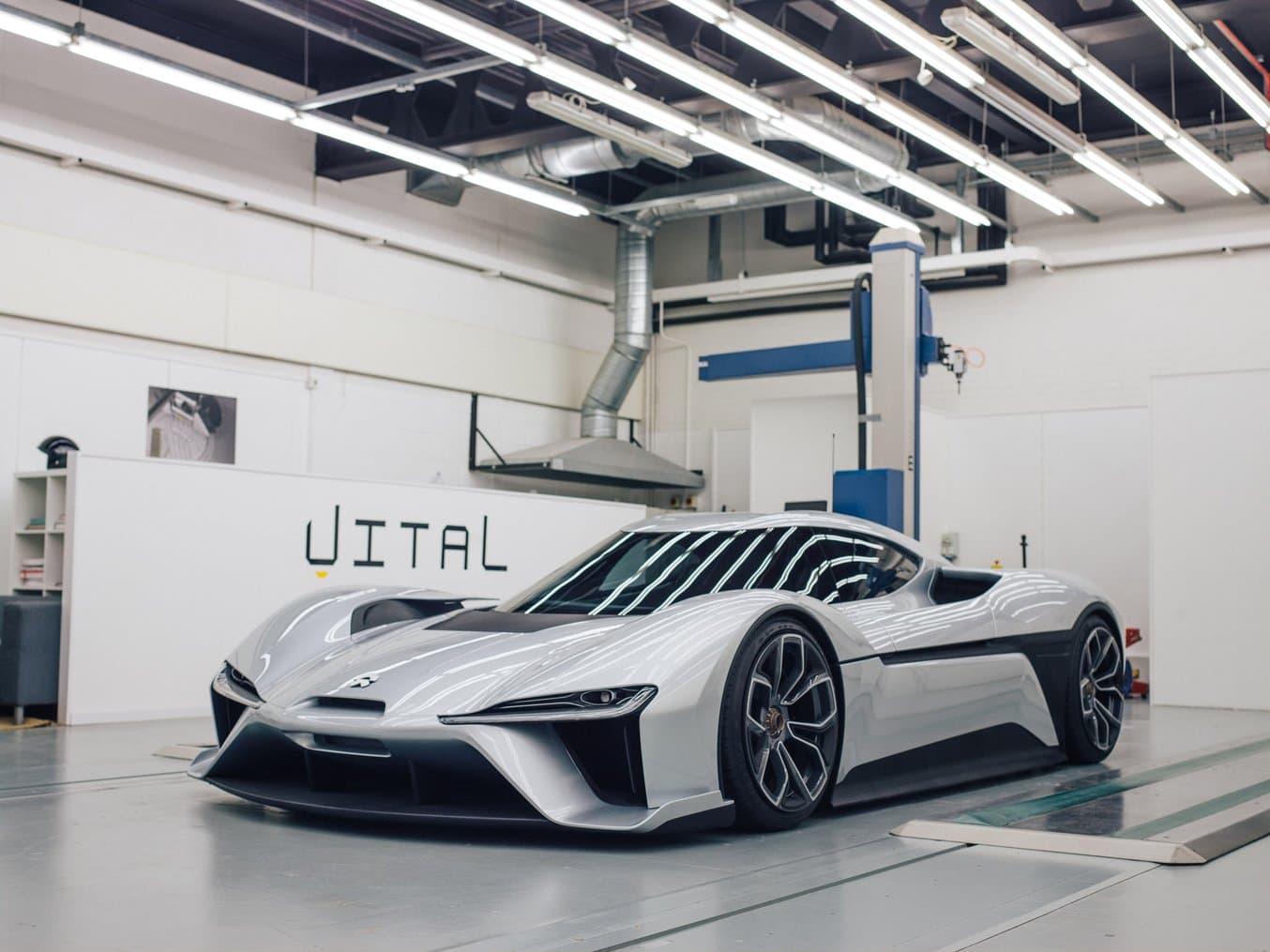
現在はディーラーで3Dプリント製の自動車を買うことはまだできませんが、3Dプリントは何年にも渡って自動車業界の開発工程で大切な役割を果たしてきましたが、近年では製造工程の幅広い場面での3Dプリントの活用がますます定着してきています。
3Dプリントでサプライチェーンに大きな付加価値を与えられるだけでなく、より広い用途への活用の可能性も広がります。3Dプリントはますます使いやすく手頃になっており、内製でのアディティブマニュファクチャリングで製造現場を支えています。弾力性のある新材料で、実製品用部品の代わりとなる高精細かつ高機能な3Dプリント部品を製作し、(マス)カスタマイゼーションや高パフォーマンスな生産を実現できる可能性が広がりますが、これはまだ始まりに過ぎません。
設計から製造、さらにその先の工程まで、3Dプリントが自動車業界全体のイノベーションを支えている9つの例をご紹介します。
3Dプリントを自動車設計と試作品製作に活用
これまで自動車業界で3Dプリントが最も活用されてきたのは、試作品製作です。3Dプリントを活用した試作品製作はスピードが格段に上がることから、ラピッドプロトタイピングという言葉は事実上3Dプリントと同義になり、このことからも3Dプリントが製品開発工程に革命をもたらしてきたことが伺えます。
3Dプリントにより、自動車設計者はシンプルな内装部品からダッシュボード、さらには自動車全体の縮尺模型に至るまで、物理的な部品やアセンブリの試作品を迅速に製作できます。ラピッドプロトタイピングにより、企業が製品構想を説得力のある概念実証(PoC)に落とし込めるようになり、そこから最終的な製品に近い忠実な試作品を製作し、一連の検証段階を経て最終的に量産を目指します。
試作品製作では試作・検証が何度も繰り返されるため、これまでは時間とコストのかかる工程でした。3Dプリントを活用することで、アイデアを具体的に表現した機能試作を僅か1日以内で、かつ従来の製造方法よりもはるかに低コストで製作できます。デスクトップ型の3Dプリンタにより、エンジニアリングチームやデザインチームが工程を内製化して試作・検証の反復サイクルを増やし、アイデアから最終的な製品になるまでの時間を短縮しすることで、製品開発工程全体が強化されてます。
1. 3Dプリントで自動車の試作を即日製作
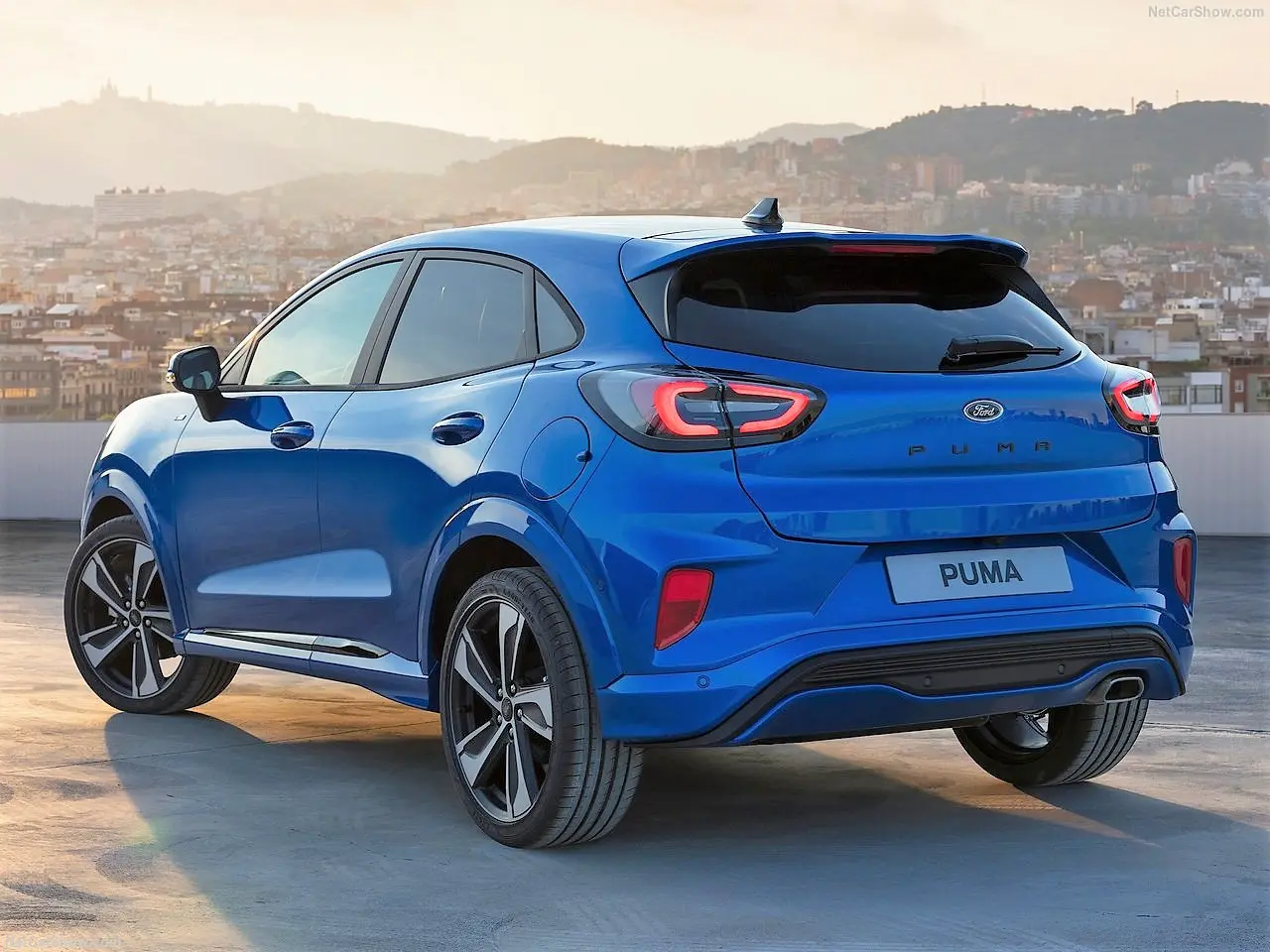
Fordのデザイナーが、Formlabsの3Dプリンタを使用してFord Pumaの車体後部のレタリング試作を数時間で製作。
ドイツのメルケニヒにあるFordのRapid Technology Centerでは、様々な3Dプリント方式を駆使して短納期で試作品を製作しています。依頼から完成品の到着まで数週間かかる外注とは対照的に、僅か数時間でエンジニアやデザイナーが試作品を手に取って確認できます。
Rapid Technology Centerでは、数時間でデザインの試作・検証を繰り返し試作品の即日製作が可能です。「物理的な試作品は、デジタルモデルよりもメリットが大きいのです」と語るのはFordのアディティブマニュファクチャリングエキスパート、Bruno Alves氏です。
例えば、Formlabsの3DプリンタでFord Pumaの車体後部のレタリング試作を製作し、デザイナーが様々な照明条件で文字の線や影の見え方を確認することができました。「造形スピードが速くこの種のレタリングには非常に効果的だったので、デザイナーに複数のデザインを出して確認してもらうことができました」とAlves氏。 「CATIAやその他ソフトウェアを使えば照明のシミュレーション自体はできるのですが、実際に車体にレタリングをつけて手触りや光の反射を目で確認できると、やはり感覚が全く違います」
3Dプリントが自動車業界大手のイノベーションを支えている様子については、Ford Motor Co.のBruno Alves氏とBroseのChristian Kleylein氏をお迎えして開催したウェビナーをご覧ください。
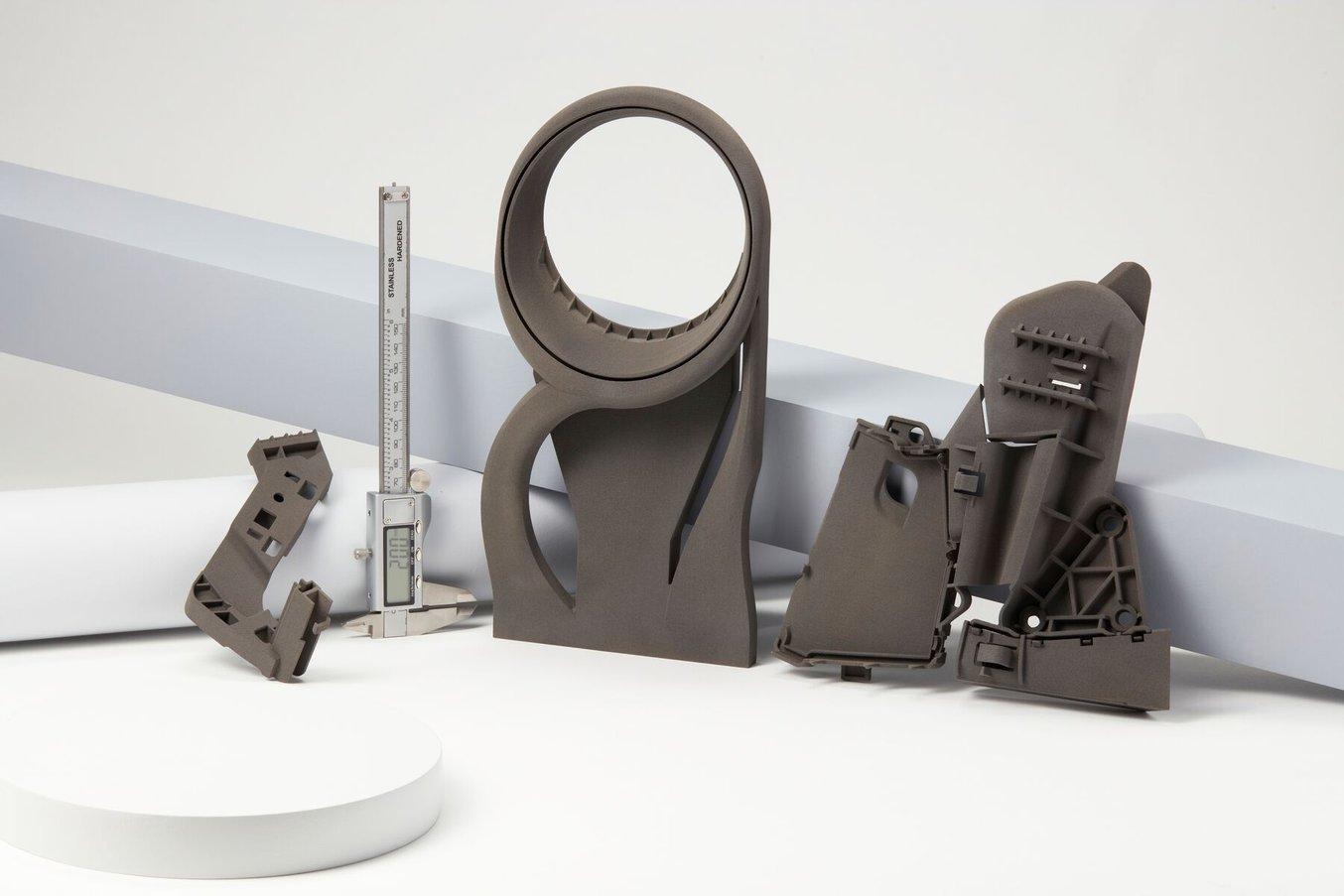
Ford、Broseの社員と語る:自動車業界大手2社による3Dプリント活用事例(英語)
このウェビナーでは、家族経営のTier 1自動車メーカーの1つであるBroseの技術者Christian Kleylein氏と、FordのアディティブマニュファクチャリングエキスパートのBruno Alves氏が、設計から製造、さらにその先の工程に至るまで、3Dプリントが自動車業界のイノベーションに貢献している事例をご紹介します。
2. 3Dプリントで自動車部品を軽量化
IGESTEKは、プラスチックや複合材料を用いて軽量化ソリューションの開発を専門とするスペインの自動車メーカーで、形状を検証する構想設計から機能確認用試作を作る詳細設計まで、製品開発工程全体で3Dプリントを活用しています。また、プラスチック射出成形用のインサートや複合材料の熱成形で使用する金型製作など、ラピッドツーリングにも3Dプリントを使用しています。
軽量化で今話題になっているのが、トポロジー最適化です。IGESTEKは、Autodesk Fusion 360を使用して一連のパラメータに基づく複数のデザインを生成しています。
サスペンションマウントを製作した時は、ジェネレーティブデザインで生成した形状の金属3Dプリントと軽量な複合材料を組み合わせたマルチマテリアルアーキテクチャで、現在市場に出ている既製品と比べて40%の軽量を実現し、最高の性能を引き出すことに成功しました。この試作品製作には、大型3Dプリンタ大容量3Dプリンタを使用しました。複数デザインの試作品を同時に製作できるだけの容量があり、試作・検証工程をさらに高速できるためです。
この用途の詳細と、IGESTEKが自動車部品の軽量化を実現した他の2つの方法については、IGESTEKの特集記事をご覧ください。
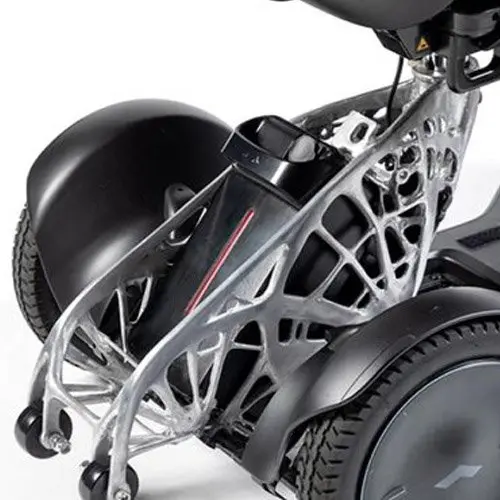
ジェネレーティブデザイン入門:3Dプリントで軽量部品を製作(英語)
本ウェビナーでは、Formlabsの製品マーケティングリードのJennifer Milneが、「ジェネレーティブデザインとは何か」について機械部品の設計の観点から概要をご説明するとともに、Fusion 360の使い方をステップごとに説明しながら実際に軽量ブラケットを製作していきます。
3. 3Dプリンタでコンセプトカーを実現
イギリスの工業用デザインスタジオVital Autoは、Volvo、日産、Lotus、McLaren、Geely、TATAなど大手自動車メーカーから業務を請け負っています。部品の製造元メーカー(OEM)が自社内で実験的な試みを行う時間がない場合、アイデアや初期のスケッチ、図面、あるいはその仕様を完全に形にするための相談がVital Auto社に持ち込まれます。
「弊社では創業当初から3Dプリントを活用しています。コスト削減だけでなく、顧客のデザインやアイデアをより多様に実現する方法として、製造工程に導入したいと考えていました」と、アディティブマニュファクチャリングを担当するデザインエンジニアのAnthony Barnicott氏は述べています。
Barnicott氏は現在、14台の大型FDM(熱溶解積層)方式3Dプリンタの他、Formlabsの大型光造形方式3DプリンタForm 3Lを3台、SLS(粉末焼結積層造形)方式3DプリンタのFuse 1を5台設置した3Dプリント部門を統括しています。「すべてのプリンタが、導入初日からほぼ100%稼働を続けています。コンセプトや設計など、すべての工程でプリンタを使用していて、通常、生産用にはFuse 1を、コンセプト用にはForm 3Lを使っています」とBarnicott氏は続けます。
3Dプリントでより良い製品をより高速に製作できるだけでなく、新しいビジネスチャンスも広がります。同社は、最新のテクノロジーに触れたい、あるいは最先端の材料でコンポーネントを作りたい、という理由で業務を依頼してくれる顧客が多くいることに気づきました。
「過去10年間での3Dプリント技術の進歩は驚異的です。導入当初は少量生産のニッチな車両に使っていましたが、今では3Dプリンタ無しでは作れない製品もあります。今ではこういった部品も作れるようになっただけでなく、非常にコスト効率良く、そして高速に生産できるのです」とBarinicott氏は語ります。
3Dプリント製部品の活用方法に関する詳しい洞察は、Vital Autoの特集記事をご覧ください。
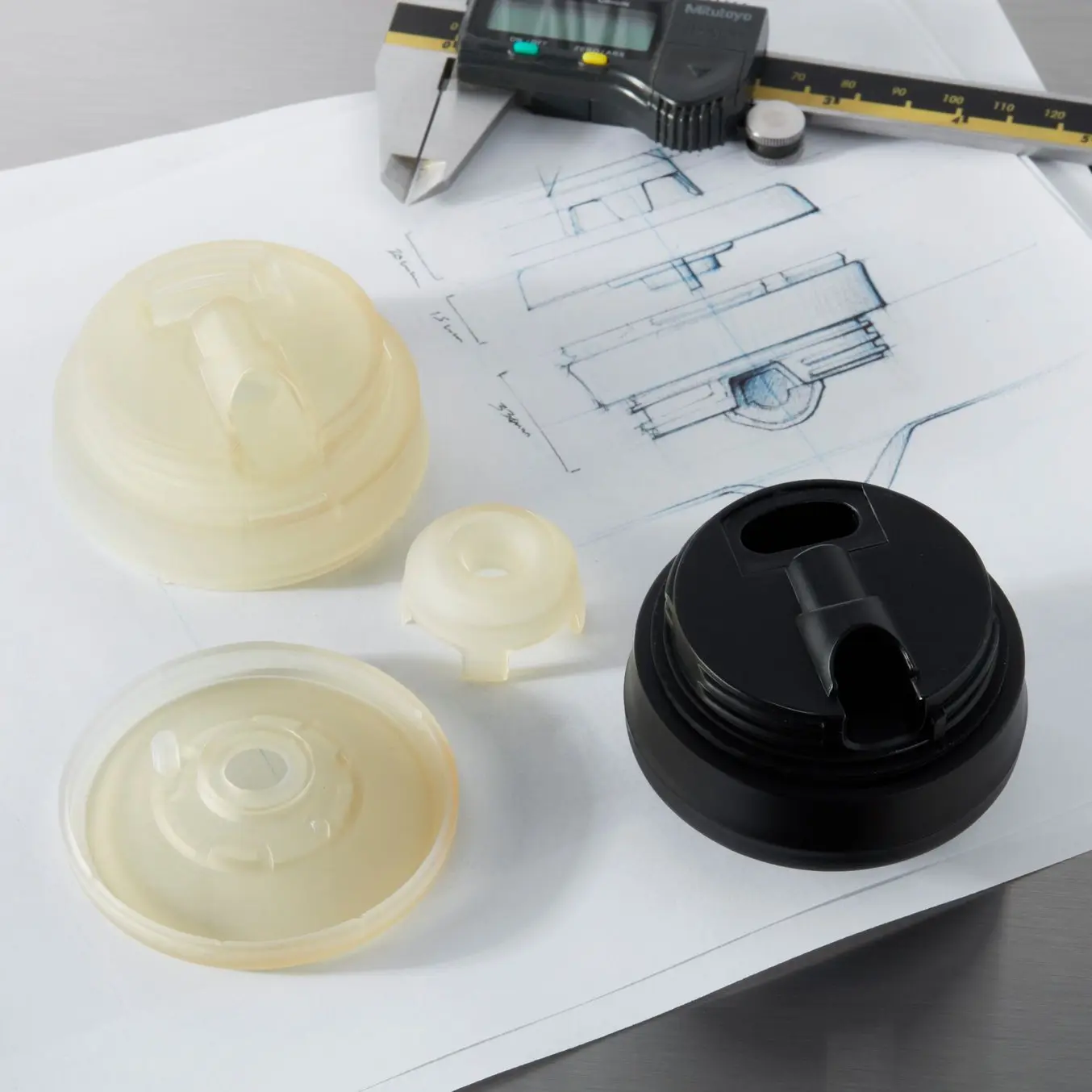
製品開発用ラピッドプロトタイピングガイド
本ガイドでは、製品開発工程にラピッドプロトタイピングを組み込む方法、活用事例、そして現代の製品開発で使用できるラピッドプロトタイピングツールをご紹介します。
自動車業界で3Dプリントを活用
3Dプリンタと高機能材料の急速な進化により、アディティブマニュファクチャリングで過酷な環境にも耐えられる部品を製造できるようになりました。
製造工程で3Dプリントを活用することで、カスタム治工具などを製作して間接費を削減し生産の効率を上げ、ラピッドツーリングで射出成形や熱成形など従来の製造法で使用する金型なども少量生産できます。
3Dプリント製の実製品用部品の活用は自動車業界でも一般的になりつつあり、特にアフターマーケット、カスタム部品、交換部品など、他の製造法ではコストも製作時間もかさんでしまう用途で使われています。
4. 3Dプリント製の金型とダイで自動車部品を製作
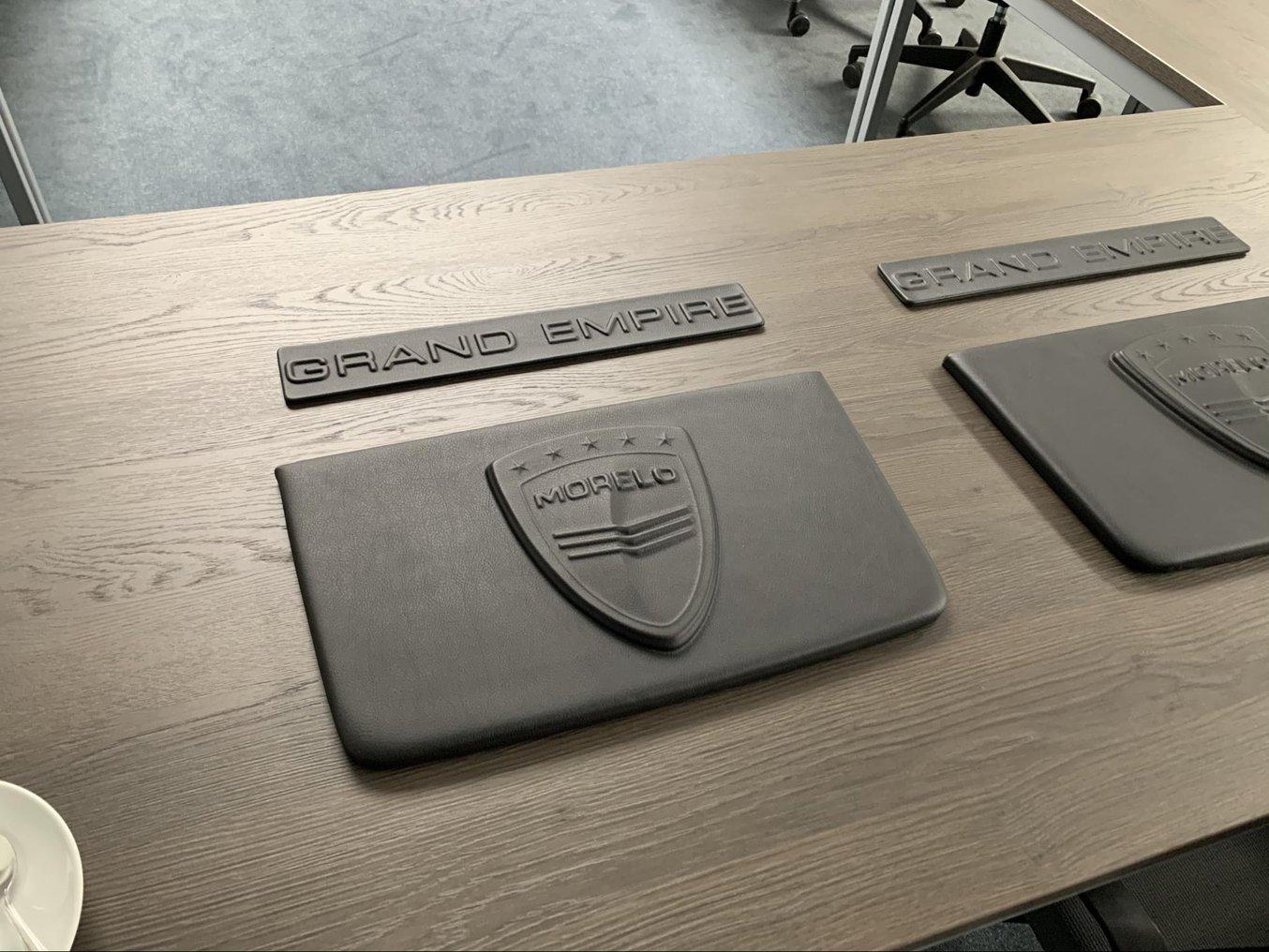
Makra Proは、3Dプリント製の金型でレザートリム品を成形する新しい手法を開発。
Makra Proはアディティブマニュファクチャリングサービスを提供するメーカーで、高級車のトリム材料として人気があるものの成形が難しいレザーを3Dプリント製の金型で成形する新しい手法を開発しました。同社は、高級車、モーターサイクル、モーターホームのメーカーなど顧客数社と提携し、本物のレザーを成形しエンボス加工を施す方法を検証しました。
Form 3で3Dプリントした金型を使うMakra Proの新技術では、発泡スチロールを使って伸ばしたレザーのパネル全体に圧力を均等に分散させます。発泡スチロールが固まると、レザーが金型に押し込まれて成形されます。
完成したレザー品は、車のドアパネルやシートカバーに装着することができます。限定版高級車のチューニングを専門とする有名企業では、この手法で成形したレザー品を車の壁や天井のパネルに使用しています。
射出成形や熱成形など、ラピッドツーリングの用途の詳細についてはMakra Proの特集記事または技術資料をダウンロードしてご確認ください。
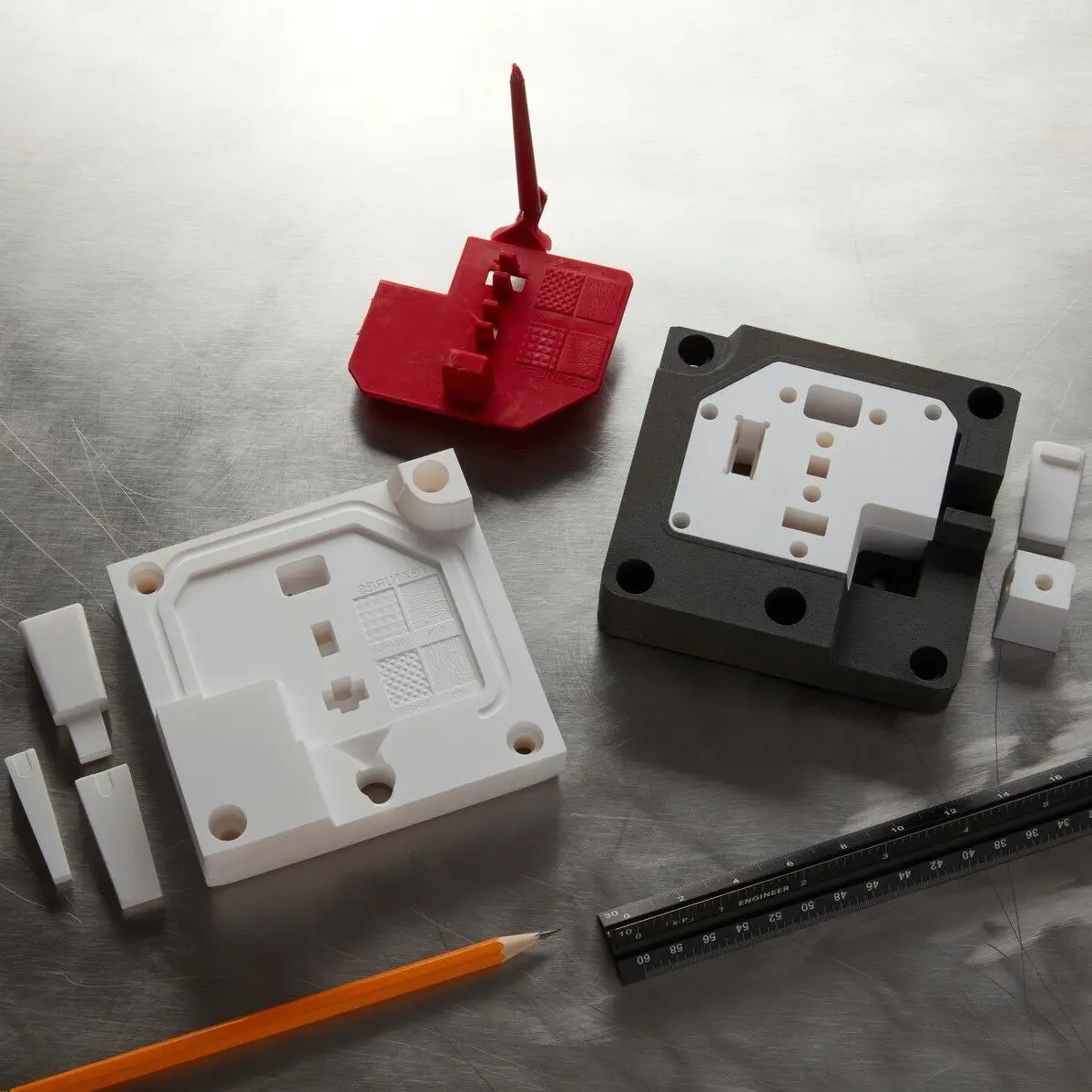
5. 3Dプリント製治具
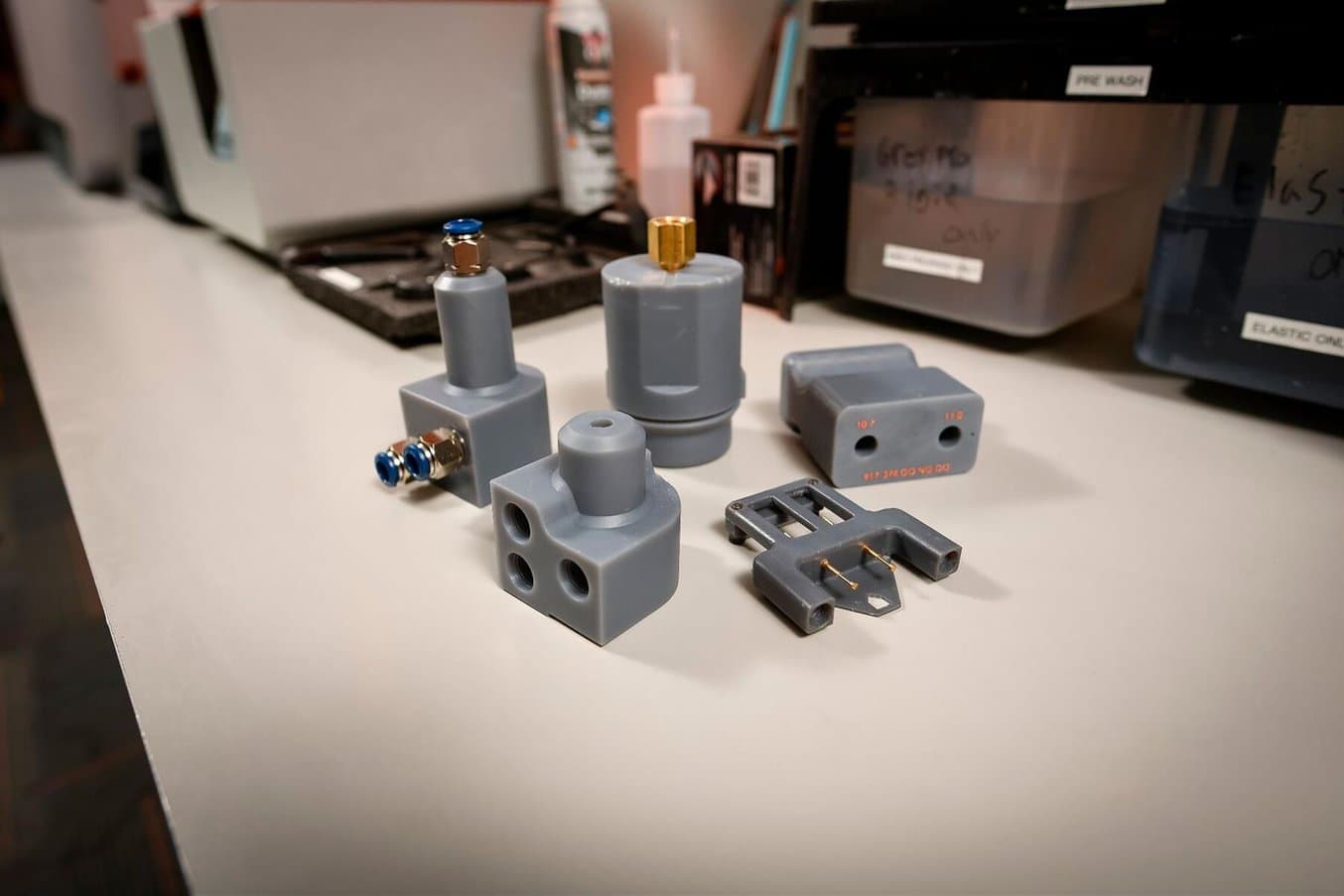
Dorman Productsは、+/-0.05 mmの精度を誇るGreyレジンを使用して合否判定用検査治具を製作している。
Dorman Productsは、何百種類もの車両用に10万点以上の部品を設計し、データベースで管理しています。「これまでずっと、新しい部品を毎年4,000から5,000点ほどリリースしてきました」とメカニカルデザインチームマネージャーのEric Tryson氏は言います。
アフターマーケットサプライヤーであるDormanの製品設計・製造チームは、単なるロジスティクスの課題だけでなく、いかに素早い対応ができるかが肝になると言うのはアディティブマニュファクチャリングリードのChris Allebach氏です。「OEMには1つの部品に専属の設計チームがいて、早い時には新車が発売される2年前から設計を開始しています。なので、私たちは信頼できる交換部品を確実に作りながら、迅速に市場投入できる方法を見つけないといけません。
3Dプリンタを使った試作・検証工程を取り入れる前は、カスタム治工具の製作が開発工程を遅らせる原因となっていました。機械加工には多額のコストと長い製作期間がかかります。
それが3Dプリンタを導入したことで、部品を試作しながら試験用の治具やゲージも製作できるようになり、今では部品の最終設計が決まる頃には試験で使う治具も出来上がっているという状態です。生産性を最大限に高めようとしているんです」とAllebach氏は言います。
Dormanが最初に3Dプリンタを導入したのは10年前。それ以来、Allebach氏とTryson氏は大容量のForm 3Lを始めとするプリンタを徐々に追加していき、既存ユニットの生産能力を高め、FormlabsのSLA光造形プリンタで使える材料を最大限に活用してきました
「[最初の3Dプリンタ]は2ヶ月以内に元が取れました。Formlabsプリンタ導入のコストの妥当性や投資利益率(ROI)について検討したところ、2年どころかわずか数か月で投資を回収できることがわかり、3Dプリントへの投資価値を経営陣にも納得してもらうことができました」とTryson氏は言います。
Dorman Productsは、他にも様々な用途で3Dプリントを使用しています。詳細については、弊社の記事をご覧ください。
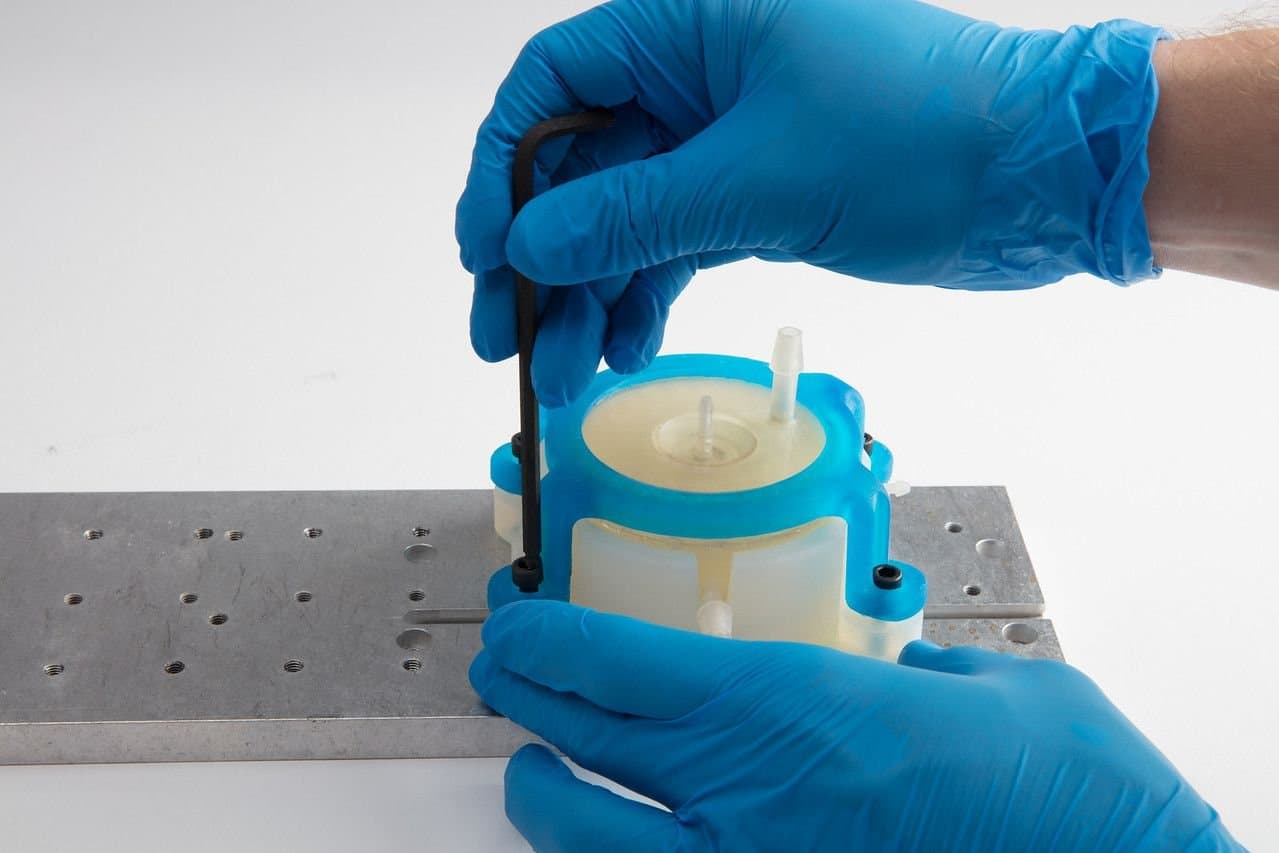
3Dプリント製治工具の設計
メーカーにとって、生産スピードの最大化と高品質の維持を両立させることは何よりも重要です。治工具は、製造工程や組立工程の効率化や安定化、サイクル時間の短縮、作業者の安全性向上などの目的で使用されます。
6. 3Dプリントで実製品用アフターマーケットの部品を製作
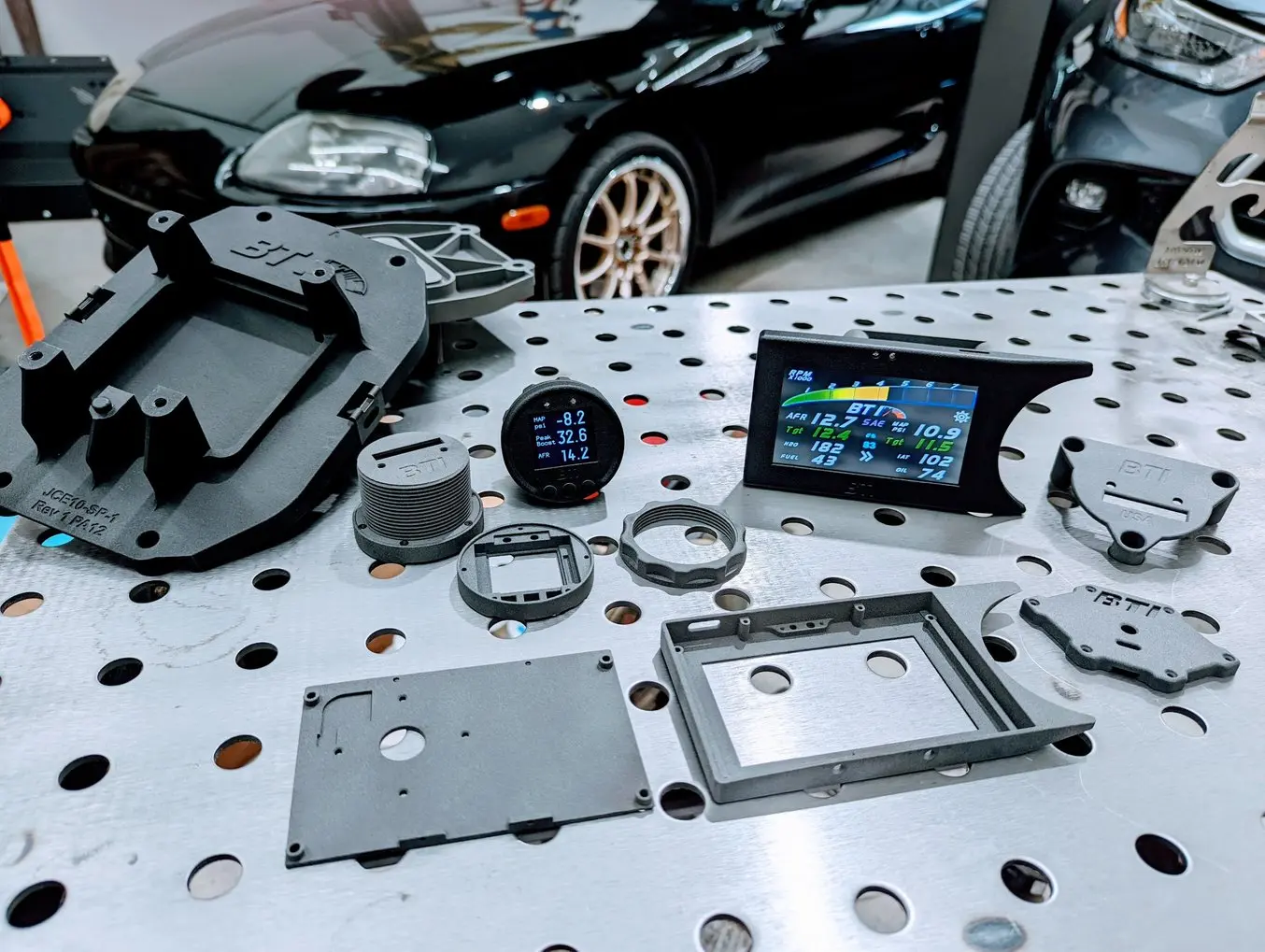
BTI Gaugesは、高性能車用の距離測定ディスプレイを設計しています。
ビジネスで成功する企業の多くがそうであるように、BTI Gaugesも市場のギャップに目をつけました。創業者でありオーナーでもあるBrandon Talkmitt氏は、高性能車用の距離測定ディスプレイをカスタマイズする方法を探していました。
Talkmitt氏は、フロントガラスに複数のスクリーンが溢れて確認が煩雑になる状態を解消できるような、複数のパフォーマンスメトリックを組み込めるメーターを探していましたが、残念ながら既製品で適したものは見つかりませんでした。そこから3Dプリンタでメーターのケーシングを試作し、高温の車内と試験用オーブンの中に試作品を放置して耐熱性試験を自身で実施しました。そこで得られた結果を元に、様々なな車種を考慮した設計調整を行いました。
メーターが完成するとすぐに、普段から付き合いのあった90年代スタイルの日本製レーシングカーや、Lamborghinis、Dodge Vipers、その他の高性能車のオーナーから関心が寄せられました。
その後Talkmitt氏は、粉末床溶融結方式3DプリンタやSLA光造形方式3Dプリンタ、手頃な価格でコンパクトサイズのSLS方式プリンタを比較・評価し始めました。しかし、中には1台50万ドルほどの高価な製品や、別の販売元から材料を購入する手順が煩雑だったりと、なかなか導入可能な製品がありませんでした。そんな時にFuse 1と出会います。「サンプルを取り寄せてみて『これはすごい、自分のメーターもこんな仕上がりにしたい』と思いましたね。取り寄せたサンプルで、どの程度の高温に耐えられるのか耐熱試験をしてみました。さらに仕上げと塗装をしてみて、これでいけると判断しました」とTalkmitt氏は語ります。
サプライチェーンの問題が発生した過去2年間、BTI Gaugesはタッチスクリーンのディスプレイやその他9製品の生産に必要な部品が不足する状態に陥りました。しかしFuse 1で3Dプリントによる生産を内製化していたことで、数千万ドルもかけて新しい加工機を購入したり古くなった製品の在庫に対処する必要なく、新設計へと迅速に舵を切ることができました。
「プラスチック製品に囲まれて身動きが取れなくなるところでしたが、Fuse 1を導入していたおかげですぐに設計を変更できました。かかった時間は、ファイル差し替えの30分だけだったと思います。Fuse 1がなければ、今頃は間違いなく生産に行き詰まっていたと思います」とTalkmitt氏は話しています。
実製品用のアフターマーケット部品の製造については、BTI Gaugesの特集記事をご覧ください。
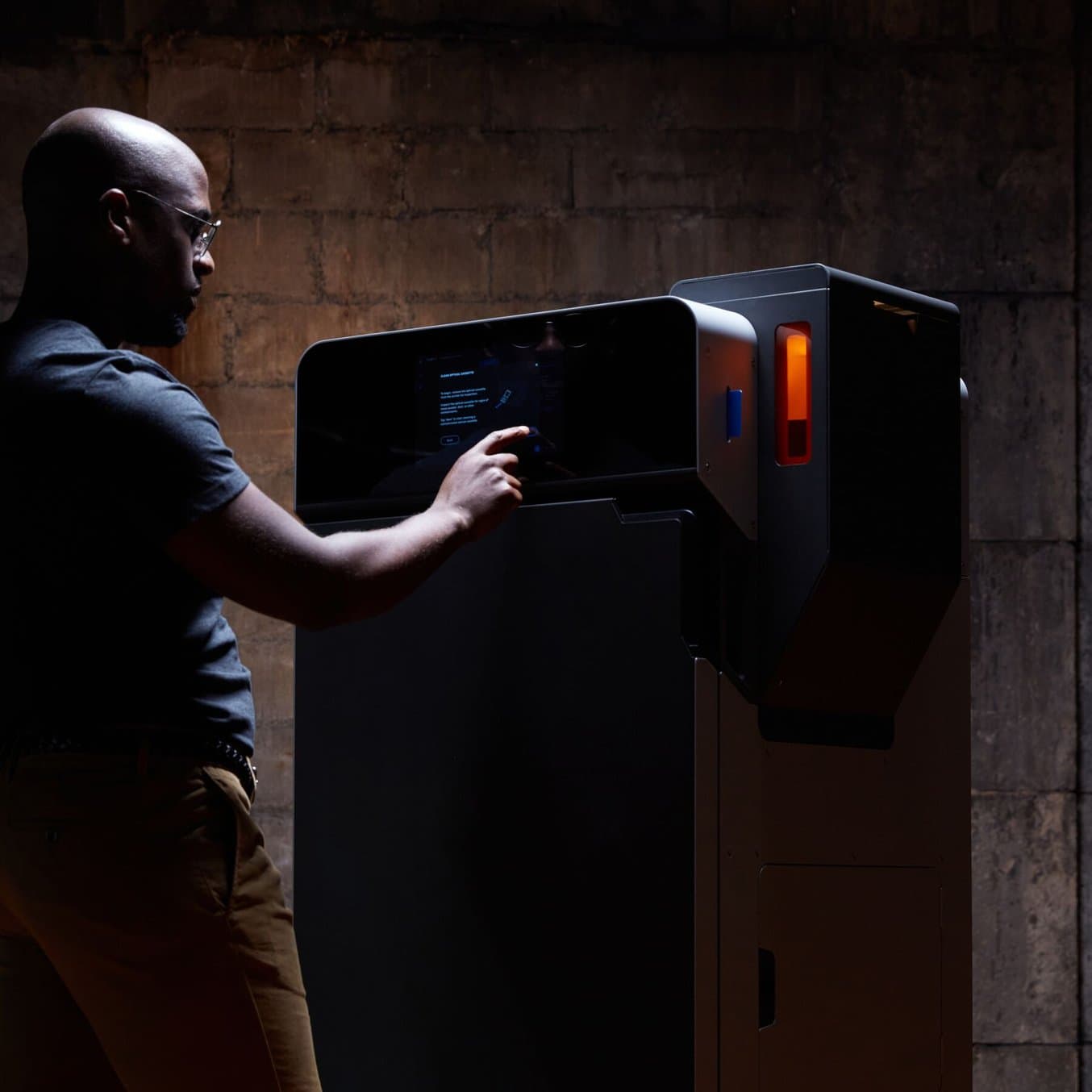
外注か内製か:SLS方式3Dプリントが適するケースとは?
本技術資料では、SLS方式3Dプリンタでの内製と、SLSプリント品を外注で製作した場合を比較し、SLS 3Dプリンタの導入の費用対効果の評価を行います。
レーシングカーとモーターサイクルに3Dプリントを活用
3Dプリントはモータースポーツに最適な金型レスの製造方法で、少ロット量産やカスタム生産を迅速かつコスト効率よく実現する強力なツールです。金型製作の時間とコストが削減されることで、製品設計を迅速に修正でき市場投入までの時間を短縮できます。設計の自由度も高まり、カスタマイズ製品や格子構造などの複雑な形状も追加コストをかけずに製作できます。
3Dプリントを使った内製により、モータースポーツチームは製品の開発スピードを上げ、知的財産を守り、より多くのアイデアを検証し、最終的に競争に打ち勝つことができます。
7. 3Dプリントを活用した反復検証でエンジン性能を向上
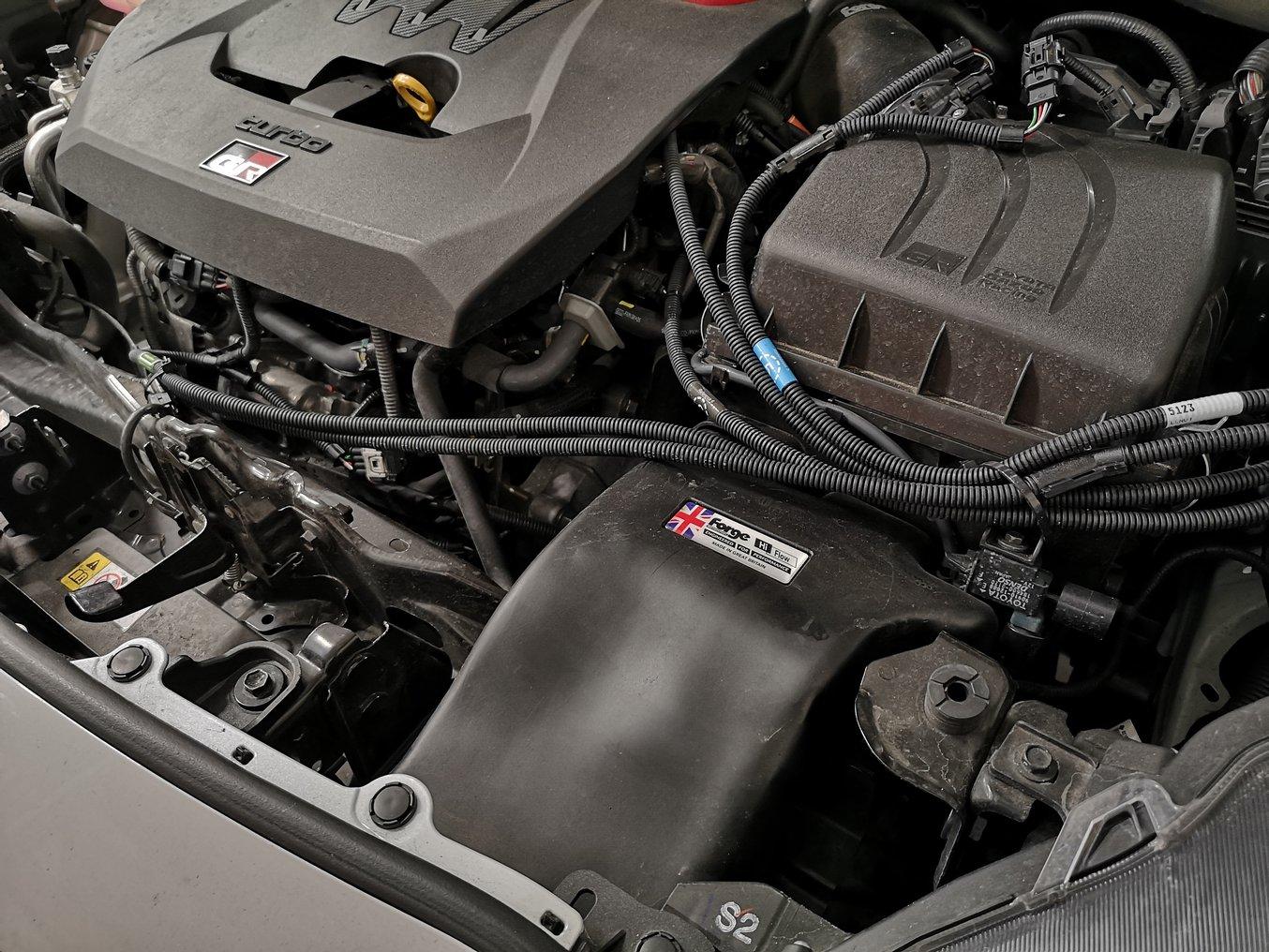
Forge Motorsportはダクトを再設計し、吸気温度を6°C下げることに成功。
高性能車のアフターマーケット部品を製造するForge Motorsportは、試作品製作に3Dプリントを使用しています。Toyota Yaris GRの発売時、Forgeのエンジニアは吸気ダクトに設計改善の余地があることに気づきました。エアボックス開口部をずらし部品全体のサイズを大きくすることで、エンジン性能の予測を難しくする吸気温度(IAT)の変動を減らし、全体の平均温度を下げることができたのです。
彼らは3DスキャンでOEM部品をリバースエンジニアリングし、SOLIDWORKSで仮想的に設計を変更し、空気流をシミュレートしました。造形可能な3Dモデルが完成したら、高速造形が可能なDraftレジンで試作品を製作し、エアボックス開口部の新しい位置が意図したとおりに機能すること、および部品全体のサイズが大きくなっても他の部品やケーブルに干渉しないことを確認しました。基本的なフィット感を確認した後、強度と耐衝撃性に優れたTough 1500レジンで部品を再度造形し、実製品に似せて黒く塗装し、顧客に渡して検証してもらいました。
顧客は3Dプリント製の部品をYaris GRに5カ月間装着し、その間、サーキットや上り坂など様々な条件下で性能データを収集しました。純正IATの温度の変動域は42~45°Cで、レース中にもかなりの変動が観察されました。一方で、Tough 1500レジンでプリントした改善後の部品を使ったIATは、顧客の検証の結果、変動域が35~36°Cでした。予想通り、改善後の部品は全体的なIATや変動率が減少しました。Forgeはこのデータを元に設計変更後の部品がOEMの設計よりも改善されていることを確信し、炭素繊維材料を使った実製品用部品の製造に踏み切りました。
3Dスキャンを使ったリバースエンジニアリングの詳細については、Forge MotorsportとPeel3Dによるウェビナーをご覧ください。

自動車業界における3Dスキャンと3Dプリントの活用法をForge Motorsportが紹介
Formlabs、Solid Print3D、Peel 3Dがお届けするこのウェビナーでは、バルブ、インタークーラー、アクチュエーターなどのアフターマーケット自動車業界向けに性能アップグレード部品を製造するForge Motorsportにお話を伺います。
8. フォーミュラカーの実製品用部品を炭素繊維材料の成形と3Dプリントで製作
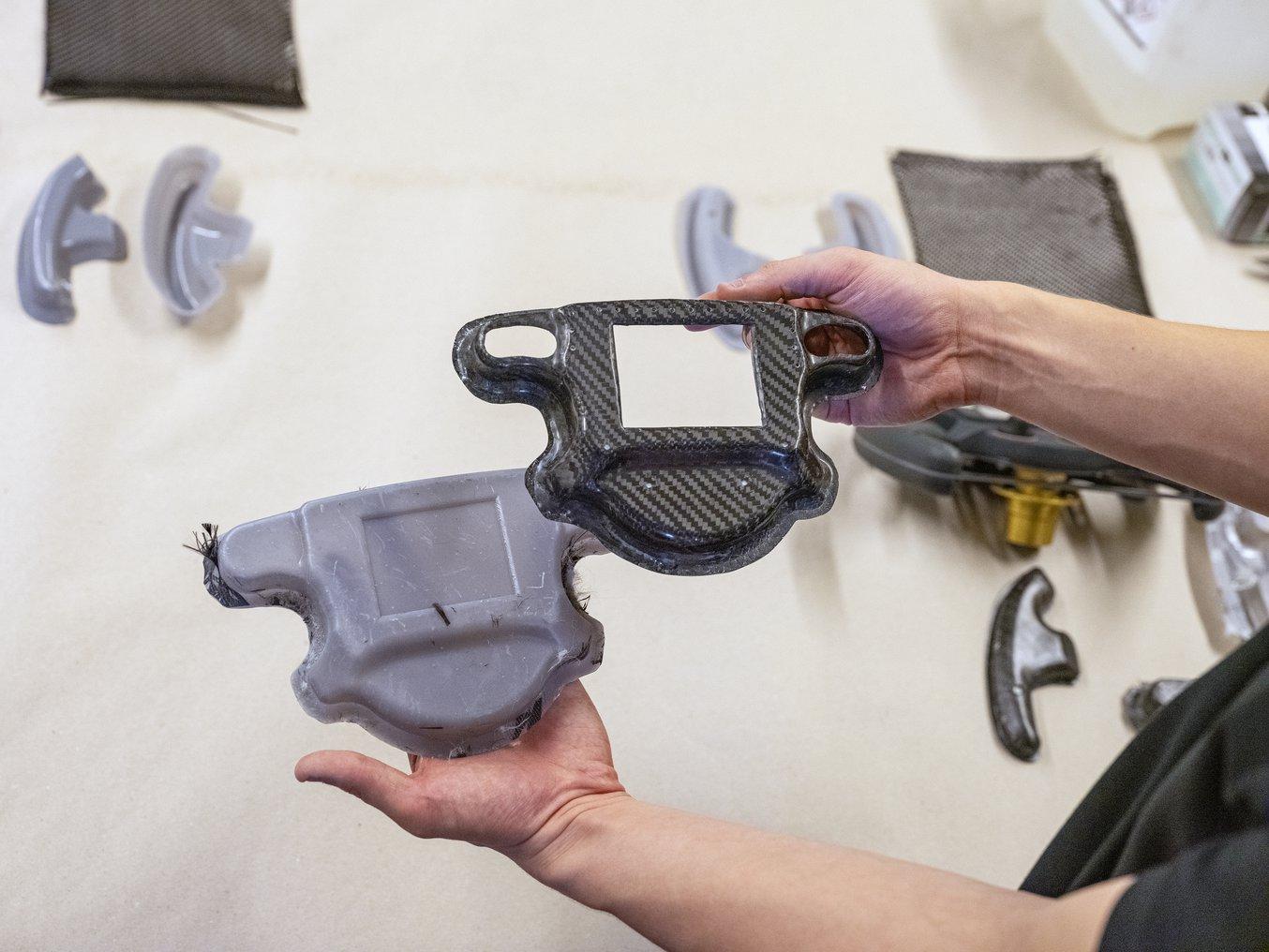
ベルリン工科大学の競技チームは、社内で金型を3Dプリントすることで写真の炭素繊維部品の製作コストと製作期間を大幅に削減。
学生フォーミュラは、年に一度開催されるエンジニアリングデザインのコンテストで、世界中の学生チームがフォーミュラスタイルの車両を自ら設計・製造し、競い合う大会です。学生フォーミュラTeam TU Berlin(FaSTTUBe)は最大規模グループの1つで、2005年以来、80~90名の学生が新たなレーシングカーの開発を行っています。ベルリン工科大学の学生フォーミュラチームは、FormlabsのSLA光造形3DプリンタForm 3を導入し、製作にかかる時間とコストを削減しただけでなく、他の製造法では高額な出費が必要な炭素繊維部品の製造を実現しました。
複合材料の成形で使用する金型を3Dプリントすることで、柔軟性を大幅に高め、製造時間を短縮し、ステアリングホイールのシャーシなどの主要部品を設計する際のコストを削減することができました。この部品の金型を従来の方法で加工するには高額な特殊装置が必要で、成形品を外注した場合には製作に数週間、そして€1000近くのコストがかかっていたでしょう。一方で、金型を3Dプリントで内製し、手作業でラミネート加工した場合、材料費はわずか€10、製作時間は1.5時間程度で済みます。
同大学のチームは、3Dプリントで試作品や軽量部品の他、実製品用部品まで製作しました。この用途の詳細については、特集記事をご覧ください。
3Dプリントの導入により、ベルリン工科大学のチームはコスト削減だけでなく、設計の自由さと調整・変更が可能な柔軟性を手に入れることができました。さらに、学生たちは当プロジェクトを通して試作品や金型、実製品用部品の製造経験を積むことができました。ここで学んだスキルと貴重な体験は、学生が将来、エンジニアリングのどの分野で就職しても大いに役立つでしょう。
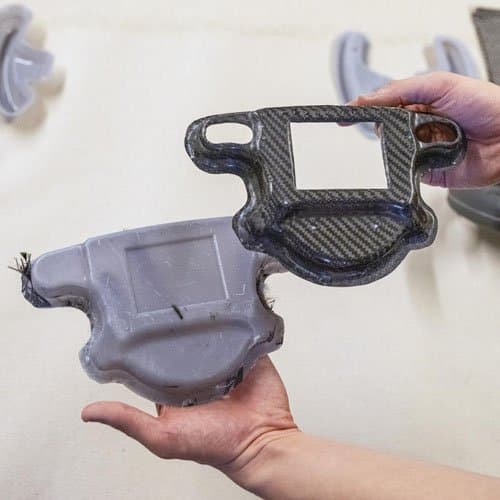
3Dプリント製の型で炭素繊維製パーツを製作
本技術資料では、複合材料を使用した成形型の設計ガイドラインや、炭素繊維部品の製造に必要なプリプレグや手作業によるラミネート成形について、手順ごとに詳しく解説しています。
9. 予備のエンジン部品を3Dプリント
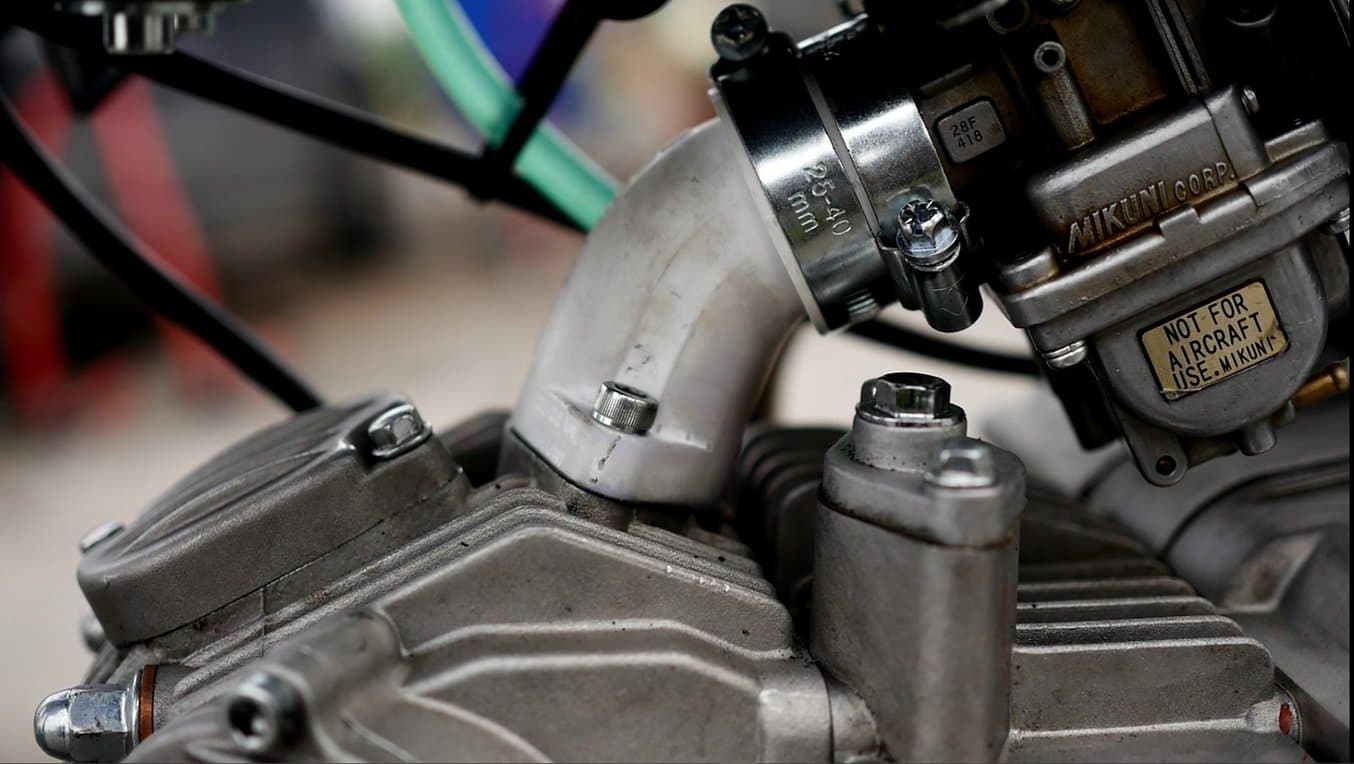
Rigid 10Kレジンで3Dプリントしたインテークマニホールドは、元のアルミ部品よりもレース後の温度が低いこと確認。
2012年からモーターサイクルに乗っているAndrea Pirazzini氏は、自分のバイク用に機能的で安全な3Dプリント製のインテークマニホールドを設計・製作したいと考えていました。彼は過去にFDMプリントを使用したことがありますが、部品の気密性が低くエンジンの機能を損なうなど、期待した結果を得られませんでした。
プロジェクトの開始にあたり、Pirazzini氏はまず3DスキャンとAutodeskのFusion 360を使ってマニホールドのリバースエンジニアリングから始めました。2ストロークエンジンのフレームとキャブレターを3Dスキャンすることでマニホールドのサイズを正確に測定でき、最適な場所に設置することができました。CADソフトウェアを使用したことでシリンダーヘッドの吸気口の直径をキャブレターと合わせることができ、段差や圧力低下、乱流の発生を避けることができました。
Pirazzini氏が新しく設計したマニホールドは、Rigid 10Kレジンを使ってForm 3で積層ピッチ100ミクロンでプリント。積層痕がほとんど目立たない滑らかな表面に仕上がりました。表面処理には従来通り耐水性のサンドペーパーを使いました。FDM方式で製作したマニホールドの場合は外部や内部に防水処理を施す必要がありますが、SLA光造形方式なら最初から剛性と防水性の高い部品を製作できます。
Pirazzini氏がForm 3で3Dプリントしたマニホールドは、高温と低温のどちらにも完璧に耐え、今でも彼のピットバイクに搭載されています。サーモグラフィを使った検証では、Rigid 10Kレジンの熱的特性が格段に優れていることもわかりました。3Dプリント製のマニホールドに冷却フィンを搭載した場合、従来のアルミ製のマニホールドと比べて40~50度も低い温度を保っていることがわかったのです。さらに、外気温度が約33度にものぼる屋外で20~25分間のレースを行った後でさえ、火傷することなくマニホールドに触れることができました。
このプロジェクトは単なる成功を超え、エンジンの性能を向上するまでに至りました。Pirazzini氏が元の設計に加えた改善により、3Dプリント製のマニホールドではチャンピオンシップの規則制限を守りながら、標準的な切削加工のマニホールドと比較してエンジンの馬力を約1馬力、ほぼ10%向上させることができたのです。
Pirazzini氏のプロジェクトの詳細については、詳細なケーススタディをご覧ください。
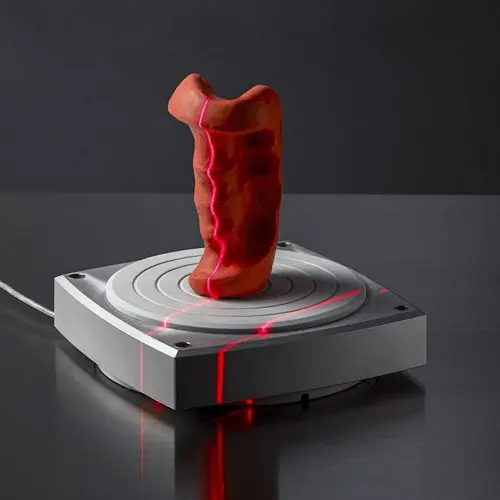
リバースエンジニアリングやその他用途向けの3Dスキャンと3Dプリント
3Dスキャンと3Dプリントを活用した工程は、複製や修復、リバースエンジニアリング、計測などにも応用できます。こちらの技術資料では、これら活用法の詳細や導入にあたって準備すべきことをご確認いただけます。
ボーナス:3Dプリントカー
2010年代初頭に流行した3Dプリントの熱狂の中で、3Dプリントカーなど大規模で複雑なアセンブリの3Dプリントができると主要メディアで取り上げられ、さらに人気が出ました。しかし、「すべてを」3Dプリントで作った自動車の熱狂的なファンでさえ、その後は徐々にエンジンやその他の電気機械アセンブリから、シャーシやボディ、シートなどの構造部品やトリム部品のプリントに焦点を移していきました。
Local MotorsやEDAGなどの一部の企業がシャーシとボディを3Dプリントした完全なコンセプトカーを製作し、2010年代半ばのSEMAなどの見本市イベントで一般公開しましたが。いずれも連続生産には至りませんでした。
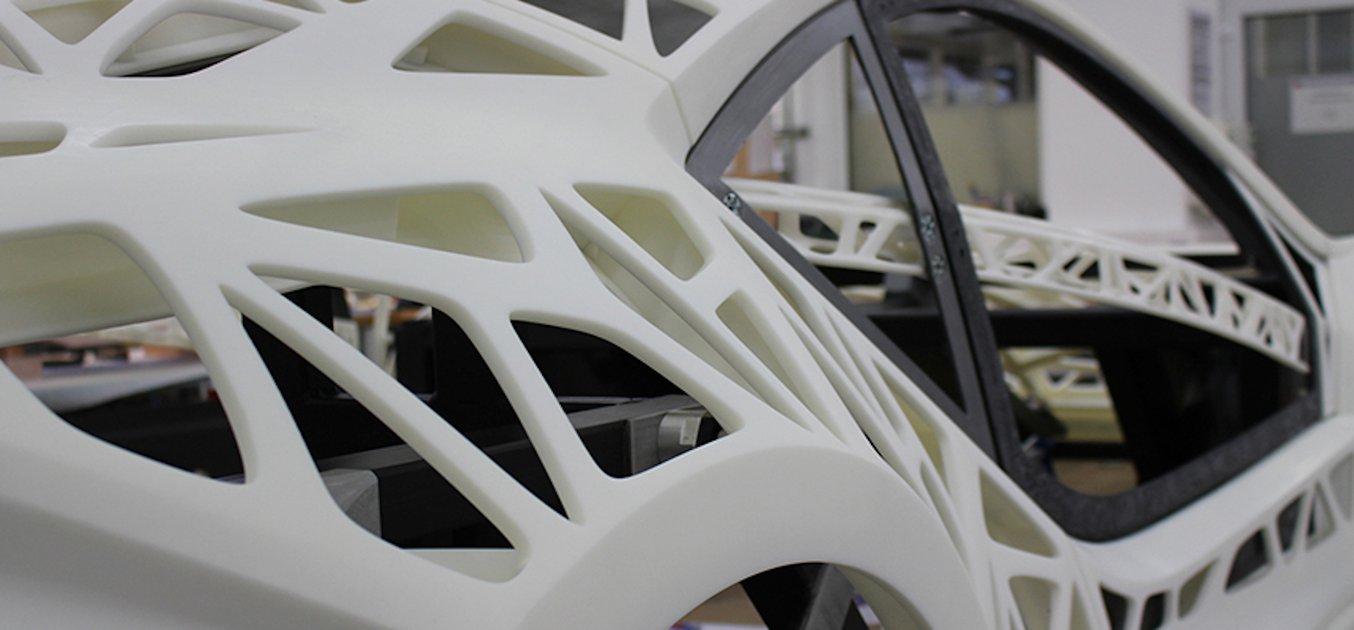
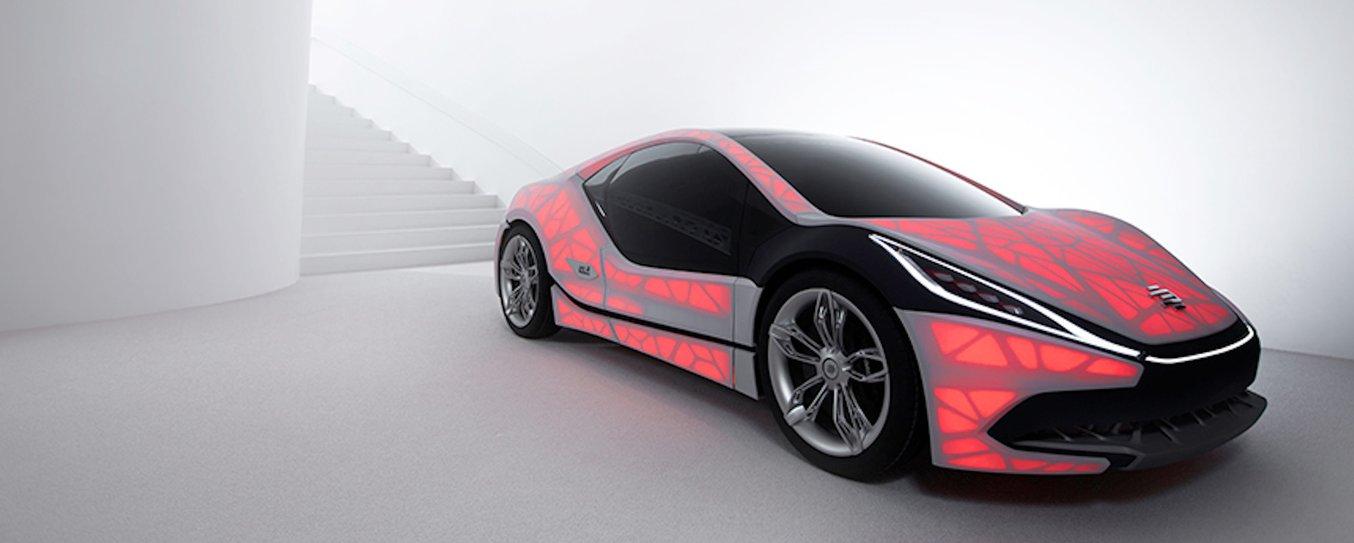
EDAGのLight Cocoonのカバーは、耐候性だけでなく設計や個別化の点で絶対的な自由度が特徴(出典:EDAG)。
現在、連続生産に最も近い状態にあるプロジェクトと企業はDivergent 3DとXEVのようです。
Divergent 3Dは、ジェネレーティブデザインと3Dプリントを組み合わせ、自動車部品メーカー向けにカスタムメイドの部品を提供しています。設計後は、同社の金属3Dプリンタで部品を製造します。同社初となる公開プロジェクトはハイパーカー「Czinger 21C」で、同時にAston Martinなど大手OEMのサプライヤーでもあります。
一方、イタリアのXEV社が開発した「YoYo」は、3Dプリンタで製作した初の「大衆向け」電気自動車で、現在顧客向けに出荷されています。YoYoの目に見える部分は、シャーシ、シート、フロントガラス以外すべて3Dプリントで製作されています。3Dプリントを多用することで、部品点数を2,000点からわずか57点に減らすことに成功し、その結果、重量はわずか450キロという軽量設計を実現しました。
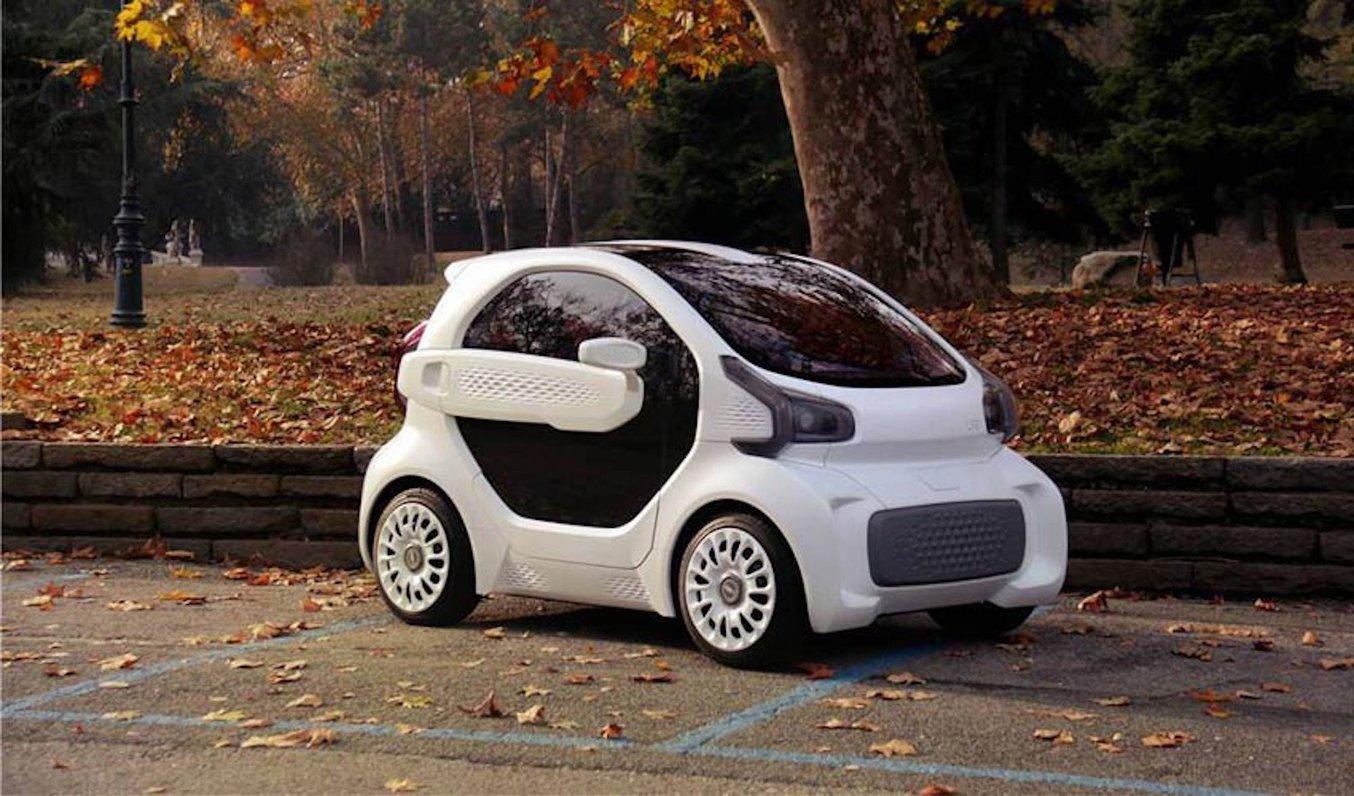
YoYoは3Dプリンタで製作された初の「大衆向け」電気自動車で、出荷が始まっている。
自動車業界での3Dプリント活用事例
本記事で紹介したすべての事例からもわかるように、3Dプリントをクリエイティブに活用することで製品の市場投入までの時間を短縮し、車両の性能が上がることから、サプライヤー、OEM、消費者に大きなメリットとなります。3Dプリントで限界を押し広げ、設計・製造工程で全く新しい可能性を実現できたケースや、製造にかかるコストと時間を削減できたケースがあります。
3Dプリントの価値と現実に対する理解が業界全体に広がり、技術と利用可能な材料がさらに多様化するにつれ、アディティブマニュファクチャリングは今後も世界中で自動車の設計や製造、メンテナンスの方法を今後も変えていくことになるでしょう。