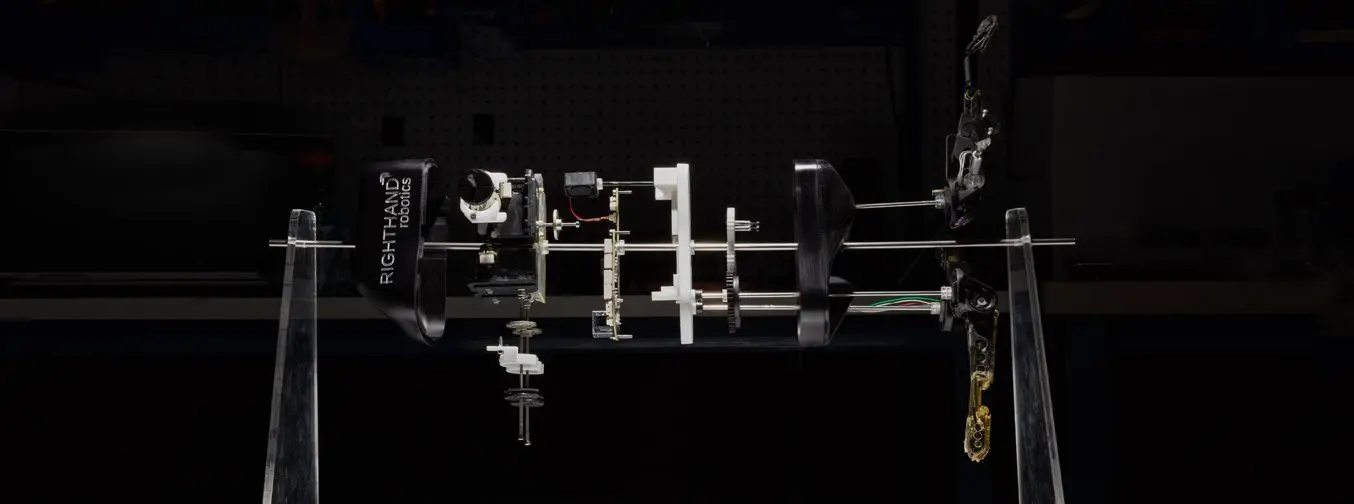
プラスチックは、消費者製品から医療機器までさまざまな実製品用部品の製造に最も広く使用されている材料の一つです。プラスチックは汎用性の高い材料カテゴリーで、数千ものポリマーが存在し、それぞれが独自の機械的特性を持っています。では、プラスチック部品はどのように作られているのでしょうか?
これまで、さまざまな用途、部品の形状、プラスチックの種類に対応するため、多種多様なプラスチックの製造プロセスが開発されてきました。製品開発に携わるデザイナーやエンジニアにとって、現在利用可能な製造オプションだけでなく、未来の部品製造を担う新しい技術についても理解しておくことが非常に重要です。
本ガイドでは、プラスチック部品を製造するための最も一般的な製造プロセスの概要と、用途に応じて最適なオプションを選択するためのガイドラインをご紹介します。
適切なプラスチック製造プロセスの選び方
製品の製造プロセスを選択する際は、以下の要素を考慮してください。
形状:製作するパーツに複雑な内部構造や厳しい公差要件は設定されていますか?設計の形状によっては、使用できる製造法が制限されたり、経済的な製造を可能にするために製造性を考慮した設計(DFM)による大幅な最適化が必要になることがあります。
生産量/コスト:製造するパーツの総数または年間の生産量はどの程度と見込まれますか?製造プロセスによっては、金型製作や設備のセットアップに高額な初期費用が必要となる代わりに、パーツ1点当たりの製造単価を低く抑えられるものもあります。一方、少量生産用の製造プロセスの場合は初期費用は低く抑えられても、1サイクルを完了させるまでの所要時間が長かったり、自動化できるステップが少なく手作業に頼る部分が多かったりするために、1パーツ当たりの製造単価が常に一定、または生産量が増えても単価を思うように低減できないことがあります。
製造期間:パーツまたは実製品をどれだけ早く完成させる必要がありますか?24時間以内に最初のパーツを製作できる製造プロセスもありますが、大量生産向けの金型製作とセットアップには数か月かかることもあります。
材料:製品はどの程度の応力や負荷に耐える必要がありますか?用途ごとに最適な材料は、複数の要因によって決定されます。コストは機能的要件と審美的要件のバランスを取る必要があります。特定の用途に対する理想的な特性を考慮し、利用可能な製造プロセス間で比較する必要があります。
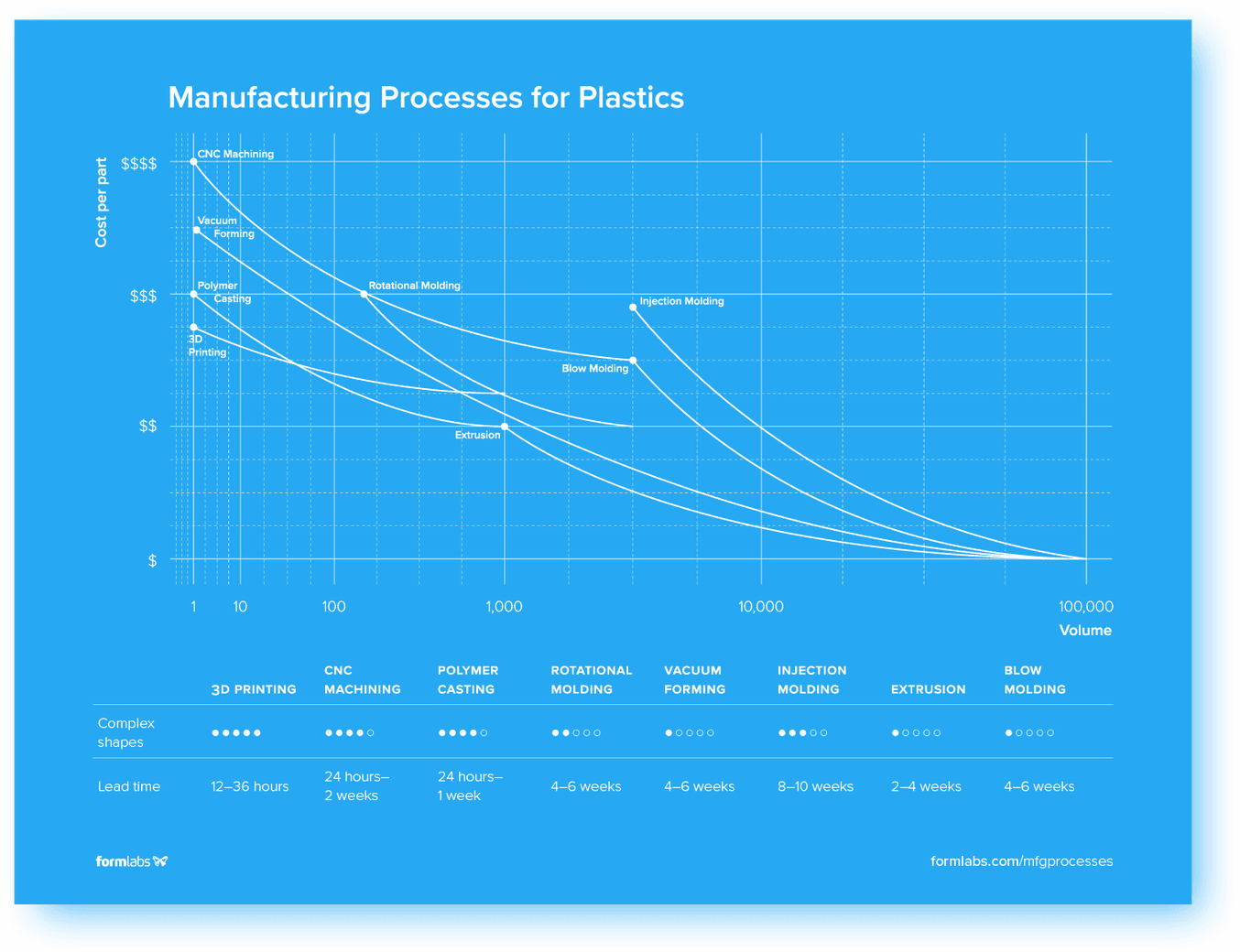
高解像度版のインフォグラフィックはこちらからダウンロードできます。
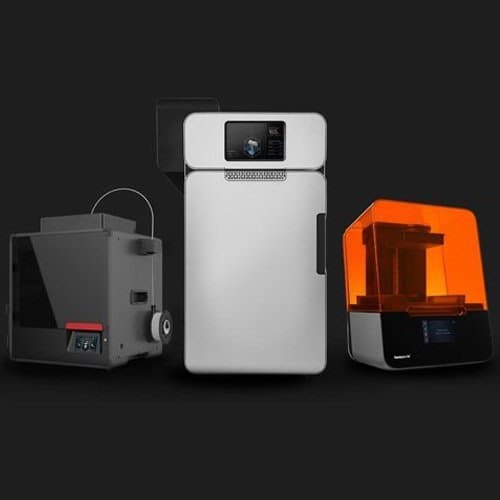
最適な3Dプリント方式の選定方法
ニーズに適した3Dプリント方式選びでお困りですか?本動画ガイドでは、FDM、SLA光造形、SLSの3方式の比較を行います。購入前の検討材料として、是非お役立てください。
プラスチックの種類
プラスチックは、基本化学物質、誘導体、添加剤によって数千もの種類があり、幅広い機能的特性や審美的特性をカバーできるよう配合されています。
特定の部品や製品に最適な材料を簡単に見つけられるよう、まずはプラスチックの中でも主要な2種類、熱可塑性プラスチックと熱硬化性プラスチックについて見てみましょう。
熱可塑性プラスチック
熱可塑性プラスチックは、最も広く使われているプラスチックの種類です。熱硬化性プラスチックと異なる主な特徴は、重大な劣化なしに何度も溶融・固化サイクルを繰り返すことができる点です。熱可塑性プラスチックは通常、小さなペレットやシートの形で供給され、加熱することでさまざまな製造プロセスの中で希望の形状に成形されます。化学的な結合が起こらないためプロセスは完全に可逆的で、リサイクルや溶解・再利用が可能です。
一般的な熱可塑性プラスチック材料の種類:
- アクリル(PMMA)
- アクリロニトリルブタジエンスチレン(ABS)
- ポリアミド(PA)
- ポリ乳酸(PLA)
- ポリカーボネート(PC)
- ポリエーテルエーテルケトン(PEEK)
- ポリエチレン(PE)
- ポリプロピレン(PP)
- ポリ塩化ビニル(PVC)
熱硬化性プラスチック
熱可塑性プラスチックとは対照的に、熱硬化性プラスチック(熱硬化性樹脂とも呼ばれます)は、硬化後に固体状態が永久的に維持されます。熱硬化性材料のポリマーが、熱、光、または適切な放射線照射によって誘発される硬化プロセス中に架橋することで不可逆的な化学結合を起こします。熱硬化性プラスチックは加熱すると溶融ではなく分解するため、冷却しても再形成ができません。そのため、熱硬化性プラスチックのリサイクルや元の材料への再生は不可能です。
一般的な熱硬化性プラスチック材料の種類:
- シアン酸エステル
- エポキシ
- ポリエステル
- ポリウレタン
- シリコン
- 加硫ゴム
製造工程の種類
3Dプリント
工業品質の3Dプリンタは、材料をレイヤーとして積み重ねていくことで、CADモデルから直接、管全体としての部品を形成します。
製造工程
- プリントの準備:造形準備ソフトウェアを使用して、プリンタのビルドチャンバー内でのモデルの向きと配置を決め、必要に応じてサポート材を追加し、モデルをスライスしてレイヤーにします。
- プリント:造形プロセスは使用する3Dプリント方式によって異なります。FDM(熱溶解積層)方式はプラスチックフィラメントを溶かし、SLA光造形方式は液体レジンを硬化させ、SLS(粉末焼結積層造形)方式は粉末状のプラスチックを焼結することで造形していきます。
- 後処理:プリントが完了したらパーツをプリンタから取り出し、洗浄・二次硬化を経て(採用する3Dプリント方式による)サポート材を除去します(サポート材を使用した場合)。
3Dプリンタを活用すると金型レスでの製作が可能で、新しい設計を反映する場合のセットアップ時間も最小限にできるため、カスタムパーツの製造コストは従来の製造プロセスと比較して無視できる程度になります。
3Dプリントプロセスは一般的に、大量生産に使用される製造プロセスよりも遅く、作業量も多くなりがちです。
しかし、3Dプリント技術の発達に伴い造形単価も下がり続けてきた今では、少量から中量規模の生産など幅広い用途での応用が可能になっています。
3Dプリント | |
---|---|
形状 | 高い自由度 |
製作期間 | 24時間未満 |
サイクル時間 | 最大1時間〜数時間。パーツのサイズや数量によって変動。 |
セットアップ費 | $ |
造形単価 | $$$ |
生産量 | 少量〜中量生産用(1~1000個) |
プラスチック製造プロセスの多くでは高価な産業用機械、専用施設、熟練したオペレーターが求められますが、3Dプリントを活用すればプラスチック部品の製作やラピッドプロトタイピングを社内で簡単に行えるようになります。
プラスチック部品の製作に使用できるコンパクトなデスクトップまたはベンチトップサイズの3Dプリンタは、価格帯も手頃で省スペース、取り扱いにも特別なスキルが必要ないことから、エンジニアやデザイナー、メーカーはこれまで数日〜数週間かけて行っていた試作・検証の反復や生産サイクルをわずか数時間へと短縮できます。
材料
市場にはさまざまな種類の3Dプリンタや3Dプリント方式が出回っています。どの材料が利用可能かは、導入するプリント方式によって変わります。
3Dプリント材料 | |
---|---|
FDM(熱溶解積層)方式 | 熱可塑性プラスチック(主にABSとPLA) |
SLA光造形方式 | 熱硬化性レジン |
SLS(粉末焼結積層造形)方式 | 熱可塑性プラスチック(主にナイロンやナイロンが入った複合材料) |
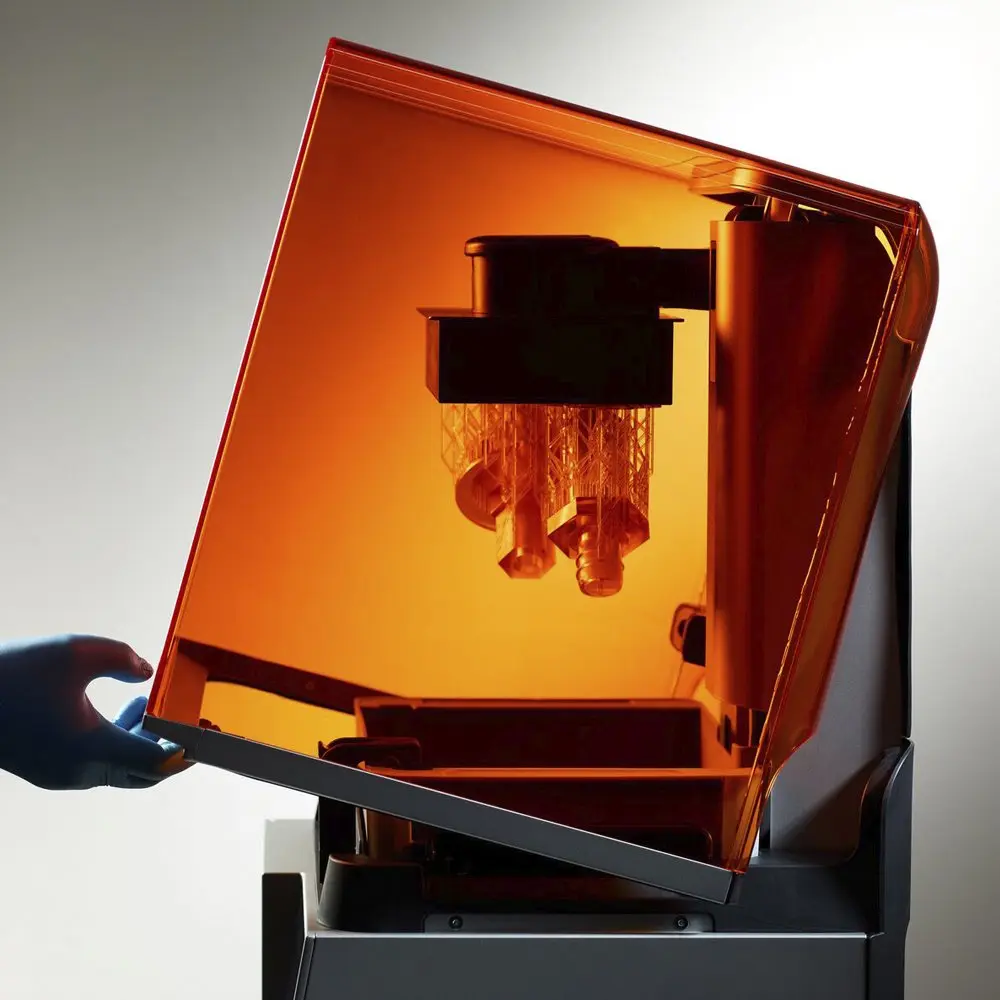
デスクトップサイズSLA光造形方式3Dプリンタの概要
高精細3Dモデルを製作できる光造形3Dプリンタをお探しですか?本技術資料では、SLA光造形プリントの仕組み、そして高精細な造形品の製作にSLA方式が選ばれる理由を解説しています。
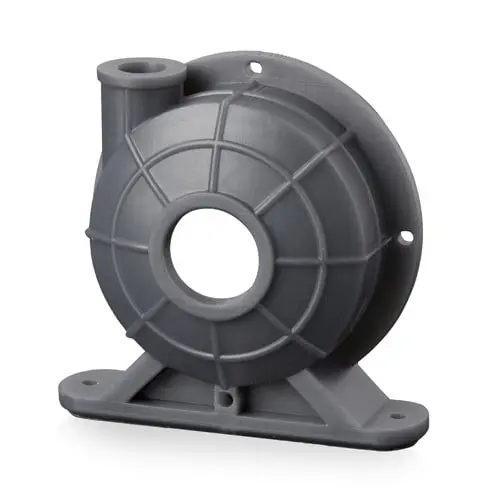
CNC加工
CNC加工には、ミル、旋盤、その他コンピュータ制御によるサブトラクティブプロセスが含まれます。これらのプロセスではまず、金属またはプラスチックのブロック、バー、ロッドなどの固形物を用意し、切削、ボーリング、穴あけ、研削などの方法で材料を削って形状を作ります。
他の多くのプラスチック製造プロセスとは異なり、CNC加工は材料を削り取るサブトラクティブ製法です。固定したワークに対してツールを回転させることで切削するフライス加工、またはツールを固定してワークを回転させる旋盤加工があります。
製造工程
- ジョブのセットアップ:CNC機械では、ツールパスの生成と検証を行う中間ステップが必要(CADからCAM)です。ツールパスは、切削工具が通る場所、速度、およびツールの交換などを制御します。
- 加工:ツールパスが機械に送られ、指定された除去加工プロセスが開始します。最終的な製品の形状に応じて、ツールヘッドが新しい領域に到達できるようワークの位置を変える必要が出てくる場合もあります。
- 後処理:切削後、ワークをクリーニングしてバリ取りやトリミングなどの仕上げを行います。
機械加工は、公差要件が厳しく成形では実現が難しい形状を持つプラスチック部品の少量製作に最適です。典型的な用途には、プーリー、ギア、菅継手(ブッシング)などの試作品や実製品用部品があります。
CNC加工は初期費用が低~中程度で、幅広い材料を使って短期間で高品質なプラスチック部品を製造できます。
しかし、加工による製造の場合は3Dプリントよりも形状の制約が多くなります。加工では製作する部品の複雑さに応じて製造単価が増加するため、アンダーカットや貫通穴、複数面にわたるフィーチャーなどはすべて製造単価の増大につながります。
加工プロセスではツールがアクセスできるようある程度余裕を持った形状が必要で、曲線を描く内部チャネルのような形状の場合、従来のサブトラクティブ工法では製造が困難または不可能です。
CNC加工 | |
---|---|
形状 | 中程度の自由度 |
製作期間 | 24時間未満 |
サイクル時間 | 最大1時間〜数時間。パーツのサイズ、デザインや複雑さによって変動。 |
セットアップ費 | $$ |
造形単価 | $$$$ |
生産量 | 少量〜大量生産用(1~5000個) |
材料
硬質プラスチックの場合はほとんどが加工可能ですが、難易度に多少の違いがあります。他のプラスチックより柔らかい熱硬化性プラスチックは加工中にワークを固定するための特殊な治具が必要で、充填プラスチックの場合は摩擦によって切削工具が短命化する可能性があります。
一般的に機械加工されるプラスチックには以下があります:
- アクリル(PMMA)
- アクリロニトリルブタジエンスチレン(ABS)
- ポリアミドナイロン(PA)
- ポリ乳酸(PLA)
- ポリカーボネート(PC)
- ポリエーテルエーテルケトン(PEEK)
- ポリエチレン(PE)
- ポリプロピレン(PP)
- ポリ塩化ビニル(PVC)
- ポリカーボネート(PC)
- ポリスチレン(PS)
- ポリオキシメチレン(POM)
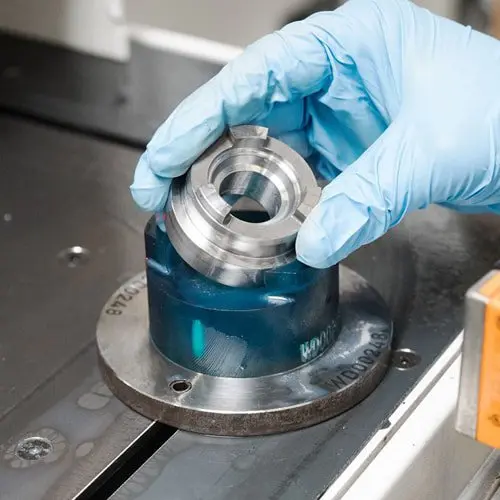
3Dプリント製の治具と固定具を活用し、製造現場にイノベーションを起こす
このウェビナーでは、冶具や固定具を機械加工せずに3Dプリントする方法を設計段階から解説し、製作現場に3Dプリント環境を置くことによって、いかに現場の作業効率が向上するかを5つの視点で説明します。
ポリマー鋳造
ポリマー鋳造では、化学反応によって固化する反応性の液体樹脂やゴムを金型に流し込みます。鋳造によく使用されるポリマーとしては、ポリウレタン、エポキシ、シリコーン、アクリルなどがあります。
製造工程
- 金型の準備:金型に離型剤を塗布します。これにより、鋳造後の部品の取り外しが容易になります。また、使用する材料に応じて金型を特定の温度まで予熱することが一般的です。
- 鋳造:合成樹脂と硬化剤の混合物を金型に注入または射出し、金型のキャビティを満たします。
- 硬化:金型内で材料が固化します(材料によっては加熱することで硬化時間を短縮できます)。
- 離型:硬化した部品を金型から取り出します。
- トリミング:鋳造時に発生したバリやスプルーを切断または研磨で取り除きます。
ラテックスゴムやRTV(室温加硫)シリコンゴムで作られた弾力性のある金型は、硬質の金型に比べて安価ではあるものの、ウレタン、エポキシ、ポリエステル、アクリルなどの化学反応によって金型表面が劣化するため、製造できる数量は25~100個程度に限られます。
RTVシリコンゴムで作る金型は非常に細かなディテールまで再現でき、高品質な鋳造品を製作できます。SLA光造形3Dプリントは、高精細で微細な形状を再現できるため、CAD設計から直接金型の原型を製作する方法として広く活用されています。
ポリマー鋳造は初期投資が少なく比較的安価ですが、鋳造用の熱硬化性ポリマーは通常、熱可塑性プラスチックに比べて高価であり、製造に手間がかかります。そのため、最終的な製造単価は射出成形などの自動化されたプロセスに比べて高くなります。
ポリマー鋳造は、プロトタイピングや短期生産、一部の歯科やジュエリー製作の用途に適しています。
ポリマー鋳造 | |
---|---|
形状 | 高い自由度 |
製作期間 | 24時間未満〜数日 |
サイクル時間 | 数分〜数日(硬化時間による) |
セットアップ費 | $ |
造形単価 | $$ |
生産量 | 少量生産用(1~1000個) |
材料
- ポリウレタン
- エポキシ
- ポリエーテル
- ポリエステル
- アクリル
- シリコン
回転成形
回転成形(ロート成形とも呼ばれます)は、粉末状の熱可塑性プラスチックを充填した中空の金型を2軸で回転させながら加熱し、主に大型の中空固体を製造するプロセスです。熱硬化性プラスチックの回転成形プロセスも存在しますが、あまり一般的ではありません。
製造工程
- 充填:プラスチック粉末を金型のキャビティに充填し、その後、金型の残りの部分を取り付けてキャビティを閉じ、加熱工程に移ります。
- 加熱:金型を加熱し、プラスチック粉末が溶けて金型の壁に付着するまで、金型を2つの垂直軸で回転させます。
- 冷却:金型をゆっくりと冷却しながら回転を続け、部品の表面が完全に固まる前に垂れ下がったり崩れたりしないようにします。
- 取り外し:金型から部品を取り外し、バリがあればトリミングで除去します。
回転成形は遠心力を利用して金型に材料を充填するため、他の成形技術に比べてツーリング費用を低く抑えることができます。金型はエポキシやアルミニウムを使ってCNC加工、鋳造、成形などで製作されます。他の成形プロセス、特に大型部品用の金型と比較してコストが低く、製作期間も短く済みます。
回転成形では、肉厚がほぼ均一な部品を製造できます。金型と製造プロセスのセットアップが一度完了してしまえば、部品の大きさに対して非常に低コストで製造できます。また、金型に金属ネジや内部パイプ、構造物などの前仕上げを追加することも可能です。
このような理由から、回転成形は短期生産や少量のブロー成形の代替として最適です。回転成形で作られる典型的な製品には、タンク、ブイ、大型コンテナ、玩具、ヘルメット、カヌーの船体などがあります。
回転成形には設計上の制約が一部ありますが、実製品の許容誤差も緩やかです。金型全体を加熱・冷却する必要があるためサイクルタイムが長く、作業量も多くなるため大量生産には不向きです。
回転成形 | |
---|---|
形状 | 中程度の自由度(大型の中空部品に最適) |
製作期間 | 数日〜数週間 |
サイクル時間 | 一般的に最大1時間 |
セットアップ費 | $$$ |
造形単価 | $$ |
生産量 | 中量生産用(200~5000個) |
材料
回転成形で最も一般的な材料はポリエチレン(PE)で、用途全体の80%で使用されています。これは、PEが室温で容易に粉末化できるためです。
一般的に回転成形に使用されるプラスチックには以下があります:
- ポリエチレン
- ポリプロピレン
- ポリ塩化ビニル
- ナイロン
- ポリカーボネート
真空成形
真空成形(または熱成形)は、プラスチックを加熱し、通常は金型を使用して成形する製造方法です。真空成形機は、低コストのデスクトップ機から自動化された産業用機械まで、サイズや複雑さがさまざまです。以下は、産業用真空成形の一般的なプロセスです。
製造工程
- クランプ:プラスチックシートをフレームに固定します。
- 加熱:シートとフレームを発熱体に近づけることで、プラスチックが柔らかく、しなやかになります。
- 真空:フレームを下げ、プラスチックを金型上で伸ばしながら、真空装置を作動させてプラスチックと金型の間の空気をすべて吸い出して成形します。
- 冷却と取り外し:金型上で成形したら、取り外し可能になるまで冷却する必要があります。ファンやスプレーミストなどの冷却システムを使用してサイクルタイムを短縮することも可能です。
- トリミング:成形品を取り外したら、手作業またはCNC機で余分な材料を切り取ります。
真空成形では低い応力と圧力で成形が可能なため、他の成形技術に比ベて金型製作費用は低く抑えられます。金型は木材、石膏、レジンを使った3Dプリントなどから作られ、短期生産やカスタム部品の製作に使用されます。大量生産の場合、メーカーはより耐久性のある金属製の金型を使用します。
熱成形や真空成形機は種類が多く、ハイエンドの機械では自動化も可能です。カスタム製品やプロトタイプから大量生産まで、あらゆる用途に適しています。しかし、このプロセスは形状の自由度が限られており、比較的薄肉の構造と単純な形状の部品しか製造できません。
真空成形でよく製造されるものには、製品パッケージ、シャワートレイ、車のドアライナー、ボートの船体、歯科用アライナーなどがあります。
真空成形 | |
---|---|
形状 | 自由度は限定的(薄肉部品のみ、複雑な形状は不可) |
製作期間 | 24時間以内〜数週間 |
サイクル時間 | 数秒〜数分(使用する機械による) |
セットアップ費 | $〜$$$$ |
造形単価 | $〜$$$ |
生産量 | あらゆる量に対応 |
材料
ほとんどの熱可塑性プラスチックは真空成形で使用可能なため、材料の選択肢は多くなります。
一般的に真空成形に使用されるプラスチックには以下があります:
- アクリル(PMMA)
- アクリロニトリルブタジエンスチレン(ABS)
- ポリエチレンテレフタレートグリコール(PETG)
- ポリスチレン(PS)
- ポリカーボネート(PC)
- ポリプロピレン(PP)
- ポリエチレン(PE)
- ポリ塩化ビニール(PVC)
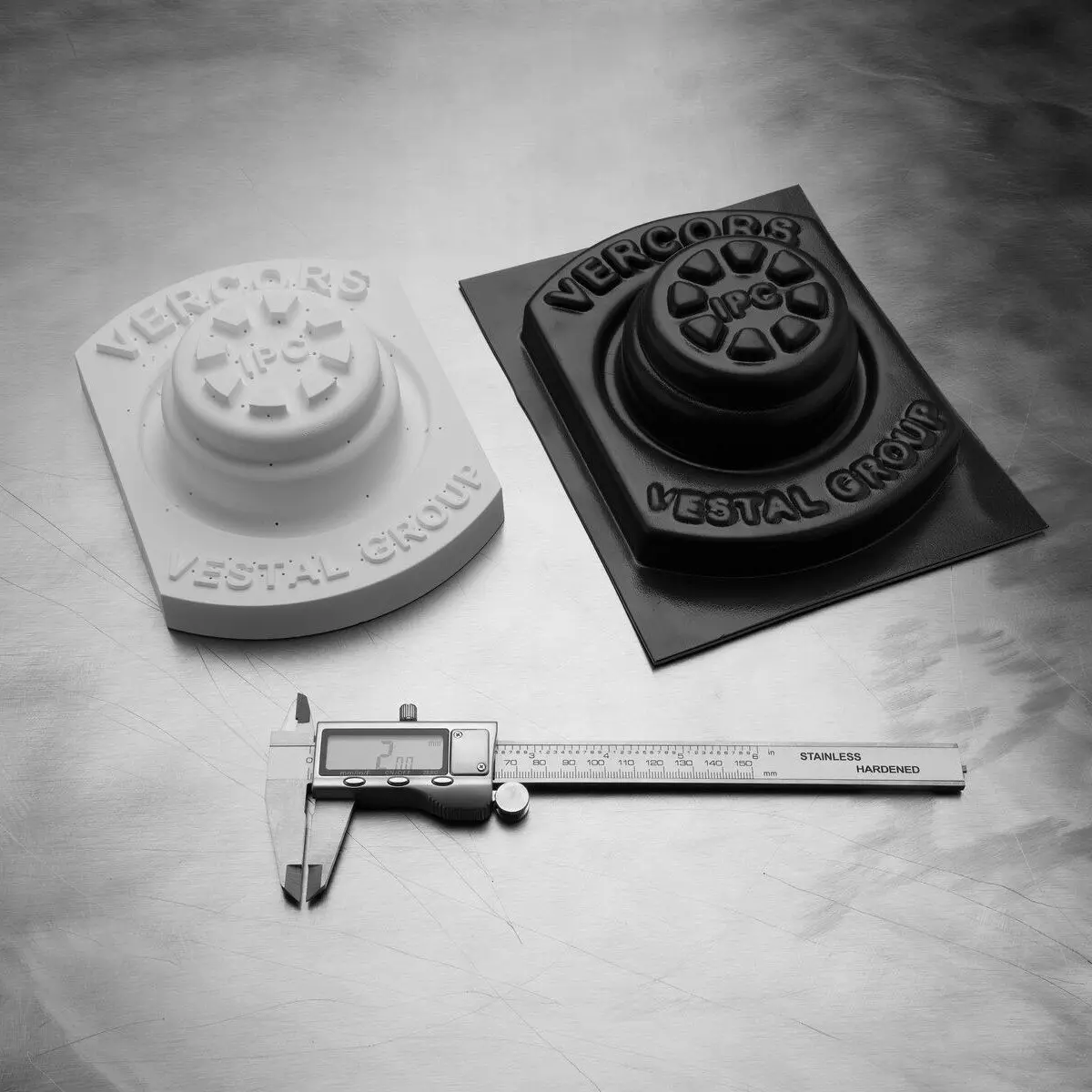
3Dプリント製の型を使用した少量高速熱成形
こちらの技術資料では、3Dプリントで複雑な成形型を短時間で製作する方法や、成形型を製作する際に参考になるヒントやガイドラインをご紹介しています。ダウンロードしてご覧ください。
射出成形
射出成形(IM)は、溶融した熱可塑性プラスチックを金型に注入して成形する製造プロセスで、プラスチック部品の大量生産に最も広く使用されています。
製造工程
- 金型のセットアップ:部品にヘリサートがある場合は、手作業またはロボットで追加します。金型を油圧プレスで閉じます。
- プラスチックの射出:小さなプラスチックペレットを溶かし、スクリューで加熱されたチャンバーに押し込みます。
- 成形:溶融したプラスチックを金型に注入します。
- 冷却と取り外し:成形品が十分に固まり、機械または圧縮空気で取り外し可能になるまで金型内で冷却します。
- 後処理:スプルー、ランナー、バリがある場合はそれらを成形品から取り除きます。このプロセスは金型開閉の一部として自動的に行われることが多いです。
射出成形用の金型は非常に複雑で、高品質な部品を製造するために厳密な公差で製造する必要があります。高温・高圧がかかるため、金型は硬化鋼などの金属を加工して製作されます。より柔らかいアルミニウム製の金型はコストが低く済むものの、摩耗が早いため通常は生産量が中程度の場合に使用されます。
射出成形は非常に複雑な部品を製造できますが、特定の形状によってはコストが大幅に増加することがあります。製造性を考慮した設計(DFM)ガイドラインに従うことで、金型製作のコストをコントロールしやすくなります。射出成形用の新しい金型の作成には数か月かかり、コストは数十万ドルに達することもあります。
初期コストが高く立ち上げにも時間がかかるものの、大量生産用途では射出成形に匹敵するプロセスはありません。一旦準備が整い設備が稼働し始めると、サイクルタイムは数秒しかかからず、他の製造プロセスの数分の一のコストで数百万個の高品質な部品を製造できます。
射出成形 | |
---|---|
形状 | 中程度〜高い自由度 |
製作期間 | 2~4か月 |
サイクル時間 | 数秒 |
セットアップ費 | $$$$$ |
造形単価 | $ |
生産量 | 大量生産用(5000個以上) |
材料
射出成形では、ほとんどの熱可塑性プラスチックが使用可能です。熱硬化性プラスチックを使用する場合は、反応射出成形(RIM)と呼ばれる類似の方法が使用されます。
一般的に射出成形に使われるプラスチックには以下があります:
- アクリル(PMMA)
- アクリロニトリルブタジエンスチレン(ABS)
- ポリアミド(PA)
- ポリエチレンテレフタレートグリコール(PETG)
- ポリスチレン(PS)
- ポリカーボネート(PC)
- ポリプロピレン(PP)
- ポリエチレン(PE)
- ポリ塩化ビニール(PVC)
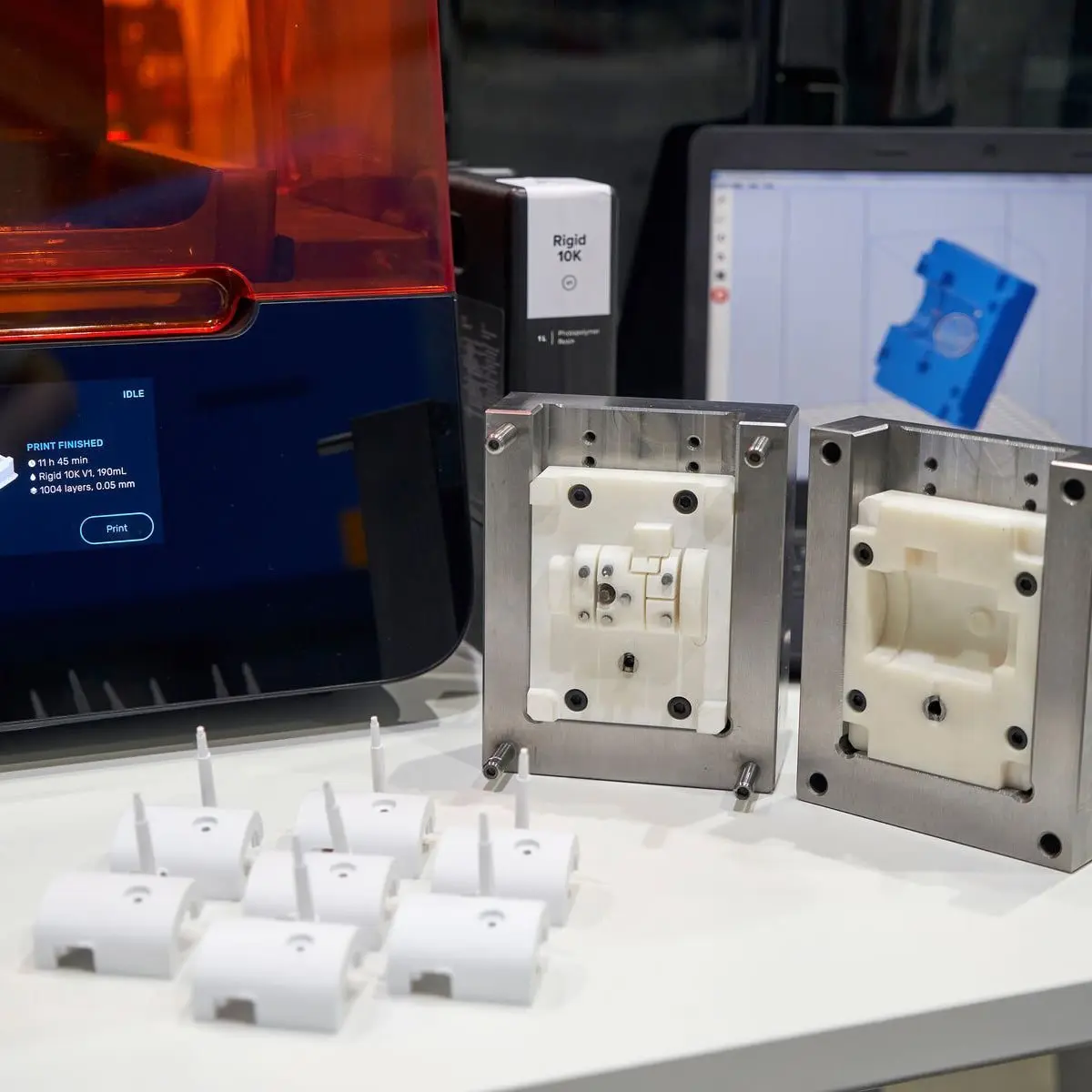
3Dプリントした金型を使った少量高速射出成形
FormlabsのWebサイトでは、3Dプリント製の型を使ってコストと時間を削減しながら射出成形を行う際のガイドライン、また実際にこの手法を導入しているBraskemやHolimaker、Novus Applicationsの事例を掲載した技術資料をダウンロードできます。
押出成形
押出成形では、プラスチックをダイに押し込みます。ダイの形状は最終的な成形品の断面形状と一致します。
製造工程
- プラスチックの押出:プラスチックを加熱し、スクリューで加熱されたチャンバーに押し出します。
- 成形:プラスチックをダイに押し込み、部品の最終形状を作ります。 '
- 冷却:押し出されたプラスチックを冷却します。
- 切断または巻き取り:連続した形状は適切な長さに切断するか、スプールに巻きつけます。
押出成形機は、CNCや射出成形などの他の産業用機械に比べてそれほど複雑ではなく、高い機械精度も必要としないため、比較的低コストで導入できます。また、形状が単純なため、ダイのコストも射出成形用の金型の数分の一程度で済みます。
射出成形と同様に、押出成形はほぼ連続的に行われるため、押出成形品の価格は非常に低くなります。
押出成形で製造できる形状は、T字型、I字型、L字型、U字型、四角形、円形などの連続した断面形状に限られます。典型的な用途には、パイプ、ホース、ストロー、窓枠の型などがあります。
押出成形 | |
---|---|
形状 | 限定的(長い連続した形状のみ) |
製作期間 | 数週間 |
サイクル時間 | 数秒(または連続) |
セットアップ費 | $$$ |
造形単価 | $ |
生産量 | 中量〜大量生産用(1000個以上) |
材料
押出成形には、下記を含むほぼすべての熱可塑性プラスチックが使用可能です:
- アクリル(PMMA)
- アクリロニトリルブタジエンスチレン(ABS)
- ポリアミド(PA)
- ポリエチレンテレフタレートグリコール(PETG)
- ポリスチレン(PS)
- ポリカーボネート(PC)
- ポリプロピレン(PP)
- ポリエチレン(PE)
- ポリ塩化ビニル(PVC)
ブロー成形
ブロー成形は、加熱したプラスチックチューブを金型内で膨らませ、目的の形状に成形することで中空のプラスチック部品を製造する方法です。
製造工程
- 金型のセットアップ:小さなプラスチックペレットを溶かし、パリソンまたはプリフォームと呼ばれる中空のチューブ型に成形します(ブロー成形のサブタイプによる)。
- 成形:パリソンを金型に挟み込み、加圧空気で膨らませて金型内の形状に合わせます。
- 冷却と取り外し:成形品が固化して取り外し可能になるまで金型内で冷却します。
ブロー成形は射出成形よりもはるかに低い圧力で行われるため、金型のコストも低く抑えることができます。射出成形や押出成形と同様に、ブロー成形は完全に自動化可能な連続プロセスであり、高い生産率と製造単価の低減を実現できます。
ブロー成形は、中空のプラスチック製品の大量生産に最もよく使用されています。典型的な用途には、ボトル、玩具、自動車部品、工業用部品、包装材などがあります。
ブロー成形 | |
---|---|
形状 | 自由度は限定的(中空で薄肉の形状のみ、複雑な形状は不可) |
製作期間 | 数週間 |
サイクル時間 | 数秒 |
セットアップ費 | $$$$ |
造形単価 | $ |
生産量 | 大量生産用(5000個以上) |
材料
ブロー成形ではさまざまな熱可塑性プラスチックが使用可能ですが、一般的な例としては以下があります:
- ポリエチレンテレフタレート(PET)
- ポリプロピレン(PP)
- ポリ塩化ビニル(PVC)
- ポリスチレン(PS)
- ポリカーボネート(PC)
- アクリロニトリルブタジエンスチレン(ABS)
3Dプリンタでプラスチック部品を高速製造
プラスチック部品の製造プロセスは常に進化しており、設備、材料、規模の経済の改善により、製造方法の考慮点も変化しています。
3Dプリントは比較的新しい技術であるものの、急速に成熟しつつある技術でもあり、ハードウェアと材料の発展、造形単価の低下により、少量〜中量のさまざまな製造用途に対応できるようになっています。
以下では、大手メーカーが3Dプリントを活用し、設計から生産までの時間短縮やコストの削減を実現している方法について詳しくご紹介しています。