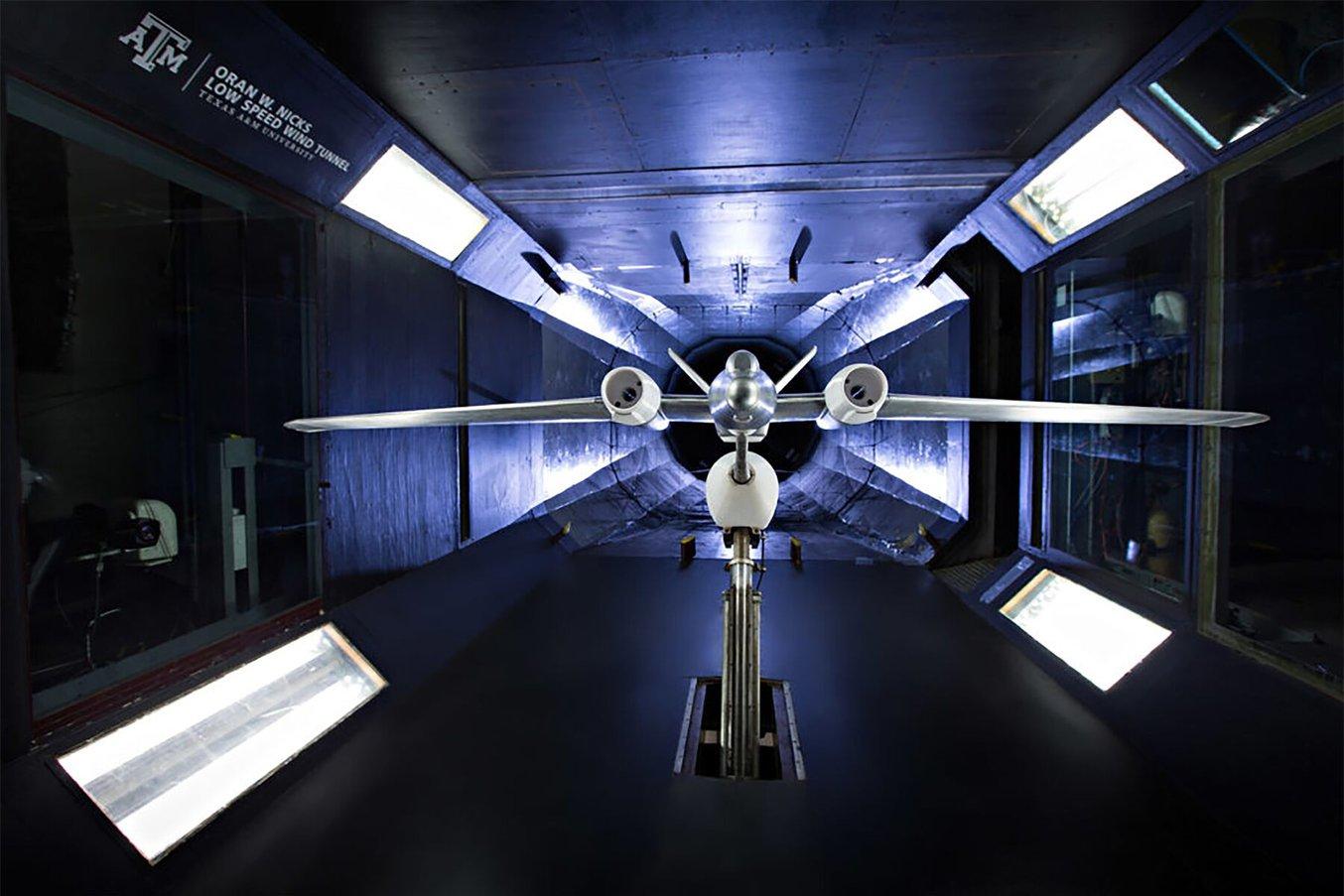
3Dプリントとしても知られるアディティブマニュファクチャリングは、航空宇宙業界で設計から製造、さらにその先の工程に至るまで幅広い分野で活用されている。
航空宇宙業界は、3Dプリント(アディティブマニュファクチャリング)が発明された時に、最も早く商業利用を開始した業界の1つです。実際、多くのOEM、サプライヤー、政府機関が、すでに数十年にも渡って3Dプリントを使用しており、最新世代の民間航空機には3Dプリント製の部品が1000個以上搭載されています。
しかし、従来の工業用3Dプリンタの価格は、資金力のある最大規模の組織以外には手の届かないものでした。それが過去10年間で、高性能プリンタも含めて3Dプリンタの価格が大幅に低下したこと、さらに材料科学が発達したことで、高機能が要求される用途での3Dプリントの活用が可能になりました。入手しやすい価格になったことで、中小企業の他、以前は中央集中型の試作品製作工場に隔離されていたような大企業の新部門でも3Dプリンタを使用できるようになりました。アディティブマニュファクチャリングの技術をより多くのエンドユーザーに提供することで、Formlabsの3Dプリンタは、さらに多くの航空宇宙エンジニアや研究者が各分野の限界を押し広げることを可能にしています。
設計から製造、さらにその先の工程まで、3Dプリントが航空宇宙業界全体のイノベーションを支えている9つの例をご紹介します。
3Dプリントで航空宇宙製品を開発
1. ロケットの機能試験用に3Dプリントでラピッドプロトタイピング
Gravity Industriesは、まるでSF映画に出てきそうなジェットスーツを開発しています。同社のジェットスーツは、ヘリコプターが届かない、または安全に着陸できない捜索救助などの場面での使用を想定しています。複数の3Dプリント方式を駆使することで、試作品製作と試験工程を高速化することに成功しました。いくつかの試験では、現在利用可能な材料のうち、熱硬化性フォトポリマー樹脂の使用が最良と判断されたものもあります。
テストパイロット兼リードデザイナーであるSam Rogers氏は、Form 3にてClearレジンで造形した部品を使って、ボルテックス冷却装置を搭載したロケットエンジンの点火装置を開発しました。透明材料は試験環境での使用に最適で、Rogers氏は試験装置内部での燃焼パターンを観察することができました。
設計試験中、Rogers氏はチャンバーをモジュール式に設計し、チャンバーとノズルの両方を異なるバージョンで組み合わせられるようにしました。「旋回する酸素の壁」で最高温度の熱がチャンバー壁に当たらないようにすることで、レジンの部品がそれぞれ数秒間、高熱でも持ちこたえられるようになりました。試験発射では点火パターンを観察することが目的のため、それだけ持ちこたえることができれば十分です。
このために何十種類ものモデルを金属で作っていたら、莫大な費用がかかっていたでしょう。その代わり、試験時間が短期間なことと部品の材料費の低さを活かし、Rogers氏は最小限の支出と製作期間で高機能設計を実現しました。
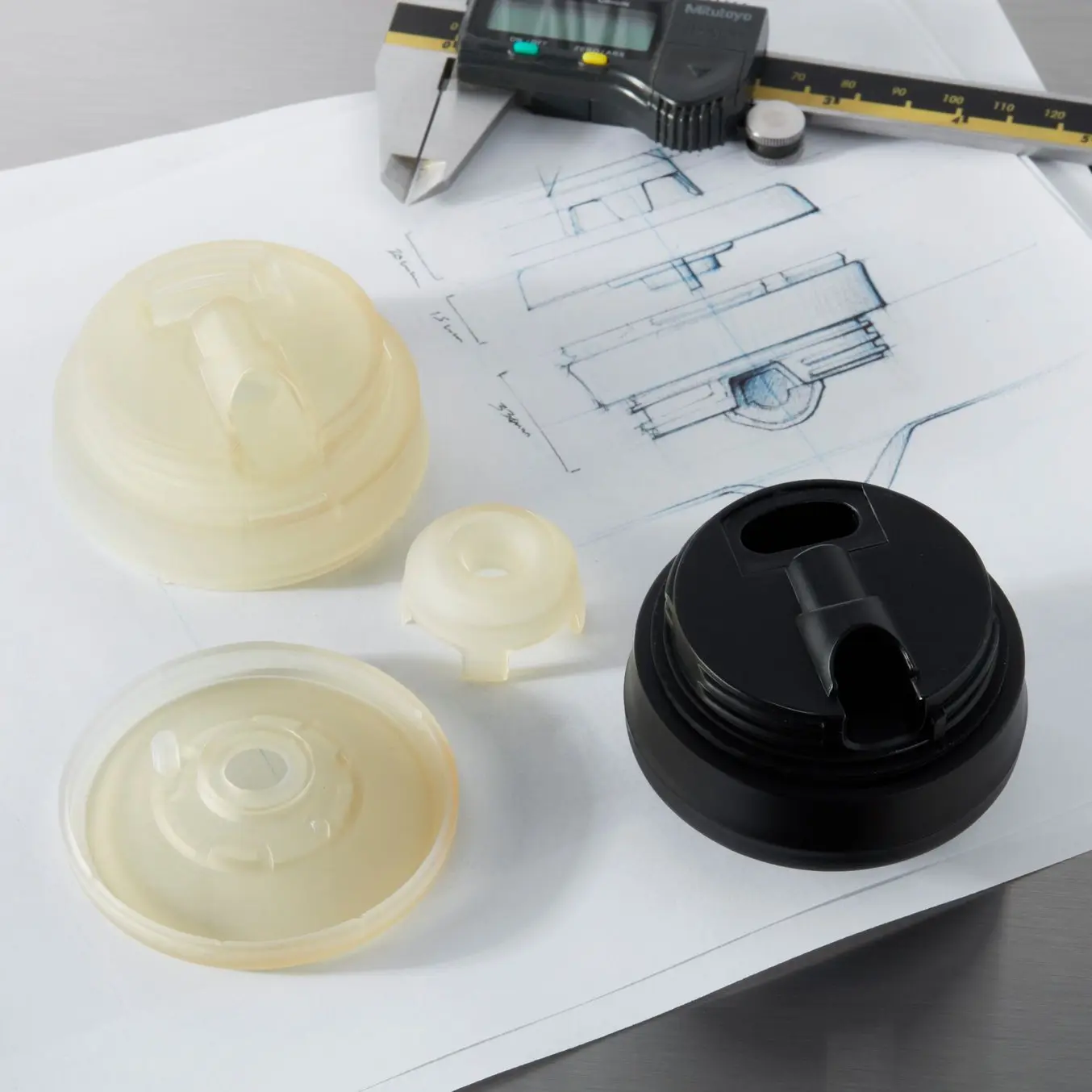
製品開発用ラピッドプロトタイピングガイド
本ガイドでは、製品開発工程にラピッドプロトタイピングを組み込む方法、活用事例、そして現代の製品開発で使用できるラピッドプロトタイピングツールをご紹介します。
2. 3Dプリントで複雑なロケット部品を製作
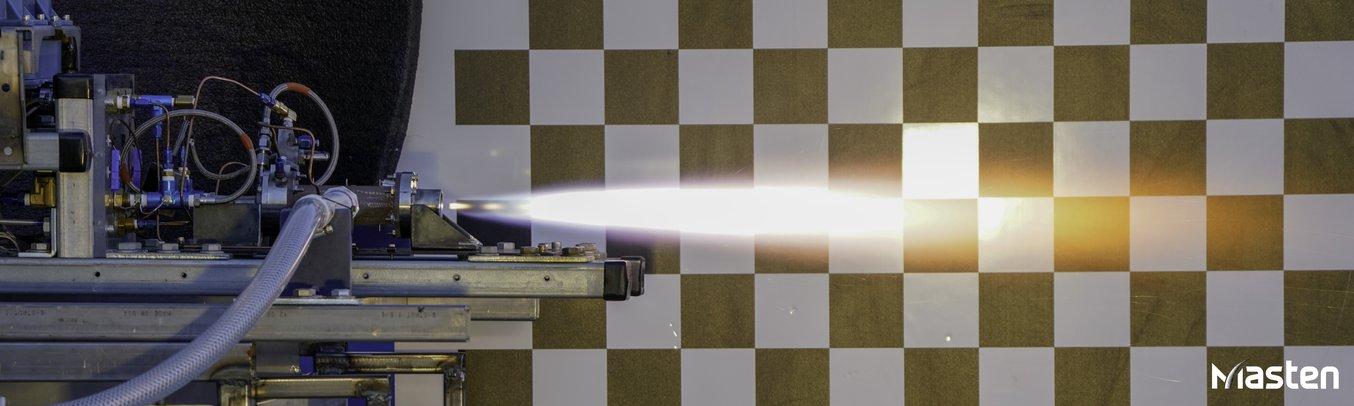
Masten Space Systemsは、3Dプリントで複雑な形状のロケット部品を製造している。
Masten Space Systemsは、垂直離着陸ロケットの製造を専門としています。Mastenは2014年にロケットエンジンの3Dプリントを開始し、小型の試験用スラスターから始まり、最終的には2016年に推力25,000ポンドのブロードソードエンジンにまで製造を拡大しました。同社は、プラスチックと金属の両方を使ったアディティブマニュファクチャリングの経験があります。Mastenの研究・試験エンジニアであるKimberly Devore氏によると、同社は従来の機械加工と3Dプリントの両方を活用してロケットエンジンを製造してきたと言います。古いエンジンはまだ従来の製造法で製造していますが、設計の自由度と製造スピードに優れていることから、3Dプリントも活用しています。
「[3Dプリントの]良いところは、思い通りにモデリングできることです。従来の機械加工のように試作・検証を繰り返す必要がありません。最初からニーズに応じた設計をすればいいのです」とDevore氏は言います。「一般的に、従来の機械加工ではかなりベーシックな設計にする必要があります。何かしらの形状を加えるたびに追加費用が発生し、それを回収しなければいけませんから」
一方の3Dプリントなら、性能向上のために形状を複雑にしても、追加費用がかかることも、余分なリスクを背負う必要もありません。比較的短時間で安価に複数の部品を作ることができるため、新しい設計も試すことができます。「こういうことを迅速かつ何度も行えるというのは、大きなメリットです」
3. 3Dプリントで航空宇宙用部品を試作
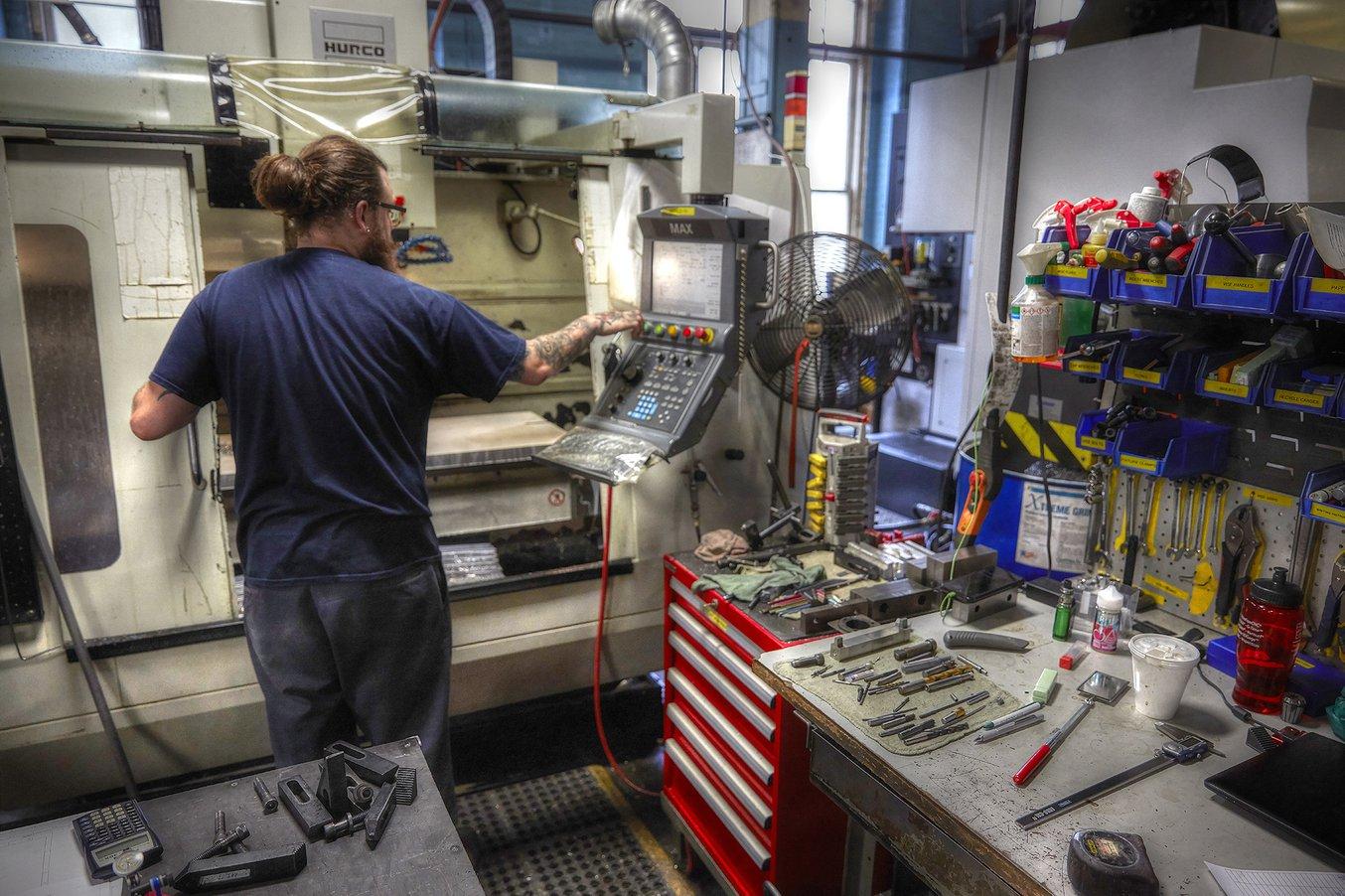
CNCのプログラムには技術と時間が必要。必要な部品が必ずしも金属でなくてよい場合は、3Dプリントなら試作品製作や生産用の金型を高速かつ低コストで製作できる。
A&M Tool and Designは、航空宇宙、光学、ロボティクス用の部品やカスタムマシンを製造しています。この工場では、長年に渡って近代化を行い、信頼性の高い従来の技術や改良を加えた装置に加え、3Dプリントを含む様々な新機器を導入してきました。A&M Toolの機械エンジニアであるRyan Little氏は、同社のニーズに最も適した3Dプリンタを調査し、Formlabsの3Dプリンタを選択しました。
この工場では3Dプリントで試作品を製作し、フィット感と機能性の検証を行いました。3Dプリントにより、Little氏率いるチームはこれまでよりも高速に部品を製作し、一日中活用できています。夜のうちに部品をプリントしておき、翌日には使用できる状態にしておくのです。3Dプリントは、CNC加工ではコストも時間もかかっていたであろう部品の製作に特に役立っています。
Little氏はこう言います。「3DプリンタはCADの補助ツールのような感覚で、多種多様な部品の試作品製作を大量に行っています。もしForm 2がなかったら、試作品の多くは加工の準備が整うまでCADデータのまま放置されていたでしょう。また、従来の方法では実用性がなく、そもそも設計や製作ができなかった部品もあるでしょうね」
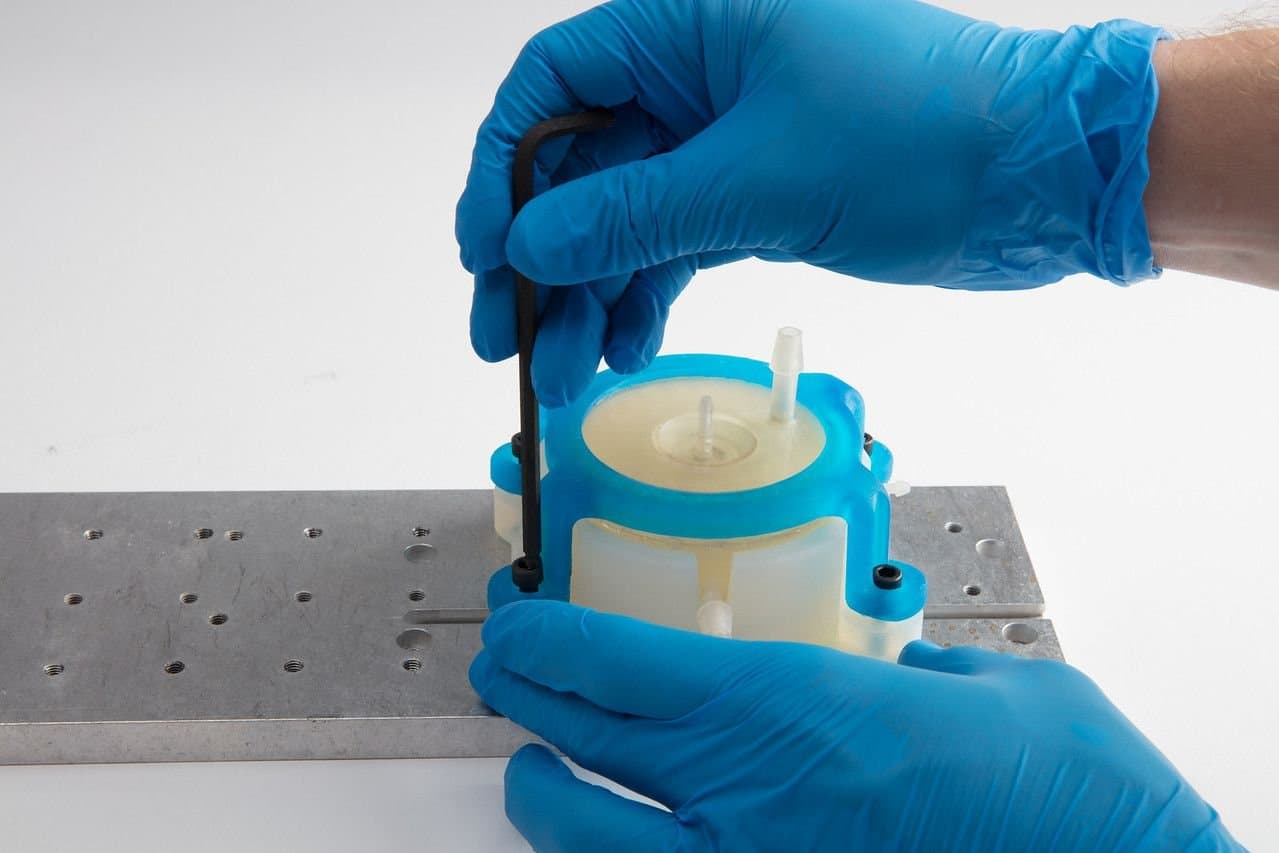
3Dプリント製治工具の設計
メーカーにとって、生産スピードの最大化と高品質の維持を両立させることは何よりも重要です。治工具は、製造工程や組立工程の効率化や安定化、サイクル時間の短縮、作業者の安全性向上などの目的で使用されます。
航空宇宙業界の製造に3Dプリントを活用
4. 航空機用にカスタム治具を3Dプリントしコストを削減
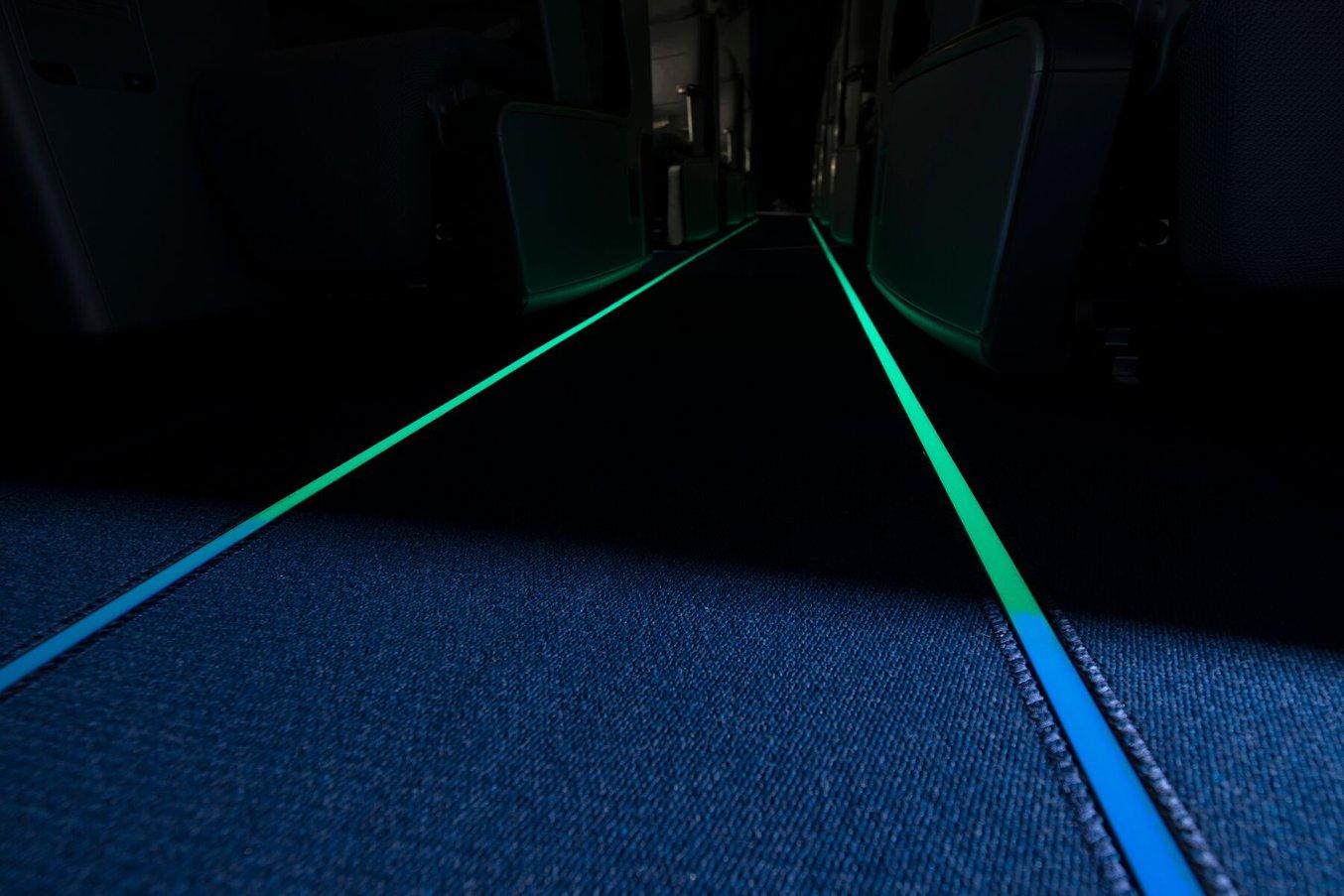
Lufthansa Technikは、押出ノズルを3Dプリントし、写真の自己発光型脱出経路マーキングを製作。
Lufthansa Technikは、世界最大の航空業界向けサプライヤーの1つとして、メンテナンス、修理、オーバーホール(MRO)を行っています。同社独自の避難経路表示、Guide Uは、航空機の客室に搭載するアフターマーケット品として設計されています。この革新的なフロアマーキングには、蓄光塗料、つまり平時に客室内の照明で蓄光し、電源が停止した非常時には暗闇の中で発光し続ける性質を備えた塗料が使用されています。
生産に先立って行われた、治具に使用する材料と製造工程の検証の結果、カスタム押出ノズルの3Dプリントが最も費用対効果が高く、柔軟な製造方法であることがわかりました。「理論的には、射出成形でノズルを作ることも可能でした。しかしノズルの形状をこれほど柔軟かつ迅速に調整することは不可能だったでしょう。3Dプリントの大きな利点は、こういうところにあるのだと思います」と、Guide UプロジェクトのエンジニアであるUlrich Zarth氏は説明しています。
この治具は、Formlabsの正規代理店であるmyprintooとの協力で、Form 3Lを使用してプリントされました。大容量のビルドプラットフォームを備えたForm 3Lは、一度のプリントでノズルを72個生産することが可能です。Formlabsの複数の材料で試験を実施し、十分な安定性と表面品質を備え、Lufthansa Technikの生産工程の最適化にも役立つClearレジンが選定されました。
「特にプラスチックの分野で精密さとスピードを求めるのであれば、迷わず3Dプリントを選びます」
Lufthansa Technik AG社 プロジェクトエンジニア、Ulrich Zarth氏
Zarth氏率いるチームは、この小型ノズルが内製で3Dプリンタ可能となったことで、生産工程における膨大な時間とコストの削減を実現しました。このような生産用治具を製作する従来の方法と比較すると、必要数を上回る外注時の最小注文数を気にすることなく必要な分のみ内製することもでき、以前よりもはるかに柔軟に工程が効率化されました。
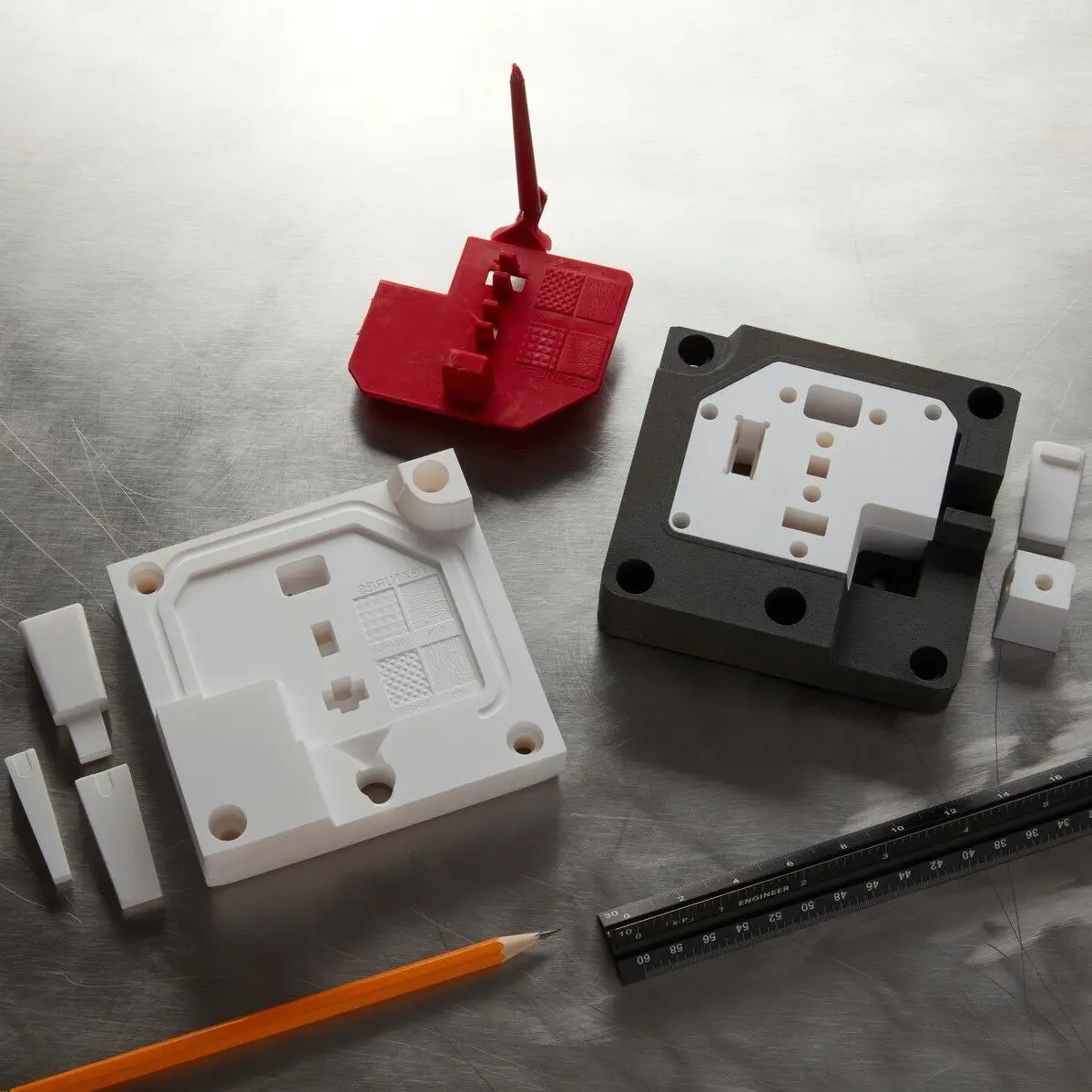
5. 3Dプリント製のマスキング治具で航空宇宙業界の作業時間を短縮
AMRCの統合製造グループは、業界のパートナーと協力して高度な技術を結集し、統合システムを開発しています。研究グループは、ヨーロッパ最大の航空宇宙メーカーであるAirbusのプロジェクトに関わってきました。このプロジェクトには、炭素繊維、アルミニウム、またチタン部品の高温掘削と機械加工が含まれていました。AMRCのプロジェクトエンジニアであるGeorge Sleath氏は、次のように述べています。「1つ穴を開け終わり、次の穴を開ける時に、スクラップが2番目の穴を汚してしまわないよう、最初の穴を覆っておく必要がありました」
チームは当初、小さなゴム製Oリングのついたアルミニウム片の使用を試みましたが、問題解決には至りませんでした。これ以外にもさらに2つの問題がありました。様々なサイズのキャップが必要で、期日に間に合わせるためには合計500個のキャップを10日以内に調達する必要性に迫られていたのです。
このようにカスタム製品の製造期間が短い場合、3Dプリント以外の製造方法は現実的ではありません。当時は、AMRCの内製能力に確信が持てなかったため、Sleath氏は外部の3Dプリントメーカー3社に見積もりを依頼したものの、その金額は高額でした。
「その後、設計・プロトタイピンググループのMark Cocking氏と話をして、内製できるものは何かないかと尋ねました。24時間待っても返信がなかったのですが、その後連絡があった時にはなんと「もう半分はプリントが終わったよ」と言われました。24時間で250個のドリルキャップが製造されていたんです。驚くべき速さですよ」とSleath氏は続けます。
最終的に、2日以内にすべての部品を製造することに成功し、キャップは現場で意図したとおりの性能を発揮しました。「取付を担当したオペレーターからのフィードバックは素晴らしいものでした。部品の大部分は意図したとおりに正確に機能し、操作中の破損もありませんでした」とSleath氏は述べています。
6. 宇宙航空向け部品を3Dプリント+電解めっき処理
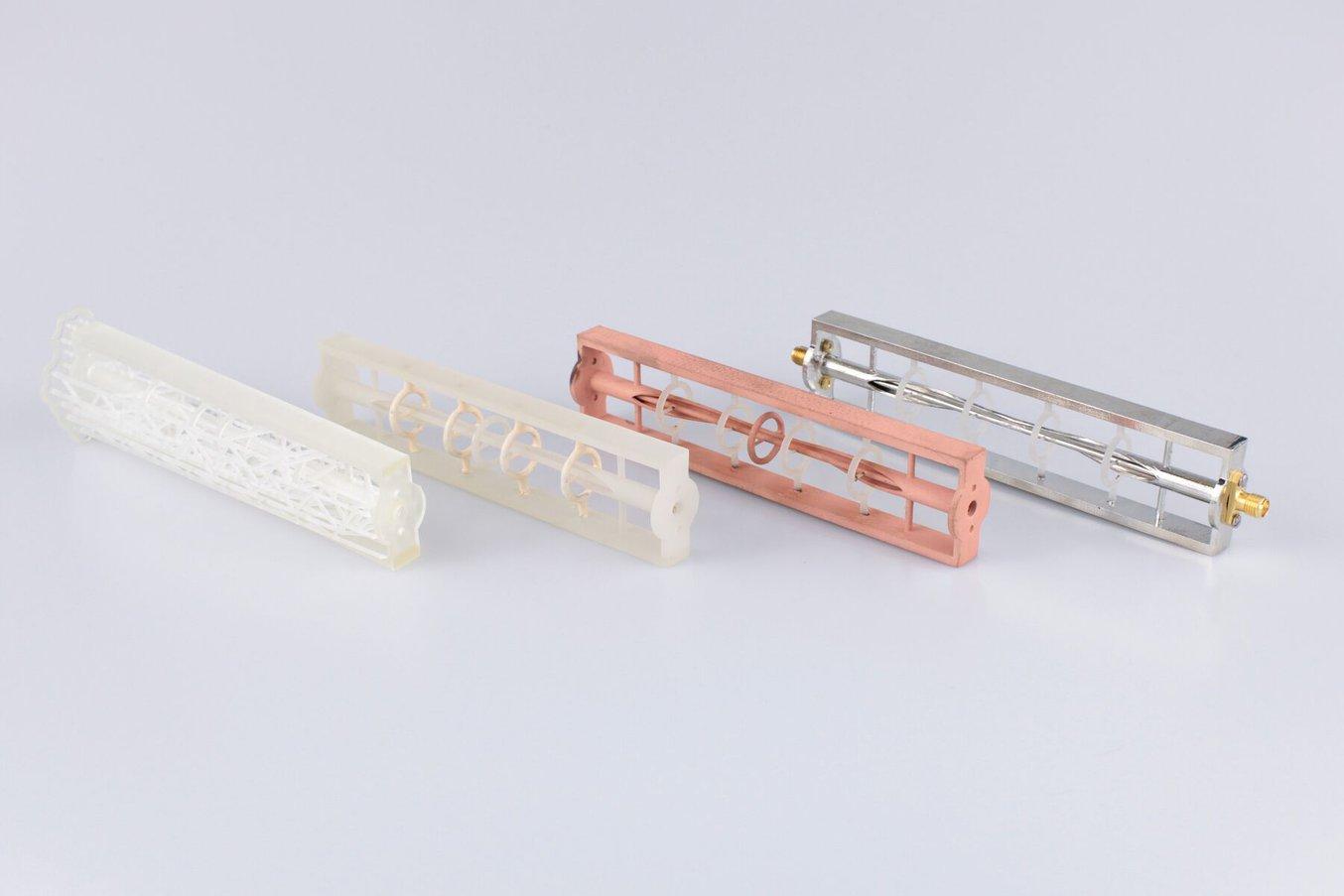
実製品用部品を3Dプリントすることで、Elliptikaは全く新しいデザインのアンテナを高速製作し、その過程でコスト削減にも成功。
Elliptikaは、高周波やマイクロ波の製品およびソリューションの設計・開発を専門とする企業です。同社はカスタムフィルターやアンテナを設計しており、これらの製品は自動車、防衛、医薬品、教育業界の様々な企業で研究開発に利用されています。無線周波数の設計者であるGwendal Cochet氏とAlexandre Manchec氏は、複雑な形状を実現し、コストを抑えながら、高速に製造する方法が必要でした。これらの厳しい要件を満たすために、彼らは従来の製造技術に捉われない方法を学びました。
Elliptikaのチームは、様々なアディティブマニュファクチャリング方式を検討した結果、 SLA光造形方式による3Dプリントなら造形品の表面が滑らかで、電解めっき処理に最適であることがわかりました。「3Dプリントが完了したら、造形品からサポート材を取り除き、表面を整えて二次硬化を行う必要があります。次に、造形品に化学処理を施して約3µmほどの薄い銅の層を表面に付着させ、最後に厚めのスズの層を重ねるなどして仕上げを行います」
Elliptikaは、Formlabsの3Dプリンタに投資した金額をわずか2回の作業で回収しました。外部のサプライヤーに部品を外注した場合の費用は約3000ユーロですが、社内でアンテナを3Dプリントして電解めっき処理した場合の材料費と人件費はわずか20ユーロで済みました。
業務のスピードもアップしました。従来の製造方法では、アンテナ1本の製造に3カ月程度はかかっていたでしょう。「3Dプリントによる内製では、2日で部品が完成します。プリントに1日、めっき処理に1日で機能する部品ができあがるので、製造期間は大幅に短くなりました」とCochet氏は言います。
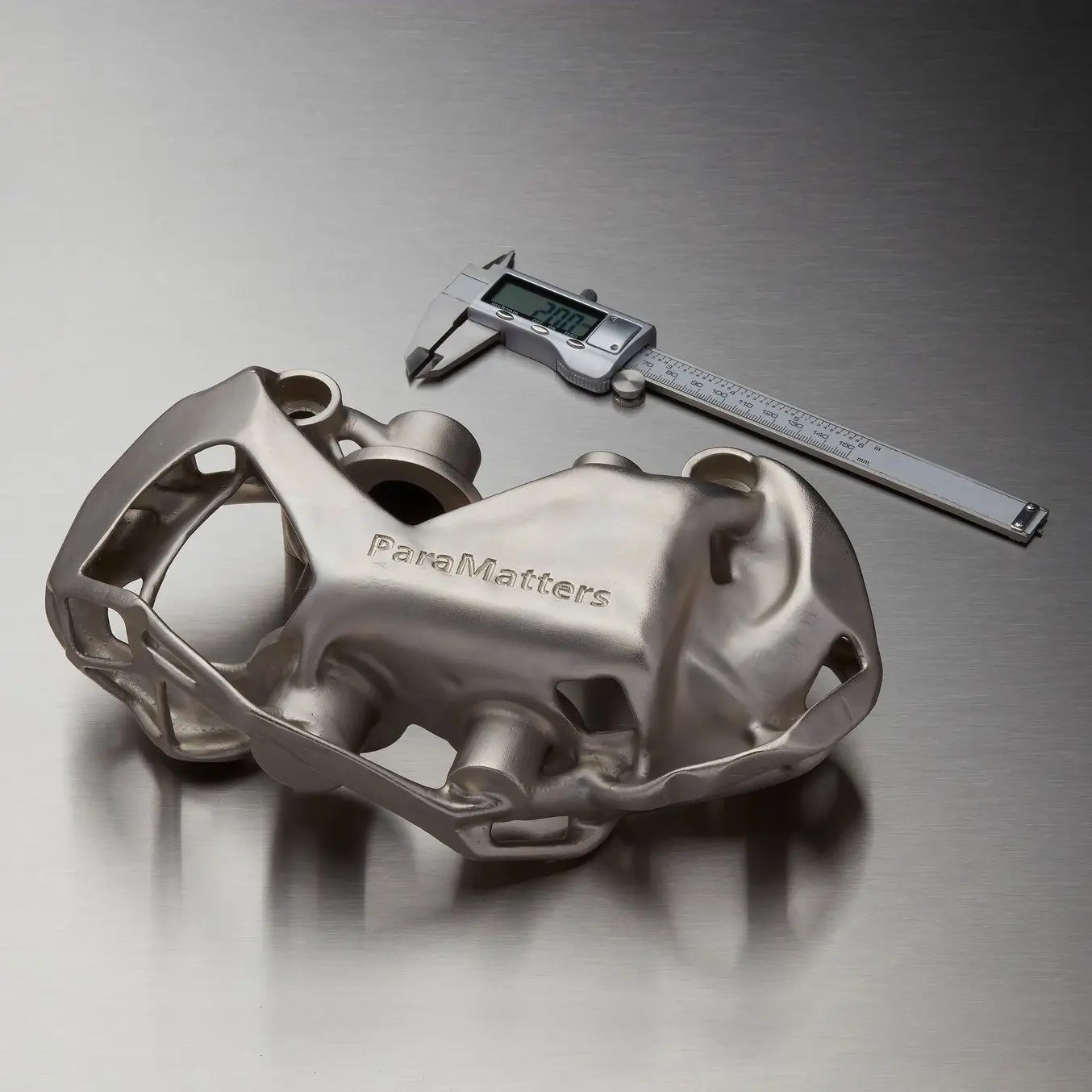
金属の強度を手に入れる:SLA光造形品の電解めっき方法と活用事例
本技術資料では、レジンで3Dプリントした部品のメタルコーティングに取り組むエンジニアの事例、そしてハイブリッド金属による実製品用部品の強度・耐久性の向上や用途の拡大といった新たな可能性について詳しく解説しています。
航空宇宙の研究・教育で3Dプリントを活用
7. 宇宙空間で3Dプリント製部品をテスト
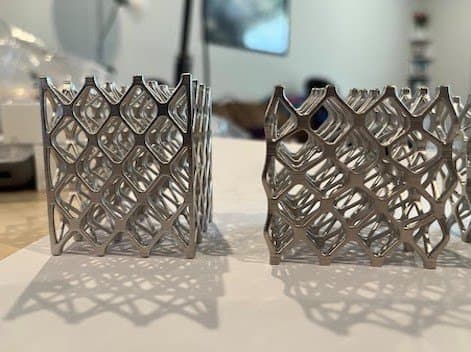
Rigid 10Kレジンで造形し電解めっき処理を施したラティス構造の圧縮試験用サンプル(左)と、上部から圧力をかけた試験後のサンプル(右)。
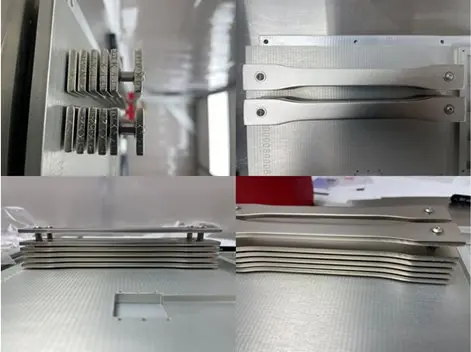
Rigid 10Kレジンで3Dプリントし電解めっきを施した部品がISSに送られる。
NASAの研究者たちは、SLA光造形方式で3Dプリントし電解めっき処理を施した部品が宇宙空間でどのように機能するかを調べています。NASAのゴダード宇宙飛行センターのエンジニアは、ブラケットを設計してFormlabsのプリンタで3Dプリントし、電解めっき処理を施した後、2022年夏に行われたSpaceXの国際宇宙ステーション(ISS)への商業補給サービス(CRS-25)ミッションで宇宙へ送りました。
Alpha Spaceの国際宇宙ステーション試験プラットフォーム「国際宇宙ステーション材料曝露実験装置(MISSE-16)」を使用し、サンプルを宇宙ステーションの外部環境に晒した後、さらなる試験のために地球に戻します。この試験結果は、NASAや他の航空宇宙メーカーが電解めっき処理とアディティブマニュファクチャリングを将来の製品計画にどう組み込んでいくかについて、洞察を提供できる可能性があります。
8. 3Dプリント製の風洞試験用部品
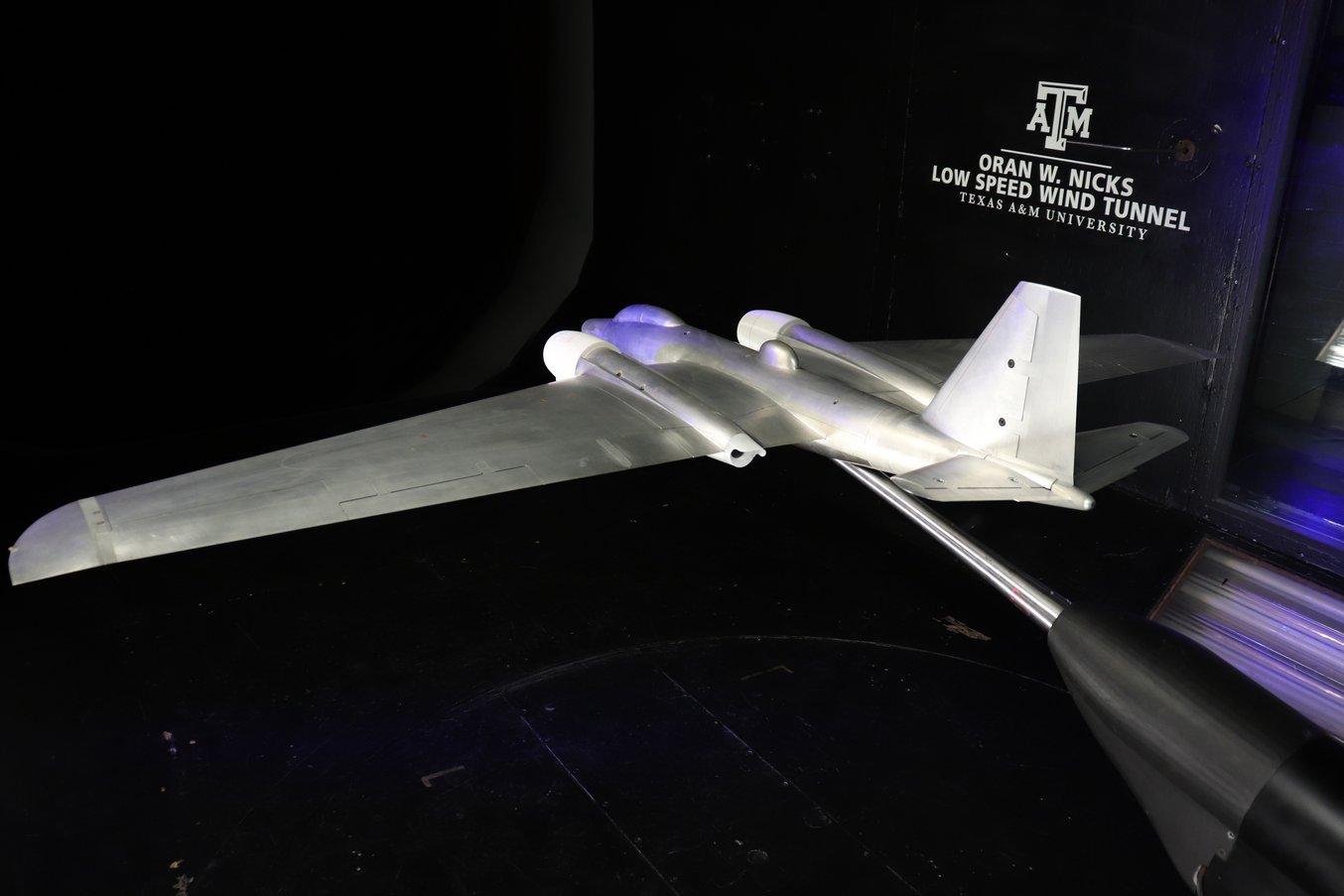
高性能の3Dプリント部品は、風洞で飛行機のスケールモデルに取り付けられる。
世界中の教員や学生が風洞試験でFormlabsの3Dプリンタを使用し、研究に役立てています。
Texas A&M Oran W. Nicks Low Speed Wind Tunnelは、幅広いプロジェクト向けに風洞試験を行っています。Texas A&M Wind Tunnelのマネージャー兼エンジニアであるLisa Brown氏は、研究者の試験計画策定、モデル設計、関連データを収集するためのコード作成を支援しています。彼女のチームは3Dプリントを使用してスケールモデルを作成し、様々なオブジェクトで試験を行っています。
Brown氏は、ヘリコプターのブレードのフラップを研究するプロジェクトで、試験に3Dプリントを活用した時のことを教えてくれました。「機体が十分な速度で飛行し、ブレードも十分な速度でフラップすると、ブレードの前縁から衝撃波が発生するんです。ヘリコプターにとっては、望ましいことではありません。私たちの作った低速空洞では実際に衝撃波を見ることができて、面白い体験でした。前縁に3Dプリント製の小型インサートを装着し、その中にセンサーを入れました。モデル全体としては、アルミニウムの翼に小型インサートが取り付けられていて、このインサート部分を交換できるようにしたんです」
Brown氏が選んだ材料と選定理由については、ケーススタディをご覧ください。
大西洋の反対側、カールスルーエ工科大学(KIT)の風洞でも3Dプリント部品の試験が行われています。博士課程の学生であるLars von Deyn氏は、乱流の予測方法を研究しています。彼の研究は、モビリティの摩擦を減らすための材料や設計の選択に役立つ可能性があります。
von Deyn氏は、試験部品を製作する方法として3Dプリントに注目しました。「機械加工で作るのが難しい構造を調べたいんです」という彼は、Form 3Lを選びました。造形サイズが大きく、風洞実験エリアを少ない部品でカバーでき、パターンの中断が少なくて済むからです。
こちらの実験結果は、ケーススタディでご覧いただけます。
9. 3Dプリントで次世代のエンジニアを育成
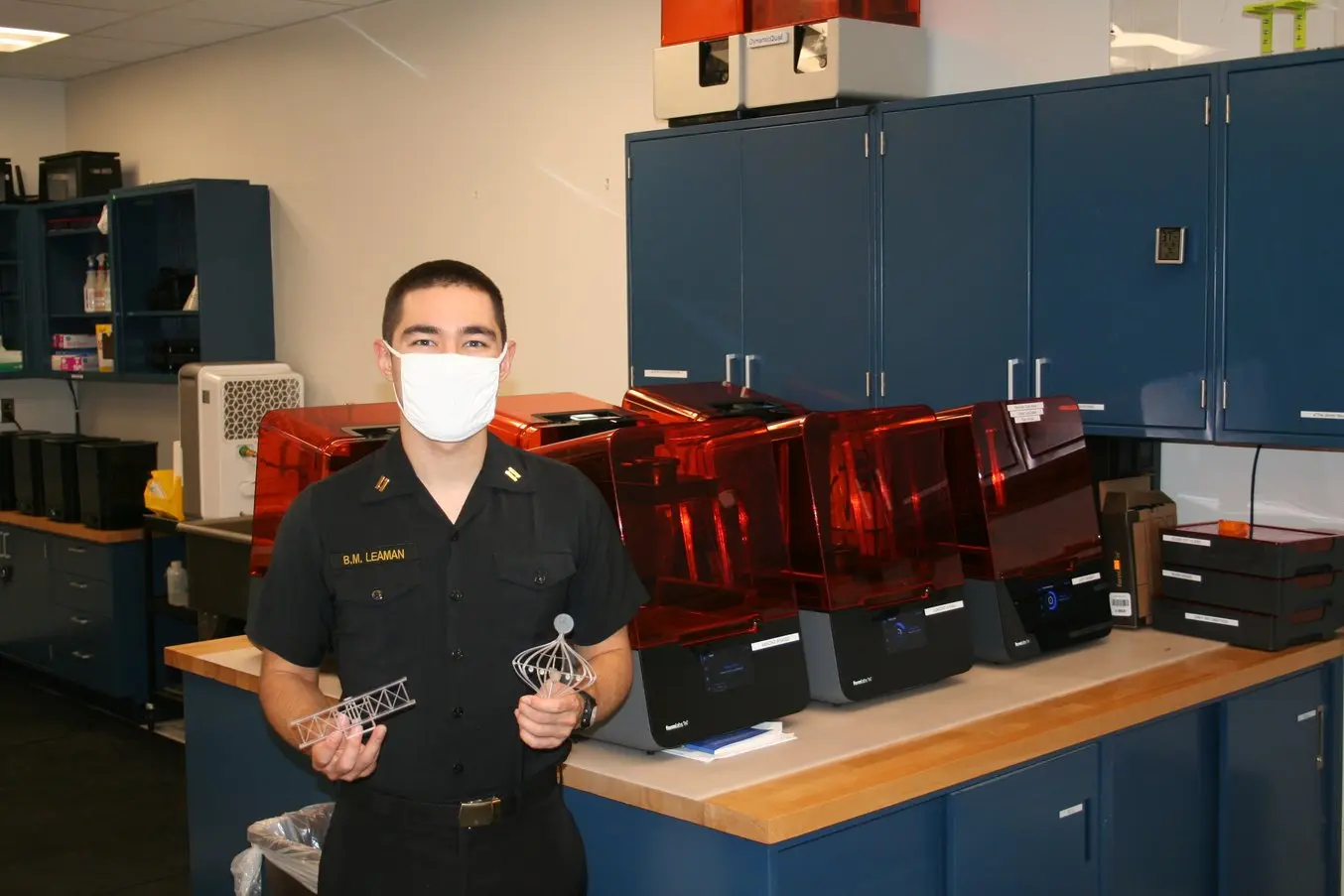
2021年のAM Olympicsで、FormlabsのForm 3でプリントした受賞作品を披露するUSNA海軍建築専攻の海軍技術士官候補生1/C Ben Leaman氏。
アメリカ合衆国海軍兵学校は、アメリカ海軍およびアメリカ海兵隊に仕える士官候補生を育成しています。USNAの助教授であるBrad Baker大尉は、実際の製造設備を使用できないことが工学部生たちの試作・検証プロセス、すなわち学習ペースそのもののボトルネックになっていることに気がつきました。キャップストーンプロジェクト専用のマシンショップ(工作機械を設置した作業場)はあっても、 1年間のコース期間中に学生達が実際に作業できる機会は3〜4回程度に限られていたのです。
大学の講義で3Dプリンタを学生に提供した教授は、Brad Baker大尉が初めてではありません。しかし、Baker大尉はMakerSpaceUSNAを立ち上げた際に設計機能と製造機能を1箇所に集約したのです。当初はFDM方式の3Dプリンタ数台だけでしたが、これらを機械工学部のカリキュラムに導入し、キャップストーンプロジェクトでも使用できるよう、学生に3Dプリンタを解放しました。
工学部での専攻が始まると、まずCADソフトウェアの使い方を学びます。次にFDMプリンタの操作方法、それからSLA光造形、そして最後にSLS(粉末焼結積層造形)方式の3Dプリンタへと進んでいきます。さらに最近では3Dスキャナも導入し、使い方を学んだスキャナやCAD、プリンタなどを駆使してリバースエンジニアリングのすべての工程を経験できるようにもなっています。
FDM、SLA光造形、SLSという品質と信頼性の高い各方式の3Dプリンタがあることで、MakerSpaceUSNAは、USNAの学生一人一人に様々なアディティブマニュファクチャリング技術を体験させることができています。Baker大尉の教育哲学である「実践での学び」と「失敗からの学び」により、工学部の学生達はさらに一歩踏み込んだ経験ができ、米国海軍やそれ以外の分野でも活躍できるような基礎スキルを習得しています。
航空宇宙業界における3Dプリントの未来
アディティブマニュファクチャリングがこれまで以上にパワフルかつ利用しやすくなったことで、航空宇宙業界はより多くの企業が参入・貢献できる場となりつつあります。今後5~10年で、OEM、サプライヤー、公的機関、スタートアップ企業、アカデミアのどこで最大のブレークスルーが起こるのかは分かりませんが、これまで以上に多くの人々が3Dプリントを使用できるようになったことで、こうしたイノベーションもこれまで以上に加速していくことでしょう。
3Dプリントに対する理解が航空宇宙業界全体に広がり、技術と利用可能な材料がさらに多様化するにつれ、アディティブマニュファクチャリングは今後も世界中で航空機や宇宙探査機の設計や製造、メンテナンスの方法を変えていくことになるでしょう。