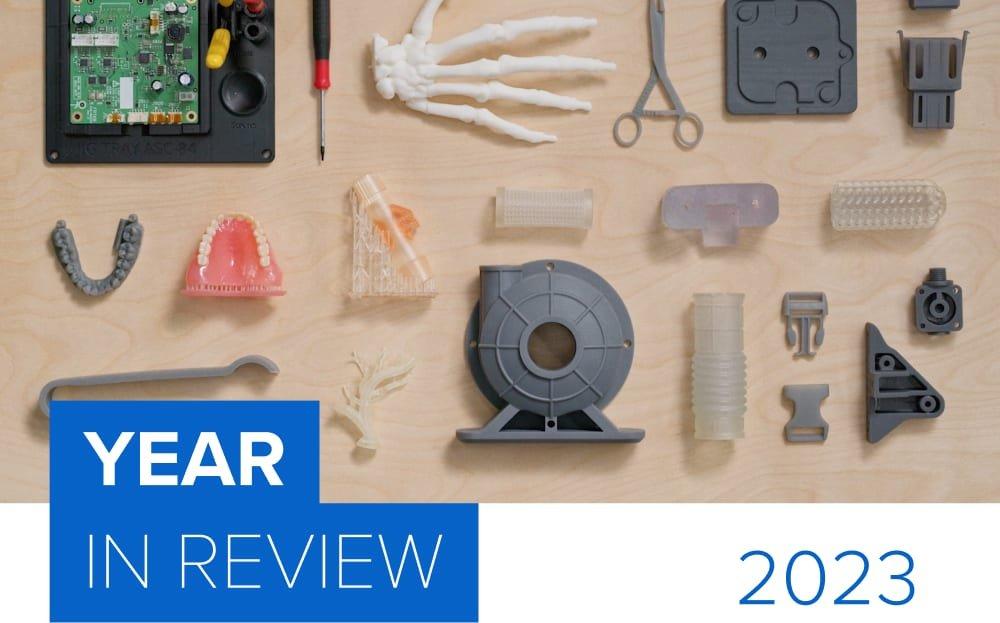
As 2023 comes to a close, we’re looking back at some of the highlights from the year. New hardware and software releases focused on efficiency and time-savings, while new materials expanded the scope of what it’s possible to print. Behind it all was a team of excited, passionate innovators, pushing 3D printing forward.
New Releases: Advanced Post-Processing for SLS, Automation, and Groundbreaking New Materials
Fuse Blast
November saw a new addition to the Fuse Series ecosystem, the Fuse Blast, the first affordable, industrial-quality cleaning and polishing solution for selective laser sintering (SLS) 3D printing. With it, users experience an 80% reduction in SLS post-processing time and more than a 400% extension of media lifetime due to a passive media separation feature.
“Adding this system to any new or existing SLS workflow is a massive improvement over a manual cleaning and post-processing workflow. The Blast also takes stress off of our bodies due to removing the repetitive movement of manual cleaning.”
Chris Haak, Operations Lead at Autotiv
Automation Ecosystem
Almost a year ago, we announced the Formlabs Automation Ecosystem for high-productivity 3D printing at scale, reduced cost per part, and improved user experience managing multiple desktop stereolithography (SLA) printers. Composed of Form Auto, Fleet Control, and a High Volume Resin System, these releases pushed what it means to reduce costs while improving productivity.
Expanding the Materials Catalog
As 3D printing applications expand, so too does the need for the development of suitable materials. This year marked the release of new resins, including Silicone 40A Resin and multiple biocompatible materials, as well as a new powder for SLS printing.
Resins for SLA
Silicone 40A Resin, the first accessible pure silicone 3D printing material, is made possible by our patent-pending Pure Silicone Technology™. The pliable, durable, and compressive qualities can be used in a range of applications and industries including rapid prototyping, low volume or custom manufacturing, and manufacturing aids and tooling. View Silicone 40A Resin’s mechanical properties and explore uses including the creation of silicone molds.
The first accessible, affordable, high-performance technical ceramic material for SLA 3D printers was announced this fall: Alumina 4N Resin. This 99.99% purity alumina material opens the doors to intuitive and cost-effective ceramic 3D printed part manufacturing, providing an attractive alternative to constrictive and expensive traditional methods of fabricating ceramic parts.
The development of three biocompatible materials expanded our resin portfolio and the breadth of suitable applications. BioMed Durable Resin was developed specifically to address the need for a biocompatible material that can withstand impact, rough handling, and pressure, and is ideal for patient-specific instruments (PSI) and customizable surgical instruments. BioMed Flex 80A Resin and BioMed Elastic 50A Resin enable the direct 3D printing of elastomeric, biocompatible medical devices and models, providing an efficient replacement to multi-step silicone molding processes, which are often labor-intensive and messy.
Powders for SLS 3D Printing
For the Fuse SLS 3D printer, we introduced TPU 90A Powder, a flexible elastomer that unlocks new possibilities in applications by combining the high tear strength and elongation at break of rubber materials with the design freedom and durability of SLS 3D printing. This versatile material allows for in-house production of soft-touch parts so you can bridge the gap between manufacturing stages, optimize your processes, and take full control of your supply chain, improving efficiency and minimizing downtime.
Formlabs: One of the Best Workplaces for Innovators
In 2023, Formlabs was recognized by Fast Company as one of the 100 Best Workplaces for Innovators, in part due to the annual Formlabs Hackathon. During this three-day event, people from various departments come together to work on projects. One past Hackathon cross-collaboration led to the development of Form Auto, released this year.
Printing Anything
We're continuously amazed by how our customers are driving innovation. From custom orthotics and compressive masks for treating facial burns to bicycle wheels and drone customization, 3D printing is being used across industries and for applications we couldn’t have conceived. Here are just a few of the stories that inspired us this year.
Treating Children With Severe Burns
At Romans Ferrari, a French rehabilitation center known throughout Europe for providing care to children and adolescents, a new digital workflow for creating custom compressive masks for treating facial burns using 3D scanning and 3D printing, has been developed. Thanks to a multi-team collaboration among doctors, prosthetists, and engineers, young patients are more comfortable and experiencing better outcomes.
Riding Into the Future
The Rider Firm is behind the design and manufacturing of popular bike component brands — both high-performance competitive racing bikes and direct to consumer cruisers. Seeking to make their components accessible to all riders requires a smart and efficient workflow. With a Form 3L SLA 3D printer, they can prototype and wind-tunnel test in house. For a single project, 3D printing saved them about six months and nearly $5,000 in production tooling.
How Lufthansa Technik Uses 3D Printed Tools
As one of the world's largest maintenance, repair, and overhaul (MRO) providers in aviation, Lufthansa Technik AG makes extensive use of additive manufacturing for constructing aviation products. The Guide U escape route markings on aircraft interiors are self-illuminating strips that mark the way to emergency exits. To produce these markings, Lufthansa Technik’s team leveraged manufacturing aids produced by SLA 3D printing. Specifically, they created a nozzle as a tooling component for the manufacturing process.
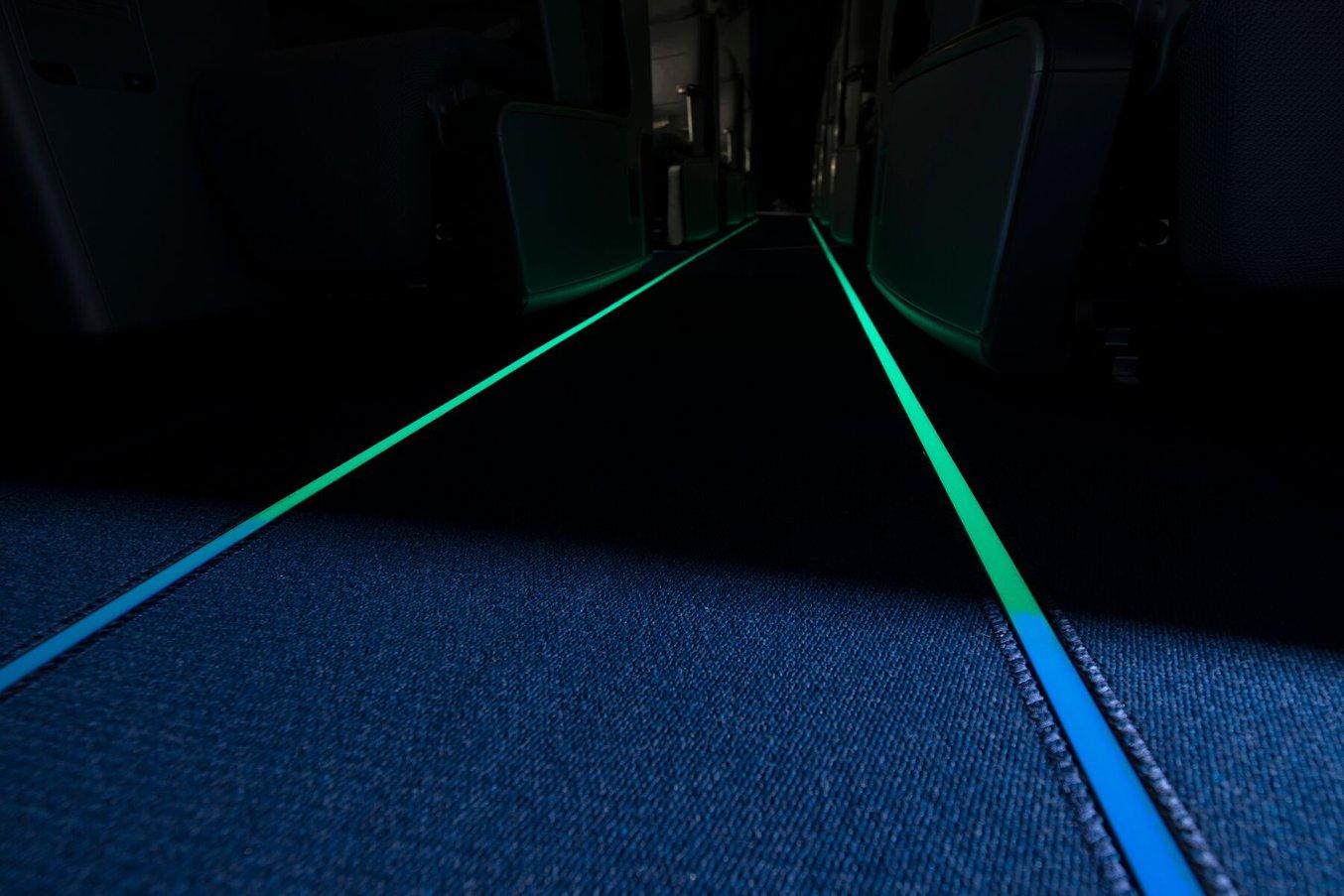
Lufthansa Technik's uses 3D printing to product photoluminescent Guide U escape route markings for aircraft interiors.
Learn more about how they achieved dimensional accuracy and increased flexibility with SLA 3D printing.
restor3d Drives Innovation With Surgical Instruments
restor3d leverages 3D printing capabilities to drastically improve surgical care delivery by printing procedure-specific metal implants and polymer instrumentation. With a fleet of over 25 Formlabs 3D printers, they’re reducing costs for hospitals by 3D printing patient-specific instrumentation.
Learn from restor3D’s team, and surgeons working with their tools, how 3D printing is enabling the creation of personalized medical devices for reduced recovery time and better results.
Big Strides for Orthotics
Kriwat GmbH is an orthopedic specialist medical provider with a unique focus on combining sports performance with cutting-edge medical research. Creating orthotics is a laborious project, but Lais Kriwat developed a digital workflow for insole production with SLS 3D printing to modernize the business and address these challenges. With this digital workflow, Kriwat GmbH is producing 10,000 pairs of insoles a year with 3D printing.
Nextech Customizes Drones With 3D Printing
Nextech, a drone manufacturer based in South Africa, uses Formlabs SLS 3D printers to fabricate high-performance customized drones, or unmanned aerial vehicles (UAVs) for their customers in a wide range of industries. The rugged, end-use qualities of SLS parts enable Nextech to design, prototype, and manufacture with one streamlined workflow. “The 3D printing workflow allows us to solve unique client requirements, develop new products, and improve on designs at a much faster rate,” says Mechanical Design Engineer Liam Kroone.
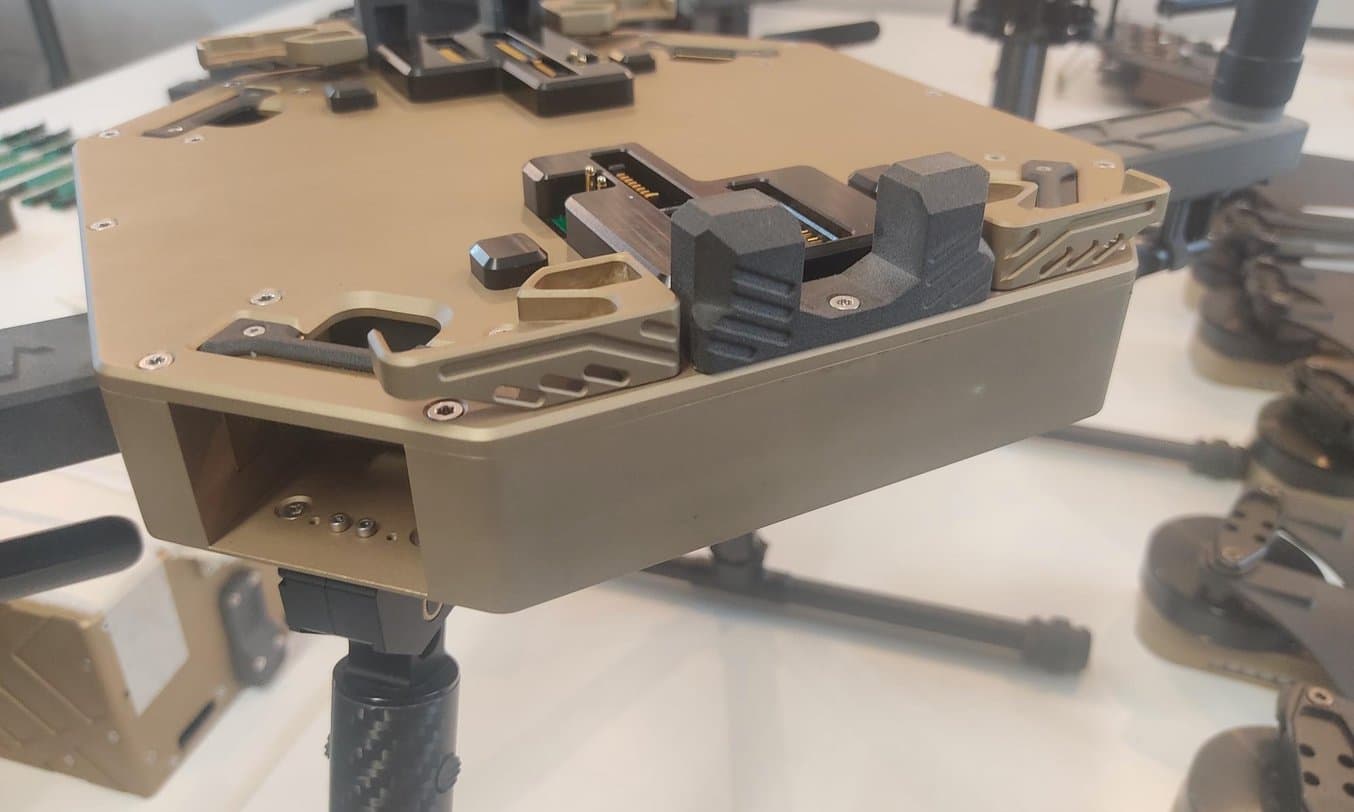
A quad with battery locator utilizes 3D printed parts.
Learn how they replaced millions of dollars in CNC machining and met customer demands with Formlabs’ Fuse Series SLS printers.
Hyphen Feeds Food Automation With 3D Printing
Hyphen, a restaurant automation start-up based in San Jose, California, creates and deploys restaurant automation tools. 3D printing has played a significant role in their speed to market and their unique modular approach to food creation.
Daniel Fukuba, CTO and co-founder at Hyphen, says, “We were able to cut down our cycle times of iteration on hoppers from two weeks to three days. And from a cost perspective, we get ROI on a machine like the 3L within three to four weeks, which is pretty significant for the capacity we're looking for.”
Learn how 3D printing is enabling Hyphen’s agile, customized automation solutions for the restaurant industry.
Looking to 2024
2023 brought new products, materials, innovations, and a lot of work on things to come. Seeing everything our community has already accomplished with 3D printing inspires us to continue pushing forward. 2024 will bring new innovations – from us and you.
If you’re looking for inspiration, we’re here to help.