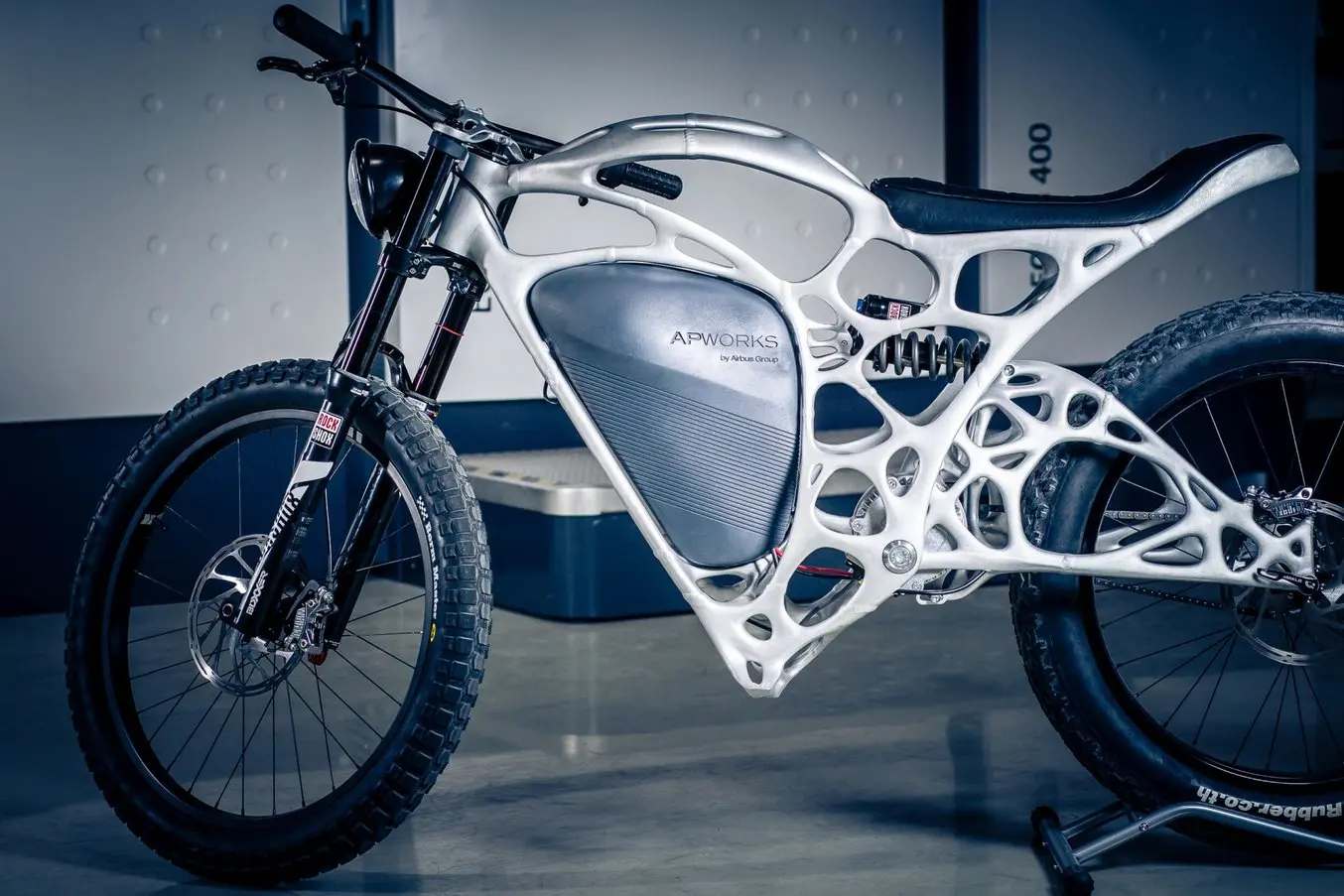
ジェネレーティブデザインは、製造業のすべての分野で働くエンジニアにとってCAD設計の新境地とも言える技術です。人工知能(AI)の力を活用し、複雑な課題の解消や部品の軽量化、製造コストの削減、大規模なカスタマイゼーション、性能の最適化を実現できる新しい高機能設計をいくつも編み出すことができます。
格子構造で各所に繊細なディテールが施された形状は一見現実離れして見えるかもしれませんが、ジェネレーティブデザインのおかげで、そのような形状が実践的な用途に導入されるケースが増えてきています。
本記事では、ジェネレーティブデザインの仕組み、メリットと用途、そしてジェネレーティブデザインで作った設計を具現化する際に3Dプリントが果たす役割について、包括的に解説します。実際の導入事例と実践的なヒントを織り交ぜながら、ジェネレーティブデザインを始める方法を確認していきましょう。
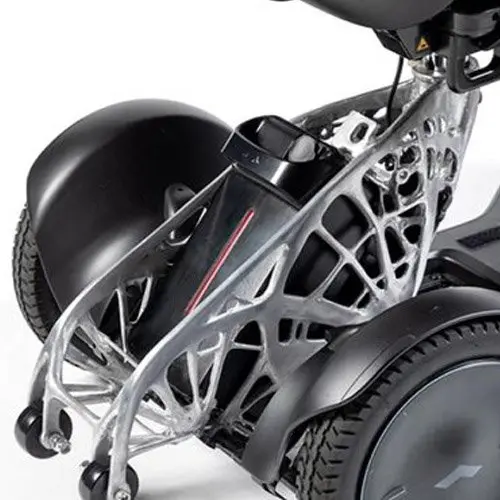
ジェネレーティブデザイン入門:3Dプリントで軽量部品を製作(英語)
本ウェビナーでは、Formlabsの製品マーケティングリードのJennifer Milneが、「ジェネレーティブデザインとは何か」について機械部品の設計の観点から概要をご説明するとともに、Fusion 360の使い方をステップごとに説明しながら実際に軽量ブラケットを製作していきます。
ジェネレーティブデザインとは
ジェネレーティブデザインの定義
ジェネレーティブデザインとは、AIベースのソフトウェアプログラムが指定の条件内で複数の設計を提案するプロセスです。従来の設計方法ではまず、エンジニアが持っている知識を頼りにモデルを作成する必要がありましたが、ジェネレーティブデザインでは設計条件を指定すればAIがモデルを作成してくれます。
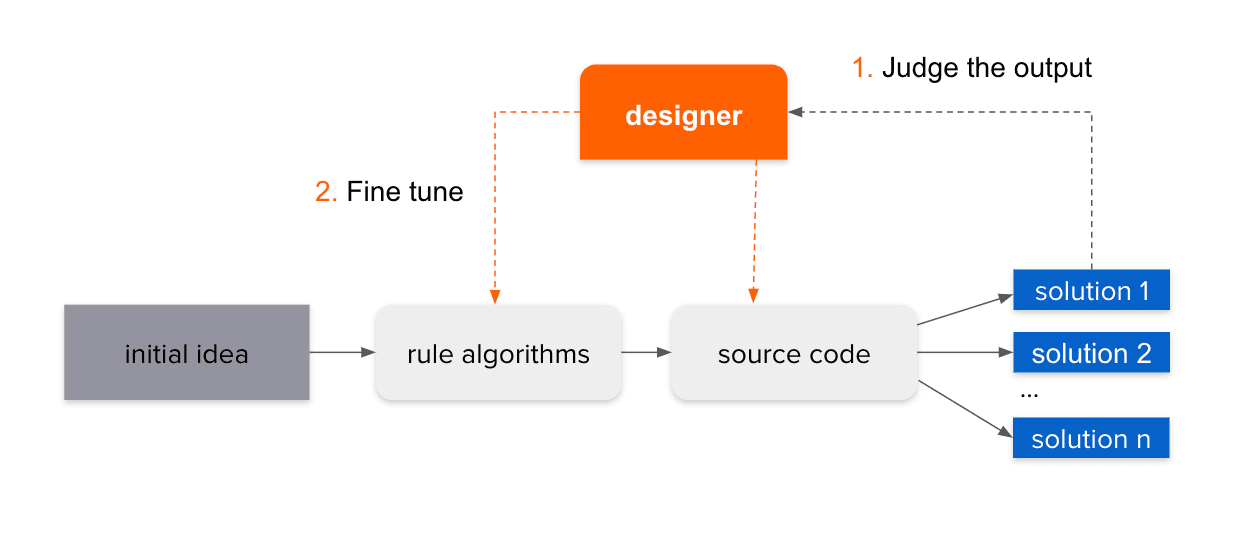
ジェネレーティブデザインのプロセス。出典:『Generative Design(Generative Design Processingで切り拓く、デザインの新たな地平)』H Bohnacker、J Laub、B Groß、C Lazzeroni著、2009年。
設計条件を編集するたびに洗練されていくフィードバックループの中でさらに条件を調整することで、エンジニアは製品部品の軽量化、強化、費用対効果の向上など、エンジニアリング分野のさまざまな課題に幅広く対応できる高度に最適化・カスタマイズされた設計を見つけ出すことができます。
トポロジー最適化とジェネレーティブデザインの違い
ジェネレーティブデザインとトポロジー最適化(位相最適化)はどちらもCAD設計業界でよく聞く言葉になりましたが、この2つを同類のものと誤解しているケースも多くあります。
トポロジー最適化は新しい技術ではありません。20年以上前から存在している技術で、一般的なCADソフトウェアに広く導入されてきました。トポロジー最適化の手順ではまず、人間のエンジニアが荷重や拘束条件、その他条件を考慮しながらCADモデルを作成する必要があります。その後、ソフトウェアが指定の条件に従って最適化されたメッシュモデルを1つ生成し、エンジニアが評価を行います。つまり、トポロジー最適化では部品を構想段階から実際に製造できる状態にするにはまず人間が設計したモデルが必要で、プロセスや結果、スケールに制約があります。
ある意味で、トポロジー最適化はジェネレーティブデザインの基礎になっているとも言えます。ジェネレーティブデザインはトポロジー最適化の手順をさらに進化させ、プロセスの開始時に人間が設計したモデルを必要とせず、事前に定義された条件に基づいて自動で設計を行います。
ジェネレーティブデザインで変化するエンジニアの役割
技術の発達に伴い、エンジニアの役割も進化しています。設計工程におけるコンピュータソフトウェアの比重が大きくなるにつれ、デジタルツールを使いこなせて設計上の課題の解決方法をしっかり理解していることが、すべての業界で働くエンジニアに求められています。ジェネレーティブデザインが誕生する前は、スケッチやモデリングによって製品の構想を考えたり設計を検証することがエンジニアの役割でした。
今では、エンジニアがジェネレーティブデザインソフトウェアを使用して高度な機能要件や一般的な設計フレームワークを定義し、その他の詳細はソフトウェアに任せられる時代になりました。しかし、これらの設計条件を定義するのは難しく、特に新材料の特性や値として定義するのが難しい課題や解決策を反映したモデリングを行う場合は特に複雑になります。
従来の設計プロセスとは根本的に異なり、エンジニアが自ら設計案を作成する必要はありません。その代わり、ジェネレーティブデザインでは環境を明確に定義して最適な設計を作れるようにすることがエンジニアの役割です。「考える」部分をソフトウェアに任せられるので、ジェネレーティブデザインではエンジニアがイノベーションやよりハイレベルな問題解決に集中することができます。
ジェネレーティブデザインの用途
ジェネレーティブデザインは、航空宇宙、建築、製造、消費者製品など、さまざまな業界で活用されています。エンジニアは、エンジアリング関連の複雑な問題を解決しようとするときにジェネレーティブデザインを使用することが多く、部品の軽量化や製造コストの削減、カスタマイゼーションのスケール化、性能の最適化などに取り組みます。
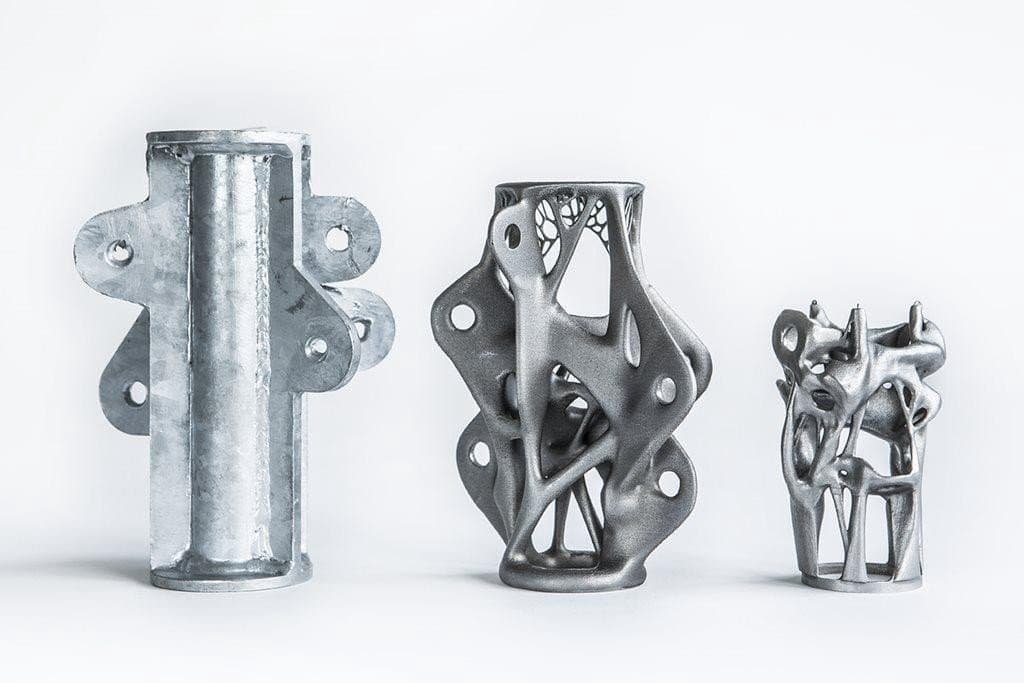
荷重がかかる箇所が決まっているブラケットやストラットは、ジェネレーティブデザインが活用されることの多い部品。
例えば、自動車業界ではエンジニアが部品の軽量化、設計として弱い箇所の改善、部品の結合により製造コストを削減、新製品の市場投入までの時間を削減するためにジェネレーティブデザインを活用しています。
スポーツ用品業界でも同様に、デザイナーたちが製造コストを最小化しながらこれまでにない製品性能を実現しようと、ジェネレーティブデザインを活用しています。航空宇宙業界では、ジェネレーティブデザインによってエアラインメーカーが機体に使われる部品の軽量化や強化に成功し、燃料消費にかかるコストや二酸化炭素の排出量削減に役立っています。
ジェネレーティブデザインのメリット
複数の設計案を同時に比較:ジェネレーティブデザインの最も大きなメリットは、数百・数千という設計案を同時に検討、検証、比較できることです。ソフトウェアで複数の設計案を表示して比較してできるため、エンジニアが効率的かつ素早くプロジェクトの要件やニーズに最適な設計を選ぶことができます。
設計工程を高速化:エンジニアがAIを活用して複雑な新設計を素早く、効率的に、かつ大量に見つけることができるので、新製品の研究開発工程を大幅に短縮することができます。その結果、ジェネレーティブデザインを活用する企業は、製品の市場投入までの時間を短縮し競争力を得ることができます。
先進的な製造工程を活用:ジェネレーティブデザインにより、アディティブマニュファクチャリング技術でしか得られない設計の自由さを活かした有機的な形状や格子構造を持つ複雑な形状も作成できるようになります。また、部品同士の結合も可能になるため、ジェネレーティブアルゴリズムで生成した複雑な形状の単一部品を3Dプリントし、これまで複数の部品で構成されていたアセンブリを単一部品に置き換えることができます。
ジェネレーティブデザインが使えるソフトウェア
CADソフトウェアに慣れている方なら、ジェネレーティブデザインソフトウェアもすぐに使いこなせるようになるでしょう。ジェネレーティブデザインに特化したソフトウェアだけでなく、ジェネレーティブデザイン機能をプラグインとして統合しているCADソフトウェアも多くあります。
しかし、ジェネレーティブデザインソフトウェアでは、これまでCADソフトウェアで提供されていた以上の機能を使うことができます。ユーザーはソフトウェア上で荷重や材料、コスト、その他任意の情報を設計プロファイルに入力し、設計のグラフィックをもとに一部の設定を優先させたり微調整したりすることができます。
もちろん、ここで紹介するものがすべてではありませんが、以下がジェネレーティブデザイン機能を提供する人気のソフトウェアです。
-
Fusion 360(Autodesk):Fusion 360では、スケッチやダイレクトモデリング、サーフェスモデリング、パラメトリックモデリング、メッシュモデリング、レンダリング、その他さまざまなモデリングツールを使用できます。Fusion 360のジェネレーティブデザイン機能では、設計要件、制約条件、材料、製造条件を定義し、製造が可能な設計を生成することができます。これらすべてを機械学習やAIの力を活用し、クラウド生成された設計案を見た目の類似性や図面、フィルターをもとに比較することができます。
-
Creo Generative Design(PTC):クラウドを活用するこのソフトウェアでは、最適化された設計構想を生成し、膨大な量の設計案を同時に比較・検証できます。また、設定した設計条件をもとに、ユーザーのニーズに最も適した設計案をハイライトしてくれます。Creoの設計環境では、他の競合ソフトウェアよりも短時間で、高品質かつ低コストな製造可能な設計を生成できます。
-
nTop Platform(nTopology):nTop Platformでは、生成された結果に対してユーザー自身があらゆる観点から最適化を行うことができます。高度なジェネレーティブデザインを使って、用途の特殊要件に適した再利用可能なカスタムワークフローを生成できます。このソフトウェアで優れた機能は、壊れないモデリング、格子構造、トポロジー最適化、再利用可能な設計ワークフロー、現場指向の設計、機械的有限要素分析のシミュレーションです。
-
NX(Siemens):NXでジェネレーティブデザイン以外に利用できる主要機能に、デジタルツイン技術があります。この技術が提供する柔軟でパワフルな統合型ソリューションにより、良い製品の設計・納品工程を合理化することができます。NXでは設計の総合運用性、検証、モデルベースの定義、その他の機能を組み合わせ、製品の品質を向上させながらより低コストで製品の研究開発工程を高速化させることができます。
-
MSC Apex Generative Design(MSC Software):高精細な金属部品を競合ソフトウェアより高速に、かつ人の介入を必要とせずに作るための一貫したソリューションを提供します。MSC Softwareのレポートによると、ユーザーは初期設計と立ち上げの時間を80%程度短縮することができたといいます。このソフトウェアを一目見ただけで、簡潔さと設計の自動化、インポート、検証、直接出力機能が1つのプロセスに統合されているとわかるでしょう。
ジェネレーティブデザインと3Dプリント
ジェネレーティブデザインと3Dプリントの相性が良い理由
ジェネレーティブデザインのアルゴリズムは、非常に効率的でありながら、CNC加工などのサブストラクティブマニュファクチャリング用マシンや射出成形など、従来の工法ではコストが高くなったりそもそも製造が不可能な、格子構造や有機的な形状を設計として生成することが多いのです。このような最適化設計がどうしても必要になる性能要件が厳しい用途では、アディティブマニュファクチャリングとしても知られる3Dプリントなどの高度な製造ツールが必要です。
複数の設計案で高精細な3次元モデルを柔軟かつ高速で、コスト効率よく実製品を生産できる3Dプリント技術は、ジェネレーティブデザインとの相性が抜群です。費用的な観点から考えると、設計案が複雑になれbなるほど、3Dプリントで製造する場合のコスト効率が上がることになります。
導入費用を回収するために製品を大量に生産する必要がない3Dプリントは、製品を少量だけ生産する場合により費用面でのメリットを享受しやすいと言えます。そのため、ジェネレーティブデザインで可能になるマスカスタマイゼーションがしやすくなるのです。3Dプリンタの価格は年々下がり続ける一方、使用できる材料の種類は増え続けているので、中小規模の生産でより多くの用途に適した部品の生産には実用的な方法です。

最適な3Dプリント方式の選定方法
ニーズに適した3Dプリント方式選びでお困りですか?このビデオガイドでは、FDM、SLA、SLS方式を比較しています。購入前の検討材料としてご参照ください。
ジェネレーティブデザインと3Dプリントを融合した活用事例
ジェネレーティブデザインと3Dプリンタを活用している実際の事例を3つご紹介します。
IGESTEKは、プラスチックや複合材料を用いて、自動車産業向けの軽量化ソリューションの開発を専門とするリーディングカンパニーです。同社は、複合部品を製造するための様々なハイブリッド加工技術を開発・統合して提供し、それらを自動車部品サプライヤーやOEM(委託先ブランド製造)企業が高級車やオートバイの部品製造に用います。
IGESTEKの最新の革新的プロジェクトの1つが、サスペンション・ショックアブソーバー・サポート(トップマウント式)です。これらの部品は、自動車のサスペンションシステムの一部で、自動車のローリングによって発生する振動を低減し、乗員の快適性を向上させることを目的としています。
ショックアブソーバーサポートは、限定された一連の要件に基づいて複数のソリューションを提供する、AutodeskのジェネレーティブデザインソフトウェアFusion 360を使って開発されました。
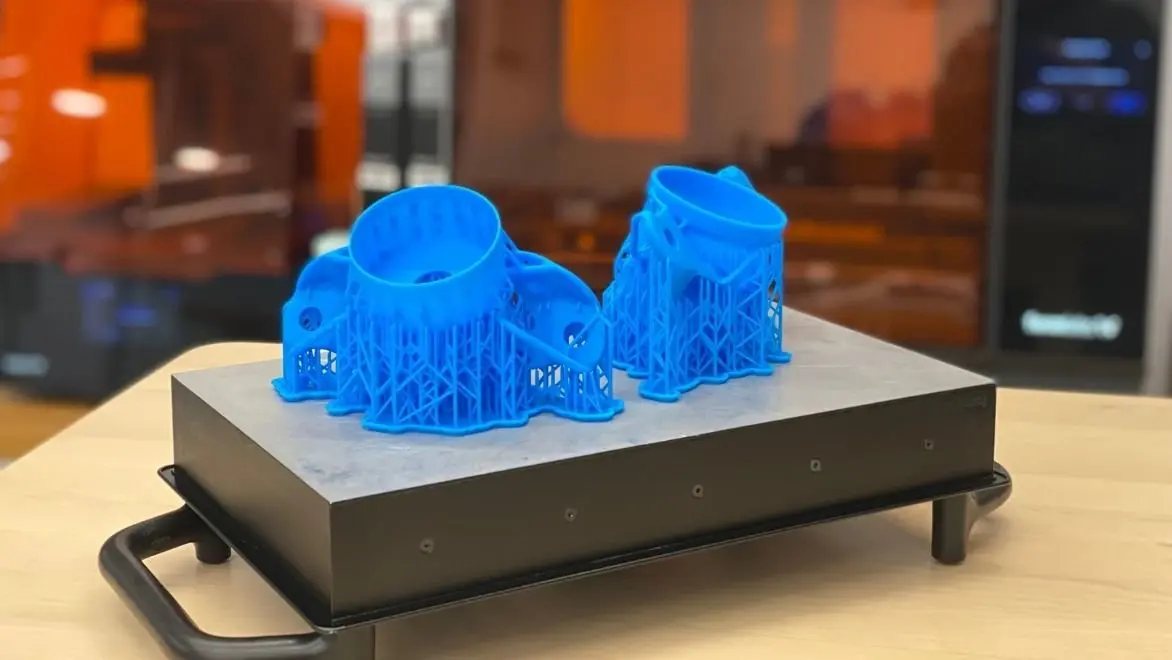
Form 3Lは造形エリアが広い為、複数の部品を同時プリントすることが可能。
チームは、最も期待できるデザインを社内の大容量光造形3Dプリンタ Form 3Lを使って3Dプリントして形状を検証しましたが、最大造形サイズが大きいことで最大3種類のバージョンの同時プリントが可能になりました。SLA方式3Dプリント
で、高価な金型に投資することなく、ジェネレーティブデザインで得られた複雑な形状を実現し、機能プロトタイプで組み立てや動作確認の検証を可能にしました。研究開発の結果として、ジェネレーティブデザインの金属3Dプリントと軽量な複合材料を組み合わせたマルチマテリアルアーキテクチャで、現在市場にあるソリューションよりも40%軽量かつ最高の性能を引き出すことに成功しました。
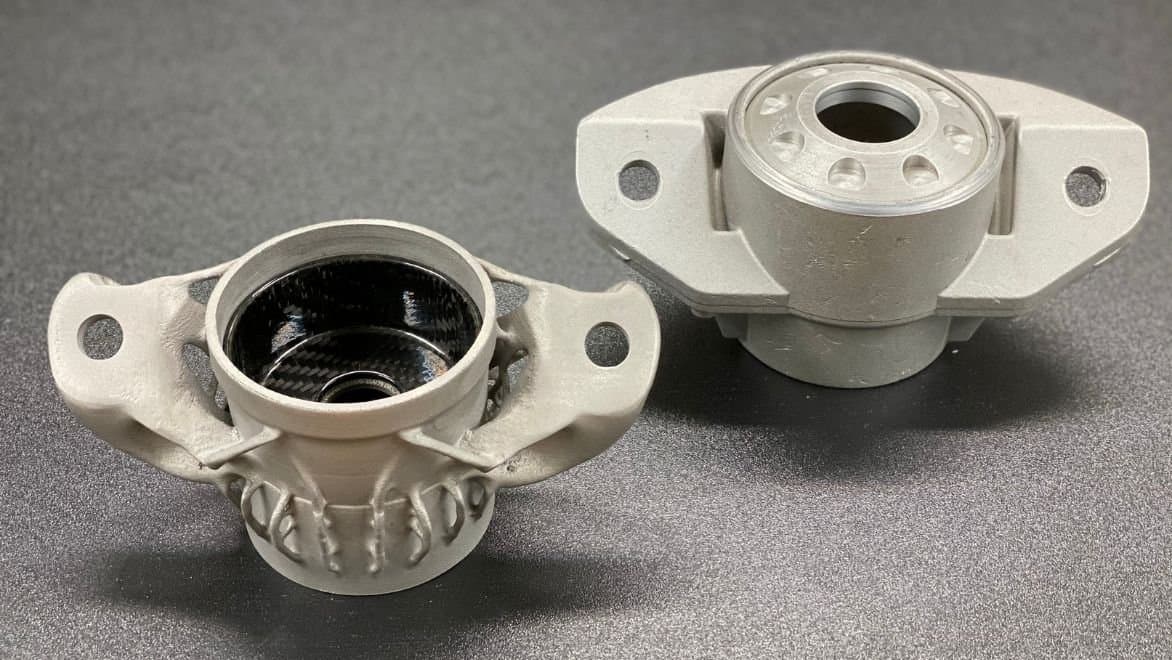
金属3Dプリントと複合材料を組み合わせて作られた部品。
日本の電動近距離モビリティ製品メーカーWHILLは、電動車椅子の中で重量が最大になる部品、バッテリーケースを軽量化をすることで、より移動のしやすい電動車椅子を作るという課題に挑戦しました。WHILLのエンジニアは、AutodeskのジェネレーティブデザインソフトウェアFusion 360を使って新しい設計を編み出し、バッテリーケースを40%軽量化することに成功しました。
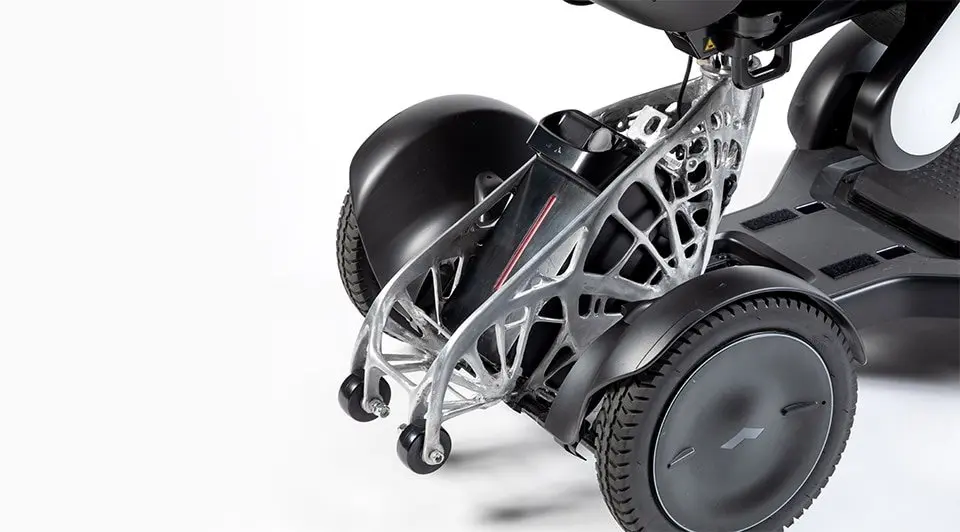

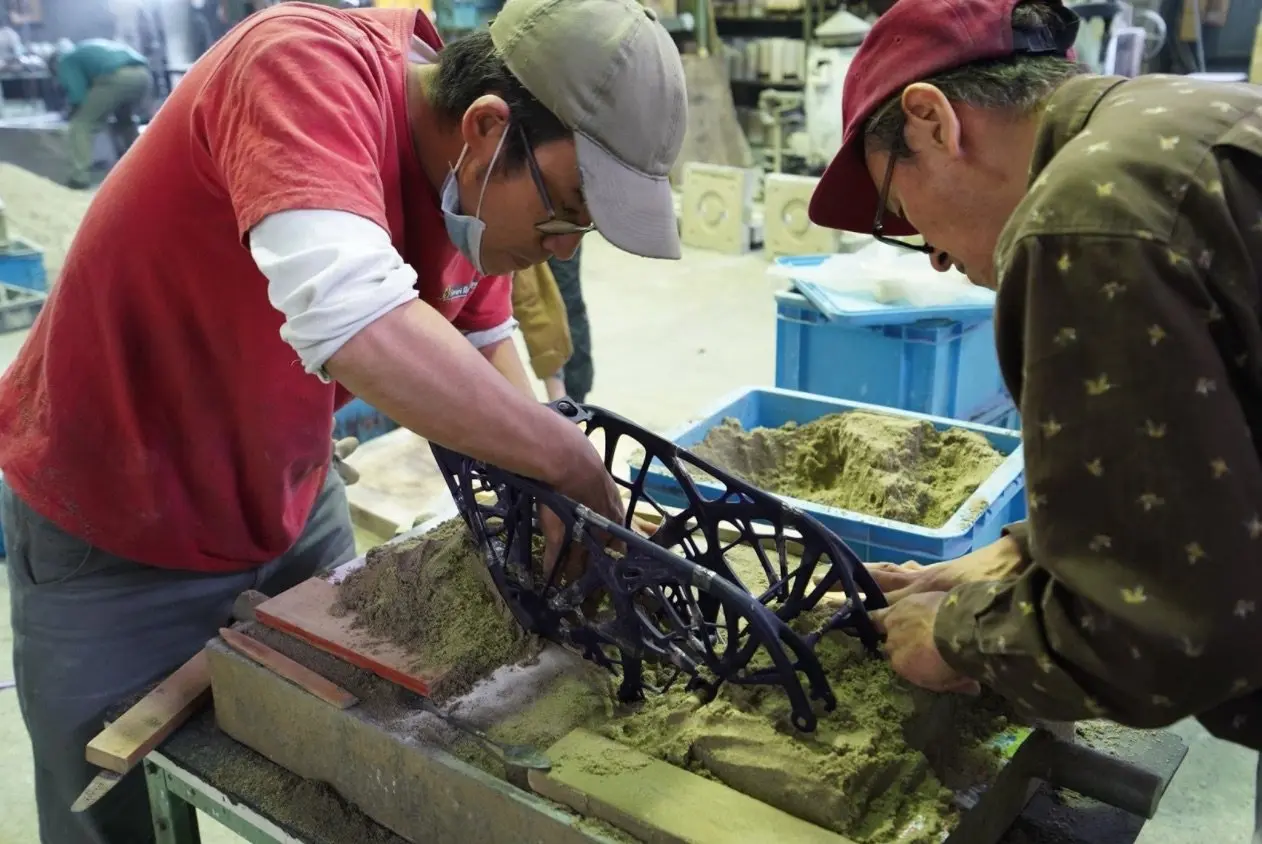
日本の電動近距離モビリティ製品メーカーWHILLは、ジェネレーティブデザインを活用して電動車椅子の中で最も重量のある部品、バッテリーケースの軽量化に成功。WHILLのチームは、デスクトップサイズのSLA光造形3Dプリンタを使用してインベストメント鋳造で使うパターンを製作。
その後、製品開発チームは3Dプリントを使った新たな製造工程で設計を具現化しました。FormlabsのデスクトップサイズSLA光造形3Dプリンタの最大造形サイズに収まるよう、バッテリーケースの設計を4つの部品に分け、各部品をCastable Waxレジンでプリントしてインベストメント鋳造用のパターンを製作し、造形後に各部品を組み合わせ、砂型鋳造によって最終的な金属製の鋳造型を作りました。3Dプリントによる内製とジェネレーティブデザインを融合したことで課題解決の突破口が見つかり、WHILL車椅子に使われる部品の合計数を減らすことで最終的な製造コスト削減に成功しました。
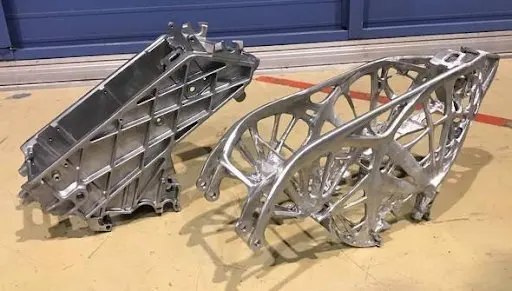
ジェネレーティブデザインで開発した部品でバッテリーケースの40%軽量化に成功。
WHILLと同様、フットウェアメーカーのNew Balanceもジェネレーティブデザインと3Dプリントを融合させることで飛躍的な進歩を遂げました。長期的なイノベーションを目指すカスタムシューズの製品ラインを作るため、New Balanceは2015年にデジタルデザインスタジオのNervous Systemと提携し、ジェネレーティブデザインを使ってランナーのパフォーマンスデータにより即したミッドソールの開発に力を入れてきました。
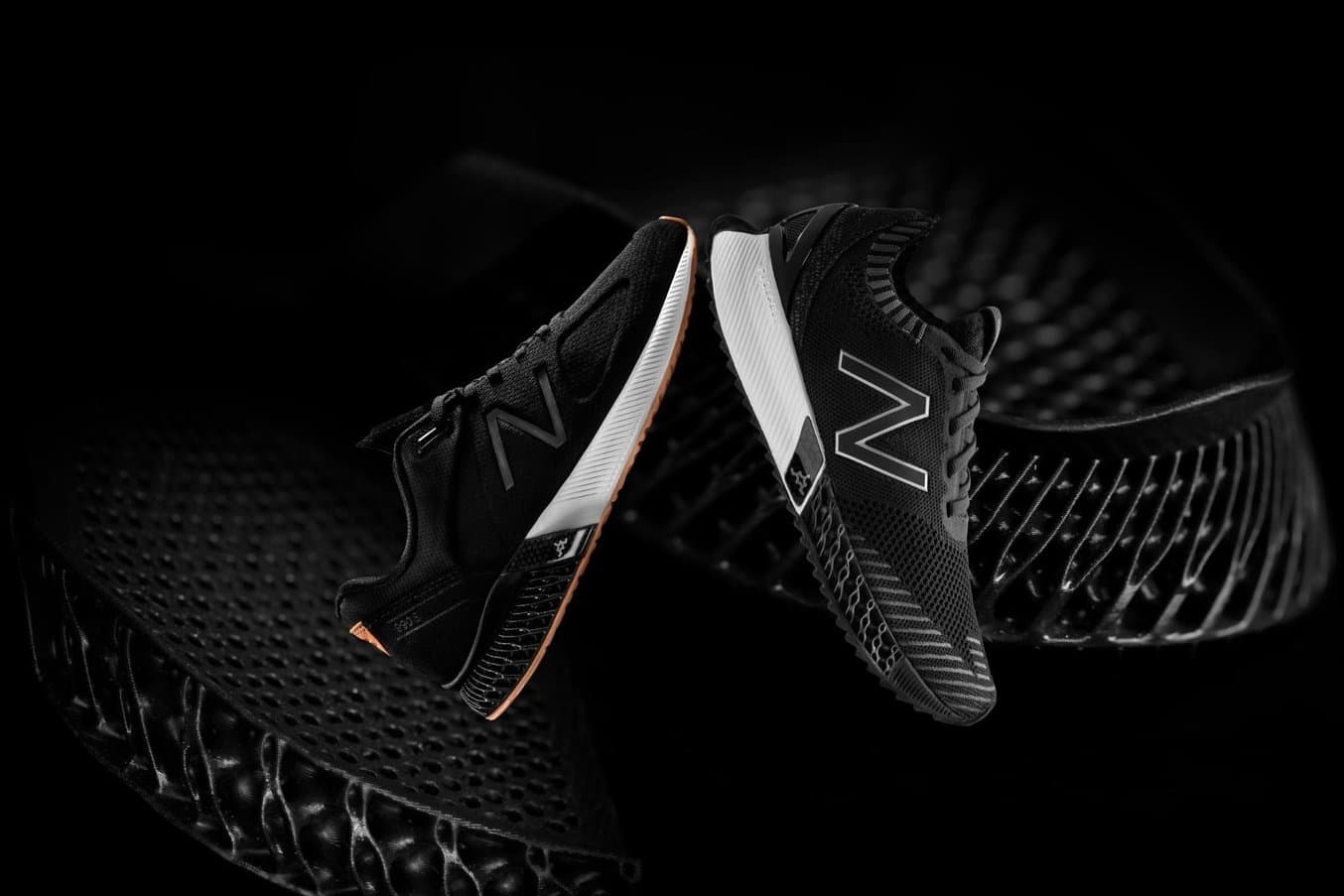
New BalanceはFormlabsと連携して全く新しい材料を一から開発し、ジェネレーティブデザインで開発したミッドソールを取り入れた高機能なカスタムシューズを実現。
そして2017年、New BalanceはFormlabsと提携して製造で利用可能なReboundレジンを独自開発しました。一般に流通している他の弾性材料と比べて5倍の引裂強さ、3倍の引張強さ、2倍の伸び率を誇るReboundレジンは、高い弾力性と強度を備えた部品の3Dプリントに最適です。New BalanceとFormlabsの協同により、シューズの生産に画期的な進歩をもたらし、消費者により良い製品を提供することができています。
New BalanceとFormlabsは、ユーザーひとりひとりに合わせたカスタムのランニングシューズを、ジェネレーティブデザインと3Dプリント用材料で大量生産するという大きな目標を実現すべく、提携を続けています。
ジェネレーティブデザインを始める
どこから始めたら良いかわからないという方向けに、主要なポイントをいくつかご紹介します。
始めやすい:CADソフトウェアを使ったことがある方なら、ジェネレーティブデザインもすぐに使いこなすことができるでしょう。ジェネレーティブデザインは、色々と試しながら明確な定義がされた既知の問題に対処しやすい機能です。30日間トライアル付きのCADソフトウェアの多くに、ジェネレーティブデザイン機能が搭載されています。
初めてのプロジェクトには既存部品の軽量化が最適:足掛かりとして、部品にかかる荷重が既によくわかっており、機能性を維持しながら軽量化のために最適な設計を探求するプロジェクトが始めやすいでしょう。
長期的なビジョンを小規模なR&Dプロジェクトに細分化: ジェネレーティブデザインとアディティブマニュファクチャリングでは、それぞれ求められる考え方や作業手順が異なります。最適化された高機能カスタム製品を3Dプリントで製作し、世界中で大規模展開するというのは、一夜にして実現できることではありません。成功するプロジェクトは、時間をかけて何度も試作・検証を繰り返す戦略的なプロジェクトなのです。
専門知識が豊富な技術パートナーを探す:Formlabs Factory Solutionsのように、ソフトウェアやAM企業にはプロジェクトを支援する専門チームを用意してくれるところが多くあります。専門知識を持ったチームの支援を得ながら、すぐにプロジェクトを立ち上げて学んでいくことができます。
ジェネレーティブデザインで未来を創る
ジェネレーティブデザインは、幅広い業界で製品設計の主戦力として使われることが多くなってきています。飛行機のエンジンブラケットの軽量化、より移動がしやすい電動車椅子の開発、ランニングシューズのカスタマイズなど、ジェネレーティブデザインと3Dプリントを融合することで、完全に最適化・カスタマイズされた未来が切り開かれようとしています。
AIとアディティブマニュファクチャリング技術の進化に伴い、これからもジェネレーティブデザインの可能性は広がり続け、新たな用途やこれら革新技術で得られるメリットは今後も増えていくでしょう。
ジェネレーティブデザインにご興味がある場合は、弊社ウェビナー「ジェネレーティブデザイン入門:3Dプリントで軽量部品を製作」をご覧いただき、ジェネレーティブデザインを活用した事例とFusion 360を使った軽量ブラケット製作のチュートリアルをご確認ください。