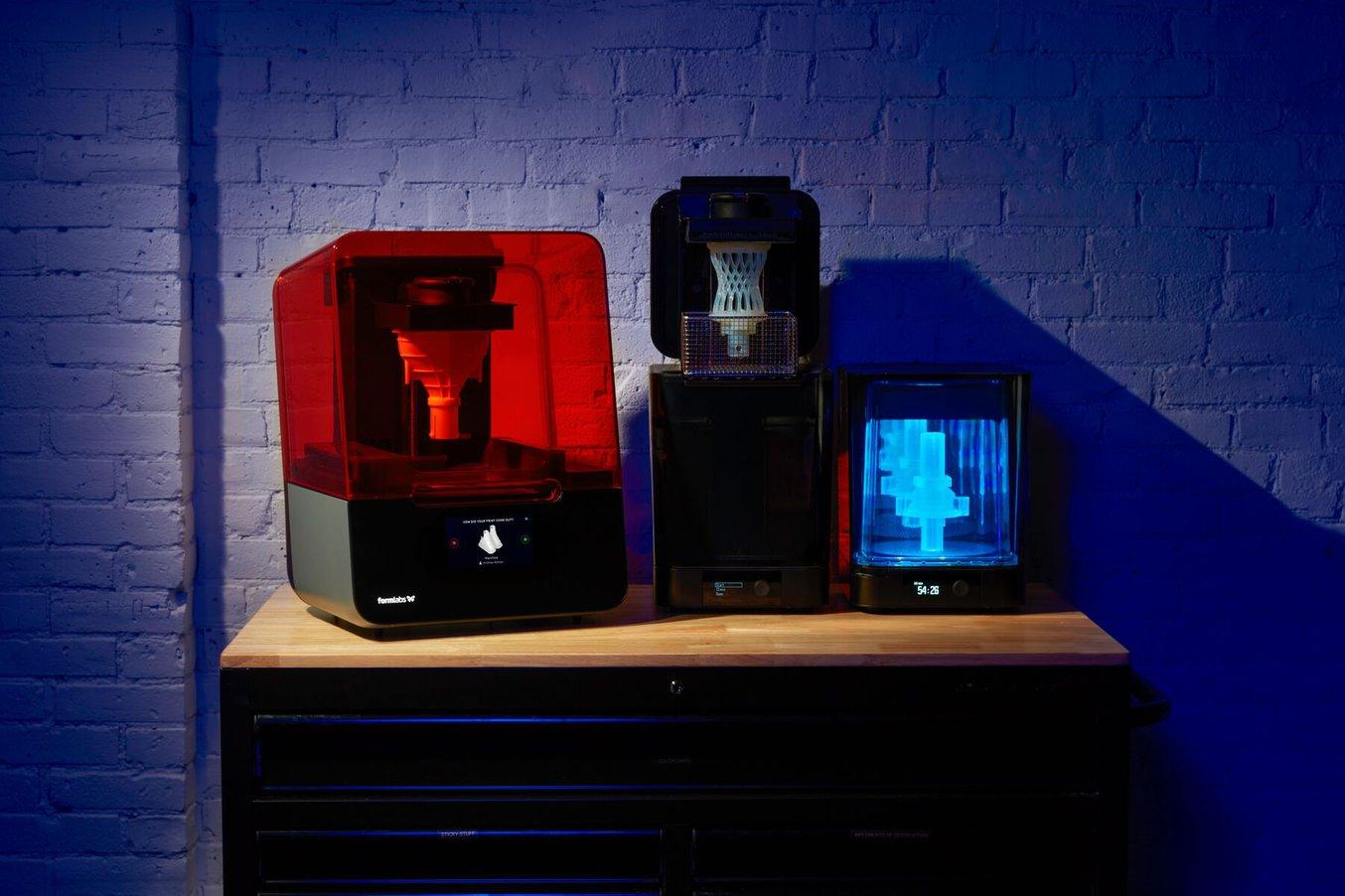
3Dプリント製の型を使ってシリコン部品を成形する場合も、他の材料での鋳造用にシリコン型を製作する場合も、FormlabsのFlexibleレジンやElasticsレジンファミリーなどのシリコンライクな軟質材料を使って部品を直接3Dプリントする場合も、3Dプリントが大いに役立ちます。
使いやすい包括的な手順で操作可能なFormlabs製品なら、3Dプリント製の型を使ったシリコン部品の生産が簡単に実現し、製品やプロジェクトポートフォリオに軟質のゴムライク部品を追加できます。
無償サンプルパーツをリクエストいただくと、Formlabsの材料で造形したサンプル品を実際に手に取ってご確認いただけます。また、お客様の用途に最適なソリューションについては、Formlabsのスペシャリストまでお気軽にご相談ください。