近年、ハードウェア、ソフトウェア、材料を含む3Dプリント技術の急速に進化に伴い、3Dプリンタはこれまでの「目新しさ」という概念を超えて、今ではあらゆる業界の設計、エンジニアリング、製造工程において不可欠な存在となっています。
現在市場に最も普及している3Dプリンタは、FDM(熱溶融積層)方式、SLA光造形方式、SLS(粉末焼結積層造形)方式の3つです。過去10年で技術革新が急速に進んだ結果、より多くの企業が3Dプリントにアクセスできるようになった一方、競合する様々な3Dプリント製品の中から最適なものを選ぶことが難しくなりました。
この包括的なガイドでは、3Dプリンタの購入を検討中の方に向けたガイドとして、FDM、SLA光造形、SLS(それぞれフィラメント、光造形、パウダー方式とも呼ばれます)のそれぞれの方式の3Dプリンタについて詳細を解説するとともに、造形品質や材料、用途、作業手順、スピード、コストなどを比較しながら、ビジネスに最適なものを見つけられるようサポートします。

最適な3Dプリント方式の選定方法
ニーズに適した3Dプリント方式選びでお困りですか?本動画ガイドでは、FDM、SLA光造形、SLSの3方式の比較を行います。購入前の検討材料として、是非お役立てください。
FDM(熱溶解積層)方式3Dプリントとは
FDM(熱溶解積層)方式は、FFF(フィラメント溶解造形)またはフィラメント3Dプリント方式とも呼ばれ、一般消費者レベルで最も広く使用されている3Dプリント方式です。3Dプリントの経験が浅い一般的な初心者の方にもよく知られており、「3Dプリント=ホットグルーガンのようなもので造形する」というコンセプトに最も近い方式です。
FDM 3Dプリンタで初めて3Dプリント技術に触れるという方も多く、幼稚園から高校までの学校や、多くの大学のメイカーズスペースでも最もよく使用されている3Dプリンタです。デザイン、エンジニアリング、製造業界では、より機能的な試作品製作に移行する前の、デザインチームが合意形成を目的として製作する概念実証(POC)の段階で頼りにされることの多い方式です。
FDM 3Dプリンタは、サイズも価格も様々です。造形技術と作業手順がシンプルなFDM方式は、これから3Dプリントを始めようとする人にとっては負担の少ない魅力的な選択肢です。しかし、FDM方式はシンプルさと手頃な価格と引き換えに造形品質や性能の面で劣ることが多く、機能的性能や防水性、等方性、滑らかな表面品質をお求めの場合にはSLA光造形やSLS 3Dプリンタの方がはるかに優れた選択肢となります。
SLA光造形方式3Dプリントとは
SLA光造形方式3Dプリントは、1980年代に発明された世界初の3Dプリント技術です。しかし、SLA光造形方式はFDM方式に比べて価格が高く工程もやや複雑になるため、広く普及し認知されるまでに時間がかかりました。
光造形とも呼ばれるこの方式は、光源を照射することで液体レジンを硬化させ、層ごとに固めていくことで造形します。もともとは光源にレーザーを使用していましたが、最近ではDLP方式ではデジタル投光器に、MSLA方式やLCD方式では発光ダイオード(LED)に置き換えられるようになりました。つまり、現在レジンを使用する3Dプリンタは全て光造形3Dプリンタということになりますが、「光造形」という用語は一般的に「レーザーでレジンを硬化させる」ものを指す時に用いられます。
SLA光造形3Dプリンタは、他の3Dプリント方式よりも滑らかな表面品質と高い寸法精度、そして厳しい公差にも対応できる高精細な部品を造形できます。この種のプリンタは、射出成形品に匹敵する外観を実現できるため機能確認用試作の製作に最適ですが、優れた表面品質と非常に多様な材料特性により、実製品用部品や成形型の製作にも向いています。
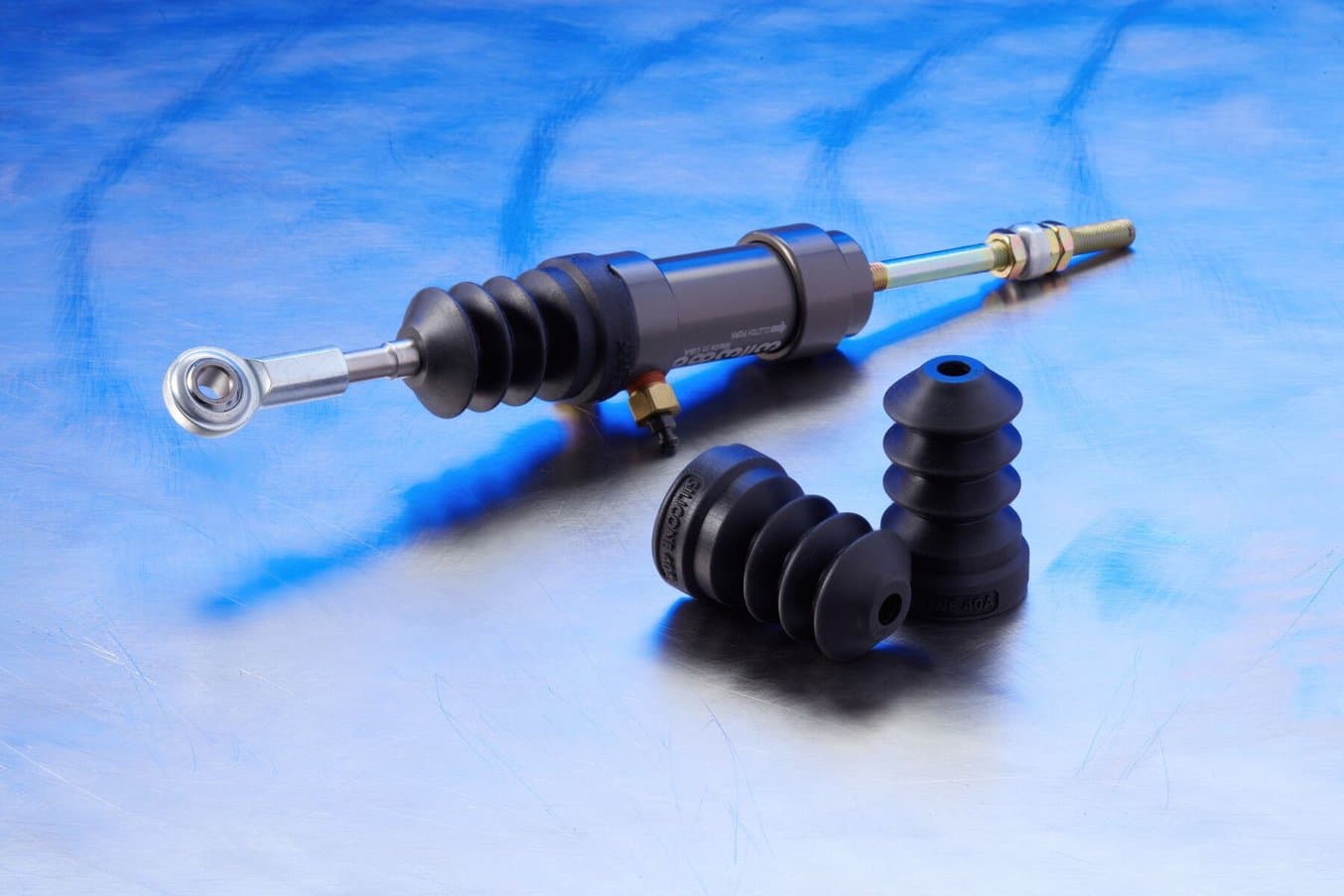
SLA光造形の最大の利点の1つは、使用できる材料の豊富さと、それによって可能になる幅広い用途にある。写真のクラッチブーツは、Formlabs Form 4 MSLA方式3DプリンタでSilicone 40Aレジンを使って造形したもの。
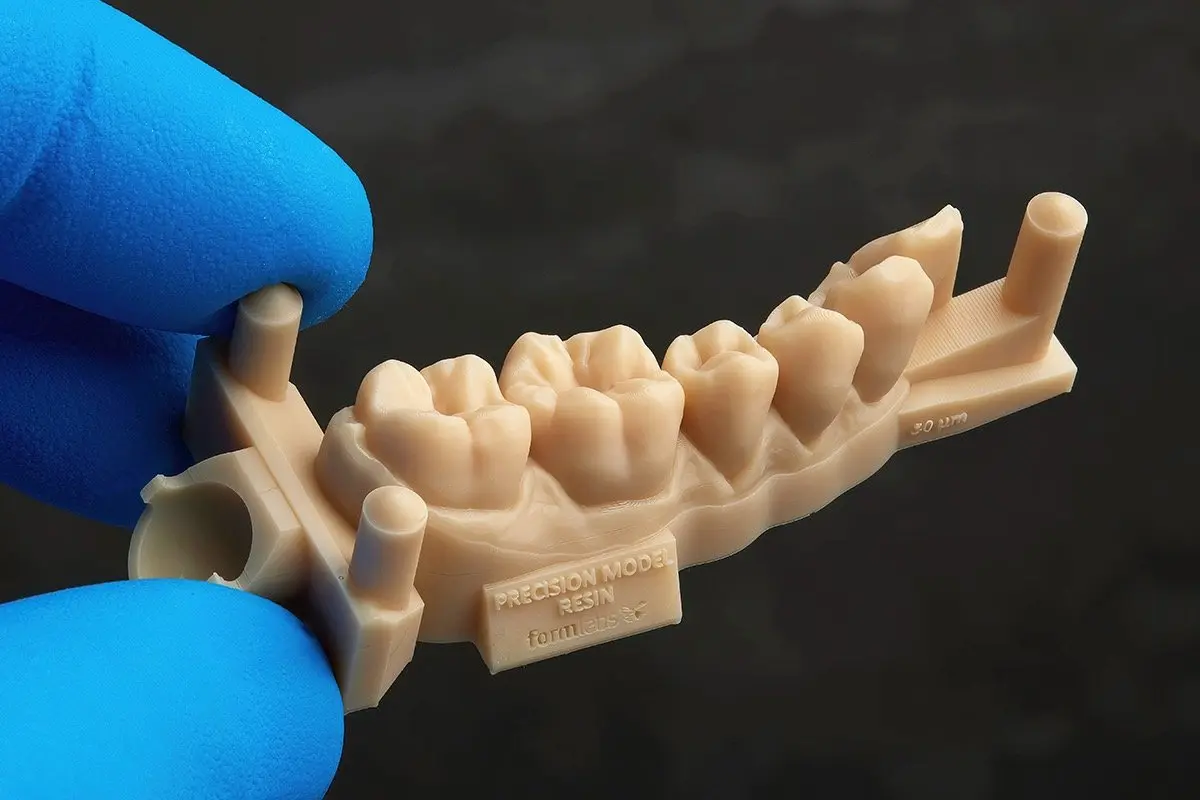
SLA光造形品は表面品質が滑らかで、極めて厳しい公差にも対応できる優れた寸法精度を備えていることから、歯科修復モデルのように厳しい条件が求められる用途に理想的な方式。
FDM方式やSLS方式3Dプリントで使用される業界標準の熱可塑性プラスチックとは対照的に、SLA光造形用の材料は独自に調合されています。このように多様な材料が使用できる点も、SLA光造形の主な利点の1つです。様々なメーカーが、標準的な熱可塑性プラスチック、エンジニアリングプラスチック、工業用熱可塑性プラスチックの他、難燃性、ESDセーフ、生体適合性などの特殊な機能を必要とする特定の用途にも対応できる幅広い光学的・機械的・熱的特性を備えた革新的なSLA光造形用レジンを開発してきました。このような幅広い材料特性とSLA光造形方式の精度・表面品質を組み合わせることで、航空宇宙、自動車、消費者製品、ヘルスケア、歯科など、あらゆる業界での活用が可能になります。
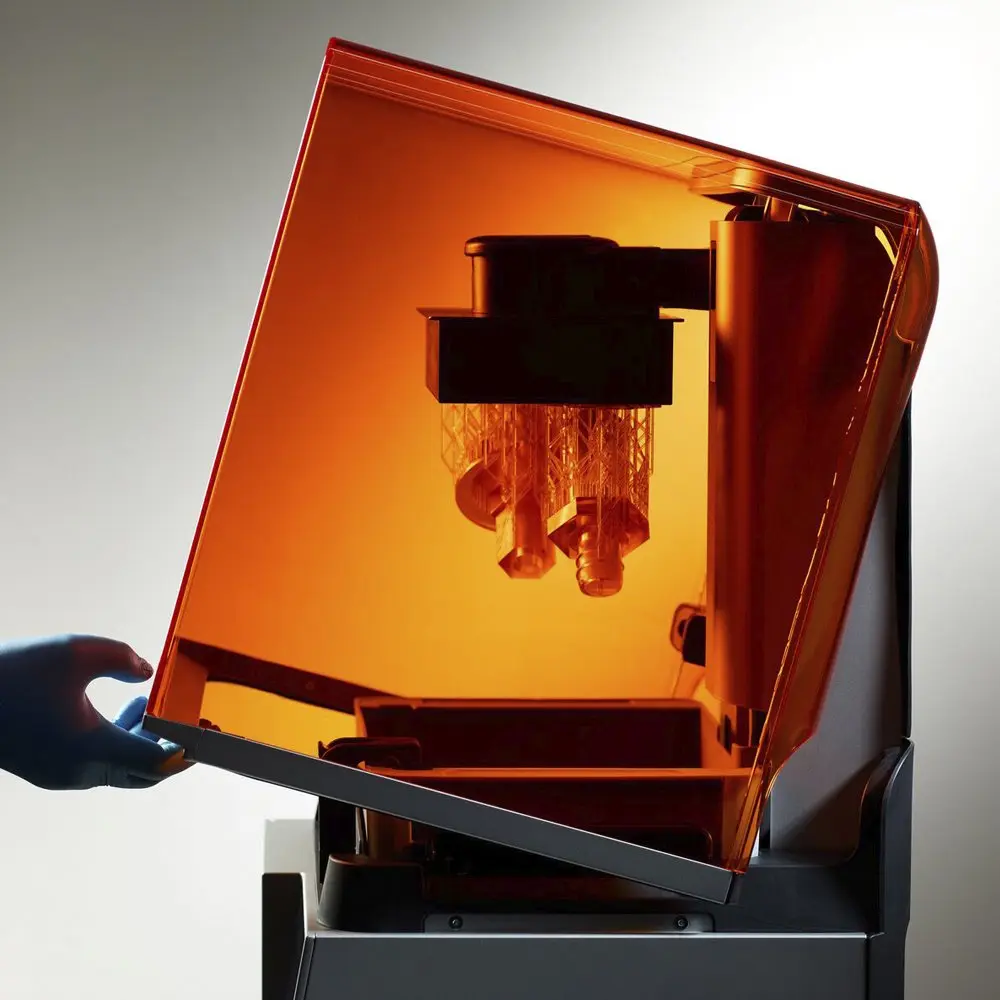
デスクトップサイズSLA光造形方式3Dプリンタの概要
高精細3Dモデルを高速製作できる3Dプリンタをお探しですか?こちらの技術資料をダウンロードして、高精細で高次元な優れた表面仕上がりのモデルを製作できる3Dプリント方式としてSLA光造形方式がどれほど広く活用されているかご確認ください。
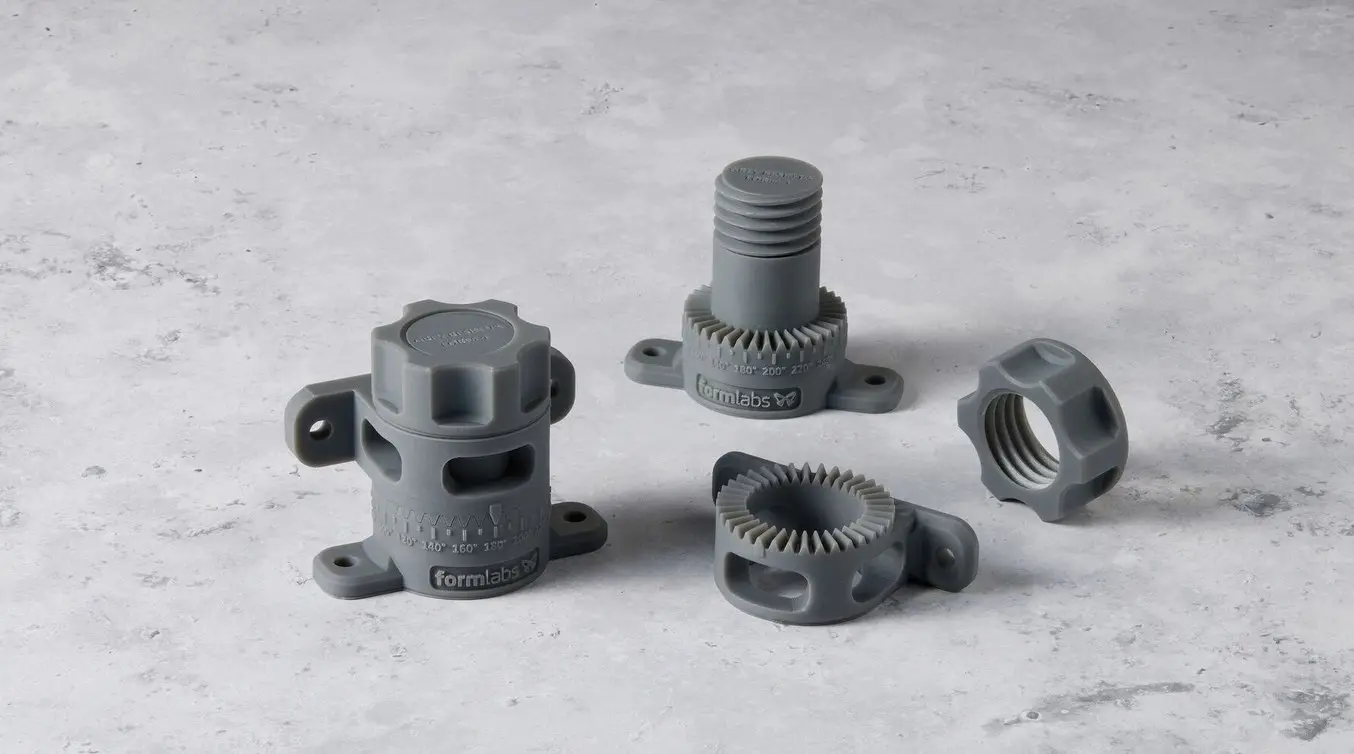
SLS方式3Dプリントとは
SLS(粉末焼結積層造形)方式は、高強度な機能部品が製作できることから、さまざまな業界のエンジニアやメーカーから信頼され、工業用途で最も普及しているアディティブマニュファクチャリング技術です。
SLS 3Dプリンタは、高出力レーザーでポリマー粒子を焼結することで造形します。プリント中は未焼結パウダーが造形品を支えるため、専用のサポート材が不要で、内部構造やアンダーカット、薄肉構造、空洞構造などの複雑な形状の製作に最適なだけでなく、量産用途にも対応できます。造形中は未焼結パウダーが周りを支えるため、モデルをビルドチャンバー内で「入れ子」状態にして高密度で造形することが可能で、1台のプリンターでも量産レベルの生産量を実現できます。
SLS方式で3Dプリントした部品は、射出成形品に匹敵するほどの高い強度など、非常に優れた機械的特性を備えています。SLSに最もよく使われる材料は、優れた機械的特性を有し人気の高い工業用熱可塑性材料、PA(ポリアミド/ナイロン材)です。ナイロンは軽量、高強度、高弾力性を特徴とし、衝撃、化学物質、熱、紫外線、水、土に対する耐性があります。他にも、ナイロン複合材、PP、軟質のTPUなどもSLS 3Dプリントで人気の高い材料です。
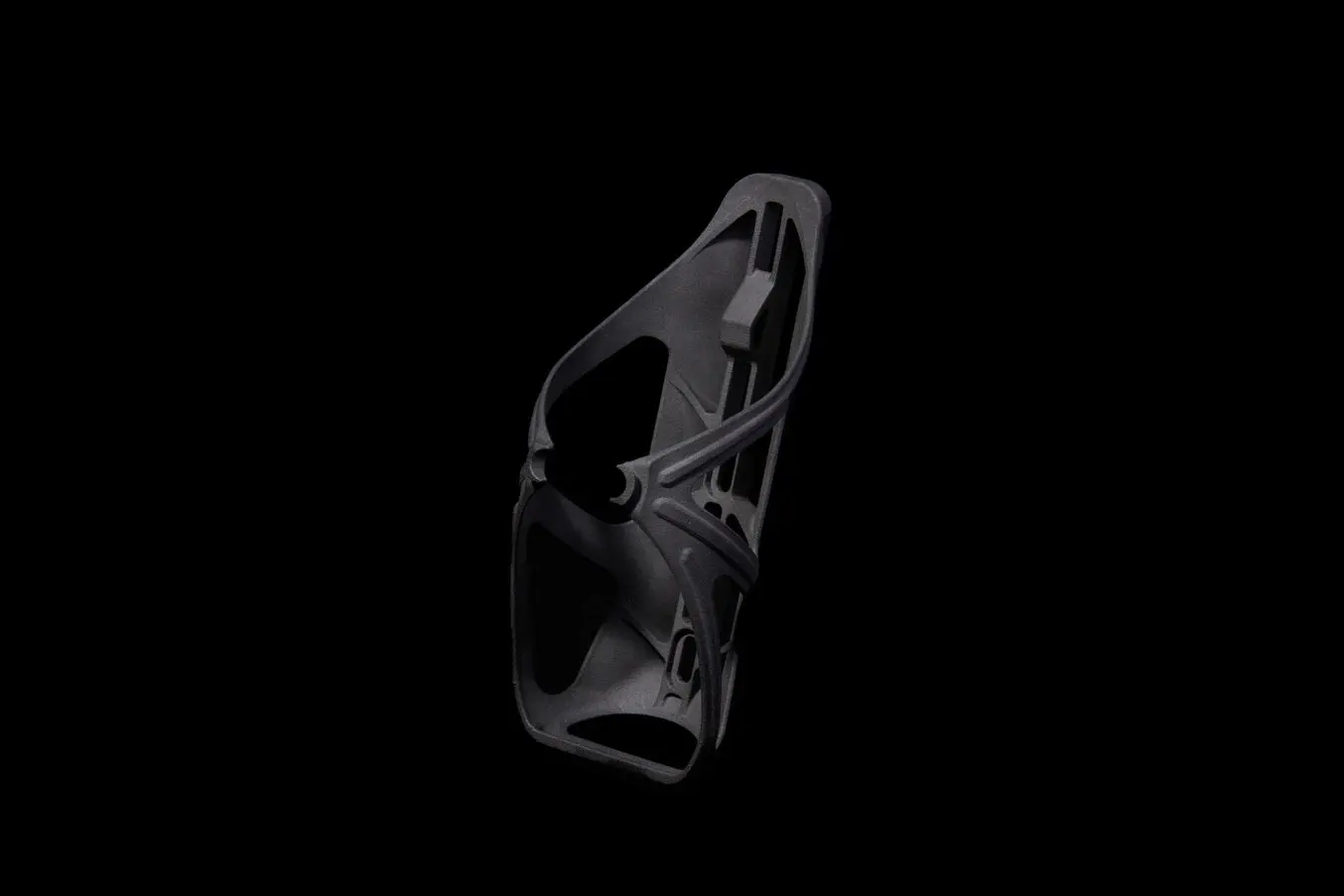
SLS方式は機能確認用試作の製作に最適で、少量生産や量産移行前のテスト生産としても射出成形に代わるコスト効率の高い方法となる。
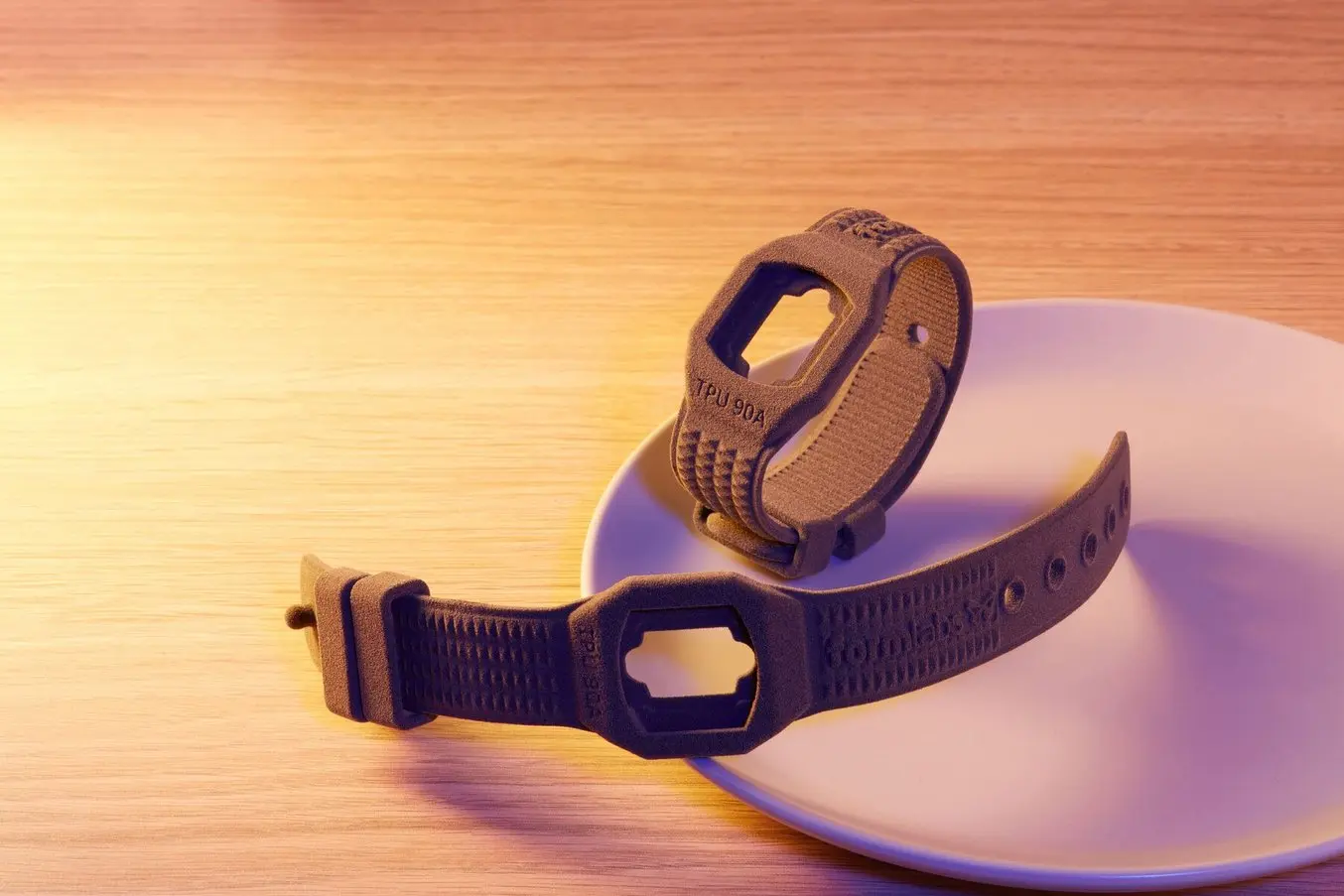
SLS 3Dプリントにより、柔軟材料を使った腕時計用ストラップなど実使用が想定される製品の製造も可能。写真のストラップはFuse 1+ 30W SLS 3DプリンタでTPU 90Aパウダーを使用してプリントしたもの。
SLSは、製造単価の安さ、高い生産性、定評のある材料により、機能試作の製造法として広く支持されています。また、少量生産や量産前のテスト生産を行う際に、射出生成に代わるコスト効率の高い方法になります。近年、SLSの作業手順や価格帯がこれまでよりはるかにアクセスしやすい状態になったことで、より多くの企業がSLSを社内に導入し、サプライチェーンの強化や試作から生産までの作業手順の高速化を実現しています。
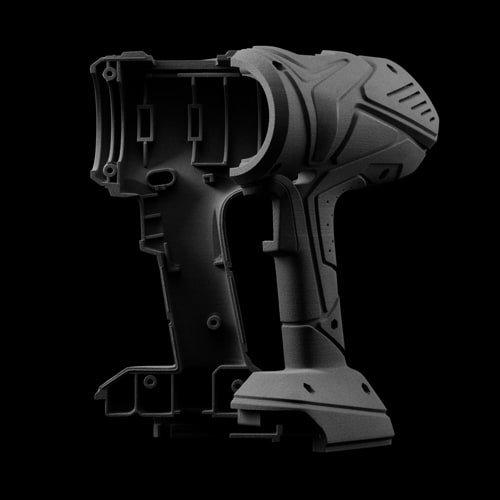
SLS(粉末焼結積層造形)方式3Dプリンタの概要
高強度・高機能な部品を製造できる3Dプリンタをお探しですか?本技術資料では、SLS方式プリンタの仕組み、そして機能確認用試作や実製品用部品の量産に広く用いられている理由を紹介しています。ダウンロードしてご覧ください。
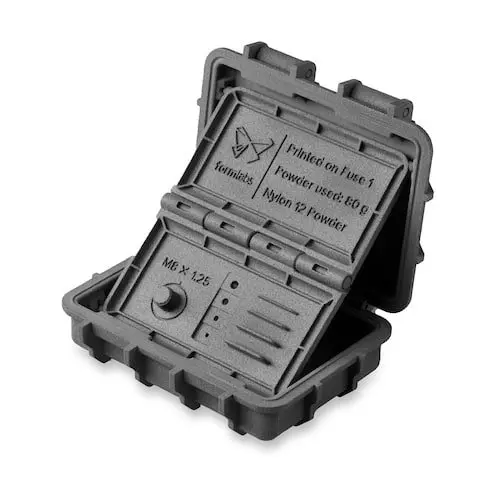
FDM vs. SLA光造形 vs SLS:フィラメント、レジン、パウダーベースの3Dプリンタ比較
3Dプリントに投資している企業の多くは、複数の種類の3Dプリント技術を活用しています。それぞれに長所と短所があるため、各方式を状況に応じてうまく使い分けられるようにすることが、最も完成度の高い作業手順と言えます。
独自のニーズに合わせて複数ある3Dプリント方式の中から1種類だけを選択したい場合は、いくつかの要素を考慮する必要があります。以下の表に、FDM方式、SLA光造形方式、SLS方式の3Dプリンタを選択する際に考慮すべき主なポイントをまとめました。
FDM(熱溶解積層)方式 | SLA光造形方式 | SLS(粉末焼結積層造形)方式 | |
---|---|---|---|
精細度 | ★★☆☆☆ | ★★★★★ | ★★★★☆ |
精度 | ★★★★☆ | ★★★★★ | ★★★★★ |
表面品質 | ★★☆☆☆ | ★★★★★ | ★★★★☆ |
スループット | ★★★☆☆ | ★★★★☆ | ★★★★★ |
複雑な形状 | ★★★☆☆ | ★★★★☆ | ★★★★★ |
使いやすさ | ★★★★★ | ★★★★★ | ★★★★☆ |
長所 | 低コストな消費者向け機器と材料 シンプルな小型部品を高速かつ簡単に造形 | 価格に対して品質が高い 高精度 滑らかな表面仕上がり 造形スピードが速い 幅広い機能的用途 | 高強度の機能部品 自由度の高いデザイン サポート材不要 |
短所 | 精度が低い ディテール表現が困難 デザインの自由度が低い | 材料によっては長時間の紫外線照射への耐性が低い | やや粗めの表面品質 使用可能な材料が限定的 |
代表的な用途 | コンセプトモデル ラピッドプロトタイピング 機能確認用試作 治具 | コンセプトモデル ラピッドプロトタイピング 機能確認用試作 ラピッドツール 治具 少量生産、量産前のテスト生産、カスタム生産 歯科モデル・器具 医療モデル・器具 ジュエリーの試作・鋳造 模型・小道具 | ラピッドプロトタイピング 機能確認用試作 少量生産、量産前のテスト生産、カスタム生産 耐久性の高い治具 医療器具、人工装具、矯正器具 |
造形サイズ | 最大300 x 300 x 600mm(デスクトップやベンチトップ型3Dプリンタ) | 最大353 x 196 x 350 mm(デスクトップやベンチトップ型3Dプリンタ) | 最大165 x 165 x 300mm(ベンチトップ型工業用3Dプリンタ) |
材料 | ABSやPLAなどの標準的な熱可塑性材料とそのブレンド材。 | 豊富なレジン材料(熱硬化性プラスチック)。スタンダード系、エンジニアリング系 (ABS、PPやシリコンのような高弾力性、耐熱性、ガラス充填材料) 、鋳造可能な種類、歯科や医療系 (生体適合性)純シリコン、セラミック。 | エンジニアリング系熱可塑性材料。Nylon 12、Nylon 11、ガラスまたは炭素繊維強化ナイロン複合材料、PP、TPU。 |
トレーニング | 造形設定、プリンタの操作、仕上げに関しては簡単なトレーニングが、メンテナンスには中程度のトレーニングが必要。 | プラグ&プレイ設定、メンテナンス、機械の操作、仕上げに関する基礎トレーニング。 | 設定、メンテナンス、機械の操作、仕上げに関する簡易トレーニング。 |
設備要件 | デスクトップ型プリンタには空調完備、できれば専用換気装置のある環境が望ましい | デスクトップ、ベンチトップサイズのプリンタはオフィス環境に最適。 | ベンチトップ型プリンタには十分なスペースのある作業場が必要。 |
補助設備 | 可溶性サポート材の除去装置(自動化が可能)、仕上げ用ツール。 | 洗浄・二次硬化装置(自動化が可能)、仕上げ用ツール。 | パウダー処理および造形品の粉末除去用の後処理装置。 |
設備費 | ローエンドのプリンタや3Dプリンタキットの場合、$200程度から購入可能。業務用デスクトップサイズFDMプリンタは$2,000~$8,000、産業用機の場合は$15,000から。 | 格安光造形3Dプリンタの場合は$200〜$1000。工業品質SLA光造形3Dプリンタの場合は$2,500〜$10,000の範囲、大型の光造形3Dプリンタは$5,000〜$25,000。 | ベンチトップサイズの産業用SLS 3Dプリンタは、本体価格が$30,000弱から、パウダー処理装置や粉末除去装置を含むエコシステム一式の場合は$60,000から。従来の産業用SLSプリンタは$200,000から。 |
材料コスト | 最も一般的なフィラメントは$50〜$150/kg、サポート材またはエンジニアリング系フィラメントの場合は$100〜$200/kg程度。 | スタンダードレジン、エンジニアリングレジンの場合は$100-$200/L、生体適合材料の場合は$200-$500/L。 | ナイロンの場合は$100/kg。SLS方式は専用のサポート材が不要で、プリントで使用しなかった未焼結パウダーは次のプリントで再利用可能なため、材料コストを抑えることができる。 |
必要な作業 | 手動でのサポート材の取り外し(可溶性サポートが使用可能な工業用プリンタの場合はほぼ自動化が可能)。品質を高めるための後処理に時間がかかる。 | 洗浄と二次硬化(どちらの工程もほぼ自動化が可能)。サポート痕を消すための簡単な後処理作業。 | シンプルで半自動化された作業手順で造形品からの粉末除去・回収が可能。 |
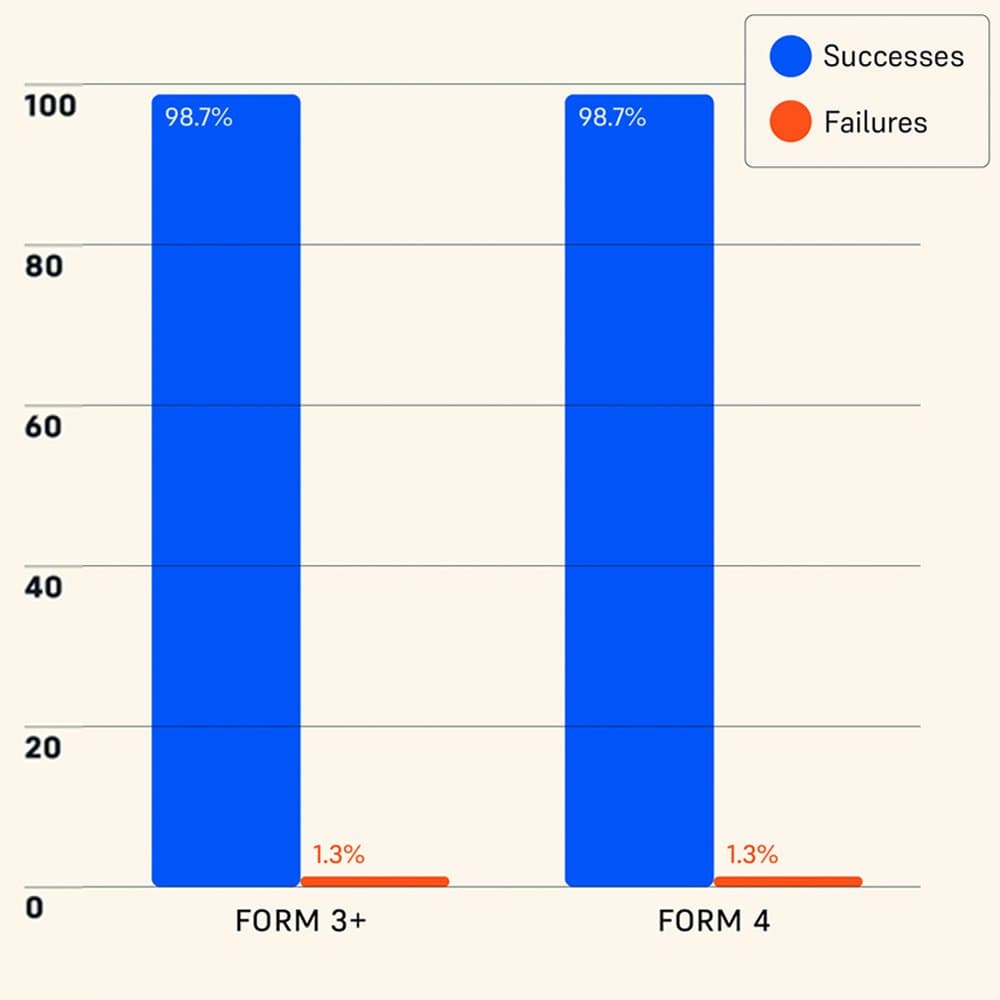
Form 4と他社製光造形3Dプリンタの信頼性に関する第三者試験
独立試験機関により、Form 4 のプリント成功率は 98.7 % と評価されました。テスト方法と結果の詳細についてはこちらの技術資料でご確認いただけます。
精細度
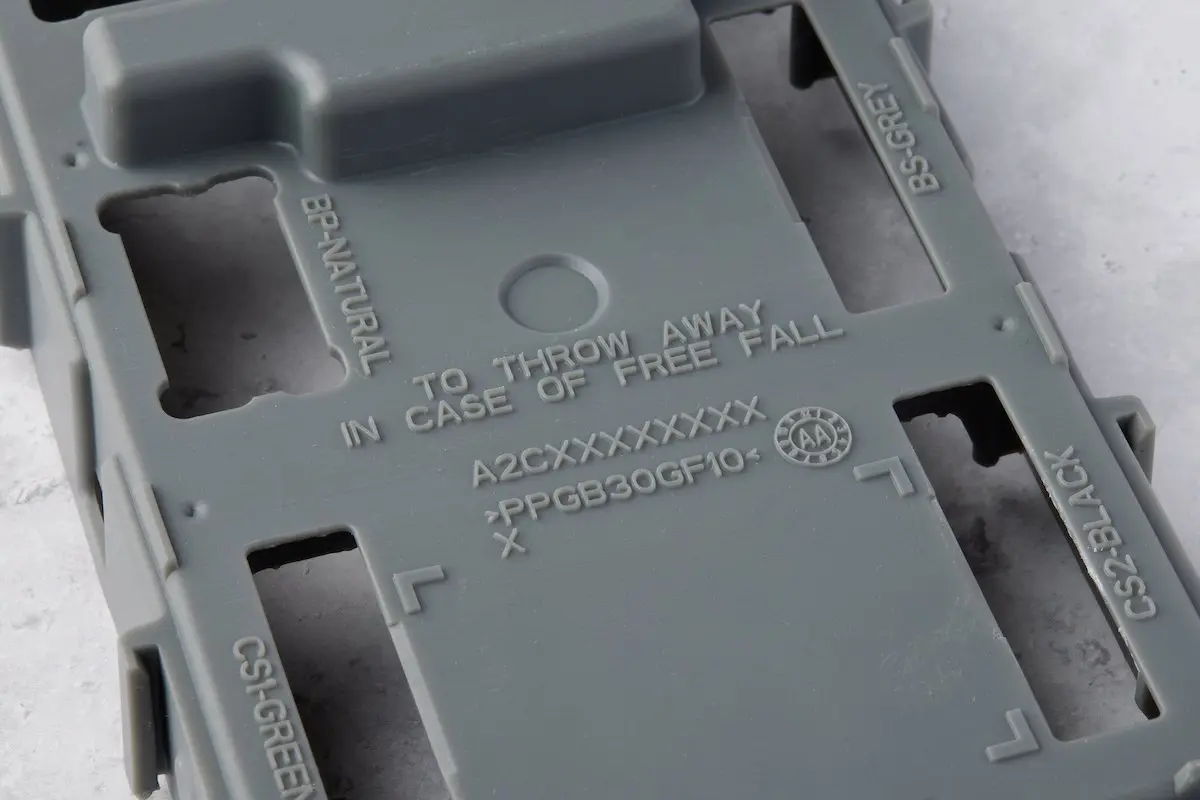
写真はFormlabs Form 4で造形したエンクロージャ。SLA光造形品はシャープなエッジ、滑らかな表面、ほとんど目立たない積層痕が特徴。
解像度という言葉は仕様として誤解を招きやすい表現で、その測定方法はメーカーや3Dプリント工程によって異なることがほとんどです。通常、解像度というのは表現できる最小フィーチャーを指し、ディテールをどれだけ繊細に表現できるか、または3Dプリンタで再現可能な繊細な表面テクスチャを意味することが多く、表現可能な最小サイズなどのメトリクスで計測されることが一般的です。3つの異なる3Dプリント方式(FDM方式、SLA光造形方式、SLS方式)の仕組みが、造形品の解像度(高精細さ)に大きな影響を与えます。
FDM 3Dプリンタは、溶かしたプラスチックをノズルから押し出して指定の形状になるよう層を形成し、徐々に上に重ねていくことで造形します。そのためFDM方式による造形品の解像度は、ノズルのサイズ、材料が持っている材料特性、およびモーターがノズルをXY軸と層間のZ軸で移動させる制御方法に依存します。FDM 3Dプリンタは通常、壁の厚みが約0.8mm程度で、エンボス加工やデボス加工が目に見える状態にするためには幅を約0.6mm、高さを約2mmにする必要があります。
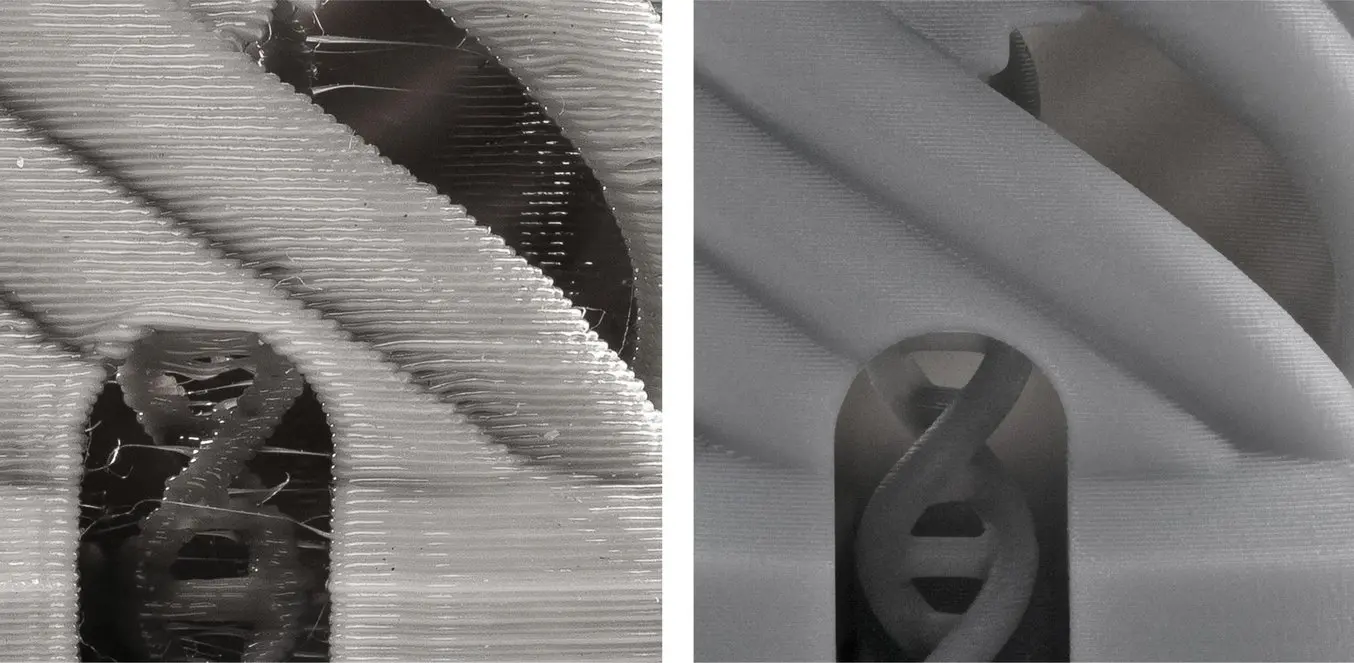
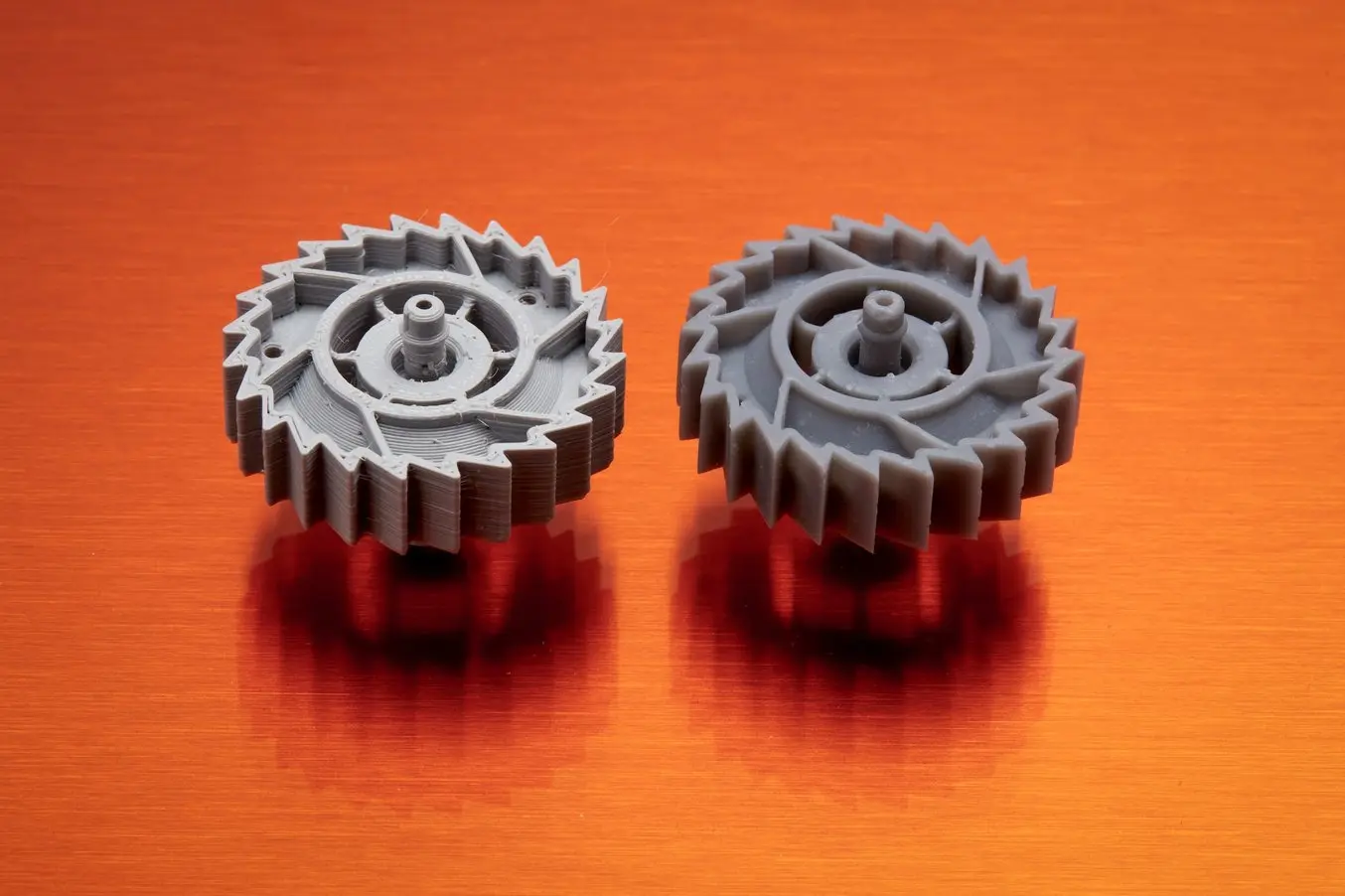
FDMプリンタ(左)では、SLA光造形プリンタ(右)に比べて複雑な形状やディテールの凝った形状は再現が難しい。
SLA光造形3Dプリンタは、光源(レーザー、デジタル投光器、LED)を照射して液体レジンを1層ずつ硬化させることで造形します。SLA光造形3Dプリンタの解像度は、使用する光源の種類や、レジンの光散乱特性、ブリードアウト、重合特性によって異なりますが、一般的にはXY平面でモデルを正確にトレースする能力とZ軸で実現できる最小積層ピッチの組み合わせと考えることができます。
使用する光源には様々な種類があることを考慮しても、FDM方式やSLS方式3Dプリントと比較すると、SLA光造形は最も解像度の高い方式です。光源がレーザーであれデジタル投光器であれ、マスキングLCDスクリーンで光を制御するLEDであれ、液体レジンに非常に高精度で光を照射できるためです。SLA光造形方式で3Dプリントした造形品は、ディテールの細かさ、繊細なテクスチャでも完全に滑らかなテクスチャでも表現できる表面品質、そして寸法精度の高さによって優れた解像度を実現します。Formlabs Form 4などの工業品質のSLA光造形3Dプリンタは、薄肉構造であれば僅か0.2mmという薄さを実現し、それぞれ0.1mmと0.15mmという非常に繊細なエンボス加工やデボス加工を施すことができます。
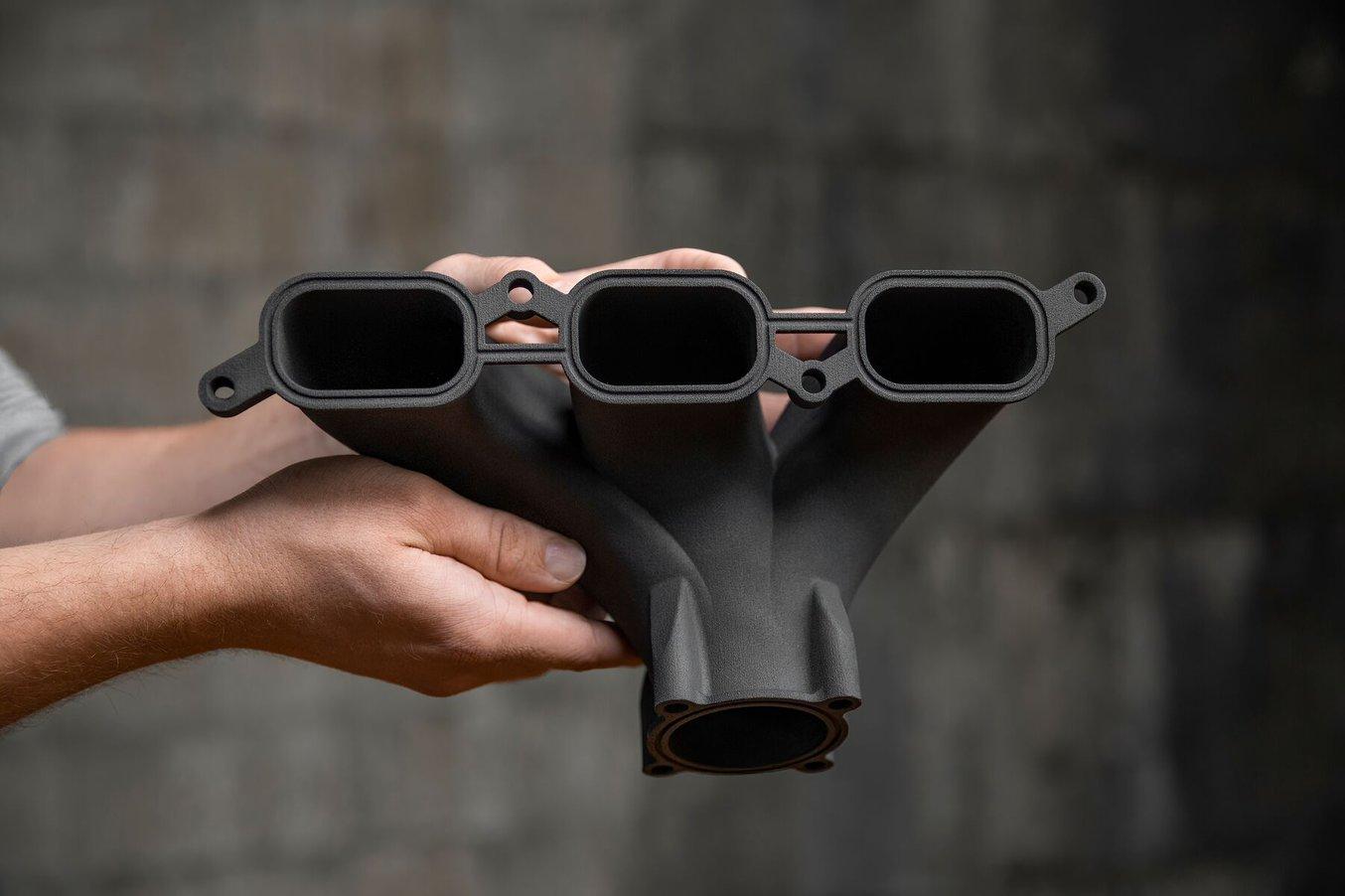
Fuse 1+ 30Wのような工業用品質のSLS 3Dプリンタも解像度に優れ、高強度で有機的な曲線や凹凸形状も正確に表現した高度なディテールの造形品を製作できる。
SLS 3Dプリンタは、高出力レーザーでポリマー粒子を焼結することで造形します。SLSの解像度は、ガルバノメーターでレーザーをどの程度精密に制御できるかによって変わります。レーザーの品質、ソフトウェア、ファームウェア、レーザーアセンブリ全体の較正なども要因の一つです。SLSでの造形中は未焼結パウダーが造形品を支えるため、細かなフィーチャーのある高度に繊細な形状でもサポート材によって犠牲にすることなく造形できます。FUse 1+ 30Wは横方向であれば0.3mm、縦方向であれば0.6mmの壁の厚みに対応できます。エンボス加工やデボス加工によるディテールを追加する場合は、ビルドチャンバー内のレイアウトによって深さおよび幅を0.1〜0.4mm以上にする必要があります。
設計ルールの比較
FDM(熱溶解積層)方式 | SLA光造形方式 | SLS(粉末焼結積層造形)方式 | |
---|---|---|---|
サポート付きの壁の最小厚み | 0.8mm | 0.2mm | 0.3mm(横方向の壁) 0.6mm(縦方向の壁) |
サポート無しの壁の最小厚み | 0.8mm | 0.2mm | 0.3mm(横方向の壁) 0.6mm(縦方向の壁) |
垂直ワイヤの最小直径 | 3mm | 0.3mm(高さ7mm) 0.6mm(高さ30mm) | 0.8mm |
表現可能な最小エンボス加工 | 0.6mm(幅) 2mm(高さ) | 0.1mm | 0.15mm(奥行き、横方向の面) 0.35mm(幅、横方向の面) 0.35mm(奥行き、縦方向の面) 0.4mm(幅、縦方向の面) |
表現可能な最小デボス加工 | 0.6mm(幅) 2mm(高さ) | 0.15mm | 0.1mm(奥行き、横方向の面) 0.3mm(幅、横方向の面) 0.15mm(奥行き、縦方向の面) 0.35mm(幅、縦方向の面) |
設計ルールはプリンタの機種によって異なる場合があります。この表に記載の値は、FDM方式はProtolabs / Hubsを、SLA光造形方式はForm 4を、SLS方式はFuseシリーズの設計ルールをもとに概算したものです。
3つの造形方式のうち解像度が最も高いのはSLA光造形で、それに僅差で続くのがSLS方式です。FDM 3Dプリンタは通常、平面からテクスチャを正確に描き出したり細かなフィーチャーを明確に定義するのに苦労する一方、SLA光造形とSLSはどちらも元のCAD設計に組み込まれている微細なディテールを再現できます。
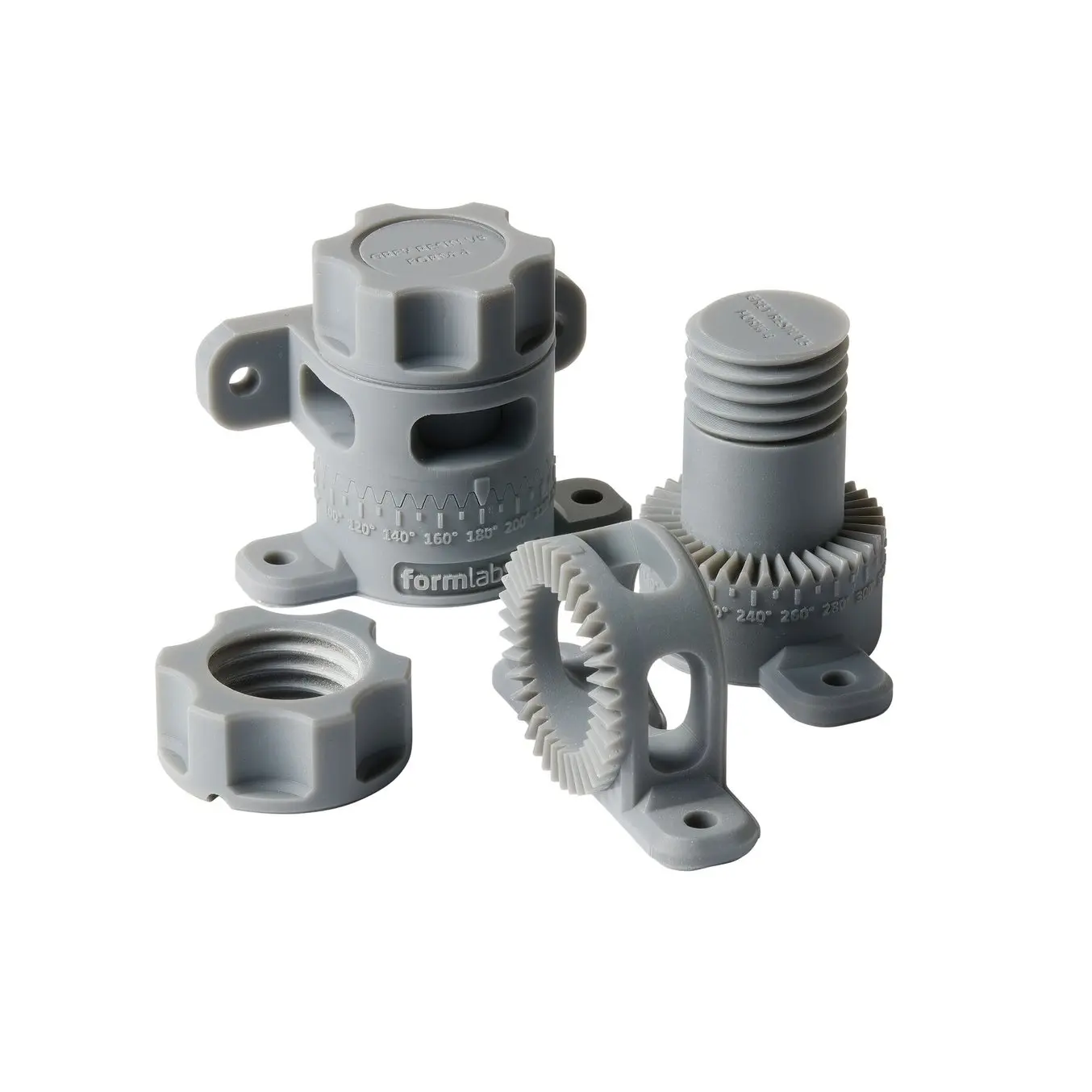
Form 4シリーズデザインガイド
3Dプリントの成功の秘訣は、モデルを適切に設計することにあります。以下にベストプラクティスをご紹介します。設計の最適化やプリント失敗を最小限に抑えるヒントとしてお役立てください。
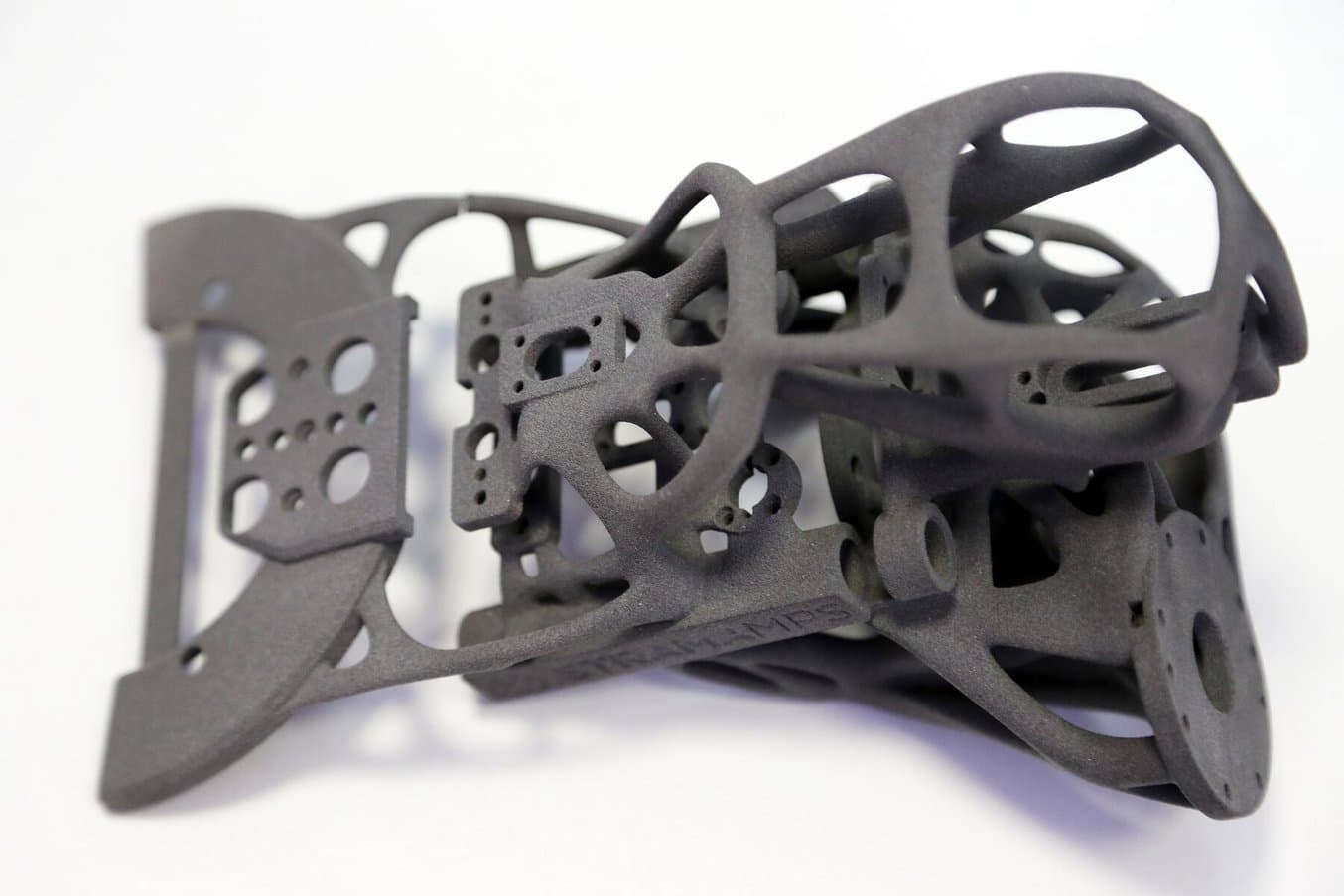
Fuseシリーズデザインガイド
本デザインガイドでは、Fuseシリーズを使ってSLS方式の3Dプリントをする際に考慮すべき重要なポイントをご紹介するとともに、このポイントを実際に活用してプリントを成功させる方法を解説しています。
寸法精度と高精細さ
造形品の各断面が3Dファイルで意図した形状をどれだけ忠実に再現できているかを意味する精度、そしてその精度が造形品全体でどの程度一貫して再現できているかを意味する高精細さは、3Dプリント方式の種類やメーカーによって異なります
FDM方式の3Dプリンタの場合、精度は押出工程の一貫性と再現性、およびフィラメントが溶けて押し出される際の特性に左右されます。押出工程では、レイヤー内およびレイヤー間でばらつきが出ることがあります。この原因となるのは、ノズルがスムーズに移動しない、フィラメントの直径が一定でない、押出温度にばらつきがある、材料が同じ速度と量で積層されない、などがあります。
全体的な精度を見ると、半硬化した層が「つぶれ」を起こすことでさらに差異が発生する可能性があります。また、押出工程で使用する熱が造形品の反りや歪みを引き起こす原因になることがありますが、この温度を安定させてより制御しやすい状態を作るために加熱ベッドや密閉ビルドチャンバーを使用するメーカーもあります。
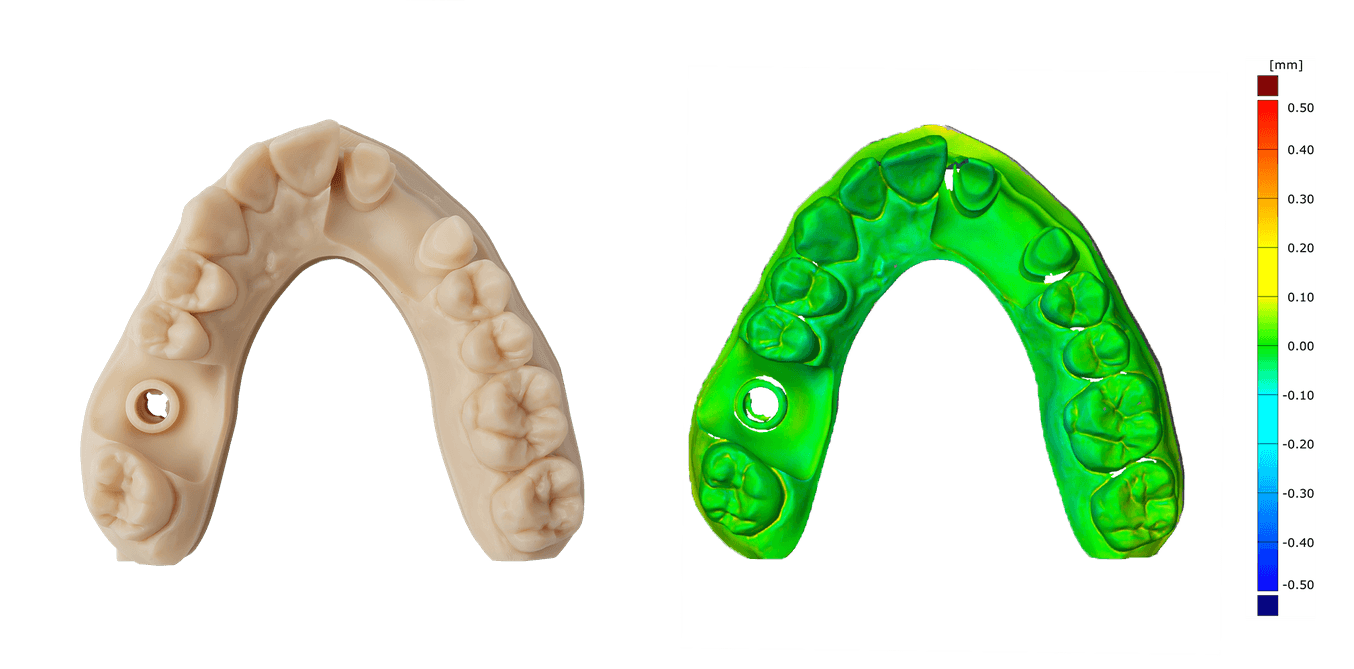
精度は、3Dプリント品を3Dスキャンし元のモデルと比較することで測定できる。さらに、サンプルパーツや独自デザインのカスタムサンプルパーツを依頼し、元の設計と付き合わせてフィット感や寸法を確認することも可能。写真の歯科用モデルはForm 4B MSLAプリンタで造形したもの。テストの結果、造形品の表面積の99%以上で設計パラメータとの誤差が100μm以内に収まっていることを確認。
SLA光造形方式の精度は、プリンタの光学性能や造形中に造形品にかかる応力、プリンタ内部の液体レジンの特性に依存します。光源や光学ユニットによってどの程度の精度で断層面を硬化できるかが変わりますが、それでも全体的なパフォーマンスとしてFDM方式の精度を上回ります。
さらに、1層が完成するごとにビルドプラットフォームが光源から離れるように持ち上がりますが、造形済みの層が引き剥がされる時に大きな応力が加わり、僅かな歪みが生じます。工業品質の光造形プリンタは、これらの負荷を緩和するために様々な措置を講じています。例えば、FormlabsのForm 4ではレジンタンクの底に搭載されている2層の柔らかいフィルムで剥離力を軽減する他、リリーステクスチャと呼ばれる独自のマイクロテクスチャ光学フィルムでレジンタンクとLCDの間に空気の通り道を作ることでフィルムの吸着を防ぎ、さらに高い精度を実現します。
光造形3Dプリンタの精度に影響を与える3つ目の要素は、材料特性です。液体レジンの硬化は、レジンの温度や均質性、散乱性、粘度など、多くの変数に左右されます。これら変数がわずかでも変化すると、硬化すべきレジンの量に増減が発生し、硬化済みの層のサイズや形状に最大で数百ミクロンのズレが生じる可能性があります。ほとんどの光造形3Dプリンタではこれらの変数を制御していないため、寸法精度が予想外に変化してしまうことがよくあります。
FormlabsのForm 4では、正確なヒーター、赤外線温度センサー、高速レジンミキサーを使用し、液体レジンの温度と均質性を正確に制御することでこの問題に対処しています。また、Formlabs独自の材料を開発・製造することで、全材料の反応性、粘度、散乱性といった特性を厳密に制御しています。
実現可能な寸法精度を測定するため、箇所によってフィーチャーのサイズが様々に異なるモデルを、3種類の3DプリンタでGreyレジンV5を使って積層ピッチ100µmで造形し、その後室温で5分間二次硬化しました。それぞれのモデルで測定された精度は以下の通りです。
- 1〜30mm:±0.15%(最小:±0.02mm)
- 31〜80mm:±0.2%(最小:±0.06mm)
- 81〜150mm:±0.3%(最小:±0.15mm)
SLS 3Dプリンタはレーザーやガルバノメータにより精密な制御が可能なため、一般的に精度が非常に高くなります。SLS 3Dプリンタの精度は、レーザーの光学性能、パウダー設定に合わせて造形設定がどの程度うまく調整されているか、造形環境がどの程度制御されているかによって決まります。SLS方式で高精度な部品を作るためには、一貫性が非常に高く精密に調整された温度での造形が必要です。サードパーティ製の材料で使用するオープン設定の場合、反りなどの造形不良だけでなく造形品の品質・性能低下の可能性が高まります。
一般的に、3Dプリント方式の中で最も正確かつ精密な造形ができるのは光造形およびSLS 3Dプリンタです。標準的な
CNC加工の公差+/-0.3mmと比較しても、FormlabsのForm 4 SLA光造形プリンタとFuseシリーズ SLSプリンタは同等の性能を発揮することがわかっています。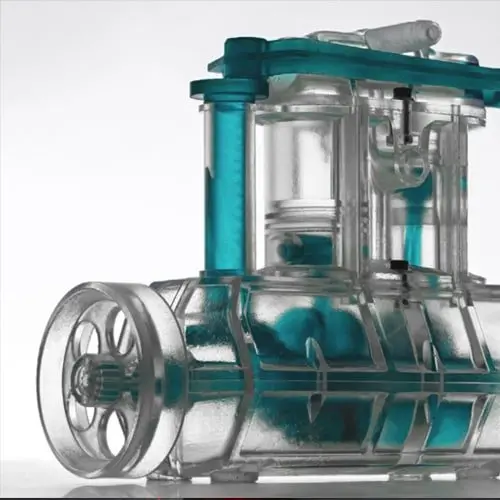
機能的な3Dプリントアセンブリの設計を最適化
公差とフィット感は、エンジニアが機械アセンブリの機能や生産コストを最適化するために不可欠な要素です。こちらの技術資料を、3Dプリント製の機能アセンブリを設計する際のリソースとして、あるいは造形した部品同士を接続するはめ合い部分の設計の足がかりとしてお役立てください。
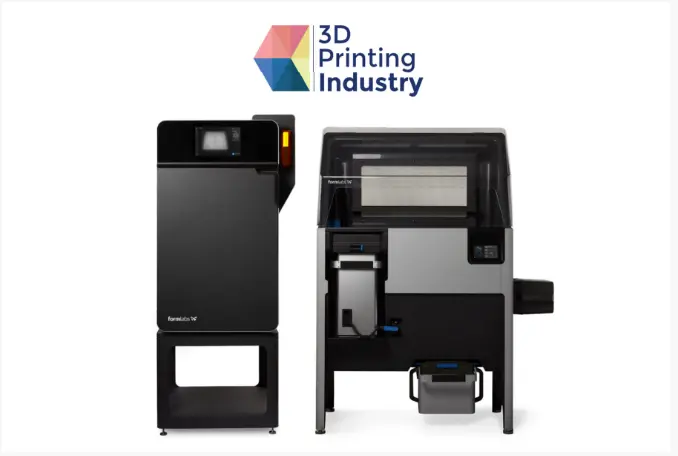
3D Printing IndustryによるFomlabs Fuse 1とFuse Siftの徹底レビュー
本技術資料では、3Dプリント関連メディア3D Printing IndustryのエンジニアによるFormlabsのSLS方式3Dプリンタの徹底レビューと精度試験の結果をご覧いただけます。
等方性と水密性
等方性と水密性は、3Dプリントの中でもよく話題に上る要素です。3Dプリントでは一度に一層ずつ積層して造形するため、造形品質は造形中の向きによって強度にばらつきが生じ、X、Y、Z軸で特性が異なる場合があります。
FDMの造形品は、その造形プロセスにより異方性が生じてしまうことが知られています。こうした異方性を解決するためには、異方性が許容できる用途にだけFDM方式を用いるか、造形品の形状でこの欠点をカバーできるよう設計面で調整を行う必要があります。
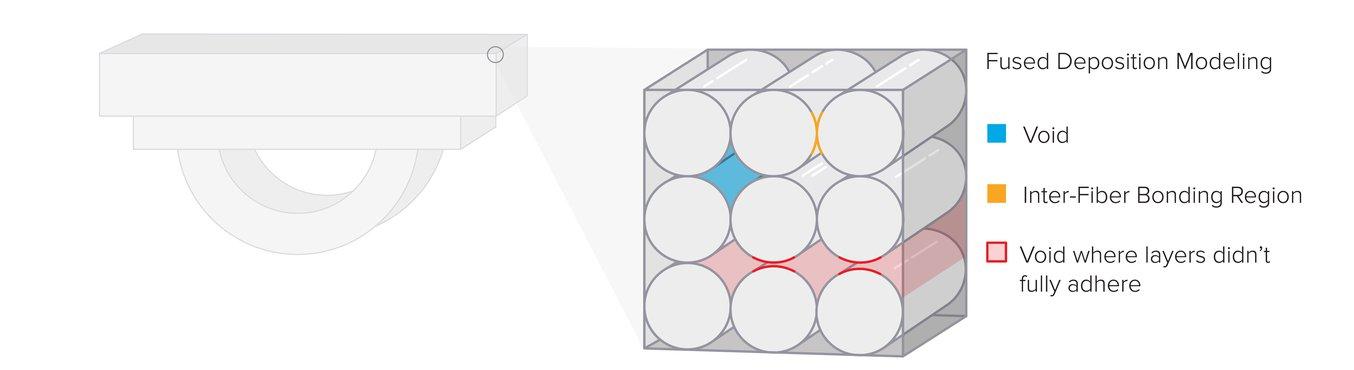
FDM 3Dプリンタは、溶かした熱可塑性プラスチックを重ね合わせることで造形。この工程では上下に重ねられた層同士がライン(フィラメントの射出)ほど強く結合しておらず、丸みを帯びたラインの間に空洞ができ、層同士が完全に固着しない可能性がある。
一方で、SLA光造形方式では優れた等方性を備えた造形品を製作できます。造形品に等方性を持たせるためには、造形プロセスと材料科学を統合することで、多くの要素を緻密に制御する必要があります。造形中は、レジンの成分は共有結合状態となるものの上下の層同士はグリーン状態のままとなります。
グリーン状態の間、レジンは光重合性化合物を維持するため上下の層同士が結合可能な状態となり、最終的にレジンを硬化する時に等方性と水密性が加わります。分子レベルでは、X、Y、Z面の違いはありません。治具や実製品用部品、機能確認用試作など、意図した通りに機能することが求められる部品の製作が可能です。
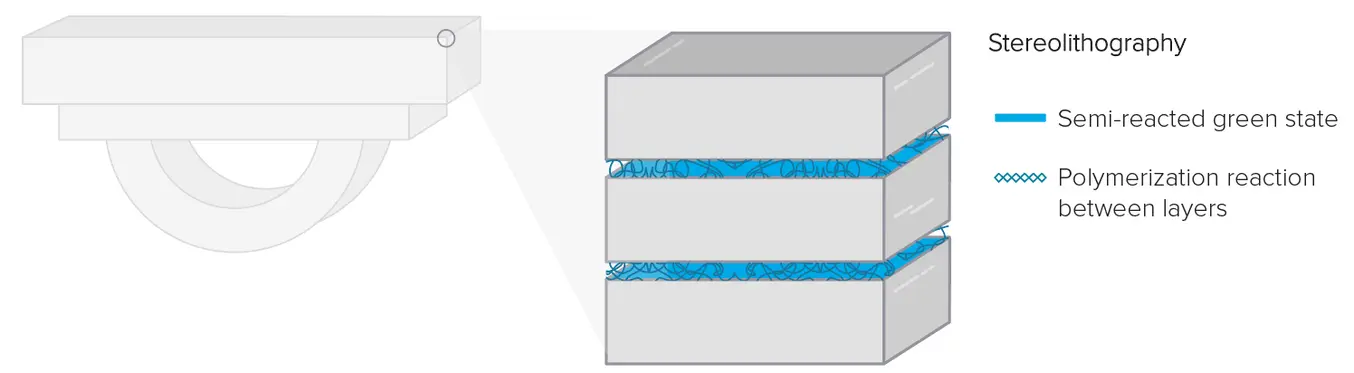
SLA光造形ではZ軸とXY面で化学的な結合状態に差異がなく、光造形プリンタによる単一の造形品は一つの連続した高分子網目となる。
SLS 3Dプリンタでは、ほとんど等方的な造形品を製作できます。FDM 3Dプリントではフィラメントを溶かしてから押し出して前の層と接触させますが、SLS 3Dプリントでは周囲の材料とすでに接触している粒子を焼結するため、粒子は同じ平面または層に属する材料と融合し、さらに下の平面や層とも部分的に融合します。しかし、材料によって熱を保持する時間や半焼結状態を維持する時間が異なるため、SLSの等方性はパウダーの種類によって異なります。また、パウダーによって下の層と融合する時の速度や融合する程度も異なります。
等方性は表面の気孔率や粒子密度とも関連し、これらの特徴がすべて部品の水密性や防水性に影響します。水密性とは部品やアセンブリが液体の浸入や浸出を防ぐ能力を指し、防水性とは外面が水をはじく能力を指します。3Dプリント品の場合は、「水密性」が重要視されることがほとんどです。それは、水中に入れることのできる電子部品用エンクロージャなど、単に表面に接触する水をはじくだけでなく内部の部品を保護したいという目的で3Dプリント製の部品やアセンブリを製作することが多く、水密性の方が部品の機能を包括的に考えるのに適しているためです。
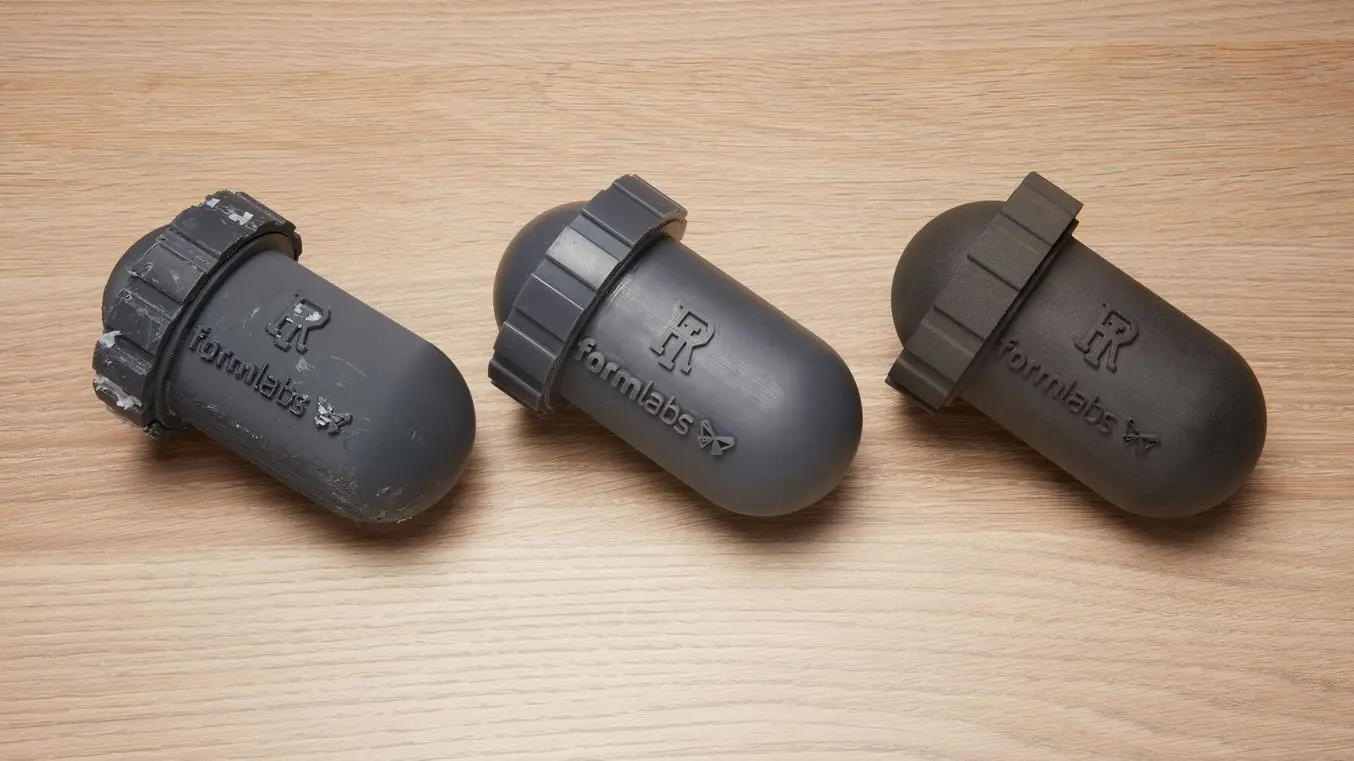
University of Rhode Island Underwater Robotics and Imaging Laboratory(URIL)が行った広範なテストでは、FDM方式(左)、SLA光造形方式(中央)、SLS方式(右)で製作した3Dプリント製エンクロージャを加圧チャンバー内に入れて検証した。
University of Rhode Island Underwater Robotics and Imaging Laboratory(URIL)が行った広範なテストでは、FDM方式で製作した3Dプリント製のロボティクスエンクロージャは数秒水に浸しただけで内部の機器が水で濡れてしまいました。SLA光造形方式による3Dプリント品は非常に高い加圧レベルでも水密性を維持することができ、SLS方式による3Dプリント品は中程度の加圧レベルまで内部の電子機器を水から守ることができました。ベーパースムージング施したSLSエンクロージャは、圧力が上昇しても水密性を維持することができました。
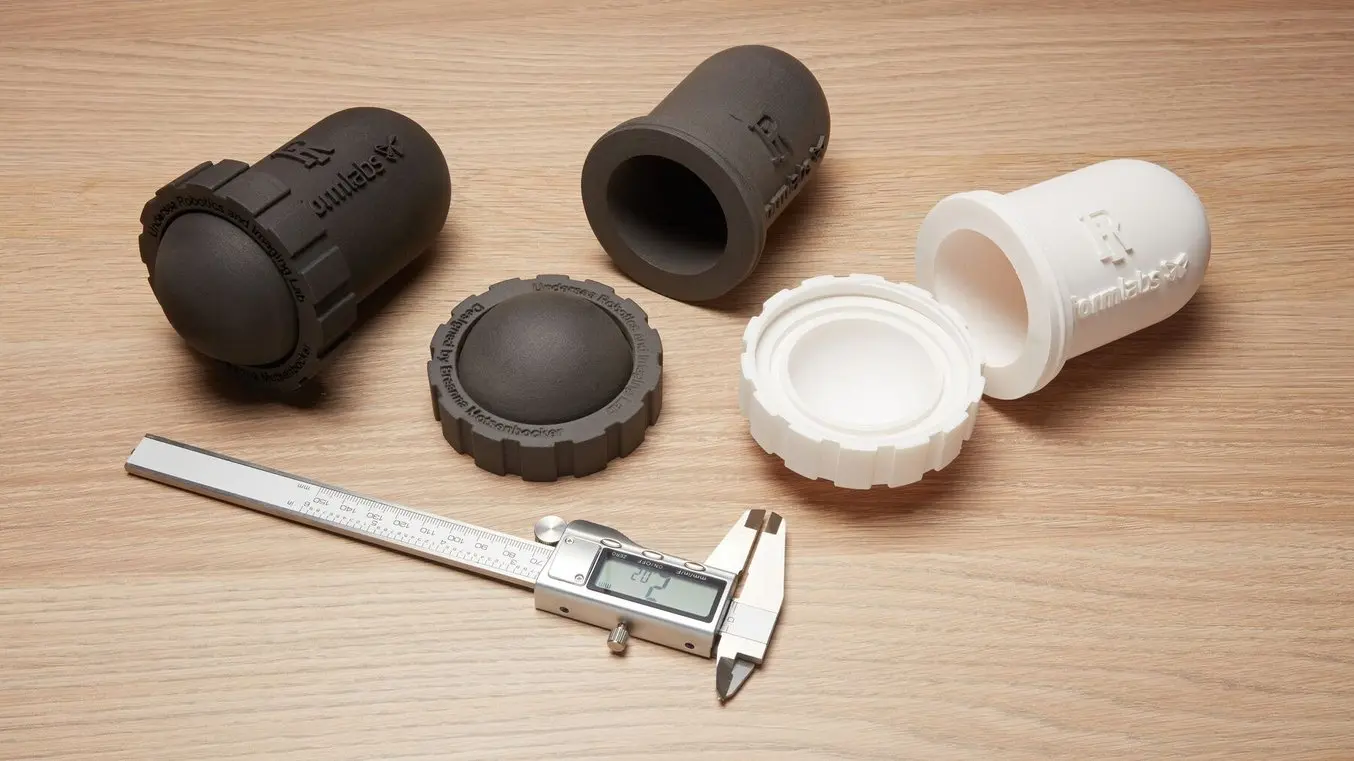
3Dプリント製水密エンクロージャの耐圧試験結果
本製品仕様では、検証結果の詳細と、手頃な価格で水密エンクロージャを3Dプリントでカスタム製作するガイドラインをご紹介します。
表面品質
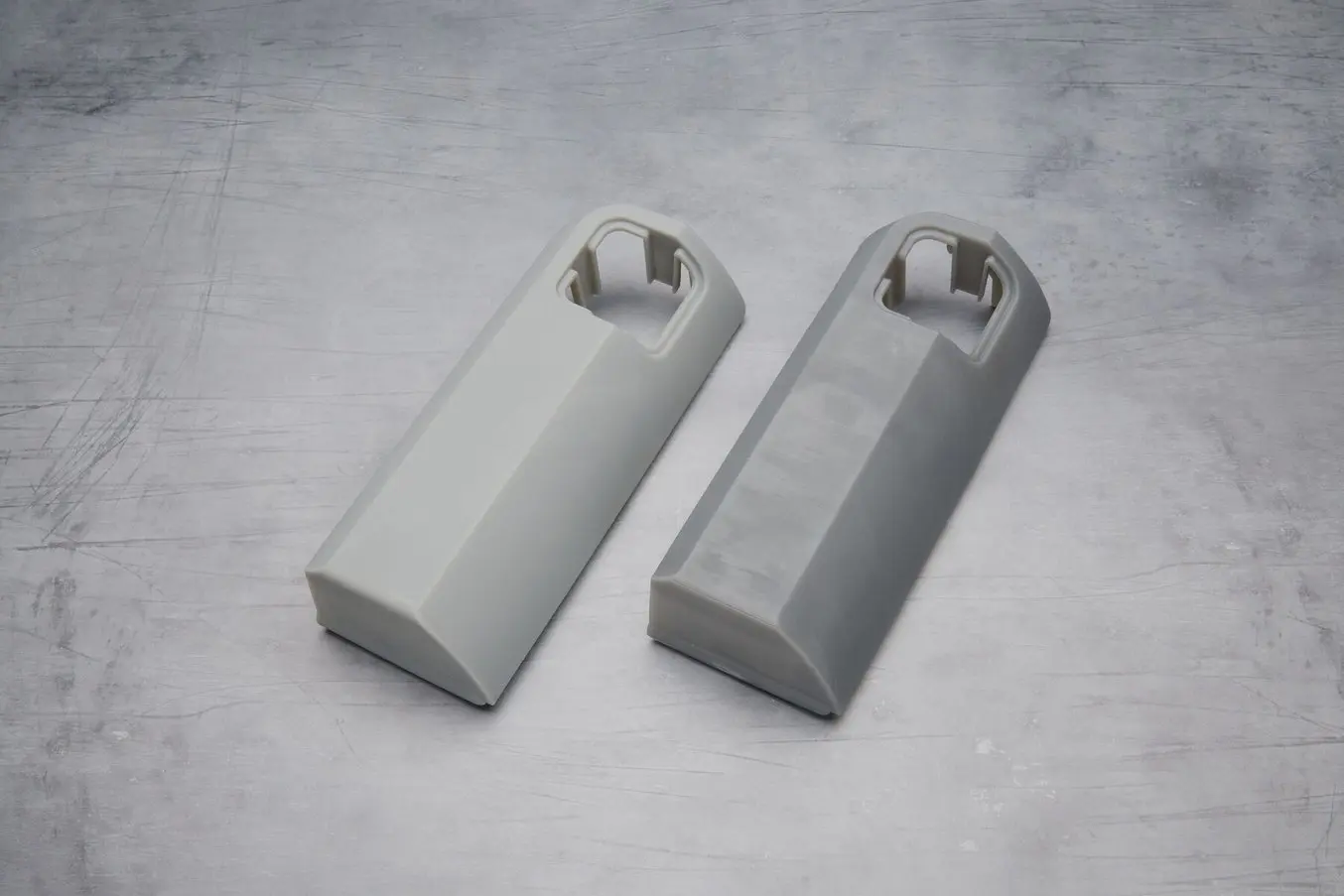
SLA光造形方式では、滑らかでマットな質感を備えた最高の表面品質を実現できる。表面品質は、3Dプリント業界全体、特にSLA光造形方式の技術の進歩に伴い向上されてきた。
FDM方式、SLA光造形方式、SLS方式の造形品で最も顕著な違いが出るのは、表面品質です。「ホットグルーガン」方式とも言われるFDM方式の場合、よく見るとレイヤーを一層ずつ重ねたことがわかる積層痕が目立ちます。このような場合はより徹底した後処理が必要となり、部品の全体的な製造時間として余分な作業が発生してしまいます。また、積層痕が残ることで、セミクリアな材料や半透明材料を使っても真に半透明の部品を作ることが難しくなってしまいます。たとえ微小な積層痕であってもそこで光の屈折が生じてしまい、完成品としての造形品の透明性が損なわれるためです。
一方、SLA光造形3Dプリンタでは、射出成形品とほとんど見分けがつかないほどの造形品を製作できます。その優れた表面品質により、表面品質や滑らかさが最も重視される消費者製品のカテゴリーでさえ、最終設計レビュー用の試作品や実製品用部品としても使用できるほどです。さらに積層痕が残らないため、ほぼ完全に透明な造形品の製作が可能です。透明な部品は、射出中の様子を目視で確認できる成形型としての用途や、透明なプラスチック製品の設計用途、マイクロ流体工学、医療用途などでも役立ちます。歯科用3Dプリントでは、Premium TeethレジンのようなSLA光造形用材料でエナメル質の滑らかな外観を再現できるため、本物の歯と見分けがつかない入れ歯を作ることができます。
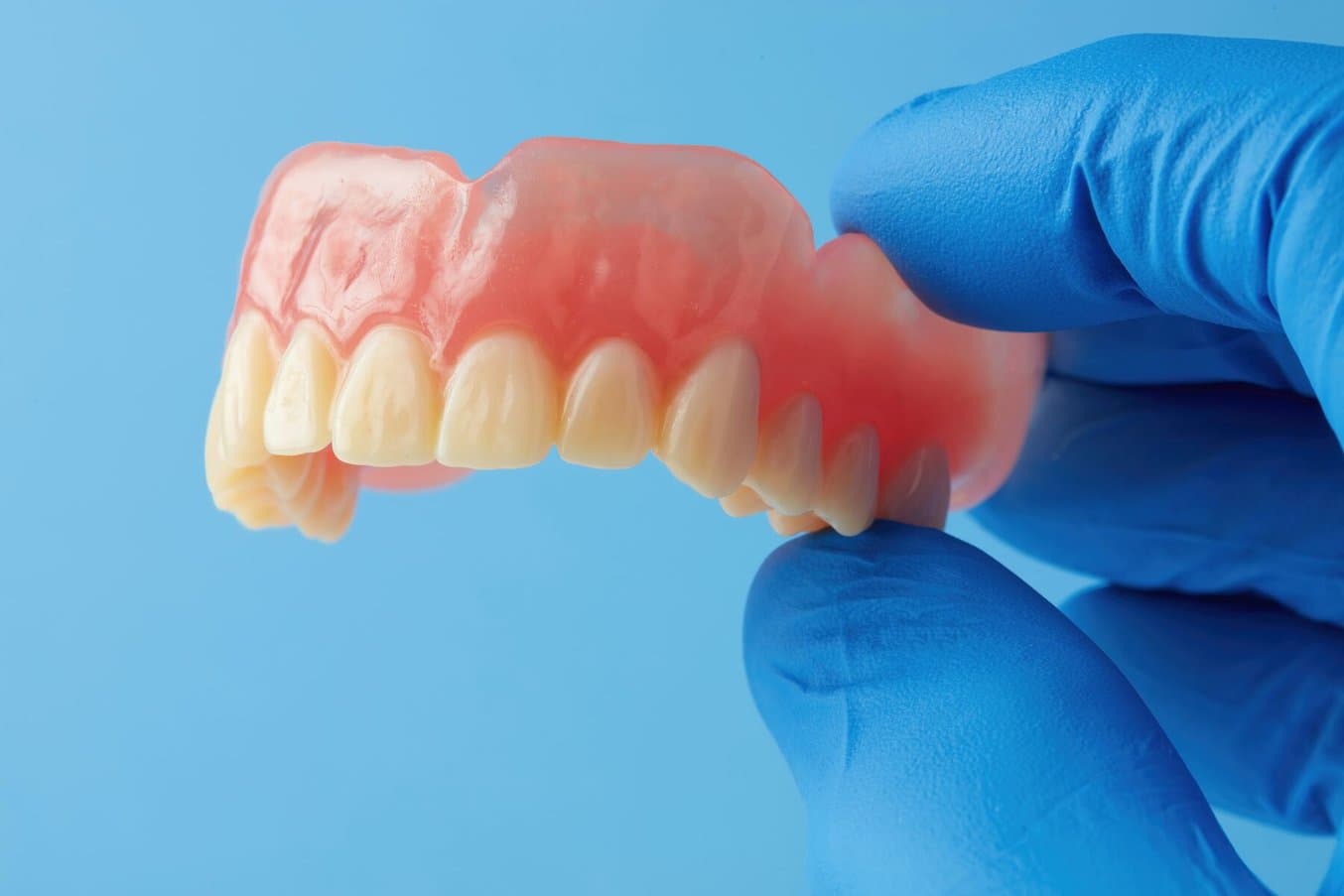
SLA光造形品は表面品質に優れ、写真のように本物の歯と見分けがつかない3Dプリント製義歯の製作が可能。
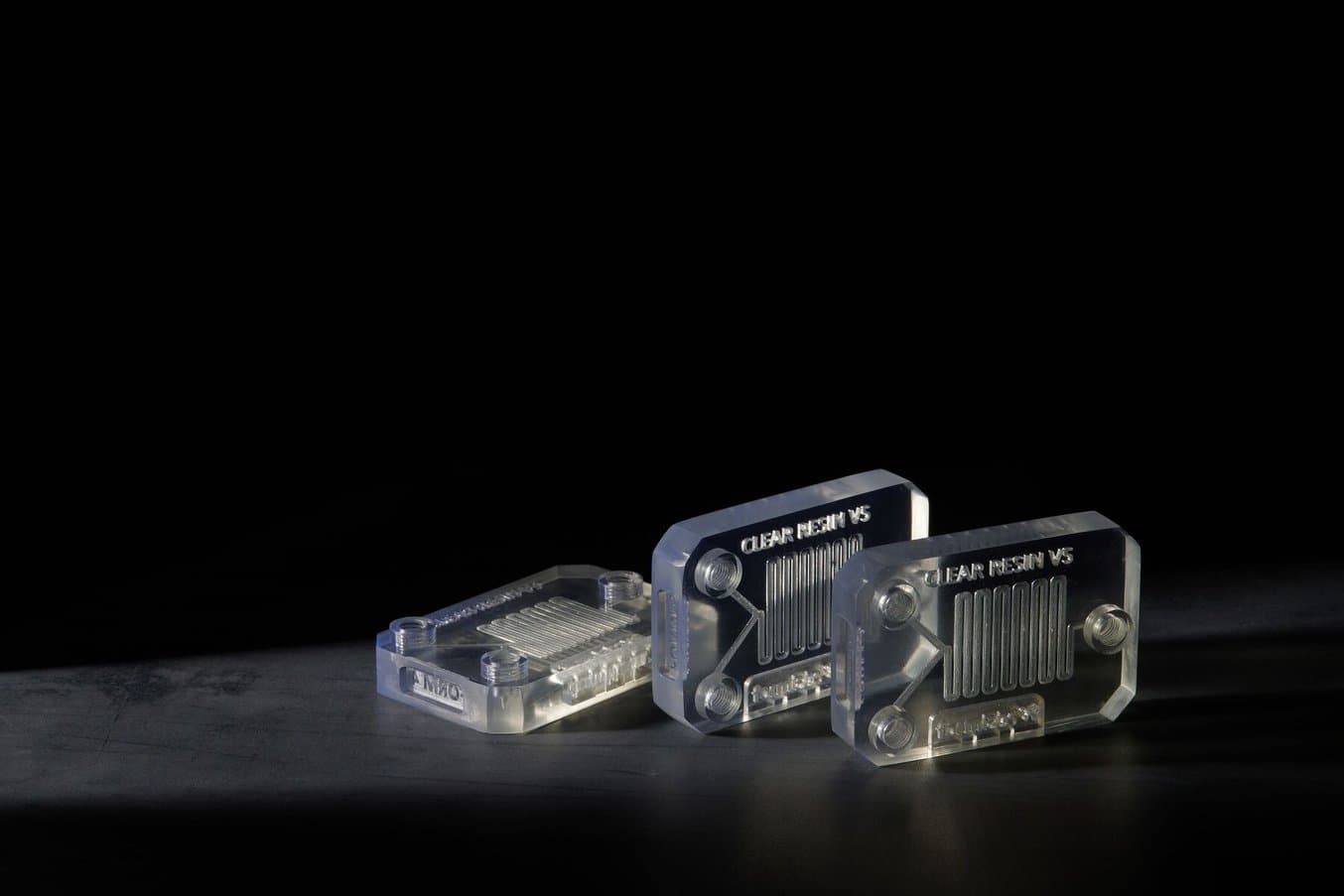
積層痕が残らないため、SLA光造形で作る透明なレジン部品はほぼ完璧な透明性を実現できる。
SLS方式の造形品は、やや粗くざらついた質感の表面品質が特徴です。しかし、SLSプリント品は造形時にサポート材が不要なため、造形品全体で均一な表面品質を実現することができます。SLA光造形やFDMの造形品の場合、サポート痕を除去するために後処理が必要なことを考えると、後処理の作業が削減されます。さらに、SLS 3Dプリント品にベーパースムージングやブラスト処理、研磨を施すことで、光造形品のように光沢のある滑らかな表面を実現できます。
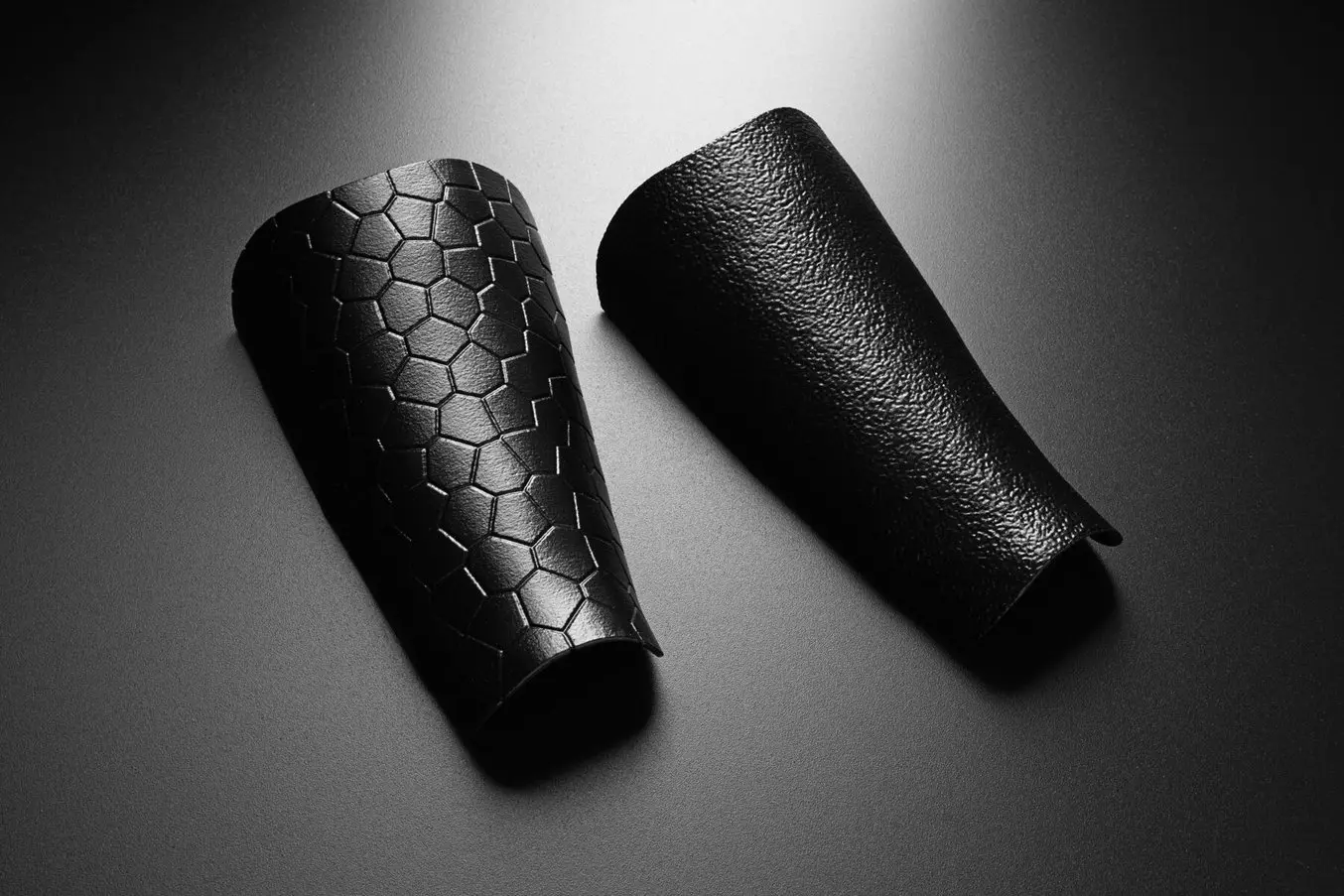
SLSの造形品は、プリンタから出てきた時点では表面が僅かにざらついていることがあるものの、ベーパースムージングなどの表面処理を施すことで実製品用品質の表面品質を実現できる。写真の造形品はそれぞれ異なる表面テクスチャで造形後、ベーパースムージングで表面の粗さを取り除いたもの。
作業手順と使いやすさ
考えたデザインをForm 4 SLA光造形3Dプリンタで具現化する様子をご覧ください。この動画では、ソフトウェア、材料、造形、後処理に至るまで、Form 4の基本的な使用方法を解説しています。
FDM、SLA光造形、SLSのいずれの方式でも作業手順は一貫して同じです。まずは作りたいものをデザインし、その後3Dプリントをし、最後に後処理を行います。
まず、一般のCADソフトウェアまたは3Dスキャンデータを使ってモデルをデザインし、完成したら3Dプリンタ対応の形式(STLまたはOBJ)でファイルをエクスポートます。3Dプリンタで直接造形準備を行うか、スライサーツールを使って造形準備を行い、デジタルモデルをスライスしてレイヤーに変換します。造形時の方向づけについては、Formlabsの造形準備ソフトウェアPreFormなら「ワンクリックプリント」をクリックするだけで簡単に行えます。ワンクリックプリントを使用しない場合は、手作業で造形設定を選択し材料設定を微調整できるオプションもあります。格安プリンタの場合は通常、事前準備としてユーザー自身が多くの作業を行わなければならず、これが造形失敗や造形工程の効率低下につながる可能性があります。
Form 4 SLA光造形3DプリンタやFuseシリーズ SLS 3Dプリンタのような工業品質の3Dプリンタには、モデルを自動的にセットアップするオプションが用意されていることが多く、徹底的にテストされた設定と材料設定を使用できます。Fuseシリーズ用のPreFormで使用できるSLSパッキング機能はサードパーティ製のソフトウェアを上回る性能で、モデルを積み重ねたり入れ子状にして配置することでビルドチャンバー内の密度を高め、製造単価を抑えます。
3Dプリンタのほとんどは、一旦3Dプリントが開始すると夜通しかかる場合でも完成まで放置しておけます。Form 4のような先進的なSLA光造形3Dプリンタの場合、材料を自動充填できるカートリッジになっていたり、Form 3シリーズで使用できるForm Autoのような外付けの自動化装置もあります。
この動画では、FuseシリーズSLS 3Dプリンタの作業手順について詳しく解説しています。設計からビルドチャンバーのパッキング、パウダーの回収、ブラスト処理まで、SLS方式3Dプリントの各工程をご紹介しています。
3Dプリントの作業手順の締めは、後処理です。基本的な後処理の作業は、FDMとSLA光造形の場合はサポート材の除去、SLA光造形の場合はその後に洗浄と二次硬化、SLSの場合は余分なパウダーの除去と造形品のクリーニングです。
FDM方式の場合、積層痕が目に見える形ではっきりと残ることがよくあります。積層痕が残る造形品をより高度な用途で使用できる状態にするためには、入念なサンディングやスムージングが必要になります。サポート材は可溶性フィラメントを使用できる場合もありますが、硬質なサポート材の切り離しが必要な造形品も多く、サポート痕を取り除くために表面のサンディングが必要になります。この2つのステップには多大な時間がかかるため、FDM方式の場合は3Dプリントにかかる全体の作業時間が増加し、結果的に生産量が低下します。
SLA光造形の後処理工程の基本となるのは、アルコールやエーテルで造形品を洗浄して表面に付着している余分なレジンを取り除く作業です。洗浄は手動でも自動でも行え、自動の場合は専用の自動洗浄装置を使って事前設定された洗浄時間で溶剤を撹拌し洗浄します。一部のSLA光造形品では、洗浄後に材料特性を最大限に引き出すために二次硬化が必要になりますが、これも高度な二次硬化装置で自動化が可能です。
SLSの基本的な後処理作業としては、造形品の表面についている余分な未焼結パウダーを取り除いた後、ブラスト処理で粉末を完全に除去し表面を滑らかにします。SLSメーカーの中には、指定のブラスターや完結型の粉末回収装置を提供していなかったり、提供していたとしても非常に高価な値段で販売しているケースがあります。Formlabsの包括的なSLSパッケージにはFuse SiftとFuse Blastが含まれており、粉末除去・回収、そしてブラスト処理をより速く簡単に、そしてより綺麗に行えます。
また、コーティング、スムージング、塗装、ベーパースムージング、電解めっき処理などの高度な表面処理を施すことも可能で、審美性や機械的特性、全体的な性能を向上させて幅広い用途に対応できる造形品を作ることも可能です。後処理や表面処理については、SLA光造形およびSLS方式3Dプリントの後処理に関するガイドをご覧ください。
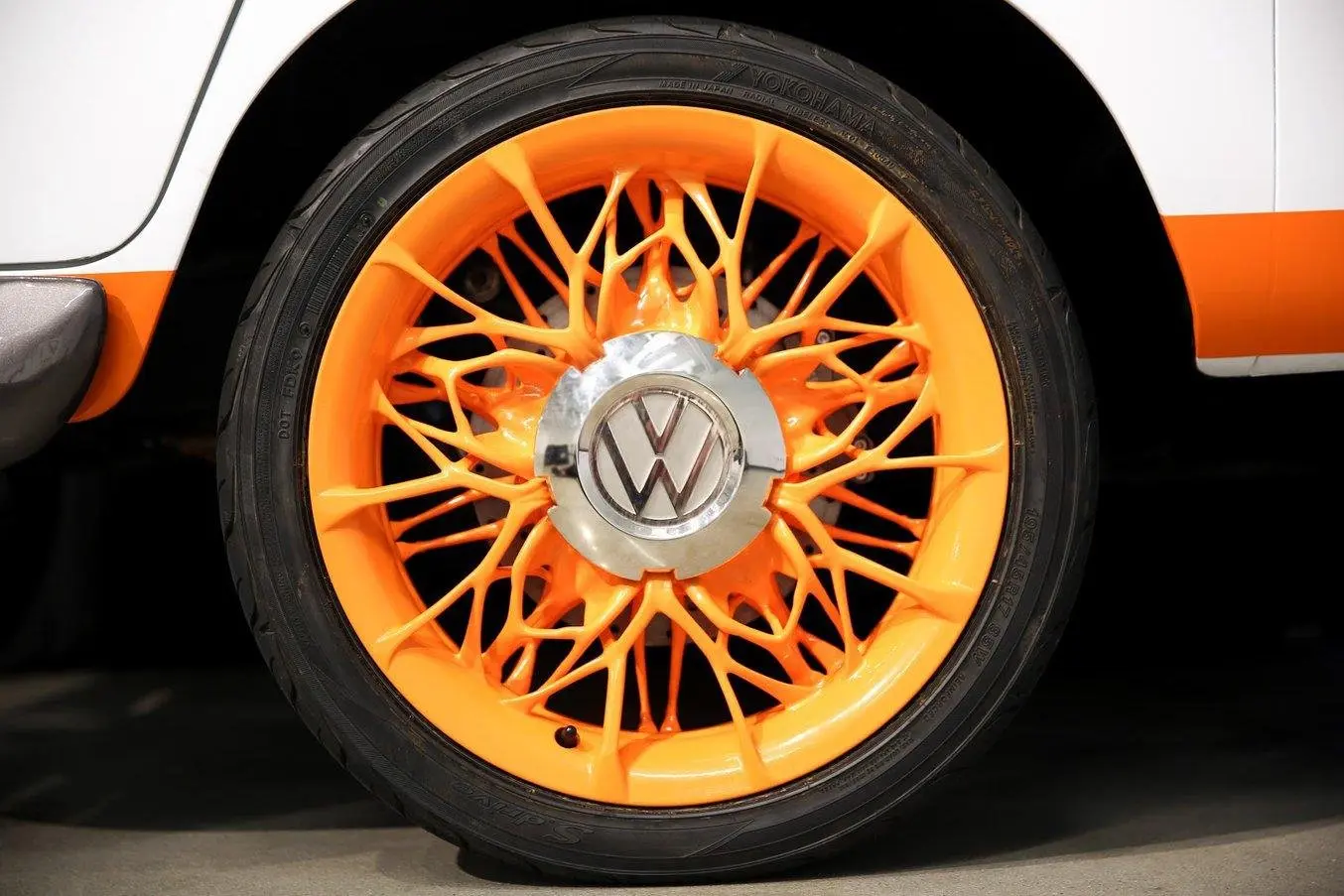
3Dプリント用の高度な後処理方法
このウェビナーでは、Cerakote、電解めっき、ベーパースムージングなど、3Dプリント品に施すことのできる11種類以上の高度な後処理方法をご紹介しています。
材料と代表的な用途
適切な3Dプリント方式を選定するためには、他にも検討すべきことがあります。求める機械的・機能的特性や外観を持つ造形品が作れるかどうかは、3Dプリント用材料の選定に大きく左右されます。
FDM方式でフィラメントで作られた造形品、レジンを使ったSLA光造形品、パウダーを使ったSLS造形品は、それぞれ異なる材料と造形プロセスを使用するため、性能を直接比較するのが難しい場合があります。しかし、どの方式にも類似の材料があるため、方式は違っても同じ材料特性(または非常に近い特性)を達成することは実はそれほど難しくありません。
FDM(熱溶解積層)方式:フィラメント | SLA光造形方式:レジン | SLS(粉末焼結積層造形)方式:パウダー | |
---|---|---|---|
一般的な使用 | PLA | スタンダードレジン(マット、クリア、豊富な色彩) | Nylon 12 |
丈夫なエンジニアリング材料 | ABS、ナイロン、PETG | Toughレジン、Durableレジン | Nylon 12、Nylon 11、PP |
剛性のあるエンジニアリング材料 | PEEK、ULTEM 複合材(ガラス充填または炭素繊維強化材料) | 高剛性・高強度・硬質レジン(ガラス充填) | ナイロン複合材(ガラス充填または炭素繊維強化材料) |
柔軟なエンジニアリング材料 | TPU | 柔軟性または弾性のあるレジン、純シリコン材料 | TPU、PP、Nylon 11 |
スペシャルティ材料 | 複合材料 (炭素繊維、ケブラー、ガラス繊維) | 難燃性レジン、インベストメント鋳造材料、テクニカルセラミックス、ワックス複合材、歯科・医療用材料 | ナイロン複合材(ガラス充填または炭素繊維強化材料) |
FDMプリンタでは、主にABSやPLAなどの一般的に馴染みの深い熱可塑性プラスチックのフィラメントを使用します。ナイロン、PETG、TPUなどのエンジニアリング材料や、PEEKや炭素繊維複合材料などの高性能熱可塑性プラスチックも利用できますが、厳選された業務用FDMプリンタでしか使用できない場合がほとんどです。
FDM方式で使用するフィラメントは、射出成形や真空成形のような大量生産工程で使用される材料と同じであることがよくあります。共通の材料が使用できるということは、エンジニアにとっては設計と製造の工程を通して同じ材料を使用できることになるため、FDMをプロトタイピング用のオプションとして選ぶ確率が上がります。しかし、FDM方式では積層痕が残ってしまうこと、および造形品の機能強度が低下するため、より高い機能性が求められる用途での活用は難しくなります。
FDM方式は、デザイナーが造形品の外観を素早く確認する必要があるような場合や、教育機関などで学生が3Dプリントのトレーニングを受ける場合などには優れた選択肢となります。消費者製品のプロトタイピングでは、FDM方式を使用することでコストを抑えながら造形品の見た目や手に取った時の感触を確かめることができます。
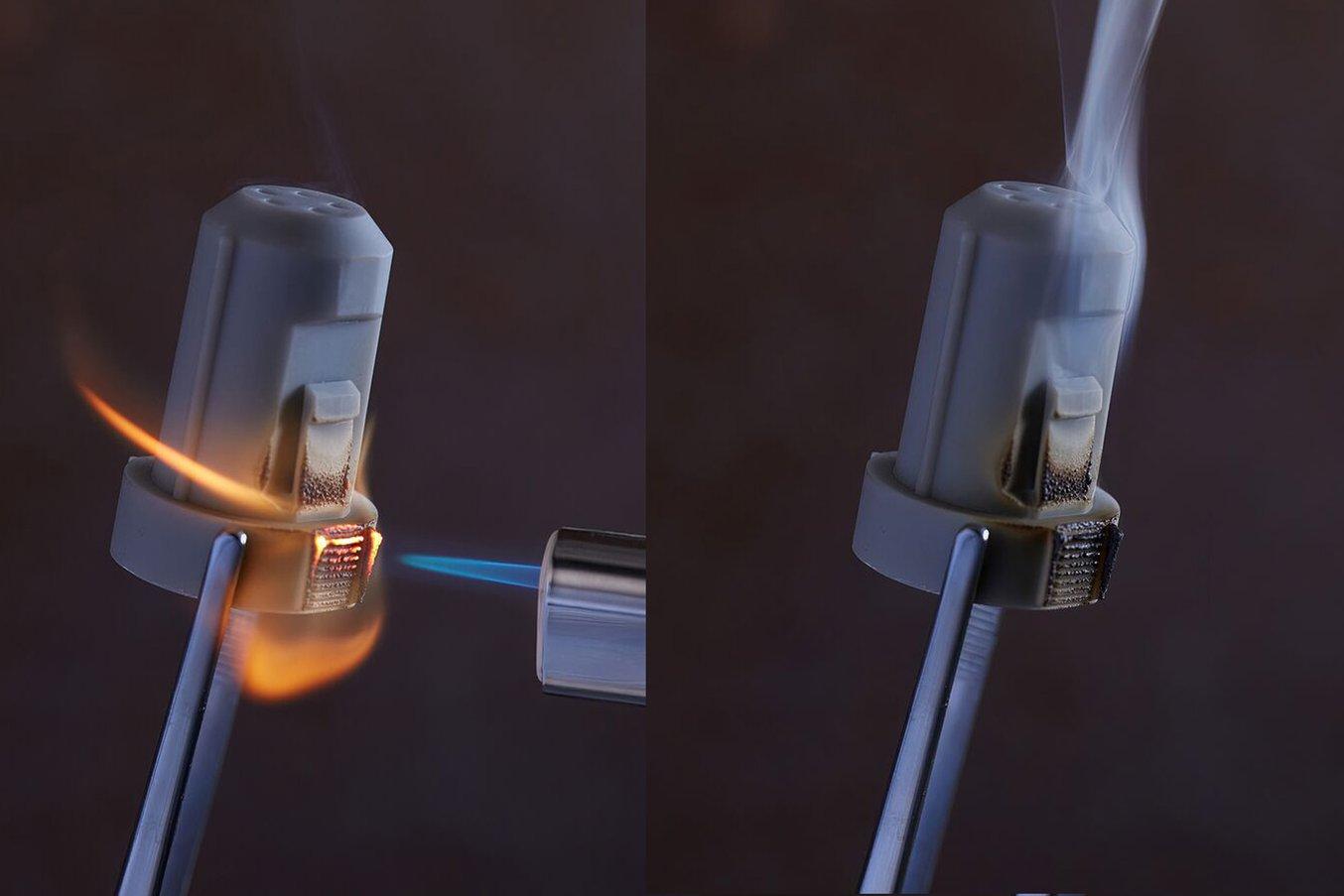
Flame Retardant(難燃性)レジンは、ハロゲンフリーのUL94 Blue Card認証取得済のスペシャルティ材料で、良好なFST(炎、煙、毒性)評価を獲得。
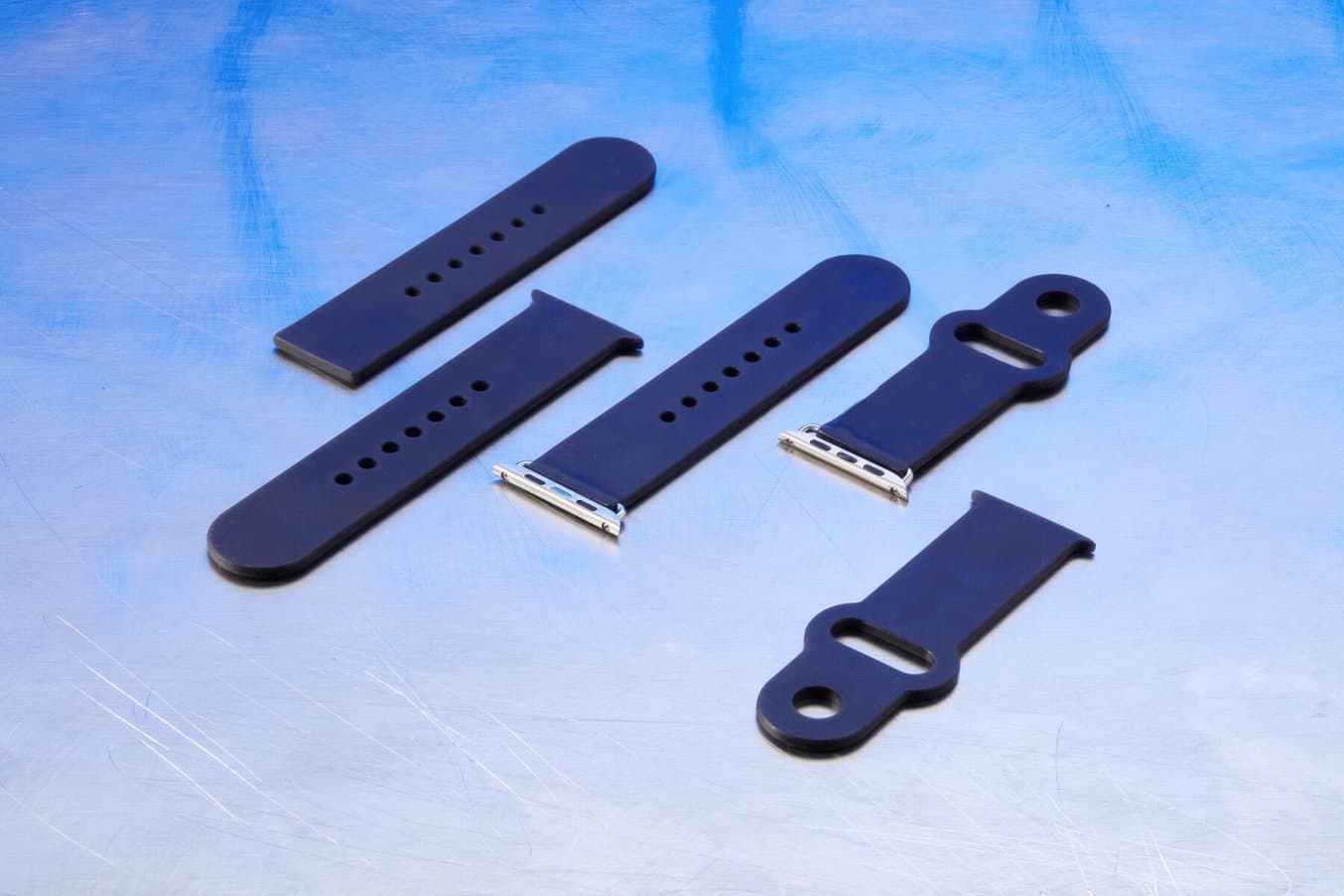
Silicone 40Aレジンは、 エンジニアやプロダクトデザイナーにとって馴染みのある機械的特性を備えた純シリコン材料。
SLA光造形3Dプリンタでは、メーカーごとに異なる独自の材料が使用できます。独自材料を使用する利点は、メーカーが自社のプリンタを使って独自配合のレジンをプリントできるよう入念なキャリブレーションを実施しているため、精度の向上や再現性の高い結果が期待できることです。欠点としては、SLA光造形で使用するレジンに馴染みのないユーザーが多いため、知見にギャップがありなかなか導入が進まないことが挙げられます。SLA光造形では、独自レジンにより歯科用レジンやセラミック材料など、高度な用途に特化した材料が提供されています。
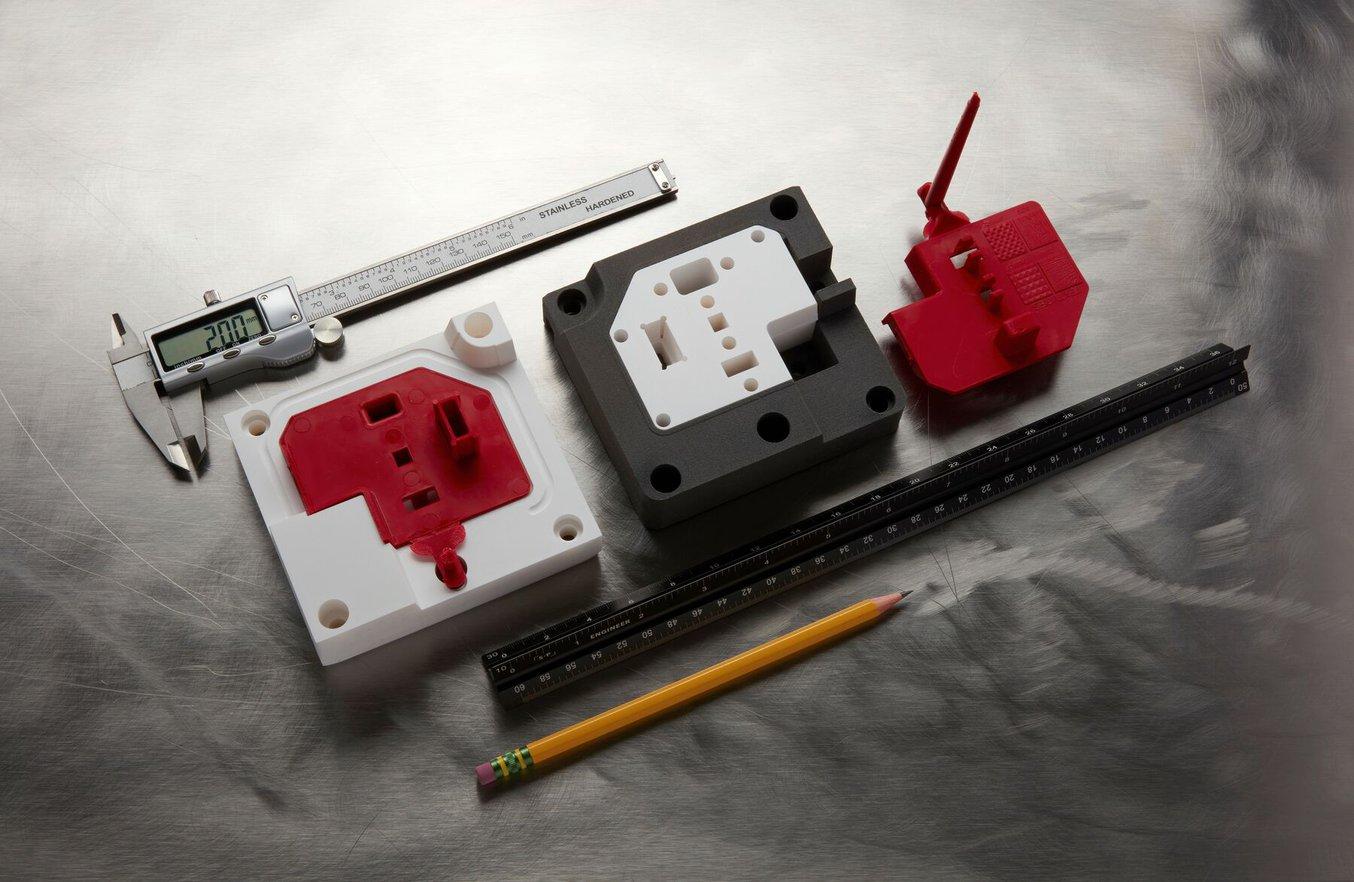
Rigid 10Kレジンはガラスを高密度充填した非常に剛性の高い材料で、ガラスまたは炭素繊維の熱可塑性プラスチックと同様の特性を有する。射出成形、ブロー成形、真空成形で使用するための型をラピッドツーリングする場合に最適な材料。
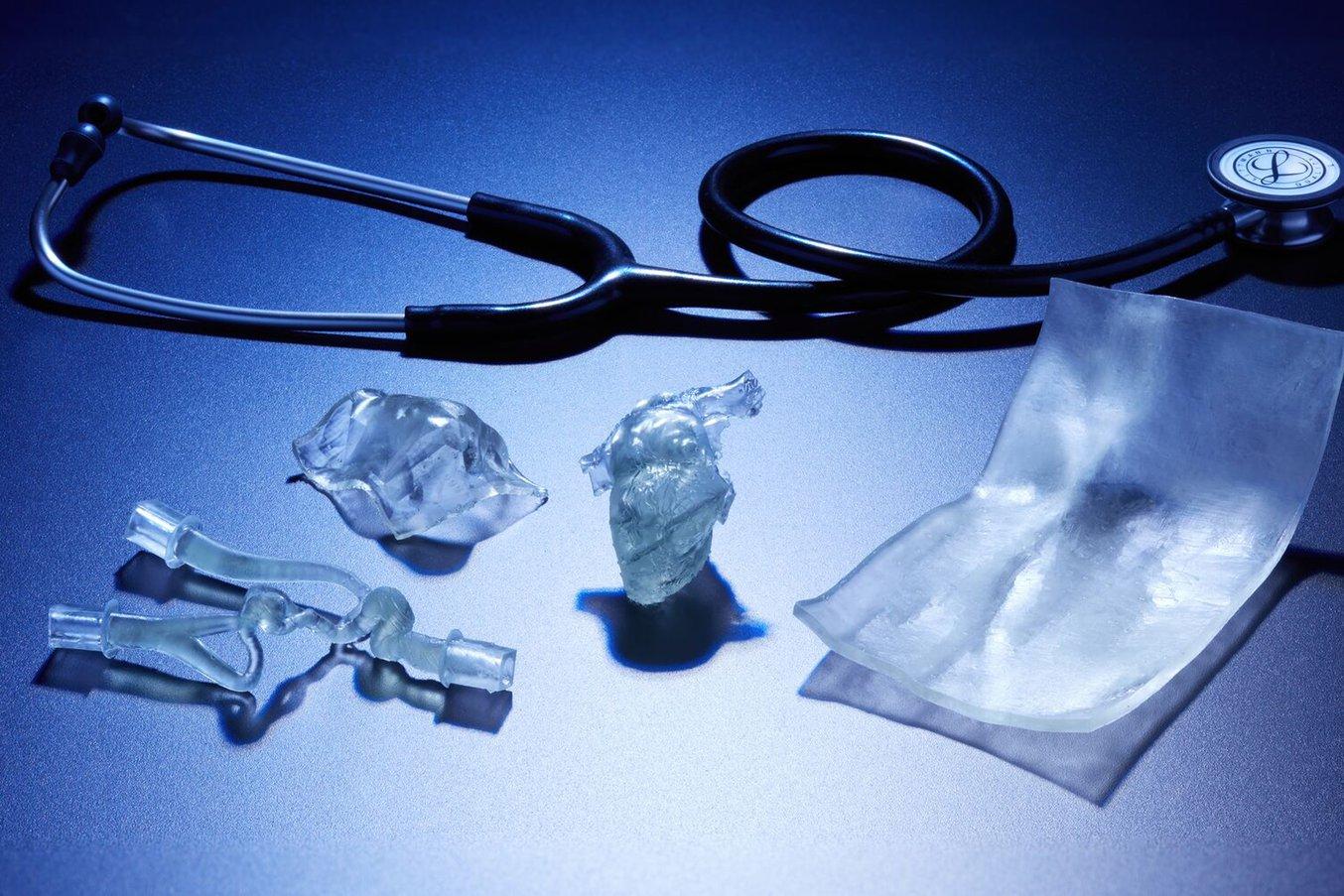
BioMed Elastic 50Aレジンを使用することで、ヘルスケアプロバイダーは患者様専用にカスタマイズした医療機器や軟組織モデルなど、形状が複雑で柔らかく伸縮性のある生体適合性器具を3Dプリントすることができる。
通常、SLA光造形は設計から製造までのあらゆる段階で活用することができます。等方性を備えた材料特性と優れた表面品質により、機能的なプロトタイピング、Go/No-Goテスト、実製品用部品や治具の製作に最適です。テクニカルセラミックスや灰を残さず完全に燃え尽きるタイプのワックス複合材のように、新しい独自配合の材料を開発できることで、SLA光造形方式は特定の産業や用途に完璧にマッチした方式となります。SLA光造形用レジンは、複数の業界で広く使用できる一般的な用途として、エンドオブ・アーム・ツーリング、ロボティクス用エンクロージャ、シール、手術ガイドなどにも使用可能な耐久性と強度を備えています。配合可能な範囲が広いため、レジンで製作できる部品はほぼ無限大に広がります。
Formlabsでは、高度なテクニカルセラミックス、煙および毒性評価で良好な結果を獲得した難燃性レジン、ESDセーフ材料、さらには義歯や永久クラウンのような実際の使用を想定した医療機器具向け材料など、SLA光造形方式で使用できる40種類以上の独自配合レジンを提供しています。
SLS 3Dプリント用材料としては、ナイロン、TPU、PPなど、お馴染みの熱可塑性プラスチックをパウダー状でご利用いただけます。これらのパウダーは高機能で、材料特性もよく知られています。SLS 3Dプリンタメーカーは、独自配合のパウダーを提供したり、メーカーからパウダーを一括購入してホワイトラベル化したりしています。業界で馴染みのある材料がSLS 3Dプリントの特徴である形状の自由度と生産能力、強度と組み合わさることで、SLSプリント用材料はプロトタイプから機能試験、治具、実製品の製造まで、あらゆる用途にお使いいただけます。
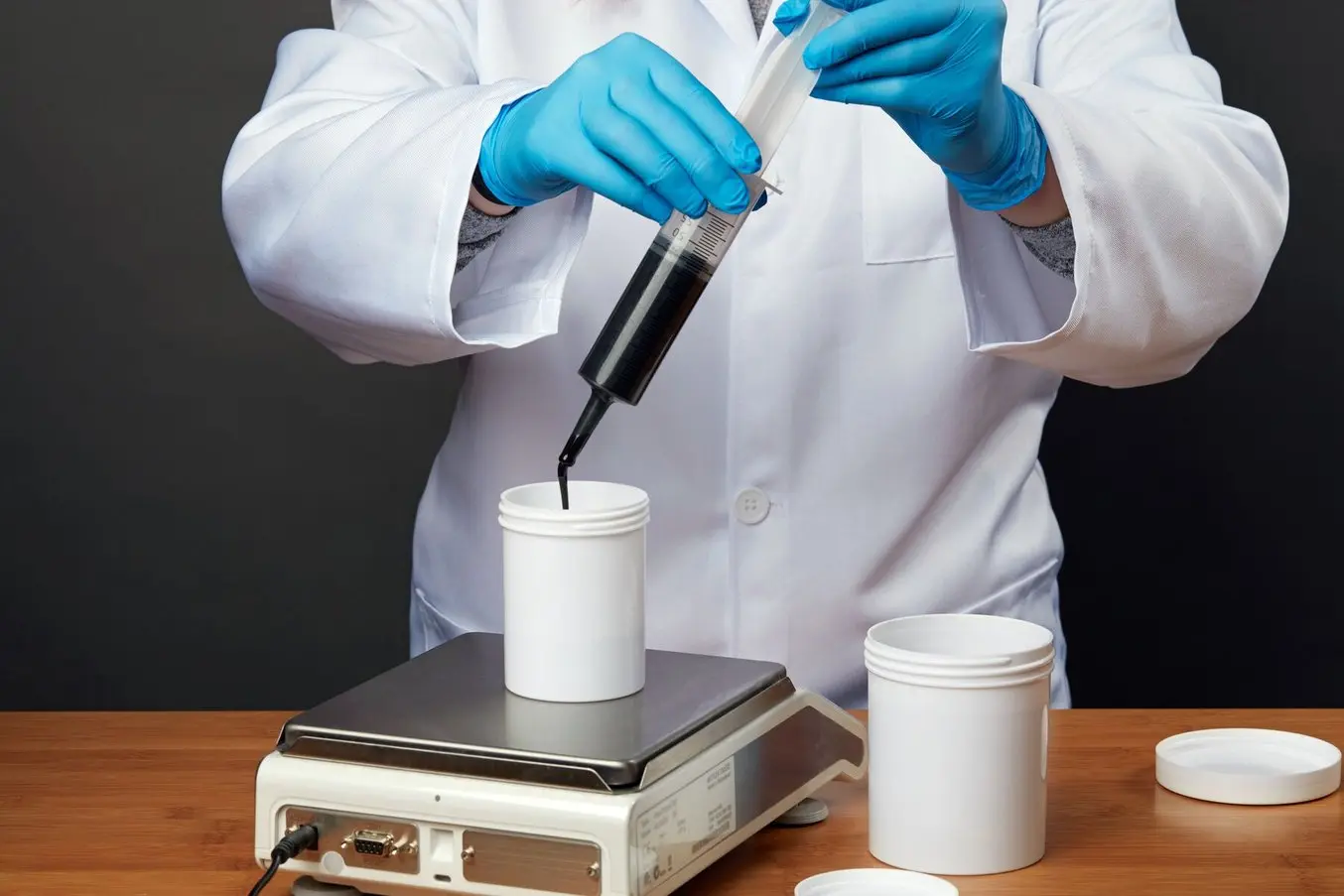
Formlabsが遂にオープンに
Formlabs Developer Platformでお使いの3Dプリンタの可能性を最大限に引き出してみませんか。波長405nmのUV光に対応するレジンや、波長1,64nmのレーザー光に対応するパウダーをFormlabsの3Dプリンタでご利用いただけるほか、造形設定のカスタマイズや他社ソフトウェアとの統合機能も実装できます。
最大造形サイズ
FDM方式、SLA光造形方式、SLS方式の最大造形サイズは大きく異なります。いずれの方式でも大容量サイズの造形は可能ですが、FDM 3DプリンタおよびSLA光造形3Dプリンタで最も一般的なのはデスクトップサイズまたはベンチトップサイズで、SLSについてはベンチトップサイズかそれ以上の大きさが一般的です。
FDM 3Dプリンタのサイズと価格は多岐に渡ります。FDM方式はサイズによる制限や影響を受けません。高精度のノズルでも大型モデルの造形は可能ですが、モーターシステムがより広範囲にわたって移動することになるため、サイズが大きくなればなるほど造形にかかる時間が長くなります。ベンチトップサイズやデスクトップサイズのプリンタというよりは小さな部屋を彷彿とさせる巨大なFDM 3Dプリンタもありますが、非常にニッチであまり一般的ではありません。より普及しているFDM 3Dプリンタは、デスクトップまたはベンチトップサイズで、通常は迅速なプロトタイピングや教室・ファブラボでの教育ツールとして使用されます。一般的なデスクトップサイズのFDM方式の最大造形サイズは200 x 200 x 200mmです。
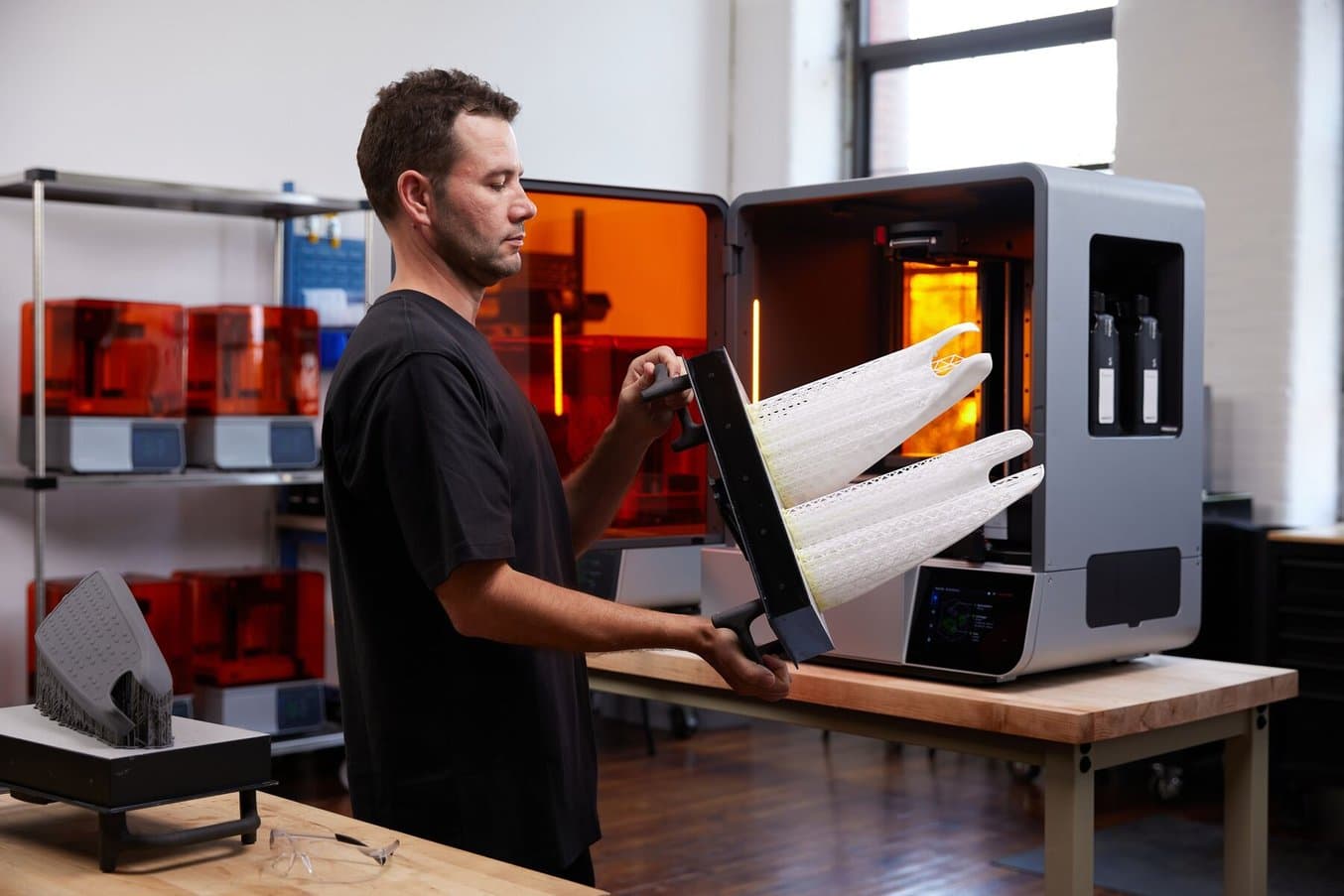
Form 4Lは、ヒューマンスケールのプロトタイピングや複数パーツの超高速製作に最適な大容量SLA光造形3Dプリンタ。ほとんどの造形が6時間以内に完了し、ビルドプラットフォームの最大高さいっぱいのモデルでも1日以内に製作が可能。
SLA光造形3Dプリンタには、デスクトップサイズから大型の産業用プリンタまで様々なサイズがあります。従来、「トップダウン式」と呼ばれるレーザー駆動型のSLA光造形3Dプリンタは非常に大型で、設置面積は何メートルにもおよび、補助的な換気設備や専用の電気回路の整備も必要でした。このような工業用サイズのプリンタは過去数十年に渡り、トップダウンの光重合プリンタで必要となる大きな設置面積とインフラ整備、高額な購入費用とメンテナンス費用のすべてを賄うことのできる大企業に採用されてきました。
反転型SLA光造形プリント方式が開発されたことでデスクトップサイズの光造形3Dプリンタが実現したわけですが、導入メーカーが増えるにつれ、各方向の造形面が100~200mm程度の立方体の小型プリンタが主流になりました。例えば、FormlabsのForm 3+は最大造形サイズが145 × 145 × 193mm、Form 4の場合は30%拡大した200 × 125 × 210mmです。
さらに、反転型SLA光造形方式の登場と剥離技術の改善により、ベンチトップサイズの光造形3Dプリンタも実現しました。Form 4Lのようなベンチトップサイズの3Dプリンタは、最大造形サイズが353 × 196 × 350mmでありながらコンパクトで使いやすく、従来の産業用大型プリンタと同等の造形容量を叶えます。ベンチトップサイズの3Dプリンタは、ヒューマンスケールの消費者製品のプロトタイピングに優れているだけでなく、3Dプリントした成形型を使って実製品を製作することもできます。
SLS 3Dプリンタも従来は大型のものしかなく、デスクトップサイズのFDMプリンタやSLA光造形プリンタよりも大容量になることが一般的でした。しかし近年の努力により、デスクトップサイズのSLSプリンタが誕生しました。それでもSLS 3Dプリンタの大半はベンチトップサイズかそれ以上で、従来の産業機ともなるとそれ以上の設置面積が必要になります。FormlabsのFuseシリーズは最大造形サイズが165 × 165 × 300mmでありながら、コストとサイズの両面で利用しやすい初のSLSプリンタとして、設置面積に限りのある小企業でもようやく社内に導入できるようになりました。
速度とスループット
より多くの企業が量産だけでなく、迅速な試作・検証プロセスを実現するために3Dプリントを利用するようになったことで、3Dプリント方式の選定基準として造形速度とスループットがさらに重視されるようになりました。最適な3Dプリンタとは、精度、信頼性、材料の性能を犠牲にすることなく、高品質の造形品を迅速に製造できるプリンタです。
FDMの造形速度は、押し出し工程とモーター出力による制約を受けます。精度の高い部品を製作するために、FDM 3Dプリンタは特定の速度でフィラメントをムラなく押し出し、XY平面にノズルを均一かつ滑らかなペースで移動させる必要があります。この工程を高速化すると、押し出されたフィラメントの機械的特性にばらつきが生じ、造形品の精度が低下する可能性があります。
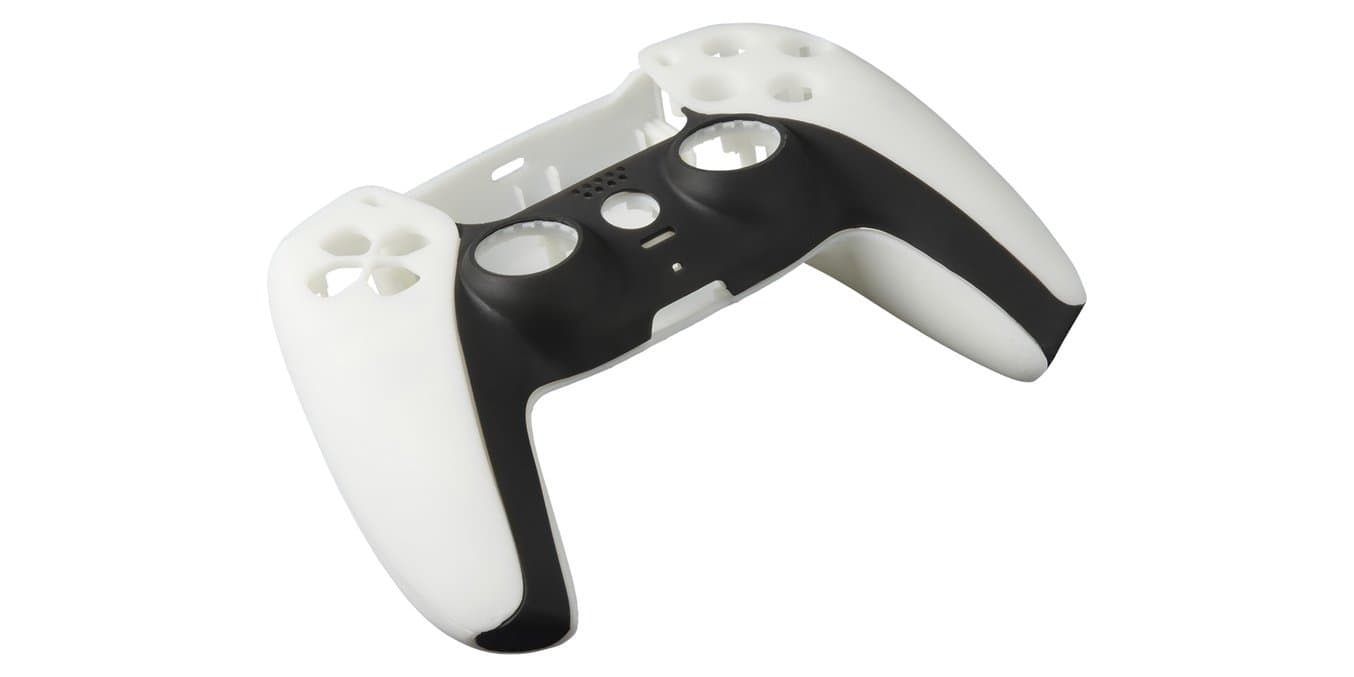
造形スピードの比較:ゲームコントローラー
FDM 3Dプリント | SLA光造形3Dプリント | SLS 3Dプリント | |
---|---|---|---|
アセンブリ x 1(3部品) | 10時間32分 | 2時間36分 | 造形:3時間52分(冷却:6時間52分) |
アセンブリ x 5(15部品) | 52時間40分 | 13時間 | 造形:9時間38分(冷却:13時間47分) |
比較対象のプリンタ機種と造形設定:
- FDM 3Dプリンタ:Bambu Lab X1、PLA Basic、積層ピッチ120μm、充填率15%
- SLA光造形3Dプリンタ:Form 4、Greyレジン、積層ピッチ100μm
- SLS 3Dプリンタ:Fuse 1+ 30W、Nylon 12パウダー、積層ピッチ110μm
SLA光造形の場合、一般的な造形速度は使用する3Dプリント方式によって異なりますが、現時点で最速となるのはMSLA方式です。FormlabsのForm 4などに代表される最新世代のMSLA 3Dプリンタは、強力なプリントエンジンと高度な光学システムの組み合わせにより各層をほぼ瞬時に硬化させることができます。
Form 4とForm 4Lは、Fast Modelレジンなど高速造形に特化して開発された材料を使った場合に、最大時速100mm/時というスピードを実現できるよう設計されています。Form 4で行う造形はどの材料を使ってもほとんどが2時間以内に完了するため、1日数回にわたって試作・検証プロセスを繰り返せます。Form 4Lでは、ほとんどの造形が6時間以内に完了します。プリンタの最大高さいっぱいのモデルでも、ビルドプラットフォーム全体を覆うような複数モデルの大量造形でも、1日以内に完成するため、大型モデルと複数の小型パーツのどちらも同日中の試作・検証が可能になります。
どの3Dプリント方式も時代とともに造形速度の高速化が進んでいますが、光造形プリントの進化には敵いません。これが日ごと、週ごとに積み重なれば、高速造形による高スループットのメリットは非常に大きくなります。Form 4やForm 4Lでは、射出成形のような高い生産性を誇る技術に匹敵する速度を実現します。ビルドチャンバーいっぱいの造形を数時間で1日に何度も造形できるようになることで、金型製作にかかる高額な間接費を心配することなく中程度の射出成形機にも劣らない生産量を実現できます。
SLS 3DプリントはFDMよりも高速ですが、それは高出力のレーザーを粉末に照射することで、FDM方式の押出ノズルがプリントベッドの上を移動するよりも速く造形面を走査できるためです。ただし高出力のレーザーも、DLP方式やMSLA方式の光造形3Dプリンタの光源が点滅する速度に比べるとスピードは劣ります。その他、厳密には造形速度ではないものの、SLS 3Dプリント工程ではビルドチャンバーの冷却時間も考慮する必要があります。レーザーが粉末を高温で一気に焼結するため、後処理を行う前にビルドチャンバーを冷却する必要があり、これが工程全体にかかる時間を増加させることになります。
しかしこの造形+冷却にかかる時間は、生産においてあまり大きな弊害にはなりません。1点あたりの造形スピードは他の方式より若干長くても、SLS 3Dプリントでは1回のプリントでビルドチャンバーいっぱいの造形が可能なため、全体的な生産量としては非常に優れています。最大造形サイズが大きくネスティングが可能なため、チャンバー内に造形品を高密度にパッキングし、最大造形サイズをフルに活用することができます。例えばFuse 1+ 30Wでビルドチャンバーいっぱいに造形した場合、勤務時間外となる夜の間に造形とプリンタ庫内での冷却が完了し、日中にプリンタ庫外で二次冷却を行うことで、同日中の部品製作を24時間365日連続で行うことができます。さらに、Fuse SiftやFuse Blastのような装置で多くの工程を自動化でき、サポート材の取り外しも不要なため、後処理作業にかかる時間を大幅に短縮できます。
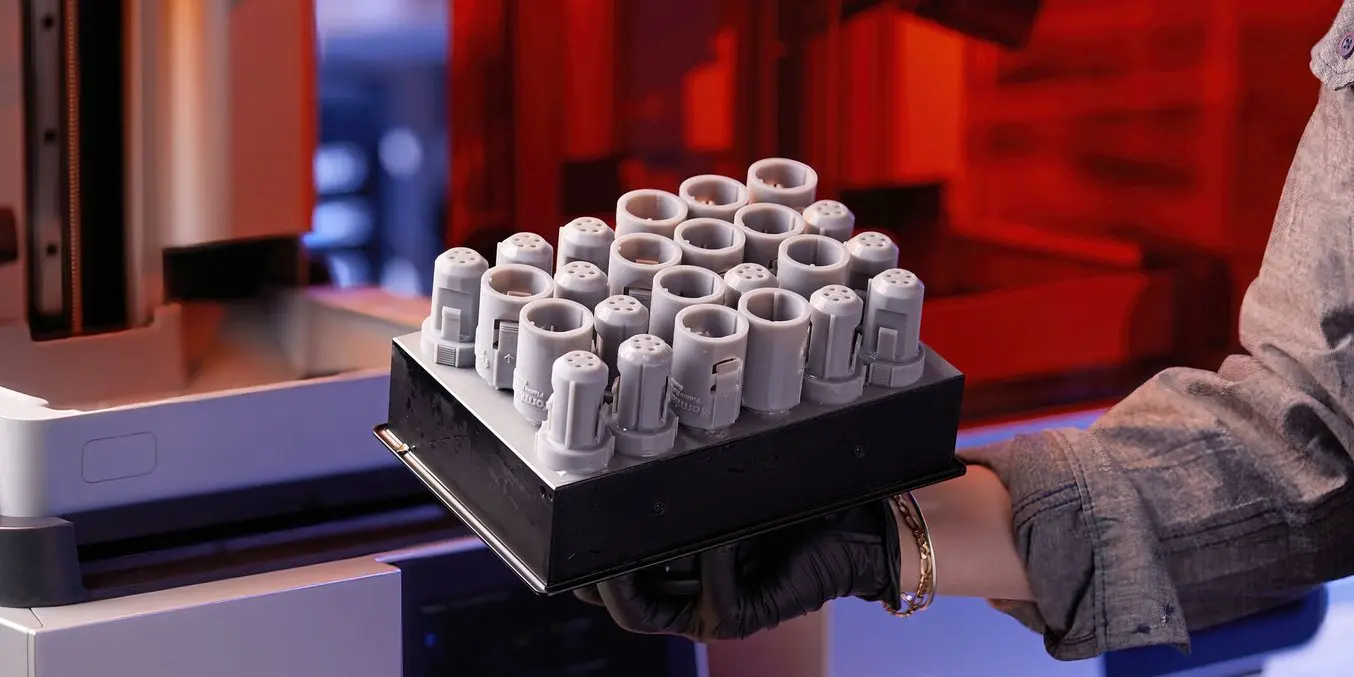
造形スピードの比較:電子機器コネクタ
FDM 3Dプリント | SLA光造形3Dプリント | SLS 3Dプリント | |
---|---|---|---|
アセンブリ x 1(2部品) | 2時間38分 | 1時間3分 | 造形:3時間30分(冷却:6時間27分) |
アセンブリ x 50(100部品) | 84時間 | 13時間2分 | 造形:12時間59分(冷却:13時間49分) |
比較対象のプリンタ機種と造形設定:
- FDM 3Dプリンタ:Bambu Lab X1、PLA Basic、積層ピッチ120μm、充填率15%
- SLA光造形3Dプリンタ:Form 4、Greyレジン、積層ピッチ100μm
- SLS 3Dプリンタ:Fuse 1+ 30W、Nylon 12パウダー、積層ピッチ110μm
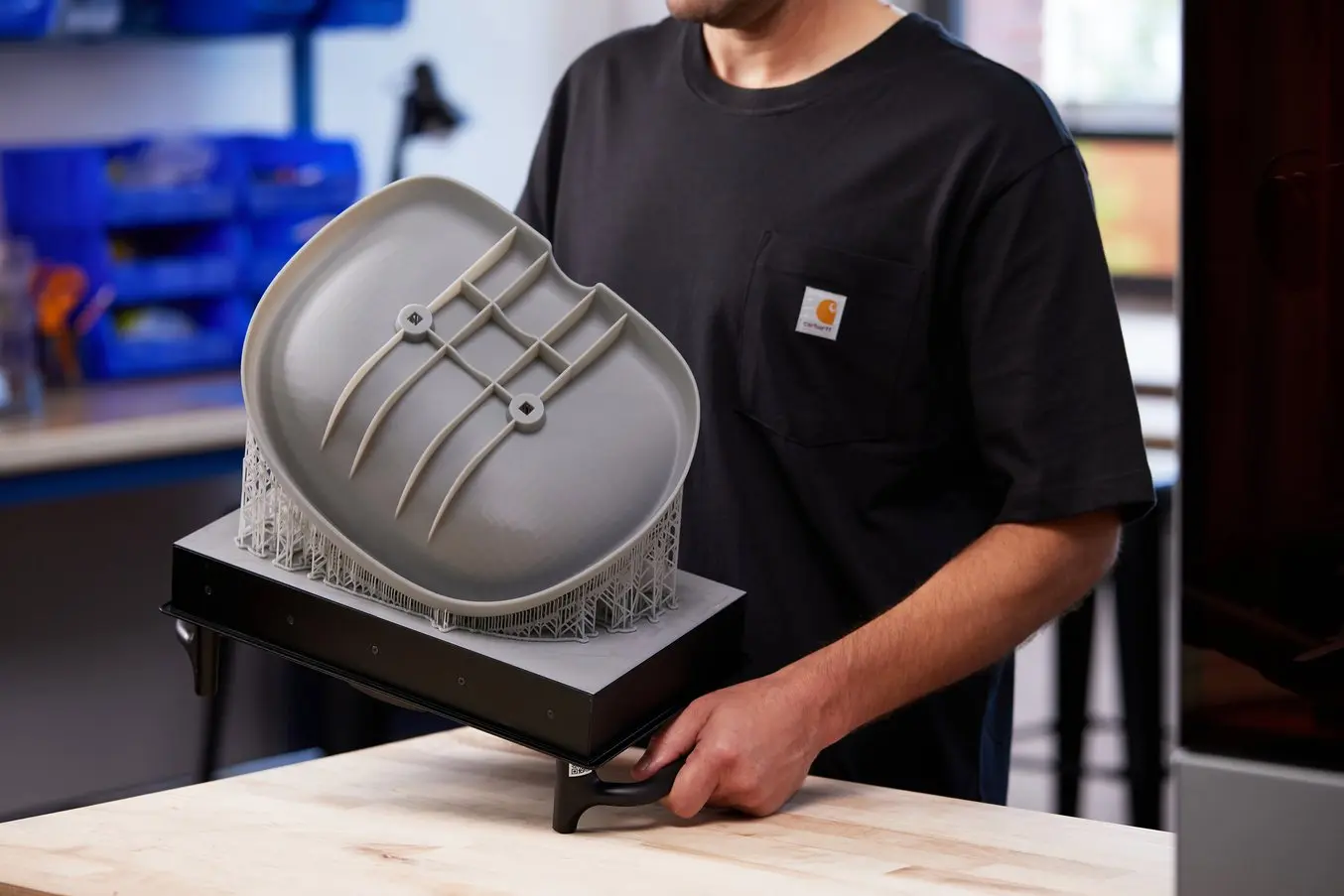
造形速度の比較:Radio Flyer シートプロトタイプ
FDM 3Dプリント | SLA光造形3Dプリント | |
---|---|---|
プロトタイプ(1点) | 42時間3分 | 2時間37分 |
比較対象のプリンタ機種と造形設定:
- FDM 3Dプリンタ:Ultimaker S7、PLA、積層ピッチ100ミクロン、充填率20%
- SLA光造形3Dプリンタ:Form 4、Fast Modelレジン、積層ピッチ200ミクロン
コストと投資対効果(ROI)
FDM方式、SLA光造形方式、SLS方式の3Dプリンタのコストと投資対効果(ROI)は実際にはどの程度になるのでしょうか?ROIを計算する際は、機器本体の購入価格、継続的な所有コスト、材料費、人件費を理解する必要があります。
FDM 3Dプリンタの利点の1つは、プリンタ本体の手頃な価格帯です。初心者用のFDMプリンタは数百ドルで購入できるため、ホビイストや小企業の場合はまずはFDMで試してみて3Dプリントの有用性を確かめることができます。手始めにどのプリンタを選べばよいか迷った場合には、低価格の初心者向けFDMプリンタなら無理なく手が届く選択肢になります。しかし、低価格のFDMプリンタは信頼性が低く、長期的な使用には専門知識が必要になることが多々あります。
工業品質のデスクトップサイズのFDMプリンタは$2,000~$8,000、産業用機ともなると$15,000以上になります。こういった3Dプリンタは信頼性、造形品質、最大造形サイズともに高く、機能部品の製作には適していますが、SLA光造形プリンタの用途の広さや優れた造形品質と比較すると価格面での競争が非常に厳しくなります。
低価格帯のものでは、格安LCD 3Dプリンタが$200~1000で購入できます。ホビイストや初心者に適していますが、レジンの種類に合わせてキャリブレーションや微調整が必要なうえ、一般的に信頼性や耐久性に欠けるため、メンテナンスや調査にかかる時間、造形失敗、材料の無駄などが重なりコストが高くなることがあります。
工業品質のSLA光造形3Dプリンタの価格は一般的に$2,500〜$10,000の範囲ですが、大容量光造形3Dプリンタとなると$5,000〜$25,000の範囲になります。
SLS方式については、選択肢があまりありません。通常、SLS 3DプリンタはFDMやSLA光造形よりも高額ですが、ここ数年で手の届きやすいSLSプリンタが誕生したことで、中小企業では生産に対するコントロールの強化を、そして大企業ではアジャイルな製造プロセスを可能にしています。
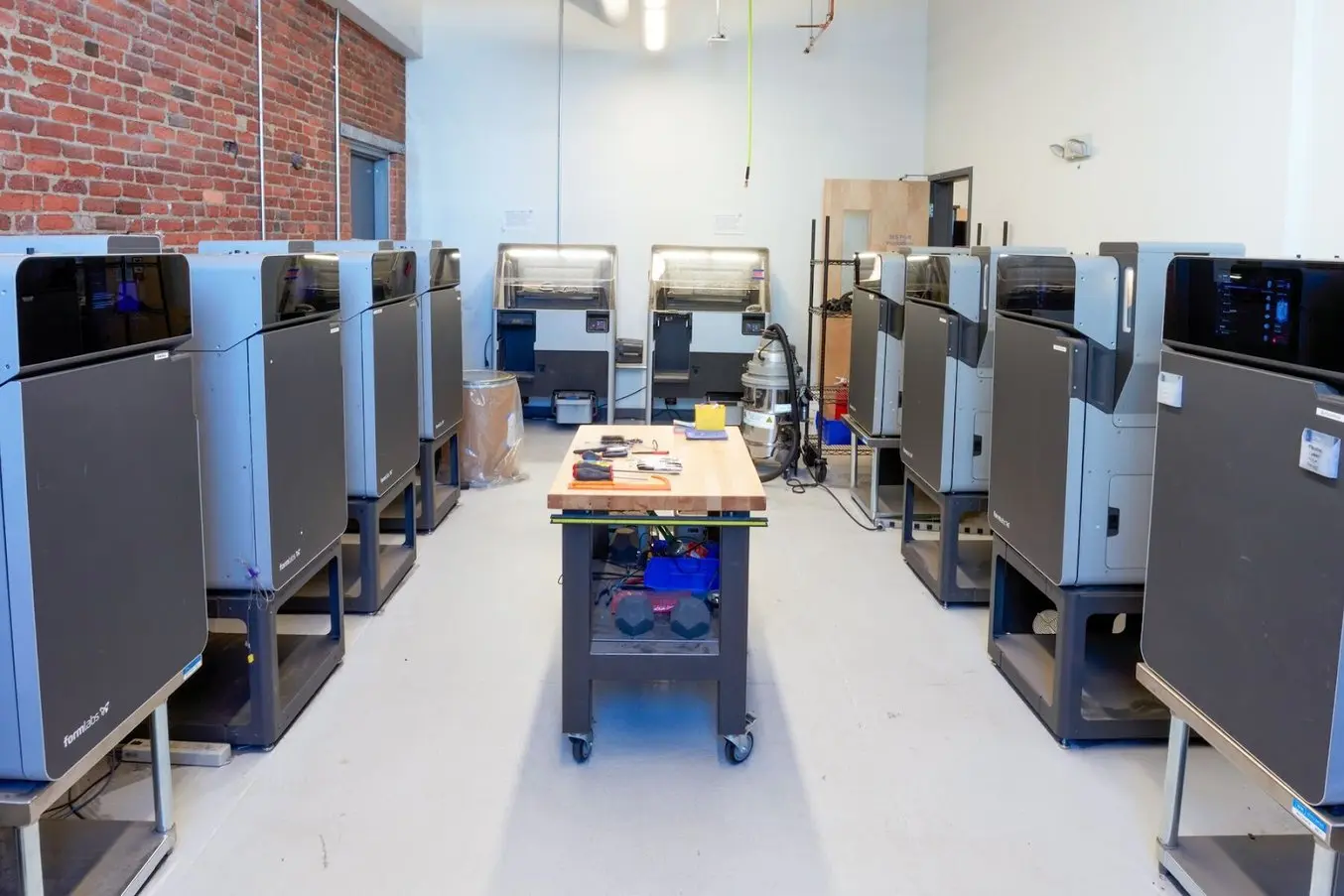
手頃な価格のSLSプリンタにより、工業用のパワフルさを社内に導入し生産規模を拡大することができる。写真のSLSプリンタ群のようにアクセスしやすい手頃な価格帯のプリンタを複数台導入することで、部品をコスト効率良く製作できる。
これまで、SLSプリンタはほとんどが$200,000を超える価格帯のものばかりでした。Fuseシリーズの登場によって初めて手頃な価格でSLSプリンタにアクセスできるようになり、プリンタと粉末除去キット付きで$30,000以下で購入できるという全く新しいコンセプトが生まれました。Fuseシリーズは、工業品質やパワフルさはそのままに、アクセスのしやすさで新たな基準を打ち立てることとなりました。粉末除去・回収・再利用を一台で可能にするFuse SiftとFuse Blastがセットになったエコシステム一式が$60,000以下という革命的な価格帯を実現したことで、中小企業や個人、教育機関などより多くの人々に、パワフルなSLS 3Dプリントを使った内製の可能性を追求いただけるようになりました。次の価格帯になると購入時に数十万ドルがかかる他、年間$30,000ものサービスプランを利用することになります。Formlabsは、Fuseシリーズの前世代機(Fuse 1プリンタ)をさらに低価格で提供し続けることで、SLSをさらに身近なものにしています。大量生産とスループットがそこまで重視されないプロトタイピングラボなどにとって、Fuse 1は高品質のSLSパーツを一貫して提供できる最適なオプションとなります。
3Dプリンタの所有コストを考える場合、3Dプリント用の材料と消耗品のコストも欠かせない要素になります。その点、FDMは広く普及していることと造形工程がそこまで複雑ではないことで、SLA光造形方式に比べて比較的低コストになります。
ABSやPLAといったFDMの標準的な材料と各ブレンド材は1kgあたり$30から、エンジニアリング用の特殊材料になると1kgあたり$100~$150で購入できます。2本の押出ノズル搭載のFDM 3Dプリンタで使用する可溶性サポート材は、1kgあたり$100~$200です。これらのフィラメントは簡単に入手でき、さまざまな製造工程で広く使用されているため、競争によって価格が下がっています。フィラメントは保存が可能で有効期限がないため、供給者は欠品や需要の変化を考慮せずに価格を設定できるのです。
一方、SLA光造形用レジンは配合や製造、保管方法が複雑で、こういった要素が全て関連して価格帯が上がっています。格安レジンの入手も可能ではあり、通常は既存プリンタのサードパーティ製ソリューションとしてプリンタとは別売りで販売されていますが、造形時により細かな調整が必要で、臭いが強いものや潜在的に有害な化学物質などが使用されていることもあります。
Formlabsのスタンダードレジンは、1Lあたり$99と高品質の材料をよりアクセスしやすい価格帯で提供することで、様々な用途や業界でより広く活用できるオプションとなっています。
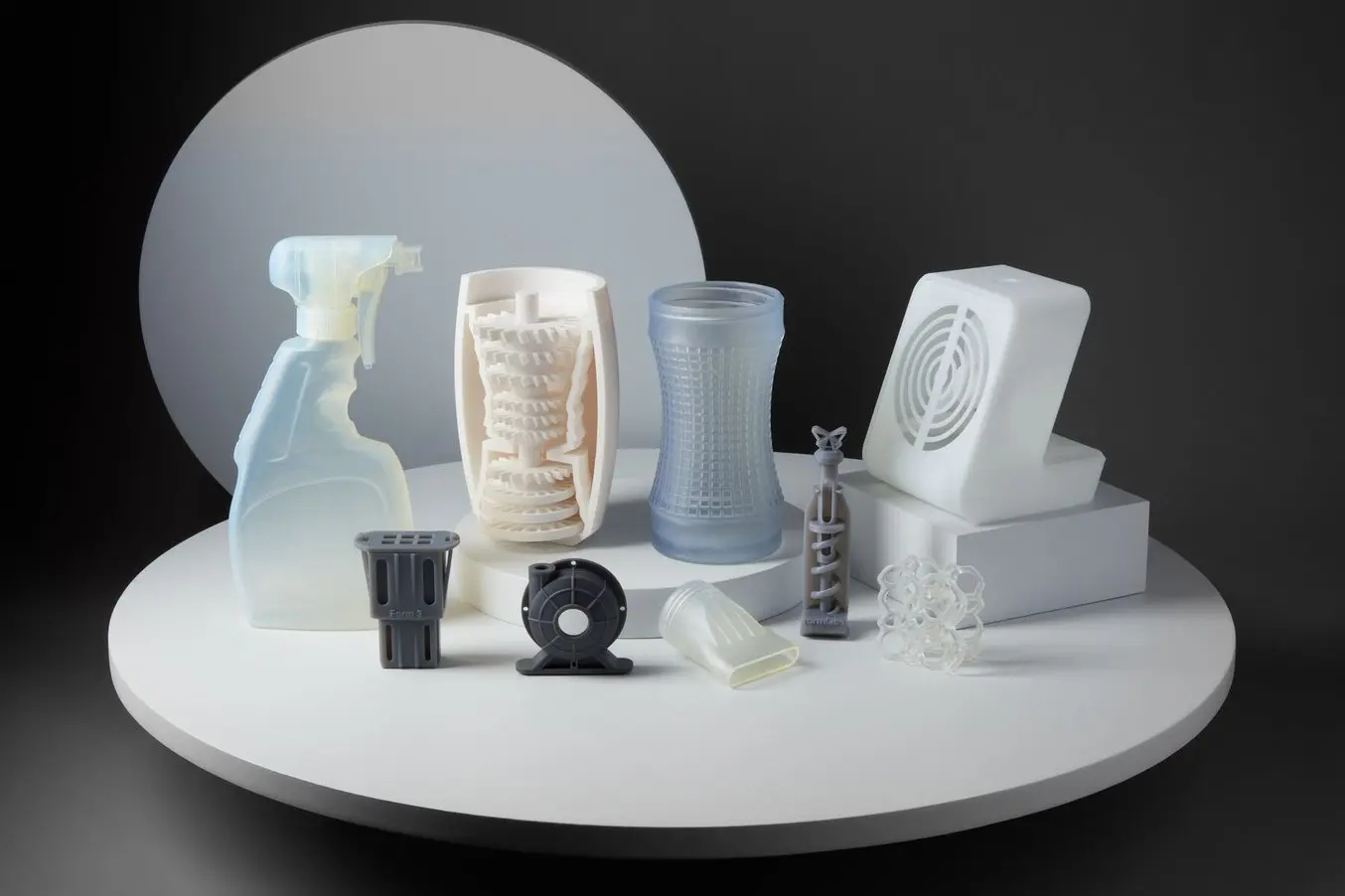
SLA光造形用のレジンは、FDM用レジンよりもコストがかかります。その理由は純粋に、特定の用途や製造方法に合わせて独自配合で製造されているため、業界標準のフィラメント材料よりも開発コストがかかるためです。
レジンは通常、プリンターメーカーによって配合され(ただし、オープンプラットフォームや単にホワイトラベル化して提供しているメーカーもあります)、その価格には開発にかかる高額な研究費が反映されています。独自レジンを製造するメーカーは、特定のプリンタで使用できるようレジンの設定をテスト・検証するためにもリソースを費やしています。このような研究開発への投資は消費者が支払うコストに影響を与えるものの、結果的により良い造形品質や信頼性の向上につながります。メーカー独自開発のレジンはABSやPLAのような業界標準ではなく、全く新しい材料であることも多く、その開発には膨大なリソースが必要です。
ほとんどのSLSメーカーは、パウダーを1kgあたり約$100ドルという業界標準の価格で提供していますが、Formlabsを含むいくつかのメーカーは、大容量生産を行うユーザー向けにボリュームディスカウントを提供しています。1kgあたりの価格が低いパウダーにはトレードオフもあります。造形時に熱が蓄積するのを防ぐために造形品同士の間隔を大きく開けて配置しなければならず、結果的に1回で造形できる量が減ってしまうのです。推奨のパッキング密度は約8~10%に制限されており、実際に造形に使用したのとほぼ同量のパウダーを廃棄しなければなりません。つまり、MJF方式プリンタの場合は多くのパウダーが再利用されずに廃棄されることになり、プリンタの運用コストが高まります。FormlabsのSLSプリンタにはパッキング率の制限がなく、密度が高ければ高いほどプリンタはより効率的に稼働します。
最後に、忘れがちな人件費も考慮すべき大切な要素の1つです。FDM方式の造形品は、特にサポート材をつけて造形した場合、滑らかな表面品質を実現するためにより入念な後処理作業が必要になります。一部の工業品質FDMプリンタでは可溶性のサポート材が使用できるため、溶剤でサポート材を溶解するだけでよく、後処理を素早く行うことができます。しかし、可溶性のサポート材を使用した場合でも、FDM方式の造形品でSLA光造形品と同じ表面品質と滑らかさを実現するためには、手作業によるサンディングが必要になることがあります。工業用途で使用する場合には、この追加の作業量がフィラメント3Dプリントの全体的な造形単価を押し上げる最も大きな要因になります。
SLA光造形方式の後処理作業としては、洗浄と材料によって二次硬化が必要ですが、これらの工程はFormlabsのForm WashやForm Cure、Form Wash LとForm Cure Lなどの装置を使用することでほぼ自動化が可能で、作業時間を最小限に抑えられます。工業品質のSLA光造形3Dプリンタでは、ソフトウェア、ファームウェア、材料エンジニアリングによってサポート材の迅速な取り外しが可能なライトタッチサポートや、後処理の簡素化が可能になります。
デザインによってはSLA光造形でもサポート材なしで造形できるものもあり、サポート材ありの場合でもサポート痕を除去して表面品質を整えるために軽くサンディングする程度で済みます。
SLS方式3Dプリントでは、造形品から未焼結パウダーを除去する後処理(サポート材が不要なためサポート材の取り外しはなし)と、表面品質を滑らかにするブラスト処理が必要です。これらの工程は、Fuse SiftやFuse Blastのような後処理ソリューションで簡単に高効率化・自動化できるため、人件費を最小限に抑えながら一貫性を確保できます。さらに、こういった自動化タスクはバッチで実行可能なため、大量生産における人件費削減にもつながります。
比較的単純な構造の試作品を限られた数量だけプリントする場合には、FDM方式の3Dプリンタが3つの方式の中で最も安い選択肢になります。SLA光造形プリンタは造形品質が高く、高精細かつ様々な材料を使用したプリントが可能です。複雑なデザインや大量のバッチ生産などには不向きですが、その分後処理にかかる労力が他の方式より少なく済みます。SLS 3Dプリンタは、他の方式に比べて初期費用は最も高くなるものの、材料であるパウダーのコストは競争力があり、人件費も最小限に抑えられるため、高スループットが求められる用途では最も費用対効果が高くなります。
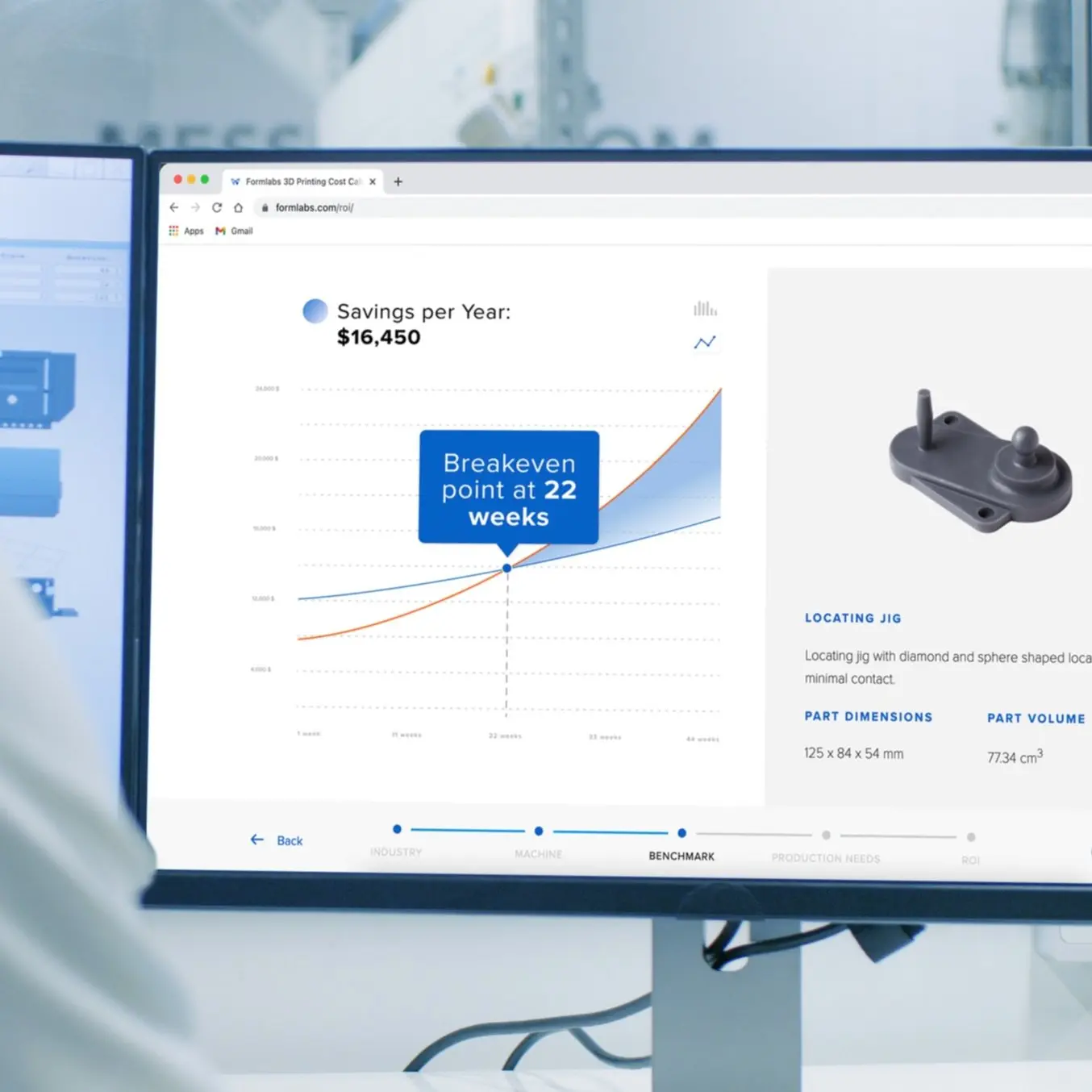
削減可能なコストと時間を算出
Formlabsの3Dプリンターでどれだけのコストと時間が削減できるのか、FormlabsのインタラクティブなROI計算ツールで是非ご確認ください。
FDM、SLA光造形、SLS 3Dプリンタを併用する
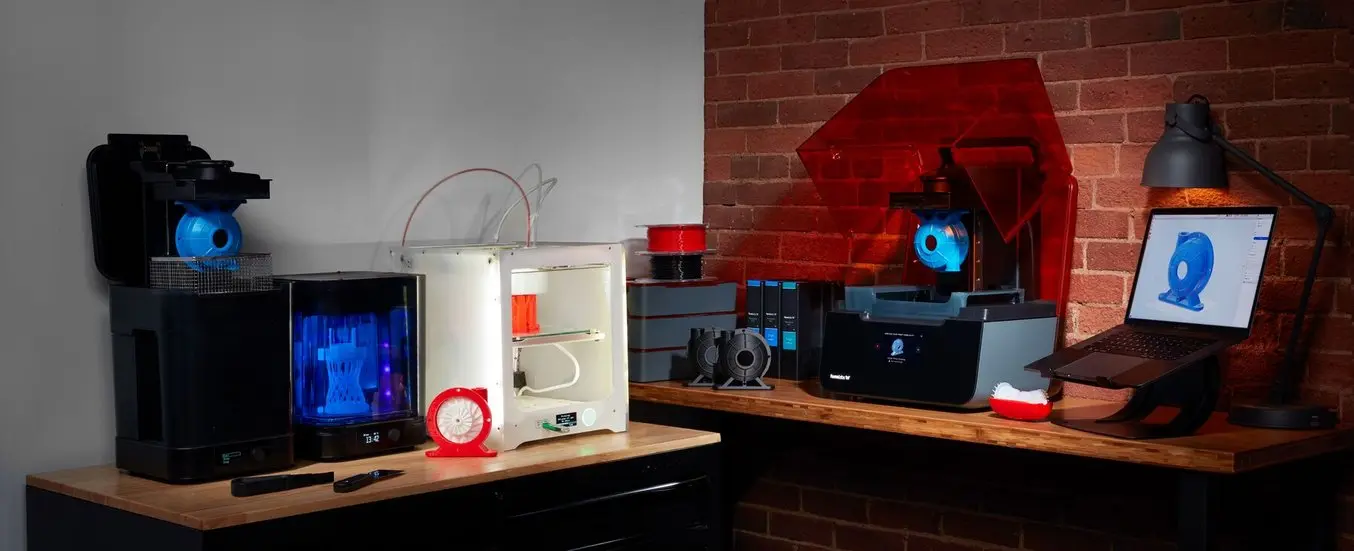
作業工程として定期的に3Dプリントを使用する企業の大半は、複数の方式を併用で活用しています。CNCや射出成形機と同様に、3Dプリンタはほとんどのエンジニア、デザイナー、メーカーにとって最適なものが異なります。製作する部品に求められる要件や製造工程のどの段階で使用するかによって適切な方式が変わるためです。FDM方式、SLA光造形方式、SLS方式の3Dプリンタはそれぞれ得意とする分野が異なり、補助的なツールとして使用することで最も価値を発揮します。
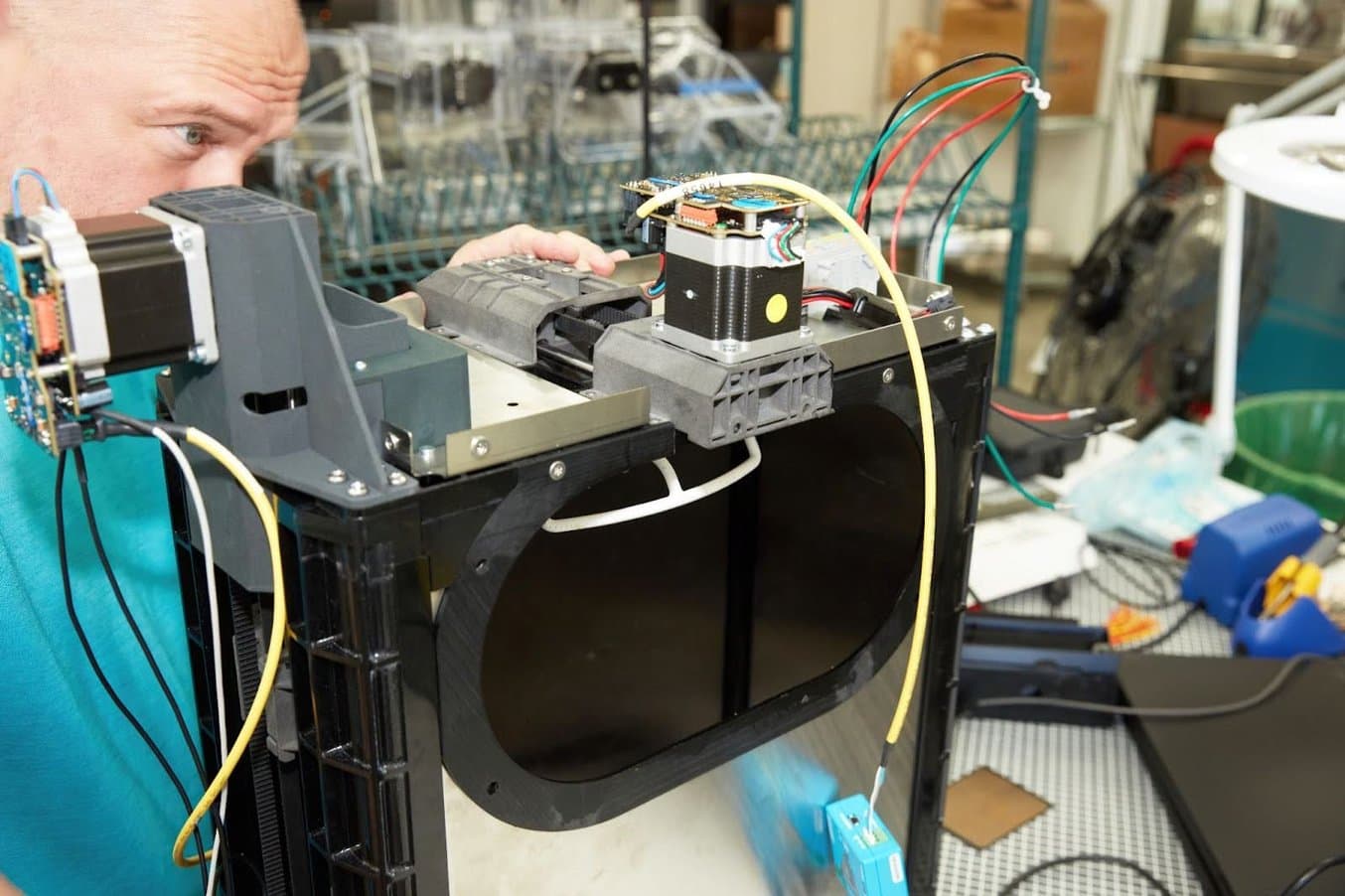
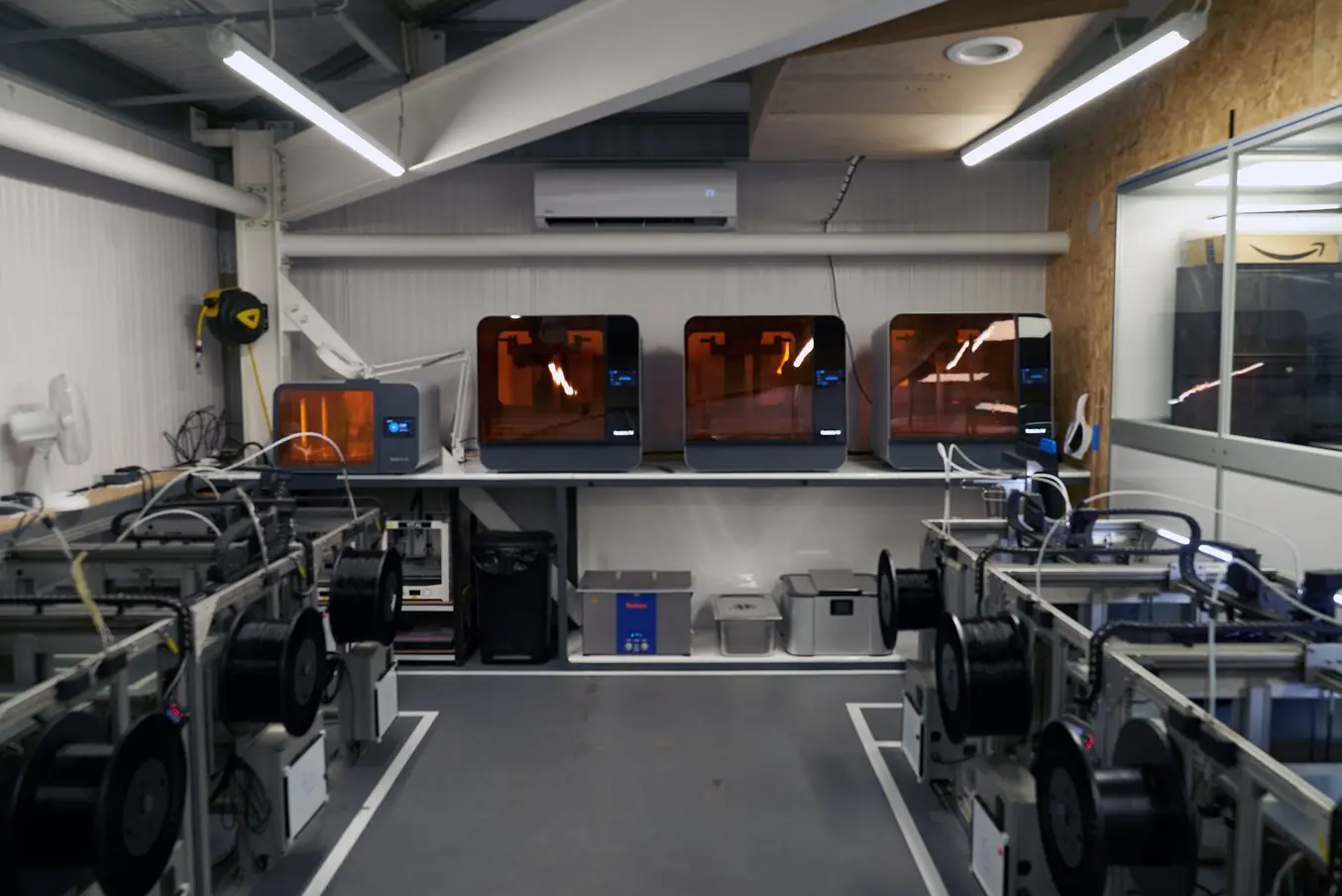
いくつか実用例を挙げます。
-
Broseは、FDM、SLA光造形、SLS方式のプリンタを駆使し、初期のプロトタイプから量産用のシートアセンブリに使用する250,000点もの部品まで、ありとあらゆるものを製作しています。
-
Labconcoは、SLA光造形、FDM、SLS方式を利用して実使用を目的としたラボ設備の製品コンポーネント、成形型、治具・固定具、試作品を製造しています。製品エンジニアのBrent Griffith氏はFDM方式をアイデアの構想と試作品製作に用いることでコストを削減し、その後SLA光造形またはSLSで実製品用に造形したものを機器やラボに導入しています。
-
Hyphenは、FDM方式の3Dプリンタを迅速な設計レビューに活用しながら、Formシリーズ SLA光造形プリンタで高精度かつ低摩擦な成形型部品や実製品用部品を製作しています。また、FuseシリーズのSLSプリンタも3台導入しており、繰り返しの荷重や負荷に耐えられる実製品用部品や繊細な電子機器を収容する実製品用部品を製作しています。同社の機械の構造部品の多くは、全てSLS 3Dプリントで製作したものを使用しています。
-
Vital AutoのラボマネージャーであるAnthony Barnicott氏は、14台のFDMプリンタ、3台のFormシリーズ 大容量SLA光造形プリンタ、5台のFuseシリーズ SLSプリンタを活用し、McLaren、Volvo、Nissan、Lotusなどの大手ブランドから依頼されたコンセプトカーの機能試作や設計レビュー用のパーツを製作しています。
-
Black Diamondでは、Fuseシリーズ SLS 3DプリンタにてNylon 12パウダーで実製品として使用するクライミング用品の部品を製作。射出成形に移る前にワサッチ山脈で実際に機能テストを行っています。また、Black Diamondチームは、ヘルメットのように大型モデルの設計レビュー用にデスクトップおよびベンチトップサイズのFormシリーズ SLA光造形3Dプリンタを活用し、滑らかで実製品に匹敵する表面品質を実現しています。
-
オーストラリアの水中翼船メーカーであるFoil Driveは、Fuseシリーズ SLSプリンタで実使用を想定した電気エンジン用エンクロージャを100~2000点ほど製作しています。Nylon 12パウダーはプロペラのアセンブリとして水中での酷使にも耐えることができ、同社が求める中程度の生産量にはSLS 3Dプリントは最も理にかなった選択肢となっています。Foil Driveは、Formシリーズ SLA光造形3DプリンタでTough 2000レジンとRigid 10Kレジンを使用し、製作した造形品をスナップインとスナップアウトが可能なプロペラとインペラのブレードに使用しています。SLA光造形はこのように、小型のアセンブリがスムーズに機能するよう厳しい公差が求められる用途に最適です。